viking pump备件手册
丹佛斯变量容积泵系列20、20-27系列零件手册说明书

MAKING MODERN LIVING POSSIBLEQuick Reference Parts ManualVariable Displacement Pump Series 20, 20-27 seriesAX00000099 en-US | 520L0910 • Rev 0203 • August23AX00000099 en-US | 520L0910• Rev 0203 • August Contents Exploded view drawing (20 thru 23 series) (4)Service parts (20 thru 23 series) (5)Exploded view drawing (24 thru 27 series) (6)Service parts (24 thru 27 series) (7)SPV2/033 (20 series) (8)SPV2/052 (21 series) (8)SPV2/070 (22 series) (8)SPV2/089 (23 series) (8)SPV2/119 (24 series) (9)SPV2/166 (25 series) (9)SPV2/227 (26 series) (9)SPV2/334 (27 series) (9)Service parts Drive shafts4AX00000099 en-US | 520L0910 • Rev 0203 • August5AX00000099 en-US | 520L0910• Rev 0203 • August Item # Discription SPV2/033 (20) SPV2/052 (21) SPV2/070 (22) SPV2/089 (23) Overhaul seal kit 9510224 9510227 9510230 9510233 1 Shaft seal kit 050088 050088 050088 0503022 O-ring 056788 (9004104-2340) 056788 (9004104-2340) 056788 (9004104-2340) 071860 (9004104-2380)3 O-ring 008821 (9004104-1290) 008821 (9004104-1290) 008821 (9004104-1290) 008979 (9004104-1360)4 Seal kit 9510022 9510022 9510022 95100215 Front bearing kit 050575 (9510251) 050575 (9510251) 050625 (9510256) 050658 (9510259)6 Swashplate, 18° 002725 9210279 9220570 95107617 Cylinder block kit 510149 593251 596890 92309738 Piston kit, set of 3 711291 (not a kit of 3) 9510408-0010 9510408-0001 9510408-0002 8 Remanufactured 711291 R9510408-0010 R9510408-0001 R9510408-00029 Slipper retainer 9200158 003210 (9210292) 003707 (9220628) 004176 (9230234) 10 Slipper ret. guide J9200124 003160 (9210219) 9220500 9230158 11 Pilot ring 002709 010678 013862 00432512 Bearing plate 002733 585885 585893 56167013 Valve plate, cw 002881 003368 003889 004333Valve plate, ccw 002899 003376 003897 00434114 Rear bearing kit 050567 (9510250) 050591 (9510253) 050617 (9510255) 050641 (9510258) 15 End cap gasket 9200088 9210204 9220425 9231081 16 Chg pump gasket, gear 9801235 9801235 9801235 9801235 gerotor with IPOR n/a 9803241* 9803241* 9803241* gerotor without IPOR n/a 9803252* 9803252* 9803252*17 O-ring 000869 (9004100-1390) 000869 (9004100-1390) 512007 (9004100-1430) 512007 (9004100-1430) 18 O-ring 000851 (9004100-1360) 000851 (9004100-1360) 512008 (9004100-1410) 512008 (9004100-1410) 19 Thrust plate 010520 003228 (9210293) 003699 (9220626) 00418420 Trunnion bearing kit 050583 (9510252) 050609 (9510254) 050633 (9510257) 050666 (9510639) prior to 88-01-xxxxx 951026021 O-ring 000927 (9004100-2260) 000935 (9004100-2280) 000943 (9004100-2300) 000950 (9004100-2320) 22 Trunnion shim kit 9510422-0001 9510422-0002 9510422-0003 9510422-0004 23 Servo piston link 589317 589317 589325 59467187-13 thru 97-23 n/a 9210620 9221367 9230787 24 Retaining ring 9006300-0050 9006300-0050 9006300-0062 9006300-006225 Pin 013904 (9004830-0001) 013904 (9004830-0001) 013680 (9004830-0002) 013680 (9004830-0002) 26 Check valve assembly 075366 (9800648) 075366 (9800648) 075366 (9800648) 075366 (9800648) 27 O-ring 056770 (9004101-0150) 056770 (9004101-0150) 056770 (9004101-0150) 056770 (9004101-0150) 28 Servo sleeve assembly 9200582 9200582 9510207 9510207 29 Servo sleeve assembly 9200583 9200583 9510350 9510350 30 Stroke limiter kit 9200515 9200515 9221078 9221078 31 Torx screw 9007276-0011 9007276-0011 9007276-0011 9007276-0011 32 Servo retainer 9200087 9200087 9220419 9220419 33 Control gasket 9803340 9803340 9803340 980334034 O-ring 001032 (9004101-0140) 001032 (9004101-0140) 001032 (9004101-0140) 001032 (9004101-0140) 35 Front cover gasket 9200076 9210201 9221528 9230124 36 Cylinder block 049155 049163 014878 01491036 Remanufactured n/a R9210576 R9221102 R9230651 37 Cylinder block assy n/a n/a 11077853 520087/P * Indicated special charge pump gaskets (item # 16) are not included in the overhaul seal kit.Service parts6AX00000099 en-US | 520L0910 • Rev 0203 • August7AX00000099 en-US | 520L0910• Rev 0203 • August Service parts Item # Discription SPV2/119 (24) SPV2/166 (25) SPV2/227 (26) SPV2/334 (27) Overhaul seal kit 9510236 9510239 9510316 9510242 1 Shaft seal kit 050302 050302 058537 0505342 O-ring 000984 (9004100-2380) 000984 (9004100-2380) 049718 (9004100-2420) 000992 (9004100-2430)3 O-ring 008979 (9004104-1360) 008979 (9004104-1360) 680892 (9004104-1440) 012187 (9004104-1490)4 Seal kit 9510021 9510021 n/a n/a5 Front bearing kit 050658 (9510259) 9510264 9510267 050732 (9510270)6 Swshplate, 18° 9240197 9250164 9260152 9270462 7 Cylinder block kit 9240641 634923 9260369 9270658 8 Piston kit, set of 3 9510408-0004 9510408-0005 9510408-0006 9510408-0009 8 Remanufactured R9510408-0004 R9510408-0005 R9510408-0006 R9510408-0009 9 Slipper retainer 9240125 9250170 9260072 9270486 10 Slipper ret. guide 9240097 005090 046243 00558711 Pilot ring 702381 634907 634915 63489912 Bearing plate 9240560 585901 9260321 58592713 Valve plate, cw 004895 651810 9260355 62232413 Valve plate, ccw 004903 628933 9260356 65196814 Rear bearing kit 050674 (9510261) 050690 (9510263) 055434 (9510266) 050724 (9510386) 15 End cap gasket 9240549 9250587 9260144 9270710 16 Chg pump gasket, gear 9801604 9801604 9801604 9801604 gerotor with IPOR 9803241* n/a n/a n/agerotor without IPOR 9803252* n/a n/a n/a17 O-ring 000901 (9004100-1510) 000901 (9004100-1510) 000919 (9004100-1560) 000919 (9004100-1560) 18 O-ring 000893 (9004100-1500) 000893 (9004100-1500) 000992 (9004100-2430) 000992 (9004100-2430) 19 Thrust plate 011015 (9240124) 005181 (9250171) 049635 (9260073) 004184 (9230235) 20 Trunnion bearing kit 050682 (9510262) 050609 (9510254) 050633 (9510257) 050666 (9510639) 21 O-ring 000968 (9004100-2340) (9004100-2280) (9004100-2300) 000950 (9004100-2320) 22 Trunnion shim kit 9510422-0005 9510422-0006 9510422-0007 9510422-0008 23 Servo piston link 9240584 9250617 9260252 9270653 24 Retaining ring 9006300-0075 9006300-0075 9006300-0087 9006300-008725 Pin 9004830-0008 9004830-0008 013680 (9004830-0002) 013680 (9004830-0002) 26 Check valve assembly 075366 (9800648) 543553 (9802028) 543553 (9802028) 543553 (9802028) 20 gpm 527887 n/a n/a n/a27 O-ring 056770 (9004101-0150) 063230 (9004101-0270) 063230 (9004101-0270) 063230 (9004101-0270) 20 gpm valve 012575 (9004105-1170) n/a n/a n/a28 Servo sleeve assembly 9510208 9510208 n/a n/a29 Servo sleeve assembly 9510351 9510351 9510331 9510331 30 Stroke limiter kit 9240326 9240326 9260185 9260185 31 Torx screw 9007276-0011 9007276-0011 9007276-0011 9007276-0011 32 Servo retainer 9240076 9240076 9270178 9270178 33 Control gasket 9803340 9803340 9803340 980334034 O-ring 001032 (9004101-0140) 001032 (9004101-0140) 001032 (9004101-0140) 001032 (9004101-0140) 35 Front cover gasket 9240070 9250158 9260145 9270175 17 Cylinder block 049171 073585 073619 07118317 Remanufactured R9240394 R9250470 R9260231 R9270495 * Indicated special charge pump gaskets (item # 16) are not included in the overhaul seal kit.8AX00000099 en-US | 520L0910 • Rev 0203 • AugustPart Number Description010827 14 tooth spline, gear charge pump707828 20 tooth spline, gear charge pump046557 21 tooth spline, M10 threaded hole, gear charge pump708073 Straight key, 3/8-24 UNF-2B threaded hole, gear charge pump 9003261-3132 Key, 5/16 x 5/16 x 2 1/2080465 14 tooth spline, gear charge pump9210663 14 tooth spline, gerotor charge pump018812 21 tooth spline, gear charge pump9210673 21 tooth spline, gerotor charge pump9210428 Tapered, gear charge pump9003310-3724 Key5000606 (9700169) Slotted nut9210538 Straight key, gear charge pump9003261-3132 Key, 5/16 x5/16 x 2 1/2144402 14 tooth spline, gear charge pump9221447 14 tooth spline, gerotor charge pump079913 (9220515) 19 tooth spline, gear charge pump9220527 20 tooth spline, 3/8-24 UNF-2B threaded hole, gear charge pump 9221475 20 tooth spline, 3/8-24 UNF-2B threaded hole, gerotor charge pump 048504 (9220417) 21 tooth spline, gear charge pump9221441 21 tooth spline, gerotor charge pump046581 (9220884) Tapered, gear charge pump9003310-3724 Key5000606 (9700169) Slotted nut039644 (9221065) Straight key, 3/8-24 UNF-2B threaded hole, gear charge pump 9003261-3132 Key, 5/16 x5/16 x 2 1/29230476 14 tooth spline, gear charge pump9230951 14 tooth spline, gerotor charge pump014985 (9230325) 21 tooth spline, gear charge pump9230968 21 tooth spline, gerotor charge pump9230173 23 tooth spline, 3/8-24 UNF-2B threaded hole, gear charge pump 9231014 23 tooth spline, 3/8-24 UNF-2B threaded hole, gerotor charge pump 9230147 27 tooth spline, 3/8-24 UNF-2B threaded hole, gear charge pump 9230445 Tapered, 1.5” nominal shaft dia., gear charge pump9003310-3724 Key5000606 (9700169) Slotted nut9230989 Tapered, 1.375” nominal shaft dia., gerotor charge pump 9003310-3724 Key5000606 (9700169) Slotted nut9230626 Straight key, 3/8-24 UNF-2B threaded hole, gear charge pump 9003261-3132 Key, 3/8 x 3/8 x 2 1/2SPV2/033 (20 series)SPV2/052 (21 series)SPV2/089 (23 series)SPV2/070 (22 series)9AX00000099 en-US | 520L0910• Rev 0203 • August Drive shaft Part Number Description 07930113 tooth spline, M14 x 2-6H tapped hole, gear charge pump 924068513 tooth spline, gerotor charge pump 04684727 tooth spline, M14 x 2-6H tapped hole, gear charge pump 9240231Tapered, gear charge pump 9003326-0005Key 9700189Slotted nut 9240713Tapered, gerotor charge pump 9003326-0005Key 9700189Slotted nut 039982Straight key, 1/2-20 UNF-2B threaded hole, gear charge pump 9003261-3732Key, 3/8 x 3/8 x 2 1/2054940 13 tooth spline, gear charge pump047894 27 tooth spline with M14 x 2-6H tapped hole, gear charge pump9250409 Straight key, 1/2-20 UNF-2B threaded hole, gear charge pump9003261-3732 Key, 3/8 x 3/8 x 2 1/29260140 13 tooth spline, gear charge pump045930 27 tooth spline, M14 x 2-6H tapped hole, gear charge pump9260176 Straight key, 1/2-20 UNF-2B threaded hole, gear charge pump9003261-5040 Key, 1/2 x 1/2 x 3 1/2077727 15 tooth spline, gear charge pump9270741 40 tooth spline, M16 tapped hole, gear charge pump561530 Straight key, 1/2-20 UNF-2B threaded hole, gear charge pump 9003261-6244 Key, 5/8 x 5/8 x 4SPV2/166 (25 series)SPV2/119 (24 series)SPV2/334 (27 series)SPV2/227 (26 series)AX00000099 en-US | 520L0910 • Rev 0203 • August1011AX00000099 en-US | 520L0910• Rev 0203 • August NotesDanfoss Power Solutions is a global manufacturer and supplier of high-quality hydraulic and electronic components. We specialize in providing state-of-the-art technology and solutions that excel in the harsh operating conditions of the mobile off-highway market. Building on our extensive applications expertise, we work closely with our customers to ensure exceptional performance for a broad range of off-highway vehicles. We help OEMs around the world speed up system development, reduce costs and bring vehicles to market faster. Danfoss – Your Strongest Partner in Mobile Hydraulics.Go to for further product information.Wherever off-highway vehicles are at work, so is Danfoss. We offer expert worldwide support for our customers, ensuring the best possible solutions for outstanding performance. And with an extensive network of Global Service Partners, we also provide comprehensive global service for all of our components. Please contact the Danfoss Power Solution representative nearest you.Products we offer:y Bent Axis Motorsy Closed Circuit Axial Piston Pumps and Motorsy Displaysy Electrohydraulic Power Steeringy Electrohydraulicsy Hydraulic Power Steeringy Integrated Systemsy Joysticks and Control Handlesy Microcontrollers and Softwarey Open Circuit Axial Piston Pumpsy Orbital Motorsy PLUS+1® GUIDEy Proportional Valvesy Sensorsy Steeringy Transit Mixer Drives Comatrol Schwarzmüller-Inverter www.schwarzmueller- Turolla Valmova Hydro-Gear Daikin-Sauer-Danfoss Local address:Danfoss can accept no responsibility for possible errors in catalogues, brochures and other printed material. Danfoss reserves the right to alter its products without notice. This also applies to products already on order provided that such alterations can be made without subsequential changes being necessary in specifications already agreed.All trademarks in this material are property of the respective companies. Danfoss and the Danfoss logotype are trademarks of Danfoss A/S. All rights reserved.Danfoss Power Solutions 22F, Block C, Yishan Rd Shanghai 200233, China Phone: +86 21 3418 5200Danfoss Power Solutions GmbH & Co. OHG Krokamp 35D-24539 Neumünster, Germany Phone: +49 4321 871 0Danfoss Power Solutions ApS Nordborgvej 81DK-6430 Nordborg, Denmark Phone: +45 7488 2222Danfoss Power Solutions US Company 2800 East 13th Street Ames, IA 50010, USA Phone: +1 515 239 6000AX00000099 en-US | 520L0910 • Rev 0203 • August © Danfoss A/S, 2015。
技术服务手册-VikingPump

图 1 – 图 GG、HJ 和 HL4197 系列 采用法兰端口的支座型手泵图 2 – 图 AS、AK 和 AL4197 系列 采用法兰端口的支座型手泵吸液口图 3特殊机械密封:维修这些泵时应格外小心。
请务必阅读并遵照随泵提供的所有特殊说明。
系列泵设计合理,可在各种条件下长时间、无故障地工作,而且只需很少的维护。
以下要点有助于确保泵能长时间正常工作。
让泵尽可能保持干净,这样做便于开展检查、调整和维修工作,以免遗漏脏污的黄油嘴。
如果泵要存放六个月或更长时间(或这么长时间不使用泵),则必须排干泵中的液体,然后在所有内部零件上涂抹薄薄的一层非去污型 .SAE .30 .号油。
润滑各接头,在泵轴延伸部分涂上润滑脂。
Viking .建议您每隔轴拨转一周,以便使油扩散开来。
建议维修工具:为了确保正确维修 4197系列泵,必须使用以下工具。
这些工具是对标准机修工具(如:开口扳手、钳子和螺丝刀等)的补充,大多数都可以从工业用品店购得。
内六角扳手(定位螺丝和特殊机械密封).– .Viking .P/N . -810-047-999 .GG-HJ-HL .4197 ..– .Viking .P/N . -810-0 9-375 .GG-HJ-HL .4197机械密封安装套筒.0 75 .英寸密封的 . -751-001-730.1 5 .英寸密封的 . -810-004-730轴承锁紧螺母活动扳手 .– . -810-043-375可调销式活动扳手,用于轴承套端盖机械密封泵体滚珠轴承空转销溢流阀图 4– GG、HJ 或 HL 4197 型号剖视图图 5 – GG、HJ 和 HL 4197 型号部件分解图编号零件名称编号零件名称编号零件名称锁紧螺母8泵体15空转销卡环(外)9管塞16泵盖和空转销组件滚珠轴承(外)10机械密封17泵盖有头螺丝泵轴卡环11转子和泵轴组件18溢流阀垫圈轴承套12空转轴套19溢流阀卡环(内)13空转轮和轴套组件20阀的有头螺丝滚珠轴承(内)14泵盖垫圈图 6 – AS、AK 和 AL 4197型号部件分解图编号零件名称编号零件名称编号零件名称1锁紧螺母9轴承护圈17空转轴套2轴承隔圈10泵体18空转轮和轴套组件3轴承套端盖11溢流阀垫圈19泵盖垫圈4轴承套唇形密封12溢流阀20空转销5滚珠轴承(外)13管塞21泵盖和空转销组件6轴承套14阀的有头螺丝22泵盖有头螺丝7轴承隔圈15转子和泵轴组件23管塞8滚珠轴承(内)16机械密封部分 . .TSM164版本E页码 第 .5 .页, .共 1 页泵轴卡环轴承套定位螺丝泵轴外卡环锁紧螺母图 7 – 推力轴承组件 GG 、HJ 和 HL轴承护圈轴承隔圈定位螺丝锁紧螺母唇形密封端盖尼龙衬垫泵轴内滚珠轴承轴承套定位螺丝滚珠轴承图 8 – 推力轴承组件 AS 、AK 和 AL 型号组装采用 PTFE .的机械密封安装新密封:请参见图 9 到图 13。
德国威纳泵装置手册(Woerner pump unit manual)

Leaflet-No.0704.12.11 EN Replaces No.0704.09.11 ENPage 1 of 10Pump unit GMG-B Pump unit GMG-BUse:As pump unit in central lubrication systemsTechnical data:Admissibledelivery pressure:at max.250barNumber of pump elements:at max.2Delivery volume per stroke and elementwith pump element 04:0,04cm³with pump element 08:0,08cm³with pump element 16:0,16cm³Temperature range:-20...+60°C At low temperatures,grease pene-tration needs to be observed.Mounting position:verticallyMaterialCasing:Aluminium Pump element:Steel Reservoir:St /Polyamide transparent Gaskets:NBR (Perbunane)Medium:Oil and grease up to NLGI class 2(Mind conditions of use of both the reservoir and filling level monitoring device!)Drive (without control unit):Mains voltage:24VDC Current at max.:2,5A Speed(load-dependent):approx.30min System of protection:IP55for control unit Current:-1+++++for the delivery of oil,liquid grease orgrease1or 2pump outletsup to 20outlets with progressivedistributor flanged-onelectric control and monitoring with function stirring without deli-very higher IP on requestDepending on type of construction,the DC gear motor should only be used in pulse mode.For other modes of operation,three-phase current motors are of advantage (e.g.Pump unit GMA-C)Power pack (.):min.3,0A Voltage:24V ±10%DCEUGEN WOERNERGmbH & Co. KGPostfach 1661DE-97866 Wertheim Hafenstrasse 2DE-97877 Wertheim Tel.+49 (0) 9342 803-0Fax.+49 (0) 9342 803-202www.woerner.deinfo@woerner.de - S u b j e c t t o m o d i f i c a t i o n s -Leaflet-No.0704 ENPage 2 of 10Description:Drive:54Delivery function:32.11Function stirring without delivery:33The pump unit GMG-B is driven by a gear motor flanged to the pump casing from downside.When the eccentric shaft rotates,the dlivery piston of every pump element makes a suction and delivery stroke per rotation each,whilst delivering lubricant from the reservoir to the lubrication points...GMG-B ....Pump elements:suction stroke 2.2 2.1312.32.4delivery stroke 32.12.32.42.5 2.6R At ,the pressure spring moves the delivery piston against the eccentric shaft .Concurrently,the lubricant available in the reservoir is drawn through the suction hole into the metering chamber .At ,the eccentric shaft shifts the delivery piston .At the same time,the suction hole is closed up and the lubricant volume available in the metering chamber delivered through the check valve to the outlet .Marking the pumpe elements:Size:Delivery volume:Marking :040,04cm³white ring 080,08cm³without ring 160,16cm³black ringDepending on the case of operation (lubricant,lubricant requirement,etc.),the pump unit can be fitted with different pump elements,reservoirs,and monitoring elements In some modes of operation,improvement of lubricant quality and delivery behaviour requires the lubricant to be stirred additionally Such stirring is facilitated in the pump by means of a specifi-cally designed eccentric drive When the eccentric shaft rotates into the one direction of rotation,the pump ele-ments are operating while the stirring device supplies them with the lubricant As soon as the eccentric shaft starts to rotate into the other direction,the lubricant is stirred without any delivery operation by the pump elements taking place The integrated control unit allows operating and off-duty periods for both the delivery with and without stirring to be programmed independently from each other unit EUGEN WOERNER GmbH & Co. KGPostfach 1661DE-97866 Wertheim Tel.+49 (0) 9342 803-0Fax.+49 (0) 9342 803-202www.woerner.deHafenstrasse 2DE-97877 Wertheim info@woerner.de - Subject to modifications -Leaflet-No.0704 ENPage 3 of 10Technical data:Temperature range:0...+60°CSwitching voltage at max.:30VDC Switching current at max.:0,25A Switching power at max.:3,0W Contact function:Opener For inductive and capacitive loads protec-tive circuits (diode,RC-member,varistor)have to be provided for.Level control "F":min.level monitoring for oilThe level control "F"consists of a float that is lifted in the oil.If oil falls below minimum filling level,the contact opened.Note:The PUR float is suited for mineral oils only.In case of other media,their compatibility needs to be checked.Notes on operation:The pump unit must be operated with clean oil or grease from original packages only.During start-up,the pump has initially to be filled with gear oil up to stirring blade level.Thus,proper venting is ensured.The lines to the lubrication points must be clean andhave free throughput.They shall not be connected to the lub-rication points unless the lubricant comes out free of bubbles.All connectors of the delivery line have to be checked for leakage.To protect the pump unit and the lines connected from overload,protec-tive elements such as pressure control valves have to be integrated basically.Level control:Level control "C":min.level monitoring for liquid grease NLGI-class 000up to grease NLGI-class 2.Version without control:In case of empty reservoir and rotating pump drive shaft,the contact is switched.(approx.5seconds).When "stirring without delivery",signal evaluation has to be suppressed.The "Empty"signal is intermittent The switching mechanism may shift as for instance during reservoir filling.In case of external control,signal evaluation must therefore be delayed when the pump is switched onFilling connector "W"Closing nippleFilling connector:This part is located beneath the left-side pump element.Filling connector "A"1)Cone lubricator nipple DIN 71412 -AG1/4WFilling connector "C"1)Flat lubricator nipple DIN 3404 - M22Filling connector "G"Closing nippleG 1)not for oil suitablyAccessory for filling connector "G" and "W":Quick release coupling 954.002-09(p = 35 bar)max G 1/4Leaflet-No.0704 ENPage 4 of 10other reservoir versions available on requestCapacity[l]2Polyamide translucent PolypropylenePolypropylene4Reservoir "2"Reservoir 4P""MaterialLid Reservoir Polyamide translucent Reservoir "7"7Stainless steelStainless steelEUGEN WOERNER GmbH & Co. KGPostfach 1661DE-97866 Wertheim Tel.+49 (0) 9342 803-0Fax.+49 (0) 9342 803-202www.woerner.deHafenstrasse 2DE-97877 Wertheim info@woerner.de - Subject to modifications -Leaflet-No.0704 ENPage 5 of 10At the right-side pump element,progressive distributors of theVPB type can be flanged on directly.As much as 20lubrication points with different distribution volumes are possible.A selection of progressive distri-butors can be chosen by means of the GMG-B purchase-designation.By monitoring the movement of one distri-butor piston,the lubricant allocation to all outlets is monitored.Evaluation through the pump control unit requires selection of a progressive distributor fitted with the func-tion control In case of oil,metering accuracy depends on viscosity,flow resistance at the outlets,and delivery speed.Functionality:Function control:Technical data progressive distributor:The lubricant supplied by the pump element is delivered to the outlet progressively (i.e.progressing in the distributor).RK.Metering volume per cycleand outlet:0,20cm³Lubrication point connectors:4,6or 8other versions available on request (up to 20lubrication points)Operating pressure at max.:150barDelivery mediumOil-viscosity:as of approx.140cP(equals ISO VG46at 20°C)Grease up to:NLGI class 2MaterialOuter body:AluminiumInner parts:Steel Additional information on VPB-G:Leaflet-no.:0177on VPB-B:Leaflet-no.:0378Switching voltage:10...36VUCSwitching current at max.:25mA Switching power at max.:0,9VA Ambient temperature:0...60°C Material (casing):PA or 1.4305Function control RK:Distributor variants :(VPB-G)4outletswithout function checking device "P4"with function checking device RK "P5"6outletswithout function checking device "P0"with function checking device RK "P1"8outletswithout function checking device "P2"with function checking device RK "P3"Note on operation:Note:N The 0,16cm³delivery volume pump element is marked by means of a grey plastic pimple .Upon start-up,both pump element and progressive distributor need to be vented.The lubricant must come out free of bubbles from all outlets.At first,the connecting case should be vented at venting screw or at the built-in pressure control valve.Then,the progres-sive distributor should be vented.6Auxiliaries:Pressure control valve at the pro-gressive distributor:Opening pressure:Purchase-no.:70bar 110.566-65150bar110.564-65Customised setting:50...150bar110.568-65For delimitation of the maximum operating pressure,pressure control valves instead of the venting screw can be screwed in.76Flanged progressive distributor:6N7EUGEN WOERNERGmbH & Co. KGPostfach 1661DE-97866 Wertheim Tel.+49 (0) 9342 803-0Fax.+49 (0) 9342 803-202www.woerner.deHafenstrasse 2DE-97877 Wertheim info@woerner.de - S u b j e c t t o m o d i f i c a t i o n s -Leaflet-No.0704 ENPage 6 of 10The control unit serves to monitor and trigger the pump aggregate.It is capable of switching the pump on and off depending on time and load.Besides,the control unit can be used to monitor the filling level and functionality of the progressive distributor In case of failure,a corresponding message can be made accessible to a higher ranking system The control unit must be started via an external E1=Motor overloadedE2=Progressive distributor faulty E3=Level faultFault messages can be deleted by keeping the SAVE key depressed for a while.Fault Description:.."release".""Control variant "C":Control without distributor monitoringControl variant "C1":Control with distributor monitoring for pro-gressive distributor flanged onControl variant "C2":Control with distributor monitoring for ex-ternally mounted progressive distributor (with functional checking device "RS").For connecting cable see "Auxiliaries"page 7Control unitControl unit operation:1.Menu call-up:By long pressing the "MODE"key,the menu structure is called up.2.:""3.Changing of values:""""""""Navigation within the menus By keeping the Mode key depressed another time,the menu items P1…P11can be selected successively.The SELECT key can be used to change setting values and functions.In case of time data,short pressing of the SELECT key results in a shifting by +1,whereas any longer pressing will result in a shifting by +20.When the SAVE key is depressed for a while,the set values will be saved.Pres-sing the MODE key enables the next menu item to be accessed without any saving action.4.::"""".5.:""""Special Functions Specific lube delivery When the SELECT key is depressed in the operating mode ON for a while,pum-ping action will be carried out for 60seconds Test Mode By pressing the keys SAVE and MODE quickly in one go and in the order mentio-ned,a pump test mode will be invoked (the keys have to be kept depressed for 0,5seconds at least).In this mode,a pumping process will be actuated for 10seconds.Thereafter,the pump continues to stir for another 5seconds.6.Change of password starting from soft-ware version 2.52:1.Press Save +Select +Mode2.Keep keys depressedand switch voltage on 3.Enter current password(factory default: 1234)4.Save by pressing Save 5.Enter new password 6.Save by pressing Save 7.The program will change intonormal mode If the newly changed password gets lost,the control unit can be reset to the original parameters in the factory.This,however,will result in loosening all changes made.For that reason,all changes made to the parameters should always be recorded and archived.""""""""""EUGEN WOERNER GmbH & Co. KGPostfach 1661DE-97866 Wertheim Tel.+49 (0) 9342 803-0Fax.+49 (0) 9342 803-202www.woerner.deHafenstrasse 2DE-97877 Wertheim info@woerner.de - Subject to modifications -Leaflet-No.0704 ENPage 7 of 10Connection diagram for the control C version""Electric connection 8:Explanation:Equipotential bonding 9:Connection type:Connector socket5-pin (M12)Version with control unit:1-+24VDC2-+24VDC (external release)3-0V4-Alarm output Version without control unit:1-+24VDC (delivery function)2-+24VDC (stirring function)3-0V4-Level monitoringDelivery function:24V to Pin 1Stirring function:24V to Pin 1and 2Threaded hole:M41)1)1)Stirring function active when PIN2is actuated.1432Auxiliaries Cable jack for electric connection:913.404-65913.405-07Connecting cable for externally moun-ted progressive distributor:913.405-23913.405-06:Operating voltage:10...30VDCPurchase-numberCable length 10m:Cable length 15m:Purchase-numberCable length 0,6m:Cable length 2m:Connection type:-pinM12-M12Cable cross section:4x0,34mmSystem of protection:IP672(other cable lengths available on request)Power pack connection (optional)470.218-60Power pack for 86...264VAC connection,24VDC /3Aoutput:Plug on socket 4Technical data:Power consumption:1,7W24VDC Supply voltage:18V...30VDC Voltage at inputs:24VDC Response time of inputs:200ms Input resistance:4kR Temperature range:-20°C...+60°C Outlet alarm:200mA/24VDC /60W Data buffer:10yearsSupply voltage/target value:For pump operation, the voltage supply must be available. In case ofTime ON operation , it is additionally necessary to change PIN2 to +24 V.Otherwise, time will not elapse. In pulse operation, the machine pulses have to be applied to Pin 2.""+24 V0 VStandard cable, 4-pin,M12x1,5BN WHBU BKINPUT +24 V voltage supply release +24 V voltage supply+0 VOutput Alarm +24 Vto be provided by customerWOERNER*Synchronisationcontact with the machineProgressive distributorPlug forassembly RS ""LevelMotorGMG12341489EUGEN WOERNERGmbH & Co. KGPostfach 1661DE-97866 Wertheim Tel.+49 (0) 9342 803-0Fax.+49 (0) 9342 803-202www.woerner.deHafenstrasse 2DE-97877 Wertheim info@woerner.de - S u b j e c t t o m o d i f i c a t i o n s -Page 8 of 10Postfach 1661DE-97866 Wertheim Tel.+49 (0) 9342 803-0Fax.+49 (0) 9342 803-202www.woerner.deHafenstrasse 2DE-97877 Wertheim info@woerner.de - Subject to modifications -Leaflet-No.0704 ENPage 9 of 10Purchase-example:Pump unit GMG-B with reservoir 2l;withlevel monitoring "C";with filling connector "G";pump element with 0,08cm³delivery stroke on the left side and 0,16cm³delivery stroke on the right side;with elec-tric control unit incl.distributor monitoring C1and A ;and progressive distributor with 6outlets and monitoring""24VDC drive type "3"Purchase-designation:GMG-B.B /2/C /0/G /08/16/C1/3A /P1Pressure control valve at the pump element:72For operating pressure delimitation,pressure control valves can be connected to the pump element Auxiliary:(state purchase-no.,please)Should the function control of a mounted progressive distributor with separate pur-chase-designation be connected to the GMG-B pump control unit,the variant "P "for the pump and the function control "R0"for the progressive distributor have to be selected.When using variant "P ",progressive distri-butors of the types VPB-B or VPB-G with up to 20lubrication points can be mounted.For the versions,please see Data sheet VPB-B:No.0378Data sheet VPB-G:No.0177**1)2)Progressive distributors P...with functioncontrol can only be selected together with control unit C1.If the function control of a progressive distributor is not to be connected to the pump control unit,then GMG-B with variant "PX"has to be selected with the progressive distributor getting a separate purchase designation.With level monitoring "F",grease cannot be stirred.Flanged progressive distributor only at pump element 08or 16possible.3)782Pressure control valve Purchase-no.:with opening pressure:250bar752.502-90Customised setting 160...250bar752.502-67770bar 752.502-65150bar 752.502-62:50...160bar 752.502-66Screwing kit Purchase-no.:Ø10752.502-648for pipe:Ø6752.502-68Ø8752.502-63EUGEN WOERNERGmbH & Co. KGPostfach 1661DE-97866 Wertheim Tel.+49 (0) 9342 803-0Fax.+49 (0) 9342 803-202www.woerner.deHafenstrasse 2DE-97877 Wertheim info@woerner.de - S u b j e c t t o m o d i f i c a t i o n s -Leaflet-No.0704 ENPage 10 of 10Technical documents also valid for this product:B Operating instructions GMG-B0743Important information on this publicationReproduction,also in extracts,only permitted with the approval of the firm of EUGEN WOERNER GmbH &Co.KG.All the information in this publication has been examined for correctness with great care.Nevertheless,WOERNER cannot assume any liability for losses or damage resulting directly or indirectly from the application of the information contained in this publication.All products from WOERNER may only be used as intended and corresponding to the information in this publication.For products supplied with operating instructions,the additional directives and information contained in them are to be complied with.Materials deviating from those mentioned in this publication and the technical documents which further apply may only be poured into and processed in the appliances and systems manufactured and supplied by WOERNER by following agreement with and written approval by WOERNER.The safety and danger information stated in the safety data sheets of the substances used must be taken into account at all costs.Transportation of gases,liquefied gases,gases under pressure,vapours and liquids,the vapour pressure of which is more than 0,5bar above normal atmospheric pressure (1013mbar)at the maximum admissible temperature,of easy inflammable or explosive media as well as transportation of foodstuffs is forbidden.With Directive 2002/95/EC of January 27,2003,for the limitation of the use of certain hazardous substances in electrical and electronic devices (RoHS)material bans come into effect from July 2006for electrical and electronic devices newly placed on the market for lead,cadmium,hexavalent chromium,mercury and brominated flame retardants.In its controls and switching devices,WOERNER only uses materials which fulfil the criteria of EU Directive 2002/95/EC.To the extent that hexavalent chromium has been used as corrosion protection in the parts which we produce ourselves,it has already been replaced by other environmentally tolerable protective measures.The mechanical devices supplied by WOERNER are not affected by EU Directive 2002/95/EC as they are appliances added or installed on "large-scale stationary industrial tools"(cf.EU Directive 2002/96/EC,Annex IA).But as WOERNER is conscious of its responsibility towards the environment,we shall also use materials fulfilling the requirements of the Directive for devices not covered by EU Directive 2002/95/EC as soon as they are generally available and their use is technically possible.Information on EU Directive 2002/95/EC (RoHS)EUGEN WOERNER GmbH & Co. KGPostfach 1661DE-97866 Wertheim Tel.+49 (0) 9342 803-0Fax.+49 (0) 9342 803-202www.woerner.deHafenstrasse 2DE-97877 Wertheim info@woerner.de - Subject to modifications -。
维克斯45VPF系列-21设计-高压高性能梭形泵部件手册说明书
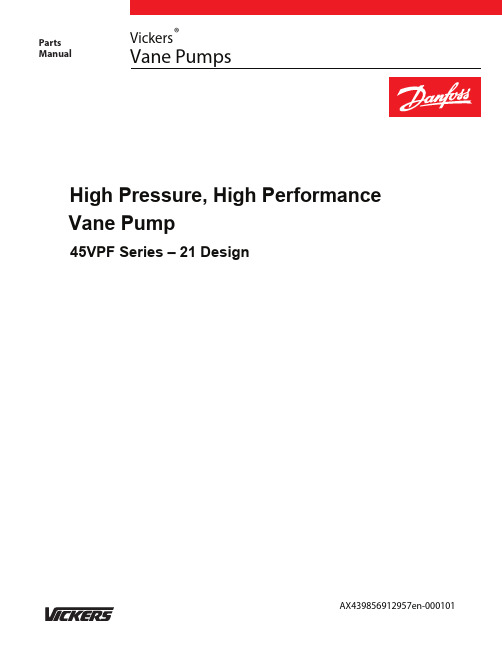
45VPF Series – 21 DesignHigh Pressure, High PerformanceVane PumpParts ManualAX439856912957en-000101High Pressure, High Performance Vane Pump45VPF Series – 21 DesignService DataViton is a registered trademark of E.I. DuPont Co.Parts prefixed with symbols areavailable only in kits (see back page).NOTE: Lubricate all parts and seals with a thin coat of oil at assembly.45VPF–***–***–*–*–01Model Code45VPF–***–***–*–*–0245VPF–***–***–*–*–0345VPF–***–***–*–*–0545VPF–***–***–*–*–06883356883357883358883359860370Key 928543928547Shaft Included in Cartridge Kit (see table)Included in Flange Kit (see table)928542Model CodeTypical sectional viewTo reverse Cartridge rotation remove Retaining Ring and Bearing Carrier S/A. Install Bearing Carrier S/A and Retaining Ring in opposite end ofCartridge and reinstall Cartridge facing in opposite direction. For R.H. rotation the end of the Cartridge with screw heads showing will be installed toward the cover end. For L.H. rotation the end of the Cartridge with screw heads showing will be installed toward the shaft end.02–142427 STD Seal Kit, Single Shaft Seal or02–142429 Viton Seal Kit, Single Shaft seal.02–142428 STD Seal Kit, Double Shaft Seal or02–142430 Viton Seal Kit, Double Shaft Seal.Shaft Seal OptionC –Primary and secondary seals:both with spring loaded sealing member facing inward.B –Primary and secondary seals:primary seal with spring loaded sealing member facing inward and secondary seal with spring loaded sealing member facing outward.A –Primary seal only: sealing member facing inward.Danfoss Power Solutions is a global manufacturer and supplier of high-quality hydraulic and electric components. We specialize in providing state-of-the-art technology and solutions marine sector. Building on our extensive applications expertise, we work closely with you to ensure exceptional performance for a broad range of applications. We help you and other customers around the world speed up system development, reduce costs and bring vehicles and vessels to market faster.Danfoss Power Solutions – your strongest partner in mobile hydraulics and mobile Go to for further product information.outstanding performance. And with an extensive network of Global Service Partners, we also provide you with comprehensive global service for all of our components.Local address:DanfossPower Solutions GmbH & Co. OHG Krokamp 35D-24539 Neumünster, Germany Phone: +49 4321 871 0DanfossPower Solutions ApS Nordborgvej 81DK-6430 Nordborg, Denmark Phone: +45 7488 2222DanfossPower Solutions (US) Company 2800 East 13th Street Ames, IA 50010, USA Phone: +1 515 239 6000DanfossPower Solutions Trading (Shanghai) Co., Ltd.Building #22, No. 1000 Jin Hai Rd Jin Qiao, Pudong New District Shanghai, China 201206Phone: +86 21 2080 6201Danfoss can accept no responsibility for possible errors in catalogues, brochures and other printed material. Danfoss reserves the right to alter its products without notice. This also applies to productsagreed.All trademarks in this material are property of the respective companies. Danfoss and the Danfoss logotype are trademarks of Danfoss A/S. All rights reserved.© Danfoss | September 2022•Cartridge valves •DCV directional control valves•Electric converters •Electric machines •Electric motors •Gear motors •Gear pumps •Hydraulic integrated circuits (HICs)•Hydrostatic motors •Hydrostatic pumps •Orbital motors •PLUS+1® controllers •PLUS+1® displays •PLUS+1® joysticks and pedals•PLUS+1® operator interfaces•PLUS+1® sensors •PLUS+1® software •PLUS+1® software services,support and training •Position controls and sensors•PVG proportional valves •Steering components and systems •TelematicsHydro-GearDaikin-Sauer-Danfoss。
维克斯涡轮泵零件说明书
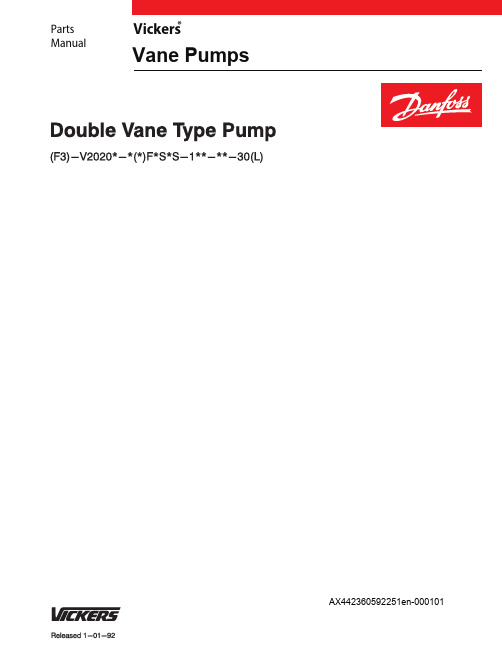
Vickers®Vane PumpsParts ManualAX442360592251en-000101Model CodeTypical Sectional ViewPrinted in U.S.A.Danfoss Power Solutions is a global manufacturer and supplier of high-quality hydraulic and electric components. We specialize in providing state-of-the-art technology and solutions marine sector. Building on our extensive applications expertise, we work closely with you to ensure exceptional performance for a broad range of applications. We help you and other customers around the world speed up system development, reduce costs and bring vehicles and vessels to market faster.Danfoss Power Solutions – your strongest partner in mobile hydraulics and mobile Go to for further product information.outstanding performance. And with an extensive network of Global Service Partners, we also provide you with comprehensive global service for all of our components.Local address:DanfossPower Solutions GmbH & Co. OHG Krokamp 35D-24539 Neumünster, Germany Phone: +49 4321 871 0DanfossPower Solutions ApS Nordborgvej 81DK-6430 Nordborg, Denmark Phone: +45 7488 2222DanfossPower Solutions (US) Company 2800 East 13th Street Ames, IA 50010, USA Phone: +1 515 239 6000DanfossPower Solutions Trading (Shanghai) Co., Ltd.Building #22, No. 1000 Jin Hai Rd Jin Qiao, Pudong New District Shanghai, China 201206Phone: +86 21 2080 6201Danfoss can accept no responsibility for possible errors in catalogues, brochures and other printed material. Danfoss reserves the right to alter its products without notice. This also applies to productsagreed.All trademarks in this material are property of the respective companies. Danfoss and the Danfoss logotype are trademarks of Danfoss A/S. All rights reserved.© Danfoss | September 2022•Cartridge valves •DCV directional control valves•Electric converters •Electric machines •Electric motors •Gear motors •Gear pumps •Hydraulic integrated circuits (HICs)•Hydrostatic motors •Hydrostatic pumps •Orbital motors •PLUS+1® controllers •PLUS+1® displays •PLUS+1® joysticks and pedals•PLUS+1® operator interfaces•PLUS+1® sensors •PLUS+1® software •PLUS+1® software services,support and training •Position controls and sensors•PVG proportional valves •Steering components and systems •TelematicsHydro-GearDaikin-Sauer-Danfoss。
丹福斯 Vane Pumps AX438766743846en-000101 服务和零部件手册说明书
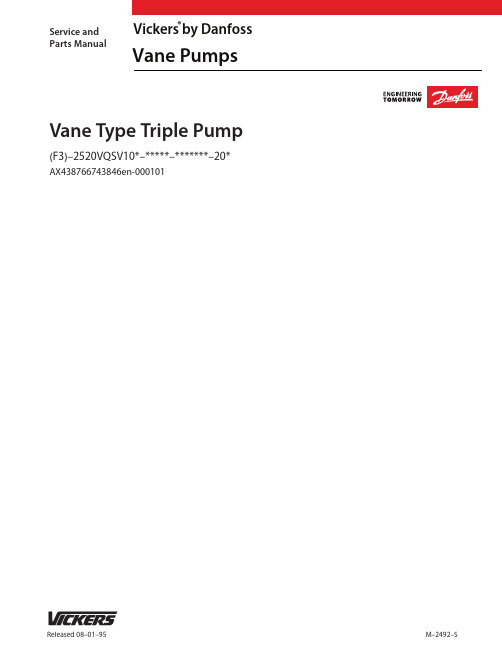
Released 08–01–95Service and Parts ManualM–2492–SVane Type Triple Pump(F3)–2520VQSV10*–*****–*******–20*Vickers by Danfoss®Vane PumpsAX438766743846en-000101V10F control valve S/ABolt (4 Req ’d) (See T able)T orque 41–61 N.m.(35–45 lb. ft.)590019“O” Ring 941038 Shim Kit Bolt (4 Req ’d) (See T able)T orque 41–61 N.m.(35–45 lb. ft.)320353 Plug590019“O” Ring 309199 Plug389460 Spring Control Valve S/A (See T able)386524 PistonV10P Cover Option (See T able)590019“O” Ring 2706 Seat 82800 Poppet Spring (See T able)307354 PlugV10S Cover Option(See T able)586581“O” Ring28422 Spring374343 Pressure Plate S/AVane Kit (See T able)Rotor (See T able)Ring (See T able)Pin (2 Req ’d) (See T able)586582 “O” Ring374865 Plug 590019“O” Ring 239766 SpringV10F Cover Option (See T able)Bolt (4 Req ’d)(See T able)T orque 41–61 N.m.(35–45 lb. ft.)374865 Plug229613233018232794232795232796232797232798232799233019233020923471923470923496923469923468923497923498295344432511295346SAE rated capacity (V10 cover end cartridge)USgpm Rotor V ane Kit (12 vanes)Ring Pin (V10S)Pin(V10F/V10P)Bolt (V10S)Bolt (V10F)Bolt (V10P)Cartridge Kit 1234567245616662179341111561278432509295344432511295346317681351247357286923499923500923501317674317675317676317677317678355641331813Pressure setting – V10P/V10F (Omit for V10S)250 psi 500 psi 750 psi 1000 psi 1250 psi 1500 psi 1750 psi 2000 psi 2250 psi 2500 psiCode A B C D E F G H J K Pressure setting V10P/V10FV10P Spring 252886228022822281V10 port connectionCode V10S Cover V10F Cover V10P Cover P R S Y T K 37286337286437286537782937954337285138826291017155023 Ring 396095“O” Ring 572823 Wear plate 586582 “O” Ring 245616662179341(See T able)Included in 25** VQ shaft end cartridge kit. Included in **20 VQ center cartridge kit.Included in V10 cover end cartridge kit.Included in seal kit 920166. (Kit contains F3components & both shaft seals.) Included in ex side plate kit; bronze face of plate must be installed toward the rotor. Kit also contains four seal packs. Assemble seal with spring loadedsealing member towards bearing. Seals to be completely wetted with oil prior to assembly.Install 419673 & 419672 sealing ring into body, then install cartridge kit.T orque 4–5 N.m. (40–50 lb.in.)NOTE: Body kit includes body, ball, and plug. (Ball and plug not shown)Primary portStr. thd Secondary port Str. thd.T ank port Str. thd CodeControlled ow rate, V10F & V10P(Omit for standard cover)Pump series designationModel CodeSpecial sealsPump series designation25**VQ – Shaft end pump **20VQ – Center pumpBody mounting angeS – SAE mounting per J –744 101–2V10 cover end pumpV10 pump cover optionsS – Standard coverF – Flow control and relief cover P – Priority valve and relief coverA – 4 bolt ange (inch thread)AM – 4 bolt ange (metric thread)VQ port connections (inlet & outlet #1 & #2)F3– Vition ”O”Rings and shaft seals SAE rated capacity(VQ shaft – end cartridge)10– 10 USgpm 12– 12 USgpm 14– 14 USgpm 16– 16 USgpm17– 17 USgpm 19– 19 USgpm 21– 21 USgpmCodeSAE rated capacity(V10 cover end cartridge)1– 1 USgpm 2– 2 USgpm 3– 3 USgpm 4– 4 USgpm5– 5 USgpm 6– 6 USgpm 7– 7 USgpmCode Code Shaft sealBlank – Single seal S – Double sealShaft type297 – All seriesDesign (Subject to change)Rotation(Viewed from shaft end of pump)Port orientation (Outlet #3or primary outlet)(Viewed from cover end of pump;refer to table on next page)3– 3 USgpm 4– 4 USgpm 5– 5 USgpm6– 6 USgpm 7– 7 USgpm 8– 8 USgpmCode Code Relief valve pressure setting,V10F & V10P(Omit for standard cover)A – 250 psiB – 500 psiC – 750 psiD – 1000 psiE – 1250 psiCode Code F – 1500 psi G – 1750 psi H – 2000 psi J – 2250 psi K – 2500 psiL – Left hand for counterclockwise R – Right hand for clockwiseCodeV10 port connections V10S standard covers and outlet # 3S – .750–16 Str. thd.P –1/2”–NPT thd.Y – .875–14 Str. thd.R – 1.062–12 Str. thd.CodeV10F ow/relief control cover Outlet # 3T ank port T – .750–16 Str. thd P – .750–16 Str. thd..750–16 Str. thd.1/2”–NPT thd.Code V10P priority control coversK – .5625–18.750–16.5625 –18Port orientation (Outlet #1)(Viewed from cover end of pump;refer to table on next page)Port orientation (Outlet #2)(Viewed from cover end of pump;refer to table on next page)5– 5 USgpm 6– 6 USgpm 8– 8 USgpm 9– 9 USgpm11– 11 USgpm 12– 12 USgpm 14– 14 USgpmCodeSAE rated capacity (VQ center cartridge)Code 81234576910111213141516171819Position view onlyPort orientation code131415NOTETo reverse cartridge kit rotation, remove the twoscrews and reverse the location of the inlet support plate and the outlet support plate. Reinstall the two screws hand tight. Use pump cover to align all sections of the cartridge. Carefully remove the cover and tighten the screws.When ordering spare cartridge parts, it is recommended they be obtained in cartridge kits. Kits are assembled and tested for either right or left hand rotation. If left hand rotation is required, it should be speci ed on parts order by adding su x ”L” to cartridge kit number.V10 cover can be assembled in any of four positions refer to drawing M –2005–S.Danfoss Power Solutions is a global manufacturer and supplier of high-quality hydraulic and electric components. We specialize in providing state-of-the-art technology and solutions that excel in the harsh operating conditions of the mobile off-highway market as well as the marine sector. Building on our extensive applications expertise, we work closely with you to ensure exceptional performance for a broad range of applications. We help you and other customers around the world speed up system development, reduce costs and bring vehicles and vessels to market faster.Danfoss Power Solutions – your strongest partner in mobile hydraulics and mobile electrification.Go to for further product information.We offer you expert worldwide support for ensuring the best possible solutions foroutstanding performance. And with an extensive network of Global Service Partners, we also provide you with comprehensive global service for all of our components.Local address:DanfossPower Solutions GmbH & Co. OHG Krokamp 35D-24539 Neumünster, Germany Phone: +49 4321 871 0DanfossPower Solutions ApS Nordborgvej 81DK-6430 Nordborg, Denmark Phone: +45 7488 2222DanfossPower Solutions (US) Company 2800 East 13th Street Ames, IA 50010, USA Phone: +1 515 239 6000DanfossPower Solutions Trading (Shanghai) Co., Ltd.Building #22, No. 1000 Jin Hai Rd Jin Qiao, Pudong New District Shanghai, China 201206Phone: +86 21 2080 6201Danfoss can accept no responsibility for possible errors in catalogues, brochures and other printed material. Danfoss reserves the right to alter its products without notice. This also applies to products already on order provided that such alterations can be made without subsequent changes being necessary in specifications already agreed.All trademarks in this material are property of the respective companies. Danfoss and the Danfoss logotype are trademarks of Danfoss A/S. All rights reserved.Products we offer:•Cartridge valves •DCV directional control valves•Electric converters •Electric machines •Electric motors •Gear motors •Gear pumps •Hydraulic integrated circuits (HICs)•Hydrostatic motors •Hydrostatic pumps •Orbital motors •PLUS+1® controllers •PLUS+1® displays •PLUS+1® joysticks and pedals•PLUS+1® operator interfaces•PLUS+1® sensors •PLUS+1® software •PLUS+1® software services,support and training •Position controls and sensors•PVG proportional valves •Steering components and systems •TelematicsHydro-GearDaikin-Sauer-Danfoss。
丹福斯Vane Pumps服务和零件手册说明书

Vickers by Danfoss®Vane PumpsService and Parts ManualAX438768604875en-000101SPACER KITVTA VTB VTBP VTC58493658492294129694129702-136817MODEL ADAPTER PLATE ADAPTERKIT COUPLING RETAINING RING COUPLINGKIT 58183394129822317283003 (1)83003 (2)10398942677058492402-13681002-13681302-13681402-136816NOTEFOR BP MODELS AN ADAPTER KIT AND SPACER KIT IS REQUIRED.Included in seal kit (See Table)Included in cartridge kit (See Table)Included in coupling kit (See Table)Included in adapter kit (See Table)Included in spacer kit (BP models only)F3 equivalent seal kit (See Table)585658Parts pre xed with symbols available only in kits.For satisfactory service life of these components in industrial applications,use full ow ltration to provide uid which meets ISO cleanliness code 16/13 or cleaner. OFP , OFR, and OFRS series lters are recommended.NOTEsealing member towards bearing. Seals to be completely wetted with oil prior to assembly.Model CodeDanfoss Power Solutions is a global manufacturer and supplier of high-quality hydraulic and electric components. We specialize in providing state-of-the-art technology and solutions that excel in the harsh operating conditions of the mobile off-highway market as well as the marine sector. Building on our extensive applications expertise, we work closely with you to ensure exceptional performance for a broad range of applications. We help you and other customers around the world speed up system development, reduce costs and bring vehicles and vessels to market faster.Danfoss Power Solutions – your strongest partner in mobile hydraulics and mobile electrification.Go to for further product information.We offer you expert worldwide support for ensuring the best possible solutions foroutstanding performance. And with an extensive network of Global Service Partners, we also provide you with comprehensive global service for all of our components.Local address:DanfossPower Solutions GmbH & Co. OHG Krokamp 35D-24539 Neumünster, Germany Phone: +49 4321 871 0DanfossPower Solutions ApS Nordborgvej 81DK-6430 Nordborg, Denmark Phone: +45 7488 2222DanfossPower Solutions (US) Company 2800 East 13th Street Ames, IA 50010, USA Phone: +1 515 239 6000DanfossPower Solutions Trading (Shanghai) Co., Ltd.Building #22, No. 1000 Jin Hai Rd Jin Qiao, Pudong New District Shanghai, China 201206Phone: +86 21 2080 6201Danfoss can accept no responsibility for possible errors in catalogues, brochures and other printed material. Danfoss reserves the right to alter its products without notice. This also applies to products already on order provided that such alterations can be made without subsequent changes being necessary in specifications already agreed.All trademarks in this material are property of the respective companies. Danfoss and the Danfoss logotype are trademarks of Danfoss A/S. All rights reserved.Products we offer:•Cartridge valves •DCV directional control valves•Electric converters •Electric machines •Electric motors •Gear motors •Gear pumps •Hydraulic integrated circuits (HICs)•Hydrostatic motors •Hydrostatic pumps •Orbital motors •PLUS+1® controllers •PLUS+1® displays •PLUS+1® joysticks and pedals•PLUS+1® operator interfaces•PLUS+1® sensors •PLUS+1® software •PLUS+1® software services,support and training •Position controls and sensors•PVG proportional valves •Steering components and systems •TelematicsHydro-GearDaikin-Sauer-Danfoss。
海格威尔 12V 手动排水泵 配件表说明书

151********PUMP & MOTOR ASSY .115054150541• Motor - 12 Volt 215026150261• Pump Assy.315581155811•• Shaft Seal 415045152041Cylinder Tank 5*151********O-Ring 3-1/2 I.D.6*151********O-Ring 1-15/16 I.D.7*151********O-Ring 1-1/8 I.D.815194151941Cover & Seal Assy.905119051191• Wiper10*151********• O-Ring 3-1/2 I.D.1115199151991• Sleeve08473084731PRESSURE RELIEF VALVE KIT 1221805218051• Reducer Bushing 1/4 - 1/81321806218061• Pressure Relief Valve 1415207152051Cylinder 1515209152091Washer16a 153********RAM ASSEMBL Y 1615208152061• Ram 1715158151581• Piston1815219152191• Piston Follower 19157601• Spacer20*151********• Packing Cup 21*15125151251• O-Ring 7/16 I.D.221• Locknut 1/2-13233Locknut 5/16-242415573155731Base & Strainer Assy.2515326153261• Strainer 2615042152033Stud 2715043150433Stud2815574155741PUMP CHECK VALVE KIT 29*1• O-Ring 3/8 I.D.301• Seat311• Ball, 9/32321• Spring33*151********O-Ring 1/4 I.D.3415620156201FILTER KIT - 1/2"3515619156191• Filter3621827218271• Plug w/O-Ring - 1/2"3621827218272Plug w/O-Ring - 1/2"34156411FILTER KIT - 9/16"E-463515619156191• Filter3621999219991• Plug w/O-Ring - 9/16"3621999219992Plug w/O-Ring - 9/16"3415620156202FILTER KIT - 1/2"3515619156191• Filter3621827218271• Plug w/O-Ring - 1/2"3621827218271Plug w/O-Ring - 1/2"3415641156412FILTER KIT - 9/16"E-473515619156191• Filter3621999219991• Plug w/O-Ring - 9/16"3621999219991Plug w/O-Ring - 9/16"37*151********O-Ring 5/8 I.D.38*21929219293Washer, Nyltite 5/163920697206973Locknut 5/16 - 244015356153561"A" Solenoid Assembly 4115392153921• "A" Coil, Black Wire 4215393153931• "A" Cartridge Valve *15431154311•• Seal Kit, "A" Valve 40a 156********"A" Solenoid Assembly 41a 156********• "A" Coil, Black Wire 42a 156********• "A" Cartridge Valve *15431154311•• Seal Kit, "A" Valve 4315758157581• VALVE ASSY . w/COUP .4422295222951•• Forged 90 Degree Elbow 4522294222941•• Coupler, Female Half4622293222931• Coupler, Male Half 4715606156061• Kit-Crossover Valve 481•• O-ring 491•• O-ring 501•• Cage511•• O-ring w/Glyd. Ring 521•• Poppet 531•• Washer 541•• Guide 551•• Spring 561•• Spacer 571•• Disc 581•• Plug591•• Adj. Screw 601•• O-ring611•• Acorn Nut 9/16-18*156********•• Seal Kit-Crossover Valve (includes items 48,49,51,60)6215639156391• Kit-Pilot Check Valve 631•• Ball, Steel 641•• Spring 651•• Plug 6615609156091• Piston6715359153591• Plug Valve Block 68*151********•• O-ring 9/16 I.D.6915697156971• "B" Solenoid Assembly 7015382153821•• "B" Coil, Red Wire 7115698156981•• "B" Cartridge Valve *15432154321•• Seal Kit-"B" Cartridge 7215358153581• "C" Solenoid Assembly 7315430154301•• "C" Coil, Green Wire 7415381153811•• "C"-Cartridge Valve *15433154331•• Seal Kit-"C" Cartridge7515576155761• Kit-"B" Solenoid Check Valve 761•• Ball, 7/16771•• Spring7821826218264Scr., Soc. Head 5/16-18 x 1-1/2"7915646156461End Plate8021859218594Scr., Soc. Head 5/16-18 x 3/48115621156211Baffle8221980219802Retainer Ring155********VALVE ASSEMBLY 8315578155781• Kit - Crossover Valve 841•• Poppet 851•• Spring861•• O-Ring 1/4 I.D.871•• Plug8815577155771• Kit - "C" Solenoid Check Valve 891•• Ball 3/16901•• Spring 911•• Plug9215575155751• Kit - Pilot Check Valve 931•• Ball 941•• Spring 951•• Plug 9615366153661• Piston974Scr., Soc. Head9815611156111Kit - Pump Relief Valve 991• Poppet 1001• Spring 1011• Guide 1021• O-Ring 1031• Retainer 1041• Set Screw1052• Washer w/O-Ring 1061• Jam Nut 1071• Acorn NutForm No. 1-523R17July, 2001PARTS & INSTALLATION INSTRUCTIONSE-46 & E-47 ELECTRO-LIFT ®"Old Style"with 3/8" stem on valve and small hole in coil. (Requires brass nut)"New Style"with 9/16"stem on valve and large hole in coil.PARTS LISTSTANDARD-LONG STROKE-UP THROUGHHM-9 & HM-10C-9ONL YITEM1-1/8" x 6" Stroke 1-1/8" x 8" Stroke QTY . DESCRIPTIONE-46E-47E-46H E-47HSTANDARD-LONG STROKE-UP THROUGHHM-9 & HM-10C-9ONL YITEM 1-1/8" x 6" Stroke 1-1/8" x 8" Stroke QTY . DESCRIPTIONE-46E-47E-46H E-47HNOTES: 1. *Parts included in Master Seal Kit Part No. 15456.2.Set Crossover Relief Valve @ 3800 ± 400 P .S.I. @ 2-1/2 G.P .M. flow.3.Set Pump Relief Valve @ 1650 ± 50 P .S.I. full flow.Parts indented are included in assembly under which they are indented.Meyer Products and Diamond Equipment reserves the right, under its continuing product improvement program, to change construction or design details,E-46, E-46H, E-47 and E-47HExploded ViewNote: Oil seepage, if any, at O-ring (60)is normal, DO NOT attempt to stop thisseepage by further tightening of theAcorn Nut.GENERAL INFORMATIONBefore the Meyer Electro-Lift® unit is disassembled for repairs, make certain that all the maintenance procedures have been checked; refer to Owner's Manual.When the unit is to be overhauled, Master Seal Kit Part No. 15456 is required. This Kit contains all necessary Seals for rebuilding. NOTE: DO NOT REUSE OLD O-RINGS.When ordering parts, furnish Type of Unit, Part No., Name and Description.These instructions are intended as a guideline for overhaul of an E-46/E-47 Electro-Lift® unit.More detailed information covering principles of Operation, Troubleshooting, Disassembly and Repair are found in Electro-Lift® Service Manual 1-562. This is available for a nominal fee from your Meyer Distributor or directly from Meyer Products.DISASSEMBLY AND INSPECTION OF UNIT Drain fluid from the unit by removing Pressure Relief Valve (13) or Drain Plug (36). Clamp Sump Base (24) firmly into vise.1.To disassemble COVER ASSEMBLY, TANK, RAM &CYLINDER PARTS, remove three Locknuts (39).2.To disassemble MOTOR from PUMP, loosen Motormounting bolts, but DO NOT REMOVE.Note: Motor end plate to be held in place. Temporarily install two 1/4-20 nuts on the motor mounting bolts to keep motor intact. Remove nuts when reinstalling Motor to pump.3.To disassemble Pump from Base, remove three Locknuts(23).4.To disassemble VALVE BLOCK from BASE, remove Soc.Hd. Screws (78, 80 or 97).SUBASSEMBLIES - INSPECTION1.COVER ASSEMBLY, TANK, RAM & CYLINDER PARTS:a)Check Cover (8), and Base (24) castings for cracksand damage.b)Replace Wiper Seal (9) pressed in Cover (8).c)Inspect Sleeve (11), Piston (17), the Piston Follower(18), Spacer (19) for excessive wear. Replace PackingCup (20). Inspect Cylinder (14) for scoring and pittingin bore.d)Inspect Ram (16) for nicks and rust.2.MOTOR (1)Note: Complete Motor Assemblies are only availablefrom Meyer Products. Service and repair parts can bepurchased from your nearest authorized Prestolite orAmerican Bosch Service Stations.a)Prestolite Motor can be identified by a "Domed TopCover" and name "Prestolite" stamped on Motor Body.b)American Bosch Motors have a "Flat Top Cover" andno identifying marks.3.PUMP (2)DO NOT at any time disassemble this Pump. This will void the warranty.a)The damaged pump drive Shaft Seal (3) may beremoved by careful extraction with a pointed tool. Dipnew Seal in oil and with lip down, press into PumpHousing flush to 1/32 inch below face of boss.4.BASE (24)a)Remove and clean Solenoid (40) and inspect forexternal damage.b)Test Coil (41) for electrical continuity. Nominal Coilresistance is 9.6 ohms. Replace O-rings from Seal KitPart No. 15431 contained in Seal Kit No. 15456.c)To reassemble, carefully guide the Coil (41) over theValve Cartridge (42) and use the original External BrassNut.d)Remove and clean the Filter Screen (34) usingkerosene and blow out with air. Replace O-rings (33)from Seal Kit No. 15456.5.VALVE BLOCKSa)Remove items (69), (76) & (77). Clean "B" Solenoid(69) and inspect for damage. Disassemble CartridgeValve (71) and replace O-rings from Seal Kit No. 15432contained in Seal Kit No. 15456.b)Remove and clean "C" Solenoid (72) and inspect fordamage. Disassemble Cartridge Valve (74) and replaceO-rings and nylon back-up rings from Seal Kit No.15433 contained in Seal Kit No. 15456. Be certain O-rings and spacers are oriented properly.c)Test both Coils (70 & 73) for electrical continuity.Nominal Coil resistance is 3.7 ohms.d)Remove Plug (67) and Piston Assembly (66 or 96) andinspect the Piston for scratches. Replace O-ring (68)from Seal Kit No. 15456.e)Remove Pilot Check Valve Parts (62 or 92) and inspectall parts for damage.f)Remove Plugs (87) with caution as these are springloaded.g)Remove all parts of Item 47 or 83 and inspect fordamage. Replace O-rings from Seal Kit No. 15456. Setadjustable crossover to 3800 P.S.I. ± 400 P.S.I.h)Remove all parts of Item 88 and inspect for damage.i)With parts removed from Valve Block, clean and blowout with air to remove any foreign particles in Block.6.UNIT REASSEMBLYa)Before reassembling, make certain all components andsub-assemblies are clean and free from all dirt andother foreign material.b)When replacing parts, install (63), (64) & (65) or (93),(94) & (95) before installing Piston (66 or 96) and Plug(67).c)Motor mounting bolts must be sealed with Permatexor an all weather Type sealant.d)USE NEW SEALS AND M-1 FLUID WHENREASSEMBLING THE UNIT.d)Proper fluid level is 1-1/2" below filler hole. It must bechecked with Lift Ram fully retracted.。
Viking Pump, Inc. Technical Service Manual

FIGURE 2 SIZE 31 With Solid Input Shaft
CAUTION !
To avoid oxidation and possible seizure of the motor shaft to the NEMA-C or IEC motor flange adaptor bore, apply an anti-seize product to the motor shaft prior to assembly.
Electronic copies of the most current TSM issue can be found on the Viking Pump website at
TECHNICAL SERVICE MANUAL
Viking® In-Line Helical Gear Reducers Sizes 11, 21, 31, 35, 41, 51, 61, 70, 80, 90, 100
Contact your authorized distributor or Viking Technical Service for vertical or other mounting arrangements.
Table 1
Size 11 * 21 * 31 * 35 * 41 * 51 61 70 80 90 100
C) For long term storage (over 60 days), all machined surfaces such as flanges, shafts and couplings must be protected with a suitable rust inhibiting product (Mobilarma 248 or equivalent).
莫诺L系列泵维护手册说明书

Section:L and J FRAME PUMPSPage: 1Date: (Revision 6/93) OPERATION – ASSEMBLY INSTRUCTIONS AND PARTS LIST FOR“L6” DRIVE END(FRAME SIZES 1L6, 2L6, 3L6, 3M4, 6M4, 3P3, 6P3, 9P3)GENERALThe Moyno® Pump is one of the most versatile pumps available. It has been proven in thousands of applications over the past 50 years. It is backed by the experience gained over the years, both in application and manufacturing know-how.The Moyno progressing cavity pump is a single-screw rotary pump. The pumping action is created by the single helical rotor rolling eccentrically in the double threaded helix of the stator. In its revolution, the rotor forms in conjunction with the stator a series of sealed cavities 180 degrees apart. As the rotor turns the cavities progress from the suction to the discharge. As one cavity diminishes, the opposing cavity is increasing at exactly the same rate. Thus, the sum of the two discharges is a constant volume. The result is a pulsation-less positive displacement flow with no valves.WARNING1. Enclose all rotating belts, pulleys, drive shafts, etc., tocomply with acceptable industry safety standards for rotating equipment. Failure to comply could result in personal injury.2. All pulleys have speed limitations. Refer to pulleymanufacturer’s literature for specifications and follow all recommendations, to prevent personal injury. NAMEPLATE DATAThe Moyno Pump nameplate, located on the bearing housing, carries the serial number, frame size, and type designation. All are extremely important and must be used when ordering spare parts.Record the nameplate data of your pump in the spaces provided in the heading of Page 3.Moyno Pumps are identified by Frame and Type. Pump Frame is essentially an indication of size. It consists of a number, a letter, and a number (i.e. 2L6). The first number indicates the number of stages in the pumping elements. The letter indicates the model. The final number indicates the size of the rotor-stator pumping elements. A frame 2L6 pump, therefore, has two stages of size 6 pumping elements.The “L” in the frame size indicates a standard relationship between the housing, bearings, and drive shaft and the size of the pumping elements. Many variations may be made by adapting smaller element sizes to a larger drive end size. This may be necessary due to the severity of a specific pumping application. In cases where the drive end (housing, bearings, and drive shaft) is one size larger than the element size normally used, the pump is referred to as an “M” frame pump (i.e. 3M4). If the drive end is two sizes larger than the element size, the pump is referred to as a “P” frame. Thus, a frame 3L6, 3M4, and 3P3 would all use a common drive end.Type designation is a series of letters which identify the “Materials of Construction” in component groups of parts. The usual type designation will consist of three letters.The first letter identifies the material of the suction housing casting or the body casting where the bearing housing is a part of the suction housing.C — Cast IronE — Alloy cb-20 StainlessH — Hastelloy “C”M — MonelS — 316 Stainless SteelW — Cast SteelX — Special to applicationThe second letter indicates the material used in the drive shaft, pins, connecting rod, rotor, and other minor metallic parts in contact with the material being pumped.D — Alloy SteelE — Alloy cb-20 StainlessG — 416 Stainless SteelH — Hastelloy “C”J — 17-4 PH Stainless SteelM — MonelS — 316 Stainless SteelX — Special to applicationThe third letter determines the material of the stator. It identifies only the stator material and not that of the tube in which the stator is placed.B — EPDM 300, 70 DurometerC — Buna “N” 103, 50 DurometerD — Tool SteelE — Buna “N” 110, 70 DurometerF — Viton 500, 75 DurometerG — 416 Stainless SteelH — Hastelloy “C”J — 17-4 PH Stainless SteelK — Hypalon 800, 70 DurometerM — Buna “N” 100M. 70 DurometerP — Thiokol 70 DurometerQ — Buna “N” 100, 700 DurometerR — Natural Rubber 200, 55 DurometerT — Teflon 15% glassU — Urethane 70 DurometerX — Special to applicationZ — Buna “N” 150, 70 Durometer• 2* ADD THIRD LETTER OF TYPE DESIGNATION TO COMPLETE PART NO. EX: TYPE CDQ PUMP – ADD Q TO BASIC NUMBER OF STATOR. ** Bearing Kit includes Items A thru G *** Connecting Rod Kit includes items Q thru V. + see pages 5 – 6 for variations“L6” DRIVE END PARTS TYPE DESIGNATIONSSelect type column corresponding to type designation at left.Order by part number Refer to frame size to select proper rotor and stator.REF. NO .DESCRIPTION CDQ CDR CDB CDF Part No. CDD CDG CDT Part No. CSQ CSR CSB CSF Part No. CSG CSD CST Part No. SSQ SSR SSB SSF Part No. SSG SST Part No. A. Ball Bearing (Radial)A06291 A06291 A06291 A06291 A06291 A06291 B. Ball Bearing (Thrust)A06301 A06301 A06301 A06301 A06301 A06301 C. Bearing SpacerA06331 A06331 A06331 A06331 A06331 A06331 D. Bearing Lock NutA06581 A06581 A06581 A06581 A06581 A06581 E. Bearing Lock WasherA06591 A06591 A06591 A06591 A06591 A06591 F. Grease Seal (Radial)A06611 A06611 A06611 A06611 A06611 A06611 G. Grease Seal (Thrust) A06621 A06621 A06621 A06621 A06621 A06621Bearing Kit** K06291 K06291 K06291 K06291 K06291K06291 H. Bearing Housing A06051 A06051 A06051 A06051 A06051A06051 I. Bearing Cover Plate A06341 A06341 A06341 A06341 A06341A06341 J. Pump Support with Cap A06371 A06371 A06371 A06371A06371 A06371 K. Shaft Collar A06491 A06491 A06491 A06491 A06491A06491 M. Lantern Ring A06571 A06571 A06571 A06571 A06571A06571 N. Stator Support with cap (All but 9P3 A06381 A06381 A06381 A06381A06381 A06381 9P3 only A06382 ---------- A06382 ----------A06382 ---------- O. Support Bushing 3M4, 3P3, 6P3 only A06711 A06711 A06711 A06711A06711 A06712 Support Bushing 3P3 only A04711 A06711 A04711 A06711A04711 A06711 P. Pin Retainer A06501 A06501 A06501 A06501 A06501A06501 Q. Retaining Screw Washer A06731 A06731 A06731 A06731 A06731A06731 R. Connecting Rod Washer A06531 ---------- A06531 ---------- A06531---------- All but Type F A0653Q ---------- A0653Q ----------A0653Q ---------- CDF, CSF, SSF A0653F ---------- A0653F ----------A0653F ---------- S. Connecting Rod B0625D B0625D B0625S B0625SB0625S B0625S T. Rotor Pin B0645D B0645D B0645S B0645SB0645S B0645S U. Shaft Pin B0646D B0646D B0646S B0646SB0646S B0646S V. Drive Pin Retaining Screw B0654D B0654D B0654S B0654S B0654SB0654S Connecting Rod Kit***All but Type F K0625D K0625D K0625S K0625SK0625S K0625S CDF, CSF, SSF K0625D ---------- K0625D ----------K0625D ---------- W. Suction Housing B06021 B06021 B06021 B06021 B06026B06026 X. Reducer 1L6, 2L6, 3L6, 6M4 B06091 B06091 B06091 B06091 B06096B06096 3M4, 6P3 B04091 B04092 B04091 B04092 B04096B04097 3P3 B03091 B03092 B03091 B03092 B03096B03097 9P3 B04092 ---------- A04092 ---------- B04097---------- Y. Drive Shaft + B06261 B06261 B06266 B06266B06266 B06266 Z. Packing Gland B0641D B0641D B0641S B0641SB0641S B0641S AA. Packing + B06421 B06421 B06425 B06425 B06425B06425 BB. Packing Washer B0665D B0665D B0665S B0665SB0665S B0665S CC. Adapter Bushing 3M4, 6P3 B06511 B06512 B06511 B06512B06516 B06517 3P3 only B06513 B06511 B06513 B06511B06518 B06516 9P3 only B06512 ---------- B06512 ----------B06517 ---------- FF. Stator Frame 1L6 C4106* C4106* C4106* C4106* C5106*C5106* Frame 2L6 C4206* C4206* C4206* C4206*C5206* C5206* Frame 3L6 C4306* C4306* C4306* C4306*C5306* C5306* Frame 3M4 C4304* C4304* C4304* C4304*C5304* C5304* Frame 6M4 C4604* C4604* C4604* C4604*C5604* C5604* Frame 3P3 C4303* C4303* C4303* C4303*C5303* C5303* Frame 6P3 C4603* C4603* C4603* C4603*C5603* C5603* Frame 9P3 C4903* C4903* C4903* C4903*C5903* C5903* GG. Rotors Frame 1L6 + C71061 C71061 C81061 C81061C81061 C81061 Frame 2L6 + C72061 C72061 C82061 C82061C82061 C82061 Frame 3L6 + C73061 C73061 C83061 C83061C83061 C83061 Frame 3M4 + M73041 M73041 M83041 M83041M83041 M83041 Frame 6M4 + C76041 C76041 C86041 C86041C86041 C86041 Frame 3P3 + P73031 P73031 P83031 P83031P83031 P83031 Frame 6P3 + P76031 P76031 P86031 P86031P83031 P83031 Frame 9P3 + P79031 P79031 P89031 P89031P89031 P890313A typical type designation such as CDQ would result in the following:C = Cast Iron Suction HousingD =Carbon Steel Internals including drive shaft, pins,connecting rod, rotor, and other minor metallicparts in contact with the material being pumped0 = Buna ‘N’ Synthetic Rubber Stator (70 durometer)Also included on the nameplate is the three-character trim code designation. This only appears on pumps which have semi-standard or special construction. The first letter identifies sealing variations, the second character indentifies internal variations, and the third letter identifies rotor variations.On page 5 of this manual are variations available for modifying pumps to meet specialized pumping conditions. If the trim code of your pump is other than “AAA", contact your nearest Moyno representative for clarification. Do not use any variation unless you have determined that it is compatible with your application.INSTRUCTIONS FOR DISASSEMBLY AND ASSEMBLY Frames 1L6, 2L6, 3L6, 3M4, 6M4, 3P3, 6P3, 9P3 Disassembly Procedure1. Disconnect the power source.2. Close the suction and discharge valves to isolate thepump from the line.3. Turn off flush water to packing or rotary seal if used.4. Remove drain plug in suction housing to drain awayany fluid remaining in pump.5. Place a support block under suction housing in area ofdrain plug. Wooden blocks are sufficient. The purpose Is to prevent undue stress on pump support when pumpis disassembled.6. Disconnect piping from stator end of pump.7. Stator Removal - With pipe wrench or strap wrenchremove discharge reducer (X). Remove cap of stator support and with strap wrench or pipe wrench, unscrewthe stator (FF) from the suction housing. Pull Stator offthe rotor.8. Rotor Removal - The rotor (GG) is removed with theconnecting rod (S) and rotor pin (T) as a unit. Removalof the unit is accomplished by removing the two drive pin retaining screws (V) located in the shaft collar (K).This step reveals the shaft drive pin (U) which is removed by driving the pin from the drive shaft (Y) witha small punch or drift pin. Slide the shaft collar towardthe packing gland (Z) and remove the retaining screw washers (Q) from each side of the drive shaft. The rotorand connecting rod can now be removed by pulling them from the pump. To disassemble, clamp theconnecting rod (S) by its mid-section in a vise and, witha drift pin, drive the pin retainer (P) from the head of therotor. The rotor pin (T) can now be removed from the rotor freeing the connecting rod. Remove the connecting rod washers (R) if present.9. To remove packing (AA), remove nuts holding packinggland (Z). Slip packing gland from studs, remove packing rings, lantern ring (M), and remaining packing rings. Packing rings can be removed with a standard packing puller. Note: If step 10 is to be performed, it should precede step 9 as packing can then be removedby freeing packing gland and driving packing, lanternring, and packing washer (BB) from housing using a small rod. Rod should enter where stator screws intosuction housing. Place rod on pack-ing washer and tap.Entire set should easily exit from opposite end of stuffing box.10. Drive Shaft & Bearing Removal - With rotor removedit is now possible to remove the drive shaft and bearings as a sub-assembly. Remove the four cap screws holding the bearing cover plate (I) and slip from shaft. Insert a bar or rod into the hollow end of drive shaft (Y) where it enters the suction cavity. By tapping on the rod the entire assembly will be forced from the bearing housing.To disassemble, remove bearing lock nut (D) and bearing lock washer (E). Using an arbor press remove radial bearing (A), bearing spacer (C), and thrust bearing (B). Apply pressure to inner race only.When replacing drive shaft and/or bearings, it is recommended that both grease seals be replaced.Grease seals are pressed into the bearing housing and bearing cover plate.Assembly ProcedureMoyno pumps are reassembled in the reverse order of disassembly with special notes as outlined below:1. Always replace all old washers, “O” rings, and packing.We also recommend replacing grease seals when new bearings are installed.2. Bearing Shaft Assembly - When installing newbearings, make sure that they are seated against the shoulder on the shaft. Replace bearing lock washer and bearing lock nut. Tighten bearing lock nut securely.Bend tab down onto lock nut to prevent loosening of nut.Make sure that the shaft collar, packing gland, and packing washer are installed on the drive shaft as the hollow end emerges in the bearing housing and approaches the stuffing box area.When replacing the bearing cover plate, tighten all cap screws evenly to prevent damage to the bearing cover plate and thrust grease seal.Do not over-lubricate bearings. (See Maintenance) 3. When installing the connecting rod, make sure that thehole in the rod is aligned with the holes in the drive shaft and shaft collar before inserting the pin. Always use retaining screw washers and make sure that the hollowed end of the retaining screw fits over the end of the shaft pin to ensure a tight fit. Retaining screws must seat on retaining screw washers and not on pin.4. When replacing packing, insert four rings on the shaft,the lantern ring, and then four more rings. This will allow the lantern ring to line up with the grease fitting on the stuffing box. Make sure you stagger the ends of the packing rings.When installing the new packing, you may find that all but one ring will go on the drive shaft. When the pump has run for a short time and the new packing is compressed, this final ring can be installed.5. When installing the stator on the rotor, it is best tolubricate the rotor with water (or a lubricant compatible with the rubber in the stator) to allow the stator to slip on easier. (Grease or oil Is not compatible with type “R”or “B” stators.)When replacing the stator, always tighten it with the pipe wrench on the end of the stator nearest the suction housing. This will prevent it from binding and damaging the threads.4If your stator has a stainless steel sleeve, use a teflon tape or similar material on the threads before replacing -- on all stators with a carbon steel sleeve, use pipe dope. 6. Caution: Dry operation Is harmful to the pump.Always fill the pump with fluid to be handled prior to start up. Check any valves In discharge line to determine that no restrictions exist.MAINTENANCEThe Moyno pump has been designed for a minimum of maintenance, the extent of which is routine lubrication and adjustment of packing and infrequent lubrication of the bearings. The pump is one of the easiest to work on in that the main elements are very accessible and require few tools to disassemble.PackingThe Moyno pump is normally furnished with die formed packing. The packing may be either grease lubricated through a grease fitting in the stuffing box or have plumbing connected to the housing to allow a water flush. (See Water Flush of Packing)Packing gland adjusting nuts should be evenly adjusted so they are little more than finger tight. Over-tightening of the packing gland may result in premature packing failure and possible damage to the shaft and gland. When the packing is new, frequent minor adjustments are recommended for the first few hours of operation in order to compress and seat the packing. Greasing the packing often but with limited quantities of grease is the best practice. This can be done through a grease fitting which leads to a lantern ring in the mid-section of the packing. Do not use a one-piece spiral wrap of packing.Water Flush of PackingWhen the material being pumped is abrasive in nature, itmay be advantageous to flush the packing to prevent leakage under packing and excessive shaft wear.Clean water can be injected through a 1/8” NPT tapped hole that normally houses the grease fitting for lubricatingthe packing. The water can be permitted to leak axially along the shaft In either direction or can be removed from the second tapped hole In the stuffing box. In both cases, the discharge from the stuffing box should be throttled slightly to maintain 10-15 PSI higher pressure in the stuffing box than is present In the suction housing.This is a basic arrangement, other variations can be used.(1) Throttling Valve (2) Pressure Guage (3) Pressure Regulating ValveBearingsThe Moyno pump is equipped with ball bearings in the drive end size L2 through L10. The bearings are lubricated at the factory and do not need additional lubrication for at least 1500 hours of normal operation.When relubricating the bearings, the bearing-shaft assembly should be removed (See Disassembly Instructions) and cleaned of old grease. Add only enough grease to fill the area between the bearings 1/3 full. Add a few drops of oil to bearing seals before reassembling. It is normal for bearings to run warm to the touch for the first few hours of operation.Any type of Ep Lithium soap base grease is satisfactory for bearing lubrication. The use of Sodium or Calcium base grease is not recommended.The following is a partial listing of approved bearing lubricants:Dow Corning DC 33Keystone Lubricating Co. Keystone #89Texaco RegalAFB2 Shell Oil Co. Cyprina #3Humble Oil & Refining Co. Beacon 325American Oil Co. Supermil Grease #A72832Mobil EP1Shell Oil Co. Alvania #2VARIATIONS OF STANDARD PARTSFollowing are variations available for modifying pumps to meet specialized pumping conditions. If the trim code of your pump is other than “AAA,” contact your nearest Moyno representative for clarification. Do not modify your pump with any variation unless you have determined that it is compatible with your application.The three.character trim code is designed as follows. The first character identifies any sealing variations, the second character identifies any internal variations, and the third character identifies any rotor variations.5The trim code “AAA” represents a pump with standard features. Deviations from standard are to be indicated by changing the appropriate character from the choices listed. When two or more letters are combined, dashes are used to separate the three areas of the trim code for clarity. SEALING VARIATIONSA — BRAIDED TEFLON & GRAPHITE PACKING,(Black) Standard to all lines except QuickDisassembly pumps. Optional on QuickDisassembly pumps.C — BRAIDED TEFLON PACKING, (White) Optionalpacking on all lines.D — DOUBLE MECHANICAL SEAL, Optional on alllines. Not offered on #2 “L” frame.F — BRAIDED TEFLON FOOD GRADE PACKING,(White) Standard on all Quick Disassembly pumps.Optional on all other lines.G — 100% GRAPHITE PACKING, (Gray) Optional to alllines.S — SINGLE MECHANICAL SEAL, Optional on all lines.W — WATER FLUSH, Optional on all lines.X — Special to application.INTERNAL VARIATIONSA — Standard plated shaftB — Non-plated shaftC — Solid drive shaft configurationD — Grit seal, for “L” frame onlyE — Extension tube with extended augerF — Extended drive shaft (for back stop or large pulley)G — Ceramic coatingS — Shaft sleeveX — Special to applicationROTOR VARIATIONSA — Standard size with chrome platingB — Non-plated (no plating)C — Standard undersizeE — Standard oversizeF — Counter clockwise rotation (Centennial line only)G — Ceramic coatingX — Special to applicationPACKING VARIATIONS listed are common to most type designations. Others may be specified by changing the last digit to the following:1 = Standard on all type CDQ pumps3 = Standard on all type CDR & SSR pumps5 = Standard on all type SSQ pumps7 = Optional--Solid Braided Teflon8 = Optional--Teflon Impregnated white asbestosDRIVESHAFTS shown have hard-chrome plating on thepacking wear area. If non-plated driveshafts are required,select the standard part number and change the last digit tonext higher number. Example: B06261 to B06262.L6 STANDARD HARDWAREITEM SIZE#REO.Bearing Cover Plate Screw 1L X 3/8D-16 4Lock Washer 4Packing Gland Stud 3 3/8LX 1/2D-14 2Nut2 Stator & Pump Support Screws 1 1/2L X 1/2D-13 4Suction Housing Bolts 2L X 1/2D-13 4Lock Washers 4Suction Housing Drain Plug 1/2 NPT 3Grease Fitting on Stuffing box 1/8 NPT 1Drain Plug on Stuffing Box 1/8 NPT 1Pipe Plug on Bearing Housing 1/8 NPT 1Hex Key 5/16 1RECOMMENDED SPARE PARTSThe Moyno pump has been designed and built with allwearable parts replaceable. A recommended inventory ofspare parts is dependent upon the application and importanceof continued operation.For the shortest possible down time, we recommend thefollowing parts be stocked:1 - Rotor1 - Stator1 - Connecting Rod KitThe above is only a suggested list. For further assistance indetermining what you’ll need for your application, contact yourMoyno representative.6© 1993 by Moyno, Inc.® Moyno is a registered trademark of Moyno, Inc. Moyno, Inc. is a Unit of Robbins & Myers, Inc. Teflon® is a registered trademark of DuPont。
Goulds Pumps安装、运行和维护手册- LF 3196 i-Frame说明书

安装、运行及维护手册ModΒιβλιοθήκη l LF 3196 i-FRAME
目录
目录
介绍与安装..........................................................................................................................................................................5 安全.....................................................................................................................................................................................5 安全警示等级...............................................................................................................................................................5 环境安全........................................................................................................................................................................5 用户健康与安全...........................................................................................................................................................6 易爆环境中防爆产品的安全规定...........................................................................................................................8 产品认证标准..................................................................................................................................................................9 CSA 合格证书................................................................................................................................................................10 产品保修.........................................................................................................................................................................12
viking齿轮泵说明书

部分 页码 期号
TSM 630.1 第 1 页 共 14 页 D
目录
特别须知 . . . . . . . . . . . . . . . . . . . . . . . . . 3 维护检修 . . . . . . . . . . . . . . . . . . . . . . . . . 3 机械密封泵 . . . . . . . . . . . . . . . . . . . . . . . . 4 集装式机械密封 . . . . . . . . . . . . . . . . . . . . . . 4 填料密封泵 . . . . . . . . . . . . . . . . . . . . . . . . 6 可选的转子后密封 . . . . . . . . . . . . . . . . . . . . 8 调节止推轴承 . . . . . . . . . . . . . . . . . . . . . . 10 安装碳石墨轴套 . . . . . . . . . . . . . . . . . . . . . 11 卸压阀操作说明 . . . . . . . . . . . . . . . . . . . . . 11
在将泵投入运行之前,请确保装好所有驱动部件的护 罩。
如果吸液或排液管道没有接好,请不要将泵投运行。
如果泵轴存在旋转的可能性,请不要将手指放入泵室、 泵室接口或驱动系的任何部分。
泵压、转速和温度不能超过额定值。在没有确定泵是 否适合新工况之前,请不要更改原来的系统(工况) 参数。
在将泵投入运行前,请确保: ● 泵干净整洁,无残渣。 ● 吸液口和排液口管道上的所有阀门处于全开状态。 ● 与泵相连的所有管道应支撑牢固。并且与泵正确对
viking pump使用手册

FEATURES① Pressure Range 250 PSI (17 BAR) for 100 SSU (20 cSt) and above 150 PSI (10 BAR) for 38 to 100 SSU (3 cSt to 20 cSt) 100 PSI (7 BAR) for below 38 SSU (3 cSt)① TemperatureRange- 40° F. to + 350°F. (- 40° C. to + 177°C.)① Viscosity Range 28 SSU to 15,000 SSU(0.1 cP to 3,300 cSt)GPM up to 75(M³/Hr up to 17)② (Nominal Rating)BALL BEARINGS(Standard Equipment) Pumps are equipped with inner cas-ing ball bearing installed outside of mechanical seal and a radial thrust ball bearing permitting heavy-duty service up to 250 PSI (17 BAR). Bearings are “Sealed for Life”.DUCTILE IRON PARTS(Standard Equipment)(“AS”, “AK”, “AL” Sizes) Internal pumping gears (rotor and idler) are constructed of ductile iron for added strength in handling all types of liquids up to 15,000 SSU (3,300 cSt). “HL” size rotor also furnished in ductile iron.PRESSURE LUBRICATION(Standard Equipment)(“AS”, “AK”, “AL” Sizes)A patented pressure lubrication system automatically lubricates the idler bushing. This system provides a constant film of liquid between the idler bushing and idler pin at a pre-ssure equal to the pump discharge pressure regardless of pump rotation.O-RING GASKETS(Standard Equipment)O-Ring gaskets are used between casing and head plate and between casing and relief valve or valve plates. Flat valve gaskets furnished on “G”, “GG”, “H”, “HJ” and “HL” size pumps. These gaskets provide a positive seal eliminating a chancefor leakage at these points.Viking’s high-speed, heavy-duty Series 4195 pumps are available in capacities up to 75 GPM. These pumps can be furnished directly connected to a 50 Hz or 60 Hz motor. (See Series 4195D units shown on page 144.3.) All eight sizes of Viking Series 4195 pumps are furnished with single mechanical seals. This seal is a simple self-adjusting, non-leak method of shaft sealing located ahead of the casing ball bearing. The Series 4195 pumps are built for con t inuous or intermittent duty for such applications as filtering, circulating, transferring, or booster service in general industrial, petroleum and marine uses. NOTE: “UL” listed pumps for handling flammable liquids require special construction. Externals are high strength cast iron. (Ductile Iron Casing on “AS”, “AK” and “AL” sizes). See Catalog Section 440 for details and pricing information. Model numbers for these pumps must be designated by a suffix -F, eg. GG4195-F or when used with a “D” drive, GG4195D-F. “UL” listed models must be equipped with either an internal or return-to-tank safety relief valve. Maximum discharge pressure for “UL” listed models is 125 PSIG.①Values shown represent minimums or maximums. Some special construc t ion orconsideration may be required before a cataloged pump can be ap p lied to an application involving maximum pressure or minimum or max i mum temperature and/or viscosity. Certain models have restrictions in pressures and/or viscosities.See specifications, page 144.2, and perform a nce curves.②Nominal capacities based on handling thin liquids.Metric conversions are based on US measurements and rounded to the nearest whole number.SERIES 4195 Pumps Cutaway View “G”, “GG”, “H”, “HJ”, “HL”SERIES 4195 Pumps Cutaway View“AS”, “AK”, “AL”UNMOUNTED PUMPSCONSTRUCTION — SERIES ① 4195 (“GG” THROUGH “AL” SIZES)SERIES 4195 Pumps“G”, “GG”, “H”, “HJ” and “HL” SizesSERIES 4195 Pumps“AS”, “AK” and “AL” SizesStandard Construction ModelsCasing Head RotorIdlerRotor Shaft and Idler PinIdler Bushing Internal Safety Relief ValveG4195 , GG4195H4195 , HJ4195Iron Iron ② Iron③ IronSteel Carbon Graphite Iron HL4195Iron Iron Ductile Iron Iron Steel Carbon Graphite Iron AS4195 , AK4195 , AL4195IronIronDuctile IronDuctile IronSteelCarbon GraphiteIron① Standard Buna-N seal from -20°F. to +225°F. (-29°C. to +107°C.) With specialconstruction, temperatures from -40°F. to +350°F. (-40°C. to +177°C.) can be handled with this series.② When steel fitted construction is required, “GG” will have steel rotor, “HJ” will have ductile iron rotor.③ “GG” size has steel idler.④ Nominal capacities based on handling thin liquids.⑤ For viscosities above 15,000 SSU (3,300 cSt), provide details for recommendations.⑥ These models have ductile iron rotors; steel fitted rotors not necessary. ⑦ If suction pressure exceeds 100 PSIG (7 BAR), consult factory.In addition to the famous features listed on the previous page, Series 4195 heavy-duty pumps are furnished with an integral relief valve as shown in the pump photos above. Return-to-tank valves are also available on all models on request. Note: On the “G”, “GG”, “H”, “HJ” and “HL” sizes, the valve mounts on the pump head. The “AS”, “AK” and “AL” size value mounts on top of the pump casing. All sizes equipped with Buna-N mechanical seal with carbon rotating and Ni-Resist stationary faces.Dimensions for Unmounted Pumps—See Page 144.6.Performance Data for Unmounted Pumps—See Pages 144.13 through 144.26.MECHANICAL SEAL ① Buna-N bellows.② Buna-N O-ring.③ Carbon rotating face (washer).④ Ni-Resiststationary seat.⑤ Steel metal parts.⑥ Stainless steel spring.Metric conversions are based on US measurements and roundedDIRECT DRIVE UNITS (“D” DRIVE)① Nominal capacities based on handling thin liquids.② With special construction, temperatures to + 350°F . (177°C.) can be handled withthis series.③ For viscosities above 15,000 SSU (3,300 cSt), provide details for recommendations.④ These models have ductile iron rotors; steel fitted rotors not necessary.⑤ If suction pressure exceeds 100 PSIG (7 BAR), consult factory.SERIES 4195 Pumpswith “D” Drive“AS”, “AK” and “AL” SizesSeries 4195 pumps in the “G”, “GG”, “H”, “HJ” and “HL” size are designed for high-speed, heavy-duty service. The pump is connected by a flexible coupling with guard directly to a 50 Hz or 60 Hz motor. See series 4195D chart below. Both pump and motor mount on a sturdy formed steel base. This makes a very compact, rugged unit for heavy-duty ser v ice, handling many types of fluids up to 15,000 SSU (3,300 cSt).The three large size Series 4195D direct connected units all feature the 4195 high-speed pump connected by a flexible coupling with guard to 50 Hz or 60 Hz motor. See chart below. Both pump and motor are mounted on a heavy-duty formed steel base. The three larger sizes are equipped with ductile iron pump gears (rotor and idler). O-Ring head and valve gaskets, mechanical seals and automatic pressure lubrication systems are also standard construction. These pumps are also available with steel externals, see Section 154.Dimensions for “D” Drive—See Page 144.7.Performance Data for “D” Drive—See Pages 144.13 through 144.26.SERIES 4195 Pumpswith “D” Drive“G”, “GG”, “H”, “HJ” and “HL” SizesMetric conversions are based on US measurements and roundedSPECIFICATIONS — “D” DRIVE UNITSSERIES 495 Pumps“AS”, “AK” and “AL” SizesCONSTRUCTION — SERIES ⑤ 495 (“GG” THROUGH “AL” SIZES)SPECIFICATION — UNMOUNTED PUMPSStandard Construction Models Mounting Bracket (Units Only)Casing Head Rotor Idler Rotor Shaft and Idler PinIdler Bushing Internal Safety Relief ValveG495 , GG495H495 , HJ495Iron Iron Iron ⑥ Iron ⑦ Iron Steel Carbon Graphite Iron HL495Iron Iron Iron Ductile Iron Iron Steel Carbon Graphite Iron AS495 , AK495 , AL495IronIronIronDuctile IronDuctile IronSteelCarbon GraphiteIronGPM up to 75 (M ³/Hr up to 17)④ (Nominal Rating)Series 495 pumps are similar to the Series 4195 on preceding pages with the exception of a flange bracket mount casing.All eight sizes are furnished with single mechanical seals, including Buna-N elastomer gaskets.Standard construction features internal type safety relief valve on pump head or casing (depending on pump size), O-Ring head and valve gaskets, and automatic pressure lubrication system on the three larger size pumps.The 495 series offers an optional flange port for sizes H-AL. Contact the factory for details.Dimensions for Unmounted Pumps—See Page 144.8.Performance Data for Unmounted Pumps—See Pages 144.13 through 144.26.SERIES 495 Pumps“G”, “GG”, “H”, “HJ” and “HL” SizesFLANGE BRACKET UNMOUNTED PUMPSMetric conversions are based on US measurements and rounded ① Pressure Range 250 PSI (17 BAR) for 100 SSU (20 cSt) and above 150 PSI (10 BAR) for 38 to 100 SSU (3 cSt to 20 cSt)100 PSI (7 BAR) for below 38 SSU (3 cSt)① Temperature Range - 40° F. to + 350°F. (- 40° C. to + 176°C.)① Viscosity Range28 SSU to 15,000 SSU(0.1 cP to 3,300 cSt)① Consult factory for specific recommendations.② Standard Buna-N seal from -20°F. to +225°F. (-29°C. to +107°C.) With special construction, temperatures from -40°F. to +350°F. (-40°C. to +177°C.) can be handled with this series.③ For viscosities above 15,000 SSU (3,300 cSt), provide details for recommendations.④ Nominal capacities based on handling thin liquids.⑤ Buna-N elastomer used in mechanical seal of Series 495 pumps.⑥ When steel fitted construction is required, “GG” will have steel rotor, “HJ” will have ductile iron rotor.⑦ “GG” size has steel idler.⑧ These models have ductile iron rotors; steel fitted rotors not necessary. ⑨ If suction pressure exceeds 100 PSIG (7 BAR), consult factory.① Nominal capacities based on handling thin liquids.② With special construction, temperatures to + 350°F . (177°C.) can be handled with thisseries.③ For viscosities above 15,000 SSU (3,300 cSt), provide details for recommendations.④ These models have ductile iron rotors; steel fitted rotors not necessary.⑤ If suction pressure exceeds 100 PSIG (7 BAR), consult factory.FLANGE BRACKET MOUNTED UNITS (“M” DRIVE)SPECIFICATIONS — “M” DRIVE UNITSFor a compact horizontal mounting, the face mounted 495M heavy-duty pump units in all eight sizes in c lude a combination motor “C ” flange and square pump flange bracket with coupling connecting motor and pump.The three larger size pumps are equipped with ductile iron pump gears (rotor and idler) and automatic pressure lubrication system. All sizes have O-Ring head and valve gaskets and mechanical seals as standard construction. These pumps are also available with steel externals, see Section 154.Dimensions for “M” Drive—See Page 144.9 and 144.10.Performance Data for “M” Drive—See Pages 144.13 through 144.26.SERIES 495 Pumpswith “M” Drive“AS”, “AK” and “AL” SizesSERIES 495 Pumpswith “M” Drive“G”, “GG”, H”, “HJ” and “HL” SizesMetric conversions are based on US measurements and roundedMODELNO.A B D E F G H J K L M N O P S T U V W X Y ZAS4195in2½5.00 5.25 2.88 2.006.75 4.00.41 2.25 1.25 1.00 2.00.44 1.1212.12 2.50 1.000.25 x .127.00.50 1.00 1.72 mm1271337351171102105732255111293086025.40 6.35 x 3.181********AK4195in2½5.00 5.25 2.88 2.006.75 4.00.41 2.25 1.25 1.00 2.00.44 1.1212.12 2.50 1.000.25 x .127.00.50 1.00 1.72 mm1271337351171102105732255111293086025.40 6.35 x 3.181********AL4195in35.00 5.25 2.88 2.006.75 4.00.41 2.25 1.75 1.00 2.50.44 1.1212.12 2.50 1.000.25 x .127.00.50 1.00 1.72 mm1271337351171102105744256411293086025.40 6.35 x 3.181********For specifications, see page 144.2.DIMENSIONS—SERIES 4195UNMOUNTED PUMPS“AS”—“AK”—“AL” SIZESMODEL NO.A B D E F G H J K L M N O P S T U V W XG4195 GG4195in12.75 2.75 1.62 1.31 4.00 2.44.34.94.03.66 1.12.31.627.31 1.12.500FLAT2.66.38 mm7070413310262924117298161862912.706710H4195 HJ4195 HL4195in1½3.754.12 1.75 2.005.00 3.50.41 1.50 1.25.88 1.50.44.6210.00 1.62.750.19 x .09 3.28.75 mm95105445112789103832223811162544119.05 4.76 x 2.388319For specifications, see page 144.2.DIMENSIONS—SERIES 4195UNMOUNTED PUMPS“G”—“GG”—“H”—“HJ”—“HL”SIZESDIMENSIONSThese dimensions are average and not for construction purposes. Certified prints on request.DIMENSIONSThese dimensions are average and not for construction purposes. Certified prints on request.MODEL NO.A B D E F H J K L M M1N P SG4195D GG4195Din12.75①3.50 1.5020.50.75.758.50.38 3.78.62.624.25 mm708938445191921610961613108 in12.75②3.50 1.5020.50.75.758.50.38 3.78.62.624.25 mm708938521191921610961613108H4195D HJ4195D HL4195Din1½3.75③4.12⑦2.1220.50.75.758.500 4.78.62.62 4.25 mm9511454521191921601211613108 in1½3.75④4.12 2.9429.00 1.00 1.509.00.25 4.78.62.62 4.50 mm9511475635253822961211614114 in1½3.75⑤5.25 2.9429.00 1.00 1.509.00.25 4.78.62.62 4.50 mm9513375635253822961211614114AS4195D AK4195D AL4195Din2½5.00④4.50⑧3.6929.00 1.00 1.509.0007.00 1.12.624.50 mm12711494660253822901782914114 in2½5.00⑤5.25 2.9429.00 1.00 1.509.0007.00 1.12.62 4.50 mm12713375737253822901782914114 in35.00⑥6.25 4.0039.00 1.38 1.3816.00 3.757.00 1.12.628.00 mm1271591029913535406951782916203For specifications, see page 144.3.DIMENSIONS—SERIES 4195(“D” DRIVE)“G”—“GG”—“H”—“HJ”—“HL”—“AS”—“AK”—“AL” SIZES① 56 frame motors (short base). (Available with “G” & “GG”size pumps.)② 143T and 145T frame motors (long base). (Availablewith “G” & “GG” size pumps.)③ 56, 143T and 145T frame motors. (Available with “H”,“HJ” or “HL” size pumps.)④ 182, 182T, 184, 184T frame motors. (Available with“H” through “AL” size pumps.)⑤ 213, 213T, 215, 215T frame motors. (Available with“H” through “AL” size pumps.)⑥ 254U, 254T, 256U, 256T frame motors. (Availablewith “AK” through “AL” size pumps.)⑦ Dimensions includes motor block, base height is 1½”.⑧ Dimension includes motor block, base height is 2 ¹⁵⁄₁₆”. NOTE: All “AS”, “AK”, “AL” pump sizes available with anyof the three motors shown in columns.MODEL NO.A B C E F G H J K L P R S T U V W X Y ZAS495AK495in2½5.008.384.756.25.56.752.005.75.752.254.2504.24812.12 2.50 1.000.25 x .127.001.121.00 1.72mm21351AL495in 38.88 2.50mm12722512115914196414622571083086425.406.35 x 3.18178292540MODEL NO.A B C E F G H J K N P R T U V X G495GG495in12.752.663.004.00.41.50 3.44 2.81 1.12.94 2.8752.873 1.12.500FLAT.62mm 706776102101387712924732912.7016H495HJ495HL495in1½3.75 3.284.755.88.56.75 4.50 4.00 1.50 1.50 3.8753.873 1.62.750.19 x .09.62mm 958312114914191141023838984119.054.76 x 2.3816For specifications, see page 144.4.DIMENSIONS—SERIES 495UNMOUNTED PUMPS “AS”—“AK”—“AL” SIZESDIMENSIONSThese dimensions are average and not for construction purposes. Certified prints on request.For specifications, see page 144.4.DIMENSIONS—SERIES 495UNMOUNTED PUMPS“G”—“GG”—“H”—“HJ”—“HL”SIZESDIMENSIONSThese dimensions are average and not for construction purposes. Certified prints on request.MODEL NO.A B C J L M NMOTOR FRAMED EFGH KG495M GG495Min 12.75 2.663.44.62.19 1.1256C 3.502.44 1.50 2.568.88.34 SLOTmm 6238659in143TC 2.752.00 2.88.34mm 51in 145TC 2.50mm 897064732259in 182TC 4.503.75 2.25 3.389.56.41mm 57in 184TC 2.75mm 7067871652911495708624310H495M HJ495M HL495Min 1½3.75 3.284.50.62.19 1.5056C 3.502.44 1.50 2.5611.12.34 SLOTmm 6238659in 143TC 2.752.00 2.88.34mm51in 145TC2.50mm 897064732839in 182TC 4.503.75 2.25 3.3811.81.41mm 57in 184TC 2.75mm 11495708630010in 213TC 5.254.25 2.75 4.2512.56.41mm 70in 215TC3.50mm9583114165381331088910831910MODEL NO.A B①C D E F G H J K➀LM N O P R S YAS495M in 2½5.0019.066.25 2.757.00 5.007.00 1.00.568.44 6.382.00.50 1.127.00.19 1.00AK495M mm 48451AL495Min 319.562.50mm127497159701781271782514214162641329178525For specifications, see page 144.5.DIMENSIONS—SERIES 495(“M” DRIVE) — NEMA C “AS”—“AK”—“AL” SIZES① Dimensions are correct for 182TC through 215TCmotors. For 254TC/256TC motors, add .88” to the dimensions shown.NOTE: Jaw type coupling with straight jaws recommended to facilitate assembly of motor and pump to bracket.COUPLING IS GUARDED WITH PLATES OVER SIDE OPENINGS ON MOUNTING BRACKET.For specifications, see page 144.5.DIMENSIONS—SERIES 495(“M” DRIVE) — NEMA C“G”—“GG”—“H”—“HJ”—“HL” SIZESNOTE: Jaw type coupling with straight jaws recommended to facilitate assembly of motor and pump to bracket.COUPLING IS GUARDED WITH PLATES OVER SIDEOPENINGS ON MOUNTING BRACKET.。
SG-051010-G0美国VIKING威肯齿轮泵技术参数

SG-051010-G0美国VIKING威肯齿轮泵技术参数SG-051010-G0美国VIKING威肯齿轮泵技术参数VIKING齿轮泵SG04 VIKING齿轮泵SG05 VIKING齿轮泵SG07美国VIKING威肯齿轮泵SG-051010-G0进口现货,此品牌的询价都需要提供铭牌,因为有些是带了安全阀,有些没有带安全阀的,查序列号SN就可以知道。
SG-051010-G0美国VIKING威肯齿轮泵技术参数Viking直齿轮单泵系列SG-04、SG-05和SG-07正在成为低容量、高速和高压输送应用的工业选择。
这些系列的泵在紧凑型抽油机。
通过精密加工和优质部件的使用,Viking直齿轮单泵提供安静、低波纹的流量,以满足工业需要。
SG-04、SG-05和SG-07系列固定排量直齿轮单泵的设计使容量以40%的均匀增量增加,因此Viking正齿轮单泵始终在您容量需求的20%以内。
显示的值表示z小值或z大值。
在编目泵应用于涉及z大压力或z低或z高温度和/或粘度的应用之前,可能需要一些特殊结构或考虑事项。
某些型号在压力和/或粘度方面有限制。
见规范第341.2页和性能曲线,第341.19至341.66页。
额定容量基于1750 RPM低压下处理稀液体。
SG-04、SG-05和SG-07系列正齿轮单泵可提供未安装或已安装的装置,如下页所示。
Viking正齿轮单泵可提供多种密封选项和驱动设备,以满足特定需求。
VIKING填料密封常备货型号:SG-0417 SG-40417SG-0418 SG-40418SG-0425 SG-40425SG-0435 SG-40435SG-0450 SG-40450SG-0470 SG-40470SG-0518 SGN-0518SG-0525 SGN-0525SG-0535 SGN-0535SG-0550 SGN-0550SG-0570 SGN-0570SG-0510 SGN-0510SG-0514 SGN-0514SG-0519 SGN-0519SG-0528 SGN-0528SG-0729 SGN-0729SG-0741 SGN-0741SG-0758 SGN-0758SG-0782 SGN-0782SG-0711 SGN-0711SG-0716 SGN-0716SG-0722 SGN-0722SG-0732 SGN-0732VIKING机械密封常备货型号:SG-40417SG-40418SG-40425SG-40435SG-40450SG-40470SG-40518 SGN-40518SG-40525 SGN-40525SG-40535 SGN-40535SG-40550 SGN-40550SG-40570 SGN-40570SG-40510 SGN-40510SG-40514 SGN-40514SG-40519 SGN-40519SG-40528 SGN-40528SG-40729 SGN-40729SG-40741 SGN-40741SG-40758 SGN-40758SG-40782 SGN-40782SG-40711 SGN-40711SG-40716 SGN-40716SG-40722 SGN-40722SG-40732 SGN-40732VIKING驱动器选项:四螺栓电机安装装置(“M4”驱动):提供SG-04或SG-05系列整体式泵和电机装置。
WILDEN PUMP使用手册
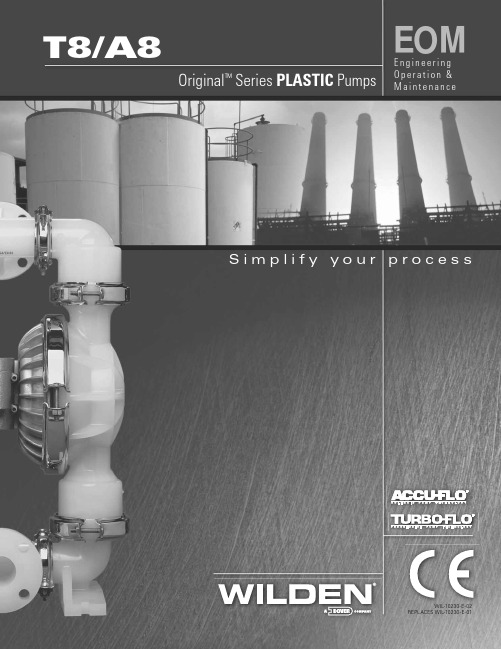
EOMWIL-10230-E-02REPLACES WIL-10230-E-01TABLE OF CONTENTSPAGE # SECTION 1 — CAUTIONS (1)SECTION 2 — PUMP DESIGNATION SYSTEM (2)SECTION 3 — HOW IT WORKS (PUMP & AIR SYSTEMS) (3)SECTION 4 — DIMENSIONAL DRAWINGSA. T8 PLASTIC Air-Controlled (4)B. A8 PLASTIC Accu-Flo™ (4)SECTION 5 — PERFORMANCE CURVESA. T8 PLASTIC Rubber-Fitted (5)B. T8 PLASTIC Ultra-Flex™-Fitted (5)C. T8 PLASTIC TPE-Fitted (6)D. T8 PLASTIC PTFE-Fitted (6)E. A8 PLASTIC Accu-Flo™ Rubber/TPE-Fitted (7)F. A8 PLASTIC Accu-Flo™ Rubber/TPE-Fitted 70/30 Operating Condition (7)G. A8 PLASTIC Accu-Flo™ Ultra-Flex™/PTFE-Fitted (8)H. A8 PLASTIC Accu-Flo™ Ultra-Flex™/PTFE-Fitted 70/30 Operating Condition (8)SECTION 6 — SUCTION LIFT CURVES & DATAA. T8 PLASTIC Air-Controlled (9)B. A8 PLASTIC Accu-Flo™ (9)SECTION 7 — INSTALLATION & OPERATIONA. Installation — Air-Controlled Pumps (10)B. Air-Controlled Operation and Maintenance (11)C. Accu-Flo™ Operating Principles (12)D. Installation — Accu-Flo™ Pumps (12)E. Accu-Flo™ Operation and Maintenance (13)F. Troubleshooting Air-Operated Pumps (14)G. Troubleshooting Accu-Flo™ Pumps (14)SECTION 8 — DIRECTIONS FOR DISASSEMBLY/REASSEMBLYA. T8 PLASTIC Wetted Path — Tools Required (15)B. Turbo-Flo™ Air Valve — Disassembly, Cleaning, Inspection (18)C. Reassembly Hints & Tips, Torque Specs (20)D. Gasket Kit Installation (21)SECTION 9 — EXPLODED VIEW/PARTS LISTINGA. T8 PLASTIC Rubber/TPE-Fitted (22)B. T8 PLASTIC PTFE-Fitted (24)C. A8 PLASTIC Accu-Flo™ (26)SECTION 10 — REFERENCE (28)A. ElastomerOptionsB. Accu-Flo™ Electrical Information (28)SECTION 1T8 PLASTICCAUTIONS – READ FIRST!TEMPERATURE LIMITS:Polypropylene 0°C to 79°C 32°F to 175°FPVDF –12°C to 107°C 10°F to 225°FNeoprene –17.8°C to 93.3°C 0°F to 200°FBuna-N –12.2°C to 82.2°C 10°F to 180°FEPDM –51.1°C to 137.8°C –60°F to 280°F Viton®–40°C to 176.7°C –40°F to 350°F Wil-Flex™ –40°C to 107.2°C –40°F to 225°FPolyurethane 12.2°C to 65.6°C 10°F to 150°FSaniflex™ –28.9°C to 104.4°C –20°F to 220°FPTFE 4.4°C to 104.4°C 40°F to 220°FT etra-Flex™ PTFE 4.4°C to 107.2°C 40°F to 225°F W/NeopreneT etra-Flex™ PTFE -10°C to 137°C 14°F to 280°F W/EPDMT etra-Flex™ PTFE 4.4°C to 176.6°C 40°F to 350°FCAUTION: When choosing pump materials, be sureto check the temperature limits for all wetted compo-nents. Example: Viton® has a maximum limit of 176.7°C(350°F) but polypropylene has a maximum limit of only79°C (175°F).CAUTION: Maximum temperature limits are basedupon mechanical stress only. Certain chemicals willsignificantly reduce maximum safe operating tempera-tures. Consult engineering guide for chemical compat-ibility and temperature limits.CAUTION:Always wear safety glasses when operat-ing pump. If diaphragm rupture occurs, material beingpumped may be forced out air exhaust.WARNING: Prevention of static sparking — If staticsparking occurs, fire or explosion could result. Pump,valves, and containers must be properly grounded whenhandling flammable fluids and whenever discharge ofstatic electricity is a hazard.CAUTION:Do not exceed 8.6 bar (125 psig) air supplypressure.CAUTION:Before any maintenance or repair is attempted, the compressed air line to the pump shouldbe disconnected and all air pressure allowed to bleedfrom pump. Disconnect all intake, discharge and airlines. Drain the pump by turning it upside down andallowing any fluid to flow into a suitable container. CAUTION: Blow out air line for 10 to 20 seconds before attaching to pump to make sure all pipe line debris is clear. Use an in-line air filter. A 5µ (micron) air filter is recommended.NOTE:When installing PTFE diaphragms, it is impor-tant to tighten outer pistons simultaneously (turning in opposite directions) to ensure tight fit.NOTE: Tighten clamp bands and retainers prior to installation. Fittings may loosen during transportation. NOTE: Before starting disassembly, mark a line from each liquid chamber to its corresponding air chamber. This line will assist in proper alignment during reas-sembly.CAUTION: Verify the chemical compatibility of the process and cleaning fluid to the pump’s component materials in the Chemical Resistance Guide (see E4). NOTE: Pastic series pumps are made of virgin plastic and are not UV stabilized. Direct sunlight for prolonged periods can cause deterioration of plastics. CAUTION:When removing the end cap using compressed air, the air valve end cap may come out with considerable force. Hand protection such as a padded glove or rag should be used to capture the end cap.CAUTION: Only explosion proof (NEMA 7) solenoid valves should be used in areas where explosion proof equipment is required.NOTE:Non lube-free pumps must be lubricated. Wilden suggests an arctic ISO grade 15 (5 weight oil). Do not over-lubricate air supply. Over-lubrication will reduce pump performance.1WILDEN PUMP & ENGINEERING, LLC WIL-10230-E-022WILDEN PUMP & ENGINEERING, LLCWIL-10230-E-02SECTION 2NOTE: MOST ELASTOMERIC MATERIALS USE COLORED DOTS FOR IDENTIFICATION.Viton is a registered trademarks of DuPont Dow Elastomers.0100 Wil-Gard II™ 110V0102 Wil-Gard II™, sensor wires ONLY 0103 Wil-Gard II™ 220V0145 Accu-Flo™, 110V AC x-proof coil, Wil-Gard II™ 110V 0150 Accu-Flo™, 24V DC coil0151 Accu-Flo™, 24V AC / 12V DC coil0153 Accu-Flo™, 24V AC / 12V DC x-proof coil 0154 Accu-Flo™, 24V DC x-proof coil 0155 Accu-Flo™, 110V AC coil0156 Accu-Flo™, 110V AC x-proof coil0157 Accu-Flo™, 24V DC coil, international,PTB approved0164 Accu-Flo™, 110V AC coil,Wil-Gard sensor wires only0167 Accu-Flo™ 24V AC / 12V DC coil,Wil-Gard II™ 110V0168 Accu-Flo™, 110V AC coil, Wil-Gard II™ 110V 0169 Accu-Flo™, 110V AC coil, PFA coated hardware 0170 Accu-Flo™, 110V AC x-proof coil,PFA coated hardware0180 Accu-Flo™, 24V AC / 12V DC coil,PFA coated hardware0181 Accu-Flo™, 24V AC / 12V DC x-proof coil,PFA coated hardware0183 Accu-Flo™, 24V AC / 12V DC x-proof coil,Wil-Gard II™ 110V0184 Accu-Flo™, 24V DC coil, PFA coated hardware 0185 Accu-Flo™, 24V DC x-proof coil,PFA coated hardware 0206 PFA coated hardware,Wil-Gard II™ sensor wires ONLY 0360 Accu-Flo™, 24V DC coil, DIN flange0362 Accu-Flo™, 110V AC coil, PFA coated hardware,Wil-Gard II™ 110V0363 Accu-Flo™, 110V AC coil, Stallion ® internals(balls & seats)0502 PFA coated hardware 0513 SS outer pistons 0560 Split manifold0561 Split manifold, PFA coated hardware 0563 Split manifold, discharge ONLY 0564 Split manifold, inlet ONLY0608 PFA coated hardware, Wil-Gard II™ 220V 0660 Split manifold, Wil-Gard II™ 110V 0661 Split manifold, PFA coated hardware,Wil-Gard II™ 110V3WILDEN PUMP & ENGINEERING, LLCWIL-10230-E-02SECTION 3THE WILDEN PUMP — HOW IT WORKSThe Wilden diaphragm pump is an air-operated, positive displacement, self-priming pump. These drawings show the flow pattern through the pump upon its initial stroke. It is assumed the pump has no fluid in it prior to its initial stroke.FIGURE 1 The air valve directs pres-surized air to the back side of diaphragm A. The compressed air is applied directly to the liquid column separated by elas-tomeric diaphragms. The diaphragm acts as a separation membrane between the compressed air and liquid, balanc-ing the load and removing mechani-cal stress from the diaphragm. The compressed air moves the diaphragm away from the center block of the pump. The opposite diaphragm is pulled in by the shaft connected to the pressur-ized diaphragm. Diaphragm B is on its suction stroke; air behind the diaphragm has been forced out to the atmosphere through the exhaust port of the pump. The movement of diaphragm B toward the center block of the pump creates a vacuum within chamber B. Atmospheric pressure forces fluid into the inlet mani-fold forcing the inlet valve ball off its seat. Liquid is free to move past the inlet valve ball and fill the liquid chamber (see shaded area).FIGURE 2 When the pressurized diaphragm, diaphragm A, reaches the limit of its discharge stroke, the air valve redirects pressurized air to the back side of diaphragm B. The pressurized air forces diaphragm B away from the center block while pulling diaphragm A to the center block. Diaphragm B is now on its discharge stroke. Diaphragm B forces the inlet valve ball onto its seat due to the hydraulic forces developed in the liquid chamber and manifold of the pump. These same hydraulic forces lift the discharge valve ball off its seat, while the opposite discharge valve ball is forced onto its seat, forcing fluid to flow through the pump discharge. The move-ment of diaphragm A toward the center block of the pump creates a vacuum within liquid chamber A. Atmospheric pressure forces fluid into the inlet mani-fold of the pump. The inlet valve ball is forced off its seat allowing the fluid being pumped to fill the liquid chamber.FIGURE 3 At completion of the stroke, the air valve again redirects air to the back side of diaphragm A, which starts diaphragm B on its exhaust stroke. As the pump reaches its original starting point, each diaphragm has gone through one exhaust and one discharge stroke. This constitutes one complete pump-ing cycle. The pump may take several cycles to completely prime depending on the conditions of the application.RIGHT STROKEMID STROKE LEFT STROKEINLETAIR SUPPL YAB INLET AIR SUPPL YAB CLOSEDINLETAIR SUPPL YAB4WILDEN PUMP & ENGINEERING, LLCWIL-10230-E-02SECTION 4ADIMENSIONAL DRAWINGT8 PLASTIC19 mm (3/4")FNPTAIR EXHAUSTSECTION 4BDIMENSIONAL DRAWINGA8 PLASTIC ACCU-FLO™DIMENSIONSITEM METRIC (mm)STANDARD (inch)A 49019.3B 76 3.0C 69327.3D 77030.3E 44717.6F 89 3.5G 34513.6H 33313.1J 38615.2K 30712.1L 2299.0M 25410.0N 150.6DIN (mm)ANSI (inch)P 125 DIA. 4.8 DIA.R 165 DIA. 6.0 DIA.S18 DIA.0.8 DIA.DIMENSIONSITEM METRIC (mm)STANDARD (inch)A 49019.3B 76 3.0C 40916.1D 69327.3E 77030.3F 89 3.5G 34513.6H 33313.1J 86 3.4K 38615.2L 30712.1M 2299.0N 25410.0P 150.6DIN (mm)ANSI (inch)R 125 DIA. 4.8 DIA.S 165 DIA. 6.0 DIA.T18 DIA.0.8 DIA.SECTION 5APERFORMANCE CURVEST8 PLASTIC RUBBER-FITTEDHeight ..................................770 mm (30.3”)Depth ..................................333 mm (13.1”)Est. Ship Weight ........Polypropylene 35 kg (77 lbs)Air Inlet ....................................19 mm (3/4”)Inlet ............................................51 mm (2”)Outlet .........................................51 mm (2”)Suction Lift ..........................2.7 m Dry (9.0’)9.5 m Wet (31.0’)Displacement / Stroke ...... 2.84 l (0.75gal.)1Max. Flow Rate ...............579 lpm (153 gpm)Max. Size Solids .....................6.4 mm (1/4”)1Displacement per stroke was calculated at 4.8 bar(70 psig) air inlet pressure against a 2 bar (30 psig)head pressure.Example: To pump 303 lpm (80 gpm) againsta discharge pressure head of 2 bar (30 psig)requires 4.1 bar (60 psig) and 80 Nm3/h (47scfm) air consumption. (See dot on chart.)Caution: Do not exceed 8.6 bar (125 psig) airsupply pressure.Flow rates indicated on chart were determined by pumping water.For optimum life and performance, pumps should be specified so that daily operation p arameterswill fall in the center of the pump performance curve.SECTION 5BPERFORMANCE CURVEST8 PLASTIC UL TRA-FLEX™-FITTEDHeight ..................................770 mm (30.3”)Depth ..................................333 mm (13.1”)Est. Ship Weight ........Polypropylene 35 kg (77 lbs)Air Inlet ....................................19 mm (3/4”)Inlet ............................................51 mm (2”)Outlet .........................................51 mm (2”)Suction Lift ...........................3.4 m Dry (11’)9.1 m Wet (30’)Displacement / Stroke ..... 1.74 l (0.46 gal.)1Max. Flow Rate ...............556 lpm (147 gpm)Max. Size Solids .....................6.4 mm (1/4”)1Displacement per stroke was calculated at 4.8 bar(70 psig) air inlet pressure against a 2 bar (30 psig)head pressure.Example: To pump 303 lpm (80 gpm) againsta discharge pressure head of 2 bar (30 psig)requires 4.1 bar (60 psig) and 82 Nm3/h (48scfm) air consumption. (See dot on chart.)Caution: Do not exceed 8.6 bar (125 psig) airsupply pressure.Flow rates indicated on chart were determined by pumping water.For optimum life and performance, pumps should be specified so that daily operation p arameterswill fall in the center of the pump performance curve.5WILDEN PUMP & ENGINEERING, LLC WIL-10230-E-02SECTION 5CPERFORMANCE CURVEST8 PLASTIC TPE-FITTEDHeight ..................................770 mm (30.3”)Depth ..................................333 mm (13.1”)Est. Ship Weight ........Polypropylene 35 kg (77 lbs)Air Inlet ....................................19 mm (3/4”)Inlet ............................................51 mm (2”)Outlet .........................................51 mm (2”)Suction Lift ...........................4.6 m Dry (15’)9.5 m Wet (31’)Displacement / Stroke ..... 2.91 l (0.77 gal.)1Max. Flow Rate ...............591 lpm (156 gpm)Max. Size Solids .....................6.4 mm (1/4”)1Displacement per stroke was calculated at 4.8 bar(70 psig) air inlet pressure against a 2 bar (30 psig)head pressure.Example: To pump 322 lpm (85 gpm) againsta discharge pressure head of 2 bar (30 psig)requires 4.1 bar (60 psig) and 85 Nm3/h (50scfm) air consumption. (See dot on chart.)Caution: Do not exceed 8.6 bar (125 psig) airsupply pressure.Flow rates indicated on chart were determined by pumping water.For optimum life and performance, pumps should be specified so that daily operation p arameterswill fall in the center of the pump performance curve.SECTION 5DPERFORMANCE CURVEST8 PLASTIC PTFE-FITTEDHeight ..................................770 mm (30.3”)Depth ..................................333 mm (13.1”)Est. Ship Weight ........Polypropylene 35 kg (77 lbs)Air Inlet ....................................19 mm (3/4”)Inlet ............................................51 mm (2”)Outlet .........................................51 mm (2”)Suction Lift ...........................3.1 m Dry (10’)9.5 m Wet (31’)Displacement / Stroke ...... 1.51 l (0.40 gal)1Max. Flow Rate ...............458 lpm (121 gpm)Max. Size Solids .....................6.4 mm (1/4”)1Displacement per stroke was calculated at 4.8 bar(70 psig) air inlet pressure against a 2 bar (30 psig)head pressure.Example: To pump 265 lpm (70 gpm) againsta discharge pressure head of 2 bar (30 psig)requires 4.1 bar (60 psig) and 93.5 Nm3/h (55 scfm) air consumption. (See dot onchart.)Caution: Do not exceed 8.6 bar (125 psig) airsupply pressure.Flow rates indicated on chart were determined by pumping water.For optimum life and performance, pumps should be specified so that daily operation p arameterswill fall in the center of the pump performance curve.6WILDEN PUMP & ENGINEERING, LLC WIL-10230-E-027WILDEN PUMP & ENGINEERING, LLCWIL-10230-E-02SECTION 5EPERFORMANCE CURVESA8 PLASTIC ACCU-FLO™RUBBER/TPE-FITTEDHeight ..................................770 mm (30.3”)Width ...................................490 mm (19.3”)Depth ..................................333 mm (13.1”)Est. Ship Weight ........Polypropylene 34 kg (75 lbs)PVDF 43 kg (95 lbs)Air Inlet ....................................19 mm (3/4”)Inlet ............................................51 mm (2”)Outlet .........................................51 mm (2”)Suction Lift ...........................6.1 m Dry (20’)8.5 m Wet (28’)Displacement / Stroke ..... 0.55 gal. (2.08 l)1Max. Flow Rate ...............420 lpm (111 gpm)Max. Size Solids .....................6.4 mm (1/4”)1Displacement per stroke was calculated at 4.8 bar (70 psig) air inlet pressure against a 2 bar (30 psig) head pressure.Example: To pump 197 lpm (52 gpm) against a discharge pressure head of 2.7 bar (40 psig) requires 5.5 bar (80 psig) inlet air pressure, 68 Nm 3/h (40 scfm) air consumption and a pump speed of 108 strokes/minute. (See dot on chart.)Caution: Do not exceed 8.6 bar (125 psig) air supply pressure.Flow curves are for “optimal speed” conditions only. The “optimal speed” is that speed which provides the maximum flow under a particular air and fluid pressure condition. The optimal speed varies for different fluid and air pressures. Recommendations for optimal speed can be found on the right side of the flow curve.Flow rates indicated on chart were determined by pumping water.For optimum life and performance, pumps should be specified so that daily operation p arameters will fall in the center of the pump performance curve.Note: TPE suction lift is approximately half that of rubber-fitted.SECTION 5F70/30 OPERATING CONDITIONA8 PLASTIC ACCU-FLO™RUBBER/TPE-FITTEDA8 Plastic Accu-Flo™ Rubber / TPE-Fitte d@ 70 / 30 operating condition10203040506070S p e e d20406080100120140160180200220GPM [LPM][114][151][189][38][76][227][265]SPM Water Discharge Flow RateThis curve demonstrates the flow created when the stroke rate is modi-fied under a static air and fluid pres-sure condition. This curve can be applied to different pressure conditions to estimate the change in flow due to stroke rate.8WILDEN PUMP & ENGINEERING, LLCWIL-10230-E-02SECTION 5H70/30 OPERATING CONDITIONA8 PLASTIC ACCU-FLO™UL TRA-FLEX™-PTFE-FITTEDSECTION 5GPERFORMANCE CURVESA8 PLASTIC ACCU-FLO™UL TRA-FLEX™/PTFE-FITTEDHeight ..................................770 mm (30.3”)Width ...................................490 mm (19.3”)Depth ..................................333 mm (13.1”)Est. Ship Weight ........Polypropylene 34 kg (75 lbs)PVDF 43 kg (95 lbs)Air Inlet ....................................19 mm (3/4”)Inlet ............................................51 mm (2”)Outlet .........................................51 mm (2”)Suction Lift ...........................3.4 m Dry (11’)8.5 m Wet (28’)Displacement / Stroke ..... 1.74 l (0.46 gal.)1Max. Flow Rate ...............386 lpm (102 gpm)Max. Size Solids .....................6.4 mm (1/4”)1Displacement per stroke was calculated at 4.8 bar (70 psig) air inlet pressure against a 2 bar (30 psig) head pressure.Example: To pump 189 lpm (50 gpm) against a discharge pressure head of 2.7 bar (40 psig) requires 5.5 bar (80 psig) inlet air pressure, 85 Nm 3/h (50 scfm) air consump-tion and a pump speed of 120 strokes/minute. (See dot on chart.)Caution: Do not exceed 8.6 bar (125 psig) air supply pressure.Flow curves are for “optimal speed” conditions only. The “optimal speed” is that speed which provides the maximum flow under a particular air and fluid pressure condition. The optimal speed varies for different fluid and air pressures. Recommendations for optimal speed can be found on the right side of the flow curve.Flow rates indicated on chart were determined by pumping water.For optimum life and performance, pumps should be specified so that daily operation p arameters will fall in the center of the pump performance curve.This curve demonstrates the flow created when the stroke rate is modi-fied under a static air and fluid pres-sure condition. This curve can be applied to different pressure conditions to estimate the change in flow due to stroke rate.A8 Plastic Accu-Flo™ Ultra-Flex™/PTFE-Fitted@ 70 / 30 operating condition10203040506070S p e e d[114][151][189][38][76][227][265]020406080100120140160180200220GPM [LPM ]SPM Water Discharge Flow RateT8 Plastic Suction Lift CapabilityInlet Air Pressure102030405060708090100D r y V a c u u m02468101214161820222426Meter 01234567FT H 2OPSIG [BAR][0.7][1.4][2.0][2.7][3.4][4.1][4.8][5.5][6.2][6.9]SECTION 6ASUCTION LIFT CURVES & DATASuction lift curves are calibrated for pumps operating at305 m (1,000’) above sea level. This chart is meant to be a guide only. There are many variables which can affect your pump’s operating characteristics. The number of intakeand discharge elbows, viscosity of pumping fluid, elevation (atmospheric pressure) and pipe friction loss all affect the amount of suction lift your pump will attain.SECTION 6BSUCTION LIFT CURVES & DATASuction lift curves are calibrated for pumps operating at 305 m (1,000’) above sea level. This chart is meant to be a guide only. There are many variables which can affect your pump’s operating characteristics. The number of intakeand discharge elbows, viscosity of pumping fluid, elevation (atmospheric pressure) and pipe friction loss all affect theamount of suction lift your pump will attain.A8 Plastic Accu-Flo™ Suction Lift CapabilityInlet Air Pressure102030405060708090100D r y V a c u u m02468101214161820222426Meter 01234567FT H 2OPSIG [BAR][0.7][1.4][2.0][2.7][3.4][4.1][4.8][5.5][6.2][6.9]The solenoid was running at 150 strokes / minute.Actual suction lift may vary with different pump speeds.SECTION 7AINSTALLATION – T8 PLASTIC AIR-OPERATED PUMPSThe Model T8 plastic pump has a 51 mm (2”) inlet and 51 mm (2”) outlet and is designed for flows to 591 lpm (156 gpm). The T8 plastic pump is manufactured with wetted parts of polypropylene. The center block of the T8 is constructed of glass-filled polypropylene. A variety of diaphragms, valve balls, valve seats, and o-rings are available to satisfy temper-ature, chemical compatibility, abrasion and flex concerns. The suction pipe size should be at least 51 mm (2”) diam-eter or larger if highly viscous material is being pumped. The suction hose must be non-collapsible, reinforced type as the T8 is capable of pulling a high vacuum. Discharge piping should be at least 51 mm (2”); larger diameter can be used to reduce friction losses. It is critical that all fittings and connections are airtight or a reduction or loss of pump suction capability will result.For T8 plastic models, Wilden offers 68 kg (150 lb.) standard or metric flanges. The following details should be noted when mating these to piping:• A 60–80 shore gasket that covers the entire flange face should be used.• The gasket should be between .075” and .175” thickness.• Mating flanges with flat as opposed to raised surfaces should be used for proper mechanical sealing.• The flanges should be tightened to a minimum of 6.8 N•m(5 ft-lbs) but no more than 13.6 N•m (10 ft-lbs).A non-raised surfaced-flange adapter should be utilized when mating to the pump’s inlet and discharge manifolds for proper sealing.INSTALLATION: Months of careful planning, study, and selec-tion efforts can result in unsatisfactory pump performance if installation details are left to chance.Premature failure and long term dissatisfaction can be avoided if reasonable care is exercised throughout the installation process. LOCATION: Noise, safety, and other logistical factors usually dictate that “utility” equipment be situated away from the production floor. Multiple installations with conflicting require-ments can result in congestion of utility areas, leaving few choices for siting of additional pumps.Within the framework of these and other existing conditions, every pump should be located in such a way that four key factors are balanced against each other to maximum advantage. ACCESS: First of all, the location should be accessible. If it’s easy to reach the pump, maintenance personnel will have an easier time carrying out routine inspections and adjustments. Should major repairs become necessary, ease of access can play a key role in speeding the repair process and reducing total downtime.AIR SUPPLY: Every pump location should have an air line large enough to supply the volume of air necessary to achieve the desired pumping rate (see pump performance chart). Use air pressure up to a maximum of 8.6 bar (125 psig) depending upon pumping requirements.The use of an air filter before the pump will ensure that the majority of any pipeline contami-nants will be eliminated. For best results, the pumps should use an air filter, regulator, and lubricator system. ELEVATION: Selecting a site that is well within the pump’s suction lift capability will assure that loss-of-prime trou-bles will be eliminated. In addition, pump efficiency can be adversely affected if proper attention is not given to elevation (see pump performance chart).PIPING: Final determination of the pump site should not be made until the piping problems of each possible loca-tion have been evaluated. The impact of current and future installations should be considered ahead of time to make sure that inadvertent restrictions are not created for any remaining sites.The best choice possible will be a site involving the shortest and the straightest hook-up of suction and discharge piping. Unnecessary elbows, bends, and fittings should be avoided. Pipe sizes should be selected so as to keep friction losses within practical limits. All piping should be supported inde-pendently of the pump. In addition, it should line up without placing stress on the pump fittings.Expansion joints can be installed to aid in absorbing the forces created by the natural reciprocating action of the pump. If the pump is to be bolted down to a solid foundation, a mounting pad placed between the pump and foundation will assist in minimizing pump vibration. Flexible connections between the pump and rigid piping will also assist in mini-mizing pump vibration. If quick-closing valves are installed at any point in the discharge system, or if pulsation within a system becomes a problem, a surge suppressor should be installed to protect the pump, piping and gauges from surges and water hammer.When pumps are installed in applications involving flooded suction or suction head pressures, a gate valve should be installed in the suction line to permit closing of the line for pump service.The T8 can be used in submersible applications only when both wetted and non-wetted portions are com p atible with the material being pumped. If the pump is to be used in a submersible application, a hose should be attached to the pump’s air exhaust and the exhaust air piped above the liquid level.If the pump is to be used in a self-priming application, be sure that all connections are airtight and that the suction lift is within the pump’s ability. Note: Materials of construction and elastomer material have an effect on suction lift param-eters. Please refer to pump performance data.Pumps in service with a positive suction head are most effi-cient when inlet pressure is limited to 0.5–0.7 bar (7–10 psig). Premature diaphragm failure may occur if positive suction is 0.8 bar (11 psig) and higher.THE MODEL T8 WILL PASS 6.4 mm (1/4”) SOLIDS. WHEN-EVER THE POSSIBILITY EXISTS THAT LARGER SOLID OBJECTS MAY BE SUCKED INTO THE PUMP, A STRAINER SHOULD BE USED ON THE SUCTION LINE.CAUTION: DO NOT EXCEED 8.6 BAR (125 PSIG) AIR SUPPLY PRESSURE.BLOW OUT AIR LINE FOR 10 TO 20 SECONDS BEFORE ATTACHING TO PUMP TO MAKE SURE ALL PIPE LINE DEBRIS IS CLEAR. ALWAYS USE AN IN-LINE AIR FILTER.PUMPS SHOULD BE THOROUGHLY FLUSHED WITH WATER BEFORE INSTALLING INTO PROCESS LINES. FDA AND USDA APPROVED PUMPS SHOULD BE CLEANED AND/OR SANITIZED BEFORE BEING USED ON EDIBLE PRODUCTS.。
Wayne Pumps 操作说明书和零件手册

Operating Instructions and Parts Manual INSTALLATION (CONTINUED)Leaking joints or couplings will allow air to leak into the pipe and cause abnormal pump operation. Make sure to use pipe joint compound on all male pipe threads.DUG WELL, CISTERN, LAKE AND SPRING INSTALLATION (FIGURE 16, ON PAGE 10)• Install a foot valve on inlet pipe and lower into water.The foot valve should be at least 18 in. from thebottom of the well or sand or sediment could bedrawn into the system.NOTE: When a lake is used as a water supply, make sure the inlet pipeis deep enough to be submerged at all times.Slope the horizontal piping upward toward the pump to prevent trappingair. The pipe must be removed during winter months or protected againstfreezing.Protect the pipe from damage from swimmers and boats.Install a screen around the inlet pipe to preventthe entrapment of swimmers.DEEP WELL INSTALLATIONDRILLED WELL (4 IN. OR LARGER) WITH TWO PIPE JET (FIGURES 16,ON PAGE 10 AND 3, ON PAGE 4)1. Assemble a 1-1/4 in. foot valve (not included) to the jet body. A 1-1/4in. coupling is required to connect the larger pipe to the jet assembly.2. Connect the 1 in. pipe threads into the smaller opening in the jetbody.3. Lower the jet into the well. Add pipe as needed. Be sure to use pipejoint compound, or plumber’s seal tape on all male threads.4. Position the jet 10 - 20 feet below the lowest anticipated water level,but never closer than 5 feet from the bottom of the well, if possible.5. Install a well seal to support the pipe and prevent surface water andother contaminants from entering the well.6. Install the horizontal pipe from the well to the pump. Piping from thevertical well pipe to the pump should never be smaller than the wellpipes.7. Slope both pipes upward toward the pump to prevent trappingair. If the horizontal distance exceeds 25 feet, see Chart 1 for therecommended pipe sizes.DUG WELL, CISTERN, LAKE AND SPRING WITH TWO PIPE JET(FIGURE 16, ON PAGE 10)1. Install a 1-1/4 in. foot valve (not included) to the jet body. A 1-1/4 in.coupling is required to connect the larger pipe to the jet assembly.2. Connect the 1 in. pipe threads into the smaller opening in the jetbody.3. Lower the jet into the water below the lowest anticipated water level,but never closer than 18 in. from the bottom. Sand or debris may bedrawn into the system if the jet is too close to the bottom.4. Provide protection for the jet and pipes against damage from boatsor swimmers if a lake is used for the water supply.Install a screen around the inlet pipe to preventthe entrapment of swimmers.5. Slope the horizontal pipes upward toward the pump to preventtrapping air. If horizontal distance exceeds 25 feet, see Chart 1 forrecommended pipe sizes.DRILLED WELL (2 IN.) WITH SINGLE PIPE PACKER (FIGURES 16 AND4)NOTE: Single pipe packer jets rely on the space between single pipe andinside of well casing for return water to operate jet. T wo inch installationsmust use 1-1/4 in. galvanized steel pipe with special turned couplings (1-13/16 in. O.D.) to avoid restricting flow of return water back to jet.1. Assemble the foot valve and packer to the jet body.2. Lubricate the rubber cups with petroleum jelly.3. Attach the first section of pipe and lower jet into well.4. Add pipe until the jet is positioned 5 - 15 feet below the lowestanticipated water level. The jet should never be closer than 5 feetfrom the bottom of the well or sand and sediment may be drawninto the system.5. With the jet in position, fill the pipes with water to make sure therubber cups are sealed against inside of the well casing. It may benecessary to move the jet up and down to seat the cups.6. Install the casing adapter and the horizontal pipes.7. Slope both pipes upward toward the pump to eliminate trappingair. If the horizontal distance exceeds 25 feet, see Chart 1 for therecommended pipe sizes.1-1/4 IN. PIPEFigure 4 - Single Pipe JetPACKERFOOT VALVECUPSCWS SeriesDeep WellInlet: Suction 1-1/4 in.1-1/2 in.Inlet: Drive 1 in.1-1/4 in.Outlet3/4 in.1 in.DEEP WELL PUMP WITH HORIZONTAL AND VERTICAL STORAGE TANK (FIGURES 5 AND 6)1. Install the air volume control on the tank as shown.2. Connect the copper tube from the air volume control to the 1/8 in.NPT opening directly above the 1-1/4 in. opening on the front of the pump.3. Install a valve and isolating hose between the system and the houseplumbing to aid in pump removal for servicing and for reducing noise transmitted through the house piping.4. Provide a hose bib (faucet) at the lowest point in the system to drainfor service or storage.DEEP WELL PUMP WITH PRE-CHARGED STORAGE TANK (FIGURE 7)1. Check tank pre-charge using a tire pressure gauge. Set air pressurein tank to 28 psi which is 2 psi below pressure switch cut-in level. An air valve is located on the side and will accept a standard fitting from a bicycle pump or air line.2. Check the pressure with the power off, faucets open and no waterflowing (zero water pressure).3. Install a valve and isolator hose between the system and the houseplumbing to aid in pump removal for servicing and for reducing noise transmitted to the house through the piping.4. Provide a hose bib (faucet) at the lowest point in the system to drainfor service or storage.AIR VOLUME CONTROL TUBINGSUCTION。
潘姆泵维修部件清单说明书
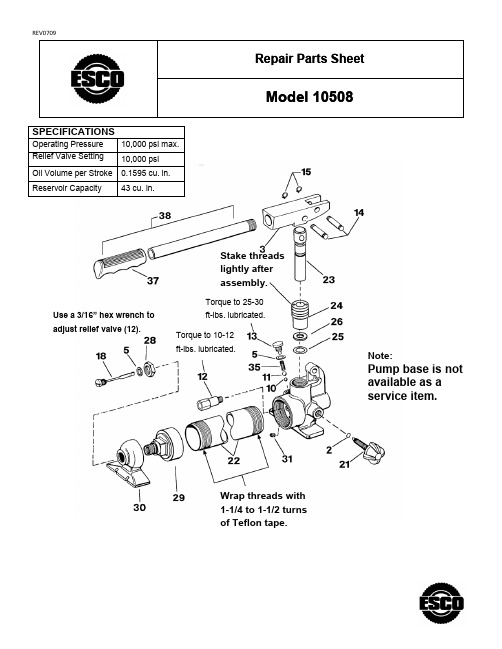
Note:Pump base is not available as a service item.Stake threads lightly after assembly.Use a 3/16” hex wrench to adjust relief valve (12).Torque to 10-12 ft-lbs. lubricated.Torque to 25-30ft-lbs. lubricated.Wrap threads with 1-1/4 to 1-1/2 turns of Teflon tape.INSTALL ALL KIT COMPONENTS TO INSURE A COMPLETE AND PROPER REAIR OF THE PUMPVisually inspect all components for shipping damage. If any shipping damage is found, notify carrier at once. Shipping damage is NOT covered by warranty. The carrier is responsible for all repair or replacement costs resulting from damage in shipment.CONTENTSEnglish ............................................... I nstruction Sheet ............................................ P age 2 - 5 Hollands .................................. H andleiding ................................................... B ladzidje 6 - 10 Français ................................... N otice d’Emploi ........................................ Page 11 - 15 Deutsch .................................... B edienungsanleitung ................................. Seite 16 - 20 Italiano ..................................... M anuale Istruzioni ..................................... Pagina 21 - 25 Español .................................... I strucciones ............................................... Página 26 - 30SAFETYINFORMATIONRead and follow all CAUTIONS, WARNINGS, and INSTRUCTIONS included with each product to avoid personal injury or property damage during system operation. ESCOCANNOT BE RESPONSIBLE FOR DAMAGE OR INJURY RESULTING FROM UNSAFE USE OF PRODUCT, LACK OF MAINTENANCE, OR INCORRECT PRODUCT AND SYSTEM APPLICATION.Co n tac tE SC Ow h e nind o u btas to safety precautions, or applications.CAUTIONAlways use the handle to carry the pump. Carrying the pump by the hose may damage the hose and/or the pump.WARNING Make sure that all system components are protected from external sources of damage, such as excessive heat, flame, moving machineparts, sharp edges, and corrosive chemicals.WARNING Wear proper personal protective gear when operating hydraulic equipment. WARNING Always check product limitations regarding pressure ratings, loadcapacities, and set-up requirements. The system operating pressure must not exceed the pressure rating of the lowest rated component in the system. WARNINGNEVER set the relief valve to a higher pressure than the maximum rated pressure of the pump. Higher settings may result in equipment damage and/or personal injury. See chart on page 1 to find the maximum pressure rating for your pump.WARNINGThese pumps are operated with a non-vented reservoir. If the reservoir is subjected to high pressure, the casing may rupture, causing personal injury and/or equipment damage. NEVER attempt to return more oil to the reservoir than it is capable of holding.INSTALLATIONConnecting the Pump1. Thread hose into pump outlet. Use 11 2 wraps of Teflon tape (or suitable thread sealant)on hose fitting, leaving the first complete thread free of tape to ensure that tape does not shed into hydraulic system, causing damage. Trim loose ends.2. Install a pressure gauge in-line from the pump for added safety and better control.3.Connect the hose to your cylinder or tool.OPERATIONBefore Using the Pump1. Check all system fittings and connections to be sure they are tight and leak free.2. Check oil level in reservoir before operating pump. See "Adding Oil to the Pump" onpage 4.WARNINGIn certain situations the pump handle can "kick back". Always keep your body to the side of the pump, away from the line of force of the handle.NOTE: To reduce handle effort at high pressure, take short strokes. Maximum leverage isobtained in the last 5 degrees of stroke.NOTE: When operating the pump in the vertical position, the hose end must be pointeddown, or the pump will pick up air and will not build pressure properly.Single-Acting Applications with Release Valve1.Close release valve by turning clockwise as shown in Figure 2.Figure 22.Operate pump handle to deliver hydraulic power to system. Pressure will bemaintained until release valve is opened.3. Open release valve (turn counter-clockwise) to release pressure, allowing oil to flow back to the reservoir.CAUTIONNEVER add extensions to pump handle. Extensions cause unstable pump operation.CAUTIONClose release valve finger tight ONLY. Using tools on releasevalve can damage it and cause the pump to malfunction.Air RemovalRemoving air from the hydraulic system will help the cylinder to advance and retract smoothly.Pump With Single-Acting Cylinder (A):1. Close release valve.2. Position pump at higher elevation than cylinder.3. Position cylinder with the plunger end down (up if using pull cylinder). See Figure 3.4.Operate pump to fully extend the cylinder (retract if using pull cylinder).5. Open release valve to retract cylinder (extend if a pull cylinder). This will force the trapped air to move up to the pump reservoir.6. Repeat the above steps as necessary.7.Add oil if necessary.Adding Oil to the PumpCheck oil level regularly.1. Remove vent/fill cap from reservoir.2. Fill reservoir only to level mark shown on pump.3. Remove air from system if necessary. Recheck oil level after removing air.4. Return vent/fill cap to proper position.NOTE: Non-vented hand pumps require air in the reservoir to function properly. If thereservoir is completely filled, a vacuum will form preventing oil from flowing out of the pump.WARNINGAlways add oil with cylinders fully retracted (extended if pull cylinders) or the system will contain more oil than the reservoir can hold.Keeping Oil Lines CleanWhen coupler halves are disconnected, always screw on dust caps. Use everyprecaution to guard unit against entrance of dirt because foreign matter may causepump, cylinder, or valve failure.Lubricating the PumpTo extend pump life and improve performance, lubricate the beam pin (A), cross pin(B), and piston head (C) regularly, using roller bearing grease. See Figure 4 below.Changing the Oil1. Drain all oil and refill with clean oil every 12months. If pump is used in dirty environments,change the oil more often.2. Remove vent/fill cap or plugfrom reservoir.3. Tiltpump to drain out old oil.4. Fill reservoir only to level mark shown on pump.5.Replace the vent/fill cap or plug. 6. Dispose of used oilproperly.Figure 4 TROUBLESHOOTINGGUIDE The following information is intended as an aid in determining if a problem exists. For repair service, contact the Authorized ESCO Service Center in your area.。
维京(Viking)手动蒸汽泵说明书
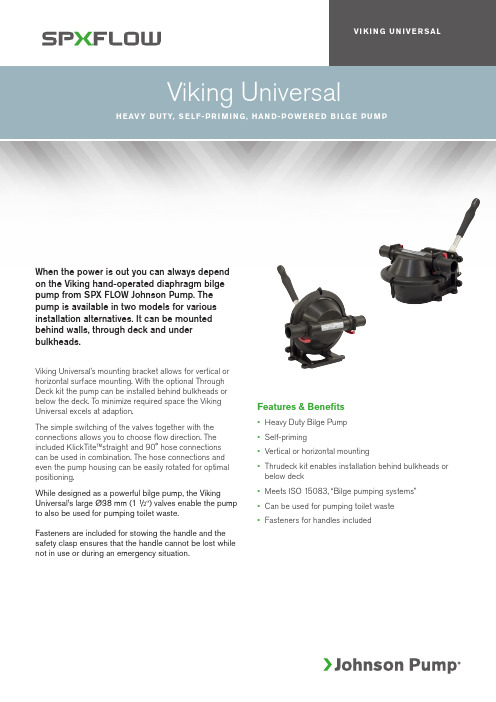
When the power is out you can always depend on the Viking hand-operated diaphragm bilge pump from SPX FLOW Johnson Pump. The pump is available in two models for various installation alternatives. It can be mounted behind walls, through deck and under bulkheads.Viking Universal’s mounting bracket allows for vertical or horizontal surface mounting. With the optional Through Deck kit the pump can be installed behind bulkheads or below the deck. T o minimize required space the Viking Universal excels at adaption.The simple switching of the valves together with the connections allows you to choose flow direction. The included KlickTite™straight and 90° hose connections can be used in combination. The hose connections and even the pump housing can be easily rotated for optimal positioning.While designed as a powerful bilge pump, the Viking Universal’s large Ø38 mm (1 ½") valves enable the pump to also be used for pumping toilet waste.Fasteners are included for stowing the handle and the safety clasp ensures that the handle cannot be lost while not in use or during an emergency situation.Features & Benefits• Heavy Duty Bilge Pump• Self-priming• Vertical or horizontal mounting• Thrudeck kit enables installation behind bulkheads or below deck• Meets ISO 15083, “Bilge pumping systems”• Can be used for pumping toilet waste• Fasteners for handles includedJP-930-EN Version: 01/2017 Issued:11/2017 COPYRIGHT © 2017 SPX FLOW, Inc.Available modelsFor more information about our worldwide locations, approvals, certifications, and local representatives, please visit .SPX FLOW, Inc. reserves the right to incorporate our latest design and material changes without notice or obligation. Design features, materials of construction and dimensional data, as described in this bulletin, are provided for your information only and should not be relied upon unless confirmed in writing.SE +46 19 21 83 10 *******************************US +1 847 671-7867 ******************************AUS +61 03 9589 9222 *********************Customer Service & Support Johnson Pump Marine At 45 strokes/min and a 1 m (3.28') head (10 kPa (1.45 psi) pressure) the Viking Universal has a flow of 60 l/min -16 GPM.Body and cover Polypropylene plastic reinforced with 30% fiberglass Diaphragm and valves Nitrile rubber Wetted parts PP30GF, PA66 GF30, POM, stainless steel, nitrile rubber Maximum suction 3 meters (10')Maximum head 4 meters (13')Combined suction/head 7 meters (23')Connection KlickTite™ connectors 38 mm (1½") hose. Both straight and 90˚ bends are included.Max. liquid temp +60°C (140°F)Weight 1,5 kg (3.3 lbs)Technical specifications and capacity data09-36250。
威肯泵 技术服务手册
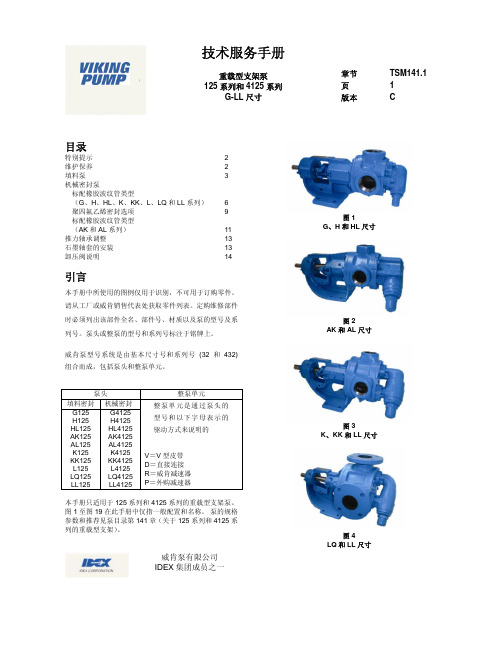
9.使用多功能润滑脂 NLGI#2 润滑球轴承。把轴承安放在 轴上并在支架中轻轻推动使其到位。
10.使唇面向轴端在外端盖中按下油封,并在支架中插入端 盖。在支架中转动端盖,直到紧靠在轴承上。请参考 第 4 页上的图 6。
11.在轴上安装锁紧垫圈和防松螺母。通过泵端口插入一段 硬木或黄铜到转子齿间,防止轴发生转动。拧紧防松 螺母,并弯曲锁紧垫圈的柄脚进入防松螺母的槽中。G 尺寸的泵上没有锁紧垫圈。
项目 19 20 21 22 23 24 25 26 27
零件名称 支架垫片 泵壳 管道堵头 转子和轴 惰轮和轴套 惰轮轴套 泵盖垫片 惰轮轴 泵盖和惰轮轴
项目 28 29 30 31 32 33
零件名称 夹套泵盖板的垫片 夹套泵盖 泵盖螺丝 卸压阀垫片 阀门螺丝 内置卸压阀
3
拆卸
危险
6.小心拆下转子和轴,避免损坏支架轴套。 7.从支架侧拆下填料函压盖。
泵的清洗:尽可能保持泵的清洁。这将便于检查、调整或 修理作业,并有助于防止污物阻塞润滑油嘴。
储存:如果需要储存泵,或在六个月或更长时间内不使用 泵,则泵中的液体必须排空,并在泵内部零件上涂抹一薄 层 SAE 30 重油。对装置润滑,并在泵轴延长部分上涂抹 润滑脂。威肯建议每 30 天手动旋转泵轴一整圈,以保证润 滑油的流通。
3.必须明确泵输送的是何种液体,还需了解液体 安全输送的相关注意事项。参考液体原料安 全数据表(MSDS),以更好地理解上述注意 事项。
不遵守以上的警示会导致严重受伤或死亡。
旋转:威肯泵均可顺时针或逆时针方向旋转。轴的旋转方 向决定了哪端吸入,哪端排出。齿轮分开的端口是吸入端。 卸压阀: 1. 威肯泵为容积泵,必须提供一定的压力保护装置。有采
AMT Pump Company 产品维修部件手册 A201-90A201-250-00说明书

Please read and save this Repair Parts Manual. Read this manual and the General Operating Instructions carefully before attempting to assemble, install, operate or maintain the product described. Protect yourself and others by observing all safety information. The Safety Instructions are contained in the General Operating Instructions. Failure to comply with the safety instructions accompanying this product could result in personal injury and/or property damage! Retain instructions for future reference. AMT reserves the right to discontinue any model or change specifications at any time without incurring any obligation.©2019 AMT Pump Company, A Subsidiary of The Gorman-Rupp Company, All Rights Reserved.Periodic maintenance and inspection is required on all pumps to ensure proper operation. Unit must be clear of debris and sediment. Inspect for leaks and loose bolts. Failure to do so voids warranty.Mounting FrameSPECIFICATIONSMaterial: Steel PlateFinish: Paint or powder coated finish, color: blackWeight: 10 lb. [5 kg]Overall dimensions (max): 22.1” [560mm] long10.1”[256mm]wide2.9”[74mm]tallGENERALMounting frame is designed to support a pump end and driver while also providing a convenient way to secure the entire assembly to a suitable grounding base plane.GROUNDING BASE PLANEMounting frame must be secured to a grounding base plane. Grounding plane must be flat, level, and of sufficient strength and size to support the entire frame/driver/pump assembly along with any loads the piping system generates. Frame is designed to provide a convenient form of mounting the driver/pump. It is not designed to handle excessive piping system loads or provide total support in and of itself. Frame is designed to transfer the loads to a flat grounding base plane that supports the entire frame. If frame is not supported correctly, damage to frame and pump assembly may occur. FRAME MOUNTING FASTENER LAYOUTRefer to Figure 1Frame mounting holes are sized to accommodate 5/16” [8 mm] diameter fasteners. A dimensional drawing is provided for fastener spacing and layout. Due to dimensional tolerances and assembly variations, it is best to measure your actual unit to determine the exact fastener spacing before installation.VIBRATIONMounting frame can be fastened directly to the grounding plane, but if unit vibration is excessive during operation, pump damage may occur. Some form of vibration dampening mount between pump/frame assembly and grounding plane should be considered.PUMP/DRIVER TO FRAME MOUNTINGRefer to Figure 2If A201-90 mounting frame is purchased as an accessory to be mounted to a pump in the field, follow the following instructions:• Measure vertical distance from pump end support foot or casing bottom to motor mounting foot.• If motor foot is 0” to 0.55” higher than the pump end support foot or casing bottom, fasten motor to frame driver mount.• If motor foot is 0.55” to 1.4” higher than the pump end support foot or casing bottom, the driver mount must first be repositioned. Loosen four M8 bolts securing driver mount to mounting rails. Slide driver mount up to required height and tighten bolts. Fasten motor to frame driver mount.• If distance is greater than 1.4”, motor must be spaced above driver mount as needed. Adding spacers will void any warranty.• 316 Series: Fasten motor to frame driver mount. Loosen two bottom casing bolts and install the casing clips ensuring that the holes are aligned with the holes in the pump support. Tighten casing bolts.• Loosen four M8 bolts securing pump support to mounting rails. Slide pump support up until it supports the pump foot or casing bottom. Tighten bolts to secure pump support in place. If pump foot has provisions for mounting bolts, holes must be drilled into the pump support at appropriate locations.Secure pump foot to pump support.REPAIR/REPLACEMENT PARTSMounting frame is available as a complete unit only. Replace entire unit if damage occurs.DESCRIPTIONMounting frame for 56 frame motor driven pumps. Additional casing clips included for mounting 316 series pumps. ExclusionsPump must be closed coupled to a motor with a foot. Mounting frame will NOT be able to be used with the following models:• 4292-96• 4782-95• 4785-95Figure 1Figure 2。
- 1、下载文档前请自行甄别文档内容的完整性,平台不提供额外的编辑、内容补充、找答案等附加服务。
- 2、"仅部分预览"的文档,不可在线预览部分如存在完整性等问题,可反馈申请退款(可完整预览的文档不适用该条件!)。
- 3、如文档侵犯您的权益,请联系客服反馈,我们会尽快为您处理(人工客服工作时间:9:00-18:30)。
WARNING
Warning - In addition to possible serious injury or death, failure to follow the
indicated instruction may cause damage
to pump and/or other equipment.
etc.) be sure that :
pressures.
● Any pressure in the chamber has been completely
vented through the suction or discharge lines or other appropriate openings or connections.
figure 1 - GG, HJ, HL 4195-G Unmounted pump
INTRODUCTION
The illustrations used in this manual are for identification purposes only and should not be used for ordering parts. Secure a parts list from the factory or a Viking® representative. Always give complete name of part, part number and material with model number and serial number of the pump when ordering repair parts.
● The pump drive system means (motor, turbine, engine, etc.) has been “locked out” or otherwise been made non-operational so that it cannot be started while work is being done on the pump.
figure 2 - as, ak, al 4195-G Unmounted pump
CAUTION ! The 4195-G series is a UL listed pump. Any changes or repairs to the pump will void the UL listing. To maintain the UL listing, the pump will need to be replaced with a new pump or repaired and retested at the factory. If the UL listing is no longer required, refer to TSM 144 for repair instructions. These can be obtained from your authorized Viking Pump distributor.
D = Direct Drive
This manual deals exclusively with the 4195-G Series LP-Gas pumps. Refer to Figures 1 thru 10 for general configuration and nomenclature used in this manual.
TECHNICAL SERVICE MANUAL
VIKING LP-GAS PUMPS SERIES 4195-G SIZES GG - AL
SECTION PAGE ISSUE
TSM 442 1 of 10 B
CONTENTS
Introduction . . . . . . . . . . . . . . . . . . . . . . . . 1 Safety Information . . . . . . . . . . . . . . . . . . . . 2 Special Information . . . . . . . . . . . . . . . . . . . . 3 Maintenance . . . . . . . . . . . . . . . . . . . . . . . 3 Disassembly . . . . . . . . . . . . . . . . . . . . . . . 5 Assembly . . . . . . . . . . . . . . . . . . . . . . . . . 6 Thrust Bearing Adjustment . . . . . . . . . . . . . . . . 6 Pressure Relief Valve Instructions . . . . . . . . . . . 6 Supplementary Section . . . . . . . . . . . . . . . . . 8 Warranty . . . . . . . . . . . . . . . . . . . . . . . . 10
DO NOT exceed the pump’s rated pressure, speed, temperature, or change the system/duty parameters from those the pump was originally supplied, without confirming its suitability for the new service.
GG 4195-G HJ 4195-G HL 4195-G AS 4195-G AK 4195-G AL 4195-G
UNITS
Units are designated by the . unmounted pump model numbers followed by a letter(s) indicating drive style.
● You know what material the pump has been handling, have obtained a material safety data sheet (MSDS) for the material, and understand and follow all precautions appropriate for the safe
THE FOLLOWING SAFETY INSTRUCTIONS MUST BE FOLLOWED AND ADHERED TO AT ALL TIMES.
ห้องสมุดไป่ตู้
Symbol Legend :
Danger - Failure to follow the indicated
!
instruction may result in serious injury . or death.
!
BEFORE opening any liquid chamber (pumping chamber, reservoir, relief valve adjusting cap fitting,
WARNING
INSTALL pressure gauges/sensors next to the pump suction and discharge connections to monitor
VIKING PUMP, INC. • A Unit of IDEX Corporation • Cedar Falls, IA 50613 USA
SAFETY INFORMATION AND INSTRUCTIONS
IMPROPER INSTALLATION, OPERATION OR MAINTENANCE OF PUMP MAY CAUSE SERIOUS INJURY OR DEATH AND/OR RESULT IN DAMAGE TO PUMP AND/OR OTHER EQUIPMENT. VIKING’S WARRANTY DOES NOT COVER FAILURE DUE TO IMPROPER INSTALLATION, OPERATION OR MAINTENANCE.
The unmounted pump or pump unit model number and serial number can be found on a nameplate attached to the pump or base.
Model Number Chart
UNMOUNTED PUMPS
handling of the material.
DO NOT attempt to dismantle a pressure relief valve
!
BEFORE operating the pump, be sure all drive guards
!
are in place.
that has not had the spring pressure relieved or is mounted on a pump that is operating.
!
WARNING
USE extreme caution when lifting the pump. Suitable lifting devices should be used when appropriate. Lifting eyes installed on the pump must be used only to lift the pump, not the pump with drive and/or base plate. If the pump is mounted on a base plate, the base plate must be used for all lifting purposes. If slings are used for lifting, they must be safely and securely attached. For weight of the pump alone (which does not include the drive and/or base plate) refer to the Viking Pump product catalog.