塑性加工工艺与设备
GB-50241 工业金属塑性加工工程施工及验收规范

GB-50241 工业金属塑性加工工程施工及验收规范1. 范围本规范适用于新建、扩建、改建和迁建的工业金属塑性加工工程,包括锻造、轧制、挤压、拉拔、铸造等工序。
本规范规定了工业金属塑性加工工程施工及验收的要求、程序和标准。
2. 规范性引用文件下列文件对于本文件的应用是必不可少的,凡是注日期的引用文件,仅所注日期的版本适用于本文件。
凡是不注日期的引用文件,其最新版本(包括所有的修改单)适用于本文件。
GB 50009-2012 建筑结构荷载规范GB 50010-2010 混凝土结构设计规范GB 50017-2003 钢结构设计规范GB 50018-2002 冷弯薄壁型钢设计规范GB 50019-2003 热轧型钢设计规范GB 50020-2002 钢结构设计规范GB 50028-2006 城镇燃气设计规范GB 50041-2008 热水锅炉房设计规范GB 50044-2008 热力管道设计规范GB 50046-2006 蒸汽锅炉房设计规范GB 50053-1994 工业炉内部设计规范GB 50057-2010 建筑物防雷设计规范GB 50060-2008 电力变压器选择设计规范GB 50068-2001 工业金属管道设计规范GB 50093-2013 自动化仪表工程施工质量验收规范GB 50109-2010 工业炉砌筑工程施工质量验收规范GB 50110-2010 工业炉热工测试与调节设计规范GB 50113-2009 工业炉热工设备安装工程施工质量验收规范GB 50121-2005 工业炉机械设备安装工程施工质量验收规范GB 50126-2003 工业炉调试与验收规范GB 50160-2008 石油化工企业设计防火标准GB 50169-2012 电气装置安装工程设计规范GB 50183-2004 石油天然气工程设计防火规范GB 50187-2012 工业企业总平面设计规范GB 50188-2012 工业炉冷却水系统设计规范GB 50191-2012 工业炉炉底通风设计规范GB 50201-2015 工业炉炉体结构设计规范GB 50202-2018 工业炉砌筑工程施工及验收规范GB 50203-2011 工业炉热工测试与调节施工及验收规范GB 50204-2015 工业炉热工设备安装工程施工及验收规范GB 50205-2020 工业炉机械设备安装工程施工及验收规范GB 50206-2012 工业炉调试与验收规范GB 50233-2014 工业金属管道工程施工及验收规范GB 50236-2011 工业炉热工设备安装工程施工及验收规范GB 50241-2008 工业金属塑性加工工程施工及验收规范GB 50242-2002 工业炉机械设备安装工程施工及验收规范GB 50243-2016 工业炉调试与验收规范GB 50244-2008 工业炉砌筑工程施工及验收规范GB 50245-2015 工业炉热工设备安装工程施工及验收规范GB 50246-2018 工业炉热工测试与调节施工及验收规范GB 50247-2018 工业炉调试与验收规范GB 50248-2018 工业金属管道工程施工及验收规范GB 50249-2018 工业金属塑性加工工程施工及验收规范GB 50250-2018 工业金属塑性加工设备安装工程施工及验收规范GB 50251-2018 工业金属塑性加工设备调试与验收规范GB 50252-2018 工业金属塑性加工设备维护与保养规范GB 50253-2014 工业金属塑性加工设备安全技术规范GB 50254-2018 工业金属塑性加工设备检验与检测规范GB 50255-2018 工业金属塑性加工设备使用与操作规范GB 50256-2018 工业金属塑性加工设备安装与调试规范GB 50257-2018 工业金属塑性加工设备验收与评估规范GB 50258-2018 工业金属塑性加工设备改造与升级规范GB 50259-2018 工业金属塑性加工设备设计与选型规范GB 50260-2018 工业金属塑性加工设备材料选择与处理规范GB 50261-2018 工业金属塑性加工设备润滑与冷却规范GB 50262-2018 工业金属塑性加工设备电气控制与自动化规范GB 50263-2018 工业金属塑性加工设备机械结构与传动规范GB 50264-2018 工业金属塑性加工设备液压与气动规范GB 50265-2018 工业金属塑性加工设备热处理与表面处理规范GB 50266-2018 工业金属塑性加工设备焊接与连接规范GB 50267-2018 工业金属塑性加工设备检验与检测规范GB 50268-2018 工业金属塑性加工设备安全技术规范GB 50269-2018 工业金属塑性加工设备使用与操作规范GB 50270-2018 工业金属塑性加工设备安装与调试规范GB 50271-2018 工业金属塑性加工设备验收与评估规范GB 50272-2018 工业金属塑性加工设备改造与升级规范GB 50273-2018 工业金属塑性加工设备设计与选型规范GB 50274-2018 工业金属塑性加工设备材料选择与处理规范GB 50275-2018 工业金属塑性加工设备润滑与冷却规范GB 50276-2018 工业金属塑性加工设备电气控制与自动化规范GB 50277-2018 工业金属塑性加工设备机械结构与传动规范GB 50278-2018 工业金属塑性加工设备液压与气动规范GB 50279-2018 工业金属塑性加工设备热处理与表面处理规范GB 50280-2018 工业金属塑性加工设备焊接与连接规范GB 50281-2018 工业金属塑性加工设备检验与检测规范GB 50282-2018 工业金属塑性加工设备安全技术规范GB 50283-2018 工业金属塑性加工设备使用与操作规范GB 50284-2018 工业金属塑性加工设备安装与调试规范GB 50285-2018 工业金属塑性加工设备验收与评估规范GB 50286-2018 工业金属塑性加工设备改造与升级规范GB 50287-2018 工业金属塑性加工设备设计与选型规范GB 50288-2018 工业金属塑性加工设备材料选择与处理规范GB 50289-2018 工业金属塑性加工设备润滑与冷却规范GB 50290-2018 工业金属塑性加工设备电气控制与自动化规范GB 50291-2018 工业金属塑性加工设备机械结构与传动规范GB 50292-2018 工业金属塑性加工设备液压与气动规范GB 50293-2018 工业金属塑性加工设备热处理与表面处理规范GB 50294-2018 工业金属塑性加工设备焊接与连接规范GB 50295-2018 工业金属塑性加工设备检验与检测规范GB 50296-2018 工业金属塑性加工设备安全技术规范GB 50297-2018 工业金属塑性加工设备使用与操作规范GB 50298-2018 工业金属塑性加工设备安装与调试规范GB 50299-2018 工业金属塑性加工设备验收与评估规范GB 50300-2018 工业金属塑性加工设备改造与升级规范GB 50301-2018 工业金属塑性加工设备设计与选型规范GB 50302-2018 工业金属塑性加工设备材料选择与处理规范GB 50303-2018 工业金属塑性加工设备润滑与冷却规范GB 50304-2018 工业金属塑性加工设备电气控制与自动化规范GB 50305-2018 工业金属塑性加工设备机械结构与传动规范GB 50306-2018 工业金属塑性加工设备液压与气动规范GB 50307-2018 工业金属塑性加工设备热处理与表面处理规范GB 50308-2018 工业金属塑性加工设备焊接与连接规范GB 50309-2018 工业金属塑性加工设备检验与检测规范GB 50310-2018 工业金属塑性加工设备安全技术规范GB 50311-2018 工业金属塑性加工设备使用与操作规范GB 50312-2018 工业金属塑性加工设备安装与调试规范GB 50313-2018 工业金属塑性加工设备验收与评估规范GB 50314-2018 工业金属塑性加工设备改造与升级规范GB 50315-2018 工业金属塑性加工设备设计与选型规范GB 50316-2018 工业金属塑性加工设备材料选择与处理规范GB 50317-2018 工业金属塑性加工设备润滑与冷却规范GB 50318-2018 工业金属塑性加工设备电气控制与自动化规范GB 50319-2018 工业金属塑性加工设备机械结构与传动规范GB 50320-2018 工业金属塑性加工设备液压与气动规范GB 50321-2018 工业金属塑性加工设备热处理与表面处理规范GB 50322-2018 工业金属塑性加工设备焊接与连接规范GB 50323-2018 工业金属塑性加工设备检验与检测规范GB 50324-2018 工业金属塑性加工设备安全技术规范GB 50325-2018 工业金属塑性加工设备使用与操作规范GB 50326-2018 工业金属塑性加工设备安装与调试规范GB 50327-2018 工业金属塑性加工设备验收与评估规范GB 50328-2018 工业金属塑性加工设备改造与升级规范GB 50329-2018 工业金属塑性加工设备设计与选型规范GB 50330-2018 工业金属塑性加工设备材料选择与处理规范GB 50331-2018 工业金属塑性加工设备润滑与冷却规范GB 50332-2018 工业金属塑性加工设备电气控制与自动化规范GB 50333-2018 工业金属塑性加工设备。
塑性成形的特点与基本生产方式

一.板料冲压的基本工序
分离工序:落料、冲孔、切断、切口 变形工序:弯曲、拉深、翻边、成形
1、分离工序
将冲压件与板料按要求的轮廓线分离的工序,如剪 切、落料、冲孔。落料和冲孔总称为冲裁。
(2)冲裁件断裂面
① 蹋角带 ② 光亮带:表面光滑,断
面质量最好。 ③ 剪裂带:表面粗糙,略
带斜度。 ④ 毛刺:微裂纹出现时产
July 2021
2、Our destiny offers not only the cup of despair, but the chalice of opportunity. (Richard Nixon, American President )命运给予我们的不是失望之酒,而是机会之杯。二〇二一年六月十七日2021年6月17日星期四
难易程度。
衡量指标:
塑性 变形抗力
目 标:
塑性好 变形抗力小
影响锻造性能的因素:(1)金属本质 (2)变形条件
1. 金属本质的影响
纯金属锻造性能好
化学成分
合金差 碳钢,含碳量越少,锻造性能越好
硫、磷含量越少,可锻性越好
内部组织
纯金属、固溶体可锻性好 金属碳化物差 细晶粒好,粗晶粒差
2. 变形条件的影响
(1)变形温度
适当高温利于锻造
过热
温度过高产生
过烧 氧化
脱碳
在始锻与终锻温度之间
温 度 /C °
1538A 固相线液相线 L
1250 始锻温度L+A
碳 钢
的
E
A
锻
造
G 912
温
800
A+Fe3CⅡ
度
A+F
K
第三篇(塑性加工)

纤维组织的稳定性很高,不能用热处理或其它方法加以消 除,只有经过锻压使金属变形,才能改变其方向和形状。 合理利用纤维组织
应使零件在工作中所受的最大正应力方向与纤维方向重合;
最大切应力方向与纤维方向垂直; 并使纤维分布与零件的轮廓相符合,尽量不被切断。
§1-3
金属的可锻性
金属材料通过塑性加工获得优质零件的难易程度。 (经塑性加工而不断裂) 塑性
三拐曲轴的锻造过程
§2-1 锻造方法
自由锻特点
●
坯料表面变形自由;
● 设备及工具简单,锻件重量不受限制; ● ● ●
锻件的精度低; 生产率低,适用于单件小批生产; 是大型锻件的唯一锻造方法。
§2-1 锻造方法
模锻
使加热后的金属在模膛内
受压变形以获得所需锻件 的方法。 应用: 大批量生产中小锻件。 <150Kg,如曲轴、连 杆、齿轮。
在冷加工时,形变强化使金属塑性降低,进
一步加工困难,应安排中间退火工艺。 实质:塑性变形时位错运动受阻,使交叉滑移中位错运动范围缩小,因 此,金属性能随之改变。
一、金属材料产生加工硬化
金属材料 强度和硬 度提高, 塑性和韧 性下降。
有利:加工硬化可提高产品性能! 不利:进一步的塑性变形带来困难! 加热可消除硬化现象!
压力使金属成型为各种型材和锻件等。
a)自由锻 b)模锻 c)胎模锻 胎模锻:自由锻设备上,采用不与上、下砧相连接的活动模具 成形锻件的方法。是介于自由锻和模锻之间的锻造工艺方法。 2)冲压 利用冲模将金 属板料切离或变形 为各种冲压件。
3)轧制 使金属坯料通过两个旋转轧辊之间的间隙而产生塑性变形的 加工方法。 用于生产各种型材、管材、板材等。
模锻
模锻是利用锻模使坯 料变形而获得锻件的 锻造方法。
金属塑性成型工艺

第二篇金属的塑性成形工艺金属塑性成形——在外力作用下,金属产生了塑性变形,以此获得具有一定形状、尺寸和机械性能的原材料、毛坯或零件。
此生产方法称金属塑性成形(也称压力加工)外力冲击力——锤类设备压力——轧机、压力机有一定塑性的金属——压力加工(热态、冷态)基本生产方法:1.轧制——钢板、型材、无缝管材(图6-1)(图6-2)2.挤压——低碳钢、非铁金属及其合金(图6-3)(图6-4)3.拉拔——各种细线材,薄壁管、特殊几何形状的型材(图6-5)(图6-6)4.自由锻——坯料在上、下砥铁间受冲击力或压力而变形(图6-7a)5.模锻——坯料在锻模模腔内受冲击力或压力而变形(图6-7b)6.板料冲压——金属板料在冲模之间受压产生分离或变形的加工方法(图6-7c)金属的原材料,大部通过轧制、挤压、拉拔等制成。
第六章金属塑性成形的工艺理论基础压力加工——对金属施加外力→塑性变形金属在外力作用下,使其内部产生应力——发生弹性变形外力>屈服应力塑性变形塑性变形过程中一定有弹性变形存在,外力去除后,弹性变形将恢复→“弹复”现象,它对有些压力加工件的变形和工件质量有很大影响,须采取工艺措施的保证产品质量。
§6-1 塑性变形理论及假设一、最小阻力定律金属塑性成形问题实质,金属塑性流动,影响金属流动的因素十分复杂(定量很困难)。
应用最小阻力定律——定性分析(质点流动方向)最小阻力定律——受外力作用,金属发生塑性变形时,如果金属颗粒在几个方向上都可移动,那么金属颗粒就沿着阻力最小的方向移动。
利用此定律,调整某个方向流动阻力,改变金属在某些方向的流动量→成形合理。
最小阻力定律示意图在镦粗中,此定律也称——最小周边法则二、塑性变形前后体积不变的假设弹性变形——考虑体积变化塑性变形——假设体积不变(由于金属材料连续,且致密,体积变化很微小,可忽略)此假设+最小阻力定律——成形时金属流动模型三、变形程度的计算变形程度——用“锻造比”表示拔长时锻造比为: T 拔=Fo/F镦粗时锻造比: Y 镦=Ho/H式中:H 0、F 0——坯料变形前的高度和横截面积H 、F ——坯料变形后的高度和横截面积T 锻=2~2.5 (要求横向力学性能)纵向Y 锻↑由Y 锻可得坯料的尺寸。
塑性成形第14章塑性加工工艺(轧制挤压)
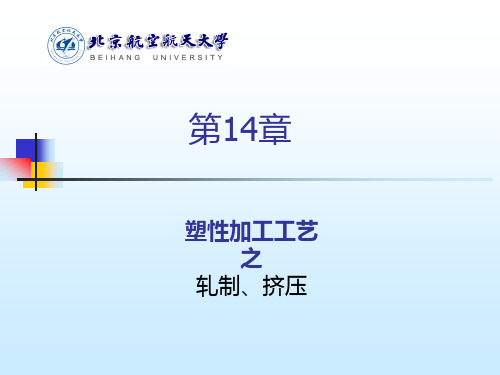
品表面光洁、板形平直、尺寸精度高和机械性能好。 工艺特点: (1)加工温度低,产生加工硬化,需要中间退火。 (2)采用工艺冷却和润滑 (3)张力轧制
管材轧制
(1)压下量
h h0 h1 h 2R(1 cos)
咬入角 entering angle
D R
O
(2)变形区长度
l2 R2 (R h )2 2
h0
a
A
C
B
l
h1
l Rh (h2 ) Rh 4
b1
b0
tg
R
Rh ( h)
h R
2
h 2R
(3)延伸系数 λ=L1/L0
(4)压下率Biblioteka 表面夹杂暴露在钢材表面上的非金属物质称为 (1)钢坯带来的表面非金属夹杂物。 表面夹杂,一 般呈点状、块状和条状 (2)在加热或轧制过程中,偶然有非金 分布,其颜色有暗红、淡黄、灰白等, 属夹杂韧(如加热炉的耐火材料及炉 机械的粘结在型钢表面上,夹杂脱落 渣等),炉附在钢坯表面上,轧制时 后出现一定深度的凹坑,其大小、形 被压入钢材,冷却经矫直后部分脱落 状无一定规律。
名。例工、槽、角钢的腿长、腿短、腰 (2)切深孔切人太深,造成腿长无法消除。 厚、腰薄及一腿长,一腿短。
斜轧穿孔生产管材
板带材轧制
特点:宽厚比(B/H)大 规格:中厚板(中板4~20mm,厚板20~60mm,
特厚板60mm以上) 薄板和带材(0.2~4mm) 极薄带材和箔材(0.001~0.2mm) 技术要求: 尺寸精度、板形、表面光洁度、性能
《塑性加工工艺》课件

强度
强度是材料在塑性加工过程中抵抗形变的能力,可以通 过抗拉强度等参数来评估。
塑性加工的变形和回弹
1
变形
材料在塑性加工过程中会发生持久性的形变,改变其初始形状。
2
回弹
塑性材料在受力解除后,可能会出现一定程度的恢复原状的现象。
3
影响因素
变形和回弹程度受材料的硬度、强度和加工工艺等因素的影响。
塑性加工的参数和工艺控制
材料要求 高塑性 易加工 良好的延展性 耐热
物理性质 弹性模量低 低熔点 变形温度、形变速率等参数,以及材料的力学性 质对加工过程的影响。
塑性加工中的应变和强度概念
应变
应变是材料在塑性加工过程中发生形变的程度,可以通 过应变曲线来描述。
高塑性
塑性材料具有良好的可塑性和可延展性,适用于各 种加工工艺。
耐腐蚀
塑性材料通常具有良好的耐腐蚀性能,适用于化工 等领域。
轻质
塑性材料相比于金属材料更轻,因此适用于需要轻 质结构的应用领域。
应用领域
塑性材料广泛应用于汽车制造、电子产品、包装材 料等领域。
塑性加工的分类及其工艺流程
1
热塑性加工
材料通过加热软化后,经过挤压、吹塑等工
1 温度
控制加热温度可以影响材料的流动性和成型效果。
2 压力
合理的施加压力可以保证塑性材料充分填充模具,并使产品形状更加精确。
3 速度
控制运动速度可以影响产品的表面质量和成型效率。
塑性加工中的模具设计和加工 工艺
模具设计和加工工艺决定了产品的精度和质量,包括模具材料的选择、结构 设计等方面。
热固性加工
2
艺进行加工。
材料通过加热固化后,经过模压、压缩成型
第八章塑性加工

第八章塑性加工※8·1 锻造成形8·2 板料冲压成形8·3 挤压、轧制、拉拔成形8·4 特种塑性加工方法8·5 塑性加工零件的结构工艺性8·6 塑性加工技术新进展本章小结塑性加工的基本知识塑性变形的主要形式:滑移、孪晶。
滑移的实质是位错的运动。
金属经过塑性变形后将使其强度、硬度升高,塑性、韧性降低。
即产生形变强化。
此外,还将形成纤维组织。
塑性加工特点:1·塑性加工产品的力学性能好。
2·精密塑性加工的产品可以直接达到使用要求,不须进行机械加工就可以使用。
实现少、无切削加工。
3·塑性加工生产率高,易于实现机械化、自动化。
4·加工面广(几克~几百吨)。
常用的塑性加工方法:锻造、板料冲压、轧制、挤压、拉拔等。
8·1 锻造成形8·1·1 自由锻定义、手工自由锻、机器自由锻设备(锻锤和液压机)1·自由锻工序(基本工序、辅助工序、精整工序)基本工序:镦粗、拔长、弯曲、冲孔、切割、扭转、错移辅助工序:压钳口、压钢锭棱边、切肩各种典型锻件的锻造2·自由锻工艺规程的制订(举例)8·1·2 模锻定义、特点(生产率高、尺寸精度高、加工余量小、节约材料,减少切削、形状比自由锻的复杂、生产批量大但质量不能大)1·锤上模锻2·压力机上模锻8章塑性加工拔长29使坯料横截面减小而长度增加的锻造工序称为拔长。
拔长主要用于轴杆类锻件成形,其作用是改善锻件内部质量。
(1)拔长的种类。
有平砥铁拔长、芯轴拔长、芯轴扩孔等。
8章塑性加工30芯轴拔长8章塑性加工芯轴扩孔型砧拔长圆形断面坯料冲孔采用冲子将坯料冲出透孔或不透孔的锻造工序叫冲孔。
其方法有实心冲子双面冲孔、空心冲子冲孔、垫环冲孔等。
8章塑性加工各种典型锻件的锻造1、圆轴类锻件的自由锻2、盘套类锻件的自由锻3、叉杆类锻件的自由锻4、全纤维锻件的自由锻8章塑性加工典型锻件的自由锻工艺示例43锻件名称工艺类别锻造温度范围设备材料加热火次齿轮坯自由锻1200~800℃65kg空气锤45钢1锻件图坯料图序号工序名称工序简图使用工具操作要点1局部镦粗火钳镦粗漏盘控制镦粗后的高度为45mm序号工序名称工序简图使用工具操作要点2冲孔火钳镦粗漏盘冲子冲孔漏盘(1)注意冲子对中(2)采用双面冲孔3修整外圆火钳冲子边轻打边修整,消除外圆鼓形,并达到φ92±1 mm续表序号工序名称工序简图使用工具操作要点4修整平面火钳镦粗漏盘轻打使锻件厚度达到45±1 mm续表自由锻工艺规程的制订(1)绘制锻件图(敷料或余块、锻件余量、锻件公差)※锻件图上用双点画线画出零件主要轮廓形状,并在锻件尺寸线下面用括号标出零件尺寸。
金属塑性加工工艺
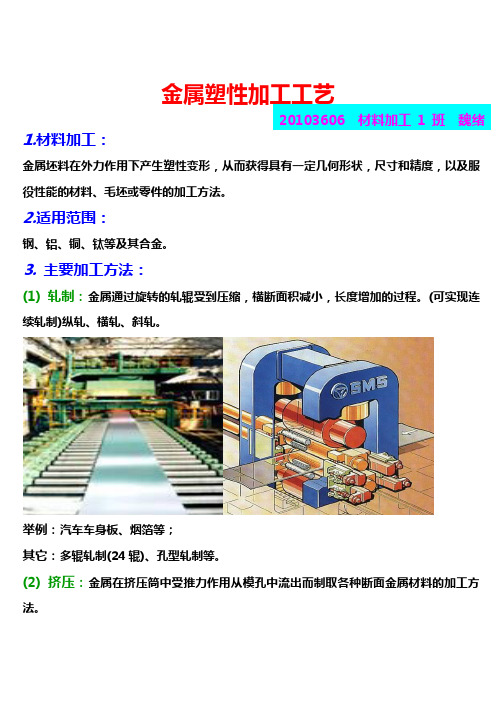
金属塑性加工工艺20103606 材料加工1班魏绪1.材料加工:金属坯料在外力作用下产生塑性变形,从而获得具有一定几何形状,尺寸和精度,以及服役性能的材料、毛坯或零件的加工方法。
2.适用范围:钢、铝、铜、钛等及其合金。
3.主要加工方法:(1) 轧制:金属通过旋转的轧辊受到压缩,横断面积减小,长度增加的过程。
(可实现连续轧制)纵轧、横轧、斜轧。
举例:汽车车身板、烟箔等;其它:多辊轧制(24辊)、孔型轧制等。
(2) 挤压:金属在挤压筒中受推力作用从模孔中流出而制取各种断面金属材料的加工方法。
定义:金属材料在挤压模内受压被挤出模孔而变形的加工方法。
挤压法非常适合于生产品种、规格、批数繁多的有色金属管、棒、型材及线坯。
正挤压—— 坯料流动方向与凸模运动方向一致。
反挤压—— 坯料流动方向与凸模运动方向相反。
举例:管、棒、型;其它:异型截面。
特点: ① 具有比轧制更为强烈的三向压应力状态图,金属可以发挥其最大的塑性,获得大变形量。
可加工用轧制或锻造加工有困难甚至无法加工的金属材料。
② 可生产断面极其复杂的,变断面的管材和型材。
卧式挤压机 正挤反挤③灵活性很大,只需更换模具,即可生产出很多产品。
④产品尺寸精确,表面质量好。
(3) 锻造:锻锤锤击工件产生压缩变形•定义:借助锻锤、压力机等设备对坯料施加压力,使其产生塑性变形,获得所需形状、尺寸和一定组织性能的锻件。
垂直方向(Z向)受力,水平方向(X、Y向)自由变形。
A.自由锻:金属在上下铁锤及铁砧间受到冲击力或压力而产生塑性变形的加工我国自行研制的万吨级水压机B.模锻:金属在具有一定形状的锻模膛内受冲击力或压力而产生塑性变形的加工。
举例:飞机大梁,火箭捆挷环等。
万吨级水压机模锻的飞机大梁、火箭捆挷环特点:在塑性变形中,能使坯料的粗晶粒破碎、疏松、孔隙被压实、焊合,锻件的内部组织和性能得到较大改善。
应用:锻造应用十分的广泛,可以生产几克重到200t以上各种形状的锻件,如各种轴类、曲柄和连杆。
材料成型工艺学 金属塑性加工
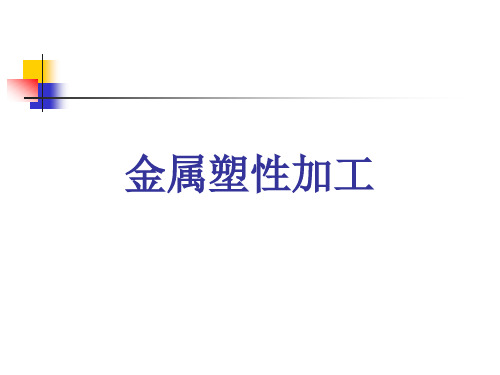
二、模锻件的结构工艺性
1. 模锻件上必须具有一个合理的分模面 2. 零件上只有与其它机件配合的表面才需进行机械加工,
其它表面均应设计为非加工表面 (模锻斜度、圆角) 3. 模锻件外形应力求简单、平直和对称。避免截面间差别
过大, 薄壁、高筋、高台等结构 (充满模膛、减少工序) 4. 尽量避免深孔和多孔设计 5. 采用锻- 焊组合结构
自由锻设备:锻锤 — 中、小型锻件 液压机 — 大型锻件
在重型机械中,自由锻是生产大型和特大型锻件的 惟一成形方法。
1.自由锻工序 自由锻工序:基本工序 辅助工序 精整工序
(1) 基本工序 使金属坯料实现主要的变形要求, 达
到或基本达到锻件所需形状和尺寸的工序。 有:镦粗、拔长、冲孔、弯曲、
扭转、错移、切割 (2) 辅助工序
金属的力学性能的变化:
变形程度增大时, 金属的强度及硬度升高, 而塑 性和韧性下降。
原因:由于滑移面上的碎晶块和附近晶格的强烈 扭曲, 增大了滑移阻力, 使继续滑移难于进行所致。
几个现象:
▲ 加工硬化
(冷变形强化): 随变形程度增大, 强度和硬度上升而塑性下降的现象。
▲回复:使原子得以回复正常排列, 消除了晶格扭曲, 致使
§3 金属的可锻性
金属的可锻性:材料在锻造过程中经受塑性变形 而不开裂的能力。
金属的可锻性好,表明该金属适合于采用压力加工 成形; 可锻性差,表明该金属不宜于选用压力加工方法 成形。
衡量指标:金属的塑性(ψ、δ ); 变形抗力(σb、HB)。
塑性越好,变形抗力越小,则金属的可锻性好。
金属的可锻性取决于金属的本质和加工条件。
弹复:
金属塑性变形基本规律:
体积不变定律: 金属塑变后的体积与变形前的体积相等。
金属塑性加工工艺
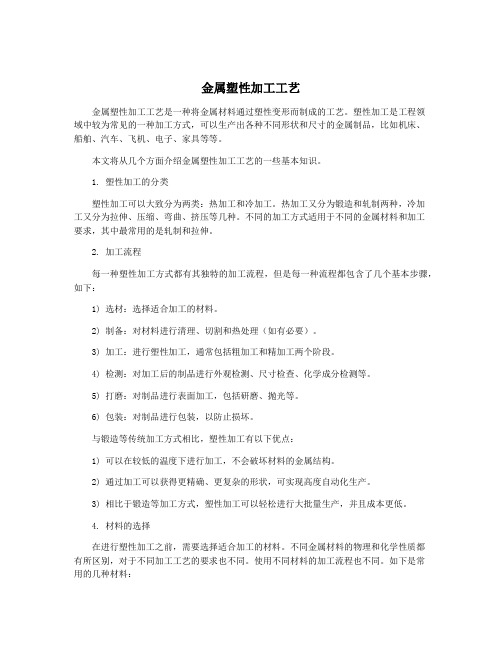
金属塑性加工工艺金属塑性加工工艺是一种将金属材料通过塑性变形而制成的工艺。
塑性加工是工程领域中较为常见的一种加工方式,可以生产出各种不同形状和尺寸的金属制品,比如机床、船舶、汽车、飞机、电子、家具等等。
本文将从几个方面介绍金属塑性加工工艺的一些基本知识。
1. 塑性加工的分类塑性加工可以大致分为两类:热加工和冷加工。
热加工又分为锻造和轧制两种,冷加工又分为拉伸、压缩、弯曲、挤压等几种。
不同的加工方式适用于不同的金属材料和加工要求,其中最常用的是轧制和拉伸。
2. 加工流程每一种塑性加工方式都有其独特的加工流程,但是每一种流程都包含了几个基本步骤,如下:1) 选材:选择适合加工的材料。
2) 制备:对材料进行清理、切割和热处理(如有必要)。
3) 加工:进行塑性加工,通常包括粗加工和精加工两个阶段。
4) 检测:对加工后的制品进行外观检测、尺寸检查、化学成分检测等。
5) 打磨:对制品进行表面加工,包括研磨、抛光等。
6) 包装:对制品进行包装,以防止损坏。
与锻造等传统加工方式相比,塑性加工有以下优点:1) 可以在较低的温度下进行加工,不会破坏材料的金属结构。
2) 通过加工可以获得更精确、更复杂的形状,可实现高度自动化生产。
3) 相比于锻造等加工方式,塑性加工可以轻松进行大批量生产,并且成本更低。
4. 材料的选择在进行塑性加工之前,需要选择适合加工的材料。
不同金属材料的物理和化学性质都有所区别,对于不同加工工艺的要求也不同。
使用不同材料的加工流程也不同。
如下是常用的几种材料:1) 铝:适合进行拉伸、挤压等冷加工流程。
总之,对于不同的加工工艺都需要选择不同的材料,以便在加工过程中获得最佳效果。
5. 结论。
塑性加工
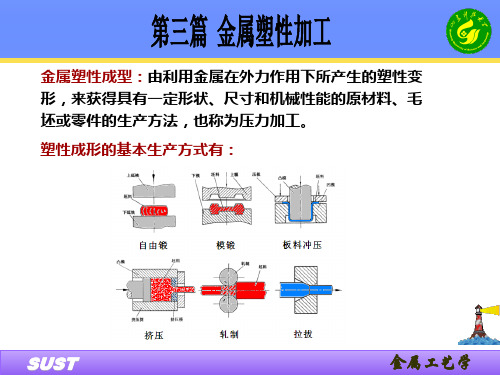
钳口、压肩、倒棱等
(3)修整工序——为减少锻件表面缺陷(不平、歪扭等)进行的
工序。如校正、滚圆、平整等
SUST
金属工艺学
一、自由锻
基本工序
SUST
金属工艺学
一、自由锻
基本工序
圆截面拔长
SUST
金属工艺学
一、自由锻
基本工序
矩形截面拔长
SUST
金属工艺学
一、自由锻
基本工序
SUST
金属工艺学
一、自由锻
SUST
金属工艺学
二、变形工序(拉深)
拉深:使坯料在凸模的作用下压入凹模, 获得空心体零件的冲压工序。
SUST
金属工艺学
二、变形工序(拉深)
变形过程
SUST
金属工艺学
二、变形工序(拉深)
拉深中的废品
拉裂(拉穿)
起皱
SUST
金属工艺学
二、变形工序(拉深)
防止皱折:加压边圈 压边力不宜过 大能压住工件不致 起皱即可。
(2)应变速率:也称变形速度,是应变相对于时间的变化率。
SUST
金属工艺学
三、金属的可锻性
(3)应力状态:通过受力物体内一点的各个截面上的应力状况
简称为物体内一点处的应力状态,常用主应力图来定性地说明。
压应力数量越多,数值越大,金属的塑性就越好。
SUST
金属工艺学
利用冲击力或压力使金属在抵铁间或锻模中变形, 从而获得所需形状和尺寸的锻件的工艺方法称为锻造。
一、分离工序(冲裁)
冲裁变形过程
a圆角带 b光亮带 c断裂带 d毛刺
SUST
金属工艺学
一、分离工序(冲裁)
凸凹模间隙 考虑到模具制造 中的偏差及使用 中的磨损,生产 中通常是选择一 个适当的范围作 为合理间隙,这 个范围的最小值 称为最小合理间 隙,最大值称为 最大合理间隙。
塑性加工工艺

塑性加工工艺塑性加工工艺是一种将塑料材料加工成各种形状和尺寸的方法。
塑性加工工艺广泛应用于塑料制品的生产中,包括塑料零件、塑料容器和塑料包装等。
首先,塑性加工工艺包括热塑性和热固性两种类型。
热塑性加工工艺是指将塑料材料加热至一定温度后,通过外力使其变形成所需的形状。
这种加工工艺常用于塑料制品的注塑、挤出和吹塑等过程。
热固性加工工艺则是将塑料材料加热至一定温度后,通过化学反应使其固化成为硬质塑料。
这种加工工艺常用于制作热固性塑料制品,如玻璃纤维增强塑料和环氧树脂工件。
其次,塑性加工工艺还包括一系列的步骤和设备。
其中,塑料材料的预处理是塑性加工的重要步骤之一,它包括塑料颗粒的干燥和混合等过程。
此外,塑性加工还需要一系列的设备,如注塑机、挤出机、吹塑机和模具等。
这些设备可以根据不同的塑料制品要求进行调整和控制,以完成塑性加工过程。
再次,塑性加工工艺在实际应用中具有很高的灵活性和适应性。
通过调整加工温度、流量速度和压力等参数,可以控制塑料制品的形状和尺寸。
此外,还可以通过添加填充剂、增塑剂和颜料等辅助材料,改变塑料制品的性能和外观。
最后,塑性加工工艺在现代工业生产中发挥着重要作用。
它具有加工周期短、成本低和生产效率高等优势,广泛应用于汽车、家电、电子、包装和建筑等行业。
随着科学技术的不断发展,塑性加工工艺也在不断创新和改善,以满足人们对塑料制品的多样化需求。
塑性加工工艺在现代工业生产中扮演着重要的角色。
随着科技的进步和人们对塑料制品需求的增加,塑性加工工艺变得越来越复杂和多样化。
下面将继续介绍一些常见的塑性加工工艺。
一种常见的塑性加工工艺是注塑。
注塑是使用注塑机将加热熔化的塑料材料注入模具中,然后在一定的压力和温度下保持一段时间,使塑料快速冷却硬化成型。
注塑工艺适用于制造各种形状和尺寸的塑料零件,如电子产品外壳、汽车零部件和家用电器配件等。
注塑工艺具有生产效率高、成本低、产品质量稳定的优点,因此被广泛应用于各个行业。
精确塑性成形工艺技术概念
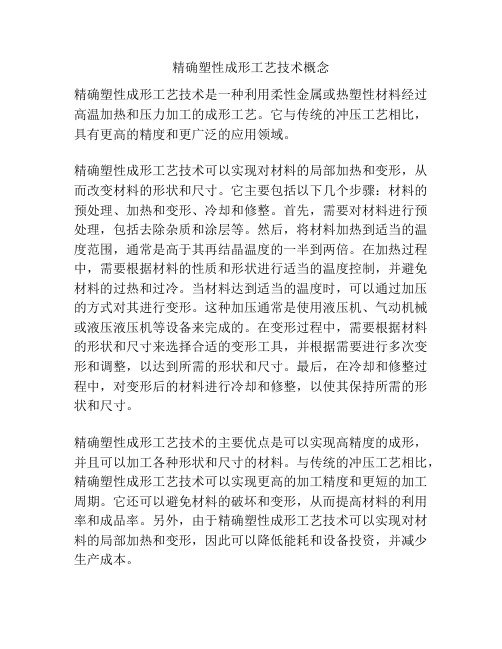
精确塑性成形工艺技术概念精确塑性成形工艺技术是一种利用柔性金属或热塑性材料经过高温加热和压力加工的成形工艺。
它与传统的冲压工艺相比,具有更高的精度和更广泛的应用领域。
精确塑性成形工艺技术可以实现对材料的局部加热和变形,从而改变材料的形状和尺寸。
它主要包括以下几个步骤:材料的预处理、加热和变形、冷却和修整。
首先,需要对材料进行预处理,包括去除杂质和涂层等。
然后,将材料加热到适当的温度范围,通常是高于其再结晶温度的一半到两倍。
在加热过程中,需要根据材料的性质和形状进行适当的温度控制,并避免材料的过热和过冷。
当材料达到适当的温度时,可以通过加压的方式对其进行变形。
这种加压通常是使用液压机、气动机械或液压液压机等设备来完成的。
在变形过程中,需要根据材料的形状和尺寸来选择合适的变形工具,并根据需要进行多次变形和调整,以达到所需的形状和尺寸。
最后,在冷却和修整过程中,对变形后的材料进行冷却和修整,以使其保持所需的形状和尺寸。
精确塑性成形工艺技术的主要优点是可以实现高精度的成形,并且可以加工各种形状和尺寸的材料。
与传统的冲压工艺相比,精确塑性成形工艺技术可以实现更高的加工精度和更短的加工周期。
它还可以避免材料的破坏和变形,从而提高材料的利用率和成品率。
另外,由于精确塑性成形工艺技术可以实现对材料的局部加热和变形,因此可以降低能耗和设备投资,并减少生产成本。
精确塑性成形工艺技术广泛应用于汽车、航空航天、电子、医疗器械等工业领域。
在汽车工业中,它主要用于生产汽车零部件,如车身、发动机、悬挂系统等。
在航空航天工业中,它主要用于生产飞机和航天器的结构件和连接件。
在电子工业中,它主要用于生产电子元件和电子设备的外壳等。
在医疗器械领域,它主要用于生产人工关节、人工心脏瓣膜等。
综上所述,精确塑性成形工艺技术是一种利用柔性金属或热塑性材料经过高温加热和压力加工的成形工艺。
它具有高精度、灵活性、成本低等优点,被广泛应用于汽车、航空航天、电子、医疗器械等工业领域。
塑性成形重要知识点总结

塑性成形重要知识点总结塑性成形是一种通过应变作用将金属材料变形为所需形状的加工方法,也是金属加工领域中的一种重要工艺。
以下是塑性成形的重要知识点总结。
1.塑性成形的原理塑性成形是通过施加外力使金属材料发生塑性变形,使其形状和尺寸发生改变。
塑性成形的原理包括应力与应变关系、材料的流动规律和力学模型等。
2.塑性成形的分类塑性成形可以根据加工过程的不同进行分类,主要包括拉伸、压缩、挤压、弯曲、冲压等。
不同的成形方法适用于不同的材料和形状要求。
3.塑性成形的设备塑性成形通常需要使用专门的设备进行加工,包括拉伸机、压力机、挤压机、弯曲机、冲床等。
这些设备提供必要的力量和变形条件,使金属材料发生塑性变形。
4.金属材料的选择不同的金属材料具有不同的塑性特性,因此在塑性成形中需要根据不同的应用需求选择合适的材料。
常用的金属材料包括钢、铝、铜、镁等。
5.塑性成形的加工方法塑性成形的加工方法非常多样,包括冲压、拉伸、挤压、压铸、锻造等。
不同的加工方法适用于不同的材料和形状要求,可以实现复杂的金属成形。
6.塑性成形的工艺参数塑性成形的工艺参数对成形质量和效率具有重要影响。
常见的工艺参数包括温度、应变速率、应力等。
合理的工艺参数可以提高成形质量和生产效率。
7.塑性成形的变形行为塑性成形过程中金属材料的变形行为是研究的重点之一、金属材料的变形行为包括弹性变形、塑性变形和弹变回复等,通常通过应力-应变曲线来描述。
8.塑性成形的缺陷与控制塑性成形过程中可能发生一些缺陷,如裂纹、皱纹、细化等。
为了控制这些缺陷,需要采取合适的工艺和工艺措施,如加热、模具设计优化等。
9.塑性成形的优点与局限塑性成形具有成本低、加工效率高、灵活性好等优点,可以制造出复杂的金属零件。
然而,塑性成形也存在一些局限性,如对材料性能有一定要求、成形限制等。
10.塑性成形的应用领域塑性成形广泛应用于各个领域,如汽车制造、航空航天、电子、家电等。
不仅可以生产大批量的零部件,还可以满足不同产品的形状和性能要求。
塑性成形第17章塑性加工工艺(新技术

塑性加工新技术及发展趋势
塑性加工的一般情况
塑性加工过程是在外力(载荷)和一定的加载方式、 加载速度、约束条件、几何形状、接触摩擦条件、温 度场等作用下对材料进行“力”处理和“热处理”的 过程,使材料发生所希望的几何形状的变化(成形) 与组织性能的变化。
塑性加工具有高效、优质、低耗等特点,是材料加工 和零部件制造的重要手段。据粗略估计,有75%的零 件毛坯和50%的精加工零件是采用塑性成形的方式完 成的。
塑性加工新技术
柔性快速制造技术:无模多点成形和数控渐进 成形,借助于高度可调整的基本体群构成离散 的上、下工具表面,代替传统的上、下模具进 行板材的曲面成形;
复合材料塑性成形技术:双金属复合、铝塑复 合板、管、叠层材料成形;
复合加工方式的技术:连续挤压、连续铸挤、 连铸连轧和连续铸轧等。
新能源的利用---- 激光
改变超声波强度,可改变坯料变形阻力和设备载荷,大 幅度提高产品的质量和材料成形极限;
管材、线材和棒材的拉拔成形、板材拉深成形都可以引 入超声波,形成塑性成形新技术,成为一些特殊新材料 的有效加工途径。
功率超声波成形
柔性成形技术
以软介质(主要是各种液体)代替半边刚性模具, 减小模具制造成本;
显著地提高材料的抗疲劳和抗应力腐蚀等性能,
激光冲击成形原理
吸收层:黑漆、石墨、铝箔 约束层:水、树脂、硅胶
单次激光冲击下板料的典型成形截面
新能源的利用----电磁场力
利用金属材料在交变电磁场中产生感生电流(涡流), 感生电流又受到电磁场的作用力,当电磁压力达到材料 的屈服强度时,金属材料将发生塑性变形;
凹模的高覆模性, 可控性好:单脉冲冲压变形可控在0.035mm,最大变形可控在若
金属塑性加工技术5-有色金属板带材生产

连铸连轧工艺流程
熔炼、连铸、轧制、冷却、卷 取等环节组成,具有高效、节 能、环保等优点。
连铸连轧设备
包括熔炼炉、结晶器、轧机、 冷却装置、卷取机等,设备精 度和稳定性对产品质量影响较
大。
熔融纺丝法
熔融纺丝原理
将高分子聚合物加热至熔融状态,通 过喷丝孔挤出形成纤维,并在冷却过 程中固化。
有色金属纤维制备
将有色金属粉末与高分子聚合物混合, 经过熔融纺丝制备出有色金属纤维。
熔融纺丝设备
包括熔融装置、喷丝头、冷却装置、 卷取装置等,设备参数对纤维的直径 和形态有重要影响。
熔融纺丝法应用
主要用于制备连续的有色金属纤维, 在复合材料、增强材料等领域有广泛 应用。
其他生产技术
粉末冶金法
通过粉末制备和压制烧结等工艺制备有 色金属板带材,具有材料利用率高、产
表面处理
根据需要,对板带材进行热处理,以调整 其内部组织结构,提高其力学性能和耐腐 蚀性能。
对板带材进行表面处理,如涂装、电镀等 ,以提高其装饰性和功能性。
市场现状与发展趋势
市场现状
随着经济的发展和科技的进步,有色金属板带材市场需求不断增长,尤其在新能 源汽车、5G通信等领域,对高性能有色金属板带材的需求更为迫切。
在熔融纺丝过程中,金属材料的熔 融状态需要保持稳定,否则会导致
纺丝过程中断或产品质量下降。
B
C
D
解决方案
优化纺丝喷嘴设计,提高喷嘴的均匀性和 稳定性,同时控制纺丝速度和温度,以保 证金属丝的均匀性。
纺丝均匀性问题
在熔融纺丝过程中,金属丝的均匀性是关 键,不均匀的丝可能导致产品质量下降。
塑性加工工艺

锤上模锻:速度高、金属流动速度快,f降低,金属流动的惯性和变形的热效应突出,有利于挤入方式成形。压力机上模锻:在一次行程中坯料内外层同时变形,变形深透均匀、流线分布连续、锻件力学性能一致性较好。
第六节 板材成形
定义:通过模具和冲压设备,使板材产生塑性变形,获得具有一定形状、尺寸和性能的冲压件的加工方法。特点:生产效率高,产品尺寸精度稳定,材料利用率高,操作简便,易实现自动化 。分类: 分离(冲裁)— 落料、冲孔、切割 成形—弯曲、拉深、胀形、翻边
拉拔成形原理示意图
2. 拉拔方法 实心材拉拔—棒材、型材、线材 空心材拉拔—管材
3. 特点(1)拉拔制品尺寸精度高,表面光洁度好。(2)工具与设备简单,维护方便。(3)最适合于连续高速生产断面尺寸小的长制品。(4)拉拔道次变形量和两次退火间的总变形量受到限制,工艺过程长。过大的道次加工率将导致制品尺寸、形状不合格,甚至被拉断。原因是变形区内为两压一拉应力状态,不利于充分发挥金属的塑性。
小结: 挤压法非常适合于生产品种、规格、批数繁多的有色金属管、棒、型材及线坯。在生产断面复杂的或薄壁的管材和型材,直径与壁厚之比趋近于2的超厚壁管材,以及脆性的有色金属和钢铁材料方面,挤压法是唯一可行的压力加工方法。
二、挤压基本理论
正挤压时金属的流动
(1)填充挤压阶段:锭筒间隙,填充系数 Rt=Ft/F0坯锭的长度与直径之比
(2)基本挤压阶段挤压比=锭坯断面积/制品断面积
纵向线两次弯曲,弯曲角度由外向内逐渐缩小。压缩锥(变形区)。横向线弯曲。外层网格变形为平行四边形,说明承受了剪切变形,外层金属的主延伸变形比内层的大,沿纵向制品后端的主延伸变形比前端的大。使用平模或大模角锥模挤压时,都存在死区。模角增大、摩擦加大、挤压比减小、挤压速度降低,死区增大。死区的存在对提高制品表面质量极为有利。棒材前端横向线弯曲很小,制品头部晶粒粗大,机械性能低劣,应切除。
冲床的概念是什么

冲床的概念是什么冲床是一种常见的金属加工设备,用于对金属材料进行塑性成形的加工工艺。
冲床采用冲击力将金属板材或其他金属材料置于模具中,在模具的作用下通过冲压,使金属材料发生塑性变形,从而得到所需的零件或产品。
冲床是金属冲压工艺中一种重要的设备,广泛应用于制造各种零部件,例如汽车零部件、电器零部件、家具五金件等。
冲床的工作原理是通过压力机的压力将金属板材放置在模具的工作台上,然后通过模具的下冲运动对金属板材进行塑性加工。
冲床的工作过程通常包括送料、下冲、退料和上冲等步骤,每个步骤都经过精确的控制和协调,以保证冲压过程的准确性和效率。
冲床通常由以下几个主要部分组成:机架、滑块、床身、驱动装置和控制系统。
其中,机架作为支撑和固定整个冲床的结构,具有高度稳定性和刚性;滑块是冲床上下运动的主要部件,其采用滑动连接或滚动连接方式与机架相连;床身是放置工件的工作台,具有平整且坚固的表面,用于保证冲床上下运动时的稳定性;驱动装置通常由电动机、减速器、离合器和齿轮机构组成,用于提供冲床运动所需的动力和力量;控制系统由电气元件、液压元件和计算机等组成,用于控制和监控冲床的各项操作参数,以确保冲压过程的准确性和稳定性。
冲床在金属加工中具有许多优点。
首先,冲床采用模具进行加工,可以快速、高效地批量生产具有相同形状的零部件,提高生产效率。
其次,冲床加工时保持金属板材的冲压温度较低,有利于保持材料的力学性能和表面质量。
此外,冲床具有较高的加工精度和一致性,能够满足对尺寸和形状要求较高的零部件的加工需求。
此外,冲床还可以加工各种不同材料的金属板材,如碳钢、不锈钢、铝合金等,具有很高的适应性。
不过,冲床也存在一些局限性和挑战。
首先,冲床的模具制造成本较高,需要具备一定的设计和制造能力。
其次,冲床对材料的要求较高,材料的韧性和塑性决定了冲床能否成功加工。
另外,冲床加工过程中材料会发生一定程度的应力和变形,因此需要对模具和冲床进行严格的检验和维护,以确保加工质量。
有色金属塑性加工工艺设计课程设计

一、绪言1.1挤压加工的特点所谓挤压,就是对放在容器(挤压桶)中的锭坯一端施加以压力,使之通过模孔成型的一种的压力加工方法。
挤压方法有很多种,最基本的方法是正挤压与反挤压,按坯料温度区又可分为热挤压、冷挤压和温挤压3种。
作为生产管、棒、型材以及线坯的挤压法与其他加工方法,如型材轧制和斜扎穿孔相比具有以下一些优点:(1)具有比轧制更为强烈的三向压应力状态图,金属可以发挥其最大的塑性;(2)不只是可以再一台设备上生产形状简单的管、棒和型材,而且还可以生产断面及其复杂的,以及变断面的管材和型材;(3)具有极大的灵活性,在同一台设备上能够生产出很多的产品品种和规格;(4)产品尺寸精确,表面质量高;(5)实现生产过程自动化和封闭化比较容易。
综上所述可知,挤压法非常适合于生产品种、规格和批数繁多的有色金属管、棒、型材以及线坯等。
在生产断面复杂的或薄壁的管材和型材,直径与壁厚之比趋近于2的超厚壁管材,以及脆性的有色金属和钢铁材料方面,挤压法是唯一可行的压力加工方法。
1.2铝合金的特点及经济地位铝合金是工业中应用最广泛的一类有色金属结构材料,其密度低,但强度比较高,接近或超过优质钢,塑性好,可加工成各种型材,具有优良的导电性、导热性和抗蚀性,可分为防锈铝、硬铝、超硬铝等种类,各种类均有各自的使用范围,并有各自的代号,以供使用者选用。
铝合金的一系列优良特性,使之在金属材料的应用中,仅次于钢材而居第二位。
目前全世界铝材的消费量在1800万吨以上,其中用于交通运输(包括铁道车辆、汽车、摩托车、自行车、汽艇、快艇、飞机等)的铝材约占27%,用于建筑装修的铝材约23%,用于包装工业的铝材约占20%。
随着中国经济建设的高速发展,人民生活水平的不断提高,中国的建筑行业发展迅速,包括铝型材在内的建筑装饰材料不断增加。
铝型材的应用已经扩展到了国民经济的各个领域和人民生活的各个层面。
1.3铝合金型材的成分性能铝合金型材具有强度高、重量轻、稳定性强、耐腐蚀性强、可塑性好、变形量小、无污染、无毒、防火性强、使用寿命长(可达50—100年)、回收性好以及可回炉重炼等特点。
- 1、下载文档前请自行甄别文档内容的完整性,平台不提供额外的编辑、内容补充、找答案等附加服务。
- 2、"仅部分预览"的文档,不可在线预览部分如存在完整性等问题,可反馈申请退款(可完整预览的文档不适用该条件!)。
- 3、如文档侵犯您的权益,请联系客服反馈,我们会尽快为您处理(人工客服工作时间:9:00-18:30)。
(4)摩擦↑,挤压力↑。 (5)模角 (6)锭坯长度↑, 挤压力↑ (7)反挤压力比 正挤压力低 20~30%。
挤压机主体结构
后置式穿孔缸
•
挤压机的主要零部件: 挤压机的主要零部件:
• • • • • 模座 机架 压余分离装置 调整装置 挤压牵引机构
纵动式模座
(
横动式模座
回转式模座
角钢
槽钢
工字钢
孔型系统示例
六、线材轧制
• 特点: (1)总的延伸率大,轧件温降快,头尾温差大,轧制速度高。 (2)机架多、分工细,产品比较单一、轧机专业程度高。 (3)高速无扭转轧机具有特殊的孔型节 挤压
一、挤压原理、基本方法 及特点
1. 挤压定义:对放在挤压筒内的金属坯料 施加压力,使之从特定的模孔中流出, 获得所需断面形状和尺寸的一种塑性加 工方法。 2. 挤压方法: 可按挤压方向、变形特征、 润滑状态、挤压温度、挤压速度、模具 种类或结构、坯料形状或数目、制品形 状或数目分类。
二、挤压基本理论
1. 正挤压时金属的流动
挤 压 力 P
正挤压
反挤压 Ⅰ Ⅱ 挤压轴位移 Ⅲ
(1)填充挤压阶段: 锭筒间隙,填充系数 Rt=Ft/F0 坯锭的长度与直径之比
(2)基本挤压阶段 挤压比λ=锭坯断面积/制品断面积
圆棒正挤压时子午面上网格变化示意图
锥模挤压 平模挤压
• 纵向线两次弯曲,弯曲角度由外向内逐渐缩小。 压缩锥(变形区)。 • 横向线弯曲。 • 外层网格变形为平行四边形,说明承受了剪切变 形,外层金属的主延伸变形比内层的大,沿纵向 制品后端的主延伸变形比前端的大。 • 使用平模或大模角锥模挤压时,都存在死区。模 角增大、摩擦加大、挤压比减小、挤压速度降低, 死区增大。死区的存在对提高制品表面质量极为 有利。 • 棒材前端横向线弯曲很小,制品头部晶粒粗大, 机械性能低劣,应切除。
3. 咬入条件
α
φ
θ
a R N N
Nx
T T
Tx
P
T
咬入时
咬入后
α≤β
β ≥ϕ = α +θ
2
改善咬入条件的途径: (1)降低α角: (2)提高β角:
4. 轧制压力 (1)轧制压力的基本概念 轧制压力是轧制时轧辊施加于轧件使之变形 的力。但通常把轧件施加于轧辊总压力的垂 直分量称为轧制压力。
R α
(σ x + dσ x )(h + dh) − hσ x + 2( Pr dx dx ) sin θ ± 2 µ ( Pr ) cosθ = 0 cosθ cosθ
dθ
θ
pr
h1
h+Δh
h0
σx+dσx
σx prcosθ pr
α
μpr μpr μprsinθ μprcosθ
h
prsinθ Rdθ
hdσ x + σ x dh + 2 Pr tgθdx ± 2 µPr dx = 0
单孔模设计
模角 工作带长度 模孔尺寸 入口圆角半径 模孔出口处直径 模子外形尺寸
挤压模具的设计
多孔模设计
模孔数目 模孔排列原则 型材模孔设计
重心布置 模孔布置 工作带长度设计
挤压模具的设计
分流组合模设计
挤压比 分流比 分流孔 分流桥 模芯 焊合室
挤压模具的制造
模具材料的选择 模具的加工
机械加工 热处理
挤压工艺设计
锭坯尺寸的选择
选择原则 挤压比的确定 锭坯长度的确定
•温度的选择 温度的选择 •速度的选择 速度的选择 •润滑剂的选择 润滑剂的选择
第四节 拉拔加工
一、拉拔原理、方法、特点
1.拉拔定义: 在外加拉力的作用下,迫使金属通过模孔 产生塑性变形,以获得与模孔形状、尺寸相 同的制品的加工方法,称之为拉拔(或称为 拉伸)。是生产管材、棒材、型材及线材的 主要方法之一。
θ
H
tθ
dx l
x
h
a γ dx dx dx P = B∫ p cosθ + B ∫ t sin θ − B ∫ t sin θ γ cos θ 0 0 cos θ cosθ a
一般通称的轧制压力或实测的轧制总压 力,并非为轧制单位压力之合力,而是轧制 单位压力、单位摩擦力的垂直分量之和。
(2)轧制力的理论计算
二、拉拔基本原理
1. 圆棒拉拔时的应力与变形
dN dR
β
dT
α
D1
D2
拉拔制品内部的周期性裂纹示意 图
D2
D1
2. 管材拉拔时的应力与变形 (1)空拉 σ
σl
r
σr
σl
α1 α
σr σl σr σl
εr εθ εr εθ
减壁厚
εl
增壁厚
εl
• 空拉时的主应力: σ1—轴向应力σl σ2—径向应力σr σ3—切向应力σθ 空拉时的壁厚变化取决于σr- σm σm=( σ1+ σ2+σ3)/3 σr- σm >0,管壁增厚 σr- σm =0,管壁不变 σr- σm<0,管壁变薄 空拉能起到自动纠正管坯偏心的作用。
常用挤压方法
3. 特点: ① 具有比轧制更为强烈的三向压应力状态图, 金属可以发挥其最大的塑性,获得大变形 量。可加工用轧制或锻造加工有困难甚至 无法加工的金属材料。 ② 可生产断面极其复杂的,变断面的管材和 型材。 ③ 灵活性很大,只需更换模具,即可生产出 很多产品。 ④ 产品尺寸精确,表面质量好。
dN dT
dN
dN
dN
σr
坯料
σθ εr εθ
σl
dT
α
P
坯料
εl
坯料
拉拔成形原理示意图
2. 拉拔方法 实心材拉拔—棒材、型材、线材 空心材拉拔—管材
3. 特点 (1)拉拔制品尺寸精度高,表面光洁度好。 (2)工具与设备简单,维护方便。 (3)最适合于连续高速生产断面尺寸小的长制品。 (4)拉拔道次变形量和两次退火间的总变形量受到 限制,工艺过程长。过大的道次加工率将导致制品 尺寸、形状不合格,甚至被拉断。原因是变形区内 为两压一拉应力状态,不利于充分发挥金属的塑性。
联合式模座
挤压杆
挤压垫片
穿孔针
四、挤压模具
• 挤压模具类型 • 整体模 • 可拆卸模 • 舌模 • 分流组合模
整体模
(a) 平平
(b)平平平
(c) 双锥平
(d) 锥平
(e) 平锥平
(f) 碗圆平
可拆卸模具
挤压模具的设计
整体模的设计
单孔模设计 多孔模的设计
舌形模的设计 分流模的设计
挤压模具的设计
——冯.卡尔曼微分方程 积分,采里科夫解,求得Pr与θ(即h)的关系 式,则影响Pr的主要因素如下:
轧制力的影响:
a. 轧辊弹性压扁 任何一台给定的轧机,都有一个最小可轧制厚度值, 低于这一厚度,轧辊会产生很大变形,而被轧制的材料 无任何塑性变形。 b. 轧辊弯曲 会导致所生产的金属板中心厚边缘薄。 c. 轧机弹性或塑性 轧辊分离力使机架产生变形,辊缝增大
1.变形区主要参数 轧件在轧辊作用下产生变形的 区域 叫变形区,变形区以外两端 不 产生变 形的区域叫外区或刚端。
(1)压下量
∆h = 2 R(1 − cos α )
h0
D O a A l C B h1 b1 R
∆h = h0 − h1
∆h 2 l = R − (R − ) 2 ∆h 2 l = R∆h − ( ) ≈ R∆h 4
2 2
(2)变形区长度
tgα =
R∆h ∆h ≈ ∆h R R−( ) 2
2
∆h ≈ µ R
b0
(3)延伸系数 λ=L1/L0 (4)压下率
ε = (∆h / h0 ) ×100%
(5)宽展
∆b =b1-b0
2. 轧制过程中的金属流动 前滑区 后滑区 中性面: 轧件运动速度=轧辊线速度的水平分量 中性角: γ = α (1 − α ) 2 2β 秒流量相等原则:单位时间内通过变形区内 任一横断面的金属体积应该为一常数。 FHvH=Fxvx=Fhvh=常数
⑤ 工艺流程简单,设备投资少,实现生产过程 自动化和封闭化比较容易。 ⑥ 金属的固定废料损失较大。压余量10~15%, 轧件的切头尾损失仅为1~3%。 ⑦ 加工速度低。 ⑧ 沿长度和断面上制品的组织、性能不够均一。 ⑨ 工具消耗较大。
小结: 挤压法非常适合于生产品种、规格、批数繁多 的有色金属管、棒、型材及线坯。在生产断面复杂 的或薄壁的管材和型材,直径与壁厚之比趋近于2的 2 超厚壁管材,以及脆性的有色金属和钢铁材料方面, 挤压法是唯一可行的压力加工方法。
5. 轧制力矩
M = Pa
(b0 + b1) P= pF = p R∆h 2 ψ为力臂系数,一 a = ψ R∆h 般取ψ=0.3~0.6
(b0 + b1 ) M=p R∆hψ 2
M = pR∆hψ(b0 + b1)
二、轧制方法
1. 按轧制温度 热轧 冷轧 2. 按轧件与轧辊的相对运动关系 纵轧:轧辊的纵轴线相互平行,轧件运动方向 与延伸方向与轧辊纵轴线垂直。 斜轧:轧辊的纵轴线倾斜互成一定角度,轧件 边旋转边沿自身纵轴线方向前进,且前进 方 向与轧辊纵轴线方向成一定角度。 横轧:轧辊的纵轴线相互平行,轧件沿自己的 横轴线方向运动前进,与轧辊纵轴线垂直。
3. 按轧制生产过程 半成品轧制—开坯 成品轧制—粗轧、精轧
纵轧
斜轧
横轧
三、板带材轧制
特点:宽厚比(B/H)大 规格:中厚板(中板4~20mm,厚板20~60mm, 特厚板60mm以上) 薄板和带材(0.2~4mm) 极薄带材和箔材(0.001~0.2mm) 技术要求: 尺寸精度、板形、表面光洁度、性能