干膜光成像工艺规范
底片干膜工艺技术资料

底片干膜工艺技术资料一、底片干膜工艺概述底片干膜工艺是一种常用于光刻技术中的工艺方法。
在硅片制造过程中,光刻技术用于制造集成电路中的微细图案。
底片干膜工艺是光刻技术的一个重要环节,其主要作用是在硅片表面形成一层薄膜,用于保护或增强光刻图案。
二、底片干膜工艺流程底片干膜工艺流程包括以下几个步骤:1. 底片准备在进行底片干膜工艺之前,需要先准备好底片。
底片是一种透明平板,通常由玻璃或石英制成。
底片表面应保持干净无尘,以免影响后续的工艺步骤。
2. 底片清洁底片在使用前需要进行清洁处理,以去除底片表面的杂质和污染物。
清洁方法可以采用化学溶液浸泡或超声波清洗。
3. 干膜涂覆底片清洁完毕后,需要进行干膜涂覆的过程。
干膜是指一种特殊的聚合物材料,可以在底片表面形成一层均匀的薄膜。
干膜涂覆可以采用旋涂法或喷涂法,在涂布的过程中需要控制好涂布速度和涂布厚度,以保证干膜的质量。
4. 烘烤干膜涂覆完成后,需要进行烘烤处理。
烘烤的目的是将干膜固化,并使其与底片表面紧密结合。
烘烤的温度和时间根据具体的干膜材料而定,需要严格控制参数,以确保烘烤效果良好。
5. 剥膜经过烘烤后,干膜与底片表面形成了牢固的结合。
为了制作光刻图案,需要将部分干膜剥离,留下所需的图案。
剥膜的方法可以采用化学溶解或机械剥离,需要根据具体情况选择合适的方法。
6. 检验剥膜完成后,需要对底片进行检验,确保干膜工艺的质量符合要求。
检验的内容可以包括干膜的厚度、表面光洁度等指标。
三、底片干膜工艺的应用底片干膜工艺广泛应用于集成电路的制造过程中。
其主要作用有:1. 保护硅片表面底片干膜可以形成一层保护膜,用于保护硅片表面不被污染或损坏。
在后续的工艺步骤中,底片上的干膜可以起到保护的作用,确保光刻图案的准确传递。
2. 增强光刻图案对比度在光刻过程中,底片上的干膜可以增强光刻图案的对比度,使其更容易识别和处理。
干膜的颜色和透明度可以根据需求来选择,以提高图案的可见度。
(工艺技术)干膜光成像工艺规范
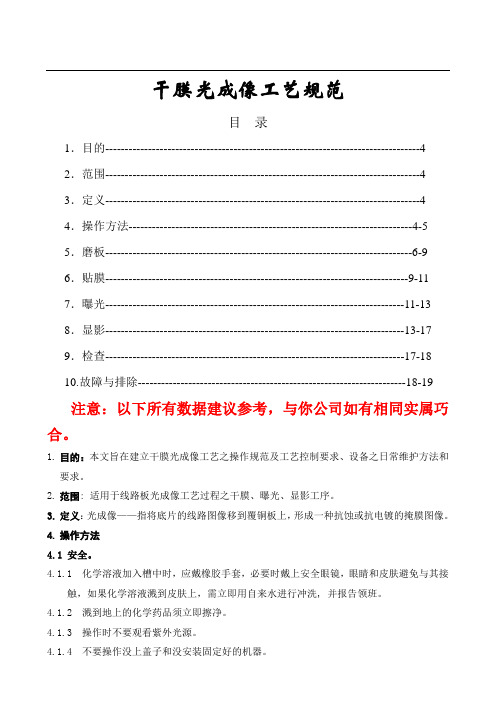
干膜光成像工艺规范目录1.目的---------------------------------------------------------------------------------42.范围---------------------------------------------------------------------------------43.定义---------------------------------------------------------------------------------44.操作方法-------------------------------------------------------------------------4-5 5.磨板-------------------------------------------------------------------------------6-9 6.贴膜------------------------------------------------------------------------------9-11 7.曝光-----------------------------------------------------------------------------11-13 8.显影-----------------------------------------------------------------------------13-17 9.检查-----------------------------------------------------------------------------17-1810.故障与排除---------------------------------------------------------------------18-19注意:以下所有数据建议参考,与你公司如有相同实属巧合。
水溶性干膜显影工艺及常见问题的处理方法

水溶性干膜显影工艺及常见问题的处理方法水溶性干膜的显影液为l一2%的无水碳酸钠溶液,液温30—40℃。
显影的速度在范围内随温度增高而加快,不同的干膜显影温度略有差别,需根据实际情况调整,温度过高会使膜缺乏韧性变脆。
显影机理是感光膜中未曝光部分的活性基团与稀碱溶液反应生成可溶性物质而溶解下来,显影时活性基团羧基一COOH与无水碳酸钠溶液中的Na+作用,生成亲水性集团一COONa。
从而把未曝光的部分溶解下来,而曝光部分的干膜不被溶胀。
显影操作一般在显影机中进行,控制好显影液的温度,传送速度,喷淋压力等显影参数,能够得到好的显影效果。
正确的显影时间通过显出点(没有曝光的干膜从印制板上被溶解掉之点)来确定,显出点必须保持在显影段总长度的一个恒定百分比上。
如果显出点离显影段出口太近,未聚合的抗蚀膜得不到充分的清洁显影,抗蚀剂的残余可能留在板面上。
如果显出点离显影段的入口太近,已聚合的于膜由于与显影液过长时间的接触,可能被浸蚀而变得发毛,失去光泽。
通常显出点控制在显影段总长度的40%一60%之内。
其显影点的计算方法较为简单,使用一至几块长的板材,其长度大于等于显影段的长度,贴完膜后不曝光直接显影,当板子的最前端走到显影出口时关闭显影药水的喷淋。
根据板子显影的情况可得知显影点在显影段中的位置。
从而根据显示情况调整显影速度达到最佳的显影状态。
显影机在使用时由于溶液不断地喷淋搅动,会出现大量泡沫,因此必须加入适量的消泡剂。
如正丁醇、印制板专用消泡剂AF一3等。
消泡剂起始的加入量为0.1%左右,随着显影液溶进干膜,泡沫又会增加,可继续分次补加。
部份显影机有自动添加消泡剂的装置。
显影后要确保板面上无余胶,以保证基体金属与电镀金属之间有良好的结合力。
在显影的过程中碳酸钠不断需要补充,在某些他天气较寒冷地区在冬天显影时其补充碳酸钠的药桶要有加热装置,以防止显影段由于补充药液导致温度下降造成显影不良。
显影后板面是否有余胶,肉眼很难看出,可用1%甲基紫酒精水溶液或l一2%的硫化钠或硫化钾溶液检查,染十甲基紫颜色和浸入硫化物后没有颜色改变说明有余胶。
底片干膜工艺技术资料

2024年8月15日星期四
电路图形转移材料的演变
电路图形转移材料的演变
v 印制电路图形的转移所使用的原材料,自出现印制电路 以来,原材料的研制与开发科学攻关工作从未停止过。 从原始阶段设计采用抗蚀油漆或虫胶漆手工描绘简单的 线路图形转移工艺技术的需要。但随着微电子技术的飞 速发展,大规模集成电路和超大规模集成电路的广泛应 用,要求印制电路板的制造技术,必须适应高密度、高 精度、细导线、窄间距及小孔径电路图形转移需要。几 十年来,研制与开发出新型的光致抗蚀剂与电路图形转 移技术: 如光致抗蚀干膜、湿法贴膜技术、电泳光致抗 蚀膜和直接成像技术,都逐步地被制造印制电路板商家 所采用,使电路图形的转移品质大幅度的提高。为叙述 简便,就印制电路板制造过程中,所采用的电路图形转 移原材料,按顺序加以简单论述:
v 以上两种工艺过过程概括如下:
v 印制蚀刻工艺流程:
v 下料→板面清洁处理→涂湿膜→曝光→显影(贴干膜→ 曝光→显影)→蚀刻→去膜→进入下工序
v 畋形电镀工艺过程概括如下:
v 下料→钻孔→孔金属化→预镀铜→板面清洁→涂湿膜→ 曝光→显影(贴干膜→曝光→显影)→形成负相图象 →图形镀铜→图形电镀金属抗蚀层→去膜→蚀刻→进入 下工序
v 6)热阻聚剂 在干膜的生产及应用过程中, 很多步骤需要接受热能, 为阻止 热能对干膜的聚合作用加入 热阻聚剂。如甲氧基酚、对苯二 酚等均可作为热阻聚剂。
v 7)色料 为使干膜呈现鲜艳的颜色, 便于修版和检查而添加色料。如 加入孔雀石绿、苏丹三等色料 使干膜呈现鲜艳的绿色、兰色 等。
v 8)溶剂 为溶解上述各组份必须使用溶剂。通常采用丙酮、酒精作溶 剂。 此外有些种类的干膜还加入光致变色剂, 使之在曝光后 增色或减色, 以鉴别是否曝光, 这 种干膜又叫变色于膜。
干膜的技术性能要求

干膜的技术性能要求
2008-9-23作者:来源::
干膜光致抗蚀剂的技术条件
外观
使用干膜时,首先应进行外观检查。质量好的干膜必须无气泡、颗粒、杂质;抗蚀膜厚度均匀;颜色均匀一致;无胶层流动。如果干膜存在上述要求中的缺陷,就会增加图像转移后的修版量,严重者根本无法使用。膜卷必须卷绕紧密、整齐,层间对准误差应小于1mm,这是为了防止在贴膜时因卷绕误差而弄脏热压辊,也不会因卷绕不紧而出现连续贴膜的故障。聚酯薄膜应尽可能薄,聚酯膜太厚会造成曝光时光线严重散射,而使图像失真,降低干膜分辨率。聚酯薄膜必须透明度高,否则会增加曝光时间。聚乙烯保护膜厚度应均匀,如厚度不均匀将造成光致抗蚀层胶层流动,严重影响干膜的质量。干膜外观具体技术指标如表7—1所述:
◎其它性能
在生产操作过程中为避免漏曝光和重曝光,干膜在曝光前后颜色应有明显的变化,这就是干膜的变色性能。当使用于膜作为掩孔蚀刻时,要求干膜具有足够的柔韧性,以能够承受显影过程、蚀刻过程液体压力的冲击而不破裂,这就是干膜的掩蔽性能。
◎光谱特性
在紫外——可见光自动记录分光光度计上制作光谱吸收曲线(揭去聚乙烯保护膜,以聚酯薄膜作参比,光谱波长为横坐标,吸收率即光密度D作纵坐标),确定光谱吸收区域波长及安全光区域。技术要求规定,干膜光谱吸收区域波长为310~440毫微M(nm),安全光区域波长为≥460毫微M(nm)。
高压汞灯及卤化物灯在近紫外区附近辐射强度较大,均可作为干膜曝光的光源。低压钠灯主要幅射能量在波长为589.0~589.6nm的范围,且单色性好,所发出的黄光对人眼睛较敏感、明亮,便于操作。故可选用低压钠灯作为干膜操作的安全光。
光化学、干膜、曝光及显影制程
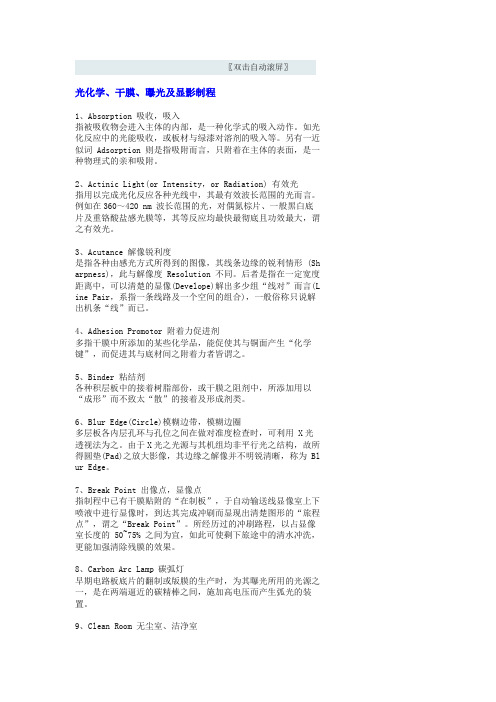
〖双击自动滚屏〗光化学、干膜、曝光及显影制程1、Absorption 吸收,吸入指被吸收物会进入主体的内部,是一种化学式的吸入动作。
如光化反应中的光能吸收,或板材与绿漆对溶剂的吸入等。
另有一近似词 Adsorption 则是指吸附而言,只附着在主体的表面,是一种物理式的亲和吸附。
2、Actinic Light(or Intensity,or Radiation) 有效光指用以完成光化反应各种光线中,其最有效波长范围的光而言。
例如在360~420 nm 波长范围的光,对偶氮棕片、一般黑白底片及重铬酸盐感光膜等,其等反应均最快最彻底且功效最大,谓之有效光。
3、Acutance 解像锐利度是指各种由感光方式所得到的图像,其线条边缘的锐利情形 (Sh arpness),此与解像度 Resolution 不同。
后者是指在一定宽度距离中,可以清楚的显像(Develope)解出多少组“线对”而言(L ine Pair,系指一条线路及一个空间的组合),一般俗称只说解出机条“线”而已。
4、Adhesion Promotor 附着力促进剂多指干膜中所添加的某些化学品,能促使其与铜面产生“化学键”,而促进其与底材间之附着力者皆谓之。
5、Binder 粘结剂各种积层板中的接着树脂部份,或干膜之阻剂中,所添加用以“成形”而不致太“散”的接着及形成剂类。
6、Blur Edge(Circle)模糊边带,模糊边圈多层板各内层孔环与孔位之间在做对准度检查时,可利用 X光透视法为之。
由于X光之光源与其机组均非平行光之结构,故所得圆垫(Pad)之放大影像,其边缘之解像并不明锐清晰,称为 Bl ur Edge。
7、Break Point 出像点,显像点指制程中已有干膜贴附的“在制板”,于自动输送线显像室上下喷液中进行显像时,到达其完成冲刷而显现出清楚图形的“旅程点”,谓之“Break Point”。
所经历过的冲刷路程,以占显像室长度的 50~75% 之间为宜,如此可使剩下旅途中的清水冲洗,更能加强清除残膜的效果。
干膜生产工艺

干膜生产工艺干膜生产工艺是一种在电子工业中广泛应用的技术,用于制作薄膜电路板和其他电子产品。
下面是一个关于干膜生产工艺的700字的介绍。
干膜生产工艺是一种先进的制造技术,它可以用于制作高品质的电路板。
干膜是一种特殊的光敏胶片,它可以与印刷电路板表面紧密结合,在光的作用下形成图形。
与传统的湿膜工艺相比,干膜工艺具有更高的精度和稳定性。
干膜生产工艺的主要步骤包括准备基板、涂敷干膜、曝光、显影、蚀刻和清洗。
首先,需要准备好需要制作电路的基板。
基板的材料可以是FR4、铜或其他导电材料。
然后,在基板表面涂敷一层干膜。
干膜有多种类型,可以根据需要选择不同的干膜来实现不同的功能。
涂敷干膜后,需要将其暴露在紫外光下,以形成所需的电路图案。
曝光的过程中,光线会通过掩膜上的图案,然后照射到干膜上。
只有暴露在光下的部分会发生化学反应,形成稳定的图案结构。
完成曝光后,接下来是显影的步骤。
显影是指将不需要的部分从干膜上去除的过程。
显影液会分解暴露在光下的部分干膜,使其变得可溶于溶剂。
而未暴露在光下的部分干膜则保持不变。
通过显影,可以形成所需的电路图案。
在显影完成后,接下来是蚀刻的步骤。
蚀刻是指将基板表面的铜或其他导电材料去除,从而形成所需的电路图案。
蚀刻液会溶解掉没有被干膜保护的铜层,使电路图案明确可见。
最后一步是清洗。
清洗的目的是去除干膜残留物和其他杂质,以保证电路板的质量和可靠性。
清洗过程通常使用酒精或其他溶剂进行。
干膜生产工艺具有许多优点。
首先,它可以实现高精度的电路图案,使电路板具有更好的性能和可靠性。
其次,与传统的湿膜工艺相比,干膜工艺更加环保,能够节约更多的水资源和能源。
此外,干膜工艺操作简单,工艺周期短,能够大大提高生产效率。
总之,干膜生产工艺是一种先进的制造技术,适用于电子行业中的薄膜电路板制造。
它具有高精度、稳定性和环保等优点,能够提高电路板的性能和可靠性,同时还能提高生产效率。
随着电子行业的快速发展,干膜生产工艺将继续在电子制造领域发挥重要作用。
干膜介绍及干膜工艺详解

干膜介绍及干膜工艺详解干膜是一种常用的覆盖材料,用于保护电子元件表面免受污染、腐蚀和机械损伤。
它由聚酰胺树脂制成,具有优异的耐温性、耐化学性和机械强度。
干膜广泛应用于电子工业、半导体制造业、汽车制造业等领域。
本文将详细介绍干膜的工艺及应用。
干膜工艺主要分为涂布、曝光、显影和固化四个步骤。
首先,将干膜涂布在待保护的基板表面,然后通过热压或UV曝光使干膜与基板紧密结合。
曝光是将覆盖了光掩膜的基板和干膜放置在紫外线曝光机中,通过控制曝光时间和光强来实现显影效果。
显影是将经过曝光的基板和干膜放入化学液中,使未曝光部分的干膜溶解,从而揭露出基板的表面。
最后,通过热固化或UV固化使干膜与基板牢固结合,形成保护层。
干膜具有许多优越的特性。
首先,干膜具有出色的耐化学性,能够抵抗酸、碱和溶剂的侵蚀,保护电子元件不受腐蚀。
其次,干膜具有良好的耐温性,能够在高温环境下保持稳定性,适用于高温焊接和其他高温工艺。
此外,干膜具有优秀的机械强度,能够抵御机械冲击和摩擦,确保元件表面的完整性。
最重要的是,干膜具有良好的电绝缘性能,能够有效隔离电子元件,保证电路的正常运行。
干膜广泛应用于各种电子元件的保护和焊接过程中。
在印制电路板(PCB)制造过程中,干膜可以作为覆盖材料,保护线路图案在酸碱腐蚀、高温焊接和表面处理中不受损坏。
在集成电路制造中,干膜可用作衬底保护层,保护器件免受机械和化学损伤。
此外,干膜还可以用于电子元件的封装和封装,提高元件的可靠性和稳定性。
总之,干膜作为一种常用的保护材料,具有优越的性能和广泛的应用领域。
通过涂布、曝光、显影和固化等工艺步骤,可以将干膜均匀附着在基板表面,形成坚固耐用的保护层。
干膜能够有效保护电子元件免受污染、腐蚀和机械损伤,提高元件的可靠性和稳定性。
在电子工业、半导体制造业和汽车制造业等领域发挥着重要作用。
干膜作为一种常用的保护材料,具有许多优越的特性,因此在各个领域得到广泛应用。
下面将进一步介绍干膜的应用以及其在电子工业、半导体制造业和汽车制造业中的具体应用。
干膜工艺流程

干膜工艺流程干膜工艺是一种常用于半导体和电子元件制造过程中的一项关键工艺。
它能够有效地保护电路板表面,并在保护过程中提供高质量的光刻图案传输。
本文将详细描述干膜工艺的流程,包括准备工作、涂敷干膜、曝光、显影、烘干和剥离等步骤。
一、准备工作1. 确定干膜工艺的适用性和要求:在开始干膜工艺之前,需要评估电路板的设计和制造需求,以确保干膜工艺能够满足这些需求。
2. 准备所需材料和设备:包括干膜材料、涂敷设备、曝光设备、显影设备、烘干设备和剥离设备等。
二、涂敷干膜1. 清洁电路板表面:使用适当的清洁剂和清洁方法清洁电路板表面,以去除灰尘、污垢和油脂等杂质。
2. 涂敷干膜:将干膜材料倒入涂敷设备中,并按照设备操作手册的指示,使用涂敷设备将干膜均匀地涂敷在电路板表面上。
3. 干燥干膜:将涂敷完成的电路板放置在烘干设备中,根据干膜材料的要求,控制烘干温度和时间,使干膜完全干燥。
1. 准备光刻模板:根据电路板设计,准备好相应的光刻模板。
光刻模板包括了所需的光刻图案,能够对干膜进行曝光和显影。
2. 曝光干膜:使用曝光设备,将准备好的光刻模板对准涂敷好干膜的电路板,并进行曝光。
曝光的时间和强度应根据干膜材料和制造需求进行调整和控制。
1. 准备显影液:根据干膜材料的要求,准备好适当的显影液。
显影液用于去除未曝光部分的干膜,使光刻图案显现出来。
2. 进行显影:将电路板浸入显影液中,根据显影液的要求,控制显影时间和温度,使干膜上未曝光的部分被显影液溶解。
五、烘干和剥离1. 烘干:经过显影后的电路板需要用烘干设备进行烘干,以去除显影液残留和使电路板表面完全干燥。
2. 剥离:将烘干后的电路板放入剥离设备中,通过剥离设备的力和温度控制,剥离干膜并使其与电路板分离。
剥离后,电路板的光刻图案得以完整保留,并可用于后续加工和制造。
干膜工艺是一项使用干膜材料在电路板制造过程中保护电路板表面和传递光刻图案的关键工艺。
其流程包括准备工作、涂敷干膜、曝光、显影、烘干和剥离等步骤。
光化学、干膜、曝光及显影制程
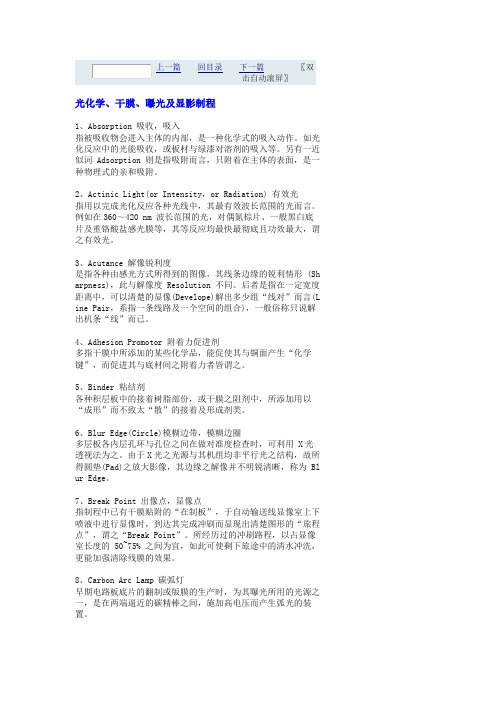
上一篇回目录下一篇〖双击自动滚屏〗光化学、干膜、曝光及显影制程1、Absorption 吸收,吸入指被吸收物会进入主体的内部,是一种化学式的吸入动作。
如光化反应中的光能吸收,或板材与绿漆对溶剂的吸入等。
另有一近似词 Adsorption 则是指吸附而言,只附着在主体的表面,是一种物理式的亲和吸附。
2、Actinic Light(or Intensity,or Radiation) 有效光指用以完成光化反应各种光线中,其最有效波长范围的光而言。
例如在360~420 nm 波长范围的光,对偶氮棕片、一般黑白底片及重铬酸盐感光膜等,其等反应均最快最彻底且功效最大,谓之有效光。
3、Acutance 解像锐利度是指各种由感光方式所得到的图像,其线条边缘的锐利情形 (Sh arpness),此与解像度 Resolution 不同。
后者是指在一定宽度距离中,可以清楚的显像(Develope)解出多少组“线对”而言(L ine Pair,系指一条线路及一个空间的组合),一般俗称只说解出机条“线”而已。
4、Adhesion Promotor 附着力促进剂多指干膜中所添加的某些化学品,能促使其与铜面产生“化学键”,而促进其与底材间之附着力者皆谓之。
5、Binder 粘结剂各种积层板中的接着树脂部份,或干膜之阻剂中,所添加用以“成形”而不致太“散”的接着及形成剂类。
6、Blur Edge(Circle)模糊边带,模糊边圈多层板各内层孔环与孔位之间在做对准度检查时,可利用 X光透视法为之。
由于X光之光源与其机组均非平行光之结构,故所得圆垫(Pad)之放大影像,其边缘之解像并不明锐清晰,称为 Bl ur Edge。
7、Break Point 出像点,显像点指制程中已有干膜贴附的“在制板”,于自动输送线显像室上下喷液中进行显像时,到达其完成冲刷而显现出清楚图形的“旅程点”,谓之“Break Point”。
所经历过的冲刷路程,以占显像室长度的 50~75% 之间为宜,如此可使剩下旅途中的清水冲洗,更能加强清除残膜的效果。
底片干膜工艺技术资料

感谢您的观看
汇报人:
底片的质量检测:检查底片是否符合工艺要求,包括曝光、显影、定影等环节
底片的清洁处理:使用专业的清洁剂和工具对底片进行清洁,去除表面的污渍和尘埃
底片的烘干处理:将清洁后的底片进行烘干,以避免潮湿对底片的影响 底片的存储与保管:将烘干后的底片按照规定的方式进行存储和保管,以避免损坏和污染
底片干膜工艺参数 与控制
添加标题
添加标题
添加标题
添加标题
平整度要求:确保底片表面平整, 无气泡、皱褶等缺陷
底片张力与平整度的检测方法:通 过观察、测量等方法对底片进行检 查,确保符合工艺要求
温度控制:确保底片干膜在适宜的温度下进行固化 压力控制:通过调整压力,确保底片干膜与基材紧密贴合 时间控制:确定底片干膜的固化时间,确保其完全固化 设备维护:定期对设备进行检查和维护,确保工艺参数的稳定性和准确性
干膜的组成:由聚合物、感 光剂和溶剂等组成
干膜的固化程度:可以通过控 制曝光时间和光源波长来调节
干膜的固化特点:具有较高 的耐热性和耐化学腐蚀性
底片表面处理:底片表面进行粗化处理,使其表面不平整,增加附着力 干膜材料:采用高分子材料,具有较好的粘附性和化学稳定性 附着原理:干膜与底片之间通过化学键合、物理吸附等作用力产生附着 烘烤固化:在高温下进行烘烤,使干膜固化附着在底片表面
形项正文
其他领域
此处输入你的智能图 形项正文
案例一:某电子制 造公司的应用
案例二:某汽车零 部件公司的应用
案例三:某航空航 天公司的应用
案例四:某医疗设 备公司的应用
案例一:某公司采用底片干膜 工艺提高产品质量
案例二:某工厂利用底片干膜 工艺降低生产成本
案例三:某项目采用底片干膜 工艺解决技术难题
干膜曝光工艺(一)
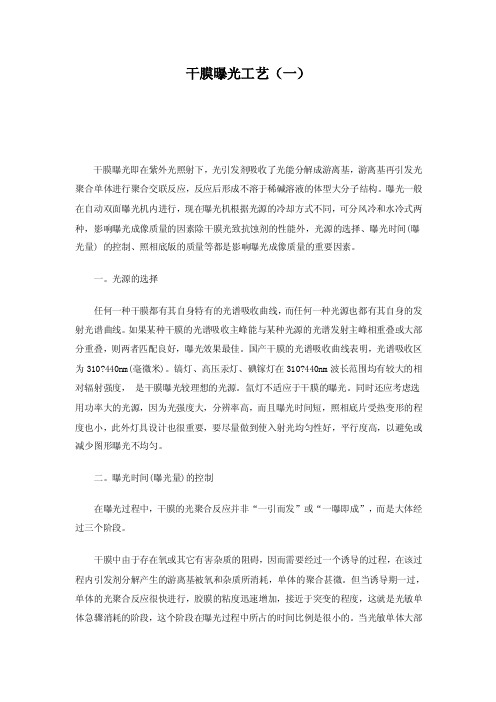
干膜曝光工艺(一)干膜曝光即在紫外光照射下,光引发剂吸收了光能分解成游离基,游离基再引发光聚合单体进行聚合交联反应,反应后形成不溶于稀碱溶液的体型大分子结构。
曝光一般在自动双面曝光机内进行,现在曝光机根据光源的冷却方式不同,可分风冷和水冷式两种,影响曝光成像质量的因素除干膜光致抗蚀剂的性能外,光源的选择、曝光时间(曝光量) 的控制、照相底版的质量等都是影响曝光成像质量的重要因素。
一。
光源的选择任何一种干膜都有其自身特有的光谱吸收曲线,而任何一种光源也都有其自身的发射光谱曲线。
如果某种干膜的光谱吸收主峰能与某种光源的光谱发射主峰相重叠或大部分重叠,则两者匹配良好,曝光效果最佳。
国产干膜的光谱吸收曲线表明,光谱吸收区为310?440nm(毫微米)。
镐灯、高压汞灯、碘镓灯在310?440nm波长范围均有较大的相对辐射强度,是干膜曝光较理想的光源。
氙灯不适应于干膜的曝光。
同时还应考虑选用功率大的光源,因为光强度大,分辨率高,而且曝光时间短,照相底片受热变形的程度也小,此外灯具设计也很重要,要尽量做到使入射光均匀性好,平行度高,以避免或减少图形曝光不均匀。
二。
曝光时间(曝光量)的控制在曝光过程中,干膜的光聚合反应并非“一引而发”或“一曝即成”,而是大体经过三个阶段。
干膜中由于存在氧或其它有害杂质的阻碍,因而需要经过一个诱导的过程,在该过程内引发剂分解产生的游离基被氧和杂质所消耗,单体的聚合甚微。
但当诱导期一过,单体的光聚合反应很快进行,胶膜的粘度迅速增加,接近于突变的程度,这就是光敏单体急骤消耗的阶段,这个阶段在曝光过程中所占的时间比例是很小的。
当光敏单体大部分消耗完时,就进入了单体耗尽区,此时光聚合反应已经完成。
该过程类似于原子弹爆炸的过程。
正确控制曝光时间是得到优良的干膜抗蚀图像非常重要的因素。
当曝光不足时,由于单体聚合的不彻底,在显影过程中,胶膜溶涨变软,线条不清晰,色泽暗淡,甚至脱胶,在电镀前处理或电镀过程中,膜起翘、渗镀、甚至脱落。
干膜线路
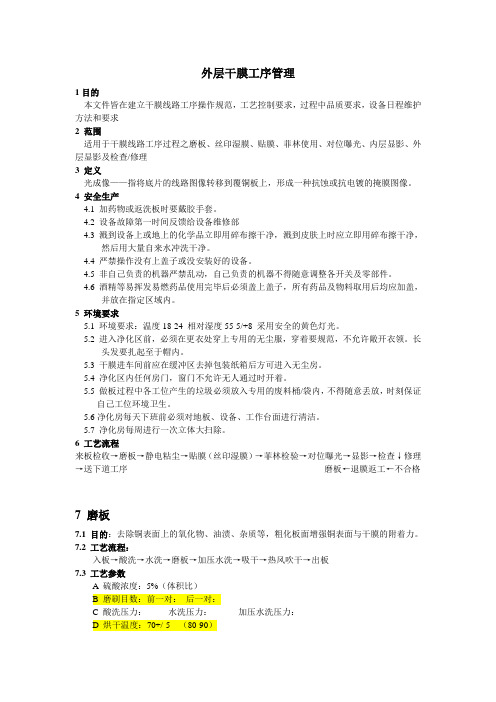
外层干膜工序管理1目的本文件皆在建立干膜线路工序操作规范,工艺控制要求,过程中品质要求,设备日程维护方法和要求2 范围适用于干膜线路工序过程之磨板、丝印湿膜、贴膜、菲林使用、对位曝光、内层显影、外层显影及检查/修理3 定义光成像——指将底片的线路图像转移到覆铜板上,形成一种抗蚀或抗电镀的掩膜图像。
4 安全生产4.1 加药物或返洗板时要戴胶手套。
4.2 设备故障第一时间反馈给设备维修部4.3 溅到设备上或地上的化学品立即用碎布擦干净,溅到皮肤上时应立即用碎布擦干净,然后用大量自来水冲洗干净。
4.4 严禁操作没有上盖子或没安装好的设备。
4.5 非自己负责的机器严禁乱动,自己负责的机器不得随意调整各开关及零部件。
4.6 酒精等易挥发易燃药品使用完毕后必须盖上盖子,所有药品及物料取用后均应加盖,并放在指定区域内。
5 环境要求5.1 环境要求:温度18-24 相对湿度55-5/+8 采用安全的黄色灯光。
5.2 进入净化区前,必须在更衣处穿上专用的无尘服,穿着要规范,不允许敞开衣领。
长头发要扎起至于帽内。
5.3 干膜进车间前应在缓冲区去掉包装纸箱后方可进入无尘房。
5.4 净化区内任何房门,窗门不允许无人通过时开着。
5.5 做板过程中各工位产生的垃圾必须放入专用的废料桶/袋内,不得随意丢放,时刻保证自己工位环境卫生。
5.6净化房每天下班前必须对地板、设备、工作台面进行清洁。
5.7 净化房每周进行一次立体大扫除。
6 工艺流程来板检收→磨板→静电粘尘→贴膜(丝印湿膜)→菲林检验→对位曝光→显影→检查↓修理→送下道工序磨板←退膜返工←不合格7 磨板7.1 目的:去除铜表面上的氧化物、油渍、杂质等,粗化板面增强铜表面与干膜的附着力。
7.2 工艺流程:入板→酸洗→水洗→磨板→加压水洗→吸干→热风吹干→出板7.3 工艺参数A硫酸浓度:5%(体积比)B 磨刷目数:前一对:后一对:C 酸洗压力:水洗压力:加压水洗压力:D 烘干温度:70+/-5 (80-90)E 磨刷电流:1.8-2.4AF 磨刷速度:7.4 酸缸配制:(L)7.4.1 先放掉旧酸液,同时清洗缸内残渣,并排放干净。
PCB光成像工艺知识

影响贴膜效果的主要因素——温度
a.贴膜温度是指干膜与板面铜箔介面的实际 温度,(生产上常以压辘温度作参考)。
b.贴膜温度决定于压辘与干膜接触时间, (贴膜时间)。
c.压辘温度预热温度介于压辘和光阻铜箔介面 的热导系数。
影响贴膜效果的主要因素——压膜时间
a. 压膜时间是指滚轮与干膜接触点的时间。 b.压膜时间由贴膜压力(实际是压痕宽度)与
贴膜辘的压力及外形对良率的影响
辘压力(bar) 普通压辘的缺陷率 凸面压辘的缺陷率
4
1%
0.15%
7
0.18%
0.05%
四、曝光
曝光是指UV光线穿过菲林及保护膜,而 到达感光膜体上,使进行一连串的光聚 合反应,形成不溶于显影液聚合物。
流程图
紫外光照射
单体吸收自由基 出现自由基 启始剂裂解
单体发生光聚反应形成聚合体
显影
聚合过程
光源
点光源
点光源
ORC手动曝光机
1、由于曝光框架两层各为麦拉层和玻 璃层,因此上下曝光的能量各不相同。 2、设备通过对灯罩的开合控制曝光时 间的多少。 3、灯罩有冷却水,冷却水在保养时需 要更换。 4、离子罐需要检查,无吸附能力时, 需要更换。 5、反光罩对能量的均匀性有比较大影 响,通常通过调整反光罩的位置来调整 能量均匀性。
平行光源
平行光源就是将由点光源发出的光经过抛物面反射通过移动反射镜来达到上下两面的先后 曝光。平行光的最大优点是在曝光时,所有光线是垂直照射到光致抗蚀剂上,因而可以得 到与底片“相同”的尺寸图形(显影后),得到较理想的图形。
平行光源
1、平行光机保养时,清洁反光罩上面的灰尘,通常使用掸子 掸落灰尘,再用吸尘器吸附。 2、检查过滤器有无堵塞。
感光干膜工艺详解
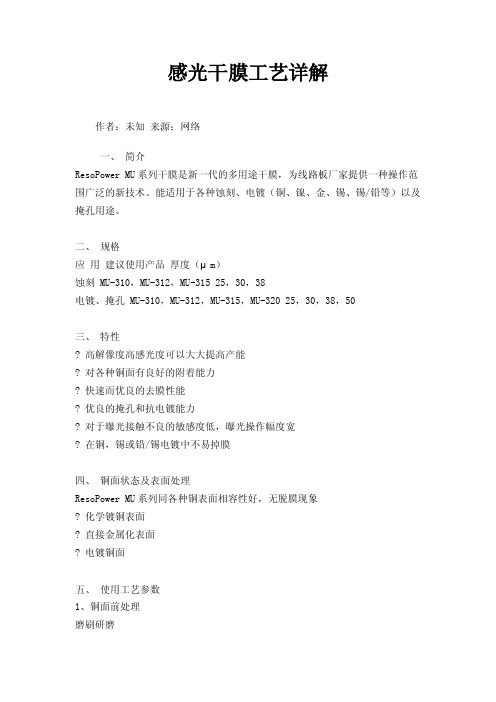
感光干膜工艺详解作者:未知来源:网络一、简介ResoPower MU系列干膜是新一代的多用途干膜,为线路板厂家提供一种操作范围广泛的新技术。
能适用于各种蚀刻、电镀(铜、镍、金、锡、锡/铅等)以及掩孔用途。
二、规格应用建议使用产品厚度(μm)蚀刻 MU-310,MU-312,MU-315 25,30,38电镀、掩孔 MU-310,MU-312,MU-315,MU-320 25,30,38,50三、特性高解像度高感光度可以大大提高产能对各种铜面有良好的附着能力快速而优良的去膜性能优良的掩孔和抗电镀能力对于曝光接触不良的敏感度低,曝光操作幅度宽在铜,锡或铅/锡电镀中不易掉膜四、铜面状态及表面处理ResoPower MU系列同各种铜表面相容性好,无脱膜现象化学镀铜表面直接金属化表面电镀铜面五、使用工艺参数1、铜面前处理磨刷研磨2、贴膜推荐贴膜参数如下表:手动贴膜机自动贴膜机预热(℃)视情况定视情况定压合温度(℃) 50-80压辘温度(℃) 110-130 110-130贴膜压力(PSI) 60-80 60-80贴膜速度(m/min) 0.6-1.5 1.5-3.0压合时间(Sec) 1-4板出温度内层板:60-70℃;外层板:45-55℃(镀铜/锡);50-65℃(镀金)建议:温度达到110℃以上后开始贴膜为减少孔破,可以适当减低压膜温度和压力贴膜前孔内应无水分或水气贴膜后的板冷却至室温后,再曝光3、静置时间:30min(15min以上)4、曝光ResoPower MU系列产品可在各种曝光机上进行曝光,灯管的波长值应分布在350-380nm推荐使用曝光参数(PSI)MU310 MU312 MU315 MU320SST(21) 7-10 7-10 7-10 7-10mJ/cm2 30-100 30-100 35-100 40-1005、静置时间:30min(15min以上)6、显影ResoPower MU系列干膜可以在Na2CO3 、K2CO3中显影,显影范围宽。
干膜介绍及干膜工艺详解(40页)
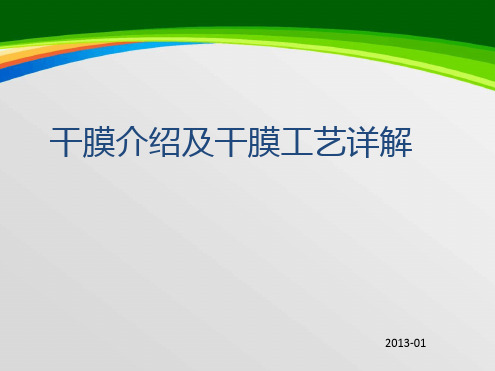
CO OH C OO H
C OOH
C OO H C OO H
CO OH
聚合体主链 起始剂
C OO H COO H
C OO H
Na2CO3/H2O 显影 (乳化)
Na+ CO O-
H2O
Na+
N a+
Rー COOH + Na 2 CO3 H2O R- COO- Na +
+ NaHCO 3
基本工艺要求
显影的作用: 将未曝光部分的干膜去掉,留下感光的部分。
显影的原理: 未曝光部分的感光材料没有发生聚合反应,遇
弱碱Na2CO3(0.8-1.2%) 或K2CO3溶解。而聚合的 感光材料则留在板面上,保护下面的铜面不被蚀刻 药水溶解。
?SES 工艺流程详细介绍
显影反应机理
显影
单体
CO OH CO OH
?SES 工艺流程详细介绍
贴膜:
? 贴膜的作用:是将干膜贴在粗化的铜面上。 ? 贴膜机将干膜通过热压辘与铜面附着,同时撕掉
PE膜。
基本工艺要求
? 贴膜
预热段温度
:80~100 ℃
贴膜前板面温度 :40~60℃
压辘设定温度 :110~120℃
压膜时压辘温度 :100~115 ℃
贴膜压力
:3.0~5.0kgf/cm 2
电镀铜+锡/锡铅:
电镀的作用: 将我们所需要的图形处的铜层进行加
厚,并且在铜面上镀上一层抗蚀刻层(即 锡或锡铅)。
基本工艺要求
? 电镀铜+锡或锡铅
以电镀供应商工艺要求为准。
?SES 工艺流程详细介绍
去膜:
去膜的作用:
通过强碱溶液(一般为NaOH溶液, 浓度为2-3%)将覆盖在铜面上抗电镀的干 膜去掉。
- 1、下载文档前请自行甄别文档内容的完整性,平台不提供额外的编辑、内容补充、找答案等附加服务。
- 2、"仅部分预览"的文档,不可在线预览部分如存在完整性等问题,可反馈申请退款(可完整预览的文档不适用该条件!)。
- 3、如文档侵犯您的权益,请联系客服反馈,我们会尽快为您处理(人工客服工作时间:9:00-18:30)。
个磨板系统是否正常,磨出来的板是否干燥洁净,有无污渍、水迹、氧化点,合格后方
可批量生产。
5.6.2 接板员工将检查合格的板先插架放置 3-6min,再叠板放置(0.6mm 以下的薄板可直接
叠板放置),为了防止板子放置时间太长、板面氧化导致贴膜不牢,原则上要求现磨现贴,
但积板数量不许超过 100 块且存板时间不可超过一小时。否则需重新磨板。
迹、氧化点。 5.5.2 磨痕试验:
取一块未经钻孔或已钻孔但未作图形的且与生产板同厚度的覆铜板作试板。 5.5.2.1 打开输送→放板入上(下)刷位置→关闭输送→调动磨刷进给压力到设定值→打
开上(下)刷喷啉并磨板 8-10 秒→关闭磨刷→打开输送→取出试板。 5.5.2.2 将板子传送出来,检查上(下)刷的磨痕是否均匀,宽度在 10-15mm 之间,过窄
干膜光成像工艺规范
目录
1.目的---------------------------------------------------------------------------------4 2.范围---------------------------------------------------------------------------------4 3.定义---------------------------------------------------------------------------------4 4.操作方法-------------------------------------------------------------------------4-5 5.磨板-------------------------------------------------------------------------------6-9 6.贴膜------------------------------------------------------------------------------9-11 7.曝光-----------------------------------------------------------------------------11-13 8.显影-----------------------------------------------------------------------------13-17 9.检查-----------------------------------------------------------------------------17-18 10. 故障与排除---------------------------------------------------------------------18-19
6.4 工艺条件: 6.4.1 压辘(上/下)温度:100-120℃,最佳范围:110±5℃ 6.4.2 气压:40-55psi
一般金板:45-50psi,喷锡板:40-50psi 6.4.3 速度:1.0-1.5m/min,最佳 1.1-1.3m/min。
一般大压辘机 2.0-2.7 格,最佳 2.5 格,小压辘机 4.5-6 格,最佳 5 格,用秒表测出一 块已知长度的板经过压辘所需的时间再用已知长度(m)与所需时间(min)的比值即为 速度。 6.4.4 贴膜出板表面温度:40-65℃,最佳 50±5℃
用电子测温仪,检测烘 烘干温度表
干段温度通知维修
显示温度,设定温度实际温度偏差±5℃
空气过滤网
用吸尘器吸 有灰尘的一面
空气滤网上
无明显的灰尘
5.8.3 月保养:除日保养、周保养以外,由维修负责人负责安排人员每月月底进行一次大保
养。
a.将各输送轮、压轮、吸水辊、过滤网、风刀、喷管、喷咀,拆出进行全面保养,整机
入板→稀硫酸洗→循环水洗→水洗→ 磨刷(1 对 320 目)→ 磨刷(1 对 500 目)→中
压水洗→水洗→挤干→吹干→烘干→出板。
5.3 工艺条件 控制项目
输送速度
磨刷压力 硫酸浓度
控制范围
最佳范围
内层:2.0-3.0m/min 铅 锡 板 : 1.8-3.0m/min 金板:1.6-2.0m/min
(一般用接触式电子测温仪轻轻接触板面即可测得) 6.5 操作规程
6.5.1 开机:依次打开下列开关 总电源开关→压辘加热开关→压辘气压开关→输送开关
6.5.2 打开机后先预热 15min 左右。 6.5.3 戴指套对板面进行检查,必须保证压膜前的板面干燥清洁无氧化、无污渍、磨痕均匀。 6.5.4 待机器进入正常待压干膜状态,将板子平放在上、下两压辘的输送口间,后试压膜一
5.7 注意事项:
5.7.1 取硫酸时,需戴手套,用吸管吸取,以免发生意外。
5.7.2 为防止磨板时叠板,放板时要求板与板的间距约 10mm。
5.8 维护与保养
5.8.1 日保养
检查项目 维护方式
工艺要求
保养周期
药缸、 水洗缸
清洗更换
缸内液体清澈 液位达标
1 次/班
过滤网 清水冲洗 无堵孔、垃圾
1 次/班
则顺时针方向旋转调压手柄调大进给压力,过宽则逆时针方向旋转调压手柄减少进给压 力,直到磨痕宽度在要求范围内,同时查相应的电表头指示值是否正确,并要求工作员 工在试板上作记录(时间、板子厚度、磨刷压力,磨痕宽度)。 5.5.3 水膜破裂试验
将刚磨出来的板,浸入干净的水中,然后取出竖直放置,若水膜能保持 15 秒以上,说 明此板合格,否则重新调试直到符合要求为止。 5.6 安全生产 5.6.1 当调整好磨板各参数后,先做磨痕试验和水膜破裂试验,然后试刷 3-5 块板,检查整
4.3 主要物品
干膜 重氮片 重氮片保护膜 氨水
名称
酒精 浓硫酸 碳酸钠 消泡剂
4.4 制程能力
项目
尺寸(mm)
板尺寸
610×460
干膜隔离环
0.13
外层线宽/线间距
0.10
干膜盖孔能力
6.5
对位精度
±0.05
4.5 工艺流程图
4.5.1 双面板制作过程
备注 Max Min Min Max Min
来板检查→磨板→贴膜 →停留 15min→对位→曝光→停留 15min→显影→检查修正→
触,如果化学溶液溅到皮肤上,需立即用自来水进行冲洗, 并报告班。 4.1.2 溅到地上的化学药品须立即擦净。 4.1.3 操作时不要观看紫外光源。 4.1.4 不要操作没上盖子和没安装固定好的机器。
4.1.5 酒精、丙酮等易燃品使用完后应盖好盖子。
4.2 主要设备
机械磨板机 贴膜机
设备名称
双面曝光机 显影机
5.6.3 为了防止磨刷不均匀磨损成腰鼓形,批量磨板时,放板要左右均匀放置,通常每个月
用 80 目砂纸将磨刷整平一次。
5.6.4 磨刷使用寿命
每道磨刷通过板子的长度累积达 4 万至 5 万米,要求更换该道磨刷,并作相关的运行记录。
5.6.5 吸水辊应以清水充分润湿,不许让吸水辊干燥工作,一般要求 2 个月换一次吸水辊。
致或略小于板宽 4-6mm 最佳,但单边露铜不能超过 5mm。 6.5.8.2 关掉转动开关,去掉剩的旧干膜(不允许超过三英尺即 91.5cm)。 6.5.8.3 用刮胶擦或酒精擦洗压辘上的干膜碎等杂物。 6.5.8.4 装上新干膜,将上、下两卷干膜对齐调试合格后方可生产。 6.5.8.5 换干膜后的左视图如下:
内层:2.8m/min 铅锡板:2.5m/min(其中有长条孔 的锡板速度为 1.5-2.0m/min) 金板:1.8m/min
1.5-3.0A
1.5-2.0A
1%-3%
2%
烘干温度
60-90℃
硫酸喷淋压力
10-28psi
水洗喷淋压力
10-28psi
磨痕宽度
10-15mm
水膜破裂时间
水膜保持 15 秒以上
裤脚,防静电服只能在指定范围内穿着,并要保持整洁。 4.6.5 风淋门不允许开着或半掩着,不允许两道门同时是开启状态,否则有过量的灰尘和污
物进入,不许将有灰尘的物品(如纸箱)带入工作区域内。风淋门前面的过道每天必须 进行清洁。 4.6.6 除了对位、曝光人员不戴手套取放板子外,工序的其它工位(磨板、贴膜、显影、检 板)取放、接收板子的人员一律要戴洁净干燥的白细纱手套取放板子,磨板接板贴膜放 板人员戴指套操作。并要做到轻拿轻放,手指不得触及线路图形,板角不得碰伤其它板 的铜面或干膜线路。 5. 磨板 5.1 目的:保证贴膜前的板面干燥清洁无氧化、胶渍等污物。 5.1.1 物料:硫酸(工业)、尼龙磨刷(第 1 对为 320 目,第 2 对为 500 目)。 5.1.2 工具:吸管、胶手套、无毛白纱手套。 5.2 工序流程:
块。 6.5.5 检查试压膜的板,若板面无气泡、无起皱、无干膜碎、无流胶、颜色均匀,且单边露
铜不大于 3-5mm,则可批量生产。 6.5.6 贴膜合格的板不允许平叠,要求先插架冷却之后,再竖直叠板放置于专用架子上,静
置 15min 后再转下工序。 6.5.7 关机:依开机的相反顺序进行。 6.5.8 换干膜: 6.5.8.1 根据所要生产的板来选择对应尺寸的干膜,一般生产板的大小和干膜大小基本一
平行,同时磨刷处之喷淋必须均匀喷在磨刷上。
e.保养完毕、安装后要先试运转,试磨一块废板,合格后方可生产。
6. 贴膜
6.1 目的:通过热压方式将干膜抗蚀剂贴附在清洁的铜面上。
6.2 工具:介膜刀片、刮胶擦、框架。
6.2.1 物料:干膜、无毛白纱手套、指套、压辘。
6.3 流程: 插架
来料检查→压膜→介膜———→静置
检查清理喷咀 无堵塞,喷出水 各喷咀
内异物或更换 形为圆锥形