教案表面技术概论气相沉积技术
表面处理技术概论-气相沉积技术

⑤被溅射出来的原子具有的能量要比由真空蒸发飞 出的原子所具有的能量(大约在0.1eV)大1~2个 数量级。
第五章 气相沉积技术
⑵ 溅射原子、分子的形态
• 单体物质引起溅射时,通常,离子的加速 电压越高,被溅射出来的单原子就越少, 复合粒子就越多。通常把这种复合粒子称 为群。
第五章 气相沉积技术
常见电阻式加热器
第五章 气相沉积技术 电阻蒸发沉积的缺点:
• ①加热所能达到最高温度有限,加热器的 寿命也较短。
• ②坩埚的成本高 • ③蒸发率低; • ④加热时合金或化合物会分解
第五章 气相沉积技术
5.1.3 电子束蒸发沉积
电阻蒸发存在许多致命的缺点,如蒸发物与坩 埚发生反应;蒸发速率较低。 为了克服这些缺点,可以通过电子轰击实现材 料的蒸发。 在电子束蒸发技术中,一束电子通过5~10kV 的电场后被加速→最后聚焦到待蒸发材料的表 面→当电子束打到待蒸发材料表面时,电子会 迅速损失掉自己的能量→将能量传递给待蒸发 材料使其熔化并蒸发。 也就是待蒸发材料的表面直接由撞击的电子束 加热,这与传统的加热方式形成鲜明的对照。
第五章 气相沉积技术
• 电子束源形式多样,性能可靠,但电子束 蒸发设备较为昂贵,且较为复杂。如果应 用电阻加热技术能获得所需要的薄膜材料, 一般则不使用电子束蒸发。
• 在需要制备高纯度的薄膜材料,同时又缺 乏合适的盛装材料时,电子束蒸发方法具 有重要的实际意义。
第五章 气相沉积技术
电子束加热装置
第五章 气相沉积技术
5.1.4 溅射沉积
• 利用带有电荷的离子在电场中加速后具有 一定动能的特点,将离子引向欲被溅射的 靶电极。在离子能量合适的情况下,入射 的离子将在与靶电极表面的原子的碰撞过 程中使后者溅射出来。这些被溅射出来的 原子带有一定的动能,并且会沿着一定的 方向射向基材,从而实现在基材表面上的 沉积。
表面技术(第8讲 气相沉积技术(Ⅱ))
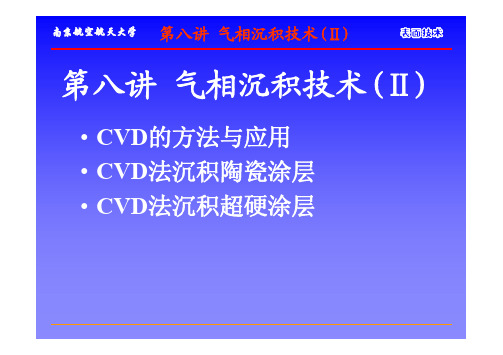
南京航空航天大学
第八讲 气相沉积技术(Ⅱ)
表面技术
5. CVD技术的应用
• 1).复合材料制备:CVD法制备的纤维状或晶 须状的沉积物多半用来制造各种复合材料; • 2).微电子学工艺:CVD法制备半导体膜的外 延、p-n结扩散源的形成、介质隔离、扩散掩 膜和金属膜,CVD法制备高纯硅、使半导体 进入了集成化的新时代; • 3).半导体光电技术:CVD法可以制备半导体 激光器、半导体发光器件、光接受器、集成 光路等;
南京航空航天大学
第八讲 气相沉积技术(Ⅱ)
表面技术
金刚石厚膜透波窗口
0.7 0.6 0.5 0.4
(a)10×10的透明金刚石样品
1000
2000
3000
4000
成核面与生长面的透射率曲线 (b) 多尺寸透明金刚石样品
南京航空航天大学
第八讲 气相沉积技术(Ⅱ)
表面技术
金刚石工具
金刚石 厚膜刀具
金 刚 石 涂 层 刀 具
直流等离子喷 射CVD设备
南京航空航天大学
第八讲 气相沉积技术(Ⅱ)
表面技术
南京航空航天大学
第八讲 气相沉积技术(Ⅱ)
表面技术
大面积均匀CVD金刚石厚膜沉积
CVD厚膜
SEM及Raman 谱
南京航空航天大学
第八讲 气相沉积技术(Ⅱ)
表面技术
南京航空航天大学
第八讲 气相沉积技术(Ⅱ)
表面技术
大面积曲面金刚石厚膜沉积
南京航空航天大学
第八讲 气相沉积技术(Ⅱ)
表面技术
2. CVD的化学反应类型
南京航空航天大学
第八讲 气相沉积技术(Ⅱ)
表面技术
3. CVD技术主要工艺参数
第24教学单元表面处理新技术1--气相沉积技术

2
冶金与建筑工程系
教
案
真空槽中散发,蒸发原子在各个方向的通量并不相等。基体设在蒸气源 的上方阻挡蒸气流,且使基体保持相对较低的温度,蒸气则在其上形成 凝固膜。为了弥补凝固的蒸气,蒸发源要以一定的比例供给蒸气。 真空容器(提供蒸发所需的真 空环境)。 蒸发源(为蒸镀材料的 蒸发提供热量)。 基片(即被镀工件,在 它上面形成蒸发料沉 积层),基片架(安装夹 持基片)。 加热器。 蒸发镀膜系统 蒸发成膜过程是由蒸发、蒸发材料粒子的迁移和沉积三个过程所组成。
冶金与建筑工程系
教
案
第
课
24
教学单元
题:表面处理新技术 1—气相沉积技术 知识目标 掌握气相沉积技术各种方法的原理 能选择合适的气相沉积技术进行镀膜 爱岗敬业 诚实守信 技能过硬 自主创新
教学 目标 能力目标 职业素质目标 教学重点 教学难点 辅助教学手段 教学准备 授课班级 授课日期 月 日 月 日 月 日 月 日 月 日 各种气相沉积技术的原理 采用实物、标本、模型、图表、幻灯和录像等手段 准备教学目标、准备学生情况、准备教学材料、准备教学 心理、准备教学过程、准备教学评价
7
冶金与建筑工程系 布臵任务:1.蒸发镀的原理? 2.溅射镀膜的原理? 3.CVD 反应需满足的三个条件? 注:各栏大小可根据需要进行调整。
教粒子 基片 (工件)
被镀材料 蒸发过程
蒸发材料 粒子迁移 过程
蒸发材料 粒子沉积 过程
在真空容器中将蒸镀材料(金属或非金属)加热,当达到适当温度后, 便有大量的原子和分子离开蒸镀材料的表面进入气相。 因为容器内气压足够低,这些原子或分子几乎不经碰撞地在空间内 飞散, 当到达表面温度相对低的被镀工件表面时,便凝结而形成薄膜。
本科表面工程第5章 气相沉积技术
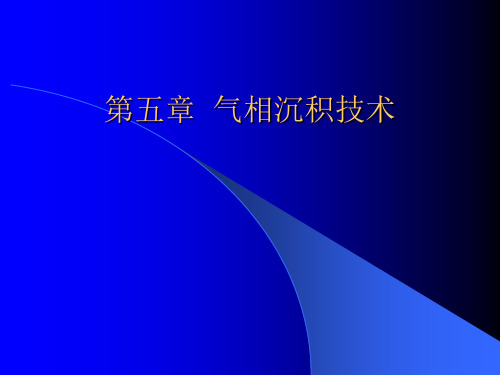
3. 蒸发源与基体表面的距离 近水楼台先得月 均镀能力不强→通过工件旋转弥补
四、蒸镀设备简介
1. 电阻加热法 原理:
电阻丝直接加热镀膜材料 (或蒸发器皿加热、或通过 坩埚加热镀膜材料)→蒸发 →沉积。 优点:设备简单 缺点: ① 坩埚污染或灯丝污染 ② 蒸发温度小于1500C,不 能用于高熔点成膜材料。 ③ 加热蒸发速度慢
⑵ 离化:
镀膜材料被加热蒸发,反应气 体(N)和蒸发粒子在等离子体 中部分离化(10-20%)。 ⑶ 沉积
在蒸发沉积的基础上,在工件 上加负偏压,吸引高能离子轰击 并沉积成膜。
⑷ 特点:
结合力高
沉积速率不太高→因离化率只 有10-20%。
2. 多弧离子镀
⑴ 蒸发离化 a 引弧→一触即离 b 弧光斑点高速游动在靶面 c 斑点在靶面上形成瞬间微熔池 d 因温度极高,熔料瞬间喷发并 大部离化,形成等离子体。 e 工作气体(N)亦被离化。
团(cluster)。 ③当原子数超过某一临界
值时就变为稳定核。 2. 长大
①稳定核通过捕获入射原 子的直接碰撞而长大。
⑤继续生长,和临近的稳 定核合并,进而变成连续膜。
三、影响蒸镀薄膜质量的因素
1. 基体表面状态 ① 表面清洁度→不洁表面会使膜基结合力↓ ② 基体温度 →T↑,有利于膜基结合力↓ ↘ ↘T↓,有利于膜的凝聚成核 → 矛盾 ③ 晶体结构 →膜基晶体结构相近,有利于薄膜的形核长大。
二、CVD的主要工艺参数
1. 温度:T↑,反应速度↑ ↘ 2. 压力:P ↑, 反应速度↑ →需高温、高压→最大问题 3. 反应物配比:如Ti、N,Si、O要匹配 三、CVD设备(以镀TiN涂层为例)
技能培训 材料表面工程学 气相沉积技术(一)
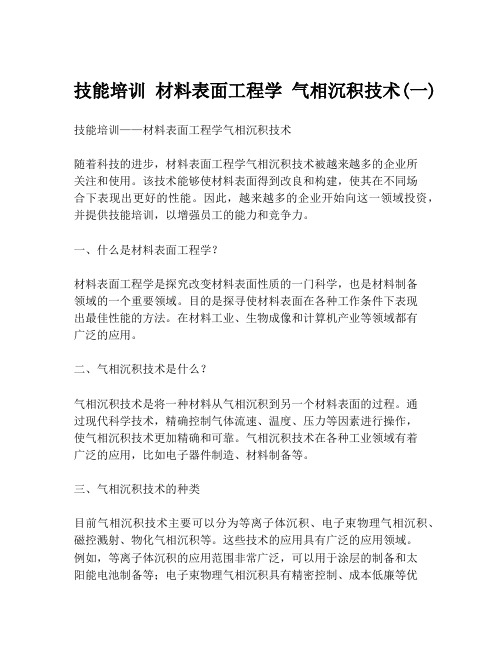
技能培训材料表面工程学气相沉积技术(一)技能培训——材料表面工程学气相沉积技术随着科技的进步,材料表面工程学气相沉积技术被越来越多的企业所关注和使用。
该技术能够使材料表面得到改良和构建,使其在不同场合下表现出更好的性能。
因此,越来越多的企业开始向这一领域投资,并提供技能培训,以增强员工的能力和竞争力。
一、什么是材料表面工程学?材料表面工程学是探究改变材料表面性质的一门科学,也是材料制备领域的一个重要领域。
目的是探寻使材料表面在各种工作条件下表现出最佳性能的方法。
在材料工业、生物成像和计算机产业等领域都有广泛的应用。
二、气相沉积技术是什么?气相沉积技术是将一种材料从气相沉积到另一个材料表面的过程。
通过现代科学技术,精确控制气体流速、温度、压力等因素进行操作,使气相沉积技术更加精确和可靠。
气相沉积技术在各种工业领域有着广泛的应用,比如电子器件制造、材料制备等。
三、气相沉积技术的种类目前气相沉积技术主要可以分为等离子体沉积、电子束物理气相沉积、磁控溅射、物化气相沉积等。
这些技术的应用具有广泛的应用领域。
例如,等离子体沉积的应用范围非常广泛,可以用于涂层的制备和太阳能电池制备等;电子束物理气相沉积具有精密控制、成本低廉等优势,在材料制备领域有着广泛的应用。
四、技能培训的必要性目前,企业面临快速发展的挑战,拥有高素质的员工才能提高企业的核心竞争力。
因此,企业需要提供全方位的培训来提高员工的工作技能和竞争力。
我们需要专门的培训机构来负责公司员工的技能培训,使他们在实践中掌握材料表面工程学和气相沉积技术,提高其技术水平和工作效率。
五、技能培训的目标技能培训的目标是使培训方式贴合企业的实际情况,提高员工工作技能和竞争力。
培训是一个全面的过程,需要从掌握材料表面工程学的基本原理和技术流程开始,逐步加深学习,如何运用气相沉积技术加工制造让材料表面性能得到提升。
六、结论在现代技术快速发展的时代,提高员工的技能水平显得尤为重要。
6现代表面技术-气相沉积技术-物理气相沉积

气相沉积( NPCVD)系统的压强约为一个大气压外,都是负
压。沉积气氛在真空室内反应,原料转化率高,可节省贵重 材料资源。
②一般说来,气相沉积可降低来自空气等的污染,所得到的 沉积膜或材料纯度高。例如,CVD法在蓝宝石基片上沉积αAl2O3单晶材料时,其杂质含量仅为30~ 34 mg/kg,远小于
气相沉积层的结构
气相沉积膜大多是晶体结构,沉积膜组织与沉积条件有 关 基片温度 表面状态 真空度 ...... 基片温度是决定膜组织的主要因素之一,基片温度高 ,蒸气原子的动能大,克服表面扩散激活能的几率增多,容 易发生结晶,并且膜中缺陷少,内应力小。基片温度高于膜 材熔点0.5Tm时,吸附原子扩散能力强,沉积膜得到再结晶 的等轴晶。基片温度较低,高于0.3Tm时,吸附原子扩散能 力较强,晶粒细化,得到致密的细柱状晶。基片温度低于 0.3Tm时,吸附原子难于扩散,容易形成岛状晶核,生成锥 状晶、粗柱状晶。基片温度过低将抑制结晶过程,发生非晶 态化转变,形成非晶态膜。
气相沉积的过程
气相沉积基体过程包括三个走骤: 提供气相镀料;
蒸发镀膜: 使镀料加热蒸发; 溅射镀膜: 用具有一定能量的离子轰击,从靶材上击出镀料原子。
镀料向所镀制的工件(或基片)输送 (在真空中进行,这主要是为了避免过多气体碰撞)
高真空度时(真空度为 10-2Pa): 镀料原子很少与残余气体分子碰撞,基本上是从镀源直线前进至基 片; 低真空度时(如真空度为 10Pa): 则镀料原子会与残余气体分子发生碰撞而绕射,但只要不过于降低 镀膜速率,还是允许的。 真空度过低,镀料原子频繁碰撞会相互凝聚为微粒,则镀膜过程无法 进行。
电刷镀
电子教案与课件:表面处理技术概论 第5章气相沉积技术
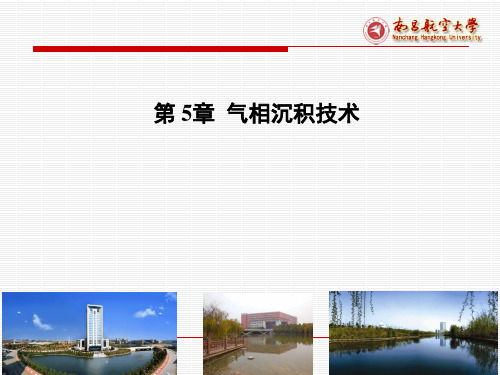
守形核和晶体长大的一般规律,当结晶条件受到抑制时,则按非晶化规律转变,形 成非晶膜。气相沉积的特殊性是气相直接凝固成固相。
5.2 气相沉积基础-分类
物理气相沉积(PVD)是把固态或液态成膜材料通过某种物理方式(高温蒸发、溅 射 、等离子体、离子束、激光束、电弧等)产生气相原子、分子、离子(气态、等离 子态),再经过输运在基体表面沉积,或与其他活性气体反应形成反应产物在基体 上沉积为固相薄膜的过程。
5.3 蒸发镀膜-过程
气相物质的产生:包括固相或液相转变为气相的相变过程(固相或液相→气相) ,每种物质在不同的温度有不同的饱和蒸气压。
气相物质在蒸发源与基片之间的输运:此过程中汽化原子或分子与残余气体分子 发生碰撞的次数决定于蒸发原子或分子的平均自由程以及蒸发源---基片的距离。
气相物质的沉积:蒸气的凝聚成核,核生长形成连续膜(气相→固相相变过程) 。
5.2 气相沉积基础-分类
化学气相沉积(CVD)是通过化学反应的方式,利用加热、等离子激励或光辐射等 各种能源,在反应器内使气态或蒸汽状态的化学物质在气相或气固界面上经化学反 应形成固态沉积物的技术。
5.3 蒸发镀膜
定义 真空蒸发(Vacuum Evaporation)镀简称蒸发镀,是在 真空条件下用蒸发器加热待蒸发物质,使其汽化并向 基板输送,在基板上冷凝形成固态薄膜的过程。 真空蒸发镀膜装置,一般由四部分组成: ✓ 真空室:用于放置镀件,进行镀膜的场所; ✓ 真空系统:机械泵、扩散泵、管道、阀门等; ✓ 蒸发系统:蒸发源,加热蒸发源的电气设备 ✓ 电气设备:真空测量系统,控制台等。
溅射镀膜:在真空室中,利用荷能粒子轰击材料表面,使 其原子获得足够的能量而溅出进入气相,然后在工件表面沉 积的过程。
教案表面技术概论气相沉积技术(优秀版)word资料

教案表面技术概论气相沉积技术(优秀版)word资料授课学时:3学时上连续蒸镀铝膜。
8.2.1 蒸镀原理和液体一样,固体在任何温度下会或多或少的气化(升华),形成该物质的蒸气。
蒸镀过程真空蒸镀时,蒸发粒子动能为~1.0ev,膜对基体的附着力较弱。
解决措施①加热基极,使基板保持适当的温度,使膜和基体之间形成一薄的扩散层,增大了附着力;②对于蒸镀像Au这样附着力弱的金属,可以先蒸镀像Cr,Al等结合力高的薄膜作底层。
8.蒸镀方法蒸发源:加热待蒸发材料并使之挥发的器具,也称加热器。
蒸镀方法:电阻加热法、电子束加热、高频感应加热、激光蒸镀法电子束加热:用高能电子束直接轰击蒸发物质的表面,使其蒸发。
电子束加热的特点:由于是直接在蒸发物质中加热,避免了蒸发物质与容器的反应和蒸发源材料的蒸发,故可制备高纯度的膜层。
可用于粉末、块状材料的蒸发。
用电子束加热也可以使高熔点金属(如W,Mo,Ta等)熔化、蒸发。
8.2.3 蒸发镀膜设备<1>真空室:用于放置镀件,进行镀膜的场所;<2>真空系统:一般由机械泵、扩散泵、管道、阀门等组成;<3>蒸发系统:包括蒸发源,加热蒸发源的电气设备;<4>电气设备:用于测量真空系统,膜厚测量系统,控制台等。
8.2.4 蒸镀用途蒸镀只用于镀制对结合强度要求不高的某些功能膜,例如用作电极的导电膜,光学镜头的增透膜等。
蒸镀用于镀制合金膜时,在保证合金成分这点上,要比溅射困难得多,但在镀制纯金属时,蒸镀可以表现出镀膜速度快的优势。
蒸镀纯金属膜中,90%是铝膜。
铝膜在IC行业、制镜工业、电子器件、食品包装、着色装饰等领域具有广泛的应用。
8.3溅射镀膜溅射镀膜:在真空室中,利用荷能粒子轰击材料表面,使其原子获得足够的能量而溅出进入气相,然后在工件表面沉积的过程。
●在溅射镀膜中,被轰击的材料称为靶。
●由于离子易于在电磁场中加速或偏转,所以荷能粒子一般为离子,这种溅射称为离子溅射。
第8章 气相沉积技术-用

− 化学气相沉积 (Chemical Vapor Deposition)
气相沉积技术可以沉积金属膜、合金膜以及各种化合物、非金属、 半导体、陶瓷、塑料膜等。根据使用要求,目前几乎可以在任 何基体上沉积任何物质的薄膜。 与光刻腐蚀、离子刻蚀、离子注入、离子束混合改性等微细加工 技术一起,成为微电子及信息产业的基础工艺,在促进电子电 路小型化、功能高度集成化方面发挥关键作用。
以 Ni.Cr 二元合金为例,它经常用于制造电阻薄膜和抗蚀层。
蒸镀的合金膜,其组成为 80/20。蒸发温度约 2000K,而铬在 2000K 时的蒸气压强比镍要高 100 倍。如果镀料是一次加热,则因 铬原子消耗较快,而使镀层逐渐贫铬。
− 为了消除这种成分偏差,通常采用如下工艺方法
− 镀料蒸发:蒸气与其液 态或固态间的非平衡过 程 − 蒸气迁移:气体分子的 运动 − 基片表面凝聚:气体分 子与固体表面碰撞、吸 附和形核长大
14
(2)成膜机理
发源 射向基片的途中一般不发生碰撞,即入射原子在迁移过程中无 能量损耗。当入射原子到达基片后就进入了基片表面的力场, 此时入射原子与基片就可能出现几种相互作用
薄膜(涂层、镀层)的制备方法
液相法(电镀和化学镀) 气相沉积 按气相物质的产生方式分类 1.物理气相沉积
在真空条件下,采用各种物理方法将固态的镀料转化为原子、分 子或离子态的气相物质后再沉积于基体表面,从而形成固体薄膜 按沉积薄膜气相物质的生成方式和特征分类
真空蒸镀 (Evaporation)--镀材以热蒸发原子或分子的形式沉积成膜 溅射镀膜 (Sputtering)--镀材以溅射原子或分子的形式沉积成膜 离子镀膜 (Ion)--镀材以离子和高能量的原子或分子的形式沉积成膜
表面技术(第7讲 气相沉积技术(Ⅰ))

南京航空航天大学第七讲 气相沉积技术(Ⅰ)表面技术第七讲 气相沉积技术(Ⅰ)• 物理气相沉积(PVD):真空蒸 镀、溅射镀膜、离子镀等。
• 化学气相沉积(CVD)南京航空航天大学第七讲 气相沉积技术(Ⅰ)表面技术一、真空技术基础•1. 真空:在指定的空间内压力低于101325 Pa的气体状态。
真空度通常用压力表示。
•真空度单位:Torr、Pa、mmHg、bar。
1标准大气压=1bar=760Torr=760mmHg = 101325 Pa •真空划分:低真空(105~102Pa)、中真空 (102~10-1Pa) 、高真空(10-1~10-5Pa) 、超高 真空(<10-5Pa) 。
南京航空航天大学第七讲 气相沉积技术(Ⅰ)表面技术2. 真空成膜技术的特点• 1) 排除了空气的不良影响,可防止金属 氧化、物体腐烂; • 2) 除去或减少气体、杂质污染,提供清 洁条件; • 3) 减少气体分子之间的碰撞次数; • 4) 真空的绝热性强; • 5) 可降低物质的沸点或气化点。
南京航空航天大学第七讲 气相沉积技术(Ⅰ)表面技术3. 真空的应用•宇航环境的模拟,加速器技术,可控热 核反应技术,真空输送,真空过滤,真 空干燥,真空蒸馏,真空制盐,真空浓 缩,真空除臭,真空结晶,冷冻干燥, 真空浸渍,真空调湿,真空渗金属,真 空热处理,真空离子氮化,真空制冷, 真空烧结,真空熔炼,真空镀膜,低温 绝热等。
南京航空航天大学第七讲 气相沉积技术(Ⅰ)表面技术4. 真空获得设备• 机械真空泵:往复真空泵(单级103Pa,双 级10Pa)、水环真空泵(单级103Pa,双级 102Pa)、油封旋转式真空泵(单级10-1Pa , 双级10-2Pa)、罗茨真空泵(10-2Pa)、涡轮分 子泵(10-8Pa); • 蒸气流泵:扩散泵(10-1 ~10-7Pa) 、喷射泵 (104 ~10-1Pa) 、扩散喷射泵(10 ~10-2Pa) ; • 物理化学泵:吸附泵、升华泵、离子泵、 低温泵等。
第五章-气相沉积法学习教案
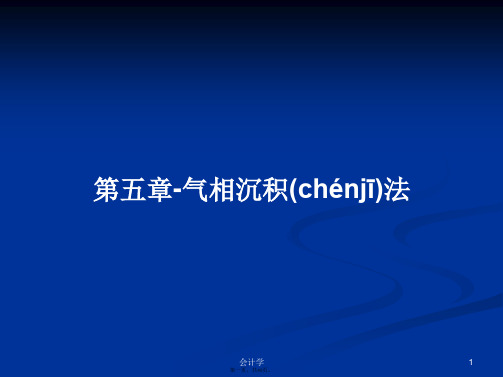
31
第三十一页,共40页。
2.1 等离子化学气相沉积 ( P-CVD ):
辉光放电
形成低温(dīwēn)等离子体
高能量 激活化学气相沉积反应
第31页/共40页
32 第三十二页,共40页。
2.2 等离子体(děnglízǐtǐ)在CVD中的作用:
降低反应温度:将反应物气体分子激活成活性离子 ;
第9页/共40页
第十页,共40页。
3. CVD反应体系(tǐxì)必须具备三个条件 3.1 CVD化学反应方式: 1)反应气体间的反应; 2)气相与基体表面(biǎomiàn)间的反应 3.2 条件 原料:反应物具有较高的蒸气压; 产物:反应副产物易于挥发; 反应类型:反应易于控制
第10页/共40页
AB(g) Q A(s) B(g)
主要问题:
源物质的选择(蒸汽压-温度)
确定分解温度(不同温度下的产物)
第14页/共40页
15 第十五页,共40页。
热分解(fēnjiě)反应类型 (1)氢化物分解(fēSnijHiě4)700-1000 ℃ Si + 2H2
(2)金属(jīnshǔ)有机化合物分解 (M-C键能小于C-C键)
化学气相沉积(CVD)
——Chemical Vapor Deposition
CVD反应范指反应物为气体而生成物之一为固体 的
化学反应。
第8页/共40页
9
第九页,共40页。
2. 化学(huàxué)气相沉积工 艺及设备 气相反应室
CVD装置
加热(jiā rè)系统
气体(qìtǐ)控制系 统
排气系统
3SiH4 +4NH3 7 500CSiN4 +12H2 W(s)+3I2 (g) ~ 134000 0 000CC WI6 (g)
- 1、下载文档前请自行甄别文档内容的完整性,平台不提供额外的编辑、内容补充、找答案等附加服务。
- 2、"仅部分预览"的文档,不可在线预览部分如存在完整性等问题,可反馈申请退款(可完整预览的文档不适用该条件!)。
- 3、如文档侵犯您的权益,请联系客服反馈,我们会尽快为您处理(人工客服工作时间:9:00-18:30)。
授课学时:3学时
真空蒸镀时,蒸发粒子动能为0.1~1.0ev,膜对基体的附着力较弱。
解决措施
●在溅射过程中,通过动量传递,95%的离子能量作为热量而被
损耗,仅有5%的能量传递给二次发射的粒子。
影响溅射率的主要因素
①入射离子
②与靶有关
包括靶原子的原子序数、靶表面原子的结合状态、
材是纯金属、合金或化合物等;
与元素的升华热有关,呈明显周期性;随外层d电子数的增加,溅射率提高。
③与温度有关
一般认为:在某一温度内,溅射率几乎不随温度变化而变化,当温度超过这一范围时,溅射率有迅速增加。
3.2 溅射镀膜的方式
具体的溅射工艺:二极溅射、三(四)极溅射、磁控溅射、射频溅射、离子束溅射
磁控溅射:磁控溅射特点是在阴极靶面上建立一个环状磁靶,
制二次电子的运动。
环形磁场的目的
●延长电子飞向阳极的行程。
其目的是让电子尽可能多产生几次
碰撞电离,从而增加等离子体密度,提高溅射效率。
●抑制由靶产生的高速电子对基片的轰击,避免基片温度升高。
优点
高速:高速是指沉积速率快;磁控溅射的镀膜速率与二极溅射相比提高了一个数量级。
低温和低损伤:基片的温升低、对膜层的损伤小。
8.3.3 溅射镀膜的特点
与真空蒸镀相比,溅射有如下特点:
结合力高;。