高强度中空铝型材成形工艺研究
铝型材行业知识点总结

铝型材行业知识点总结一、铝型材的基本概念1. 铝型材的定义铝型材是以铝合金为主要原料,通过挤压、轧制、拉拔等加工工艺,制成各种截面形状的材料。
其特点是重量轻、强度高、耐腐蚀、易加工等。
2. 铝型材的分类铝型材根据截面形状的不同,可以分为实心型材、中空型材和复合型材等;根据用途的不同,可以分为建筑型材、工业型材、交通运输型材等。
3. 铝型材的特点铝型材具有良好的导热性能、抗氧化性能和可塑性,而且重量轻、易加工、成形性好等,因此在各个领域有着广泛的应用。
二、铝型材的生产工艺1. 铸造铸造是生产铝型材的一种常见工艺,它包括压铸、砂型铸造、永铸等多种方法,通过将铝液浇铸到模具中,然后冷却凝固,最终得到所需要的铝型材。
2. 挤压挤压是生产铝型材的主要工艺,它通过将铝坯料加热至一定温度,然后置于挤压机内,利用模具对其进行加压挤出,制成各种截面形状的铝型材。
3. 轧制轧制是将铝坯料经过加热后,置于轧机中通过多次轧制,使其逐渐变薄,最终制成所需的铝型材。
4. 拉拔拉拔是将铝坯料通过拉拔机进行一定拉伸和挤压,使其变细,得到各种细长型的铝型材。
三、铝型材的应用领域1. 建筑装饰铝型材在建筑装饰方面应用广泛,如门窗框架、幕墙、天花吊顶、室内隔断、楼梯扶手等,其外观美观、质量轻、耐腐蚀等特点,使其成为建筑装饰的主要材料。
2. 电力行业铝型材在电力行业主要用于输电线路的导线杆、变电站结构、电力设备支架等,因其良好的导电性能和抗氧化性能,使其成为电力行业不可或缺的材料。
3. 机械制造铝型材在机械制造领域应用广泛,如汽车零部件、航空航天零部件、轨道交通车辆等,其重量轻、强度高、耐磨损等特点,使其在机械制造领域有着重要的地位。
4. 交通运输铝型材在交通运输领域主要用于汽车、船舶、航空器等交通工具的制造,以及桥梁、隧道、码头等交通设施的建设,其重量轻、抗腐蚀、强度高等特点,使其在交通运输领域有着广泛的应用。
四、铝型材的市场现状和发展趋势1. 市场现状目前,全球铝型材市场规模庞大,需求量稳步增长,尤其在建筑、交通运输、电力等领域有着广阔的市场空间。
铝合金高强度薄板成型工艺研究

铝合金高强度薄板成型工艺研究一、背景介绍铝合金材料由于其轻巧、强度高、耐腐蚀、易于加工等特点,被广泛应用于航空、航天、汽车等领域。
其中,铝合金高强度薄板的成型技术是其应用的重要环节之一。
铝合金高强度薄板(以下简称铝薄板)的成型工艺在现代制造业中起着至关重要的作用。
二、问题及挑战铝薄板的成型工艺面临的挑战主要体现在以下几个方面:1. 铝薄板的冲压性能较差,容易出现撕裂、鼓包等缺陷;2. 铝薄板在成型过程中容易发生回弹现象,导致成型尺寸难以控制;3. 铝薄板的成型质量要求较高,需要保证表面光洁度和尺寸精度。
三、铝薄板成型工艺研究进展1. 冲压成型工艺方面(1)多工位成形技术:通过多次成形减小单次成形变形量,从而减小成形残余应力,提高成形质量。
(2)温度控制技术:适当的加热可以改善铝薄板的塑性,减小冲压过程中的残余应力,同时可以提高表面光洁度。
(3)多模工艺技术:在冲压成形中使用多个模具,以减小成形变形量、减轻残余应力、提高成形精度。
(4)成形前预弯技术:在冲压成形前对铝薄板进行预弯,可以减小撕裂和鼓包的发生概率。
2. 回弹控制技术方面(1)板材弹性重构技术:在冲压成形时,通过钎焊、铆接等方式让板材发生重构,从而控制板材的回弹;(2)离线补偿技术:根据成形模具的状态和板材的性能,通过计算机模拟,预测出成型后板材的形状,进而制定出控制回弹的补偿措施。
3. 成形质量控制技术方面(1)成形工艺参数优化:通过自动控制工艺参数的变化,如冲压力、温度、深度等,自动适应板材性能施加恰当力度,以保证成型质量。
(2)模具表面处理技术:通过涂覆特殊涂料、花纹加工等方式,提高模具表面的光洁度和硬度,从而减小成型质量的不稳定性。
四、未来展望铝薄板的成型工艺目前还面临众多挑战,未来的研究方向包括:1. 发展新的铝合金材料,以改善铝薄板在成型过程中的性能;2. 研发新的成型工艺,以提高成型质量和生产效率;3. 探索智能化铝薄板成型技术,实现生产线的自动化、高效化。
哈工程《城市轨道交通车辆构造》教学资料 课后习题答案 《城市轨道交通车辆构造》课后习题答案(哈工大)
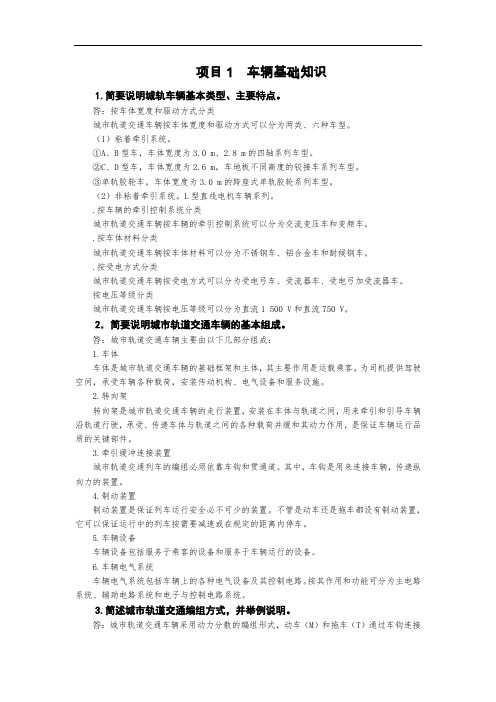
项目1 车辆基础知识1.简要说明城轨车辆基本类型、主要特点。
答:按车体宽度和驱动方式分类城市轨道交通车辆按车体宽度和驱动方式可以分为两类、六种车型。
(1)粘着牵引系统。
①A、B型车,车体宽度为3.0 m、2.8 m的四轴系列车型。
②C、D型车,车体宽度为2.6 m,车地板不同高度的铰接车系列车型。
③单轨胶轮车,车体宽度为3.0 m的跨座式单轨胶轮系列车型。
(2)非粘着牵引系统。
L型直线电机车辆系列。
.按车辆的牵引控制系统分类城市轨道交通车辆按车辆的牵引控制系统可以分为交流变压车和变频车。
.按车体材料分类城市轨道交通车辆按车体材料可以分为不锈钢车、铝合金车和耐候钢车。
.按受电方式分类城市轨道交通车辆按受电方式可以分为受电弓车、受流器车、受电弓加受流器车。
按电压等级分类城市轨道交通车辆按电压等级可以分为直流1 500 V和直流750 V。
2.简要说明城市轨道交通车辆的基本组成。
答:城市轨道交通车辆主要由以下几部分组成:1.车体车体是城市轨道交通车辆的基础框架和主体,其主要作用是运载乘客,为司机提供驾驶空间,承受车辆各种载荷,安装传动机构、电气设备和服务设施。
2.转向架转向架是城市轨道交通车辆的走行装置,安装在车体与轨道之间,用来牵引和引导车辆沿轨道行驶,承受、传递车体与轨道之间的各种载荷并缓和其动力作用,是保证车辆运行品质的关键部件。
3.牵引缓冲连接装置城市轨道交通列车的编组必须依靠车钩和贯通道。
其中,车钩是用来连接车辆,传递纵向力的装置。
4.制动装置制动装置是保证列车运行安全必不可少的装置。
不管是动车还是拖车都设有制动装置,它可以保证运行中的列车按需要减速或在规定的距离内停车。
5.车辆设备车辆设备包括服务于乘客的设备和服务于车辆运行的设备。
6.车辆电气系统车辆电气系统包括车辆上的各种电气设备及其控制电路。
按其作用和功能可分为主电路系统、辅助电路系统和电子与控制电路系统。
3.简述城市轨道交通编组方式,并举例说明。
高强度中空铝型材成形工艺研究

高强度中空铝型材成形工艺研究一、引言介绍中空铝型材的发展背景及其在工程领域的应用价值,指出存在的成形难题及本文研究的目的和意义。
二、相关技术综述对现有的中空铝型材成形工艺进行总结和评价,包括传统的挤压成形、拉伸成形、壳模成形,以及近年来出现的多弯曲工艺、高压水流冲压和粉末沉积成型技术。
三、中空铝型材成形工艺设计介绍基于中空铝型材的特性和应用要求,以及各种成形工艺的优缺点,设计出适合中空铝型材成形的工艺流程,详细论述流程中每一个环节的实现方法。
四、高强度中空铝型材成形实验根据之前设计出的工艺流程,进行成形实验,检验各项参数的合理性和成形效果。
对结果进行数据统计分析,得出关键参数对成形结果的影响规律,并进行实验验证。
五、结论与展望总结本文的研究内容及实验结果,指出其在实际应用中的针对性和可行性。
进一步提出未来中空铝型材成形方面的发展方向和研究重点,为相关产业的发展提供指导意见。
注:以上仅为提纲,具体内容和细节需要根据研究内容具体情况进行拓展。
一、引言随着现代工业技术的不断发展,中空铝型材作为一种轻质、高强度、高刚度的新型材料,已经得到广泛的应用。
在建筑、汽车、电子、航空航天等行业中,中空铝型材产品已成为不可替代的材料之一。
然而,中空铝型材的成形仍然是一个存在着许多技术难题的领域。
传统的成形技术往往无法满足高质量、高效率的需求。
因此,本文旨在研究中空铝型材的高强度成形工艺,为中空铝型材的应用推广和提高提供技术支持。
在本文中,我们将全面调研和综述目前已有的中空铝型材成形技术,并探讨了不同技术的优缺点及其适用范围。
在此基础上,我们设计了一种针对中空铝型材成形的高强度工艺,并进行了成形实验。
最后,我们总结了本文研究的过程和结论,并对中空铝型材成形技术未来的发展方向和研究重点进行了探讨。
二、相关技术综述目前,中空铝型材的成形技术已经得到了广泛的应用,主要包括传统的挤压成形、拉伸成形、壳模成形,以及近年来出现的多弯曲工艺、高压水流冲压和粉末沉积成型技术等。
2024高强度铝合金薄壁型材挤压工艺研究

2024高强度铝合金薄壁型材挤压工艺研究王义斌;王睿;李延军;杨志勇;张健;刘丽瑜【摘要】文章研究采用正挤压方法对2024高强度铝合金薄壁型材进行挤压成型.主要从模具设计、挤压参数、淬火制度、淬火夹具制作及整形等方面进行调试,找出最合理的的挤压生产工艺使产品满足GJB2507A标准要求.【期刊名称】《有色金属加工》【年(卷),期】2018(047)005【总页数】3页(P50-52)【关键词】挤压工艺;模具设计;淬火制度;淬火夹具【作者】王义斌;王睿;李延军;杨志勇;张健;刘丽瑜【作者单位】辽宁忠旺集团有限公司,辽宁辽阳111003;辽宁忠旺集团有限公司,辽宁辽阳111003;辽宁忠旺集团有限公司,辽宁辽阳111003;辽宁忠旺集团有限公司,辽宁辽阳111003;辽宁忠旺集团有限公司,辽宁辽阳111003;辽宁忠旺集团有限公司,辽宁辽阳111003【正文语种】中文【中图分类】TG3792024铝合金又称为高强度硬铝合金,具有强度高、耐热性好[1-2]等优点。
其挤压型材主要应用于飞机机身框架、机翼桁条、翼肋等受力结构件[3]。
此次试验薄壁型材是我公司航空事业部与某飞机设计制造有限公司合作产品,选取壁厚仅为1.0mm的薄壁型材进行挤压成型试验,此型材的成型性和尺寸精度较难控制,现有生产工艺无法实现产品挤压成型。
本文将以此型材为例,对2024高强硬铝合金薄壁型材挤压生产工艺进行研究分析。
1 型材基本信息此2024硬铝合金薄壁型材为直角型材,直角边长为15mm,壁厚为1.0mm。
型材性能要求满足GJB2507A。
其中力学性能标准Rp0.2≥ 290 MPa,Rm≥ 395 MPa,A%≥10 %。
2 型材挤压过程难点(1)合金成分2024属于2xxx硬铝合金,合金中Cu、Mg元素含量较高,而合金化程度高金属流动性差,导致变形抗力过大[4],挤压过程中容易闷车无法挤出。
(2)模具设计原有模具为单孔挤压模具且带有导流坑,单孔模具挤压比达到150,过大的挤压比和带导流坑的设计均会显著提高挤压变形抗力,造成闷车无法挤动的现象。
高强度铝合金新材料及其成型技术的研究与应用

高强度铝合金新材料及其成型技术的研究与应用高强度铝合金新材料及其成型技术的研究与应用引言:高强度铝合金是一种具有重要应用价值的材料,以其优异的力学性能、良好的耐蚀性和良好的可加工性在航空航天、汽车制造、船舶建造等领域得到广泛应用。
然而,高强度铝合金的研究与应用仍然面临一些挑战,主要包括材料的力学性能、成型技术和加工工艺等方面。
一、高强度铝合金的研究:1.1 物理性能:高强度铝合金具有较低的密度和高的强度,这使得它成为一种理想的结构材料。
根据需求,高强度铝合金可以具备强度超过钢铁的特点,使其在航空航天和汽车工业中具有广泛的应用前景。
1.2 耐蚀性:高强度铝合金具有良好的耐蚀性,这使其能够在恶劣的环境条件下使用,例如海洋环境和高温高湿度环境。
1.3 可加工性:高强度铝合金具有良好的可加工性,可通过挤压、锻造、压铸等方法制备出具有复杂形状的零部件。
二、高强度铝合金的成型技术研究:2.1 挤压:挤压是高强度铝合金成型的一种重要方法,通过将铝合金坯料放入挤压机中,通过加热和压力使其通过模具形成所需的形状。
挤压成型具有高生产效率和较高的成型精度。
2.2 锻造:锻造是一种通过将高强度铝合金坯料放入锻造机中,通过加热和压力使其在模具中形成所需形状的成型方法。
锻造成型具有较高的成型精度和较好的力学性能。
2.3 压铸:压铸是一种通过将高强度铝合金熔融后注入模具中,在模具中冷却并形成所需的形状的成型方法。
压铸成型具有高生产效率和较好的成型精度,适用于大批量生产。
2.4 成型模具设计与制造:成型模具是高强度铝合金成型过程中的关键装备,其设计与制造对成型质量和成型效率具有重要影响。
成型模具的设计应考虑到铝合金的物理性能、成型工艺和产品要求等因素,以确保成型过程的稳定性和一致性。
三、高强度铝合金的应用:3.1 航空航天领域:高强度铝合金具有低密度和高强度的特点,因此,它在航空航天器制造中得到广泛应用。
例如,它可以用于制造飞机的机身、机翼和起落架等部件,以提高飞机的整体性能。
新型铝型材制造工艺介绍

新型铝型材制造工艺介绍铝型材是一种应用广泛的材料,它具有重量轻、强度高、导热性好、抗腐蚀性强等优点,在建筑、交通运输、航空航天等领域得到广泛应用。
传统的铝型材制造工艺主要包括挤压、拉伸、轧制等方法,但随着科技的进步,新型铝型材制造工艺相继出现,大大提高了生产效率和产品质量。
下面将介绍几种新型铝型材制造工艺。
一、精密铸造法:精密铸造法是一种将铝液注入模具中,通过冷却凝固成型的工艺。
这种工艺具有制作复杂形状铝型材的优点,可以制作出各种高精密度、高强度的铝型材。
采用该工艺制造的铝型材具有表面平整度高、尺寸精度高、内部组织均匀等特点,广泛用于汽车零部件、光学仪器等领域。
二、注射挤压法:注射挤压法是一种将铝液直接注入模具中,然后通过挤压使其成型的工艺。
与传统挤压相比,注射挤压法具有成型速度快、能耗低、生产效率高等优点。
此外,注射挤压法还可以制造更复杂的产品形状,提高了产品的设计自由度。
该工艺适用于制造电子设备外壳、电池外壳等被广泛应用的产品。
三、快速凝固浇铸法:快速凝固浇铸法是一种通过快速冷却使铝液迅速凝固成型的工艺。
相比传统的凝固浇铸法,快速凝固浇铸法具有凝固时间短、铝液流动性好等优点。
由于凝固速度快,使得铝型材内部的结晶细化,提高了强度和韧性。
该工艺适用于制造高强度、高耐磨性的铝合金型材,广泛应用于航空航天、汽车制造等领域。
四、高能量激光焊接法:高能量激光焊接法是一种利用激光束进行焊接的工艺。
与传统的焊接方法相比,高能量激光焊接法具有热影响区小、焊接速度快的优点。
采用该工艺焊接的铝型材接头强度高、气密性好,广泛应用于航空航天、汽车制造等领域。
以上介绍了几种新型的铝型材制造工艺,这些工艺的出现大大提高了铝型材的制造效率和产品质量。
随着科技的不断发展,相信将会有更多新型铝型材制造工艺出现,满足不断增长的市场需求。
高强度铝合金材料的制备与性能优化

高强度铝合金材料的制备与性能优化铝合金是一种被广泛使用的轻质材料,特别适用于制造航空、航天器等高科技产品。
与钢材相比,铝合金具有比强度高、重量轻的优势,但传统的铝合金材料强度有限,难以满足某些高强度、高韧性以及抗腐蚀等方面的要求。
因此,深入探究高强度铝合金材料的制备、性能和机理对于拓展其应用领域具有重要意义。
一、铝合金的制备高强度铝合金的制备需要从原材料制备、晶粒尺寸控制、合金元素设计等方面进行优化,实现良好的生产工艺和微观组织结构。
1、原材料制备铝合金制备的关键在于铝的纯度和生产工艺。
为了保证合金成分的准确性和均匀性,通常先向工业纯铝中加入需要的元素(如铜、锌、镁等),再将混合物加热至熔点进行铸造和挤压。
同时,还需要规范的技术和严格的质量控制,确保铝合金的物理、化学和力学性能符合要求。
2、晶粒尺寸控制晶粒尺寸对铝合金的性能有很大的影响。
小晶粒可以提高合金的塑性和强度,提高抗拉强度和冲击能力。
因此,制备高强度铝合金需要尽可能缩小晶粒尺寸。
现阶段,通过增加稀土元素等成分来控制晶粒尺寸,制备出晶粒尺寸小于5μm的铝合金。
3、合金元素设计对于不同的应用要求,可以通过调整合金元素的组合、含量和处理方式来改变铝合金的性能。
例如,铜可以增加合金的强度和硬度,锌可以增加抗腐蚀性能,镁可以改善力学性能。
而通过加热、冷却、拉伸、退火等处理方式,可以调整晶格结构,提高强度与韧性的平衡性能。
二、铝合金的性能优化铝合金的优化可以从强度、韧性和耐腐蚀性几个方面进行考虑。
1、强度优化铝合金的强度是衡量其综合性能的重要参数,可以通过合金元素控制、热处理、变形和加固技术等方式来提高。
其中,热处理是目前最广泛应用的提高铝合金强度的方法,包括时效和固溶处理两种方式。
2、韧性优化韧性是材料在受外力破坏时发生塑性变形的能力,铝合金在强度提高的同时,必须保证韧性的充分发挥。
实现铝合金材料力学性能和力学性能之间的均衡,对韧性的增强也起到了很好的作用。
一种高强度铝合金型材加工系统及加工方法

一种高强度铝合金型材加工系统及加工方法随着工业化进程的发展,铝合金材料在各个领域得到广泛应用。
而高强度铝合金型材作为一种重要的材料,其加工过程和加工方法也变得越来越重要。
本文将介绍一种高强度铝合金型材加工系统及加工方法,以满足市场对高强度铝合金型材的需求。
一、高强度铝合金型材加工系统的组成高强度铝合金型材加工系统主要由以下几个部分组成:1. 设备部分:包括铝合金型材加工机床、自动送料系统、切削工具、冷却液系统等。
其中,铝合金型材加工机床是核心设备,可以根据型材的形状和尺寸进行精确加工。
2. 控制系统:包括数控系统、传感器和执行机构等。
数控系统可以实现对加工过程的精确控制,传感器可以实时监测加工过程中的各项参数,执行机构可以根据指令进行相应的动作。
3. 数据管理系统:包括加工参数数据库、工艺规程库和质量监控系统等。
加工参数数据库存储了各种型材的加工参数,工艺规程库存储了各种型材的加工工艺,质量监控系统可以实时监测加工质量并进行反馈调整。
二、高强度铝合金型材加工方法高强度铝合金型材加工方法主要包括以下几个步骤:1. 材料准备:选择符合要求的高强度铝合金材料,并进行切割成适当尺寸的型材。
2. 设备设置:根据型材的形状和尺寸,调整铝合金型材加工机床和自动送料系统的参数,确保加工精度和效率。
3. 加工工艺选择:根据型材的要求和工艺规程库中的信息,选择适当的加工工艺。
包括切削速度、进给速度、切削深度等参数的选择。
4. 加工操作:将铝合金型材固定在加工机床上,通过数控系统设置好加工参数,启动自动加工过程。
在加工过程中,切削工具根据设定的加工路径进行切削操作,冷却液系统则起到冷却切削区域和清除切削屑的作用。
5. 检验和调整:在加工完成后,对加工后的型材进行检验,检查其尺寸精度和表面质量等指标。
如果不满足要求,可以通过调整加工参数或更换切削工具等方式进行调整。
通过以上步骤,可以实现对高强度铝合金型材的精确加工。
高强度铝合金型材加工系统及加工方法的应用,可以提高型材的加工精度和效率,减少人工操作的难度,提高生产效率和产品质量。
- 1、下载文档前请自行甄别文档内容的完整性,平台不提供额外的编辑、内容补充、找答案等附加服务。
- 2、"仅部分预览"的文档,不可在线预览部分如存在完整性等问题,可反馈申请退款(可完整预览的文档不适用该条件!)。
- 3、如文档侵犯您的权益,请联系客服反馈,我们会尽快为您处理(人工客服工作时间:9:00-18:30)。
对 5组 试 验 数 据 进 行 处 理 分 析 , 按 照 下 式 得 到
 ̄ o = L n ( 1 + r / )
= e
变 形 等 特 点 所 致 , 在 弯 曲 成 形 过 程 中表 面 易 产 生 波
滚压 工艺对铜瓦 尸 值 的 影 响
秦 剑 , 郭 世 彦 。柯 尊 芒
( 徐 州 锻 压 机 床 厂 有 限公 司 , 江苏 徐州 2 2 1 1 1 6)
摘要 : 随着超 声滚 压 加工在 铜 瓦机加 工 艺上 的应用 和推 广 , 与 传 统 的机 加 工 艺 相 比 , 铜 瓦 的表 面 粗 糙 度 显 著 降低 、 表 面显微硬 度 却得到 提高 , 扩 大 了铜 瓦 PV值 的许 用 范 围。本 文 通 过 运 用 粘 着 摩 擦 理 论 , 对 此 工 艺
空气 动力 学 、 噪声 、 轻 量化 等 。为保 证 高速列 车 的车 体 强 度 并 满 足 轻 量 化 的要 求 ,在 铝 合 金 车 体 结 构 的
设 计 制 造 中广 泛 使 用 中空 型 材 。 随 着 动 车 组 车 型 的
日益 增 多 , 不 同截 面 、 不 同 形 状 中空 铝 型 材 的 高 质 量
关键 词 : 弯 曲成 形 ; 管材 ; 中空型材 ; 成 形性 能 ; 高 速 动 车 组
中 图5 ) - - 类号: T G3 8 6 . 4 3
材料 参数 性能 测试 为 了 获 得 A6 N0 1 S — T 5的 力 学 性 能 参 数 以及 真 实应 力 一 应 变 曲线 , 按 照 GB T 2 2 8 — 2 0 0 2国 家 标 准 进 行 型材 的 拉伸 试 验 。考 虑 到材 料 的各 向异 性 , 分别 沿挤压方向( 0 。 ) 、 垂 直 于挤 压 方 向( 9 0 。 ) 以及 4 5 。 方 向加 工 标 准 试 样 , 考虑材料批次不均匀性 , 选 取 不 同 批 次 型 材 的 5根 铝 合 金 型 材 ,加 工 得 到 5套 试
应变 图 1 试 验 型 材示 意 图
2
成 形 过 程 仿 真 分 析
收 稿 日期 : 2 0 1 3 一 O 1 — 2 7
作者简介 : 王汝彪( 1 9 8 2 一 ) , 男, 工程师 , 从事高速 动车组车体 工艺技
术 研 究
文章 编号 : 1 6 7 2 — 0 1 21 ( 2 0 1 3 ) 0 2 — 0 0 9 6 — 0 4
型材进 行 成形试 验 、 仿 真 分 析 。 研 究 型 材 在 不 同 弯 曲半 径 下 的 塑 性 变 形 规 律 , 成 形 缺 陷 的 产 生 原 因及 抑 制 方
法, 探 索 降低 缺 陷 的 成 形 参 数 及 工 艺 方 法 , 为 动车组 用铝 型材零 件 的设 计和 制造提 供依 据 。
纹或 塌陷 , 内部 加 强 筋 发 生 变 形 甚 至 断 裂 等 。 本 文针 对 铝 合 金 中 空 型 材 的 弯 曲 成 形 开 展 研 究 ,选 取 具 有 典型 断面 的 中空型 材进行 研究 , 如图 1 所示 , 材 料为
所 用材 料 的真实 应力 一 应 变 曲 线 如 图 2所 示 , 并 得 到 材 料 的屈服 极 限 2 8 4 MP a , 抗拉 强度 3 2 1 . 8 MP a 。
A6 N0 1 S — T 5 。 通 过 有 限元 仿 真 及 模 具 压 弯 成 形 两 种
手 段 ,研 究 型 材 在 不 同弯 曲 半 径 下 的 塑 性 变 形 规 律
及 成形 性 能 。
O. O O 0 . 0 1 O . O 2 0 . 0 3 0 . 0 4 0 . 0 5
样 。
随 着 我 国 高 速 列 车 的 发 展 ,新 一 代 动 车 组 的 时 速 已达到 3 8 0 k m/ h 。该 速 度 已经 超 过 飞 机 起 飞 速 度 , 从 而 带 来 了与 传 统 列 车 完 全 不 同 的 系 列 问题 , 包 括
W/ R
5 O 5 O ∞ 5
2 F _ 汝 彪 。 刘 纯 国
( 1 . 南车青 岛四方机 车车 辆股 份有 限公 司 , 山东 青 岛 2 6 6 1 1 l ;
2 . 吉林 大学 , 吉林 长春 1 3 0 0 1 2 )
摘要 : 为 了掌 握 高 速 动 车 组 用 高 强度 铝 合 金 中 空 型 材 的 成 形 性 能 及 变 形 规 律 , 本 文 选 取 典 型 断 面 的 中 空
对5组试验数据进行处理分析按照下式得到由于铝合金型材的中空结构材料特性以及难oln1r变形等特点所致在弯曲成形过程中表面易产生波e纹或塌陷内部加强筋发生变形甚至断裂等
文章编 号 : 1 6 7 2 — 0 1 2 1 ( 2 01 3 ) 0 2 — 0 0 9 3 — 0 3
高 强 度 中 空 铝 型 材 成 形 工 艺 研 究
引起 的 PV值 变 化 情 况 进 行 了分 析 。 关 键词 : 滚压 加工 ; 铜瓦; PV值 ; 粘 着 摩 擦 理 论
中图分 类号 : T G3 1 5 . 5 文 献标识 码 : A
高速 重载 滑动轴 承是 高速压 力机 的核 心研究 课 题之 一 , 而 滑 动 轴 承 又 以采 用 铜 瓦 的形 式 居 多 。 随着 超 声 滚 压 加 工 在 铜 瓦 机 加 工 艺 上 的 应 用 和
的 P值 ( 压强 ) 、 V值 ( 速度 ) 、 PV乘 积 值 ( 功率 ) 三 个 参 数确定 。其 中 , P值 的 许 用 值 选 用 , 主 要 依 据 铜 瓦 的磨损 率 测算 ; V值 和 PV乘 积 值 的 许 用 值 选 用 , 主
要 依据铜 瓦 的放热 量计算 。
推广, 与传统 的机加 工艺 相 比 , 铜瓦 的表 面粗糙 度显 著 降低 、 表 面显 微 硬度 却得 到提 高 , 扩 大 了铜 瓦 P V