基于ANSYS的平台式汽车大梁校正仪设计
基于ANSYS的车架结构优化设计

1.3 本文的主要研究内容
本文以某运油车的车架为研究对象, 运用 CATIA 软件对车架模型进行简化与 建立,利用 ANSYS 对车架进行参数定义,网格划分,作用力施加,自由度约束。 对车架进行包括弯曲工况、扭转工况、急减速工况、急转弯工况的静态分析,对 位移图与应力图进行分析, 为提高车架与整车的设计水平提供了理论基础,对提 高安全性与节能提供了理论价值。同时也对车架进行了模态分析,得出固有频率 与振型图, 提高整车的设计水平, 对提高乘坐舒适性与避免共振提供了理论支持。
2 基于 CATIA 与 ANSYS元分析分为三个阶段, 即前处理是对几何模型划分网格,建立能够求解 的有限元模型;处理是施加作用力,进行自由度约束,建立边界条件进行求解的 过程;后处理是使用户查看求解分析结果,分析计算问题的实质,方便后期研究 分析。 (1) 有限元法的分析步骤 有限元求解问题的基本步骤包括: ① 结构离散化。 ② 选择位移模式。 ③ 分析单元的力学特性。 ④ 把所有离散单元的平衡方程整合成一个整体平衡方程。 ⑤ 由平衡方程求解节点位移。 ⑥ 计算单元应变和应力。 (2) 有限元法的特点 ① 对复杂几何构形的适应性 单元具有良好的空间性, 并且具有不同的形状与连接方式,在实际的应用领 域中许多繁琐复杂不规则的结构都可以进行网格划分建立有限元模型。 ② 对各种物理问题的适用性 由于场函数形式并未受到限制,因此适用于各种力学,电磁学等有关问题, 而且还可以用于相互耦合的各种物理有关的问题[7]。 (3) ANSYS 单元库体系 ANSYS 单元库体系中有对各种问题分析时所需的单元类型,每种单元类型都 有一个特定的标识,例如,SOLID45,SHELL28,BEAM24 等单元类型,其数字表 示编号,数字前面的是表示单元类型的前缀[9],SOLID 表示实体单元,SHELL 表 示壳单元,BEAM 表示板单元。主要类型见表 2.1。
(完整版)1车架ANSYS建模过程
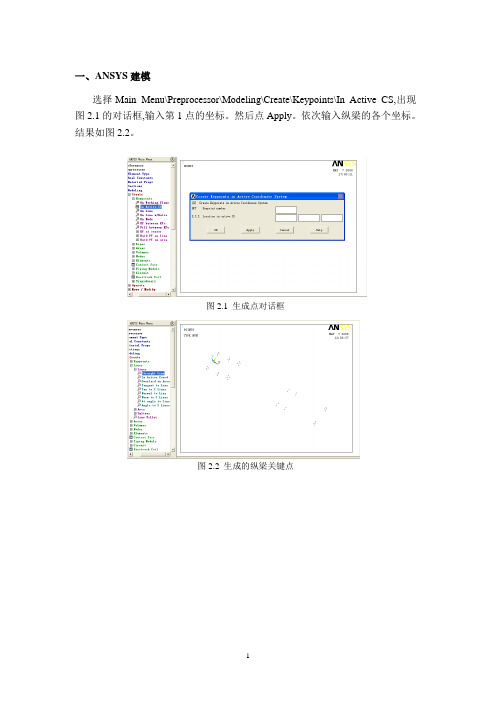
一、ANSYS建模选择Main Menu\Preprocessor\Modeling\Create\Keypoints\In Active CS,出现图2.1的对话框,输入第1点的坐标。
然后点Apply。
依次输入纵梁的各个坐标。
结果如图2.2。
图2.1 生成点对话框图2.2 生成的纵梁关键点图2.3 横梁关键点建立第3,4,5,6横梁在纵梁上的关键点。
选择MainMenu\Preprocessor\Modeling \Create\Keypoints\In Active CS命令。
copy各个横梁的点,以建立横梁翼板。
选择Main Menu\Preprocessor\Modeling\Copy\Keypoints,建立了图2.3中横梁关键点。
图2.4 车架骨架关键点将现所有点向Y轴的负方向偏移100mm,仍然用copy命令。
然后将所有点镜像Main Menu\Preprocessor\Modeling\Reflect\Keypoints,以xz平面为镜象中心。
结果如图2.4。
基本生成了NJ1030车架骨架点模型。
图2.5 车架轮廓将所有的关键点连接生成线(必须依次连接并且都在同一平面内)并如图2.5所示:Main Menu\Preprocessor\Modeling\Create\Lines\Straight Line。
将所有的线连接生成面(必须依次连接并且都在同一平面内),结果如图2.6:Main Menu\Preprocessor\Modeling\Create\Areas\Arbitrary\By Lines。
为了将车架所有的面连接起来以进行网格划分和对梁厚度的不同的设立,需要将所有的面粘合起来。
选择Main Menu\Preprocessor\Modeling\Operate\Booleans\Glue\Areas出现对话框,选择Pick ALL即可。
图2.6 NJ1030车架骨架几何模型至此NJ1030车架的有限元模型以在ANSYS中建立成功。
基于ansys汽车车身课程设计
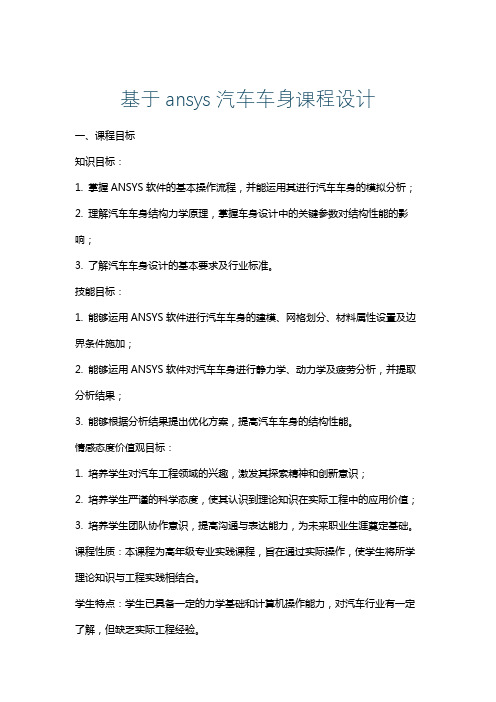
基于ansys汽车车身课程设计一、课程目标知识目标:1. 掌握ANSYS软件的基本操作流程,并能运用其进行汽车车身的模拟分析;2. 理解汽车车身结构力学原理,掌握车身设计中的关键参数对结构性能的影响;3. 了解汽车车身设计的基本要求及行业标准。
技能目标:1. 能够运用ANSYS软件进行汽车车身的建模、网格划分、材料属性设置及边界条件施加;2. 能够运用ANSYS软件对汽车车身进行静力学、动力学及疲劳分析,并提取分析结果;3. 能够根据分析结果提出优化方案,提高汽车车身的结构性能。
情感态度价值观目标:1. 培养学生对汽车工程领域的兴趣,激发其探索精神和创新意识;2. 培养学生严谨的科学态度,使其认识到理论知识在实际工程中的应用价值;3. 培养学生团队协作意识,提高沟通与表达能力,为未来职业生涯奠定基础。
课程性质:本课程为高年级专业实践课程,旨在通过实际操作,使学生将所学理论知识与工程实践相结合。
学生特点:学生已具备一定的力学基础和计算机操作能力,对汽车行业有一定了解,但缺乏实际工程经验。
教学要求:结合学生特点,注重实践操作,以案例教学为主,引导学生掌握课程目标所要求的知识和技能。
在教学过程中,关注学生情感态度价值观的培养,提高其综合素质。
通过课程学习,使学生能够独立完成汽车车身的设计与分析任务,为从事相关工作奠定基础。
二、教学内容1. ANSYS软件基本操作:包括软件安装、界面认识、基本操作流程介绍,使学生熟悉软件环境;对应教材章节:第1章 ANSYS软件概述与安装;2. 汽车车身结构力学原理:讲解汽车车身结构类型、力学特性,分析关键参数对结构性能的影响;对应教材章节:第2章 汽车车身结构力学基础;3. 汽车车身建模与网格划分:介绍汽车车身建模方法、网格划分技巧,指导学生实际操作;对应教材章节:第3章 汽车车身建模与网格划分;4. 材料属性设置与边界条件施加:讲解材料属性设置原则、边界条件类型及施加方法;对应教材章节:第4章 材料属性设置与边界条件施加;5. 汽车车身静力学分析:介绍静力学分析原理,指导学生进行汽车车身静力学分析;对应教材章节:第5章 静力学分析;6. 汽车车身动力学分析:讲解动力学分析原理,指导学生进行汽车车身动力学分析;对应教材章节:第6章 动力学分析;7. 汽车车身疲劳分析:介绍疲劳分析原理,指导学生进行汽车车身疲劳分析;对应教材章节:第7章 疲劳分析;8. 分析结果提取与优化:教授如何提取分析结果,根据结果提出优化方案;对应教材章节:第8章 分析结果处理与优化。
基于ANSYS的平台式汽车大梁校正仪设计-开题报告

架在受到撞击后,撞击力的传递将会造成纵梁前部发生变形。骨架拆下后没有合适固定很难采取一个 缓和的矫正力进行修复,另外修复完骨架后还需要对前纵梁进行修复。所以比较好的方法是进行就位 修理。但目前国内还有 60%的汽修厂没有专业的事故汽车修理设备,这将严重制约我国汽修业的发 展。因此每个汽修企业应该追踪和关注大梁校正仪技术发展趋势。
毕业设计(论文)开题报告
学生姓名 指导教师姓名
题目名称
院系 职称
汽车与交通工程学
院
讲师
从事 专业
专业、班级 车辆工程 是否外聘 □是■否
基于 ANSYS 的平台式汽车大梁校正仪设计
一、课题研究现状、选题目的和意义 1、研究现状 目前大梁校正仪有两种:框架式与平台式,也称欧式和美式,两类中各分国产进口两类。欧式平
未来 1-2 年大梁校正仪市场价格总体走势将平稳,专家的主要判断依据是,未来我国汽车车身大 梁校正设备整体质量水平和技术含量将不断提升,行业标准和技术门槛也不断提高,但国产化比例也 将大幅提高,需求量也不断上升,总体而言未来市场价格水平将呈平稳走势。不过由于近年来,汽保 生产商与日俱增,一些新势力大打价格战必然导致在制造上的偷工减料,导致质量缺陷,为防止这种 现象的发生,有实力的汽修设备企业应大力注重新产品的研究和开发,不断提高产品的性能和附加值, 并且在生产管理上多下功夫,大大降低生产成本,在使产品能够不断满足市场日益增长的需求的同时, 适当降低销售价格,提高产品和企业的市场竞争能力,提高市场占有率。
但就功能性而言,相比较欧式设备,劣势很明显:操作空间有限,操作复杂,费时费劲,且由于 环形处的死角问题导致了修理的死角,但基本能满足维修需要,而且由于设备价格有优势,4-12 万 左右,但是随着维修要求的不断提高,环形设备的技术升级和欧式设备的走俏,貌似不可避免。但就 目前市场上畅销的几种最强力品牌:奔腾,三重,卓越,杜卡,奔腾借助其强势的营销手段,市场占 有极高,但就产品功能性而言,各产品差异不大,就稳定性而言,奔腾和三重比较领先,但三重公司 长期致力于行走质量路线,营销劣势使其在市场占有上于奔腾有了一定差距,但价格较适宜,其他产 品价格虽低,但质量很难保证。
基于ANSYS Workbench的桥式起重机主梁仿真分析

基于ANSYS Workbench的桥式起重机主梁仿真分析作者:杨从从袁秀峰陈嘉磊樊一波来源:《山东工业技术》2018年第12期摘要:主梁是桥式起重机的主要组成部分和承载部件。
本文以40/16t-22.5m-20m A5桥式起重机主梁为研究对象,采用Solidedge建立其实体模型,并导入ANSYS Workbench对主梁进行了静力学和模态仿真分析。
得到主梁的等效应力云图、变形云图以及前6阶模态的固有频率和相对振型,对仿真结果进行了分析,为该主梁的优化设计提供了一定的理论基础。
关键词:桥式起重机;主梁;ANSYS Workbench;静力学分析;模态分析DOI:10.16640/ki.37-1222/t.2018.12.0070 引言智能制造是现代制造业发展的方向,为了提高效率,降低生产成本,人们越来越重视对制造设备的智能化发展。
桥式起重机在制造业智能化发展的进程中占据着至关重要的作用,其是物料搬运的大型设备,被搬运物体质量大,搬运频率高。
主梁是桥式起重机的主要组成部件和承载部件,主梁设计的好坏直接影响了整机的制造成本、工作性能、使用寿命等。
而主梁传统设计方法是模型简化后手工计算,与实际工况会有一定的偏差且计算复杂[1-2]。
基于此,本文以40/16t-22.5m-20m A5桥式起重机主梁为研究对象,采用Solidedge建立主梁的三围实体模型,并导入ANSYS Workbench对主梁进行了静力学和模态仿真分析,并对得到的等效应力云图、变形云图以及前6阶模态的固有频率和相对振型进行了分析。
即采用ANSYS Workbench软件从主梁的强度、刚度以及固有特性角度进行仿真研究。
为主梁在保证其刚度、强度、固有特性的前提下进一步优化结构,节省材料提供一定的理论基础和依据,具有一定的理论和实际意义[3-4]。
1 模型建立本文研究对象为40/16t-22.5m-20m A5桥式起重机的主梁,该主梁为偏轨箱型梁结构,主要由上、下盖板,主、副腹板,隔板,加强筋等焊接而成。
基于ANSYS的农用轻型载重汽车车架结构接触法计算与模态分析

基于ANSYS的农用轻型载重汽车车架结构接触法计算与模态分析0.引言现代汽车绝大多数都具有作为整车骨架的车架,其功用是支承连接汽车的各部件,并承受来自车内外的各种载荷。
车架是整个汽车的基体,农用轻型载重汽车的绝大多数部件和总成都是通过车架来固定其位置的。
因此,车架的性能在整车设计中就显得尤为重要。
1.利用ANSYS对整个车架结构进行计算和分析1.1车架模型的网格划分车架有限元接触分析的分析对象是车架在三维实体模型的基础上,通过单元属性定义、网格划分、摩擦接触单元、定义边界条件和施加载荷等前处理过程得到的三维模型。
车架的有限元模型可以作如下简化:(1)包括驾驶员在内的驾驶室重量平均分布在驾驶室与车架相接触的面积上;货箱质量及货箱载重量均布在货箱与车架相接触的面积上;发动机、离合器与变速器重量均匀分布在发动机、离合器与变速器与其支架相接触的平面上。
(2)不考虑钢板弹簧对车架的作用。
(3)忽略受载较小和对结构受力影响甚微的微小特征,如小孔、小半径的圆倒角。
根据以上假设,利用Pro\E软件与ANSYS软件的接口将建立好的三维模型导入到ANSYS软件中得到相对应的车架有限元模型,选用20节点实体单元划分的网格。
划分网格时应注意先将车架结构进行网格划分,然后再将铆钉进行网格划分。
以此得到比较满意的网格。
放大网格模型的一部分以看清楚单元。
由于结构对称,载荷分布也基本上对称,故取纵向对称的二分之一模型来计算,梁选用的是20节点实体单元Solid186单元,铆钉选用的是20节点实体单元Solid95单元,采用智能网格划分后,车架包括铆钉在内总的节点数为115871,单元数为56189。
将整个车架视为一个整体零件时,采用20节点实体单元Solid186单元且同样采用智能网格划分,总的节点数为104777,单元数为53047。
1.2加摩擦接触单元网格划分后,下一步工作就是加摩擦接触元,在板与板之间加摩擦接触元的同时,在铆钉孔的圆柱面与铆钉的圆柱面之间以及铆钉帽与板接触的圆环面与圆环面之间也加上摩擦接触元。
车辆工程毕业设计26基于ANSYS的平台式汽车大梁校正仪设计

摘要车身校正是通过一定的外力将因事故损坏或疲劳损坏的部位修复到车辆出场时技术标准"状态“的过程。
汽车在人们的日常生活中起着不可或缺的作用,当然有使用就会有损坏,而且损坏的情况也越来越严重,从而一些专门的修复工具也随之产生—平台式汽车车身校正设备。
目前,国内普遍采用的车身校正设备主要有框架式和平台式,其中平台式较多。
这种设备较为先进,国内外制造的设备一般都采用这种形式,是国际间比较流行的一种车身校正设备。
平台式车身校正设备主要包括有举升支架,工作台,加力塔及其连接机构。
本设计的目的旨在对平台式汽车大梁校正仪的二维设计及三维虚拟设计进行探索和实践,为校正仪的设计提供参考。
本设计是通过对现有设备的调查研究,再结合自己的想法设计一台结构简单,使用方便的平台式汽车大梁校正设备。
本设计首先利用AutoCAD进行二维设计计算及校核,再利用三维建模软件CATIA对汽车大梁校正仪的整机进行虚拟建模,最后利用有限元受力分析软件ANSYS,对关键部件进行有限元分析。
虚拟设计中首先利用三维建模软件CATIA对大梁校正仪整体三维实体进行建模,然后将关键部位零件文件类型另存为IGS格式,通过IGS格式将零件模型导入ANSYS进行有限元结构静力学分析,验证结果的可行性。
利用CATIA和ANSYS软件对平台式汽车大梁校正设备的设计开发完全是在虚拟的环境中进行的,通过更改技术参数就可以实现对设计方案的完善,缩短开发周期,提高设计质量和效率,降低研发成本。
这也是未来产品设计开发方法的发展方向。
关键字:大梁校正仪;结构设计;三维建模;虚拟装配;有限元分析ABSTRACTBody through certain correction is a force for accident damaged or fatigue damage repair to vehicles out of the technical standards “state” process.Car in People's Daily life plays an indispensable role, of course, have use will have damaged, and the damage situation of also more and more serious, which some special repair tools generates - using automotive calibration equipment.At present, the domestic car calibration equipment widely used are mainly frame type, including using more peaceful desktop.This equipment, advanced manufacturing equipment both at home and abroad are usually use this form, is international popular a kind of body calibration ing body calibration equipment mainly include lifting stents, workbench, strength tower and its connection institutions.This design is based on the investigation and study of existing equipment, coupled with his own idea design a simple structure, easy to use and using car girders of calibration ing three-dimensional modeling software CATIA, finite element stress analysis software ANSYS, the whole car girders is corrective on virtual modeling,the key components in finite element analysis.Firstly, the 3d modeling software to beam is corrective CATIA overall three-dimensional entity is modeled,then will key parts parts file types save as IGS format,through the IGS formats will import ANSYS finite element part modeling statics analysis, structure of the feasibility of the results of the ing CATIA and ANSYS software using cars for the design and development of calibration equipment beam is completely in a virtual environment.By changing the technical parameters can be achieved on the perfect design scheme, shorten the development cycle, improve the design quality and efficiency, reduce the r&d costs.This is the future product design and development method development direction.Key words:Girders calibration apparatus;Structure design;3D modeling;Virtual assembly;Finite element analysis目录摘要 (Ⅰ)Abstract (Ⅱ)第1章绪论 (1)1.1 研究背景 (1)1.2 研究的目的和意义 (1)1.3 课题研究的现状 (3)1.4 研究内容及研究方法 (4)1.4.1 研究内容 (4)1.4.1 研究方法 (4)1.5 承载式车身矫正原理介绍 (5)第2章大梁校正仪二维结构设计及校核 (6)2.1 简述平台式汽车大梁校正仪工作原理 (6)2.2 车身校正设备的特点 (6)2.3 车身校正设备的特点 (7)2.4 平台主要结构确定 (8)2.4.1 平台整体结构形式及基本组成 (9)2.4.2 平台表面设计 (10)2.4.3 选材 (10)2.4.4 平台支撑梁的校核 (10)2.5 平台后支撑架的主要结构确定 (12)2.5.1 平台后支撑架整体结构形式及基本组成 (12)2.5.2 平台支撑架的选材 (13)2.5.3 平台支撑架的校核 (15)2.6 拉塔的主要结构确定 (15)2.6.1 拉塔的主要结构形式及基本组成 (15)2.6.2 拉链固定装置的设计 (16)2.6.4 拉塔的选材 (18)2.6.5 拉塔的校核 (18)2.7 夹具的主要结构确定 (20)2.7.1 夹具的主要结构形式及基本组成 (20)2.7.2 夹具基座的主要结构 (21)2.7.3 夹具基座的选材 (21)2.7.4 夹具升降调节块的主要结构 (22)2.7.5 夹具升降调节块的选材 (22)2.7.6 夹钳体的主要结构 (22)2.7.7 夹钳体的选材 (23)2.7.8 夹钳体的校核 (23)2.7.8 螺栓与螺母的选侧 (24)2.8 举升臂的主要结构确定 (25)2.8.1 举升臂的主要结构 (25)2.8.2 举升臂的选材 (25)2.8.3 举升臂的校核 (25)第3章大梁校正仪的三维结构设计 (27)3.1 CATIA软件简介 (27)3.2利用CATIA进行三维建模 (28)3.2.1 平台的三维建模 (28)3.2.2 后支架的三维建模 (30)3.2.3 夹具基座的三维建模 (31)3.2.4 夹钳体的三维建模 (31)3.3 利用CATIA进行三维虚拟装配 (32)3.3.1 CATIA装配功能概述 (32)3.3.2装配的CATIA零件图 (33)3.2.3 CATIA整机装配图及爆炸图 (37)3.4 本章小结 (38)第4章大梁校正仪的有限元分析 (39)4.1 ANSYS有限元分析软件介绍 (39)4.1.1ANSYS软件简介 (39)4.2 ANSYS与CATIA接口的建立 (39)4.3利用ANSYS对主要零部件进行分析 (42)4.3.1定位夹具卡钳体的有限元分析 (42)4.3.2夹钳体受侧向力的有限元分析 (48)4.3.3后支架的有限元分析 (54)4.3.4前支架的有限元分析 (60)4.3.5举升臂的有限元分析 (65)结论 (72)参考文献 (73)致谢 (74)附录A (75)附录B (80)第1章绪论1.1研究背景由于汽车拥有量的不断增多,汽车使用过程中的损伤是不可避免的,如何使损伤后的汽车恢复良好的状态,一直是汽车维修行业的主体努力的主题。
基于ANSYS的桥梁检测车有限元分析及优化1

摘要桥梁在一个国家的交通运输和经济发展中占有十分重要的位置,而桥梁的检测则是保证桥梁安全运营的重要手段。
随着技术的发展,桥梁检测车已经发展成为专业桥梁检测领域中必不可少的专用设备,桁架式桥梁检测车更是代表了桥梁检测车的主流发展方向,具有广阔的市场前景。
本文的研究对象为QJS18C桁架式桥梁检测车,采用有限元法对该车结构进行了有限元分析和优化。
本文认真研究了桥梁检测车的结构组成和工作原理,对桥检车各组成部件进行了合理的模型处理和简化,利用有限元分析软件ANSYS的APDL语言,采用自底向上的建模方式,建立了各部件的有限元参数化模型。
按照真实情况采用合理的方式模拟各部件间的连接关系,将各部件组成一个整体。
通过以上工作建立了桁架式桥梁检测车整车的有限元分析模型。
本文首先对桥梁检测车整车结构进行了静力分析,选取了桥检车工作过程中常用的10种工况,按实际情况施加约束和载荷,获得了不同工况下各部件的应力分布和变形等详细力学性能;针对该10种工况,对上车工作装置进行了模态分析,确定了结构的固有频率和模态振型等信息,可避免结构在工作过程中发生共振现象。
然后取垂直臂为主要研究对象,采用接触单元来模拟垂直臂与滑块之间的滑动连接,得到了更为精细准确的结果,通过改变垂直臂的结构参数进行分析比较,可以看到不同参数变化对垂直臂性能的影响;取工作平台为主要研究对象,分析了伸缩臂的受力特点,按实际情况进行加载对危险工况下的滚轮和伸缩臂进行了接触分析,获得了接触区域的应力、应变分布,并比较了不同的滚轮材料对接触行为的影响,为设计过程中零部件的选型提供了理论依据。
最后为实现整车轻量化和提高整车的性能和稳定性,对关键部件进行了优化和改进,包括对支腿的板厚进行优化减重,对车架平台和一回转设计不合理的地方进行改进等。
改进的结果不仅减少了整车重量,而且提高了整车性能。
论文中提出的一些方法可用于同类型的桥检车的分析中,论文的分析成果为设计人员对结构的改进和优化提供了理论依据。
基于ANSYS的某轻型车车架纵梁优化设计

2 0 1 3年 8月
柳
州
师
专
学
报
V0 l _ 2 8 No . 4 Au g . 2 0 1 3
J o u mM o f L i u z h o u T e a c h e r s C o l l e g e
基于 A N S Y S的某 轻 型 车 车 架 纵 梁 优 化 设 计
Re s e a r c h o n Co g e ne r a t i o n Fa u l t Di a g no s i s Ba s e d o n Fu z z y Ne u r a l Ne t wo r k
J I ANG We n s h e n g
中图分类号 : T G 3 8 6 文献标识码 : A 文章编 号 : 1 0 0 3 - 7 0 2 0 ( 2 0 1 3 ) 0 4 - 0 1 5 2 - 0 4
0 引 言
某 公 司 开发 的整 体式轻 型 车 车架 , 车 架 满 载 后 出
现 车 身下 沉 , 严 重影 响 行 车 安 全 。针 对 这 些 问题 , 本
车架 满载 参数 见 表 1 。对 车 架满 载 弯 曲变 形 , 加 载时将 车 架载 荷乘 以 动载荷 系 数 , 模 拟 行 车 时 的 载 荷
波动 , 所 得 动 载 荷 施 加 在 相 应 的 节 点 上 。 结 果 如 图
2~图 5所 示 。
移, 将 前后 车 轮悬 架 处 用 赋 予 刚度 的 弹簧 单 元 模 拟 ,
为 2 1 1 G Pa 。
1 车 架 结 构 ANS YS有 限 元 模 型 建 立
由于本 文 车架 结 构 优 化 设 计 时 使 用 有 限元 软 件
基于ANSYS与MATLAB的桥式起重机主梁优化设计
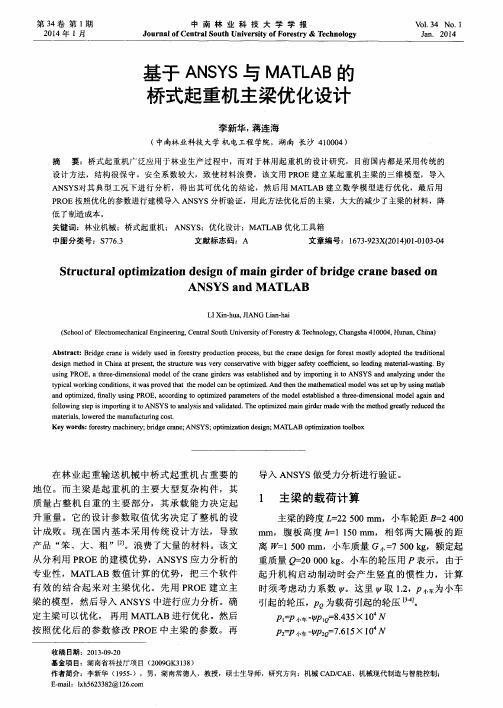
yp t i c a l wo r k i n g c o n d i t i o n s , i t wa s p r o v e d t h a t t h e mo d e l c a n b e o p t i mi z e d . An d t h e n t h e ma he t ma t i c a l mo d e l wa s s e t u p b y u s i n g ma t l a b
第3 4卷 第 1 期 2 0 1 4年 1月
中 南 林 业 科 技 大 学 学 报
J o u r n a l o f Ce n t r a l S o u t h Un i v e r s i t y o f Fo r e s t r y& T e c h n o l o g y
LI Xi n - h u a , J I ANG Li a n — h a i
( S c h o o l o f E l e c t r o me c h a n i c a l E n g i n e e i r n g , C e n r t a l S o u t h Un i v e r s i t y o f F o r e s t r y& T e c h n o l o g y , Ch a n g s h a 4 1 0 0 0 4 , Hu n a n , C h i n a )
、 bl _ 3 4 NO . 1
J a n. 2A T L A B的 桥 式起 重机 主梁优 化设计
李 新华 , 蒋连海
( 中南林 业科技 大学 机 电工程 学院,湖南 长 沙 4 1 0 0 0 4 )
摘 要 :桥式 起重 机广泛应 用于林 业生 产过程 中,而对 于林 用起 重机 的设计研 究 , 目前 国内都是采 用传 统的 设 计方 法,结 构很保 守 。安全 系数较 大 ,致 使 材料 浪费 。该文 用 P R O E建立 某起 重机 主梁 的三维 模 型,导入 A NS YS 对其 典型 工况 下进 行分 析,得 出其 可优 化 的结论 ,然后 用 MAT L A B建立 数 学模型 进行 优化 ,最后 用 P R O E按 照优 化的参数进行 建模 导入 A NS YS分析验证 ,用此方法优化后 的主梁,大大 的减少 了主梁 的材料 ,降
基于ANSYS的东风货车车架仿真和有限元分析

基于ANSYS的东风货车车架仿真和有限元分析摘要:货车车架是车子的关键受力部分,货车上受到的来自内部和外界的各种载荷最后都要传递给货车车架,所以车架结构强度的大小是货车整体设计的关键因素之一。
在汽车设计中,有限元分析法可以对汽车进行动态性能、静态性能和车架结构分析,从而,对车身结构优化,提高整车性能、缩短设计时间。
有限元软件ANSYS具有独一无二的分析优化功能和良好的可靠性,在结构动力分析、静力分析和优化设计方面具有出色的表现。
本文以东风货车为研究对象,运用Pro/E和ANSYS软件,先创建货车车架的三维实体建模型,在对其动态分析、静态分析及模态分析研究。
以实体为基础进行建立他的简单尺寸来优化,以车架的截面面积作为参数,把他最小的体积作为其最终结果。
简单介绍Pro/E三维建模的简化技巧和ANSYS结构优化设计时的基本思想和方法。
通过对东风货车车架结构的有限元仿真和有限元分析,积累许多宝贵的经验,得到一些重要数据,在以后货车车架的设计优化中有借鉴和指导作用。
关键词:东风货车车架;ANSYS;Pro/E;静态分析;动态分析;模态分析Dongfeng truck frame based on ANSYS simulation and finite element analysisAbstract:Truck frame is the car key part of the force, van from internal and external load, the last to be passed on to the truck frame, so the size of frame structure strength is one of the key factors of the overall design of the truck. In the automobile design, the finite element analysis method can be used to analyze the dynamic performance, static performance and frame structure of the vehicle, so as to improve the performance of the vehicle and shorten the design time. Finite element software ANSYS has a unique analysis optimization function and good reliability, and has excellent performance in structural dynamic analysis, static analysis and optimization design.In this paper, Dongfeng truck as the research object, the use of Pro / E and ANSYS software, to create a three-dimensional model of the truckframe, the dynamic analysis, static analysis and modal analysis. Optimization structure based on the entity unit model to create the frame size is simple constraints, with the frame of the longitudinal cross section area size as a design parameter, the frame structure of the total volume minimization as optimization the final result. The simplified technique of Pro/E 3D modeling and the basic idea and method of ANSYS structure optimization are introduced in this paper. Through the finite element simulation and finite element analysis of the frame structure of the Dongfeng truck, accumulated many valuable experiences, and get some important data, which have reference and guidance in the design optimization of the truck frame.Key words:Dongfeng truck frame;ANSYS; Pro/E; Static analysis; Dynamic analysis; The modal analysis基于ANSYS的东风货车车架仿真和有限元分析1 引言1.1 课题的目的和意义当代汽车工业中,有限元分析法在已经普遍应用在车辆骨架的研发里面。
CAE-ANSYS在汽车设计中的应用

一、汽车整车及车身静动力学分析
利用ANSYS结构静力学和结构动力学分析功能,可以对汽车整车及车身进行结构力学方面的仿真 。这种仿真得益于ANSYS具有先进的模型建立技术以及完善的包括模态、单多点响应谱、随机振动 、瞬态等在内的线性和非线性静动力学分析功能。
南汽IVECO客车的国产化过程中,车身出 现了开裂现象,请国外专家会诊加强后仍 未解决问题,后经东南大学进行了整车车 架的静动力分析,找出了原因,并依据 ANSYS有限元计算结果进行了加强,最终 解决了困扰已久的质量问题,左图为车架 的振动模态。
2023年4月1日
ADAPCO公司用ANSYS分析V6 缸发动机,节点数343,252个,单元数215,114个 ,进行了热分析、结构分析/动力分析、热-结构耦合分析。
2023年4月1日
发动机总体结构分析
2023年4月1日
连接部位详细分析模型
2 曲柄连杆机构运动件 :活塞组、连杆组、曲轴组
曲柄连杆机构的运动件是发动机中的最主要部件,也是热负荷、机械 负荷最高的部件, 因而也是整个发动机中分析要求最高的部件。ANSYS热变形、 热应力、蠕变分析能力可计算出活塞、活塞环工作状态下的形状及应力,为活 塞形状设计、气缸与活塞间隙设计、热强度设计提供了准确的依据,从而可保 证气缸的密封性要求及活塞组工作可靠性的要求。活塞组的热分析同时又为冷 却系、润滑系的设计提供了设计依据。
万向联轴器整体模型
法兰接头
轴承座
十字轴、圆柱套及垫片
连接螺栓
辊端接头及衬板等
2023年4月1日
有限元模型
有限元分析结果 - 各部件上应力分布
主要接触面上的接触压力分布
2023年4月1日
十字轴上的应力分布及疲劳寿命分布
基于ANSYS的框架式汽车大梁校正仪设计-任务书

毕业设计(论文)任务书学生姓名系部汽车与交通工程学院专业、班级指导教师姓名职称讲师从事专业车辆工程是否外聘□是■否题目名称基于ANSYS的框架式汽车大梁校正仪设计一、设计(论文)目的、意义大梁校正仪即对车身矫正,是指通过一定的外力将因事故损坏或疲劳损坏的部位修复到车辆出厂时技术标准状态的过程,在汽车修理厂及4S店被广泛应用。
分析框架式汽车大梁校正仪的结构形式及工作原理,完成校正仪的方案设计及校核计算,利用AutoCAD完成校正仪二维总体结构设计及零部件设计,利用CATIA建立校正仪三维实体模型,并进行整机虚拟装配,将关键零部件模型通过专用模型数据转换接口导入ANSYS软件进行有限元分析,获得校正仪在载荷工况作用下的应力、应变及变形状。
在产品制造之前就可以发现并更正设计缺陷,完善设计方案,缩短开发周期,提高设计质量和效率,为生产实际提供理论支持。
二、设计(论文)内容、技术要求(研究方法)1、设计内容技术参数:剪刀式垂直升降平台,要求任何事故车上、下车十分方便,降到最低点为230mm,最大举升高度1060mm,电动液压泵控制,工作台长度2300mm,工作台高度230-1060mm,工作台宽度950mm,拉塔工作范围360度,液压系统最大工作压力16Mpa,气源压力要求0.8Mpa,拉塔牵引最大拉力70KN,整机重量600kg。
分析框架式汽车大梁校正仪的结构形式及工作原理,完成校正仪的方案设计及校核计算,利用AutoCAD完成校正仪二维总体结构设计及零部件设计,利用CATIA建立校正仪三维实体模型,并进行整机虚拟装配,将关键零部件模型通过专用模型数据转换接口导入ANSYS软件进行有限元分析,获得校正仪在载荷工况作用下的应力、应变及变形状。
2、技术要求(1)校正仪方案设计及校核计算;(2)利用AutoCAD软件完成校正仪二维总体结构设计及零件设计;(3)利用CATIA软件完成校正仪三维建模及虚拟装配;(4)利用ANSYS软件完成关键零件有限元分析。
基于ANSYS的框架式汽车大梁校正仪设计-开题报告

毕业设计(论文)开题报告学生姓名系部汽车与交通工程学院专业、班级指导教师姓名职称讲师从事专业车辆工程是否外聘□是■否题目名称基于ANSYS的框架式汽车大梁校正仪设计一、课题研究现状、选题目的和意义1、研究现状近年来随着中国汽车市场的快速发展,汽车维修行业也如雨后春笋般迅速涌现。
在竞争激烈的售后服务行业中,如何能够提高自己的维修质量水平是所有企业为了在竞争中胜出的核心所在。
而维修设备的优劣成为重要的衡量指标,汽车大梁校正仪是现代汽车售后服务体系中至关重要的设备之一,针对因事故碰撞损坏以及疲劳受损的部位进行原型恢复,以达到汽车大梁出厂值的技术数据标准。
目前,市场上的汽车大梁校正仪主要分为两种:框架式和平台式。
据有关数据统计:目前我国汽修企业每年对汽车大梁校正仪的需求量大约在1000台左右,而据估计约目前有60%的汽修企业尚没有专业的维修设备,这一状况严重制约着我国汽车维修行业技术的整体水平的提高,所以从市场分析来看它的需求量将会呈现出上升的趋势。
框架式汽车大梁校正仪目前是市场上主流的产品之一。
它具有使用方便,移动灵活,占地面积小等特点。
此产品很受中小型维修企业的青睐。
此前市面上产品主要由欧洲及美国设计制造,在这其中美式大梁校正仪凭借价格优势及外观而市场占有率较高,但随着维修质量要求的提高,操作设备的不断升级,欧式凭借其功能的强大,操作灵活及占地面积小等优势逐渐在市场上走俏。
但仍然只是少数维修企业及汽车4S店会购置进口设备。
90年代末,在我国出现了一些制造汽车大梁校正仪的中小型企业。
由于起步较晚,所以目前多数企业是借鉴国外的先进技术。
随着时间的推移,目前市场上自主的品牌已经逐渐成熟起来,并且在不断地扩大销售网络于全省,基本在各大省会城市均有销售代理,且价格一般比较低廉,多数在3-4万元左右。
但质量水平,技术先进性等方面与进口品牌还有一定的差距,而且产品类型主要以平台式为主。
由此可见目前中国汽车维修设备市场对框架式大梁校正仪的需求将会上升。
基于ANSYS的汽车车架的建模与模态分析
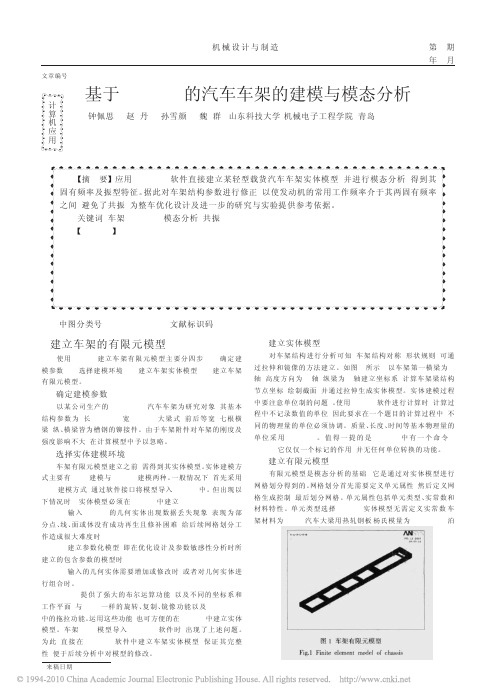
用
ZHONG Pei- si, ZHAO Dan, SUN Xue- yan, WEI Qun
( Shandong Science & Technology University, Qingdao 266510, China)
!!!!!!!!!!!!!!!!!!!!!!!!!!!!!!!!!!!!!!!!!!!" 【摘 要】应用 ANASYS 软件直接建立某轻型载货汽车车架实体模型, 并进行模态分析, 得到其
2 模态计算与分析
于发动机的怠速频率 25Hz, 不易发生共振; ( 2) 发动机常见工作频 率 范 围 为( 48 ̄65) Hz, 车 架 第 三 阶 频
率 52.237 落在范围之内, 此时车架易与发动机发生共振。车架 第三阶模态振型, 如图 2 所示。
由振动力学可知, 固有频率和振型均取决于系统的 M 阵和
图 1 车架有限元模型 Fig.1 Finite element model of chassis
* 来稿日期: 2007- 10- 22
第6期
钟佩思等: 基于 ANSYS 的汽车车架的建模与模态分析
- 53 -
松比为 0.3, 材料密度为 7800kg/m3。网格生成控制采用智能网格 划分, 单元划分尺度控制为 9。最后划分网格得到车架有限元模 型。共划分网格单元 115462 个, 节点 41741 个。车架有限元模型 如图 1 所示。利用该有限元模型, 对车架进行模态分析。
That can avoid resonance effectively. At the same time, the reference for optimum design of the whole truck
and further research is offered.
基于ANSYS的框架式汽车大梁校正仪设计
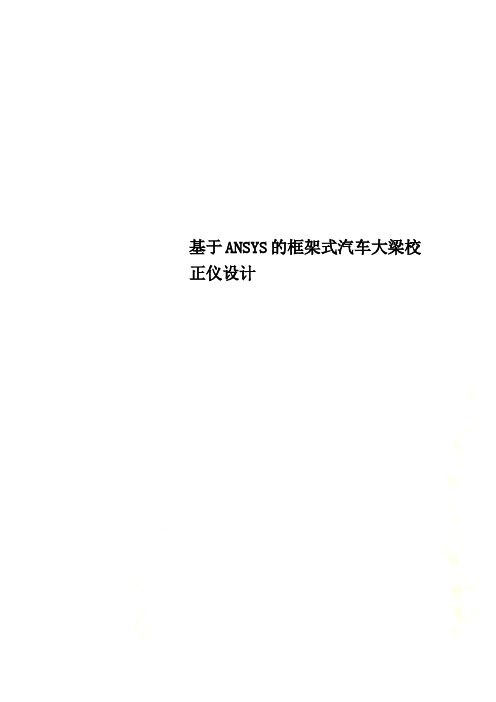
基于ANSYS的框架式汽车大梁校正仪设计目录第1章绪论 (1)1.1 选题背景,研究目的及意义 (1)1.2 国内外研究现状 (1)1.2.1 大梁校正仪的发展历史 (1)1.2.2 国内外研究状况及结果 (2)1.3 研究内容及研究方法 (2)1.3.1 研究内容 (2)1.3.2 研究方法 (3)第2章校正仪的整体结构设计 (4)2.1 简述框架式汽车大梁校正仪工作原理 (4)2.2 举升机构主要结构确定 (4)2.2.1 举升机构整体结构形式及基本组成 (4)2.2.2 举升机构各零部件安装位置及润滑 (5)2.3 举升平台及定位夹具主要结构确定 (5)2.3.1 举升平台整体结构形式及基本组成 (5)2.3.2 定位夹具整体结构形式及基本组成 (6)2.4 拉塔的主要结构确定 (6)2.4.1 拉塔横梁处整体结构形式及基本组成 (6)2.4.2 拉塔柱的结构形式及基本组成 (7)2.5 其它附件 (7)2.6 确定框架式大梁校正仪各结构尺寸及材料 (7)2.6.1 建立待修汽车基本参数模型 (8)2.6.2 校正仪底部结构部分主要尺寸及材料的确定 (8)2.6.3 校正仪中间结构部分尺寸及材料的确定 (8)2.6.4 校正仪上部平台结构尺寸及材料的确定 (9)2.6.5 定位夹具的尺寸及材料的确定 (11)2.6.6 拉塔组件的尺寸及材料的确定 (12)2.6.7 方凳及斜坡板凳的尺寸确定 (13)2.7 设备各部件质量的估算及设计举升质量 (13)2.7.1 估算拉塔组件的质量 (14)2.7.2 估算平台上设备的质量 (14)2.7.3 估算平台中部的质量 (14)2.7.4 估算底板处的质量 (15)2.7.5 实际设计举升质量 (15)2.8 本章小结 (15)第3章校正仪的力学分析及校核 (16)3.1 双铰接剪刀式举升机构的力学模型 (16)3.1.1 举升机构力学模型建立与分析 (16)3.1.2 举升机构主要关系参数的确定 (17)3.2 液压机构力的分析与计算 (17)3.2.1 确定载荷与液压缸推力的关系 (17)3.2.2 计算液压缸的推力 (18)3.3 举升机构的力学分析与计算 (19)3.3.1 举升机最低状态时,各臂受力情况 (19)3.3.2 举升机举升到最高位置时,各臂受力情况 (20)3.4 定位夹具及拉塔的力学分析与计算 (22)3.4.1 定位夹具的受力分析 (22)3.4.2 拉塔的受力分析 (22)3.5 主要零部件的强度校核 (23)3.5.1 举升臂AOB的强度校核 (23)3.5.2 举升臂COD的强度校核 (25)3.5.3 液压缸上端支承轴的强度校核 (27)3.5.4 连接举升臂销轴的强度校核 (27)3.5.5 平台内横梁的强度校核 (28)3.5.6 定位夹具的强度校核 (29)3.5.7 定位夹具支撑横梁的强度校核 (30)3.5.8 拉塔的强度校核 (31)3.5.9 拉塔处液压缸支撑销轴的强度校核 (32)3.6 本章小结 (33)第4章校正仪液压系统的选择与计算 (34)4.1 液压系统的选择 (34)4.1.1液压系统的介绍 (34)4.1.2液压系统的选型 (34)4.2 液压系统的计算 (35)4.2.1 举升处液压缸行程的计算 (35)4.2.2 举升处液压系统工作压力的计算 (36)4.2.3 关于拉塔处液压系统的相关选择 (36)4.3 本章小结 (36)第5章校正仪三维建模与整机装配 (37)5.1 CATIA软件简介 (37)5.2 利用CATIA进行三维建模 (38)5.2.1 底坐板的建立 (38)5.2.2 举升臂AOB的建立 (39)5.2.3 液压缸支承轴的建立 (39)5.2.4 上平台的建立 (40)5.2.5 夹具的建立 (40)5.2.6 拉塔柱的建立 (42)5.3 整机装配 (42)5.3.1CATIA装配功能概述 (43)5.3.2 装配的CATIA零件图 (43)5.3.3CATIA整机装配图及爆炸图 (48)5.4 本章小结 (50)第6章校正仪主要零部件有限元分析 (51)6.1 ANSYS有限元分析软件介绍 (51)6.2 ANSYS与CATIA接口的建立 (51)6.3利用ANSYS对主要零部件进行分析 (52)6.3.1定位夹具卡钳的有限元分析 (52)6.3.2液压缸支撑轴的有限元分析 (56)6.3.3举升臂的有限元分析 (59)6.3.4拉塔柱的有限元分析 (62)6.4 本章小结 (65)结论 (66)参考文献 (67)致谢 (68)附录A (69)附录B (72)附录C (73)附录D (74)第1章绪论1.1选择背景、研究目的及意义随着汽车市场的不断发展与壮大,与之相协调的汽车维修行业也迅速发展起来。
汽车钣金-大梁校正仪

大梁校正仪大梁校正仪称车身校正架是一个用液压设备拉拔校正大的损伤的结构。
一、校正台及附件校正台是校正仪最主要的基础部件,由工作平台来钳辅助支撑上架桥板等部件组成。
1.校正仪---是一个框架式平台夹钳辅助支撑测量系统等置于其上是用于车身测量固定的基础;2.夹钳—通过夹紧轿车裙边来固定车辆可以在工作台平面上多处位置安装具有调节高度的功能;3.辅助支撑—主要有底座调整组件及定位附件等部件组成;4.上架桥板—便于车辆上下工作台;5.下拉过轮及脚踏板----下拉过轮主要用于牵引方向引变为下牵引。
脚踏板---方便于工作人员工作。
二、校正技术1.校正仪的使用,车辆上架前的准备---校正设备准备到位,工作台上的夹钳辅助支撑测量支架等部件,拉塔转向一边。
2.车辆上架,将上架桥板放置工作台一端,将等待维修车辆置于工作台上,等待维修车辆尽量对称工作台中心轴线上停放。
大致测量车身长度轴距裙边间宽度,以便合理调整夹钳的位置于精确放置测量支架,利用举升机装置将等待维修车辆抬升到一定高度夹钳分别放置在汽车两侧,裙边下方,调节好夹钳位置同等高度,将汽车裙边夹紧并且锁定;汽车定位后在车底前部后部适当位置辅助支撑进行辅助定位;3.测量支架的放置,将测量导轨放置于等待维修车辆底盘下方工作台的枕木上,可以利用底盘测尺来调整测量导轨的位置,使测量导轨正对汽车中心线,再用紧固块固定测量导轨,然后可以用龙门测量架和底盘测尺放在测量导轨上,即可对车辆进行测量;4.校正操作,根据车辆变形损坏情况选择拉塔的校正位置方向及角度,针对变形部位选择夹具,必要时可以根据变形部位角度自制些实用工具配合拉塔进行校正,校正时,灵活运用边校正,边测量,最终达到技术要求为止。
三、车身结构的一般校正过程1.了解校正设备的使用及安全过程;2.分析车辆变形成变,确定校正部位;3.固定车辆;4.连接定位拉伸链;5.检查夹钳和对正情况,有计划进行拉伸校正。
四、大梁校正仪操作安全注意事项1.根据说明正确使用校正设备;2.在没有指导情况下:非熟练人员或未经过培训的人员不得操作校正设备;3.校正拉伸时,必须不定时,检查夹钳,确保紧固;4.使用与校正仪配套的使用设备及拉件链;5.链条必须稳固,拉伸过程,以防滑脱;6.在有人车上或下面工作时,禁止校正或使用千斤顶支撑车辆;7.严禁人员或非工作人员与拉伸链处在一条直线上以免发生链条断裂夹具滑落或钢板撕断,造成伤害事故;8.校正气割拉伸时,必须切断蓄电池电源;9.初次拉伸时,必须检查夹钳,有可能会有所轻微松动。
- 1、下载文档前请自行甄别文档内容的完整性,平台不提供额外的编辑、内容补充、找答案等附加服务。
- 2、"仅部分预览"的文档,不可在线预览部分如存在完整性等问题,可反馈申请退款(可完整预览的文档不适用该条件!)。
- 3、如文档侵犯您的权益,请联系客服反馈,我们会尽快为您处理(人工客服工作时间:9:00-18:30)。
摘要车身校正是通过一定的外力将因事故损坏或疲劳损坏的部位修复到车辆出场时技术标准"状态“的过程。
汽车在人们的日常生活中起着不可或缺的作用,当然有使用就会有损坏,而且损坏的情况也越来越严重,从而一些专门的修复工具也随之产生—平台式汽车车身校正设备。
目前,国内普遍采用的车身校正设备主要有框架式和平台式,其中平台式较多。
这种设备较为先进,国内外制造的设备一般都采用这种形式,是国际间比较流行的一种车身校正设备。
平台式车身校正设备主要包括有举升支架,工作台,加力塔及其连接机构。
本设计的目的旨在对平台式汽车大梁校正仪的二维设计及三维虚拟设计进行探索和实践,为校正仪的设计提供参考。
本设计是通过对现有设备的调查研究,再结合自己的想法设计一台结构简单,使用方便的平台式汽车大梁校正设备。
本设计首先利用AutoCAD进行二维设计计算及校核,再利用三维建模软件CATIA对汽车大梁校正仪的整机进行虚拟建模,最后利用有限元受力分析软件ANSYS,对关键部件进行有限元分析。
虚拟设计中首先利用三维建模软件CATIA对大梁校正仪整体三维实体进行建模,然后将关键部位零件文件类型另存为IGS格式,通过IGS格式将零件模型导入ANSYS进行有限元结构静力学分析,验证结果的可行性。
利用CATIA和ANSYS软件对平台式汽车大梁校正设备的设计开发完全是在虚拟的环境中进行的,通过更改技术参数就可以实现对设计方案的完善,缩短开发周期,提高设计质量和效率,降低研发成本。
这也是未来产品设计开发方法的发展方向。
关键字:大梁校正仪;结构设计;三维建模;虚拟装配;有限元分析ABSTRACTBody through certain correction is a force for accident damaged or fatigue damage repair to vehicles out of the technical standards “state” process.Car in People's Daily life plays an indispensable role, of course, have use will have damaged, and the damage situation of also more and more serious, which some special repair tools generates - using automotive calibration equipment.At present, the domestic car calibration equipment widely used are mainly frame type, including using more peaceful desktop.This equipment, advanced manufacturing equipment both at home and abroad are usually use this form, is international popular a kind of body calibration ing body calibration equipment mainly include lifting stents, workbench, strength tower and its connection institutions.This design is based on the investigation and study of existing equipment, coupled with his own idea design a simple structure, easy to use and using car girders of calibration ing three-dimensional modeling software CATIA, finite element stress analysis software ANSYS, the whole car girders is corrective on virtual modeling,the key components in finite element analysis.Firstly, the 3d modeling software to beam is corrective CATIA overall three-dimensional entity is modeled,then will key parts parts file types save as IGS format,through the IGS formats will import ANSYS finite element part modeling statics analysis, structure of the feasibility of the results of the ing CATIA and ANSYS software using cars for the design and development of calibration equipment beam is completely in a virtual environment.By changing the technical parameters can be achieved on the perfect design scheme, shorten the development cycle, improve the design quality and efficiency, reduce the r&d costs.This is the future product design and development method development direction.Key words:Girders calibration apparatus;Structure design;3D modeling;Virtual assembly;Finite element analysis目录摘要 (Ⅰ)Abstract (Ⅱ)第1章绪论 (1)1.1 研究背景 (1)1.2 研究的目的和意义 (1)1.3 课题研究的现状 (3)1.4 研究内容及研究方法 (4)1.4.1 研究内容 (4)1.4.1 研究方法 (4)1.5 承载式车身矫正原理介绍 (5)第2章大梁校正仪二维结构设计及校核 (6)2.1 简述平台式汽车大梁校正仪工作原理 (6)2.2 车身校正设备的特点 (6)2.3 车身校正设备的特点 (7)2.4 平台主要结构确定 (8)2.4.1 平台整体结构形式及基本组成 (9)2.4.2 平台表面设计 (10)2.4.3 选材 (10)2.4.4 平台支撑梁的校核 (10)2.5 平台后支撑架的主要结构确定 (12)2.5.1 平台后支撑架整体结构形式及基本组成 (12)2.5.2 平台支撑架的选材 (13)2.5.3 平台支撑架的校核 (15)2.6 拉塔的主要结构确定 (15)2.6.1 拉塔的主要结构形式及基本组成 (15)2.6.2 拉链固定装置的设计 (16)2.6.4 拉塔的选材 (18)2.6.5 拉塔的校核 (18)2.7 夹具的主要结构确定 (20)2.7.1 夹具的主要结构形式及基本组成 (20)2.7.2 夹具基座的主要结构 (21)2.7.3 夹具基座的选材 (21)2.7.4 夹具升降调节块的主要结构 (22)2.7.5 夹具升降调节块的选材 (22)2.7.6 夹钳体的主要结构 (22)2.7.7 夹钳体的选材 (23)2.7.8 夹钳体的校核 (23)2.7.8 螺栓与螺母的选侧 (24)2.8 举升臂的主要结构确定 (25)2.8.1 举升臂的主要结构 (25)2.8.2 举升臂的选材 (25)2.8.3 举升臂的校核 (25)第3章大梁校正仪的三维结构设计 (27)3.1 CATIA软件简介 (27)3.2利用CATIA进行三维建模 (28)3.2.1 平台的三维建模 (28)3.2.2 后支架的三维建模 (30)3.2.3 夹具基座的三维建模 (31)3.2.4 夹钳体的三维建模 (31)3.3 利用CATIA进行三维虚拟装配 (32)3.3.1 CATIA装配功能概述 (32)3.3.2装配的CATIA零件图 (33)3.2.3 CATIA整机装配图及爆炸图 (37)3.4 本章小结 (38)第4章大梁校正仪的有限元分析 (39)4.1 ANSYS有限元分析软件介绍 (39)4.1.1ANSYS软件简介 (39)4.2 ANSYS与CATIA接口的建立 (39)4.3利用ANSYS对主要零部件进行分析 (42)4.3.1定位夹具卡钳体的有限元分析 (42)4.3.2夹钳体受侧向力的有限元分析 (48)4.3.3后支架的有限元分析 (54)4.3.4前支架的有限元分析 (60)4.3.5举升臂的有限元分析 (65)结论 (72)参考文献 (73)致谢 (74)附录A (75)附录B (80)第1章绪论1.1研究背景由于汽车拥有量的不断增多,汽车使用过程中的损伤是不可避免的,如何使损伤后的汽车恢复良好的状态,一直是汽车维修行业的主体努力的主题。
尤其是汽车车身由结构式向整体式发展,对汽车车身修理行业推出了越来越多的技术要求。
在汽车碰撞修理包括许多方面的知识,如车身矫正,喷漆、焊接,设备维修等。
许多维修设备生产厂家投入了大量的人力物力财力开发和研制车身矫正设备,取得了许多应我成果,并投入生产使用。
本课题在意识到车身校正维修中越发重要之后,经过老师仔细研究选择的,在本次设计也中,主要研究的是车身校正。
经过对市场多家汽车维修厂调查发现,有的仍然是靠维修技工的经验来进行校正工作。
有的采用已经使用了很久的陈旧设备,只有几家从国外引进了先进的设备并投入使用。
令我感到遗憾的是,有几家维修厂引进先进的设备却放置不用。
反而仍用原来的陈旧设备。
经过询问得知,维修工人认为新设备虽然先进,但是使用起来相当复杂,而且维修结果也相差无几。
带着这一问题,结合我的设计课题—平台式车身校正设备设计,我找到了我的指导老师—王强老师,一同研究了先进的进口设备之后,结合目前我国维修行业的现状,通过自己的思考和老师的指导,设计一台既能达到维修目的又操作简单方便易学易用的平台是车身校正仪。