2AO.1.3硼扩散
硼磷扩散原理以及过程
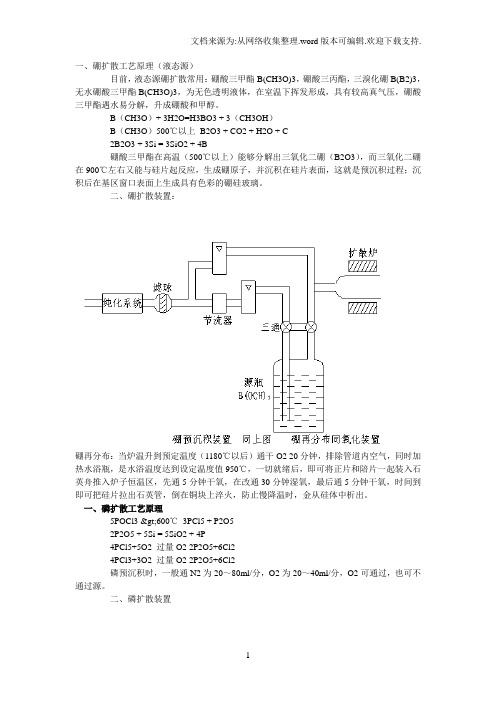
一、硼扩散工艺原理(液态源)目前,液态源硼扩散常用:硼酸三甲酯B(CH3O)3,硼酸三丙酯,三溴化硼B(B2)3,无水硼酸三甲酯B(CH3O)3,为无色透明液体,在室温下挥发形成,具有较高真气压,硼酸三甲酯遇水易分解,升成硼酸和甲醇。
B(CH3O)+ 3H2O=H3BO3 + 3(CH3OH)B(CH3O)500℃以上B2O3 + CO2 + H2O + C2B2O3 + 3Si = 3SiO2 + 4B硼酸三甲酯在高温(500℃以上)能够分解出三氧化二硼(B2O3),而三氧化二硼在900℃左右又能与硅片起反应,生成硼原子,并沉积在硅片表面,这就是预沉积过程;沉积后在基区窗口表面上生成具有色彩的硼硅玻璃。
二、硼扩散装置:硼再分布:当炉温升到预定温度(1180℃以后)通干O2 20分钟,排除管道内空气,同时加热水浴瓶,是水浴温度达到设定温度值950℃,一切就绪后,即可将正片和陪片一起装入石英舟推入炉子恒温区,先通5分钟干氧,在改通30分钟湿氧,最后通5分钟干氧,时间到即可把硅片拉出石英管,倒在铜块上淬火,防止慢降温时,金从硅体中析出。
一、磷扩散工艺原理5POCl3 >600℃3PCl5 + P2O52P2O5 + 5Si = 5SiO2 + 4P4PCl5+5O2 过量O2 2P2O5+6Cl24PCl3+3O2 过量O2 2P2O5+6Cl2磷预沉积时,一般通N2为20~80ml/分,O2为20~40ml/分,O2可通过,也可不通过源。
二、磷扩散装置磷扩散源POCl3是无色透明有窒息性气味的毒性液体,要求扩散系统密封性好,源瓶进出口两端最好用聚四氟乙烯或聚氯乙烯管道连接。
若用其他塑料管或乳胶管连接易被腐蚀,就需要经常更换。
接口处最好用封口胶,由系统流出气体应通过排风管排到室外,不要泄漏在室内。
源瓶要严加密封,切勿让湿气进入源瓶。
因为三氯氧磷吸水汽而变质,做扩散温度上不去。
2POCl3+3H2O=P2O5+5HCl发现三氟氧磷出现淡黄色就不能使用。
topcon电池二次硼扩散的作用_解释说明以及概述
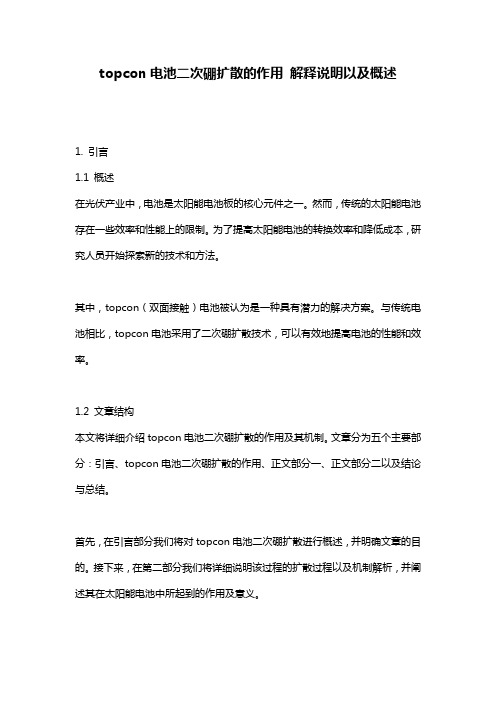
topcon电池二次硼扩散的作用解释说明以及概述1. 引言1.1 概述在光伏产业中,电池是太阳能电池板的核心元件之一。
然而,传统的太阳能电池存在一些效率和性能上的限制。
为了提高太阳能电池的转换效率和降低成本,研究人员开始探索新的技术和方法。
其中,topcon(双面接触)电池被认为是一种具有潜力的解决方案。
与传统电池相比,topcon电池采用了二次硼扩散技术,可以有效地提高电池的性能和效率。
1.2 文章结构本文将详细介绍topcon电池二次硼扩散的作用及其机制。
文章分为五个主要部分:引言、topcon电池二次硼扩散的作用、正文部分一、正文部分二以及结论与总结。
首先,在引言部分我们将对topcon电池二次硼扩散进行概述,并明确文章的目的。
接下来,在第二部分我们将详细说明该过程的扩散过程以及机制解析,并阐述其在太阳能电池中所起到的作用及意义。
在第三和第四部分,我们将进一步展开讨论,阐述topcon电池二次硼扩散在正文部分一和正文部分二中的关键要点。
这些要点包括技术原理、性能提升、成本效益等方面的内容。
最后,在结论与总结部分,我们将对本文所述的内容进行总结,并得出相应的结论。
1.3 目的本文旨在通过对topcon电池二次硼扩散的研究,全面展示其作用及意义。
通过详细阐述这一技术的工作原理和机制,读者可以更好地理解并认识到topcon电池二次硼扩散在太阳能电池中所具有的潜力和优势。
同时,我们也希望为光伏行业研究人员和相关从业者提供参考和启发,促进光伏技术的创新与进步。
2. topcon电池二次硼扩散的作用2.1 扩散过程说明:topcon电池是一种太阳能电池技术,通过二次硼扩散可以提高其性能和效率。
在了解二次硼扩散的作用之前,我们首先需要理解其扩散的具体过程。
二次硼扩散是指将硼元素再次加入到已经掺入硼元素的材料中。
这个过程主要包括两个步骤:预处理和扩散。
首先,在预处理阶段,通过对topcon电池进行高温退火处理来减少内部缺陷和杂质等对后续工艺流程的影响。
硼磷扩散

一、硼扩散工艺原理(液态源)目前,液态源硼扩散常用:硼酸三甲酯B(CH3O)3,硼酸三丙酯,三溴化硼B(B2)3,无水硼酸三甲酯B(CH3O)3,为无色透明液体,在室温下挥发形成,具有较高真气压,硼酸三甲酯遇水易分解,升成硼酸和甲醇。
B(CH3O)+ 3H2O=H3BO3 + 3(CH3OH)B(CH3O)500℃以上B2O3 + CO2 + H2O + C2B2O3 + 3Si = 3SiO2 + 4B硼酸三甲酯在高温(500℃以上)能够分解出三氧化二硼(B2O3),而三氧化二硼在900℃左右又能与硅片起反应,生成硼原子,并沉积在硅片表面,这就是预沉积过程;沉积后在基区窗口表面上生成具有色彩的硼硅玻璃。
二、硼扩散装置:硼再分布:当炉温升到预定温度(1180℃以后)通干O2 20分钟,排除管道内空气,同时加热水浴瓶,是水浴温度达到设定温度值950℃,一切就绪后,即可将正片和陪片一起装入石英舟推入炉子恒温区,先通5分钟干氧,在改通30分钟湿氧,最后通5分钟干氧,时间到即可把硅片拉出石英管,倒在铜块上淬火,防止慢降温时,金从硅体中析出。
一、磷扩散工艺原理5POCl3 >600℃3PCl5 + P2O52P2O5 + 5Si = 5SiO2 + 4P4PCl5+5O2 过量O2 2P2O5+6Cl24PCl3+3O2 过量O2 2P2O5+6Cl2磷预沉积时,一般通N2为20~80ml/分,O2为20~40ml/分,O2可通过,也可不通过源。
二、磷扩散装置磷扩散源POCl3是无色透明有窒息性气味的毒性液体,要求扩散系统密封性好,源瓶进出口两端最好用聚四氟乙烯或聚氯乙烯管道连接。
若用其他塑料管或乳胶管连接易被腐蚀,就需要经常更换。
接口处最好用封口胶,由系统流出气体应通过排风管排到室外,不要泄漏在室内。
源瓶要严加密封,切勿让湿气进入源瓶。
因为三氯氧磷吸水汽而变质,做扩散温度上不去。
2POCl3+3H2O=P2O5+5HCl发现三氟氧磷出现淡黄色就不能使用。
硼扩散工艺实验报告
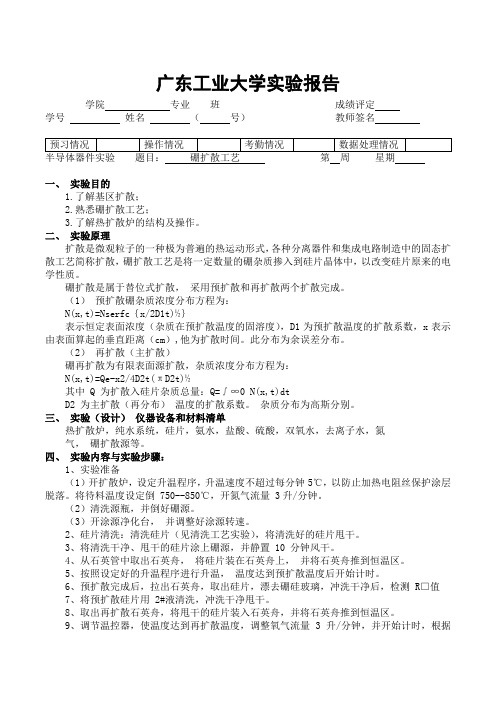
广东工业大学实验报告学院专业班成绩评定学号姓名(号)教师签名题目:硼扩散工艺第周星期一、实验目的1.了解基区扩散;2.熟悉硼扩散工艺;3.了解热扩散炉的结构及操作。
二、实验原理扩散是微观粒子的一种极为普遍的热运动形式,各种分离器件和集成电路制造中的固态扩散工艺简称扩散,硼扩散工艺是将一定数量的硼杂质掺入到硅片晶体中,以改变硅片原来的电学性质。
硼扩散是属于替位式扩散,采用预扩散和再扩散两个扩散完成。
(1)预扩散硼杂质浓度分布方程为:N(x,t)=Nserfc{x/2D1t)½}表示恒定表面浓度(杂质在预扩散温度的固溶度),D1为预扩散温度的扩散系数,x表示由表面算起的垂直距离(cm),他为扩散时间。
此分布为余误差分布。
(2)再扩散(主扩散)硼再扩散为有限表面源扩散,杂质浓度分布方程为:N(x,t)=Qe-x2/4D2t(πD2t)½其中 Q 为扩散入硅片杂质总量:Q=∫∞0 N(x,t)dtD2 为主扩散(再分布)温度的扩散系数。
杂质分布为高斯分别。
三、实验(设计)仪器设备和材料清单热扩散炉,纯水系统,硅片,氨水,盐酸、硫酸,双氧水,去离子水,氮气,硼扩散源等。
四、实验内容与实验步骤:1、实验准备(1)开扩散炉,设定升温程序,升温速度不超过每分钟5℃,以防止加热电阻丝保护涂层脱落。
将待料温度设定倒 750--850℃,开氮气流量 3升/分钟。
(2)清洗源瓶,并倒好硼源。
(3)开涂源净化台,并调整好涂源转速。
2、硅片清洗:清洗硅片(见清洗工艺实验),将清洗好的硅片甩干。
3、将清洗干净、甩干的硅片涂上硼源,并静置 10 分钟风干。
4、从石英管中取出石英舟,将硅片装在石英舟上,并将石英舟推到恒温区。
5、按照设定好的升温程序进行升温,温度达到预扩散温度后开始计时。
6、预扩散完成后,拉出石英舟,取出硅片,漂去硼硅玻璃,冲洗干净后,检测R□值7、将预扩散硅片用 2#液清洗,冲洗干净甩干。
8、取出再扩散石英舟,将甩干的硅片装入石英舟,并将石英舟推到恒温区。
硼磷扩散原理和示意图

一、硼扩散工艺原理(液态源)目前,液态源硼扩散常用:硼酸三甲酯B(CH3O)3,硼酸三丙酯,三溴化硼B(B2)3,无水硼酸三甲酯B(CH3O)3,为无色透明液体,在室温下挥发形成,具有较高真气压,硼酸三甲酯遇水易分解,升成硼酸和甲醇。
B(CH3O)+ 3H2O=H3BO3 + 3(CH3OH)B(CH3O)500℃以上B2O3 + CO2 + H2O + C2B2O3 + 3Si = 3SiO2 + 4B硼酸三甲酯在高温(500℃以上)能够分解出三氧化二硼(B2O3),而三氧化二硼在900℃左右又能与硅片起反应,生成硼原子,并沉积在硅片表面,这就是预沉积过程;沉积后在基区窗口表面上生成具有色彩的硼硅玻璃。
二、硼扩散装置:硼再分布:当炉温升到预定温度(1180℃以后)通干O2 20分钟,排除管道内空气,同时加热水浴瓶,是水浴温度达到设定温度值950℃,一切就绪后,即可将正片和陪片一起装入石英舟推入炉子恒温区,先通5分钟干氧,在改通30分钟湿氧,最后通5分钟干氧,时间到即可把硅片拉出石英管,倒在铜块上淬火,防止慢降温时,金从硅体中析出。
一、磷扩散工艺原理5POCl3 >600℃3PCl5 + P2O52P2O5 + 5Si = 5SiO2 + 4P4PCl5+5O2 过量O2 2P2O5+6Cl24PCl3+3O2 过量O2 2P2O5+6Cl2磷预沉积时,一般通N2为20~80ml/分,O2为20~40ml/分,O2可通过,也可不通过源。
二、磷扩散装置磷扩散源POCl3是无色透明有窒息性气味的毒性液体,要求扩散系统密封性好,源瓶进出口两端最好用聚四氟乙烯或聚氯乙烯管道连接。
若用其他塑料管或乳胶管连接易被腐蚀,就需要经常更换。
接口处最好用封口胶,由系统流出气体应通过排风管排到室外,不要泄漏在室内。
源瓶要严加密封,切勿让湿气进入源瓶。
因为三氯氧磷吸水汽而变质,做扩散温度上不去。
2POCl3+3H2O=P2O5+5HCl发现三氟氧磷出现淡黄色就不能使用。
半导体制造工艺之扩散原理概述

半导体制造工艺之扩散原理概述引言半导体器件是现代电子化工程的重要组成部分,而半导体制造工艺中的扩散过程是其中的核心步骤之一。
扩散是指将外部杂质或原子通过加热和蒸发的方式引入半导体晶体内部,从而改变其导电性能的过程。
本文将概述半导体制造工艺中的扩散原理,包括扩散的定义、分类、扩散过程的主要步骤以及应用。
扩散的定义和分类扩散在半导体制造加工中是用于改变材料电学特性和形成器件结构的重要工艺。
它通过在半导体材料中掺杂外部杂质或原子,改变其禁带宽度、导电性能和晶格结构,从而实现对器件特性的控制。
根据掺杂的原子种类和结构变化,扩散可以分为以下几类:1.硼扩散(Boron diffusion):将硼原子引入到半导体材料中,可以增加材料的p型掺杂浓度。
2.磷扩散(Phosphorus diffusion):将磷原子引入到半导体材料中,可以增加材料的n型掺杂浓度。
3.氮扩散(Nitrogen diffusion):将氮原子引入到半导体材料中,可以改变半导体材料的特性,如降低材料的电阻率和增加材料的硬度。
4.氢扩散(Hydrogen diffusion):将氢原子引入到半导体材料中,可以提高材料的电阻率。
5.金属扩散(Metal diffusion):在半导体材料中引入金属原子,可以改变材料的特性,如增强导电性能或改变器件结构。
扩散过程的主要步骤扩散过程是一个涉及多个步骤的复杂过程,主要包括以下几个步骤:清洗在扩散之前,半导体晶体需要进行清洗,以去除表面的污染物和杂质,保证扩散过程的准确性和稳定性。
清洗步骤可以使用化学清洗方法或物理清洗方法,如溶剂洗涤、超声波清洗等。
预处理预处理步骤是为了提高扩散效果和降低生产成本而进行的一系列处理。
包括表面氧化、蚀刻、离子注入等工艺,以提高扩散层的质量和一致性。
掺杂掺杂是扩散过程中的核心步骤,通过向半导体晶体中注入外部杂质,改变材料的导电性能。
掺杂过程中需要控制掺杂浓度和深度,以满足器件设计要求。
硼扩散优点

硼扩散优点硼,作为一种非金属元素,在材料科学中扮演着重要的角色。
特别是硼扩散技术,已经成为改善和优化材料性能的关键手段之一。
硼扩散不仅能显著提高材料的硬度、耐磨性和耐腐蚀性,还能微调材料的电学和热学性能。
本文将详细探讨硼扩散的优点及其在材料科学中的广泛应用。
一、硼扩散的基本原理在讨论硼扩散的优点之前,有必要简要介绍硼扩散的基本原理。
硼扩散是一种将硼原子引入目标材料(通常是金属或半导体)的过程,通过高温下的扩散作用,硼原子能够渗透到材料的晶格中,从而改变材料的物理和化学性质。
二、硼扩散的优点1.提高材料硬度硼扩散能够显著提高材料的硬度。
硼原子在材料晶格中的固溶强化作用,能够有效阻碍位错的运动,从而提高材料的硬度。
这对于需要承受高机械应力的应用场合尤为重要,如切削工具、轴承和齿轮等。
2.增强耐磨性和耐腐蚀性硼扩散还能增强材料的耐磨性和耐腐蚀性。
硼化物层在材料表面形成后,能够有效抵抗外界环境的侵蚀,减少材料的磨损和腐蚀。
这对于延长材料的使用寿命和提高设备的可靠性具有重要意义。
3.微调电学性能硼扩散在半导体材料领域具有独特的优势。
通过精确控制硼的扩散浓度和深度,可以微调半导体材料的电学性能,如载流子浓度、迁移率和电阻率等。
这对于制造高性能的半导体器件和集成电路至关重要。
4.优化热学性能硼扩散还能优化材料的热学性能。
硼原子的引入可以改变材料的热导率和热膨胀系数,从而提高材料的热稳定性和抗热震性能。
这对于高温环境下的应用,如航空航天和汽车发动机部件,具有重要的实用价值。
三、硼扩散在材料科学中的应用1.钢铁工业在钢铁工业中,硼扩散技术被广泛应用于提高钢材的性能。
通过硼化处理,可以在钢材表面形成一层坚硬且耐磨的硼化物层,从而提高钢材的硬度、耐磨性和耐腐蚀性。
这种硼化钢材被广泛应用于制造切削工具、模具和耐磨部件等。
2.半导体工业在半导体工业中,硼扩散是实现半导体材料掺杂的关键技术之一。
通过精确控制硼的扩散条件,可以在硅、锗等半导体材料中引入适量的硼原子,从而调整材料的电学性能。
硼的固态源开管扩散工艺流程

硼的固态源开管扩散工艺流程
硼的固态源开管扩散工艺流程主要包括以下步骤:
1. 材料准备:准备硼源材料和扩散材料。
硼源材料可以是硼化硅(SiB6)或者硼化硅饼。
扩散材料一般使用硅(Si)单晶或者多晶硅。
2. 清洗:将硅片或者硼化硅饼进行表面清洗,以去除表面杂质。
3. 涂覆扩散材料:将扩散材料涂覆在硅片或硼化硅饼的表面。
这可以通过化学气相沉积(CVD)或者物理气相沉积(PVD)等方法完成。
4. 高温处理:将硼源材料和硅片或硼化硅饼一起置于高温环境中,进行扩散反应。
通过控制温度、时间和气氛等参数,使硼元素从硼源材料向硅片或硼化硅饼中扩散。
5. 冷却和清洗:待扩散反应完成后,将样品从高温环境中取出,进行冷却。
然后,用适当的溶液进行清洗,以去除表面残余的杂质。
6. 测量和分析:通过一系列的测试和分析,确定扩散过程的质量和结果。
常用的测试方法包括电子探针测试、拉曼光谱、X射线衍射等。
这些步骤组成了硼的固态源开管扩散工艺流程。
具体的实施细节可能因不同的工艺和材料而有所不同,具体实施时需遵循相关的安全操作规程和指导。
topcon硼扩散工艺原理

topcon硼扩散工艺原理一、引言硼扩散工艺是一种常用的半导体工艺,用于在硅晶片表面形成硼掺杂层。
这种工艺可以调控晶体的电导率和电阻率,从而实现对半导体器件性能的控制和优化。
本文将介绍topcon硼扩散工艺的原理。
二、硼扩散工艺的基本原理硼扩散工艺是通过在硅晶片表面形成高浓度硼掺杂层,以改变硅晶片的电性能。
硼扩散工艺是一种常见的掺杂工艺,它通过在硅晶片表面形成硼掺杂层,实现对硅晶片电性能的调控。
硼是一种五价元素,其在硅晶片中的掺杂可以引入额外的电子空穴,从而改变硅晶片的导电性能。
三、topcon硼扩散工艺的原理topcon硼扩散工艺是一种改进的硼扩散工艺,它通过在硅晶片表面形成一层薄膜,然后在薄膜上进行硼扩散。
这种工艺的特点是可以在硅晶片表面形成均匀的硼掺杂层,并且可以控制硼掺杂的深度和浓度。
topcon硼扩散工艺主要包括以下几个步骤:1. 涂覆薄膜:首先在硅晶片表面涂覆一层薄膜,通常使用二氧化硅作为薄膜材料。
这层薄膜的作用是阻止硼原子从硅晶片表面扩散到内部。
2. 硼扩散:将硼原子通过扩散源加热到一定温度,使其扩散到薄膜上。
在扩散过程中,硼原子会穿过薄膜并扩散到硅晶片中。
3. 深度控制:通过控制扩散源的温度和时间,可以控制硼扩散的深度。
温度越高,扩散越快,深度也越大。
时间越长,扩散越深。
4. 浓度控制:通过控制扩散源中硼原子的浓度,可以控制硼掺杂的浓度。
浓度越高,硼掺杂的浓度也越高。
5. 清洗和退火:在硼扩散完成后,需要进行清洗和退火处理,以去除表面的杂质和缺陷,并修复晶体结构。
四、topcon硼扩散工艺的优势相比传统的硼扩散工艺,topcon硼扩散工艺具有以下优势:1. 均匀性:topcon硼扩散工艺可以在硅晶片表面形成均匀的硼掺杂层,提高器件的稳定性和可靠性。
2. 控制性:通过调控扩散源的温度、时间和浓度,可以精确控制硼扩散的深度和浓度,实现对器件性能的精确调节。
3. 一致性:topcon硼扩散工艺可以在不同硅晶片上实现一致的硼扩散效果,保证器件的一致性和可复制性。
光伏 前道 硼扩散 后道
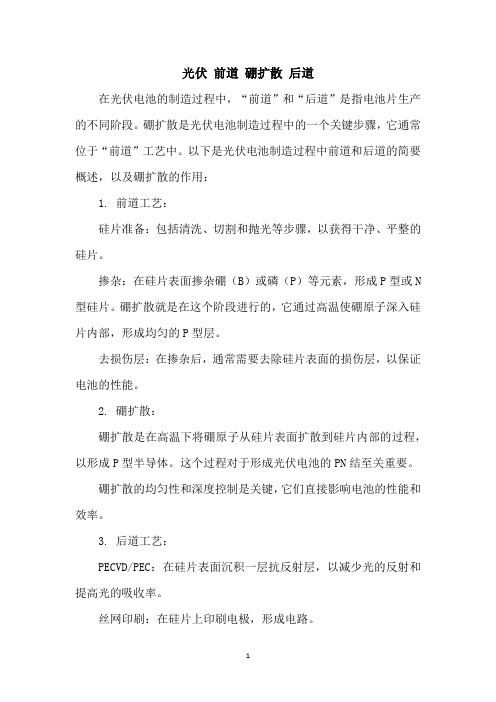
光伏前道硼扩散后道
在光伏电池的制造过程中,“前道”和“后道”是指电池片生产的不同阶段。
硼扩散是光伏电池制造过程中的一个关键步骤,它通常位于“前道”工艺中。
以下是光伏电池制造过程中前道和后道的简要概述,以及硼扩散的作用:
1. 前道工艺:
硅片准备:包括清洗、切割和抛光等步骤,以获得干净、平整的硅片。
掺杂:在硅片表面掺杂硼(B)或磷(P)等元素,形成P型或N 型硅片。
硼扩散就是在这个阶段进行的,它通过高温使硼原子深入硅片内部,形成均匀的P型层。
去损伤层:在掺杂后,通常需要去除硅片表面的损伤层,以保证电池的性能。
2. 硼扩散:
硼扩散是在高温下将硼原子从硅片表面扩散到硅片内部的过程,以形成P型半导体。
这个过程对于形成光伏电池的PN结至关重要。
硼扩散的均匀性和深度控制是关键,它们直接影响电池的性能和效率。
3. 后道工艺:
PECVD/PEC:在硅片表面沉积一层抗反射层,以减少光的反射和提高光的吸收率。
丝网印刷:在硅片上印刷电极,形成电路。
烧结:通过高温烧结使电极材料与硅片表面结合,同时完成电池片的固化。
质量检测:对电池片进行性能测试,包括电流-电压特性、光谱响应等。
在整个光伏电池的制造过程中,前道和后道工艺的每个步骤都非常重要,它们共同决定了电池片的最终性能。
硼扩散作为前道工艺的关键步骤,对于确保电池片的导电性和光电转换效率具有重要作用。
因此,对硼扩散工艺的优化和控制是提高光伏电池质量的关键。
硼扩散实验——精选推荐
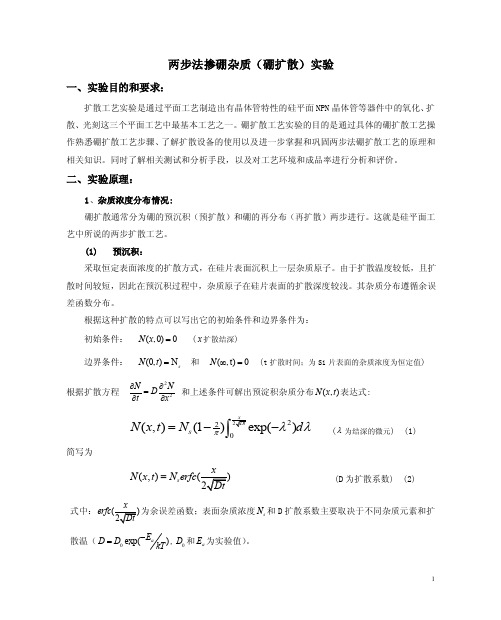
两步法掺硼杂质(硼扩散)实验一、实验目的和要求:扩散工艺实验是通过平面工艺制造出有晶体管特性的硅平面NPN 晶体管等器件中的氧化、扩散、光刻这三个平面工艺中最基本工艺之一。
硼扩散工艺实验的目的是通过具体的硼扩散工艺操作熟悉硼扩散工艺步骤、了解扩散设备的使用以及进一步掌握和巩固两步法硼扩散工艺的原理和相关知识。
同时了解相关测试和分析手段,以及对工艺环境和成品率进行分析和评价。
二、实验原理:1、杂质浓度分布情况:硼扩散通常分为硼的预沉积(预扩散)和硼的再分布(再扩散)两步进行。
这就是硅平面工艺中所说的两步扩散工艺。
(1) 预沉积:采取恒定表面浓度的扩散方式,在硅片表面沉积上一层杂质原子。
由于扩散温度较低,且扩散时间较短,因此在预沉积过程中,杂质原子在硅片表面的扩散深度较浅。
其杂质分布遵循余误差函数分布。
根据这种扩散的特点可以写出它的初始条件和边界条件为:初始条件: (,0)0N x = (x 扩散结深)边界条件: (0,)N s N t = 和 (,t)0N ∞= (t 扩散时间;为Si 片表面的杂质浓度为恒定值)根据扩散方程 22N N D t x∂∂=∂∂ 和上述条件可解出预淀积杂质分布(,)N x t 表达式:220(,)(1)exp()s N x t N d πλλ=-- (λ为结深的微元) (1)简写为(,)s N x t N erfc = (D 为扩散系数) (2) 式中:erfc 为余误差函数;表面杂质浓度s N 和D 扩散系数主要取决于不同杂质元素和扩散温(0exp()a E D D kT -=,0D 和a E 为实验值)。
注:N s 是半导体内表面处的杂质浓度,它并不等于半导体周围气氛中的杂质浓度。
当气氛中得分压强较低时,在半导体内表面处的杂质溶解度将与其周围气氛中杂质的压强成正比。
当杂质分压强较高时,则与周围气氛中杂质的分压强无关,数值上等于扩散温度下杂质在半导体中的固溶度。
(2) 再分布:是把由预沉积过程在硅片表面淀积了一定杂质的硅片,放入较高温度的扩散炉内加热,使杂质向硅片内部扩散,扩散过程中没有外来杂质的补充,是一种限定源扩散。
硼再扩散实验报告(3篇)

第1篇一、实验目的本次实验旨在研究硼元素在特定条件下的再扩散行为,探讨不同因素对硼扩散速率的影响,为半导体材料制备和器件设计提供理论依据。
二、实验原理硼再扩散是指半导体材料中硼掺杂原子在高温条件下从高浓度区域向低浓度区域扩散的现象。
实验中,通过在单晶硅(Si)基板上制备硼掺杂层,然后加热至一定温度,观察并记录硼掺杂原子在材料中的再扩散情况。
三、实验材料与设备1. 实验材料:- 高纯度单晶硅(n型,电阻率为0.01Ω·cm)- 硼掺杂源(三氯化硼,BCl3)2. 实验设备:- 真空系统- 硅片清洗设备- 气相沉积设备- 真空炉- 温度控制器- 光学显微镜- 扫描电子显微镜(SEM)- 能量色散光谱仪(EDS)四、实验步骤1. 硅片清洗:将单晶硅片在去离子水中清洗,然后依次用丙酮、乙醇、去离子水超声清洗,最后用氮气吹干。
2. 硼掺杂:将清洗干净的硅片置于真空系统中,用气相沉积设备在硅片表面沉积一层厚度为1μm的硼掺杂层。
3. 硼再扩散实验:- 将沉积硼掺杂层的硅片放入真空炉中,设置不同的温度(例如:800℃、900℃、1000℃)。
- 在设定的温度下,加热硅片一定时间(例如:30分钟、60分钟、120分钟)。
- 加热结束后,迅速取出硅片,进行后续测试。
4. 分析与测试:- 利用光学显微镜观察硅片表面的形貌变化。
- 利用SEM和EDS分析硅片表面及内部的硼掺杂分布。
- 利用能量色散光谱仪(EDS)测定硅片中硼掺杂原子的浓度。
五、实验结果与分析1. 实验结果显示,随着加热温度的升高,硼掺杂原子在硅片中的再扩散速率逐渐加快。
2. 在800℃条件下,加热30分钟,硼掺杂原子在硅片中的扩散深度约为0.5μm;加热60分钟,扩散深度约为1μm;加热120分钟,扩散深度约为1.5μm。
3. 在900℃条件下,加热30分钟,硼掺杂原子在硅片中的扩散深度约为1μm;加热60分钟,扩散深度约为1.5μm;加热120分钟,扩散深度约为2μm。
硼扩散机理及工艺应用技术研究

硼扩散机理及工艺应用技术研究硼扩散机理及工艺应用技术研究报告1. 研究背景•硼扩散机理的研究在半导体行业中具有重要的意义。
•工艺应用技术的研究能够提高硼扩散工艺的效率和稳定性。
2. 硼扩散机理的理论基础•硼扩散是指通过热处理使得硼原子从高浓度的区域向低浓度的区域扩散。
•扩散过程中硼原子通过晶格空位或替代晶格中的其他原子进行扩散。
硼扩散的动力学模型•硼扩散可以通过Fick定律进行描述,其中扩散通量与浓度梯度成正比。
•硼扩散的速率还受到温度、时间和硼浓度的影响。
硼扩散的影响因素•晶体表面状态对硼扩散的影响较大。
•杂质的存在可能导致硼扩散机理发生改变。
3. 硼扩散工艺应用技术研究•硼扩散工艺的研究旨在提高掺杂均匀性和扩散速率。
控制掺杂均匀性的方法•通过改变扩散源的形状和结构可以提高掺杂均匀性。
•优化扩散参数可以控制掺杂均匀性的分布。
提高扩散速率的方法•使用特殊的扩散源可以提高扩散速率。
•增加热处理温度和时间可以加快扩散速率。
4. 工艺应用技术的实验研究•进行实验以验证理论模型和工艺应用技术的效果。
硼扩散实验设计•设计实验方案,包括扩散源的选择、扩散温度和时间的控制等。
实验结果分析•分析实验数据,验证理论模型的正确性。
•评估工艺应用技术在实验中的效果。
5. 结论与展望•硼扩散机理的研究对于半导体行业具有重要意义。
•工艺应用技术的研究能够提高硼扩散工艺的效率和稳定性。
•进一步的研究可以探索更高效的硼扩散工艺应用技术。
以上是对于”硼扩散机理及工艺应用技术研究”的相关研究报告,希望能对您的研究有所帮助。
硼扩散工艺原理
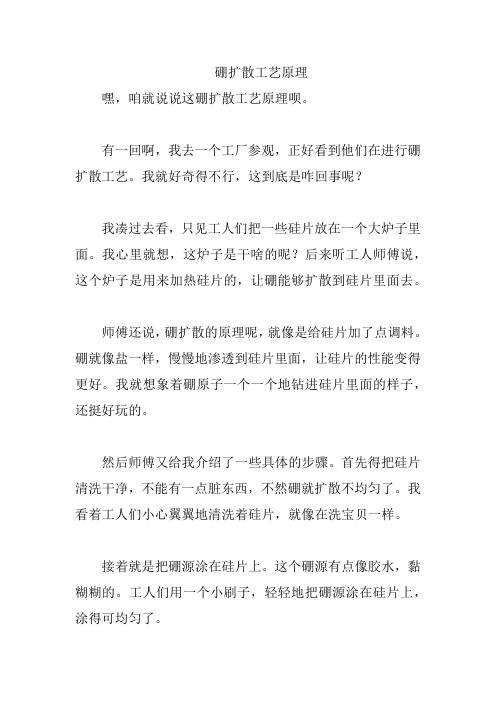
硼扩散工艺原理
嘿,咱就说说这硼扩散工艺原理呗。
有一回啊,我去一个工厂参观,正好看到他们在进行硼扩散工艺。
我就好奇得不行,这到底是咋回事呢?
我凑过去看,只见工人们把一些硅片放在一个大炉子里面。
我心里就想,这炉子是干啥的呢?后来听工人师傅说,这个炉子是用来加热硅片的,让硼能够扩散到硅片里面去。
师傅还说,硼扩散的原理呢,就像是给硅片加了点调料。
硼就像盐一样,慢慢地渗透到硅片里面,让硅片的性能变得更好。
我就想象着硼原子一个一个地钻进硅片里面的样子,还挺好玩的。
然后师傅又给我介绍了一些具体的步骤。
首先得把硅片清洗干净,不能有一点脏东西,不然硼就扩散不均匀了。
我看着工人们小心翼翼地清洗着硅片,就像在洗宝贝一样。
接着就是把硼源涂在硅片上。
这个硼源有点像胶水,黏糊糊的。
工人们用一个小刷子,轻轻地把硼源涂在硅片上,涂得可均匀了。
涂好硼源后,就把硅片放进炉子里面加热。
这个炉子的温度可高了,能有好几百度呢。
我看着炉子上的温度表,心里直打鼓,这硅片不会被烧坏了吧?师傅说不用担心,他们有经验,知道怎么控制温度和时间。
加热一段时间后,硼就扩散到硅片里面了。
然后把硅片拿出来,进行一些检测,看看扩散的效果好不好。
如果不好,就得重新调整工艺参数,再做一遍。
从那以后啊,我对硼扩散工艺原理有了点了解。
这工艺虽然看起来挺复杂的,但是做出来的硅片可厉害呢。
硼向奥氏晶界的扩散机制

硼在金属中的扩散问题是金属材料研究中的一 部分源于晶界领域的“贫硼区”. 随着晶界偏析的硼
个热门话题 ,由扩散导致的硼向奥氏体晶界的非平 增多晶界邻域的贫硼区宽度增大 ,这两者同时随淬
衡偏聚会对淬火钢的综合机械性能产生一系列的影 火加热温度升高和冷却速度的降低而增加 ,在晶界
响. 硼在淬火时向奥氏体晶界的偏聚是一种在冷却 形成连续的偏聚带进而发展成为不连续的聚集状
(11)
其中 n 是 ( a , b) 区间划分的份数 , b
n
a
=
h 是每个
梯形的高 , yi 是不同 x 处的 f ( x) 值.
在本问题中 , b -
a
=
t
-
0
=
t, b
Байду номын сангаас
n
a
=
t n
=
Δt ,
τ=
( xi ) 2 2. 80
=
D0 2tn〔y0
+
2 y1 + …… + 2 yn- 1 + yn〕,
设晶粒比较大而贫硼区的尺寸与晶粒的尺寸相
比小得多时 ,从而可以把扩散过程的一侧视为无限 ,
取 x = 0 处 C = 0 是把晶界设想为这种扩散原子团
的无限势阱 ,它可以不断地向晶界迁移 ,导致硼原子
在晶界的富集. 对于硼原子团的扩散过程 ,其扩散方程可以表
示为
1 D ( t)
9C 9t
=
92 C 9x2
.
(4)
利用式 (1) ,将 T 换成 t ,则 D = D ( t) ,作变量替
换 ,令 dτ = D ( t) d t ,有
∫ ∫ t
[太阳能电池硼扩散工艺]硼扩散工艺
![[太阳能电池硼扩散工艺]硼扩散工艺](https://img.taocdn.com/s3/m/d447651605087632301212cd.png)
[太阳能电池硼扩散工艺]硼扩散工艺太阳能电池硼扩散工艺1. 准备工作:1.光刻间坚膜烘箱开启,参数:120℃;2.预设定硼扩散炉温度为950℃;3.1#HF配制,参数:HF:H2O=1:5,360mL;4.2#HF配制,参数:HF:H2O=1:10,440mL;5.清洗干净聚四氟乙烯架、石英烧杯和小石英舟各一套,烘干备用。
6.预设定氧化炉温度为1050℃;7.清洗干净倒扣皿(大体积)一套,烘干备用。
2. 操作步骤:1.背面氧化铁的去除:(1)硅片另一面涂正胶并120℃坚膜30分钟(目的:侵害正面二氧化硅);(2)将坚膜后的硅片放入1#HF溶液中刻蚀(提前放入填料架,硅片就斜靠在里面架子上),时间(8-12)分钟后捞出,无水乙醇简单冲洗干净,氮气吹干硅片表面(无明显的水汽),经测试方块电阻为(40.5Ω·cm),再进行下一步;(3)醚去除正面的正胶,再用无水乙醇洗去丙酮(乙醇的份量多于丙酮1/3),纯水冲洗(10杯)并用氮气吹干,小心存放于烧杯中的小石英舟内;2.硼扩散掺杂(预扩散):(1)硼扩散炉使用扩散源为直径2英寸的铋陶瓷扩散源片(二氧化钛舟和陶瓷源片预放于硼二氧化硅扩散炉石英管中央)。
待硼扩散炉温度为950℃,设定氮气参数(2L/min,3-5分钟,排尽空气之后,降为0.5 L/min)停留10分钟后,缓慢拖出石英舟到炉口冷(2)设定硼扩散炉气压为980℃,当温度达到980℃的时候,用夹子夹出石英舟放于炉口下塑瓷盖子内冷却(小心操作);(3)把硅片到手氧化炉处,小心取出硅片放入氧化炉的大石英舟内(硅片背面和硼扩散源片一定铪要平行放置,整个操作过程一定得很小心)。
把装好硅片的石英舟拉到氧化炉炉口(稍微靠炉口里面一点,外面完全不会碰到为止,注意安全);(4)硅片炉口预热5分钟,待温度稳定在980℃之后,缓慢推进石英舟直至硼扩散炉石英管中央,关上炉口钟罩(出气口向下)。
(5)秒表计时,扩散时间为(25-30)分钟;(6)扩散完成后,关闭硼扩散炉,不关闭氮气的供应。
光伏硼扩深度

光伏硼扩深度
光伏硼扩(Boron diffusion)是太阳能电池制造过程中的一个重要环节,用于提高电池的开路电压和转换效率。
硼扩深度是指在硼扩散过程中硼原子扩散的深度,是硼扩散工艺控制的关键参数之一。
硼扩深度的大小直接影响到太阳能电池的性能,硼扩深度过浅会导致电池的开路电压降低,转换效率下降;硼扩深度过深则会导致电池的短路电流降低,转换效率下降。
因此,硼扩深度的控制是太阳能电池制造过程中的一个重要环节。
目前,光伏硼扩深度的控制主要通过控制硼扩散温度、扩散时间、扩散气体流量等参数来实现。
一般来说,硼扩散温度越高、扩散时间越长、扩散气体流量越大,硼扩深度就越深。
但是,硼扩散温度过高或扩散时间过长会导致电池的短路电流降低,因此需要在硼扩散深度和电池性能之间进行平衡。
此外,硼扩深度的控制还受到材料和设备的影响。
例如,扩散炉中的材料和设备的质量和精度会影响硼扩散的效果,从而影响硼扩深度。
因此,在太阳能电池制造过程中,需要选择合适的材料和设备,并进行严格的工艺控制,以确保硼扩深度的控制达到最佳状态。
- 1、下载文档前请自行甄别文档内容的完整性,平台不提供额外的编辑、内容补充、找答案等附加服务。
- 2、"仅部分预览"的文档,不可在线预览部分如存在完整性等问题,可反馈申请退款(可完整预览的文档不适用该条件!)。
- 3、如文档侵犯您的权益,请联系客服反馈,我们会尽快为您处理(人工客服工作时间:9:00-18:30)。
PASSIVATION OF LASER-DRILLED VIA HOLES FOR EMITTER-WRAP-THROUGH-CELLSN. Mingirulli, S.Trittler, M. Bui, A. Grohe , D. Biro, R. Preu, S. GlunzFraunhofer Institute for Solar Energy Systems (ISE)Heidenhofstrasse 2, D-79110 Freiburg, Germanynicola.mingirulli@ise.fraunhofer.deABSTRACT: A high speed via-hole drilling laser process for emitter-wrap through cell production is investigated concerning the removal of induced crystal damage by a subsequent alkaline etching step. The etching time necessary for damage removal is identified. Further the passivating properties at the via-hole surface of two passivation layers are compared. The passivating effect of a PECVD-SiN layer deposited on both sides of the wafers is confronted to thermal oxide passivation by lifetime measurement. A theoretical frame work using the analogy of via-holes and dislocations is applied to extract values for the surface recombination velocity at the via-hole wall. Both analysis indicate that the passivating effect of the PECVD layer depends on the via hole radius whereas the passivation quality of the SiO2-layer saturates for an etching time of equal or greater 240 s. For the highest etching times surface recombination velocities of down to 60 cm/s are found for SiN.Keywords: EWT, laser processing, laser damage analysis, passivation1INTRODUCTIONOne of the key features of the EWT (emitter-wrapthrough) cell concept [1] is an emitter via that connectsthe front side emitter with the back side emitter, wherethe contact metal is deposited. State-of-the-art laserprocesses allow drilling a plurality of via-holes within aprocessing time appropriate for industrial application.Since the drilling process is expected to harm the Sicrystal around the borehole, material must be removed ina subsequent etching step to avoid detrimental effects on EWT-cell performance, caused by recombination or increased via-hole resistance. In this work we investigate a state-of-the-art process as described elsewhere ([2], [3]) concerning the removal of crystal damage induced by alkaline etching with SEM and lifetime analysis. Since a sensitive damage analysis requires a passivation of the via-hole wall two passivation layers, namely thermal oxide and silicon nitride deposited by plasma enhanced chemical vapour deposition (PECVD) are compared in this regard.2EXPERIMENTAL2.1 Sample PreparationA disc laser system was used in “on the fly”- mode[2] to drill honeycomb patterns of different numbers of via-holes per unit area (Figure 1) into 4 W cm polished FZ-samples of 330 µm thickness. The wavelength emitted by the Yb:YAG crystal is 1030 nm, whereas a diode current of 42 A, a pulse frequency 15 kHz and 12 repetitions per hole were used. The via-hole densities were chosen to be between N i via = 200...1850 cm-2 to achieve a strong influence of the via-holes on the investigated parameters. At the sample center no via-holes were drilled in order to measure the background lifetime. At the via-hole positions the samples were not in contact with the laser chuck. Subsequently the samples were alkaline etched in 30% KOH at 80°C, varying etching time sample wise from 5s…960 s, starting at very low values since the laser process is expected to induce little damage. After a cleaning step a thermal oxidation process was applied aiming at 105 nm thickness to a part of the samples. On the remaining samples SiN x with a refractive index of n (l = 632 nm) = 2.8 and a thickness of 70 nm was deposited by means of PECVD. Finally all samples were annealed in a forming gas atmosphere. Figure 1 Lifetime sample design. t eff (N via i) is measured on 4 areas of different via-density surrounding a reference area without via-holes.2.2Results2.2.1SEM-analysisIn order to analyze the surface structure of the via-holes the same drilling process and etching steps were applied to Cz – material with saw damage. Cross sections were prepared with a wafer saw. Figure 2 to Figure 4 show cross sections through different via-holes with varying etching time, whereas the laser incident side of the sample as well as the via-hole wall are visible. The cutting depth d saw was chosen to be smaller than the wafer thickness d wafer, thus the lower part of the cross sections with less smooth surface is a broken edge. After drilling, the via-hole wall appears to be smooth and slightly wavy, and laser debris is visible on the wafer surface. After 60s etching in aqueous solution of 30 % KOH aq debris on the original wafer surface is nearly removed (Figure 3). The via-hole wall exhibits brighter stripes in <110> directions, indicating that the anisotropy of the alkaline bath is beginning to play a role. Thus at this stage the material is of at least partly crystalline structure. Figure 4 finally displays a via-hole that was etched for 240s. The surface topology in <110> and <100> direction is clearly different. The <100> part is rather smooth with few steps whereas the <110> directions exhibit a corrugated surface and several steps. In a top view one would expect an octahedron of decreasing size moving from the laser incident side to the back. Figure 5 displays the (equivalent) radius vs. the etching time (FZ-samples) measured on front and back side with a microscope, where required calculated from the area enclosed by a polygon to account for the deviation from a non circle shape.Figure 2 Cross section of via-hole in Cz-wafer after drilling. Laser debris is present on the surface. The via-hole wall appears to be smooth.Figure 3 Cross section of via-hole in Cz-wafer after t KOH =60s. The anisotropy of the alkaline etch is visible.Figure 4 Cross section of via-hole in Cz-wafer after t KOH =240s. The anisotropy of the alkaline etching leads to a direction dependence of the surface topology. In <100> direction the surface is smooth with some steps whereas in <110> direction the surface is corrugated and exhibits several steps.r a d i u s [µm ]t KOH [s]Figure 5 (Equivalent) radius vs. etching time microscopically measured on both wafer sides. If necessary an equivalent radius was calculated from the area enclosed by a polygon to account for deviations from the circle shape.t KOH[s] τe f f @ Δn = 5 1014c m -3[µs ]τe f f /τe f f 0 @ Δn = 5 1014c m-3t KOH [s]Figure 6 upper part: absolute lifetime dependence on etching time for PECVD-SiN and thermal SiO 2 for N via =295cm -2; lower part: ratio of effective lifetime to background lifetime for both layers for N via =295cm -22.2.2 Lifetime AnalysisFor lifetime measurement a WCT 120 QSSPC-set up by Sinton Consulting was used illuminating the samples on the side of smaller diameter of the conical via hole. For the case that the area fraction of the via-holes exceeded 5% this was accounted for in the optical factor assuming the light entering a via-hole not to be absorbed. Lifetimes were evaluated at the injection density D n = 5x1014 cm -3. Figure 6 displays results of lifetime measurement for both sample types at a via-hole density of N via = 295 cm -2.5s30s 60s120s 240s 480s Fit1/τe f f [µs -1] @ Δn = 5x 1014c m-3N via [cm -2]Figure 7 Inverse t eff vs. N via for different etching times with fits according to Opdorp et al. for SiN layer. Recombination decreases with etching time as well as decreasing via-hole density. The extracted S via ranges from 18200cm/s to 60cm/s (Table 1).The lifetime measured on the samples with thermal oxide increases with etching time, reaches a maximum value at t KOH = 240s and then slightly decreases. Considering the ratio of effective lifetime and background lifetime t eff / t eff 0 a clear saturation starting at t KOH = 240s can be observed. Thus the passivation cannot be improved by further etching leading to the conclusion that the via-hole is laser damage free.Lifetime for the SiN-samples increases even for the lowest etching times, whereas it is lower than for the oxide samples for t KOH = 60s and 120s and and exceeds the lifetime of oxide samples above 240s. Hence the layer has some passivating effect inside the via-hole as has already been observed in previous work ([3],[4]). The ratio however increases and remains at lower values than for the oxide samples for all etching times realized, and no saturation with etching time nor a maximum can be observed. Thus the passivation quality of PECVD-SiN improves with increasing via-hole radius.In order to compare the samples further it is helpful to extract a parameter that describes the recombination activity independently of background lifetime. A model originally derived to describe recombination activity of dislocations by Opdorp et al. is applied, resulting in a lifetime attributed to “via-hole-recombination” ([3], [4]):⎥⎦⎤⎢⎣⎡+−−≈00017.1)ln(21),,(Sr D N r DN S r N via πτ eq. 1The term reduces to the first two summands for diffusion limited recombination (S >> D/r 0) and to the third for boundary rate limited rcombination (S << D/r 0). In the latter case the recombination depends linearly S, r 0 and N. The effective lifetime t eff is assumed to be determined by a surface, bulk and via-hole contribution:111111effvia b S via eff ττττττ+=++= eq. 2 1/τe f f [µs -1] @ Δn = 5x 1014c m-3N via [cm -2]Figure 8 Inverse t eff vs. N via for different etching times with fits according to Opdorp et al. for SiO layer. The values of S via of the oxide samples is about half of the values of the SiN-samples.Figure 7 displays the inverse lifetime measured on the SiN samples. Recombination systematically decreases with etching time and increases with via-hole density to a large extent. The recombination value at N via = 0 was measured at the sample center. The data points marked with asterisk exhibited lifetime dips in spatially resolved measurements not correlating with the shape of the via-hole area, and were therefore not considered in the following fit. Error-weighted fitting of the data according to eq. 1 with S via as free parameter results in values starting with 18200 cm/s up to 60 cm/s (Table 1) whereas average radius values from the microscopic measurements where used. The error is estimated to be about 30%. The background surface recombination velocity was calculated to range between 10…15 cm/s assuming the bulk lifetime to be Auger-limited.It is interesting that S does not tend to the thermal velocity of electrons for very low etching time as has been found for different laser processes in previous work [3]. A possible interpretation is that a passivating effect of the SiN-layer is present even for the lowest etching time meaning that the near surface bulk of the via-hole is only moderately damaged so that the physical surface does play a role in the recombination dynamics of the via-hole. On the other hand the sensitivity of the method is limited for very high recombination velocities.Figure 8 displays the same graph for the SiO-samples. Recombination generally decreases with etching time, however for t KOH equal or greater 240s there is no improvement. Further it can be observed, that for low etching times the inverse lifetime depends in the expected manner on via density, however for t KOH equal or greater 240s this is partly not the case. In spatially resolved lifetime measurements the oxide passivation was found to exhibit lateral inhomogenities affecting the areas of N via 2 and N via 4 for higher etching times, since background recombination plays a significant role in this etching time regime. Since the change in background lifetime cannot be quantified it was neglected in the fits (Table 1). In Figure 9 the extracted values for the two passivation layers can be compared. S via of the SiO 2 samples decreases up to t KOH = 240 s whereas for higher etching time it does not change significantly indicating that all damage detectable with this method is removed.S v i a [c m /s ]t KOH [s]Figure 9 S via values extracted from fits vs. etching time for both sample types. For the SiO-samples saturation for t KOH equal or greater can be observed. The SiN-samples show lower values up to 240s indicating the radius-dependence of the passivating effect.However, the average surface recombination velocity on the original wafer surface S 0~40 cm/s calculated assuming the bulk lifetime to be Auger limited is not reached. Considering that the via-hole surface is partly rough and a larger fraction of the surface consists of {111} planes (Figure 4) it can be expected that the passivation layer is less effective.Svia-values for SiN do not exhibit saturation within the considered etching time, and are lower than for the SiO 2-samples up t KOH = 240 s. As could already be concluded from the lifetime measurement this indicates that the passivating effect of PECVD-SiNx depends on the via-hole radius. For the highest etching time Svia= 60 cm/s are extracted, however S0 is not reached as well as for SiO2 samples.Table 1 Values for S via extracted from fits. The error is estimated to be 30%. The values for the nitride samples are significantly higher and exceed the values for the oxide samples by a factor of about two.t KOH [s] S [cm/s] SiO 2 SiN x 5 - 18200 30 - 8700 60 2600 5100 120 600 1430 240 100 260 480 160 60 960 90 -3 CONCLUSIONA state of the art laser drilling process has been investigated concerning the removal of crystal damage by alkaline etching. It is found that an etching time of equal or greater 4 min in 30% KOH @ 80°C is sufficient for damage removal. Further the passivation of the via-hole of thermal SiO 2 was found to be more effective than PECVD-SiN for low etching times. The passivation quality of the latter layer improves with the via-hole radius. The coverage of the PECVD-SiN x -layer of thevia-hole wall depends on via-hole geometry, qualifying thermal silicon oxide for damage analysis, though the passivation quality that can be reached and thus the sensitivity is lower. Extracting S via -values from the data, one finds that the values for silicon oxide passivation are lower than for silicon nitride passivation for low etching times. The values SiO-layer reach around 100cm/s whereas for the SiN-layer 60 cm/s are reached for the highest etching time of t KOH = 480 s.4 ACKNOWLEDGEMENTSR. Neubauer and T. Leimenstoll are gratefully acknowledged for sample preparation.5 REFERENCES [1] J.M. Gee, et al., Proceedings of the 23rd IEEEPhotovoltaic Specialists Conference, Louisville, Kentucky, USA (1993) 265.[2] R. Mayerhofer, et al., Proceedings of the 4th WorldConference on Photovoltaic Energy Conversion, Waikoloa, Hawaii, USA (2006). [3] N. Mingirulli, et al., Applied Physics Letters 91(2007).[4] N. Mingirulli, et al., 22nd PVSEC Milan (2007).。