精益生产报告精品PPT课件
合集下载
精益生产报告PPT课件

作业顺序安排的示例参见教材第5页。
.Electronic Technology CO.,LTD
-9-
③.标准手持
标准手持的计算 入料口、成品货店上的库存不算标准手持。 标准手持包括生产线内设备上正在加工的零件数量和工序间滑道规定保 持的零件个数
标准手持的计算基本原则——顺流0,逆流1;手动0,自动1
.Electronic Technology CO.,LTD
-4-
工序能力: 各工序在加工零件是的生产能力。即各工序(设备)进行生产时,考虑到手动作业时间、设备的加 工时间、更换设备的时间,单班所能加工的最大数量。
1班的运转时间(定时) 加工能力=
完成时间/件+交换设备时间/件
标准作业组合票(分析几个工序之间共性存在或重复的浪费) 明确各工序的手工作业时间及步行时间,用于考察T.T内一个作业者能够承担的工序的范围是多大。
1.在工序内造就品质 2.省人化
实施的工具、方针
物-----同期化 人-----多能工化 设备--按工序顺序配置
标准作业
看板方式 出现异常停机 显示异常 将人和机械的工作分开
-2-
简言之:通过有效率的劳动提高生产效率
标准作业的根本目的 目的一:使用必要的、最小数量的作业人员进行生产——省人化; 目的二:实现与适时生产有关的各工序的同步化——JIT之同期化; 目的三:把在制品的“标准手持量”限制在必要的最小数量——标准手持;
2 把作业项目填写在时间观测纸上,边看作业边记住观测点(观测点是读表瞬间)
3 观测时间
★中途不能停表,将各项作业结束时的秒表指针数字如实填写在时间观测纸上。
★观测次数必须在10次左右。
★例外的作业内容、时间在其发生时逐一记录。
《精益生产培训》ppt课件精品模板分享(带动画)
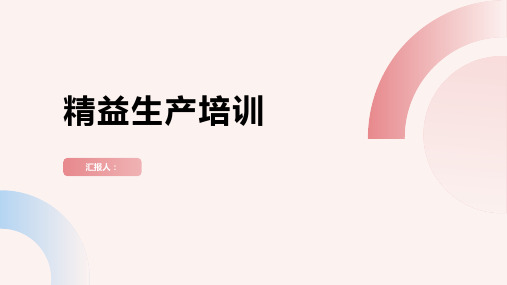
结论:美的集团 的精益生产成功 案例表明,通过 科学管理和创新 技术手段,企业 可以提高生产效 率和产品质量, 降低成本和缩短 交货期,增强市 场竞争力。
如何推广精益生产文化
第六章
提高员工意识
培训:定期组织精益生产培训,让员工了解精益生产理念、方法和工具。
宣传:通过内部宣传、精益文化墙等方式,宣传精益生产的重要性和优势, 增强员工的认同感和归属感。
建立示范点
选择具有代表性的生产现场作为示范点 制定具体的实施方案和计划 安排专业的技术人员进行指导和监督 总结经验教训,不断完善和优化实施方案
激励和奖励机制
建立精益生产知识竞赛,鼓励员工 参与
设立精益生产优秀员工奖,激励员 工积极参与
添加标题
添加标题
添加标题
添加标题
针对实施精益生产的部门或团队进 行奖励
增强客户满意 度
提高产品性能 和质量
提升企业品牌 形象和竞争力
增强企业竞争力
提高生产效率
降低成本
优化资源配置
提升产品质量
创新产品研发
增强市场竞争力
精益生产的核心工具
第三章
价值流分析
定义:识别和追踪产品或服务在生产过程中的所有活动 目的:找出浪费和不增值的环节 方法:绘制价值流图,包括生产流程、时间、人力、物力等 作用:为精益生产提供分析和改进的依据
添加标题
添加标题
它通过消除浪费、提高效率、减少 成本来最大化价值
浪费是指任何消耗了资源而不增加 价值的活动
精益生产的起源
目的:消除浪费,提高效率
起源:20世纪50年代,日本 丰田汽车公司
方法:采用生产流程分析和 改进工具,如价值流图、流
程图等
结果:提高了生产效率和质 量,降低了成本,增强了竞
精益生产(完美版)ppt课件
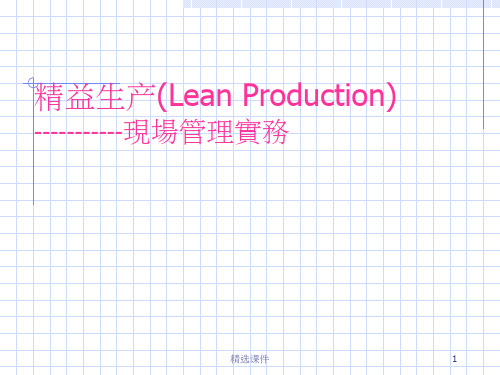
零目标 目的
现状
思考原则与方法
零
质量 低级错误频发,
· 三不主义
77个个““零””目目标标 不良
保证
不良率高企, 批量事故多发, 忙于“救火”
· 零缺陷运动 · 工作质量 · 全员质量改善活动 · 自主研究活动 · 质量改善工具运用
零 故障
生产 效率
故障频繁发生,
加班加点与待工待料一 样多
· 效率管理 · TPM全面设备维护 · 故障分析与故障源对策 · 初期清扫与自主维护
零 停滞
缩短 交货期长、延迟交货多 · 同步化、均衡化
交货期 顾客投诉多,
· 生产布局改善
加班加点、赶工赶精料选课件 · 设备小型化、专用化 17
7个“零”目标
零目标 目的
现状
思考原则与方法
7个“零”目标 零 事故
安全 保证
忙于赶货疲于奔命, 忽视安全事故频发, 意识淡薄,人为事故多
例:市场需求100件/天
10个人1天 生产
100件产品
10个人1天 生产
120件产品
假效率
8个人1天 生产
100件产品
真效率
精选课件
4
假效率
固定的人员
真效率
最少的人员
生产出仅需的产品
生产出更多的产品
能力提升是效率的基础。 但效率建立在有效需求的基础 上,以【是否创造利润】为标 准;如果不创造效益甚至造成 精选课件在库,则此种效率是假效率。 5
精选课件
8
(3)消除浪费——管理的重要目的之一
Management
创造性的管理活动 提高产品和服务的附加价值
+1 增加价值
0
-1
精益生产(经典课件)

2020/8/27
Value Stream 价值流
价值流包含的是特定产品从进公司到发货至客户 的所有要素 (包括增值的和非增值的)。
需求
设计
8
总装厂
精益六西格玛工具Lean6Sigma Tools
标准化作业 Standard Work
单元化制造
Cellular
5S
Manufacturing
减少换型时间 Set Up Reduction
价值流图 Value Stream
Mapping
防错 Mistake Proofing
全面设备维护 Total
传统做法
供应商 L/T
运送
原材料
在制品
成品
顾客
根据预测 生产/采购
根据需求 生产
流动制造/准时生产
2020/8/27
顾客
原材料/在制品/成品
2
Value Stream Mapping
价值流分析
供应商
信息控制
顾客
工序A
工序B
工序C
理解流程…看到价值…憧憬未来状态
2020/8/27
Value Stream 价值流
需求拉动 BTR-按需求生产
象开发的河流 一样通畅流动
Flow 流动
2020/8/27
降低成本, 改善质量, 缩短生产周期
The Competition Advantage Of A Lean Enterprise
精益企业的竞争优势
在三到五年的时间里பைடு நூலகம்
✓ 生产时间减少 90% ✓ 库存减少 90% ✓ 生产效率提高 60% ✓ 到达客户手中的缺陷减少 50% ✓ 废品率降低 50% ✓ 与工作有关的伤害降低 50%
Value Stream 价值流
价值流包含的是特定产品从进公司到发货至客户 的所有要素 (包括增值的和非增值的)。
需求
设计
8
总装厂
精益六西格玛工具Lean6Sigma Tools
标准化作业 Standard Work
单元化制造
Cellular
5S
Manufacturing
减少换型时间 Set Up Reduction
价值流图 Value Stream
Mapping
防错 Mistake Proofing
全面设备维护 Total
传统做法
供应商 L/T
运送
原材料
在制品
成品
顾客
根据预测 生产/采购
根据需求 生产
流动制造/准时生产
2020/8/27
顾客
原材料/在制品/成品
2
Value Stream Mapping
价值流分析
供应商
信息控制
顾客
工序A
工序B
工序C
理解流程…看到价值…憧憬未来状态
2020/8/27
Value Stream 价值流
需求拉动 BTR-按需求生产
象开发的河流 一样通畅流动
Flow 流动
2020/8/27
降低成本, 改善质量, 缩短生产周期
The Competition Advantage Of A Lean Enterprise
精益企业的竞争优势
在三到五年的时间里பைடு நூலகம்
✓ 生产时间减少 90% ✓ 库存减少 90% ✓ 生产效率提高 60% ✓ 到达客户手中的缺陷减少 50% ✓ 废品率降低 50% ✓ 与工作有关的伤害降低 50%
精益生产-课程内容PPT课件

生产控制的内容包括:
1、作业安排。
2、测定偏差
掌握实际完成量与计划完成量之间的偏差。
3、纠正偏差。
4、提供信息。
.
63
二、生产进度控制
生产进度控制的主要任务,是按照预先制定的作业 计划,检查各种零部件的投入和出产时间、数量以及 配套性,保证产品能准时装配出厂。
.
64
(一)生产预计分析
生产预计分析就是要做到事先控制,掌握生产管理的主动 权。
2. A suggestion to help you reduce expenses by 10%
.
25
降低成本比增加销售更能带来效益
Scenario A – 销售收入增加 10%
Before After
Sales $100M $110M
Costs $90M $99M
Profits $10M
$11M
10 days 15 days
剩余工作 10 days 10 days 10 days
比率 .5
1.0 1.5
If CR (<) 1: If CR (=) 1:
If CR (>)1:
订单延迟 订单准时交付
订单提前
.
5-39
58
生产汇报
按工厂和工作中心
订单状态 例外报告 库存状态 工时报告 机器效率
派工规则
先来先做 (FCFS) 最先到期的优选 (EDD) 工序到期优选 (ODD) 最短流程优选 (SPT) 关键比率 (CR)
.
5-38
57
关键比率
关键比率= 剩 剩余 余工 时作 间
Example: 今天时第 180 天
关键订单 A B C
精益生产方式PPT课件

提升企业竞争力
精益生产方式能够帮助企业快速响应 市场需求,提高产品质量和客户满意 度,从而提升企业竞争力。
精益生产方式的起源与发展
起源
精益生产方式起源于日本丰田汽车公 司的生产方式,旨在消除浪费、提高 效率和效益。
发展
随着精益生产方式的广泛应用和推广 ,其理论和方法不断完善和发展,逐 渐形成了包括精益研发、精益采购、 精益物流等方面的完整体系。
单元化生产
单元化生产是将生产线划分为 若干个独立的单元,每个单元 负责特定的产品或工序。
通过单元化生产,企业可以更 好地组织和管理生产过程,提 高生产效率和产品质量。
单元化生产需要合理规划和管 理,以确保单元之间的协调和 配合。
减少生产浪费
精益生产强调消除浪费,包括减 少不良品、减少库存、减少等待
性,促进企业的可持续发展。
03
精益生产方式的主要工 具和技术
5S管理
5S管理是精益生产中的一项基础工具, 包括整理(Sort)、整顿 (Straighten)、清扫(Sweep)、清 洁(Sanitize)和素养(Sustain)五个 方面。
实施5S管理有助于企业实现标准化、 规范化的管理,提高整体形象和品质。
和全面性。
04
精益生产方式的应用案 例
某汽车制造企业的精益生产实践
总结词:全面优化
详细描述:该汽车制造企业通过精益生产方式,实现了从产品设计、生产计划、 生产流程到供应链管理的全面优化。通过消除浪费、提高生产效率和产品质量, 该企业成功降低了成本并提高了市场竞争力。
某电子制造企业的精益生产实践
精益生产方式ppt课件
目录
• 精益生产方式概述 • 精益生产方式的核心理念 • 精益生产方式的主要工具和技术 • 精益生产方式的应用案例 • 精益生产方式的未来发展 • 结论
部门每月精益生产活动总结报告课件

改善者 廖淑娟
班组 主管
部门
安装车 间
日期
2011.05. 08
• 另一面:移印
• 【问题点说明】 :出口H60后芯型号分两面喷印,而
由于CE字母喷码达不到品质标准,导致物料在喷码只喷型号 F211后,再转移印在另一面印(Made in P.R.C),造成物料重 复喷印时间浪费,物料周转时间长,人员搬运时间浪费
• PPT文档 演模板
部门每月精益生产活动总结报告
•改善名称: A3通用外框包装方式 的改善
改善前
••••• 改善者风采
改善后
改善者
班组
部门
日期
• 【问题点说明】 :A3通用外框,供应商发过来
时,一个胶袋里只装一个外框,拉线在生产过程 中拆包装时时间增加,影响生产效率。
• 【改善对策】 :在不影响产品质量的前提下,
A3外框每个胶袋装两个外框,减少一半的外框拆
包装时间,提高生产率。
• 【改善效果】: 1、减少拆包装时间,提高生产效率。
•
2 、同时供应商也减少拆包装车间,赢得供应商信任。
•
PPT文档演模板
部门每月精益生产活动总结报告
•改善名称:产品打印标签纸尺寸 的改善
改善前
• • • • •
改 善 者 风 采
部门 岗位 姓名
安装车间
部门 岗位 姓名
安装车间
部门 岗位 姓名
PPT文档演模板
安装车间
部门 岗位 姓名
安装车间
部门 岗位 姓名
安装车间
部门 岗位 姓名
安装车间
部门每月精益生产活动总结报告
六、后续工作重点
•1、问题暴露和提案改善提案 •2、上阶段改善工作维护与水平展开 •3、员工作业效率竟赛(含打螺丝、印 日期、弯线、贴标小胶袋标签) •4、下月辅导后作业改善完成跟进
精益生产知识培训演示课件(29张)

利润是如何产生的?
获得利润的两大手法: 手法一:降低成本(节流) 手法二:提高效率(开源) 通过改善消除浪费,提高附加价值 实现
成本中心型 售价=成本+利润
以计算或实际成本为中心,加上预先设定的利润,得出为产品的售价。
售价中心型
利润=售价-成本
以售价为中心,当市场售价变动时,利润随着变动。
利润中心型
板
保
证
保 全
· 安 全
产
目视管理
推进顺序2
步骤1:意识改革
步骤2:5S
步骤2:流动生产
舍弃陈旧的想法,采用JIT思想。
JIT
JIT改善的基础是整理、整顿、 清扫、清洁、教养等5S
步骤5:标准作业
停止大批制造,让每一项工程 都遵循顺序来制造。
步骤4:平准化
JIT
好不容易所完成的物品流程, 不可弄乱,要牢记在心。
精益生产知识培训
目
录
一、什么是精益生产 二、为什么要进行精益生产 三、精益生产的七大浪费 四、如何做精益生产
一、什么是精益生产
企业的基本经营概念
●为股东创造利润—维系企业生存 ●向社会提供好的产品——占领市场空间 ●企业和员工共同的发展
企业经营的真正目的在于制造利润,因此在企业的 整个经营过程中如何获得最大的利润是企业的头等 大事!
• 基本思想就是消灭包括库存再内的一切无效的劳 动与浪费,达到降低成本,提高产品质量来增强 企业的竞争优势的目的。精,即是不投入任何多 余的生产要素,只在适当的时间生产必要的产品; 益,即所有经营活动均应有益有效。
二、为什么要进行精益生产
成本的构成 成本一般有以下要素组成: 材料、人工、制造费用、消耗品、管理费用、设备、工资… …等
精益生产报告ppt课件
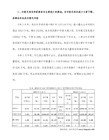
试损失原料
2:彩色,白色,透 明原料使AS原料开 机
3:白色大机台开机 打油使用白色次料 ,抽粒料
责任人(日期) 常鑫(1/15)
11
小工单的原因分析及改善对策
问题
原因
对策
责任人(日期)
机台及辅助设备 调度紧张(20.6%)
人力不足 (11%)
客户需求点集中
辅助设备不足或 损坏(如机械手模 温机)
孙福兰(1/15) 余倩(1/15)
12
小工单合并生产改善状况(2/15-3/15)
业务需求工单 81笔
合并工单 26笔
节省换模 损耗原料
159kg
节省原料 金额
2716RMB
节省换模损 耗工时金额 10260RMB
A:50T-160T小机台,每次换模损耗原料3kg 人工:2人/2H/30元/H B:180T-320T中型机台,每次换模损耗原料5kg 人工:2人/2H/30元/H C:420T-650T大型机台,每次换模损耗原料10kg 人工:2人/2H/30元/H
3
Leader NIU YF
王大芬 可行性评估
4
课题项目 1:库存周转天数
重要 紧泊 可行 效益 综合
性性
性
性 得分
24 18 13
15 70
是否 選用
不选
2:成型小工单与开机料
损耗管控
25Байду номын сангаас26 24
23 98
選取
3:成型前三大使用原料
的替代原料导入
24 25 22
20 91
不选
表中:每个方面的考虑区间设为1-5分,由所有圈员参与打分,最後综合后得分排序
2:彩色,白色,透 明原料使AS原料开 机
3:白色大机台开机 打油使用白色次料 ,抽粒料
责任人(日期) 常鑫(1/15)
11
小工单的原因分析及改善对策
问题
原因
对策
责任人(日期)
机台及辅助设备 调度紧张(20.6%)
人力不足 (11%)
客户需求点集中
辅助设备不足或 损坏(如机械手模 温机)
孙福兰(1/15) 余倩(1/15)
12
小工单合并生产改善状况(2/15-3/15)
业务需求工单 81笔
合并工单 26笔
节省换模 损耗原料
159kg
节省原料 金额
2716RMB
节省换模损 耗工时金额 10260RMB
A:50T-160T小机台,每次换模损耗原料3kg 人工:2人/2H/30元/H B:180T-320T中型机台,每次换模损耗原料5kg 人工:2人/2H/30元/H C:420T-650T大型机台,每次换模损耗原料10kg 人工:2人/2H/30元/H
3
Leader NIU YF
王大芬 可行性评估
4
课题项目 1:库存周转天数
重要 紧泊 可行 效益 综合
性性
性
性 得分
24 18 13
15 70
是否 選用
不选
2:成型小工单与开机料
损耗管控
25Байду номын сангаас26 24
23 98
選取
3:成型前三大使用原料
的替代原料导入
24 25 22
20 91
不选
表中:每个方面的考虑区间设为1-5分,由所有圈员参与打分,最後综合后得分排序
《精益生产方式》课件

《精益生产方式》PPT课 件
这是一份关于精益生产方式的PPT课件,通过学习这种生产方式,您将掌握 精益化生产流程、工具和案例,以及未来的发展趋势。
什么是精益生产?
精益生产是一种优化生产流程和提高效率的方法。它的定义、原则和优势都 将在本节中介绍。
精益生产的定义
精益生产是一种以最大程度减少浪费、提高价值流动性和灵活性为目标的生产方式。
生产流程优化
通过分析和优化生产流程,最大限度地提高价值流动性和生产效率。
生产极端化
通过精确计划和协调,实现批量生产的极端化,减少缺货和过度生产。
价值流
通过价值流图,可视化并分析产品价值的流动,以便识别和减少浪费。
5S管理
使用整理、整顿、清扫、清洁和素养的方法,提高工作场所的效率和观导向
关注客户需求,优化生产过程。
3 持续改进
通过PDCA循环实现不断改善。
2 流程优化
消除浪费,提高生产效率。
精益生产的优势
1 降低成本
通过减少浪费和提高效 率降低生产成本。
2 提高质量
减少错误和缺陷,提供 更高质量的产品。
3 增加灵活性
快速响应市场需求,适 应变化。
精益生产流程
通过持续改进来逐步改进和优化生产过程。
精益生产的工具
PDCA循环
通过计划、执行、检查和执行的循环,实现持续改进。
价值流图
通过绘制产品价值流动的图表,可视化并识别在生产过程中存在的浪费。
A3 报告
使用A3报告来概括问题、分析原因并提出解决方案。
按需生产
根据订单和客户需求,实现精确的按需生产,减少库存和浪费。
精益生产的未来
未来趋势
预测精益生产将继续发展,成为未来生产方式的主流。
精益生产(完美版)(PPT109页)
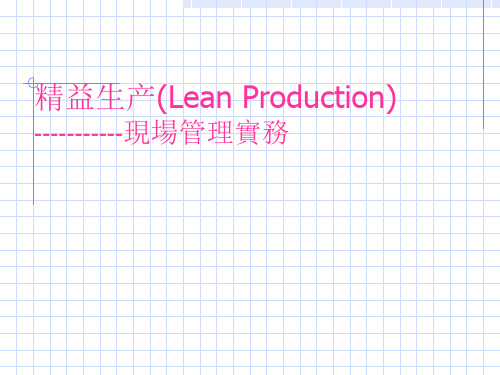
(3)消除浪费——管理的重要目的之一
Management
创造性的管理活动 提高产品和服务的附加价值
+1 增加价值
0
-1
消除浪费
最大限度地减少不增值劳动 封闭性的管理活动
精益思维(Lean Thinking)的5个基本原则
No.1 从顾客的角度而不是从某个公司、部门或机构 的角度确定价值;
No.2 确定设计、采购和生产产品的整个价值流中的 步骤,找出不增加价例 能力需求:100件/H
项目 能力 达成率 奖金 效率
工序1 100件/H
100% 标准产量奖金 个别效率合格
工序2 125件/H
125% 125%奖金 个别效率高
工序3 80件/H
80% 0
个别效率低
工序4 100件/H
80% 0
个别效率低
≠ 个别效率
整体效率
专业化作业有利于提高个别效率,不少企 业因此实行计件工资。
精益生产(Lean Production)
-----------現場管理實務
第一部分 精益生产簡介
很多精益技术源于日本企业的生产管理方法, 如看 板管理、全面质量管理(TQM)、快速换模等技术 都是 在丰田等日本公司的生产管理(NPS)中产生的。美国 的丹尼尔·琼斯教授等人通过大量细致的研究,并与 当 时欧美大量生产方式相比较后得出结论,正是这 些生 产管理方式使得日本企业(如丰田汽车公司)迅速成为 世界级的公司。这些管理思想和原则就是精益生产。
· 三不主义
77个个““零””目目标标 不良
保证
不良率高企, 批量事故多发, 忙于“救火”
· 零缺陷运动 · 工作质量 · 全员质量改善活动 · 自主研究活动 · 质量改善工具运用
精益生产课件-109页PPT资料
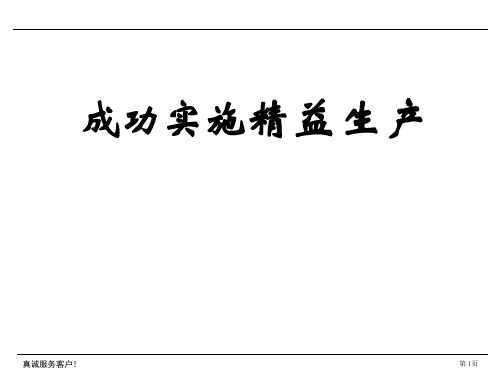
真诚服务客户!
第 20页
从“精益生产”到“精益思想”
从(1993年-2019年)
美国军方1993年出台美国“国防制造企业战略”、 “精益航空计划Lean Aerospace Initiative”等政府指 令性的活动。除了汽车行业又有更多的美国企业如波
音、洛克希德马丁、普惠等投入到实施精益生产的大
明显提升。 • 等等诸多收益~~
真诚服务客户!
第 9页
• 全球经济一体化把企业逼入“角斗场”进行 生与死的决斗。
• 企业与企业的企业竞争取决于企业采用的生 产方式和企业文化。(角斗士的武器)
• 生产方式决定生产关系;决定上层建筑;决 定军队和国家的实力。
• 结论:国家与国家的竞争归根到底是企业与 企业的竞争。
• 精:即少而精,不投入多余的生产要素,只是在适 当的时间生产必要数量的市场急需产品(或下道工 序急需的产品);
• 益:即所有经营活动要有益有效,具有经济性。
• 精益生产是当前工业界最佳的一种生产组织体系和 方式。
真诚服务客户!
第 16页
精益生产出现的历史背景及历程发展进程。
• 历史背景(1950) • 管理技术背景(1955··1960) • 石油危机带来的机遇(1973-1980)
成功实施精益生产
真诚服务客户!
第 1页
工业社会第二次生产方式革命 • 做正确的事=研究精益生产是什么? • 做什么?
• 把事情做正确=如何成功实施精益生产? • 如何做?
真诚服务客户!
第 2页
课程目录:
• 前言:为什么要搞精益生产? • 1、认识精益生产 • 2、精益生产的基本架构和内容 • 3、改变从认识浪费开始 • 4、如何实现精益生产 • 5、精益生产的基础-5S管理 • 6、全员设备保全-TPM • 7、标准化作业 • 8、精益生产中的拉动式生产体系 • 9、精益生产相关配套管理体系和模块 • 10、精益生产在中国成功实施的运作模式 • 精益案例分享
精益生产PPT(56P)
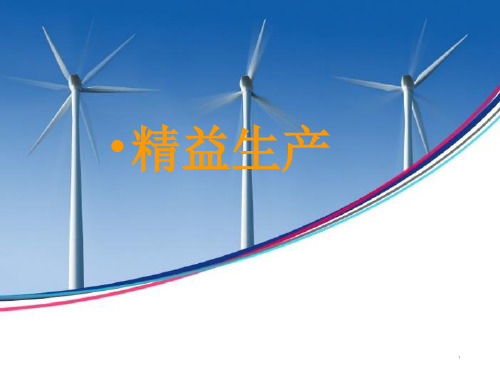
*
5年内生产周期时间的改进
按时交货
交付周期时间 (天)
库存周转
广泛应用精益生产技术
稍有应用/不应用
55%的改进
44%的提高
40%的提高
40%的提高
精益企业的领先优势
*
风电行业生产现状
1.生产成本不断上升,这里主要包括:能源成本 、人力成本 、物流成本 、原料成本等。 2,出口形势严峻 ,内销以价格竞争者居多,主要表现在出口产品不断遭受外国反倾销调查、人民币不断升值、出口仍是以低价格产品为主。 3,生产管理以粗放生产为主,国内的很多企业以前可以说是没有管理,现在也只是粗放式管理,原来原料、燃料、人工低的时候也挣钱,现在原料、燃料、人工涨了还挣钱。浑然不知道利润从哪里来的,其实这都是靠精细化管理中来的 。
标准作业单
3、标准作业
标准
标准序列
*
3、标准作业
简言之:通过有效率的劳动提高生产效率
目的一:使用必要的、最小数量的作业人员进行生产——省人化; 目的二:实现与适时生产有关的各工序的同步化——JIT之同期化; 目的三:把在制品的“标准手持量”限制在必要的最小数量——标准手持;
标准作业的根本目的
目的一:明确安全的、低成本的生产优良产品所必须的制造方法。 目的二:将标准作业作为改善的工具使用。
*
四、从价格谈与我们的关系
旧模式: 成本+ 效益 = 价格 [固定] [固定] [获得] 新模式: 价格 –效益 =成本 [固定] [固定] [获得]
旧模式: .公司目标利润是通过价格设定而得.
新模式:价格由市场而定,利润由股东而定,這意味必须达至最高成本,而节省成本便成为公司的重要策略.
2S
3S
5S
5年内生产周期时间的改进
按时交货
交付周期时间 (天)
库存周转
广泛应用精益生产技术
稍有应用/不应用
55%的改进
44%的提高
40%的提高
40%的提高
精益企业的领先优势
*
风电行业生产现状
1.生产成本不断上升,这里主要包括:能源成本 、人力成本 、物流成本 、原料成本等。 2,出口形势严峻 ,内销以价格竞争者居多,主要表现在出口产品不断遭受外国反倾销调查、人民币不断升值、出口仍是以低价格产品为主。 3,生产管理以粗放生产为主,国内的很多企业以前可以说是没有管理,现在也只是粗放式管理,原来原料、燃料、人工低的时候也挣钱,现在原料、燃料、人工涨了还挣钱。浑然不知道利润从哪里来的,其实这都是靠精细化管理中来的 。
标准作业单
3、标准作业
标准
标准序列
*
3、标准作业
简言之:通过有效率的劳动提高生产效率
目的一:使用必要的、最小数量的作业人员进行生产——省人化; 目的二:实现与适时生产有关的各工序的同步化——JIT之同期化; 目的三:把在制品的“标准手持量”限制在必要的最小数量——标准手持;
标准作业的根本目的
目的一:明确安全的、低成本的生产优良产品所必须的制造方法。 目的二:将标准作业作为改善的工具使用。
*
四、从价格谈与我们的关系
旧模式: 成本+ 效益 = 价格 [固定] [固定] [获得] 新模式: 价格 –效益 =成本 [固定] [固定] [获得]
旧模式: .公司目标利润是通过价格设定而得.
新模式:价格由市场而定,利润由股东而定,這意味必须达至最高成本,而节省成本便成为公司的重要策略.
2S
3S
5S
第4章 精益生产ppt课件

零库存、零停滞、零切换、零工伤、 零工序间在制品
ppt精选版
7
精益生产的好处
精益生产主要研究时间和效率 , 注重提 升系统的稳定性 ,50 多年来精益生产的 成功案例已证实:
●精益生产让生产时间减少 90% ●精益生产让库存减少 90% ●精益生产使生产效率提高 60% ●精益生产使市场缺陷减少 50% ●精益生产让废品率降低 50% ●精益生产让安全指数提升 50%
与上述概念关系密切的是生产线平衡(line balancing),这种方法两 天就可学会加以运用。一方面,它可以用于确定工人人数及每个工人 需要完成的任务量以满足变化的需求。这必须平衡各工作站的任务分 配,做到某个给定的产出水平上工作站数量最少,各工作站总闲置时 间最少。在平衡这些任务的时候,对于各项任务单位产品所需时间及 其于其他任务之间的顺序关系都要加以考虑。另一方面,该技术可以 用于确定装配线上运作的产品组合,这种组合能让装配线上的工作流 按照计划的生产线速率(即takt 时间)基本连续地运作。
ppt精选版
14
标准作业三要素
1、节拍时间
节拍时间=制造一个产品所需要的时间 日产量=每月产量/每月工作日数 节拍时间=每日工作时间/每日产量
2、作业顺序 3、标准手持
ppt精选版
15
第四招:确保设备运转的TPM
●实施TPM——日常保养、定期保养、 突发保养、预防保养
●日常保养:清扫、润滑、点检 ●迈向零故障
ppt精选版
23
一个流
One Piece Flow 或者叫“一个流”、“一件流”,通过 这样的方式达到生产线的连续流动。要点如下: 1. 单件流动: 避免以批量为单位加工,应逐个完成相关工 序加工 2. 按工序排列设备布置流水线 3. 按节拍进行生产,按看板和用户需求适时、适量、适 物连续流动 4. 站立式走动作业 5. 培养多能工,一人多机(工序)操作 6. 设备小型化,排列U、L、三角形等 7. 作业标准化
ppt精选版
7
精益生产的好处
精益生产主要研究时间和效率 , 注重提 升系统的稳定性 ,50 多年来精益生产的 成功案例已证实:
●精益生产让生产时间减少 90% ●精益生产让库存减少 90% ●精益生产使生产效率提高 60% ●精益生产使市场缺陷减少 50% ●精益生产让废品率降低 50% ●精益生产让安全指数提升 50%
与上述概念关系密切的是生产线平衡(line balancing),这种方法两 天就可学会加以运用。一方面,它可以用于确定工人人数及每个工人 需要完成的任务量以满足变化的需求。这必须平衡各工作站的任务分 配,做到某个给定的产出水平上工作站数量最少,各工作站总闲置时 间最少。在平衡这些任务的时候,对于各项任务单位产品所需时间及 其于其他任务之间的顺序关系都要加以考虑。另一方面,该技术可以 用于确定装配线上运作的产品组合,这种组合能让装配线上的工作流 按照计划的生产线速率(即takt 时间)基本连续地运作。
ppt精选版
14
标准作业三要素
1、节拍时间
节拍时间=制造一个产品所需要的时间 日产量=每月产量/每月工作日数 节拍时间=每日工作时间/每日产量
2、作业顺序 3、标准手持
ppt精选版
15
第四招:确保设备运转的TPM
●实施TPM——日常保养、定期保养、 突发保养、预防保养
●日常保养:清扫、润滑、点检 ●迈向零故障
ppt精选版
23
一个流
One Piece Flow 或者叫“一个流”、“一件流”,通过 这样的方式达到生产线的连续流动。要点如下: 1. 单件流动: 避免以批量为单位加工,应逐个完成相关工 序加工 2. 按工序排列设备布置流水线 3. 按节拍进行生产,按看板和用户需求适时、适量、适 物连续流动 4. 站立式走动作业 5. 培养多能工,一人多机(工序)操作 6. 设备小型化,排列U、L、三角形等 7. 作业标准化
精益生产(经典课件)

VSM Tools 绘制价值流分析图所需工具
Manufacturing Process
Scrap
Kaizen闪光点/ 爆炸点
外部资源/ 客户
数据盒
I
库存
o oo
卡车运输
成品至客户
缓冲区/ 安全库存
手工的 信息流 Electronic Information Flow
Production Kanban
➢ Helps identify the sources of waste 帮助发现浪费源 ➢ Shows the linkage between information flow and the material flow 展
示了信息流与物流之间的联系
➢ Provides a communication tool for all levels 广泛沟通的工具 ➢ Helps establish priorities based on barriers to flow 确定优先次序
Ship Order
Customer Receives Order
Manufacturing
Will product be available before order ships? No
Is production scheduled to manufacture product? No
Yes Yes
Future status 未来状态图
工作计划及 实施
➢ 设计一个精益价值流 ➢ 制订“未来状态”的实施计划
精益生产(经典课件)
Value Stream Mapping – Icons 绘价值流分析图 之 图标
物流图标
ASSEMBLY
精益生产PPT教程

一个点进行时不需要存货零件。
= Production TimeBreaks,Lunch
=生产时间-休息、午餐
Annual Production(determined by customer)年产量 (由用户决定)
Working period in the year 年度内工作周期时间
5.标准化工作进程:周期时间观察、工作要素确定、时间 测量、制作SOS。
handling routes
Part Number
Quick Set-up 快速换模
Lead Time 缩短制 Reduction 造周期
Pull Systems 拉动式生产
Customer Requirement Rate
客户需求率
准时化生产是什么? (Just In Time)
✓ Right Material ✓ Right Time ✓ Right Quantity ✓ Right Quality ✓ Right Place
精益生产的核心内容
Standardized 标准化 Operations 操作
Error 防错 Proofing
Zero Stock 零库存
Smart Card 看板管理
U Style Cell U型制造单元
连续流
SPF 一物流
5S 5S
TEM 预防性维修
Lean Organization
精益组织
2 11 1
2
Spot Welder
Work Sequence Layout
35
1
8
7
Robotic Welder
8
Punch Press
QC
Lock(s)
Safety Glasses
= Production TimeBreaks,Lunch
=生产时间-休息、午餐
Annual Production(determined by customer)年产量 (由用户决定)
Working period in the year 年度内工作周期时间
5.标准化工作进程:周期时间观察、工作要素确定、时间 测量、制作SOS。
handling routes
Part Number
Quick Set-up 快速换模
Lead Time 缩短制 Reduction 造周期
Pull Systems 拉动式生产
Customer Requirement Rate
客户需求率
准时化生产是什么? (Just In Time)
✓ Right Material ✓ Right Time ✓ Right Quantity ✓ Right Quality ✓ Right Place
精益生产的核心内容
Standardized 标准化 Operations 操作
Error 防错 Proofing
Zero Stock 零库存
Smart Card 看板管理
U Style Cell U型制造单元
连续流
SPF 一物流
5S 5S
TEM 预防性维修
Lean Organization
精益组织
2 11 1
2
Spot Welder
Work Sequence Layout
35
1
8
7
Robotic Welder
8
Punch Press
QC
Lock(s)
Safety Glasses
- 1、下载文档前请自行甄别文档内容的完整性,平台不提供额外的编辑、内容补充、找答案等附加服务。
- 2、"仅部分预览"的文档,不可在线预览部分如存在完整性等问题,可反馈申请退款(可完整预览的文档不适用该条件!)。
- 3、如文档侵犯您的权益,请联系客服反馈,我们会尽快为您处理(人工客服工作时间:9:00-18:30)。
-1-
HuaYing GKD Electronic Technology CO.,LTD
精益生产方式的 两大支柱
JUST IN TIME
准时化(Just In Time) 在必要的时候
生产及运送必要数量的 必要的产品
自动化
HuaYing GKDElectronic Technology CO.,LTD
标准作业的直接目的
目的一:明确安全的、低成本的生产优良产品所必须的制造方法。 目的二:将标准作业作为改善的工具使用。
HuaYing GKD Electronic Technology CO.,LTD
-3-
标准作业 以人的动作为中心,把工序集中起来,以没有MUDA(浪费)的操作顺序有效的进行生产的方 法。
的地方就没有改善。 b) 发现MUDA(浪费) 。
前提条件
① 应以人的动作为中心。
② 应是反复作业。
Hale Waihona Puke 遵守标准作业可以保证品质也决定数量、成本 HuaYing GKD Electronic Technology CO.,LTD
-6-
2.标准作业三要素
用最小限度的作业人员和在制品进行的 所有工序之间的同步生产
一 档 齿 坯 精车
10
9
插齿
8
一
标准手持
档
成
~~~~~
剃齿
品
7
6
1
2
二 精车 档 齿 坯 HuaYing GKD Electronic Technology CO.,LTD
3
插齿
~~~~~
4
5
剃齿
二
档
成
-10-
品
①.工序能力表
作用:是用来核算生产线瓶颈工序在哪里,另外可以看出拖后退的是设备还是手动作业。
HuaYing GKD Electronic Technology CO.,LTD
-4-
工序能力: 各工序在加工零件是的生产能力。即各工序(设备)进行生产时,考虑到手动作业时间、设备的加 工时间、更换设备的时间,单班所能加工的最大数量。
1班的运转时间(定时) 加工能力=
完成时间/件+交换设备时间/件
标准作业组合票(分析几个工序之间共性存在或重复的浪费) 明确各工序的手工作业时间及步行时间,用于考察T.T内一个作业者能够承担的工序的范围是多大。
标准作业票(体现一个的标准作业步骤) 用图表示每个作业者的作业范围,应填入标准作业的三要素及检查品质和注意安全等记号。(原则 是一个作业
三积表
形象地H表uaYin现g GK了D El一ectro条nic T生echn产olog线y CO各.,LTD作业人员的作业时间、作业内容等信息的一种柱状分析图-表5- 。
标准工时(T.T) 生产一件产品应该使用的时间值。
1班的运转时间(定时) T.T= 1班的必需生产量
循环时间(C.T) 作业者一个人进行标准作业时,毫不困难的、最快的、一个循环的实际作业时间(包括步行 时间),但不包括空手等待时间。
标准中间在库(标准手持) 按照标准作业规定的作业顺序进行操作时,为了能够反以相同的循序、动作操作生产而在工 序内持有的最少限度的待加工品。(入料口和成品货店的在库不属于标准手持)
说明: a) 工序能力是核算生产线各道工序加工过程中,考虑到手动作业时间、设备的加工时间、更
换刀具的时间,单班所能加工的最大数量。 b) 加工能力是与人的因素、设备的能力、刀具的换刀频次等因素相关联的,教材中没有考虑
换夹具时间,原因可能是由于日本生产线混线生产的现象不多,基本上是专线生产。
1班的运转时间(定时) 加工能力=
作业顺序安排的示例参见教材第5页。
HuaYing GKD Electronic Technology CO.,LTD
-9-
③.标准手持
标准手持的计算 入料口、成品货店上的库存不算标准手持。 标准手持包括生产线内设备上正在加工的零件数量和工序间滑道规定保 持的零件个数
标准手持的计算基本原则——顺流0,逆流1;手动0,自动1
完成时间/件+交换刀具时间/件
表样及工序能力表的填写方法参见教材第5页。
条件: ☆ 月产 50000台
☆ 定时运转 8H×2班
(480分-休息时间20分)×2班
5000台÷20工作日
=3分40秒
HuaYing GKD Electronic Technology CO.,LTD
-8-
②.作业顺序
作业者能够效率最好的生产合格品的生产操作顺序 这里需要区别“工序顺序”和 “作业顺序”。 工序顺序是工艺文件上规定的加工先后顺序。 作业顺序是作业者的生产操作顺序。 实际生产中作业顺序与工序顺序往往不相同的。
HuaYing GKD Electronic Technology CO.,LTD
HJR 精益革新科 2017.02.25
汇总 /
生产 /
审核 品质
-0-
/
工程 /
批准 /
目录
1. 标准作业的产生背景 2. 标准作业的推行目的 3. 标准作业的相关名词 4. 标准作业的三要素 5. 标准作业的三件套 6. 标准作业的制定程序 7. 标准作业改善的实施方法
标准作业
(
标
准 工 时 )
T.T
作 业 顺 序
标 准 手 持 量
标准作业三要素
HuaYing GKD Electronic Technology CO.,LTD
-7-
①.标准工时(T.T) 生产一件产品应该使用的时间值。
1班的运转时间(定时) T.T=
1班的必需生产量
T.T的计算例
手机生产线的例子
1.标准作业概要
定义
以人的动作为中心,把工 序集中起来,以没有MUDA 的操作顺序有效的进行生 产的方法,由:
T.T 作业顺序 标准手持 三要素组成。
标 准 作业 目的
① 明确产品的制造方法 它市制造方法和管理的根本,在考虑 品质、数量、成本、安全的基础上, 制定工作的方法。
② 改善的工具 a) 没有标准(没有正常、异常的区分)
基本原则
1.工序的流畅化 2.以需要数决定T.T 3.后工序领取
1.在工序内造就品质 2.省人化
实施的工具、方针
物-----同期化 人-----多能工化 设备--按工序顺序配置
标准作业
看板方式 出现异常停机 显示异常 将人和机械的工作分开
-2-
简言之:通过有效率的劳动提高生产效率
标准作业的根本目的 目的一:使用必要的、最小数量的作业人员进行生产——省人化; 目的二:实现与适时生产有关的各工序的同步化——JIT之同期化; 目的三:把在制品的“标准手持量”限制在必要的最小数量——标准手持;
HuaYing GKD Electronic Technology CO.,LTD
精益生产方式的 两大支柱
JUST IN TIME
准时化(Just In Time) 在必要的时候
生产及运送必要数量的 必要的产品
自动化
HuaYing GKDElectronic Technology CO.,LTD
标准作业的直接目的
目的一:明确安全的、低成本的生产优良产品所必须的制造方法。 目的二:将标准作业作为改善的工具使用。
HuaYing GKD Electronic Technology CO.,LTD
-3-
标准作业 以人的动作为中心,把工序集中起来,以没有MUDA(浪费)的操作顺序有效的进行生产的方 法。
的地方就没有改善。 b) 发现MUDA(浪费) 。
前提条件
① 应以人的动作为中心。
② 应是反复作业。
Hale Waihona Puke 遵守标准作业可以保证品质也决定数量、成本 HuaYing GKD Electronic Technology CO.,LTD
-6-
2.标准作业三要素
用最小限度的作业人员和在制品进行的 所有工序之间的同步生产
一 档 齿 坯 精车
10
9
插齿
8
一
标准手持
档
成
~~~~~
剃齿
品
7
6
1
2
二 精车 档 齿 坯 HuaYing GKD Electronic Technology CO.,LTD
3
插齿
~~~~~
4
5
剃齿
二
档
成
-10-
品
①.工序能力表
作用:是用来核算生产线瓶颈工序在哪里,另外可以看出拖后退的是设备还是手动作业。
HuaYing GKD Electronic Technology CO.,LTD
-4-
工序能力: 各工序在加工零件是的生产能力。即各工序(设备)进行生产时,考虑到手动作业时间、设备的加 工时间、更换设备的时间,单班所能加工的最大数量。
1班的运转时间(定时) 加工能力=
完成时间/件+交换设备时间/件
标准作业组合票(分析几个工序之间共性存在或重复的浪费) 明确各工序的手工作业时间及步行时间,用于考察T.T内一个作业者能够承担的工序的范围是多大。
标准作业票(体现一个的标准作业步骤) 用图表示每个作业者的作业范围,应填入标准作业的三要素及检查品质和注意安全等记号。(原则 是一个作业
三积表
形象地H表uaYin现g GK了D El一ectro条nic T生echn产olog线y CO各.,LTD作业人员的作业时间、作业内容等信息的一种柱状分析图-表5- 。
标准工时(T.T) 生产一件产品应该使用的时间值。
1班的运转时间(定时) T.T= 1班的必需生产量
循环时间(C.T) 作业者一个人进行标准作业时,毫不困难的、最快的、一个循环的实际作业时间(包括步行 时间),但不包括空手等待时间。
标准中间在库(标准手持) 按照标准作业规定的作业顺序进行操作时,为了能够反以相同的循序、动作操作生产而在工 序内持有的最少限度的待加工品。(入料口和成品货店的在库不属于标准手持)
说明: a) 工序能力是核算生产线各道工序加工过程中,考虑到手动作业时间、设备的加工时间、更
换刀具的时间,单班所能加工的最大数量。 b) 加工能力是与人的因素、设备的能力、刀具的换刀频次等因素相关联的,教材中没有考虑
换夹具时间,原因可能是由于日本生产线混线生产的现象不多,基本上是专线生产。
1班的运转时间(定时) 加工能力=
作业顺序安排的示例参见教材第5页。
HuaYing GKD Electronic Technology CO.,LTD
-9-
③.标准手持
标准手持的计算 入料口、成品货店上的库存不算标准手持。 标准手持包括生产线内设备上正在加工的零件数量和工序间滑道规定保 持的零件个数
标准手持的计算基本原则——顺流0,逆流1;手动0,自动1
完成时间/件+交换刀具时间/件
表样及工序能力表的填写方法参见教材第5页。
条件: ☆ 月产 50000台
☆ 定时运转 8H×2班
(480分-休息时间20分)×2班
5000台÷20工作日
=3分40秒
HuaYing GKD Electronic Technology CO.,LTD
-8-
②.作业顺序
作业者能够效率最好的生产合格品的生产操作顺序 这里需要区别“工序顺序”和 “作业顺序”。 工序顺序是工艺文件上规定的加工先后顺序。 作业顺序是作业者的生产操作顺序。 实际生产中作业顺序与工序顺序往往不相同的。
HuaYing GKD Electronic Technology CO.,LTD
HJR 精益革新科 2017.02.25
汇总 /
生产 /
审核 品质
-0-
/
工程 /
批准 /
目录
1. 标准作业的产生背景 2. 标准作业的推行目的 3. 标准作业的相关名词 4. 标准作业的三要素 5. 标准作业的三件套 6. 标准作业的制定程序 7. 标准作业改善的实施方法
标准作业
(
标
准 工 时 )
T.T
作 业 顺 序
标 准 手 持 量
标准作业三要素
HuaYing GKD Electronic Technology CO.,LTD
-7-
①.标准工时(T.T) 生产一件产品应该使用的时间值。
1班的运转时间(定时) T.T=
1班的必需生产量
T.T的计算例
手机生产线的例子
1.标准作业概要
定义
以人的动作为中心,把工 序集中起来,以没有MUDA 的操作顺序有效的进行生 产的方法,由:
T.T 作业顺序 标准手持 三要素组成。
标 准 作业 目的
① 明确产品的制造方法 它市制造方法和管理的根本,在考虑 品质、数量、成本、安全的基础上, 制定工作的方法。
② 改善的工具 a) 没有标准(没有正常、异常的区分)
基本原则
1.工序的流畅化 2.以需要数决定T.T 3.后工序领取
1.在工序内造就品质 2.省人化
实施的工具、方针
物-----同期化 人-----多能工化 设备--按工序顺序配置
标准作业
看板方式 出现异常停机 显示异常 将人和机械的工作分开
-2-
简言之:通过有效率的劳动提高生产效率
标准作业的根本目的 目的一:使用必要的、最小数量的作业人员进行生产——省人化; 目的二:实现与适时生产有关的各工序的同步化——JIT之同期化; 目的三:把在制品的“标准手持量”限制在必要的最小数量——标准手持;