我国复合材料风机叶片的几种制造工艺与发展前景_何东晓
风电叶片成型工艺

风电叶片成型工艺风能作为一种绿色环保型能源是可再生能源中最具开发潜力的一种。
随着风电技术的发展与日趋成熟,机型已达到5MW以上,叶片长度超过60米。
叶片是风力发电机组关键部件之一,具有尺寸大,外形复杂,精度要求高,对强度、刚度、和表面光滑度要求高等特点。
复合材料在风机叶片的制造中具备很多优势。
制造工艺主要有手糊成型、模压成型、预浸料成型、拉挤成型、纤维缠绕、树脂传递模塑以及真空灌注成型等工艺。
1、手糊工艺手糊是生产复合材料风机转子叶片的一种传统工艺。
在手糊工艺中,将纤维基材铺放于单模内,然后用滚子或毛刷涂敷玻璃布和树脂,常温固化后脱模。
手糊方法可用于低成本制造大型、形状复杂制品。
因为它不必受加热及压力的影响。
使用简单的设备和模具即可,另外相对于其他可行性方案成本更低廉。
手糊工艺生产风机叶片的主要缺点是产品质量对工人的操作熟练程度及环境条件依赖性较大,生产效率低和产品质量均匀性波动较大,产品的动静平衡保证性差,废品率较高。
特别是对高性能的复杂气动外型和夹芯结构叶片,还需要粘接等二次加工,粘接工艺需要粘接平台或型架以确保粘接面的贴合,生产工艺更加复杂和困难。
手糊工艺制造的风力发电机叶片在使用过程中出现问题往往是由于工艺过程中的含胶量不均匀、纤维/树脂浸润不良及固化不完全等引起的裂纹、断裂和叶片变形等。
手糊工艺往往还会伴有大量有害物质和溶剂的释放,有一定的环境污染问题。
手糊是一种已被证明的生产复合材料叶片工艺方法,但由于其产量低及部件的不连续性以及很难实现结构复杂,力学性能要求高的大型产品,促使人们将研究重点转移至其他生产方法。
2、模压成型模压成型工艺首先将增强材料和树脂置于双瓣模具中,然后闭合模具,加热加压,然后脱模,进行后固化。
这项工艺的优点在于纤维含量高和孔隙率低,并且生产周期短,精确的尺寸公差及良好的表面处理。
然而,模压成型适用于生产简单的复合材料制品如滑雪板,很难制造包括蒙皮、芯材和梁的叶片等复杂形状部件。
复合材料在风机叶片中的应用及能力认可现状

摘要本文简述了风机叶片用复合材料中不同纤维增强复合材料的优缺点,以及未来增强体和基体应用的发展趋势,同时总结了CNAS认可的风机叶片以及叶片中材料性能检测的认可现状。
认为碳纤维和玻璃纤维的混杂纤维、高性能纤维等增强体,以及聚氨酯树脂、热塑性树脂或可回收树脂等基体是未来风机叶片用复合材料的研究方向;同时通过总结分析风机叶片检测实验室在认可过程中的常见问题,为后续相关实验室认可提供了关注点。
风能是可再生的清洁能源,风力发电作为一种优质的发电方式,能够有效改善电力行业对石油、煤炭等不可再生能源的依赖,对于生态环境保护和适应时代发展具有重要的意义。
风力发电非常环保,且风能蕴量巨大,因此日益受到世界各国的重视。
根据国家能源局的统计数据显示,截止到2023年7月底我国风电装机容量约3.9亿kW,同比增长14.3%。
随着风机单机容量的不断扩大,风机叶片的长度也要求不断增加。
风力机叶片作为风能发电机中的核心部件,其良好的设计、可靠的质量和优越的性能是保证机组正常运行的重要因素。
叶片在工作中要承受多种外部环境的影响,因此要求叶片材质具有良好的强度、刚度和韧性以及抗风沙、抗冲击、耐腐蚀等性能。
目前,纤维增强复合材料在风力机叶片上得到了广泛的应用,其质量轻、强度高、耐久性好,已成为大型风力发电机叶片的首选材料。
1玻璃钢复合材料玻璃纤维增强热固性树脂复合材料,俗称玻璃钢,是一种以玻璃纤维或其制品为增强体,以热固性树脂为基体,并通过一定的成型工艺复合成的材料。
玻璃钢具有成本低、强度高、重量轻、耐腐蚀、易加工等特点,被广泛应用于风力发电机叶片的制造。
常见的玻璃纤维分为E型和S型,E型玻璃纤维也称无碱玻璃纤维,是一种硼硅酸盐玻璃,因其良好的电气绝缘性和机械性能,被大量用于生产玻璃钢。
S型玻璃纤维是一种特制的抗拉强度极高的硅酸铝-镁玻璃纤维,它的模量比E型玻璃纤维材料高出了18%;它的纤维拉伸强度为4600MPa,比E型玻璃纤维的3450MPa 增加了33%。
风力发电机叶片成型方法发展趋势
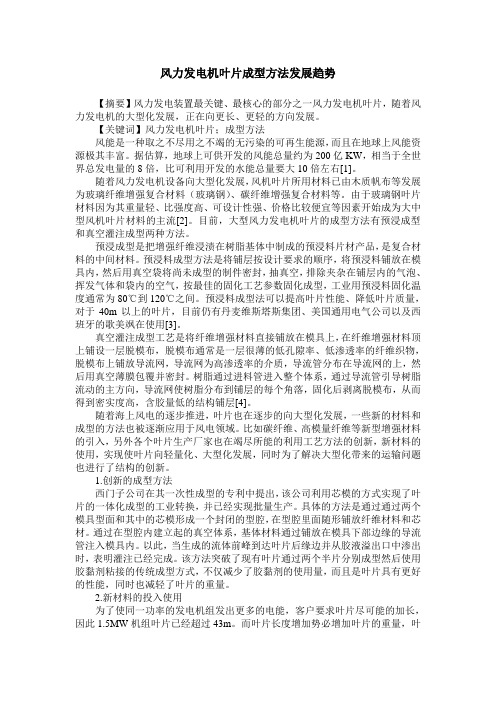
风力发电机叶片成型方法发展趋势【摘要】风力发电装置最关键、最核心的部分之一风力发电机叶片,随着风力发电机的大型化发展,正在向更长、更轻的方向发展。
【关键词】风力发电机叶片;成型方法风能是一种取之不尽用之不竭的无污染的可再生能源,而且在地球上风能资源极其丰富。
据估算,地球上可供开发的风能总量约为200亿KW,相当于全世界总发电量的8倍,比可利用开发的水能总量要大10倍左右[1]。
随着风力发电机设备向大型化发展,风机叶片所用材料已由木质帆布等发展为玻璃纤维增强复合材料(玻璃钢)、碳纤维增强复合材料等。
由于玻璃钢叶片材料因为其重量轻、比强度高、可设计性强、价格比较便宜等因素开始成为大中型风机叶片材料的主流[2]。
目前,大型风力发电机叶片的成型方法有预浸成型和真空灌注成型两种方法。
预浸成型是把增强纤维浸渍在树脂基体中制成的预浸料片材产品,是复合材料的中间材料。
预浸料成型方法是将铺层按设计要求的顺序,将预浸料铺放在模具内,然后用真空袋将尚未成型的制件密封,抽真空,排除夹杂在铺层内的气泡、挥发气体和袋内的空气,按最佳的固化工艺参数固化成型,工业用预浸料固化温度通常为80℃到120℃之间。
预浸料成型法可以提高叶片性能、降低叶片质量,对于40m以上的叶片,目前仍有丹麦维斯塔斯集团、美国通用电气公司以及西班牙的歌美飒在使用[3]。
真空灌注成型工艺是将纤维增强材料直接铺放在模具上,在纤维增强材料顶上铺设一层脱模布,脱模布通常是一层很薄的低孔隙率、低渗透率的纤维织物,脱模布上铺放导流网,导流网为高渗透率的介质,导流管分布在导流网的上,然后用真空薄膜包覆并密封。
树脂通过进料管进入整个体系,通过导流管引导树脂流动的主方向,导流网使树脂分布到铺层的每个角落,固化后剥离脱模布,从而得到密实度高,含胶量低的结构铺层[4]。
随着海上风电的逐步推进,叶片也在逐步的向大型化发展,一些新的材料和成型的方法也被逐渐应用于风电领域。
比如碳纤维、高模量纤维等新型增强材料的引入,另外各个叶片生产厂家也在竭尽所能的利用工艺方法的创新,新材料的使用,实现使叶片向轻量化、大型化发展,同时为了解决大型化带来的运输问题也进行了结构的创新。
风电叶片制造工艺的自动化发展综述

风电叶片制造工艺的自动化发展综述风电叶片是风力发电机组的核心部件之一,其制造工艺的自动化发展对于提高生产效率、降低成本、保障产品质量具有重要意义。
本文将从风电叶片制造的工艺流程、自动化技术在叶片制造中的应用以及未来发展趋势等方面进行综述,以探讨风电叶片制造工艺自动化发展的现状与未来。
一、风电叶片制造工艺流程风电叶片的制造工艺流程主要包括复合材料预制、叶片结构加工和表面处理三个主要环节。
在复合材料预制环节,主要包括纤维预浸料纺丝、叶片拼接和模具制作等工序;在叶片结构加工环节,主要包括叶片结构加固、连接部件安装和内部结构加工等工序;在表面处理环节,主要包括抛光、外观检验和防腐处理等工序。
整个工艺流程需要大量的人工操作和专业技能,制约了叶片制造的生产效率和产品质量。
二、自动化技术在风电叶片制造中的应用为了提高风电叶片制造的生产效率和产品质量,自动化技术在叶片制造中得到了广泛应用。
在复合材料预制环节,自动化技术主要体现在纺丝机的控制系统、自动拼接机器人和智能模具制作等方面,可以实现纺丝和拼接的自动化。
在叶片结构加工环节,自动化技术主要体现在数控加工设备、自动化连接件安装机器人和智能结构加固设备等方面,可以实现叶片结构加工的自动化。
在表面处理环节,自动化技术主要体现在自动抛光设备、外观检验机器人和智能防腐处理装置等方面,可以实现叶片表面处理的自动化。
这些自动化技术的应用使得风电叶片制造的生产效率得到了大幅提升,同时也提高了产品质量和稳定性。
三、风电叶片制造工艺自动化发展的未来趋势随着风电叶片的制造规模不断扩大和技术水平不断提高,风电叶片制造工艺的自动化发展也面临着新的挑战和机遇。
未来风电叶片制造工艺自动化的发展趋势可以从以下几个方面进行展望:1. 智能制造技术的应用:随着人工智能、物联网和大数据技术在制造业的不断发展,风电叶片制造工艺将会更加智能化。
通过智能传感器、自动控制系统和数据分析技术,可以实现叶片制造生产过程的实时监测和智能调控,提高生产效率和产品质量。
复合材料风电叶片技术现状及趋向
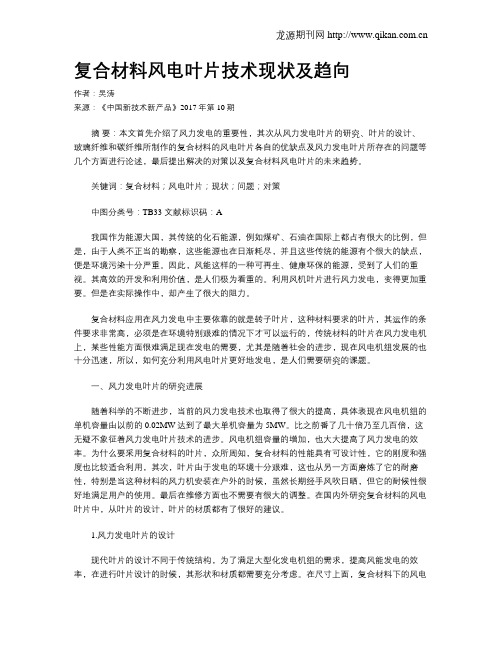
复合材料风电叶片技术现状及趋向作者:吴涛来源:《中国新技术新产品》2017年第10期摘要:本文首先介绍了风力发电的重要性,其次从风力发电叶片的研究、叶片的设计、玻璃纤维和碳纤维所制作的复合材料的风电叶片各自的优缺点及风力发电叶片所存在的问题等几个方面进行论述,最后提出解决的对策以及复合材料风电叶片的未来趋势。
关键词:复合材料;风电叶片;现状;问题;对策中图分类号:TB33 文献标识码:A我国作为能源大国,其传统的化石能源,例如煤矿、石油在国际上都占有很大的比例,但是,由于人类不正当的勘察,这些能源也在日渐耗尽,并且这些传统的能源有个很大的缺点,便是环境污染十分严重。
因此,风能这样的一种可再生、健康环保的能源,受到了人们的重视。
其高效的开发和利用价值,是人们极为看重的。
利用风机叶片进行风力发电,变得更加重要。
但是在实际操作中,却产生了很大的阻力。
复合材料应用在风力发电中主要依靠的就是转子叶片,这种材料要求的叶片,其运作的条件要求非常高,必须是在环境特别艰难的情况下才可以运行的,传统材料的叶片在风力发电机上,某些性能方面很难满足现在发电的需要,尤其是随着社会的进步,现在风电机组发展的也十分迅速,所以,如何充分利用风电叶片更好地发电,是人们需要研究的课题。
一、风力发电叶片的研究进展随着科学的不断进步,当前的风力发电技术也取得了很大的提高,具体表现在风电机组的单机容量由以前的0.02MW达到了最大单机容量为5MW。
比之前番了几十倍乃至几百倍,这无疑不象征着风力发电叶片技术的进步。
风电机组容量的增加,也大大提高了风力发电的效率。
为什么要采用复合材料的叶片,众所周知,复合材料的性能具有可设计性,它的刚度和强度也比较适合利用,其次,叶片由于发电的环境十分艰难,这也从另一方面磨炼了它的耐磨性,特别是当这种材料的风力机安装在户外的时候,虽然长期经手风吹日晒,但它的耐候性很好地满足用户的使用。
最后在维修方面也不需要有很大的调整。
复合材料风机叶片设计的现状与未来
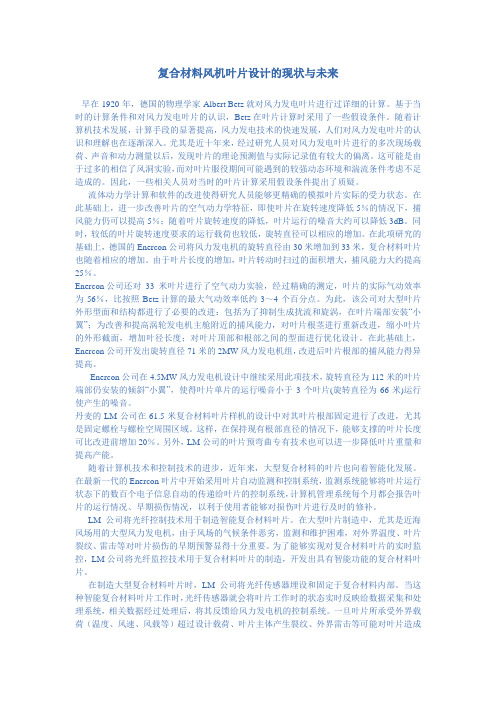
复合材料风机叶片设计的现状与未来早在1920年,德国的物理学家Albert Betz 就对风力发电叶片进行过详细的计算。
基于当时的计算条件和对风力发电叶片的认识,Betz 在叶片计算时采用了一些假设条件。
随着计算机技术发展,计算手段的显著提高,风力发电技术的快速发展,人们对风力发电叶片的认识和理解也在逐渐深入。
尤其是近十年来,经过研究人员对风力发电叶片进行的多次现场载荷、声音和动力测量以后,发现叶片的理论预测值与实际记录值有较大的偏离。
这可能是由于过多的相信了风洞实验,而对叶片服役期间可能遇到的较强动态环境和湍流条件考虑不足造成的。
因此,一些相关人员对当时的叶片计算采用假设条件提出了质疑。
流体动力学计算和软件的改进使得研究人员能够更精确的模拟叶片实际的受力状态。
在此基础上,进一步改善叶片的空气动力学特征,即使叶片在旋转速度降低5%的情况下,捕风能力仍可以提高5%;随着叶片旋转速度的降低,叶片运行的噪音大约可以降低3dB。
同时,较低的叶片旋转速度要求的运行载荷也较低,旋转直径可以相应的增加。
在此项研究的基础上,德国的Enercon 公司将风力发电机的旋转直径由30米增加到33米,复合材料叶片也随着相应的增加。
由于叶片长度的增加,叶片转动时扫过的面积增大,捕风能力大约提高25%。
Enercon 公司还对33米叶片进行了空气动力实验,经过精确的测定,叶片的实际气动效率为56%,比按照Betz 计算的最大气动效率低约3~4个百分点。
为此,该公司对大型叶片外形型面和结构都进行了必要的改进:包括为了抑制生成扰流和旋涡,在叶片端部安装“小翼”;为改善和提高涡轮发电机主舱附近的捕风能力,对叶片根茎进行重新改进,缩小叶片的外形截面,增加叶径长度;对叶片顶部和根部之间的型面进行优化设计。
在此基础上,Enercon 公司开发出旋转直径71米的2MW 风力发电机组,改进后叶片根部的捕风能力得异提高。
Enercon 公司在4.5MW风力发电机设计中继续采用此项技术,旋转直径为112米的叶片端部仍安装的倾斜“小翼”,使得叶片单片的运行噪音小于3个叶片(旋转直径为66米)运行使产生的噪音。
2023年风电叶片芯材行业市场发展现状
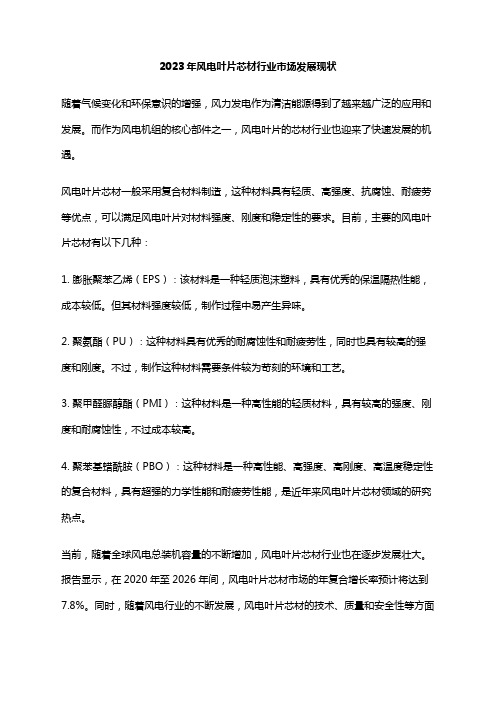
2023年风电叶片芯材行业市场发展现状随着气候变化和环保意识的增强,风力发电作为清洁能源得到了越来越广泛的应用和发展。
而作为风电机组的核心部件之一,风电叶片的芯材行业也迎来了快速发展的机遇。
风电叶片芯材一般采用复合材料制造,这种材料具有轻质、高强度、抗腐蚀、耐疲劳等优点,可以满足风电叶片对材料强度、刚度和稳定性的要求。
目前,主要的风电叶片芯材有以下几种:1. 膨胀聚苯乙烯(EPS):该材料是一种轻质泡沫塑料,具有优秀的保温隔热性能,成本较低。
但其材料强度较低,制作过程中易产生异味。
2. 聚氨酯(PU):这种材料具有优秀的耐腐蚀性和耐疲劳性,同时也具有较高的强度和刚度。
不过,制作这种材料需要条件较为苛刻的环境和工艺。
3. 聚甲醛脲醇酯(PMI):这种材料是一种高性能的轻质材料,具有较高的强度、刚度和耐腐蚀性,不过成本较高。
4. 聚苯基蜡酰胺(PBO):这种材料是一种高性能、高强度、高刚度、高温度稳定性的复合材料,具有超强的力学性能和耐疲劳性能,是近年来风电叶片芯材领域的研究热点。
当前,随着全球风电总装机容量的不断增加,风电叶片芯材行业也在逐步发展壮大。
报告显示,在2020年至2026年间,风电叶片芯材市场的年复合增长率预计将达到7.8%。
同时,随着风电行业的不断发展,风电叶片芯材的技术、质量和安全性等方面也得到了更高的要求。
因此,市场对高性能、高质量、环保的风电叶片芯材的市场需求也日益增加。
我国作为全球最大的风电市场,风力发电行业发展迅速。
目前,我国风电叶片芯材行业发展也已经进入到了快速发展的阶段。
我国已经具备了一定的风电叶片芯材生产能力和技术水平,并在不断进行技术创新和升级。
另外,我国的人力成本和生产成本也较低,因此我国的风电叶片芯材具有较强的价格竞争力。
总的来说,随着全球风电行业的不断发展和市场需求的不断增加,风电叶片芯材行业也将越来越受到关注和追捧。
对于风电叶片芯材企业来说,需要不断创新、提升技术水平和产品质量,以应对市场的竞争和满足客户的需求。
我国复合材料风机叶片的几种制造工艺与发展前景

1 日 舌 U
千 瓦 , 20 是 0 6年风 电装 机 72 千 瓦 的 4 。全 4 2万 O倍 球 风 电装 机长 期 增 长潜 力 巨大 , 来 三 年我 国其 丰 富 , 为刚 刚起 风 作 步发 展 风 电的国 家 具有 很 大 的市 场潜 力 。 随着 《 可
风力 发 电有着如 下显 著优点 : ①风力 发 电是一 种绿 色能源 。用 矿物 燃料发 电
每千 瓦要 产 生 0 6 1 斤 C 2风 力 发 电不 会 产 生 .8 公 0,
C2 0。 .
② 风力 发 电机 技术 成熟 , 障率低 , 故 可用 率高 达
9 %。大 型并 网 风力 发 电机 自动 化 程度 高 , 人 值 8 无 班, 可远程 控 制 。
维普资讯
第 2期
l 2
纤
维
复
C㈣
合
材
料
No 2 .
2O O 7年 6月
FⅡ | I
S 1E I[ 1
Jn. 2X7 u ,()
我 国复合 材 料 风 机 叶 片 的几 种 制造 工 艺 与 发 展前 景
何 东晓 黄 力 刚 , , 杨 松 安 庆 升 ,
千瓦 时 , 丹 麦 的 风 电市 场 上 , 发 电 15万 千 瓦 在 能 3
2 复合材料 风机 叶片的几种制造工艺
2 1 空腹薄壁填充泡沫结构合模工艺 . 这种 结 构 形式 的叶 片在 国 内使用 极 为普 遍 , 它
it d c s e h t a y s v r n ua trn rc se d t e k y tc n lg . nr u e mp ai l e ea ma f c i gp o es s a h e e h oo y o cl l u n
浅谈风电叶片的特点及制造工艺

浅谈风电叶片的特点及制造工艺【摘要】风力发电是一种清洁能源,而风电叶片是风力发电机组的核心部件之一。
本文从风电叶片的设计理念、材料选择、制造工艺、性能测试以及未来发展等方面进行了探讨。
在设计理念方面,风电叶片需要具有良好的气动性能以及结构稳定性,以提高风力发电效率。
在材料选择上,玻璃纤维和碳纤维等轻质高强度材料被广泛应用于风电叶片制造中。
制造工艺则包括模具制作、叶片成型、表面处理等多个环节,需要严格控制每一个步骤以确保叶片质量。
性能测试是评估叶片性能的重要环节,包括动态试验、静态试验等。
未来发展方向则是提高风电叶片的耐久性和轻量化设计,以满足不断增长的风力发电需求。
风电叶片作为风力发电的关键组成部分,其设计和制造工艺的不断创新将推动风力发电产业迈向更加繁荣和可持续发展。
【关键词】风电叶片、特点、制造工艺、设计、材料选择、性能测试、未来发展、总结、浅谈、引言、正文、结论1. 引言1.1 介绍浅谈风电叶片的特点及制造工艺风力发电是一种清洁能源,近年来得到了广泛的关注和发展。
而风力发电的核心部件之一就是风电叶片。
风电叶片是将风能转化为机械能的装置,是风力发电机组中最重要的组成部分之一。
风电叶片的设计理念是为了最大化地捕捉风能,并将其转化为旋转动能。
为了达到这一目的,风电叶片的外形通常是扁平且宽大的,这样可以在风场中更有效地捕捉风能。
叶片的表面通常会采用光滑的设计,减小风阻,提高效率。
在材料选择方面,风电叶片通常采用玻璃纤维增强复合材料,或者碳纤维等高强度材料。
这些材料具有轻量化,高强度,耐腐蚀等特点,非常适合用于风电叶片的制造。
制造工艺方面,风电叶片通常是通过模具成型的方式进行生产。
首先设计好叶片的模具,然后将复合材料注入模具进行成型,最后经过固化、热处理等工艺步骤,最终制成完整的风电叶片。
风电叶片的性能测试非常重要,可以通过风洞测试、动力学模拟等方式对叶片的性能进行评估,确保其符合设计要求并具有良好的稳定性。
复合材料在风电叶片制造领域的应用和未来发展

一、复合材料在风电叶片中的应用 常用的结构泡沫
Balsa轻木 PET
PVC HPE
对结构泡沫的技术要求: 抗压缩强度高; 吸胶量低; 热稳定性好; 需要有适宜树脂流
动的沟槽、孔结构; 工艺切口,利于铺
放时随型。
一、复合材料在风电叶片中的应用 Balsa轻木技术要求:
序号
测试项目
主梁 叶根
蒙皮
腹板
蒙皮:双轴玻纤,轻木,PVC 主梁:单向织物(UD) 叶根:双轴织物,三轴织物 腹板:双轴织物,PVC
大型风电叶片复合材料结构示意图
一、复合材料在风电叶片中的应用 大型风电叶片中使用的5种主要原材料
树脂基体:环氧树脂,乙烯基树脂 增强材料:玻璃纤维(E玻纤,高模玻纤),碳纤维 结构芯材:PVC,Balsa轻木 粘接胶:环氧粘接胶,聚氨酯粘接胶 涂料:聚氨酯涂料
碳纤维真空灌注复合材料 1880 141 631 119 57 9.9 177 9.22 70.84 5.13
碳纤维预预浸料 2050 134 765 133 39.47 6.91 126 7.86 57.39 3.56
三、复合材料在风电叶片中应用的未来发展
碳玻混杂复合材料
纵向拉伸模量随纤维质量含量变化的曲线
单位
值
测试方法及标准
1
标准密度
2
压缩模量Eyc
3
压缩模量Eyc和Ezc
5
剪切模量Gxy和Gxz
含水率
kg/m3
GPa MPa MPa
%
ISO 845 150±22.5
(测整板样品:1220*610mm)
≥1
35‐120 ≥ 70 <12
GB/T 8813‐2008 ISO 844:2004
复合材料风电叶片技术的现状与发展
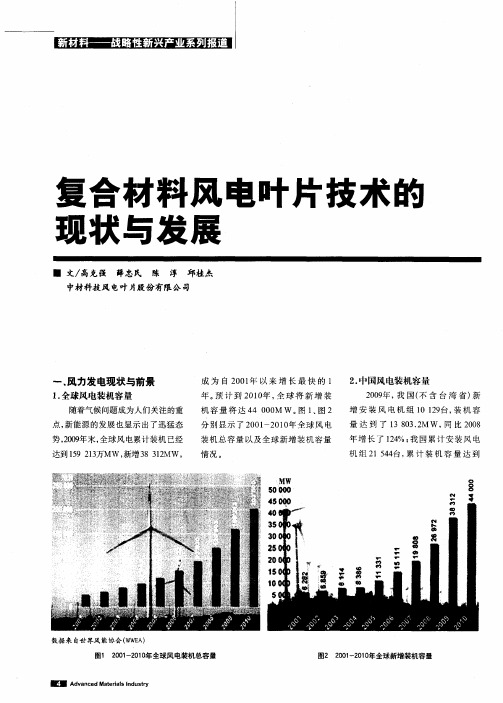
( ME A) GA S 仍使用预浸料工艺。
3 真空导入成型( I . R M)
真空导入成 型方法是先将 纤维织
物 等增强材料铺放在 模腔里进行抽真 空作业 , 此时树 脂基 体在 真空压 力 的
出新 的更 高要求 , 比如 , 随着 叶片长度 的增 加 , 高性 能碳 纤维 的用量 会越 来
预浸料成 型方法 是按设计要 求的
铺层顺序先将预浸料铺放在模具内, 然
2 世纪 末 , 电机组 主 流规格 在 0 风
欧 洲 是 70 5 kW , 国 是 5 0 美 0 kW 。 入 进
2 世 纪, 流机 型 已经达到 10 kW 。 l 主 50 比如 丹麦 新 建 风场 的单 机容 量 都 在 10 kW以 上 , 国 在北 海 建 设 的 风 00 德 场的单机功率在 5 0 k 。 00 W 国 内目前的主流风机是 10 k , 50 W 正在开发20kW 、50 、0 0 00 20kW 3 0 kW、
50 kW 甚 至 更 大 风 机 。 随 着 风 机 00 而
后用真空袋将尚未成型的制件密封 , 抽 真空, 以排 除在铺 层 内的气 泡、 挥发分 和袋 内的空气 , 按最佳 的固化工艺参数
在热压罐内固化成型叶片。 预浸料成型
四、叶片主要原材料
当前 , 国叶片主 要原 材料 包括 我 树 脂和 增 强 材料 , 下面 就 2 原 材料 种 的性能和分类加 以介绍 。
机 组 2 4 台 , 计 装 机 容 量 达 到 15 4 累
数 据 来 自世 界 风 能协 会 ( WE ) W A
图I 2 0 - 0 0 0 1 2 1年全球风电装机总容量
图2 20 - 0 0 0 1 2 1 年全球新增装机容量
文献综述 风机叶片发展研究
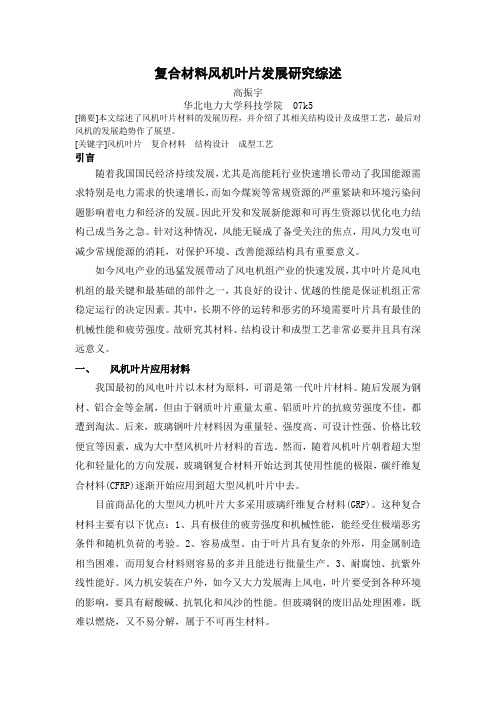
复合材料风机叶片发展研究综述高振宇华北电力大学科技学院 07k5[摘要]本文综述了风机叶片材料的发展历程,并介绍了其相关结构设计及成型工艺,最后对风机的发展趋势作了展望。
[关键字]风机叶片复合材料结构设计成型工艺引言随着我国国民经济持续发展,尤其是高能耗行业快速增长带动了我国能源需求特别是电力需求的快速增长,而如今煤炭等常规资源的严重紧缺和环境污染问题影响着电力和经济的发展。
因此开发和发展新能源和可再生资源以优化电力结构已成当务之急。
针对这种情况,风能无疑成了备受关注的焦点,用风力发电可减少常规能源的消耗,对保护环境、改善能源结构具有重要意义。
如今风电产业的迅猛发展带动了风电机组产业的快速发展,其中叶片是风电机组的最关键和最基础的部件之一,其良好的设计、优越的性能是保证机组正常稳定运行的决定因素。
其中,长期不停的运转和恶劣的环境需要叶片具有最佳的机械性能和疲劳强度。
故研究其材料、结构设计和成型工艺非常必要并且具有深远意义。
一、风机叶片应用材料我国最初的风电叶片以木材为原料,可谓是第一代叶片材料。
随后发展为钢材、铝合金等金属,但由于钢质叶片重量太重、铝质叶片的抗疲劳强度不佳,都遭到淘汰。
后来,玻璃钢叶片材料因为重量轻、强度高、可设计性强、价格比较便宜等因素,成为大中型风机叶片材料的首选。
然而,随着风机叶片朝着超大型化和轻量化的方向发展,玻璃钢复合材料开始达到其使用性能的极限,碳纤维复合材料(CFRP)逐渐开始应用到超大型风机叶片中去。
目前商品化的大型风力机叶片大多采用玻璃纤维复合材料(GRP)。
这种复合材料主要有以下优点:1、具有极佳的疲劳强度和机械性能,能经受住极端恶劣条件和随机负荷的考验。
2、容易成型。
由于叶片具有复杂的外形,用金属制造相当困难,而用复合材料则容易的多并且能进行批量生产。
3、耐腐蚀、抗紫外线性能好。
风力机安装在户外,如今又大力发展海上风电,叶片要受到各种环境的影响,要具有耐酸碱、抗氧化和风沙的性能。
航空发动机风扇叶片预制体研发现状及趋势

航空发动机风扇叶片预制体研发现状及趋势1 研究背景在航空领域高速发展的今天,我国航空发动机研发技术的落后,限制了航空领域的发展,而国外对我国实行技术封锁,也成为了我国发展的制约力。
发展提高发动机制造技术已成为我国迫切需要解决的问题,而发动机风扇叶片的性能对发动机性能提升起到了关键的作用。
因此,对发动机风扇叶片的研究就显得尤为重要。
目前,发动机已经发展到了第四代,应用复合材料及先进的工艺技术,增强体主要为3D编织物或3D机织物。
风扇叶片预制体主要有3种制备工艺,分别是预浸料铺层工艺、3D编织工艺以及3D机织工艺。
预浸料铺层形成的风扇叶片厚度方向没有纤维连接会使叶片在受到外力冲击时,容易造成分层而导致叶片整体失效。
这种技术制备的材料,层间黏结性较3D编织物、3D机织物差,但其自动化程度高、技术相对简单,且对于形状各异的构件来说,后期加工方便。
随着技术进步,此项技术实现了自动化,被称为自动铺丝工艺,并成功应用于预制体的制备当中,Rolls-Royce公司的TRENT系列发动机风扇叶片就是应用此项技术实现了预制体的自动化生产。
风扇叶片是一种结构较复杂的构件,3D编织可实现其结构的近净成型,后期加工简单。
在编织风扇叶片预制件时,可通过工艺结构设计和适当的增减纱技术来实现叶片厚度的变化,通过一次成型实现风扇叶片预制件的完整编织。
目前,国内的3D编织技术还停留在半自动化水平,与国外相比差距较大,由此造成了编织结构件的成本较高,发展速度缓慢。
在采用3D机织工艺进行风扇叶片预制体织造时,其核心技术是如何实现风扇叶片厚度的连续变化和一次成型。
通过设计,可形成两种工艺,第一种是通过减少经纱层的方式来实现厚度变化[1],这种方式存在织物中经纱断头的现象,织物完整性差;第二种是通过结构设计的方式实现,这种方式织成的构件完整性较好,且一次成型,对工艺结构设计要求较高。
2 国内外风扇叶片预制体制备技术研究现状2.1 国外制备技术发展现状预制体结构和制备技术成熟度影响着复合材料最终的性能,作为复合材料风扇叶片制造的关键技术之一,国外许多国家已经采用了多种复合材料风扇叶片预制体制备技术并实现了较高程度的自动化。
复合材料风力发电叶片制造技术及应用现状毕业论文

复合材料风力发电叶片制造技术及应用现状[摘要]:随着世界能源危机的日益严重,风能作为一种清洁的可再生能源日益受到各国政府重视。
作为风力发电装置中的重要一员,叶片技术成为制约风力发电发展的瓶颈。
复合材料具有高的比强度、比刚度,具有金属材料无可比拟的优越性,加上耐疲劳、结构稳定、抗腐蚀、耐高温等优势,成为大型风力发电叶片的首选材料。
[关键词]:风力发电;叶片;复合材料The Manufacturing Technology and Application ofComposite Wind Turbine BladeGao Qian(Class 01,Grade 07,material formation and control engineering,school of material science and engineering,Shaanxi University of Technology,Hanzhong,723003,Shaanxi )Tutor: Ai TaotaoAbstract:With the increasingly serious world energy crisis, wind, as a kind of clean and renewable energy resources, received a lot of attention from government all over the world. Being an important member of wind power device, blade technology has become the bottleneck on the development of wind power generation. Composite, with its high specific strength, high specific stiffness, incomparable advantage of metallic material, fatigue resistance, structural stability, corrosion resistance and thermo stability, has become the preferred material in large-scale wind power blades.Key words:wind power generation; blade; composite毕业设计(论文)原创性声明和使用授权说明原创性声明本人郑重承诺:所呈交的毕业设计(论文),是我个人在指导教师的指导下进行的研究工作及取得的成果。
2MW风机复合材料叶片材料及工艺研究

3 满足性能要求的材料种类及特点
3 1 增强材料 玻璃纤维增强叶片的受力特点是在玻璃纤维方 向能承受很高的拉应力 , 而其它方向承受的力相对 较小。叶片结构是由蒙皮和腹板组成 , 蒙皮采用夹 芯结构, 中间层是轻木, 上下面层为玻璃纤维增强材 料。面层由单向层和 , 45 − 层组成。单向层可选用 单向织物或单向玻璃纤维铺设 , 一般用 7 .1 或 4 .1 玻璃纤维布, 以承受由离心力和气动弯矩产生的轴 向应力。为简化成型工艺 , 可不用 , 45− 玻璃纤维布 层, 而采用 1 .1 玻璃纤维布, 均沿轴向铺设, 以承受 主要由扭矩产生的剪切应力, 一般铺放在单向层外 侧。腹板的结构形式也是夹芯结构。但是, 在蒙皮 与腹板的结合部位 , 即梁帽处必须是实心玻璃纤维 增强结构。这是因为此部分腹板与蒙皮相互作用, 应力较大 , 必须保证蒙皮的强度和刚度。 经过对长度为 10~ 60m 的叶片进行的统计表 明, 叶片质量按长度的三次方增加。叶片轻量化对 运行、 疲劳寿命、 能量输出有重要的影响。同时为了 保证在极端风载下叶尖不碰塔架, 叶片必须具有足 够的刚度。既要减轻叶片的质量, 又要满足强度与 刚度要求 , 有效的办法是采用碳纤维增强材料。碳 纤维增强材料的拉伸弹性模量是玻璃纤维增强材料 的 2~ 3 倍。 2 MW 叶片采用碳纤维增强可充分发挥 其高弹轻质的优点。经过分析 , 采用碳纤维 /玻璃纤 维混杂增强的方案, 叶片可减重 20 % ~ 40 % 。因此 采用碳纤维 /玻 璃纤维混杂增强对抑制质量的增大 是必要的 , 同时降低了风能成本, 叶片也可具有足够 刚性和长度
风力机复合材料叶片是风力机自主研发的核心 设备之一, 其价值达 到整机价值的 20 % 左右 , 其中 叶片的设计、 材料选择、 制造工艺选取对复合材料叶 片性能和成本起决定性作用。随着风力机组容量增 大 , 风力机叶片的尺寸随之增大 , 兆瓦级大型风力机 叶片已成为风力机国产化发展的主要瓶颈。 当前, 复合材料叶片追求容量大、 重量轻、 结构 强度高、 生产制造成本低、 运行安全可靠、 安装和维 护方便 , 整个风力机组单位千瓦时成本低 , 经济收益 高。复合材料叶片基本上是由聚酯树脂、 乙烯基树 脂和环氧树脂等热固性基体树脂与 E 玻璃纤维、 S 玻璃纤维、 碳纤维等增强材料, 通过手工铺放或树脂 注入等成型工艺复合而成。在自主研发 2MW 风力 机复合材料叶片的基础上, 综合考虑性能、 成本、 可 靠性等因素 , 选取合适的原材料及制造工艺是复合 材料叶片研制的关键。
航空发动机复合材料风扇叶片制造工艺应用进展
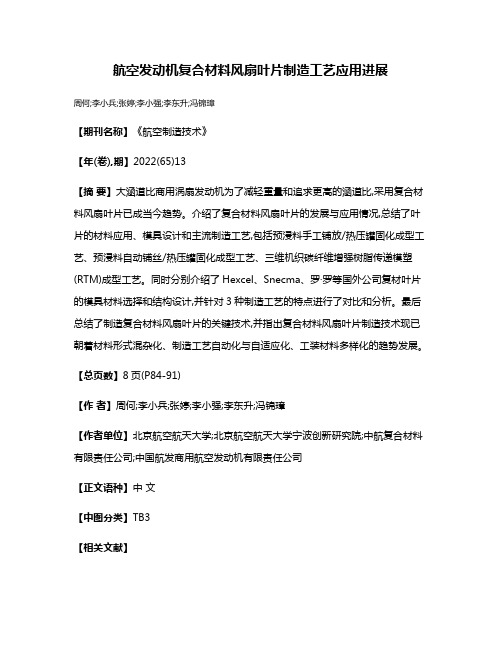
航空发动机复合材料风扇叶片制造工艺应用进展
周何;李小兵;张婷;李小强;李东升;冯锦璋
【期刊名称】《航空制造技术》
【年(卷),期】2022(65)13
【摘要】大涵道比商用涡扇发动机为了减轻重量和追求更高的涵道比,采用复合材料风扇叶片已成当今趋势。
介绍了复合材料风扇叶片的发展与应用情况,总结了叶片的材料应用、模具设计和主流制造工艺,包括预浸料手工铺放/热压罐固化成型工艺、预浸料自动铺丝/热压罐固化成型工艺、三维机织碳纤维增强树脂传递模塑(RTM)成型工艺。
同时分别介绍了Hexcel、Snecma、罗·罗等国外公司复材叶片的模具材料选择和结构设计,并针对3种制造工艺的特点进行了对比和分析。
最后总结了制造复合材料风扇叶片的关键技术,并指出复合材料风扇叶片制造技术现已朝着材料形式混杂化、制造工艺自动化与自适应化、工装材料多样化的趋势发展。
【总页数】8页(P84-91)
【作者】周何;李小兵;张婷;李小强;李东升;冯锦璋
【作者单位】北京航空航天大学;北京航空航天大学宁波创新研究院;中航复合材料有限责任公司;中国航发商用航空发动机有限责任公司
【正文语种】中文
【中图分类】TB3
【相关文献】
1.商用航空发动机先进复合材料风扇叶片研究进展
2.航空发动机宽弦空心风扇叶片的发展及应用
3.航空发动机风扇/压气机叶片制造关键技术
4.航空发动机风扇/压气机叶片激光冲击强化技术的发展与应用
5.第五代航空发动机空心风扇叶片的制造技术
因版权原因,仅展示原文概要,查看原文内容请购买。
- 1、下载文档前请自行甄别文档内容的完整性,平台不提供额外的编辑、内容补充、找答案等附加服务。
- 2、"仅部分预览"的文档,不可在线预览部分如存在完整性等问题,可反馈申请退款(可完整预览的文档不适用该条件!)。
- 3、如文档侵犯您的权益,请联系客服反馈,我们会尽快为您处理(人工客服工作时间:9:00-18:30)。
论是弯矩、 扭矩和离心力都是从叶尖向叶根逐渐递 增的 , 所以叶片结构的壁厚也是从叶尖向叶根逐渐
14
纤
维复合 材料 Nhomakorabea2007 年
递增的。由于复合材料具有高强度和低弹性模量的 特性, 叶片除满足强度条件外 , 尚需满足变形条件 , 特别是较长的风力机叶片尤其要注意叶片和塔架的 碰撞。叶身设计尽可能按等强度布置, 且在叶根部 分需有较大的安全系数。 3. 3 制造工艺 叶片的制造工艺向着工艺技术多样化的先进制
3
3. 1
复合材料风机叶片制造的关键技术
复合材料风机叶片的结构设计 复合材料风机叶片设计中要进行风力空气动力
学计算和结构力学计算。叶片的外形是通过空气动 力学设计确定的, 尺寸较复杂, 而且其尺寸、 表面光 洁度以及质量分布、 疲劳强度等都有较高要求。叶 片的结构形式是通过结构力学计算确定的 , 常见的 形式为设有加强筋的空腹薄壁和薄壁泡沫塑料夹芯 结构。确定合理的结构 , 以防止在受载 ( 离心力、 弯 矩和扭矩) 时失稳或局部变形。 叶根设计是叶片结构设计的关键。因为在叶根 处的荷载最大 , 而叶根连接大多靠复合材料的剪切 强度、 挤压强度或胶层剪切强度来传递荷载的, 而复 合材料的这些强度均低于其拉伸压缩及弯曲强度。 选择根端形式 时要注意防止根端出现 较大的剪应 力 , 尤其要避免出现层间剪切应力。目前用于大中 型风力机复合材料叶片的根端连接形式主要有复合 材料翻边法兰、 金属法兰和预埋螺栓。其中复合材 料法兰和预埋螺栓是运用最广泛的两种方法。 3. 2 叶片铺层设计 叶片的铺层是由叶片所受的外载荷决定的。无
1
前
言
千瓦, 是 2006 年风电装机 7422 万千瓦的 40 倍。全 球风电装机长期增长潜力巨大, 未来三年我国风电 设备市 场爆发 增长 : 据 权威 预测 我 国 2007、 2008、 2009 、 2010 年的新增风电装机容量分别达到 240 万 千瓦、 300 万千瓦、 400 万千瓦、 500 万 千瓦, 到 2010 年累计风电装机预计达到 1700 万千瓦 , 未来三年给 中国风电设备厂家带来了爆发式增长的市场。 风力发电设备一般由五部分组成: 电机、 叶片、 变速箱、 控制系统、 支柱塔架。其中叶片生产是国内 薄弱项, 大部分依赖进口。复合材料叶片是实现风 能转换成电能装置中的关键件, 特别是因其重量轻、 耐腐蚀、 耐气候性、 疲劳性能好、 成型工艺适合制造 复杂外形、 无需后加工等一系列其它材质无法比拟 的优点 , 已在大中型叶片中普遍采用 , 复合材料叶片 在国外风机上的 应用率为 95% 以上。目前我国风 力发电机组国产化率只达到 30~ 40% , 国家要求机 组国产化率达到 70% 以上 , 因此推进复合材料风机 叶片技术国产化面临着广阔的发展前景。
2
2. 1
复合材料风机叶片的几种制造工艺
空腹薄壁填充泡沫结构合模工艺
这种结构形式的叶片在国内使用极为普遍 , 它 由玻璃钢壳和泡沫芯组成, 它的成型方法比较简单, 主要有两种 , 一种是预发泡沫芯后整体成型, 另一种 是先成型两个半壳 , 粘接后再填充泡沫。它的特点 是抗失稳和局部变形能力较强, 成型时采用上下对
中国幅员辽阔, 风力资源极其丰富 , 作为刚刚起 步发展风电的国家具有很大的市场潜力。随着 可 再生能源法 的颁布和 京都协议书 的生效, 中国把 可再生能源中的风能利用放在首要位置, 使得风力 发电面临着前所未有的发展形势。 风力发电有着如下显著优点: 风力发电是一种绿色能源。用矿物燃料发电 每千瓦要产生 0. 681 公斤 CO2 , 风力发电不 会产生 CO2 。 风力发电机技术成熟, 故障率低 , 可用率高达 98% 。大型并网风力发电机自动化程度高 , 无人值 班, 可远程控制。 发电成本低。在可再生能源中, 风力发电的 成本最低。随 着风力发电机的 单机容量的不 断提 高, 技术的不断完善 , 风力发电成本可与常规能源相 竞争。以德国和丹麦为例。一台 600 千瓦的并网风 力发电机 , 在德国的风电市场上, 每年能发电 130 万 千瓦时 , 在丹麦的 风电市场 上, 能 发电 135 万千 瓦 时, 假设风力发电机的寿命 20 年, 再加上维修等费 用, 风力发电成本在德国和丹麦分别为 5. 6 美分/ 千 瓦时和 4. 1 美分/ 千瓦时。 全球风电增长潜力巨大 : 风力发电是目前技术 最成熟、 最具规模化发 展前景的可再 生能源, 根据 GWEC 的乐观预测 , 2050 年全球风电装机达到 30 亿
叶片长 54 米 , 重 20 吨。目前 , 该公司也有意进入中 国风力机组及叶片市场。此外 , 西班牙的 GAMESA 公司也是国际著名的风力设备和叶片生产商 , 目前 也已决定在中国设厂进行叶片制造。 2007 年 4 月, 天津东汽风电叶片工程公司在天 津经济技术开发区化学工业区开工奠基 , 到 2008 年 可形成 600 套 1. 5 兆瓦风电机组叶片的生产能力。 二期工程将形成 100 套 2. 5 兆瓦、 50 套 5 兆瓦风电 机组叶片以及整机设计、 总装能力。 有关数据显示, 1994 年之前 , 世界上大量使用 的风电机单机容量在 200 千瓦以下, 1996 年 300 千 瓦机组成为主流机型, 1998 年 600 千瓦机组成了主 力机型。 1999 年以后, 兆瓦级机组占当年世界新增 风电机组容量的 9. 7% , 2001 年达到 52. 3% , 2003 年 达到 71. 4% 。目前美国主流机型为 1. 5 兆瓦 , 丹麦 主流机型为 2. 0 兆瓦至 3. 0 兆瓦。业内专家分析指 出 , 从我国现有的风电项目来看 , 2004 年以前建成 的项目选用的机型基本为 600 千瓦至 850 千瓦, 从 2004 年起国内风电场开始选用兆瓦级机组 , 部分正 在立项的海上风电场选用了 2 兆瓦的机组。上海目 前规模各为 10 万千瓦的东海大桥海上风电场和奉 贤海上风电场已经完成可行研究, 两处风电场均将 选择单机容量 2 兆瓦机型。由于兆瓦级机组在任何 风场条件下, 在投资、 运营等方面相对于小机组 ( 如 850 千瓦 ) 都具有 明显的 经济性。根据 专家估 计, 十一五 期间, 全国新建风电场 2/ 3 左右将采用 1. 5 兆瓦及以上机型。只有山区等交通、 运输、 吊装等受 到限制的地区将采用 1. 5 兆瓦以下的机型。而 2 兆 瓦机组陆上风电的优势不明显, 更适合海上风电场。 因此, 1. 5 兆瓦在相当长时间内会成为一种主流机 型 , 在国内将有一个较大的市场。 随着我国风电市场的迅猛发展和国家相关政策 的出台, 从风电机组到风机叶片的国产化步伐会逐 渐加快。未来几年内 , 国内风电机组及风机叶片将 打破基本上完全依赖进口的局面, 叶片制造领域将 会出现数家具有竞争力的企业, 结束国外叶片制造 企业垄断国内市场的局面。
2期
何东晓等 : 我国复合材料风机叶片的几种制造工艺与发展前景
13
模、 螺栓或液压等机械加压成型, 对模具的刚度和强 度要求高。这种方法只在小型叶片生产中采用。 大中型叶片宜采用两半壳胶合工艺 , 采取空腹 薄壁结构 , 成型方式主要有两种, 即两半壳胶合及内 气压袋整体成型。安装在福建平潭的风电站, 由比 利时政府资助, HMZ 公司生产的 4 台 200KW 风力机 就采用了空腹薄壁结构叶片。一般内气压袋成型仅 限于较小的叶片。 上述两种结构工艺通常只用于生产叶片长度比 较短和批量比较小的时候。 2. 2 闭模真空浸渗工艺 ( RTM) 闭模真 空 浸 渗工 艺 又 称 真 空灌 注 成 型 工 艺 ( RTM) 。采用闭模真空浸渗工艺制备风力发电转子 叶片时, 首先把增强材料铺覆在涂硅胶的模具上, 增 强材料的外形和铺层数根据叶片设计确定, 在先进 的现代化工厂, 采用专用的铺层机进行铺层, 然后用 真空辅助浸渗技术输入基体树脂 , 真空可以保证树 脂能很好地充满到增强材料和模具的每一个角落。 真空辅助浸渗技术制备风力发电转子叶片的关 键有 : 2. 2. 1 2. 2. 2 优选浸渗用的基体树脂。特别要保证树脂 的最佳粘度及其流动性; 模具设计必须合理。特别对模具上树脂注 入孔的位置、 流通分布更要注意, 确保基体树脂能均 衡地充满任何一处。 2. 2. 3 工艺参数要最佳化。真空辅助浸渗技术的 工艺参数要事先进行实验研究 , 保证达到最佳化。 2. 2. 4 增强材料在铺放过程中保持平直, 以获得良 好的力学性能。同时注意尽可能减少复合材料中的 孔隙率。 闭模真空浸渗工艺适用于大型叶片的生产 ( 叶 片长度在 40 米以上时 ) 和大批量的生产 , 闭模真空 浸渗工艺被认为效率高、 成本低、 质量好, 因此为很 多生产单位所采用。 2. 3 拉挤工艺 在垂直轴风力发电机组中 , 叶片为鱼骨型不变
The Outlook and Manufacturing Process of Composite Turbine Rotor Blades
HE Dong- xiao 1 , HUANG Li- gang 1 , YANG Song1 , AN Qing- Sheng 2
( 1.Harbin FRP Institute, Harbin 150036) ( 2. Shanghai Composite Material Company, Shanghai 201206) ABSTRACT This paper states the outlook and manufacturing process of our Chinese composite wind turbine rotor blades, and introduces emphatically several manufacturing processes and the key technology. KEYWORDS Composites; Blades; Manufacturing process; Structural design
截面 , 且不需考虑转子动平衡问题 , 可采用拉挤工艺 方法生产。 用拉挤成型工艺方法生产复合材料叶片可实现 工业化连续生产 , 产品无需后期修整, 质量一致 , 无 需检测动平衡 , 成品率 95% , 用拉挤成型工 艺方法 生产复合材料叶片与其他成型工艺方法生产的复合 材料叶 片 相比 , 成 本 可 降低 40% , 销 售价 格 降 低 50% 。