GUI Tool User Manual for TW8823
DiCal-ToM Swissphone-POCSAG 桌面接收器用户手册说明书
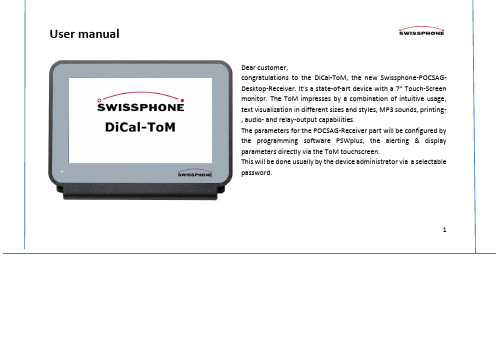
DirectoryWhat’s in the box (3)Start-up information (4)Operating-Menu (6)Reception of an alert (7)Alert-memory management (8)Visualization of text (9)Visualization of older messages (10)Deleting of Messages (11)Settings (12)Tasks for Administrators .................................................... 13Time and date setup .. (14)Configuration of basic settings (14)Relay switching times (16)RIC and sound combination, volume adjustment (17)Adding & deleting of soundfiles (18)Formatting of text, adjustment of number of prints (19)Printing of messages (21)Programming (22)Software-Update (23)Technical data & accessories: (24)Further information (25)23What’s in the box∙ DiCal-ToM ∙ Rod antenna∙ AC adaptor, 12 Volt/1 A∙USB-printer cable type A to type B(to be used reversely as programming cable) ∙ User manualStart-upConnect antenna eventually printer and AC-adaptor cable to ToM. The antenna hast to be put in vertical position. ToM starts automatically after plugging in the AC-adaptor to a power outlet, visualized by a green power-on LED at the front. In areas with low field strength the antenna can be installed remotely via an optional 50 Ohm RF-cable (e.g. outdor antenna).3,5mm jack socket for audio-line-outSpeaker vents BNC-antenna-connectorAntenneUSB-B for Prog.-cableconnector für relay-outputConnector for AC-adaptor USB-A connector forprinter cable4Start-up informationDuring the start, process the Swissphone-Logo appears on the screen, after that the start photo on the left will be shown for some seconds, followed by the DiCal-ToM logo. In parallel the start- sound will be played.While the start-sound cannot be interrupted, it can be changed by MP3-files and volume via the menu “RIC & Sound combination” (page 17).5After the successful start-, (boot-) process the screen shows …DiCal -ToM ready for use“.The sound playback can be stopped by touching the screen.ToM is now prepared to receive POCSAG-messages, depending on the proper programming of the POCSAG-receiver device (page 21).If you are using a low power POCSAG-test-trans-mitter it can be necessary to hold it close to the antenna in some cases.According to the text settings the messages will be visualized in 3 different font sizes (1,2,3) or dynami-cally in full-screen mode.After the timeout, the screen-saver shows the actual time at different positions on the screen. The screen-saver can be set in the configurationmenu.6Operating-MenuAfter a click on the touch-screen the “me nu bar” appears at the right part of the screen.Actual timeScroll up for the recent message in the message- memoryScroll down for the oldest message in the message-memoryProtect and unprotect selected messageDelete messagePrint selected message; printing time for first page can be up to 40s depending on printer type.Go to menu SettingsExplanations to the messages see page 87Reception of an alertThe reception of a new message will be audible by playing the sound file attached to the specific RIC. In parallel the message will flash in red colour. The playback of the soundfile can be stopped by touching the screen and the message will be marked as ‘read’.The message flashes still in red colour, while it is not confirmed (Unread). In the flash –mode the text-colour can be shown inblack, blue, dark-blue, green, dark-green, purple and yellow, depending on the settings. The sound-file, flash-time and text-colour can be set RIC-dependant and individually in the “Format Text” menu.8Alert-memory managementThe Alert-timer shows the time elapsed from the recent alert(from 00 min. und 00 sec. to 11 h und 59 min. max).Number of unread messages or alertsThe unread messages will be displayed in red colour, the last message will be visualized in the colour specified. All read messages exept the last one will be displayed in grey colour.0/ number of protected messages, 16 max. When a protected message will be selected, the background of the storage button turns to green colour.1/ number of all messages stored, which is actually displayed Max. number of messages in memory is 17.9Visualization of textIn the left window the text is shown in full-screen mode, the right window shows the menu bar also, both in maximum character size. The menu bar will be visible by a touch-click.arrows indicating a message to be scrolledMessages will be printed in maximum character size always. Multiple copies of a message can be configured.10Visualization of older messagesBar graph for field strenght of the last message. One bar: small field strength, 3 bars large field strength.When the screen-saver is active, the Logo apears again.While the recent message always will be displayed in red colour and after confirmation in the selected colour, older messages will always be shown in grey colour.After the timeout the screen-saver shows the actual time at different positions on the screen. Thescreen-saver time can be set in the configuration menu.11Deleting of Messages by clicking on the - ButtonIn this menu the current, all unread, all unprotected or all messages can be deleted, independently if they are protected, read or unread. Be careful !Delete current messageDelete all unread messagesDelete all unprotected messagesDelete all messagesCancel process12SettingsEnter the menu …Settings“ by touching the– ButtonFirst setup & Change passwordType in the password …0000“ (state of despatch) and enter the “S ettings ” menu e to perform your configurations.By pressing the buttons …Configuration“ → …Change admin password“, → Yes “ → …OK“ a new password can be created.Important:Please absolutely note down the new password ! The device cannot be configured anymore without a valid password and has to be sent to the Swissphone service eventually.The user can perform a Restart by pressing the …Restart“ button13Tasks for AdministratorsAfter entering a valid password and pressing …Enter“ the following configurations can be performed:Date/Time adjustmentSetup of the basic configurationAdjust relay switching (closing) timeCombine RIC und sound, adjust volumeFormat text, enter number of print copiesRestart14Time and date setupThe ToM has a built in real-time clock. To change date and time there two options:ManuallyType in the actual values and press …Ok “Over the airBy using POCSAG on-air commands (OAP) amanual setup of date and time can be resign15Configuration of basic settingsSelect the parameters in the pull-down-menus and press …Ok“Text sizesDynamically: depending on text in full-screen mode 1: small font : 9 x 28 (252) characters 2: midsize font: 6 x 18 (108) characters 3: large font: 5 x 16 ( 80) charactersUpdateThe software of the ToM can be updated via an USB-Stick containing the new software file : …Patch.zip“. More details see page 23.Change Admin Password :The administrator can set a new password with 4 …30 characters16Relay switching timesSelect RIC first in the pull-down menu.Then type in the relay switching (closing) time in seconds and minutes and press “Ok”. When an alert will be received, the relay closes (short-circuit between the two pins of the green connector) for the time specified.The confirmation of an alert doesn’t affect the closing time of the relay, only If the time is set to ∞ .∞ = infinite switching (closing) time. When confirming the alert by a touch-click, the relaywill open again.17RIC and sound combination, volume adjustmentAt …Start “ a start-up sound can be allocated in the pull-down menu.At …Default “ a sound can be allocated to a RIC or RIC-range, which don’t need an individual sound.Select RIC/RIC-ranges with sub-addresses needing an individual sound. Then allocate the sound in the right pull-down menu.Adjust Repetition and Volume with “+” and “–“ buttons. = infiniteBy pressing the selected sound can beplayed.By pressing soundfiles can be added andremoved.18Adding & deleting of soundfilesPut an USB-Stick containing MP3-soundfiles (in main directory!) into the “USB ” -connectorWhen pressing the button in the …Sound Assignment“ menu, the left window opens:The highlighted files in the upper list will be copied and stored into the ToM memory, the highlighted files in the lower list will be deleted when pressing “Ok”.Maximum memory size for soundfiles in total:40 MB19Formatting of text, adjustment of print-copiesThe text format can be configured individually for each RIC or RIC-range.Select RIC or RIC-rangeThe Flashing duration of a message can be set in seconds or to inifinite.Select one of seven text colours.Configure the number of print copies depending of RIC or RIC-range.Automatic correction of an incomplete received message if it will be received twice..20Printer ManagementSelect the desired printer from the list of printers available.Check whether the right device is selected.If you wish to change your selection, please select the desired printer from the pull-down menu and click “Ok”.Currently available printer drivers:- Samsung Xpress M2020, 2022, 2025 und 2026 - HP Deskjet 2540 All-in-One series- HP Officejet Pro 8620 e-All-in-One Printer series Additional print drivers upon request. E-Mail:**********************21Printing of messagesAn alert message can be printed manually with the -button or automatically with a defined number of copies asdescribed before. The printout of the first page lasts between 20-40 seconds, depending on the printer model. It is printed always in maximum character size.The following picture (left) displays an economic black & white laser printer:Samsung Xpress M2020, 2022, 2025 und 2026. Important:The listed Samsung printers switch-off after 1 hour by default when no print-job exists. For permanent operation, this can be configured with a separate PC and a software for printer configuration.The instruction for that, as well as more printer drivers in the future, can be downloaded from the ToM-user group at https://.USB-KabelProgrammingThe POCSAG-Receiver module in DiCal-ToM has to be programmed essentially as a Swissphone pager with the programming software PSWplus (Standard).Please be aware of the following specialities in PSWplus:USB-cable- Message output has to be active at each RIC (hook atcolumn M)- Dical-ToM supports 1 profile only, therefore profile 1 hato be active at each RIC.- The switching pattern within PSWplus must not be selected !- By using several RIC-ranges, be careful not to double-select a RIC; even an overlapping must be avoided. Every RIC has to be usedonce only. If necessary a RIC-range has to be separated in two parts.Decryption with IDEABy using encryption in a POCSAG network the IDEA-keys must be programmed in ToM with the PSWplus software, as in a pager.22- When a single RIC has to be programmed, the same RIC must be specified in the columns …RIC“ and …to RIC“.- There is no need to programm an EA Delimiter-RIC.- DiCal-ToM interpretes no Tone-only addresses; therefore there are no fix texts in DiCal-ToM.Advice:After programmierung the POCSAG-receiver part with PSWplus in ToM, the programming cable must be detached and the device hast to be restarted by unplugging and reconnecting the DC-connector.Instructions for programming can be found also in the closed user-group for ToM-users at www.swissphone.de/Login/Login Germany.Software-UpdateCopy the new …Patch.zip“ -file from the closed user group of the Swissphone homepage (see above) to a USB-stick into the main directory. Go to menu “Settings” and enter the password. Then press “Configuration” and put the USB-stick into the “USB” –connector. Press “Start” button right next to the “Update” command. After rebooting the device the USB-stick can be removed.2324Technical data & accessories:Accessories: - rod antenna for 2m Band, 165-174 MHz - AC-adapter 100 – 240V AC / 12V DC, 1000 mAInterfaces:- USB A – connector for printer- USB B – connector for programming - Audio-line-output (3.5mm) for audio - Relay – output (plug-in terminal 3.5mm) - Antenna-connector (BNC)- 12V DC – connector for AC-adaptor (5.5 / 2.5mm)Data:- Temperature:0°C – 40°C (working range)- Voltage: 12V DC- Current consumption: appr. 500 mA- Measures: appr. 197 x 127 x 126 mm - Weight: appr. 680g - Conformity: RoHS, CE, ULFurther informationSoftware-Updates etc. for this device will be available in the closed user group for ToM-user atwww.swissphone.de/Login/Login Germany. An activation to that group you can get upon request under **********************Safety adviceThis product must not be used in explosion hazardous areas.The product must not be opened (a.o. for warranty reason).DisclaimerSwissphone Telecommunications GmbH grants no liability or warranty in association with the content of this document.DiCal-ToM and this manual are subject to changes.The device meets the requirements of the european guideline R&TTE 99/05/EG («Radio Equipment and Telecommunications Terminal Equipment»).*****************************************************************.version: 01b/2016 © Swissphone Telecommunications GmbH25。
NuMicro N9H30系列开发板用户手册说明书

NuMicro®FamilyArm® ARM926EJ-S BasedNuMaker-HMI-N9H30User ManualEvaluation Board for NuMicro® N9H30 SeriesNUMAKER-HMI-N9H30 USER MANUALThe information described in this document is the exclusive intellectual property ofNuvoton Technology Corporation and shall not be reproduced without permission from Nuvoton.Nuvoton is providing this document only for reference purposes of NuMicro microcontroller andmicroprocessor based system design. Nuvoton assumes no responsibility for errors or omissions.All data and specifications are subject to change without notice.For additional information or questions, please contact: Nuvoton Technology Corporation.Table of Contents1OVERVIEW (5)1.1Features (7)1.1.1NuMaker-N9H30 Main Board Features (7)1.1.2NuDesign-TFT-LCD7 Extension Board Features (7)1.2Supporting Resources (8)2NUMAKER-HMI-N9H30 HARDWARE CONFIGURATION (9)2.1NuMaker-N9H30 Board - Front View (9)2.2NuMaker-N9H30 Board - Rear View (14)2.3NuDesign-TFT-LCD7 - Front View (20)2.4NuDesign-TFT-LCD7 - Rear View (21)2.5NuMaker-N9H30 and NuDesign-TFT-LCD7 PCB Placement (22)3NUMAKER-N9H30 AND NUDESIGN-TFT-LCD7 SCHEMATICS (24)3.1NuMaker-N9H30 - GPIO List Circuit (24)3.2NuMaker-N9H30 - System Block Circuit (25)3.3NuMaker-N9H30 - Power Circuit (26)3.4NuMaker-N9H30 - N9H30F61IEC Circuit (27)3.5NuMaker-N9H30 - Setting, ICE, RS-232_0, Key Circuit (28)NUMAKER-HMI-N9H30 USER MANUAL3.6NuMaker-N9H30 - Memory Circuit (29)3.7NuMaker-N9H30 - I2S, I2C_0, RS-485_6 Circuit (30)3.8NuMaker-N9H30 - RS-232_2 Circuit (31)3.9NuMaker-N9H30 - LCD Circuit (32)3.10NuMaker-N9H30 - CMOS Sensor, I2C_1, CAN_0 Circuit (33)3.11NuMaker-N9H30 - RMII_0_PF Circuit (34)3.12NuMaker-N9H30 - RMII_1_PE Circuit (35)3.13NuMaker-N9H30 - USB Circuit (36)3.14NuDesign-TFT-LCD7 - TFT-LCD7 Circuit (37)4REVISION HISTORY (38)List of FiguresFigure 1-1 Front View of NuMaker-HMI-N9H30 Evaluation Board (5)Figure 1-2 Rear View of NuMaker-HMI-N9H30 Evaluation Board (6)Figure 2-1 Front View of NuMaker-N9H30 Board (9)Figure 2-2 Rear View of NuMaker-N9H30 Board (14)Figure 2-3 Front View of NuDesign-TFT-LCD7 Board (20)Figure 2-4 Rear View of NuDesign-TFT-LCD7 Board (21)Figure 2-5 Front View of NuMaker-N9H30 PCB Placement (22)Figure 2-6 Rear View of NuMaker-N9H30 PCB Placement (22)Figure 2-7 Front View of NuDesign-TFT-LCD7 PCB Placement (23)Figure 2-8 Rear View of NuDesign-TFT-LCD7 PCB Placement (23)Figure 3-1 GPIO List Circuit (24)Figure 3-2 System Block Circuit (25)Figure 3-3 Power Circuit (26)Figure 3-4 N9H30F61IEC Circuit (27)Figure 3-5 Setting, ICE, RS-232_0, Key Circuit (28)Figure 3-6 Memory Circuit (29)Figure 3-7 I2S, I2C_0, RS-486_6 Circuit (30)Figure 3-8 RS-232_2 Circuit (31)Figure 3-9 LCD Circuit (32)NUMAKER-HMI-N9H30 USER MANUAL Figure 3-10 CMOS Sensor, I2C_1, CAN_0 Circuit (33)Figure 3-11 RMII_0_PF Circuit (34)Figure 3-12 RMII_1_PE Circuit (35)Figure 3-13 USB Circuit (36)Figure 3-14 TFT-LCD7 Circuit (37)List of TablesTable 2-1 LCD Panel Combination Connector (CON8) Pin Function (11)Table 2-2 Three Sets of Indication LED Functions (12)Table 2-3 Six Sets of User SW, Key Matrix Functions (12)Table 2-4 CMOS Sensor Connector (CON10) Function (13)Table 2-5 JTAG ICE Interface (J2) Function (14)Table 2-6 Expand Port (CON7) Function (16)Table 2-7 UART0 (J3) Function (16)Table 2-8 UART2 (J6) Function (16)Table 2-9 RS-485_6 (SW6~8) Function (17)Table 2-10 Power on Setting (SW4) Function (17)Table 2-11 Power on Setting (S2) Function (17)Table 2-12 Power on Setting (S3) Function (17)Table 2-13 Power on Setting (S4) Function (17)Table 2-14 Power on Setting (S5) Function (17)Table 2-15 Power on Setting (S7/S6) Function (18)Table 2-16 Power on Setting (S9/S8) Function (18)Table 2-17 CMOS Sensor Connector (CON9) Function (19)Table 2-18 CAN_0 (SW9~10) Function (19)NUMAKER-HMI-N9H30 USER MANUAL1 OVERVIEWThe NuMaker-HMI-N9H30 is an evaluation board for GUI application development. The NuMaker-HMI-N9H30 consists of two parts: a NuMaker-N9H30 main board and a NuDesign-TFT-LCD7 extensionboard. The NuMaker-HMI-N9H30 is designed for project evaluation, prototype development andvalidation with HMI (Human Machine Interface) function.The NuMaker-HMI-N9H30 integrates touchscreen display, voice input/output, rich serial port serviceand I/O interface, providing multiple external storage methods.The NuDesign-TFT-LCD7 can be plugged into the main board via the DIN_32x2 extension connector.The NuDesign-TFT-LCD7 includes one 7” LCD which the resolution is 800x480 with RGB-24bits andembedded the 4-wires resistive type touch panel.Figure 1-1 Front View of NuMaker-HMI-N9H30 Evaluation BoardNUMAKER-HMI-N9H30 USER MANUAL Figure 1-2 Rear View of NuMaker-HMI-N9H30 Evaluation Board1.1 Features1.1.1 NuMaker-N9H30 Main Board Features●N9H30F61IEC chip: LQFP216 pin MCP package with DDR (64 MB)●SPI Flash using W25Q256JVEQ (32 MB) booting with quad mode or storage memory●NAND Flash using W29N01HVSINA (128 MB) booting or storage memory●One Micro-SD/TF card slot served either as a SD memory card for data storage or SDIO(Wi-Fi) device●Two sets of COM ports:–One DB9 RS-232 port with UART_0 used 75C3232E transceiver chip can be servedfor function debug and system development.–One DB9 RS-232 port with UART_2 used 75C3232E transceiver chip for userapplication●22 GPIO expansion ports, including seven sets of UART functions●JTAG interface provided for software development●Microphone input and Earphone/Speaker output with 24-bit stereo audio codec(NAU88C22) for I2S interfaces●Six sets of user-configurable push button keys●Three sets of LEDs for status indication●Provides SN65HVD230 transceiver chip for CAN bus communication●Provides MAX3485 transceiver chip for RS-485 device connection●One buzzer device for program applicationNUMAKER-HMI-N9H30 USER MANUAL●Two sets of RJ45 ports with Ethernet 10/100 Mbps MAC used IP101GR PHY chip●USB_0 that can be used as Device/HOST and USB_1 that can be used as HOSTsupports pen drives, keyboards, mouse and printers●Provides over-voltage and over current protection used APL3211A chip●Retain RTC battery socket for CR2032 type and ADC0 detect battery voltage●System power could be supplied by DC-5V adaptor or USB VBUS1.1.2 NuDesign-TFT-LCD7 Extension Board Features●7” resolution 800x480 4-wire resistive touch panel for 24-bits RGB888 interface●DIN_32x2 extension connector1.2 Supporting ResourcesFor sample codes and introduction about NuMaker-N9H30, please refer to N9H30 BSP:https:///products/gui-solution/gui-platform/numaker-hmi-n9h30/?group=Software&tab=2Visit NuForum for further discussion about the NuMaker-HMI-N9H30:/viewforum.php?f=31 NUMAKER-HMI-N9H30 USER MANUALNUMAKER-HMI-N9H30 USER MANUAL2 NUMAKER-HMI-N9H30 HARDWARE CONFIGURATION2.1 NuMaker-N9H30 Board - Front View Combination Connector (CON8)6 set User SWs (K1~6)3set Indication LEDs (LED1~3)Power Supply Switch (SW_POWER1)Audio Codec(U10)Microphone(M1)NAND Flash(U9)RS-232 Transceiver(U6, U12)RS-485 Transceiver(U11)CAN Transceiver (U13)Figure 2-1 Front View of NuMaker-N9H30 BoardFigure 2-1 shows the main components and connectors from the front side of NuMaker-N9H30 board. The following lists components and connectors from the front view:NuMaker-N9H30 board and NuDesign-TFT-LCD7 board combination connector (CON8). This panel connector supports 4-/5-wire resistive touch or capacitance touch panel for 24-bits RGB888 interface.Connector GPIO pin of N9H30 FunctionCON8.1 - Power 3.3VCON8.2 - Power 3.3VCON8.3 GPD7 LCD_CSCON8.4 GPH3 LCD_BLENCON8.5 GPG9 LCD_DENCON8.7 GPG7 LCD_HSYNCCON8.8 GPG6 LCD_CLKCON8.9 GPD15 LCD_D23(R7)CON8.10 GPD14 LCD_D22(R6)CON8.11 GPD13 LCD_D21(R5)CON8.12 GPD12 LCD_D20(R4)CON8.13 GPD11 LCD_D19(R3)CON8.14 GPD10 LCD_D18(R2)CON8.15 GPD9 LCD_D17(R1)CON8.16 GPD8 LCD_D16(R0)CON8.17 GPA15 LCD_D15(G7)CON8.18 GPA14 LCD_D14(G6)CON8.19 GPA13 LCD_D13(G5)CON8.20 GPA12 LCD_D12(G4)CON8.21 GPA11 LCD_D11(G3)CON8.22 GPA10 LCD_D10(G2)CON8.23 GPA9 LCD_D9(G1) NUMAKER-HMI-N9H30 USER MANUALCON8.24 GPA8 LCD_D8(G0)CON8.25 GPA7 LCD_D7(B7)CON8.26 GPA6 LCD_D6(B6)CON8.27 GPA5 LCD_D5(B5)CON8.28 GPA4 LCD_D4(B4)CON8.29 GPA3 LCD_D3(B3)CON8.30 GPA2 LCD_D2(B2)CON8.31 GPA1 LCD_D1(B1)CON8.32 GPA0 LCD_D0(B0)CON8.33 - -CON8.34 - -CON8.35 - -CON8.36 - -CON8.37 GPB2 LCD_PWMCON8.39 - VSSCON8.40 - VSSCON8.41 ADC7 XPCON8.42 ADC3 VsenCON8.43 ADC6 XMCON8.44 ADC4 YMCON8.45 - -CON8.46 ADC5 YPCON8.47 - VSSCON8.48 - VSSCON8.49 GPG0 I2C0_CCON8.50 GPG1 I2C0_DCON8.51 GPG5 TOUCH_INTCON8.52 - -CON8.53 - -CON8.54 - -CON8.55 - -NUMAKER-HMI-N9H30 USER MANUAL CON8.56 - -CON8.57 - -CON8.58 - -CON8.59 - VSSCON8.60 - VSSCON8.61 - -CON8.62 - -CON8.63 - Power 5VCON8.64 - Power 5VTable 2-1 LCD Panel Combination Connector (CON8) Pin Function●Power supply switch (SW_POWER1): System will be powered on if the SW_POWER1button is pressed●Three sets of indication LEDs:LED Color DescriptionsLED1 Red The system power will beterminated and LED1 lightingwhen the input voltage exceeds5.7V or the current exceeds 2A.LED2 Green Power normal state.LED3 Green Controlled by GPH2 pin Table 2-2 Three Sets of Indication LED Functions●Six sets of user SW, Key Matrix for user definitionKey GPIO pin of N9H30 FunctionK1 GPF10 Row0 GPB4 Col0K2 GPF10 Row0 GPB5 Col1K3 GPE15 Row1 GPB4 Col0K4 GPE15 Row1 GPB5 Col1K5 GPE14 Row2 GPB4 Col0K6GPE14 Row2GPB5 Col1 Table 2-3 Six Sets of User SW, Key Matrix Functions●NAND Flash (128 MB) with Winbond W29N01HVS1NA (U9)●Microphone (M1): Through Nuvoton NAU88C22 chip sound input●Audio CODEC chip (U10): Nuvoton NAU88C22 chip connected to N9H30 using I2Sinterface–SW6/SW7/SW8: 1-2 short for RS-485_6 function and connected to 2P terminal (CON5and J5)–SW6/SW7/SW8: 2-3 short for I2S function and connected to NAU88C22 (U10).●CMOS Sensor connector (CON10, SW9~10)–SW9~10: 1-2 short for CAN_0 function and connected to 2P terminal (CON11)–SW9~10: 2-3 short for CMOS sensor function and connected to CMOS sensorconnector (CON10)Connector GPIO pin of N9H30 FunctionCON10.1 - VSSCON10.2 - VSSNUMAKER-HMI-N9H30 USER MANUALCON10.3 - Power 3.3VCON10.4 - Power 3.3VCON10.5 - -CON10.6 - -CON10.7 GPI4 S_PCLKCON10.8 GPI3 S_CLKCON10.9 GPI8 S_D0CON10.10 GPI9 S_D1CON10.11 GPI10 S_D2CON10.12 GPI11 S_D3CON10.13 GPI12 S_D4CON10.14 GPI13 S_D5CON10.15 GPI14 S_D6CON10.16 GPI15 S_D7CON10.17 GPI6 S_VSYNCCON10.18 GPI5 S_HSYNCCON10.19 GPI0 S_PWDNNUMAKER-HMI-N9H30 USER MANUAL CON10.20 GPI7 S_nRSTCON10.21 GPG2 I2C1_CCON10.22 GPG3 I2C1_DCON10.23 - VSSCON10.24 - VSSTable 2-4 CMOS Sensor Connector (CON10) FunctionNUMAKER-HMI-N9H30 USER MANUAL2.2NuMaker-N9H30 Board - Rear View5V In (CON1)RS-232 DB9 (CON2,CON6)Expand Port (CON7)Speaker Output (J4)Earphone Output (CON4)Buzzer (BZ1)System ResetSW (SW5)SPI Flash (U7,U8)JTAG ICE (J2)Power ProtectionIC (U1)N9H30F61IEC (U5)Micro SD Slot (CON3)RJ45 (CON12, CON13)USB1 HOST (CON15)USB0 Device/Host (CON14)CAN_0 Terminal (CON11)CMOS Sensor Connector (CON9)Power On Setting(SW4, S2~S9)RS-485_6 Terminal (CON5)RTC Battery(BT1)RMII PHY (U14,U16)Figure 2-2 Rear View of NuMaker-N9H30 BoardFigure 2-2 shows the main components and connectors from the rear side of NuMaker-N9H30 board. The following lists components and connectors from the rear view:● +5V In (CON1): Power adaptor 5V input ●JTAG ICE interface (J2) ConnectorGPIO pin of N9H30Function J2.1 - Power 3.3V J2.2 GPJ4 nTRST J2.3 GPJ2 TDI J2.4 GPJ1 TMS J2.5 GPJ0 TCK J2.6 - VSS J2.7 GPJ3 TD0 J2.8-RESETTable 2-5 JTAG ICE Interface (J2) Function●SPI Flash (32 MB) with Winbond W25Q256JVEQ (U7); only one (U7 or U8) SPI Flashcan be used●System Reset (SW5): System will be reset if the SW5 button is pressed●Buzzer (BZ1): Control by GPB3 pin of N9H30●Speaker output (J4): Through the NAU88C22 chip sound output●Earphone output (CON4): Through the NAU88C22 chip sound output●Expand port for user use (CON7):Connector GPIO pin of N9H30 FunctionCON7.1 - Power 3.3VCON7.2 - Power 3.3VCON7.3 GPE12 UART3_TXDCON7.4 GPH4 UART1_TXDCON7.5 GPE13 UART3_RXDCON7.6 GPH5 UART1_RXDCON7.7 GPB0 UART5_TXDCON7.8 GPH6 UART1_RTSCON7.9 GPB1 UART5_RXDCON7.10 GPH7 UART1_CTSCON7.11 GPI1 UART7_TXDNUMAKER-HMI-N9H30 USER MANUAL CON7.12 GPH8 UART4_TXDCON7.13 GPI2 UART7_RXDCON7.14 GPH9 UART4_RXDCON7.15 - -CON7.16 GPH10 UART4_RTSCON7.17 - -CON7.18 GPH11 UART4_CTSCON7.19 - VSSCON7.20 - VSSCON7.21 GPB12 UART10_TXDCON7.22 GPH12 UART8_TXDCON7.23 GPB13 UART10_RXDCON7.24 GPH13 UART8_RXDCON7.25 GPB14 UART10_RTSCON7.26 GPH14 UART8_RTSCON7.27 GPB15 UART10_CTSCON7.28 GPH15 UART8_CTSCON7.29 - Power 5VCON7.30 - Power 5VTable 2-6 Expand Port (CON7) Function●UART0 selection (CON2, J3):–RS-232_0 function and connected to DB9 female (CON2) for debug message output.–GPE0/GPE1 connected to 2P terminal (J3).Connector GPIO pin of N9H30 Function J3.1 GPE1 UART0_RXDJ3.2 GPE0 UART0_TXDTable 2-7 UART0 (J3) Function●UART2 selection (CON6, J6):–RS-232_2 function and connected to DB9 female (CON6) for debug message output –GPF11~14 connected to 4P terminal (J6)Connector GPIO pin of N9H30 Function J6.1 GPF11 UART2_TXDJ6.2 GPF12 UART2_RXDJ6.3 GPF13 UART2_RTSJ6.4 GPF14 UART2_CTSTable 2-8 UART2 (J6) Function●RS-485_6 selection (CON5, J5, SW6~8):–SW6~8: 1-2 short for RS-485_6 function and connected to 2P terminal (CON5 and J5) –SW6~8: 2-3 short for I2S function and connected to NAU88C22 (U10)Connector GPIO pin of N9H30 FunctionSW6:1-2 shortGPG11 RS-485_6_DISW6:2-3 short I2S_DOSW7:1-2 shortGPG12 RS-485_6_ROSW7:2-3 short I2S_DISW8:1-2 shortGPG13 RS-485_6_ENBSW8:2-3 short I2S_BCLKNUMAKER-HMI-N9H30 USER MANUALTable 2-9 RS-485_6 (SW6~8) FunctionPower on setting (SW4, S2~9).SW State FunctionSW4.2/SW4.1 ON/ON Boot from USB SW4.2/SW4.1 ON/OFF Boot from eMMC SW4.2/SW4.1 OFF/ON Boot from NAND Flash SW4.2/SW4.1 OFF/OFF Boot from SPI Flash Table 2-10 Power on Setting (SW4) FunctionSW State FunctionS2 Short System clock from 12MHzcrystalS2 Open System clock from UPLL output Table 2-11 Power on Setting (S2) FunctionSW State FunctionS3 Short Watchdog Timer OFFS3 Open Watchdog Timer ON Table 2-12 Power on Setting (S3) FunctionSW State FunctionS4 Short GPJ[4:0] used as GPIO pinS4Open GPJ[4:0] used as JTAG ICEinterfaceTable 2-13 Power on Setting (S4) FunctionSW State FunctionS5 Short UART0 debug message ONS5 Open UART0 debug message OFFTable 2-14 Power on Setting (S5) FunctionSW State FunctionS7/S6 Short/Short NAND Flash page size 2KBS7/S6 Short/Open NAND Flash page size 4KBS7/S6 Open/Short NAND Flash page size 8KBNUMAKER-HMI-N9H30 USER MANUALS7/S6 Open/Open IgnoreTable 2-15 Power on Setting (S7/S6) FunctionSW State FunctionS9/S8 Short/Short NAND Flash ECC type BCH T12S9/S8 Short/Open NAND Flash ECC type BCH T15S9/S8 Open/Short NAND Flash ECC type BCH T24S9/S8 Open/Open IgnoreTable 2-16 Power on Setting (S9/S8) FunctionCMOS Sensor connector (CON9, SW9~10)–SW9~10: 1-2 short for CAN_0 function and connected to 2P terminal (CON11).–SW9~10: 2-3 short for CMOS sensor function and connected to CMOS sensorconnector (CON9).Connector GPIO pin of N9H30 FunctionCON9.1 - VSSCON9.2 - VSSCON9.3 - Power 3.3VCON9.4 - Power 3.3V NUMAKER-HMI-N9H30 USER MANUALCON9.5 - -CON9.6 - -CON9.7 GPI4 S_PCLKCON9.8 GPI3 S_CLKCON9.9 GPI8 S_D0CON9.10 GPI9 S_D1CON9.11 GPI10 S_D2CON9.12 GPI11 S_D3CON9.13 GPI12 S_D4CON9.14 GPI13 S_D5CON9.15 GPI14 S_D6CON9.16 GPI15 S_D7CON9.17 GPI6 S_VSYNCCON9.18 GPI5 S_HSYNCCON9.19 GPI0 S_PWDNCON9.20 GPI7 S_nRSTCON9.21 GPG2 I2C1_CCON9.22 GPG3 I2C1_DCON9.23 - VSSCON9.24 - VSSTable 2-17 CMOS Sensor Connector (CON9) Function●CAN_0 Selection (CON11, SW9~10):–SW9~10: 1-2 short for CAN_0 function and connected to 2P terminal (CON11) –SW9~10: 2-3 short for CMOS sensor function and connected to CMOS sensor connector (CON9, CON10)SW GPIO pin of N9H30 FunctionSW9:1-2 shortGPI3 CAN_0_RXDSW9:2-3 short S_CLKSW10:1-2 shortGPI4 CAN_0_TXDSW10:2-3 short S_PCLKTable 2-18 CAN_0 (SW9~10) Function●USB0 Device/HOST Micro-AB connector (CON14), where CON14 pin4 ID=1 is Device,ID=0 is HOST●USB1 for USB HOST with Type-A connector (CON15)●RJ45_0 connector with LED indicator (CON12), RMII PHY with IP101GR (U14)●RJ45_1 connector with LED indicator (CON13), RMII PHY with IP101GR (U16)●Micro-SD/TF card slot (CON3)●SOC CPU: Nuvoton N9H30F61IEC (U5)●Battery power for RTC 3.3V powered (BT1, J1), can detect voltage by ADC0●RTC power has 3 sources:–Share with 3.3V I/O power–Battery socket for CR2032 (BT1)–External connector (J1)●Board version 2.1NUMAKER-HMI-N9H30 USER MANUAL2.3 NuDesign-TFT-LCD7 -Front ViewFigure 2-3 Front View of NuDesign-TFT-LCD7 BoardFigure 2-3 shows the main components and connectors from the Front side of NuDesign-TFT-LCD7board.7” resolution 800x480 4-W resistive touch panel for 24-bits RGB888 interface2.4 NuDesign-TFT-LCD7 -Rear ViewFigure 2-4 Rear View of NuDesign-TFT-LCD7 BoardFigure 2-4 shows the main components and connectors from the rear side of NuDesign-TFT-LCD7board.NuMaker-N9H30 and NuDesign-TFT-LCD7 combination connector (CON1).NUMAKER-HMI-N9H30 USER MANUAL 2.5 NuMaker-N9H30 and NuDesign-TFT-LCD7 PCB PlacementFigure 2-5 Front View of NuMaker-N9H30 PCB PlacementFigure 2-6 Rear View of NuMaker-N9H30 PCB PlacementNUMAKER-HMI-N9H30 USER MANUALFigure 2-7 Front View of NuDesign-TFT-LCD7 PCB PlacementFigure 2-8 Rear View of NuDesign-TFT-LCD7 PCB Placement3 NUMAKER-N9H30 AND NUDESIGN-TFT-LCD7 SCHEMATICS3.1 NuMaker-N9H30 - GPIO List CircuitFigure 3-1 shows the N9H30F61IEC GPIO list circuit.Figure 3-1 GPIO List Circuit NUMAKER-HMI-N9H30 USER MANUAL3.2 NuMaker-N9H30 - System Block CircuitFigure 3-2 shows the System Block Circuit.NUMAKER-HMI-N9H30 USER MANUALFigure 3-2 System Block Circuit3.3 NuMaker-N9H30 - Power CircuitFigure 3-3 shows the Power Circuit.NUMAKER-HMI-N9H30 USER MANUALFigure 3-3 Power Circuit3.4 NuMaker-N9H30 - N9H30F61IEC CircuitFigure 3-4 shows the N9H30F61IEC Circuit.Figure 3-4 N9H30F61IEC CircuitNUMAKER-HMI-N9H30 USER MANUAL3.5 NuMaker-N9H30 - Setting, ICE, RS-232_0, Key CircuitFigure 3-5 shows the Setting, ICE, RS-232_0, Key Circuit.NUMAKER-HMI-N9H30 USER MANUALFigure 3-5 Setting, ICE, RS-232_0, Key Circuit3.6 NuMaker-N9H30 - Memory CircuitFigure 3-6 shows the Memory Circuit.NUMAKER-HMI-N9H30 USER MANUALFigure 3-6 Memory Circuit3.7 NuMaker-N9H30 - I2S, I2C_0, RS-485_6 CircuitFigure 3-7 shows the I2S, I2C_0, RS-486_6 Circuit.NUMAKER-HMI-N9H30 USER MANUALFigure 3-7 I2S, I2C_0, RS-486_6 Circuit3.8 NuMaker-N9H30 - RS-232_2 CircuitFigure 3-8 shows the RS-232_2 Circuit.NUMAKER-HMI-N9H30 USER MANUALFigure 3-8 RS-232_2 Circuit3.9 NuMaker-N9H30 - LCD CircuitFigure 3-9 shows the LCD Circuit.NUMAKER-HMI-N9H30 USER MANUALFigure 3-9 LCD Circuit3.10 NuMaker-N9H30 - CMOS Sensor, I2C_1, CAN_0 CircuitFigure 3-10 shows the CMOS Sensor,I2C_1, CAN_0 Circuit.NUMAKER-HMI-N9H30 USER MANUALFigure 3-10 CMOS Sensor, I2C_1, CAN_0 Circuit3.11 NuMaker-N9H30 - RMII_0_PF CircuitFigure 3-11 shows the RMII_0_RF Circuit.NUMAKER-HMI-N9H30 USER MANUALFigure 3-11 RMII_0_PF Circuit3.12 NuMaker-N9H30 - RMII_1_PE CircuitFigure 3-12 shows the RMII_1_PE Circuit.NUMAKER-HMI-N9H30 USER MANUALFigure 3-12 RMII_1_PE Circuit3.13 NuMaker-N9H30 - USB CircuitFigure 3-13 shows the USB Circuit.NUMAKER-HMI-N9H30 USER MANUALFigure 3-13 USB Circuit3.14 NuDesign-TFT-LCD7 - TFT-LCD7 CircuitFigure 3-14 shows the TFT-LCD7 Circuit.Figure 3-14 TFT-LCD7 CircuitNUMAKER-HMI-N9H30 USER MANUAL4 REVISION HISTORYDate Revision Description2022.03.24 1.00 Initial version NUMAKER-HMI-N9H30 USER MANUALNUMAKER-HMI-N9H30 USER MANUALImportant NoticeNuvoton Products are neither intended nor warranted for usage in systems or equipment, anymalfunction or failure of which may cause loss of human life, bodily injury or severe propertydamage. Such applications are deemed, “Insecure Usage”.Insecure usage includes, but is not limited to: equipment for surgical implementation, atomicenergy control instruments, airplane or spaceship instruments, the control or operation ofdynamic, brake or safety systems designed for vehicular use, traffic signal instruments, all typesof safety devices, and other applications intended to support or sustain life.All Insecure Usage shall be made at customer’s risk, and in the event that third parties lay claimsto Nuvoton as a result of customer’s Insecure Usage, custome r shall indemnify the damagesand liabilities thus incurred by Nuvoton.。
金蝶K3 V12.2 BOS插件开发手册

K/3 BOS插件開發手冊K/3 BOS插件開發手冊(版本:V12.2)金蝶軟體(中國)有限公司K/3產品部K/3 BOS開發部目錄概述 (1)COM (1)K3ClassEvents的物件模型 (1)使用說明 (1)K3ClassEvents的對象 (2)ListEvents對象參考 (3)DataSrv 屬性 (3)EnableListFillRowEvents 屬性 (4)K3Lib 屬性 (5)List 屬性 (6)ListEntrySort 屬性 (6)ListFilterString 屬性 (7)ListHeadSort 屬性 (7)MenuBar 屬性 (7)MultiCheckMgr 屬性 (8)RsId 屬性 (8)ShowMode 屬性 (9)ShowMsg 屬性 (9)DeleteBill 函數 (9)GetDataFldByKey 函數 (10)GetDataFld 函數 (11)GetCurrentSelRowInfo 函數 (12)GetSelectedBillInfo 函數 (13)LoadSelectedBill 函數 (14)RefreshList函數 (14)SenderMessage 函數 (15)UpdateNormalFld 函數 (16)UpdateNormalFldByKey 函數 (16)RefreshMenu 函數 (17)AfterBatchMultiCheck事件 (17)AfterBusinessCheck 事件 (18)AfterBusinessCheckEx 事件 (18)AfterCopyBillCreateData 事件 (19)AfterDeleteBill 事件 (19)AfterMergeCopyBill事件 (20)AfterMultiCheck 事件 (20)AfterMultiCheckEx 事件 (20)AfterSelList 事件 (21)AfterUnBusinessCheck 事件 (21)AfterUnBusinessCheckEx 事件 (22)AfterUnMultiCheck 事件 (22)BeforeMultiCheck 事件 (23)BeforeMultiCheckEx 事件 (24)BeforePrintBill 事件 (24)BeforeSenderMessage 事件 (25)BeforRefreshToolBar 事件 (25)BusinessCheck 事件 (26)BusinessCheckEx 事件 (26)FinishMultiCheck 事件 (26)FinishMultiCheckEx 事件 (27)ListFillRow 事件 (27)ListRowSelected 事件 (29)MenuBarClick 事件 (30)MenuBarInitialize 事件 (30)MultiCheck 事件 (30)MultiCheckEx 事件 (31)PrintSuccessful事件 (32)StartMultiCheck 事件 (32)StartMultiCheckEx 事件 (33)UnBusinessCheck 事件 (33)UnBusinessCheckEx 事件 (33)UnMultiCheck 事件 (34)UnMultiCheckEx 事件 (35)ReMultiCheck 事件 (35)ReMultiCheckEx 事件 (35)ReUnMultiCheck 事件 (36)ReUnMultiCheckEx 事件 (36)BaseClassEvent對象參考 (38)BrowseCtl 屬性 (38)DataSrv 屬性 (38)EnableListFillRowEvents 屬性 (38)InsertNewRowAndFillOption屬性 (40)K3Lib 屬性 (40)ListActiveBar 屬性 (41)ListEntrySort 屬性 (41)ListFilterString 屬性 (41)ListHeadSort 屬性 (42)MenuBar 屬性 (42)RsClassGroup 屬性 (43)RsId 屬性 (43)GetActiveCtl 函數 (43)GetSelectedClassID 函數 (44)GetSelectedClassType 函數 (45)GetSelectedItemID 函數 (45)IsSearchState 函數 (47)PitchItemByID 函數 (47)SelectClassGroupByID 函數 (48)SenderMessage 函數 (49)SetStatus函數 (50)RefreshClassGroups 方法 (50)RefreshListByClassGroupID 方法 (51)RefreshSelectedClassGroup 方法 (51)RefreshSelectedClassGroupList 方法 (52)AfterGetData 事件 (52)BeforePrintBill 事件 (53)BeforeSenderMessage 事件 (53)ClassGroupSelected 事件 (54)DeleteBillSucessful事件 (54)ListFillRow 事件 (55)ListRowSelected 事件 (57)MenuBarClick 事件 (57)MenuBarInitialize 事件 (57)RefreshList 事件 (58)BillEvent對象參考 (59)AccessoryTypeID 屬性 (59)BillCtl 屬性 (59)BillEntrys 屬性 (59)BillHeads 屬性 (60)BillHeight 屬性 (60)BillName 屬性 (60)BillStatus 屬性 (61)BillWidth 屬性 (61)CancelPrintControl屬性 (62)ClassType 屬性 (62)ClassTypeEntry 屬性 (62)ClassTypeKey 屬性 (63)Data 屬性 (63)DataSrv 屬性 (63)EntryPrimaryKey 屬性 (64)FID 屬性 (64)InsertNewRowAndFillOption屬性 (65)IsDoAction 屬性 (65)IsDoActionData 屬性 (65)K3Lib 屬性 (66)LayerCount 屬性 (66)LayerNames屬性 (66)MenuBar 屬性 (67)ObjectID 屬性 (68)ObjectType 屬性 (68)OriginalFieldValue屬性 (68)PrimaryKey 屬性 (69)ReSaveSuccess 屬性 (69)rsBillID 屬性 (69)ShowType 屬性 (70)TableInfo 屬性 (70)TableName 屬性 (70)TaskID 屬性 (71)ShowMsg 屬性 (71)BatchToDoActions函數 (71)DeleteEntryData 函數 (72)GetActiveCtl 函數 (73)GetActiveField 函數 (74)GetCommonControl函數 (74)GetDataFld 函數 (75)GetDataFldbyKey 函數 (76)GetFieldInfoByKey 函數 (77)GetDynamicCtlByKey函數 (78)GetFieldValue 函數 (78)GetToolIndex 函數 (79)GetVariable函數 (80)InsertNewRowAndFill 函數 (81)IsChange 函數 (81)IsFileNeedFilter 函數 (82)LockBill 函數 (83)RefreshBill 函數 (83)SenderMessage 函數 (83)SetDecimal 函數 (84)SetFieldSumValue函數 (85)SetFieldValue 函數 (85)SetSumDecimal 函數 (86)SetText 函數 (87)SetTypeFloatMax 函數 (88)SetTypeFloatMin 函數 (88)ShowHideField 函數 (89)ShowHideGrid 函數 (89)Sum 函數 (90)UpdateLookFld 函數 (90)UpdateNormalFld 函數 (91)DoAction 方法 (91)IsDoActionByKey 方法 (92)RemoveRow 方法 (93)SaveBill 方法 (93)SetActiveTab方法 (94)SetBillFormCaption 方法 (94)SetCaption 方法 (95)SetGridMaxRows方法 (95)SetStatus 方法 (96)SetActiveCell 方法 (96)SetBillWindowState方法 (97)SetRowsPerRequest方法 (97)SetStateStampPicture方法 (98)SetStatusBarInfo方法 (98)SetVariable函數 (99)SizeBillControl方法 (100)AddNewRow 事件 (100)AfterBusinessCheck 事件 (100)AfterBusinessCheckEx 事件 (101)AfterCopyBill 事件 (101)AfterDeleteRow 事件 (101)AfterDoAction 事件 (102)AfterFillRow 事件 (103)AfterFirstNewBill 事件 (103)AfterInputBillSetSumData 事件 (103)AfterLoadBill 事件 (104)AfterLoadBillSetSumData 事件 (104)AfterLoadDynamicCtl事件 (104)AfterMergeCopyBill 事件 (105)AfterMultiCheck 事件 (105)AfterMultiCheckEx 事件 (106)AfterNewBill 事件 (106)AfterNewEmptyData 事件 (106)AfterSave 事件 (107)AfterSelBill 事件 (107)AfterSelBillBeforeFillData 事件 (107)AfterStockQuery事件 (108)AfterUnBusinessCheck 事件 (108)AfterUnBusinessCheckEx 事件 (108)AfterUnMultiCheck 事件 (108)AfterUnMultiCheckEx 事件 (109)BeforeDeleteRow事件 (110)BeforeDoAction 事件 (110)BeforeLoadBill 事件 (111)BeforeMultiCheck 事件 (111)BeforePrintBill 事件 (113)BeforeSave 事件 (113)BeforeSelBills 事件 (113)BeforeSelBillShowFilter 事件 (114)BeforeSenderMessage 事件 (115)BeforeSetMutilSelData事件 (115)BeforeSetMutilSelData2事件 (116)BeforeVerify 事件 (116)BeforeWindowExit事件 (117)BeforLoadBillFillData 事件 (117)BeginEdit 事件 (117)BusinessCheck 事件 (117)BusinessCheckEx 事件 (118)Change 事件 (118)CommandClick事件 (119)EntryFieldChanged事件 (119)FinishMultiCheck 事件 (119)FinishMultiCheckEx 事件 (120)GetFocus 事件 (120)HeadCtlClick 事件 (121)LostFocus 事件 (121)MenuBarClick 事件 (122)MenuBarInitialize 事件 (122)MultiCheck 事件 (122)MultiCheckEx 事件 (123)ReMultiCheck 事件 (124)ReMultiCheckEx 事件 (124)ReUnMultiCheck 事件 (125)ReUnMultiCheckEx 事件 (125)SaveBillFailed 事件 (125)SaveBillSuccess事件 (126)SSTabClick事件 (126)StartMultiCheck 事件 (126)StartMultiCheckEx 事件 (127)UnBusinessCheck 事件 (128)UnBusinessCheckEx 事件 (128)UnMultiCheck 事件 (128)UnMultiCheckEx 事件 (129)Verify 事件 (130)K3Lib對象參考 (131)Account 屬性 (131)Net 屬性 (132)User 屬性 (132)CreateK3Object 函數 (136)GetData 函數 (137)GetK3Language 函數 (138)LoadKDString 函數 (139)UpdateData 方法 (141)GetStockQty 函數 (141)LookUpClass函數 (142)LoadBill 方法 (144)LoadList方法 (144)LoadOldList方法 (145)Account對象參考 (147)AccountID 屬性 (147)AccountName 屬性 (147)SetupType 屬性 (147)Net對象參考 (149)BeginMutex 函數 (149)CommitMutex 函數 (149)QueryFunc 函數 (150)QuerySubSys 函數 (150)User對象參考 (151)UserID 屬性 (151)UserName 屬性 (151)MenuBar對象參考 (152)MenuBar 物件結構圖 (152)ActiveBand 屬性 (153)BOSBands 屬性 (153)BOSTools 屬性 (154)Refresh 方法 (154)BOSBands對象參考 (155)Count 屬性 (155)Item 屬性 (155)Add 函數 (155)Remove 方法 (156)RemoveAll 方法 (156)BOSBand對象參考 (157)BandName 屬性 (157)BandType 屬性 (157)BOSTools 屬性 (157)Caption 屬性 (157)CurrentTool 屬性 (158)DockingArea 屬性 (158)DockingOffset 屬性 (158)DockLine 屬性 (159)Visible 屬性 (159)Wrappable 屬性 (160)Refresh 方法 (160)BOSTools對象參考 (161)Count 屬性 (161)Item 屬性 (161)Add 函數 (161)GetFreeToolID 函數 (162)InsertAfter 方法 (162)InsertBefore 方法 (163)Remove 方法 (163)RemoveAll 方法 (164)BOSTool對象參考 (165)Alignment 屬性 (165)BeginGroup屬性 (165)Caption 屬性 (165)CaptionPosition 屬性 (166)Checked 屬性 (166)Default 屬性 (166)Description 屬性 (167)Enabled 屬性 (167)ShortcutKey 屬性 (167)Style 屬性 (170)SubBand 屬性 (170)Tag 屬性 (170)ToolID 屬性 (170)ToolName 屬性 (171)ToolPicture 屬性 (171)TooltipText 屬性 (171)Visible 屬性 (171)PasteToolFace 方法 (171)SetPicture 方法 (172)BillHeads\BillHead\BillEntrys\BillEntry\BOSFields\BOSField對象參考 (174)MenuBar 物件結構圖 (174)BillHeads對象參考 (175)Count 屬性 (175)Item 屬性 (176)BillHead對象參考 (177)BOSFields 屬性 (177)BillEntrys對象參考 (178)Count 屬性 (178)Item 屬性 (179)BillEntry對象參考 (180)EntryHeight 屬性 (180)EntryIndex 屬性 (180)EntryLeft 屬性 (180)EntryTop 屬性 (180)EntryType 屬性 (181)EntryWidth 屬性 (181)KeyField 屬性 (181)Layer 屬性 (181)MaxRows 屬性 (182)TableName 屬性 (182)Visible 屬性 (182)AddRow 方法 (182)RemoveRow 方法 (183)BOSFields對象參考 (184)Count 屬性 (184)Item 屬性 (184)BOSField對象參考 (185)Caption 屬性 (185)FieldHeight 屬性 (185)FieldLeft 屬性 (185)FieldLock 屬性 (185)FieldName 屬性 (186)FieldTop 屬性 (186)FieldWidth 屬性 (186)Filter 屬性 (186)FKey 屬性 (186)FontBold 屬性 (187)FontItalic 屬性 (187)FontName 屬性 (187)FontSize 屬性 (187)FrameBorder 屬性 (188)FrameBorderColor 屬性 (188)LabelColor 屬性 (188)LabelWidth 屬性 (188)Layer 屬性 (188)MustInput 屬性 (189)NeedSave 屬性 (189)Note 屬性 (189)Number 屬性 (189)Page 屬性 (189)Row 屬性 (190)TableName 屬性 (190)Text 屬性 (190)Value 屬性 (190)Visible 屬性 (191)SetFieldSumValue方法 (191).Net (192)基礎配置 (192)開發環境 (192)使用說明 (192)引用 (192)插件跟蹤 (192)K3ClassEvents的物件模型 (193)K3ClassEvents的對象 (193)ListEvents對象參考 (194)事件聲明 (194)AfterCopyBillCreateData 事件 (195)OnBarInitialize事件 (195)AfterShowBill事件 (195)OnBarItemClick事件 (196)ShowBill函數 (196)AspxGetSelectList函數 (197)AddBarItem函數 (197)AddBarItemLink函數 (198)SetBarItemProperty函數 (199)AddBarItemLink函數 (199)RemoveBarItem函數 (200)RemoveBarItemLink函數 (200)BillName 屬性 (201)ClassType 屬性 (201)ClassTypeEntry 屬性 (201)ClassTypeKey 屬性 (202)PrimaryKey 屬性 (202)EntryPrimaryKey 屬性 (203)TableInfo 屬性 (203)TableName 屬性 (203)BillEvent對象參考 (205)事件聲明 (205)OnBarInitialize事件 (206)OnBarItemClick事件 (207)AfterNewBill 事件 (207)BeforLoadBillFillData事件 (207)AfterLoadBill事件 (207)AfterShowBill 事件 (208)AfterConfirm事件 (208)AfterF7Select事件 (208)BeforeSave 事件 (209)AfterSave 事件 (209)AddBarItem函數 (210)AddBarItemLink函數 (211)GetBarItemProperty函數 (211)SetBarItemProperty函數 (212)AddBarItemLink函數 (212)RemoveBarItem函數 (213)RemoveBarItemLink函數 (213)Alter函數 (214)Confirm函數 (214)GetFieldValue函數 (215)GetRequest函數 (216)LockBillEntry函數 (216)LockCell函數 (217)LockWebTabItem函數 (218)SaveBill函數 (218)SetFieldValue函數 (219)ShowBill函數 (220)ShowF7Select函數 (221)BillName 屬性 (221)ClassType 屬性 (222)ClassTypeEntry 屬性 (222)ClassTypeKey 屬性 (223)PrimaryKey 屬性 (223)EntryPrimaryKey 屬性 (223)TableInfo 屬性 (224)TableName 屬性 (224)CurBillID屬性 (224)BillHeads對象參考 (226)Count 屬性 (226)Item 屬性 (226)BillHead對象參考 (227)BOSFields 屬性 (227)BillEntrys對象參考 (228)Count 屬性 (228)Item 屬性 (228)BillEntry對象參考 (229)BOSFields 屬性 (229)EntryHeight 屬性 (229)EntryIndex 屬性 (229)EntryLeft 屬性 (229)EntryTop 屬性 (229)EntryWidth 屬性 (230)KeyField 屬性 (230)Layer 屬性 (230)TableName 屬性 (231)Visible 屬性 (231)BOSFields對象參考 (232)Count 屬性 (232)Item 屬性 (232)BOSField對象參考 (233)Caption 屬性 (233)FieldHeight 屬性 (233)FieldLeft 屬性 (233)FieldLock 屬性 (233)FieldName 屬性 (234)FieldTop 屬性 (234)FieldWidth 屬性 (234)Filter 屬性 (234)FKey 屬性 (234)FontBold 屬性 (235)FontItalic 屬性 (235)FontName 屬性 (235)FontSize 屬性 (235)FrameBorder 屬性 (236)FrameBorderColor 屬性 (236)LabelColor 屬性 (236)LabelWidth 屬性 (236)Layer 屬性 (236)MustInput 屬性 (237)NeedSave 屬性 (237)Note 屬性 (237)Number 屬性 (237)Page 屬性 (237)Row 屬性 (238)TableName 屬性 (238)Text 屬性 (238)TextColor 屬性 (238)Value 屬性 (238)Visible 屬性 (239)用戶場景 (240)需求 (240)總體需求 (240)需求分解 (241)詳細需求 (242)單據流程 (244)多級審核 (245)憑證功能 (245)設計和實現 (246)單據資料結構設計 (246)單據頭 (246)單據體 (248)欄位的過濾條件 (251)BOS IDE中設置過濾條件 (251)通過SQL更新欄位的過濾條件 (253)Action設置 (254)自動生成Action (254)手動添加Action (257)單據流程 (259)【銷售訂單】下推生成【產品入庫通知單】 (259)練習一下 (263)多級審核 (265)多級審核設置 (265)憑證功能 (267)設置憑證數據來源 (267)操作管理 (268)插件開發 (271)部署 (272)發佈到主控台 (272)製作部署文件 (274)概述為了實現客戶個性化的需求和保持K/3 BOS架構的開放性,K/3 BOS提供了插件編程,有效的擴展了K/3 BOS平臺,K/3 BOS插件編程是通過K3ClassEvents物件代理實現的。
IONConfigTool 用户手册说明书
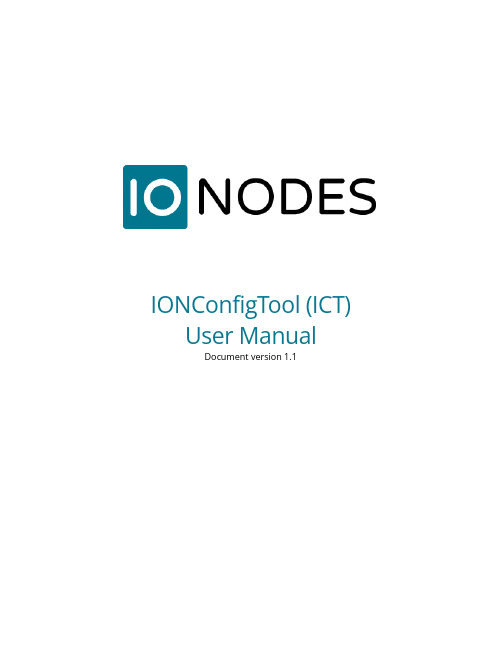
IONConfigTool (ICT) User ManualDocument version 1.1Table of Contents1Introduction (4)2The main interface (4)3The Admin menu (5)3.1Unicast Discovery (5)3.2Credentials (5)4Device Discovery & Management Using Bonjour Protocol (6)4.1Discovery list (6)4.1.1Assign IP Address (8)4.1.2Firmware upgrade (8)4.1.3Identify Device (9)4.1.4Configuration Web Page (10)4.1.5Restart Device (10)4.1.6Export Configuration (10)4.1.7Import Configuration (11)5Discovering IONODES devices when your network does not support the Bonjour Protocol (14)5.1Unicast Discovery Test (14)5.1.1Disable Bonjour protocol (14)5.2Unicast Discovery Configuration (15)5.2.1Configure Unicast Discovery (15)5.2.2Configure IP scan range(s) (16)5.2.3Configure Credentials (16)5.2.4Refresh device list results (17)6Troubleshooting (18)6.1Unable to run the IonConfigTool (18)6.2Unable to see discovered units (18)6.3Unit is discovered but remains offline (18)7Getting Help (19)IONConfigTool (ICT)User Manual©2010-2022, IONODES INCAll Rights reserved.No part of this documentation may be reproduced or transmitted in any form or by any means, electronic, photographic or mechanical, except as expressed in the Software License Agreement.IONODES shall not be liable for technical or editorial errors or omissions contained herein. The information in this document is subject to change without notice.The information in this publication is provided “as is” without warranty of any kind. The entire risk arising out of the use of this information remains with the recipient. In no event shall IONODES be liable for any direct, consequential, incidental, special, punitive, or other damages whatsoever (including without limitation, damages for loss of business profits, business interruption or loss of business information), even if IONODES has been advised of the possibility of such damages and whether in an action orcontract or tort, including negligence.This software and documentation are copyrighted. All other rights, including ownership of the software, are reserved to IONODES Inc. Windows is a registered trademark of Microsoft Corporation. All other brand and product names are trademarks or registered trademarks of the respective owners.The following words and symbols mark special messages throughout this guide:Warning:Text set off in this manner indicates that failure to follow directions could result in damage to persons or equipment.Note: Text set off in this manner indicates special instructions which should be paid attention to.1IntroductionThe IONConfigTool, also referred to as ICT, was developed to properly discover and configure IONODES devices on customer networks during initial installation, for day-to-day maintenance or for support purposes.This user manual covers essential functions to get IONODES devices up and running in the most simple and efficient manner. By default, the ICT will scan a network using the multicast Bonjour protocol. If your network does not support or filters out multicast/Bonjour discovery, a unicast discovery method is also available and is explained in section 5.2The main interface1.The Admin menu – used to input device credentials or use unicast network device discoverywork interface selection – used to select which network interface to scan (i.e., cabled vs Wi-Finetworks)3.Device listing – all IONODES devices discovered on the previously-selected network3The Admin menuClick on the drop-down arrow to display menu selections3.1Unicast DiscoveryBy default, the ICT uses multicast network discovery using the Bonjour protocol, as demonstrated in this part of the user guide. For Unicast discovery procedure, please refer to section 5 of this user guide.3.2CredentialsSelecting credentials will open the following window allowing you to enter the device credentials if different than the default admin/admin.1.Enter the device’s credentials if you have previously changed from the default admin/admin.2.Click OK to save and close this window and return to the ICT4Device Discovery & Management Using Bonjour Protocol4.1Discovery listTo make things easier when discovering multiple devices on a given network, we suggest clicking on the IP Address column heading to sort multiple devices in ascending or descending order.1. A green checkmark indicates the unit is online. A red X indicates that the unit has fallen offlinesince initial discovery list was created.Note: 2- IP addresses listed in blue are DHCP-assigned3- IP addresses listed in black are static-configured IPsA left click of the mouse on the MAC Address of a given device will open a context menu with multiple choices. In this section, we’ll see what the most often used ones do.4.1.1Assign IP AddressThis will open the IP assignment window1.Manually assign IP information2.Click Start button to apply and close the window 4.1.2Firmware upgrade1.Click to select firmware file through Windows Explorer2.Select the firmware file path3.Confirm proper device information and current firmware version4.Click start to install the new firmware followed by possible reboot, device dependant4.1.3Identify DeviceOn all IONODES encoder and decoder products, this will make their status LED flash for you to physicallyidentify them. See their respective user manual for details on the LED behavior.4.1.4Configuration Web PageThis will open the configuration web page using your computer’s default web browser.Warning:Older IONODES devices require Microsoft Silverlight and must be opened using Microsoft Internet Explorer or Microsoft Edge in Internet Explorer mode.4.1.5Restart DeviceAs indicated, this will send a signal to the device to restart.4.1.6Export ConfigurationThis will open the Export Configuration window.1.The ICT will automatically save the configuration file within its own folder structure of configuration file is automatically generated based on IP, device and date & time3.Save to finalize export operation4.1.7Import ConfigurationThis will open a warning advising that passwords and network information are not imported.The Import Configuration selection window.1.Select the file to be imported2.Ensure proper file is selected, especially if multiple files are available within the folder3.Click Open to continue the import operation1.Select all the configuration that you want to import2.Select the device where the configuration will be imported3.Click Import to start the import operation2.Click Close to end import routine and return to ICT interface5Discovering IONODES devices when your network does not support the Bonjour ProtocolSome of the more secure enterprise networks filter out the Bonjour protocol as well as other network scan functions for security reasons. When you initially plug your IONODES device into one of these networks, although it is set by default to using DHCP and will be attributed an actual network IP address, network filters might make the device undiscoverable in our IONConfigTool or other IP scanning software. To remedy this situation and allow a network discovery with our IONConfigTool, it is possible to run a Unicast scan with some very basic authentication. Here’s how to do this…If your device is already on your network and undiscoverable, head down to Section 2.5.1Unicast Discovery TestFor demonstration purposes, we have disabled the Bonjour Discovery in our ION-R200 Secure Display Station to keep it from being discovered on our network. This can be changed on the Configuration page, in the Network tab of your IONODES device if you want to run a similar test.5.1.1Disable Bonjour protocol1.Once logged in to your IONODES web user interfaceI, head over to the Configuration page2.Click on the Network tab3.Click on the Bonjour section to select it4.Disable the Bonjour protocol and click Save at the bottom of the pageNow that the Bonjour protocol is disabled. When we run the IONConfigTool, in this example, our ION-R200, with a known IP of 10.190.100.42, is not discovered.5.2Unicast Discovery Configuration5.2.1Configure Unicast Discovery1.In the Admin menu item of the IONConfigTool, click on Unicast Discovery.This will bring up the Unicast Discovery settings window.Note: The values shown in the graphic are for this specific example. Verify with your network administrator for your network-specific values5.2.2Configure IP scan range(s)1.Enter the starting address of the IP range to scan2.Enter the last address of the IP range to scan3.Enter the desired ping timeout. This is the time the ICT will wait before attempting to reach thenext device in the IP address range.4.Check Unicast Discovery Only5.Click the ADD button to add the IP range to the search criteria. Multiple IP ranges can be added toa single search6.This will add the IP range(s) to the search list7.Close the configuration window5.2.3Configure CredentialsSince the IONConfigTool will send a request on all IPs of the IP range, you must enter the proper authentication credentials of the device being discovered. In the Admin menu item of the IONConfigTool, click on CredentialsBy default, the credentials are set to admin / admin as username and password. However, if the credentials have been previously changed at some point, the new credentials must be entered in the ICT to properly discover the device. To do this:1.Enter the desired username & password combination2.Click OK to save and close the Credentials configuration window5.2.4Refresh device list results1.Simply hit the Refresh button on the IONConfigTool to force a new Unicast scan of the IP rangewith proper credentials as outlined in the previous steps2.Device will now be listed in the discovered device list when present on the same network6Troubleshooting6.1Unable to run the IonConfigTool•Make sure you have properly decompressed (unzipped) the contents of the downloaded zipped file to a selected or default empty directory before running the executable. The application cannot be run from a temporary folder, as when opening the zipped file from within Windows Explorer.6.2Unable to see discovered unitsVerify unit has power via PoE or a valid power supply.•Make sure you have connected the device to your network.•Make sure the GREEN LED on the RJ45 connector is lit. If it is not lit, verify the network connectivity with the network switch.•Before the device can be discovered, the status LED must be lit GREEN as this indicates ready state of the device.•Since Bonjour Protocol uses multicast, verify with your IT department to ensure your network is multicast-enabled.•Verify that your firewall settings allow the Bonjour protocol traffic (port 5353)•Refer to section 5 for Unicast discovery.6.3Unit is discovered but remains offline•Verify that your network is on the same subnet as the discovered device7Getting HelpYou can get help from the IONODES technical support team in many ways:•By sending an email to *******************•By calling our office during regular work hours at:o+1 (844) 696-1060 (Toll Free North America)o+1 (450) 696-1060Our technical support team is trained to support you with installation as well as maintenance of your IONODES products.。
PROXKey Tool 用户手册说明书
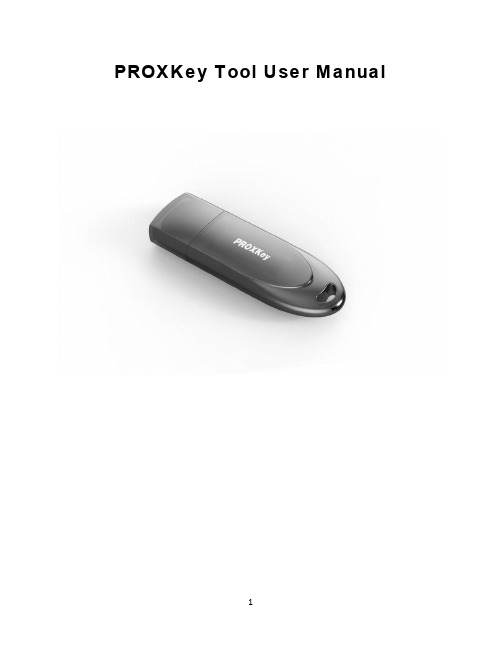
PROXKey Tool User ManualTable of Contents1 Introduction (4)2 PROXKey Product (5)2.1 PROXKey Tool (5)2.2 PROXKey function modules (6)2.3 PROXKey using environment (7)3 PROXKey Tool Installation (8)3.1 PROXKey Tool Installation (8)4 PROXKey Tool (10)4.1 Launching PROXKey Tool (10)4.2 PROXKey Tool Overview (11)Change PIN (13)Change Token Name (14)Certificate (15)Device Information (16)About (21)Help (18)5 Support (22)Where we are (22)Follow us at (22)Table of FiguresFigure 1 Installation (8)Figure 2 Installation (9)Figure 3 PROXKey Token Tool Main Menu (10)Figure 4 Running Label of PROXKey Tool (11)Figure 5 Setting up User PIN (12)Figure 6 Set PIN Successful and Warning (12)Figure 7 Change PIN (13)Figure 8 Change USER PIN fail (14)Figure 9 Change Token name (14)Figure 10 Certificate (15)Figure 11 Device Information (16)Figure 12 Update (17)Figure 13 Diagnostic Tool (18)Figure 14 Help Menu (18)Figure 15 Ticket (19)Figure 16 Remote Access (19)Figure 17 System Setting (20)Figure 18 Java Configuration (20)Figure 19 About (21)1IntroductionWith the development of Internet and fast development of network technology a clear majority of people communicate with each other online,instead of traditional methods of face to face meeting. Due to this security authentication becomes vital for the network security, also the bank transactions and fund transfer becoming online it is very important to protect data.The USB tokens provide a secure way to store the Digital Signature Certificate.The PROXKey USB Token is a hardware cryptographic module with a USB form factor for two-factor authentication which has been validated against the FIPS 140-2 at security level3. The public and private user’s key is generated and is stored on the chip embedded inside the token; the key pairs are stored in EEPROM. Private Key is secured and cannot be exported.2PROXKey ProductIn internet applications, like e-business, e-government, network communication and e-transaction, it is very important to ensure the informationsecurity.PROXKey Product is developed as a solution of this security problem. It provides a convenient and reliable secure environment for customers.2.1PROXKey ToolHigh in security1.Supporting 2048 bits RSA asymmetric cryptographic algorithms and SHA2.2.Supporting password and hardware authentication.3.Hardware device provide secure memory space which can be used to store password,private key and other secret data. The secret data is not exportable;the hardware device is not replicable.4.Secure and reliable.All encryptions and decryptions are operated inside thePROXKeydevice.Uniformity specification1.Following the worldwide universal standards: PKCS#11 v2.1 specification and MicrosoftCSP 2.0 specification.pletely realized the security communication functions supported by SSL andS/MIME. The specification covers application and storage of digital certificate, digital signature and verification, encryption/decryption, etc.ing standard interface to connect with browsers, the communications is strictly abidingbrowser’s secure communication operating regulations.4.Supporting certificate’s interoperability between CSP and PKCS#11.5.Supporting certificate application and secure email exchange in the environment ofIE/Outlook, Foxmail, NetScape, Mozilla and Firefox/Thunderbird.6.Supporting X. 509 v3 certificate storage.Excellent compatibility1.No need to install special PROXKey driver, the driver integrated inside the WindowsOperating System is used there by eliminating the driver installation.2.The hardware is a kind of USB device which is following USB1.1/USB 2.0specification. Itcan be used conveniently in every USB supported facilities.4.Uniform interfaces is used for UDK devices. One suite can supports both HID and UDKdevices.5.The UI is supported in Windows/ME/2000/2003/XP/Vista/Windows7/Windows 8 andWindows 8.1/Linux Operating Systems are all supporting.Flexible designing modularized design to meet customer’s dedicated requirements.2.A convenient platform for user’s certificates management is provided.3.UI (User Interface) is designed up to customer’s requirements.4.Secondary development interface is provided.2.2PROXKey function modulesPROXKey network security suite includes the following 5 modules:CSP module:1.It is a basic interface module based on Microsoft CSP2.0 specification.2. It is configured at registry.3.It can be used in IE browser, Outlook and Foxmail for certificate application, securitywebsite visitation and security email service, etc.PKCS#11 Module:1. Supporting PKCS#11 v2.1 interface.2. It is applicable in NetScape/Mozilla browser and ThunderBird email server. Administrator’s tool:It provides functions of key initialization, certificate operation and PIN operation, etc. User’s tool:It provides not only PIN operations of verification and modification, but also certificate operations of checking and installation/uninstall.Background:At the time of PROXKey plug in and out, certificate registration/revocation will be automatically done, and application programs will automatically start and end.2.3PROXKey using environmentThe supporting operating systems are shown as below:WIN 2000/2003/2008ServerWINDOWS 7, 8, 8.1, 10Mac OS, Linux and UbuntuThe supporting software includes:IE/Mozilla/Netscape/browsers.Outlook/Foxmail/ThunderBird email clients.3PROXKey Tool InstallationThe PROXKey comes with the Autorun supported ND (No Driver) feature. User can install the PROXKey tool just by plugging the token into the USB slot, the installation and details of the PROXKey tool is explained in detail below.3.1PROXKey Tool InstallationTo begin with the installation just plug in the token into the USB slot of the Laptop or PC, the Autorun supported product will automatically install PROXKey tool on the system1.Once the token is plugged into the USB slot the Autorun features asks for the installation of thetoken management tool as shown in the Figure 1, just click the install button to proceed with the installation of the software.Figure1Installation2.The token management software installs as shown in the Figure 2,clickfinish button to complete theinstallation.Figure2Installation4PROXKey Tool4.1Launching PROXKey ToolThe PROXKey tool can be launched using the short cut icon created on the desktop during installation, or can be found by clicking Start menu on windows and then finding the WD PROXKey Tool.The User Interface of PROX Key Token tool is easy and elegant as shown in Figure 3.All the functionalities are represented by icons which are easy to access with just a click of mouse button.Figure3PROXKey Token Tool Main MenuDuring PROXKey administrator’s tool running, the label of the tool will display in the right-handbottom corner as shown in Figure 4.Figure4Running Label of PROXKey Tool4.2PROXKey Tool OverviewAfter the installation of the software and when the token is plugged in, the user will be advised to set the PIN as shown in Figure 5. The user should enter the appropriate PIN length between 6-32 characters and set the user PIN.Each new token must be set with a user defined PIN.The length of the PIN should be between 6-32 (Alpha Numeric)characters.This PIN can be reset by the user later if needed.Figure 5shows the Set User PIN prompt and Figure 6(a) shows the successful PIN set.If the PIN is entered exceed the range of 6 to 32 characters, a warning window like Figure 6(b) will pop out to tell you PIN for the token requirements.Figure5Setting up User PINOnce the proper PIN is set the dialog as shown in Figure 6 (a) is prompted and in case of invalid length of PIN setting a dialog as shown in Figure 6 (b) is prompted.(a)Figure6Set PIN Successful and Warning(b)Figure3shows the basic functionalities of the PROXKey token tool.1.Change User PIN2.Change Token Name3.Certificate4.Device Information5.Options6.Help7.AboutChange PINIf the user wants to change the PIN which was set earlier this option helps to set a new PIN.The user needs to remember his earlier set PIN which he needs to enter first and then set a new PIN as shown in Figure 7. There is an added option of even using the softkeyboard to enter the PIN.Figure7Change PINHowever,when the user tries to change the USER PIN he needs to enter the old USER PIN and confirm the old USER PIN and then enter the new USER PIN the maximum User PIN error counter is set by default to 15so the user cannot try to update the password more than15 times.As shown in Figure 8 user gets 15attempts by default in case he wants to reset the USER PIN. If the user has forgotten the USER PIN, please contact the support for help.Figure8Change USER PIN failChange Token NameChange Label provides administrators with the interface of change the label of user’s device.It is shown in Figure9Figure9Change Token nameCertificateThe PROXKey Token tool automatically registers the CA, CCA and also the user certificate which is imported in the token, the user need not worry about registering each certificate which he dwnloads.Figure10CertificateShow CertificateThis function shows the certificate details such as the issuer information, issued toinformation and validity information.Delete CertificateThis feature enables to delete the unwanted certificates, the user PIN is needed todelete the certificates which are not needed.Import CertificateImport Certificate feature enables the user to import the certificates into the token, the user PIN is needed to import the certificates in the token.Device InformationDevice inforamtion provides the token information and the system environment asshown in the figure. Such as the Winodos version, IE version,Figure11Device InformationOptionsCache User PINThis is used to cache the USER PIN of the token so that when the token is used for multiple signing the token do not prompt to enter the USER PIN again and again. This is valid until the token is plugged out from the system. Once the token is plugged this feature must be again selected to cache the password.Figure 12 shows all the submenus whenFigure12Update✓UpdateThe PROXKey tokens have automatic update feature, where in when the new software is released for the tokens it will be uploaded in the FTP.When the “Update” is clicked with the proper internet connection the token software automatically updates itself providing ease of use for the user. Figure 12 shows the update process✓Diagnostic ToolDiagnostic tool can be used to understand the user system configurations; this basically helps to understand the technical issues or compatibility issue. This tool helps the support team to get the end use system details. The diagnostic tool also creates a log file which will be helpful for thesupport team to resolve issues. Figure13shows the Diagnostic Tool workingFigure13Diagnostic ToolHelpThis will help the end user for the support related help Remote for support helps in using team viewer support and support website Figure 14 shows the help menuFigure14Help Menu✓TicketThis feature is useful for the user to report the issues to the support team, when the user is facing any issues he/she can raise the ticket. The support team will analyse the issue and close the ticket at the earliest, this is the unique feature provided in PROXKey for user convinence. Figure14 shows the ticket raising procedure whichFigure15Ticket✓Remote AccessFigure16Remote Access✓System SettingThis is used to resolve the sytem configuration related issues, if the user faces any compatablity issue the user just need to click this button and file downloads and installs which shall resolve all the system configuration related issues. Figure 16 shows the System SettingFigure17System SettingJava ConfigurationsThis button resolves the java related issues,the user just need to click this button and a file downloads and installs which will resolve all the java related issues. Figure 17 shows the java configurationFigure18Java ConfigurationAboutThis shows the version and copyright information of the company and the version name of the software the user is usingFigure19About5SupportFor any assistance and support about the PROXKey token or the PROXKey Tool please find the help icon on the left hand top corner, click the Help>About(A) icon and you can find the link for the PROXKey Tool and PROXKey token support as shown in the Figure 13and the website where the contact details can be found is as shwon in Figure 13Where we areHead OfficeCrypto Planet(A Venture of Pagaria Advisory Private Limited) F-15, 1st Floor, Haware Centurion,Plot: 88-91, Sector–19A,Nerul–East, Navi Mumbai, Maharashtra, India–400706.Follow us atContact InfoIVR:+91 86551 86552Landline:*********************** E Mail:******************************************************Web Address:www.cryptoplanet.in。
Futronic MKII MANAGER User Manual

Futronic MKII MANAGER(PC SOFTWARE)User ManualVersion 01 March 2019Klokkestoebervej 4. DK-9490 Pandrup. DenmarkTel: +45 96 44 44 44, Fax: +45 96 44 44 45E-mail:*********************,TABLE OF CONTENTTABLE OF CONTENT (2)INTRODUCTION (3)How to download and install (3)TEST RESULTS (4)DSC COMPOSER (5)AIS COMPOSER (6)SETTINGS (7)EPIRB TEST REPORT GENERATOR (8)1. Generating reports out of stored test results (8)2. PC-controlled EPIRB tests (10)NATIONAL MARINE ELECTRONIC ASSOCIATION (NMEA) (11)VHF SENSITIVITY TEST (13)UPGRADE (14)INTRODUCTIONFutronic MKll manager allows you to:-View all test results and save them to a PC-Compose custom-made DSC messages-Compose custom-made AIS messages-Perform test box settings that cannot all be done on the test box itself-Perform PC-controlled EPIRB testsand generate complete finished EPIRB Test Reports-Monitor NMEA messages to detect suspected errors on the NMEA 0183 version 2.-Determine the VHF channels to be tested for sensitivity-Upgrade your test box with new facilities purchased from DanphoneHow to download and install1) Download Futronic MKll manager from Danphones’ website:/futronic-gmdss-testers/futronic-mkii/2) Open the zipped file.3) Double click on the file Installation guide and follow the instructions.USB Cable4) Once installed, the PC program will open a 6-tabbed dialogue box on your PC screen: Test Results - DSC Composer - AIS Composer - Settings - EPIRB- NMEA –Sensitivity -UpgradeThe tabs are explained on the following pages.TEST RESULTSThe Test Results tab provides access to all the tests and test results stored in the test box. Tests are organized with a header in the Index window to the left, under which the individualtest results are displayed in the window at the right hand side.Headers are indexed in time order with the latest test on top.Please note: In order to view a test result, you must select its header first.Press Save to PC in order to save the test results on your PC and to bring them into your own test report format, if so wished.Press Update to update the Index list with new tests performed after you opened the PC program.Press Delete to delete a test from the Index list.Press Disconnect to disconnect the test box from your PC.DSC COMPOSERUnder the DSC Composer tab you can compose your own custom-made DSC messages and transfer them to the test box accordingly.Please refer to ITU-R M.493 for composing of DSC messages.The test box can contain one DSC message for VHF, TFC and MF/HF respectively.Custom-made DSC messages can also be saved on your PC for later use.AIS COMPOSERUnder the AIS Composer tab you can compose and save your own custom-made AIS messages.When transferred to the test box, the AIS message will be transmitted on both AIS channels, AIS1 and AIS2.SETTINGSThe Settings tab allows you to change the test box settings.Test box MMSI: Write and set new MMSI number for the test box here.Target MMSI: Write and set MMSI number of the device to be tested here.LCD backlight time out: Write and set backlight time out between 0 and 200 seconds here. LCD contrast: Write and set contrast between 0 and 100% here.OCXD time out: Write and set OCXO time out between 0 and 99 minutes here.Show raw DSC on LCD: Click here to have raw DSC data presented in the display along with clear text.Sync Test Box Time with PC: Click here to synchronize the current date and time in the test box with the date and time in your PC.EPIRB TEST REPORT GENERATORThe EPIRB tab offers two options:1. Generation of complete EPIRB test reports out of test results from the test box,2. PC-controlled EPIRB testing and simultaneous generation of test reports.1. Generating reports out of stored test resultsThis feature allows you to generate complete EPIRB test reports out of the test results stored in the test box.1) Select the EPIRB test from the list at the right hand side. If there is no list,go to the “Test results” ta b and select from the Index a header that contains the relevant EPIRB test. Then return to the “EPIRB” tab.2) Fill in the beacon information form in the EPIRB dialogue box at the left hand side.3) Press “Generate Report” to cr eate the EPIRB Test Report (HTML format).See example of an EPIRB Test report on the next page.During the installation of the Futronic MKll manager, a default report template has been placed in C:\EPIRB\ on your PC. Feel free to use this HTML document as the basis for creating your own layout or design, if so wished. Then, press “Get template” and select the new one from your file system instead of the default template.Please note: Default limits of the frequency tolerance and minimum signal level are +/- 5 kHz and 190 respectively. Other limits may be inserted in accordance with specifications. Should the limits be exceeded during test, the report will write “Failed” in the status line.Example of Test Report based on the default HTML design:2. PC-controlled EPIRB testsIn addition to generating test reports from EPIRB tests stored in the memory, the EPIRB tab also enables you to perform PC-controlled EPIRB tests generating test reports automatically. With this, the system will not transfer the test results to the test box, but still generate finished test reports that can be stored in your PC.1) Turn the test box on. No need to select EPIRB tests, your PC will take control.2) Deselect all tests from the header list at the right-hand side, if any.3) Select frequency in the EPIRB dialogue box at the left-hand sideand fill in the beacon information form.4) Press “Start PC-controlled Test” and then activate the EPIRB.5) Wait for the EPIRB Test Report to be automatically generated (HTML format).See example of an EPIRB Test report on the previous page.NATIONAL MARINE ELECTRONIC ASSOCIATION (NMEA)The NMEA tab enables monitoring of NMEA 0183 version 2 messages.This feature enables monitoring of NMEA supporting units by retrieving NMEA messages via the pilot plug. Connect the NMEA bus to the pilot plug on the Futronic test box and press “Get NME A”. The test box automatically transfer the requested messages to the PC. All messages can be saved as text files.Activate filter to restrain the messages to one type.VHF SENSITIVITY TESTThe Sensitivity tab enables determination of the VHF channels to be tested for sensitivity. Futronic MKll manager allows you to configure the Futronic test box on 6 selected VHF channels. Set the VHF channel between 01 – 28 or 60 – 88, 2006, 2019, 2020, 2024 – 2028, 2078, 2079, 2084, 2085 and press “Save”.The channel is hereby visible on the test box and ready for testing.Press ↑ and ↓ on the test box to choose between the predefined channels.UPGRADEThe Upgrade tab is for upgrading the Futronic test box model.If your test box is a GMDSS-only model and you have purchased the additional AIS test facility from Danphone, you will be given an access key to be entered, and the new facility will work immediately.。
天工iSpirit3528g交换机用户操作手册说明书

目录
第 1 章 CLI 命令行介绍 ................................................................................................................ 12 1.1 访问交换机的 CLI ................................................................................................................... 13 1.1.1 用户通过 Console 口访问 CLI ............................................................................................. 13 1.1.2 用户通过 TELNET 访问 CLI ............................................................................................... 14 1.2 CLI 模式介绍 ............................................................................................................................ 15 1.2.1 CLI 模式的作用 ..........................................................................................................
ElmerguiManual[1]
![ElmerguiManual[1]](https://img.taocdn.com/s3/m/c99b6c6aa45177232f60a2b1.png)
ElmerGUI manual v.0.3Mikko LylyAugust16,20111ContentsTable of Contents2 1Introduction4 2Installation from source52.1Linux (5)2.2Windows (6)3Inputfiles73.1Geometry inputfiles and mesh generation (7)3.2Elmer meshfiles (8)3.3Projectfiles (9)4Model definitions94.1Setup menu (9)4.2Equation menu (9)4.3Material menu (11)4.4Body force menu (12)4.5Initial condition menu (12)4.6Boundary condition menu (13)5Utility functions145.1Boundary division and unification (14)5.2Saving pictures (16)5.3View menu (16)6Solver inputfiles17 7Solution and post processing177.1Running the solver (17)7.2Post preocessing I(ElmerPost) (19)7.3Post preocessing II(VTK) (19)7.3.1Python interface (20)7.3.2Public methods (21)7.3.3Example scripts (26)7.3.4ECMAScript interface (28)A ElmerGUI initializationfile31B ElmerGUI material database332C ElmerGUI definitionfiles34D Elmer meshfiles37E Adding menu entries to ElmerGUI39F ElmerGUI mesh structure40F.1GLWidget (40)F.2mesh t (41)F.3node t (44)F.4Base element class element t (45)F.5Point element class point t (46)F.6Edge element class edge t (47)F.7Surface element class surface t (48)3CopyrightThis document is licensed under the Creative Commons Attribution-No Deriva-tive Works3.0License.To view a copy of this license,visit http://creativecommons. org/licenses/by-nd/3.0/.1IntroductionElmerGUI is a graphical user interface for the Elmer software suite[1].The program is capable of importingfinite element meshfiles in various formats, generatingfinite element partitionings for various geometry inputfiles,set-ting up PDE-systems to solve,and exporting model data and results for ElmerSolver and ElmerPost to visualize.ElmerGUI has also an internal postprocessor,which can be used as an alternative to ElmerPost,to drawcolor surfaces,contours,vectorfields,and visualize time dependent data.Figure1:Main window of ElmerGUI.One of the main features of ElmerGUI is the interface to the parallel solver,ElmerSolver mpi.The GUI hides from the user a number of opera-4tions that are normally performed from command line with various external tools related to domain decomposition,launching the parallel processes,and merging the results.This makes it possible to use ElmerSolver with multi-core processors,even on interactive desktop environments.The menus of ElmerGUI are programmable and it should be relatively easy to strip and customize the interface for proprietary applications.An example of customizing the menus is provided in appendix A.ElmerGUI relies on the Qt4cross platform framework of QtSoftware[6], and it uses the Qwt5libray by Josef Wilgen and Uwe Rathman[7]to plot scientific data.The internal postprocessor of ElmerGUI is based on the Vi-sualization Toolkit(VTK)of Ken Martin,Will Schroeder,and Bill Lorensen [10].The CAD import features are implemented by the OpenCASCADE (OCC)library from OpenCASCADE S.A.S.[5].The program is also capa-ble of using Tetgen[8]and Netgen[4]asfinite element mesh generators.2Installation from sourceThe source code of ElmerGUI is available from the subversion repository of .The GPL licenced source code may be downloaded by executing the following command with a SVN client program(on Windows the Tortoise SVN client is recommended):svn co https:///svnroot/elmerfem/trunk trunk This will retrieve the current development version of the whole Elmer-suite.2.1LinuxBofore starting to compile,please make sure that you have the development package of Qt4installed on your system(i.e.,libraries,headers,and program development tools).Qt version4.3or newer is recommended.You may also wish to install Qwt5,VTK version5(compiled with support to Qt4),and OpenCASCADE6.3,for additional functionality.The program is compiled and installed by executing the following se-quence of commands in a terminal window:$cd elmerfem/trunk/ElmerGUI$qmake$make$make install5The default installation directory defined in the projectfile ElmerGUI.pri is /usr/local/bin.It is possible that the project definitionfile“ElmerGUI.pri”needs to be edited and modified,depending on how and where the external libraries have been installed.The lines that need attention can be found from the beginning of thefile.Once the build process hasfinished,it suffices to set up the environment variable ELMERGUI HOME and add it to PATH:$export ELMERGUI_HOME=/usr/local/bin$export PATH=$PATH:$ELMERGUI_HOMEThe program is launhed by the command$ElmerGUILater,it is possible to update ElmerGUI by the following commands within the build directory:$svn update$make$make install2.2WindowsOn32-bit Windows systems,it is possible to use precompiled binary pack-ages,which are distributed through thefile release system of [2].The binary packages may depend on external components,which must be installed prior to downloading Elmer.The list of possible dependencies can be found from the“Release notes”of the package.It is also possible to compile ElmerGUI from source.This can be done either by Visual Studio2008C++Express Edition[9](or any other MS compiler that provides at least the same functionality),or by using the GNU Compiler Collection provided by the MinGW project[3].The compilation instructions for MinGW are more or less the same as for Linux.The only exception is that then OCC should probably be excluded from compilation.The advantage of using MinGW is that it is then possible to use Qt’s pre-compiled binary packages[6],which otherwise have to be built from source. MinGW might also be the natural choice for users that prefer Unix-like op-erating environments.The easiest way to compile ElmerGUI with VC++is to invoke“Visual Studio2008Command Prompt”and execute the following sequence com-mands within ElmerGUI’s source directory:6>qmake>nmake>nmake installAgain,it is necessary to verify that the search paths to all external com-ponents have been correctly defined in“ElmerGUI.pri”.The build process isperformed in release mode,producing the executable“Application/release/ElmerGUI.exe”.Thefinal task is to introduce the environment variable ELMERGUI HOMEwith value c:/Elmer5.4/bin and add it to the binary search path(right-clickMy Computer→Properties→Advanced→Environment variables)3Inputfiles3.1Geometry inputfiles and mesh generationElmerGUI is capable of importingfinite element meshfiles and generatingtwo or three dimensionalfinite element partitionings for bounded domainswith piecewise linear boundaries.It is possible to use one of the followingmesh generators:•ElmerGrid(built-in)•Tetgen(optional)•Netgen(built-in)The default importfilter and mesh generator is ElmerGrid.Tetgen is anoptional module,which may or may not be available depending on the instal-lation(installation and compilation instructions can be found from Elmer’ssource tree in trunk/misc)An importfilter or a mesh generator is selected automatically by Elmer-GUI when a geometry inputfile is opened:File→Open...The selection is based on the inputfile suffix according to Table1.Iftwo or more generators are capable of handing the same format,then theuser defined“preferred generator”will be used.The preferred generator isdefined inMesh→Configure...Once the inputfile has been opened,it is possible to modify the mesh parameters and remesh the geometry for better accuracy or computationalefficiency.The mesh parameters can be found from Mesh→Configure....7The control string for Tetgen has been discussed and explained in detail in Tetgen’s user guide[8].Suffix ElmerGrid Tetgen Netgen.FDNEUT yes no no.grd yes no no.msh yes no no.mphtxt yes no no.offno yes no.ply no yes no.poly no yes no.smesh no yes no.stl no yes yes.unv no yes no.in2d no no yesTable1.Inputfiles and capabilities of the mesh generators.The mesh generator is reactivated from the Mesh menu by choosingMesh→RemeshIn case of problems,the meshing thread may be terminated by executing Mesh→Terminate meshing3.2Elmer meshfilesAn Elmer mesh consists of the following four textfiles(detailed description of thefile format can be found from Appendix B):mesh.headermesh.nodesmesh.elementsmesh.boundaryElmer meshfiles may be loaded and/or saved by opening the mesh direc-tory from the File menu:File→Load mesh...and/orFile→Save as...83.3ProjectfilesAn ElmerGUI project consists of a project directory containing Elmer mesh files and an xml-formatted document egproject.xml describing the current state and settings.Projects may be loaded and/or saved from the File menu by choosingFile→Load project...and/orFile→Save project...When an ElmerGUI project is loaded,a new solver inputfile will be generated and saved in the project directory using the sif-name defined in Model→Setup...If there is an old solver inputfile with the same name,it will be overwritten.The contents of a typical project directory is the following:case.sifegproject.xmlELMERSOLVER_STARTINFOmesh.boundarymesh.elementsmesh.headermesh.nodes4Model definitions4.1Setup menuThe general setup menu can be found fromModel→Setup...This menu defines the basic variables for the“Header”,“Simulation”,and “Constants”blocks for a solver inputfile.The contents of these blocks have been discussed in detail in the SolverManual of Elmer[1].4.2Equation menuThefirst“dynamical menu”constructed from the ElmerGUI definitionfiles (see Appendix A)isModel→Equation9Figure2:Setup menu.This menu defines the PDE-system to be solved as well as the numerical methods and parameters used in the solution.It will be used to generate the “Solver”blocks in a solver inputfile.A PDE-system(a.k.a“Equation”)is defined by choosingModel→Equation→Add...Once the PDE-system has been defined by activating the individual equa-tions,the numerical methods and parameters can be selected and tuned by pressing the“Edit Solver Settings”button.The name the PDE-system is defined in the line edit box with label“Name”.After pressing the Ok-button, the equation remains visible and editable under the Model menu.It is also possible to attach an equation to a body by holding down the SHIFT-key while double clicking one of its surfaces.A pop up menu will then appear,listing all possible attributes that can be attached to the selection.10Figure3:Equation menu.4.3Material menuThe next menu is related to material and model parameters: Model→MaterialThis menu will be used to generate the“Material”blocks in a solver input file.In order to define a material parameter set and attach it to bodies,choose Model→Material→Add...Again,it is possible to attach the material to a body by holding down the SHIFT-key while double clicking one of its boundaries.Note:The value of density should always be defined in the“General”tab.Thisfield should never be left undefined.Note:If you set focus in a line edit box of a dynamical menu and press Enter,a small text edit dialog will pop up.This allows the input of more complicated expressions than just constants.As an example,go to Model→Material and choose Add...Place the cursor in the“Heat conductivity”line edit box of“Heat equation”and press Enter.You can then define the heat conductivity as a function of temperature as a piecewise linear function.An11Figure4:Solver settings menu.example is show in Figure N.In this case,the heat conductivity gets value 10if the temperature is less than273degrees.It then rises from10to20 between273and373degrees,and remains constant20above373degrees.If the user presses SHIFT and F1,a tooltip for the active widget will be displayed.4.4Body force menuThe next menu in the list isModel→Body forceThis menu is used to construct the“Body force”blocks in a solver inputfile.Again,chooseModel→Body force→Add...to define a set of body forces and attach it to the bodies.4.5Initial condition menuThe last menu related to body properties is12Figure5:Body property editor is activated by holding down the SHIFT key while double clicking a surface.Model→Initial conditionOnce again,chooseModel→Initial condition→Add...to define a set of initial conditions and attach it to the bodies.This menu is used to construct the“Initial condition”blocks in a solver inputfile.4.6Boundary condition menuFinally,there is a menu entry for setting up the boundary conditions: Model→Boundary conditionChooseModel→Boundary condition→Add...to define a set of boundary conditions and attach them to boundaries.13Figure6:Material menu.It is possible to attach a boundary condition to a boundary by holding down the ALT or ALTGR-key while double clicking a surface or edge.A pop up menu will appear,listing all possible conditions that can be attached to the selection.Choose a condition from the combo box andfinally press Ok. 5Utility functions5.1Boundary division and unificationSome of the inputfile formats listed in Table1are not perhaps so well suited for FE-calculations,eventhough widely used.The.stl format(stereo litog-raphy format),for example,is by definition unable to distinguish between different boundary parts with different attributes.Moreover,the format ap-proximates the boundary by disconnected triangles that do not fulfill the usual FE-compatibility conditions.In order to deal with formats like.stl,ElmerGUI provides a minimal set of tools for boundary division and unification.The division is based on “sharp edge detection”.An edge between two boundary elements is con-sidered sharp,if the angle between the normals exceeds a certain value(20 degrees by default).The sharp edges are then used as a mortar to divide the surface into parts.The user may perform a sharp edge detection and14Figure7:Tooltips are shown by holding down the SHIFT and F1keys.boundary division from the Mesh menu by choosingMesh→Divide surface...In2D the corresponding operation isMesh→Divide edge...The resulting parts are enumerated starting from thefirst free index.Sometimes,the above process produces far too many distinct parts,which eventually need to be(re)unified.This can be done by selecting a group of surfaces by holding down the CTRL-key while double clicking the surfaces and choosingMesh→Unify surface...The same operation in2D isMesh→Unify edge...The result will inherit the smallest index from the selected group.The sharp edges that do not belong to a closed loop may be removed by Mesh→Clean up15Figure8:Text edit extension of a line edit box is activated by pressing Enter.This operation has no effect on the boundary division,but sometimes it makes the result look better.5.2Saving picturesThe model drawn on the display area may be scanned into a24-bit RGB image and saved in several picturefile formats:File→Save picture as...The function supports.bmp,.jpg,.png,.pbm,.pgm,and.ppmfile extensions.5.3View menuThe View menu provides several utility functions for controlling the visual behaviour of ElmerGUI.The function names should be more or less self explanatory.16Figure9:Body force menu.6Solver inputfilesThe contents of the Model menu are passed to the solver in the form of a solver inputfile.A solver inputfile is generated by choosingSif→GenerateThe contents of thefile are editable:Sif→Edit...The new siffile needs to saved before it becomes active.The recom-mended method isFile→Save project...In this way,also the current mesh and projectfiles get saved in the same directory,avoiding possible inconsistencies later on.7Solution and post processing7.1Running the solverOnce the solver inputfile has been generated and the project has been saved, it is possible to actualy solve the problem:17Figure10:Initial condition menu.Run→Start solverThis will launch either a single process for ElmerSolver(scalar solution)or multiple MPI-processes for ElmerSolver mpi(parallel solution)depending on the definitions inRun→Parallel settings...The parallel menu has three group ually,the user is supposed to touch only the“General settings”group and select the number of processes to execute.The two remaining groups deal with system commands to launch MPI-processes and external tools for domain decomposition.The parallel menu is greyed out if ElmerSolver mpi is not present at start-up.When the solver is running,there is a log window and a convergence monitor from which the iteration may be followed.In case of divergence or other troubles,the solver may be terminated by choosingRun→Kill solverThe solver willfinally write a resultfile for ElmerPost in the project directory.The name of the ep-file is defined inModel→Setup...18Figure11:Boundary condition menu.7.2Post preocessing I(ElmerPost)ElmerGUI provides two different post processors for drawing,displaying,and manipulating the results.Thefirst alternative is activated fromRun→Start postprocessorThis will launch ElmerPost,which will read in the resultfile and displays a contour plot representing the solution.If the results were prodoced by the parallel solver,the domain decomposition used in the calculations will be shown.7.3Post preocessing II(VTK)The second post processor is based on the Visualization Toolkit,VTK.It is activated fromRun→Postprocessor(VTK)...A new window will then pop up,providing methods for drawing surfaces, contours,vectors,and stream lines.19Figure12:Boundary property editor activated by holding down the ALTGR key while double clicking a surface.7.3.1Python interfaceIf ElmerGUI has been compiled with PyhthonQt-support,there is a Python console available for scripting.The console is located under the Edit-menu: Edit→PythonQt console...The console provides access to the following classes:egp//ElmerGUI post processormatc//MATC language interpreterpreferences//controls for preferencessurfaces//controls for surface plotsvectors//controls for vector fieldsisoContours//controls for isocontoursisoSurfaces//controls for isosurfacesstreamLines//controls for streamlinescolorBar//cotrols for the colorbartimeStep//controls for transient resultstext//text annotationEach of the above classes provides a number of useful methods for data and display manipulation.Tofix ideas,suppose that we want to read in the resultfile“case.ep”and display the temperaturefields as a semi trans-20Figure13:Parallel settings dialog.parent surface plot.The commands to execute are then the following(more examples can be found in section7.3.3):py>egp.ReadPostFile("case.ep")py>egp.SetSurfaces(True)py>surfaces.SetFieldName("Temperature")py>surfaces.SetOpacity(50)py>egp.Redraw()7.3.2Public methodsInterface version0.2:class egp:bool MatcCmd(QString);//evaluate MATC cmdvoid domatcSlot();//flush MATC console void SetPostFileStart(int);//first time stepvoid SetPostFileEnd(int);//last time stepbool ReadPostFile(QString);//read result filevoid Render();//rendervoid ResetCamera();//reset cameravoid Redraw();//redraw actors21void ResetAll();//reset viewvoid SetSurfaces(bool);//show/hide surfaces void SetVectors(bool);//show/hide vectors void SetIsoContours(bool);//show/hide isocontours void SetIsoSurfaces(bool);//show/hide isosurfaces void SetStreamLines(bool);//show/hide streamlines void SetColorBar(bool);//show/hide colorbar void SetMeshPoints(bool);//show/hide/nodesvoid SetMeshEdges(bool);//show/hide edgesvoid SetFeatureEdges(bool);//show/hide f-edges void SetAxes(bool);//show/hide axesvoid SetText(bool);//show/hide textbool GetClipAll();//is clipping on?void SetClipAll(bool);//clipping on/offvoid SetClipPlaneOx(double);//clip plane origin void SetClipPlaneOy(double);//clip plane origin void SetClipPlaneOz(double);//clip plane origin void SetClipPlaneNx(double);//clip plane normal void SetClipPlaneNy(double);//clip plane normal void SetClipPlaneNz(double);//clip plane normal double GetCameraDistance();//get camera distance void SetCameraDistance(double);//set camera distance double GetCameraPositionX();//get camera position double GetCameraPositionY();//get camera position double GetCameraPositionZ();//get camera position void SetCameraPositionX(double);//set camera position void SetCameraPositionY(double);//set camera position void SetCameraPositionZ(double);//set camera position double GetCameraFocalPointX();//get focal point double GetCameraFocalPointY();//get focal point double GetCameraFocalPointZ();//get focal pointvoid SetCameraFocalPointX(double);//set focal pointvoid SetCameraFocalPointY(double);//set focal pointvoid SetCameraFocalPointZ(double);//set focal pointvoid CameraDolly(double);//dollyvoid CameraRoll(double);//rollvoid CameraAzimuth(double);//azimuthvoid CameraYaw(double);//yawvoid CameraElevation(double);//elevationvoid CameraPitch(double);//pitchvoid CameraZoom(double);//zoomvoid SetCameraRoll(double);//set rollvoid SetInitialCameraPosition();//set initial position void RotateX(double);//rotate visible actors void RotateY(double);//rotate visible actors22void RotateZ(double);//rotate visible actors void SetOrientation(double,double,double);//set orientationvoid SetPositionX(double);//set positionvoid SetPositionY(double);//set positionvoid SetPositionZ(double);//set positionvoid SetPosition(double,double,double);//set positionvoid AddPosition(double,double,double);//add positionvoid SetOrigin(double,double,double);//set originvoid SetScaleX(double);//set scalevoid SetScaleY(double);//set scalevoid SetScaleZ(double);//set scalevoid SetScale(double,double,double);//set scaledouble GetLength();//get model sizedouble GetNofNodes();//get nof nodesdouble GetMinX();//bounding boxdouble GetMaxX();//bounding boxdouble GetMinY();//bounding boxdouble GetMaxY();//bounding boxdouble GetMinZ();//bounding boxdouble GetMaxZ();//bounding boxbool SavePngFile(QString);//save image filevoid SetBgColor(double,double,double);//bg color(RGB:0..1) class matc:bool SetCommand(QString);//Enter MATC cmdclass preferences:void UseSurfaceMeshForPoints(bool);//nodes of surface mesh void UseVolumeMeshForPoints(bool);//nodes of volume mesh void SetPointSize(int);//set node point size void SetPointQuality(int);//set node point quality void UseClipPlaneForPoints(bool);//clip nodesvoid UseSurfaceMeshForEdges(bool);//edges of surface mesh void UseVolumeMeshForEdges(bool);//edges of volume mesh void UseTubeFilterForEdges(bool);//use tube filtervoid UseClipPlaneForEdges(bool);//clip edgesvoid SetLineWidthForEdges(int);//edge line widthvoid SetTubeQualityForEdges(int);//edge tube qualityvoid SetTubeRadiusForEdges(int);//edge tube radiusvoid UseSurfaceMeshForFeatureEdges(bool);//surface mesh:f-edges void UseVolumeMeshForFeatureEdges(bool);//volume mesh:f-edges void UseTubeFilterForFeatureEdges(bool);//use tube filtervoid UseClipPlaneForFeatureEdges(bool);//clip f-edgesvoid DrawBoundaryEdges(bool);//draw boundary edgesint GetFeatureAngle();//get feature anglevoid SetFeatureAngle(int);//set feature anglevoid SetLineWidthForFeatureEdges(int);//f-edge line width23void SetTubeQualityForFeatureEdges(int);//f-edge tube quality void SetTubeRadiusForFeatureEdges(int);//f-edge tube radius void SetClipPlaneOx(double);//clip plane origin void SetClipPlaneOy(double);//clip plane origin void SetClipPlaneOz(double);//clip plane origin void SetClipPlaneNx(double);//clip plane normal void SetClipPlaneNy(double);//clip plane normal void SetClipPlaneNz(double);//clip plane normal class surfaces:QString GetFieldName();//get field namebool SetFieldName(QString);//set field namevoid SetMinVal(double);//set minimumvoid SetMaxVal(double);//set maximumvoid KeepLimits(bool);//keep limitsvoid SetComputeNormals(bool);//shade modelvoid SetFeatureAngle(int);//feature anglevoid SetOpacity(int);//set opacityvoid SetClipPlane(bool);//set clippingclass vectors:QString GetFieldName();//get field namebool SetFieldName(QString);//set field namevoid SetMinVal(double);//set minimumvoid SetMaxVal(double);//set maximumvoid KeepLimits(bool);//keep limitsvoid SetComputeNormals(bool);//shade modelvoid SetFeatureAngle(int);//feature anglevoid SetOpacity(int);//set opacityvoid SetClipPlane(bool);//set clippingclass isoContours:QString GetFieldName();//get field name QString GetColorName();//get color namebool SetFieldName(QString);//set field namebool SetColorName(QString);//set color namevoid SetMinFieldVal(double);//set min valuevoid SetMaxFieldVal(double);//set max valuevoid SetContours(int);//set nof contours void KeepFieldLimits(bool);//keep limitsvoid SetMinColorVal(double);//set color minvoid SetMaxColorVal(double);//set color maxvoid KeepColorLimits(bool);//keep color limits void UseTubeFilter(bool);//use tube filter void UseClipPlane(bool);//set clipping on/off void SetLineWidth(int);//set line widthvoid SetTubeQuality(int);//set tube quality void SetTubeRadius(int);//set tube radius24class isoSurfaces:QString GetFieldName();//get field name QString GetColorName();//get color namebool SetFieldName(QString);//set field namebool SetColorName(QString);//set color namevoid SetMinFieldVal(double);//set min valuevoid SetMaxFieldVal(double);//set max valuevoid SetContours(int);//nof contoursvoid KeepFieldLimits(bool);//keep limitsvoid SetMinColorVal(double);//set color minvoid SetMaxColorVal(double);//set color maxvoid KeepColorLimits(bool);//keep color limits void ComputeNormals(bool);//shade modelvoid UseClipPlane(bool);//set clpping on/off void SetFeatureAngle(int);//set feature angle void SetOpacity(int);//set opacityclass streamLines:QString GetFieldName();//get field name QString GetColorName();//get color namebool SetFieldName(QString);//set field namebool SetColorName(QString);//set color namevoid SetMaxTime(double);//max timevoid SetStepLength(double);//step lengthvoid SetThreads(int);//nof threadsvoid SetIntegStepLength(double);//integ.step length void UseSurfaceMesh(bool);//use forface mesh void UseVolumeMesh(bool);//use volume mesh void IntegrateForwards(bool);//integrate forwards void IntegrateBackwards(bool);//integrate backwards void SetMinColorVal(double);//color min valvoid SetMaxColorVal(double);//color max value void KeepColorLimits(bool);//keep color limits void DrawLines(bool);//draw using lines void DrawRibbons(bool);//draw using ribbons void SetLineWidth(int);//line widthvoid SetRibbonWidth(int);//ribbon widthvoid UseSphereSource(bool);//use sphere source void UseLineSource(bool);//use line source void UsePointSource(bool);//use point source void SetSphereSourceX(double);//sphere originvoid SetSphereSourceY(double);//sphere originvoid SetSphereSourceZ(double);//sphere originvoid SetSphereSourceRadius(double);//sphere radiusvoid SetSphereSourcePoints(int);//nof pts in sphere void SetLineSourceStartX(double);//line start point void SetLineSourceStartY(double);//line start point void SetLineSourceStartZ(double);//line start point void SetLineSourceEndX(double);//line end point25。
锈德-尼克尼 Custom Tools 目录说明书

Lyndex-Nikken AngleHeads are designedto easily and effectively upgrade yourmachine tool capabilities. RiteAngleHeads,FixedAngleHeads, FlexHeads, SlimRiteAngleHeads and Twin SpindleAngleHeads expand the capabilitiesof your existing machines.A NGLE H EADS™HiSpinners increase your toolingRPMs by up to 10 times (up to40,000 RPM), enabling you to reduceyour cycle times and per-piece costswith your current machines. Minimizespindle wear by letting the tool dothe work.H I S PINNERS™Lyndex-Nikken FluidHeads delivercoolant to the point of contact. Heatgenerated from cutting is eliminatedso there is no warping, while cuttingtool life is increased and tool breakageis reduced. FluidHeads also providelubrication and promote superior chipbreakage and chip evacuation.F LUID H EADS ™AngleHeads ™Technical Characteristics and Features ..........................4 - 5Nikken Heavy-Duty RiteAngleHeads ™........................................................6Standard RiteAngleHeads ™..........................................................................7Offset Type and Coolant-Through Offset Type RiteAngleHeads ™............8Economy 40 Taper RiteAngleHeads ™..........................................................9Slim Type RiteAngleHeads ™........................................................................10Twin Spindle AngleHeads ™........................................................................11Universal FlexHeads ™- Internal Coolant ..................................................12Quick Change AngleHeads ™..............................................................13 - 14AngleHeads ™Specials ................................................................................15AngleHeads ™Positioning Blocks . (16)A NGLE H EADS ™S PEED INCREASERS HiSpinner ™ Technical Characteristics and Features ..................................17Nikken Standard HiSpinner ™ . (18)™ (19)Nikken FluidHeads ™Features, Technical Characteristicsand Stopper Blocks ............................................................................20 - 21Nikken Side Lock FluidHeads ™ (22)Nikken SK FluidHeads ™ (23)Nikken Ultra Lock FluidHeads ™ (24)AngleHeads ™ER Collets (Inch, Metric, Coolant)................................25 - 28AngleHeads ™,HiSpinners ™and FluidHeads ™SK Collets ....................29 - 30KM, ETS and CCK Collets (Inch, Metric, Coolant)............................31 - 32F LUID H EADS ™C OLLETSA NGLE H EADS™Technical Characteristics and FeaturesOur AngleHeads are equipped with hardenedand ground gears and collet shafts. Units arealso fitted with high-precision angular contactbearings, assuring extreme rigidity and accuracy.Compact designs maintain accurate spindle andtool centerline alignment while minimizing tooloverhang - accuracy is maintained throughoutthe machining process from plane to plane.Vernier scales help to orient the cutting tool location(0 - 360°).Vernier Scales and Positioning RingsThe positioning pin and ring can also be oriented(0– 360°) to match your machining center’s spindleand automatic tool changer configuration by simplyadjusting the positioning ring.Their design allowsthem to be used in most ATCs and machine toolmagazines without interference.Locking Pin / Stopper PinCombined with our new Collet Seat, featuring grooves and ridges for tightening, the absence of the external nut creates better rigidity and a smaller profile.Collet Nut Our new Collet Seats provide stable and secure gripping force by having the collet sit totally insertedwithin the body of the AngleHead.Collet Seats The proper wrenches are included with the purchaseof your AngleHead.WrenchesA NGLE H EADS™Technical Characteristics and Features•High-precision spindle bearing, P4 quality•Stabilized spindle bearing•Bevel gear sets with helical toothing•Permanent lubrication•AngleHead can be rotated through 360°and is infinitely variable•4 x fixed 90°positioning points/ indexations•High speeds up to 15,000 rpm and high torques up to 150 NmNIKKEN HEAVY DUTY R ITE A NGLE H EADS ™•Specially designed for heavy milling•Heavy endmilling and drilling capability•Ideal for smooth ball endmilling of dies and molds•90º angular head•Multilock milling chuck nose ensures excellent rigidityand accuracy•Gear ratio: 1:1•Wrenches are includedFeaturesOffset style pictured* Positioning block (PB-RAN) not included. Please refer to page 16.** SK Collets available on pages 29-30.*** KM Collets available on page 31.ITE NGLE EADS ™ITE NGLE EADS ™(non-coolant)Coolant-ThroughITE NGLE EADSITE NGLE EADS™NGLE EADS ™* Positioning block not included. Please refer to page 16.** ER Collets available on pages 25-28.LEX EADS ™* Positioning block not included. Please refer to page 16.** Universal FlexHeads must only be used with coolant through the spindle - no dry running.*** ER Collets available on pages 25-28.NGLE EADS ™* Positioning block not included. Please refer to page 16.Collet Series - MI50 (70 Nm Torque, 6,500 RPM) C40RAM-MI50-180 CAT4017.5 180 B40RAM-MI50-187 BT40 17.5 187 C50RAM-MI50-180 CAT5026.5 180Pa r t N umbe r T ape rWeight(lbs.)L L1QUICK CHANGE A NGLE H EADS™MODULAR TOOLHOLDERS IN DIFFERENT SIZES FOR ALL PRODUCTION AREAS :•T apping toolholders•Collet toolholders (internal and external nut)•Hydro-Flex hydraulic toolholders •Thread tightening toolholder cutters •Morse taper shank toolholders•Weldon and Whistle Notch toolholders •Shell mill toolholdersFixedAngleHeads ™The specially designed case of the FixedAngleHead ensures an accuratecutting angle without the need to adjust or verify cutting angle.Multi-Spindle DrillHeads ™Special AngleHeads ™A NGLE H EADS™SpecialsApplicationsThe multi-axis positioning of the FlexHead allows total rotational and compound angle settings. Perform multiple, complexoperations without costly additional work setups or fixtures.Minimized body design is suitable for machining in tight spaces.High technology toolholders that perform beyond the main spindle's rotational characteristics, and toolholders that induce a side flow of coolant through cutting tools,require a positioning pin to operate.This pin, which is seated into a positioning block after changing, locks the toolholder's body into a stationary position relative to the spindle face. With its body properly aligned and secured, the toolholder's internal mechanisms are ready to perform their designed operations.Before using any of our stationary body tools, apositioning block must first be attached to the machiningcenter's spindle face. The block is attached to the face by utilizing the existing drilled/tapped holes on the face. Place the positioning block in a location which will assure that the positioning pin, when seated in the positioning block, will not interfere with the movements of your ATC arm or any other attachments.All Lyndex-Nikken tools have features that allow them to be easily oriented with any position of your spindle's drive keys.A positioning block may require slight modificationsto accommodate your particular machine.A NGLE H EADS™ Positioning BlocksFor use with AngleHeads on pages 7, 8, 10-13 .SpecialsCustom stopper blocks available, including combination blocks as shown, upon special request.For use with AngleHeads on page 6.Lyndex-Nikken HiSpinners offer substantial increases in spindle speeds for high speed milling applications.Our HiSpinners allow for reduced cycle times and lower per-piece costs by utilizing new high efficiency cutting tools. Cutting tool performance, in turn, is enhanced through the carried RPMs and rigidity of our HiSpinners.Excellent accuracy, ridigity and durability are achieved through the use of our integral shank spindle, tempered and ground gears, and high precision pre-loaded spindle bearings.•For use with all kinds of materials (HiSpinners do not require messy coolants) and applications, including drilling, milling, and grinding •Lightweight and easy to use •Capable of working in most ATCs •Accuracy of .01 mm or better•Some models available with coolant-throughDecrease Costs and Increase SpeedHiSpinners increase your tooling RPMs up to 10 times faster (up to 40,000 RPM), enabling you to reduce your cycle times and per-piece costs with your current machines. Minimize spindle wear, letting the tool do the work.Achieve Higher Speeds Without HeatHiSpinners maintain a comfortable operating tem-perature without the need of forced air or coolants.Highly AccurateA main spindle supported at four points by high precision (P4 grade) bearings, ensure smooth, precise rotation and increased surface finish quality.DurableHiSpinner bearings and gear chamber are isolated from contamination by specially designed seals.Positioning PinsHigh technology toolholders that perform beyond the main spindle's rotational characteristics, and toolholders that induce a side flow of coolant through cutting tools, require a positioning pin to operate. This pin, which is seated into a positioning block after changing, locks the toolholder's body into a stationary position relative to the spindle face. With its body properly aligned and secured, the toolholder's internal mechanisms are ready to perform their designed operations.A positioning block may require slight modificationsto accommodate your particular machine.H I S PINNER ™Technical Characteristics and FeaturesNIKKEN STANDARD H I S PINNER ™•Ideal for drilling, gun-drilling and milling operations •Maximum speed: 20,000 RPM •Gear ratio: 5:1•Stable runout accuracy due to TiN bearing nut •NMTB units are available upon request •Wrenches are includedFeaturesPositioning Block* Positioning block is included.** SK10 Collets available on page 29.ADVANCED H I S PINNER ™Nikken F LUID H EADS ™FeaturesProlonged Tool LifeCutting tool life is increased by coolant being directly applied to the cutting edge. Direct coolant prevents brazed tool breakage by reducing the heat factor.Improved HolemakingLyndex FluidHeads facilitate hole drilling by delivering coolant to the point of contact. The drilling-associated heat factor is eliminated, so there is no heat-related warping. In addition, chips are immediately evacuated to prevent chips from annealing to the cutting tool and the workpiece wall.Greater Feeds and SpeedsDirect coolant applied to the tool's cutting edge provides lubrication, promotes superior chip breakage and evacuation, and prevents double-cutting of chips.These factors allow for greater feeds and speeds,increasing productivity.Advanced Multi-Seal ConstructionLyndex FluidHeads unique multi-seal construction incorporates a series of O-rings, labyrinth and synthetic seals, and sealed high-speed roller bearings to provide precise trouble-free operation. They also feature our tough corrosion-resistant surface treatment to assure a long life.Quick and Simple SetupLyndex provides you with a vernier scale for ease of orientation. Vernier scales help to orient the positioning pin and drive key slots (0-360°) to match your machining center’s spindle and automatic tool changer configuration. The adjustable positioning pin will also allow you to easily adjust the height to eliminate most variances in distance between the spindle’s face and positioning pin.Special orders are available upon request.One-Touch Internal/External Coolant Feed ConversionStopper BlockNikken F LUID H EADS ™Technical Characteristics and Stopper BlocksLUID EADS ™LUID EADS™* SK Collets available on pages 29-30.** Positioning block not included. Please refer to page 21.LUID EADS ™* CCK Collets available on page 32.** Positioning block not included. Please refer to page 21.SK10 COLLETS (metric)SK10 COLLETS(inch)SK16 COLLETS (inch)SK16 COLLETS (metric)KM 3/4 METRIC COLLETSKM 1-1/4 INCH COLLETSETS 14 INCH COLLETSETS 14 METRIC COLLETSKM 3/4 INCH COLLETSCoolant-Thru NutCKFN3/4-1/8C 3/4 INCH COOLANT THRU ACCESSORIES1.1/4 INCH COOLANT THRU ACCESSORIESCNC ROTARY TABLE SERIESC U S T O M T O O L S C ATA L O G • 800-543-6237CAT2008-CUS。
X-ray FGUI 3.4 中文操作手册
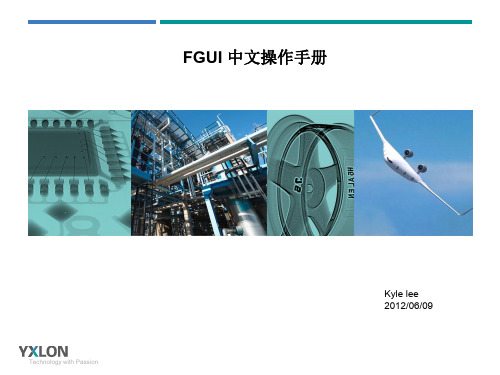
动态设置0%
Technology with Passion
FGUI 中文操作手册
Sharpening 推荐设置如图
强化程度,一般设置为7
Technology with Passion
FGUI 中文操作手册
FGUI软件操作 – 如何建立一个标准的IP
层次感增强:增强画面,使得画面层次感凸显。
Technology with Passion
FGUI 中文操作手册
FGUI软件操作 – 如何建立一个标准的IP
5um钨层
Technology with Passion
FGUI 中文操作手册
机器硬件结构的介绍
单焦点管与多焦点管 在不同焦点模式下的对应的 使用靶功率
靶材
标准靶
靶功率额度
10W
焦点模式
Nano focus Miciro focus High power Nano focus
焦点尺寸
1 um 2 um 6 um 1 um 2 um 6 um
Gamma 推荐设置如图
>1,画面变更亮 <1,画面变更暗
Technology with Passion
FGUI 中文操作手册
FGUI软件操作 – 如何建立一个标准的IP
锐化:自动调节画面黑白间隙的边缘,使得画面效果更佳。
Technology with Passion
FGUI 中文操作手册
FGUI软件操作 – 如何建立一个标准的IP
靶电流:到靶电子总数
提问:什么是靶功率?
Technology with Passion
FGUI 中文操作手册
机器硬件结构的介绍
靶材结构
高功率靶:承受上限15w,散 热层材料为金刚石薄膜。 普通靶:承受上限10w,散 热层材料为铝层。 散热层:单位面积散热能力
多功能工作台所有者手册说明书

MULTI-PURPOSE WORKBENCHStock Number W54025FOR YOUR SAFETY,please read these instructions carefully and retain them for future use.41 Workbench Tops2 2 Slide Bases 23 Bolts (Hex)4 4 Crossbars 25 Leg Frames 26 Plastic Feet 47 Washers8 8 Wood Screws 16 9 Bolts(phillips M6 x P1.0 x 37mm)8 10 Nuts (M6 x P1.0) 8 11 Nuts (M8 x P1.2) 4 12 Bench Dogs 413Washers8# DescriptionQtyLIMITED WARRANTYPERFORMANCE TOOL® extends only the following warranties, and only to original retail purchasers. These warranties give specific legal rights. Except where prohibited by local law, the law of the State of Washington governs all warranties and all exclusions and limitations of warranties and remedies. There may be other rights which vary from state to state.PERFORMANCE TOOL® warrants the product to be free from defects in materials and workmanship under normal use and service. A defective product may be returned for a free replacement within 90 days from the date of purchase, provided that product is returned to place of purchase immediately after discovery of defect. After 90 days and up to one year from date of purchase, PERFORMANCE TOOL® will replace at no charge any parts which our examination shall disclose to be defective and under warranty. These warranties shall be valid only when a sales receipt showing the date of purchase accompanies the defective product or defective part (s) being returned. For part (s) after 90 days, please remit your request, postage prepaid to:PERFORMANCE TOOL, P .O. Box 88259 Tukwila, WA 98138These warranties exclude blades, bits, punches, dies, bulbs, fuses, hoses, and other consumables which must be replaced under normal use and service. These warranties shall not apply to any product or part which is used for a purpose for which it is not designed, or which has been repaired or altered in any way so as to affect adversely itsperformance or reliability, nor shall these warranties apply to any product or part which has been subject to misuse, neglect, accident or wear and tear incident to normal use and service.PERFORMANCE TOOL® does not authorize any other person to make any warranty or to assume any liability in connection with its products.Except for warranties of title and the limited express warranties set forth above, PERFORMANCE TOOL® makes no express or implied warranties of any kind with respect to its products. In particular, PERFORMANCE TOOL® makes no implied warranty of merchantability and no implied warranty of fitness for any particular purpose, except that for goods purchased primarily for personal, family or household use and not for commercial or business use, PERFORMANCE TOOL® makes an implied warranty of merchantability (and, if otherwise applicable, an implied warranty of fitness for a particular purpose), but only for the particular qualities or characteristics, and for the duration, expressly warranted above.The laws on limitation of implied warranties may differ from state to state, so the above limitations may not apply in all cases.PERFORMANCE TOOL® shall not be liable for consequential, incidental or special damages resulting from or in any manner related to any product, or to the design, use, or any inability to use the product. The sole and exclusive remedy for a defective product or part shall be the repair, or replacement thereof as provided above. The laws on limitation of remedies or on consequential, incidental or special damages may vary from state to state, so the above limitations may not apply in all cases.© Copyright 2008 WILMAR CORPORATION, P.O. Box 88259 Tukwila, WA 98138。
巨控GRM WebGUI 使用说明书
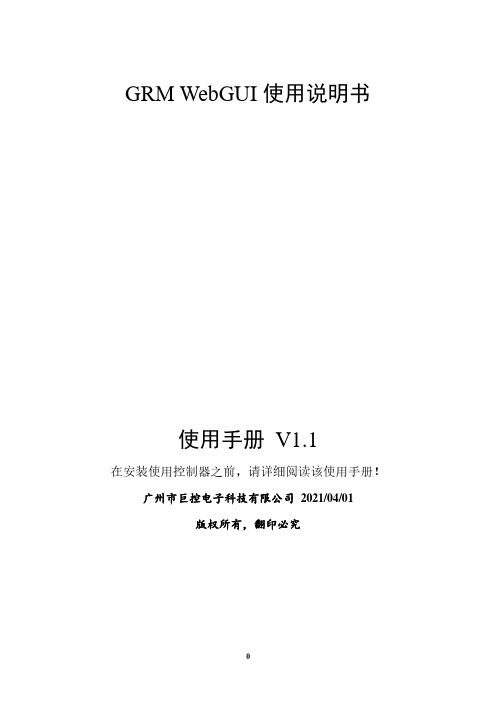
GRM WebGUI使用说明书使用手册V1.1在安装使用控制器之前,请详细阅读该使用手册!广州市巨控电子科技有限公司2021/04/01版权所有,翻印必究目录GRM WebGUI使用说明书 0一. 软件安装 (3)1 安装系统要求 (3)2 安装步骤 (3)二. GRM WebGUI 软件使用指南 (5)1 单设备.新建工程 (5)1.1 新建工程 (5)1.2 设备编辑 (6)1.3 新建画面 (8)1.4 变量绑定 (8)1.5 工程编译-压缩打包上传 (9)1.6 使用手机APP运行工程 (9)2 多设备切换.新建工程 (11)2.1 新建工程 (11)2.2 设备编辑 (12)2.3 新建画面 (15)2.4 变量绑定,设备切换,和当前设备显示 (15)2.5 工程编译-压缩打包上传 (17)2.6 模拟运行效果 (17)2.7 使用手机APP运行工程 (18)3 权限和密码管理 (20)3.1 WebGUI添加模块时使用的密码(对应模块变量权限) (20)3.2 WebGUI主账号密码管理(对应画面元件权限) (21)3.3 WebGUI子账号密码管理(元件权限) (21)3.4 元件输入操作密码 (22)4 萤石云在WebGUI上的应用 (23)4.1 GRM530模块配置LAN口 (23)4.2 查看直播ID,显示监控画面 (25)4.3 萤石云常见问题解答 (28)三. GUI设备组的介绍和使用 (32)1设备组管理 (32)1.1 基本信息 (32)1.2 密码和权限 (33)1.3 设备管理 (33)1.4 链接对象 (34)1.5 多设备变量表 (36)1.6 子账号管理 (37)1.7 GUI管理 (39)2数据交换管理与数据交换查看 (41)四. WebGUI常见问题解答 (42)1 基础操作及数据显示 (42)2 工程运行及子账户 (44)3 历史数据控件及报警控件 (45)4 其他疑问及报错 (48)一.软件安装1 安装系统要求处理器:Pentium Ⅳ1 G 以上内存:最少512MB 以上硬盘:剩余空间1G 以上显示器:VGA、SVGA 或支持桌面操作系统的任何图形适配器操作系统:Win 7/Win 102 安装步骤◆启动计算机系统。
Feynman MiniGUI 说明书
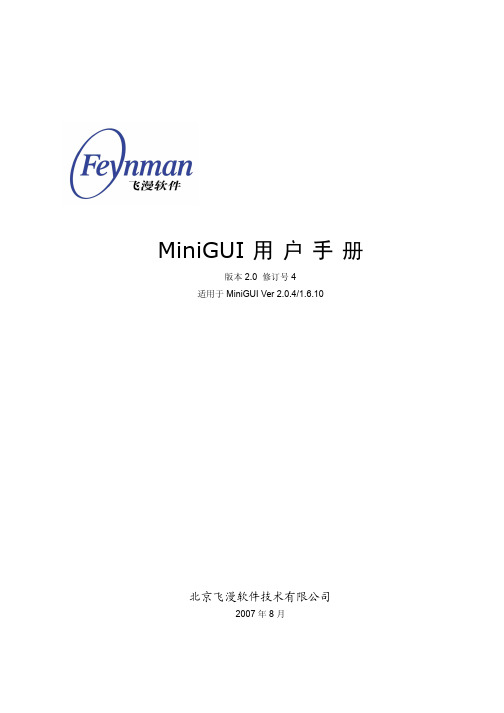
MiniGUI 用户手册版本 2.0 修订号 4适用于 MiniGUI Ver 2.0.4/1.6.10北京飞漫软件技术有限公司2007 年8 月MiniGUI 用户手册V2.0-4版权声明《MiniGUI 用户手册》版本 2.0 修订号 4,适用于MiniGUI 版本 2.0.4/1.6.10。
版权所有 (C) 2003~2007,北京飞漫软件技术有限公司,保留所有权利。
无论您以何种方式获得该手册的全部或部分文字或图片资料,无论是普通印刷品还是电子文档,北京飞漫软件技术有限公司仅仅授权您阅读的权利,任何形式的格式转换、再次发布、传播以及复制其内容的全部或部分,或将其中的文字和图片未经书面许可而用于商业目的,均被视为侵权行为,并可能导致严重的民事或刑事处罚。
I目 录版权声明 (I)1 MiniGUI 增值版介绍 (1)1.1 MiniGUI 增值版简介 (1)1.2 MiniGUI 增值版产品文档 (2)1.3 MiniGUI 源代码以及示例程序 (2)1.4 产品光盘中的其他资源 (3)1.5 可选组件产品 (4)1.6 关于本手册 (5)2 MiniGUI 的配置、编译和安装 (7)2.1 编译时配置选项的生成 (7)2.1.1 在 GNU 开发环境中使用 configure 脚本进行配置 (8)2.1.2 非 GNU 环境下的配置 (14)2.2 MiniGUI 的编译时配置选项详解 (15)2.2.1 操作系统相关的选项和宏 (15)2.2.2 目标板相关的选项和宏 (16)2.2.3 运行模式相关的选项和宏 (17)2.2.4 图形引擎相关的选项和宏 (17)2.2.5 输入引擎相关的选项和宏 (19)2.2.6 键盘布局的相关选项和宏 (21)2.2.7 系统全局配置选项和宏 (22)2.2.8 输入法相关的选项和宏 (23)2.2.9 字符集和字体相关的选项和宏 (23)2.2.10 图像文件格式相关的选项和宏 (27)2.2.11外观风格相关的选项和宏 (27)2.2.12 控件相关的选项和宏 (28)2.2.13 其他选项和宏 (28)2.3 最小配置选项 (29)2.3.1 使用 GNU configure 脚本 (29)2.3.2 对应的 mgconfig.h (31)2.4 MiniGUI 的编译和安装 (42)2.4.1 GNU 开发环境中的编译和安装 (42)2.4.2 在非 GNU 开发环境中使用 cygwin 工具编译和安装 MiniGUI (42)II3 MiniGUI 的运行时配置选项 (46)3.1 配置文件 (46)3.1.1 system 段 (47)3.1.2 fbcon 段 (47)3.1.3 qvfb 段 (48)3.1.4 rawbitmapfonts 、varbitmapfonts 、qpf 、truetypefonts 和type1fonts 段 (48)3.1.5 systemfont 段 (50)3.1.6 mouse 段 (51)3.1.7 event 段 (52)3.1.8 cursorinfo 段 (52)3.1.9 iconinfo 段 (53)3.1.10 bitmapinfo 段 (53)3.1.11 bgpicture 段 (54)3.1.12 mainwinmetrics 段 (55)3.1.13 windowelementcolors 段 (56)3.1.14 imeinfo 段 (58)3.1.15 默认配置文件 (59)3.2 内建式配置选项 (63)3.2.1 ETCSETCTION 结构 (63)3.2.2 ETC_S 结构 (64)3.2.3 mgetc.c 文件清单 (65)3.3 配置示例 (68)3.3.1 只支持 ISO8859-1 字符显示的运行时配置 (68)3.3.2 指定不同的图形引擎和输入引擎 (69)4 在 Windows 平台上开发 MiniGUI 应用程序 (70)附录 A 常见问题及解答 (72)A.1 GPL 版本问题 (72)A.2 应用问题 (72)A.3 移植性问题 (73)A.4 编译问题 (73)A.5 输入引擎 (74)A.6 运行时问题 (75)A.7 常见错误信息 (76)附录 B 索引 (78)11 MiniGUI 增值版介绍1.1 MiniGUI 增值版简介MiniGUI ( )是根据嵌入式系统应用特点量身定做的图形支持系统。
Darkglass Microtubes B7K Ultra V2 用户手册说明书

Darkglass SuiteDownload the free Darkglass Suite software from /suite to configure the pedal, load new impulses and download firmware updates.Darkglass Suite comes with a selection of cabinet IRs made by some of our artists. It also allows you to load your own IRs in WAV and AIFF formats and organize your IR files. See the online manual of Darkglass Suite for more information. DisclaimerIn the interest of continuous improvement, specifications are subject to change without notice. If you have any questions, please don’t hesitate to contact us at The manufacturer claims that the above product fulfills the requirements as set by EN55013, EN55020, EN60555-2, EN60555-3, RoHS, WEEE.Microtubes B7K Ultra v2Absolute Control.The new version of the Microtubes B7K Ultra features all the versatility and sonic possibilities of the first version plus: (1) Single user loadable cabinet simulation impulse response. (2) Micro-USB B port to connect to PC/Mac to load a different Virtual Cabinet through the Darkglass Suite. (3) 3.5mm headphone output with cabinet simulation. (4) Balanced XLR output with switchable cabinet simulation.WarningThe Microtubes B7K Ultra v2 has a current draw of 30mA. Only use a regulated 9V DC adapter with a center-negative plug. Due to ecological reasons it does not accept batteries. Unregulated power supplies and/or higher voltages may result in suboptimal noise performance and even damage your unit, voiding the warranty.WarrantyTo activate the warranty, we encourage you to register your product on: and enter the serial number on the back of your pedal.ControlsMaster: Whereas the Level K nob controls the output of the overdrive section the Master volume adjusts the overall volume of the unit. Ideal for fine tuning the output on clean mode. It also serves as a DI level control.Blend: Mixes the clean and processed signals. The clean signal remains at unity gain while the volume of the overdriven signal is set by the Level knob, allowing for fine mix tuning.Level: Sets the volume of the overdriven signal.Drive: Sets the amount of gain in the overdriven signal. Attack Switch: Sets the amount of treble content to saturate: The "Boost" setting emphasizes the treble content extra clarity and presence. The "Flat" position leaves this register untouched while the "Cut" position will reduce the amount of high frequencies being saturated.Grunt Switch: Sets the amount of low frequency content to saturate by selecting between three different bass boost levels before the clipping stage.Bass: +-12dB @ 100Hz | Lo Mids: +-12dB switchable 250Hz, 500Hz and 1kHz | Hi Mids: +-12dB switchable 750Hz, 1.5KHz and 3kHz | Treble: +-12dB @ 5kHz.Direct Output: A balanced version of the ¼” output, useful for running into PA’s or studio mixing consoles.Direct Ouput: Balanced XLR output for connecting the pedal to a microphone preamp, PA system etc.Ground lif t: Disconnects the signal ground on the Direct Output to break any ground loops. Set this switch to either position that has less noise. The switch does not affect the ¼” output.Cab Sim: Toggle the cabinet simulation on/off on the Direct Output. This switch completely bypasses all digital circuits and allows you to get a zero latency signal when needed. Headphones: B7K Ultra has an internal stereo headphone amplifier capable of driving a minimum load of 16 ohms from the 3.5mm stereo jack. Use the Master volume control to adjust the level.WARNING: When the pedal is on bypass the master volume does not affect the headphone volume. In this case the total volume is adjustable in Darkglass Suite. With sensitive headphones the bypass volume can be very loud if not adjusted.USB: A Micro USB B connector allows you to connect the pedal to PC/Mac to load cabinet simulation impulse responses to the pedal and control various other settings.Technical SpecificationsSingle user loadable cabinet simulation impulse response · 48 kHz, 16 bit internal processing· 1.6 ms latency· 88dB signal to noise ratioMicro-USB B port to connect to PC/Mac to load cabinet simulation IR3.5mm headphone output with cabinet simulation:· 16 ohm minimum load,· 50mW output power at 16 ohms,· 30mW output power at 32 ohmsBalanced XLR output with switchable cabinet simulation and switchable ground liftInput impedance: 1M ohmOutput impedance: 1k ohmPower supply: 9V DC center negativeDC current consumption 110 mADimensionsWidth 125 mm (4.92 in)Height 96 mm (3.77 in)Depth 57 mm (2.24 in) Weight 430 g (0.94 lb)EMC / EMIThis equipment has been tested and found to comply with the limits for a Class B Digital device, pursuant to part 15 of the FCC rules. These limits are designed to provide reasonable protection against harmful interference in residential installations.This equipment generates, uses and can radiate radio frequency energy and, if not installed and used in accordance with the instructions, may cause harmful interference to radio communications. There is no guarantee that interference will not occur in a particular installation.If this equipment does cause harmful interference to radio or television reception, which can be determined by turning the equipment off and on, the user is encouraged to try to correct the interference by one or more of the following measures:· Reorient or relocate the receiving antenna.· Increase the separation between the equipment and receiver.· Connect the equipment to an outlet on a circuit different from that to which the receiver is connected.· Consult the dealer or an experienced radio/TV technician for help.。
Fibocom GT8230 用户手册说明书

EVK-GT8230User ManualVersion:V2.0.0Date:2013-09-13Confidential MaterialThis document contains information highly confidential to Fibocom Wireless Inc.(Fibocom).Fibocom offers this information as a service to its customers,to support application and engineering efforts that use the products designed by Fibocom.The information provided is based upon requirements specifically provided to Fibocom by the customers.All specifications supplied herein are subject to change. Disclosure of this information to other parties is prohibited without the written consent of Fibocom.CopyrightCopy,Reproduce,Distribute and/or Edit of this document or part of it as well as utilization of its contents and communication thereof to others without express authorization are prohibited.Offenders will be held liable for payment of damages.All rights created by patent grant or registration of a utility model or design patent are reserved.Copyright©2013Fibocom Wireless Inc.All rights reserved.Trademarks NoticeThe FIBOCOM Logo is registered by Fibocom Wireless Inc.All other product or service names or logos are the property of their respective owners.Copyright©2013Fibocom Wireless Inc.All rights reserved.Revision HistoryVersion Date RemarksV1.0.02012-05-29Initial VersionV1.0.12013-01-04Update the doc`s nameV1.0.22013-01-301.Update EVK and product pictures.2.Add some notes during using mini PCIe.3.Add picture of handles socket connection.4.Delete the button of POWER_ON and POWER_OFF.V2.0.02013-09-13Update the doc`s name. Add adapter.Applicability TableNo.Type Note1H330Concert with ADP-H330-xxx-yy 2H350Concert with ADP-H350-xxx-yyContents1Preface (5)1.1Scope (5)1.2Developer Board Structure (5)1.3Application Diagram (6)2Function Description of EVB (7)2.1Power Supply (7)2.1.1Direct Power Supply (7)2.1.2Power Adaptor (8)2.1.3Power Supply Peripherals (8)2.2UART1(COM) (9)2.3UART1(USB) (10)2.4USB Interface (11)2.5UART2(COM) (12)2.6SIM Card Interface (12)2.7Audio Interface (13)2.7.1Audio1 (13)2.7.2Audio2 (14)2.7.3Speaker (14)2.8RESET Button (15)2.9Test Point (16)2.10Default Jumper Switch (18)3Adapter Introduction (19)3.1Adapter Overview (19)3.2Adapter Appearance (19)3.3Adapter Structure (20)3.4Adapter Operation (21)3.4.1Work with GT8230 (21)3.4.2Only Adapter (21)3.5Adapter Installation (22)1Preface1.1ScopeEVK-GT8230is the developer board of Fibocom3G module,it worked with corresponding adapter.This Manual describes the developer board EVK-GT8230,ensures the users can quickly and conveniently develop wireless communications using Fibocom Module.1.2Developer Board StructureFigure1-1GT82301.3Application DiagramGT8230mainly includes the four parts:each functional interface,button,test point and power supply.The diagram as listed below:Figure1-2product diagramNote:the Reset button is only for Mini PCIe,for Adapter is useless.2Function Description of EVBThis section describes the different functions of each block;take ADP-H330(H330Adapter)as an example.2.1Power SupplyThis developer board supports two kinds of power supply inputs.(1)Direct Power SupplyDirectly connected with V40BAT(pin JP3)and GND(Pin JP2)to4VNote:For mini PCIe,use DC3.3V power supply(2)External PSUSupply option can be connected through the DC-DC adapter,supplying9V through(JP1),then supply power to H330Adapter through DC-DC conversion circuit on development board.As shown in Figure2-1:•Selection of Direct Power Supply,set the power selector switch(SWP1)to the left.•Selection of Power Adaptor,set the power selector switch(SWP1)to the Right.Figure2-1Power Switch2.1.1Direct Power SupplyDirect Power Supply:The power supply is connected directly to the module,so the voltage range must comply with the H330Specifications.Power Connector DescriptionV40BAT(JP3) GND(JP2)DC Power SupplyVoltage Range:3.3V~4.2V Recommended Voltage:4.0V Input Current:>2.0ANote:Please use correct Voltage to avoid damage.2.1.2Power AdaptorWhen an external power adaptor is plugged in,the developer board will use a DC-DC Buck circuit to convert to4V supply and LV40indicator will be ON.Power Connector DescriptionStraight Insert Voltage Socket,Φ2.5mm;Input Voltage:8V~15V;Input Power:≥9W.2.1.3Power Supply PeripheralsThere are two LDO chips(UP2and UP3)on the developer board.3.3V voltage generated after VBAT40pass through UP2,1.8V voltage generated after VDD33pass through UP3,these two set of voltages support other IC,LED and circuit on the developer board.Jumper Switch DescriptionJP4On/Off 3.3V voltage outputJP6On/Off LED indicatorJM5On/Off Enable LED Indicator for Power.JM11Select Power Supply for CODEC inside the module;Jumper on Pin1:VBAT connected with VSPK_M:power supplied by VBAT Jumper on Pin3:VDD33connected with VSPK_M:power supplied by VDD33JM12Supply power to VDD_MMC inside the module;1V8connected with VDD_MMC:power supplied by1V8;VDD33connected with VDD_MMC:power supplied by VDD33JA2Supply power to CODEC on the developer board;Jumper on Pin1:VBAT connected with VSPK:power supplied by VBAT; Jumper on Pin3:VDD33connected with VSPK:power supplied by VDD33Note:When you test the parameter of current,please unplug the above six jumpers.The tested current will be the current consumed by module only.Figure2-2Jumpers Locations2.2UART1(COM)UART1is a full8-line interface,there are six LED indicators(LRI/LDCD/LDSR/DTR/LRTS/LCTS), used to display the corresponding pin logic level in the module,it can be directly connected to PC or other DTE equipment.Developer board contains RS-232Transceiver SP3238EEA inside.PC and other DTE equipment can test all the functions of the module through this interface and AT Commands.The following picture shows the connection of UART1:Jumper Switch DescriptionJU7All9Jumpers In,Turn ON UART1SignalconnectionFigure2-3Jumpers LocationsNote:For mini PCIe,connect the mini USB cable to the high speed USB port of the developer board,in the meantime,unplug jumper switch JP7,otherwise,this port cannot be used.2.3UART1(USB)U ART1(USB)connector and UART1connector are using the same internal UART interface inside the developer board,so they have the same functions and commands.The developer board contains a UART to USB converter chip(PL2303),it provides four lines(TXD/RXD/CTS/RTS)to UART interface of module after conversion,this USB connector is the mini USB connector,users can connect to the PC through switching cable(USB transfer to mini USB).There is a LED indicator(LUSB-UART)next to the USB interface,used to display the connection between the interface and PC.If it is connected successfully,the light will on.The following picture shows the connection of USB(UART1):USBJumper Switch DescriptionJU9Turn on/off USB interface as communication interfaceNote:•You cannot use(UART1)and UART1interface at the same time,please switch between JU9and JU7.•Install corresponding driver USB to Serial port driver,,EVB use PL2303interface chip)when use USB interface.•Mini PCIe doesn’t support this port.Figure2-4Jumpers Locations2.4USB InterfaceThe USB interface is a high-speed data transmission interface,a LED indicator(LUSB)used to display the connection between the interface and PC terminal.This USB interface is a mini USB interface, users can connect to the PC through switching cable(USB transfer to mini USB).If it is connected successfully,the light will on.The following picture shows the connection of High Speed USB:Jumper Switch DescriptionJU4for connecting to USB_IDNote:Install corresponding driver(driver for H330module)when use USB interface.Figure2-5Jumpers Locations2.5UART2(COM)UART2is a2-lines interface(RXD/TXD)which can test the second UART of H330.It can be directly connected to PC or other DTE equipments.The following picture shows the communication process:Jumper Switch DescriptionJU6Enable/disable UART2Note:For mini PCIe,connect the mini USB cable to the high speed USB port of the developer board,in the meantime,unplug jumper switch JP7,otherwise,this port cannot be used.2.6SIM Card InterfaceDeveloper board includes a complete SIM card socket and interface circuit.The following picture shows the diagram:Figure2-6SIM Card Circuit2.7Audio InterfaceDeveloper board includes two audio interfaces and a speaker interface.The second audio interface and speaker interface are connected to the same audio network of the module,so you cannot use these two interfaces at the same time.Besides,developer board provides two Audio frequency modulation Options.•Option1:use of the CODEC inside the moduleSome modules does not support CODEC,please refer to the module hardware user manual.•Option2:use the External CODEC in the EVBJumper Switch DescriptionJA6Jumper to JA6select the CODEC inside the moduleJA7Jumper to JA7select the use of External CODEC in the EVBJA3Jumper to JA3select the use of External CODEC in the EVBFigure2-7Jumpers Locations2.7.1Audio1The handle socket JA1on the developer board is the first channel audio interface.Jumper Switch DescriptionJA6JA6(5-6pin)On/off,connect to MIC+of the headset JA6(7-8pin)On/off,connect to MIC-of the headset JA6(9-10pin)On/off,connect to EAR-of the headsetJA6(11-12pin)On/off,connect to EAR+ofthe headsetAs shown in this picture:Figure 2-8Handle Socket JA12.7.2Audio2The handle socket JA4on thedeveloper board is the second channel audio interface.Jumper SwitchDescription JA4JA4(1-2pin)On/off ,connect to AUXI-of the handle JA4(3-4pin)On/off ,connect to AUXI+of the handleJA4(13-14pin)On/off ,connect to AUXO+of the handle JA4(15-16pin)On/off ,connect to AUXO-of the handle As shown in this picture:Figure 2-9Handle Socket JA42.7.3SpeakerThe speaker interface and handle socket are connected to the same audio interface of the module,therefore,these two interfaces cannot be used simultaneously.Jumper Switch Description JA8JA8(1-2pin)On/off,connect to AUXO-of the speakerJA8(3-4pin)On/off,connect to AUXO+of the speakerJA8(5-6pin)On/off,PA power supplyFigure2-10Jumpers Locations2.8RESET ButtonThe developer board has a RESET button.The following picture shows the diagram:Figure2-11RESET CircuitJumper Switch DescriptionJM14Enable/disable,RESET switchFigure2-12Jumpers Locations2.9Test PointFor testing and debugging,there are several multi-group test pin on the developer board,please refer to the following table:Jumper Switch Test group Test PINJA8VRTC&ADC pin1:VRTC_1V8 pin2:VBACKC pin3:ADC2pin4:ADC1JM8CLOCK&EINT pin1:CLKOUT0 pin2:CLK32Kpin3:USIF1_SCLK pin4:T_OUT0pin5:EINT2pin6:GNDpin7:EINT1JM10MMC pin1:MMC_DAT3 pin2:MMC_DAT0 pin3:MMC_CD pin4:MMC_DAT1 pin5:MMC_CLK pin6:MMC_DAT2 pin7:MMC_CMDJA3PCMpin1:I2C_SCLpin3:I2C_SDApin5:I2S_RXpin7:I2S_TXpin9:I2S_WA0 pin11:I2S_CLK0 pin13:CLKOUT0JU1HSIC pin1:USB_VBUSpin2:HSIC_USB_DATA pin3:HSIC_USB_STRB pin4:GNDJM4MIPI pin1:1V8pin2:NCpin3:MIPI_RX_DATA/SPI MISO pin4:MIPI_RX_FLG/SPI MOSI pin5:MIPI_RX_RDY/SPI Clock pin6:MIPI_RX_WAKEpin7:MIPI_TX_DATA/SPI_MRDY pin8:MIPI_TX_FLG/SPI_SRDY pin9:MIPI_TX_RDYpin10:MIPI_TX_WAKEpin11:GPIO_049pin12:GNDJM1Other pin1:I2SCLK1pin2:USIM_DMpin3:USIM_DPpin4:DACOUT2.10Default Jumper SwitchThe following picture shows the default jumper switch position on the developer board:Figure2-13Jumpers LocationNo.Jumper Switch Quantity Description1JM141RESET connection2JP414V switch to3.3V connection3JM51Module output1.8V to indicator4JP7(pin2-pin3)1Supply1.8V connection from power 5JU63UART2connection6JP61Power supply for LED indicator7JU79UART1connection8JA68Audio connection9JM11(pin2-pin3)1Power supply for CODEC inside themodule3Adapter Introduction3.1Adapter OverviewThe adapter is used to connect module and developer board together,here take H330Adapter (ADP-H330)as an example.3.2Adapter AppearanceThe following figure shows ADP-H330.Figure3-1ADP-H330Top ViewFigure3-2ADP-H330Bottom View3.3Adapter StructureFigure3-3ADP-H330No.Type Description1Test point DC4V interface2USB interface USB communication interface3Jumper USB power supply switch control4Jumper Power selection:connect DC4V and VBAT,DC4V supplies the power5Power selection:connect DC4V and VBAT,DC4V supplies the power6Button On button,power on the module7Button Off button,power off the module8Button Reset button,reset the module(standard module is power off after reset) 9Test point JTAG test point,used for Debug10Module H330communication module11Antenna interface Main antenna interface,U.FL connector12Antenna interface Diversity antenna interface,U.FL connector13Connector Connector between Adapter and EVB;80PinNote:If you connect Adapter to the developer board,please remove jumper③and④.3.4Adapter Operation3.4.1Work with GT82301.Adapter doesn’t need power supply;the jumper of adapter can be removed.2.Please notice the direction of adapter and developer board.3.Adapter80Pin corresponds to developer board80Pin socket.Note:Misplace may cause damage to the module.IM card can be installed at the bottom of adapter or developer board GT8230.Note:Do not insert the SIM card at the same time,it may works abnormal.3.4.2Only Adaptere external DC+4V power first,jumpers connect to5pin(as shown in Figure3-3),press PowerON.2.If you want to use USB to supply the power,please connect the jumpers in3and4.Note:The load capacity of USB port must be5V,700mA or above,otherwise the module maybe abnormal.3.5Adapter InstallationAdapter installation:Figure3-4Adapter(H330Adapter)Installation DiagramNote:Please pay attention to the direction of Adapter to avoid damage.MINI PCI Installation:Figure3-5H330Mini PCIe Installation DiagramNote:Before install Mini PCIe,please remove the J5screw on the developer board,otherwise it cannot be installed.。
IHawk-V_USer_Op_3设置中文说明
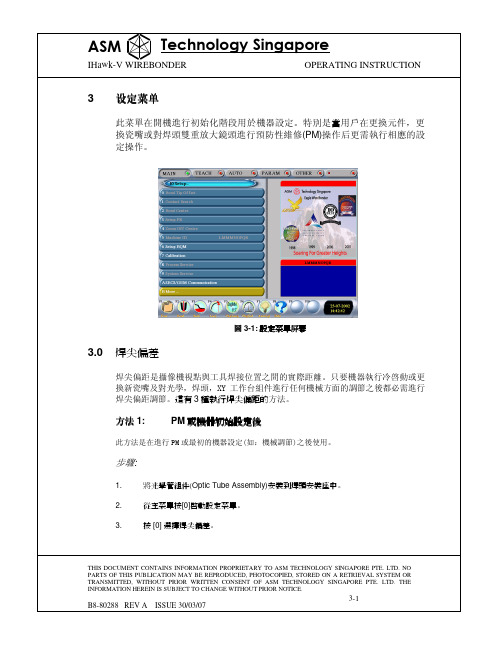
圖 3-1: 設定菜單屏幕焊尖偏差焊尖偏距是攝像機視點與工具焊接位置之間的實際距離。
只要機器執行冷啓動或更換新瓷嘴及對光學,焊頭,XY工作台組件進行任何機械方面的調節之後都必需進行焊尖偏距調節。
這有3種執行焊尖偏距的方法。
PM或機器初始設定後此方法是在進行PM或最初的機器設定(如:機械調節)之後使用。
將光學管組件(Optic Tube Assembly)安裝到焊頭安裝座中。
從主菜單按[0]啟動設定菜單。
[0] 選擇焊尖偏差。
CONTAINS INFORMATION PROPRIETARY TO ASM TECHNOLOGY SINGAPORE PTE.PARTS OF THIS PUBLICATION MAY BE REPRODUCED, PHOTOCOPIED, STORED ON A RETRIEVAL SYSTEM OR WITHOUT PRIOR WRITTEN CONSENT OF ASM TECHNOLOGY SINGAPORE圖 3-2: 設定PR 屏幕[3]選擇設定PR。
[0] 選擇圖像調節。
自動設定選項。
CONTAINS INFORMATION PROPRIETARY TO ASM TECHNOLOGY SINGAPORE PTE.PARTS OF THIS PUBLICATION MAY BE REPRODUCED, PHOTOCOPIED, STORED ON A RETRIEVAL SYSTEM OR WITHOUT PRIOR WRITTEN CONSENT OF ASM TECHNOLOGY SINGAPORE PTE.圖 3-3: 設定 BQM 菜單屏幕顯示微調信息此功能用於讓用戶檢查換能器的性能。
上升時間(ms)用於控制超聲波能量上升時間。
焊接時間應設定大於上升時間第一與第二焊接功率此功能用於讓用戶設定超聲波控制系統(BQM)的最大允許輸出功率選擇[High]功率設定時最大輸出3.2 watt, [Low]功率設定時最大輸出[Ult-Low] 功率設定時最大輸出0.4 watt 。
雕刻机雕刻软件设置
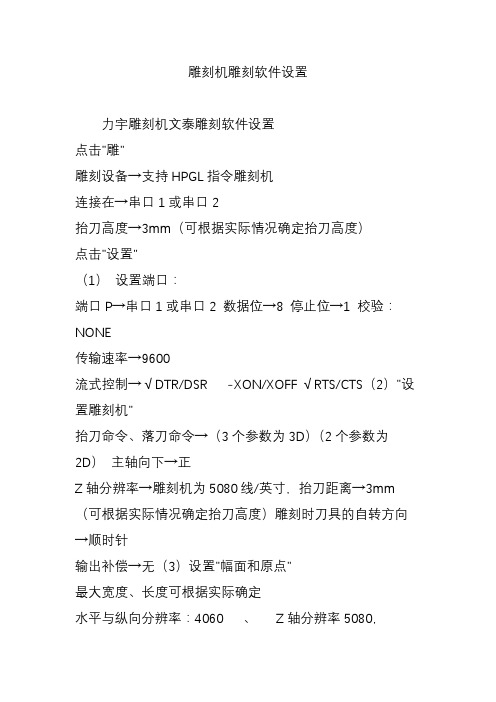
雕刻机雕刻软件设置力宇雕刻机文泰雕刻软件设置点击"雕"雕刻设备→支持HPGL指令雕刻机连接在→串口1或串口2抬刀高度→3mm(可根据实际情况确定抬刀高度)点击"设置"(1)设置端口:端口P→串口1或串口2 数据位→8 停止位→1 校验:NONE 传输速率→9600流式控制→√DTR/DSR -XON/XOFF √RTS/CTS(2)"设置雕刻机"抬刀命令、落刀命令→(3个参数为3D)(2个参数为2D)主轴向下→正Z轴分辨率→雕刻机为5080线/英寸,抬刀距离→3mm(可根据实际情况确定抬刀高度)雕刻时刀具的自转方向→顺时针输出补偿→无(3)设置"幅面和原点"最大宽度、长度可根据实际确定水平与纵向分辨率:4060 、Z轴分辨率5080,即:力宇雕刻机为4060线/英寸,坐标原点在--左侧1处,刻完后刀停在→左侧1处,纸前进方向为X 方向。
(4)命令设置初始化LIYUEGRAVING;ESC;IN@ (2D) (2个参数)LIYUEGRAVING;ESC;IN# (3D) (3个数)3D主要以电脑设置的刀具路径深度为主说明:均为阿拉伯数字0)落刀走PD 抬刀走PU 分割符,归位!PG;结束符;其余随软件默认完成后点击确认。
文泰雕刻软件可直接输出,其中F :代表镜象,即输出时整版内容将Y轴方向镜象R :代表旋转,选择旋转,输出时整版内容做90度旋转。
为什么刻的物体深浅不一原因在于:----材料不平解决方法:----1. 材料粘的不平----2. 机器台面变形,重铣面。
为什么刻圆弧出现折角?原因在于:----排版软件内结点少解决方法:----1.手动增加结点;----2.用别的软件做圆,转换至(如用文泰软件)雕刻软件。
为什么刻小字笔画乱(重叠)?原因在于:----刀具刀尖大于字体笔画解决方法:----1.做轨迹时选择“切割凹”处理----2.用单线字体做(文泰内有)。
- 1、下载文档前请自行甄别文档内容的完整性,平台不提供额外的编辑、内容补充、找答案等附加服务。
- 2、"仅部分预览"的文档,不可在线预览部分如存在完整性等问题,可反馈申请退款(可完整预览的文档不适用该条件!)。
- 3、如文档侵犯您的权益,请联系客服反馈,我们会尽快为您处理(人工客服工作时间:9:00-18:30)。
Gui Tool Document GUI_TOOL User ManualFor TW8823Techwell Shanghai9M&9N, Cross Region Plaza,No.899, Lingling Road, Xuhui DistrictURL 2010-4-12List1、Requirement of Hardware and software (2)2、Setup (2)3、Step (2)1、Requirement of Hardware and software.Winxp/vista OS.256M RAM2、SetupTBD3、Step1、Click “Gui_Tool.exe”startup software。
2、Initial UI(Picture 1)(Picture 1)3、Operation(1)New project:Click Menu: File->new,show below picture(picture 2 ~ picture 4)(Picture2 )(picture3)(Picture 4)new project windowYou can edit four items:(1) Project File Name (2)Project Path (3)Please Select CPU Type(4)flash address (5) TW2883 data output format selection. (6) touch screen onoff . Then clock OK, new project has built。
(as picture5)(picture 5) Groups ,select add group (see picture6~picture8)(二)New Group :Right click mouse on(picture6)(picture7)Click OK to new group,click Cancel if not。
You can add many groups as this;Click OK(picture 8)(picture 8)(3)new PageMouse right click Group0 select Add Page(picture 9)(picture 10)You can select the page type in this UI. The page will show as sub page if you check the “Sub Window”. The page’s position and size is setting in relative canvas id. You can change it by selecting Canvas id. Active Ctrl is the first focus ctrl when you enter this page. The tool will select one if you do not select it.Sub Page Note in TW8823:1、The hardware id in the relative canvas id must be 0 if you check the “Sub Window”;2、The memory of the canvas with hardware id 1 will reference the one with canvas 0;3、The width of canvas id must be alignment by 4;4、The user can set the sub-page position by changing ScreenX and ScreenY in canvas id.5、The remote left key and exit key support sub page exit. The left key without navigationinformation can exit current sub page.Click OK,Add Page as below(picture 11)Click page_0,as picture 12(picture 12)You can add many pages as this;(四)Load BitmapMouse right click BMPS(picture 13),(picture 13)Select BMPS->8bits(or 16bits or 24 bits)->Load Bitmap(Overwrite)(as picture 14), this item will overwrite exist bitmap in project if name is same; Select BMPS->8bits(or 16bits or 24bits)->Load Bitmap(Omit) , this item will omit new bitmap if bitmap exist;Then you can select bitmap file you want to load; click open(as picture 15)(picture 15)ctrls useAfter pag ilt ,we can add ctrls by clicking button (new text, new button, new scrollbar, tton in toolbar ,down and up ,move mouse to page areak mouse as picture 16,(五) e was bu new progress bar, new animate, new image )in toolbar 。
(1) TextctrlClick new text buClic(picture 16)You can edit the text by selecting string id or set the attribute by clicking the AttributeButton in this UI. You can also edit it by clicking edit button then it will navigate to text string edit UI. You can change the fore color or background color in this UI. You need to reselect these colors when the LUT is built.(picture 17)(2) Button ctrlClick button “New button” button in toolbar, down then up,move mouse to page area picture18,then click mouse, the button edit UI show:(picture 18)You can select focus image/unfocus image/invalid image in this UI. You can also select the relative text(focus text/unfocus text/invalid text) in it. Other set: all selected images’ attribute, all selected texts’ attribute, all selected texts’ colors, all selected texts’ content and font; you can also select navigation information for button including focus information , page’s information and mouse information for TW2880.(3) Progressbar ctrlUse New progress bar button in toolbar to add progress bar; You can select track image and potimage in progress bar edit UI;(picture 19)Click OK,Progress bar is add。
The add button is use to add progress and sub progress;(4)Scrollbar ctrlUse New scrollbar button in toolbar to add scrollbar bar; You can select track image ,pot image , curser image, add button images and sub button image in scrollbar bar edit UI(picture 20); style is use to select the direction of scrollbar; current is used to adjust initial value; navigation area issame with button ctrl;Picture 20 (5)Image ctrlUse I button in toolbar to add image ctrl; picture 21(6)Animator ctrlUse A button in toolbar to add animator ctrl; picture 22; you can add maximum is 7 images; the start id and interval also need to be selected.Picture 22(8)、scratch page addYou can right click scratch item in left resource area to select “Add Scratch Page”, then picture 23 show; here you should adjust the scratch page not to cover other scratch page and canvas area in sdrom; you can select type item to let the scratch page contain ICON or FONT;Auto place font and icon: you can auto place the font and icon on scratch page by clicking the sub-menu “Auto Image Set”;Picture 23You can add one icon scratch page and one font scratch page; after make scratch bitmap and font(you can do this after you add all groups, pages, ctrls), the bitmap and font need to scratch will show below at scratch page;How to add bitmap to scratch page? You can click one icon type scratch page, expand its sub items, select one items, move mouse to right canvas area, then bitmap frame will move with mouse, place it by clicking mouse; then the bitmap will show on scratch page; add bitmap one by one to scratch page;How to add font to scratch page? The operation will be use except of different scratch page type and font item;An icon scratch page show on picture 24, A font scratch page show on picture 25;Picture 24Picture 25(9) canvas, two default canvas loaded;(10) build:You can build code after you have complete all ctrls, page,group,scratch page design. Before Build the code, you must click Create scratch bitmap and scratch font and place scratch component rightly, after that Click menu build|build, the code will be create in code folder in project path;(11) Replace all code in core1 project then build, get core1.mot to flash in board.Replace all code in core1 project then build, get core1.mot to flash in board.Replace files gui_canvas_data.c, gui_font_data.c, gui_icon_data.c, gui_palette_data.c, gui_scratch_data.c ,zdfl_app_ctrl.c ,User_handle.h in folder core1\OSD.For TW2880 project, copy all the generated *.c and *.h file to the directory OSG.(12) multi-language textLoad strings: Click menu tool->load text after you created new project or loaded old project.Tool will show picture 26; you can load strings by clicking button “Load Text File”; the tool can load the Unicode format text file; there are two columns in this type file: the first column is string id and second is the unicode string contents in some language. The two column are separated by char tab(0x09) in every line and the line end is 0x000d0x000a. You can browse every string by click it in left resource window. String setting: you can select the font type and style and size for all strings in some language type then click set button. The tool will load all text data to tool. You can exit after you set all language type. Youcannot exit if there are some language type is not loaded.Picture 26(13)Edit some string idYou can click the menu tool->text rditor to edit some string to have different font type(size, style……). Reference picture 27.Picture 27You cannot change the string id font in load string dialog (picture 35) if you have edit it in picture 36. You also cannot change the string id in picture 36 if you enter dialog throw ctrl edit UI.You can add new string in this UI by clicking New String button and edit it.(14) Simulator fileYou can get the simulator file in project folder/code; its name is “gui_demo.sim”. you can use the simulator program to open this file tosimulate UI.How to simulate? You can open the simulate program “simulatePro.exe” in a separate folder as picture 28; Click open file button to select the file “gui_demo.sim” generated by GUI TOOL. Then you will get Picture 29:You can click left、right、enter、up、down to navigate the UI.You can use the mouse to navigate the UI when you word on TW2880 project.Picture 28Picture 29(15) Flash mode open/closeYou can set flash mode when new project or open project properties UI: Menu FIlE-> Properties; You can get data array mode when flash address equals to 0xffffffff and you can get flash mode when flash address equalsits actual value;(16) ctrl navigationto move ctrls on page; The white frame will show The tool support keyboardaround the ctrl if one ctrl is selected. Then you can pressup/down/left/right key to move the ctrl by one pixe. The focus ctrl willdisappear if you click blank area.(17) Gridee display grid modes in tool: Grid off and Grid as Background h Screen” to set CPU work There are thr and Grid as Foreground. You can align your ctrl by the grid line. There are grid value pixels between two grid lines. This value can be set by menu: “tool->grid value”. Menu “Tool->Grid off” can close gird mode. Menu “Tool->Grid as foreground” and “tool->Grid as background” can open grid mode. There are three buttons to operate gird open/close in toolbar. The grid status can be gotten from the GUI TOOL status bar.(18)Touch screen mode or remote key modeFor TW8823, there is one checkbox “Use Touc mode in project new or project properties UI. In touch screen mode, one macro “USED_TOUCH_SCREEN” is defined and there is no focus in the page just displayed. In remote key mode, the macro “USED_REMOTE_KEY” isdefined and the focus will show on the displaying page.。