骨架零件注塑模具设计
线圈骨架的注塑模具设计

毕业设计(论文)课题名称线圈高骨架的注塑模具设计学生姓名学号院(系)、专指导教师职称20**年4 月26日任务书一、设计课题线圈骨架注塑模设计二、工件图及技术要求图式:工件图1.零件名称:线圈骨架2.材料:聚氯乙烯3.技术要求:设计一模两件侧浇口注塑模三、任务要求1.材料的工艺成形性能2.塑件的工艺性分析3.模具结构设计4.相关工艺计算5.完成模具的装配图及零件图的绘制6.编写设计说明书摘要本设计主要讲述了以软聚氯乙烯(SPVC)为材料的线圈高骨架注塑模具的设计过程。
此模具在设计时,充分考虑了生产批量、以提高生产效率、降低生产成本为主要宗旨。
本产品为电动机绕线圈,形状规则,内空心,侧有凹槽,其要求它具有耐光,耐化学腐蚀、耐磨。
结合这些要求,材料选择软聚氯乙烯。
根据计算出的体积与质量选择SZ-100-60型号的注塑机注塑。
由于塑件内空心,侧有凹槽要求模具必需采用斜导柱侧抽芯机构分型。
经过比较,采用斜导柱在定模,哈夫块(斜滑块)在动模的结构。
整体斜楔定位,斜导柱侧抽芯分型,推板推出工件的工作原理。
设计中对主要零件一一的进行了设计。
文中插入了非标准零件图,以及模具结构图。
AbstractIs it tell taking soft polyvinyl chloride (SPVC ) as material coil high skeleton mould plastics idea course of mould mainly to design originally.This mould is in the design, fully consider production lot , regard improving production efficiency , reducing the production cost as the main aim.This product winds the coil for the motor, form rule, hollow inside, the side has grooves , it requires it is able to bear all, able to bear chemistry and corroded, wear-resisting . Combine these require material choose the soft polyvinyl chloride. Choose the moulding plastics machine of SZ-100-60 type to mould plastics according to the volume and quality calculated out. Mould piece hollow , side have groove demand mould must adopt oblique to lead post side release the core organization dividing into type. Through compare, adopt oblique to lead post make mould , Haff piece (oblique to slip yuan ) Move the structure of the mould . Whole oblique wedge make a reservation, oblique to lead post side release core person who divide , push board put out operation principle of work piece.To the designing one by one of major part in the design. Have inserted the non-standard part picture, and mould structure chart in the article.目录摘要 (I)Abstract (II)前言 (1)第1章塑件分析 (2)第1.1节塑件工艺性能分析 (2)第1.2节塑件批量 (2)第1.3节塑件批量体量和质量 (3)第2章注塑机的选择 (4)第2.1节注塑机的概述 (4)第2.2节选择注塑机 (6)第3章模具设计的有关计算 (6)第3.1节成型零件工作尺寸的计算 (6)第3.2节成型腔壁厚的计算 (8)第4章模具结构的设计 (9)第4.1节浇注系统的设计 (9)第4.2节模具结构草案 (14)第4.3节合模导向机构设计 (16)第4.4节塑件脱模机构设计 (18)第4.5节侧向分型与抽芯机构设计 (18)第4.6节模具温度调节系统 (22)第5章注塑机参数的校核 (23)第5.1节最大注塑量的校核 (23)第5.2节注塑压力的校核 (23)第5.3节锁模力的校核 (24)第5.4节模具与注塑机安装部分相关尺寸校核 (24)第5.5节开模行程和顶出装置的校核 (25)结论 (26)参考文献 (27)符号说明 (28)致谢 (30)前言随着塑料工业的发展,塑料制品在工业及日常生活中使用越来越大,因此对塑料模具设计人员的需求也在逐年的增加。
线圈骨架注塑成型工艺与模具设计
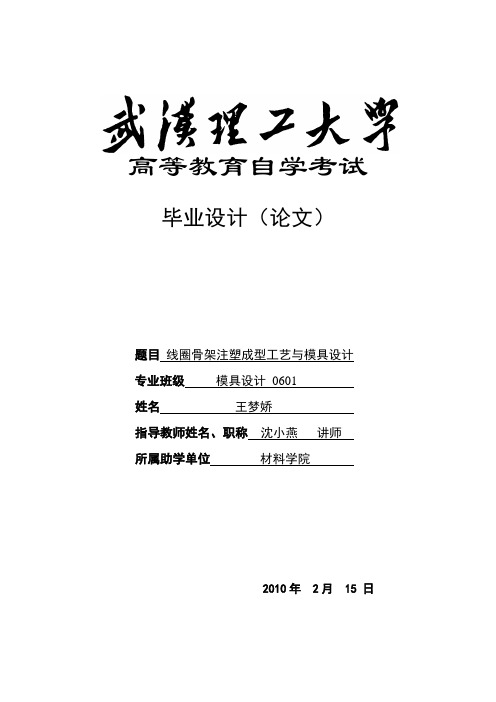
高等教育自学考试毕业设计(论文)题目线圈骨架注塑成型工艺与模具设计专业班级模具设计0601姓名王梦娇指导教师姓名、职称沈小燕讲师所属助学单位材料学院2010年 2月 15 日引言塑料膜主要有压塑成型模具、注塑成型模具、传递成型模具、挤塑成型模具、中空制品吹塑成型模具、热成型模具等等。
本次设计主要是用注塑成型模具。
注塑成型模具:塑料先加在注塑机的加热料筒内,塑料受热熔融后,在注塑机的螺杆或活塞推动下,经喷嘴和模具的浇注系统进入模具型腔,塑料在模具型腔内固化定型,这就是注塑成型的简单过程。
注塑成型所用的模具叫注塑模具。
注塑模具主要用于热塑性塑料制品的成型,但近年来也越来越多的用于热固性塑料成型。
注塑成型在塑料制件中占有很大比重,世界塑料成型模具产量中的约半数以上为注塑模具。
近年来发展了一种在注塑成型时在注入塑料熔体后,立即向制件内部充入惰性气体进行保压的气体辅助注塑成型方法及其模具,它能生产壁厚的和壁厚相差悬殊的注塑制品,能获得更加优良的制品的外观和性能,同时还能减轻制品的重量,节约原材料。
本次设计的课题是线圈骨架的注塑成型工艺与模具设计,主要是以塑料成型工艺学基本理论为依据,通过对各种注塑成型工艺基本运动的分析,提出了对注塑模具设计的要求。
首先阐述注塑过程中,机械运动的基本概念,然后逐项分析了压缩压注挤出气动等成型原理,指出模具设计中应着重控制到的内容,并介绍了在模具设计中对机械运动灵活运用的方法和一些实例。
最后总结了根据具体情况进行产品工艺运动分析的方法,并强调在模具设计中,对机械运动的控制和灵活运用对提高设计水平和保证注塑件品质的重要意义。
目录绪论................................................................................... ............................ . (5)摘要................................................................................... ............................ . (5)1塑件工艺分析 (6)1.1塑件原始资料分析 (6)1.2:材料分析 (6)1.3:PVC成型特点 (7)1.4:塑件工艺的成型工艺参数 (7)2 注塑工艺与模具结构方案 (8)2.1塑料模现状 (8)2.2模具的型腔数量与布局形式 (9)2.3模具结构设计 (10)2.4 模具的工作过程 (11)2.5分型面的选择 (11)3注塑机的选用与模具类型 (12)3.1 计算单件塑件的体积与质量 (12)3.2 初步选用成型设备 (12)3.3 模具类型 (12)3.4 选用标准模架 (12)4 浇注系统的设计 (13)4.1 浇注系统设计原则 (13)4.2 浇注系统的设计 (13)5 模具的相关设计 (14)5.1 支承零部件的设计 (14)5.2 合模导向机构的设计 (14)5.3 侧向分型抽芯机构的设计 (15)5.4 推出机构的设计 (15)5.5 射模通常用的排气方式: (16)6 抽芯机构的设计与计算 (16)6.1 确定抽芯距 (16)6.2 确定斜销倾角 (16)6.3 确定斜销的尺寸 (17)6.4 侧滑块抽芯距的计算 (17)6.5 成型零件的工作尺寸及校核 (18)6.6 模具零件的尺寸计算 (20)7 斜滑块的设计 (21)7.1 滑块型模具的特点 (21)7.2 斜滑块的设计 (21)8 部分成型零件设计 (22)8.1 模套的设计与制造 (22)8.2 顶出部分的设计 (23)8.3 定模与动模的设计 (23)8.4 脱模机构设计 (25)8.5 合模导向机构和复位机构设计 (25)8.6 止动装置的连接 (25)9 冷却系统的设计 (25)10 校核模具与注射机的有关尺寸 (26)10.1最大注射量的校核 (26)10.⒉校核锁模力 (26)10.3校核最大最小模厚 (26)10.4开合模行程校核 (27)11 部分安装方案 (27)11.1 嵌件安装方案 (27)11.2 先期方案 (27)11.3 改进方案 (27)11.4 嵌件安装手杆工作原理 (28)11.5 安装手杆工作过程 (28)12 模具钢的选择 (29)12.1 模具的类别 (29)12.2 模具的性能要求 (29)12.3 模具选材的一般原则 (30)12.4模具选材的具体考虑因素: (30)12.5 模具材料的发展趋向 (30)结束语 (31)参考文献 (31)致谢 (32)绪论塑料模具是利用其特定形状去成型具有一定形状和尺寸的塑料制品的工具。
骨架零件注塑模具设计
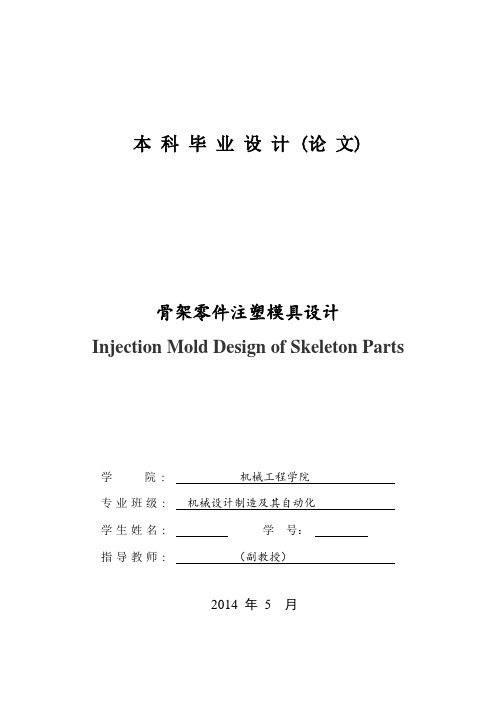
本科毕业设计 (论文)骨架零件注塑模具设计Injection Mold Design of Skeleton Parts学院:机械工程学院专业班级:机械设计制造及其自动化学生姓名:学号:指导教师:(副教授)2014 年5 月目录1 绪论 02 塑件成型工艺性分析 (2)2.1 塑件的分析 (2)2.2 ABS工程塑料的性能分析 (3)3 拟定模具的结构形式和初选注射机 (4)3.1 分型面位置的确定 (4)3.2 型腔数量和排列方式的确定 (4)3.3 注射机型号的确定 (5)4 浇注系统的设计 (7)4.1 主流道的设计 (7)4.2 分流道的设计 (7)4.3 浇口的设计 (9)4.3 冷料穴的设计 (9)5 成型零件的结构及计算 (10)5.1 成型零件的结构设计 (10)5.2 成型零件的工作尺寸计算 (10)6 模架的确定 (13)7 导向机构的设计 (15)8 脱模机构的设计 (16)9 侧向分型与抽芯机构设计 (18)10 温度调节系统的设计 (22)11 排气系统的设计 (24)12 注射机参数的校核 (25)结论 (26)致谢 (27)参考文献 (28)1 绪论一、研究意义塑料是20世纪发展起来的新兴材料,由于应用广泛,已替代部分金属、木材、皮革及硅酸盐等自然材料,成为现代工业和生活中不可缺少的一种人造化学合成材料,并与金属、木材和硅酸盐三种传统材料一起,成为现代工业生产中四种重要的原材料之一。
]5[二、国内外研究现状和水平塑料模具的发展是随着塑料工业的发展而发展的,在我国,起步较晚,但发展很快,特别是最近几年,无论在质量、技术和制造能力上都有很大发展,取得了很大成绩。
这可以在下列几个方面:(1) CAD/CAM/CAE技术在塑料模的设计制造上应用已越来越普遍,特别是CAD/CAM 技术的应用较为普遍,取得了很大成绩;(2) 应用电子信息工程技术进一步提高了塑料模的设计制造水平;(3) 气体辅助注射成型技术的使用更趋成熟;(4) 热流道技术的应用更加广泛;(5) 精密、复杂、大型模具的制造水平有了很大提高;(6) 模具寿命不断提高;(7)模具效率不断提高;(8) 采用模具先进加工技术及设备。
骨架注塑模课程设计

骨架注塑模课程设计一、课程目标知识目标:1. 让学生掌握骨架注塑模的基本概念、分类及结构特点;2. 使学生了解并掌握注塑成型工艺的基本原理及关键参数;3. 引导学生掌握注塑模的设计流程和注意事项。
技能目标:1. 培养学生运用CAD软件进行注塑模设计的能力;2. 提高学生运用CAE软件对注塑成型过程进行模拟分析的能力;3. 培养学生运用实际案例进行注塑模问题诊断和解决的能力。
情感态度价值观目标:1. 激发学生对模具设计及制造领域的兴趣,培养其专业素养;2. 培养学生严谨、细致、负责的工作态度,提高团队协作能力;3. 引导学生关注我国模具行业的发展,增强学生的社会责任感和使命感。
本课程针对高中年级学生,结合学科特点和教学要求,以实用性为导向,注重理论知识与实践技能的结合。
通过本课程的学习,旨在使学生掌握骨架注塑模的基本知识和设计方法,培养其创新意识和实际操作能力,为我国模具行业的发展输送高素质的人才。
二、教学内容1. 骨架注塑模基础知识- 骨架注塑模的定义、分类及结构特点;- 注塑成型原理及关键工艺参数;- 注塑模设计的基本流程及注意事项。
2. 注塑模设计方法与技巧- CAD软件在注塑模设计中的应用;- CAE软件在注塑成型模拟分析中的应用;- 注塑模设计中的常见问题及解决方案。
3. 注塑模设计实践- 实际案例分析与讨论;- 注塑模设计图纸绘制;- 注塑成型过程监控及质量控制。
教学内容依据课程目标进行选择和组织,注重科学性和系统性。
教学大纲明确如下:第1周:骨架注塑模基础知识学习;第2周:注塑成型原理及关键工艺参数学习;第3周:注塑模设计基本流程及注意事项学习;第4周:CAD软件在注塑模设计中的应用;第5周:CAE软件在注塑成型模拟分析中的应用;第6周:注塑模设计实践与案例分析;第7周:注塑模设计图纸绘制及质量控制;第8周:课程总结与评价。
教学内容与课本紧密关联,遵循教学实际,确保学生能够系统地掌握注塑模设计相关知识。
骨架注塑模具设计
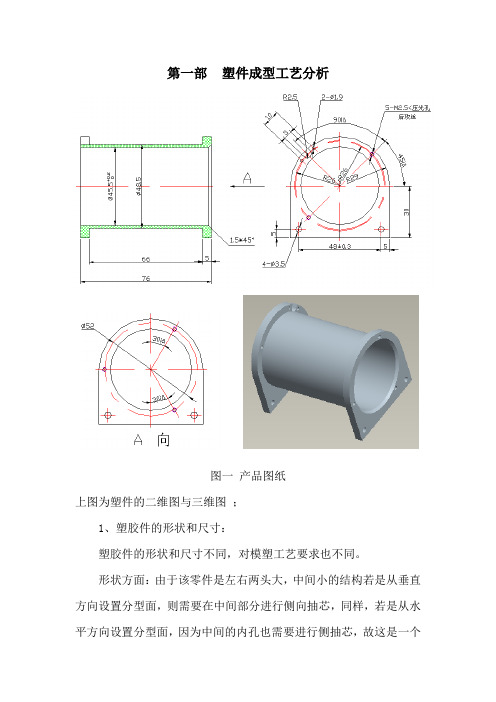
7)浇注系统应达到所需精度和粗糙度,其中浇口必须有IT8以上精度。
(2)浇注系统布置
在多腔模中,分流道的布置有平衡式和非平衡式两类,本例采用平衡式浇注系统,如下图所示:
图五 浇注系统布置
(3)流道系统设计
流道系统设计包括主流道、分流道和冷料井及其结构设计等。
主流道出口端应有1mm左右的圆角。
主流道的长度是L,一般按模板厚度确定。但为了减小充模时压力降和减少物料损耗,小模具通常应控制在50mm之内。
(5)分流道截面形状确定
在设计多型腔或者多浇口的单型腔的浇注系统时,应设置分流道。分流道就是指主流道末端与浇口之间的一段塑料熔体的流动通道。
分流道的截面形状有圆形、半圆形、矩形、梯形、V形等多种。其中圆形截面较为理想。如下图:
潜伏式浇口是点浇口在特殊场合下的一种应用形式。但可以在脱模时自动拖断;它可以隐藏在外表不露出的部位,使浇口痕迹不外漏。但加工比较空难,容易磨损。
侧浇口也称为边缘浇口,由于它开设在主分型面上,截面形状易于加工和调整。多型腔模具常采用侧浇口。
综合上所述,由于本例中有侧滑块,分流道开设在定模一侧,故采用搭接式浇口,如下图所示:
2、塑胶件的尺寸精度和外观要求:
塑胶件的尺寸精度和外观要求与模塑工艺方法、模具结构型式及制造精度等有关。
除了上面所说的这些尺寸,其他尺寸参考教材P69的公差表,在MT5~MT7中选取。本例我选择MT7。塑件表面粗糙度按照一般的标准设为08-0.2 ,(参考教材P71)本例采用0.8 。表面允许有分型线。
(2)成型零件工作尺寸计算
1)计算平均收缩率
2)型腔尺寸计算
当塑件制件尺寸较小、精度级别较高时, 此时,X=0.75 。
机械毕业设计-骨架注塑模具设计

[1]
ABSLeabharlann IIABSTRACT
With the superior performance of the continuous development of engineering plastics, industry, public sector, the needs of a variety of plastic products is growing, injection technology increasingly used in the manufacture of various performance requirements of forming the products. The quality of injection mold design, injection molding machine a ABS lications products, forming a direct impact on productivity, quality and cost. Mold can be a good injection molding millions of times, because of their longer life expectancy, on the other hand reduces the cost of plastic parts molding and die as a result of a good replacement, less maintenance, thereby increasing their production efficiency. In order to meet the growing industry demands and the people need to live goods, we should continue research and development designed to enhance the performance of injection mold injection mold in order to meet the needs of all walks of life. In this design, through the use of CAD base on the remote control to carry out a second cave-mode design and development, including convex and concave mold design, the introduction of body design, the choice of injection machine and check, gating system design, cooling system design, selection of moldbase work. In this design, is designed to focus on parts and components in the molding that is convex and concave mold design and casting systems, cooling system design. One of gating system and cooling system design is the soul of a mold design, gating system design of a direct impact on the molding plastic parts quality and production efficiency. Therefore, the gating system design is the focus of injection mold design work. During the design focused on the design of the convex and concave mold size, gating system and cooling system size and its system architecture. Through this design, we first learn to understand the plastic mold of our current situation and development situation, the basic structure of injection mold and injection-casting process, as well as the basic principles of mold design. Keywords: remote base, injection mold, design, ABS
汽车骨架零件注塑模具结构设计

汽车骨架零件注塑模具结构设计汽车骨架零件注塑模具结构设计是指在汽车骨架零件的注塑过程中,设计和制作模具的过程。
汽车骨架零件是汽车零部件的重要组成部分,具有承载和支撑汽车整体结构的作用,如车身、底盘、发动机和变速箱等。
而汽车骨架零件的注塑模具是将熔化的塑料注入到模具中,通过模具的结构将塑料冷却成所需的骨架零件形状。
因此,汽车骨架零件注塑模具结构设计的合理性和优化程度会直接影响到骨架零件的成型质量和生产效率。
下面,本文将从注塑模具结构设计的角度,分别介绍汽车骨架零件注塑模具的结构形式、设计要素、优化方法和发展趋势。
一、汽车骨架零件注塑模具的结构形式汽车骨架零件注塑模具主要分为两类:单面模和双面模。
其中,单面模是指只有一个模具可进行注塑的工具;而双面模则是指一次注塑中既可成形两个相同或不同的零件,其中一个模具固定在注塑机上,其余模具则在运动中与其配合,完成对不同位置的注塑。
相比较而言,双面模可以同时制造零件较多,效率更高,但由于复杂结构、高成本和加工难度大,使用范围较为有限。
二、汽车骨架零件注塑模具的设计要素汽车骨架零件注塑模具的设计要素主要包括注塑模具的结构、尺寸、材质、型腔和排气系统。
其中,注塑模具的结构主要包括模具底板、模具芯、模具导柱、模具行星副和模具定位装置。
模具底板是支撑模具的主体结构,也是模具的压紧及底部通道的排气系统的关键构件;模具芯是用来成型骨架零件的中空和几何形状的零件。
模具导柱用于指导和定位模具芯和模具底板,并保证整个模具精度。
模具行星副是指用于控制模具开合过程、移动模具部件及锁紧模具结构的机构。
模具定位装置是用来定位模具芯和模具底板的零件,能够提高骨架零件成型精度和生产效率。
注塑模具的尺寸是指模具的高度、宽度、深度和精度等。
模具尺寸的合理设计是关键,既要满足骨架零件的成型尺寸要求,同时要兼顾模具生产的简单性和效率。
模具材质可以根据注塑零件性质和模具生产批量选择不同类型的材料。
常用的模具材料有工具钢、硬质合金和碳纤维复合材料等。
骨架注塑模毕业设计(一模两腔带侧抽芯)

系别:专业:模具设计与制造姓名:学号:1025指导老师:老师2012年4月前言光阴似梭,大学三年的学习一晃而过,为具体的检验这三年来的学习效果,综合检测理论在实际应用中的能力,除了平时的考试、实验测试外,更重要的是理论联系实际,让我们走向社会之前完成一次综合性设计。
即本次设计的课题是骨架(SMBS-04)的注射模设计,是对以前所学课程的一个总结。
本次毕业设计课题来源于生活,应用广泛,但成型难度大,模具结构较为复杂,对模具工作人员是一个很好的考验。
它能加强对塑料模具成型原理的理解,同时锻炼对塑料成型模具的设计和制造能力。
在此次设计中,主要用到所学的注射模设计,以及机械设计等方面的知识。
着重说明了一副注射模的一般流程,即注射成型的分析、注射机的选择及相关参数的校核、模具的结构设计、注射模具设计的有关计算、模具总体尺寸的确定与结构草图的绘制、模具结构总装图和零件工作图的绘制、全面审核投产制造等。
其中模具结构的设计既是重点又是难点,主要包括成型位置的及分型面的选择,模具型腔数的确定及型腔的排列和流道布局和浇口位置的选择,模具工作零件的结构设计,推出机构的设计,拉料杆的形式选择,排气方式设计等。
通过本次毕业设计,使我更加了解模具设计的含义,以及懂得如何查阅相关资料和怎样解决在实际工作中遇到的实际问题,这为我以后从事模具职业打下了良好的基础。
本次毕业设计得到了老师和同学的帮助,特别是林章辉老师和蒋红卫老师的悉心指导,在此表示感谢!由于实践经验的缺乏,且水平有限,时间仓促。
设计过程中难免有错误和欠妥之处,恳请老师批评指正。
2012年4月目录前言绪论 (1)第一章设计任务书 (4)第二章塑件分析 (5)一、塑件工艺性 (5)二、塑件结构分析 (6)第三章塑料材料的成型特性与工艺参数 (7)第四章成型设备的选择 (9)一、初选注射机 (9)二、型腔数量的确定 (10)第五章浇注系统的设计和排溢系统的设计 (11)一、塑料制件在模具中的位置 (11)二、浇注系统的设计 (12)三、排溢系统的设计 (14)第六章成型零部件的设计与计算 (15)一、成型零件的结构设计 (15)二、成型零件工作尺寸的计算 (15)三、模架的选取 (18)第七章脱模机构的设计 (19)一、脱模力的计算 (19)二、推出机构的设计 (19)第八章合模导向机构的设计 (21)一、导柱 (21)二、导套 (21)第九章镶块的精定位设计 (22)第十章温度调节系统的设计与计算 (22)一、冷却的计算 (22)二、冷却系统的设计原则与常见冷却系统的机构 (23)第十一章注射机参数的校核 (23)一、注射量的校核 (23)二、注射压力的校核 (23)三、模具与注射机安装部分的相关尺寸 (23)四、行程的校核 (24)五、顶出装置的校核 (25)参考文献 (26)绪论一、我国塑料模具工业的发展现状及特点我国塑料模工业从起步到现在,历经半个多世纪,有了很大发展,模具水平有了较大提高。
骨架塑料模具设计说明书
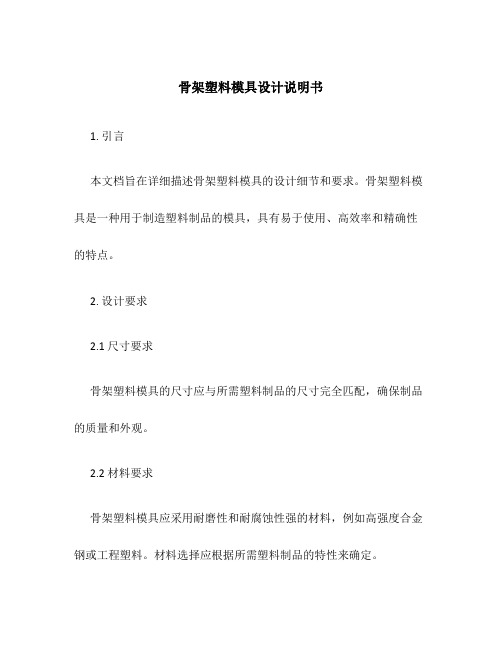
骨架塑料模具设计说明书1. 引言本文档旨在详细描述骨架塑料模具的设计细节和要求。
骨架塑料模具是一种用于制造塑料制品的模具,具有易于使用、高效率和精确性的特点。
2. 设计要求2.1 尺寸要求骨架塑料模具的尺寸应与所需塑料制品的尺寸完全匹配,确保制品的质量和外观。
2.2 材料要求骨架塑料模具应采用耐磨性和耐腐蚀性强的材料,例如高强度合金钢或工程塑料。
材料选择应根据所需塑料制品的特性来确定。
2.3 结构要求骨架塑料模具应具有合理的结构设计,可实现塑料制品的顺利成型。
模具应包括模具座、模具芯、模具腔等组成部分,并确保各部分能够准确对位和运动。
3. 设计步骤3.1 模具布局设计根据所需塑料制品的形状和尺寸,设计模具的整体布局。
将模具座、模具芯和模具腔等组成部分合理安排,并确保模具能够满足生产要求。
3.2 模具座设计设计模具座的形状和尺寸,确保模具可以稳定地安装和固定在注塑机上。
模具座还应具有足够的刚性和稳定性,以防止在注塑过程中产生变形。
3.3 模具芯设计设计模具芯的形状和尺寸,确保塑料制品的内部空间和结构可以准确复制。
模具芯还应具有光滑的表面和良好的散热性能,以便在注塑过程中快速冷却和硬化。
3.4 模具腔设计设计模具腔的形状和尺寸,确保塑料制品的外部形状和表面质量能够达到要求。
模具腔还应具有光滑的表面和足够的冷却系统,以保证制品的充分填充和快速冷却。
3.5 模具配件设计设计模具的配件,如导向柱、顶针、脱模装置等。
这些配件的形状和尺寸应与模具的其他部分相适应,以确保模具的稳定性和运行效率。
4. 模具制造和调试4.1 模具加工根据设计图纸和规格要求,进行模具的精密加工。
加工工艺应精细、准确,并确保模具的尺寸和形状与设计相符。
4.2 模具装配将加工好的模具零部件进行安装和装配。
确保模具各部分的准确对位和顺利组装,以确保模具的正常运行和高效率生产。
4.3 模具调试进行模具的调试工作,通过试产和调整模具参数,使得塑料制品的尺寸和质量达到要求。
汽车骨架零件注塑模具结构设计

汽车骨架零件注塑模具结构设计汽车骨架零件注塑模具结构设计Auto parts injection mold frame structure design摘要本课题以中国汽车产业进展为背景,对汽车骨架零件模具设计。
通过汽车骨架零件模具设计,提高汽车骨架零件模具的质量,为汽车骨架零件提供良好的铸造环境。
本设计依照汽车骨架零件模具的设计作为动身点,对注射口,动定模和推板等进行设计。
由于此模具用于快速生产,因此在设计时要充分便利的特色。
在设计中运用成熟的技术对其设计。
要紧工作:第一对国内外注射模具进行调研,对模具的工作环境进行比较、分析、设计,确定主题。
其次,基于模具人机工程学等相关资料结合模具基础理论知识对本模具环境做出比较分析,提出模具设计优化方案。
最后,利用相关综合软件对设计进行展现。
关键字:汽车骨架零件;模具设计SummaryThe issue of China's automobile industry as the background, on the car frame parts mold design. Through the vehicle frame parts mold design, mold to improve the quality of automotive frame parts, frame parts for the automotive environment to provide a good cast.The design of automobile parts mold design framework as a starting point, on the injection port, moving the fixed mold and push board design. Because the mold for rapid production, so the design must fully and convenient features. In the design of their design using proven technology.Main tasks: first to conduct research at home and abroad injection mold, the mold's working environment to compare, analyze, design, identification of themes. Secondly, based on ergonomics and other related materials mold mold base combination theoretical knowledge of the mold to make more environmental analysis, mold design optimization. Finally, the use of relevant software design integrated display.Keywords: car frame parts; mold design名目第一章绪论 (1)1.1我国模具工业的现状 (1)1.2模具工业的重要地位 (2)1.3 模具技术的现状及进展趋势 (3)1.4 注塑模具的现状与进展前景 (4)1.5 毕业设计的目的和意义 (5)第二章塑料制件设计 (6)2.1 汽车骨架零件的测绘与设计 (6)2.2汽车骨架零件工艺分析 (6)2.3 汽车骨架零件塑件材料选用及特性 (7)2.4汽车骨架零件注塑的差不多要求 (9)第三章汽车骨架零件注射成型的模拟分析 (10)3.1 流淌模拟分析 (10)3.2 模具温度的模拟分析 (10)3.3熔体温度的模拟分析 (10)3.4注塑速率的模拟分析 (11)3.5注塑压力的模拟分析 (11)3.6汽车骨架零件成型的实验研究 (11)3.7 结论 (12)第四章注射模具总体结构设计 (13)4.1 塑件体积的运算 (13)4.2 运算塑件的质量 (13)4.3 按注射机的最大注射量确定型腔数目 (13)4.4 运算浇注系统的体积 (14)4.5 导柱的设计 (14)4.6导向结构的总体设计 (15)第五章模具的设计 (16)5.1 分型面的选择设计原那么 (16)5.2 型腔数目的确定 (17)5.3 浇注系统设计 (18)5.4 成型零部件设计 (21)5.5 导向机构的设计 (24)5.6 推出机构的设计 (25)5.7 冷却系统的设计 (27)5.8 模具排气槽的设计 (28)5.9 校核 (28)总结 (32)参考文献 (33)致谢 (34)附表第一章绪论1.1我国模具工业的现状80年代以来,中国模具工业进展十分迅速。
骨架注塑模课程设计
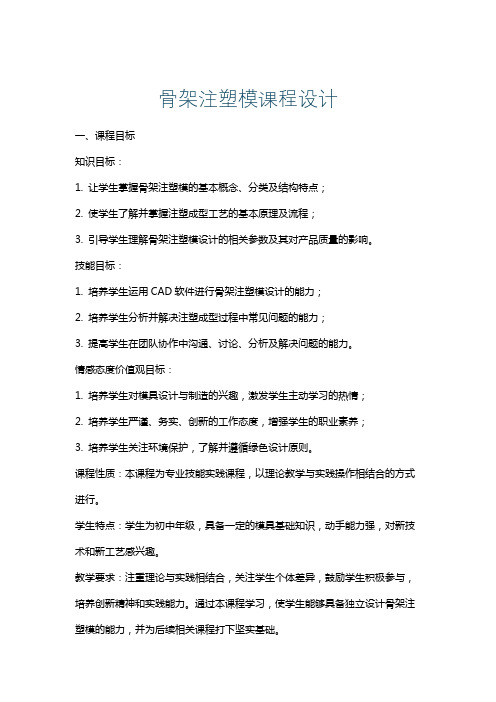
骨架注塑模课程设计一、课程目标知识目标:1. 让学生掌握骨架注塑模的基本概念、分类及结构特点;2. 使学生了解并掌握注塑成型工艺的基本原理及流程;3. 引导学生理解骨架注塑模设计的相关参数及其对产品质量的影响。
技能目标:1. 培养学生运用CAD软件进行骨架注塑模设计的能力;2. 培养学生分析并解决注塑成型过程中常见问题的能力;3. 提高学生在团队协作中沟通、讨论、分析及解决问题的能力。
情感态度价值观目标:1. 培养学生对模具设计与制造的兴趣,激发学生主动学习的热情;2. 培养学生严谨、务实、创新的工作态度,增强学生的职业素养;3. 培养学生关注环境保护,了解并遵循绿色设计原则。
课程性质:本课程为专业技能实践课程,以理论教学与实践操作相结合的方式进行。
学生特点:学生为初中年级,具备一定的模具基础知识,动手能力强,对新技术和新工艺感兴趣。
教学要求:注重理论与实践相结合,关注学生个体差异,鼓励学生积极参与,培养创新精神和实践能力。
通过本课程学习,使学生能够具备独立设计骨架注塑模的能力,并为后续相关课程打下坚实基础。
二、教学内容1. 骨架注塑模基本概念:介绍骨架注塑模的定义、作用及其在工业生产中的应用;2. 骨架注塑模的分类及结构:讲解不同类型的骨架注塑模及其结构特点,结合教材章节进行实例分析;3. 注塑成型工艺原理:阐述注塑成型过程中原料、温度、压力等参数对产品质量的影响,引导学生掌握工艺优化方法;4. 骨架注塑模设计原则及参数:介绍骨架注塑模设计的基本原则,分析设计参数对模具性能和产品成型质量的影响;5. CAD软件在骨架注塑模设计中的应用:教授学生运用CAD软件进行模具设计的基本操作方法,提高设计效率;6. 注塑成型问题分析与解决:分析注塑成型过程中常见问题,探讨解决方案,提高学生实际操作能力;7. 绿色设计与环保:讲解绿色设计原则及其在骨架注塑模设计中的应用,培养学生的环保意识。
教学大纲安排:第一周:骨架注塑模基本概念及分类;第二周:骨架注塑模结构特点及成型工艺原理;第三周:骨架注塑模设计原则及参数;第四周:CAD软件在骨架注塑模设计中的应用;第五周:注塑成型问题分析与解决;第六周:绿色设计与环保。
最新42线圈骨架注塑模具结构设计

增加螺钉,限制滑块滑动位置。
5、成型零件结构设计
(1)型腔设计 由于塑件采用的是平面分型,为了便于加工,因
此型腔采用整体嵌入式结构。
(2)型芯设计 型芯机构设计采用组合式,可节省贵重的模具钢,
减少加工工作量。
(3)型芯的处理
镶块1
镶块2
型芯
侧型芯1 侧型芯2
四、选择标准模架
综合考虑本塑件采用一模两腔平衡布置、侧浇口一次 分型结构、型腔的壁厚要求、塑件尺寸大小、侧向抽芯机 构、冷却水道的布置等多项因素,选取模架型号: lkm_side_gate,尺寸为230×300。
R=R0+(1~2)mm d=d0+(0.5~1)mm 取主流道球面半径R=13mm; 取主流道的小端直径d= Φ4.5mm。
(2)分流道设计
分流道的形状及尺寸,应根据塑件的体积、壁厚、形 状的复杂程度、注射速率、分流道长度等因素来确定。 本塑件的形状不算复杂,熔料填充型腔比较容易。根据 型腔的排列方式可知分流道的长度较短,为了便于加工 起见,本模具选用截面形状为R4的半圆形分流道。
根据公式:L=l1+l2+l3+l4可计算斜导柱工作长度。由 于上模座板和型芯固定板尺寸尚不确定,即h0不确定, 故暂选h0=25mm。如后该设计中h0有变化,则就修正L的 长度,取D=20mm,所以根据公式计算,取L=55mm。
(4)滑块与导滑槽设计
1)滑块与侧型芯(孔)的连接方式设计 本例中侧向抽芯机构主要是用于成型零件的侧向孔 和侧向凸台,其尺寸分别为4.2×1.6×1.3mm和 3.9×0.9×0.9mm,拟采用组合式结构。由于侧向孔和 侧向凸台的尺寸较小,考虑到型芯强度和装配问题,拟 采用如图所示的结构形式。
骨架的注塑模具设计
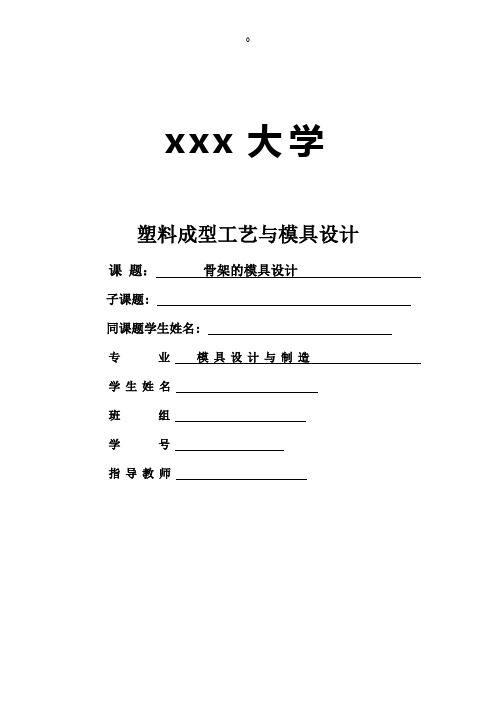
xxx大学塑料成型工艺与模具设计课题:骨架的模具设计子课题: 同课题学生姓名:专业模具设计与制造学生姓名班组学号指导教师第一章塑件工艺分析1.1、塑件的原始材料分析该材料为丙烯腈-丁二烯-苯乙烯共聚物(ABS塑料),骨架塑件如图1:图1 骨架塑件ABS是由丙烯腈、丁二烯和苯乙烯三种化学单体合成,收缩率为0.3%~0.8% 。
ABS 无毒、无味、呈微黄色,成型的塑件有较好的光泽。
从使用性能上看,该塑料具有极好的抗冲击强度,有良好的机械强度和一定的耐磨性、耐寒性、耐油性、耐水性、化学稳定性和电气性能。
从成型性能上看,该塑料在升温时粘度增高,所以成型压力较高,故塑件上的脱模斜度宜稍大;ABS易吸水,成型加工前应进行干燥处理;ABS易产生熔接痕,模具设计时应注意尽量减少浇注系统对料流的阻力;在正常的成型条件下,壁厚、熔料温度对收缩率影响极小。
在要求塑件精度高时,模具温度可控制在50~60℃,而在强调塑件光泽和耐热时,模具温度应控制在60~80℃。
1.2、塑件的结构、尺寸精度及表面质量分析1.2.1、结构分析从零件图上分析,该零件总体形状为回转体,在一个直径为38mm高为17mm的圆柱中间有一个直径为16mm高为11mm和一个直径为19mm高为6mm 的台阶孔,然后留壁厚为 1.5mm 。
该塑件有凹槽,因此,模具设计时必须设置侧向分型抽心机构,该零件属于中等复杂程度。
1.2.2、尺寸精度分析该塑件所有尺寸的精度为IT4级,对塑件的尺寸精度要求不高,对应的模具相关零件的尺寸加工可以保证。
从塑件的壁厚上来看,该塑件的所有壁厚均匀,都为1.5mm ,有利于塑件的成型。
1.2.3、表面质量分析对该塑件表面没有什么要求,故比较容易实现。
综合以上分析,注射时在工艺参数控制的好的情况下,零件的成型要求可以得到保证。
1.3、 明确塑件生产批量该塑件要求大批量生产。
1.4、估算塑件的体积和重量按照图2 塑件各部分体积近似计算: 3218.19270171914.3V mm =⨯⨯=总 321m m 1700.3169.53.14 V =⨯⨯=3222m m 4521.66)11-(193.14 V =⨯⨯=3223mm 6801.258)9.5-(193.14 V =⨯⨯=324m m 2210.561183.14 V =⨯⨯=故塑件的体积为:33cm 4.044036.46mm 2210.56-6801.25-4521.6-1700.31-19270.18V ===塑件重量为g 4.28244.041.06v G S =⨯=⨯=ρ式中ρ为塑料密度(ABS 的密度307.1~04.1cm g =ρ)图2 塑件各部分体积1.5、分析塑件的成型工艺参数干燥处理:ABS材料具有吸湿性,要求在加工之前进行干燥处理。
方形骨架塑胶模具设计
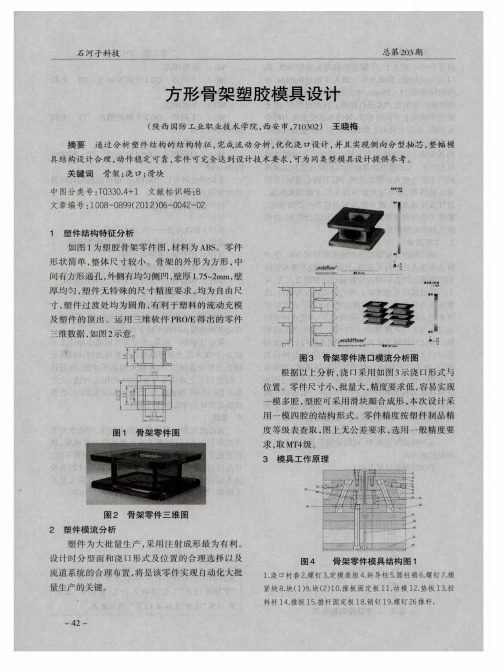
设 计 合 理 , 作 稳 定 可 靠 , 件 可完 全 达 到 设计 技 动 零
术要 求 。 参口衬套进入模具型
腔 , 端 浇 口尺 寸 大 于 上 端 浇 口尺 寸 , 以保 证 下 下 可 层 型 腔 能 够 充 满 , 适 当时 间冷 却 后 , 经 动模 向后 移
天业循 环经济被 国家工信部命 名为第一批重大示范工程
4月 2 2日, 疆 天业 干 法 乙炔— — 电石渣 干 法水 泥循 环 经济 工程 项 目被 国家 工信 部确 定为 全 国第 一 新
批 工 业循环 经 济 重大 示 范工程 。
为推 动工 业领 域 循环 经济 发展 , 快形 成 资源 循环 利用 产 业模 式 , 加 工业和 信 息化部 于 2 1 年 组织开 0 1
展 了工业 循环 经 济 重大 示 范工 程评 审和 论 证 工作 。 最终 , 国评 出 2 项工 业循 环 经济 重 大示 范工 程( 全 3 第
一
批) 。天 业集 团干 法 乙炔— — 电石渣 干 法水泥 工 程项 目是 此次 受 奖工程 之 一。
天 业 集 团在 打 造 循环 经 济 的过 程 中, 设 了 以干 法 乙炔 生产 聚氯 乙烯 的制作 工 艺 , 建 配置 有 1 O 吨 1万 电石 渣新 型干 法水 泥 生产 装 置 。该 工程 采 用 经济 、 安全 、 定运 行 的干法 乙炔技 术替 代 了传 统 的 湿法 乙 稳 炔 工 艺技 术 , 少 了因水溶 解 带来 的乙炔 溶解 损 失 , 时, 减 同 实现 了节 水效 果 以及 湿 电石渣 烘干造 成 的能源
型 。 【' l ’ 2
[]模 具 技 术 手册 》 委会 编 . ]机械 工 业 出 2《 编 [ . H
排骨架的注塑模具设计

前言模具是现代化工业生产的重要工艺装备,被称为“工业之母”。
其广泛应用于汽车、拖拉机、飞机、家用电器、工程机械、动力机械、冶金、机床、兵器、仪器仪表、轻工、日用五金等制造业中,起着极为重要的作用;模具是实现上述行业的钣金件、锻件、粉末冶金件、铸件、压铸件、注塑件、橡胶件、玻璃件、陶瓷件等生产的重要工艺装备。
采用模具生产毛坯或成品零件,是材料成形的重要方式之一,与且学加工相比,具有材料利用率高、能耗低、产品性能好、生产率高和成本低等显著特点。
塑料模具是整个模具工业中的一枝独秀,发展极为迅速,应用范围极其广泛。
其中塑料注射成型所用的模具称为注射成型模具,简称注射模。
塑料的注射成型过程,是借助于注射机内的螺杆或柱塞的推力,将已经塑化的塑料熔体以一定的压力和速率注射到闭合的模具型腔内,经冷却、固化、定型后开模而获得制品。
当塑料原材料,注射机和注射成型工艺参数确定后,制品的质量和注射成型的生产率就基本上取决于注射模的结构类型和工作特性。
本次毕业设计的题目为排骨架的注塑模具设计, 设计目的在于检验理论知识掌握情况,将理论与实践结合;培养自己的动手能力、创新能力;系统实践Pro/E,Auto—CAD 的应用,提高这两种软件的操作和应用其解决实际问题的能力;进一步掌握进行模具设计的方法和过程,为将来走向工作岗位进行科技开发工作和撰写科研论文打下基础。
主要内容包括: 制品材料的选择及材料性能的分析、注射机的选用、模具结构选择、浇注系统的设计、成型零件的设计、合模导向机构的设计、冷却系统的设计、抽芯机构的设计、推出机构的设计以及部分零件的制造工艺分析和数控加工等。
通过此次设计,加深了模具的设计中从选材到设计到成型的了解,并系统掌握模具设计和制造的各个细节;锻炼了自己的独立思考能力和创造能力,为更好更快的适应工作做了必要的准备。
由于是初次对整个模具进行设计,故在设计过程中,本人遇到了不少的困难,但通过老师的指导、同学的帮助和查阅相关资料,尤其是指导老师的耐心修改,基本上都克服那些困难了。
骨架注塑模具的设计

动 阻力 ,减少 翘 曲变形 ,采 用二个 侧 浇 口。在进 行脱 模机 构 设计 时 , 由于制 件壁 薄 ,不宜采 用顶 杆来 脱模 , 因此采 用推 板来 脱模 。综 上所述 ,确 定 了采用 制件 在模 具 中垂直 放置且 在 中部分 型和 推板 脱模 的模具 结构 ( 图 2所 示 ) 如 。
两边左 右对称 设置抽 芯机 构 , 两边 的侧 型芯就 在制
尺 寸 ,但制 件有 通 孔 而且 壁 薄 ,因此 模 具 设计 方
案 的优 劣对 模 具结 构 复杂 程度 及 模具 制 造难 易 程
度取 着 决定 性作 用 。
件 内部接合 ,型芯 的制 造误 差 、 侧压 力等情况 就极 容易造 成二 侧型芯接 合面 接触不 良, 会造成 制件 就 内部产 生飞边 , 并且 不好清 除 , 成型 的制件就 会成 为废 品 。 而采用 制件 在型腔 中垂直 放置 , 采用 推板
模 具 的 设计 制造 水平 是 模 具制 造 企业 在 市场 竞 争 中 的核心 所在 , 模 具设 计 是集 知识 的采 集 、 而 加 工技 术 应用 于 一体 的创新 过程 ,是 模具 制造 企 业 核心 竞 争力 的综合 体现 。在这 一 过 程 中对模 具 设 计人 员的设 计 经验 和技 术 积 累 、特 别是 设计 人 员 潜意 识 中的设 计经 验类 的隐 性知 识 依赖 程度 较
骨 架 注 塑 模 的 设 计 来 阐 述 模 具设 计 人 员 利 用 自 己 的设 计 经 验 和 技 术 积 累 设 计 出优 质 的模 具 。 关键 词 : 骨 架 注 塑 模 具 ;设 计方 案 ; 结 构 设 计 ; 制 造
中图分类号 :T 3 06 + T 7 文献标识码 :A 文 章编 号:1 7 -4 0 (0 0O ~13 0 Q 2 .62 G 6 6 2 8 12 l)4 0 - 2
改骨架注塑模毕业设计说明书
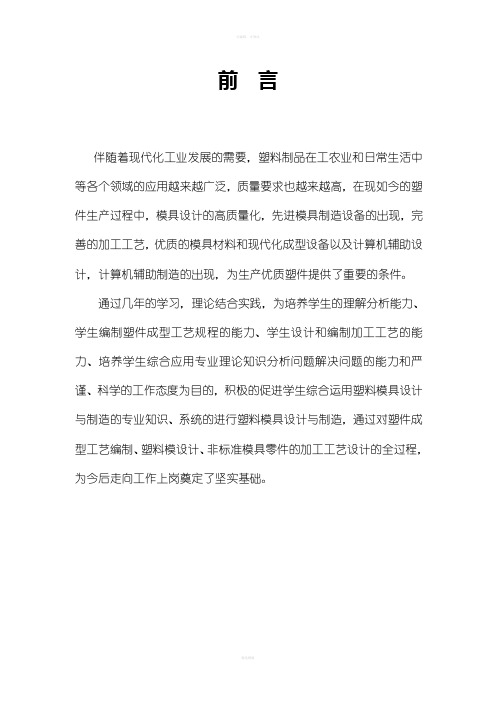
前言伴随着现代化工业发展的需要,塑料制品在工农业和日常生活中等各个领域的应用越来越广泛,质量要求也越来越高,在现如今的塑件生产过程中,模具设计的高质量化,先进模具制造设备的出现,完善的加工工艺,优质的模具材料和现代化成型设备以及计算机辅助设计,计算机辅助制造的出现,为生产优质塑件提供了重要的条件。
通过几年的学习,理论结合实践,为培养学生的理解分析能力、学生编制塑件成型工艺规程的能力、学生设计和编制加工工艺的能力、培养学生综合应用专业理论知识分析问题解决问题的能力和严谨、科学的工作态度为目的,积极的促进学生综合运用塑料模具设计与制造的专业知识、系统的进行塑料模具设计与制造,通过对塑件成型工艺编制、塑料模设计、非标准模具零件的加工工艺设计的全过程,为今后走向工作上岗奠定了坚实基础。
绪论塑料工业是新兴的工业,是随着石油工业的发展应运而生的。
目前塑料制件几乎已经进入一切工业部门以及人民日常生活的各个领域。
塑料工业又是一个飞速发展的工业领域。
世界塑料工业从20世纪30年代前后开始研制到目前的塑料产品系列化,生产工艺自动化,连续化以及不断开拓功能塑料新领域。
它经历了初创阶段(30年代以前),发展阶段(30年代),飞跃发展阶段(50至60年代)和稳定增长阶段(70年代至今)等这样几个阶段。
塑料作为一种新的工程材料,其不断被开发与应用,加之成型工艺的不断成熟,完善与发展,极大的促进了塑料成型方法的研究与应用和塑料成型模具的开发与制造。
随着工业塑料制件和日用塑料制件的品种和塑料是以树脂为主要成分的高分子有机化合物,在一定温度和压力下,塑料具有可塑性,可以利用模具将其成型为具有一定几何形状和尺寸精度的塑料制件。
塑料制件之所以能够在工业生产中得到广泛应用,是由于它们本身具有的一系列特殊优点所决定的。
塑料谜底小,质量轻。
这就是“以塑代钢”的明显优点所在。
塑料的比强度高,绝缘性能好,介电损耗低,所以塑料是现代电工行业和电器行业中不可缺少的原材料。
- 1、下载文档前请自行甄别文档内容的完整性,平台不提供额外的编辑、内容补充、找答案等附加服务。
- 2、"仅部分预览"的文档,不可在线预览部分如存在完整性等问题,可反馈申请退款(可完整预览的文档不适用该条件!)。
- 3、如文档侵犯您的权益,请联系客服反馈,我们会尽快为您处理(人工客服工作时间:9:00-18:30)。
本科毕业设计 (论文)骨架零件注塑模具设计Injection Mold Design of Skeleton Parts学院:机械工程学院专业班级:机械设计制造及其自动化学生姓名:学号:指导教师:(副教授)2014 年5 月目录1 绪论 (1)2 塑件成型工艺性分析 (3)2.1 塑件的分析 (3)2.2 ABS工程塑料的性能分析 (4)3 拟定模具的结构形式和初选注射机 (5)3.1 分型面位置的确定 (5)3.2 型腔数量和排列方式的确定 (5)3.3 注射机型号的确定 (6)4 浇注系统的设计 (8)4.1 主流道的设计 (8)4.2 分流道的设计 (8)4.3 浇口的设计 (10)4.3 冷料穴的设计 (10)5 成型零件的结构及计算 (11)5.1 成型零件的结构设计 (11)5.2 成型零件的工作尺寸计算 (11)6 模架的确定 (14)7 导向机构的设计 (16)8 脱模机构的设计 (17)9 侧向分型与抽芯机构设计 (19)10 温度调节系统的设计 (23)11 排气系统的设计 (25)12 注射机参数的校核 (26)结论 (27)致谢 (28)参考文献 (29)1 绪论一、研究意义塑料是20世纪发展起来的新兴材料,由于应用广泛,已替代部分金属、木材、皮革及硅酸盐等自然材料,成为现代工业和生活中不可缺少的一种人造化学合成材料,并与金属、木材和硅酸盐三种传统材料一起,成为现代工业生产中四种重要的原材料之一。
]5[二、国内外研究现状和水平塑料模具的发展是随着塑料工业的发展而发展的,在我国,起步较晚,但发展很快,特别是最近几年,无论在质量、技术和制造能力上都有很大发展,取得了很大成绩。
这可以在下列几个方面:(1) CAD/CAM/CAE技术在塑料模的设计制造上应用已越来越普遍,特别是CAD/CAM 技术的应用较为普遍,取得了很大成绩;(2) 应用电子信息工程技术进一步提高了塑料模的设计制造水平;(3) 气体辅助注射成型技术的使用更趋成熟;(4) 热流道技术的应用更加广泛;(5) 精密、复杂、大型模具的制造水平有了很大提高;(6) 模具寿命不断提高;(7)模具效率不断提高;(8) 采用模具先进加工技术及设备。
综上所述,我国塑料模具的质量、技术和制造能力近年来确实发展很快,有些已达到或接近国际水平。
然而,由于我国模具制造基础薄弱,各地发展极不平衡,因此总体来看与国际先进水平相比和与国内外市场需求相比,差距还很大。
这主要表现在:塑料模具产品水平,工艺装备水平,开发能力及经济效益等方面,管理及其他方面和产需矛盾等方面。
三、发展趋势从塑料模具的设计、制造及材料选择等方面的考虑,塑料模具技术发展趋势可归纳为以下几方面:(1) 塑料模具标准化。
模具标准化程度将不断提高我国模具标准化程度正在不断提高,估计目前我国模具标准件使用覆盖率已达到30%左右,国外发达国家一般为80%左右。
(2) 在模具设计制造中将全面推广CAD/CAM/CAE技术。
CAD/CAM/CAE技术是模具技术发展的一个重要里程碑。
实践证明,CAD/CAM/CAE技术是模具设计制造的发展方向。
(3) 加强理论研究。
随着塑料制件想大型化,复杂化和精密化发展,模具的制造成本也悦来越高。
所以,模具生产已由传统的经验设计想理论设计,数值模拟的方向发展。
(4) 塑料模具专用材料的研究与开发。
模具材料选用再模具设计与制造中占有重要地位,直接影响模具成本,使用寿命及塑料制件的质量。
国内外模具材料工作者进行了大量的研究工作,以开发出的材料有基本型,预硬型,时效硬化型,热处理硬化型和马氏体时效钢和粉末冶金模具钢等几种类型。
(5) 模具加工的新技术与发展。
模具加工技术与设备的现代化发展,推进了模具行业企业向着技术密集,专业化与柔性化相结合,高技术与高技艺相机和的方向发展。
2 塑件成型工艺性分析2.1 塑件的分析该塑件壁厚为2mm~3mm,塑件的外形尺寸不大,塑料的熔体流程不长,且塑件的材料为热塑性材料,流动性较好,适合于注射成型。
塑件的每个尺寸的公差都不一样,但任务书中已给出部分尺寸的给定公差,未注公差的尺寸取公差MT5.该塑件的形状是一长方体中空零件,其四周有凹槽,塑件形状尺寸如下图2-1所示图2-1 骨架零件2.2 ABS工程塑料的性能分析ABS(共聚物):无毒、无味、微黄色:密度为(1.02~1.05)g/cm 3,制品光泽较好。
冲击韧性、力学强度较高、尺寸稳定,电性能、化学耐腐蚀性好,易于成型和机械加工,可作双色成型件。
适于作一般机械零件,减磨耐磨零件,传动件电信结构件等。
]1[查文献]1[表0.1可知ABS注射参数如下表项目条件注射类型螺杆式螺杆转速30~60r/min喷嘴类型直通式;温度180~190°C料筒温度前段200~210°C 中段 210~230°C 后段180~200°C模具温度50~80°C注射压力70~90MPa保压力50~70MPa注射时间3~5 S保压时间15~30 S冷却时间15~30 S成型时间40~70 S后处理红外灯烘箱;温度70°C;时间2~4h.表2-1ABS注射参数表3 拟定模具的结构形式和初选注射机3.1 分型面位置的确定对此塑件进行结构形式的分析可知,此塑件的分型面选用垂直分型面,分型面形状如图3-1所示图3-1 分型面表示图3.2 型腔数量和排列方式的确定在本设计中,由于此骨架零件属于中小型塑件,而且它的形状比较规则,精度要求也比较一般不是很高,批量生产。
但是该塑件的四周有凹槽,所以需要有侧抽芯机构。
如果该塑件采用一模一腔虽然可以简化模具的结构以及提高塑件精度,但这样会使生产效率降低并提高生产成本。
所以考虑到以上条件在模具中采用一模两腔。
由于本塑件的四周有凹槽所以需要侧向抽芯,故本模具的型腔布置方式如图3-2所示:图3-2 型腔排列图3.3 注射机型号的确定通过Proe/E建模分析的塑件质量为5克,取材料密度为1.05g/cm3,所以塑件体积为:V塑=ρm=05.15=4.76cm3(3-1)浇注系统的体积。
由于浇注系统的凝料体积是个未知的值。
若是流动性好的普通精度塑件,浇注系统凝料月为塑件质量或体积的15%~20%(多浇口多型腔时,注塑厂的统计资料)。
若是流动性不太好、或者是金木塑件,据统计每个塑件所需浇注系统的质量或体积是塑件的0.2~1倍。
当塑料熔体粘度高,塑件愈小、壁愈薄,型腔越多又做平衡式布置是,浇注系统的质量或体积甚至还要大,而大型塑件采用直接浇口时,浇注系统质量相对很小,可忽略不计。
在学校做设计时以0.6nV塑作为预测估算。
]2[V浇=0.6n V塑=2.856 cm3(3-2)V总=n V塑+ V浇=12.376 cm3(3-3)M总=12.376x1.05=12.9948g注射压力:P注≥P成型(3-3)查文献]1[表0.1可知P成型=70~90MPa锁模力:P锁模力≥PA (3-4)P——塑料成型是型腔压力,ABS塑料的型腔压力为30MPa A——浇注系统和塑件在分型面上投影面积的总和A=25x22.5+3.14x3=571.92mm2(3-5)PA=30x571.92=17157.6KN (3-6)根据之前所计算的数据并查参考文献]2[表13-1可选择注塑机型号为XS-ZY-60的卧式注射机,其主要技术参数如下表所示:项目 条件 结构形式卧式 理论注射容积/cm 360 螺杆直径/mm 38 注射压力/MPa 122 注射行程/mm 170 注射时间/s 1.2喷嘴口孔径/mm 4φ喷嘴球半径/mm SR12定位孔直径/mm 054.0060+φ 移模行程/mm 300 锁模力/Kg 500 最大成型面积/mm 2 130 最大模具厚度/mm 200 最小模具厚度/mm 70 模板最大行程/mm 180 锁模方式液压-机械表3-1注射机参数表4 浇注系统的设计浇注系统的作用,是将塑料熔体顺利的充满到模腔深处,以获得外形轮廓清晰,内在质量优良的塑件。
因此要求充模过程快而有序,压力损失小,热量散失少,排气条件好,浇注系统凝料易于与制品分离或切除。
]3[4.1 主流道的设计主流道是指连接注射机喷嘴与分流道的塑料熔体通道,是熔体注入模具最先经过的一段流道,其形状、大小会直接影响熔体的流动速度和注射时间。
]2[在本设计中我采用的是垂直式主流道。
在卧式注射机上主流道垂直于分型面,为了使凝料能顺利拔出,主流道结构为圆锥形。
锥角取4°,内壁粗糙度Ra 小于0.4m μ,主流道小端直径取决于注射机喷嘴孔孔径d=喷嘴孔孔径+(0.5-1)mm=5mm 浇口套的材料为T8A ,热处理要求为53~57HRC , SR=喷嘴球半径+(1-2)mm=13mm主流道长度L 一般控制在60以内在本设计L=50mm 主流道大端直径D=d+2Ltan2α=8mm 球面配合高度h=3-5mm 在本设计中取h=3mm 主流道具体尺寸如下图4-1所示图4-1 浇口套在多型腔或单型腔多浇口(塑件尺寸大)时应设置分流道,分流道是指主流道末端与浇口之间这一段塑料熔体的流动通道。
它是浇注系统中熔融状态的塑料由主流道流入型腔前,通过截面积的变化及流向变换以获得平稳的流态的过渡段。
因此分流道设计应满足良好的压力传递和保持理想的充填状态,并在流动过程中压力损失尽可能小,能将塑料熔体均衡的分配到各个型腔。
]3[分流道长度L=25mm分流道布置形式及截面的形状尺寸如图4-2,4-3所示:图4-2 分流道布置形式图图4-3分流道截面图浇口也称进料口,是连接分流道和型腔的通道,除了直接浇口外,它是浇注系统中截面最小的部分,但却是浇注系统中的关键部分,浇口的位置、形状及尺寸对塑件性能和质量的影响很大。
浇口的作用是使从流道来的熔融塑料以较快的速度进入并充满型腔,型腔充满塑料以后,浇口应按要求迅速冷却封闭,防止预塑时(螺杆后退)型腔内还未凝固的熔体回流。
]3[本设计中塑料的材料为ABS,ABS适用于各类浇口,在本设计中选用侧浇口,浇口截面形状为半圆形,其半径为0.5mm长度为0.5mm4.3 冷料穴的设计在完成一次注射循环的间隔,考虑到注射机喷嘴和主流道入口这一小段熔体因辐射散热而低于所要求的塑料熔体的温度,从喷嘴端部到注射机料筒以内约10mm~25mm的深度有个温度逐渐升高的区域,这时才达到正常的塑料溶体温度。
位于这一区域内的塑料的流动性能及成型性能不佳,如果这里温度相对较低的冷料进入型腔,便会产生次品。
为克服这一现象的影响,用一个井穴将主流道延长以接受冷料,防止冷料进入浇注系统的流道和型腔,把这一用来容纳注射间隔所产生的冷料的井穴成为冷料穴(冷料井)。