Power Balance Control of Multi-motor Driving Belt System using
比亚迪电动豪华车Han EV说明书
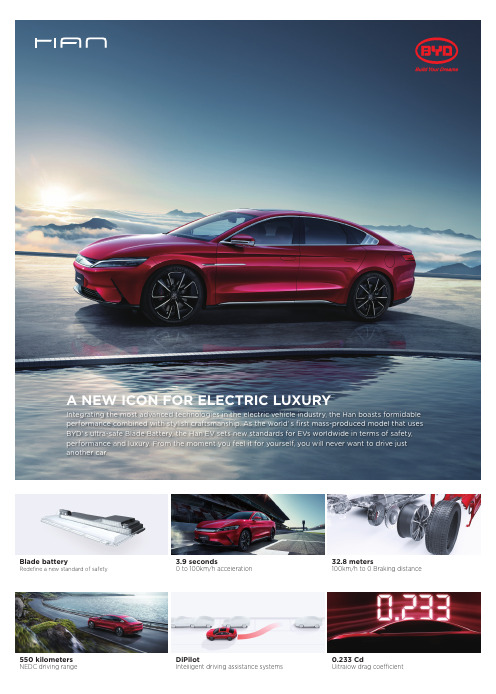
Disc
Configuration
New Energy
Charging booking system
●
Battery heater
●
Battery cooler
●
Wall-mounted charger (7kW)
○
On-board charger (7kW)
○
Portable charger (3 to 7)
●
Red interior
○
Driver & front passenger sun visor with make-up mirror & lamp
●
12.3-inch LCD combination instrument
●
Leather dashboard with real wood
●
Leather dashboard with real aluminum
DiPilot
Intelligent driving assistance systems
0.233 Cd
Ultralow drag coe cient
BYD Han EV SPECIFICATIONS & CONFIGURATIONS
Model
LUX
Basic Parameters
Length x Width x Height (mm)
Blade battery
Redefine a new standard of safety
3.9 seconds
0 to 100km/h acceleration
32.8 meters
100km/h to 0 Braking distance
电力工程专业英语词汇

电压互感器
Potential transformer
PT
电压互感器
Potential transformer
PT
电压互感器
Voltage transformer
电源变
Unit transformer
电子的、电子学的
Electronic
垫圈、补垫
Washer
调度、发送派遣
Dispatch
点
Point
电/液控制
Electric-hydraulic control
电厂
Power plant
电厂负荷因数
Plant load factor
电池
Battery
电池组、组、群
Cluster
电磁阀锁阀
Electrical lockout solenoid vlv
电的
Electric
电的、电气的
Electrical
Part per million
PPM
摆动
Tilting
扳手
Spanner
班,组,队,大队
brigade
班、组
Gang
搬运机、载波、带电粒子
carrier
办公室
Office
办公室、会议室
Chamber
磅
Pound
LB
磅/平方英寸(表压力)
Psig
磅/平方英寸(绝对压力)
Psia
饱和
Saturate
饱和条件、饱和状态
EXTR
抽汽逆止阀
Extraction check valve
EXTR CHK VLV
抽汽温度
Extr temp
电机学课程常用词汇英汉对照表

“电机学”课程常用词汇英汉对照表Aac excitation 交流励磁ac machine 交流电机active load 有功负载active power 有功功率active source 有功电源air gap 气隙air-gap fringing field 气隙边缘磁场air-gap inductances of distributed winding 分布绕组的气隙电感air-gap line 气隙线air-gap space-harmonic flux 气隙空间谐波磁通air-gap voltage 气隙电动势allowable temperature rise 允许温升alnico 阿尔尼科合金,磁钢alternator 交流发电机ammeter 安培表(或:电流表)amortisseur winding 阻尼绕组ampere turn 安匝anode 阳极apparent coercivity 视在矫顽(磁)力apparent power 视在功率approximate transformer equivalent circuit 变压器近似等效电路armature mmf wave 电枢磁动势波形armature phase-to-phase mutual inductance 电枢绕组相间互感armature wingding 电枢绕组armature-circuit resistance control 电枢回路电阻控制armature-frequency control 电枢频率控制armature-terminal voltage control 电枢端电压控制armature-winding heating 电枢绕组发热asynchronous torque 异步转矩autotransformer 自耦变压器auxiliary winding 辅(副)绕组axes of easy magnetization 易磁化方向Bbalanced three-phase system 对称三相系统base value 基值B-H curve B-H曲线blocked-rotor test 堵转试验Blondel two-reaction method Blondel双反应方法breadth factor 分布因数(或:分布系数)breakdown torque 临界转矩brush-contact loss 电刷接触损耗brush 电刷brushless dc motor,无刷直流电(动)机brushless excitation system,无刷励磁系统brushless motor,无刷电(动)机Ccantilever circuit 倒L型电路(或:悬臂电路)cantilever equivalent circuit 倒L型等效电路(或:悬臂等效电路)capability curve 容量曲线capacitative 容性capacitative load 容性负载capacitative power-factor correction 容性功率因数调节capacitor 电容(器)capacitor-start capacitor-run motor,电容启动运转电动机capacitor-start motor,电容启动电动机capacitor-type motor,电容型电动机castleation 裂极cathode 阴极ceramic magnet 陶瓷磁体ceramic permanent magnet material 陶瓷永久磁性材料charge density 电荷密度class B insulation B级绝缘class F insulation F级绝缘class H insulation H级绝缘coenergy 磁共能coercive force 矫顽(磁)力coercivity 矫顽(磁)力coil voltage phasor 线圈电势相量collector ring 集电环(也称:滑环)commutating pole 换向极commutation 换向、换流commutator 换向器compensating winding 补偿绕组compound 复励compound motor 复励电(动)机compound generator 复励发电机compounding curve 调整特性曲线(或:调节特性曲线)concentrated full-pitch winding 整距集中绕组conduction angle 导通角conductor cooling 导体冷却conservation of energy 能量守恒conservative system 保守系统constant-power drive 恒功率驱动constant-power regime 恒功率状态constant-torque drive 恒转矩驱动constant-torque regime 恒转矩状态continuous rating 连续定额control of dc motor 直流电动机控制control of induction motor 感应电动机控制control of synchronous motor 同步电动机控制conversion of ac to dc 交流到直流的变换(即:整流)conversion of dc to ac 直流到交流的变换(即:逆变)cooling 冷却core flux 铁心磁通core loss 铁心损耗(简称:铁损或铁耗)core-loss component 铁耗分量core-loss resistance 铁耗电阻(习惯叫:激磁电阻)core-type transformer 芯式变压器coupled-circuit viewpoint 耦合电路观点critical field resistance 临界场阻cross-magnetizing armature reaction 交轴(磁化)电枢反应current 电流current density 电流密度current-source inverter 电流源型逆变器current transformer 电流互感器(缩写为:CT)cutting-of-flux equation 切割磁力线公式cylindrical rotor 圆形转子(习惯称:隐极转子)Ddamper winding 阻尼绕组dc bus voltage 直流母线电压dc link current 直流环节电流dc machine 直流电机dc magnetization curve 直流磁化曲线(习惯称:基本磁化曲线)deep-bar rotor 深槽式转子definite-purpose machine 特种电机delayed commutation 延迟换向delta-delta connection D,d联结delta-Y connection D,y联结demagnetizing effect of cross-magnetizing armature reaction 交轴电枢反应的去磁作用differential compound 差复励differential compound generator 差复励发电机direct axis 直轴(也称:d轴或纵轴)direct-and quadrature-axis theory 直轴和交轴理论direct-axis air-gap flux 直轴气隙磁通direct-axis component 直轴分量direct-axis magnetizing reactance 直轴激磁电抗(习惯称:直轴电枢反应电抗)direct-axis permeance 直轴磁导direct-axis synchronous inductance 直轴同步电感direct-axis synchronous reactance 直轴同步电抗disk armature permanent-magnet seromotor 盘式电枢永磁伺服电(动)机distributed ac winding 分布式交流绕组distributed fractional-pitch winding 分布式分数节距绕组distributed winding 分布式绕组distribution transformer 配电变压器double-layer winding 双层绕组double-squirrel-cage rotor 双笼型转子dqO transformation dq0变换dynamic equation 动态方程Eeddy current 涡流eddy-current loss 涡流损耗effective permeability 有效磁导率effective value 有效值efficiency 效率electric field intensity 电场强度electric machine 电机electric machinery 电机electrical degree 电角度electrical radian 电弧度electromagnetic power 电磁功率electromagnetic relay 电磁继电器electromechanical-energy-conversion principle 机电能量转换原理electromotive force 电(动)势(缩写为:emf)emf 电(动)势(为electromotive force的缩写)end effect 端部效应end-turn flux 端部漏磁通energy balance 能量平衡energy method 能量法equivalent circuit 等效电路equivalent series impedance 等效串联阻抗equivalent series reactance 等效串联电阻equivalent series resistance 等效串联电抗equivalent-T circuit T型等效电路excitation 励磁、激磁excitation branch 激磁支路excitation phenomena 激磁现象excitation system 励磁系统exciter 励磁机exciting component 激磁分量exciting current 激磁电流exciting impedance 激磁阻抗FFaraday’s law 法拉第定律ferrite 铁氧体ferrite magnet 铁氧体磁体(即:陶瓷永久磁性材料)ferromagnetic material 铁磁材料fictitious winding 虚拟线圈field axis 磁场轴线field-current control 励磁电流控制field-current waveform 励磁电流波形field-oriented control 磁场定向控制field-resistance line 场阻线finite-element method 有限元法first law of thermodynamics 热力学第一定律flat-compounded 平复励flux 磁通(量)flux linkage 磁链force density 力密度forced commutation 强迫换流Fourier series 傅立叶级数four-phase system 四相系统four-pole dc machine 四极直流电机four-pole single-phase synchronous generator 四极单相同步发电机four-pole synchronous-reluctance motor 四极同步磁阻电动机fractional-horsepower motor 分马力电动机fractional slip 转差率fractional-pitch coil 分数节距线圈full load 满载full-pitch coil 整距线圈fundamental 基波Ggeneral-purpose motor 通用电动机generated voltage 感应电势generator 发电机grain-oriented steel 有取向钢grain-oriented electrical steel 有取向电工钢gross motion 蠕动Hhard magnetic material 硬磁材料harmonic 谐波heating 发热high-voltage side 高压侧hunting transient 瞬态猎振hybrid stepping motor 混合步进电动机hydraulic turbine 水轮机hydrogen cooling 氢冷hydro station 水电站hydropower station 水电站hysteresis effect 磁滞效应hysteresis loop 磁滞回线hysteresis loss 磁滞损耗hysteresis motor 磁滞电动机Iideal current transformer 理想电流互感器ideal potential transformer 理想电压互感器ideal transformer 理想变压器idealized synchronous machine 理想化同步电机IEEE (美国)电气电子工程师协会(为Institute of Electrical and Electronics Engineers的缩写)impedance 阻抗indirectly cooled bar 间接冷却线棒induced voltage 感应电压inductance 电感inductance machine 感应电机inductance-motor speed-torque characteristic 感应电机的速度转矩特性inductive 感性inductive load 感性负载infinite bus 无穷大母线inner cooling 内冷instantaneous power 瞬时功率Institute of Electrical and Electronics Engineers (美国)电气电子工程师协会(缩写为:IEEE)instrumentation transformer 仪用变压器insulating varnish 绝缘漆insulation 绝缘insulation life test 绝缘寿命试验integral-horsepower dc motor 整数马力直流电动机internal voltage 内电动势interpole 中间极(即:换向极)inversion 逆变inverter 逆变器I2R loss 电阻损耗(即:铜耗,也称:欧姆损耗)iron-core transformer 铁心变压器Kkilovar 千乏(缩写为:kvar)Llagging 滞后leading 超前leakage field 漏磁场leakage flux 漏磁通leakage inductance 漏电感leakage reactance 漏电抗linear commutation 线性换向linear machine 直线电机linearization 线性化line-to-line voltage 线电压line-to-neutral voltage 相电压load component 负载分量load loss 负载损耗long-shunt connection 长并励连接loss of synchronism 失步loss 损耗lossless-energy-storage system 无损电场储能系统low-voltage side 低压侧Mmachine efficiency 电机效率machine loss 电机损耗machine rating 电机定额magnetic circuit 磁路magnetic circuit model 磁路模型magnetic field intensity 磁场强度magnetic field viewpoint 磁场观点magnetic-field electromechanical energy conversion device 基于磁场的机电能量转换装置magnetic fields in rotating machinery 旋转电机中的磁场magnetic flux 磁通(量)magnetic flux density 磁通密度magnetic material 磁性材料magnetic hysteresis 磁滞magnetic permeability 磁导率magnetic saturation 磁饱和magnetic stored energy 磁储能magnetization curve 磁化曲线magnetizing current 磁化电流magnetizing inductance 激磁电感magnetizing reactance 激磁电抗magnetizing resistance 激磁电阻magnetomotive force 磁(动)势(缩写为:mmf)main-field mmf 主极磁势maximum electromechanical torque 最大电机转矩maximum energy product 最大磁能积mechanical loss 机械损耗megavar 兆乏(缩写为:Mvar)minor hysteresis loop 局部磁滞回线mmf 磁势(为magnetomotive force的缩写)mmf drop 磁势降mmf wave磁势波形motor size 电机规格motorette 电机模型motor 电(动)机multicircuit transformer 多绕组变压器multiply-excited magnetic field system 多边励磁磁场系统multi-stack variable-reluctance stepping motor 多段变磁阻步进电动机multiwinding transformer 多绕组变压器mutual flux 互磁通(习惯称:主磁通)mutual inductance 互感Nnameplate 铭牌negative excitation 反向励磁(或:负励磁)negative sequence 负(相)序neodymium-iron-boron 钕-铁-硼no-load 空载(或:无载)no-load magnetization characteristic 空载磁化特性no-load rotational loss 空载损耗no-load test 空载试验nominal characteristic 标称值(即:额定值)nonoriented electrical steel 无取向电工钢nonoriented steel 无取向钢nonuniform air gap 不均匀气隙normal magnetization curve 基本磁化曲线(也称:直流磁化曲线)nonsalient-pole 隐极nuclear station 核电站OOhmic loss 欧姆损耗(习惯称:电阻损耗、铜耗)open-circuit characteristic 开路特性open-circuit core loss 开路铁心损耗open-circuit core-loss curve 开路铁心损耗曲线open-circuit test 开路试验open-circuited secondary二次侧开路open-delta connection 开口三角形联结opposite phase sequence 相反相序overexcited 过励(磁的)P permanent magnet 永磁体permanent-magnet ac motor 永磁交流电(动)机permanent-magnet dc machine 永磁直流电机permanent-magnet stepping motor 永磁步进电(动)机permanent-split-capacitor motor 永久裂相电容电动机permeability 磁导率permeance 磁导per-unit system 标幺值体系phase 相phase order 相序phase sequence 相序phasor 相量phasor diagram 相量图pitch factor 节距因数(或:节距系数、短距系数)pole-changing motor 变极电动机pole-face winding 极面绕组(习惯称:补偿绕组)polyphase induction machine 多相感应电机polyphase mmf 多相绕组磁动势polyphase synchronous machine多相同步电机polyphase system 多相系统positive sequence 正(相)序potential transformer 电压互感器(缩写为:PT)power 功率power angle 功率角power electronics 电力电子(学)power factor 功率因数power switch 电力电子开关power-angle characteristic 功角特性power-factor angle 功率因数角power triangle 功率三角形primary 一次侧(或:原方、原边、初级)primary leakage inductance一次侧绕组漏电感primary leakage reactance 一次侧绕组漏电抗primary resistance一次侧绕组电阻prime mover 原动机projecting pole 凸极pulling out of step 失步pull-out torque 临界转矩pulse-width-modulated voltage-source inverter 脉宽调制电压型逆变器pulse-width modulation 脉宽调制(缩写为:PWM)Qquadrature axis 交轴(也称:q轴、横轴)quadrature-axis air-gap flux交轴气隙磁通quadrature-axis component 交轴分量quadrature-axis magnetizing reactance 交轴激磁电抗(习惯称:交轴电枢反应电抗)quadrature-axis synchronous inductance 交轴同步电感quadrature-axis synchronous reactance交轴同步电抗Rrating of machinery 电机定额ratio of transformation 变比reactance 电抗reactance voltage 电抗电压reactive load 无功负载reactive power 无功功率reactive source 无功电源reactor 电抗(器)real power 有功功率recoil line 回复线recoil permeability 回复磁导率rectification 整流reference direction 参考方向referring 折算(或:归算)regenerating 再生reluctance 磁阻remanent magnetization 剩磁residual flux density剩磁residual magnetism 剩磁resistor 电阻(器)resistance 电阻resistance commutation 电阻换向resultant core flux 合成铁心磁通revolving-field theory 旋转磁场理论right-hand rule 右手定则rms (value) 有效(值)(rms为root-mean-square的缩写)rms-kW method 有效值kW方法rotor 转子rotor self inductance 转子自感rotor-resistance control 转子电阻控制run winding 运行绕组Ssalient pole 凸极salient-pole synchronous machine凸极同步电机samarium-cobalt 钐-钴saturated 饱和的saturation 饱和saturation curve 饱和曲线sawtooth armature mmf wave 锯齿形电枢磁势波sawtooth waveform 锯齿波形Scott connection 斯科特联结secondary 二次侧(或:副边、副方、次级)secondary leakage inductance二次侧漏电感secondary leakage reactance二次侧漏感抗secondary resistance二次侧电阻self-excitation 自励(或:自激)self-excited generators 自励发电机self-starting synchronous-reluctance motor 自启动同步磁阻电动机separately-excited generator 他励发电机separately-excited motor 他励电动机series motor 串励电动机series universal motor 通用串励电动机series-field diverter 串励绕组分流器service factor 运行系数(或:负载系数)shading coil 罩极线圈shared-pole inductance motor 罩极感应电动机shell-type transformer 壳式变压器short-circuit characteristic 短路特性short-circuit load loss 短路损耗short-circuit ratio 短路比(缩写为:SCR)short-circuit test 短路试验short-circuit secondary 二次侧短路short-shunt connection 短并励连接short-time rating 短时定额shunt motor 并励电动机shunted-armature method 并联电枢法silicon controlled rectifier 可控硅(缩写为:SCR)silicon-iron steel lamination 硅钢片single-line diagram 单线图single-phase system 单相系统single-phase winding space-fundamental air-gap mmf 单相绕组空间基波气隙磁势single-stack variable-reluctance stepping motor 单段变磁阻步进电动机singly-excited electromechanical system 单边励磁机电系统size of machine 电机规格slip 转差(或:滑差)slip frequency 转差频率slip ring 滑环(习惯称:集电环)slot-leakage flux 槽漏磁通snubber circuit 缓冲电路soft magnetic material 软磁材料space-fundamental air-gap flux 空间基波气隙磁通sparking 火花sparkless commutation 无火花换向special-purpose motor 特种电动机speed control 速度控制(或:调速)speed voltage 速度电势squired-cage induction motor 笼型感应电动机squired-cage rotor 笼型转子stabilizing winding 稳定绕组star connection 星形联结(即:Y联结)start winding 启动绕组starting capacitor 启动电容stator 定子stator inductance 定子电感stator winding定子绕组stator-to-rotor mutual inductance 定转子互感starter 启动器steady-state power-angle characteristic 稳态功角特性stepping motor 步进电动机stray load loss 负载杂散损耗stream-turbine generator 汽轮发电机switched-reluctance machine 开关磁阻电机(缩写为:SRM)symmetrical-component concept 对称分量法synchronous angular velocity 同步角速度synchronous condenser 同步补偿机synchronous generator capability curve 同步发电机容量曲线synchronous inductance 同步电感synchronous machine 同步电机synchronous reactance 同步电抗synchronous speed 同步速度synchronous-generator V curve 同步发电机V型曲线synchronous-machine equivalent circuit 同步电机等效电路Ttemperature rise 温升test 试验thermal station 火电站(或:热电站)Thevenin-equivalent circuit 戴维宁等效电路Thevenin-equivalent impedance 戴维宁等效阻抗Thevenin-equivalent stator impedance 戴维宁等效定子阻抗Thevenin-equivalent voltage 戴维宁等效电压Thevenin’s theory 戴维宁定理three-phase ac machine 三相交流电机three-phase circuit 三相电路three-phase connection 三相联结three-phase system 三相系统three-phase three-stack variable-reluctance stepping motor三相三段变磁阻步进电动机three-phase transformer 三相变压器three-phase transformer bank 三相变压器组three-phase transformer connection三相变压器联结torque 转矩torque angle 转矩角(或:矩角)torque constant 转矩常数torque control 转矩控制torque-angle characteristic矩角特性torque-angle curve 矩角曲线total ampere-turns 总安匝transducer 变换器transformer 变压器transformer equivalent circuit 变压器等效电路transformer reactance 变压器电抗transient reactance 瞬变电抗(或:暂态电抗)true power 有功功率turbine generator 汽轮发电机turbine-generator excitation system 汽轮发电机励磁系统two-phase permanent magnet stepping motor 两相永磁步进电动机two-phase system 两相系统two-pole cylindrical-rotor field winding 两极隐极转子励磁绕组two-pole single-phase synchronous generator 两极单相同步发电机two-pole three-phase generator两极三相发电机two-pole three-phase stator winding 两极三相定子绕组two-winding transformer 双绕组变压器three-winding transformer 三绕组变压器Uunbalanced operation of symmetrical two-phase machine 对称两相电机的不对称运行unbalanced three-phase system 不对称三相系统underconmmutation 欠换向(习惯称:延迟换向)underexcited 欠励uniform air gap 均匀气隙universal motor 通用电动机unsaturated synchronous reactance 不饱和同步电抗unsymmetrical two-phase induction machine 不对称两相感应电机VV connection V形联结(或:开口三角形联结)V curve V形曲线var 乏(或:无功伏安,为volt-ampere reactive的缩写)varmeter 无功功率表variable-reluctance machine 变磁阻电机(缩写为:VRM)vector control 矢量控制ventilating system 通风系统v-i characteristic v-i特性(或:伏安特性)voltage behind leakage reactance 即:air-gap voltagevoltage commutation 电势换向voltage ratio (电势)变比voltage regulation 电压调整率voltage-regulating system 电压调整系统voltage-source inverter 电压源型逆变器voltage transformer 电压互感器voltmeter 伏特表(或:电压表)Wwater-cooled bar 水冷线棒water-cooled rotor 水冷转子wattmeter 瓦特表(或:有功功率表)watthourmeter 电度表winding factor 绕组因数winding 绕组wound rotor 绕线转子wound-rotor motor 绕线转子电动机wye connection Y联结YY-delta connection Y,d联结Y-Y connection Y,y联结Zzero sequence 零(相)序zero-sequence component 零序分量zero-sequence inductance 零序阻抗。
美国Eaton公司产品说明书:Eaton LGC340035B22G型电子保护电路断路器
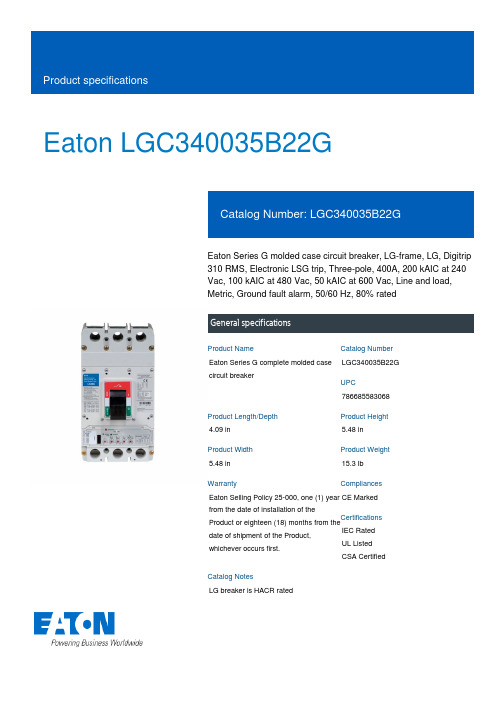
Eaton LGC340035B22GEaton Series G molded case circuit breaker, LG-frame, LG, Digitrip 310 RMS, Electronic LSG trip, Three-pole, 400A, 200 kAIC at 240 Vac, 100 kAIC at 480 Vac, 50 kAIC at 600 Vac, Line and load, Metric, Ground fault alarm, 50/60 Hz, 80% ratedGeneral specificationsEaton Series G complete molded case circuit breakerLGC340035B22G 7866855830684.09 in5.48 in 5.48 in 15.3 lb Eaton Selling Policy 25-000, one (1) year from the date of installation of theProduct or eighteen (18) months from thedate of shipment of the Product,whichever occurs first.CE Marked IEC RatedUL ListedCSA Certified LG breaker is HACR ratedProduct NameCatalog Number UPCProduct Length/Depth Product Height Product Width Product Weight WarrantyCompliancesCertificationsCatalog Notes200 kAIC at 240 Vac 100 kAIC at 480 Vac 50 kAIC at 600 VacLG80% rated400 AThree-poleSeries GMetricComplete breakerLG50 to 60 HzComplete breakerGround fault alarmLine and loadElectronic LSG Application of Multi-Wire Terminals for Molded Case Circuit Breakers Application of Tap Rules to Molded Case Breaker TerminalsCircuit breaker motor operators product aidCurrent limiting molded case circuit breaker module for series G, JG and CL310+ MCCB product family pocket folderPlug-in adapters for molded case circuit breakers product aidMotor protection circuit breakers product aidPower metering and monitoring with Modbus RTU product aidSeries G MCCB quick selectorMolded case circuit breakers providing higher levels of selective coordination product aidStrandAble terminals product aidMulti-wire lugs product aidHigh performance operating handles for Series G circuit breakers product aidCurrent limiting molded case circuit breaker module product aid Comprehensive circuit protection for control panel applicationsJ-Frame 310+ and L-Frame 310+ Molded-case circuit breakers Breaker service centersEaton's Volume 4—Circuit ProtectionMolded case circuit breakers catalogInstallation Instructions for Series G L-Frame Circuit BreakersEaton Specification Sheet - LGC340035B22GMOEM MCCB product selection guideL-Frame 310+ Molded-case circuit breakers 100A-600ANG and ND-Frame molded case circuit breakersInterrupt ratingFrameRatingAmperage Rating Number of polesSeriesMounting hardwareTypeCircuit breaker type Frequency ratingCircuit breaker frame type Alarm lockoutTerminalsTrip Type Application notesBrochuresCatalogsInstallation instructions Specifications and datasheetsEaton Corporation plc Eaton House30 Pembroke Road Dublin 4, Ireland © 2023 Eaton. All Rights Reserved. Eaton is a registered trademark.All other trademarks areproperty of their respectiveowners./socialmedia。
连续电驱动四足机器人设计与分析
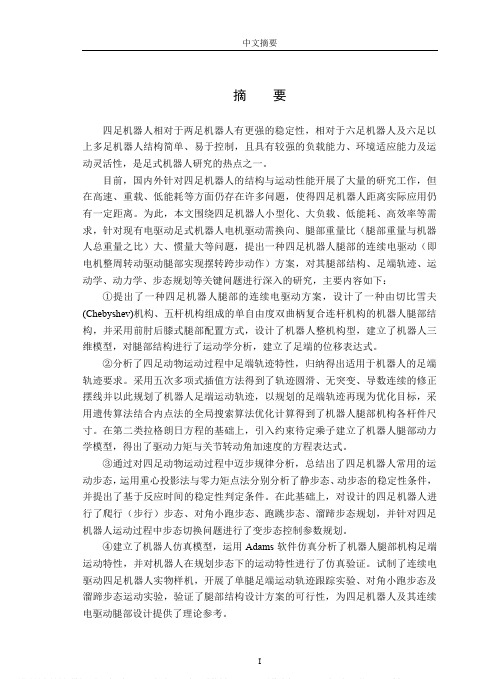
中文摘要摘要四足机器人相对于两足机器人有更强的稳定性,相对于六足机器人及六足以上多足机器人结构简单、易于控制,且具有较强的负载能力、环境适应能力及运动灵活性,是足式机器人研究的热点之一。
目前,国内外针对四足机器人的结构与运动性能开展了大量的研究工作,但在高速、重载、低能耗等方面仍存在许多问题,使得四足机器人距离实际应用仍有一定距离。
为此,本文围绕四足机器人小型化、大负载、低能耗、高效率等需求,针对现有电驱动足式机器人电机驱动需换向、腿部重量比(腿部重量与机器人总重量之比)大、惯量大等问题,提出一种四足机器人腿部的连续电驱动(即电机整周转动驱动腿部实现摆转跨步动作)方案,对其腿部结构、足端轨迹、运动学、动力学、步态规划等关键问题进行深入的研究,主要内容如下:①提出了一种四足机器人腿部的连续电驱动方案,设计了一种由切比雪夫(Chebyshev)机构、五杆机构组成的单自由度双曲柄复合连杆机构的机器人腿部结构,并采用前肘后膝式腿部配置方式,设计了机器人整机构型,建立了机器人三维模型,对腿部结构进行了运动学分析,建立了足端的位移表达式。
②分析了四足动物运动过程中足端轨迹特性,归纳得出适用于机器人的足端轨迹要求。
采用五次多项式插值方法得到了轨迹圆滑、无突变、导数连续的修正摆线并以此规划了机器人足端运动轨迹,以规划的足端轨迹再现为优化目标,采用遗传算法结合内点法的全局搜索算法优化计算得到了机器人腿部机构各杆件尺寸。
在第二类拉格朗日方程的基础上,引入约束待定乘子建立了机器人腿部动力学模型,得出了驱动力矩与关节转动角加速度的方程表达式。
③通过对四足动物运动过程中迈步规律分析,总结出了四足机器人常用的运动步态,运用重心投影法与零力矩点法分别分析了静步态、动步态的稳定性条件,并提出了基于反应时间的稳定性判定条件。
在此基础上,对设计的四足机器人进行了爬行(步行)步态、对角小跑步态、跑跳步态、溜蹄步态规划,并针对四足机器人运动过程中步态切换问题进行了变步态控制参数规划。
基于PLC 的多机驱动功率平衡研究

1引言随着自动化产业的持续发展,气力输送系统由于结构简单,在钢厂、电力行业领域得到了广泛应用,但由于动力消耗相对大,对运量大并且需要长距离输送的物料有一定的限制,逐步被带式输送机所代替,研究开发具有可变频启动、可变频调速、具有集中统一控制功能的带式输送机刻不容缓。
在采用变频器控制电机驱动的同时,保持功率平衡是系统长期稳定运行的必要条件。
对于不同的负载,每台变频器将分别根据其自行估算的转速补偿其滑差,以实现无偏差地达到给定转速。
但在实际运行过程中,由于每台电机和传动机构的不同造成的误差会导致出现某台电动机出力大,某台电动机出力小的情况,在比较极端的情况下,会出现部分电机处于电动运行模式,另一部分电机处于发电运行模式,使系统不能稳定运行,甚至短时间内就会对设备造成损害。
因此,类似这样的常规传动模式并不能满足系统的实际工作要求,在实际运行过程中,系统还要求各传动点电动机功率尽可能保持平衡。
2现场设备配置2.1变频器的选择多机驱动控制系统中,低速验带和大力矩重载启动必须通过有速度传感器的速度闭环来控制,否则就会出现低速脉动转矩,使皮带出现振颤现象,无法进行低速验带工作,也会降低启动力矩。
施耐德公司的“无速度传感器矢量控制技术”不仅解决低速验带和重载启动问题,又可使系统更简化,减少故障点,提高可靠性,使整个系统故障停运时间大大减少。
所以选择变频器时,可选择具有“无速度传感器矢量控制技术”的施耐德ATV320变频器。
2.2电机的选择每一组电机内部力矩平衡是多电机驱动要解决的最主要问题,负载变化、电机参数及皮带松紧等因素,都会对电机的速度和出力产生扰动性影响。
为了使系统稳定工作,几台电机必须保持一致的速度,同时,尽可能保持均匀的出力,异步电动机具有结构简单、运行可靠、价格低廉、维护方便等一系列优点,并且在调速性能方面完全可与直流电动机相媲美。
因此,可采用性价比更高的异步电机。
3系统控制原理本系统利用PLC实时调节变频器输入频率达到功率平基于PLC的多机驱动功率平衡研究Research on the Power Balance of Multi-Motor Driving Based on PLC陈晓川(福建龙净环保股份有限公司,福建龙岩364000)CHEN Xiao-chuan(Fujian Longking Co.,Ltd.,Longyan364000,China)【摘要】自PLC自动控制技术得到运用以来,不仅解放了劳动力,而且提高了生产效率。
LM2500+G4相关英文解释
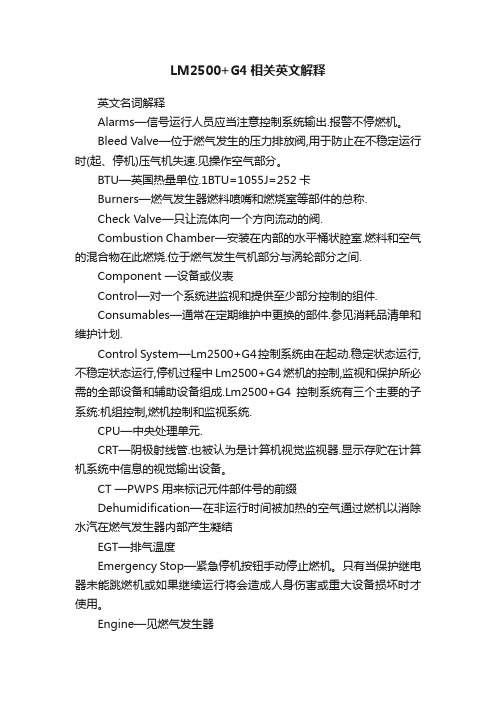
LM2500+G4相关英文解释英文名词解释Alarms—信号运行人员应当注意控制系统输出.报警不停燃机。
Bleed Valve—位于燃气发生的压力排放阀,用于防止在不稳定运行时(起、停机)压气机失速.见操作空气部分。
BTU—英国热量单位.1BTU=1055J=252卡Burners—燃气发生器燃料喷嘴和燃烧室等部件的总称.Check Valve—只让流体向一个方向流动的阀.Combustion Chamber—安装在内部的水平桶状腔室.燃料和空气的混合物在此燃烧.位于燃气发生气机部分与涡轮部分之间.Component —设备或仪表Control—对一个系统进监视和提供至少部分控制的组件.Consumables—通常在定期维护中更换的部件.参见消耗品清单和维护计划.Control System—Lm2500+G4控制系统由在起动.稳定状态运行,不稳定状态运行,停机过程中Lm2500+G4燃机的控制,监视和保护所必需的全部设备和辅助设备组成.Lm2500+G4控制系统有三个主要的子系统:机组控制,燃机控制和监视系统.CPU—中央处理单元.CRT—阴极射线管.也被认为是计算机视觉监视器.显示存贮在计算机系统中信息的视觉输出设备。
CT —PWPS用来标记元件部件号的前缀Dehumidification—在非运行时间被加热的空气通过燃机以消除水汽在燃气发生器内部产生凝结EGT—排气温度Emergency Stop—紧急停机按钮手动停止燃机。
只有当保护继电器未能跳燃机或如果继续运行将会造成人身伤害或重大设备损坏时才使用。
Engine—见燃气发生器Engine Control—控制燃机所有内部功能的计算机系统Fluid Hammer —当流体快速进入空管道时发出的锤击或振动声。
Free Turbine—动力涡轮Gas Generator—由动、静压气机(高压和低压)叶片,燃烧室,高、低压涡轮叶片等组成的内燃机。
Chroma 62000B系列模块化直流电源说明书

Chroma's new 62000B series of Modular DC Power Supplies offer many unique features for Burn-in and plating/electrolysis applications. The features include a N+1 redundancy, high power densities, hot-swappable maintenance, remote ON/OFF and programmable control via the CAN bus.The 62000B family offers 5 types of power module with ranging from 1V to 150V, current from 10A to 90A, and offers two mainframe type of six and three position. The six position mainframe can envelop in up to six power modules paralleled operation for 9KW power output. The 62000B can easily parallel up to fourteen mainframe to 120KW with current sharing and CAN bus control for bulk power applications.The Modular DC Power Supplies of 62000B are very cost effective with high power density and low current ripple. These instruments have be designed for burn-in applications such as the LCD panels, DC-DC converters, power inverters, notebook computers, battery chargers and many other types of electronic devices.Modern power factor correction circuitry is incorporated in 62000B providing an input power factor above 0.98 to meet the IEC requirements. This PFC correction circuity not only reduces the input current draw and to greatly reduce generation of input current harmonics. Optional graphic Soft Panels and CAN bus control allow for control and monitoring of the power system using an easy to use graphical interface.MODULAR DC POWER SUPPL Y MODEL 62000B SERIES1981Equipped with the functionality of N+1 redundancy and hot-swap, the 62000B Series of modular DC power supplies are most applicable for 24 hours non-stop applications such as the SMD plating production lines, as well as product life burn-in test for ITproducts like DC converters, LCD backlight inverters and routers.For continuous operation applications the modular hot-swap design allows engineers to replace the failure unit on-site without shutting down the entire system.M o d u l a r D C P o w e r S u p p l y f o r B u r n -i n & P l a t i n g A p p l i c a t i o n sThe 62000B modular power supplies are capable of providing high power output up to 120KW/2000A with minimal specification degradation via CSU(Control & Supervisor Unit). Each chassis is designed to accommodate a maximum of 9KW and include current sharing capability to ensure system stability. In addition, for convenient control of even large power systems, a CSU is provided to set and display output and protection circuits via a standard CAN bus communication protocol.Available Power Ratings A620007 CSU Key Features:■ Stand-alone controller for paralleled 62000B DC power for bulk power ■ Digital encoder knobs and function keys■ Simultaneous display of output voltage and current ■ Standard Analog programmable interface ■ Standard CAN Bus■ Optional Ethernet interface ■ User define I/O interfaceController Area Network (CAN) is a multicast shared, differential serial bus standard. CAN was specifically designed to be robust inelectromagnetically noisyenvironments and can utilize a differential balanced line like RS-485. Introduced by Bosch in 1986 for in-vehicle networks in cars, it is used in myriad applications including factory automation, building automation, aircraft and aerospace as well as in cars, trucks and buses. CAN bus replaced bulky wiring harnesses with a two-wire differential cable. CAN provides services at layers 1 and 2 of the OSI model and uses a broadcast method for placing frames on the wire. CAN provides low-speed, fault-tolerant transmission of 125 Kbps up to 40 meters, which can function over one wire if a short occurs. Transmission without fault tolerance is provided up to 1 Mbps and 40 meters, and distances up to 1 km are achieved with bit rates of 50 Kbps. Bit rates up to 1 Mbit/s are possible at network lengths below 40m. Decreasing the bit rate allows longer network distances (e.g. 125 kbit/s at 500 m).A620007 Control & Supervisor UnitFRONT PANEL 1. OUTPUT ENABLED LED 2. FAULT INDICATOR 3. OUTPUT VOLTAGE READOUT 4. VOLTAGE TRIMMER (1V-100%)5. OUTPUT CURRENT READOUT 6. CURRENT TRIMMER (1A-100%)7. OUTPUT ENABLE/DISABLE SWITCHREAR PANEL8. CURRENT SHARING CONNECTOR (FOR MAINFRAME)9. REMOTE SENSE CONNECTOR10. I/O CONNECTOR (INCLUDES REMOTE ON/OFF, DC OK, AUX POWER)11. CAN DIP ADDRESS SWITCH12. CAN BUS COMMUNICATIONS PORT (OPTIONAL)13. OUTPUT TERMINALS 14. AC INPUT TERMINAL BLOCKModel 62000B SeriesFRONT PANEL 1. OVP INDICATOR 2. VOLTAGE READOUT 3. OTP INDICATOR 4. AC-FAULT INDICATOR 5. CURRENT READOUT 6. MODULE ERROR INDICATOR 7. CV MODE INDICATOR 8. CC MODE INDICATOR9. ON/OFF ENABLE/DISABLE 10. V-SET BUTTON 11. I-SET BUTTON 12. OVP-SET BUTTON 13. I-MAX LIMITED SETTING 14. ROTARY15. AC ON/OFF SWITCH25SOFTPANELREAR PANEL 16. AC INPUT 17. ETHERNET 18. CAN ADDRESS SET 19. DIP SWITCHING FOR SYSTEM SETTING 20. I/O CONTROLINTERFACE INPUT 21. I/O CONTROL INTERFACE OUTPUT 22. TERMINAL-RESISTANCE(CAN)23. CAN BUS to PC 24. CAN BUS to MAINFRAME 25. EXT-V&I SENSE INPUT 26. APG CONTROLMain Operation Menu Program Sequence Function Basic Control Function for 30 ChannelsM o d e l 62000B S e r i e sType A - Control with CSU : User can control via APG, CAN Bus/ Ethernet, and front panel manual control for paralleled operation.Type B - Control without CSU : User can only control via CAN Bus for paralleled operation.Note: The SoftPanel can control four mainframes for paralleled operation.Type C - Control without CSU or PC : User can only control via remote on/off signal for paralleled operation.Note 1 : User can NOT adjust the output voltage when parallel the output.Note 2 : The output voltage will fixed in factory default voltage.Note 3 : If need to adjust the output voltage, please adjust when stand alone. Note 4 : Time delay from output enable until output stable: 10s max.CAN BusCAN BusCAN Bus〕Note*1 : For 50% step load variation with remote sense at maximum output voltageNote*2 : based on rise time of 100msNote*3 : Time for the output voltage to recover within 1% of its rated for a load changed of 25%Note*4 : Six Position Mainframe through CANORDERING INFORMATION62000B-3-1 : Three Position 62000B Mainframe62000B-6-1 : Six Position 62000B Mainframe62015B-15-90 : DC Power Supply Module, 15V/90A/1350W 62015B-30-50 : DC Power Supply Module, 30V/50A/1500W 62015B-60-25 : DC Power Supply Module, 60V/25A/1500W 62015B-80-18 : DC Power Supply Module, 80V/18A/1440W 62015B-150-10 : DC Power Supply Module, 150V/10A/1500W A620007 : Control & Supervisor UnitA620008 : CAN Bus Interface for mainframeA620010 : Rack Mounting Kit for mainframeA620011 : Ethernet Interface for CSUA620012 : AD-Link PCI 7841 CAN Bus CardA620013 : 19" Rack (23U) for 62000B SeriesA620014 : 19" Rack (41U) for 62000B SeriesA620016 : Rack Mounting Kit for CSUA620017 : Softpanel for 62000B SeriesA620018 : NI USB-8473 high-speed USB to CAN interfaceA620019 : USB Interface Control Box for mainframe & CSUA620020 : GPIB Interface Control Box for mainframe & CSU*A620021 : APG Interface Control Box for mainframe*A620022 : RS-485 Interface Control Box mainframe & CSU*Call for availability62000B-E-200908-PDFWorldwide Distribution and Service NetworkDistributed by:JAPANCHROMA JAPAN CORP. NARA Building 11F 2-2-8 Shinyokohama, Kouhokuku, Yokohama-shi, Kanagawa, 222-0033 JapanTel: +81-45-470-2285 Fax: +81-45-470-2287 http://www.chroma.co.jp U.S.A.CHROMA SYSTEMS SOLUTIONS, INC. 25612 Commercentre Drive, Lake Forest, CA 92630-8830 Tel: +1-949-600-6400 Fax: +1-949-600-6401Toll Free: +1-866-600-6050 E-mail:*******************Developed and Manufactured by : CHROMA ATE INC.致茂電子股份有限公司HEADQUARTERS No. 66, Hwa-Ya 1st Rd.,Hwa-Ya Technology Park, Kuei-Shan Hsiang,33383 Taoyuan County, Taiwan Tel: +886-3-327-9999 Fax: +886-3-327-8898 EUROPECHROMA ATE EUROPE B.V.Morsestraat 32, 6716 AH Ede,The NetherlandsTel: +31-318-648282Fax: +31-318-648288E-mail:****************** CHINACHROMA ELECTRONICS(SHENZHEN) CO., LTD.8F, No.4, Nanyou Tian AnIndustrial Estate, Shenzhen,China PC: 518052Tel: +86-755-2664-4598Fax: +86-755-2641-9620。
三相全波线性驱动电机驱动IC(LB11685AV)说明书

LB11685AVMonolithic Digital IC3‐phase Sensor Less Motor DriverOverviewThe LB11685A V is a three-phase full-wave current-linear-drive motor driver IC. It adopts a sensor less control system without the use of a Hall Effect device. For quieter operation, the LB11685A V features a current soft switching circuit and be optimal for driving the cooling fan motors used in refrigerators, etc.Functions•Three-phase Full-wave Linear Drive (Hall Sensor-less Method)•Built-in Current Limiter Circuit•Built-in Three-phase Output V oltage Control Circuit•Built-in Motor Lock Protection Circuit•Motor Lock Protection Detection Output•FG Output Made by Back EMF•Built-in Thermal Shut Down Circuit•Beat Lock Prevention CircuitSpecificationsMAXIMUM RATINGS (T A = 25°C)Parameter Symbol Conditions Ratings Unit Maximum SupplyVoltageV CC max19V Input AppliedVoltageV IN max−0.3 to V CC + 0.3VMaximum Output Current I O max(Note1)1.2AAllowable Power Dissipation P d max Mounted ona board (Note2)1.05WOperatingTemperatureT opr−40 to +85°CStorageTemperatureT stg−55 to +150°CJunctionTemperatureT j max150°CStresses exceeding those listed in the Maximum Ratings table may damage the device. If any of these limits are exceeded, device functionality should not be assumed, damage may occur and reliability may be affected.1.The I O is a peak value of motor-current.2.Specified board: 76.1mm × 114.3mm × 1.6mm, glass epoxy board. CAUTION:Absolute maximum ratings represent the value which cannot be exceeded for any length of time.CAUTION:Even when the device is used within the range of absolutemaximum ratings, as a result of continuous usage under hightemperature, high current, high voltage, or drastic temperaturechange, the reliability of the IC may be degraded. Pleasecontact us for the further details.SSOP24JCASE 565ASSee detailed ordering and shipping information on page7 of this data sheet.ORDERING INFORMATIONXXXXX = Specific Device CodeY = YearM = MonthDDD = Additional Traceability DataXXXXXXXXXXYMDDDMARKING DIAGRAMPIN ASSIGNMENT24VOUT UOUT123WOUT (NC)222(NC) (NC)321(NC) PGND420RF MCOM519V CC (NC)618REG SGND717VOH FG816FC1RD915FC2 (NC)1014C2 V CO1113C1CX12RECOMMENDED OPERATING CONDITIONS (T A = 25°C)Symbol Parameter Conditions Ratings Unit V CC Recommended Supply Voltage12.0V V CC op Operating Supply Voltage 4.5 to 18.0V Functional operation above the stresses listed in the Recommended Operating Ranges is not implied. Extended exposure to stresses beyond the Recommended Operating Ranges limits may affect device reliability.ELECTRICAL CHARACTERISTICS (T C = 25°C unless otherwise noted)Symbol Parameter Conditions Min Typ Max UnitI CC Supply Current FC1 = FC2 = 0V51020mAVREG Internal Regulate Voltage 3.0 3.3 3.6V VOSOUR Output Voltage (Source)I O = 0.8A (Note5) 1.3 1.7V VOSINK Output Voltage (Sink)I O = 0.8A (Note5)0.5 1.3V VOLIM Current Limiter0.2680.3000.332V VINCOM MCOM PinCommon-input Voltage Range0V CC − 2VICOM+MCOM PinSource Current for HysteresisMCOM = 7V3080m AICOM−MCOM PinSink Current for HysteresisMCOM = 7V3080m ARTCOM MCOM PinHysteresis Current RatioRTCOM = ICOM+ / ICOM−0.6 1.4I VCO VCO Input Bias Current V CO = 2.3V0.2m Af VCO min VCO Oscillation Minimum Frequency V CO = 2.1V, CX = 0.015m FDesign target (Note4)930Hzf VCO max VCO Oscillation Maximum Frequency V CO = 2.7V, CX = 0.015m FDesign target (Note4)8.6kHzI CX CX Charge/Discharge Current V CO = 2.5V, CX = 1.6V70100140m AD VCX CX Hysteresis Voltage0.350.550.75IC1(2)+C1 (C2) Charge Current V CO = 2.5V, C1(2) = 1.3V122028m A IC1(2)−C1 (C2) Discharge Current V CO = 2.5V, C1(2) = 1.3V122028m A RTC1(2)C1 (C2) Charge/Discharge Current Ratio RTC1(2) = IC1(2)+ / IC1(2)−0.8 1.0 1.2RTCCHG C1/C2 Charge Current Ratio RTCCHG = IC1+ / IC2+0.8 1.0 1.2RTCDIS C1/C2 Discharge Current Ratio RTCDIS = IC1− / IC2−0.8 1.0 1.2VCW1(2)C1 (C2) Cramp Voltage Width 1.0 1.3 1.6V VFGL FG Output Low Level Voltage IFG = 3mA0.5V VRDL RD Output Low Level Voltage IRD = 3mA0.5VTTSD Thermal Shut Down Operating Temperature (Note3)Junction temperatureDesign target (Note4)150180°CD TTSD Thermal Shut Down Hysteresis Temperature(Note3)Junction temperatureDesign target (Note4)15°CProduct parametric performance is indicated in the Electrical Characteristics for the listed test conditions, unless otherwise noted. Product performance may not be indicated by the Electrical Characteristics if operated under different conditions.3.The thermal shut down circuit is built-in for protection from damage of IC. But its operation is out of T opr. Design thermal calculation at normaloperation.4.Design target value and no measurement is made.5.The I O is a peak value of motor-current.Figure 1. P d max − T A00.51.01.5−40−20020406080100Ambient Temperature, T A (5C)A l l o w a b l e P o w e r D i s s i p a t i o n ,P d m a x (W )BLOCK DIAGRAMFigure 2. Block DiagramPIN FUNCTION PIN FUNCTIONPIN FUNCTION (continued)APPLICATION CIRCUIT EXAMPLE * Each fixed number in the following Figure3, is the referential value.Figure 3. Application Circuit Example 1 m F V CCORDERING INFORMATIONDevice Package Wire Bond Shipping† (Qty / Packing) LB11685AV−TLM−H SSOP24J (275mil)(Pb-Free / Halogen Free)Au-wire2000 / Tape & ReelLB11685AV−W−AH SSOP24J (275mil)(Pb-Free / Halogen Free)Cu-wire2000 / Tape & Reel†For information on tape and reel specifications, including part orientation and tape sizes, please refer to our Tape and Reel Packaging Specifications Brochure, BRD8011/D.DATE 31 OCT 2013NOTE:The measurements are not to guarantee but for reference only.*For additional information on our Pb −Free strategy and soldering details, please download the ON Semiconductor Soldering and Mounting Techniques Reference Manual, SOLDERRM/D.XXXXX = Specific Device Code Y = Year M = MonthDDD = Additional Traceability Data GENERICMARKING DIAGRAM**This information is generic. Please refer to device data sheet for actual part marking.Pb −Free indicator, “G” or microdot “ G ”,may or may not be present.XXXXXXXXXX YMDDDMECHANICAL CASE OUTLINEPACKAGE DIMENSIONSON Semiconductor and are trademarks of Semiconductor Components Industries, LLC dba ON Semiconductor or its subsidiaries in the United States and/or other countries.ON Semiconductor reserves the right to make changes without further notice to any products herein. ON Semiconductor makes no warranty, representation or guarantee regarding the suitability of its products for any particular purpose, nor does ON Semiconductor assume any liability arising out of the application or use of any product or circuit, and specifically disclaims any and all liability, including without limitation special, consequential or incidental damages. ON Semiconductor does not convey any license under its patent rights nor theON Semiconductor and are trademarks of Semiconductor Components Industries, LLC dba ON Semiconductor or its subsidiaries in the United States and/or other countries.ON Semiconductor owns the rights to a number of patents, trademarks, copyrights, trade secrets, and other intellectual property. A listing of ON Semiconductor’s product/patent coverage may be accessed at ON Semiconductor makes no warranty, representation or guarantee regarding the suitability of its products for any particular purpose, nor does ON Semiconductor assume any liability arising out of the application or use of any product or circuit, and specifically disclaims any and all liability, including without limitation special, consequential or incidental damages.PUBLICATION ORDERING INFORMATIONTECHNICAL SUPPORTNorth American Technical Support:Voice Mail: 1 800−282−9855 Toll Free USA/Canada Phone: 011 421 33 790 2910LITERATURE FULFILLMENT :Email Requests to:*******************ON Semiconductor Website: Europe, Middle East and Africa Technical Support:Phone: 00421 33 790 2910For additional information, please contact your local Sales RepresentativeMouser ElectronicsAuthorized DistributorClick to View Pricing, Inventory, Delivery & Lifecycle Information:O N Semiconductor:LB11685AV-TLM-H LB11685AV-MPB-H LB11685AV-W-AH。
大惯量负载多电机驱动系统协调控制方法综述

大惯量负载多电机驱动系统协调控制方法综述杨春雨!,孟凡仪!,许一鸣!,黄新利#(1.中国矿业大学信息与控制工程学院,江苏徐州221008;2.酒泉卫星发射中心,甘肃酒泉 735000)摘要:大惯量负载往往采用多个电机协同驱动,整体系统的稳态和动态性能都与多电机驱动系统的协 调控制密切相关。
根据国内外多电机驱动系统协调控制的研究成果,综述相关控制结构和控制算法。
通过对 比分析,说控制方法的 和适用 & ,根据目前的 ,展望了多电机驱动系统协调控制的研究方向和发展趋势。
关键词:多电机驱动系统;协调控制;大惯量负载;控制结构;控制算法中图分类号:TM 301.2 文献标志码:B 文章编号:1673-6540(2019)03-0001-07Coordinated Control Methods for Multi-Motor Drive Systems ofLarge Inertia Load : A Survey **基金项目:国家自然科学基金项目(61873272)作者简介:杨春雨(1979—),男,教授,研究方向为多电机控制系统设计。
孟凡仪(1994—),女,硕士研究生,研究方向为多电机协调控制。
许一鸣(1993—),男,硕士研究生,研究方向为柔性机器人的运动控制。
YANG Chunyu 1, MENG Fan)1, XU Yiming 1, HUANG Xinli 2(1. School of Information and Control Engineering ,China University of Mining and Technology ,Xuzhou 221008,China ;2. Jiuquan Satelliir Launch Centro ,Jiuquan 735000, China )Abstract : Large inertia load was often driven by multiplo motors. The steady state and dymamic performance ofthe whole system was closely related to tOe coordinated controi of the multi-motor drive systems. According to theexisting coordinated controi methods for multi-motor drive systems , the related controi structures and controi alyorithms were surveyed. By comparision ,the advantaaes and disadvantaaes of each existing coodinated controimethod wero analyzed and the corresponding applicable engineering fielOs wero provided. Findy , according to thecurrent industiy demands ,the research directions and development trends of coordinated control of multi-motor drivesystems were presented.Key words : multi-motor drive system ; coordnated control ; large inertia load ; control structerr ;control algorithm0引言对于大惯量负载,例如水泥窑⑴、造纸[2]、带式输送机[3 ]等,为了 驱动系统结构的灵活性、电机体积、能,采用2 者多台电机协同驱动。
多电机拖动皮带输送机恒压频比控制变频器

多电机拖动皮带输送机恒压频比控制变频器摘要:在变频器驱动多机拖动皮带机系统中,一个重要的问题是如何解决系统中各个电动机的功率输出平衡。
介绍了一种基于恒压频比控制型的多机拖动皮带机变频器。
变频器采用主从控制模式,通过对各自有功电流做闭环控制来实现对其输出频率的调整。
变频器的输出电压按照恒压频比控制方式,保证了电机气隙磁通的恒定,最终能够达到各个电动机输出功率一致的目的。
通过现场的成功应用,证明了恒压频比控制型多机拖动皮带机变频器的有效性和实用性。
关键词:多机拖动皮带机恒压频比功率平衡变频器Abstract:In the application of the Inverter driving Multi-Motor Belt Conveyor system, an important problem is how to ensure the output of the motors balance. A Multi-Motor Driving Belt Conveyor Inverter based on VVVF control was proposed. Master-slave control mode is used in the system. The active current is controled by closed-loop mothod to realize the adjustment of their respective output frequency. The output voltage of the Inverter is according to VF control, it ensures the motor’s air gap flux constant, and it ensures that the output of the motors are basically consistent. The feasibility and practicability of this Inverter is verified by being successful applied in the Multi-Motor Driving Belt Conveyor system.Key words:Multi-Motor Driving Belt Conveyor;Variable V oltage and Variable Frequency(VVVF); Power Balance; Inverter1引言现阶段,在采用变频器驱动多电机拖动的皮带输送机系统中,多用一台功率较大的变频器来同时驱动多台电机。
S120驱动控制系统介绍

Page: 5 - 3
版本: V1.0
System overview
SINAMICS S120 chassis and cabinet modules
Line-side components Power supply Line modules: ALM, SLM, BLM DC link components Control units Motor modules
课程代号:SFAE_D_B_02
Page: 5 - 12
版本: V1.0
Motor-side system components
Motor reactor
– Required for all cable lengths > 300 / 450 m (shielded / non-shielded) – Reduces the capacitive re-charging currents – In conjunction with the cable capacitance, reduces the voltage rate-of-rise dv/dt
G110
0.12 kW
S120
G130
G150 / S150
1 MW 100 MW
功能强大
SINAMICS
G110
基本功能
G130 G150
S120
S150
S120
运动控制 / 伺服功能
பைடு நூலகம்应用广泛
SINAMICS
G110
常规驱动器
G130 G150
高性能驱动器
S150
S120
组合驱动器,伺服驱动器
课程代号:SFAE_D_B_02
美国电气制造商协会(NEMA)电机应用指导

© Copyright 2001 by the National Electrical Manufacturers Association. All rights including translation into other languages, reserved under the Universal Copyright Convention, the Berne Convention for the Protection of Literary and Artistic Works, and the International and Pan American Copyright Conventions.
NOTICE AND DISCLAIMER
The information in this publication was considered technically sound by the consensus of persons engaged in the development and approval of the document at the time it was developed. Consensus does not necessarily mean that there is unanimous agreement among every person participating in the development of this document.
NEMA standards and guideline publications, of which the document contained herein is one, are developed through a voluntary consensus standards development process. This process brings together volunteers and/or seeks out the views of persons who have an interest in the topic covered by this publication. While NEMA administers the process and establishes rules to promote fairness in the development of consensus, it does not write the document and it does not independently test, evaluate, or verify the accuracy or completeness of any information or the soundness of any judgments contained in its standards and guideline publications. NEMA disclaims liability for any personal injury, property, or other damages of any nature whatsoever, whether special, indirect, consequential, or compensatory, directly or indirectly resulting from the publication, use of, application, or reliance on this document. NEMA disclaims and makes no guaranty or warranty, express or implied, as to the accuracy or completeness of any information published herein, and disclaims and makes no warranty that the information in this document will fulfill any of your particular purposes or needs. NEMA does not undertake to guarantee the performance of any individual manufacturer or seller’s products or services by virtue of this standard or guide. In publishing and making this document available, NEMA is not undertaking to render professional or other services for or on behalf of any person or entity, nor is NEMA undertaking to perform any duty owed by any person or entity to someone else. Anyone using this document should rely on his or her own independent judgment or, as appropriate, seek the advice of a competent professional in determining the exercise of reasonable care in any given circumstances. Information and other standards on the topic covered by this publication may be available from other sources, which the user may wish to consult for additional views or information not covered by this publication. NEMA has no power, nor does it undertake to police or enforce compliance with the contents of this document. NEMA does not certify, test, or inspect products, designs, or installations for safety or health purposes. Any certification or other statement of compliance with any health or safety–related information in this document shall not be attributable to NEMA and is solely the responsibility of the certifier or maker of NTS
六相永磁同步电机逆变器故障诊断与容错策略研究
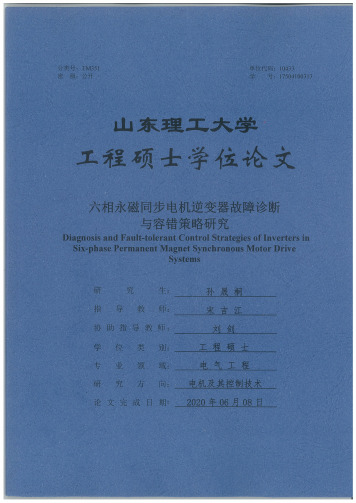
摘 要六相永磁同步电机具有低压大功率、效率高、可容错、噪声低等性能优点,已被应用于舰船推进、航空作动器等可靠性要求较高的应用场合。
在电机驱动系统中,功率转换器中的功率开关管及驱动电路存在较高的故障率,保持逆变器可靠性的相关问题始终没有得到有效处理。
快速、准确识别逆变器发生的故障,并采取适当的容错控制策略,可以确保系统的稳定性,恢复系统原有的性能,保证系统在故障修复之后依旧具备较高的执行力。
因此,对电机驱动系统中逆变器的故障诊断和容错控制策略开展研究具有重要的理论意义和工程应用价值。
对逆变器发生的故障进行诊断,是对电机驱动系统实施容错控制策略的前提,故障诊断的快速性和准确性往往与容错效果成正比。
传统电机的建模方法一般将电机和逆变器分别进行建模,不能很好地揭示电机和逆变器共同的运行状态信息。
本文将混杂系统理论引入到多相电机的故障诊断过程中,将逆变器的离散电压模型与电机的稳态方程进行联立,建立了电机驱动系统的混合逻辑动态模型,为提出新型故障诊断策略提供理论依据。
基于六相电机驱动系统混合逻辑动态模型,提出了基于基波子空间和谐波子空间的电流残差联合对逆变器故障进行诊断方法。
通过推导多相逆变器开关管故障后的电流动态模型,构建了多相电机系统的电流残差方程,得到电流残差用于故障的诊断与定位,并提出了提高多相电机系统故障诊断鲁棒性的基波子空间和谐波子空间阈值电流判定方法。
该方法可以极大地减小故障状态下闭环控制算法对诊断效果的影响,同时可将诊断时间缩短至四分之一个基波周期以内。
基于六相电机驱动系统混合逻辑动态模型,提出了基于误差电压的多相逆变器故障诊断方法,即通过桥臂中点对接地点电压实测值与估计值之间的误差来诊断故障。
为尽可能模拟实际工作情况,提出对误差电压的幅值及时间宽度进行双重判断,以此消除功率管开关延时和死区的影响。
在保证诊断策略的可靠性和鲁棒性的同时,该方法还可将诊断时间锁定在几个开关周期以内。
以上两种诊断方法得到了仿真验证。
基于自校正自抗扰控制的多电机协同系统
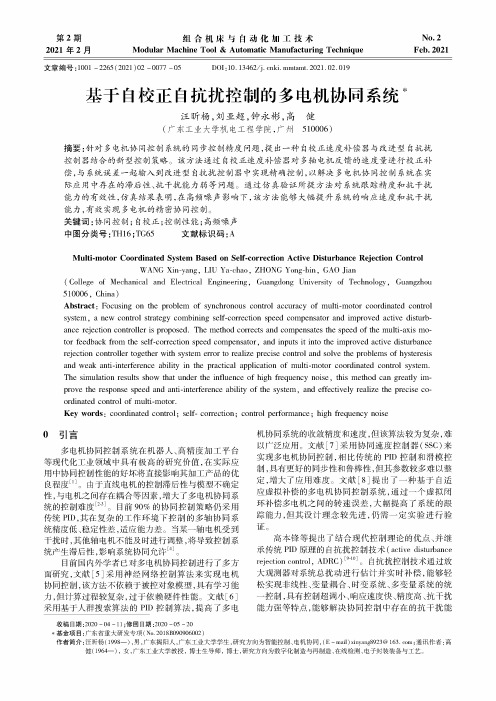
No.2Feb.2021第2期2021年2月组合机床与自动化加工技术Modular Machine Tool & Automatic Manufadtring Techninur文章编号:1001 -2265(2021)02 -0077 -05DOI : 10.13462/j. cnki mmtamt. 2021.02. 019基于自校正自抗扰控制的多电机协同系统汪昕杨,刘亚超,钟永彬,高健(广东工业大学机电工程学院,广州510006)摘要:针对多电机协同控制系统的同步控制精度问题,提出一种自校正速度补偿器与改进型自抗扰 控制器结合的新型控制策略。
该方法通过自校正速度补偿器对多轴电机反馈的速度量进行校正补偿,与系统误差一起输入到改进型自抗扰控制器中实现精确控制,以解决多电机协同控制系统在实际应用中存在的滞后性、抗干扰能力弱等问题。
通过仿真验证所提方法对系统跟踪精度和抗干扰 能力的有效性,仿真结果表明,在高频噪声影响下,该方法能够大幅提升系统的响应速度和抗干扰能力,有效实现多电机的精密协同控制。
关键词:协同控制;自校正;控制性能;高频噪声中图分类号:TH16;TG65文献标识码:AMulti-motor Coordinateb System Based on Self-sorrection Active Disttrdancc Rejection ControlWANG Xin-yang , LID Ya-chao , ZHONG Yong-bin , GAO Jian(Colleae of Mechanicai and Electricai Engineering , Guangdong University of Technoloyy , Guangzhou 510006, China )Abstract : Focusing on the proMem of synchronous conaol accuracy of multi-motor coordinated conhoi syshem , anew conheo2sheahegy combining sef-co e echion speed compensahoeand impeoved achivedishueb-ance t V —tion conWoller is proposed. The method correcti and compensates the speed of the multi-axis mo- hoefeedback feom hhe elf-co e echion peed compen ahoe , and inpuhihinho hheimpeoved achivedihuebanceV —tion contoHeT together with system error to realize precise contoi and solve the problems of hysteresis and weak anti-interference ability in the practical application of multi-motor coordinated conhoi system.The simulation vsu U s show that under the influence of high frequency noise , this method can greatly im prove the response speed and anh-interference ability of the system, and effec t ively realize the pvcise co ordinated conhoi of multi-motor.Key wors : coordinated coniol ; self- correction ; coniol performance ; high frequency noise0引言多电机协同控制系统在机器人、高精度加工平台 等现代化工业领域中具有极高的研究价值,在实际应 用中协同控制性能的好坏将直接影响其加工产品的优 良程度⑴。
PowerXL DG1 调节频率驱动器多机器室风控制软件应用介绍说明书

Multi-Pump and Fan Software ApplicationIntroductionThe PowerXL DG1 adjustable frequency drive Multi-Pump and Fan Control software application is de-signed to be utilized in applications where multiple pumps or fan systems are implemented to maintain a desired flow rate, pressure, or temperature value. It enables the drive to use a single PID loop to control auxiliary motors networked together to provide increase power on demand while reducing overall system control cost. The auxiliary motors can be powered by across the line starters, soft starters, or drives de-pending on the system performance requirements. There are two main features in the Multi-Pump and Fan Control software application: the auto-change feature, which will equalizes the run time of each mo-tor; and the booster mode, that can add additional pumps or fans in periods of higher demand. Both fea-tures may also be used simultaneously and a total of five motors can be controlled by one PowerXL DG1 drive.Motor Control SequenceTo provide a common example of how the system would operate, refer to Figure 1 and 2 on the next two pages. Figure 1 shows the basic control scheme used for the interlocked contactor system shown in Fig-ure 2. In this configuration, the single PowerXL DG1 drive is controlling two motors. Upstream of each motor is a set of interlocked starters to both isolate and transfer power from the drive to a starter upon demand or vice versa. The interlocked starters are controlled by the relay output terminals on the drive. Once motor 1 ramps up to full speed, if additional demand is required, the second motor can be ener-gized by the starter to provide increased capacity. If this configuration was using the auto-change fea-tures, the next time both motors reached zero speed, the interlocks would reverse via the drive relays, making motor 2 controlled by the drive and motor 1 by the starter. This would be done to equalize run time as discussed before. If they system had addition motors beyond these two, the same logic would apply as it system moved from motor to motor for run time equalization.Application Note AP0400072EN Multi-Pump and Fan Software Application Effective July 20142 EATON CORPORATION Multi-Pump and Fan Software Application Application Note AP040072ENEffective July 2014Figure 2: Multi-Pump Two Motor Power WiringProgrammingFirst the PowerXL DG1 application should be set to any application other than Standard (P21.1.2) to enable this functionality, then the initial motor name plate information should be entered into the basic parameter group, this will set up the initial V/Hz curve that the drive will output to the motor. Along with the motor parameters, the control scheme needs to be set for both the Local and Remote control place. Typically this would be set up as follows:P1.10: Local Control – KeypadP1.11: Remote Control - I/O TerminalP1.12: Local Reference – KeypadP1.14: Remote Reference – PID1 ControlUpon completion of the basic parameters, the next group to set up is the Analog inputs. In this example we will just us the default values being AI2 set up for 0-20mA (P2.11) and a range of 20-100% (P2.12). If either AI1 or AI2 require being changed from either Voltage or Current, there are dip switches on the side of the control module along with parameters that will need to be adjusted. For more information refer to the PowerXL DG1 Application Manual.Next will be the digital inputs that will require some additional configuration. With the default settings, the application will have the start command given on DIN1 for forward and DIN2 for Reverse. From this point, the number of motors will be need to be known to set up the required number of interlocks. (1 to 5 motors can be used in the sequence, refer to P3.37 to P3.41). These interlocks can be set up on any of digitalEATON CORPORATION 3Application Note AP0400072EN Multi-Pump and Fan Software Application Effective July 2014inputs from DIN3 through DIN8. It is suggested that the default settings be changed so that the functions are disabled in order for the inputs to not have multiple functions. Note: For most inputs, Force Open will cause the function to always be disabled, if Force Closed is used, that function is always enabled. See the PowerXL DG1 Application Manual for more parameter information.Once the I/O control logic is set, then the analog output signal can be set, but it is not required for this particular example. The Relay outputs are used to trigger the interlocked starters to supply power to the auxiliary motors when they are required. Depending on how many motors are in the system will determine how many relays are necessary. For this example, two relays are required for the motor contacts and we will use the third for a run indication. See the PowerXL DG1 Application Manual for more parameter information.P5.2: RO1 Function - RunP5.3: RO2 Function – Motor 1 ControlP5.4: RO3 Function – Motor 2 ControlThe next steps would be to set up the PID function for the drive in order to try and maintain a required flow, pressure, or temperature. These values would be set in the PID1 Control group. For this example, the set point will be coming from the keypad P10.14, with the feedback being monitored at AI2 P10.32. The keypad set point would be set at P10.11. The P10 group also has addition values that will allow you for further tuning of the PID loop.After setting up the PID loop parameters the Multi Pump Control parameter can be setup P18 group. This is where the number of motors would be set, in this example there are two. Then the Bandwidth and Bandwidth Delay can be set for how the PID loop is tracked, if the feedback is outside the bandwidth value for the delay time, the drive will use the relay outputs to engage the next motor. In our case, we choose to use auxiliary contacts on the starters to indicate if they are connected, so this needs to be enabled. In addition, the Interlock Auto Change can be set up to equal the run time on each motor by setting up the parameters to control the auto change feature.At this point the drive should be set to run and maintain the set reference value, the system will start out using the first motor and if the set point can’t be reached it will bring in the second motor online to assist. Once the auto change time and frequency is met the lead motor will switch.4 EATON CORPORATION Multi-Pump and Fan Software Application Application Note AP040072ENEffective July 2014 OperationThe below images show how the relay output interlock functions are used to tell it which motors are ac-tive, and then what the change sequence of motors that are running will be maintain to achieve the re-quired set point. If one of the interlock drops out, the drive will continue to run, but the relay output that controls the starter powering a particular auxiliary motor will drop out. With each motor that is engaged, the main motor will slow down to compensate for the large inrush of bringing a motor on across the line. This helps to allow for improved performance in controlling the flow and these transitions occur based off the bandwidth values and the feedback from the system.Figure 3: Multi-Pump Interlock Control SchemeEATON CORPORATION 5Application Note AP040072EN Multi-Pump and Fan Application Effective July 2014Additional HelpIn the US or Canada: please contact the Technical Resource Center at 1-877-ETN-CAREor 1-877-326-2273 option 2, option 6.All other supporting documentation is located on the Eaton web site at /DrivesEaton1000 Eaton BoulevardCleveland, OH 44122 USA© 2014 EatonAll Rights ReservedPrinted in USAPublication No. AP040072ENJuly 2014Eaton is a registered trademarkof Eaton Corporation.All other trademarks are propertyof their respective owners。
伦茨变频器参数如下

伦茨变频器参数如下Allen-Bradley PowerFlex 7-Series AC Drives, or drives that use a variable frequency drive (VFD), are designed to give optimized motor control for a wide range of applications. The main parameters that must be considered when specifying a PowerFlex 7-Series drive are the voltage rating, current rating, frequency of operation, number of phases, type of enclosure, control mode, and number of I/O.Voltage rating: The voltage rating of the PowerFlex 7-Series drive must be sufficient to allow it to control the motor in the application. Voltage ratings can range from 120 VAC to 690 VAC.Current rating: The current rating of the PowerFlex 7-Series drive must be capable of powering the motor in the application. Current ratings can range from 0.5 Amps to 1700 Amps.Frequency of operation: The frequency output of the PowerFlex 7-Series drive can be adjusted to match the motor’s operating frequency. The range is 1 Hz to 650 Hz.Number of phases: The PowerFlex 7-Series drive is available in single-phase, three-phase, and multi-phase configurations.Type of enclosure: The PowerFlex 7-Series drive is available in NEMA 1, NEMA 12, and IP66 enclosures.Control mode: The PowerFlex 7-Series drive can be operatedin either current or voltage mode.Number of I/O: The PowerFlex 7-Series drive is available with a variety of I/O options, including 0 to 24 analog inputs, 0 to 32 digital inputs, 0 to 16 analog outputs, and 0 to 32 digital outputs.The PowerFlex 7-Series AC Drives use a VFD to control the motor, providing smooth control of speed, torque, and power. The adjustable parameters of the PowerFlex 7-Series drive vary depending on the application and can be configured by the customer. Additionally, the PowerFlex 7-Series drive has built-in protection features, including over-voltage protection,under-voltage protection, over-current protection, ground fault protection, and short-circuit protection. The drives also offer motor fault diagnostics, allowing for quick troubleshooting of any motor issues. PowerFlex 7-Series drives are also backed by Allen-Bradley’s global network of service and support.。
多电机单驱动器应用指南说明书

Multiple m otors - s ingle d riveIntroductionThis document is to help with the installation and setup of a system with multiple motors that are run on a single drive at the same time. In this type of application, the drive can no longer protect individual motors so there are different system considerations as compared to a single drive/ single motor application. System considerations•Because the drive can’t protect individual motors each motor has to have it own thermal protection device. This device cannot be self-resetting and should be something you can turn off to be able to disconnect the motor if needed. This is normally a manual motor protector. It is not recommended to use fuses on the motor unless the fuses are monitored and will remove all 3 phases if it blows one phase.•When calculating the distance of the output run you have to add all of the cabling together. As an example, let’s say we have a single run between the drive and the distribution box of 100’. From there we go to 5 different motors and each of those runs is 25’. The equivalent output run would be 25+25+25+25+25+100=225’. We would need to protect the output for a 225’ output run. In the minimum any multiple motor system should have an output reactor on it. On the above example we would want to put a DV/DT filter on this to be safe.o0-150’ recommended output reactoro150-700’ recommended DV/DT filtero Above 700’ recommended sine filter (need to spec a sine filter capable of DC braking)•As with any drive installation the output cable should be run with a high quality VFD cable. This is to improve performance and reduce risk of adverse results.•For best results all motors should be the same make and model. These motors need to share the load as well as possible and any differences in the motors could cause an unbalanced load share. Drive setupThe following parameters are what you set for this type of setup:•Motor nameplate current: add all of the motor FLAs together and put this in the drive as nameplate current.•Motor nameplate voltage: this is the voltage off of the rating plate of the motor. If you want to output more or less voltage to the motor, it is better to use voltage at field weakening point and not by changing the motor nameplate voltage. The drive uses the motor nameplate information forcalculating a lot of things in the drive so if you skew this data you will make the drive calculatethings like power, torque and temperature incorrectly. As an example, if you have a 230V motor buta 208V input to the drive do not put the motor nameplate at 208, it should be 230. If you want thevoltage to increase up until the field weakening point we would change the voltage at fieldweakening point. In this case we would divide 208 by 230 which would give you 90%. You would put this in the drive for voltage at field weakening point.Multiple m otors - si ngle d riveApplication Note AP 040212ENEffective A pril 20202 EATON •Motor nameplate frequency: this should be taken directly off of the motor.•Motor nameplate speed: this should be taken directly off of the motor.•Power factor: this is taken directly off of the motor. If you can’t find it on the motor rating plate leave it as the default setting. This could potentially change power and torque calculations but hopefully it is close.•Current limit: should be set somewhere between 110-125%. I would start on the low end of this and increase it if we need more starting torque.•Minimum frequency: this is application specific. This will set the minimum reference you can set to the drive.•Maximum frequency: this is application specific. This is the maximum reference you can set to the drive.•Acceleration time: this is application specific. Preferably you set this to a value that will allow the drive to accelerate the application without going into a current limit.•Deceleration time: this is application specific. Preferably this is set to a value that will allow the drive to slow the application down without going into an overvoltage controller.•Start mode: start mode should be set to ramp to start. On multiple motors you can’t really use flying start because you can’t find magnetizing current on multiple motors at the same time. If there is the possibility of flying motors, we will need to use DC braking at start.•Stop mode: this will be application specific. Most of these applications will be fan banks which generally you will coast to stop. There are other applications where ramp to stop may be more preferable.•DC brake current: this is the current that you would use during DC braking. If we have the potential of flying motors when we start, we want to bring them to a stop before starting. I would start with about 30% of the combined FLA of all motors for this value. You do not want to go too high with this value in case motors are removed from the circuit you don’t want to put too much current to theremaining motors. If you go too low you may not be able to slow down the motors. The rough range would be between 30% to 75% of the combined FLA. If you go too high with this value you do not want to remove too many motors from the circuit without lowering this value.•Start DC brake time: this is going to depend on the application. We will use this in combination with the DC brake current to bring the motors to a stop before we start them. A good starting point would be about 60 seconds.•Voltage at field weakening point: this is the setting that you will use if you want the drive to output higher than motor nameplate voltage. If the input voltage is higher than the motor nameplate voltage you may want to use this voltage. You do this by increasing this number above 100%. As anexample, let’s say your input voltage is typically 490VAC. Your motor nameplate is 460V. With default settings the drive will output 460VAC at 60Hz. If we want to output the 490VAC at 60Hz instead of 460V we would take our input voltage and divide it by our motor nameplate voltage and put this in for this value. 490/460=106%Setup of b raking at s tartIf you have an application where it is possible for the motors to be moving when the drive starts you will need to use DC braking at start. You can’t use flying start because the motors are not synced with each other so the drive will not be able to find what speed the motors are at because they are all at different speeds. The way to set this up is to do the following:•The best way to watch the system is normally using the trendplotter on the HMAX or SVX series of drives or the powerexpert tool for DG1 series. This way you can look at multiple readings at once on your laptop. You can do this through the keypad but on the SVX and HMAX series you can record the readings which makes it easier to look at all the data.•Set DC braking current to about 30% of FLA.*•Set DC braking time at start to 60 sec.*•If you are using ramp to stop change to coast to stop.•Start the application with all of the motors attached. Ramp up to full speed if possible.Multiple m otors - s ingle d rive Application Note AP 040212ENEffective A pril 2020EATON 3•Stop the application and then immediately restart it. Time how long it takes the motors to come to a stop.•If the motors did not come to a complete stop before the drive tried to start the motors, you should either increase the braking current or increase the braking time. The caution with this is if you have to go high in braking current you have to be cautious about removing motors. Motors will take more than 100% current for a short period of time but as an example if you have 6 motors in the bank and you have braking set to 75% of the combined FLA you probably would not want to remove more than 3 of the motors from the circuit without changing this current. If you removed 3of the motors from the circuit when you would start you would be putting 150% of FLA to the motors for the length of time you have the braking set for. This won’t hurt for motor for theamount of time we should be using for braking but if you remove 1 more motor that percentage now goes to 225% of FLA. This is getting into an area that you shouldn’t be running and if you go down to 1 motor you will now be at 450% of FLA. This will heat the motor and start to degrade the motor insulation along with the cabling insulation going to the individual motor.•If the motors stopped well before the drive restarts the motors, you will probably want to decrease the braking time. I would recommend setting this about 5 to 10 seconds longer than it takes to stop the motors. This way if system characteristics change we have some leeway in the system.•Retry this after adjusting these settings to make sure everything looks okay while starting and stopping the application.•If you need ramp to stop change back to ramp to stop.*If you are doing this on an HMAX drive you do not have DC braking at start. You will need to use pre-magnetizing current and pre-magnetizing time to get the same results.Motor p rotection d evice Each motor on the system has to be protected individually because the drive cannot tell the difference between motors and know where all of the current is going on the output.This protection has to be something that will not auto-reset. We do not want the motor to bereconnected to a drive that is running. This will cause a lot of current to be drawn off of the drive and will trip the drive. Normally manual motor protectors (MMP) are used for this because you can also manually remove the motor from the circuit if you need to. Fuses should not be used to protect the motors unless there is something that will recognize a blown fuse and remove the other 2 phases to the motor.When you set the protection devices you do not set them for the service factor of the motor. The service factor of the motor is for a clean sinusoidal output. The drive does not put out a cleansinusoidal output so there are harmonics involved. This makes the service factor of the motor 1.0 due to the extra heating. This is what you would set your protection devices for. You may want to give it a little extra to stop any false tripping, but you do not want to use the service factor rating of the motor.Multiple m otors - s ingle d rive Application Note AP040212ENEffective A pril 2020Additional h elpIn the US or Canada: please contact the Technical Resource Center at 1-877-ETN-CAREor 1-877-326-2273 option 2, option 6.All other supporting documentation is located on the Eaton web site at /DrivesEaton1000 Eaton BoulevardCleveland, OH 44122 USA© 2020 EatonAll Rights ReservedPrinted in USAPublication No. AP040212ENApril 2020Eaton is a registered trademark.All other trademarks areproperty of their respectiveowners.。
电力电子术语中英文对照

电力电子技术术语Absorber Circuit 吸收电路AC/ACFrequency Converter 交交变频电路AC power control 交流电力控制AC Power Controller 交流调功电路AC Power Electronic Switch 交流电力电子开关AC Voltage Controller 交流调压电路Asynchronous Modulation 异步调制Baker Clamping Circuit 贝克箝位电路Bi-directional Triode Thyristor 双向晶闸管Bipolar Junction Transistor——BJT 双极结型晶体管Boost—Buck Chopper 升降压斩波电路Boost Chopper 升压斩波电路Boost Converter 升压变换器Bridge Reversible Chopper 桥式可逆斩波电路Buck Chopper 降压斩波电路Buck Converter 降压变换器Commutation 换流Conduction Angle 导通角Constant Voltage Constant Frequency——CVCF恒压恒频Continuous Conduction-—CCM (电流)连续模式Control Circuit控制电路CUK Circuit CUK 斩波电路Current Reversible Chopper 电流可逆斩波电路Current Source Type Inverter-—CSTI 电流(源)型逆变电路Cycloconvertor 周波变流器DC—AC-DC Converter 直交直电路DC Chopping 直流斩波DC Chopping Circuit直流斩波电路DC—DC Converter 直流-直流变换器Device Commutation 器件换流Direct Current Control 直接电流控制Discontinuous Conduction mode (电流)断续模式Displacement Factor 位移因数Distortion Power 畸变功率Double End Converter 双端电路Driving Circuit 驱动电路Electrical Isolation 电气隔离Fast Acting Fuse 快速熔断器Fast Recovery Diode 快恢复二极管Fast Recovery Epitaxial Diodes 快恢复外延二极管Fast Switching Thyristor 快速晶闸管Field Controlled Thyristor 场控晶闸管Flyback Converter 反激电流Forced Commutation 强迫换流Forward Converter 正激电路Frequency Converter 变频器Full Bridge Converter 全桥电路Full Bridge Rectifier 全桥整流电路Full Wave Rectifier 全波整流电路Fundamental Factor 基波因数Gate Turn-Off Thyristor--GTO可关断晶闸管General Purpose Diode 普通二极管Giant Transistor—-GTR 电力晶体管Half Bridge Converter 半桥电路Hard Switching 硬开关High Voltage IC 高压集成电路Hysteresis Comparison 带环比较方式Indirect Current Control 间接电流控制Indirect DC—DC Converter 直接电流变换电路Insulated-Gate Bipolar Transistor——IGBT 绝缘栅双极晶体管Intelligent Power Module——IPM 智能功率模块Integrated Gate—Commutated Thyristor--IGCT集成门极换流晶闸管Inversion 逆变Latching Effect 擎住效应Leakage Inductance 漏感Light Triggered Thyristo——-LTT 光控晶闸管Line Commutation 电网换流Load Commutation 负载换流Loop Current 环流元件设备三绕组变压器:three—column transformer ThrClnTrans 双绕组变压器:double-column transformer DblClmnTrans 电容器:Capacitor并联电容器:shunt capacitor电抗器:Reactor母线:Busbar输电线:TransmissionLine发电厂:power plant断路器:Breaker刀闸(隔离开关):Isolator分接头:tap电动机:motor状态参数有功:active power无功:reactive power电流:current容量:capacity电压:voltage档位:tap position有功损耗:reactive loss无功损耗:active loss功率因数:power-factor功率:power功角:power-angle电压等级:voltage grade空载损耗:no-load loss铁损:iron loss铜损:copper loss空载电流:no-load current阻抗:impedance正序阻抗:positive sequence impedance负序阻抗:negative sequence impedance零序阻抗:zero sequence impedance电阻:resistor电抗:reactance电导:conductance电纳:susceptance无功负载:reactive load 或者QLoad有功负载: active load PLoad遥测:YC(telemetering)遥信:YX励磁电流(转子电流):magnetizing current 定子:stator功角:power-angle上限:upper limit下限:lower limit并列的:apposable高压:high voltage低压:low voltage中压:middle voltage电力系统power system发电机generator励磁excitation励磁器excitor电压voltage电流current母线bus变压器transformer升压变压器step-up transformer高压侧high side输电系统power transmission system输电线transmission line固定串联电容补偿fixed series capacitor compensation 稳定stability电压稳定voltage stability功角稳定angle stability暂态稳定transient stability电厂power plant能量输送power transfer交流AC装机容量installed capacity电网power system落点drop point开关站switch station双回同杆并架double-circuit lines on the same tower 变电站transformer substation补偿度degree of compensation高抗high voltage shunt reactor无功补偿reactive power compensation故障fault调节regulation裕度magin三相故障three phase fault故障切除时间fault clearing time极限切除时间critical clearing time切机generator triping高顶值high limited value强行励磁reinforced excitation线路补偿器LDC(line drop compensation)机端generator terminal静态static (state)动态dynamic (state)单机无穷大系统one machine - infinity bus system 机端电压控制AVR电抗reactance电阻resistance功角power angle有功(功率)active power无功(功率) reactive power功率因数power factor无功电流reactive current下降特性droop characteristics斜率slope额定rating变比ratio参考值reference value电压互感器PT分接头tap下降率droop rate仿真分析simulation analysis传递函数transfer function框图block diagram受端receive-side裕度margin同步synchronization失去同步loss of synchronization 阻尼damping摇摆swing保护断路器circuit breaker电阻:resistance电抗:reactance阻抗:impedance电导:conductance电纳:susceptance导纳:admittance电感:inductance电容: capacitance一般术语电力电子变流器的型式(表1-2)电力电子开关和交流电力电子控制器电力电子设备的基本元件电力电子设备的电路和电路单元电力电子设备的运行电力电子设备的性能电力电子变流器的特性曲线稳定电源。
起重机中英文对照外文翻译文献

起重机中英⽂对照外⽂翻译⽂献中英⽂对照外⽂翻译(⽂档含英⽂原⽂和中⽂翻译)Control of Tower Cranes WithDouble-Pendulum Payload DynamicsAbstract:The usefulness of cranes is limited because the payload is supported by an overhead suspension cable that allows oscilation to occur during crane motion. Under certain conditions, the payload dynamics may introduce an additional oscillatory mode that creates a double pendulum. This paper presents an analysis of this effect on tower cranes. This paper also reviews a command generation technique to suppress the oscillatory dynamics with robustness to frequency changes. Experimental results are presented to verify that the proposed method can improve the ability of crane operators to drive a double-pendulum tower crane. The performance improvements occurred during both local and teleoperated control.Key words:Crane , input shaping , tower crane oscillation , vibrationI. INTRODUCTIONThe study of crane dynamics and advanced control methods has received significant attention. Cranes can roughly be divided into three categories based upontheir primary dynamic properties and the coordinate system that most naturally describes the location of the suspension cable connection point. The first category, bridge cranes, operate in Cartesian space, as shown in Fig. 1(a). The trolley moves along a bridge, whose motion is perpendicular to that of the trolley. Bridge cranes that can travel on a mobile base are often called gantry cranes. Bridge cranes are common in factories, warehouses, and shipyards.The second major category of cranes is boom cranes, such as the one sketched in Fig. 1(b). Boom cranes are best described in spherical coordinates, where a boom rotates aboutaxes both perpendicular and parallel to the ground. In Fig. 1(b), ψis the rotation aboutthe vertical, Z-axis, and θis the rotation about the horizontal, Y -axis. The payload is supported from a suspension cable at the end of the boom. Boom cranes are often placed on a mobile base that allows them to change their workspace.The third major category of cranes is tower cranes, like the one sketched in Fig. 1(c). These are most naturally described by cylindrical coordinates. A horizontal jib arm rotates around a vertical tower. The payload is supported by a cable from the trolley, which moves radially along the jib arm. Tower cranes are commonly used in the construction of multistory buildings and have the advantage of having a small footprint-to-workspace ratio. Primary disadvantages of tower and boom cranes, from a control design viewpoint, are the nonlinear dynamics due to the rotational nature of the cranes, in addition to the less intuitive natural coordinate systems.A common characteristic among all cranes is that the pay- load is supported via an overhead suspension cable. While this provides the hoisting functionality of the crane, it also presents several challenges, the primary of which is payload oscillation. Motion of the crane will often lead to large payload oscillations. These payload oscillations have many detrimental effects including degrading payload positioning accuracy, increasing task completion time, and decreasing safety. A large research effort has been directed at reducing oscillations. An overview of these efforts in crane control, concentrating mainly on feedback methods, is provided in [1]. Some researchers have proposed smooth commands to reduce excitation of system flexible modes [2]–[5]. Crane control methods based on command shaping are reviewed in [6]. Many researchers have focused on feedback methods, which necessitate the addition necessitate the addition of sensors to the crane and can prove difficult to use in conjunction with human operators. For example, some quayside cranes have been equipped with sophisticated feedback control systems to dampen payload sway. However, the motions induced by the computer control annoyed some of the human operators. As a result, the human operators disabled the feedback controllers. Given that the vast majority of cranes are driven by human operators and will never be equipped with computer-based feedback, feedback methods are not considered in this paper.Input shaping [7], [8] is one control method that dramatically reduces payload oscillation by intelligently shaping the commands generated by human operators [9], [10]. Using rough estimates of system natural frequencies and damping ratios, a series of impulses, called the input shaper, is designed. The convolution of the input shaper and the original command is then used to drive the system. This process is demonstrated with atwo-impulse input shaper and a step command in Fig. 2. Note that the rise time of the command is increased by the duration of the input shaper. This small increase in the rise time isnormally on the order of 0.5–1 periods of the dominant vibration mode.Fig. 1. Sketches of (a) bridge crane, (b) boom crane, (c) and tower crane.Fig. 2. Input-shaping process.Input shaping has been successfully implemented on many vibratory systems including bridge [11]–[13], tower [14]–[16], and boom [17], [18] cranes, coordinate measurement machines[19]–[21], robotic arms [8], [22], [23], demining robots [24], and micro-milling machines [25].Most input-shaping techniques are based upon linear system theory. However, some research efforts have examined the extension of input shaping to nonlinear systems [26], [14]. Input shapers that are effective despite system nonlinearities have been developed. These include input shapers for nonlinear actuator dynamics, friction, and dynamic nonlinearities [14], [27]–[31]. One method of dealing with nonlinearities is the use of adaptive or learning input shapers [32]–[34].Despite these efforts, the simplest and most common way to address system nonlinearities is to utilize a robust input shaper [35]. An input shaper that is more robust to changes in system parameters will generally be more robust to system nonlinearities that manifest themselves as changes in the linearized frequencies. In addition to designing robust shapers, input shapers can also be designed to suppress multiple modes of vibration [36]–[38].In Section II, the mobile tower crane used during experimental tests for this paper is presented. In Section III, planar and 3-D models of a tower crane are examined to highlight important dynamic effects. Section IV presents a method to design multimode input shapers with specified levels of robustness. InSection V, these methods are implemented on a tower crane with double-pendulum payload dynamics. Finally, in Section VI, the effect of the robust shapers on human operator performance is presented for both local and teleoperated control.II. MOBILE TOWER CRANEThe mobile tower crane, shown in Fig. 3, has teleoperation capabilities that allow it to be operated in real-time from anywhere in the world via the Internet [15]. The tower portion of the crane, shown in Fig. 3(a), is approximately 2 m tall with a 1 m jib arm. It is actuated by Siemens synchronous, AC servomotors. The jib is capable of 340°rotation about the tower. The trolley moves radially along the jib via a lead screw, and a hoisting motor controls the suspension cable length. Motor encoders are used for PD feedback control of trolley motion in the slewing and radial directions. A Siemens digital camera is mounted to the trolley and records the swing deflection of the hook at a sampling rate of 50 Hz [15].The measurement resolution of the camera depends on the suspension cable length. For the cable lengths used in this research, the resolution is approximately 0.08°. This is equivalent to a 1.4 mm hook displacement at a cable length of 1 m. In this work, the camera is not used for feedback control of the payload oscillation. The experimental results presented in this paper utilize encoder data to describe jib and trolley position and camera data to measure the deflection angles of the hook. Base mobility is provided by DC motors with omnidirectional wheels attached to each support leg, as shown in Fig. 3(b). The base is under PD control using two HiBot SH2-based microcontrollers, with feedback from motor-shaft-mounted encoders. The mobile base was kept stationary during all experiments presented in this paper. Therefore, the mobile tower crane operated as a standard tower crane.Table I summarizes the performance characteristics of the tower crane. It should be noted that most of these limits areenforced via software and are not the physical limitations of the system. These limitations are enforced to more closely match theoperational parameters of full-sized tower cranes.Fig. 3. Mobile, portable tower crane, (a) mobile tower crane, (b) mobile crane base.TABLE I MOBILE TOWER CRANE PERFORMANCE LIMITSFig. 4 Sketch of tower crane with a double-pendulum dynamics.III. TOWER CRANE MODELFig.4 shows a sketch of a tower crane with a double-pendulum payload configuration. The jib rotates by an angle around the vertical axis Z parallelto the tower column. The trolley moves radially along the jib; its position along the jib is described by r . The suspension cable length from the trolley to the hook is represented by an inflexible, massless cable of variable length 1l . The payload is connected to the hook via an inflexible, massless cable of length 2l . Both the hook and the payload are represented as point masses having masses h m and p m , respectively.The angles describing the position of the hook are shown in Fig. 5(a). The angle φrepresents a deflection in the radial direction, along the jib. The angle χ represents a tangential deflection, perpendicular to the jib. In Fig. 5(a), φ is in the plane of the page, and χ lies in a plane out of the page. The angles describing the payload position are shown in Fig. 5(b). Notice that these angles are defined relative to a line from the trolley to the hook. If there is no deflection of the hook, then the angleγ describes radial deflections, along the jib, and the angle α represents deflections perpendicular to the jib, in the tangential direction. The equations of motion for this model were derived using a commercial dynamics package, but they are too complex to show in their entirety here, as they are each over a page in length.To give some insight into the double-pendulum model, the position of the hook and payload within the Newtonian frame XYZ are written as —h q and —p q , respectivelyWhere -I , -J and -K are unit vectors in the X , Y , and Z directions. The Lagrangian may then be written asFig. 5. (a) Angles describing hook motion. (b) Angles describing payload motion.Fig. 6. Experimental and simulated responses of radial motion.(a) Hook responses (φ) for m 48.01=l ,(b) Hook responses for m 28.11=lThe motion of the trolley can be represented in terms of the system inputs. The position of the trolley —tr q in the Newtonian frame is described byThis position, or its derivatives, can be used as the input to any number of models of a spherical double-pendulum. More detailed discussion of the dynamics of spherical double pendulums can be found in [39]–[42].The addition of the second mass and resulting double-pendulum dramatically increases the complexity of the equations of motion beyond the more commonly used single-pendulum tower model [1], [16], [43]–[46]. This fact can been seen in the Lagrangian. In (3), the terms in the square brackets represent those that remain for the single-pendulum model; no —p q terms appear. This significantly reduces the complexity of the equations because —p q is a function of the inputs and all four angles shown in Fig. 5.It should be reiterated that such a complex dynamic model is not used to design the input-shaping controllers presented in later sections. The model was developed as a vehicle to evaluate the proposed control method over a variety of operating conditions and demonstrate its effectiveness. The controller is designed using a much simpler, planar model.A. Experimental V erification of the ModelThe full, nonlinear equations of motion were experimentally verified using several test cases. Fig.6 shows two cases involving only radial motion. The trolley was driven at maximum velocity for a distance of 0.30 m, with 2l =0.45m .The payload mass p m for both cases was 0.15 kg and the hook mass h m was approximately 0.105 kg. The two cases shown in Fig. 6 present extremes of suspension cable lengths 1l . In Fig. 6(a), 1l is 0.48 m , close to the minimum length that can be measured by the overhead camera. At this length, the double-pendulum effect is immediately noticeable. One can see that the experimental and simulated responses closely match. In Fig. 6(b), 1l is 1.28 m, the maximum length possible while keeping the payload from hitting the ground. At this length, the second mode of oscillation has much less effect on the response. The model closely matches the experimental response for this case as well. The responses for a linearized, planar model, which will be developed in Section III-B, are also shown in Fig. 6. The responses from this planar model closely match both the experimental results and the responses of the full, nonlinear model for both suspension cable lengths.Fig. 7. Hook responses to 20°jib rotation:(a) φ (radial) response;(b) χ (tangential) response.Fig. 8. Hook responses to 90°jib rotation:φ(radial) response;(b) χ(tangential) response.(a)If the trolley position is held constant and the jib is rotated, then the rotational and centripetal accelerations cause oscillation in both the radial and tangential directions. This can be seen in the simulation responses from the full nonlinear model in Figs. 7 and 8. In Fig. 7, the trolley is held at a fixed position of r = 0.75 m, while the jib is rotated 20°. This relatively small rotation only slightly excites oscillation in the radial direction, as shown in Fig. 7(a). The vibratory dynamics are dominated byoscillations in the tangential direction, χ, as shown in Fig. 7(b). If, however, a large angular displacement of the jib occurs, then significant oscillation will occur in both the radial and tangential directions, as shown in Fig. 8. In this case, the trolley was fixed at r = 0.75 m and the jib was rotated 90°. Figs. 7 and 8 show that the experimental responses closely match those predicted by the model for these rotational motions. Part of the deviation in Fig. 8(b) can be attributed to the unevenness of the floor on which the crane sits. After the 90°jib rotation the hook and payload oscillate about a slightly different equilibrium point, as measured by the overhead camera.Fig.9.Planardouble-pendulummodel.B.Dynamic AnalysisIf the motion of the tower crane is limited to trolley motion, like the responses shown in Fig. 6, then the model may be simplified to that shown in Fig. 9. This model simplifies the analysis of the system dynamics and provides simple estimates of the two natural frequencies of the double pendulum. These estimates will be used to develop input shapers for the double-pendulum tower crane.The crane is moved by applying a force )(t u to the trolley. A cable of length 1l hangs below the trolley and supports a hook, of mass h m , to which the payload is attached using rigging cables. The rigging and payload are modeled as a second cable, of length 2l and point mass p m . Assuming that the cable and rigging lengths do not change during the motion, the linearized equations of motion, assuming zero initial conditions, arewhere φ and γ describe the angles of the two pendulums, R is the ratio of the payload mass to the hook mass, and g is the acceleration due to gravity.The linearized frequencies of the double-pendulum dynamics modeled in (5) are [47]Where Note that the frequencies depend on the two cable lengths and the mass ratio.Fig. 10. Variation of first and second mode frequencies when m l l 8.121=+.。
- 1、下载文档前请自行甄别文档内容的完整性,平台不提供额外的编辑、内容补充、找答案等附加服务。
- 2、"仅部分预览"的文档,不可在线预览部分如存在完整性等问题,可反馈申请退款(可完整预览的文档不适用该条件!)。
- 3、如文档侵犯您的权益,请联系客服反馈,我们会尽快为您处理(人工客服工作时间:9:00-18:30)。
combining fuzzy inference with neural network in the power balance control system. II. CONTROL SCHEME When belt conveyor is working, its driving motor's output power is [4]: P = 3UIη cos ϕ (1)
978-1-4244-7050-1/10/$26.00 c 2010 IEEhm is put forward. In the power balance control system, the belt speed v is a reference variable, while motor currents are the basis for adjusting. So a T/2 forecast algorithm is adopted in current collection, where T is sampling period.
International Conference on Intelligent Control and Information Processing August 13-15, 2010 - Dalian, China
Power Balance Control of Multi-motor Driving Belt System using Fuzzy Neural Network
B
I. INTRODUCTION
ELT conveyor is a common transport equipment in coal industry, and it is often driven by several alike type motors in the applications of big transportation burden, long distance and high belt speed. Whereas the output powers of these motors are usually unbalance which may reduce production efficiency, and even destroy the equipment and lead to great economic loss. Furthermore, the power unbalance problem can exist in various multi-motor driving occasions, so the research on this subject has both economic and theoretical value. For the characteristics of multivariable, big delay, nonlinear and time-variation, accurate mathematical model of belt conveyor system driven by several motors is difficult to be established. So in recent years intelligent control, such as fuzzy control, is introduced in this system. It is a valid way by constituting language system and converting it to a inference of control strategy. The fuzzy method has been adopted in a belt system driven by two motors [1], and got some effects, but it still had delay and did not learn fuzzy rules on-line [2]. For three-motor-driving belt system, Juan Qi has used BP network to predict system's outputs, but its inference speed was very slow and was liable to local minimum [3]. In this paper, a parameter forecast method is introduced and a new control idea is presented and simulated. That is
For the same type motors, the η 、 cos ϕ are almost equal, and power network voltage U is a definite value, so the change of motor current can represent the change of power. Taking three-motor-driving as an example, the structure diagram of power balance control system is shown in Fig.1. According to motor currents, three catheters of variable speed fluid coupling that linked to three motors act
Manuscript received April 21, 2010. Lihong Mo is with the Faculty of Electronic and Electrical Engineering, Huaiyin Institute of Technology, Huai’an, CO 223003 China (phone:0086-15950399140; e-mail:xueren502@). Shuai Chen is with Huaiyin Institute of Technology, Huaian, CO 223003 China (e-mail:chen4307@). Yeqin Wang is with the Faculty of Electronic and Electrical Engineering, Huaiyin Institute of Technology, Huai’an, CO 223003 China (e-mail:yeqin-wang@).
Abstract—Multi-motor driving belt conveyor system has the characteristics of nonlinear, big delay and multivariable. To achieve its power balance control, a T/2 parameter forecast method was introduced, and a multi-variable fuzzy controller was built. It adopted currents as control variables and belt speed as the reference. For its too many rules a modified CPN (Counter Propagation Network) was analyzed. It can realize fuzzy algorithm by executing pattern matching and weight average. Meanwhile membership functions and rules can be adjusted on-line. Simulation was made and compared with BP and conventional CPN algorithms. Results show that it has faster learning convergence speed and stronger generalization than the other two, and has faster response speed, smaller overshoot and steady-state error than fuzzy algorithm. The trained network was tested on a three-10kw-motor driving system, and power kept balance within its 4%, which donates that the modified CPN is suitable for this system.
Fig. 1. The block diagram of power-balance control system 1. Controller 2. Motor 3. Actuator 4. Variable speed fluid coupling 5. Speed reducer 6. Belt conveyor 7. Cylinder drive 8. Speed sensor
correspondingly. For example, if a motor current is bigger than expected, its linked coupler’s catheter will be adjusted to reduce the inner oil-contended content, and thus decrease the power of this motor. Taking the middle motor current among the three as the reference( I ∑ ), we can make the other two move toward it, that is, if a single motor current I n is bigger than I ∑ , the catheter will be pushed in to reduce the inner oil-contended content of coupler and its connecting motor's output power will decrease thereupon. On the contrary, if I n is smaller than I ∑ , the catheter will be pulled outward to increase the inner oil-contended content and then enhance the motor's output power. And if I n is within the allowable range of I ∑ , the catheter will not act. III. CURRENT FORECAST In view of the system's hysteretic character, a parameter