工厂生产异常工时划分表
生产线_异常工时明细纪录表_柏拉图分析
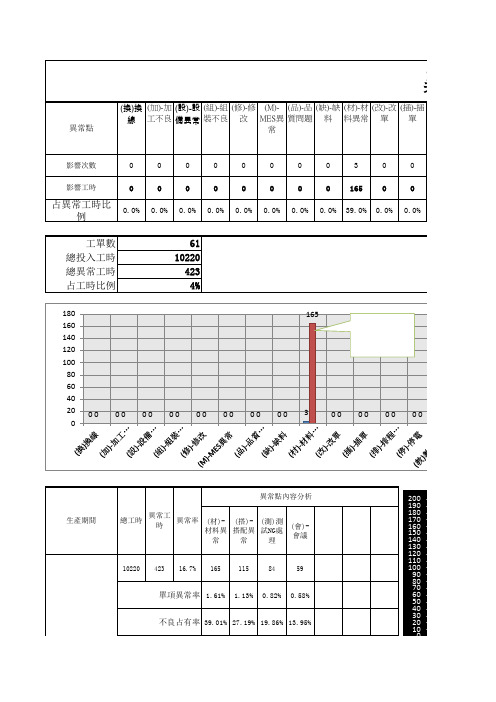
200 190 180 170 160 150 140 130 120 110 100 90 80 70 60 50 40 30 20 10 0
0 累計不良占有率
39.0% 66.2% 86.1% 100.0%
(材)-材料異常
異常時間
日期
上線機種
問題
異常工時明細
(排)-排 (停)-停 (教)教 (掃)-掃 (新)-新 (搭)-搭 (E)- (試)-試 (測)測 (N (準)-上 (會)-會 (作)-作 (出)-人 程異動 電 育訓練 除 人作業 配異常 ECN/R 產 試NG )NOT 線準備 議 業落後 力調出 D 處理 ES
0 0 0.0%
0 0 0.0%
0 0 0.0%
0 0 0.0%
0 0 0.0%
2 115 27.2%
0 0 0.0%
0 0 0.0%
1 84 19.9%
0 0 0.0%
0 0 0.0%
3 59 13.9%
0 0 0.0%
0 0 0.0%
115
84 59
0
00
00
00
2
00
00
1
00
00
3
00
00
00
3
00
பைடு நூலகம்
00
00
00
異常點內容分析 生產期間 總工時 異常工 異常率 (材)- (搭)- (測)測 時 (會)材料異 搭配異 試NG處 會議 常 常 理
10220
423
16.7%
165
115
84
59
單項異常率 1.61%
1.13%
0.82%
0.58%
异常工时管理规范(含表格)
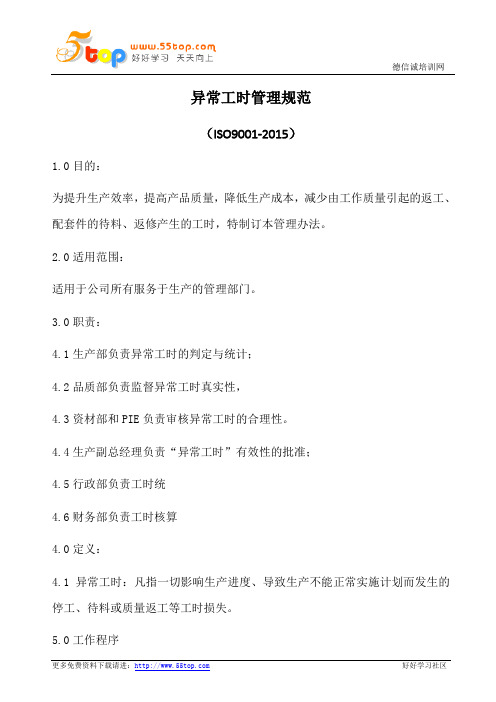
异常工时管理规范(ISO9001-2015)1.0目的:为提升生产效率,提高产品质量,降低生产成本,减少由工作质量引起的返工、配套件的待料、返修产生的工时,特制订本管理办法。
2.0适用范围:适用于公司所有服务于生产的管理部门。
3.0职责:4.1生产部负责异常工时的判定与统计;4.2品质部负责监督异常工时真实性,4.3资材部和PIE负责审核异常工时的合理性。
4.4生产副总经理负责“异常工时”有效性的批准;4.5行政部负责工时统4.6财务部负责工时核算4.0定义:4.1异常工时:凡指一切影响生产进度、导致生产不能正常实施计划而发生的停工、待料或质量返工等工时损失。
5.0工作程序5.1异常的处理5.1.1生产部按生产计划排期提前到仓库领料并安排做首件并量产。
5.1.2生产部在生产过程中发现产品、物料与要求不符,生产的成品达不到标准要求或来料无法使用等现象,5分钟内上报部门负责人、工程、资材部、品质部等相关人员确认。
5.1.3工程部、品质部确认异常可接受,通知生产继续生产,如确认异常不能接收,则由生产部或品质IPQC在接到需特别加工或退货信息10分钟内开出《品质异常处理单》进行跟踪处理。
5.1.4经品质分析,给出初步分析结果,结果为工艺问题,设计问题,来料问题。
5.1.5由品质分析,如果需要返工或改变工艺则由工程部更改样品给品质部确认,品质判定方案可行后,工程必须在现场跟进指导产线员工作业方法。
品质判定是否符合要求,工程等员工生产出2件合格品后方可离开现场,品质部跟踪监控过程确认。
5.1.6如果确认是来料问题,按照解决方案的意见,找供应商沟通协助处理或由我司加工挑选扣除供应商相应费用并要求在一个工作日内对来料问题给予回复处理意见(临时解决办法),生产部要给予相应的配合,和支持。
同时品质应协助。
5.1.7如果由于制程异常原因造成的,则由相关责任部门协助处理。
5.1.8待工,返工工时,由生产线记录,并填定在《车间导常工时申报表》,并在当天的《生产日报表》上备注。
生产异常工时单
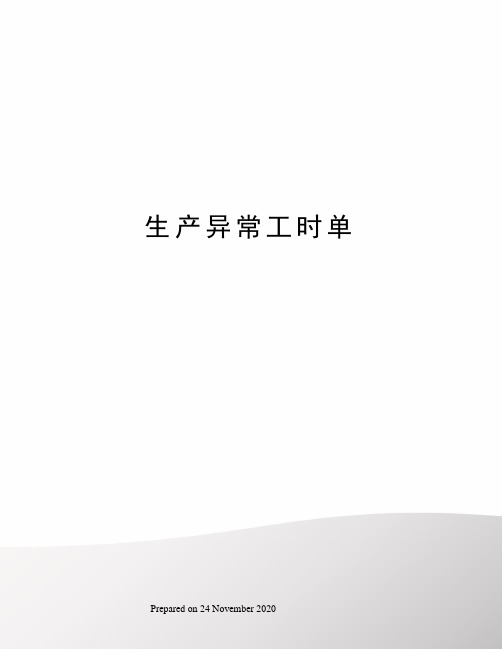
以上工时处理部门进行核算
小计
合计金额:
万
千
百
拾
元
角
分
备注:异常工时费用统一按每小时25元人民币收取,财务部根据责任归属在结算货款时扣除。
责任归属
□供应商:□责任部门:
填表:
生产部确认:
工程部确认:
品质部确认:
采购部确认:
总经理批准:
供应商确认:
财务部签收:
生产异常工时单
深圳市电子有限公司
生产异常工时单
产品型号
数量
日期
异常类型
□资料错误□检验错误□物料异常□生产错误□生产质量异常□客户质量投诉
异常描述
处理方法
□挑选□加工□返工(检查外观和检测功能)
损耗物料名细
材料名称
数量
单价
金额(元)
以上物料损耗金额由采购部进行核算
小计
损耗工时名细
处理流程/工序
小时
单价
生产异常工时单
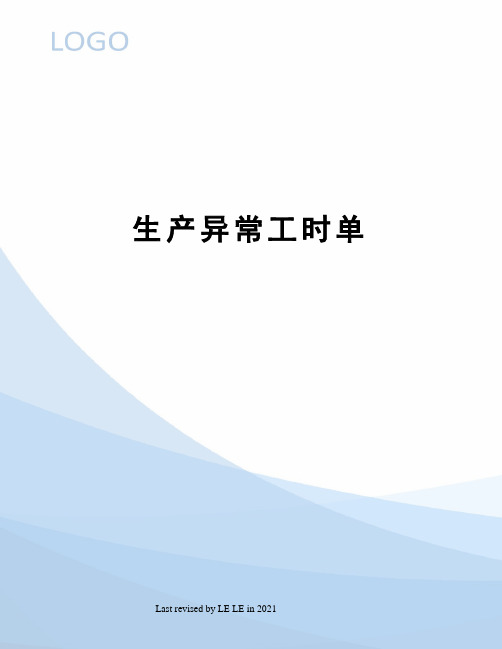
以上工时由处理部门进行核算
小计
合计金额:
万
千
百
拾
元
角
分
备注:异常工时费用统一按每小时25元人民币收取,财务部根据责任归属在结算货款时扣除。
责任归属
□供应商:□责任部门:
填表:Βιβλιοθήκη 生产部确认:工程部确认:品质部确认:
采购部确认:
总经理批准:
供应商确认:
财务部签收:
生产异常工时单
深圳市电子有限公司
生产异常工时单
产品型号
数量
日期
异常类型
□资料错误□检验错误□物料异常□生产错误□生产质量异常□客户质量投诉
异常描述
处理方法
□挑选□加工□返工(检查外观和检测功能)
损耗物料名细
材料名称
数量
单价
金额(元)
以上物料损耗金额由采购部进行核算
小计
损耗工时名细
处理流程/工序
小时
单价
工时异常原因分析与改善表
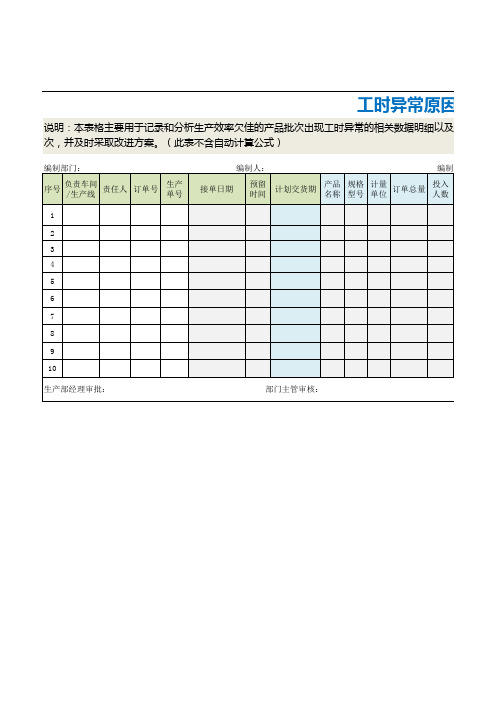
常原因分析与改善表
据明细以及具体原因,并提出相应的改进措施。可以帮助生产管理者集中性的分析生产效率偏低的产品批
编制日期: 标准 标准工时 所需天 实际交货日期 日产能 (H) 数 挡产 实际使用 生产效率 超用工时 时间 工时 超期 天数 差异率
制表:
产效率偏低的产品批原因分析改进措施备注工时异常原因分析与
说明:本表格主要用于记录和分析生产效率欠佳的产品批次出现工时异常的相关数据明细以及具体原因, 次,并及时采取改进方案。(此表不含自动计算公式)
编制部门: 序号 1 2 3 4 5 6 7 8 9 10 生产部经理审批: 部门主管审核: 制表: 负责车间 生产 责任人 订单号 /生产线 单号 接单日期 编制人: 预留 时间 计划交货期 编制日期: 产品 规格 计量 投入 订单总量 名称 型号 单位 人数
除外工时明细及定义
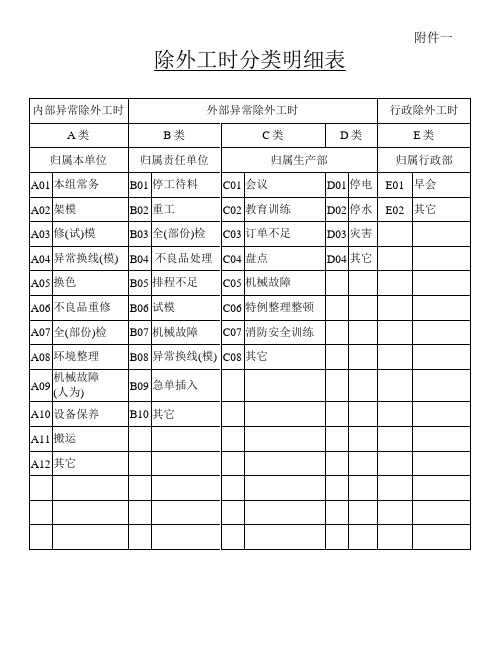
急单插入
因业务等其它部门之急需,导致正常生产之产品在未原批状况下继续生产,必须换线(模)所耗用之时间超出标准工时制定之时间者.
B10
其它
未在以上项目列示,但符合B类定义的除外工时.提报时需列明内容,并会办工程部后呈生产部最高主管核准.
C01
会议
上班时间内参加公司召开之会议所耗用之时间.
C02
教育训练
C06
特例整理
整顿
定期性或计划性之整理整顿时间(年终大扫除等).
C07
消防安全
训练
生产单位直接人员参加公司或消防队举办的消防训练或演习所投入的时间.
C08
其它
未在以上项目列示,但符合C类定义的除外工时.提报时需列明内容,并呈生产部最高主管核准.
D01
停电
因停电造成无法生产之停工损失时间.
D02
停水
因停水造成无法生产之停工损失时间.
B03
全(部份)检
生产单位因非本单位因素,应他单位要求对原料或产品全部或部份检验的时间.
B04
不良品
处理
因原料或前后站移转品有瑕疵,于生产前需预先处理或在生产中增加动作所耗用的工时.
B05
排程不足
生管所下排程不能满足生产单位生产能力且未对生产单位人力进行调整造成人力资源浪费及生产效率无法达成者.
附件二(2/2)
A04
异常换线(模)
B04
不良品处理
C04
盘点
D04
其它
A05
换色
B05
排程不足
C05
机械故障
A06
不良品重修
B06
试模
C06
特例整理整顿
A07
周生产异常明细表

品质异常面 17%
生管(采 购)物料
面 0%
生产异常项分布未图结案 1
模具异常面 25%
3.
设备异常面 58%
已结案 7
设备异常面 模具异常面 品质异常面 生管(采购)物料面
模具异常面 18%
品质异常面 27%
异常工时分布图
生管(采购)物料面 0%
设备异常面 55%
设备异常面 模具异常面 品质异常面 生管(采购)物料面
异常处理进度分布图
1,以 备注: 上
本周未结案追踪:
呈总经 理:
已结案 8ቤተ መጻሕፍቲ ባይዱ%
MR-011-04-A2
核准:
审核:
未结案 12%
未结案 已结案
作成:
年 月份第 周生产异常报告( 月 日— 月 日)
序号 1 2 3
项目
项数 占有比率 异常工时 占有比率
已结案 未结案
设备异常面 模具异常面
7 58% 41.5 55%
5 0
3 25% 13.5 18%
1 0
品质异常面
2 17% 20 27%
1 1
生管(采购)物料 面 0 0% 0 0% 0 0
合计
12 100% 75.0 100%
异常工时统计表
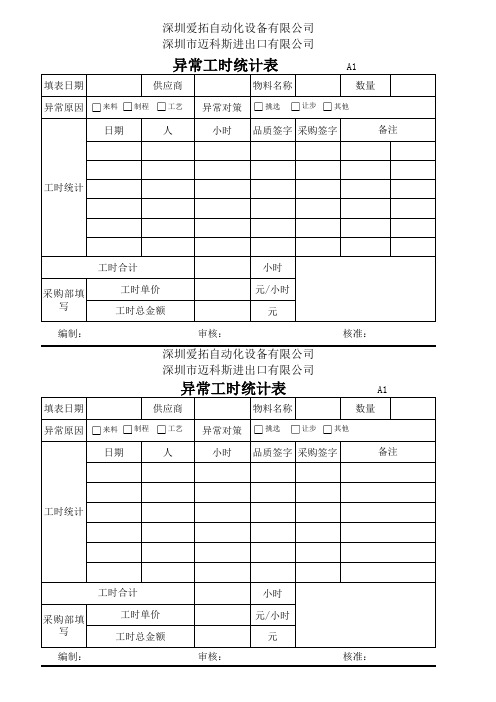
异常工时统计表
填表日期 异常原因
来料 制程
A1 数量
让步 其他
供应商
工艺
物料名称采购签字
备注
工时统计
工时合计 采购部填 写 编制: 工时单价 工时总金额 审核:
小时 元/小时 元 核准:
深圳爱拓自动化设备有限公司 深圳市迈科斯进出口有限公司
异常工时统计表
填表日期 异常原因
来料 制程
A1 数量
让步 其他
供应商
工艺
物料名称 异常对策 小时
挑选
日期
人
品质签字 采购签字
备注
工时统计
工时合计 采购部填 写 编制: 工时单价 工时总金额 审核:
小时 元/小时 元 核准:
深圳爱拓自动化设备有限公司 深圳市迈科斯进出口有限公司
异常工时
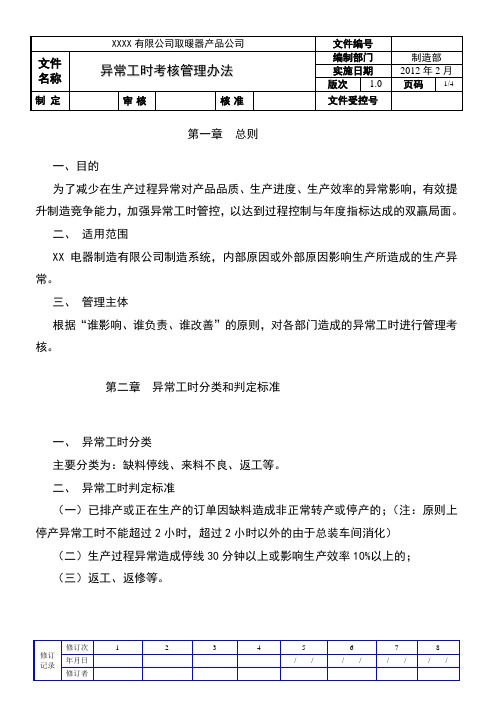
第一章总则一、目的为了减少在生产过程异常对产品品质、生产进度、生产效率的异常影响,有效提升制造竞争能力,加强异常工时管控,以达到过程控制与年度指标达成的双赢局面。
二、适用范围XX电器制造有限公司制造系统,内部原因或外部原因影响生产所造成的生产异常。
三、管理主体根据“谁影响、谁负责、谁改善”的原则,对各部门造成的异常工时进行管理考核。
第二章异常工时分类和判定标准一、异常工时分类主要分类为:缺料停线、来料不良、返工等。
二、异常工时判定标准(一)已排产或正在生产的订单因缺料造成非正常转产或停产的;(注:原则上停产异常工时不能超过2小时,超过2小时以外的由于总装车间消化)(二)生产过程异常造成停线30分钟以上或影响生产效率10%以上的;(三)返工、返修等。
第三章异常工时管理细则一、异常工时的计算规则:(一)停产工时=停产时间*生产线人数(二)非正常转产工时=转产时间*生产线人数注:转产时间=最后一台产品下线到下一机型第一台产品下线的时间(转产时间在30分钟内不计)(三)物料全选或加工工时=挑选或加工时间*参与挑选或加工人数(四)效率损失工时=(标准产出-实际产出)/标准产出*生产时间*生产线人数(五)返工工时=返工时间*返工人数二、各类异常工时的界定细则(一)采购员(供应商)造成的异常工时1、由于欠料或来料不及时(包括未及时进仓)而导致生产线停产或非正常转产的异常工时(设计原理:采购员必须从发出订单开始,跟踪到物料合格上线);2、物料需生产线挑选或加工后方可生产的,从而造成降低生产效率或占用人力的异常工时。
注:所有供应商造成的异常工时均属于采购员责任,并纳入采购中心异常工时考核;(二)生产管理中心造成的异常工时1、计划排产不合理导致生产线无法正常安排生产导致的异常;2、计划变更未及时通知相关部门造成的生产异常;(三)前工序车间(冲压车间&喷涂车间&焊接车间)造成的异常工时1、由于前工序车间未能及时生产提供物料而造成生产线停产或非正常转产所产生异常工时;2、前工序车间的物料需生产线挑选或加工后方可生产的,从而造成降低生产效率或占用人力的异常工时。
异常工时浪费统计分析图表范例

货/排产需求,重新刷固件;(合计
1
8
50台)
8
销售部50% PMC部50%
PMC部; 4; 1%
合计
253
销售部; 4; 2%
供应商; 245; 97%
1
2
2
供应商
1
1.5
1.5
供应商
1
ห้องสมุดไป่ตู้65
1
48
1
2
1
26
1
35
2
3
1
4
2
5
1
8
1
15
65
供应商
48
供应商
2
供应商
26
供应商
35
供应商
6
供应商
4
供应商
10
供应商
8
供应商
15
供应商
FQC
重新刷固件;
工时浪费 问题点分
责任部门
供应商
PMC部
销售部
合计
浪费工时(H) 245 4 4 253
销售订单与实物固件不一致,满足出
来源 IQC IQC IQC IQC
IQC
IQC
IQC
IQC IQC IQC IQC IQC IQC IQC IQC IQC
XX月份-异常工时浪费-品质部
机型/物料名称
异常描述
加热铝板(华尔康) 孔径偏大,线路反,变形;
0.4喷嘴(几维鸟) 孔径偏小,堵孔; USB转接线B(建军) 万用表测试导通
异常原因 供应商来料问题; 供应商来料问题; 供应商来料问题;
供应商来料问题;
无法调
线材 (深海盛)
线序反,端子坏,端子脱落
生产异常管理程序(含表格)
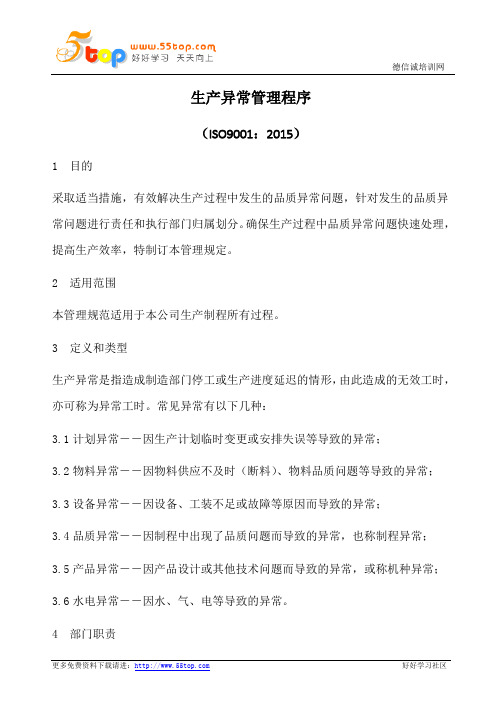
生产异常管理程序(ISO9001:2015)1 目的采取适当措施,有效解决生产过程中发生的品质异常问题,针对发生的品质异常问题进行责任和执行部门归属划分。
确保生产过程中品质异常问题快速处理,提高生产效率,特制订本管理规定。
2 适用范围本管理规范适用于本公司生产制程所有过程。
3 定义和类型生产异常是指造成制造部门停工或生产进度延迟的情形,由此造成的无效工时,亦可称为异常工时。
常见异常有以下几种:3.1计划异常--因生产计划临时变更或安排失误等导致的异常;3.2物料异常--因物料供应不及时(断料)、物料品质问题等导致的异常;3.3设备异常--因设备、工装不足或故障等原因而导致的异常;3.4品质异常--因制程中出现了品质问题而导致的异常,也称制程异常;3.5产品异常--因产品设计或其他技术问题而导致的异常,或称机种异常;3.6水电异常--因水、气、电等导致的异常。
4 部门职责4.1技术部职责4.1.1未及时确认零件样品;4.1.2设计错误或疏忽;4.1.3设计临时变更;4.1.4设计资料未及时完成;4.1.5设计需要修改,设计人员未得到相关负责人的确认就安排生产;4.1.6其他因设计开发原因导致的异常;4.1.7制定的工艺流程或作业标准工时不合理4.1.8技术变更失误;4.1.9未作工装夹具或工装夹具设计不合理;4.1.10生产线发生的异常问题,未能在规定的时间内分析出原因和制定临时/永久的改善对策,解决异常问题的时效性差,造成等待或停工;4.1.11其他因工作疏忽所致的异常。
4.2制造部职责4.2.1生产计划日程安排错误;4.2.2临时变换生产安排;4.2.3物料领料错误造成物料断料而停工;4.2.4未进行生产安排;4.2.5其他因生产安排、物料计划而导致的异常。
4.3质量部职责4.3.1未按照检验标准、规范作业;4.3.2进料检验合格,但实际上不良率明显超过约定标准;4.3.3进料检验延迟;4.3.4上工序检验员检验合格的物料在下工序出现较高不良;4.3.5过程检验员未及时发现品质异常(如代用错误、未依规定作业等等);4.3.6其他因工作疏忽所致的异常。
异常工时管理规范(含表格)
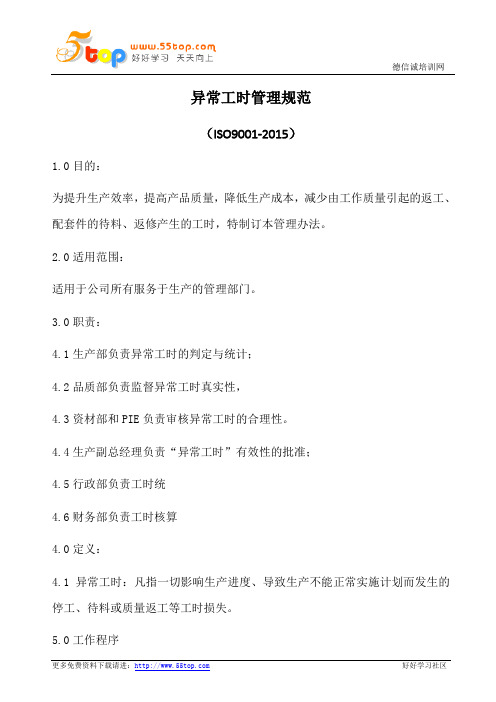
异常工时管理规范(ISO9001-2015)1.0目的:为提升生产效率,提高产品质量,降低生产成本,减少由工作质量引起的返工、配套件的待料、返修产生的工时,特制订本管理办法。
2.0适用范围:适用于公司所有服务于生产的管理部门。
3.0职责:4.1生产部负责异常工时的判定与统计;4.2品质部负责监督异常工时真实性,4.3资材部和PIE负责审核异常工时的合理性。
4.4生产副总经理负责“异常工时”有效性的批准;4.5行政部负责工时统4.6财务部负责工时核算4.0定义:4.1异常工时:凡指一切影响生产进度、导致生产不能正常实施计划而发生的停工、待料或质量返工等工时损失。
5.0工作程序5.1异常的处理5.1.1生产部按生产计划排期提前到仓库领料并安排做首件并量产。
5.1.2生产部在生产过程中发现产品、物料与要求不符,生产的成品达不到标准要求或来料无法使用等现象,5分钟内上报部门负责人、工程、资材部、品质部等相关人员确认。
5.1.3工程部、品质部确认异常可接受,通知生产继续生产,如确认异常不能接收,则由生产部或品质IPQC在接到需特别加工或退货信息10分钟内开出《品质异常处理单》进行跟踪处理。
5.1.4经品质分析,给出初步分析结果,结果为工艺问题,设计问题,来料问题。
5.1.5由品质分析,如果需要返工或改变工艺则由工程部更改样品给品质部确认,品质判定方案可行后,工程必须在现场跟进指导产线员工作业方法。
品质判定是否符合要求,工程等员工生产出2件合格品后方可离开现场,品质部跟踪监控过程确认。
5.1.6如果确认是来料问题,按照解决方案的意见,找供应商沟通协助处理或由我司加工挑选扣除供应商相应费用并要求在一个工作日内对来料问题给予回复处理意见(临时解决办法),生产部要给予相应的配合,和支持。
同时品质应协助。
5.1.7如果由于制程异常原因造成的,则由相关责任部门协助处理。
5.1.8待工,返工工时,由生产线记录,并填定在《车间导常工时申报表》,并在当天的《生产日报表》上备注。
车间异常工时方案
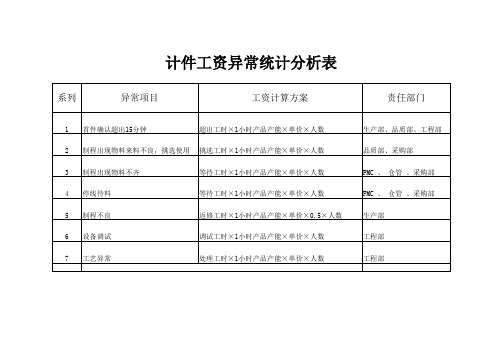
异常项目
首件确认超出15分钟 制程出现物料来料不良,挑选使用 制程出现物料不齐 停线待料 制程不良 设备调试 工艺异常
工资计算方案
超出工时×1小时产品产能×单价×人数 挑选工时×1小时产品产能×单价×人数 等待工时×1小时产品产能×单价×人数 等待工时×1小时产品产能×单价×人数 返修工时×1小时产品产能×单价×0.5×人数 调试工时×1小时产品产能×单价×人数 处理工时×1小时产品产能×单价×人数
责任部门
生产部、品质部、工程部 品质部、采购部 PMC 、 仓管 、采购部 PMC 、 仓管 、采购部 生产部 工程部 工程部
异常工时记录表[空白模板]
![异常工时记录表[空白模板]](https://img.taocdn.com/s3/m/21b972179b89680202d82515.png)
5
/
6
/
7
/
8
/
9
/
10
/
11
/
12
/
13
/
14
/
15
/
16
/
17
/
18
/
19
/
20
/
21
/
22
/
23
/
1.异常工时累计在半小时内属正常损耗可不予记录。
备 注:
2.异常工时审批权限:试模技术员1H内
试模领班2H内
试模课长3H内。
3.异常工时起止时间由责任部门在开始和结束时分别确认,当起止时间全部未确认,异常工时不生效。当有开始时间确认无结束时间确认,工时默认生效到当班结束时间。
表单编号:
版本: V03
表单保存期限:五年
超时 审核
异常工时起止时间由责任部门在开始和结束时分别确认当起止时间全部未确认异常工时不生效
试模试产异常工时记录表
日期: 年 月
序 号
日期
机型
品名
模号
机台 编号
开始时间
起止工时 (H)
KPI有 效工
时 (H)
异常工时原因
发生 阶段
责任部门
责任 部门确认
试模 技术员
1
/
2
/
3
/
4
/
异常工时责任划分与责任判定标准参照表

产品研发中心开发的产品在分公司试产产生的异常工时(记录异常工时需要注明)
正常费用补偿、 只做统计不考核
产品结构不良
产品工程部 因产品结构改良设计、产品结构不良等造成的异常;
工程问题
开发遗留问题点-开发部
开发部
研发部负责开发的产品,其产品未释放,在产品开发过程中遗留未能解决的问题造成的 异常(《新产品试(生)产问题改善一览表》中记录的且未改善完成问题点)
异常工时责任划分与责任判定标准参照表
异常大类 异常小类
具体细项
责任部门
异常产生原因概述
备注
换产品工时
换产品工时
生产部
生产线切换产品生产造成多能工岗位训练
人力闲置-总装部
生产部
产品切换,导致多余人力无法外借
人力闲置-综合部(取消)
生产部
综合部招人多出公司配置人员
人员不足-总装部
生产部
人员离职、请假、旷工、自离导致生产时人力不足
人
人员状态
人员内部借调-产品工程部 人员内部借调-开发部 人员内部借调-PMC部
产品工程部 开发部 PMC部
产品工程部从总装部借调直接人员 开发部从总装部借调直接人员 PMC部从总装部借调直接人员
人员内部借调-IE部
IE部
IE部从总装部借调直接人员
塑胶件缺料(发外)
PMC部
塑胶件供应不及时,供应商为PMC部发外厂家
排程提前-主计划员
主计划员 突然的大单/急货而总装提前生产造成的缺料
排程提前-PMC
PMC部
大单/急货而总装提前生产,主计划已提前通知,造成的缺料
物料结构缺陷或规格变更-产品 工程部
产品工程部
物料规格临时变更等造成的异常(如﹕来料需做加工才能上线等)
生产线异常管理规范(含表格)
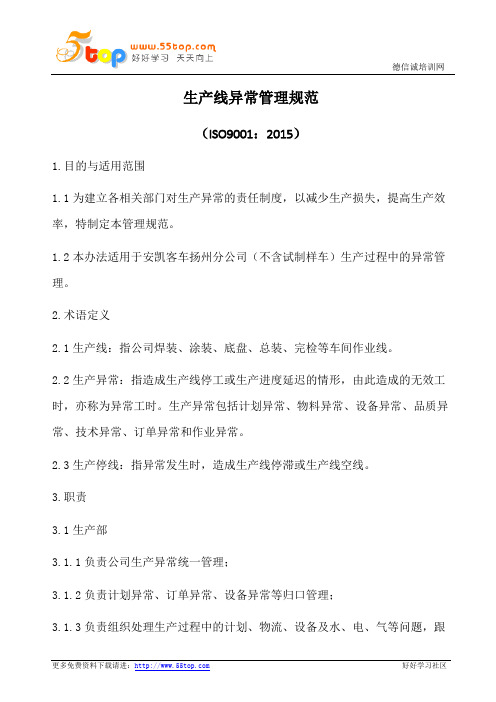
生产线异常管理规范(ISO9001:2015)1.目的与适用范围1.1为建立各相关部门对生产异常的责任制度,以减少生产损失,提高生产效率,特制定本管理规范。
1.2本办法适用于安凯客车扬州分公司(不含试制样车)生产过程中的异常管理。
2.术语定义2.1生产线:指公司焊装、涂装、底盘、总装、完检等车间作业线。
2.2生产异常:指造成生产线停工或生产进度延迟的情形,由此造成的无效工时,亦称为异常工时。
生产异常包括计划异常、物料异常、设备异常、品质异常、技术异常、订单异常和作业异常。
2.3生产停线:指异常发生时,造成生产线停滞或生产线空线。
3.职责3.1生产部3.1.1负责公司生产异常统一管理;3.1.2负责计划异常、订单异常、设备异常等归口管理;3.1.3负责组织处理生产过程中的计划、物流、设备及水、电、气等问题,跟踪闭环3.1.4负责生产、设备等异常责任单位的判定;3.1.5负责异常归口管理单位处理异常,跟踪闭环的责任判定和考核。
3.2技术部3.2.1负责公司技术异常归口管理;3.2.2负责组织处理生产过程中的设计、切换、试装和工艺等问题,跟踪闭环;3.2.3负责技术异常责任单位判定;3.2.4负责及时审核处理异常申报。
3.3质保部3.3.1负责公司品质异常归口管理;3.3.2负责组织处理外购件质量和生产过程检验以及检验信息录入等问题,跟踪闭环。
3.3.3负责品质异常责任单位判定;3.3.4负责及时审核处理异常申报。
3.4采购部3.4.1负责公司物料异常归口管理;3.4.2负责组织处理满足质量要求的物料到位及时性、未与车间办理量产交接等,跟踪闭环;3.4.3负责物料异常责任单位判定;3.4.4负责及时审核处理异常申报;3.5采购部(仓库)3.5.1负责公司常规物料及库管件配送物料(含直送工位件)异常归口管理;3.5.2负责组织处理满足质量要求的常规件(含直送工位件)到位及时性、在原图号进行尺寸和性能提升修改的物料(含直送工位件)未及时到货问题,跟踪闭环;3.5.3负责组织处理库管件配送物料异常、送料维护、及时报缺和首件送检等问题,跟踪闭环;3.5.4负责常规物料及库管件配送物料异常责任单位判定;3.5.5负责及时审核处理异常申报。