多篇关于热冲压的论文
冲压技术论文
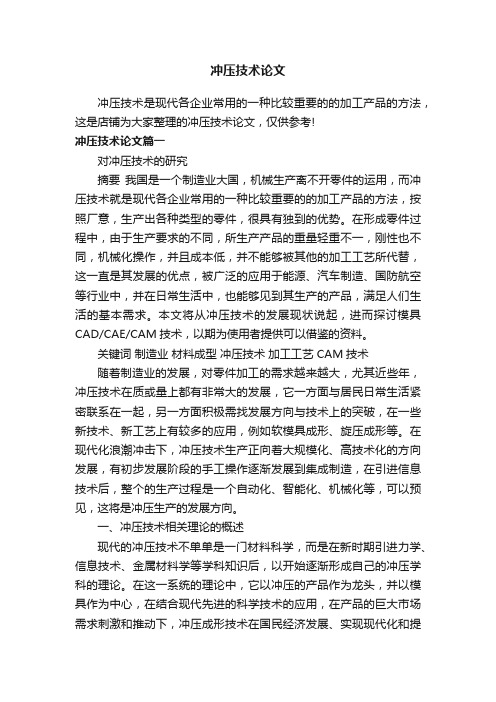
冲压技术论文冲压技术是现代各企业常用的一种比较重要的的加工产品的方法,这是店铺为大家整理的冲压技术论文,仅供参考!冲压技术论文篇一对冲压技术的研究摘要我国是一个制造业大国,机械生产离不开零件的运用,而冲压技术就是现代各企业常用的一种比较重要的的加工产品的方法,按照厂意,生产出各种类型的零件,很具有独到的优势。
在形成零件过程中,由于生产要求的不同,所生产产品的重量轻重不一,刚性也不同,机械化操作,并且成本低,并不能够被其他的加工工艺所代替,这一直是其发展的优点,被广泛的应用于能源、汽车制造、国防航空等行业中,并在日常生活中,也能够见到其生产的产品,满足人们生活的基本需求。
本文将从冲压技术的发展现状说起,进而探讨模具CAD/CAE/CAM技术,以期为使用者提供可以借鉴的资料。
关键词制造业材料成型冲压技术加工工艺 CAM技术随着制造业的发展,对零件加工的需求越来越大,尤其近些年,冲压技术在质或量上都有非常大的发展,它一方面与居民日常生活紧密联系在一起,另一方面积极需找发展方向与技术上的突破,在一些新技术、新工艺上有较多的应用,例如软模具成形、旋压成形等。
在现代化浪潮冲击下,冲压技术生产正向着大规模化、高技术化的方向发展,有初步发展阶段的手工操作逐渐发展到集成制造,在引进信息技术后,整个的生产过程是一个自动化、智能化、机械化等,可以预见,这将是冲压生产的发展方向。
一、冲压技术相关理论的概述现代的冲压技术不单单是一门材料科学,而是在新时期引进力学、信息技术、金属材料学等学科知识后,以开始逐渐形成自己的冲压学科的理论。
在这一系统的理论中,它以冲压的产品作为龙头,并以模具作为中心,在结合现代先进的科学技术的应用,在产品的巨大市场需求刺激和推动下,冲压成形技术在国民经济发展、实现现代化和提高人民生活水平方面发挥着越来越重要的作用。
冲压自动化生产的实现使冲压制造的概念有了本质的飞跃。
结合现代技术信息系统和现代化管理信息系统的成果,由这三方面组合又形成现代冲压新的生产模式―计算机集成制造系统CIMS。
汽车工业中热冲压成形工艺的应用
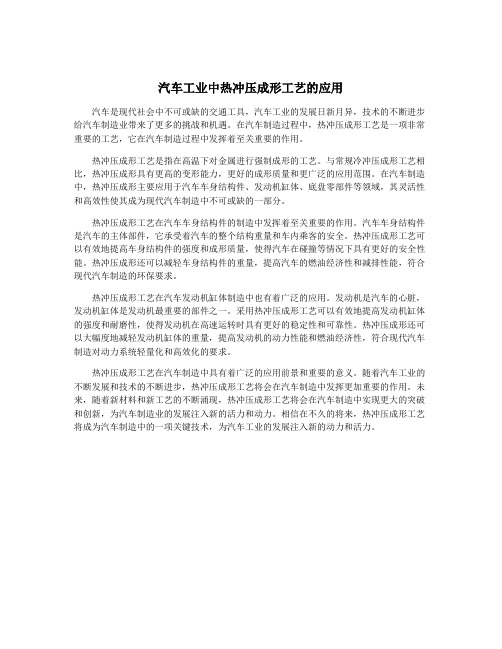
汽车工业中热冲压成形工艺的应用汽车是现代社会中不可或缺的交通工具,汽车工业的发展日新月异,技术的不断进步给汽车制造业带来了更多的挑战和机遇。
在汽车制造过程中,热冲压成形工艺是一项非常重要的工艺,它在汽车制造过程中发挥着至关重要的作用。
热冲压成形工艺是指在高温下对金属进行强制成形的工艺。
与常规冷冲压成形工艺相比,热冲压成形具有更高的变形能力,更好的成形质量和更广泛的应用范围。
在汽车制造中,热冲压成形主要应用于汽车车身结构件、发动机缸体、底盘零部件等领域,其灵活性和高效性使其成为现代汽车制造中不可或缺的一部分。
热冲压成形工艺在汽车车身结构件的制造中发挥着至关重要的作用。
汽车车身结构件是汽车的主体部件,它承受着汽车的整个结构重量和车内乘客的安全。
热冲压成形工艺可以有效地提高车身结构件的强度和成形质量,使得汽车在碰撞等情况下具有更好的安全性能。
热冲压成形还可以减轻车身结构件的重量,提高汽车的燃油经济性和减排性能,符合现代汽车制造的环保要求。
热冲压成形工艺在汽车发动机缸体制造中也有着广泛的应用。
发动机是汽车的心脏,发动机缸体是发动机最重要的部件之一。
采用热冲压成形工艺可以有效地提高发动机缸体的强度和耐磨性,使得发动机在高速运转时具有更好的稳定性和可靠性。
热冲压成形还可以大幅度地减轻发动机缸体的重量,提高发动机的动力性能和燃油经济性,符合现代汽车制造对动力系统轻量化和高效化的要求。
热冲压成形工艺在汽车制造中具有着广泛的应用前景和重要的意义。
随着汽车工业的不断发展和技术的不断进步,热冲压成形工艺将会在汽车制造中发挥更加重要的作用。
未来,随着新材料和新工艺的不断涌现,热冲压成形工艺将会在汽车制造中实现更大的突破和创新,为汽车制造业的发展注入新的活力和动力。
相信在不久的将来,热冲压成形工艺将成为汽车制造中的一项关键技术,为汽车工业的发展注入新的动力和活力。
汽车工业中热冲压成形工艺的应用

汽车工业中热冲压成形工艺的应用【摘要】热冲压成形工艺在汽车工业中扮演着重要的角色,本文将从汽车车身制造、发动机制造、零部件制造等方面介绍其应用。
热冲压成形不仅提高了零部件的强度和耐久性,还能减轻汽车重量,提高汽车性能。
但是在实际应用中,由于工艺复杂和设备投资较高,还存在一定的挑战。
随着技术的不断进步和发展,热冲压成形工艺在汽车工业中仍具有巨大的应用前景。
通过本文的介绍与分析,读者可以了解到热冲压成形工艺在汽车工业中的重要性和广泛应用,以及对汽车工业发展的积极影响,为相关领域的研究和应用提供参考。
【关键词】汽车工业、热冲压成形工艺、车身制造、发动机制造、零部件制造、影响、优势、不足、应用前景1. 引言1.1 热冲压成形工艺概述热冲压成形是一种将金属材料加热至高温,然后在高温下进行冲压成形的工艺。
这种工艺可以提高金属材料的塑性,减少成形过程中的应力和变形,从而得到更加复杂和精密的零件。
热冲压成形一般包括加热、成形和冷却三个阶段,其中加热阶段可以采用火炬加热、电加热或感应加热等不同方式。
成形阶段主要通过模具对加热后的金属材料进行形状调整,而冷却阶段则是将成形后的零件迅速冷却至室温,固定其形状。
热冲压成形工艺具有成形速度快、成形精度高、表面质量好等优点,特别适用于生产复杂形状、高精度要求的汽车零部件。
热冲压成形还可以有效提高金属材料的强度和硬度,延长零件的使用寿命。
在汽车工业中,热冲压成形已经成为一项重要的制造工艺,广泛应用于车身、发动机和各种零部件的制造中,为汽车工业的发展提供了强大的支撑。
2. 正文2.1 热冲压成形在汽车车身制造中的应用热冲压成形技术在汽车车身制造中具有重要的应用价值。
通过热冲压成形,可以实现复杂形状的零部件生产,并提高零部件的强度和耐磨性。
在汽车车身制造中,热冲压成形可以用于生产车门、车轮罩、车顶等车身部件。
热冲压成形可以实现对车身零部件的精确成形。
传统的冲压工艺往往无法满足对复杂形状的要求,而热冲压成形技术可以通过加热金属材料,使其更加易于成形,从而实现对复杂形状的零部件的生产。
冲压毕业设计论文

冲压毕业设计论文冲压毕业设计论文冲压技术作为一种常见的金属加工方法,广泛应用于各个行业。
随着现代工业的发展,冲压技术在产品制造中扮演着重要的角色。
本文将探讨冲压技术在毕业设计中的应用,以及相关的挑战和解决方案。
首先,冲压技术在毕业设计中的应用非常广泛。
无论是机械工程、汽车工程还是航空航天工程,冲压技术都扮演着重要的角色。
例如,在汽车工程中,冲压技术可以用于制造车身和车门等零部件。
通过冲压工艺,可以将金属板材按照设计要求进行成形,从而满足产品的功能和外观要求。
其次,冲压技术在毕业设计中也面临着一些挑战。
首先是材料选择的问题。
不同的产品对材料的要求不同,需要根据产品的性能要求选择合适的材料。
其次是冲压模具的设计。
冲压模具的设计需要考虑产品的形状、尺寸和工艺要求,同时还需要考虑生产效率和成本等因素。
最后是冲压过程中的变形和缺陷问题。
冲压过程中,材料可能会发生变形、裂纹和皱纹等问题,需要通过合理的工艺参数和模具设计来解决。
针对上述挑战,我们可以提出一些解决方案。
首先是材料选择方面,可以通过实验和模拟分析等方法来确定最适合产品要求的材料。
其次是冲压模具设计方面,可以利用计算机辅助设计和模拟分析等技术来优化模具结构,提高冲压效率和产品质量。
最后是冲压过程中的变形和缺陷问题,可以通过调整工艺参数、优化模具结构和改进冲压工艺等手段来解决。
除了上述的技术问题,冲压毕业设计还需要考虑一些其他因素。
例如,设计师需要考虑产品的可制造性和可维修性。
在设计过程中,需要充分考虑到冲压工艺的限制和生产设备的能力,以确保产品的可制造性。
同时,还需要考虑到产品的可维修性,即产品在使用过程中出现故障时的维修难度和成本。
最后,冲压毕业设计还需要关注环境保护和可持续发展。
随着人们对环境保护意识的提高,冲压工艺也需要不断优化,减少对环境的影响。
例如,可以采用节能设备和环保材料,减少废料产生和能源消耗。
综上所述,冲压技术在毕业设计中具有广泛的应用前景。
高强度钢板热冲压材料性能研究及应用

高强度钢板热冲压材料性能研究及应用
高强度钢板热冲压是一种先进的汽车制造技术,其在汽车轻量化和安全性能方面具有
重要的应用价值。
本文旨在介绍高强度钢板热冲压的材料性能研究及其在汽车制造中的应用。
高强度钢板热冲压的材料特性是研究的重点。
高强度钢板具有较高的拉伸强度和屈服
强度,以及较好的塑性和焊接性能。
其具有更高的抗拉强度和疲劳强度,可以更好地满足
汽车轻量化和安全性能的要求。
研究高强度钢板的组织结构、晶界和析出相等特征,可以
进一步了解其力学性能和加工性能。
高强度钢板热冲压的应用主要集中在汽车制造领域。
汽车轻量化是目前汽车工业发展
的重要趋势,而高强度钢板热冲压可以实现汽车零部件的轻量化设计。
通过在汽车车身、
底盘和动力系统等部件中应用高强度钢板热冲压技术,可以有效减少车身重量,提高燃油
利用率和行驶性能。
高强度钢板热冲压可以提高汽车的安全性能,增加车辆的抗碰撞能力,保护乘客的生命安全。
高强度钢板热冲压技术在国内外已经得到了广泛的应用。
国内汽车制造企业在汽车轻
量化和安全性能方面的应用越来越多。
国际上的汽车制造企业也纷纷将高强度钢板热冲压
技术应用到车辆生产中。
随着技术的不断发展和成熟,高强度钢板热冲压将在未来的汽车
制造中发挥更加重要的作用。
汽车工业中热冲压成形工艺的应用
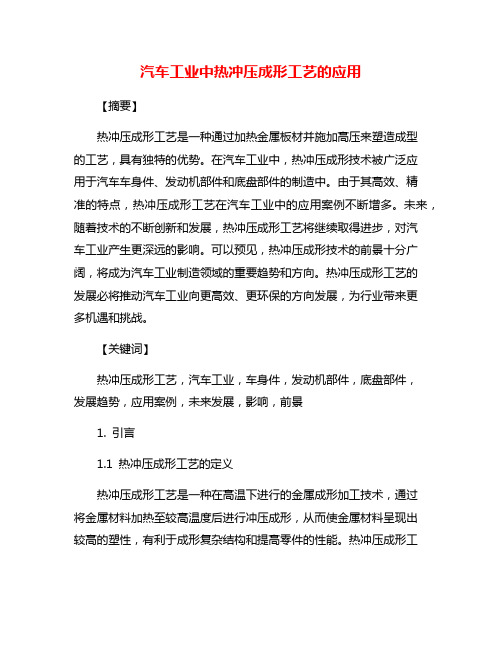
汽车工业中热冲压成形工艺的应用【摘要】热冲压成形工艺是一种通过加热金属板材并施加高压来塑造成型的工艺,具有独特的优势。
在汽车工业中,热冲压成形技术被广泛应用于汽车车身件、发动机部件和底盘部件的制造中。
由于其高效、精准的特点,热冲压成形工艺在汽车工业中的应用案例不断增多。
未来,随着技术的不断创新和发展,热冲压成形工艺将继续取得进步,对汽车工业产生更深远的影响。
可以预见,热冲压成形技术的前景十分广阔,将成为汽车工业制造领域的重要趋势和方向。
热冲压成形工艺的发展必将推动汽车工业向更高效、更环保的方向发展,为行业带来更多机遇和挑战。
【关键词】热冲压成形工艺,汽车工业,车身件,发动机部件,底盘部件,发展趋势,应用案例,未来发展,影响,前景1. 引言1.1 热冲压成形工艺的定义热冲压成形工艺是一种在高温下进行的金属成形加工技术,通过将金属材料加热至较高温度后进行冲压成形,从而使金属材料呈现出较高的塑性,有利于成形复杂结构和提高零件的性能。
热冲压成形工艺可以有效地改善金属材料的变形性能和力学性能,同时还可以减少成形过程中的应力和变形,提高成形零件的表面质量和精度。
1.2 热冲压成形工艺的优势热冲压成形工艺的优势包括:1. 制造成本低:相比传统的冷冲压成形工艺,热冲压成形可以减少成本,提高生产效率。
2. 成形精度高:热冲压成形可以在较高温度下进行,使得金属材料更容易塑性变形,从而实现更高的成形精度。
3. 降低材料损耗:利用热冲压成形可以减少材料的冷硬化现象,有效降低材料损耗,提高材料利用率。
4. 改善材料性能:热冲压成形可以改善材料的塑性和韧性,提高零件的强度和耐久性。
5. 可实现复杂结构:热冲压成形可以实现更复杂的汽车零部件结构,提高产品的功能性和设计性。
6. 环保节能:热冲压成形可以减少二次加工工序,减少能源消耗和环境污染,符合现代环保要求。
7. 适用性广泛:热冲压成形工艺适用于各种金属材料,适用于多种汽车零部件的制造,具有很高的通用性和适应性。
热冲压成形装备设计【文献综述】
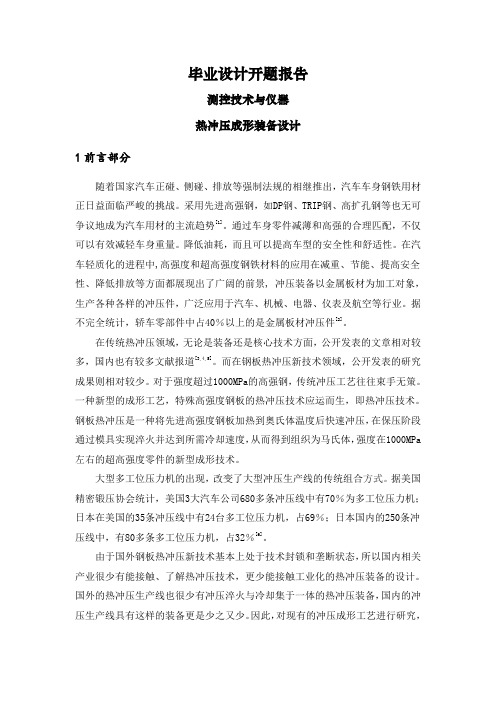
毕业设计开题报告测控技术与仪器热冲压成形装备设计1前言部分随着国家汽车正碰、侧碰、排放等强制法规的相继推出,汽车车身钢铁用材正日益面临严峻的挑战。
采用先进高强钢,如DP钢、TRIP钢、高扩孔钢等也无可争议地成为汽车用材的主流趋势[1]。
通过车身零件减薄和高强的合理匹配,不仅可以有效减轻车身重量。
降低油耗,而且可以提高车型的安全性和舒适性。
在汽车轻质化的进程中,高强度和超高强度钢铁材料的应用在减重、节能、提高安全性、降低排放等方面都展现出了广阔的前景, 冲压装备以金属板材为加工对象,生产各种各样的冲压件,广泛应用于汽车、机械、电器、仪表及航空等行业。
据不完全统计,轿车零部件中占40%以上的是金属板材冲压件[2]。
在传统热冲压领域,无论是装备还是核心技术方面,公开发表的文章相对较多,国内也有较多文献报道[3,4,5]。
而在钢板热冲压新技术领域,公开发表的研究成果则相对较少。
对于强度超过1000MPa的高强钢,传统冲压工艺往往束手无策。
一种新型的成形工艺,特殊高强度钢板的热冲压技术应运而生,即热冲压技术。
钢板热冲压是一种将先进高强度钢板加热到奥氏体温度后快速冲压,在保压阶段通过模具实现淬火并达到所需冷却速度,从而得到组织为马氏体,强度在1000MPa 左右的超高强度零件的新型成形技术。
大型多工位压力机的出现,改变了大型冲压生产线的传统组合方式。
据美国精密锻压协会统计,美国3大汽车公司680多条冲压线中有70%为多工位压力机;日本在美国的35条冲压线中有24台多工位压力机,占69%;日本国内的250条冲压线中,有80多条多工位压力机,占32%[6]。
由于国外钢板热冲压新技术基本上处于技术封锁和垄断状态,所以国内相关产业很少有能接触、了解热冲压技术,更少能接触工业化的热冲压装备的设计。
国外的热冲压生产线也很少有冲压淬火与冷却集于一体的热冲压装备,国内的冲压生产线具有这样的装备更是少之又少。
因此,对现有的冲压成形工艺进行研究,并针对高强度钢的热成形装置进行设计,进而从机电一体化和机械机构设计出发,从根本上解决高强度钢热冲压淬火与冷却生产工艺的改善,是一项不但有学术价值,而且将会产生巨大经济效益和提高汽车安全性能。
冲压新工艺(3篇)

第1篇随着我国制造业的快速发展,冲压工艺在汽车、家电、电子等行业中的应用越来越广泛。
传统的冲压工艺在满足产品性能和品质要求的同时,也存在一定的局限性,如能耗高、生产效率低、产品精度不足等。
为了推动制造业高质量发展,提升我国制造业的竞争力,冲压新工艺应运而生。
本文将从冲压新工艺的背景、关键技术、应用领域及发展趋势等方面进行探讨。
一、冲压新工艺的背景1. 传统冲压工艺的局限性传统冲压工艺主要依靠人力操作,设备较为简单,生产效率低,能耗高,且产品精度和一致性难以保证。
随着市场竞争的加剧,传统冲压工艺已无法满足现代制造业的需求。
2. 制造业高质量发展的需求为了提升我国制造业的竞争力,实现高质量发展,迫切需要提高生产效率、降低能耗、提高产品精度和一致性。
冲压新工艺的出现,为制造业提供了新的解决方案。
二、冲压新工艺的关键技术1. 智能化控制系统智能化控制系统是冲压新工艺的核心技术之一,通过引入PLC、工控机等智能设备,实现冲压过程的自动化、智能化。
智能化控制系统具有以下特点:(1)实时监控:对冲压过程中的各项参数进行实时监控,确保生产过程的稳定性和安全性。
(2)故障诊断:对设备故障进行实时诊断,提高设备运行效率。
(3)工艺优化:根据实际生产情况,优化工艺参数,提高产品精度和一致性。
2. 高精度模具技术高精度模具是冲压新工艺的关键,通过采用CNC加工、电火花加工等先进加工技术,实现模具的高精度制造。
高精度模具具有以下特点:(1)精度高:满足产品尺寸精度和形状精度要求。
(2)耐磨性:延长模具使用寿命。
(3)一致性:提高产品的一致性。
3. 精密检测技术精密检测技术在冲压新工艺中扮演着重要角色,通过引入高精度测量设备,如三坐标测量机、光学投影仪等,对产品进行全方位检测,确保产品质量。
精密检测技术具有以下特点:(1)高精度:满足产品精度要求。
(2)高效:提高检测效率。
(3)自动化:实现检测过程的自动化。
4. 绿色环保技术绿色环保技术是冲压新工艺的重要组成部分,通过优化工艺流程、降低能耗、减少废弃物排放,实现生产过程的绿色环保。
冲压工艺文献综述范文
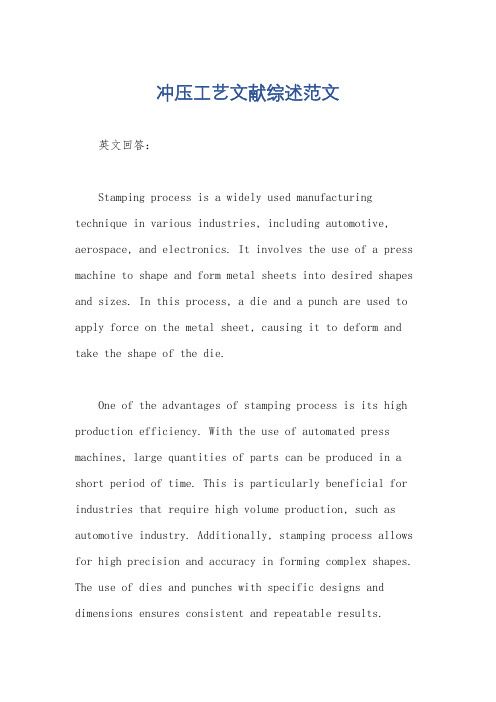
冲压工艺文献综述范文英文回答:Stamping process is a widely used manufacturing technique in various industries, including automotive, aerospace, and electronics. It involves the use of a press machine to shape and form metal sheets into desired shapes and sizes. In this process, a die and a punch are used to apply force on the metal sheet, causing it to deform and take the shape of the die.One of the advantages of stamping process is its high production efficiency. With the use of automated press machines, large quantities of parts can be produced in a short period of time. This is particularly beneficial for industries that require high volume production, such as automotive industry. Additionally, stamping process allows for high precision and accuracy in forming complex shapes. The use of dies and punches with specific designs and dimensions ensures consistent and repeatable results.Another advantage of stamping process is its versatility. It can be used to form a wide range of materials, including steel, aluminum, and copper. Furthermore, different types of stamping processes can be employed to achieve different results. For example, deep drawing is a type of stamping process used to create cylindrical or box-shaped parts, while progressive stamping is used to produce complex parts with multiple operations.Despite its advantages, stamping process also has some limitations. One of the challenges in stamping is the occurrence of defects, such as wrinkles, cracks, and springback. These defects can affect the quality and functionality of the stamped parts. To overcome these challenges, various techniques and strategies, such as adjusting the process parameters and using lubricants, can be employed.In conclusion, stamping process is a widely used manufacturing technique that offers high production efficiency, precision, and versatility. It is an essentialprocess in the production of various metal parts. However,it also presents challenges that need to be addressed to ensure the quality of the stamped parts.中文回答:冲压工艺是一种广泛应用于各个行业的制造技术,包括汽车、航空航天和电子等。
汽车冲压生产论文总结(热门18篇)

汽车冲压生产论文总结第1篇时光如水,日月如梭,转眼间我来到车间工作已经有十个多月的的时光,这十个多月的时光,承蒙车间领导和各位同事的帮忙指导,再通过自己的努力,在思想上、业务工作水平上都有了很大的提高,基本上完成了自己的本职工作,并取得了一些较好的成绩。
现将一年来工作总结如下:一、努力学习、勤奋工作日常工作中,我用心向其他人员学习。
我觉得,每位同事都是我的老师,他们中有业务高手,有技术尖兵。
正是不断地虚心向他们求教,使我在调入车间后,在最短的时光内熟悉了工作环境,懂得了各种材料的使用、一般问题出现的原因、维修的方法也都基本掌握。
在业务上,将以前的维修工作经验和车间的实际状况结合起来,使自身的素质和工作潜力得以不断提高。
二、班组管理在六月份,我被任命为维修主任,我深感自己肩上任务的重大。
为了不辜负领导的期望,我在严格要求自己的同时,还加强了班组管理:1、按照班前、后会议程序要求,开好会议,并做好记录。
将矿部、车间的各种文件和要求快速的传达给班组员工,使自己上承下达、承上启下的作用得以充分发挥。
使班组工人尽量了解好、了解透彻上级的`精神。
2、加强班组管理。
我制定了较为详细的班组规章制度和考核标准,性格强调从根本的管理入手。
三、进行设备规划,缩短维修周期我和车间领导一起,对设备进行了规划、从维修组织(设计、测量)到维修控制(工时、材料、库存量、费用),都做到有据可查。
我认为,做好设备的保养工作,将设备的备品备件预备的充足,是减少在故障发生后缩短维修时光的必要前提。
维修的方式有两种,一是事后维修,二是定期维修。
我们不能单纯的做到损坏了再维修,只要设备能用就尽量用,坏了再修。
而是就应在设备损坏前将故障排除,降低设备的故障率。
四、努力做好节资降耗和维修工作本人任维修主任以来,十分重视节资降耗和维修工作。
主要如下:(1)修旧利废16吨;(2)在对绿皮吉普车的修理过程中,维修班利用旧件,组装了后传动轴、后桥差速器、刹车总泵、后弹簧钢板;(3)对28#铲斗进行翻新;(4)下放并安装3立方内燃铲运机、立方电动铲运机、铲运机各2台;(5)下放复新凿岩台车一台;(6)架设风水管路1000多米;(7)安装钢溜井30多节;(8)新架设格筛、护栏10多个;(9)对各种安全防护设施及设备出现的临时性突发故障,做到及时抢修;(10)大修内燃机2次。
冲压工艺文献综述范文

冲压工艺文献综述范文一、冲压工艺的发展历程最早的冲压工艺可以追溯到古希腊时期。
古希腊人利用木制模具,通过手工操作对金属材料进行冲压加工。
随着工业革命的到来,冲压工艺得到了快速发展。
19世纪末,出现了机械化冲压设备,如手动冲床和液压冲床。
20世纪初,随着电气化技术的引入,出现了电动冲床和自动化冲床。
20世纪50年代,出现了数控冲床,标志着冲压工艺步入了数字化时代。
二、冲压工艺的基本原理冲压工艺通过在模具之间施加力使金属材料发生塑性变形,从而得到所需的形状和尺寸。
冲压工艺包括以下几个步骤:设计模具、选材、热处理、摸具、焊接、安装、试制、调整和使用,其中设计模具是冲压工艺中至关重要的一环。
三、冲压工艺的材料选择在冲压工艺中,金属材料选择直接影响到产品质量和生产成本。
常见的冲压材料有冷轧板、热轧板、镀锌板、不锈钢、铝合金等。
不同材料有不同的力学性能和加工性能,需要根据产品的要求和批量选择合适的材料。
四、冲压工艺的模具设计模具在冲压工艺中起着至关重要的作用,直接关系到产品的成型质量和生产效率。
模具设计需要考虑以下几个要素:产品几何形状、材料特性、加工工艺、成本等。
合理的模具设计可以减少废品率、提高生产效率,降低生产成本。
五、冲压工艺的优势与发展趋势冲压工艺具有高效、精密、经济、节能等优点,是现代工业生产中不可或缺的一种重要工艺。
未来,随着新材料、新工艺的不断涌现,冲压工艺将进一步发展和完善,为工业制造带来更多的机遇和挑战。
六、结语冲压工艺作为一种重要的金属加工工艺,在现代工业生产中发挥着不可替代的作用。
通过对冲压工艺的综述,我们可以看到其发展历程、基本原理、材料选择、模具设计、优势与发展趋势等方面的内容,对于深入了解和应用冲压工艺具有一定的参考价值。
希望本文能对读者有所启发,促进冲压工艺在工业领域的广泛应用与发展。
浅谈热冲压成形技术
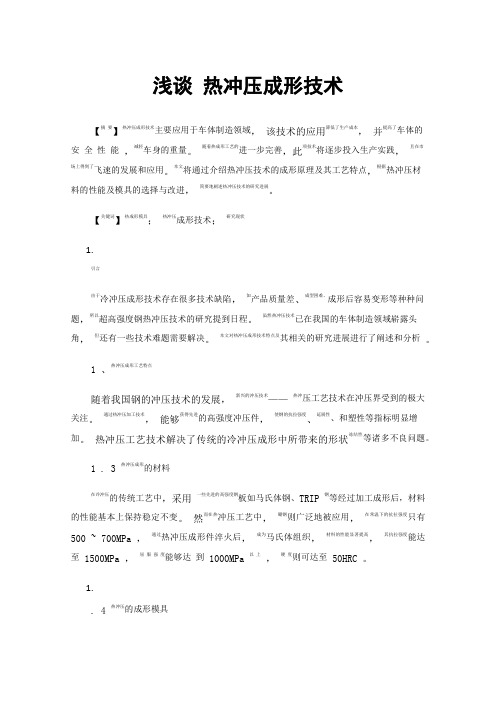
浅谈热冲压成形技术【摘要】热冲压成形技术主要应用于车体制造领域,该技术的应用降低了生产成本,并提高了车体的安全性能,减轻车身的重量。
随着热成形工艺的进一步完善,此项技术将逐步投入生产实践,且在市场上得到了飞速的发展和应用。
本文将通过介绍热冲压技术的成形原理及其工艺特点,根据热冲压材料的性能及模具的选择与改进,简要地阐述热冲压技术的研究进展。
【关键词】热成形模具;热冲压成形技术;研究现状1.引言由于冷冲压成形技术存在很多技术缺陷,如产品质量差、成型困难、成形后容易变形等种种问题,所以超高强度钢热冲压技术的研究提到日程。
虽然热冲压技术已在我国的车体制造领域崭露头角,但还有一些技术难题需要解决。
本文对热冲压成形技术特点及其相关的研究进展进行了阐述和分析。
1 、热冲压成形工艺特点随着我国钢的冲压技术的发展,新兴的冲压技术——热冲压工艺技术在冲压界受到的极大关注。
通过热冲压加工技术,能够获得先进的高强度冲压件,使钢的抗拉强度、延展性、和塑性等指标明显增加。
热冲压工艺技术解决了传统的冷冲压成形中所带来的形状冻结性等诸多不良问题。
1 . 3 热冲压成形的材料在冷冲压的传统工艺中,采用一些先进的高强度钢板如马氏体钢、TRIP 钢等经过加工成形后,材料的性能基本上保持稳定不变。
然而在热冲压工艺中,硼钢则广泛地被应用,在常温下的抗拉强度只有500 ~ 700MPa ,通过热冲压成形件淬火后,成为马氏体组织,材料的性能显著提高,其抗拉强度能达至 1500MPa ,屈服强度能够达到 1000MPa 以上,硬度则可达至 50HRC 。
1.. 4 热冲压的成形模具在传统的冷冲压成形技术中,模具只是用于零件的成形,冲压前后的机械强度不会发生显著差别。
但在热冲压的工艺中,模具需要成形、淬火等技术工艺,工序复杂,零件的强度高,综合性能很好。
热冲压模具的材料在成形和冷却淬火的技术中需要实现快速且均匀冷却还要有快速传热、冷却的功能。
热冲压工艺技术

热冲压工艺技术热冲压工艺技术是一种常用的金属加工方法,通常用于生产高精度、复杂形状的金属零件。
本文将介绍热冲压工艺技术的原理、应用领域,以及其优缺点。
热冲压是将金属板材加热至一定温度后,在冲床的作用下,通过模具将其冲压成所需形状的工艺。
由于加热后的金属板材具有良好的延展性和塑性,可以更容易地形成复杂的形状。
与传统的冷冲压相比,热冲压工艺技术具有以下几个优点:首先,热冲压可以改善金属板材的延展性。
在加热状态下,金属板材的结晶结构发生改变,晶格结构内的位错被激活,从而使金属板材具有更好的延展性,可以更容易地实现复杂形状的冲压。
其次,热冲压可以提高冲压成形的精度和表面质量。
由于加热状态下的金属板材具有更好的塑性,可以更容易地填充模具中的形状,从而得到更精确的冲压成形。
同时,加热状态下的金属板材有更好的流动性,可以减少表面缺陷,提高表面质量。
再次,热冲压可以减少变形力和模具磨损。
在加热状态下,金属板材的延展性增强,冲压时所需的变形力较小,可以降低模具的磨损。
热冲压工艺技术在许多领域得到了广泛应用。
例如,汽车制造领域,热冲压可以用于生产汽车车身、座椅骨架等复杂形状的零件;电子设备制造领域,热冲压可以用于生产手机壳、电池罩等精密零件;航空航天领域,热冲压可以用于生产飞机的机身、发动机零件等。
然而,热冲压工艺技术也存在一些局限性和挑战。
首先,热冲压工艺需要对加热温度、加热时间等参数进行精确控制,否则容易导致冲压成形不良。
其次,由于金属在加热过程中容易发生氧化、变色等问题,需要采取相应的防护措施,增加生产成本。
此外,热冲压工艺还需要使用专门的设备和模具,投入成本较高。
综上所述,热冲压工艺技术是一种高效、精确的金属加工方法,具有广泛的应用前景。
随着科技的不断进步和工艺技术的不断改进,相信热冲压工艺技术将在未来的金属加工领域发挥更大的作用。
热冲压的发展史

热冲压的发展史全文共四篇示例,供读者参考第一篇示例:热冲压技术是一种利用热力对金属进行塑性变形加工的方法,广泛应用于金属制造、汽车制造、航空航天等领域。
热冲压技术的发展历程可以追溯到上世纪50年代,随着科技的不断进步和工艺的不断完善,热冲压技术已经取得了长足的发展。
热冲压技术最初是在冷冲压工艺的基础上发展起来的。
冷冲压技术虽然具有高效、高精度、低成本的优势,但在处理高强度、高硬度的金属时往往会遇到困难。
热冲压技术的出现填补了这一空白,为金属加工技术的发展注入了新的活力。
上世纪50年代,美国、德国等发达国家开始推广热冲压技术。
热冲压技术通过提高金属的温度,使其易于塑性变形,并能够降低工件的强度和硬度,从而实现更高效、更精确的加工。
在这一时期,热冲压技术主要应用于军工、航空航天等领域,为国防建设和科技发展做出了重要贡献。
随着全球工业化的快速发展,热冲压技术逐渐走向了民用领域。
特别是在汽车制造领域,热冲压技术得到了广泛应用。
汽车零部件通常需要具有一定的强度和硬度,同时又要求精度高、成本低,热冲压技术正好满足了这些需求。
采用热冲压技术可以大幅提高汽车零部件的生产效率,降低生产成本,同时还能提高产品的质量和性能。
随着科技的不断进步,热冲压技术也在不断创新和完善。
近年来,一些新兴的热冲压技术逐渐兴起,如热成形、热冲熔复合成形等。
这些新技术在提高加工效率、降低能耗、改善工件质量等方面具有独特的优势,为热冲压技术的发展带来了新的契机。
未来,随着智能制造、数字化技术等的不断发展,热冲压技术将会迎来新的发展机遇。
热冲压技术将更加智能化、自动化,加工精度、效率将会大幅提高,同时还会实现对多品种、小批量生产的适应。
热冲压技术的应用领域也将不断拓展,涵盖更多的金属材料和产品类型。
第二篇示例:热冲压技术最早可以追溯到19世纪末。
当时,工业革命的推动下,人们开始寻求更有效率的金属加工方式。
在试图解决冲压过程中金属脆化和延展性下降的难题时,科学家们开始研究采用加热的方法来提高金属的变形性能。
热成型冲压
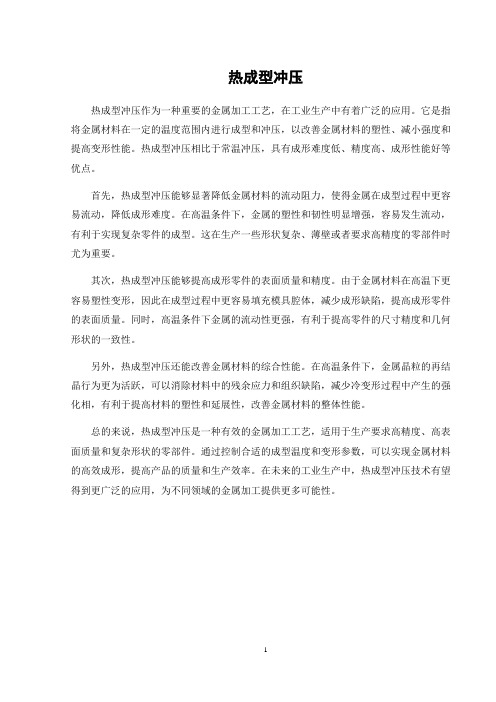
热成型冲压
热成型冲压作为一种重要的金属加工工艺,在工业生产中有着广泛的应用。
它是指将金属材料在一定的温度范围内进行成型和冲压,以改善金属材料的塑性、减小强度和提高变形性能。
热成型冲压相比于常温冲压,具有成形难度低、精度高、成形性能好等优点。
首先,热成型冲压能够显著降低金属材料的流动阻力,使得金属在成型过程中更容易流动,降低成形难度。
在高温条件下,金属的塑性和韧性明显增强,容易发生流动,有利于实现复杂零件的成型。
这在生产一些形状复杂、薄壁或者要求高精度的零部件时尤为重要。
其次,热成型冲压能够提高成形零件的表面质量和精度。
由于金属材料在高温下更容易塑性变形,因此在成型过程中更容易填充模具腔体,减少成形缺陷,提高成形零件的表面质量。
同时,高温条件下金属的流动性更强,有利于提高零件的尺寸精度和几何形状的一致性。
另外,热成型冲压还能改善金属材料的综合性能。
在高温条件下,金属晶粒的再结晶行为更为活跃,可以消除材料中的残余应力和组织缺陷,减少冷变形过程中产生的强化相,有利于提高材料的塑性和延展性,改善金属材料的整体性能。
总的来说,热成型冲压是一种有效的金属加工工艺,适用于生产要求高精度、高表面质量和复杂形状的零部件。
通过控制合适的成型温度和变形参数,可以实现金属材料的高效成形,提高产品的质量和生产效率。
在未来的工业生产中,热成型冲压技术有望得到更广泛的应用,为不同领域的金属加工提供更多可能性。
1。
热冲压工作总结

热冲压工作总结
热冲压工作是一项非常重要的工艺,它在制造业中扮演着至关重要的角色。
热
冲压工作可以用于生产各种各样的零部件,从汽车零部件到家用电器的外壳都可以通过热冲压工艺来完成。
在这篇文章中,我们将对热冲压工作进行总结,以帮助读者更好地了解这一工艺的重要性和应用。
首先,热冲压工作的原理是利用高温和压力来改变金属材料的形状。
通过加热
金属材料,使其变得更加柔软和易于成形,然后通过压力来将其塑形成所需的形状。
这种工艺可以大大提高金属材料的变形能力,使其能够完成更加复杂的形状。
其次,热冲压工作在制造业中有着广泛的应用。
无论是汽车制造、航空航天、
还是家用电器制造,都离不开热冲压工作。
通过热冲压工艺,可以大大提高生产效率,降低成本,同时还能够生产出更加精密和复杂的零部件,满足不同行业的需求。
另外,热冲压工作也需要严格的工艺控制和操作技能。
在进行热冲压工作时,
需要控制好加热温度、压力大小和成形时间等参数,以确保成形零部件的质量。
同时,操作人员需要具备丰富的经验和技能,才能够熟练地操作热冲压设备,完成高质量的生产任务。
总的来说,热冲压工作是一项非常重要的工艺,它在制造业中有着广泛的应用。
通过热冲压工艺,可以生产出各种各样的精密零部件,满足不同行业的需求。
因此,我们需要加强对热冲压工作的研究和应用,以推动制造业的发展,提高产品质量,降低生产成本。
汽车工业中热冲压成形工艺的应用

汽车工业中热冲压成形工艺的应用
热冲压成形工艺是一种将板材通过在热状态下冲压成型的工艺。
在汽车工业中,由于其一系列优越的性能(如更好的成形性、更高的成形效率、更好的性能一致性和更小的成本),该工艺应用日益广泛。
热冲压成形工艺的实现需要先将所需板材放入热膜处理器中进行加热处理。
热态下的板材,可以通过压力形变得更容易,变得更加延展和韧性更好。
此外,加热可以去除板材中含有的内部应力,从而增强板材的韧性和加工性。
与传统冷冲压相比,热冲压的最大优点是其更好的成形性。
特别是在复杂形状、细小尺寸或难以压制的材料方面,其成形能力优势更为明显。
由于在热状态下进行成形,所以材料在成形过程中的回弹和收缩都得到了降低,提高了成形效率和成品的一致性。
在汽车制造中,热冲压技术可以广泛应用于制造车身结构零部件、车门(尤其是边框)、座椅结构、液压布局安排、行李架、仪表板载体等零部件。
热冲压技术造就了沃尔沃汽车中高效的座椅结构制造、斯巴鲁汽车生产的车顶DTM组件等具体案例。
热冲压工艺使得汽车设计师可以设计出更加轻薄、更加复杂、更加坚固的材料。
汽车工业中零部件的制造需要满足的高要求,如材料的高强度、刚度和抗腐蚀性能等,都可以通过这种工艺实现。
同时,热冲压也可以大大降低汽车零部件的成本,为原材料的生产和加工提供了巨大的经济效益。
总之,热冲压工艺在汽车工业中的广泛应用,为提高零部件的成形性能、降低汽车零部件的成本、促进汽车工业的发展做出了贡献。
随着技术的不断发展,热冲压技术的应用范围将越来越广泛,为汽车工业的未来注入更加强劲的动力。
多篇关于热冲压的论文
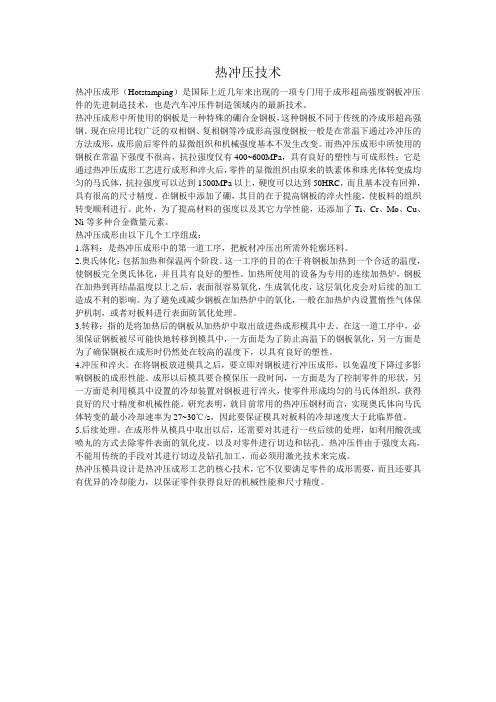
热冲压技术热冲压成形(Hotstamping)是国际上近几年来出现的一项专门用于成形超高强度钢板冲压件的先进制造技术,也是汽车冲压件制造领域内的最新技术。
热冲压成形中所使用的钢板是一种特殊的硼合金钢板,这种钢板不同于传统的冷成形超高强钢。
现在应用比较广泛的双相钢、复相钢等冷成形高强度钢板一般是在常温下通过冷冲压的方法成形,成形前后零件的显微组织和机械强度基本不发生改变。
而热冲压成形中所使用的钢板在常温下强度不很高,抗拉强度仅有400~600MPa,具有良好的塑性与可成形性;它是通过热冲压成形工艺进行成形和淬火后,零件的显微组织由原来的铁素体和珠光体转变成均匀的马氏体,抗拉强度可以达到1500MPa以上,硬度可以达到50HRC,而且基本没有回弹,具有很高的尺寸精度。
在钢板中添加了硼,其目的在于提高钢板的淬火性能,使板料的组织转变顺利进行。
此外,为了提高材料的强度以及其它力学性能,还添加了Ti、Cr、Mo、Cu、Ni等多种合金微量元素。
热冲压成形由以下几个工序组成:1.落料:是热冲压成形中的第一道工序,把板材冲压出所需外轮廓坯料。
2.奥氏体化:包括加热和保温两个阶段。
这一工序的目的在于将钢板加热到一个合适的温度,使钢板完全奥氏体化,并且具有良好的塑性。
加热所使用的设备为专用的连续加热炉,钢板在加热到再结晶温度以上之后,表面很容易氧化,生成氧化皮,这层氧化皮会对后续的加工造成不利的影响。
为了避免或减少钢板在加热炉中的氧化,一般在加热炉内设置惰性气体保护机制,或者对板料进行表面防氧化处理。
3.转移:指的是将加热后的钢板从加热炉中取出放进热成形模具中去。
在这一道工序中,必须保证钢板被尽可能快地转移到模具中,一方面是为了防止高温下的钢板氧化,另一方面是为了确保钢板在成形时仍然处在较高的温度下,以具有良好的塑性。
4.冲压和淬火。
在将钢板放进模具之后,要立即对钢板进行冲压成形,以免温度下降过多影响钢板的成形性能。
冲压热成型工艺

冲压热成型工艺
《冲压热成型工艺真有趣》
嘿,你们知道吗?我最近接触到了一个超有意思的东西,那就是冲压热成型工艺!
就说有一次啊,我去参观了一个工厂,一进去就被那巨大的机器轰鸣声给吸引住了。
我看到那些工人们正围着一台大机器在忙碌着。
那台机器可不简单,就是用来进行冲压热成型的。
我凑过去仔细瞧,只见一块平平无奇的金属板被送进了机器里。
然后“哐当”一声,机器就像大力士一样,狠狠地压了下去。
哇塞,就那么一瞬间,那块金属板就被压成了一个奇奇怪怪但又特别有型的形状。
就好像是变魔术一样,太神奇啦!
工人们熟练地操作着,一个接一个的零件就这么被快速地制造出来了。
我在旁边看得那叫一个目瞪口呆呀,这冲压热成型工艺也太牛了吧!看着那些被精准成型的零件,我心里不禁感叹,原来我们生活中好多东西都是通过这样的工艺制造出来的呀。
从那以后,我对冲压热成型工艺就有了特别深刻的印象。
每次看到一些金属制品,我就会想,这是不是也是通过冲压热成型做出来的呢。
这工艺可真是了不起,能把普通的金属变成各种有用的东西,为我们的生活带来了好多便利呀。
哎呀,冲压热成型工艺,真是让我大开眼界,我算是彻底被它给折服啦!哈哈!。
冲压工艺技术创新论文

冲压工艺技术创新论文
冲压工艺技术创新
冲压工艺技术是一种用来制造金属零件的常用方法。
随着科学技术的不断发展,冲压工艺技术也在不断创新,以满足不断变化的需求。
本文着重介绍了三种冲压工艺技术的创新。
首先,随着数字化技术的不断进步,计算机辅助设计(CAD)和计算机辅助制造(CAM)的应用成为冲压工艺技术创新的
重要手段。
通过CAD软件,设计师可以快速准确地绘制出零
件的图纸,并进行虚拟试验,以便进行优化设计。
CAM软件
则可以将CAD图纸转化为机器指令,实现自动化生产。
这种
数字化技术的应用,大大缩短了产品研发周期,提高了生产效率。
其次,材料的创新也推动了冲压工艺技术的发展。
例如,高强度钢的应用,使得冲压件可以承受更大的载荷,适用于更复杂的工作环境。
而镀锌钢板的应用则增加了冲压件的耐腐蚀性能,延长了使用寿命。
通过对材料性能的优化,冲压件的质量和可靠性得到了很大的提升。
最后,新型设备的应用也使得冲压工艺技术更加高效、精准。
例如,光纤激光切割机的应用,使得冲压件的切割更加精细,减少了材料的浪费。
而全自动冲压机的应用,实现了冲压工艺的连续化生产,提高了工作效率。
这些新型设备的应用,使得冲压工艺技术在制造业中得到了更广泛的应用。
综上所述,冲压工艺技术的创新涉及到许多方面,包括数字化技术的应用、材料的创新和新型设备的应用。
这些创新使得冲压工艺技术不断发展,更好地满足了人们对金属零件的需求。
未来,随着科学技术的不断进步,冲压工艺技术将会继续创新,为制造业的发展做出更大贡献。
- 1、下载文档前请自行甄别文档内容的完整性,平台不提供额外的编辑、内容补充、找答案等附加服务。
- 2、"仅部分预览"的文档,不可在线预览部分如存在完整性等问题,可反馈申请退款(可完整预览的文档不适用该条件!)。
- 3、如文档侵犯您的权益,请联系客服反馈,我们会尽快为您处理(人工客服工作时间:9:00-18:30)。
热冲压技术
热冲压成形(Hotstamping)是国际上近几年来出现的一项专门用于成形超高强度钢板冲压件的先进制造技术,也是汽车冲压件制造领域内的最新技术。
热冲压成形中所使用的钢板是一种特殊的硼合金钢板,这种钢板不同于传统的冷成形超高强钢。
现在应用比较广泛的双相钢、复相钢等冷成形高强度钢板一般是在常温下通过冷冲压的方法成形,成形前后零件的显微组织和机械强度基本不发生改变。
而热冲压成形中所使用的钢板在常温下强度不很高,抗拉强度仅有400~600MPa,具有良好的塑性与可成形性;它是通过热冲压成形工艺进行成形和淬火后,零件的显微组织由原来的铁素体和珠光体转变成均匀的马氏体,抗拉强度可以达到1500MPa以上,硬度可以达到50HRC,而且基本没有回弹,具有很高的尺寸精度。
在钢板中添加了硼,其目的在于提高钢板的淬火性能,使板料的组织转变顺利进行。
此外,为了提高材料的强度以及其它力学性能,还添加了Ti、Cr、Mo、Cu、Ni 等多种合金微量元素。
热冲压成形由以下几个工序组成:
1.落料:是热冲压成形中的第一道工序,把板材冲压出所需外轮廓坯料。
2.奥氏体化:包括加热和保温两个阶段。
这一工序的目的在于将钢板加热到一个合适的温度,使钢板完全奥氏体化,并且具有良好的塑性。
加热所使用的设备为专用的连续加热炉,钢板在加热到再结晶温度以上之后,表面很容易氧化,生成氧化皮,这层氧化皮会对后续的加工造成不利的影响。
为了避免或减少钢板在加热炉中的氧化,一般在加热炉内设置惰性气体保护机制,或者对板料进行表面防氧化处理。
3.转移:指的是将加热后的钢板从加热炉中取出放进热成形模具中去。
在这一道工序中,必须保证钢板被尽可能快地转移到模具中,一方面是为了防止高温下的钢板氧化,另一方面是为了确保钢板在成形时仍然处在较高的温度下,以具有良好的塑性。
4.冲压和淬火。
在将钢板放进模具之后,要立即对钢板进行冲压成形,以免温度下降过多影响钢板的成形性能。
成形以后模具要合模保压一段时间,一方面是为了控制零件的形状,另一方面是利用模具中设置的冷却装置对钢板进行淬火,使零件形成均匀的马氏体组织,获得良好的尺寸精度和机械性能。
研究表明,就目前常用的热冲压钢材而言,实现奥氏体向马氏体转变的最小冷却速率为27~30℃/s,因此要保证模具对板料的冷却速度大于此临界值。
5.后续处理。
在成形件从模具中取出以后,还需要对其进行一些后续的处理,如利用酸洗或喷丸的方式去除零件表面的氧化皮,以及对零件进行切边和钻孔。
热冲压件由于强度太高,不能用传统的手段对其进行切边及钻孔加工,而必须用激光技术来完成。
热冲压模具设计是热冲压成形工艺的核心技术,它不仅要满足零件的成形需要,而且还要具有优异的冷却能力,以保证零件获得良好的机械性能和尺寸精度。