注塑产品问题解决方案范文
注塑过程中常见的问题及解决方案

注塑过程中常见的问题及解决方案一、飞边(披锋)1. 问题描述- 这飞边就像塑料偷偷长出来的小翅膀,在注塑件的边缘或者分型面那里冒出来,看着可闹心了。
就像好好的一块蛋糕,边缘突然多出了一些不规则的奶油坨坨。
2. 解决方案- 首先得检查模具的合模力。
要是合模力不够,那塑料就会像调皮的小孩从门缝里挤出来。
适当增加合模力,把模具紧紧抱住,让塑料乖乖待在该待的地方。
- 模具的磨损也会导致飞边。
就像穿破了的鞋子会漏脚指头一样,磨损的模具缝隙变大了。
这时候就得修模啦,把那些磨损的地方补一补或者磨平。
- 注塑压力也不能太大。
如果压力太大,塑料就像被大力士猛推的水,到处乱流。
降低注塑压力,找到一个合适的值,既能把模具填满,又不会让塑料溢出来。
二、短射(缺料)1. 问题描述- 短射就像给一个杯子倒水,结果没倒满一样。
注塑件看着不完整,有些地方该有塑料的却空着,就像一个没发育好的小怪物。
2. 解决方案- 先看看注塑压力是不是太小。
压力小的话,塑料就像没力气的小蚂蚁,爬不到模具的每个角落。
增加注塑压力,让塑料充满整个模具型腔。
- 塑料的流动性也很关键。
如果塑料太黏,就像浓稠的糨糊,很难流到模具的远端。
这时候可以提高料筒温度,让塑料变得稀一点,流动性更好,就像把糨糊加热变成稀粥一样,能顺利流到各个地方。
- 浇口尺寸也可能有问题。
要是浇口太小,就像一个小得可怜的水龙头,水流不出来多少。
适当扩大浇口尺寸,让塑料能畅快地流进模具。
三、气泡(气穴)1. 问题描述2. 解决方案- 注塑速度可能太快了。
塑料像一阵风呼呼地冲进模具,把空气都裹在里面了。
降低注塑速度,让塑料慢慢流进去,就像散步一样,这样空气就有机会跑出来了。
- 模具的排气也很重要。
如果模具没有排气孔或者排气不良,空气就被困在里面出不来。
在模具上开排气槽或者使用透气钢材料,给空气一条逃跑的路。
- 塑料干燥不彻底也会产生气泡。
如果塑料里有水份,加热的时候就会变成水蒸气,形成气泡。
精密注塑工艺与产品缺陷解决方案100例

精密注塑工艺与产品缺陷解决方案100例【导言】精密注塑工艺是一种高精度、高要求的注塑工艺,它在汽车、电子、医疗等行业有着广泛的应用。
然而,由于产品的特殊性,精密注塑工艺中常常会出现一些产品缺陷,如翘曲、气泡、热缩等,这不仅影响产品的美观和功能,还会影响产品的使用寿命和市场竞争力。
本文将从精密注塑工艺的角度出发,总结100例产品缺陷解决方案,帮助读者更全面地了解精密注塑工艺和解决产品缺陷的方法。
【一、精密注塑工艺概述】1.1 精密注塑工艺的定义精密注塑工艺是一种高精度、高稳定性的注塑技术,它主要应用于对产品精度、表面质量和材料要求极高的领域。
1.2 精密注塑工艺的应用领域精密注塑工艺广泛应用于汽车、电子、医疗器械等行业,例如汽车外饰件、无线终端壳体、医疗器械零部件等。
1.3 精密注塑工艺的特点精密注塑工艺具有高精度、高稳定性、高材料要求、高成本等特点,是一种技术含量高、门槛高的注塑工艺。
【二、产品缺陷解决方案】2.1 翘曲解决方案:优化模具结构,增加产品的冷却时间,控制注塑工艺参数。
2.2 气泡解决方案:选择适当的材料、改善模具设计、优化注塑工艺参数。
2.3 热缩解决方案:优化成型工艺、使用专业热缩材料、加强模具表面处理等。
【三、总结与展望】本文总结了100例精密注塑工艺产品缺陷解决方案,从模具设计、材料选用、工艺参数等方面提出了解决问题的方法。
未来,随着工艺技术的不断进步,相信会有更多更先进的产品缺陷解决方案出现,为精密注塑工艺的发展提供更坚实的保障。
【个人观点】作为一名资深的精密注塑工艺工程师,我深知产品缺陷对企业的影响之大。
解决产品缺陷是我们工程师的责任和使命。
通过不断学习和实践,我相信精密注塑工艺在解决产品缺陷方面一定会有更好的表现,为行业发展做出更大的贡献。
总结起来,精密注塑工艺是一门高技术含量的工艺,它在产品缺陷解决方案方面有着丰富的经验和成果。
希望本文的内容能够帮助读者更深入地了解产品缺陷的解决方法,为精密注塑工艺的发展和应用提供借鉴和参考。
注塑缺陷原因分析与解决方案
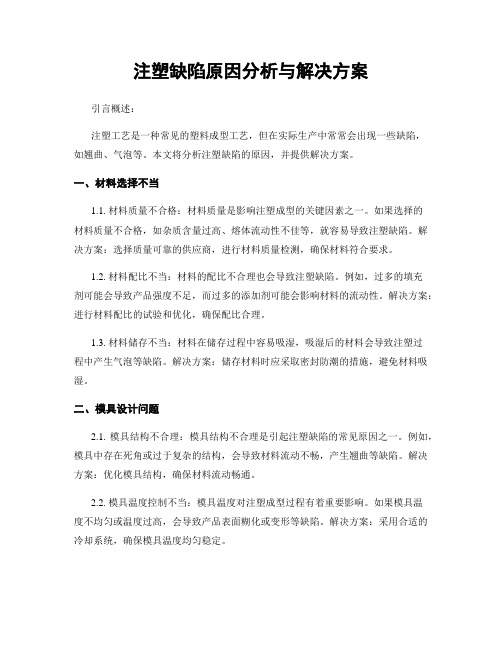
注塑缺陷原因分析与解决方案引言概述:注塑工艺是一种常见的塑料成型工艺,但在实际生产中常常会出现一些缺陷,如翘曲、气泡等。
本文将分析注塑缺陷的原因,并提供解决方案。
一、材料选择不当1.1. 材料质量不合格:材料质量是影响注塑成型的关键因素之一。
如果选择的材料质量不合格,如杂质含量过高、熔体流动性不佳等,就容易导致注塑缺陷。
解决方案:选择质量可靠的供应商,进行材料质量检测,确保材料符合要求。
1.2. 材料配比不当:材料的配比不合理也会导致注塑缺陷。
例如,过多的填充剂可能会导致产品强度不足,而过多的添加剂可能会影响材料的流动性。
解决方案:进行材料配比的试验和优化,确保配比合理。
1.3. 材料储存不当:材料在储存过程中容易吸湿,吸湿后的材料会导致注塑过程中产生气泡等缺陷。
解决方案:储存材料时应采取密封防潮的措施,避免材料吸湿。
二、模具设计问题2.1. 模具结构不合理:模具结构不合理是引起注塑缺陷的常见原因之一。
例如,模具中存在死角或过于复杂的结构,会导致材料流动不畅,产生翘曲等缺陷。
解决方案:优化模具结构,确保材料流动畅通。
2.2. 模具温度控制不当:模具温度对注塑成型过程有着重要影响。
如果模具温度不均匀或温度过高,会导致产品表面糊化或变形等缺陷。
解决方案:采用合适的冷却系统,确保模具温度均匀稳定。
2.3. 模具磨损严重:模具长时间使用后会出现磨损,磨损严重的模具会导致产品尺寸不准确或表面粗糙等缺陷。
解决方案:定期检查和维护模具,及时更换磨损严重的模具部件。
三、注塑工艺参数设置不当3.1. 注射压力过高或过低:注射压力是影响注塑成型的关键参数之一。
如果注射压力过高,会导致产品变形或开裂,而注射压力过低则会导致产品表面光洁度不高。
解决方案:根据产品要求和材料特性,合理设置注射压力。
3.2. 注射速度不合理:注射速度对产品的充填和冷却过程有着重要影响。
如果注射速度过快,会导致产品内部产生气泡或短射,而注射速度过慢则会导致产品表面瑕疵。
注塑缺陷原因分析与解决方案
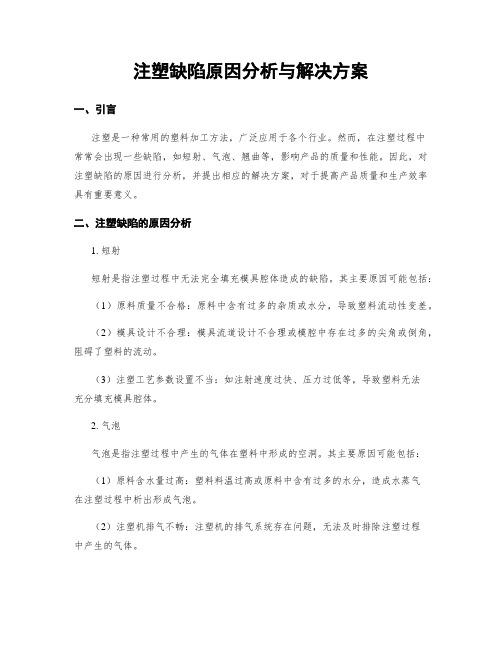
注塑缺陷原因分析与解决方案一、引言注塑是一种常用的塑料加工方法,广泛应用于各个行业。
然而,在注塑过程中常常会出现一些缺陷,如短射、气泡、翘曲等,影响产品的质量和性能。
因此,对注塑缺陷的原因进行分析,并提出相应的解决方案,对于提高产品质量和生产效率具有重要意义。
二、注塑缺陷的原因分析1. 短射短射是指注塑过程中无法完全填充模具腔体造成的缺陷。
其主要原因可能包括:(1)原料质量不合格:原料中含有过多的杂质或水分,导致塑料流动性变差。
(2)模具设计不合理:模具流道设计不合理或模腔中存在过多的尖角或倒角,阻碍了塑料的流动。
(3)注塑工艺参数设置不当:如注射速度过快、压力过低等,导致塑料无法充分填充模具腔体。
2. 气泡气泡是指注塑过程中产生的气体在塑料中形成的空洞。
其主要原因可能包括:(1)原料含水量过高:塑料料温过高或原料中含有过多的水分,造成水蒸气在注塑过程中析出形成气泡。
(2)注塑机排气不畅:注塑机的排气系统存在问题,无法及时排除注塑过程中产生的气体。
(3)注塑工艺参数设置不当:如注射速度过快、压力过高等,造成塑料内部气体无法顺利排出。
3. 翘曲翘曲是指注塑制品在冷却后出现变形的现象。
其主要原因可能包括:(1)模具温度不均匀:模具温度不均匀导致注塑制品冷却不均匀,从而引起翘曲。
(2)注塑过程中的应力积累:注塑过程中,塑料在注射后会受到冷却和收缩的影响,如果释放不及时,会导致应力积累引起翘曲。
(3)注塑工艺参数设置不当:如注射速度过快、冷却时间过短等,造成塑料冷却不充分,引起翘曲。
三、注塑缺陷的解决方案1. 短射的解决方案(1)优化原料质量:选择质量合格的原料,避免杂质和水分的存在。
(2)优化模具设计:合理设计模具流道,避免尖角和倒角的存在,保证塑料的顺畅流动。
(3)优化注塑工艺参数:合理设置注射速度和压力,确保塑料能够充分填充模具腔体。
2. 气泡的解决方案(1)控制原料含水量:确保塑料料温适宜,原料中的水分含量符合要求。
PVC注塑问题的改善措施(大全五篇)

PVC注塑问题的改善措施(大全五篇)第一篇:PVC注塑问题的改善措施PVC注塑件问题的改善措施(一)解決PVC件的牛屎紋和夾水紋問題,首先是必須降低熔膠射進型腔的速度,防止產生折疊波浪形或螺旋形射膠和分流等不平穩的充型。
但是,有時會因模具型腔过于寬大的原故,當射膠速度已經降到螺杆几乎都不能前进時,牛屎紋和夾水紋問題仍然未能解決,這种情況在生產中時常出现。
如果在靠近入水口前的流道上,增加一個阻水針或者加一個緩沖包,可以起到帮助降低熔膠進入型腔之速度的作用,从而能夠达到減輕注塑件的牛屎紋和夾水紋程度的目的。
對于牛屎紋和夾水紋不是特別嚴重的情況,使用這种方法再配合調機技巧,牛屎紋和夾水紋問題是可以解決的。
但是如果問題比较嚴重,就需要再配合更多的解決措施了解決PVC注塑件的牛屎紋和夾水紋難題,需要用到非常慢的射膠速度進行一級射膠。
但是因為速度太慢,熔膠在流道中運行的時間過長,熱量散失將會很大,溫度下降得太多,熔膠的流動性會大大下降,充型將变得更加困難,這樣對解決問題极為不利。
升高熔膠溫度和模具溫度是解決問題的一个改善措施。
升高熔膠溫度,可以使慢速射膠有足夠的溫度來保証熔膠的流動性,但所調高的溫度以不使PVC燒膠為前提。
如果再增加一點背壓,效果就更好。
有時我們宁愿不調太高的熔胶溫度,而多增加一點背壓。
因為增加背壓不但可以使PVC熔膠溫度更加均勻,流動性更好,而且還有升溫的作用,所以比單獨升高溫度對改善流動性會更好。
既升高熔膠溫度又加大背壓PVC會很容易造成燒膠問題。
適當升高模具溫度,可以減慢熔膠散熱的速度,确保PVC長時間的慢速充型仍能保障足夠的流動性。
因此,在注塑件不產生縮水問題的情況下,應盡可能地多升高一點模具溫度,減小泠卻水的流量或是干脆不通冷却水注塑。
總之能夠提高流動性的措施都會對解決PVC夾水紋和牛屎紋問題有好處。
此外,減少水口料的含量,增加一點擴散油等等也都會對問題的解決有幫助。
新機和优质的注塑機的改善效果都會好过残机和普通机。
注塑成型问题点以及解决方法

注塑成型问题点以及解决方法第一篇:注塑成型问题点以及解决方法注塑件缺陷的原因及其补救方法填充不满1.注塑件缺陷的特征注塑过程不完全,因为模腔没有填满塑料或注塑过程缺少某些细节。
2.可能出现问题的原因(1).注塑速度不足。
(2).塑料短缺。
(3).螺杆在行程结束处没留下螺杆垫料。
(4).运行时间变化。
(5).射料缸温度太低。
(6).注塑压力不足。
(7).射嘴部分被封。
(8).射嘴或射料缸外的加热器不能运作。
(9).注塑时间太短。
(10).塑料贴在料斗喉壁上。
(11).注塑机容量太小(即注射重量或塑化能力)。
(12).模温太低。
(13).没有清理干净模具的防锈油。
(14).止退环损坏,熔料有倒流现象。
3.补救方法(1).增加注塑速度。
(2).检查料斗内的塑料量。
(3).检查是否正确设定了注射行程,需要的话进行更改。
(4).检查止逆阀是否磨损或出现裂缝。
(5).检查运作是否稳定。
(6).增加熔胶温度。
(7).增加背压。
(8).增加注塑速度。
(9).检查射嘴孔有没有异物或未塑化塑料。
(10).检查所有的加热器外层用安培表检验能量输出是否正确。
(11).增加螺杆向前时间。
(12).增料斗喉区的冷却量,或降低射料缸后区温度。
(13).用较大的注塑机。
(14).适当升高模温。
(15).清理干净模具内的防锈剂。
(16).检查或更换止退环。
注塑件尺寸差异1.注塑件缺陷的特征注塑过程中重量尺寸的变化超过了模具、注塑机、塑料组合的生产能力。
2.可能出现问题的原因(1).输入射料缸内的塑料不均。
(2).射料缸温度或波动的范围太大。
(3).注塑机容量太小。
(4).注塑压力不稳定。
(5).螺杆复位不稳定。
(6).运作时间的变化、溶液黏度不一致。
(7).注射速度(流量控制)不稳定。
(8).使用了不适合模具的塑料品种。
(9).考虑模温、注射压力、速度、时间和保压等对产品的影响。
3.补救方法(1).检查有无充足的冷却水流经料斗喉以保持正确的温度。
注塑缺陷原因分析与解决方案

注塑缺陷原因分析与解决方案一、引言注塑是一种常用的塑料加工方法,广泛应用于各个行业。
然而,在注塑过程中,可能会出现一些缺陷,例如短斑、气泡、翘曲等问题,这些缺陷会影响产品质量和使用寿命。
因此,对注塑缺陷的原因进行分析,并提出相应的解决方案,对于提高产品质量具有重要意义。
二、注塑缺陷原因分析1. 温度控制不当:注塑过程中,温度是一个关键因素。
如果温度过高或过低,都会导致注塑缺陷。
例如,温度过高会导致熔融物流动性增加,易产生短斑;温度过低会导致熔融物流动性降低,易产生翘曲。
2. 压力控制不当:注塑过程中,压力也是一个重要因素。
如果压力过高或过低,都会导致注塑缺陷。
例如,压力过高会导致短斑、气泡等缺陷;压力过低会导致产品密度不足,易产生翘曲。
3. 注塑模具设计问题:注塑模具的设计也会影响产品质量。
如果模具设计不合理,例如流道设计不良、冷却系统不完善等,都会导致注塑缺陷的产生。
4. 塑料材料选择不当:不同的塑料材料具有不同的熔点、流动性等特性。
如果选择的塑料材料与产品要求不匹配,也会导致注塑缺陷。
例如,选择的塑料材料熔点过高,容易产生短斑;选择的塑料材料流动性不足,容易产生翘曲。
5. 操作人员技术水平不高:注塑过程需要操作人员具备一定的技术水平。
如果操作人员技术水平不高,不了解注塑工艺的要点,也会导致注塑缺陷的产生。
三、注塑缺陷解决方案1. 温度控制方案:合理控制注塑过程中的温度,根据塑料材料的特性和产品要求,调整熔融温度和模具温度。
可以通过使用温度传感器和温度控制器来实时监测和调整温度,确保温度在合适的范围内。
2. 压力控制方案:合理控制注塑过程中的压力,根据塑料材料的特性和产品要求,调整注射压力和保压压力。
可以通过使用压力传感器和压力控制器来实时监测和调整压力,确保压力在合适的范围内。
3. 注塑模具设计方案:优化注塑模具的设计,确保流道设计合理、冷却系统完善。
可以通过使用CAD软件进行模具设计和模拟分析,优化模具结构,减少缺陷的产生。
注塑数字化解决方案及行业标杆案例
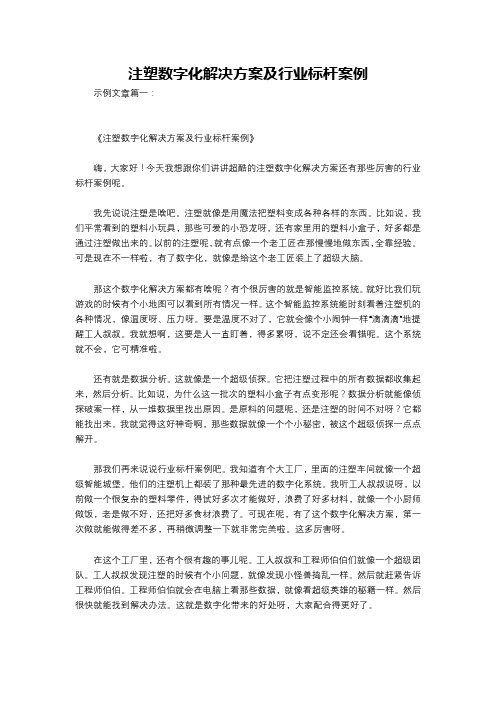
注塑数字化解决方案及行业标杆案例示例文章篇一:《注塑数字化解决方案及行业标杆案例》嗨,大家好!今天我想跟你们讲讲超酷的注塑数字化解决方案还有那些厉害的行业标杆案例呢。
我先说说注塑是啥吧。
注塑就像是用魔法把塑料变成各种各样的东西。
比如说,我们平常看到的塑料小玩具,那些可爱的小恐龙呀,还有家里用的塑料小盒子,好多都是通过注塑做出来的。
以前的注塑呢,就有点像一个老工匠在那慢慢地做东西,全靠经验。
可是现在不一样啦,有了数字化,就像是给这个老工匠装上了超级大脑。
那这个数字化解决方案都有啥呢?有个很厉害的就是智能监控系统。
就好比我们玩游戏的时候有个小地图可以看到所有情况一样。
这个智能监控系统能时刻看着注塑机的各种情况,像温度呀、压力呀。
要是温度不对了,它就会像个小闹钟一样“滴滴滴”地提醒工人叔叔。
我就想啊,这要是人一直盯着,得多累呀,说不定还会看错呢。
这个系统就不会,它可精准啦。
还有就是数据分析。
这就像是一个超级侦探。
它把注塑过程中的所有数据都收集起来,然后分析。
比如说,为什么这一批次的塑料小盒子有点变形呢?数据分析就能像侦探破案一样,从一堆数据里找出原因。
是原料的问题呢,还是注塑的时间不对呀?它都能找出来。
我就觉得这好神奇啊,那些数据就像一个个小秘密,被这个超级侦探一点点解开。
那我们再来说说行业标杆案例吧。
我知道有个大工厂,里面的注塑车间就像一个超级智能城堡。
他们的注塑机上都装了那种最先进的数字化系统。
我听工人叔叔说呀,以前做一个很复杂的塑料零件,得试好多次才能做好,浪费了好多材料,就像一个小厨师做饭,老是做不好,还把好多食材浪费了。
可现在呢,有了这个数字化解决方案,第一次做就能做得差不多,再稍微调整一下就非常完美啦。
这多厉害呀。
在这个工厂里,还有个很有趣的事儿呢。
工人叔叔和工程师伯伯们就像一个超级团队。
工人叔叔发现注塑的时候有个小问题,就像发现小怪兽捣乱一样。
然后就赶紧告诉工程师伯伯。
工程师伯伯就会在电脑上看那些数据,就像看超级英雄的秘籍一样。
精密注塑工艺与产品缺陷解决方案

精密注塑工艺与产品缺陷解决方案
《精密注塑工艺与产品缺陷解决方案》
精密注塑工艺是一种高精度、高效率的塑料加工工艺,它可以为汽车、电子、医疗等行业提供高质量的注塑产品。
然而,在实际生产过程中,由于材料、模具、工艺等方面的因素,往往会导致产品出现一些缺陷,如气泡、熔接痕、收缩不均等。
为了解决这些问题,需要采取一些有效的解决方案。
首先,对于气泡问题,可以通过优化注射速度、压力和温度,合理设计模具结构和通气系统来减少气泡的产生。
此外,选择适当的原料和合适的干燥工艺也是减少气泡的重要手段。
其次,针对熔接痕和热分解问题,可以采用增加模具温度、提高熔体温度、改善注塑压力等方式来改善熔接性能,同时合理设计产品结构和增加辅助加热系统也能有效地减少热分解问题的发生。
最后,对于收缩不均问题,可以通过调整模具结构、改变注塑工艺参数、进行模具表面处理等方法来改善产品的收缩性能,从而减少收缩不均带来的问题。
综上所述,精密注塑工艺的产品缺陷并非不可解决,只要对问题进行深入分析,综合考虑材料、模具和工艺等方面的因素,并采取有效的解决方案,就能够有效地提高产品的质量和生产效率。
希望通过不断地研究和实践,精密注塑工艺在未来能够取得更大的发展和进步。
注塑缺陷原因分析与解决方案

注塑缺陷原因分析与解决方案一、引言注塑是一种常见的塑料加工方法,广泛应用于各个行业。
然而,在注塑过程中往往会浮现一些缺陷,如短射、气泡、热缩等。
本文将对注塑缺陷的原因进行分析,并提出相应的解决方案,以匡助企业提高产品质量和生产效率。
二、注塑缺陷原因分析1. 短射短射是指注塑过程中无法将塑料彻底填充模具腔体的现象。
短射的原因可能包括以下几点:- 模具设计不合理:模具的流道设计不合理或者过小,导致塑料无法充分流动。
- 注塑参数设置不当:注塑机的注射速度、压力等参数设置不当,影响了塑料的充填性能。
- 塑料材料选择不当:选择的塑料材料流动性差,导致无法充分填充模具腔体。
2. 气泡气泡是指注塑制品中浮现的气体会萃的现象。
气泡的原因可能包括以下几点:- 塑料材料含水量高:塑料材料含水量高会在注塑过程中产生蒸汽,形成气泡。
- 注塑机排气不畅:注塑机排气系统不畅,无法及时排出注塑过程中产生的气体。
- 模具设计不合理:模具中存在死角或者过小的通气孔,导致气体无法顺利排出。
3. 热缩热缩是指注塑制品在冷却后发生尺寸变化的现象。
热缩的原因可能包括以下几点:- 注塑温度过高:注塑温度过高会导致塑料在冷却后收缩过大。
- 模具温度不均匀:模具的温度分布不均匀,导致注塑制品冷却不均匀,进而引起热缩。
- 塑料材料热性能不稳定:选择的塑料材料热性能不稳定,导致注塑制品在冷却后发生尺寸变化。
三、注塑缺陷解决方案1. 短射解决方案- 模具设计合理化:优化模具的流道设计,增加流道的截面积,确保塑料能够充分流动。
- 注塑参数优化:根据塑料材料的特性,合理设置注塑机的注射速度、压力等参数,保证塑料充填模具腔体。
- 选择合适的塑料材料:根据产品的要求,选择流动性好的塑料材料,提高充填性能。
2. 气泡解决方案- 塑料材料干燥处理:在注塑过程前,对塑料材料进行干燥处理,降低含水量,减少气泡的产生。
- 注塑机排气系统改进:优化注塑机的排气系统,增加排气孔的数量和大小,提高排气效果。
注塑产品不良原因分析及解决方案

注塑产品不良原因分析及解决方案注塑产品不良原因分析与解决方案注塑成型技术在现代制造业中无处不在,从汽车零件到家用电器,甚至医疗器械,都离不开它。
虽然这种技术已相当成熟,但问题依然层出不穷,特别是不良品的出现,真是让人感到头疼。
为了提升产品质量、降低成本、提升客户的满意度,找出问题的根源并提出有效的解决方案,显得尤为重要。
目标与范围本文的目的是要搞清楚注塑产品为何会出现不良现象,并制定具体可行的解决方案,以确保后续生产能够顺利进行。
我们将关注注塑过程中的每一个环节,从原材料的选择、模具设计、工艺流程、设备维护到质量管理,统统包括在内。
现状分析在不少企业里,注塑生产线运转频繁,效率也很高,不过,这并不意味着没有问题。
有一家汽车零部件厂家,过去一年因为不良品损失了足足50万元。
经过初步调查,发现问题主要集中在这几个方面:1. 原材料问题:一些塑料原料质量不稳定,导致成品强度不足或外观缺陷。
2. 模具设计缺陷:模具设计不合理,影响了塑料的流动,最终影响了成型质量。
3. 工艺参数设置不当:如温度、压力和注射速度等参数的控制不严,导致了产品缺陷。
4. 设备老化:一些注塑机老旧,频繁机械故障,生产效率受影响。
5. 人员素质参差不齐:操作工的技术水平参差不齐,导致操作不规范,增加了不良品的发生。
不良原因具体分析原材料问题原材料是注塑的基础,如果原料质量不过关,成品的性能和外观就会大打折扣。
不同批次的原料物性和化学成分可能差异很大,直接影响到成品的强度和韧性。
模具设计缺陷模具设计不合理会导致塑料在流动时出现不均匀现象,比如浇口设计不当可能会造成气泡或空洞,直接影响产品的密度和强度。
工艺参数设置不当每种材料都有其最佳的注塑工艺参数,未能严格遵循这些参数设置,成品就可能出现缺陷。
比如,注射温度过低可能导致塑料未能完全熔化,注射压力不足则可能导致成品填充不完全。
设备老化设备老化和维护不足会导致注塑机性能下降,常见的如注射速度不够、压力不足等,都会直接影响成品质量。
注塑产品缺陷分析报告
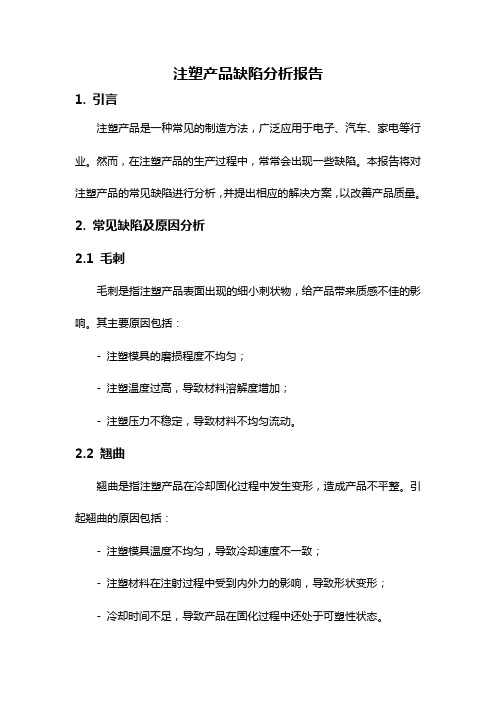
注塑产品缺陷分析报告1. 引言注塑产品是一种常见的制造方法,广泛应用于电子、汽车、家电等行业。
然而,在注塑产品的生产过程中,常常会出现一些缺陷。
本报告将对注塑产品的常见缺陷进行分析,并提出相应的解决方案,以改善产品质量。
2. 常见缺陷及原因分析2.1 毛刺毛刺是指注塑产品表面出现的细小刺状物,给产品带来质感不佳的影响。
其主要原因包括:- 注塑模具的磨损程度不均匀;- 注塑温度过高,导致材料溶解度增加;- 注塑压力不稳定,导致材料不均匀流动。
2.2 翘曲翘曲是指注塑产品在冷却固化过程中发生变形,造成产品不平整。
引起翘曲的原因包括:- 注塑模具温度不均匀,导致冷却速度不一致;- 注塑材料在注射过程中受到内外力的影响,导致形状变形;- 冷却时间不足,导致产品在固化过程中还处于可塑性状态。
2.3 气泡气泡是指注塑产品内部存在的气体充填,导致产品表面出现气孔。
气泡的产生原因主要有:- 注塑模具中脱模剂残留;- 注塑材料中含有过多的挥发性成分;- 注塑过程中注入速度过快,气体无法及时排出。
3. 解决方案针对注塑产品的常见缺陷,我们可以采取以下措施来改善产品质量:3.1 控制注塑模具质量定期检查模具是否磨损严重,对磨损严重的模具及时更换或修复,以确保模具表面的平整度和光洁度。
3.2 控制注塑温度和压力合理控制注塑温度和压力,避免温度过高或压力不稳定导致材料流动不均匀,从而减少毛刺的产生。
3.3 控制注塑模具温度保持注塑模具温度均匀,避免冷却速度不一致导致翘曲。
对于大型注塑产品,可以在模具上设置冷却系统,加速冷却过程。
3.4 增加冷却时间合理增加冷却时间,使注塑产品充分固化。
同时,可以考虑在注塑产品中增加支撑结构,以避免变形。
3.5 移除脱模剂在注塑过程中,及时清除模具表面的脱模剂残留,以避免气泡的产生。
3.6 控制注射速度合理控制注射速度,避免注入速度过快导致气体无法及时排出。
可以采用缓慢注射的方式,确保材料充分填充,同时减少气泡的产生。
注塑缺陷原因分析与解决方案
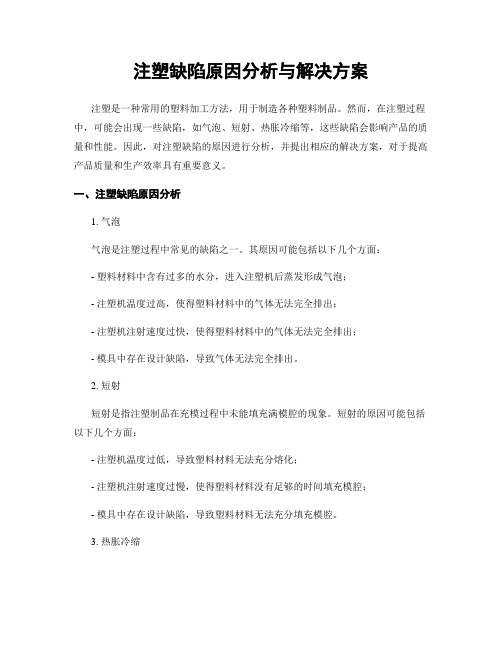
注塑缺陷原因分析与解决方案注塑是一种常用的塑料加工方法,用于制造各种塑料制品。
然而,在注塑过程中,可能会出现一些缺陷,如气泡、短射、热胀冷缩等,这些缺陷会影响产品的质量和性能。
因此,对注塑缺陷的原因进行分析,并提出相应的解决方案,对于提高产品质量和生产效率具有重要意义。
一、注塑缺陷原因分析1. 气泡气泡是注塑过程中常见的缺陷之一。
其原因可能包括以下几个方面:- 塑料材料中含有过多的水分,进入注塑机后蒸发形成气泡;- 注塑机温度过高,使得塑料材料中的气体无法完全排出;- 注塑机注射速度过快,使得塑料材料中的气体无法完全排出;- 模具中存在设计缺陷,导致气体无法完全排出。
2. 短射短射是指注塑制品在充模过程中未能填充满模腔的现象。
短射的原因可能包括以下几个方面:- 注塑机温度过低,导致塑料材料无法充分熔化;- 注塑机注射速度过慢,使得塑料材料没有足够的时间填充模腔;- 模具中存在设计缺陷,导致塑料材料无法充分填充模腔。
3. 热胀冷缩热胀冷缩是指注塑制品在冷却过程中发生尺寸变化的现象。
热胀冷缩的原因可能包括以下几个方面:- 注塑机温度控制不准确,导致塑料材料在冷却过程中温度变化不均匀;- 注塑机冷却时间过短,使得塑料材料没有足够的时间冷却固化;- 注塑机冷却压力不足,使得塑料材料在冷却过程中发生变形。
二、注塑缺陷解决方案1. 气泡解决方案- 使用干燥塑料材料,避免材料中含有过多的水分;- 控制注塑机温度,确保塑料材料中的气体能够完全排出;- 调整注塑机注射速度,使得塑料材料中的气体能够完全排出;- 设计合理的模具,确保气体能够完全排出。
2. 短射解决方案- 调整注塑机温度,确保塑料材料能够充分熔化;- 调整注塑机注射速度,使得塑料材料有足够的时间填充模腔;- 设计合理的模具,确保塑料材料能够充分填充模腔。
3. 热胀冷缩解决方案- 控制注塑机温度,确保塑料材料在冷却过程中温度变化均匀;- 增加注塑机冷却时间,使得塑料材料有足够的时间冷却固化;- 调整注塑机冷却压力,确保塑料材料在冷却过程中不发生变形。
注塑缺陷原因分析与解决方案

注塑缺陷原因分析与解决方案一、引言注塑工艺是一种常用的塑料加工方法,广泛应用于各个领域。
然而,在注塑过程中,常常会出现一些缺陷,如气泡、翘曲、短射等问题,严重影响产品的质量和性能。
因此,对注塑缺陷的原因进行分析,并提出相应的解决方案,对于提高产品质量和生产效率具有重要意义。
二、注塑缺陷的原因分析1. 模具设计不合理:模具是注塑过程中的关键因素之一,模具的设计不合理会导致产品缺陷。
例如,模具中存在过于复杂的结构、不合理的冷却系统等,都可能引起产品的翘曲、短射等问题。
2. 塑料材料选择不当:不同的塑料材料具有不同的物理性能和熔融特性,选择不当会导致产品缺陷。
例如,选择的塑料材料熔点过高或过低,都会影响产品的成型效果。
3. 注塑工艺参数设置错误:注塑工艺参数的设置对于产品质量至关重要。
例如,注射压力、注射速度、保压时间等参数的设置不当,都会导致产品的缺陷,如气泡、短射等。
4. 模具磨损和老化:长时间使用的模具会出现磨损和老化现象,导致产品的尺寸精度下降。
此外,模具的使用寿命过长也会影响产品质量。
5. 注塑设备故障:注塑设备的故障也是导致产品缺陷的原因之一。
例如,注射机的温度控制不准确、压力控制不稳定等,都会对产品的成型效果产生影响。
三、注塑缺陷的解决方案1. 模具设计优化:通过对模具的结构进行优化设计,减少复杂结构的使用,合理设计冷却系统,可以有效降低产品缺陷的发生率。
2. 塑料材料选择合理:根据产品的要求和特性选择合适的塑料材料,确保其熔融特性和物理性能与产品的要求相匹配。
3. 注塑工艺参数优化:通过合理设置注塑工艺参数,如注射压力、注射速度、保压时间等,控制好温度和压力的变化,可以提高产品的成型效果。
4. 定期维护和更换模具:定期对模具进行维护,及时更换磨损和老化的部件,可以保证模具的精度和使用寿命,提高产品的质量。
5. 定期检查和维护注塑设备:定期检查注塑设备的温度控制、压力控制等系统,确保其正常工作,减少设备故障对产品质量的影响。
注塑时出现的问题及解决方法

注塑时出现的问题及解决方法
注塑的时候要是出问题了那可真让人头疼!比如说出现飞边,这就像一个调皮的孩子在不该出现的地方捣乱。
那咋解决呢?得调整模具的合模力呀,就像给一个调皮的孩子戴上紧箍咒,让它老老实实地待在该待的地方。
注塑产品出现缩水,哎呀,这就好像一个气球瘪了一块。
这时候可以增加注射压力和保压时间,就如同给气球多吹点气,让它鼓起来。
注意哦,压力也不能太大,不然模具可受不了,那可就糟糕啦!
注塑过程安全不?那肯定得重视啊!就像开车一样,得时刻小心。
操作设备要规范,不然很容易出事故。
稳定性也很重要,要是一会儿好一会儿坏,那可就像坐过山车,让人心里七上八下的。
注塑的应用场景可多啦!玩具、电子产品外壳,到处都能看到注塑的身影。
为啥这么受欢迎呢?因为它生产效率高啊!就像一个高效的小蜜蜂,不停地为我们制造各种好用的东西。
而且可以做出各种复杂的形状,这多厉害呀!
我就知道一个实际案例,有个工厂生产玩具,一开始注塑总是出问
题,产品质量参差不齐。
后来经过技术人员的调整,问题解决了,生产出的玩具又漂亮又结实。
这效果,杠杠的!
注塑虽然有时候会出问题,但只要我们认真对待,找到解决方法,就能发挥它的巨大优势。
让我们一起用好注塑技术,创造更多美好的产品吧!。
注塑产品不良原因分析及解决方案【范本模板】

注塑成型品质改善原因分析未射饱(缺料)1。
射出压力不足;2。
保压压力不足;3。
射出时间不足;4.加料(储料)不足;5。
射料分段位置太小;6。
射出终点位置太小;7。
射出速度不够快;8。
射嘴﹑料管温度不够;9.模具温度不够;10。
原料烘干温度﹑时间不足;11.注塑周期太快,预热不足;12。
原料搅拌不均匀;(背压不足,转速不够) 13.原料流动性不足(产品壁太薄);14。
模具排气不足;15。
模具进料不均匀;16。
冷料井设计不合理;17.冷料口太小,方向不合理;18。
模穴內塑胶流向不合理;19。
模具冷卻不均匀;20.注塑机油路不精确﹑不够快速;21.电热系統不稳定,不精确;22.射嘴漏料,有异物卡住;23.料管內壁﹑螺杆磨损,配合不良;毛边(飞边)1。
射出压力和压力太大;2.锁模高压不够;3。
背压太大;4.射出和保压时间太长;5.储料延迟和冷却时间太长;6.停机太长,未射出热料;7。
射出压。
保压速度太快;8.螺杆转速太快,塑胶剪切,磨擦过热;9.料管温度太高。
流延;10.模温太高﹑模腔冷却不均匀;11。
注塑行程调试不合理;12。
保压切换点,射出终点太大;13。
模具裝配组合不严密;14.合模有异物,调模位置不足;15.锁模机构不平行﹑精确;16.顶针润滑﹑保养不足;17.滑块﹑斜导柱配合压不到位;18.模腔镶件未压到位,撐出模面;19。
进料口设计分布不均匀合理;20.产品设计导致某处內壁太薄和结尾处太远;21。
小镶件组合方式不合理,易发生变形;22。
镶件因生产中磨损﹑变形﹑圆角;23。
镶件未设计稳固性﹑未抱合,加固;24。
模腔內排气槽太深;气泡(气疮)1.射出﹑保压压力不足;2.背压太小﹑原料不够扎实;3。
射出速度太快;4。
储料速度太快;5。
料管温度太高, 模具温度太低;6。
材料烘干温度﹑时间不足;7。
射退太多;8。
注塑周期太长(预热时间增加);9.加料位置不足,射出终点太小; 10。
前﹑后松退位置太长;11.机器油压不稳定;12.料管﹑螺杆压缩比不够;13。
注塑产品内孔偏心解决方案
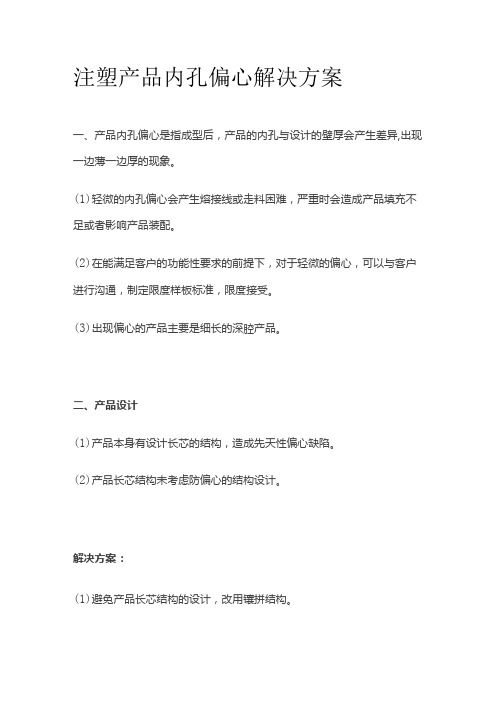
注塑产品内孔偏心解决方案
一、产品内孔偏心是指成型后,产品的内孔与设计的壁厚会产生差异,出现一边薄一边厚的现象。
(1)轻微的内孔偏心会产生熔接线或走料困难,严重时会造成产品填充不足或者影响产品装配。
(2)在能满足客户的功能性要求的前提下,对于轻微的偏心,可以与客户进行沟通,制定限度样板标准,限度接受。
(3)出现偏心的产品主要是细长的深腔产品。
二、产品设计
(1)产品本身有设计长芯的结构,造成先天性偏心缺陷。
(2)产品长芯结构未考虑防偏心的结构设计。
解决方案:
(1)避免产品长芯结构的设计,改用镶拼结构。
(2)长芯产品做碰穿结构,以防偏心。
三、模具
(1)长芯加工过程中有较大的偏心,造成产品往一边偏。
(2)模具的长芯没有设计冷却系统,生产过程中因为高温造成模具长芯往一边变形而偏心。
(3)长芯镶件的强度不足。
(4)浇口设计不合理,成型时冲偏型芯。
解决方案:
(1)提高模具加H精度,设计可调整长芯偏心的模具结构。
(2)加强模具长芯镶件的冷却效果。
(3)模具长芯镶件设计相对大一点,以保证强度。
(4)优化浇口.
四、注塑工艺
(1)注射压力过大,把模具长芯镶件冲偏。
(2)注射速度过快,使熔融的原料往一边挤压,而形成偏心。
解决方案:
(1)低压注射。
(2)先以低速进行注射,保证长芯镶件周边都有原料后,再进行高速注射,以降低偏心。
注塑堵孔分析报告模板
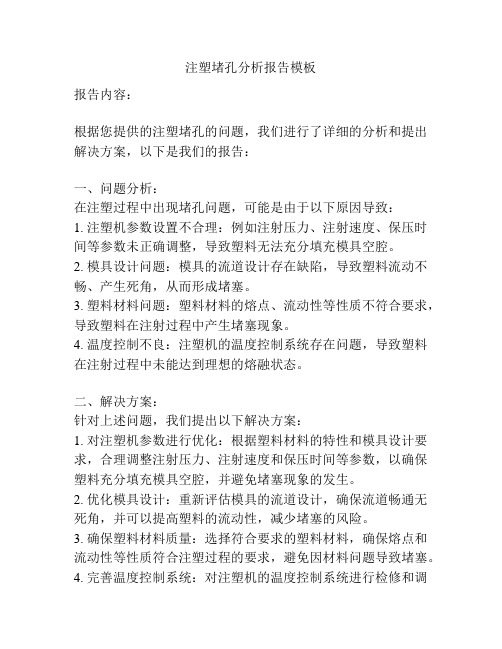
注塑堵孔分析报告模板报告内容:根据您提供的注塑堵孔的问题,我们进行了详细的分析和提出解决方案,以下是我们的报告:一、问题分析:在注塑过程中出现堵孔问题,可能是由于以下原因导致:1. 注塑机参数设置不合理:例如注射压力、注射速度、保压时间等参数未正确调整,导致塑料无法充分填充模具空腔。
2. 模具设计问题:模具的流道设计存在缺陷,导致塑料流动不畅、产生死角,从而形成堵塞。
3. 塑料材料问题:塑料材料的熔点、流动性等性质不符合要求,导致塑料在注射过程中产生堵塞现象。
4. 温度控制不良:注塑机的温度控制系统存在问题,导致塑料在注射过程中未能达到理想的熔融状态。
二、解决方案:针对上述问题,我们提出以下解决方案:1. 对注塑机参数进行优化:根据塑料材料的特性和模具设计要求,合理调整注射压力、注射速度和保压时间等参数,以确保塑料充分填充模具空腔,并避免堵塞现象的发生。
2. 优化模具设计:重新评估模具的流道设计,确保流道畅通无死角,并可以提高塑料的流动性,减少堵塞的风险。
3. 确保塑料材料质量:选择符合要求的塑料材料,确保熔点和流动性等性质符合注塑过程的要求,避免因材料问题导致堵塞。
4. 完善温度控制系统:对注塑机的温度控制系统进行检修和调整,确保温度能够准确控制在塑料熔融的温度范围内,提高塑料的流动性和填充性能。
三、预期效果:通过以上解决方案的实施,我们预计可以达到以下效果:1. 堵孔问题将得到有效解决,注塑产品的质量将得到提升。
2. 降低生产中的不良品率,改善生产效益。
3. 提高生产过程的稳定性和可靠性,降低故障率,减少维修和更换成本。
四、实施计划:为了确保解决方案的有效实施,我们建议按照以下步骤进行:1. 针对注塑机参数进行优化,进行试模和调整,找到最佳参数组合。
2. 对模具进行改进设计,并进行试模验证,确保流道畅通,并提高流动性。
3. 选择符合要求的塑料材料,并进行试模验证,检查是否满足注塑过程的要求。
塑料注塑缺陷解决方案

塑料注塑缺陷解决方案塑料注塑缺陷解决方案塑料注塑是一种常见的生产工艺,被广泛应用于各个行业。
然而,由于材料和工艺的限制,塑料注塑过程中常常会出现一些缺陷。
为了解决这些问题,我们需要采取一些有效的解决方案。
首先,一个常见的缺陷是短射。
短射是指注塑件的某些部分未能完全填充模具腔体的现象。
要解决这个问题,我们可以采取以下措施。
首先,我们可以调整模具的温度和压力,以确保塑料能够充分流动并填充整个模具腔体。
其次,我们还可以优化注塑机的注射速度和时间,以避免短射现象的发生。
此外,我们还可以通过增加模具的填充系统来改善填充效果,确保塑料能够均匀地填充整个模具腔体。
另一个常见的缺陷是气泡。
气泡是注塑件中存在的空洞或气体囊泡。
气泡的存在不仅影响产品的外观质量,还可能降低产品的强度和密封性能。
为了解决这个问题,我们可以采取以下解决方案。
首先,我们可以通过优化注塑机的压力和温度控制,以减少气体的产生和聚集。
其次,我们可以使用一些抗气泡剂,如表面活性剂,来改善塑料的流动性和排气性能,减少气泡的生成。
此外,我们还可以通过增加模具的通气系统来增加气泡的排出通道,进一步降低气泡的产生和积聚。
除了短射和气泡外,还有一些其他常见的塑料注塑缺陷,如毛刺、水口印和收缩等。
对于这些问题,我们也可以采取一些解决方案来改善产品的质量。
例如,我们可以优化模具的设计和加工工艺,以减少毛刺和水口印的产生。
此外,我们还可以选择合适的塑料材料,以减小产品的收缩率,提高产品的尺寸稳定性。
总之,塑料注塑缺陷是一个普遍存在的问题,但我们可以通过采取一些有效的解决方案来改善产品的质量。
通过调整温度和压力、优化注塑机的参数、使用抗气泡剂等方法,我们可以有效地解决短射和气泡等常见的缺陷问题。
此外,通过优化模具设计和加工工艺,以及选择合适的塑料材料,我们还可以解决其他一些常见的缺陷问题。
通过不断改进和创新,我们相信塑料注塑缺陷问题将不再是一个难题。
- 1、下载文档前请自行甄别文档内容的完整性,平台不提供额外的编辑、内容补充、找答案等附加服务。
- 2、"仅部分预览"的文档,不可在线预览部分如存在完整性等问题,可反馈申请退款(可完整预览的文档不适用该条件!)。
- 3、如文档侵犯您的权益,请联系客服反馈,我们会尽快为您处理(人工客服工作时间:9:00-18:30)。
注塑产品问题解决方案
注塑是一种常见的制造方法,注塑产品广泛应用于各种领域,例如家电、汽车、玩具等。
尽管注塑技术已经相当成熟,但在注塑过程中仍然会遇到一些问题,例如气泡、缩孔、变形等。
本文将介绍一些常见的问题以及相应的解决方案。
气泡
气泡是注塑产品中最常见的问题之一。
气泡会影响注塑产
品的外观和质量,降低产品的耐用程度。
通常,气泡的形成是由于注塑过程中的空气未被排出,随着塑料的凝固,气泡被困在塑料中。
为了避免气泡的产生,以下是几种常见的解决方案:
1. 提高注塑压力
提高注塑压力可以帮助排出空气,从而减少气泡的产生。
但增加注塑压力会增加生产成本。
2. 增加注塑温度
增加注塑温度可以使塑料更易于流动,并从根本上减少空
气的难以排出。
然而,过高的温度可能会导致塑料烧焦和质量损失。
3. 优化注塑模具
优化注塑模具可以改善塑料流动性,减少气泡产生。
例如,增加冷却系统和优化出料角度。
缩孔
缩孔是注塑产品中的一种缺陷,这是由于塑料在冷却时产
生过度收缩而导致的。
缩孔会导致注塑产品表面出现洞、裂痕、不平整等表面缺陷。
以下是几种常见的解决方案:
1. 优化注塑模具
缩孔产生的主要原因是由于注塑模具中的不均匀冷却。
通
过优化注塑模具,可以提高冷却系统的效率,减少缩孔的产生。
2. 增加塑料温度
提高塑料温度可以使塑料更易于流动,并在注塑过程中减
少缩孔的产生。
但是过高的温度可能会导致塑料烧焦和质量损失。
3. 调整注塑压力
通常情况下,缩孔的产生与注塑压力不合适有关。
调整注
塑压力可以减少缩孔的产生。
变形
由于塑料在注塑过程中的物理性质,注塑制品有时会出现
变形现象。
变形通常是由于塑料冷却时的收缩率不平衡引起的。
以下是几种常见的解决方案:
1. 优化注塑模具
优化注塑模具可以改善塑料流动性,减少变形的产生。
例如,增加冷却系统和优化出料角度。
2. 增加塑料温度
增加塑料温度可以使塑料更易于流动,并从根本上减少变
形的产生。
但是过高的温度可能会导致塑料烧焦和质量损失。
3. 关注注塑压力
通过控制注塑压力,可以控制塑料的流动速度,并减少注
塑产品的变形。
结论
注塑技术不仅在日常生活中发挥着重要作用,而且在工业生产中也发挥着重要的作用。
然而,在使用注塑技术生产注塑制品时,会出现许多问题,如气泡、缩孔、变形等,这些问题会影响注塑产品的外观和质量。
本文介绍了一些常见的问题以及相应的解决方案。
根据这些解决方案,我们可以在生产注塑制品时更好地控制生产质量,提高产品质量和效率。