板件涨缩异常分析报告1
镁合金压铸件收缩缺陷分析及对策
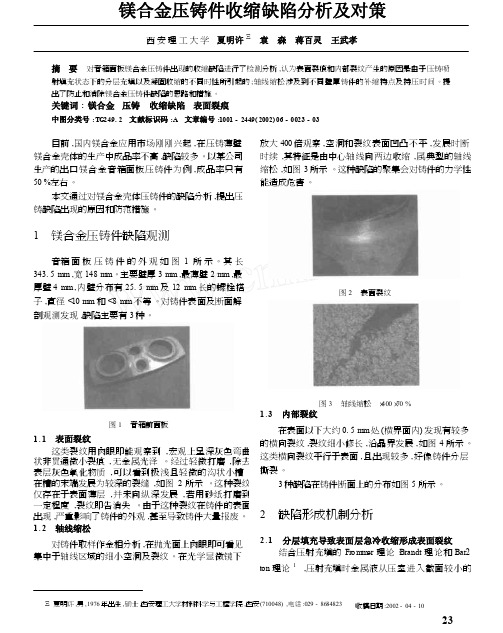
镁合金压铸件收缩缺陷分析及对策西安理工大学夏明许Ξ袁森蒋百灵王武孝摘要对音箱面板镁合金压铸件出现的收缩缺陷进行了检测分析,认为表面裂痕和内部裂纹产生的原因是由于压铸喷射填充状态下的分层充填以及凝固收缩的不同时性所引起的;轴线缩松涉及到不同壁厚铸件的补缩特点及持压时间。
提出了防止和消除镁合金压铸件缺陷的思路和措施。
关键词: 镁合金压铸收缩缺陷表面裂痕中图分类号:T G249. 2 文献标识码:A 文章编号:1001 - 2449( 2002) 06 - 0023 - 03目前,国内镁合金应用市场刚刚兴起,在压铸薄壁镁合金壳体的生产中成品率不高,缺陷较多。
以某公司生产的出口镁合金音箱面板压铸件为例, 成品率只有50 %左右。
本文通过对镁合金壳体压铸件的缺陷分析,提出压铸缺陷出现的原因和防范措施。
放大400 倍观察,空洞和裂纹表面凹击不帄,发展时断时续,其特征是由中心轴线向两边收缩,属典型的轴线缩松,如图3 所示。
这种缺陷的聚集会对铸件的力学性能造成危害。
1 镁合金压铸件缺陷观测音箱面板压铸件的外观如图 1 所示。
其长343 . 5 mm ,宽148 mm 。
主要壁厚3 mm ,最薄壁2 mm ,最厚壁4 mm ,内壁分布有25 . 5 mm 及12 mm 长的螺栓搭子,直径<10 mm 和<8 mm 不等。
对铸件表面及断面解剖观测发现,缺陷主要有3 种。
图2 表面裂纹图3 轴线缩松×400 ×70 %1 .3 内部裂纹在表面以下大约0. 5 mm 处(横界面内) 发现有较多的横向裂纹,裂纹细小修长,沿晶界发展,如图4 所示。
这类横向裂纹帄行于表面,且出现较多,好像铸件分层撕裂。
3 种缺陷在铸件断面上的分布如图5 所示。
图1 音箱前面板1. 1 表面裂纹这类裂纹用肉眼即能观察到,宏观上呈深灰色弯曲状非贯通微小裂痕,无金属光泽。
经过轻微打磨,除去表层灰色氧化物质,可以看到极浅且轻微的沟状小槽,在槽的末端发展为较深的裂缝,如图 2 所示。
冲压零件常见缺陷分析

4
起皱
5
起皱原因
主要原因:由于板料受到挤压,当平面方向的主、次应力 达到一定程度时,厚度方向失稳,从而产生起皱现象。 : , , ,. 材料堆集起皱。进入凹模腔内材料过多变成的皱纹。
.
失稳起皱 .板料厚度方向增厚失稳。
,. .拉伸应力不均匀而产生的皱纹。(例如:门把手区域)
(: )
6
Press direction
Press direction
一、冲压负角() ()
冲
冲
压
压
方
方
向
向
① ②
缺陷:在冲压方向有负角,无法成形。. :.
措施:将①和②两特征连接起来,消 除冲压负角。
: ① ②,
二、开裂() ()
缺陷:门把手局部形状太深,存在开裂风险。 : ,.
措施:降低深度并增大角,。 :, .
1
模具开发基本流程
产品 设计
冲压工 艺设计
模具结 构设计
铸造
加工装配
同步 分析
图设 同步
计
分析
调试
量产
2
冲压工艺基本流程
产品数模 生产纲领 参考工艺
技术标准 设备参数
零件工 艺性分 析
工艺制 订
拉延
冲压方向
修冲
内容分配
翻边
模具结构
…..
分模线….
3
零件常见问题
零件成形时常见问题:
起皱 开裂 回弹 表面质量(塌陷、滑移线、冲击线)
应 力
11
回弹解决办法
影响回弹的因素很多,实际生产中很难解决。
,.
目前,解决回弹常用下面几种方法:
:
生产异常分析报告模板范文
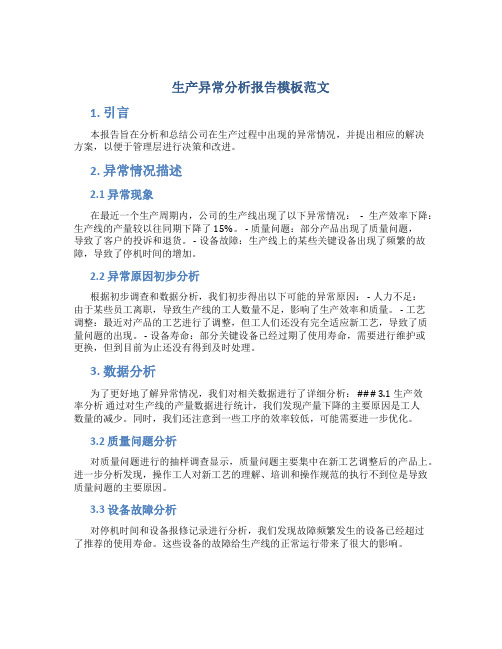
生产异常分析报告模板范文1. 引言本报告旨在分析和总结公司在生产过程中出现的异常情况,并提出相应的解决方案,以便于管理层进行决策和改进。
2. 异常情况描述2.1 异常现象在最近一个生产周期内,公司的生产线出现了以下异常情况:- 生产效率下降:生产线的产量较以往同期下降了15%。
- 质量问题:部分产品出现了质量问题,导致了客户的投诉和退货。
- 设备故障:生产线上的某些关键设备出现了频繁的故障,导致了停机时间的增加。
2.2 异常原因初步分析根据初步调查和数据分析,我们初步得出以下可能的异常原因: - 人力不足:由于某些员工离职,导致生产线的工人数量不足,影响了生产效率和质量。
- 工艺调整:最近对产品的工艺进行了调整,但工人们还没有完全适应新工艺,导致了质量问题的出现。
- 设备寿命:部分关键设备已经过期了使用寿命,需要进行维护或更换,但到目前为止还没有得到及时处理。
3. 数据分析为了更好地了解异常情况,我们对相关数据进行了详细分析: ### 3.1 生产效率分析通过对生产线的产量数据进行统计,我们发现产量下降的主要原因是工人数量的减少。
同时,我们还注意到一些工序的效率较低,可能需要进一步优化。
3.2 质量问题分析对质量问题进行的抽样调查显示,质量问题主要集中在新工艺调整后的产品上。
进一步分析发现,操作工人对新工艺的理解、培训和操作规范的执行不到位是导致质量问题的主要原因。
3.3 设备故障分析对停机时间和设备报修记录进行分析,我们发现故障频繁发生的设备已经超过了推荐的使用寿命。
这些设备的故障给生产线的正常运行带来了很大的影响。
4. 解决方案基于以上异常情况和数据分析结果,我们提出以下解决方案: ### 4.1 人力调整 - 招聘新员工:加大招聘力度,尽快补充生产线上的人力不足。
- 培训与提升:针对新工艺进行专项培训,提升工人的理解和操作能力。
4.2 工艺优化•与研发部门密切合作:与研发部门沟通,了解新工艺要求,并及时进行工艺优化。
PCB涨缩影响因素

PCB涨缩影响因素PCB涨缩影响因素1、基材来料尺寸稳定性,尤其是供应商的每个层压CYCLE 之间的尺寸一致性;即使同一规格基材不同CYCLE的尺寸稳定性均在规格要求内,但因之间的一致性较差,可引起板件首板试制确定合理的一次内层补偿后后,因不同批次板料间的差异造成后续批量生产板件的图形尺寸超差;同时,还有一种材料异常是在外层图形转移后至外形工序的过程中板件发现收缩;在生产过程中曾有个别批次的板件在外形加工前数据测量过程中发现其拼板宽度与出货单元长度相对外层图形转移倍率出现严重的收缩,比率达到3.6mil/10inch,具体数据见下表;经追查,该异常批次板件在外层层压后的X-RAY测量与外层图形转移倍率均处于控制范围内的,目前在过程监控中仍暂未找出较好的方法进行监控;2、拼板设计:常规板件的拼板设计均为对称设计,在图形转移倍率正常的情况下对成品PCB的图形尺寸并无明显影响;但是一部分板件在为提升板料利用率,降低成本的过程中而使用了非对称性结构的设计,其对不同分布区域的成品PCB的图形尺寸一致性将带来极为明显的影响,甚至在PCB的加工过程中我们都可以在激光盲孔钻孔以及外层图形转移曝光/阻焊剂曝光/字符印刷过程中发现此类非对称设计的板件其在各环节中的对准度情况相对常规板件更难以控制与改善;3、一次内层图形转移工序:此处对成品PCB板件尺寸是否满足客户要求起着极为关键的作用;如一次内层图形转移的菲林倍率补偿提供存在较大偏差其不但可直接导致成品PCB 图形尺寸无法满足客户要求外,还可引起后续的激光盲孔与其底部连接盘对位异常造成LAYER TO LAYER之间的绝缘性能下降直至短路,以及外层图形转移过程中的通/盲孔对位问题;PCB涨缩如何解决1、基材来料尺寸稳定性与批间尺寸一致性的监控:定期地对不同供应商提供的基材进行尺寸稳定性测试,从中跟踪其同规格板料不同批之间的经纬向数据差异,并可适当地使用统计技术对基材测试数据进行分析;从而也可找出质量相对稳定的供。
模具成型异常原因分析总结技术经验

1.毛邊 2.充填不足 3.縮水 4.汽泡 5.變形 6.熔合線 7.尺寸偏大 8.尺寸偏小 9.成品段差 10.粘模
11.拉傷 12.咬花不良 13.斑點料花 14.燒焦 15.有模印 16.光潔度不良 17.溢料 18.流痕 19.銀線 20.頂白
破
壓
變
塊
滑
滑
處
板
形
斜
塊
塊
太
不
彎
度
配
拉
緊
平
曲
合
合
傷
行
配
太
不
緊
良
壓
滑
板
動
配
位
合
置
不
過
良
緊
產品開模合理性 模具機構合理性 加工工藝合理性
組立裝配合理性
成型加工合理性
专业课件
28
頂針不順暢
模
頂
頂
有
仁
針
針
敲
與
孔
孔
傷
模
太
有
腫
板
緊
臟
起
上
東
下
西
頂
出
板
偏
位
頂
針 變 形
成 型 機
頂
出
不
平
衡
產品開模合理性 模具機構合理性 加专工业工藝课合件理性
7
尺寸偏大
X 澆 縮 加 加拋 溫成成
﹑ 口 水 工 工光 度型型
Y 位 率 火 時過 過時時
相 置 計 花 過大 高壓保
差 不 算位 切
力壓
太 合 錯過
過時
大 理 誤大
大間
高级精密线路板PCB涨缩异常处理方式

判定量测比例与底 片比例是否相符
相符
不符
按照计算比例绘 制新底片 确认首件
重绘底片
正常生产
申请后制程治工具
结束
20
四:防焊涨缩异常处理方法及步骤
4.2. 防焊板子涨缩量测方法
X
Y
示意图
实物图
21
四:防焊涨缩异常处理方法及步骤
4-3. 防焊板子涨缩比例计算方法:
CAM规格*比例 板子 X (D) 涨缩 (E=D-C) Y (D1) 涨缩 (E=D1-C1) X Y (C=A*A1) (C1=B*B1) 14.9901 14.9901 CAM规格 X (A) Y (B) 生产底片比例 X (A1) Y (B1)
注意事项: 1:必须以中心为原点 2:板子开几槽就在板子三孔处加几个孔 3:板子开几槽就命名为几AO
15
二:钻孔涨缩异常处理方法及步骤
b:首件制作OK后,申请后制程治工具
注意事项: 1:钻带申请时板子三孔加几孔为几孔,后制程底片就命名为几孔 2:量产申请半自动菲林,量产超过一百PNL申请全自动菲林, 3:样品申请后制程治工具时,旧治工具要构其他,并注明回收
底片
网版
25
六:压合前后涨缩量测数据收集
压合前后涨缩数据收集
收文单位: □ 研发 客户料号: □样品: 设计厂牌: 叠构: 压合板厚: 内层补偿系数: 压合程式: 设计靶据: X : L2-L3 Y □ 品保 □ 品管 □制作 厂内料号: □量产: 发料厂牌: □其他
Y: 蚀刻后量测值 靶 X
□混压,混压料号: 靶: 量测人: L4-L5 Y 压合后量测 板子 Y
量测靶间距Y -2mil≦Y≦2mil 2mil﹤Y≦6mil 6mil﹤Y≦10mil -10mil≦Y﹤-6mi
铸件缩孔和缩松缺陷十点分析

铸件缩孔和缩松缺陷十点分析缩孔和缩松都是铸造生产中常见的铸件缺陷。
缩孔是铸件在冷凝过程中收缩,得不到金属溶液的补充而产生的孔洞,形状不规则,孔壁粗糙,一般位于铸件的热节处。
缩孔和气孔在外表上往往极为相似,经常容易混淆。
一般来说,气孔的内壁是平滑的,而缩孔的内壁则呈枝状结晶的末梢状。
缩松是铸件最后凝固的区域没有得到金属溶液的补缩而形成分散和细小的小孔,常出现在铸件的较厚截面以及厚薄截面交接处或热节点上。
缩松的分布面积要比缩孔大得多,往往隐藏于铸件的内部,有时肉眼察觉不到。
缩孔和缩松在铸件废品中占有较大的比例,必须引起足够的重视,以提高铸件合格率。
笔者结合多年的生产实践经验,谈谈铸件缩孔和缩松的产生原因及其防止措施。
1.铸件和模样设计(1)铸件截面尺寸变化过大。
如果在设计中铸件截面尺寸变化过大,薄截面的冷却速度比相邻厚截面的冷凝速度要快得多,这样就很难实现铸件的顺序凝固,同时也难于进行补缩。
设计时要尽量避免这种情况,否则应采用冷铁,以实现铸件的顺序凝固并利于补缩。
(2)铸件断面过厚,如果没有采取相应措施对其进行补缩,会因补缩不良形成缩孔。
(3)圆角太小。
铸件的凹角圆角半径太小,会导致型砂传热能力降低,凝固速度下降,同时由于该处型砂受热作用强,发气压力大,析出的气体可向未凝固的金属液渗入,导致铸件产生气缩孔。
(4)圆角太大。
圆角太大,则圆角部分就成了厚截面,如果相邻的截面较薄,就难以得到有效的补缩,造成补缩不良2.模样(1)模样或芯盒磨损致使铸件截面减薄,导致铸件截面厚度减薄而妨碍补缩。
(2)模样尺寸不当或模样结构不当,导致铸件截面过厚或过薄。
设计时应注意控制模样的厚度,尽量使邻近较厚截面的薄截面保持最大的厚度。
3.砂箱(1)上箱太浅。
生产中为了节省型砂用量或为了降低砂箱和造型成本而使用高度不够的上箱,这是造成缩松缺陷的常见原因。
上箱太浅,会降低金属液的静压力,以致难以进行补缩,补缩压力不够,会导致产生缩松或缩孔,或二者兼有之。
PCB生产过程中产生变形的原因及改善
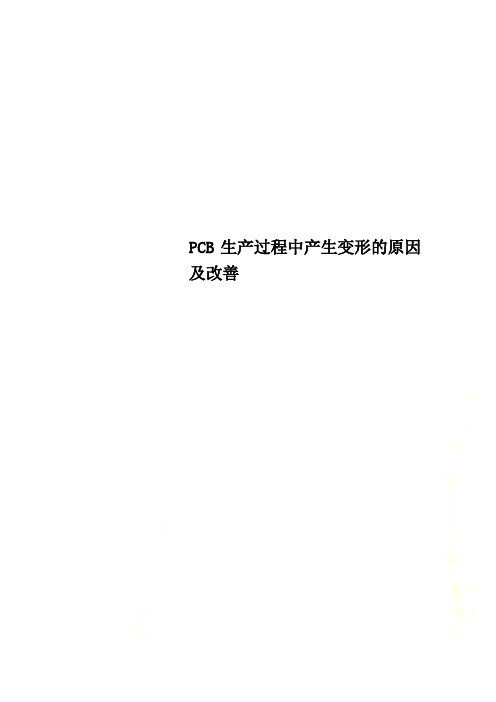
PCB生产过程中产生变形的原因及改善PCB生产过程中产生变形的原因及改善(刘海龙)(深南电路有限公司,广东深圳518053)摘要随着表面安装和芯片安装时代的到来,下游客户对电路板平整度的要求必定越来越严格.本文围绕印制电路板设备和制造的全流程,重点研究了压合、阻焊、整平、出货前校平等制程对板件变形的影响。
并根据试验结果和生产经验提出了一些有效的控制板件变形的方法。
1前言在自动化表面贴装线上,电路板若不平整,会引起定位不准,元器件无法插装或贴装到板子的孔和表面贴装焊盘上,甚至会撞坏自动插装机。
装上元器件的电路板焊接后发生弯曲,元件脚很难剪平整齐。
板子也无法装到机箱或机内的插座上,所以,装配厂碰到板翘同样是十分烦恼。
目前的表面贴装技术正在朝着高精度、高速度、智能化方向发展,这就对做为各种元器件家园的PCB板提出了更高的平整度要求。
在IPC标准中特别指出带有表面贴装器件的PCB板允许的最大变形量为0.75%,没有表面贴装的PCB板允许的最大变形量为1.5%。
实际上,为满足高精度和高速度贴装的需求,部分电子装联厂家对变形量的要求更加严格,如我公司有多个客户要求允许的最大变形量为0.5%,甚至有个别客户要求0.3%。
PCB板由铜箔、树脂、玻璃布等材料组成,各材料物理和化学性能均不相同,压合在一起后必然会产生热应力残留,导致变形。
同时在PCB的加工过程中,会经过高温、机械切削、湿处理等各种流程,也会对板件变形产生重要影响,总之可以导致PCB板变形的原因复杂多样,如何减少或消除由于材料特性不同或者加工引起的变形,成为PCB制造商面临的最复杂问题之一。
2变形产生原因分析PCB板的变形需要从材料、结构、图形分布、加工制程等几个方面进行研究,本文将对可能产生变形的各种原因和改善方法进行分析和阐述。
2.1压合材料、结构、图形对板件变形的响分析PCB板由芯板和半固化片以及外层铜箔压合而成,其中芯板与铜箔在压合时受热变形,变形量取决于两种材料的热膨胀系数(CTE),铜箔的热膨胀系数(CTE)为17X10-6左右,而普通FR-4基材在Tg点下Z向CTE为(50~70)X10-6,TG点以上为(250~350)X10-6,X向CTE由于玻璃布存在,一般与铜箔类似。
汽车覆盖件拉伸起皱和开裂现象分析及控制措施

汽车覆盖件拉伸起皱和开裂现象分析及控制措施汽车覆盖件是指车体外部的保护罩、护板、保险杠、车窗边框、车门外套等部件,这些零件的功能是保护车身结构、增加车体整体美感和减少空气阻力。
然而,在汽车生产和使用过程中,这些覆盖件可能会出现拉伸起皱和开裂的现象。
本文将分析汽车覆盖件拉伸起皱和开裂的原因,并提出相应的控制措施。
首先,汽车覆盖件拉伸起皱和开裂的原因主要有以下几点。
1.材料质量差:汽车覆盖件的材料包括金属、塑料、橡胶等。
如果材料质量有缺陷,如材料硬度不足、脆性大、不耐老化等,就容易出现拉伸起皱和开裂现象。
2.制造工艺不当:汽车覆盖件的制造过程中,如果操作不当、工艺参数不合理,例如成型温度过高或过低、成型速度过快或过慢、冷却方式不当等,都会导致覆盖件的形变和开裂。
3.加工应力过大:在覆盖件的制造过程中,可能涉及到很多的压力和挤压过程,如果加工应力过大,就会导致覆盖件的强度降低,易发生起皱和开裂。
4.环境因素:汽车覆盖件在使用过程中,会受到各种环境因素的影响,包括温度变化、大气湿度、紫外线照射等。
这些因素会导致覆盖件材料的膨胀和收缩,引起拉伸起皱和开裂。
针对上述问题,可以采取以下控制措施来避免汽车覆盖件拉伸起皱和开裂。
1.优化材料选择:选择质量好、性能稳定的材料,确保材料硬度、韧性等物理性能符合要求。
此外,还可以使用耐老化、耐候性好的材料,提高覆盖件的耐用性。
2.优化制造工艺:合理控制制造过程中的温度、速度、压力等参数,确保覆盖件的成型质量。
可以使用模具加热、冷却等手段来控制成型温度和冷却速度,防止拉伸起皱和开裂。
3.优化加工工艺:合理控制加工过程中的压力和挤压过程,避免加工应力过大。
可以采用分次加工、轻加工等方法来减小加工应力,提高覆盖件的强度和稳定性。
4.增加外部保护措施:可以在覆盖件表面涂覆保护涂层,增加抗紫外线和防水性能,预防覆盖件的老化和开裂。
此外,可以增加覆盖件的厚度和加强结构设计,提高其抗拉伸能力。
菲林涨缩不良报告
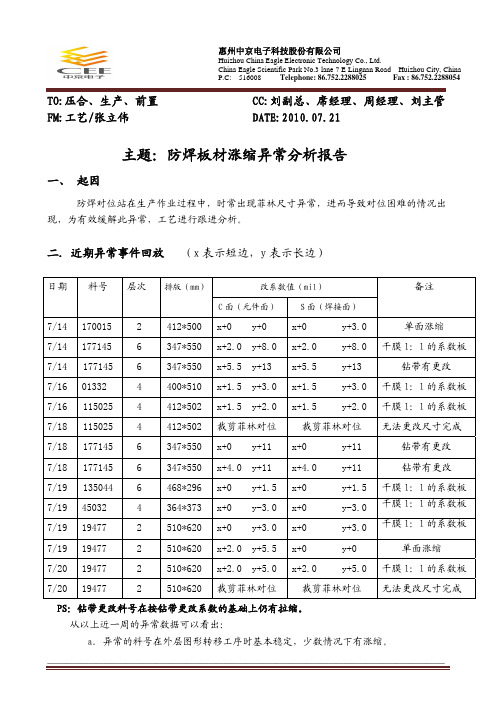
Fa同一个料号有多个拉缩系数,有拉长或缩短,如 115025、177145、19477, 每次来料均要更改系数方可生产。
c. 部分料号存在单面涨缩,即某一面用 1:1 菲林可以生产,另一面要更改系数生产。 d. 个别料号有时无法更改菲林尺寸,如 19477,主要原因为两边可以对正,但中间
7/20 19477
2 510*620 裁剪菲林对位 裁剪菲林对位 无法更改尺寸完成
PS:钻带更改料号在按钻带更改系数的基础上仍有拉缩。 从以上近一周的异常数据可以看出: a. 异常的料号在外层图形转移工序时基本稳定,少数情况下有涨缩。
__________________________________________________________________________________________________________
钻带有更改
7/16 01332
4 400*510 x+1.5 y+3.0 x+1.5 y+3.0 干膜 1:1 的系数板
7/16 115025 4 412*502 x+1.5 y+2.0 x+1.5 y+2.0 干膜 1:1 的系数板
7/18 115025 4 412*502 裁剪菲林对位 裁剪菲林对位 无法更改尺寸完成
Huizhou China Eagle Electronic Technology Co., Ltd.
China Eagle Scientific Park No.3 lane 7 E Lingnan Road Huizhou City, China
P.C: 516008 Telephone: 86.752.2288025
Fax : 86.752.2288054
产品异常分析报告(两篇)
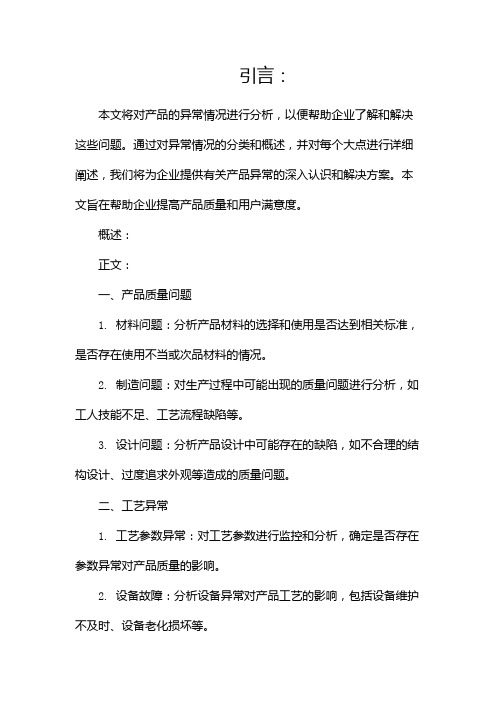
引言:本文将对产品的异常情况进行分析,以便帮助企业了解和解决这些问题。
通过对异常情况的分类和概述,并对每个大点进行详细阐述,我们将为企业提供有关产品异常的深入认识和解决方案。
本文旨在帮助企业提高产品质量和用户满意度。
概述:正文:一、产品质量问题1. 材料问题:分析产品材料的选择和使用是否达到相关标准,是否存在使用不当或次品材料的情况。
2. 制造问题:对生产过程中可能出现的质量问题进行分析,如工人技能不足、工艺流程缺陷等。
3. 设计问题:分析产品设计中可能存在的缺陷,如不合理的结构设计、过度追求外观等造成的质量问题。
二、工艺异常1. 工艺参数异常:对工艺参数进行监控和分析,确定是否存在参数异常对产品质量的影响。
2. 设备故障:分析设备异常对产品工艺的影响,包括设备维护不及时、设备老化损坏等。
3. 生产计划异常:分析生产计划和排产是否合理,是否存在过程不连贯、工艺不匹配等问题。
三、运输损坏1. 包装问题:分析产品包装是否符合运输需求,是否存在包装材料不足、包装方法不当等问题。
2. 运输方式:分析产品在运输过程中可能遇到的振动、震动、温度变化等问题对产品影响。
3. 运输管理:分析运输环节中是否存在人员管理不善、运输工具不合规等问题导致损坏。
四、用户误用1. 产品说明不清:分析产品说明书是否合理,是否清晰明了,是否存在遗漏或误导用户的信息。
2. 使用知识不足:对用户使用产品所需的知识和技巧进行分析,确定是否存在用户对产品了解不足的情况。
3. 操作误区:分析用户可能犯的操作误区,确定是否存在设计不合理导致用户误用的情况。
五、竞争对手攻击1. 产品仿冒:分析竞争对手是否存在仿制产品的情况,确定是否存在仿冒产品对市场影响的问题。
2. 产品破坏:分析竞争对手是否存在恶意破坏产品的行为,确定是否存在产品损坏的非自然原因。
3. 不实宣传:分析竞争对手是否存在虚假宣传、贴标等行为,确定是否存在通过误导用户来获得市场份额的情况。
拉延件起皱和开裂的分析及控制措施
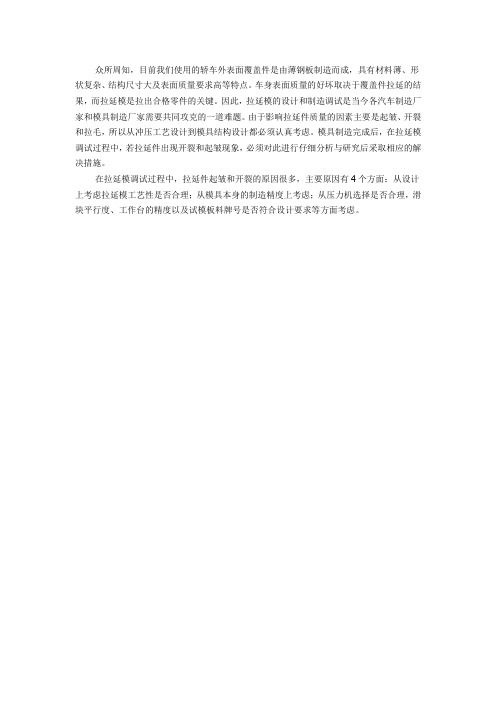
众所周知,目前我们使用的轿车外表面覆盖件是由薄钢板制造而成,具有材料薄、形状复杂、结构尺寸大及表面质量要求高等特点。
车身表面质量的好坏取决于覆盖件拉延的结果,而拉延模是拉出合格零件的关键。
因此,拉延模的设计和制造调试是当今各汽车制造厂家和模具制造厂家需要共同攻克的一道难题。
由于影响拉延件质量的因素主要是起皱、开裂和拉毛,所以从冲压工艺设计到模具结构设计都必须认真考虑。
模具制造完成后,在拉延模调试过程中,若拉延件出现开裂和起皱现象,必须对此进行仔细分析与研究后采取相应的解决措施。
在拉延模调试过程中,拉延件起皱和开裂的原因很多,主要原因有4个方面:从设计上考虑拉延模工艺性是否合理;从模具本身的制造精度上考虑;从压力机选择是否合理,滑块平行度、工作台的精度以及试模板料牌号是否符合设计要求等方面考虑。
冲压工艺对拉延件开裂和起皱的影响拉延件的工艺性是冲压工艺首先要考虑的问题,只有设计出合理的、工艺性好的拉延件,才能保证在拉延过程中不起皱、不开裂或少起皱、少开裂。
在设计拉延件时,不但要考虑冲压方向、冲压位置、压料面形状、拉延筋的形状及配置以及工艺补充部分等可变量的设计,还要合理地增加工艺补充部分,正确确定压料面。
各可变量设计之间又有相辅相成的关系,如何协调各变量的关系是成形技术的关键,不但要使之满足该工序的拉延,还要满足该工序冲模设计和制造工艺的需要,并给下道修边、整形工序创造有利条件。
拉延较复杂的拉延件成形性分析(CAE分析)是借助计算机软件来实现的,世界各大汽车制造厂家以及模具制造厂家都要借助于一种或几种板成形模拟软件来提高其成功率和确保模具制造周期。
国际上常用的软件主要有美国ETA公司的Dynaform、法国ESI集团的PAM系列软件以及德国AutoForm工程股份有限公司的AutoForm等。
成形模拟软件都有自己的专用软件包,很大程度上帮助了模具设计人员,显著减少模具开发设计时间及试模周期,不但具有良好的易用性,而且包括大量的智能化自动工具,可方便地求解各类板件成形问题,直观地看到成形过程中板料的裂纹、起皱、变薄、划痕、回弹分析以及评估板料的成形性能,从而为板金成形工艺以及模具设计提供了很大的帮助。
PCB电路板为什么会出现涨缩_如何应对PCB尺寸涨缩-华强pcb
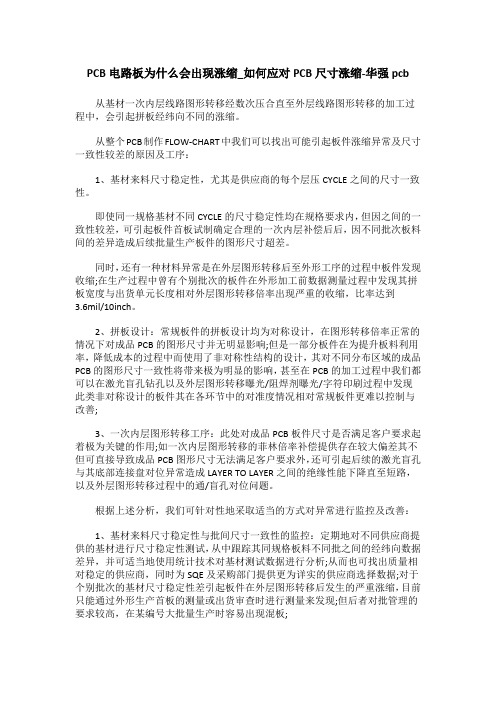
PCB电路板为什么会出现涨缩_如何应对PCB尺寸涨缩-华强pcb从基材一次内层线路图形转移经数次压合直至外层线路图形转移的加工过程中,会引起拼板经纬向不同的涨缩。
从整个PCB制作FLOW-CHART中我们可以找出可能引起板件涨缩异常及尺寸一致性较差的原因及工序:1、基材来料尺寸稳定性,尤其是供应商的每个层压CYCLE之间的尺寸一致性。
即使同一规格基材不同CYCLE的尺寸稳定性均在规格要求内,但因之间的一致性较差,可引起板件首板试制确定合理的一次内层补偿后后,因不同批次板料间的差异造成后续批量生产板件的图形尺寸超差。
同时,还有一种材料异常是在外层图形转移后至外形工序的过程中板件发现收缩;在生产过程中曾有个别批次的板件在外形加工前数据测量过程中发现其拼板宽度与出货单元长度相对外层图形转移倍率出现严重的收缩,比率达到3.6mil/10inch。
2、拼板设计:常规板件的拼板设计均为对称设计,在图形转移倍率正常的情况下对成品PCB的图形尺寸并无明显影响;但是一部分板件在为提升板料利用率,降低成本的过程中而使用了非对称性结构的设计,其对不同分布区域的成品PCB的图形尺寸一致性将带来极为明显的影响,甚至在PCB的加工过程中我们都可以在激光盲孔钻孔以及外层图形转移曝光/阻焊剂曝光/字符印刷过程中发现此类非对称设计的板件其在各环节中的对准度情况相对常规板件更难以控制与改善;3、一次内层图形转移工序:此处对成品PCB板件尺寸是否满足客户要求起着极为关键的作用;如一次内层图形转移的菲林倍率补偿提供存在较大偏差其不但可直接导致成品PCB图形尺寸无法满足客户要求外,还可引起后续的激光盲孔与其底部连接盘对位异常造成LAYER TO LAYER之间的绝缘性能下降直至短路,以及外层图形转移过程中的通/盲孔对位问题。
根据上述分析,我们可针对性地采取适当的方式对异常进行监控及改善:1、基材来料尺寸稳定性与批间尺寸一致性的监控:定期地对不同供应商提供的基材进行尺寸稳定性测试,从中跟踪其同规格板料不同批之间的经纬向数据差异,并可适当地使用统计技术对基材测试数据进行分析;从而也可找出质量相对稳定的供应商,同时为SQE及采购部门提供更为详实的供应商选择数据;对于个别批次的基材尺寸稳定性差引起板件在外层图形转移后发生的严重涨缩,目前只能通过外形生产首板的测量或出货审查时进行测量来发现;但后者对批管理的要求较高,在某编号大批量生产时容易出现混板;2、拼板设计方面应量采用对称结构的设计方案,使拼板内的各个出货单元涨缩保持相对一致;如可能,应与客户沟通建议其允许在板件的工艺边上以蚀刻/字符等标识方式将各出货单元在拼板内的位置进行具体标识;此方法在非对称方式设计的板件内效果将更明显,即使每拼板内因图形不对称引起各别单元出现尺寸超差,甚至是因此引起的局部盲孔底部连接异常亦可极为方便地确定异常单元并在出货前将其挑出处理,不至于流出造成客户封装异常而招致投诉;3、制作倍率首板,通过首板来科学地确定生产板件的一次内层图形转移倍率;在为降低生产成本而变更其它供应商基材或P片时,此点尤为重要;当发现有板件超出控制范围时应根据其单元管位孔是否为二次钻孔加工;如为常规加工流程板件则可根据实际情况放行至外层图形转移通过菲林倍率进行适当调整;如是二次钻孔板件,则对异常板件的处理需特别谨慎以确保成品板件的图形尺寸与标靶至管位孔(二次钻孔)距;附二次积层板件首板倍率收集清单;4、过程监控:利用外层或次外层板件在其层压后的X-RAY生产钻孔管位孔时所测量的板件内层标靶数据,分析其是否在控制范围内且与合格首板所收集的相应数据进行对比以判断板件尺寸是否有涨缩异常,下有附表可参考;经过理论计算,通常此处的倍率应控制在+/-0.025%以内才能满足常规板件的尺寸要求。
阀板零件低温试验后尺寸涨大故障分析
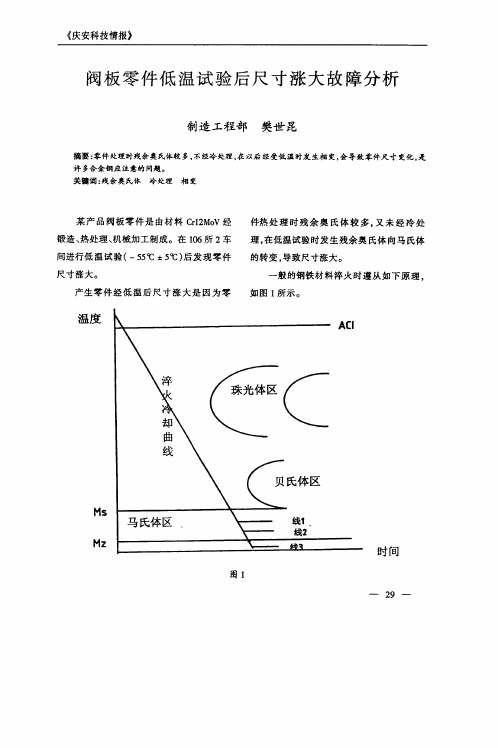
C C Ni Mo W r V A Ms
有 的可达 l —2 %。 0 o
当钢件 中的残 余奥 氏体 量 过 多时 , 采 可
用冷处 理 的方法 去 消除 。 冷 处理 实际 上 是淬 火 工 艺 的继 续 , 为 因
15 2. 0 2 5 2 6 8 5 l 5 l0 .6 l .6 0.4 0.8 0.5 1 8 0 0
钢 号 Cl M V r2 0
C s M C Mo V A 1 M i n r c s
20 90 3 8
15 4 0 2 1 3 .3 0.4 .5 0.5 .7 1 .4 0 5 2
I I I_
I
,
- l 1
体 的 体积 比奥 氏体 的体积 要 大 , 一般 可 以大 1 3 由不 同 的碳 含 量 决定 ) 所 以 奥 氏体 %( ,
C lM V是高 碳高 铬合 金 钢 , 身 的 Ms r2 o 本 和 M 温度 比较低 , z 由于成 分 的偏差 , 的马 它 氏体开 始转 变点 MS 的温 度在 10~20I范 5 5c =
围 内 变 动 , 图 2 和 图 3 所 示 的 两 种 如
. . 3
’
』
●
-
龟 电害 号 = 妄 求 萼 ÷
r
o
。
II : 1 1
fIiI l-l 由 . i I i I
图2
C lM V钢 , r2 o 化学 成分稍 有差 异 , 2的钢材 图
一
3 — O
《 庆安科技情报》
《 庆安科技情报》
阀板 零 件 低 温试 验后 尺 寸涨 大 故 障分 析
制 造 工程 部 樊世 昆
印制板涨缩研究

105PCB InformationMA Y 2021 NO.3经纬方向差异造成基板尺寸变化,由于剪切时未注意纤维方向,造成剪切应力残留在基板内,一旦释放,直接影响基板尺寸的收缩。
见图3。
基板表面铜箔部分被蚀刻掉对基板的变化限制,当应力消除时产生尺寸变化。
见图4。
刷板时由于采用压力过大,导致产生压拉应力造成基板变形。
见图5。
1.1 涨缩1.1.1 基板尺寸涨缩的原因印制板涨缩研究文/奥士康精密电路(惠州)有限公司 鲁永兴通常就是指PCB 制作流程中,其基材经过各制程受到温湿度影响及应力释放,吸湿而膨胀,脱湿而收缩以及释放应力越大,尺寸变化越大的尺寸涨缩过程。
通常我们说的尺寸涨缩分为基板和底片两种,见图1、图2。
【摘要】本文主要研究了印制板涨缩的管控,找出影响涨缩的因素进行改善以确保生产流畅。
【关键词】基板涨缩;底片涨缩;涨缩导致层偏;偏孔作者简介:鲁永兴,奥士康精密电路(惠州)有限公司流程工程师/体系工程师,主要从事厂内不良产品的判定与流程管控、体系策划。
获得证书如下:ISO14001:2015、ISO45001:2018、DOE、QCC、14QC、ISO9001:2015&IATF16949:2016、X-RAY、QRQC/知识产权管理、APQP&PPAP、VDA6.3、FMEA、中级电工证等。
0 PCB涨缩定义1 实验背景图1 基板图2 底片图3 经纬方向差异造成基板尺寸变化图5 刷板时由于采用压力过大,导致产生压拉应力造成基板变形图4 基板表面铜箔部分被蚀刻掉对基板的变化限制多层板在层压前,因基板有吸湿性,使薄基板或半固化片吸湿,造成尺寸稳定性差,基板中树脂未完全固化,导致尺寸变化。
1.1.2 底片尺寸涨缩的原因①底片从真空包装拆包后静置时间不足;②底片绘制完成后静置时间不足直接用于生产;③温湿度管控异常,造成菲林热缩冷涨,超出标准管控范围;④曝光机温度过高,曝光室无法维持恒温恒湿环2021年5月第3期106境,导致菲林涨缩变化。
- 1、下载文档前请自行甄别文档内容的完整性,平台不提供额外的编辑、内容补充、找答案等附加服务。
- 2、"仅部分预览"的文档,不可在线预览部分如存在完整性等问题,可反馈申请退款(可完整预览的文档不适用该条件!)。
- 3、如文档侵犯您的权益,请联系客服反馈,我们会尽快为您处理(人工客服工作时间:9:00-18:30)。
例:4082-2/5层,板厚0.69mm, 树脂磨板后 L:+6.2mil ,W :+3.5mil 线路磨板机:影响板件尺寸较小 例:4082-2/5层,板厚0.69mm, 线路磨板后 L:-0.5mil ,W :位参数 (线路/阻焊) X-RAY机分堆
法
拉扯/搓菲林 板件涨缩异常
Page 3
三、重要因素分析
?(一)物料 1、基板—联茂:IT-140、IT-158、IT-588
生益:S1141、S1000 台湾南亚:NP-140TL 上海南亚:NY-2150 宝得压合过期PP的基板 问题点:开料存在混用情况,不同基板与
Page 18
三、重要因素分析
?(四)方法 2、线路/阻焊曝光对位参数
问题点:如何设置参数,减少层间偏差, 减少对偏孔,减少阻焊开窗对 偏?
Page 19
三、重要因素分析
?(四)方法 3、 X-RAY打靶机分堆方法
问题点:分堆的公差±3mil是否合适? 分堆是否越细越好?
Page 20
三、重要因素分析
Page 8
三、重要因素分析
? (二)环境 4月2日AM9:00
线路3#曝光机 线路无尘房
菲林房
温度 湿度 温度 湿度 温度 湿度
18.5℃ 59.4% 20.9℃ 50.0 % 20.1℃ 59%
4月6日AM9:00 线路2#曝光机 温度 湿度 18.7℃ 57.2%
线路无尘房 温度 湿度 21.4℃ 51.0 %
相同PP搭配压板会导致涨缩异 常。
Page 4
三、重要因素分析
?(一)物料 2、PP
联茂:IT158 PP 超声:GW1500 PP
问题点:不同的PP与相同基板搭配压板也 会导致涨缩异常。
Page 5
三、重要因素分析
?(一)物料
3、菲林 富士菲林:SPR-7 ,24*26 、24*28 寸 HPR-7S ,26*30 寸
3、阻焊菲林多 ——外层线路菲林多,或预放倍率不准确
Page 2
二、板件涨缩异常鱼骨图分析
料 菲林
基板 PP
机 光绘机 贴保护膜机
二维机 压板机
X-RAY打靶机
人 线路曝光机
阻焊曝光机 线路/阻焊磨板机 树脂磨板机 钻孔机 (机 械/激光)
菲林房温湿度 线路房温湿度 阻焊房温湿度
曝光机温湿度 (线路/阻焊)
菲林房 温度 湿度 20.6℃ 58%
Page 9
三、重要因素分析
?(二)环境
4月19日PM15:00
阻焊无尘房
温度
湿度
21.4℃
54 %
菲林房
温度
湿度
21.3℃
56%
阻焊1#曝光机
阻焊2#曝光机
显示温度
湿度
显示温度
湿度
18.3℃
63%
18.4℃
61.5 %
注:1#曝光机实测台面温度:上 29 ℃,下30 ℃ 2#曝光机实测台面温度:上 31 ℃,下30 ℃
?(五)人 1、拉扯菲林/搓菲林
问题点:为何要拉扯菲林,或搓菲林? 拉扯菲林/搓菲林有何影响?
Page 21
四、改善措施
?(一)物料 1、基板: 厚度≤0.5mm,统一使用台湾南亚NP-140TL; 厚度﹥0.5mm,按台湾南亚NP-140TL、生益
?(三)设备 4、钻孔工序
激光钻机:钻孔精度±20um 机械钻机:钻孔精度±3mil 问题点:如何保证钻孔精度,减少偏孔,
减少重出钻带?
Page 17
三、重要因素分析
?(四)方法 1、基板是否烤板、及烤板参数
目前烤板参数:160℃*4小时 叠板厚度≤5cm
问题点:烤板参数是否合适,工序是否按 要求烤板,特别是叠板厚度?
问题点:如何使压合板件涨缩数据集中? 如何使每次压合的涨缩数据接近?
Page 15
三、重要因素分析
?(三)设备 3、压合工序
X-RAY打靶机:精度10um, 影响长短方向钻孔系数
问题点:如何使X-RAY打靶机测量板件 涨缩的系数准确? 2台X-RAY打靶机的数据相同?
Page 16
三、重要因素分析
问题点2:内层菲林涨缩管控± 2mil,上下菲林 对应边偏差 ≤1.5mil ,光绘后抽测, 返单板全测。公差± 2mil是否偏大? 抽测内层菲林,实际有超出± 2mil。
问题点 3:次外层、外层菲林不测量,直接生产 ,返单板亦没有量测。菲林长度是否 变化、是否变形?
Page 12
三、重要因素分析
问题点1:湿度恒定时,温度升高,菲林尺寸 膨胀,变化率0.001%/℃,可逆
问题点2:温度恒定时,湿度升高,菲林尺寸 膨胀,变化率0.001%/1% ,不可逆
Page 6
三、重要因素分析
?(二)环境 1、菲林房温湿度: 温度22±2℃
湿度 55±5% 2、线路暗房温湿度:同上 3、阻焊暗房温湿度:同上 问题点:线路、阻焊暗房和菲林房温湿度若
板件涨缩异常分析报告
一、板件涨缩异常表现 二、板件涨缩异常鱼骨图分析 三、重要因素分析 四、改善措施 五、结果验证
编制:罗旭 丘天冠 2011.4.21 Page 1
一、板件涨缩异常表现
1、次外层、外层钻孔钻带多 ——层压后涨缩不集中,X-RAY机分堆多
2、次外层、外层线路菲林多 ——钻带多,或预放倍率不准确
Page 10
三、重要因素分析
? (三)设备 1、光绘房
光绘机:光绘菲林精度 贴保护膜机:贴膜参数:速度、压力 二维机:测量精度 问题点 1:光绘机、二维机精度有偏差或贴保护
膜机参数有变化,将影响菲林尺寸。 光绘机、二维机精度有无定期校正?
Page 11
三、重要因素分析
? (三)设备 1、光绘房
三、重要因素分析
?(三)设备 2、线路、阻焊、字符工序
线路曝光机:影响层间对准精度、盲孔通 孔对准精度; 影响板件尺寸较小。
阻焊曝光机:影响阻焊开窗对准精度。 问题点:如何使预放菲林准确,减少重出
菲林?
Page 14
三、重要因素分析
?(三)设备 3、压合工序
压板机:影响板件的固化程度、应力和板 件涨缩数据
不一致,或超出控制范围,菲林尺 寸均受影响。
Page 7
三、重要因素分析
? (二)环境 4、线路曝光机温湿度:川宝机:温度 19±3℃
湿度55±10% 小野机:温度 20±2℃ 5、阻焊曝光机温湿度:川宝机:温度 22±4℃
湿度55±10% 问题点:线路、阻焊曝光机台面温度、曝光室湿度
和暗房、菲林房温湿度若不一致,或超出 控制范围,菲林尺寸均受影响。