PCBA Checklist
PCBA稽核check list

44 Carrier與元件是否干涉,擋錫杆與板邊元件無干涉.
45 產線測試&1394 code&Lan code防呆有效及SERVER 盤存儲空間.
46 SFIS Routing 適用. 異常情況說明 A:
原因分析:
臨 時 對 策 :
異常情況說明 B:
原因分析:
臨 時 對 策 :
合
不合
格
格:x
備注欄有* 應確實填寫記錄值
22 控制計劃中所要求使用之SPC管制表是否確實收集記錄,且異常時有無改善對策?
23 維修用料之料號與規格是否與BOM一致?
24 維修品經維修後,是否確認填寫維修記錄,且是否經過測試OK方可流入一下制程?
25
取維修板5片,確認不良品是否依規定刷入SFIS?并有無正確的刷入REASON CODE 。
26 作業員是否依規定作好靜電防護,同時點檢靜電防護用品並記錄?
受稽核單位主管: QPQA020917
37 所有測試用量規儀器是否為良好狀態,且在校驗周期內?
38 機板是否有未隔靜電泡棉之情形?機板放置是否符合規定?
39 靜電框內有無異物?
C 40 同一工站所插元件極性一致? 類 41 拉速與SOP是否一致?
42 使用Carrier的機板Fan chip吃錫是否飽滿,且機板的錫面是否清潔.
43 風扇(散熱片)與周圍元件無干涉,在跌落或撞擊時其它元件不會受損.
17 測試作業前是否依SOP規定執行Vcore電壓量測且量測結果在規格范圍內? B 18 產線有無正確的刷入ERROR CODE? 類
19 測試冶具是否定期點檢並記錄?
20 LAN Code和1394 Code之編碼方式是否符合文件規定?
PCBA试机DFM检查表

PCBA试机DFM检查表
1芯片表面必须完整的接触散热器
OK 2确保散热器不干涉旁边的零器件,无引起短路的隐患OK 3散热器接触芯片的底部面积必须大于或等于芯片的面积 OK 4它是否方便制作散热器安装的夹具OK 5检查散热器螺丝的扭矩要求OK 6检查散热器压扣是否到位OK 7线不干涉风扇叶片OK 8线长是否合理OK 9插头必须符合PCB上的插座,无接触不良的隐患
OK 10确保风扇叶没有干涉散热器里的任何部件(风扇线/散热器盖/风扇的螺丝等)OK 11风扇线应该没有被散热器本体破坏的可能OK 12垫圈的直径必须大于弹簧的外径OK 13垫圈是否干涉旁边的零器件OK 14CPU座背板没有压料的隐患
OK
15高温元器件是否对旁边的物料有影响(如旁边的温度敏感器件或烫伤风扇线等)OK 16它是否方便制作过炉板
OK 17设计是否方便员工作业(如插机料,BIOS IC和电池的插入)OK 18外接显卡声卡或连接器等设备和器件时是否存在干涉OK 19料件的选用是否合理(如卧式或立式;贴片或插机)OK 20料件的撘配是否恰当
OK 21PCB是否有元件方向标示或防呆措施
OK
Model: PCB P/N:
PCBA DFM checklist
Done by: Date:description
result remark Item。
PCB原理图Checklist检查表

PCB原理图Checklist检查表类别描述检视规则原理图需要进行检视,提交集体检视是需要完成自检,确保没有低级问题。
检视规则原理图要和公司团队和可以邀请的专家一起进行检视。
检视规则第一次原理图发出进行集体检视后所有的修改点都需要进行记录。
检视规则正式版本的原理图在投板前需要经过经理的审判。
差分网络原理图中差分线的网络,芯片管脚处的P 和N 与网络命令的P 和N 应该一一对应。
单网络原理图中所有单网络需要做一一确认。
空网络原理图中所有空网络需要做一一确认。
1、原理图绘制中要确认网格设置是否一致。
2、原理图中没有网格最小值设置不一致造成网络未连接的情况。
网络属性确认网络是全局属性还是本地属性1、原理图中器件的封装与手册一致。
2、原理图器件是否是标准库的symbol 。
绘制要求原理图中器件的封装与手册一致。
指示灯设计默认由电源点亮的指示灯和由MCU 点灭的指示灯,便于故障时直观判断电源问题还是MCU 问题网口连接器确认网口连接器的开口方向、是否带指示灯以及是否带PoE 网口变压器确认变压器选型是否满足需求,比如带PoE 按键确认按键型号是直按键还是侧按键电阻上下拉同一网络避免重复上拉或者下拉OD 门芯片的OD 门或者OC 门的输出管脚需要上拉匹配高速信号的始端和末端需要预留串阻三极管三极管电路需要考虑通流能力可测试性在单板的关键电路和芯片附近增加地孔,便于测试连接器防呆连接器选型时需要选择有防呆设计的型号仿真低速时钟信号,一驱动总线接口下挂器件的驱动能力、匹配方式、接口时序必须经过仿真确认,例如MDC/MDIO 、IIC 、PCI 、Local bus 仿真电路中使用电感、电容使用合适Q 值,可以通过仿真。
时序确认上电时序是否满足芯片手册和推荐电路要求。
时序确认下电时序是否满足芯片手册和推荐电路要求。
时序确认复位时序是否满足芯片手册和推荐电路要求。
复位开关单板按键开关设计,要防止长按按键,单板挂死问题,建议按键开关设计只产生一段短脉宽低电平。
试产准备Checklist

试产准备Checklist
编制:日期:
审核:日期:
批准:日期:
试产准备内容checklist
产品型号
会议记录人
会议日期
备注
制做阶段
制做数量
PCBA日期
到厂
检验
工厂:
组装日期
开始
结束
资料准备
项次
准备标准
责任人
要求日期
状态
试产BOM(PCBA、组装、包装)
与设计验收一致
硬件
SCH源文件(需工厂申请)
与设计验收一致
硬件
PCB源文件(需工厂申请)
与设计验收一致
硬件Байду номын сангаас
PCBA规格书
完整输出
硬件
维修原理图
完整输出
硬件
产品效果图
完整输出
硬件
系统方框图
完整输出
硬件
贴片图
完整输出
硬件
钢网资料
完整输出
硬件
坐标文件
完整输出
硬件
PCB制作工艺要求
完整输出
硬件
产品使用说明书
完整输出
硬件
产品规格书
完整输出
硬件
Gerber文件
完整输出
软件
产品特殊工艺说明
完整输出
结构
产品测试标准
完整输出
DQA
软件版本及路径
完整输出
软件
测试工具
完整输出
软件
QA测试规范
完整输出
DQA
样板准备与提供
OK样机4台
4台
硬件
PCBA 4套(SMT)
4PCS
硬件
PCBA CHECK LISTPPT

报告人核对送检单上的料号、品名等项目与包装标识 相符。 2.检查包装无脏污破损及防静电符不符合要求。 3.检查包装标签料号、数量、日期、PASS标签、 环保标签等符合要求。 4.标签上必须有料号、机种、数量体现。 5.标签生产日期是否标识。 6.包装内数量与外箱标签标识数量相符。 7.包装内产品是否包装整齐或散乱等。
四、功能检测 一、读碟测试 1.1BCD-100读2、8、10双声道/左声道/右声道听声音 看波形,读碟应顺畅,图像应清晰. 1.2CD碟测试画面是否正常, 读碟应顺畅,图像应清晰. 1.3TDV-540A(单面双层)测试碟片进行内外圈从第一层 17首至第二层1首测试,读碟状态应连续,不得有死机,马 赛克等不良现象. 1.4用JPG测试碟片进行读碟测试,在播放过程中按 STOP及方向左右按键无作用,按方向下键图片可进行顺 时针旋转,按MENU键LOGO上出现12画面,此时按方向 键可进行选择,按方向下按键无作用,按上键画面回到主 菜单.
二、尺寸检查 1.比照样板是否相符 2.用卡尺量测PCBA厚度看是否与样板相符。 3.比照样板核对主要元器件(IC/电容/电感晶体等) 丝印结构是否与样品相符. 4.比照样板看插座/排扣/JACK/USB/拨动开关结构 与尺寸是否与样板相符.
三、外观检测 1.检查PCBA标签料号与采购验收单清单料号是否一致. 2.用放大境镜(放大倍数5-10倍)检验PCB板面(若有疑问时 用更高倍数之放大工具进行检验。 3.目视比对外形结构与尺寸是否与样品一致.硬件是否与样 品一致 4.PCBA硬件版本号、型号、防火等级机种丝印等是否与 样品一致. 5.核对主要元器件(电容、IC、电感、晶体等)型号规格是 否与样品相符. 6.目视SMT/焊点位置是否焊到位.是否有连锡、假焊、少 焊现象. 7.检查AV JACK外观结构是否与样品一致.
PCB(射频单板)外协厂防静电稽查CHECKLIST

PCBA (射頻單板) 外 協 廠 防 靜 電 稽 查 CHECKLIST
工具、
備注:
1.問題級別的表征意義:A-非常重要、B-重要、C一般
2.查檢結果的表征意義:3-完全滿足要求、2-基本滿足要求、1-部分滿足要求、0-不滿足要求、N/A-不涉及
3.完全滿足要求:抽樣數中100%的滿足要求;基本滿足要求:抽樣數中大於或等於90%小於100%的滿足要求;部分滿足要求:抽樣數中大於
4.稽查過程,請按實際情況在查檢結果欄相應位置打"v".
5.在外協廠論證時,必須滿足所有檢查要點要求時才能通過ESD論證.
i.A類問題必須全部為滿足要求.
ii.B類問題必須90%以上完全滿足要求,100%基本滿足要求.
iii.C類問題必須有60%以上完全滿足要求,100%以上基本滿足要求.
6.外協廠論證通過後,在生產華為單板過程中,如稽查發現問題,按如下規定操作:
i.A類問題必須全部為基本滿足要求或以上,並且總分不得少於46分,否則必須停線整改,整改後必須通過華為ESD小組確定才能生產.
ii.B類問題必須70%以上完全滿足要求,90%以上基本滿足要求,並且總分不得少於110分,否則必須限期整改,並對供應商進行扣分處理.
如限期整改未完成,將進行停線處理.
iii.C類問題必須有50%以上完全滿足要求,80%以上基本滿足要求,總分不得少於42分,否則必須限期整改.如限期整改未完成,將進行
扣分處理.。
PCBA制程技术及check list讲解

短 路(Bridge)
不良品
良品
22
空 焊(Wettability)
不良品
良品
23
偏移(Horizontal shift / Vertical shift)
不良品
良品
24
缺 件(Missing Component)
Байду номын сангаас
不良品
良品
25
墓 碑(Missing Component Solder)
少时间,以不超过24小时为原则,若超过24H必须将PC板送至烤箱内烘烤,烘 烤温度为120度,时间为2H. 6.拆封后之PCB板不能置于静电框上,以防刮伤/污染PCB板板面. 7.针对打第二面时插板需注意隔一格插一片.
生产工具:
WI.料站表.静电框.条形码标签.拆封标签.盖板.板子.台车
4
送板机的工具图片
13
高速机/泛用机生产工具图片
电脑/扫描枪
材料
模组式机器Feeder
14
上料流程
1.机器显示屏提示所缺料站.确认找到所缺料站; 2.取出所缺料站FEEDER,注意一次只能提取一只FEEDER; 3.在电脑上确认正确的料表号码; 4.扫描旧料盘上料号,并输入站数; 5.拿料表和旧料盘去料车上找新料,必须确保料站表和旧料盘及新料三者
2
SMT 生产流程 SMT:
送板机
锡膏印刷机
锡膏检测机
高速机
目检打包
AOI
回焊炉
3
泛用机
1.送板机
注意事项:
1.拆封PCB必须戴静电手套. 2.PCB上架前必须确认它的料号和方向以及它的版本是否正确. 3.每次拆开的PCB不能超过3框. 4.PCB进板方向依相应机种生产参数管控计划表规定为准. 5.PCB拆箱后要在外箱注明拆箱时间以便追踪PCB拆封后在空气中暴露多
PCB 原理图 Checklist检查表

类别描述检视规则原理图需要进行检视,提交集体检视是需要完成自检,确保没有低级问题。
检视规则原理图要和公司团队和可以邀请的专家一起进行检视。
检视规则第一次原理图发出进行集体检视后所有的修改点都需要进行记录。
检视规则正式版本的原理图在投板前需要经过经理的审判。
差分网络原理图中差分线的网络,芯片管脚处的P 和N 与网络命令的P 和N 应该一一对应。
单网络原理图中所有单网络需要做一一确认。
空网络原理图中所有空网络需要做一一确认。
1、原理图绘制中要确认网格设置是否一致。
2、原理图中没有网格最小值设置不一致造成网络未连接的情况。
网络属性确认网络是全局属性还是本地属性1、原理图中器件的封装与手册一致。
2、原理图器件是否是标准库的symbol 。
绘制要求原理图中器件的封装与手册一致。
指示灯设计默认由电源点亮的指示灯和由MCU 点灭的指示灯,便于故障时直观判断电源问题还是MCU 问题网口连接器确认网口连接器的开口方向、是否带指示灯以及是否带PoE 网口变压器确认变压器选型是否满足需求,比如带PoE 按键确认按键型号是直按键还是侧按键电阻上下拉同一网络避免重复上拉或者下拉OD 门芯片的OD 门或者OC 门的输出管脚需要上拉匹配高速信号的始端和末端需要预留串阻三极管三极管电路需要考虑通流能力可测试性在单板的关键电路和芯片附近增加地孔,便于测试连接器防呆连接器选型时需要选择有防呆设计的型号仿真低速时钟信号,一驱动总线接口下挂器件的驱动能力、匹配方式、接口时序必须经过仿真确认,例如MDC/MDIO 、IIC 、PCI 、Local bus 仿真电路中使用电感、电容使用合适Q 值,可以通过仿真。
时序确认上电时序是否满足芯片手册和推荐电路要求。
时序确认下电时序是否满足芯片手册和推荐电路要求。
时序确认复位时序是否满足芯片手册和推荐电路要求。
复位开关单板按键开关设计,要防止长按按键,单板挂死问题,建议按键开关设计只产生一段短脉宽低电平。
电源PCB-CHECKLIST(布局)

所有器件满足禁布要求
需封装库人员和客户确认,新器件的封装库建库正确,元器件选用封装对应无误
确认PCB上器件安装的加工路线,并采取相应的布局方案,板边是否需要5mm 禁布区(最少3mm),或者加工艺边
压接器件是否满足安装间距要求
拨码开关、复位器件,指示灯、测试点等,不与其它器件冲突(如拉手条、 散热片、扣板、斜插或平插的器件(如DIMM条和CF卡等)等),且放在元件面
免[ ] 免[ ] 免[ ] 免[ ] 免[ ] 免[ ] 免[ ] 免[ ] 免[ ] 免[ ] 免[ ] 免[ ]
备注
是[ ] 否[ 是[ ] 否[ 是[ ] 否[ 是[ ] 否[ 是[ ] 否[ 是[ ] 否[ 是[ ] 否[ 是[ ] 否[ 是[ ] 否[ 是[ ] 否[ 是[ ] 否[
免[ ] 免[ ] 免[ ] 免[ ] 免[ ] 免[ ] 免[ ] 免[ ] 免[ ] 免[ ] 免[ ]
不耐热的元器件和热敏器件(如铝电解电容、晶体等)不靠近高热器件 开关电源MOS管的散热是否满足要求 高速与低速,数字与模拟按模块分开布局 始端匹配靠近发端器件,终端匹配靠近接收端器件 退耦电容靠近相关器件放置 晶体、晶振及时钟驱动芯片等靠近相关器件放置 根据分析仿真结果或已有经验确定总线的拓扑结构,确保满足系统要求 现有布局能否满足绝对长度要求,相对长度是否容易实现 对同步时钟总线系统的布局满足时序要求 电感、继电器和变压器等易发生磁场耦合的感性器件不相互靠近放置 为避免单板焊接面器件与相邻单板间发生电磁干扰,单板焊接面不放置敏感 器件和强辐射器件 接口器件靠近板边放置,已采取适当的 EMC 防护措施(如带屏蔽壳、电源地 挖空等措施),提高设计的EMC能力 保护电路放在接口电路附近,遵循先防护后滤波原则 发射功率很大或特别敏感的器件(例如晶振、晶体等)远离屏蔽体、屏蔽罩外壳 复位器件、复位信号远离其他强干扰器件、信号 元件面下面的平面层为地 主电源层尽可能与其对应地层相邻,电源层与对应的地满足20H规则 每个布线层尽量满足有一个完整的参考平面,关键信号至少要有一个完整的参考平面 多层板层叠、芯材(CORE)对称 过孔的厚径比大于10:1时,需要得到PCB厂家确认 光模块的电源、地与其它电源、地分开,以减少干扰 有阻抗控制要求时,层设置参数满足要求
最新PCB-Checklist

项目
序号
检查内容
EDA
设计
EDA
复审
EDA
确认
备注
资
料
输
入
阶
段
在流程上接收到的资料是否齐全(包括:原理图、*.brd文件、料单、PCB设计说明以及PCB设计或更改要求、标准化要求说明、工艺设计说明文件)
1.3
确认PCB模板是最新的
确认模板的定位器件位置无误
PCB设计说明以及PCB设计或更改要求、标准化要求说明是否明确
单板信号走线上不能有锐角和直角(一般成 135 度角连续转弯,射频信号线最好采用圆弧形或经过计算以后的切角铜箔)
对于双面板,检查高速信号线是否与其回流地线紧挨在一起布线;对于多层板,检查高速信号线是否尽量紧靠地平面走线
对于相邻的两层信号走线,尽量垂直走线
避免信号线从电源模块、共模电感、变压器、滤波器下穿越
是否在信号线跨层比较多的地方,放置了地过孔(至少需要两个地平面)
电源和地
如果电源/地平面有分割,尽量避免分割开的参考平面上有高速信号的跨越。
确认电源、地能承载足够的电流。过孔数量是否满足承载要求
(估算方法:外层铜厚1oz时1A/mm线宽,内层0.5A/mm线宽,短线电流加倍)
对于有特殊要求的电源,是否满足了压降的要求
与结构相关的器件布好局后最好锁住,防止误操作移动位置
压接插座周围5mm范围内,正面不允许有高度超过压接插座高度的元件,背面不允许有元件或焊点
确认器件布局是否满足工艺性要求(重点关注BGA、PLCC、贴片插座)
金属壳体的元器件,特别注意不要与其它元器件相碰,要留有足够的空间位置
接口相关的器件尽量靠近接口放置,背板总线驱动器尽量靠近背板连接器放置
PCB CHECKLIST

注意公母正负封装
4
功率器件是否考虑其散热效果,包括散热 铜皮大小、导热过孔、器件放的位置等等
无需检查 检查通过 OK 检查不通过
注意IC衬底
5
金属壳体的元器件是否和电路板的走线或 其他器件相碰干涉
无需检查 检查通过 OK 检查不通过 无需检查
6
器件的焊盘宽度和长度是否合适
检查通过 OK 检查不通过
7
23
是否有波峰焊接方向的标示,是否有偷锡 焊盘或其它措施,解决波峰焊的连锡问题
无需检查 检查通过 OK 检查不通过 无需检查
偷锡处理
24 线路板边框是否做圆弧或倒角处理。
检查通过 OK 检查不通过 无需检查
25 GERBER文件是否齐全
检查通过 OK 检查不通过
26
钢网文件是否去掉不必要的开窗(注意检 查那些漏铜而不需要上锡的区域,如硅胶 按键PAD)
PCB设计 CHECK LIST
表单编号: NO. 检查项 检查结果
无需检查
版本号: 确认人 备注
1
PCB、原理图和BOM三者位号是否一致
检查通过 OK 检查不通过 无需检查
2
是否按结构尺寸及要求放置元件
检查通过 OK 检查不通过
3
所有新器件的PCB封装是否和原理图对 应,封装尺寸是否和承认书相符
无需检查 检查通过 OK 检查不通过
12
是否加工艺边
13
数字电路和模拟电路及高速器件走线是否 合理。
14
敏感线是否有包地处理,与其它强信号线 的间距是否足够
无需检查 检查通过 OK 检查不通过
15
大电流的走线宽度是否满足需求,换层时 过孔大小及个数是否足够
很全面的PCB_checklist_表格
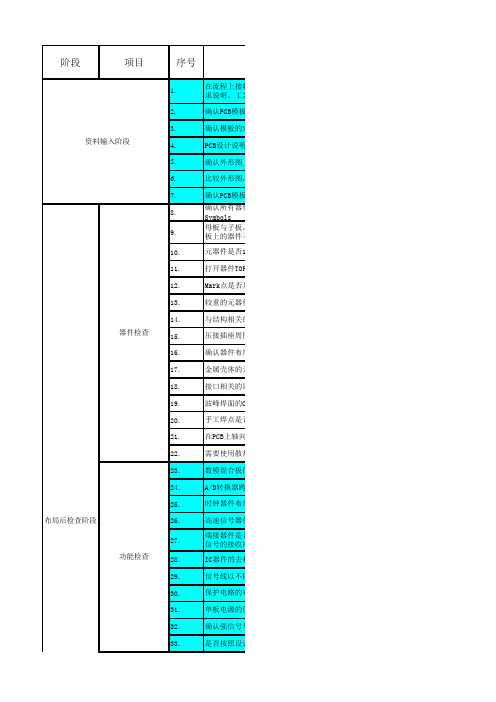
85. 86. 87. 88. 89. 90. 91. 92. 93. 94. 95. 96. 97. 98. 99.
100.
101.
如果电源/地平面有分割,尽量避免分割开的参考平面上有高速信号的跨越。 确认电源、地能承载足够的电流。过孔数量是否满足承载要求,(估算方法:外层铜厚1o 线宽,短线电流加倍) 对于有特殊要求的电源,是否满足了压降的要求 为降低平面的边缘辐射效应,在电源层与地层间要尽量满足20H原则。(条件允许的话,电 如果存在地分割,分割的地是否不构成环路? 相邻层不同的电源平面是否避免了交叠放置? 保护地、-48V地及GND的隔离是否大于2mm? -48V地是否只是-48V的信号回流,没有汇接到其他地?如果做不到请在备注栏说明原因。 靠近带连接器面板处是否布10~20mm的保护地,并用双排交错孔将各层相连? 电源线与其他信号线间距是否距离满足安规要求? 金属壳体器件和散热器件下,不应有可能引起短路的走线、铜皮和过孔 安装螺钉或垫圈的周围不应有可能引起短路的走线、铜皮和过孔 设计要求中预留位置是否有走线 非金属化孔内层离线路及铜箔间距应大于0.5mm(20mil),外层0.3mm(12mil),单板起 间距应大于2mm(80mil) 铜皮和线到板边 推荐为大于2mm 最小为0.5mm 内层地层铜皮到板边 1 ~ 2 mm, 最小为0.5mm 对于两个焊盘安装的CHIP元件(0805及其以下封装),如电阻、电容,与其焊盘连接的印 称引出,且与焊盘连接的印制线必须具有一样的宽度,对于线宽小于0.3mm(12mil)的引出 与较宽印制线连接的焊盘,中间最好通过一段窄的印制线过渡?(0805及其以下封装) 线路应尽量从SOIC、PLCC、QFP、SOT等器件的焊盘的两端引出 器件位号是否遗漏,位置是否能正确标识器件 器件位号是否符合公司标准要求 确认器件的管脚排列顺序, 第1脚标志,器件的极性标志,连接器的方向标识的正确性 母板与子板的插板方向标识是否对应 背板是否正确标识了槽位名、槽位号、端口名称、护套方向 确认设计要求的丝印添加是否正确 确认已经放置有防静电和射频板标识(射频板使用) 确认PCB编码正确且符合公司规范 确认单板的PCB编码位置和层面正确(应该在A面左上方,丝印层) 确认背板的PCB编码位置和层面正确(应该在B右上方,外层铜箔面) 确认有条码激光打印白色丝印标示区 确认条码框下面没有连线和大于0.5mm导通孔 确认条码白色丝印区外20mm范围内不能有高度超过25mm的元器件 在回流焊面,过孔不能设计在焊盘上。(正常开窗的过孔与焊盘的间距应大于0.5mm (2 盘的间距应大于0.1 mm (4mil),方法:将Same Net DRC打开,查DRC,然后关闭Same N 过孔的排列不宜太密,避免引起电源、地平面大范围断裂
终端_PCBA维修规范V2.1强制执行清单验收checklist

时风嘴垂直向下,直接向元件吹热风,从风嘴距离
元器件25mm开始预热(如果风嘴尺寸小于元器件,
加热时使热风以稳定的圆周方式运动接近元器件),
《终端PCBA维修规范》 慢慢接近元器件,风嘴与元器件最小距离保持在 第3.3章节,页码20 3~5mm,禁止风嘴接触元器件本体。
√
拆除或焊接单个电子元器件的时间最长为40s,每次
3298340382.xlsx
文档密级
华为制造标准关键项实施checklist(验收)
制造标准名 称
终端PCBA维修规范 版本
工厂名称
稽核人
V2.1
手机项目
稽核时间
总体分数
关键项类别 /工序
序号
规范/标准执行 要点
参考文件章节
具体标准
手机 大T DP GY
1、必须经过上岗培训,包括但不限于:IPC-A-
焊接操作时间最长为120s。
3)温度测量及校准每天使用校准期内的温度测量
仪来测量温度,热风温度不能超过 380°C
√ √√ √ √√ √ √√
√ √√
√ √√
设备及辅料
2020/12/17
华为保密信息,未经授权禁止扩散
第1页,共3页
3298340382.xlsx
设备及辅料
电子器件焊接、 检验
BGA修理台的温度曲线:1)典型值:预热温升要求
product safety data sheet) ,化学品必须贴有
MSDS标签
《终端PCBA维修规范》 第1.1.1章节,页码12
2、焊接维修工位需装备合适的排烟系统用于焊接 烟雾的排除 3、维修设备必须有详细的安全操作指导书
√
4、焊接操作和使用化学品人员要佩戴个人防护用
PCBA Checklist

Is there a revision controlled Work Instruction which contains details of how to assemble the 3.1 product? 3.2 Are Work Instructions readily available to the operator and are they followed at Assembly? 3.3 Are component part numbers and descriptions included on the Work Instructions? 3.4 Are components sufficiently identified to ensure the correct component is being used? 3.5 Is the layout of trays defined on Work Instructions for each assembly station?
Score % 26 100% Self Audit
1
1
1
1
1 1
1
1
1 1 1
1 1 1 1 1
Score % 26 100% LF Audit
1
1
1
1
1 1
1
1
1 1 1
1 1 1 1 1
PCB设计检查表-PCB-checklist

4.4.12
148
PAD与线的SPACING:最小要5mil(最好把线与SPACING平分成三等份)
149
PAD与PAD的SPACING:最小要8mil
150
BGA SOCKET(Through Hole TYPE)
151 4.4.13 Hole size:1.27mm pitch 用0.5mm(20mil)
133 4.4.4 Via Hole 尺寸为20mil
134 4.4.5 POWER 及 GROUND ACCESS 为32mil
135 4.4.6 GRID HOLE及其他ACCESS为45mil
136
GUIDE PIN HOLE(非镀通孔)
137 4.4.7 如图纸有提供HOLE SIZE ,按图纸做
128 4.3 与电原理图网络匹配检查
129 4.4 元件焊盘过孔尺寸检查
130 4.4.1 板厚度≤125mil时,VIA孔(过孔)为25mil
131 4.4.2 板厚度>125mil时,VIA孔(过孔)为32mil
132 4.4.3 对于长方形的PAD ,长的每边15mil ,短的每边有4mil
26 2.19 含贴片器件的PCB,贴片器件所在面的板任选2角各放置一个定位光标
27 2.20 MOUNTING孔(安装孔)是否镀铜(要镀铜)
28 2.21 GUIDE PIN孔(定位孔)是否没镀铜(除另有说明,不要镀铜)
29 2.22 元器件的1脚是否为方PAD
30 2.23 POWER PLANE 分割时是否出现瓶颈
9 2.2 所有器件已经放置到板面
10 2.3 整体布局参照原理功能框图,兼顾美观及电源、地的分割
11 2.4 高、中、低分开放置
PCB设计检查表-PCB_checklist

Annular Ring:最小要3mil(最好做5mil)
149 150
PAD与PAD的SPACING:最小要8mil BGA SOCKET(Through Hole TYPE)
151 4.4.13 Hole size:1.27mm pitch 用0.5mm(20mil) 152 153 154 1.00mm pitch 用0.35mm(14mil) BGA SOCKET(Through Hole TYPE)
3.62 OP AMP 的输入线路要远离输出线路 3.63 4 4.1 线尽可能不要走入孔的Clearance范围以内(如很难避免时,设计前一定要通 知主管) 其他 DRC检查
119 120 121 122 123 124 125 126 127 128 129 130 131 132 133 134 135 136 137 138 139
3.53 Critical TRACE(连接CLK的TRACE)以最短原则设计 Critical TRACE(连接CLK的TRACE)间距离是否尽可能远(最小为线边到线边 距离的三倍) Critical TRACE(连接CLK的TRACE)如为ANALOG TRACE ,要加上GUARD LINE 3.55 (屏蔽线) 3.54 3.56 先设计Critical TRACE(时钟信号线),再布其它线 在ANALOG PAD处是否有引线(不应有引线,否则会把ANALOG PAD的GROUND RING 割破) ANALOG PAD在TESTER SIDE时,是否把线布在DEVICE SIDE。(应该布在DEVICE 3.58 SIDE ) TRANSISTORS(三极管),不要把BASE(基极)的连线走在EMITTER和COLLECT 3.59 之间 3.57 3.60 OP AMP(放大器)输入线必须很短,一对输入线等长 3.61 所有反馈(OUTPUT TO INPUT)元件,必须放近OP AMP(放大器),连线越短 越好
PCB check list_1204资料精

主题Title PCB Check List 文件编号Doc. No.修 改 记 录Update Records版次Rev. No.修改摘要Update Summary生效日期Effective Date编制Prepared By签名Signature1.0 新发行会签/Review 批准/ApprovalHW 经理副总经理总经理文件发放部门: Distribution list: 文件受控状态(印章) Document Control Status (Stamp)主题Title PCB Check List 文件编号Doc. No.1.0 目的规范PCB检查流程,防止检查中的遗漏;提高PCB设计质量,杜绝设计中的失误。
2.0 适用范围**硬件部。
本文档用于输出制板文件前的layout最终检查,供EDA及硬件设计人员参考。
依据硬件详细设计文档、原理图、器件Spec等进行。
3.0 说明该文档仅列出各检查项清单,不涉及检查的实现方法和原理。
检查结果:指按每个检查内容要求对设计进行检查,最终判定的结果,分是、否、免三种结果。
“是”表示符合要求,“否”表示不符合要求,“免”表示此设计规格中不包含对应项的要求或该项可以忽略。
4.0 Check List主题Title PCB Check List 文件编号Doc. No.Project : PCB Check List检查结果项目 序号 检查内容是否免备注(结果说明)1 所有新器件封装与原理图symbol是否对应,是否与spec相符,封装尺寸是否已检查确认?2 所有连接器,FPC等引脚顺序,极性是否经过多人包括结构工程师确认?3 各封装是否都有必要的尺寸标注、极性标识和1脚标记。
焊盘大小和尺寸是否满足生产需要?4 晶体是否远离USB插座、耳机插座、Line In插座、按键等可能的ESD源?5 按键、Reset、USB、耳机输出、Line In 输入信号及USB电源等易接收ESD干扰的信号上是否预留并联到地的压敏电阻作防护之需?6 关键新器件单元电路布局布线是否已向原厂做技术确认?7 双工器是否放在射频屏蔽盖的外面(CDMA平台)?8 PA是否与接收系统充分隔离,是否放在独立的屏蔽盖内(MTK平台)?9 是否将强弱信号合理分开?(ransmitter and Receiver,CDMA 收发同时工作)封装&布局10 是否做到PA和LNA距离天线尽可能短?(减少损耗、避免干扰)11 天线焊盘正下方是否留有足够的挖空区域?(不允许有包括地在内地所有网络)。
- 1、下载文档前请自行甄别文档内容的完整性,平台不提供额外的编辑、内容补充、找答案等附加服务。
- 2、"仅部分预览"的文档,不可在线预览部分如存在完整性等问题,可反馈申请退款(可完整预览的文档不适用该条件!)。
- 3、如文档侵犯您的权益,请联系客服反馈,我们会尽快为您处理(人工客服工作时间:9:00-18:30)。
1
1
3.9 Are all torque drivers set to the required torque and screws inserted in the right sequence?
1
1
Is there evidence that torque drivers are checked with a calibrated tool at least once a day to 3.10 ensure the correct torque requirements?
Score % 26 100% Self Audit
1
1
1
1
1 1
1
1
1 1 1
1 1 1 1 1
Score % 26 100% LF Audit
1
1
1
1
1 1
1
1
1 1 1
1 1 1 1 1
3.6 Are all trays located in a defined position as per Work Instructions for each assembly station?
1
1
Do Work Instructions contain clear pictures to aid the operator & ensure the correct assembly 3.7 method is understood?
1
1
Are torque settings and the sequence of screw insertion specified for screw assembly 3.8 operations?
Are first-assembled boards verified against documentation to ensure mechanical items have 2.1 been assembled correctly?
Are all totes or tray locations identified with printed part numbers, descriptions, locations, and 2.2 layout information?
Are color coding techniques deployed for parts, tools, work instructions etc. in an attempt to 2.5 error proof the process? 3. Mechanical Assembly
Is there a revision controlled Work Instruction which contains details of how to assemble the 3.1 product? 3.2 Are Work Instructions readily available to the operator and are they followed at Assembly? 3.3 Are component part numbers and descriptions included on the Work Instructions? 3.4 Are components sufficiently identified to ensure the correct component is being used? 3.5 Is the layout of trays defined on Work Instructions for each assembly station?
1
1
Do all torque drivers have 'lock nuts' to fix the torque setting after calibration to prevent 3.11 operator adjustment?
11Βιβλιοθήκη Are protective guides used to ensure that torque drivers cannot cause damage to the product 3.12 due to operator error?
Is the Mechanical Assembly work cell laid out ergonomically with components & assembly tools 2.3 within easy reach? 2.4 Are mechanical items stored before and during use in a manner which prevents damage?
1
1
3.13 Are all hand tools needed by the operator listed with their descriptions on Work Instructions?
1
1
Is there evidence to demonstrate that a defect feedback process is in operation to Mechanical 3.14 Assembly?
Maximum Score 26
Pass %
90%
Outcome
Mechanical Assembly Audit Items
1. Depanelization
Is breakout tooling specially designed for the board or is a line-side Router or v-score machine used? Manual breakout = 0, 1.1 except for small support tabs in non-critical areas of PCB Can it be demonstrated that board flexing has been minimized and clearance is sufficient by 1.2 using such tooling? For v-scored boards, are boards positioned using a fixture so that the cutting tool and can only 1.3 cut occur along the v-score? Can it be demonstrated that the board is supported before and after the cut so as to prevent 1.4 board damage due to dropping? Does the press fit tooling use force feedback control that provides repeatable installation and 1.5 prevents PCB damage? 1.6 Has all tooling used at Mechanical Assembly been designed to minimize board flexing? 2. Line Set-Up
1
1
3.15 Are cosmetic standards are readily available to the assembly operator on the assembly line?
1
1
Comments: