层状氮化硅陶瓷的性能与结构
氮化硅陶瓷

由于氮化硅陶瓷脆性大,而金属材料具有优良的室温强度和延展性, 所以将氮化硅陶瓷和金属材料结合,可以制造出满足要求的复杂构件。
其他氮化物结构陶瓷
氮化铝(AlN)陶瓷 熔点:2450℃
•
AlN陶瓷具有高导热性、高强度、高 Leabharlann 热性;机械性能好,耐腐蚀,透光性强
等; • 可以作为散热片;熔融金属用 坩埚、保护管、耐热转等;
来,晶须补强陶瓷基复合材料也一直是人们研究的热点,并取得了不少积
极的研究成果,其中SiC晶须是复合材料中主要应用的晶须,研究发现
Si3N4经SiC晶须强化可大大提高强度和韧性
层状结构复合增韧
近年来,国内外学者从生物界得到启示:贝壳具有的层状结构可以产 生较大的韧性。目前,国内外已有人开始了层状复合材料的探索性研究。 Sajgalik等研究了不同显微结构或不同组成材料构成的多层Si3N4基复合材 料,发现多层材料的强度及韧性都较单相材料高,并表现出准塑性现象; 郭海制备了高韧性的层状Si3N4基复合材料,主层内加入一定量的SiC晶须, 产生两级增韧效果,层状氮化硅陶瓷的断裂韧性显著提高。
•
特别是作为耐热砖应用时,因其
在特殊气氛中的耐热性能优异,所以 常用作2000℃左右的非氧化性电炉的
AlN陶瓷基板-LED用高热导氮 化铝材料
衬材材料。
氮化硼(BN)陶瓷
氮化硼陶瓷是一种以氮化硼为主的陶瓷。具有优良的电绝缘性、 耐热性、耐腐蚀性。高导热性,能吸收中子,高温润滑性和机械加
工性好,是发展较快,应用较广的一种氮化物陶瓷。
TiN还具有良好的导电性,常用作熔盐电解的电极材料。还具有较
高的超导临界温度,是一种优良的超导材料。
15 16
• 化学稳定性:硅氮共价键结合,键能很高,生成焓很高, 形成稳定的化合物(抗氧化性,抗腐蚀性)
氮化物
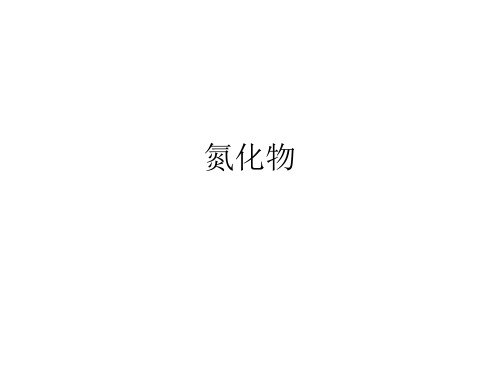
• 除氢氟酸外,它不与其他无机酸反应(反应 方程式:Si3N4+12HF═3SiF4↑+4NH3↑, 抗腐蚀能力强
应用
• 氮化硅用做高级耐火材料,如与sic结合作 SI3N4-SIC耐火材料用于高炉炉身等部位; 如与BN结合作SI3N4-BN材料,用于水平连 铸分离环。SI3N4-BN系水平连铸分离环是 一种细结构陶瓷材料,结构均匀,具有高 的机械强度。耐热冲击性好,又不会被钢 液湿润,符合连珠的工艺要求
• 在治金工业,由于氮化硅陶瓷耐高温,摩 擦系数小,具有自润滑性。对多数金属、 合金溶液稳定,因此,可制作金属材料加 工的工模具,如拨菅芯棒、挤压、拨丝模 具,轧辊、传送辊、发热体夹具、热偶套 营、金属热处理支承件、坩埚,铝液导营、 铝包内衬等
氮化硅制品的生产工艺
• 氮化硅制品按工艺可以分为反应烧结制品、热压 制品、常压烧结制品、等静压烧结制品和反应重 烧制品等。其中,反应烧结是一种常用的生产氮 化硅耐火制品的方法 • 反应烧结法生产氮化硅制品是将磨细的硅粉(粒 度一般小于80μm),用机压或等静压成型,坯体 干燥后,在氮气中加热至1350~1400℃,在烧成 过程中同时氮化而制得。采用这种生产方法,原 料条件和烧成工艺及气氛条件对制品的性能有很 大的影响
• 氮化硅 - 性质 化学式Si3N4。白色粉状晶 体;熔点1900℃,密度3.44克/厘米(20℃);有 两种变体:α型为六方密堆积结构;β型为 似晶石结构。氮化硅有杂质或过量硅时呈 灰色
• 氮化硅与水几乎不发生作用;在浓强酸溶 液中缓慢水解生成铵盐和二氧化硅;易溶 于氢氟酸,与稀酸不起作用。浓强碱溶液 能缓慢腐蚀氮化硅,熔融的强碱能很快使 氮化硅转变为硅酸盐和氨。氮化硅在 600℃ 以上能使过渡金属(见过渡元素)氧化物、 氧化铅、氧化锌和二氧化锡等还原,并放出 氧化氮和二氧化氮。1285℃ 时氮化硅与二 氮化三钙Ca3N2发生以下反应 Ca3N2+Si3N4─→3CaSiN2
陶瓷工艺学及答案
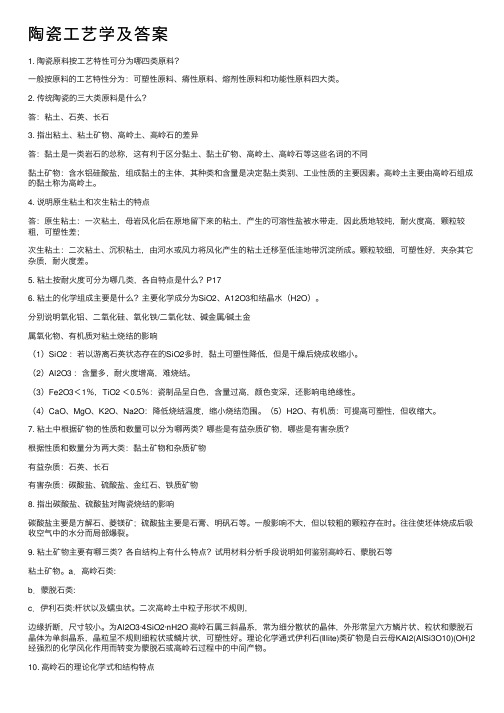
陶瓷⼯艺学及答案1. 陶瓷原料按⼯艺特性可分为哪四类原料?⼀般按原料的⼯艺特性分为:可塑性原料、瘠性原料、熔剂性原料和功能性原料四⼤类。
2. 传统陶瓷的三⼤类原料是什么?答:粘⼟、⽯英、长⽯3. 指出粘⼟、粘⼟矿物、⾼岭⼟、⾼岭⽯的差异答:黏⼟是⼀类岩⽯的总称,这有利于区分黏⼟、黏⼟矿物、⾼岭⼟、⾼岭⽯等这些名词的不同黏⼟矿物:含⽔铝硅酸盐,组成黏⼟的主体,其种类和含量是决定黏⼟类别、⼯业性质的主要因素。
⾼岭⼟主要由⾼岭⽯组成的黏⼟称为⾼岭⼟。
4. 说明原⽣粘⼟和次⽣粘⼟的特点答:原⽣粘⼟:⼀次粘⼟,母岩风化后在原地留下来的粘⼟,产⽣的可溶性盐被⽔带⾛,因此质地较纯,耐⽕度⾼,颗粒较粗,可塑性差;次⽣粘⼟:⼆次粘⼟、沉积粘⼟,由河⽔或风⼒将风化产⽣的粘⼟迁移⾄低洼地带沉淀所成。
颗粒较细,可塑性好,夹杂其它杂质,耐⽕度差。
5. 粘⼟按耐⽕度可分为哪⼏类,各⾃特点是什么?P176. 粘⼟的化学组成主要是什么?主要化学成分为SiO2、A12O3和结晶⽔(H2O)。
分别说明氧化铝、⼆氧化硅、氧化铁/⼆氧化钛、碱⾦属/碱⼟⾦属氧化物、有机质对粘⼟烧结的影响(1)SiO2 :若以游离⽯英状态存在的SiO2多时,黏⼟可塑性降低,但是⼲燥后烧成收缩⼩。
(2)Al2O3 :含量多,耐⽕度增⾼,难烧结。
(3)Fe2O3<1%,TiO2 <0.5%:瓷制品呈⽩⾊,含量过⾼,颜⾊变深,还影响电绝缘性。
(4)CaO、MgO、K2O、Na2O:降低烧结温度,缩⼩烧结范围。
(5)H2O、有机质:可提⾼可塑性,但收缩⼤。
7. 粘⼟中根据矿物的性质和数量可以分为哪两类?哪些是有益杂质矿物,哪些是有害杂质?根据性质和数量分为两⼤类:黏⼟矿物和杂质矿物有益杂质:⽯英、长⽯有害杂质:碳酸盐、硫酸盐、⾦红⽯、铁质矿物8. 指出碳酸盐、硫酸盐对陶瓷烧结的影响碳酸盐主要是⽅解⽯、菱镁矿;硫酸盐主要是⽯膏、明矾⽯等。
⼀般影响不⼤,但以较粗的颗粒存在时。
贝壳结构仿生——陶瓷基复合材料

贝壳的结构仿生——层状陶瓷基复合材料摘要论述了贝壳的结构仿生材料——层状陶瓷复合材料的性能特点,从基体及夹层材料的类型选择推ヅ洹⒔峁股杓啤⒐ひ詹问 难∪⒃鋈偷幕 啤⒅票阜椒ǖ确矫娼樯芰说鼻安阕刺沾芍票腹ひ占际醯难芯拷 梗淮有阅芗敖峁沟确矫嫣教至嗽诟春喜牧戏⒄怪心壳按嬖诘奈侍狻?关键词:贝壳仿生;层状复合陶瓷;基体材料;夹层材料;增韧机制;制备方法引言众所周知,陶瓷材料具有耐高温、耐磨损、耐腐蚀、重量轻等很多优点,在能源、冶金、石油化工、航天航空等领域有着广泛的应用前景。
但是,陶瓷材料本身脆性大,对缺陷十分敏感,导致使用可靠性和可重复性差,限制了其应用。
因此增加陶瓷材料的韧性提高其使用可靠性,一直是结构陶瓷材料研究的重点。
陶瓷的层状复合是大自然中贝壳等生物材料的一种结构仿生设计。
贝壳类生物材料是由95以上的脆性文石晶体和少量的壳角蛋白以强弱相间的层状形式复合而成的这种结构具有比一般文石晶体高得多的综合机械性能。
层状复合陶瓷也是在脆性的陶瓷层间加入不同材质的较软或较韧的材料层制成。
这种结构的材料在应力场中是一种能量耗散结构能克服陶瓷突发性断裂的致命缺点。
当材料受到弯曲或冲击时裂纹多次在层界面处受到阻碍而钝化和偏折有效地减弱了载荷下裂纹尖端的应力集中效应。
同时这种材料的强度受缺陷影响较小是一种耐缺陷材料。
这种结构可使陶瓷的韧性得到很大改善。
1. 贝壳的结构和成分贝壳根据形成的方式和组成结构不同分为3层。
最外层为角质层,是硬蛋白质的一种,能耐酸的腐蚀;中间的棱柱壳层,它占据壳的大部分,由角柱状的方解石构成,角质层和棱柱层只能由外套膜背面边缘分泌而成;内层为珍珠层,也由角柱状方解石构成,它由外套膜的全表面分泌形成,并随着贝类的生长而增厚,富有光泽,珍珠层是最强韧的部分。
珍珠层组成相的95是文石晶体(正交结构碳素钙),其余是有机基质和少量的水,因此,它是一种天然的陶瓷基复合材料。
虽然贝壳珍珠层的组成中有近95是普通陶瓷碳酸钙,但其综合力学性能,特别是断裂韧性,比单个单相碳酸钙高2-3 个数量级,研究表明,其中的文石晶体呈多边形。
氮化硅陶瓷增韧调研报告

氮化硅陶瓷增韧调研报告1、前言氮化硅陶瓷是典型的高温高强结构陶瓷,具有良好的室温及高温机械性能,强度高,耐磨蚀,抗热震能力强,抗化学腐蚀,低导热系数,密度相对较小,是结构陶瓷中研究最为广泛深入的材料,亦是陶瓷发动机及其它高温结构件、切削工具、耐磨件等的主要候选材料,近几年来仍是人们争相研究的热点材料之一。
但是,已有的研究对氮化硅陶瓷的脆性缺陷仍未获得彻底改善,从而大大限制了它的实际应用。
如何提高氮化硅韧性仍是人们研究的焦点。
目前从事氮化硅陶瓷研究的学者为了提高其韧性,主要从两大方面着手进行韧性改善。
一是通过进行“显微结构设计”来提高氮化硅陶瓷的韧性。
即降低气孔的含量,控制杂质的含量,提高氮化硅陶瓷的密度、纯度;对氮硅陶瓷的晶型、晶粒尺寸、发育完整程度进行控制;对晶界的大小、材质进行调控;对玻璃相的数量、性质、分布状态等进行控制,以求在烧结后获得最佳韧性的显微组织,从而提高氮化硅陶瓷的韧性【1】。
二是在上述基础上开展的“晶界工程”研究。
氮化硅陶瓷常以多晶陶瓷的形式出现,而对多晶材料而言,当晶体较小为微米或纳米级时,晶界状态是决定其电性能、热性能和力学性能等的一个极其重要的因素。
对于氮化硅陶瓷来说,晶界强度,尤其是晶界高温强度是决定其能否作为高温工程材料运用的关键。
氮化硅是强共价键化合物,其自扩散系数很小,致密化所必须的体积扩散及晶界扩散速度很小,同时它的晶界能V gb与粉末表面能V sv的比值(V gb/ V sv) 比离子化合物和金属要大得多,使得烧结驱动力Δv 较小,决定了纯氮化硅无法靠常规的固相烧结达到致密化,必须加入少量氧化物烧结助剂,在高温烧结过程中它们与氮化硅表面SiO2反应形成液相,通过液相烧结成致密体,冷却后该液相呈玻璃态存在于晶界。
而此玻璃相的性能在很大程度上决定了氮化硅陶瓷材料的性能。
为了提高氮化硅陶瓷的高温性能,人们对玻璃晶界结晶化进行了大量的研究工作,称之为“晶界工程”【2】。
Al2O3陶瓷

3.2.1 Al2O3结构陶瓷概念和分类
定义:以-Al2O3为主晶相的结构陶瓷
Al2O3 含量= 75.0~99.9%
分类:依据配料中Al2O3含量 75瓷,85瓷,95瓷,99瓷
Al2O3
3.3.2 性质与用途
Al2O3结构陶瓷的性质
Tm=20500C 莫氏硬度: 9 膨胀系数(10-6/℃,20~100 ℃ ):8.0, 与金 属接近 体积密度v (g/cm3) : 3.70 抗弯强度(MPa): 385 抗张强度(MPa, 1000℃ ): 245 弹性模量(GPa): >300 比体积电阻(cm/1000C ): >1014 化学稳定性良好
图5.16 刚玉瓷的两种烧成制度 p145
2)烧成气氛 Po2 愈低愈有利于烧结—有利于烧结的顺序: (好) Ar H2 NH3 O2 N2 空气 (坏) 对于晶粒长大的作用顺序: (小) Ar 空气 N2 O2 H2 NH3 (大) 氨气和氢气会加速氧化铝的重结晶作用,不利于烧结。 3)烧结方法 为使Al2O3瓷完全烧结—热压烧结 ~1000℃,制品接近理论密度 否则,即使在1800℃,也很难完全烧结
氧化铝陶瓷的低温烧结工艺
液相烧结 热等静压烧结法 微波加热烧结法 热压烧结 微波等离子体烧结 放电等离子烧结
3.2.5 氧化铝陶瓷的组成、结构、工艺与性能之间的关系
影响氧化铝陶瓷性能的因素
粉体原料(主料和辅料)的化学组成与含量、形状、 大小、结合关系、晶体结构类型与含量;(粉体制备 技术) 制备陶瓷的工艺制度和工艺设备; 成型制度 烧结制度 冷加工技术 陶瓷制品的显微形貌、物相等。
陶瓷基复合材料

陶瓷基复合材料论文2015年5月5日摘要:陶瓷基复合材料主要以高性能陶瓷为基体.通过加入颗粒、晶须、连续纤维和层状材料等增强体而形成的复合材料。
如碳化硅、氮化硅、氧化铝等,具有耐高温、耐腐蚀、高强度、重量轻和价格低等优点。
陶瓷基复合材料的研究还处于较初级阶段,我国对陶瓷基复合材料的研究则刚刚起步不久。
关键词:陶瓷基复合材料基体增强体强韧化机理制备技术前言:陶瓷基复合材料是以陶瓷为基体与各种纤维复合的一类复合材料。
陶瓷基体可为氮化硅、碳化硅等高温结构陶瓷。
这些先进陶瓷具有耐高温、高强度和刚度、相对重量较轻、抗腐蚀等优异性能,而其致命的弱点是具有脆性,处于应力状态时,会产生裂纹,甚至断裂导致材料失效。
而采用高强度、高弹性的纤维与基体复合,则是提高陶瓷韧性和可靠性的一个有效的方法。
纤维能阻止裂纹的扩展,从而得到有优良韧性的纤维增强陶瓷基复合材料。
陶瓷基复合材料具有优异的耐高温性能,主要用作高温及耐磨制品。
其最高使用温度主要取决于基体特征。
正文一、陶瓷基复合材料基本概述陶瓷基复合材料的基体为陶瓷。
如碳化硅、氮化硅、氧化铝等,具有耐高温、耐腐蚀、高强度、重量轻和价格低等优点。
化学键往往是介于离子键与共价键之间的混合键。
陶瓷基复合材料中的增强体通常也称为增韧体。
从几何尺寸上可分为纤维(长、短纤维)、晶须和颗粒三类。
碳纤维主要用在把强度、刚度、重量和抗化学性作为设计参数的构件;其它常用纤维是玻璃纤维和硼纤维。
纤维增强陶瓷基复合材料是改善陶瓷材料韧性的重要手段。
目前常用的晶须是SiC和A12O3,常用的基体则为A12O3,ZrO2,SiO2,Si3N4以及莫来石等。
晶须具有长径比,含量较高时,桥架效应使致密化困难,引起了密度的下降导致性能下降。
颗粒代替晶须在原料的混合均匀化及烧结致密化方面均比晶须增强陶瓷基复合材料要容易。
常用的颗粒也是SiC、Si3N4和A12O3等。
陶瓷基复合材料发展迟滞,发展过程中也遇到了比其它复合材料更大的困难。
陶瓷的烧结方法1

陶瓷材料的烧结方法摘要:陶瓷材料的烧结方法是决定其最终性能的关键技术,本文系统的介绍、分析了目前陶瓷材料所采用的各种烧结方法的机理、工艺、影响因素、特点及其使用范围,为陶瓷材料烧结方法的选择提供参考。
关键词:陶瓷材料,烧结方法1:前言1:作为“面向二十一世纪的新材料〞,陶瓷材料的开发与研究是目前世界各主要工业国共同共注的焦点之一。
烧结是陶瓷材料坯件消费的最后一道工序,也决定着坯件的最终性能。
因此,慎重的选择烧结方法、严格的控制烧结过程是非常重要的。
二:正文2:陶瓷材料的烧结方法陶瓷材料的烧结方法一般可分为:常规烧结、反响烧结、气氛压力烧结、热压烧结、热等静压烧结、微波烧结、放电等离子烧结及高温自蔓延烧结等。
2.1:常规烧结:常规烧结一般采用常规加热方式,在传统电炉中进展,是目前陶瓷材料消费中最常采用的烧结方法。
由于纯的陶瓷材料有时很难烧结,所以性能允许的条件下,通常引入一些烧结助剂,以期形成局部低熔点的固溶体、玻璃相或其他液相,促进颗粒的重排和粘性流动,从而获得致密的产品,同时也可以降低烧结温度。
在氧化铝的烧结中参加TiO2、Cr2O3、Fe2O3、MnO2等可形成固溶体,这类氧化物有与氧化物相近的晶格常数,同时是变价氧化物。
由于变价作用,使氧化铝内部产生晶体缺陷,活化晶格,促进烧结。
例如:参加0.5~1%的二氧化钛、钛离子和铝离子的离子半径相近〔钛离子半径0,064nmm〕因此钛离子极易取代铝离子而形成二氧化钛—三氧化二铝固溶体,并引起晶格畸变。
另外为了到达电荷平衡,必定会留下空位,这就更有利于烧结。
同时,当二氧化钛—三氧化二铝到高温时,Ti4+会复原为Ti3+,而Ti3+ 的离子半径更大,这使得三氧化二铝晶格的歪斜、扭曲比Ti4+引起的更严重。
由于Ti4+和Ti3+的综合作用,可使烧结温度降低150~200度。
在Si3N4的烧结中可参加适量的MgO、Y2O3—Al2O3稀土元素氧化物、碳化物、硅化物添加剂。
陶瓷材料结构及性能分类新结构陶瓷材料科学基础

二、陶瓷材料的分类
1、按化学成分分类 可将陶瓷材料分为氧化物陶瓷、碳化物陶瓷、 氮化物陶瓷及其它化合物陶瓷。
玻璃幕 墙 导电玻 璃
2、按使用的原材料分类
可将陶瓷材料分为普通陶瓷和特种陶瓷。
普通陶瓷以天然的岩石、 矿石、黏土等材料作原 料。 特种陶瓷采用人工合成 的材料作原料。 3、按性能和用途分类 可将陶瓷材料分为结构 陶瓷和功能陶瓷两类。
玻璃相结构特点:硅氧四面体组成不规则的空间 网, 形成玻璃的骨架。 玻璃相成分:氧化硅和其它氧化物
(三)、气相
气相是陶瓷内部残留的孔洞;成因复杂,影 响因素多。 陶瓷根据气孔率分致密陶瓷、无开孔陶瓷 和多孔陶瓷。 气孔对陶瓷的性能不利(多孔陶瓷除外) 气孔率:普通陶瓷5%~10% 特种陶瓷5%以下 金属陶瓷低于0.5%。
(2) 硅酸盐化合物的几种类型
按照连接方式划分,硅酸盐化合物可以分为以下几 种类型: ①孤立状硅酸盐 ②复合状硅酸盐 ③环状或链状硅酸盐 ④层状硅酸盐 ⑤立体网络状硅酸盐
①孤立状硅酸盐(岛状结构单元)
其单元体(SiO44-) 互相独立,不发生相 互连接。 化学组成一般可以表 示为2RO· 2。 SiO 其中RO表示金属氧化 物如MgO、CaO、 FeO等。 具有这类结构的有橄 榄石和石榴石等。
AX化合物的特征是:A和X原子或离子 是高度有序的,属于这类结构的有: (1)CsCl型 (2)NaCl型 (3) ZnS闪锌矿型 (4)纤维锌矿型
(以下分别介绍)
(1)CsCl型 这种化合物的结构见图3-2。A原子(或离 子)位于8个X原子的中心,X原子(或离子) 也处于8个A原子的中心。但应该注意的是, 这种结构并不是体心立方的。确切的说,它 是简单立方的,它相当于把简单立方的A原 子和X原子晶格相对平移a/2,到达彼此的 中心位置而形成。
陶瓷基复合材料综述报告

陶瓷基复合材料综述报告陶瓷基复合材料是以陶瓷为基体与各种纤维复合的一类复合材料,具有优异的耐高温性能,主要用作高温及耐磨制品。
陶瓷基体可为氮化硅、碳化硅等高温结构陶瓷。
这些先进陶瓷具有耐高温、高强度和刚度、相对重量较轻、抗腐蚀等优异性能,而其致命的弱点是具有脆性,处于应力状态时,会产生裂纹,甚至断裂导致材料失效。
而采用高强度、高弹性的纤维与基体复合,则是提高陶瓷韧性和可靠性的一个有效的方法。
纤维能阻止裂纹的扩展,从而得到有优良韧性的纤维增强陶瓷基复合材料。
迄今,陶瓷基复合材料已实用化或即将实用化的领域有刀具、滑动构件、发动机制件、能源构件等。
有些发达国家已将长纤维增强碳化硅复合材料应用于制造高速列车的制动件,显示出优异的摩擦磨损特性,取得了不错的使用效果[1]。
一、陶瓷基复合材料增强体用于复合材料的增强体品种很多,根据复合材料的性能要求,主要分为以下几种[2-4] :1.1纤维类增强体纤维类增强体有连续长纤维和短纤维。
连续长纤维的连续长度均超过数百。
纤维性能有方向性,一般沿轴向均有很高的强度和弹性模量。
1.2颗粒类增强体颗粒类增强体主要是一些具有高强度、高模量。
耐热、耐磨。
耐高温的陶瓷等无机非金属颗粒,主要有碳化硅、氧化铝、碳化钛、石墨。
细金刚石、高岭土、滑石、碳酸钙等。
主要还有一些金属和聚合物颗粒类增强体,后者主要有热塑性树脂粉末1.3晶须类增强体晶须是在人工条件下制造出的细小单晶,一般呈棒状,其直径为0.2~1微米,长度为几十微米,由于其具有细小组织结构,缺陷少,具有很高的强度和模量。
1.4金属丝用于复合材料的高强福、高模量金属丝增强物主要有铍丝、钢丝、不锈钢丝和钨丝等,金属丝一般用于金属基复合材料和水泥基复合材料的增强,但前者比较多见。
1.5片状物增强体用于复合材料的片状增强物主要是陶瓷薄片。
将陶瓷薄片叠压起来形成的陶瓷复合材料具有很高的韧性。
二、陶瓷基的界面及强韧化理论陶瓷基复合材料(CMC)具有高强度、高硬度、高弹性模量、热化学稳定性等优异性能,被认为是推重比10以上航空发动机的理想耐高温结构材料。
【国家自然科学基金】_层状陶瓷_基金支持热词逐年推荐_【万方软件创新助手】_20140802

2011年 序号 1 2 3 4 5 6 7 8 9 10 11 12 13 14 15 16 17 18 19 20 21 22 23 24 25 26 27 28 29 30 31 32 33 34 35 36 37 38 39 40 41 42 43 44 45 46 47 48 49 50 51 52
2010年 序号 1 2 3 4 5 6 7 8 9 10 11 12 13 14 15 16 17 18 19 20 21 22 23 24 25 26 27 28 29 30 31 32 33 34 35 36 37 38 39 40 41
科研热词 推荐指数 等离子喷涂 6 激光重熔 6 纳米结构 2 热腐蚀 2 微观组织 2 陶瓷涂层 1 表面改性 1 腐蚀性能 1 缺陷 1 组织结构 1 纳米陶瓷涂层 1 纳米sic颗粒 1 稀土 1 碳化 1 熔盐法 1 热震稳定性 1 热障涂层 1 激光熔覆 1 淬火 1 氧化镁粉体 1 机电性能 1 机理 1 抗冲蚀性能 1 微观结构 1 层状钙钛矿 1 层状结构 1 层状多孔氧化铝/氧化锆陶瓷 1 失效机理 1 复合陶瓷 1 压电陶瓷 1 剩余极化 1 凝胶注模 1 wc陶瓷涂层 1 tio2纳米陶瓷涂层 1 tial合金 1 tia1合金 1 curie温度 1 bi4ti3o12 1 al2o3-13%tio2陶瓷涂层 1 al2o3-13%tio2纳米陶瓷涂层 1 a12o3-13 1
1 1 1 1 1 1
2011年 科研热词 推荐指数 等离子喷涂 3 复合材料 3 纳米陶瓷 2 热障涂层 2 氧化锆 2 氧化铝 2 晶体结构 2 显微组织 2 抗冲蚀性能 2 性能 2 弯曲强度 2 层状复合材料 2 ti3sic2 2 高温结构材料 1 隧道防火涂料 1 陶瓷涂层 1 钢结构建筑防火涂料 1 钙钛矿结构 1 金属间化合物 1 超重力 1 自蔓延高温合成 1 羟基磷灰石 1 纳米结构 1 矫顽场 1 燃烧合成 1 热压法 1 激光重熔 1 无铅 1 干燥参数 1 差热分析 1 居里温度 1 层状孔结构 1 多孔材料 1 多孔sic陶瓷 1 增强材料 1 基体 1 原位反应烧结 1 升华时间 1 冷冻温度 1 冷冻干燥工艺 1 冷冻干燥 1 冲蚀破坏机理 1 关键技术 1 介电性能 1 产业化 1 ticxn1-x-tib2复合陶瓷 1 tial合金 1 ti3alc2 1 si 1 nb-al系 1 k-值法 1 (k0.45na0.55)nbo3晶体 1
焊工应知题库(高级技师)及答案
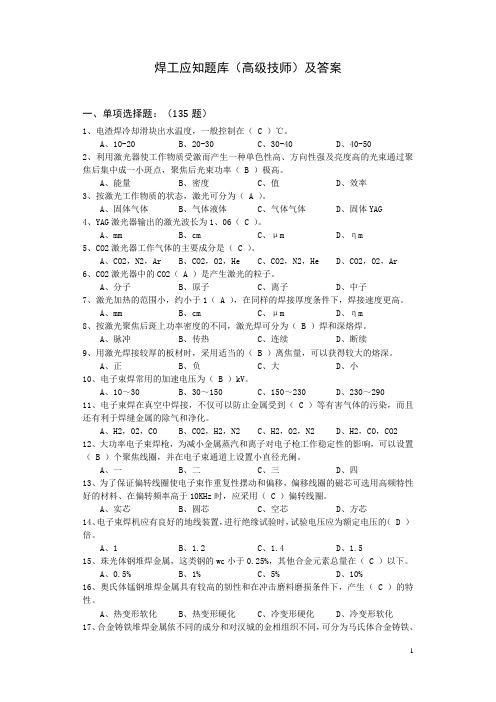
焊工应知题库(高级技师)及答案一、单项选择题:(135题)1、电渣焊冷却滑块出水温度,一般控制在( C )℃。
A、10-20B、20-30C、30-40D、40-502、利用激光器使工作物质受激而产生一种单色性高、方向性强及亮度高的光束通过聚焦后集中成一小斑点,聚焦后光束功率( B )极高。
A、能量B、密度C、值D、效率3、按激光工作物质的状态,激光可分为( A )。
A、固体气体B、气体液体C、气体气体D、固体YAG4、YAG激光器输出的激光波长为1、06( C )。
A、mmB、cmC、μmD、ηm5、CO2激光器工作气体的主要成分是( C )。
A、CO2,N2,ArB、CO2,O2,HeC、CO2,N2,HeD、CO2,O2,Ar6、CO2激光器中的CO2( A )是产生激光的粒子。
A、分子B、原子C、离子D、中子7、激光加热的范围小,约小于1( A ),在同样的焊接厚度条件下,焊接速度更高。
A、mmB、cmC、μmD、ηm8、按激光聚焦后斑上功率密度的不同,激光焊可分为( B )焊和深熔焊。
A、脉冲B、传热C、连续D、断续9、用激光焊接较厚的板材时,采用适当的( B )离焦量,可以获得较大的熔深。
A、正B、负C、大D、小10、电子束焊常用的加速电压为( B )kV。
A、10~30B、30~150C、150~230D、230~29011、电子束焊在真空中焊接,不仅可以防止金属受到( C )等有害气体的污染,而且还有利于焊缝金属的除气和净化。
A、H2,O2,COB、CO2,H2,N2C、H2,O2,N2D、H2,CO,CO212、大功率电子束焊枪,为减小金属蒸汽和离子对电子枪工作稳定性的影响,可以设置( B )个聚焦线圈,并在电子束通道上设置小直径光阑。
A、一B、二C、三D、四13、为了保证偏转线圈使电子束作重复性摆动和偏移,偏移线圈的磁芯可选用高频特性好的材料、在偏转频率高于10KHz时,应采用( C )偏转线圈。
氮化硅陶瓷化学式
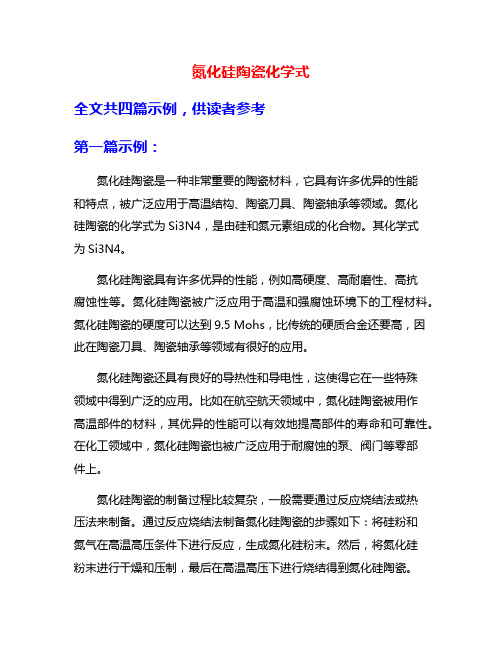
氮化硅陶瓷化学式全文共四篇示例,供读者参考第一篇示例:氮化硅陶瓷是一种非常重要的陶瓷材料,它具有许多优异的性能和特点,被广泛应用于高温结构、陶瓷刀具、陶瓷轴承等领域。
氮化硅陶瓷的化学式为Si3N4,是由硅和氮元素组成的化合物。
其化学式为Si3N4。
氮化硅陶瓷具有许多优异的性能,例如高硬度、高耐磨性、高抗腐蚀性等。
氮化硅陶瓷被广泛应用于高温和强腐蚀环境下的工程材料。
氮化硅陶瓷的硬度可以达到9.5 Mohs,比传统的硬质合金还要高,因此在陶瓷刀具、陶瓷轴承等领域有很好的应用。
氮化硅陶瓷还具有良好的导热性和导电性,这使得它在一些特殊领域中得到广泛的应用。
比如在航空航天领域中,氮化硅陶瓷被用作高温部件的材料,其优异的性能可以有效地提高部件的寿命和可靠性。
在化工领域中,氮化硅陶瓷也被广泛应用于耐腐蚀的泵、阀门等零部件上。
氮化硅陶瓷的制备过程比较复杂,一般需要通过反应烧结法或热压法来制备。
通过反应烧结法制备氮化硅陶瓷的步骤如下:将硅粉和氮气在高温高压条件下进行反应,生成氮化硅粉末。
然后,将氮化硅粉末进行干燥和压制,最后在高温高压下进行烧结得到氮化硅陶瓷。
第二篇示例:氮化硅陶瓷化学式为Si3N4,是一种先进的高性能陶瓷材料,具有优异的耐磨、耐腐蚀和耐高温性能。
氮化硅陶瓷是由硅原子和氮原子组成的二元化合物,具有特殊的晶体结构和化学性质,被广泛应用于航空航天、汽车工业、电子电器等领域。
氮化硅陶瓷化学式Si3N4的结构特点主要包括以下几个方面:1. 晶体结构:氮化硅陶瓷的晶体结构为β-Si3N4,属于非氧化物陶瓷材料,具有多种晶体相,其中β相为最稳定的结构。
β-Si3N4晶体结构具有层状结构,硼原子和氮原子呈交替排列,硅原子则位于层状结构之间。
2. 化学性质:氮化硅陶瓷具有很高的硬度和抗压强度,能够耐受极端的高温和腐蚀环境,具有优异的化学稳定性和热稳定性。
氮化硅陶瓷还具有优异的绝缘性能和磁性能,可以在高温高频环境下稳定工作。
碳化硅和氮化硅硬度

碳化硅和氮化硅硬度引言:碳化硅和氮化硅是两种重要的陶瓷材料,具有优异的物理和化学性质。
其中一个值得关注的特性是它们的硬度。
本文将比较碳化硅和氮化硅的硬度,并探讨其在不同领域的应用。
一、碳化硅的硬度碳化硅是一种具有高硬度的陶瓷材料。
它的硬度值通常在9到9.5之间,接近于天然金刚石。
这使得碳化硅成为一种理想的耐磨材料,常被用于制作切削工具、轴承和磨料。
碳化硅的高硬度可以归因于其晶体结构的特殊性。
碳化硅的晶格结构由碳和硅原子组成,硬度主要取决于碳和硅原子之间的键合强度。
碳原子与硅原子之间的键强度较高,因此使得碳化硅具有出色的硬度。
二、氮化硅的硬度与碳化硅相比,氮化硅的硬度稍低。
氮化硅的硬度值通常在8到9之间,略低于碳化硅。
然而,这仍然是非常高的硬度值,使得氮化硅在一些特定应用中非常有用。
氮化硅的硬度也与其晶体结构有关。
氮化硅的晶格结构由氮和硅原子组成,硬度主要取决于氮和硅原子之间的键合强度。
尽管氮化硅的硬度稍低于碳化硅,但它仍然具有优异的耐磨性和耐高温性能。
三、碳化硅和氮化硅的应用1. 切削工具:碳化硅的高硬度使其成为理想的切削工具材料。
它可以用于加工高硬度材料,如钢和铁。
氮化硅也常用于切削工具的制造,尤其是对高速切削和高温切削要求较高的场合。
2. 陶瓷轴承:碳化硅和氮化硅都具有优异的耐磨性和高温性能,使其成为制造陶瓷轴承的理想材料。
这些陶瓷轴承可以在高速和高温环境下运行,并具有较长的使用寿命。
3. 磨料:碳化硅和氮化硅都被广泛用作磨料。
它们的高硬度使得它们可以用于磨削和抛光不同材料的表面。
此外,它们还具有优异的耐磨性和热稳定性,使得它们在高温和高压条件下也能保持良好的性能。
4. 其他应用:碳化硅和氮化硅还在许多其他领域得到应用,如电子器件、光学材料和高温结构材料等。
它们的硬度和耐高温性能使它们成为这些领域中不可或缺的材料。
结论:碳化硅和氮化硅都是具有优异硬度的陶瓷材料。
碳化硅的硬度接近于天然金刚石,而氮化硅的硬度略低于碳化硅。
碳化硅和氮化硅的物理学和应用

碳化硅和氮化硅的物理学和应用摘要碳化硅(SiC)和氮化硅(GaN)是两种重要的半导体材料,具有许多优异的物理和化学特性。
在本文中,我们将讨论它们的物理学和应用。
我们将首先介绍它们的基本结构和特性,然后讨论它们在电子、光电、能源和生物医学领域的应用。
我们将重点讨论它们的优点、挑战和未来发展方向。
引言碳化硅和氮化硅是两种广泛应用的半导体材料。
它们具有优异的物理和化学特性,如高热导率、高击穿场强、高电子迁移率、宽带隙和高硬度等。
它们的物理性质可以根据晶体结构、晶体缺陷和表面形貌等因素进行调控,从而满足不同应用需求。
本文将对碳化硅和氮化硅的物理学和应用进行介绍和讨论。
碳化硅2.1 基本结构碳化硅是一种化合物半导体,由硅和碳元素组成。
它的晶体结构有两种常见的形式:立方晶系(3C-SiC)和六方晶系(6H-SiC和4H-SiC)。
其中,4H-SiC和6H-SiC是最常用的两种多晶形式,具有层状结构和非常优良的电学性能。
4H-SiC和6H-SiC的晶体结构如图1所示。
图1. 4H-SiC和6H-SiC的晶体结构。
2.2 物理特性碳化硅具有一系列优异的物理特性,如高硬度、高热导率、高击穿场强和高电子迁移率等。
这些特性使其在电子、光电、能源和生物医学等领域得到广泛应用。
2.2.1 电学性能碳化硅具有宽带隙(约3.2 eV),因此可以在高温和高电场下工作。
同时,碳化硅的电子迁移率比硅高3倍以上,使得其在高频和高功率应用中具有较好的性能。
此外,碳化硅的击穿场强比硅高10倍以上,使其在高电压应用中具有较好的可靠性和稳定性。
2.2.2 光学性能碳化硅的宽带隙使其具有优异的光学性能,可以在紫外光至红外光谱范围内工作。
其高透过率、低损耗和高辐射抗性等特性使得碳化硅在高功率激光器、紫外光电探测器和太阳能电池等领域得到广泛应用。
2.2.3 热学性能碳化硅的热导率比硅高4倍以上,可以在高温下快速散热。
同时,碳化硅的热膨胀系数低,可以减小温度变化对器件的影响。
氮化硅陶瓷基板高温分解温度

氮化硅陶瓷基板是一种高性能陶瓷材料,具有优异的耐高温、耐腐蚀、耐磨损等特性,广泛应用于航空航天、汽车、电子、电力等领域。
其高温分解温度是材料使用过程中的一个重要性能指标,直接关系到材料的使用温度范围和使用寿命。
氮化硅陶瓷基板的高温分解温度是指其在高温下开始分解的温度,即材料开始失去其结构和物理性能的温度。
对于氮化硅陶瓷基板,其高温分解温度通常在1200℃以上。
具体来说,氮化硅陶瓷基板在1200℃时仍能保持其基本的物理和化学性质,而当温度升高到1300℃左右时,其结构和性能开始发生变化,逐渐失去其稳定性。
氮化硅陶瓷基板的高温分解温度受到多种因素的影响,包括材料的成分、制备工艺、热处理温度等。
其中,制备工艺对高温分解温度的影响较大。
采用不同的制备工艺,可以得到具有不同高温分解温度的氮化硅陶瓷基板。
此外,热处理温度也会对高温分解温度产生影响。
通过适当的热处理可以提高氮化硅陶瓷基板的稳定性,使其能够在更高的温度下使用。
在实际使用过程中,氮化硅陶瓷基板的高温分解温度与其使用环境密切相关。
例如,在高温、高压、腐蚀等恶劣环境下,氮化硅陶瓷基板的高温分解温度可能会降低。
因此,在使用过程中需要根据具体的使用环境和要求来确定氮化硅陶瓷基板的适用范围和寿命。
总之,氮化硅陶瓷基板的高温分解温度是衡量其性能的重要指标之一。
在实际使用过程中,需要根据具体的使用环境和要求来确定其适用范围和寿命。
同时,通过改进制备工艺和采用适当的热处理技术可以提高氮化硅陶瓷基板的稳定性,使其能够在更高的温度下使用。
锂电池隔膜分类
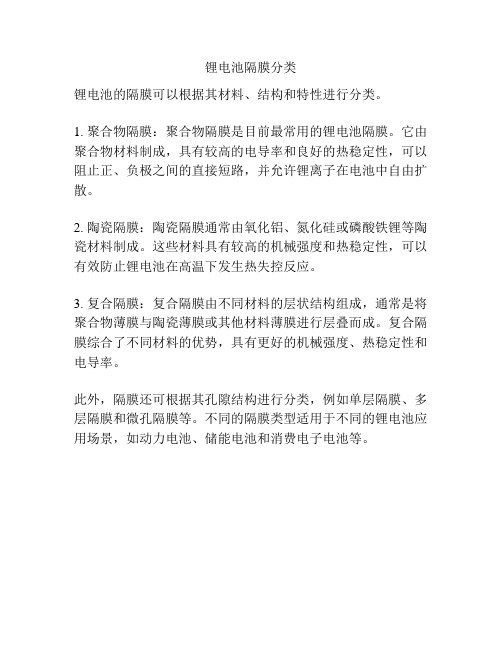
锂电池隔膜分类
锂电池的隔膜可以根据其材料、结构和特性进行分类。
1. 聚合物隔膜:聚合物隔膜是目前最常用的锂电池隔膜。
它由聚合物材料制成,具有较高的电导率和良好的热稳定性,可以阻止正、负极之间的直接短路,并允许锂离子在电池中自由扩散。
2. 陶瓷隔膜:陶瓷隔膜通常由氧化铝、氮化硅或磷酸铁锂等陶瓷材料制成。
这些材料具有较高的机械强度和热稳定性,可以有效防止锂电池在高温下发生热失控反应。
3. 复合隔膜:复合隔膜由不同材料的层状结构组成,通常是将聚合物薄膜与陶瓷薄膜或其他材料薄膜进行层叠而成。
复合隔膜综合了不同材料的优势,具有更好的机械强度、热稳定性和电导率。
此外,隔膜还可根据其孔隙结构进行分类,例如单层隔膜、多层隔膜和微孔隔膜等。
不同的隔膜类型适用于不同的锂电池应用场景,如动力电池、储能电池和消费电子电池等。
常用陶瓷原料的密度或比重

原料
比重/密度 g/cm3
备注
氮化硼BN
理论值:六方层状2.270
立方3.45
热导率 1300 W/m/K 石墨密度 2.266 金刚石密度 3.514
氮化铝 AlN
3.26
氮化硅 Si3N4
理论α- Si3N4 3.184 β- Si3N4 3.187
无熔点,常压下分解温度为1900℃左右
4.1
锡 Sn
7.3
231.9
0.0000230
14
钽 Ta
16.6
2996
0.0000065
12
钛 Ti
4.51
1677
0.0000090
3.4
钒 V
6.1
1910
0.0000083
6.4
钨 W
19.3
3400
0.0000043
29
熔点最高的金属
锌 Zn
7.014
419.5
0.0000395
27
锆 Zr
7.43
1244
0.0000230
0.9
铌 Nb
8.57
2468
0.0000071
12
常见金属材料的导热性比较
金属
热导率W/(m·K)
锂(Li)
84.7
铍
200
钠(Na)
141
镁
156
铝
237
钾
102.4
钙
200
钪
15.8
钛
21.9
钒
30.7
铬
93.7
锰
78.2
铁
80.2
- 1、下载文档前请自行甄别文档内容的完整性,平台不提供额外的编辑、内容补充、找答案等附加服务。
- 2、"仅部分预览"的文档,不可在线预览部分如存在完整性等问题,可反馈申请退款(可完整预览的文档不适用该条件!)。
- 3、如文档侵犯您的权益,请联系客服反馈,我们会尽快为您处理(人工客服工作时间:9:00-18:30)。
第25卷第5期硅 酸 盐 学 报V ol.25,N o.5 1997年10月JO U RN A L O F T HE CHIN ESE CERA M IC SO CIET Y O ct ober,1997 层状氮化硅陶瓷的性能与结构郭 海 黄 勇 李建保(清华大学材料科学与工程系)摘 要 从结构设计的角度出发研究了层状复合Si3N4陶瓷材料。
利用轧膜工艺使层内的晶粒、晶须产生定向增韧,通过调整外部层状复合结构得到材料的两级增韧效果,并实验制备了高韧性层状复合Si3N4基陶瓷材料。
主层内加入一定量的SiC晶须,层状氮化硅陶瓷的断裂韧性可达到20.11M Pa・m1/2。
关键词 氮化硅,层状复合,晶须,定向1 前 言制备高韧性的陶瓷材料,克服陶瓷灾难性的破坏,常用增韧方法的增韧效果非常有限。
为了提高增韧效果,降低增韧成本,新的增韧方法的探索是十分必要的。
近年来,国内外学者从生物界得到了启示。
贝壳具有的层状结构可以产生较大的韧性这一特点给了我们一些启发,除了从组分设计上选择不同的材料体系以外,更重要的一点就是可以从材料的宏观结构角度来设计新型材料。
目前国内外已有人从结构设计的角度出发,开始了层状复合陶瓷材料的探索性研究[1,2]。
对于层状复合陶瓷材料来讲,如果把每层看成块体材料的结构单元,则关键的技术问题在于:(1)材料各结构单元的强度、韧性优化;(2)界面结合层的选择及与结构单元的匹配。
层状结构单元基本上都是高强硬质的陶瓷材料如氮化硅、氧化铝等,通常是通过流延、干压等工艺方法制备的陶瓷薄片[3,4]。
而界面结合层的选择则种类繁多,如石墨、延性金属等,它们对陶瓷薄片起到一定的分隔作用[5]。
但总的来说,目前的研究结果并不令人满意,尚未达到单纯块体材料的性能水平。
针对层状复合陶瓷材料的两个关键问题,可以分别进行研究。
首先是改善材料结构单元的性能,由于层状复合材料具有明显的各向异性,因此可以设计结构单元具有同样的各向异性性能,如引入可能导致各向性能差异的晶须、纤维、晶种等,并使之按指定方向分布,就有可能在特定方向上得到较高的性能[6],对晶须定向陶瓷材料的各方向的性能差异的研究证实了这一假设。
其次是结构单元之间界面的选择,对层状复合陶瓷材料,界面的选择要同时考虑界面的高温性能、与陶瓷薄片的结合性能以及热匹配等多种因素,对不同的基片进行综合考虑,选择合适的界面组分及所占的比例。
1996年7月15日收到。
通讯联系人:郭 海,清华大学材料科学与工程系,北京 100084。
5322 实 验2.1 原 料制备Si3N4层状复合陶瓷,采用了国产(清华T H1)和日本产(UBE)两种粉料。
表1是这两种粉料的性能对比。
其中一种方案是将U BE粉料(加入7%Y2O3和3%Al2O3)在1850℃, 0.5MPa N2气氛下热处理1h[7],生成了长径比约为8的长柱状 Si3N4作为晶种,加到国产的 Si3N4中,以利于新生 Si3N4的生成和定向控制。
另一种方案则采用国产SiC晶须作为补强剂加入国产Si3N4中,加入量为20%(以质量计,下同),并采用Y2O3和Al2O3为助烧剂。
表1 原料氮化硅性能Table1 Properties of raw Si3N4Pow der Average particle siz e/ m Specific su rface area/m2・g-1M ain impurity conten t in the pow der w/% S i N O Fe Al C aUBE0.4312.06038.6 1.510.0050.0050.005 T H10.699.96033.4 5.520.530.260.102.2 制备工艺与测试制备Si3N4片层使用轧膜工艺。
以工业PVA(聚乙烯醇)为有机粘合剂,并加入适量的增塑剂和润滑剂,经粗轧混料,陈腐24h后精轧成厚度为0.2mm的薄片。
目前的层状复合Si3N4陶瓷材料多采用与Si3N4不发生反应的石墨薄片作为层片间的隔离材料,实验效果并不理想,隔层材料的厚度及与层片的结合强度均不易控制。
为此,采用与Si3N4具有相近热膨胀系数的BN为隔离材料,并加入适量的Al2O3以改变其与Si3N4层的结合强度。
将BN和A l2O3共同配制成悬浮液,采用浸涂的工艺,通过改变浸涂悬浮液的浓度及浸涂的时间来控制中间层的厚度。
涂层后的片层经叠层、干压预成型后,经400℃脱脂,采用1800℃,N2气氛,1h热压烧结,热压压力为25M Pa,烧成后经切割、磨削、抛光制成所需尺寸试条。
室温强度与断裂韧性测试用样品的尺寸分别为3mm×4mm×36mm及6m m×3mm×30m m,在岛津AG2000材料试验机上采用三点弯曲梁法进行测试。
强度与断裂韧性的测量方向均与叠层垂直,加载速率分别为0.5mm/min和0.05mm/min。
3 结果与讨论3.1 材料性能使用轧膜工艺制备的Si3N4薄片涂层后热压制成层状复合Si3N4基陶瓷材料,其性能与材料体系及界面的关系如表2所示。
可以看出,当材料内部引入了 Si3N4晶种和晶须以后,材料的断裂韧性有了极为显著的提高,从6.1M Pa・m1/2分别提高到11.37M Pa・m1/2(样品JZ0)和10.62M Pa・m1/2(样品JX0)。
这一方面是由于在晶种上新生 Si3N4晶粒和晶须本身所起到的增韧效果;另一方面可能是由于使用了轧膜工艺,陶瓷片层的厚度很薄,具有较大的各向异性的晶种和晶须在轧制过程中必然会产生在片层方向上的平铺,从而产生一定程度的二维定向效果,尤其是引入的 Si3N4晶粒,加入量虽然只有3%,但在氮化硅的液相烧533结过程中,它可以作为液相成核的核心,使得在很大程度上按晶种在坯体中的分布生成新的 Si3N4晶粒。
Hirao也曾采用流延的方法成功地制备了含有2%晶种的氮化硅片层,他非常清楚地观察到了在片层内晶粒的二维定向,利用这种片层制备的氮化硅陶瓷材料,其断裂韧性也可以达到11.1M Pa・m1/2[6]。
表2 层状复合Si3N4陶瓷材料的力学性能Table2 Mechanical properties of Si3N4laminated ceramicsSample Addition(in mass)Interface(in mas s) b/M Pa KⅠc/M Pa・m1/2 00—870 6.1JZ03% S i3N4—850.411.37JZ13% S i3N425%Al2O3+75%BN498.415.12J X020%SiC w—97210.62J X120%SiC w25%Al2O3+75%BN651.4720.11使用25%Al2O3和75%BN作为涂层隔离各氮化硅片层,就可以进一步引入材料的层状结构。
JZ1和JX1分别是片层内部含有 Si3N4晶种和SiC晶须,而在宏观上又具有层状结构的氮化硅基陶瓷材料。
由表2可以看出,这两种材料较JZ0和JX0在强度上均有较大的降低,但是其断裂韧性却得到了极为明显的提高,分别达到了15.12和20.11M Pa・m1/2,尤其是有层状结构的晶须增韧氮化硅基陶瓷材料,比无层状结构的同体系材料提高了将近一倍。
这是由于材料的特殊的层状结构,其内部较强的片层与较弱的界面交替排列,强的片层可以承受一定的应力,而弱的界面在裂纹扩展的过程中可以吸收大量的扩展能量,从而起到较好的增韧效果的缘故。
同时,由于材料内部存在着弱的界面,也必然会使材料的抗弯强度有所降低。
3.2 显微结构图1是层状复合Si3N4陶瓷材料的显微结构照片。
经脱脂陶瓷片层有机物挥发后再热压烧结,片层收缩,厚度由坯体时的0.2mm变为约0.1m m。
由图可以看出,间隔层与陶瓷主层交替排列,只有极少数区域由于涂层的不均匀,热压后上下主层发生粘接,间隔层被主层挤开。
同时可以明显观察到间隔层厚度不均匀,平均约为0.03mm,且并不完全致密,在其内部存在着大量微小的裂纹。
图2和图3分别是加入了晶种和晶须后的片层内部的显微结构。
可以看出,由于引入的晶种和晶须都具有较大的长径比,在轧膜过程中都会产生一定的定向。
经烧结后一部分新生的 Si3N4是以加入的晶种为晶核生长的晶粒,其长径比基本上保持原晶种的长径比,约为8左右。
这一部分晶粒和晶须均在热压面内平铺,具有了一定的定向效果。
这种二维的定向所起到的增韧作用已被许多研究所证实。
3.3 裂纹的扩展与增韧机理图4是JX1的裂纹扩展路径照片,可以清楚地看出造成材料韧性大幅度提高的原因。
当主裂纹受力扩展到达一层的边界时,一方面间隔层较弱,强度较低;另一方面在间隔层内部本身就存在着大量的微裂纹,主裂纹将首先沿界面扩展,造成了裂纹尖端的偏转与分叉。
主裂纹不再按原方向扩展,从客观上起到了减弱甚至终止裂纹纵向扩展的作用。
在图中可以看到几乎每两个陶瓷主层间主裂纹都会发生一个微小的错动;而数层以内则可能发生较大偏移,使裂纹扩展的路径成为明显的锯齿状。
这种特殊的裂纹扩展路径说明了该材料的增韧效果一534图1 层状复合Si 3N 4的显微结构F ig .1 M icr ostr uct ur e of Si 3N 4laminated ceramics 图2 加入晶种后Si 3N 4层片内部显微结构F ig.2 M icr ostr uct ur e o f sheets in Si 3N 4laminat -ed cer amics with seedsinside图3 加入晶须后Si 3N 4层片内部显微结构F ig.3 M icro str uctur e of sheet s in Si 3N 4lami-nated ceramics w it h w hiskersinside 图4 层状复合陶瓷材料JX 1中裂纹扩展的SEM 照片F ig.4 SEM micro gr aph o f cr ack pro pa gation in JX 1lam inated ceramics图5 层状复合陶瓷材料JZ1的载荷形变曲线Fig .5 Lo ad -deflectio n curv e for JZ 1laminated ce-r amics specimen方面来自于主层内晶粒、晶须的定向增韧,而另一方面则主要来自于这种主层间的裂纹的大幅度的偏转。
更为有用的是,材料的荷载形变曲线也因此而发生了极大的改变,不再是常规的陶瓷的一次脆性断裂,而变成了图5所见的多次断裂的形式,陶瓷的每一次断裂都不代表材料的破坏,而只是一个或几个陶瓷主层发生了破坏,继续加载,材料仍然可以承受一定的荷载(甚至高于断裂前的承载能力)。