8D是解决问题的8条基本准则
8D与六西格玛区别
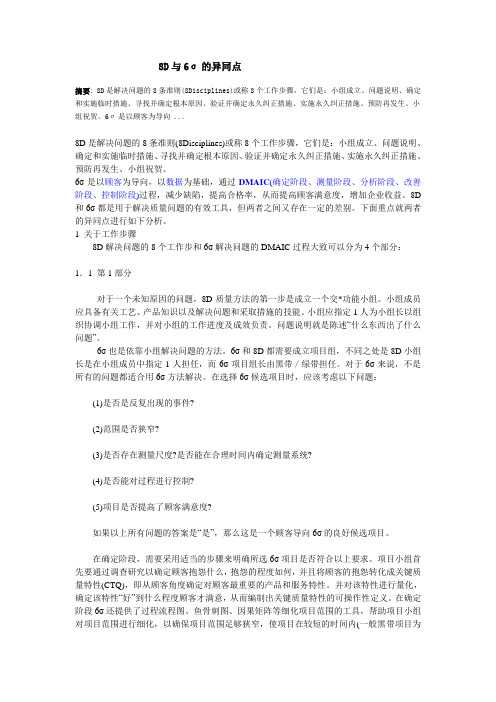
8D与6σ的异同点摘要: 8D是解决问题的8条准则(8Disciplines)或称8个工作步骤,它们是:小组成立、问题说明、确定和实施临时措施、寻找并确定根本原因、验证并确定永久纠正措施、实施永久纠正措施、预防再发生、小组祝贺。
6σ是以顾客为导向 ...8D是解决问题的8条准则(8Disciplines)或称8个工作步骤,它们是:小组成立、问题说明、确定和实施临时措施、寻找并确定根本原因、验证并确定永久纠正措施、实施永久纠正措施、预防再发生、小组祝贺。
6σ是以顾客为导向,以数据为基础,通过DMAIC(确定阶段、测量阶段、分析阶段、改善阶段、控制阶段)过程,减少缺陷,提高合格率,从而提高顾客满意度,增加企业收益。
8D 和6σ都是用于解决质量问题的有效工具,但两者之间又存在一定的差别。
下面重点就两者的异同点进行如下分析。
1 关于工作步骤8D解决问题的8个工作步和6σ解决问题的DMAIC过程大致可以分为4个部分:1.1 第1部分对于一个未知原因的问题,8D质量方法的第一步是成立一个交*功能小组。
小组成员应具备有关工艺、产品知识以及解决问题和采取措施的技能。
小组应指定1人为小组长以组织协调小组工作,并对小组的工作进度及成效负责。
问题说明就是陈述“什么东西出了什么问题”。
6σ也是依靠小组解决问题的方法。
6σ和8D都需要成立项目组,不同之处是8D小组长是在小组成员中指定1人担任,而6σ项目组长由黑带/绿带担任。
对于6σ来说,不是所有的问题都适合用6σ方法解决。
在选择6σ候选项目时,应该考虑以下问题:(1)是否是反复出现的事件?(2)范围是否狭窄?(3)是否存在测量尺度?是否能在合理时间内确定测量系统?(4)是否能对过程进行控制?(5)项目是否提高了顾客满意度?如果以上所有问题的答案是“是”,那么这是一个顾客导向6σ的良好候选项目。
在确定阶段,需要采用适当的步骤来明确所选6σ项目是否符合以上要求。
项目小组首先要通过调查研究以确定顾客抱怨什么,抱怨的程度如何,并且将顾客的抱怨转化成关键质量特性(CTQ),即从顾客角度确定对顾客最重要的产品和服务特性。
8D报告 8 Disciplines
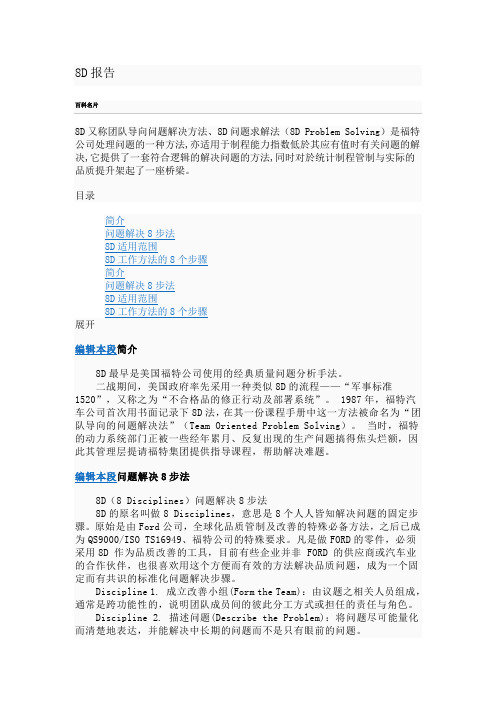
8D报告8D又称团队导向问题解决方法、8D问题求解法(8D Problem Solving)是福特公司处理问题的一种方法,亦适用于制程能力指数低於其应有值时有关问题的解决,它提供了一套符合逻辑的解决问题的方法,同时对於统计制程管制与实际的品质提升架起了一座桥梁。
目录简介问题解决8步法8D适用范围8D工作方法的8个步骤简介问题解决8步法8D适用范围8D工作方法的8个步骤展开编辑本段简介8D最早是美国福特公司使用的经典质量问题分析手法。
二战期间,美国政府率先采用一种类似8D的流程——“军事标准1520”,又称之为“不合格品的修正行动及部署系统”。
1987年,福特汽车公司首次用书面记录下8D法,在其一份课程手册中这一方法被命名为“团队导向的问题解决法”(Team Oriented Problem Solving)。
当时,福特的动力系统部门正被一些经年累月、反复出现的生产问题搞得焦头烂额,因此其管理层提请福特集团提供指导课程,帮助解决难题。
编辑本段问题解决8步法8D(8 Disciplines)问题解决8步法8D的原名叫做8 Disciplines,意思是8个人人皆知解决问题的固定步骤。
原始是由Ford公司,全球化品质管制及改善的特殊必备方法,之后已成为QS9000/ISO TS16949、福特公司的特殊要求。
凡是做FORD的零件,必须采用8D 作为品质改善的工具,目前有些企业并非 FORD 的供应商或汽车业的合作伙伴,也很喜欢用这个方便而有效的方法解决品质问题,成为一个固定而有共识的标准化问题解决步骤。
Discipline 1. 成立改善小组(Form the Team):由议题之相关人员组成,通常是跨功能性的,说明团队成员间的彼此分工方式或担任的责任与角色。
Discipline 2. 描述问题(Describe the Problem):将问题尽可能量化而清楚地表达,并能解决中长期的问题而不是只有眼前的问题。
8DReport培训教材

3 – 为什么?
4 – 为什么? 4 – 为什么?
32
5 – 为什么? 5 – 为什么?
5Why分析公司近期案例
2品0全11年部8停月线2日。,(铜运陵5W锐H展Y解反决馈方,法我司为7什月么份会所发供生的Q?J1为00什3产么品没,有出检现测气出门来环?带为间什隙么无会法出调厂配?,)产 从法(试验、检验、探测)方面分析(为什么该问题没有被检测到)
四问:为何吃早餐晚了?
答:因为起床晚了;
五问:为何起床晚了?
答:因为忘了上闹钟了……
15
课程内容
5Why质量工具简介 5Why工具应用方法 5Why问题解决方式 5Why经典案例解析
16
5 why质量工具简介
丰田生产方式创始人大野耐一总是爱在车间走来走去,停下来向 工人发问。他反复地就一个问题,问“为什么”,直到回答令他满意, 被他问到的人也心里明白为止——这就是后来著名的“五个为什么”。
恰当地定义问题。
不断提问为什么前一个事件会发生,直到回答“没有好的理由”或直 到一个新的故障模式被发现时才停止提问。
解释根本原因以防止问题重演。
文件中所有带有“为什么”的语句都会定义真正的根源(通常需要至 少5个“为什么”)
总体5个为什么图表
问题
1 – 为什么?
1 – 原因
2 -为什么?
2 -原因
2
什么是8D?
在撰写8D报告的时候,务必要保证下面的问题被清 楚准确有理有据地回答:
D2-问题是什么? D3~D6-问题如何解决? D7-将来该问题如何预防
3
什么是8D?
务必保证以下的问题被如实回答: 1.对零件的知识进行了充分的论证 2.完全确定了根本原因并聚焦于该原因 3.遗漏点已经被识别 4.确定与根本相匹配的纠正措施 5.纠正措施计划的验证已经被确定 6.包括了实施纠正措施的时间计划 7.有证据显示供方将把纠正措施纳入整个系统。
8D顾客导向问题解决步骤
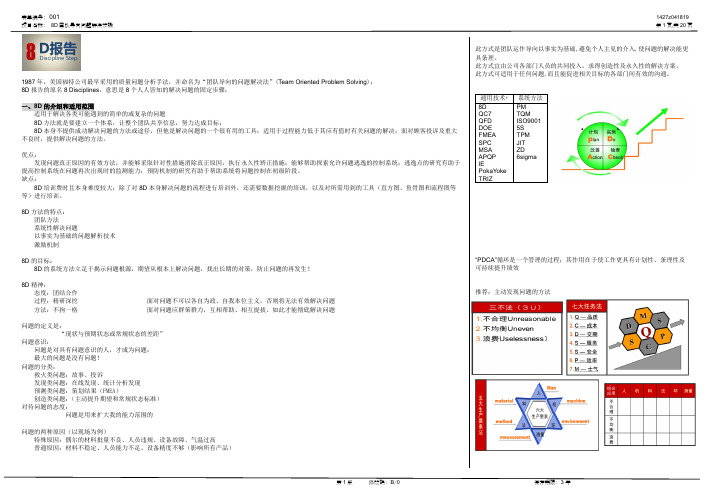
1987年,美国福特公司最早采用的质量问题分析手法,并命名为“团队导向的问题解决法”(Team Oriented Problem Solving ); 8D 报告的原名8 Disciplines ,意思是8个人人皆知的解决问题的固定步骤;一、8D 的介绍和适用范围适用于解决各类可能遇到的简单的或复杂的问题8D 方法就是要建立一个体系,让整个团队共享信息,努力达成目标;8D 本身不提供成功解决问题的方法或途径,但他是解决问题的一个很有用的工具;适用于过程能力低于其应有值时有关问题的解决;面对顾客投诉及重大不良时,提供解决问题的方法。
优点:发现问题真正原因的有效方法,并能够采取针对性措施消除真正原因,执行永久性矫正措施;能够帮助探索允许问题逃逸的控制系统;逃逸点的研究有助于提高控制系统在问题再次出现时的监测能力;预防机制的研究有助于帮助系统将问题控制在初级阶段。
缺点:8D 培训费时且本身难度较大;除了对8D 本身解决问题的流程进行培训外,还需要数据挖掘的培训,以及对所需用到的工具(直方图、鱼骨图和流程图等等)进行培训。
8D 方法的特点:团队方法系统性解决问题以事实为基础的问题解析技术 激励机制8D 的目标:8D 的系统方法立足于揭示问题根源,期望从根本上解决问题,找出长期的对策,防止问题的再发生!8D 精神:态度:团结合作过程:精研深挖 面对问题不可以各自为政、自我本位主义,否则将无法有效解决问题 方法:不拘一格 面对问题应群策群力,互相帮助、相互提拔、如此才能彻底解决问题问题的定义是:“现状与预期状态或常规状态的差距”问题意识:问题是对具有问题意识的人,才成为问题; 最大的问题是没有问题! 问题的分类:救火类问题:故事、投诉发现类问题:在线发现、统计分析发现 预测类问题:策划结果(FMEA) 创造类问题:(主动提升期望和常规状态标准) 对待问题的态度:问题是用来扩大我的能力范围的问题的两种原因(以现场为例)特殊原因:偶尔的材料批量不良、人员违规、设备故障、气温过高普通原因:材料不稳定、人员能力不足、设备精度不够(影响所有产品)此方式是团队运作导向以事实为基础,避免个人主见的介入,使问题的解决能更具条理。
有史以来最易懂的8D,从FMEA角度看G8D报告

有史以来最易懂的8D,从FMEA角度看G8D报告D0:准备8D过程D1:组建团队D2:描述问题D3:制定临时处置措施(ICA)D4:确定并验证根本起因和遗漏点D5:选择并验证针对根本原因和遗漏点的永久性纠正措施(PCA)D6:执行并确认PCAD7:预防问题重现D8:表彰小组和个人的贡献针对每一步,我们详细介绍其使用过程:D0:准备8D过程实施本阶段的原因:G8D过程是一个可能涉及大量人力、时间和资源的过程,如果使用不适当将会浪费很多时间、人力和相关的一些资源。
D0帮助我们把焦点放在问题上,以便有效地使用资源。
本阶段实施过程:了解症状并量化症状,决定是否需要ERA,选择并验证ERA,执行并确认ERA,查看是否适用G8D标准。
紧急反应措施(ERA)是保护顾客及相关的各方不受症状的影响的任何措施,它在G8D把问题和症状区分开来确认G8D是否有必要启动时应用。
症状是可测量的事件或效果(它们必须是顾客体验到的),它表示一个或多个问题存在。
如果没有症状,你就无法得知有问题存在。
当症状能被测量或量化时,它才被考虑在内。
通常有许多工具可以用来测量并量化故障:Paynter图,柏拉图,运行(趋势)图,风险图等。
G8D的适用标准:1.症状被定义;2.确定了顾客;3.存在性能差距;4.原因未知;5.管理层致力于从根本起因的层面去解决问题,并采取预防措施防止问题再次发生;6.症状很复杂,不可能单凭一个人的能力完成。
如果六个标准都满足,并且没有其他的G8D团队为同样的或类似的问题工作,那么就应该开始G8D过程。
D1:组建团队组建团队是G8D过程中的重要部分。
团队成员的指导方针:1.团队成员的人数控制在4到10个之间;2.选择具有所需技能、知识、资源、权力等,这样的人作为团队成员来解决现有的问题;3.各类成员之间合理搭配;4.按需要调整团队成员。
G8D的过程依赖于所有团队成员的努力来达到团队的目标。
为了达到团队目标,每个成员扮演一个角色。
8D(8 Discipline)-分析法
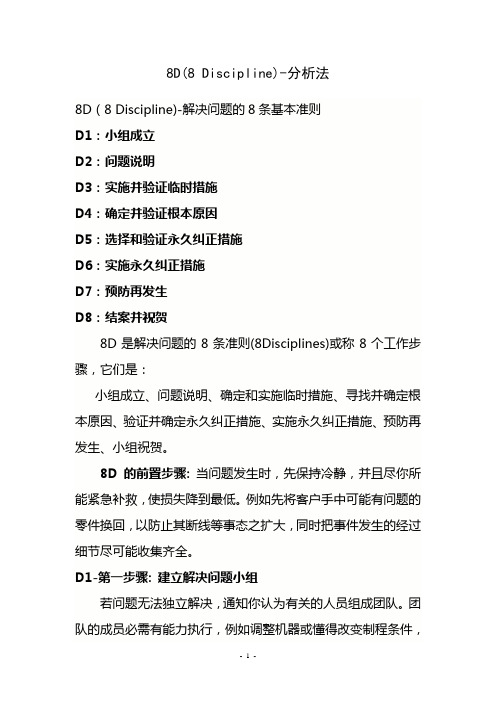
8D(8 Discipline)-分析法8D(8 Discipline)-解决问题的8条基本准则D1:小组成立D2:问题说明D3:实施并验证临时措施D4:确定并验证根本原因D5:选择和验证永久纠正措施D6:实施永久纠正措施D7:预防再发生D8:结案并祝贺8D是解决问题的8条准则(8Disciplines)或称8个工作步骤,它们是:小组成立、问题说明、确定和实施临时措施、寻找并确定根本原因、验证并确定永久纠正措施、实施永久纠正措施、预防再发生、小组祝贺。
8D的前置步骤: 当问题发生时,先保持冷静,并且尽你所能紧急补救,使损失降到最低。
例如先将客户手中可能有问题的零件换回,以防止其断线等事态之扩大,同时把事件发生的经过细节尽可能收集齐全。
D1-第一步骤: 建立解决问题小组若问题无法独立解决,通知你认为有关的人员组成团队。
团队的成员必需有能力执行,例如调整机器或懂得改变制程条件,或能指挥作筛选等。
D2-第二步骤: 描述问题向团队说明何时、何地、发生了什么事、严重程度、目前状态、如何紧急处理、以及展示照片和收集到的证物。
想象你是FBI的办案人员,将证物、细节描述越清楚,团队解决问题将越快。
D3-第三步骤: 执行暂时对策若真正原因还未找到,暂时用什么方法可以最快地防止问题?如全检、筛选、将自动改为手动、库存清查等。
暂时对策决定后,即立刻交由团队成员带回执行。
D4-第四步骤: 找出问题真正原因找问题真正原因时,最好不要盲目地动手改变目前的生产状态,先动动脑。
您第一件事是要先观察、分析、比较。
列出您所知道的所有生产条件(即鱼骨图),逐一观察,看看是否有些条件走样,还是最近有些什么异动?换了夹具吗?换了作业员?换了供应商?换了运输商?修过电源供应器?流程改过? 或比较良品与不良品的检查结果,看看那个数据有很大的差?尺寸?重量?电压值?CPK?耐电压?等等不良的发生,总是有原因,资料分析常常可以看出蛛丝马迹。
这样的分析,可以帮助您缩小范围,越来越接近问题核心。
8D问题解决方法
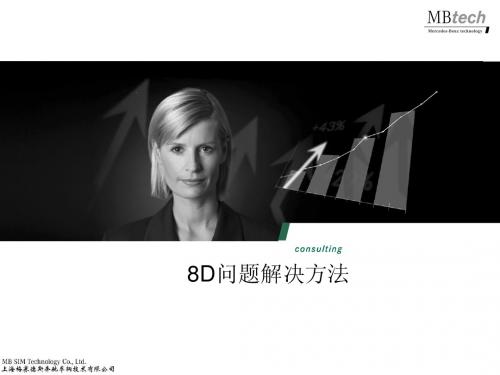
8D是解决问题的8条基本准则或称8个工作步骤,但在实际应用中却有9个步骤:
D0:征兆紧急反应措施 D1:小组成立 D2:问题说明 D3:采取临时抑制措施 D4:确定并验证根本原因 D5:选择和验证永久纠正措施 D6:实施永久纠正措施,效果确认 D7:预防再发生 D8:小组祝贺
D0:征兆紧急反应措施
12
事由:客户大众投诉,BMG喇叭接线柱批量松动 D0:征兆紧急反应措施 。 1.派人到客户处进行挑选。2.采用8D解决方法。 D1:小组成立 。质量,工艺,生产,物流。 D2:问题说明 。 2011年3月22日,奥迪生产线所用批次号为xxx的BMG喇叭33%接线柱松动… D3:采取临时抑制措施 。 1.隔离客户处、途中、固泰该批次及以后批次的该型号喇叭,进行全检。 2.生产线对接线柱进行100%检验。 D4:确定并验证根本原因 。 接线柱松动螺丝扭矩不够自动打螺丝机故障保养不彻底 D5:选择和验证永久纠正措施 1.修复自动打螺丝机 D6:实施永久纠正措施,效果确认 。经跟踪,效果良好。 D7:预防再发生 1.制作保养作业指导书,培训设备维护人员 2.对接线柱扭矩进行抽检,形成指导文件 D8:小组祝贺
鱼骨图 5个为什么
D5:选择和验证永久纠正措施
拟定方案 选择最优方案
D6:实施永久纠正措施,效果确认
实施计划 进度跟进 效果跟进
D7:预防再发生
标准化 更新相关制度、文件
D8:小组祝贺
总结 奖励
事由:出租屋内,一日早晨,小王正在水龙边洗脸准备上班,刚洗完脸,突然家中打来电话,于是把脸帕一挂 就去屋内接电话,接完电话就去上班。下午下班回家时发现家中全部被水淹了。铺在地上的草席和被子全 都漂在水中。 D0 鉴于事态严重,决定采用8D解决方法 D1 成立改善小组:马上叫上住在隔壁的几个同事,组成事故处理小组。小组成员:张三、李四、王五。 D2 问题描述 王五家中被水淹,家中所有摆放在地上的物品都浸在水中(不良率100%)。如:草席、被子和书 本等。 D3 暂时围堵行动(即应急对策或叫临时对策)1、马上与小组成员一起把家中的水设法排放出去。 负责人:张 三 2、立即把浸在水中的物品捞起并摊开到阳台去凉干。 负责人:李四 D4 根本原因分析: 1、早晨洗完脸时,接听家中突然打来的电话,然后忘记关水,造成水淹小屋。 2、下水道 出口太小,而且都采用网格式的盖子盖住。昨天洗菜洗出来的小片烂蔬菜叶梗在网格上,致使下水道出水 很慢,长时间积累后,大量未及时排放出去的水把小屋淹了。 分析人:王五 审核:王五妻子 D5(第五步)---制订永久对策(即长期对策) 1、把下水道出口上的网格式盖子去掉,以便加大出水口,不会 造成被水淹的情况。 责任人:王五 预计完成时间:2007-**-** D6 实施/确认1、经过王五实际操作,把下水道出口加大后,小片蔬菜叶不会再梗在出水口处,堵住废水往外流 。并且即使把水龙头打开到最大,水仍能及时地从下水道出水口完全地流出去。 现确认此永久对策有效, 并已经执行。 验证人:王五 D7 防止再发生(即采取预防措施) 1、早晨上班出门前一定要检验水龙头是否关闭。 2、以后洗蔬菜时一定要 把烂蔬菜叶丢到垃圾筐里,并且要把地面清理干净。 3、早晨洗脸时不能带电话在身上。在洗脸过程中, 就算电话铃响起也不能接。直到洗漱完毕后才能接听手机。 责任人:王五 预计完成时间:2007-**-** D8 结案并祝贺: 此问题已经完全处理清楚,可以结案(close)。并且今天晚上叫张三、李四、王五老婆一起 去‘毛家饭店’庆祝团队成功。
8D(8项准则)
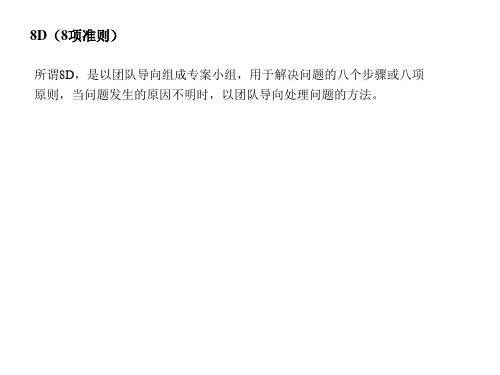
•确认所选择的纠正措施以解决问题,并
对解决方案进行挑选 制定纠正措施 Y 确认是否 有副作用
确保不会造成不希望有的副作用。
•对纠正措施执行的有效性进行验证。
N
执行纠正措施
跟踪验证纠正 措施的有效性
Step 6
第六步:实施永久性纠正措施
Step 6
•确定并实施所需的永久性纠正措施, 选
实施永久性纠正措施
择过程控制方法,以保证消除根本原因,
一旦使用,要监控长期效果。
定期跟踪永久性 措施的执行状况
Step 7
第七步:防止再发生
Step 7
•修改程序操作规范等文件化的规定, 改进工作方法和程序,对相关人员进 行培训,以防止该问题和所有类似的 问题再发生。
实施必要的程 序、规范的更该
将永久性措施文件化
Step 8
第四步:确定根本原因
Step 4
识别潜在的原因
•罗列所有潜在可以解释为何问题发生的 各项原因,相对问题描述、收集到的数 据,验证每项潜在的原因,确定可以替
N 选择较合适的原因
代的纠正措施,以消除问题发生的根本 原因。
是否是 根本原因 Y 识别多种可以 解决问题的方案
Step 5
第五步:验证纠正措施
第八步:庆贺成功
•对小组成员的共同努力给予奖励, 公布成tep 3
•确定过渡措施(短期纠正措施),以维护 顾客(包括内部顾客、外部顾客)利益不为
制定短期纠正措施
执行短期纠正措施
问题所困扰,直到永久性预防措施执行为止。 •执行过渡措施并对执行情况进行跟踪。 •用数据来验证这些措施的有效性。
对短期纠正措施的 执行情况进行跟踪
验证短期纠正 措施的有效性
知识分享:8D制作作业指导书(超级实用)

知识分享:8D制作作业指导书(超级实⽤)8D最早是美国福特公司使⽤的经典质量问题分析⼿法。
8D是解决问题的8条基本准则或称8个⼯作步骤,后来把其改良成9个步骤(改良后叫做Global 8D Report,即G8D):D0:征召紧急反应措施;判断问题的类型、⼤⼩、范畴等,以判断是否需要需要⽤8D来解决,与D3不同,D0是针对问题发⽣的反应,⽽D3是针对产品或服务问题本⾝的暂时应对措施。
D1:⼩组成⽴D2:问题说明D3:实施并验证临时措施D4:确定并验证根本原因D5:选择和验证永久纠正措施D6:实施永久纠正措施D7:预防再发⽣D8:⼩组祝贺⽬的与概述:本⽂规范了8D拟制要求、评审要求、批准发放等内容。
规范8D拟制、评审、批准发放等要求,以利于有效制定和执⾏改善措施,预防同类问题再发⽣。
职责:术语:围堵措施围堵措施也可以叫做应急措施或临时措施。
其含义是在不合格发⽣的第⼀时间对可疑产品或事件进⾏开启全⾯应急计划(标识、隔离、排查、追溯、告知客户、信息传递等作业)的⼯作。
不合格发⽣后,应及时采取围堵措施,避免事态进⼀步扩⼤⽽遭受更⼤的损失。
纠正为消除已发现的不合格所采取的措施。
针对的是不合格产品或事件,就事论事;是当机⽴断措施,当即发⽣作⽤。
如返修、返⼯、返检、降级、调整;它只是仅对不合格进⾏的处置,只是治标。
原则是:只要是不合格都要触发进⾏。
纠正措施为消除已发现的不合格或其它不期望情况的原因所采取的措施。
针对的是产⽣不合格的原因,追本溯源;时间较长,需要跟踪验证才能看到效果,如通过修订流程,从根本消除问题根源;是为了防⽌已出现的不合格等情况再次发⽣,是标本兼治。
当不合格品影响较⼤,如审核不合格、顾客抱怨、反复出现以及后果严重的不合格时,可以启动纠正措施。
预防措施为消除潜在不合格或其它潜在不期望情况的原因所采取的措施。
和纠正措施⼀样都是措施,都起到预防作⽤。
类别纠正措施预防措施共同点都是措施,都起到预防的作⽤不同点纠正措施在已发⽣不合格的情况下纠正措施的作⽤是预防不合格再次发⽣。
8D组成部分详细解答
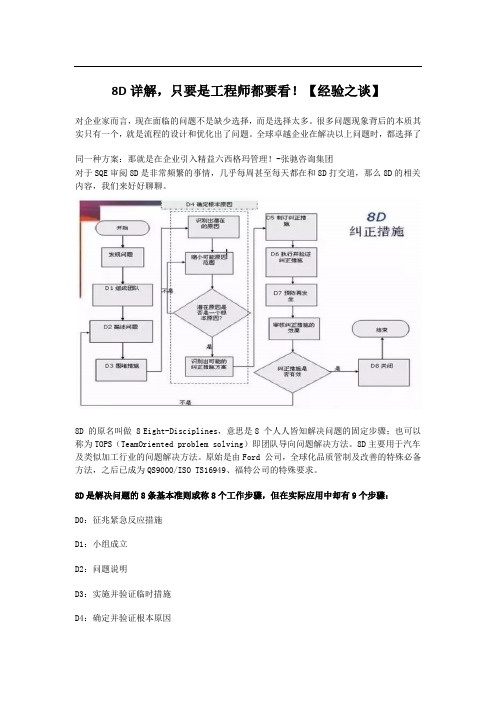
8D详解,只要是工程师都要看!【经验之谈】对企业家而言,现在面临的问题不是缺少选择,而是选择太多。
很多问题现象背后的本质其实只有一个,就是流程的设计和优化出了问题。
全球卓越企业在解决以上问题时,都选择了同一种方案:那就是在企业引入精益六西格玛管理!-张驰咨询集团对于SQE审阅8D是非常频繁的事情,几乎每周甚至每天都在和8D打交道,那么8D的相关内容,我们来好好聊聊。
8D 的原名叫做 8 Eight-Disciplines,意思是8 个人人皆知解决问题的固定步骤;也可以称为TOPS(TeamOriented problem solving)即团队导向问题解决方法。
8D主要用于汽车及类似加工行业的问题解决方法。
原始是由Ford 公司,全球化品质管制及改善的特殊必备方法,之后已成为QS9000/ISO TS16949、福特公司的特殊要求。
8D是解决问题的8条基本准则或称8个工作步骤,但在实际应用中却有9个步骤:D0:征兆紧急反应措施D1:小组成立D2:问题说明D3:实施并验证临时措施D4:确定并验证根本原因D5:选择和验证永久纠正措施D6:实施永久纠正措施D7:预防再发生D8:小组祝贺SQE在给供应商做8D报告的培训的时候,必须跟供应商讲清楚,作为供应商在撰写8D报告的时候,务必要保证下面的问题被清楚准确有理有据地回答:D2-问题是什么?D3~D6-问题如何解决?D7-将来该问题如何预防然而作为SQE在审阅供应商的8D报告的时候,也务必保证以下的问题被如实回答:1.对零件的知识进行了充分的论证2.完全确定了根本原因并聚焦于该原因3.遗漏点已经被识别4.确定与根本相匹配的纠正措施5.纠正措施计划的验证已经被确定6.包括了实施纠正措施的时间计划7.有证据显示供方将把纠正措施纳入整个系统。
8D的实施过程可能用到的质量工具总结如下:可靠性/设计验证DV/产品和过程确认/潜在失效模式及后果分析FMEA/控制计划CP/PPAP文件/SPC/DOE/QC7大工具D0:征兆紧急反应措施目的:主要是为了看此类问题是否需要用8D来解决,如果问题太小,或是不适合用8D来解决的问题,例如价格,经费等等,这一步是针对问题发生时候的紧急反应。
8D工作方法的8个步骤
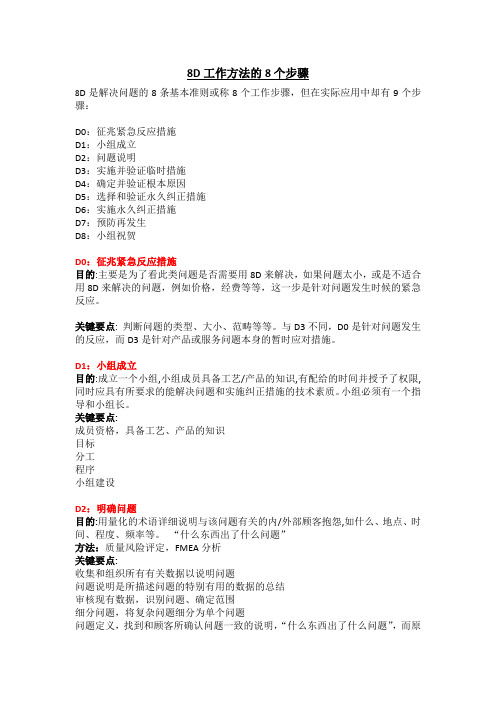
8D工作方法的8个步骤8D是解决问题的8条基本准则或称8个工作步骤,但在实际应用中却有9个步骤:D0:征兆紧急反应措施D1:小组成立D2:问题说明D3:实施并验证临时措施D4:确定并验证根本原因D5:选择和验证永久纠正措施D6:实施永久纠正措施D7:预防再发生D8:小组祝贺D0:征兆紧急反应措施目的:主要是为了看此类问题是否需要用8D来解决,如果问题太小,或是不适合用8D来解决的问题,例如价格,经费等等,这一步是针对问题发生时候的紧急反应。
关键要点: 判断问题的类型、大小、范畴等等。
与D3不同,D0是针对问题发生的反应,而D3是针对产品或服务问题本身的暂时应对措施。
D1:小组成立目的:成立一个小组,小组成员具备工艺/产品的知识,有配给的时间并授予了权限,同时应具有所要求的能解决问题和实施纠正措施的技术素质。
小组必须有一个指导和小组长。
关键要点:成员资格,具备工艺、产品的知识目标分工程序小组建设D2:明确问题目的:用量化的术语详细说明与该问题有关的内/外部顾客抱怨,如什么、地点、时间、程度、频率等。
“什么东西出了什么问题”方法:质量风险评定,FMEA分析关键要点:收集和组织所有有关数据以说明问题问题说明是所描述问题的特别有用的数据的总结审核现有数据,识别问题、确定范围细分问题,将复杂问题细分为单个问题问题定义,找到和顾客所确认问题一致的说明,“什么东西出了什么问题”,而原因又未知风险等级。
D3:实施并验证临时措施目的:保证在永久纠正措施实施前,将问题与内外部顾客隔离。
(原为唯一可选步骤,但发展至今都需采用)方法:FMEA、DOE、PPM关键要点:评价紧急响应措施找出和选择最佳“临时抑制措施”决策实施,并作好记录验证(DOE、PPM分析、控制图等)D4:确定并验证根本原因目的:用统计工具列出可以用来解释问题起因的所有潜在原因,将问题说明中提到的造成偏差的一系列事件或环境或原因相互隔离测试并确定产生问题的根本原因。
8D组成部分详细解答

8D详解,只要是工程师都要看!【经验之谈】对企业家而言,现在面临的问题不是缺少选择,而是选择太多。
很多问题现象背后的本质其实只有一个,就是流程的设计和优化出了问题。
全球卓越企业在解决以上问题时,都选择了同一种方案:那就是在企业引入精益六西格玛管理!-张驰咨询集团对于SQE审阅8D是非常频繁的事情,几乎每周甚至每天都在和8D打交道,那么8D的相关内容,我们来好好聊聊。
8D 的原名叫做8 Eight-Disciplines,意思是8 个人人皆知解决问题的固定步骤;也可以称为TOPS(TeamOriented problem solving)即团队导向问题解决方法。
8D主要用于汽车及类似加工行业的问题解决方法。
原始是由Ford 公司,全球化品质管制及改善的特殊必备方法,之后已成为QS9000/ISO TS16949、福特公司的特殊要求。
8D是解决问题的8条基本准则或称8个工作步骤,但在实际应用中却有9个步骤:D0:征兆紧急反应措施D1:小组成立D2:问题说明D3:实施并验证临时措施D4:确定并验证根本原因D5:选择和验证永久纠正措施D6:实施永久纠正措施D7:预防再发生D8:小组祝贺SQE在给供应商做8D报告的培训的时候,必须跟供应商讲清楚,作为供应商在撰写8D报告的时候,务必要保证下面的问题被清楚准确有理有据地回答:D2-问题是什么D3~D6-问题如何解决D7-将来该问题如何预防然而作为SQE在审阅供应商的8D报告的时候,也务必保证以下的问题被如实回答:1.对零件的知识进行了充分的论证2.完全确定了根本原因并聚焦于该原因3.遗漏点已经被识别4.确定与根本相匹配的纠正措施5.纠正措施计划的验证已经被确定6.包括了实施纠正措施的时间计划7.有证据显示供方将把纠正措施纳入整个系统。
8D的实施过程可能用到的质量工具总结如下:可靠性/设计验证DV/产品和过程确认/潜在失效模式及后果分析FMEA/控制计划CP/PPAP文件/SPC/DOE/QC7大工具D0:征兆紧急反应措施目的:主要是为了看此类问题是否需要用8D来解决,如果问题太小,或是不适合用8D来解决的问题,例如价格,经费等等,这一步是针对问题发生时候的紧急反应。
8D是解决问题的8条基本准则或称8个工作步骤
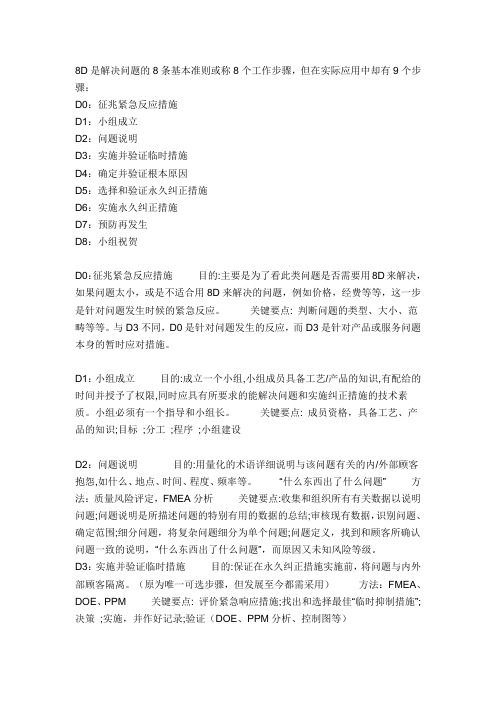
8D是解决问题的8条基本准则或称8个工作步骤,但在实际应用中却有9个步骤:D0:征兆紧急反应措施D1:小组成立D2:问题说明D3:实施并验证临时措施D4:确定并验证根本原因D5:选择和验证永久纠正措施D6:实施永久纠正措施D7:预防再发生D8:小组祝贺D0:征兆紧急反应措施目的:主要是为了看此类问题是否需要用8D来解决,如果问题太小,或是不适合用8D来解决的问题,例如价格,经费等等,这一步是针对问题发生时候的紧急反应。
关键要点: 判断问题的类型、大小、范畴等等。
与D3不同,D0是针对问题发生的反应,而D3是针对产品或服务问题本身的暂时应对措施。
D1:小组成立目的:成立一个小组,小组成员具备工艺/产品的知识,有配给的时间并授予了权限,同时应具有所要求的能解决问题和实施纠正措施的技术素质。
小组必须有一个指导和小组长。
关键要点: 成员资格,具备工艺、产品的知识;目标;分工;程序;小组建设D2:问题说明目的:用量化的术语详细说明与该问题有关的内/外部顾客抱怨,如什么、地点、时间、程度、频率等。
“什么东西出了什么问题” 方法:质量风险评定,FMEA分析关键要点:收集和组织所有有关数据以说明问题;问题说明是所描述问题的特别有用的数据的总结;审核现有数据,识别问题、确定范围;细分问题,将复杂问题细分为单个问题;问题定义,找到和顾客所确认问题一致的说明,“什么东西出了什么问题”,而原因又未知风险等级。
D3:实施并验证临时措施目的:保证在永久纠正措施实施前,将问题与内外部顾客隔离。
(原为唯一可选步骤,但发展至今都需采用)方法:FMEA、DOE、PPM 关键要点: 评价紧急响应措施;找出和选择最佳“临时抑制措施”;决策;实施,并作好记录;验证(DOE、PPM分析、控制图等)D4:确定并验证根本原因目的:用统计工具列出可以用来解释问题起因的所有潜在原因,将问题说明中提到的造成偏差的一系列事件或环境或原因相互隔离测试并确定产生问题的根本原因。
8D报告的评价标准

华阳通用电子有限公司.8D 报告的评价标准整理: SQA-Springsun 日期:2012年2月13日8D(Eight Disciplines of Problem Solving)是福特公司解决问题的8条基本准则。
是福特公司在20世纪90年代早期引进的技术方法来解决工厂和供应商的问题。
8D是解决问题的一种工具,通常是客户所抱怨的问题要求公司分析,并提出永久解决及改善的方法。
8D是由一个准备步骤和8个步骤组成。
这些步骤用来客观地确定、定义和解决问题,并防止相似问题的再次发生。
解决问题的8个步骤:问题发生成立8D 小组问题描述实施并验证临时性纠正措施确定和验证问题的根本原因选择和验证永久性纠正措施实施和确认永久性纠正措施防止问题再次发生/系统预防性建议表彰小组和个人的贡献D0D1(10分)D2(10分)D3(15分)D4(15分)D5(15分)D6(15分)D7(15分)D8 (5分)8D目标:解决问题,保证品质积累解决问题的经验。
8D准则:针对出现的问题,找出问题产生的根本原因,提出短期、中期、长期的对策,并采取相应的行动,彻底解决问题,杜绝或尽量减少问题重复出现。
8D好处:z可以通过建立小组训练内部合作能力z推进有效的问题解决和预防技术z改进整个质量和生产率z防止相同或类似问题的再发生z提高顾客满意度有效实施8D的质量工具:z控制计划(PC)z潜在失效模式及后果分析(FMEA)z生产件批准程序(PPAP)z统计过程控制(SPC)z试验计划(DOE)8D说明:1)选定了目标,一定要找出其根本原因,针对产生问题的原因,制订短期对策、中期对策、长期对策。
短期对策:是指生产现场怎么办?中期对策:是指即将要生产的怎么办?长期对策:是指如何将问题解决在发生之前?2)必须采取行动,有对策,执行是关键。
有了对策,必须是不折不扣地执行。
3)持之以恒,必须要坚持行动,解决问题必须要达到彻底清楚的目的。
绝不能因为解决了一半而导致问题周而复始,不时复出发生。
如何写8D报告什么是8D报告

如何写8D报告,什么是8D报告8D 的原名叫做8 Eight-Disciplines,意思是8 个人人皆知解决问题的固定步骤;也可以称为TOPS(TeamOriented problem solving)即团队导向问题解决方法。
8D主要用于汽车及类似加工行业的问题解决方法。
原始是由Ford 公司,全球化品质管制及改善的特殊必备方法,之后已成为QS9000/ISO TS16949、福特公司的特殊要求。
(一)9个步骤8D是解决问题的8条基本准则或称8个工作步骤,但在实际应用中却有9个步骤:D0:征兆紧急反应措施D1:小组成立D2:问题说明D3:实施并验证临时措施D4:确定并验证根本原因D5:选择和验证永久纠正措施D6:实施永久纠正措施D7:预防再发生D8:小组祝贺(二)3个问题SQE在给供应商做8D报告的培训的时候,必须跟供应商讲清楚,作为供应商在撰写8D报告的时候,务必要保证下面的问题被清楚准确有理有据地回答:D2-问题是什么?D3~D6-问题如何解决?D7-将来该问题如何预防(三)7个问题然而作为SQE在审阅供应商的8D报告的时候,也务必保证以下的问题被如实回答:1.对零件的知识进行了充分的论证2.完全确定了根本原因并聚焦于该原因3.遗漏点已经被识别4.确定与根本相匹配的纠正措施5.纠正措施计划的验证已经被确定6.包括了实施纠正措施的时间计划7.有证据显示供方将把纠正措施纳入整个系统。
(四)质量工具8D的实施过程可能用到的质量工具总结如下:可靠性/设计验证DV/产品和过程确认/潜在失效模式及后果分析FMEA/控制计划CP/PPAP 文件/SPC/DOE/QC7大工具D0:征兆紧急反应措施目的:主要是为了看此类问题是否需要用8D来解决,如果问题太小,或是不适合用8D来解决的问题,例如价格,经费等等,这一步是针对问题发生时候的紧急反应。
关键要点:判断问题的类型、大小、范畴等等。
与D3不同,D0是针对问题发生的反应,而D3是针对产品或服务问题本身的暂时应对措施。
质量改进(8D)管理办法
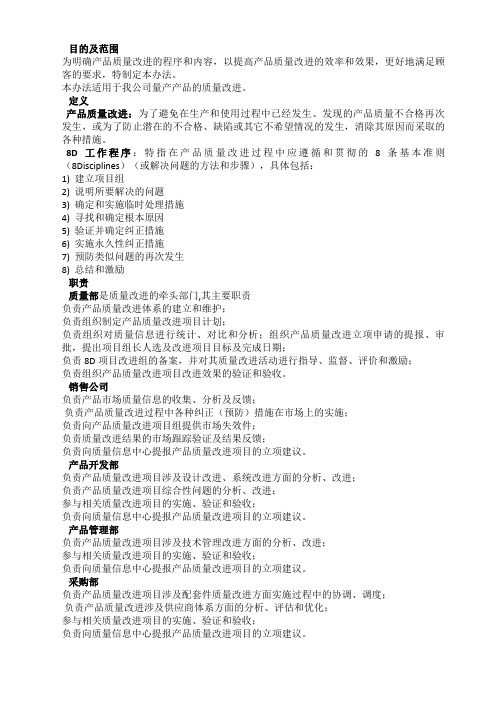
目的及范围为明确产品质量改进的程序和内容,以提高产品质量改进的效率和效果,更好地满足顾客的要求,特制定本办法。
本办法适用于我公司量产产品的质量改进。
定义产品质量改进:为了避免在生产和使用过程中已经发生、发现的产品质量不合格再次发生,或为了防止潜在的不合格、缺陷或其它不希望情况的发生,消除其原因而采取的各种措施。
8D工作程序:特指在产品质量改进过程中应遵循和贯彻的8条基本准则(8Disciplines)(或解决问题的方法和步骤),具体包括:1) 建立项目组2) 说明所要解决的问题3) 确定和实施临时处理措施4) 寻找和确定根本原因5) 验证并确定纠正措施6) 实施永久性纠正措施7) 预防类似问题的再次发生8) 总结和激励职责质量部是质量改进的牵头部门,其主要职责负责产品质量改进体系的建立和维护;负责组织制定产品质量改进项目计划;负责组织对质量信息进行统计、对比和分析;组织产品质量改进立项申请的提报、审批,提出项目组长人选及改进项目目标及完成日期;负责8D项目改进组的备案,并对其质量改进活动进行指导、监督、评价和激励;负责组织产品质量改进项目改进效果的验证和验收。
销售公司负责产品市场质量信息的收集、分析及反馈;负责产品质量改进过程中各种纠正(预防)措施在市场上的实施;负责向产品质量改进项目组提供市场失效件;负责质量改进结果的市场跟踪验证及结果反馈;负责向质量信息中心提报产品质量改进项目的立项建议。
产品开发部负责产品质量改进项目涉及设计改进、系统改进方面的分析、改进;负责产品质量改进项目综合性问题的分析、改进;参与相关质量改进项目的实施、验证和验收;负责向质量信息中心提报产品质量改进项目的立项建议。
产品管理部负责产品质量改进项目涉及技术管理改进方面的分析、改进;参与相关质量改进项目的实施、验证和验收;负责向质量信息中心提报产品质量改进项目的立项建议。
采购部负责产品质量改进项目涉及配套件质量改进方面实施过程中的协调、调度;负责产品质量改进涉及供应商体系方面的分析、评估和优化;参与相关质量改进项目的实施、验证和验收;负责向质量信息中心提报产品质量改进项目的立项建议。
- 1、下载文档前请自行甄别文档内容的完整性,平台不提供额外的编辑、内容补充、找答案等附加服务。
- 2、"仅部分预览"的文档,不可在线预览部分如存在完整性等问题,可反馈申请退款(可完整预览的文档不适用该条件!)。
- 3、如文档侵犯您的权益,请联系客服反馈,我们会尽快为您处理(人工客服工作时间:9:00-18:30)。
8D是解决问题的8条基本准则或称8个工作步骤,但在实际应用中却有9个步骤:
D0:征兆紧急反应措施
D1:小组成立
D2:问题说明
D3:实施并验证临时措施
D4:确定并验证根本原因
D5:选择和验证永久纠正措施
D6:实施永久纠正措施
D7:预防再发生
D8:小组祝贺
8D工作方法的介绍
8D又称团队导向问题解决方法,是福特公司处理问题的一种方法,亦适用于制程能力指数低於其应有值时有关问题的解决,它提供了一套符合逻辑的解决问题的方法,同时对於统计制程管制与实际的产品质量提升架起了一座桥梁。
主要步骤包括:
D1:小组成立
D2:问题说明
D3:实施并验证临时措施
D4:确定并验证根本原因
D5:选择和验证永久纠正措施
D6:实施永久纠正措施
D7:预防再发生
D8:小组祝贺
D1:小组成立
目的:
成立一个小组,小组成员具备工艺/产品的知识,有配给的时间并授予了权限,同时应具有所要求的能解决问题和实施纠正措施的技术素质。
小组必须有一个指导和小组长。
关键要点:
成员资格,具备工艺、产品的知识
目标
分工
程序
小组建设
D2:问题说明
目的:
用量化的术语详细说明与该问题有关的内/外部顾客抱怨,如什么、地点、时间、程度、频率等。
“什么东西出了什么问题”
方法:质量风险评定,FMEA分析
关键要点:
收集和组织所有有关数据以说明问题
问题说明是所描述问题的特别有用的数据的总结
审核现有数据,识别问题、确定范围
细分问题,将复杂问题细分为单个问题
问题定义,找到和顾客所确认问题一致的说明,“什么东西出了什么问题”,而原因又未知
风险等级
D3:实施并验证临时措施
目的:
保证在永久纠正措施实施前,将问题与内外部顾客隔离。
(原为唯一可选步骤,但发展至今都需采用)
方法:FMEA、DOE、PPM
关键要点:
评价紧急响应措施
找出和选择最佳“临时抑制措施”
决策
实施,并作好记录
验证(DOE、PPM分析、控制图等)
D4:确定并验证根本原因
目的:
用统计工具列出可以用来解释问题起因的所有潜在原因,将问题说明中提到的造成偏差的一系列事件或环境或原因相互隔离测试并确定产生问题的根本原因。
方法:FMEA、PPM、DOE、控制图
关键要点:
评估可能原因列表中的每一个原因
原因可否使问题排除
验证
控制计划
D5:选择并验证永久纠正措施
目的:
在生产前测试方案,并对方案进行评审以确定所选的校正措施能够解决客户问题,同时对其它过程不会有不良影响。
方法:FMEA
关键要点:
重新审视小组成员资格
决策,选择最佳措施
重新评估临时措施,如必要重新选择
验证
管理层承诺执行永久纠正措施
控制计划
D6:实施永久纠正措施
目的:
制定一个实施永久措施的计划,确定过程控制方法并纳入文件,以确保根本原因的消除。
在生产中应用该措施时应监督其长期效果。
方法:防错、统计控制
关键要点:
重新审视小组成员
执行永久纠正措施,废除临时措施
利用故障的可测量性确认故障已经排除
控制计划、工艺文件修改
D7:预防再发生
目的:
修改现有的管理系统、操作系统、工作惯例、设计与规程以防止这一问题与所有类似问题重复发生。
关键要点:
选择预防措施
验证有效性
决策
组织、人员、设备、环境、材料、文件重新确定
D8:小组祝贺
目的:
承认小组的集体努力,对小组工作进行总结并祝贺。
关键要点:
有选择的保留重要文档
流览小组工作,将心得形成文件
了解小组对解决问题的集体力量,及对解决问题作出的贡献必要的物质、精神奖励。