注塑模具收缩率的原因及解决方法
注塑成型缩水原因解析

注塑成型缩水原因解析
注塑成型缩水是指注塑制品在注塑过程中或注塑制品在冷却后出现尺寸缩小的现象。
其原因主要有以下几个方面:
1. 材料选择不当:注塑成型过程中使用的塑料材料可能不适合该制品的尺寸和形状,导致成型后产生缩水现象。
例如,一些高收缩率的塑料材料在注塑成型过程中容易出现缩水现象。
2. 温度控制不当:注塑成型过程中的温度控制非常重要。
如果注塑成型温度过高或过低,会导致塑料熔融不充分,成型后容易出现缩水现象。
3. 注塑工艺参数不合理:注塑成型过程中的一些工艺参数,如压力、注射速度等,对成型质量有直接影响。
如果这些参数不合理,可能导致塑料在注塑过程中发生过度收缩,从而引起缩水现象。
4. 模具设计问题:模具设计不合理也会导致注塑制品出现缩水现象。
例如,模具的冷却系统不良或不均匀,会导致部分塑料过早冷却,从而在冷却后出现缩水现象。
5. 环境温度变化:注塑成型后的塑料制品往往需要冷却固化。
如果环境温度发生较大变化,快速降温可能会导致塑料收缩较多,从而出现缩水现象。
综上所述,注塑成型缩水的原因可能是材料选择不当、温度控制不当、注塑工艺参数不合理、模具设计问题以及环境温度变化等。
要解决缩水问题,需要综合考虑这些因素,并进行相应的优化和调整。
注塑件缩印的产生机理及解决方案

缩印解决方案
本篇讨论的重点
2.5mm 1mm
1.5mm
2.5mm
主 壁 厚 , 筋 的 厚 度
修主 改壁 筋厚 的 厚 度
,
有缩印 无缩印
避免缩印的设计要点
根部t: 0.3T-0.5T 头部:>0.5mm
避免缩印的设计要点
火山口使螺丝柱根部的等效壁厚r变小(r<R)。当螺丝柱的根部等效壁厚r 与本体壁厚T相差不大时,零计要点
因壁厚, 发生缩印。
方案1
把翻边向左侧头部移动,减少厚壁 范围,从而减少缩印的面积
方案2
继续优化 H
可减少缩印面积,但同 时带来模具尖钢,模具 强度不足的问题。
W/H<0.5 同时满足模具强度 要求,且可有效避免缩印
方案3
滑块方向
根部减胶
增加滑块机构,同时根部减胶(请 参照加强筋尺寸设计要点),可有 效避免缩印。
缩印的表现特征
缩印发生的机理示意
缩印
树脂材料注入模具,冷却时,引起体积收缩。 如图所示,有加强筋时,A部体积比周围B部体积大,虽然收 缩率相同,但由于冷却慢,其收缩量较大,即会发生缩印。
缩印的成因
缩印
缩印
缩印成因
零件壁厚的不均
模腔内流动的熔体受到极大 阻力,或者局部型腔和浇口 太狭窄,导致没有的足够的 保压压力传递到型腔
塑料件 缩印(缩痕) 浅谈
什么是缩印?
缩印(sink mark), 是由于产品因为厚薄不均匀而导致产品表面有类似下陷的痕迹。 塑胶在冷却和减压的时候,冷却过程中的体积缩小率要比压力释放的体积增加率大,所以 在降温和压力释放的过程中,零件的体积有收缩的趋势。 在零件厚度差异比较大的地方,厚的部分体积收缩时受到的应力比较薄的部分要大, 如果 这个应力差在零件表面固化之前就已经足够大,就会在使相应的部位表面产生下陷的现象. 注射成型的过程中,厚壁部分比薄壁部分冷却较为缓慢,因而厚壁部分易出现缩印。
注塑件缩影原因分析
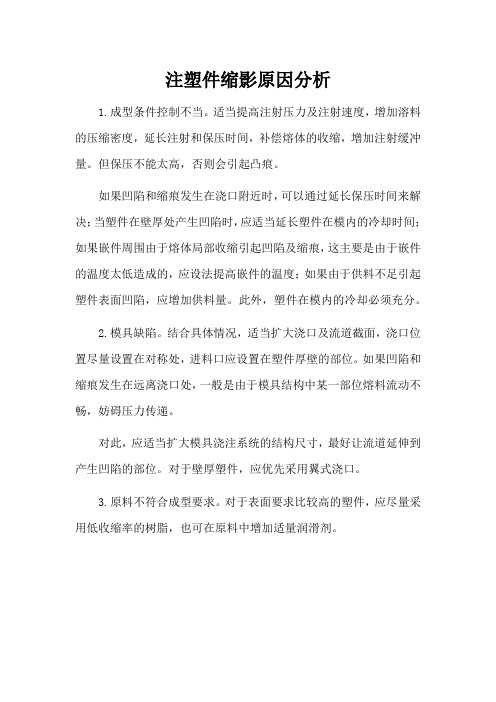
注塑件缩影原因分析
1.成型条件控制不当。
适当提高注射压力及注射速度,增加溶料的压缩密度,延长注射和保压时间,补偿熔体的收缩,增加注射缓冲量。
但保压不能太高,否则会引起凸痕。
如果凹陷和缩痕发生在浇口附近时,可以通过延长保压时间来解决;当塑件在壁厚处产生凹陷时,应适当延长塑件在模内的冷却时间;如果嵌件周围由于熔体局部收缩引起凹陷及缩痕,这主要是由于嵌件的温度太低造成的,应设法提高嵌件的温度;如果由于供料不足引起塑件表面凹陷,应增加供料量。
此外,塑件在模内的冷却必须充分。
2.模具缺陷。
结合具体情况,适当扩大浇口及流道截面,浇口位置尽量设置在对称处,进料口应设置在塑件厚壁的部位。
如果凹陷和缩痕发生在远离浇口处,一般是由于模具结构中某一部位熔料流动不畅,妨碍压力传递。
对此,应适当扩大模具浇注系统的结构尺寸,最好让流道延伸到产生凹陷的部位。
对于壁厚塑件,应优先采用翼式浇口。
3.原料不符合成型要求。
对于表面要求比较高的塑件,应尽量采用低收缩率的树脂,也可在原料中增加适量润滑剂。
注塑收缩形成原因及解决办法

注塑模具收缩率的原因及解决方法引言塑料材料模塑过程中膨胀和收缩量的大小与所加工塑料的热膨胀系数有关,模塑过程的热膨胀系数称为“模塑收缩”。
随着模塑件冷却收缩,模塑件与模腔冷却表面失去紧密接触这时冷却效率下降,模塑件继续冷却后,模塑件不断收缩,收缩量取决于各种因素的综合作用模塑件上的尖角冷却最快,比其它部件更早硬化,接近模塑件中心处的厚的部分离型腔冷却面最远,成为模塑件上最后释放热量的部分,边角处的材料固化后,随着接近制件中心处的熔体冷却,模塑件仍会继续收缩,尖角之间的平面只能得到单侧冷却,其强度没有尖角处材料的强度高。
制件中心处塑料材料的冷却收缩,将部分冷却的与冷却程度较大的尖角间相对较弱的表面向内拉。
这样在注塑件表面上产生了凹痕。
凹痕的存在说明此处的模塑收缩率高于其周边部位的收缩。
如果模塑件在一处的收缩高于另一处,那么模塑件产生翘曲的原因。
模内残余应力会降低模塑件的冲击强度和耐温性能。
有些情况下,调整工艺条件可以避免凹痕的产生。
例如,在模塑件的保压过程中,向模腔额外注入塑料材料,以补偿模塑收缩。
大多数情况下,浇口比制件其它部分薄得多,在模塑件仍然很热而且持续收缩时,小的浇口已经固化,固化后,保压对型腔内的模塑件就不起作用。
注塑件缺陷的特征,通常与表面痕有关,而且是塑料从模具表面收缩脱离形成的。
可能出现问题的原因(1).模腔内塑料不足。
(2).熔融温度不是太高就是太低。
(3).流道不合理、浇口截面过小。
(4).模温是否与塑料特性相适应。
(5).冷却阶段时接触塑料的面过热。
(6).冷却效果不好,产品脱模后继续收缩。
(7).产品结构不合理(加强进古过高,过厚,明显厚薄不一)补救方法(1).增加注塑量。
(2).调整射料缸温度。
(3).降低模具表面温度。
(4).设法让产品有足够的冷却。
(5).在允许的情况下改善产品结构。
(6).调整螺杆速度以获得正确的螺杆表面速度。
(7).根据所用塑料的特性及产品结构适当控制模温。
注塑收缩的概念是什么
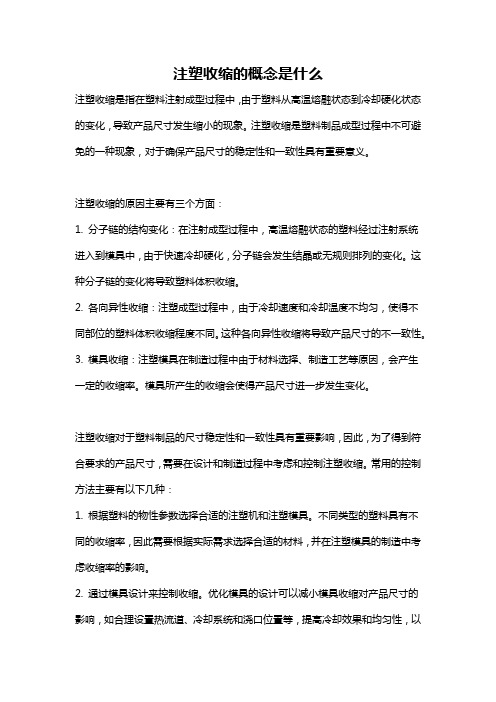
注塑收缩的概念是什么注塑收缩是指在塑料注射成型过程中,由于塑料从高温熔融状态到冷却硬化状态的变化,导致产品尺寸发生缩小的现象。
注塑收缩是塑料制品成型过程中不可避免的一种现象,对于确保产品尺寸的稳定性和一致性具有重要意义。
注塑收缩的原因主要有三个方面:1. 分子链的结构变化:在注射成型过程中,高温熔融状态的塑料经过注射系统进入到模具中,由于快速冷却硬化,分子链会发生结晶或无规则排列的变化。
这种分子链的变化将导致塑料体积收缩。
2. 各向异性收缩:注塑成型过程中,由于冷却速度和冷却温度不均匀,使得不同部位的塑料体积收缩程度不同。
这种各向异性收缩将导致产品尺寸的不一致性。
3. 模具收缩:注塑模具在制造过程中由于材料选择、制造工艺等原因,会产生一定的收缩率。
模具所产生的收缩会使得产品尺寸进一步发生变化。
注塑收缩对于塑料制品的尺寸稳定性和一致性具有重要影响,因此,为了得到符合要求的产品尺寸,需要在设计和制造过程中考虑和控制注塑收缩。
常用的控制方法主要有以下几种:1. 根据塑料的物性参数选择合适的注塑机和注塑模具。
不同类型的塑料具有不同的收缩率,因此需要根据实际需求选择合适的材料,并在注塑模具的制造中考虑收缩率的影响。
2. 通过模具设计来控制收缩。
优化模具的设计可以减小模具收缩对产品尺寸的影响,如合理设置热流道、冷却系统和浇口位置等,提高冷却效果和均匀性,以降低各向异性收缩带来的尺寸变化。
3. 调整注塑加工参数。
注塑加工参数的不同调整会对产品尺寸产生一定的影响,如调整注塑温度、压力、速度等参数,以控制塑料的流动性和冷却效果,从而控制收缩。
4. 进行后处理过程。
在注塑成型后,可以采取一些后处理措施,如热处理、冷却处理等,来改善产品的收缩性。
总之,注塑收缩是塑料制品生产过程中的一种现象,其尺寸变化对产品的表面质量、机械性能和尺寸稳定性具有重要影响。
通过合理设计注塑模具、控制加工参数以及进行后处理等措施,可以有效控制注塑收缩,从而获得符合要求的塑料制品。
塑件收缩率测量方法及其影响因素分析

塑件收缩率测量方法及其影响因素分析周必达;姜少飞;李吉泉【摘要】Aiming at the problem that uncertainty of shrinkage rate value of material, the measurement method of shrinkage rate and its influ-ence factors were studied, the calculation method of shrinkage rate was summarized. A method to calculate the shrinkage rate was proposed, which was based on shrinkage of the plastic parts measured by the thermal expansion instrument. The influence of the molding process and heat treatment on the shrinkage rate was discussed, and the relationship between the crystallinity and shrinkage was analyzed. The parts were molded by different molding process from isotactic polypropylene. The influences of molding process and heat treatment on shrinkage were discussed, the shrinkage was measured and calculated both before and after heat treatment. DSC was introduced to measure the crystallinity to analyze the effect of crystallinity on shrinkage rate. The results indicate that the measurement and calculation method of shrinkage rate is correct and validated by comparing with the shrinkage rate from molding experiment. The rapid heat cycle molding and heat treatment increa-ses the shrinkage rate because of the increases crystallization, which should not be ignored in the design of injection mold.%针对材料收缩率值的不确定性问题,对收缩率的测量方法及其影响因素进行了研究,对收缩率的计算方法进行了归纳,提出了基于热膨胀仪测量塑件收缩量来计算收缩率的方法,探讨了注塑成型工艺及热处理对收缩率的影响,分析了结晶度与收缩率之间的关系.选用等规聚丙烯为材料,采用不同成型工艺制备塑件,利用热膨胀仪分别测量热处理前后的塑件收缩量,分析了成型工艺与热处理对收缩率的影响.基于DSC测量塑件总体结晶度,分析了结晶度对塑件收缩的影响.研究结果表明,与工艺实验获得的收缩率进行对比和分析,可知采用热膨胀仪测量塑件收缩量来计算收缩率的方法是准确的,是一种简便易行的方法;快速变模温和热处理增大了塑件的结晶度,收缩量和收缩率随之变大,在模具设计过程中不可忽略.【期刊名称】《机电工程》【年(卷),期】2017(034)007【总页数】4页(P736-739)【关键词】收缩率;工艺实验;结晶度;快速变模温;热处理【作者】周必达;姜少飞;李吉泉【作者单位】浙江工业大学特种装备制造与先进加工技术教育部重点实验室,浙江杭州310014;浙江工业大学特种装备制造与先进加工技术教育部重点实验室,浙江杭州310014;浙江工业大学特种装备制造与先进加工技术教育部重点实验室,浙江杭州310014【正文语种】中文【中图分类】TH14塑件在航天、汽车、家电和日常生活领域的应用越来越广泛,尺寸精度要求也越来越高。
注塑件试模常见问题与解决方法

注塑件试模常见问题与解决方法http:2009年02月14日13:52生意社02月14日讯收縮痕一、注塑件缺陷的特征通常与表面痕有关,而且是塑料从模具表面收缩脱离形成的。
二、可能出现问题的原因(1).熔融温度不是太高就是太低。
(2).模腔内塑料不足。
(3).冷却阶段时接触塑料的面过热。
(4).流道不合理、浇口截面过小。
(5).模温是否与塑料特性相适应。
(6).产品结构不合理(加强进古过高,过厚,明显厚薄不一).(7).冷却效果不好,产品脱模后继续收缩。
三、补救方法(1).调整射料缸温度。
(2).调整螺杆速度以获得正确的螺杆表面速度。
(3).增加注塑量。
(4).保证使用正确的垫料;增加螺杆向前时间;增加注塑压力;增加注塑速度。
(5).检查止流阀是否安装正确,因为非正常运行会引致压力流失。
(6).降低模具表面温度。
(7).矫正流道避免压力损失过大;根据实际需要,适当扩大截面尺寸。
(8).根据所用塑料的特性及产品结构适当控制模温。
(9).在允许的情况下改善产品结构。
(10).设法让产品有足够的冷却。
包封一、注塑件缺陷的特征可以容易地在透明注塑件的“空气阱”内见到但也可出现在不透明的塑料中,这与厚度有关,而且常因塑料收缩离开注塑件中心而引起。
二、可能出现问题的原因(1).模具未充分填充。
(2).止流阀的不正常运行。
(3).塑料未彻底干燥。
(4).预塑或注射速度过快。
(5).某些特殊材料应用特殊的设备生产。
三、补救方法(1).增加射料量。
(2).增加注塑压力。
(3).增加螺杆向前时间。
(4).降低熔融温度。
(5).降低或增加注塑速度。
(例如对非结晶体类的塑料要增加45%速度)。
(6).检查止逆阀是否裂开或无法运作。
(7).应根据塑料的特性改善干燥条件,让塑料彻底干燥。
(8).适当降低螺杆转速和增大背压,或降低注射速度。
制品成型尺寸精度低注塑件缺陷的特征一﹐注塑过程中重量尺寸的变化超过了模具、注塑机、塑料组合的生产能力。
塑料模具收缩率表

塑料模具收缩率表一、引言在塑料模具的制造过程中,收缩率是一个非常重要的参数。
塑料模具收缩率表是用来指导模具制造过程中的尺寸设计和修正的参考依据。
本文将围绕塑料模具收缩率表展开讨论,介绍塑料模具收缩率的概念、影响因素以及如何使用收缩率表进行尺寸修正。
二、塑料模具收缩率的概念塑料模具收缩率是指塑料制品在冷却过程中由于温度变化而引起的尺寸变化率。
塑料模具收缩率是一个相对值,通常以百分比表示。
例如,如果一个塑料制品在冷却过程中尺寸缩小了2%,那么它的收缩率就是2%。
三、影响塑料模具收缩率的因素1. 塑料材料的种类:不同种类的塑料具有不同的收缩率。
一般来说,热塑性塑料的收缩率比热固性塑料高。
2. 温度:温度是影响塑料模具收缩率的重要因素。
一般来说,温度越高,塑料的收缩率越高。
3. 压力:在注塑过程中,注射机施加的压力也会影响塑料模具收缩率。
一般来说,施加较高的压力可以减小塑料的收缩率。
4. 模具结构:模具的结构也会对塑料模具收缩率产生影响。
例如,模具中的冷却系统设计不合理,会导致塑料冷却不均匀,进而影响塑料模具的收缩率。
四、塑料模具收缩率表的使用塑料模具收缩率表是模具制造过程中的重要参考工具。
使用收缩率表可以帮助工程师在设计模具尺寸时考虑到塑料的收缩,从而减少制品在冷却过程中的尺寸误差。
使用塑料模具收缩率表的步骤如下:1. 确定所使用的塑料材料的种类。
2. 根据塑料材料种类,找到对应的塑料模具收缩率表。
3. 根据模具尺寸和设计要求,在收缩率表中找到相应的收缩率数值。
4. 根据收缩率数值,计算修正尺寸。
修正尺寸= 原始尺寸× (1 + 收缩率)。
5. 在模具设计过程中,将修正尺寸应用于模具尺寸设计。
五、总结塑料模具收缩率是塑料模具制造中不可忽视的重要参数。
通过合理使用塑料模具收缩率表,可以减小塑料制品在冷却过程中的尺寸误差,提高模具制品的质量。
在实际应用中,工程师们应注意选择合适的塑料材料和合理的工艺参数,以保证模具制品具有准确的尺寸和优良的性能。
塑料收缩率及其影响因素

塑料收缩率及其影响因素塑料收缩率及其影响因素热塑性塑料的特性是在加热后膨胀,冷却后收缩.当然加压后体积也将缩小.在注塑成型过程中,首先将熔融塑料注射入模具型腔内,充填结束后熔料冷却固化,从模具中取出塑件时即出现收缩,此收缩称为成型收缩.塑件从模具取出到稳定这段时间内,尺寸仍会出现微小的变化,一种变化是继续收缩.另一种变化是某些吸湿性塑料因吸湿而出现膨胀,但是其中起主要作用的是成型收缩。
塑件形状对于成型件壁厚来说,一般由于厚壁的冷却时间较长,因而收缩率也较大.对于一般塑件来说,当沿熔料方向尺寸与垂直于熔料流动方向尺寸的差异较大时,则收缩率差异也较大.从熔料流动距离来看,远离浇口部分的压力损失大,因而该处的收缩率也比靠近浇口部位大.因加强筋、孔、凸台和雕刻等形状具有收缩抗力,因而这些部位的收缩率较小。
模具结构浇口形式对收缩率也有影响。
用小浇口时,因保压结束之前浇口即固化而使塑件的收缩率增大。
注塑模具中的冷却回路结构也是模具设计中的一个关键。
冷却回路设计不当,则因塑件各处温度不均衡而产生收缩差,其结果是使塑件尺寸差或变形。
在薄壁部分,模具温度分布对收缩率的影响则更为明显。
成行条件料筒温度:料筒温度较高时,压力传递较好而使收缩力减小。
但用小浇口时,因浇口固化早而使收缩率仍较大。
对于壁厚塑件来说,即使筒温度较高,其收缩率仍较大。
补料:在成型条件中,尽量减少补料以使塑件尺寸保持稳定。
但补料不足则无法保持压力,也会使收缩率增大。
注射压力:注射压力是对收缩率影响较大的因素,特别是充填结束后的保压压力。
在一般情况下,压力较大时候因材料的密度大,收缩率就较小。
注射速度:注射速度对收缩率的影响较小。
但对于薄壁塑件或浇口非常小,以及使用强化材料时,注射速度加快则收缩率小。
模具温度:通常模具温度较高时收缩率也较大。
但对于薄壁塑件,模具温度高则熔料的流动抗阻小,进而收缩率反而较小。
成型周期:成型周期与收缩率无直接关系。
但需注意,当加快成型周期时,模具温度、熔料温度等必然也发生变化,从而影响收缩率的变化。
塑胶件缩水的原因及改善的方法

塑胶件缩水的原因及改善的方法
1.材料因子:塑胶材料的收缩率、热变形温度和熔融温度会影响缩水
的程度。
2.注塑工艺因子:如注射温度、注射压力、注射速度和模具温度等参
数的设置不合理,会导致过热或过冷,进而引起缩水。
3.模具设计因子:模具的工艺设计不合理,如射嘴冷却不均匀、壁厚
不均匀、出线方向不合理等,都会导致缩水。
为了改善塑胶件的缩水问题,可以采取以下方法:
1.选择合适的塑胶材料:选用热稳定性好、收缩率低的材料,可以降
低缩水的程度。
2.调整注射工艺参数:合理设置注射温度、注射压力和注射速度等参数,减小温度差异和流动速度差异,有利于减少缩水现象。
3.优化模具设计:合理设计模具的型腔结构、冷却系统和出线方向等,使塑胶材料的冷却均匀,减少缩水的可能性。
4.储存与处理:将塑胶件储存在适宜的温度和湿度条件下,避免长时
间接触阳光和高温环境,以防塑胶件因受热再次发生收缩。
5.合理设计产品结构:考虑产品结构设计,避免大面积的平均壁厚的
设计,以减少缩水。
另外,还可以通过使用模流分析软件来模拟注塑过程,验证和优化塑
胶件的工艺参数和模具设计,以实现更好的缩水控制。
此外,加强对塑胶
件的质量检验和控制,以及选择有经验的塑胶制品加工厂商,也能有效降
低塑胶件缩水的发生。
总之,正确选择材料、合理调整注射工艺参数、优化模具设计和合理产品结构设计等措施是改善塑胶件缩水问题的关键。
同时,强化质量控制和使用模流分析软件等也是必要的手段,以提高塑胶件的加工质量和产品性能。
塑料模具影响设计效率的因素及对策分析

塑料模具影响设计效率的因素及对策分析当今社会人们对塑料模具的需求量与日俱增,塑料模具的设计人员应进行不断地创新,提高塑料模具质量,以满足人们日益增长的生活需要,最终提高塑料模具的质量。
塑料模具设计人员需要考虑设计标准、设计尺寸和设计成本这三个方面的问题。
只有解决了这三个方面的问题,设计出来的塑料模具的性价比才能高。
所以,塑料模具的设计人员要创新设计理念和改革设计方法,探究模具设计中的常见问题,并采取一定的方法提高塑料模具设计水平,以避免有关问题的发生,最终节约设计成本。
一、塑料模具设计中的常见问题在多种多样的工业制品中提出的要求很多,比如对塑料模具尺寸和形状的把握,所以为提升工业制品制作效率,要合理设计塑料模具。
现如今,塑料模具设计者在设计模具时主要存在三个方面的问题,1.塑料模具的收缩率不统一;2.公差不统一;3.冷却程度不统一,因而使塑料模具的设计效率受到严重的影响。
(一)收缩率不统一塑料模具的制作环境需要高温高压,因此要创设一种环境,溶解塑料,而后再注入到模腔中。
收缩的状况是在液态塑料转化为固体的过程中,根据塑料本身特点,模腔实际上会比塑料模具大一些。
因此,在设计者设计塑料模具时,必须考虑到塑料的收缩率,但是,现如今的某些设计者没有考虑到不同类型塑料的收缩率是不同的,不能程式化计算收缩率。
收缩率一旦算错,那么制成的模具形状也会受到一定的影响。
(二)公差标注不统一不同比例的塑料模具会制成不同的制品,公差标注高意味着塑料模具加工工艺相对复杂,公差标注低意味着塑料模具的精度不够高。
所以,设计者设计塑料模具考虑模具的公差问题应该成为重点。
现有的状况是,设计模具时仍然有设计人员根据过往的经验来设置公差标准,导致的情况是模具尺寸出现偏差,而且形状出现改变,这在很大程度上影响到了塑料模具设计的质量和其参考价值。
(三)热膨胀系数不统一不同的塑料材料的热膨胀系数各不相同,塑料冷却之后的形状和大小直接受到热膨胀系数的影响。
新料 回料 注塑 收缩率

新料回料注塑收缩率新料、回料、注塑和收缩率是在塑料加工领域中常用的术语。
本文将以从简到繁、由浅入深的方式来探讨这些主题,帮助读者更加全面、深入地理解它们的含义、作用以及相互关系。
1. 新料新料是指生产加工过程中所使用的经过配方设计、制造的全新塑料材料。
1.1 定义和特点新料通常是通过合成原料、添加剂和填充剂等组成,经过一系列加工工艺形成的。
不同的塑料材料具有各自的特性和用途,比如高分子量聚合物具有良好的机械性能和耐化学腐蚀性能,聚丙烯则具有优异的耐低温性能等。
1.2 应用领域新料在各个领域有广泛的应用。
在汽车制造业中,新料被广泛应用于汽车外观件、内饰件以及功能部件的制造中。
在电子产品制造业中,新料则常用于手机壳、电视外壳等塑料配件的制造中。
2. 回料回料是指在塑料加工过程中未经使用的塑料废料或废品再次回收利用,并经过一定的处理后重新投入生产。
2.1 回收处理过程回料的处理过程主要包括收集、分类、清洗、破碎、加工和再制粒等环节。
通过这些处理步骤,废弃的塑料材料可以得到有效利用,节约了资源和能源。
2.2 应用回料通常与新料混合使用,以降低生产成本。
回料的使用可以减少对原料的需求,降低废弃物的产生,并对环境保护起到积极的作用。
3. 注塑注塑是一种常用的塑料加工工艺,通过将塑料料粒加热熔化后注入模具中,然后在模具中冷却凝固而形成所需的产品。
3.1 原理和过程注塑的基本原理是通过注塑机将塑料料粒加热至熔融状态,然后将熔融的塑料通过螺杆压入模具中,再经过一段时间的冷却,最后从模具中取出形成塑料制品。
3.2 应用和优势注塑工艺广泛应用于塑料制品的生产中,如管道、容器、电子产品外壳等。
相较于其他加工工艺,注塑具有生产效率高、产品质量稳定性好、成本较低等优势。
4. 收缩率收缩率是指在塑料注塑过程中,塑料材料在冷却凝固过程中由于收缩而引起的尺寸变化。
4.1 原因和影响因素塑料材料在冷却凝固过程中由于分子间力的作用而收缩,从而导致成型件的尺寸减小。
常见注塑件缺陷及解决的方法
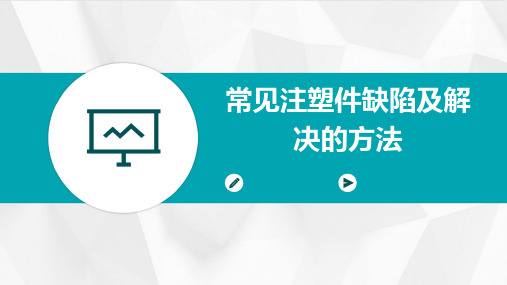
充填不足
01
总结词
充填不足是指注塑件在成型过程中未能完全填满 模具型腔,导致部分区域出现缺料或凹陷。
02
详细描述
充填不足通常是由于注射速度慢、注射压力不足、 模具温度过高或塑料流动性差等原因引起的。
缩痕
总结词
缩痕是指注塑件表面出现凹陷或收缩痕迹,影响 外观和尺寸精度。
详细描述
缩痕通常是由于塑料冷却过程中收缩率不均、模 具温度不均匀或注射压力不足等原因引起的。
常见注塑件缺陷及解 决的方法
目录
• 常见注塑件缺陷 • 注塑件缺陷原因分析 • 解决注塑件缺陷的方法 • 案例分析
01
常见注塑件缺陷
翘曲与扭曲
总结词
翘曲与扭曲是指注塑件形状发生扭曲或弯曲,不符合设 计要求。
详细描述
翘曲与扭曲通常是由于模具设计不合理、塑料收缩率差 异、注射温度和压力不适当等原因引起的。
环境条件的控制Байду номын сангаас
总结词
保持稳定的环境条件对注塑件的质量至关重 要,包括温度、湿度和清洁度等。
详细描述
确保注塑车间温度、湿度稳定,保持环境清 洁、无尘。定期对设备和环境进行清理和消 毒,防止污染和细菌滋生。同时,要关注天 气变化和季节性温差对注塑件质量的影响,
采取相应的措施进行调节。
04
案例分析
案例一:翘曲与扭曲缺陷的解决
材料选择与控制
总结词
选择合适的材料,控制材料质量是解决注塑件缺陷的重要步骤。
详细描述
根据产品使用要求和工艺特性,选择具有良好流动性和成型性的材料。同时, 要确保材料干燥、清洁,无杂质和污染。定期对材料进行质量检查,确保其性 能稳定。
模具优化与维护
塑料外壳缩水、收缩、变形的现象和原因
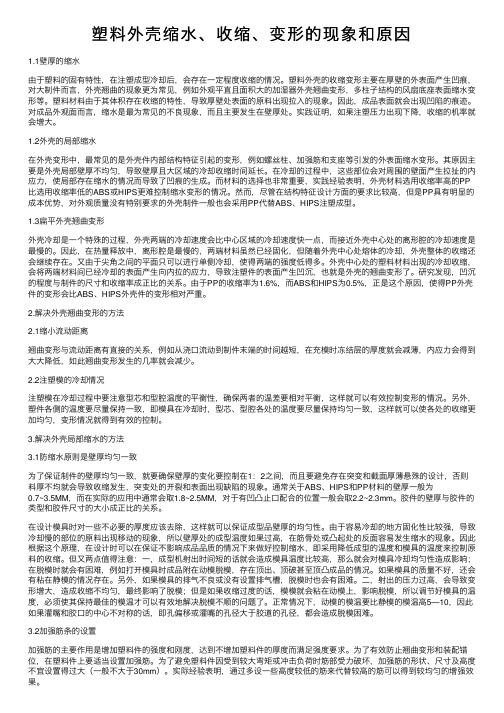
塑料外壳缩⽔、收缩、变形的现象和原因1.1壁厚的缩⽔由于塑料的固有特性,在注塑成型冷却后,会存在⼀定程度收缩的情况。
塑料外壳的收缩变形主要在厚壁的外表⾯产⽣凹痕,对⼤制件⽽⾔,外壳翘曲的现象更为常见,例如外观平直且⾯积⼤的加湿器外壳翘曲变形,多柱⼦结构的风扇底座表⾯缩⽔变形等。
塑料材料由于其体积存在收缩的特性,导致厚壁处表⾯的原料出现拉⼊的现象。
因此,成品表⾯就会出现凹陷的痕迹。
对成品外观⾯⽽⾔,缩⽔是最为常见的不良现象,⽽且主要发⽣在壁厚处。
实践证明,如果注塑压⼒出现下降,收缩的机率就会增⼤。
1.2外壳的局部缩⽔在外壳变形中,最常见的是外壳件内部结构特征引起的变形,例如螺丝柱、加强筋和⽀座等引发的外表⾯缩⽔变形。
其原因主要是外壳局部壁厚不均匀,导致壁厚且⼤区域的冷却收缩时间延长。
在冷却的过程中,这些部位会对周围的壁⾯产⽣拉扯的内应⼒,使局部存在缩⽔的情况⽽导致了凹痕的⽣成。
⽽材料的选择也⾮常重要,实践经验表明,外壳材料选⽤收缩率⾼的PP ⽐选⽤收缩率低的ABS或HIPS更难控制缩⽔变形的情况。
然⽽,尽管在结构特征设计⽅⾯的要求⽐较⾼,但是PP具有明显的成本优势,对外观质量没有特别要求的外壳制件⼀般也会采⽤PP代替ABS、HIPS注塑成型。
1.3扁平外壳翘曲变形外壳冷却是⼀个特殊的过程,外壳两端的冷却速度会⽐中⼼区域的冷却速度快⼀点,⽽接近外壳中⼼处的离形腔的冷却速度是最慢的。
因此,在热量释放中,离形腔是最慢的,两端材料虽然已经固化,但随着外壳中⼼处熔体的冷却,外壳整体的收缩还会继续存在。
⼜由于尖⾓之间的平⾯只可以进⾏单侧冷却,使得两端的强度低得多。
外壳中⼼处的塑料材料出现的冷却收缩,会将两端材料间已经冷却的表⾯产⽣向内拉的应⼒,导致注塑件的表⾯产⽣凹沉,也就是外壳的翘曲变形了。
研究发现,凹沉的程度与制件的尺⼨和收缩率成正⽐的关系。
由于PP的收缩率为1.6%,⽽ABS和HIPS为0.5%,正是这个原因,使得PP外壳件的变形会⽐ABS、HIPS外壳件的变形相对严重。
常见注塑缺陷及解决方案
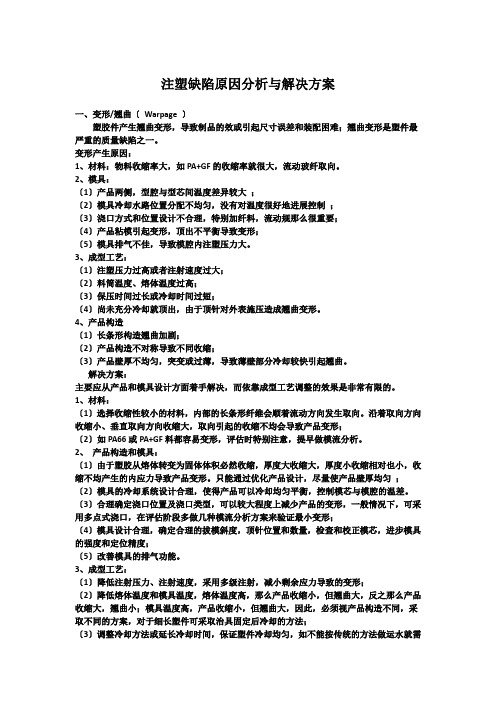
注塑缺陷原因分析与解决方案一、变形/翘曲〔Warpage 〕塑胶件产生翘曲变形,导致制品的效或引起尺寸误差和装配困难;翘曲变形是塑件最严重的质量缺陷之一。
变形产生原因:1、材料:物料收缩率大,如PA+GF的收缩率就很大,流动玻纤取向。
2、模具:〔1〕产品两侧,型腔与型芯间温度差异较大;〔2〕模具冷却水路位置分配不均匀,没有对温度很好地进展控制;〔3〕浇口方式和位置设计不合理,特别加纤料,流动规那么很重要;〔4〕产品粘模引起变形,顶出不平衡导致变形;〔5〕模具排气不佳,导致模腔内注塑压力大。
3、成型工艺:〔1〕注塑压力过高或者注射速度过大;〔2〕料筒温度、熔体温度过高;〔3〕保压时间过长或冷却时间过短;〔4〕尚未充分冷却就顶出,由于顶针对外表施压造成翘曲变形。
4、产品构造〔1〕长条形构造翘曲加剧;〔2〕产品构造不对称导致不同收缩;〔3〕产品壁厚不均匀,突变或过薄,导致薄壁部分冷却较快引起翘曲。
解决方案:主要应从产品和模具设计方面着手解决,而依靠成型工艺调整的效果是非常有限的。
1、材料:〔1〕选择收缩性较小的材料,内部的长条形纤维会顺着流动方向发生取向。
沿着取向方向收缩小、垂直取向方向收缩大,取向引起的收缩不均会导致产品变形;〔2〕如PA66或PA+GF料都容易变形,评估时特别注意,提早做模流分析。
2、产品构造和模具:〔1〕由于塑胶从熔体转变为固体体积必然收缩,厚度大收缩大,厚度小收缩相对也小,收缩不均产生的内应力导致产品变形。
只能通过优化产品设计,尽量使产品壁厚均匀;〔2〕模具的冷却系统设计合理,使得产品可以冷却均匀平衡,控制模芯与模腔的温差。
〔3〕合理确定浇口位置及浇口类型,可以较大程度上减少产品的变形,一般情况下,可采用多点式浇口,在评估阶段多做几种模流分析方案来验证最小变形;〔4〕模具设计合理,确定合理的拔模斜度,顶针位置和数量,检查和校正模芯,进步模具的强度和定位精度;〔5〕改善模具的排气功能。
注塑常见问题及解决方法.

•1.埋入物需附有防 止转动和被拔出的 设计 •2.先行将埋入物预 热 •3.清除埋入物表面 油污 •4.降低射出压力 •5.提高成型温度和 模温
•1.注意接合的精度 •2.避免埋入物周围 的应力集中在一起
•1.使用热膨胀较小 的材料
1
Байду номын сангаас
2
3
天津普利派克包装制品有限公司
天津普利派克包装制品有限公司
•1.排气要好 •2.尽量避免直角方 向的补强和肉厚产 生急剧变化 •3.修正射出嘴和模 型浇口结合处是否 紧密
•1.充分干燥 •2.使用低挥发性材 料 •3.加入热安定剂 •4.注意添加剂本身 是否有吸湿性
1
2
3
天津普利派克包装制品有限公司
五.造成银纹、气泡、针孔的原因
1.水分含量过多
原因
2.挥发气体含量过多
•1.调整成型计量 •2.调高成型温度 •3.增加射出压力、 射出时间 •4.检查塑料进入成 型机是否阻塞 •5.射出嘴是否有杂 物混入或阻塞,必 要时增加射出最孔 径
•1.浇道、浇口加大 •2.做好排气口 •3.避免极端薄肉的 部分 •4.增加肉厚,补强 支柱 •5.冷却集料出加大 •6.检查浇口是否平 衡
天津普利派克包装制品有限公司
注塑常见问题及解决方法
姓名:杨蓬 时间:2013-12-12
天津普利派克包装制品有限公司
充填不足、短射、不饱模 毛口溢料、飞边、利刃 缩水、空洞、收缩下陷 流痕(Flow Mark)、流纹 银纹、气泡、针孔
注塑 常见问题有:
喷流 结合线 焦斑、黑纹、变色 变形、翘曲、弯曲 破裂、裂痕、白化
1.成型品设计顶出幅度 不足
2.模型变形
原因
注塑成型不良及对策

第一章注塑成型不良及对策一.缩痕1.概要缩痕是指在制品的厚壁处、加强筋、凸台等部分的外表面,由于冷却不充分而无法补偿由于热收缩引起的缺料现象,从而在制品表面形成凹陷痕迹。
缩痕是制品表面所发生的不良现象中最多的。
2. 缩痕发生的原因及对策●固化太慢。
●有效保压时间太短。
●由于模具内的流动阻力较大,无法充分传达保压压力。
具体原因如下:(1)壁厚不均匀制品的壁厚不均匀,厚壁处的冷却速度比薄壁处的冷却速度慢,因此发生缩痕。
重新设计冷却方式,对厚壁处进行集中冷却, 由于凸台尺寸一般较厚,应设置缩痕去除针。
此外,设计模具时应尽可能将壁厚设计均匀,壁厚在3mm以下较为理想。
(2)模强压力不足为使制品受到足够的注塑压力,延长保压时间,同时增加保压压力。
可考虑修改浇口(变大或变短)来改善注塑压力的传递效果,在可能发生缩痕的部分设置浇口或改变浇口的位置。
另外,离浇口较远的部分由于树脂流动阻力较大,会发生很严重的收缩,可通过改变壁厚来改善保压传达效果。
成型薄壁制品时,在注塑压力还未被有效的传递之前制品就已经冷却硬化,因此就会出现缩痕。
此外,由于模具内表面不光滑有毛刺存在,其锁模压力低于注塑压力,导致使压力不足而出现缩痕。
对离浇口较远的收缩,可切断模具冷却。
这是因为模具温度升高时,熔料就不易硬图1-2加强筋周边的缩痕图1-3 壁厚不匀引起的缩痕化,注塑压力(尤其是保压压力)的传达就会变的容易。
(3)计量设定不当在设定成型条件时,螺杆前端如果不预留适量的熔融树脂用来缓冲的话,在保压过程中树脂就无法进行补料,进而出现供料不足的收缩痕。
这种现象主要以收缩点的形式存在,时常在浇口周围及产品表面发生。
因此很容易与其他原因造成的缩痕进行区别。
(4)收缩量过大成型塑料本身的收缩率越大缩痕发生越严重,特别是结晶性塑料。
如发生大面积缩痕时,一般可通过降低树脂温度、提高注塑压力等方法来改善。
假如问题仍得不到解决,在不影响制品用途的范围内可尝试更换塑料(用非结晶性聚合物代替)或混入增强性玻璃纤维、石棉等无机填充物,在一定程度上可减小缩痕,起到覆盖作用。
第28问:注塑成型过程中的收缩率?
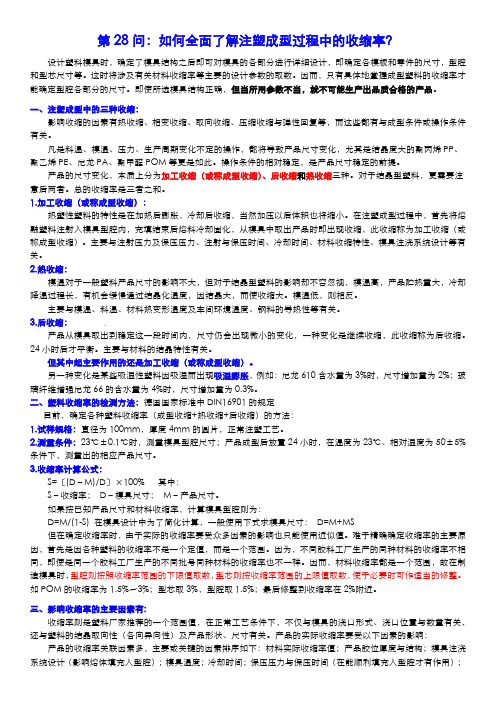
第28问:如何全面了解注塑成型过程中的收缩率?设计塑料模具时,确定了模具结构之后即可对模具的各部分进行详细设计,即确定各模板和零件的尺寸,型腔和型芯尺寸等。
这时将涉及有关材料收缩率等主要的设计参数的取数。
因而,只有具体地掌握成型塑料的收缩率才能确定型腔各部分的尺寸。
即使所选模具结构正确,但当所用参数不当,就不可能生产出品质合格的产品。
一、注塑成型中的三种收缩:影响收缩的因素有热收缩、相变收缩、取向收缩、压缩收缩与弹性回复等,而这些都有与成型条件或操作条件有关。
凡是料温、模温、压力、生产周期变化不定的操作,都将导致产品尺寸变化,尤其是结晶度大的聚丙烯PP、聚乙烯PE、尼龙PA、聚甲醛POM等更是如此。
操作条件的相对稳定,是产品尺寸稳定的前提。
产品的尺寸变化,本质上分为加工收缩(或称成型收缩)、后收缩和热收缩三种。
对于结晶型塑料,更需要注意后两者。
总的收缩率是三者之和。
1.加工收缩(或称成型收缩):热塑性塑料的特性是在加热后膨胀,冷却后收缩,当然加压以后体积也将缩小。
在注塑成型过程中,首先将熔融塑料注射入模具型腔内,充填结束后熔料冷却固化,从模具中取出产品时即出现收缩,此收缩称为加工收缩(或称成型收缩)。
主要与注射压力及保压压力、注射与保压时间、冷却时间、材料收缩特性、模具注浇系统设计等有关。
2.热收缩:模温对于一般塑料产品尺寸的影响不大,但对于结晶型塑料的影响却不容忽视,模温高,产品贮热量大,冷却降温过程长,有机会缓慢通过结晶化温度,因结晶大,而使收缩大。
模温低,则相反。
主要与模温、料温、材料热变形温度及车间环境温度、钢料的导热性等有关。
3.后收缩:产品从模具取出到稳定这一段时间内,尺寸仍会出现微小的变化,一种变化是继续收缩,此收缩称为后收缩。
24小时后才平衡。
主要与材料的结晶特性有关。
但其中起主要作用的还是加工收缩(或称成型收缩)。
另一种变化是某些吸湿性塑料因吸湿而出现吸湿膨胀,例如:尼龙610含水量为3%时,尺寸增加量为2%;玻璃纤维增强尼龙66的含水量为4%时,尺寸增加量为0.3%。
ABS注塑成型收缩率的几点关系

来源于:注塑塑料网/ABS注塑成型收缩率的几点关系塑料收缩率直接关系到制品的形状和尺寸精度。
塑料制品特性、模具设计、工艺条件控制等影响成型收缩率和后收缩的各因素,对注塑制品及其稳定性影响极大[门。
目前模具尺寸的设计通常运用公差带或平均收缩率的方法计算,模具在试模后,根据试制出的制品尺寸来修正模具,然而一些高硬度。
低粗糙度模具的表面尺寸修正起来相当困难,且费工费时,有时甚至无法修正,造成巨大的损失。
所以,要得到所需尺寸的精密注塑件,同时又能尽量减少对模具的修正,就需要充分了解成型收缩率随工艺条件的变化规律,预先精确测定成型收缩率。
(丙烯膨丁二惭苯乙烯)三元共聚物(ABS)塑料综合了丙烯睛的耐化学药品性、耐油性、刚度和硬度,丁二烯的韧性和耐寒性及苯乙烯的电性能,被广泛应用于汽车、电器仪表和机械工业中,是目前通用工程塑料中应用最广泛的品种之一[z]。
国外对塑料成型收缩率的研究开始得较早,且取得了比较丰富的研究成果「3-7],国内专门从事塑料成型收缩率研究的并不多[8-11]。
因此,笔者采用xsrn n oss-so标准测定了^ss塑料在不同工艺条件下注射模塑的成型收缩率,得出了ABS塑料的成型收缩率随工艺条件的变化规律,为制订合理的工艺条件进行正确的工艺控制和模具设计从而生产出合格尺寸的制品提供了重要依据。
一、实验部分(一)主要原材料ABS:IH-100,上海高桥石化公司。
(二)主要设备干燥料斗:FNH-A型,日本日永化工株式会社;模温调节机:NT-55型,日本日永化工株式会社;注塑机:PS40SESASE型,日本日精树脂l业株式会社;模具:按ASTM D 955-89制造,长条模、圆片模,自制。
(三)测试方法试样分别为长条门27.045 mm x 10•000 mm X3.200 mm)和圆片(o101.975 mm)。
测试时运用带百分表的靠模,精度为0.of mm,测试长条形试样在平行于流动方向及圆片形试样在平行和垂直于流动方向上的尺寸变化。
塑胶件缩水的原因及改善的方法

塑胶件缩水的原因及改善的方法塑胶件缩水是塑料加工过程中常见的一个问题,指的是注塑成型后的塑胶件尺寸变小的现象。
在注塑成型过程中,塑胶件材料会遇到高温、高压和急速冷却等条件,导致塑胶件内部的温度变化、流动速度差异等因素引起尺寸缩水。
本文将探讨塑胶件缩水的原因及改善的方法。
一、塑胶件缩水的原因1.材料因素:塑胶材料的热收缩率是造成缩水的主要原因之一、不同类型的塑胶材料具有不同的热收缩率,部分塑胶材料热收缩率较高,容易引起较大的缩水问题。
2.压力因素:注塑过程中的注塑压力对塑胶件缩水也有影响。
如果注塑压力设置过高,会使塑胶材料在注塑过程中过度流动,造成塑胶件内部的紧凑性降低,从而导致尺寸缩水。
3.温度因素:注塑过程中的温度控制对塑胶件缩水也有很大的影响。
如果注塑过程中的温度设置过高或过低,都会导致塑胶件的收缩率增大,从而引起尺寸缩水。
4.冷却因素:注塑过程中的冷却速度也是塑胶件缩水的重要原因。
如果注塑件在冷却过程中冷却速度过快,会使得塑胶件内部的温度梯度较大,从而引起尺寸缩水。
5.模具结构:模具的开口结构以及模具背压设计等因素也会对塑胶件的缩水问题产生一定的影响。
二、改善塑胶件缩水的方法1.选择低收缩率的塑胶材料:在项目设计和材料选择过程中,可以优先选择具有低热收缩率的塑胶材料,减少后续成型过程中的尺寸变化。
2.优化注塑工艺参数:合理调整注塑过程中的温度、压力和冷却速度等工艺参数,以减少塑胶件的热收缩率。
同时,优化保压时间和保压力度的设置,以提高塑胶件内部的紧凑性,减少缩水问题。
3.加强模具设计和制造:合理优化模具结构,并采用合适的模具开口方式,可以减少塑胶件的内部应力,降低缩水问题的发生。
此外,选择高品质的模具材料和制造工艺,确保模内温度均匀分布以及良好的冷却效果,有助于减少塑胶件的缩水现象。
4.控制注塑过程中的冷却速度:通过合理的冷却系统设计和冷却介质的选择,以及控制冷却时间和冷却速度的参数,可以减少注塑件过快冷却引起的尺寸缩水。
- 1、下载文档前请自行甄别文档内容的完整性,平台不提供额外的编辑、内容补充、找答案等附加服务。
- 2、"仅部分预览"的文档,不可在线预览部分如存在完整性等问题,可反馈申请退款(可完整预览的文档不适用该条件!)。
- 3、如文档侵犯您的权益,请联系客服反馈,我们会尽快为您处理(人工客服工作时间:9:00-18:30)。
注塑模具收缩率的原因及解决方法
引言
塑料材料模塑过程中膨胀和收缩量的大小与所加工塑料的热膨胀系数有关,模塑过程的热膨胀系数称为“模塑收缩”。
随着模塑件冷却收缩,模塑件与模腔冷却表面失去紧密接触这时冷却效率下降,模塑件继续冷却后,模塑件不断收缩,收缩量取决于各种因素的综合作用模塑件上的尖角冷却最快,比其它部件更早硬化,接近模塑件中心处的厚的部分离型腔冷却面最远,成为模塑件上最后释放热量的部分,边角处的材料固化后,随着接近制件中心处的熔体冷却,模塑件仍会继续收缩,尖角之间的平面只能得到单侧冷却,其强度没有尖角处材料的强度高。
制件中心处塑料材料的冷却收缩,将部分冷却的与冷却程度较大的尖角间相对较弱的表面向内拉。
这样在注塑件表面上产生了凹痕。
凹痕的存在说明此处的模塑收缩率高于其周边部位的收缩。
如果模塑件在一处的收缩高于另一处,那么模塑件产生翘曲的原因。
模内残余应力会降低模塑件的冲击强度和耐温性能。
有些情况下,调整工艺条件可以避免凹痕的产生。
例如,在模塑件的保压过程中,向模腔额外注入塑料材料,以补偿模塑收缩。
大多数情况下,浇口比制件其它部分薄得多,在模塑件仍然很热而且持续收缩时,小的浇口已经固化,固化后,保压对型腔内的模塑件就不起作用。
注塑件缺陷的特征,通常与表面痕有关,而且是塑料从模具表面收缩脱离形成的。
可能出现问题的原因
(1).模腔内塑料不足。
(2).熔融温度不是太高就是太低。
(3).流道不合理、浇口截面过小。
(4).模温是否与塑料特性相适应。
(5).冷却阶段时接触塑料的面过热。
(6).冷却效果不好,产品脱模后继续收缩。
(7).产品结构不合理(加强进古过高,过厚,明显厚薄不一)
补救方法
(1).增加注塑量。
(2).调整射料缸温度。
(3).降低模具表面温度。
(4).设法让产品有足够的冷却。
(5).在允许的情况下改善产品结构。
(6).调整螺杆速度以获得正确的螺杆表面速度。
(7).根据所用塑料的特性及产品结构适当控制模温。
(8).检查止流阀是否安装正确,因为非正常运行会引致压力流失。
(9).矫正流道避免压力损失过大;根据实际需要,适当扩大截面尺寸。
(10).保证使用正确的垫料;增加螺杆向前时间;增加注塑压力;增加注塑速度。
包封
一、注塑件缺陷的特征
可以容易地在透明注塑件的“空气阱”内见到但也可出现在不透明的塑料中,这与厚度有关,而且常因塑料收缩离开注塑件中心而引起。
二、可能出现问题的原因
(1).塑料未彻底干燥。
(2).模具未充分填充。
(3).预塑或注射速度过快。
(4).止流阀的不正常运行。
(5).某些特殊材料应用特殊的设备生产。
补救方法
(1).增加射料量。
(2).降低熔融温度。
(3).增加注塑压力。
(4).增加螺杆向前时间。
(5).检查止逆阀是否裂开或无法运作。
(6).适当降低螺杆转速和增大背压,或降低注射速度。
(7).应根据塑料的特性改善干燥条件,让塑料彻底干燥。
(8).降低或增加注塑速度。
(例如对非结晶体类的塑料要增加45%速度)。
制品成型尺寸精度低
注塑件缺陷的特征
一﹐注塑过程中重量尺寸的变化超过了模具、注塑机、塑料组合的生产能力。
二、可能出现问题的原因
(1).注塑压力不稳定。
(2).螺杆复位不稳定。
(3).注塑机容量太小。
(4).输入射料缸内的塑料不均。
(5).使用了不适合模具的塑料品种。
(6).射料缸温度或波动的范围太大。
(7).注射速度(流量控制)不稳定。
(8).运作时间的变化、溶液黏度不一致。
(9).考虑模温、注射压力、速度、时间和保压等对产品的影响。
补救方法
(1).使用背压。
(2).检查运作时间的不一致性。
(3).检查有无充足的冷却水流经料斗喉以保持正确的温度。
(4).检查是否错误的进料设定。
(5).检查是否劣质或松脱的热电偶。
(6).检查是否每次运作都有稳定的熔融热料。
(7).检查回流防止阀有否泄露,若有需要就进行更换。
(8).保证螺杆在每次运作复回位置都是稳定的,即不多于0.4mm的变化。
(9).选择适合模具的塑料品种(主要从缩率及机械强度虑)。
(10).检查与温度控制器一起使用的热电偶是否属于正确类型。
(11).检查液压系统运作是否正常,油温是否过高或过低(25—60’C)。
(12).检查注塑机的注塑量和塑化能力,然后与实际注塑量和每小时的注塑料用量进行比较。
(13).重新调整整个生产工艺。