化工和危险化学品企业安全生产重大事故隐患判别标准
化工和危险化学品生产经营单位重大生产安全事故隐患判定标准

化工和危险化学品生产经营单位重大生产安全事故隐患判定标准(试行)依据有关法律法规、部门规章和国家标准,以下情形应当判定为重大事故隐患:一、危险化学品生产、经营单位主要负责人和安全生产管理人员未依法经考核合格。
二、特种作业人员未持证上岗。
三、涉及“两重点一重大”的生产装置、储存设施外部安全防护距离不符合国家标准要求。
四、涉及重点监管危险化工工艺的装置未实现自动化控制,系统未实现紧急停车功能,装备的自动化控制系统、紧急停车系统未投入使用。
五、构成一级、二级重大危险源的危险化学品罐区未实现紧急切断功能;涉及毒性气体、液化气体、剧毒液体的一级、二级重大危险源的危险化学品罐区未配备独立的安全仪表系统。
六、全压力式液化烃储罐未按国家标准设置注水措施。
七、液化烃、液氨、液氯等易燃易爆、有毒有害液化气体的充装未使用万向管道充装系统。
八、光气、氯气等剧毒气体及硫化氢气体管道穿越除厂区(包括化工园区、工业园区)外的公共区域。
九、地区架空电力线路穿越生产区且不符合国家标准要求。
十、在役化工装置未经正规设计且未进行安全设计诊断。
十一、使用淘汰落后安全技术工艺、设备目录列出的工艺、设备。
十二、涉及可燃和有毒有害气体泄漏的场所未按国家标准设置检测报警装置,爆炸危险场所未按国家标准安装使用防爆电气设备。
十三、控制室或机柜间面向具有火灾、爆炸危险性装置一侧不满足国家标准关于防火防爆的要求。
十四、化工生产装置未按国家标准要求设置双重电源供电,自动化控制系统未设置不间断电源。
十五、安全阀、爆破片等安全附件未正常投用。
十六、未建立与岗位相匹配的全员安全生产责任制或者未制定实施生产安全事故隐患排查治理制度。
十七、未制定操作规程和工艺控制指标。
十八、未按照国家标准制定动火、进入受限空间等特殊作业管理制度,或者制度未有效执行。
十九、新开发的危险化学品生产工艺未经小试、中试、工业化试验直接进行工业化生产;国内首次使用的化工工艺未经过省级人民政府有关部门组织的安全可靠性论证;新建装置未制定试生产方案投料开车;精细化工企业未按规范性文件要求开展反应安全风险评估。
化工企业重大安全隐患判定标准

化工企业重大安全隐患判定标准化工和危险化学品生产经营单位重大生产安全事故隐患判定标准(试行)1危险化学品生产、经营单位主要负责人和安全生产管理人员未依法经考核合格。
2特种作业人员未持证上岗。
3涉及“两重点一重大”的生产装置、储存设施外部安全防护距离不符合国家标准要求。
4涉及重点监管危险化工工艺的装置未实现自动化控制,系统未实现紧急停车功能,装备的自动化控制系统、紧急停车系统未投入使用。
5构成一级、二级重大危险源的危险化学品罐区未实现紧急切断功能;涉及毒性气体、液化气体、剧毒液体的一级、二级重大危险源的危险化学品罐区未配备独立的安全仪表系统。
6全压力式液化烃储罐未按国家标准设置注水措施。
7液化烃、液氨、液氯等易燃易爆、有毒有害液化气体的充装未使用万向管道充装系统。
8光气、氯气等剧毒气体及硫化氢气体管道穿越除厂区(包括化工园区、工业园区)外的公共区域。
9地区架空电力线路穿越生产区且不符合国家标准要求。
10在役化工装置未经正规设计且未进行安全设计诊断。
11使用淘汰落后安全技术工艺、设备目录列出的工艺、设备。
12涉及可燃和有毒有害气体泄漏的场所未按国家标准设置检测报警装置,爆炸危险场所未按国家标准安装使用防爆电气设备。
13控制室或机柜间面向具有火灾、爆炸危险性装置一侧不满足国家标准关于防火防爆的要求。
14化工生产装置未按国家标准要求设置双重电源供电,自动化控制系统未设置不间断电源。
15安全阀、爆破片等安全附件未正常投用。
16未建立与岗位相匹配的全员安全生产责任制或者未制定实施生产安全事故隐患排查治理制度。
17未制定操作规程和工艺控制指标。
18未按照国家标准制定动火、进入受限空间等特殊作业管理制度,或者制度未有效执行。
19新开发的危险化学品生产工艺未经小试、中试、工业化试验直接进行工业化生产;国内首次使用的化工工艺未经过省级人民政府有关部门组织的安全可靠性论证;新建装置未制定试生产方案投料开车;精细化工企业未按规范性文件要求开展反应安全风险评估。
化工和危险化学品生产经营单位重大生产安全事故隐患判定标准

化工和危险化学品生产经营单位重大生产安全事故隐患判定标准(试行)依据有关法律法规、部门规章和国家标准,以下情形应当判定为重大事故隐患:一、危险化学品生产、经营单位主要负责人和安全生产管理人员未依法经考核合格。
二、特种作业人员未持证上岗。
三、涉及“两重点一重大”的生产装置、储存设施外部安全防护距离不符合国家标准要求。
四、涉及重点监管危险化工工艺的装置未实现自动化控制,系统未实现紧急停车功能,装备的自动化控制系统、紧急停车系统未投入使用。
五、构成一级、二级重大危险源的危险化学品罐区未实现紧急切断功能;涉及毒性气体、液化气体、剧毒液体的一级、二级重大危险源的危险化学品罐区未配备独立的安全仪表系统。
六、全压力式液化烃储罐未按国家标准设置注水措施。
七、液化烃、液氨、液氯等易燃易爆、有毒有害液化气体的充装未使用万向管道充装系统。
八、光气、氯气等剧毒气体及硫化氢气体管道穿越除厂区(包括化工园区、工业园区)外的公共区域。
九、地区架空电力线路穿越生产区且不符合国家标准要求。
十、在役化工装置未经正规设计且未进行安全设计诊断。
一、使用淘汰落后安全技术工艺、设备目录列出的工艺、设备。
二、涉及可燃和有毒有害气体泄漏的场所未按国家标准设置检测报警装置,爆炸危险场所未按国家标准安装使用防爆电气设备。
三、控制室或机柜间面向具有火灾、爆炸危险性装置一侧不满足国家标准关于防火防爆的要求。
四、化工生产装置未按国家标准要求设置双重电源供电,自动化控制系统未设置不间断电源。
五、安全阀、爆破片等安全附件未正常投用。
六、未建立与岗位相匹配的全员安全生产责任制或者未制定实施生产安全事故隐患排查治理制度。
七、未制定操作规程和工艺控制指标。
八、未按照国家标准制定动火、进入受限空间等特殊作业管理制度,或者制度未有效执行。
九、新开发的危险化学品生产工艺未经小试、中试、工业化试验直接进行工业化生产;国内首次使用的化工工艺未经过省级人民政府有关部门组织的安全可靠性论证;新建装置未制定试生产方案投料开车;精细化工企业未按规范性文件要求开展反应安全风险评估。
化工和危险化学品生产经营单位重大生产安全事故隐患判定标准

化工和危险化学品生产经营单位重大生产安全事故隐患判定标准化工和危险化学品生产经营单位是指从事化学工艺过程、原料、副产品、产品仓储以及配送等与化工和危险化学品生产经营活动有关的单位。
为了保障生产安全,防止重大生产安全事故的发生,国家制定了《化工和危险化学品生产经营单位重大生产安全事故隐患判定标准(试行)》。
一、重大生产安全事故隐患判定的基本原则1.生产过程:生产过程中存在的隐患包括工艺缺陷、操作不当、设备老化、维护不及时等问题。
2.现场管理:现场管理方面的隐患主要涉及消防管理、安全设施配备、应急预案和演练等方面。
3.安全环境:安全环境方面的隐患包括场址选址不当、环境治理不到位、周边安全隐患等问题。
4.其他因素:除了生产过程、现场管理和安全环境外,还应考虑其他因素对重大生产安全事故的影响,如管理体系、技术水平、人员素质等。
二、重大生产安全事故隐患判定的主要内容1.从事化学工艺过程、原料、副产品、产品仓储以及配送等与化工和危险化学品生产经营活动有关的单位,应严格按照标准规范进行隐患判定。
2.隐患判定应包括生产过程、现场管理和安全环境等方面的隐患。
3.生产过程方面的隐患判定应包括以下内容:a.工艺缺陷:包括工艺路线、工艺设施等方面的缺陷,如存在工艺不合理、设备不安全、操作不当等问题。
b.原料缺陷:包括原料品质、储存和使用等方面的缺陷,如存在原料不规范、储存条件差、使用方法错误等问题。
c.副产品缺陷:包括副产品的处理和处置等方面的缺陷,如存在对副产品尸体不当、处置方法不正确等问题。
d.产品仓储缺陷:包括产品储存和保管等方面的缺陷,如存在储存条件不合理、包装质量差等问题。
e.配送缺陷:包括产品配送和运输等方面的缺陷,如存在运输工具不合格、运输方式不安全等问题。
4.现场管理方面的隐患判定应包括以下内容:a.消防管理:包括消防设施、灭火器材、消防通道等方面的管理,如存在消防设施损坏、灭火器材不足、消防通道堵塞等问题。
安监总局解读-化工和危险化学品生产经营单位重大生产安全事故隐患判定规范标准20条

安监总局解读:化工和危险化学品生产经营单位重大生产安全事故隐患判定标准为准确判定、及时整改化工和危险化学品生产经营单位重大生产安全事故隐患(以下简称重大隐患),有效防范遏制重特大事故,根据《安全生产法》和《中共中央国务院关于推进安全生产领域改革发展的意见》,国家安全监管总局制定印发了《化工和危险化学品生产经营单位重大生产安全事故隐患判定标准(试行)》(以下简称《判定标准》)。
《判定标准》依据有关法律法规、部门规章和国家标准,吸取了近年来化工和危险化学品重大及典型事故教训,从人员要求、设备设施和安全管理三个方面列举了二十种应当判定为重大事故隐患的情形。
为进一步明确《判定标准》每一种情形的内涵及依据,便于有关企业和安全监管部门应用,规范推动《判定标准》有效执行,现逐条进行简要解释说明如下:一、危险化学品生产、经营单位主要负责人和安全生产管理人员未依法经考核合格。
近年来,在化工(危险化学品)事故调查过程中发现,事故企业不同程度地存在主要负责人和安全管理人员法律意识与安全风险意识淡薄、安全生产管理知识欠缺、安全生产管理能力不能满足安全生产需要等共性问题,人的因素是制约化工(危险化学品)安全生产的最重要因素。
危险化学品安全生产是一项科学性、专业性很强的工作,企业的主要负责人和安全生产管理人员只有牢固树立安全红线意识、风险意识,掌握危险化学品安全生产的基础知识、具备安全生产管理的基本技能,才能真正落实企业的安全生产主体责任。
《安全生产法》、《危险化学品安全管理条例》、《生产经营单位安全培训规定》(国家安全监管总局令第3号)均对危险化学品生产、经营单位从业人员培训和考核作出了明确要求,其中《安全生产法》第二十四条要求“生产经营单位的主要负责人和安全生产管理人员必须具备与本单位所从事的生产经营活动相应的安全生产知识和管理能力。
危险物品的生产、经营、储存单位以及矿山、金属冶炼、建筑施工、道路运输单位的主要负责人和安全生产管理人员,应当由主管的负有安全生产监督管理职责的部门对其安全生产知识和管理能力考核合格。
化工和危险化学品生产经营单位重大生产安全事故隐患判定标准
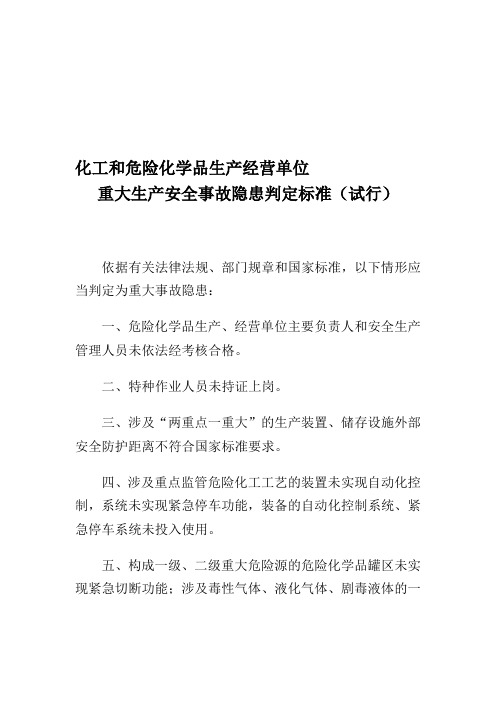
化工和危险化学品生产经营单位重大生产安全事故隐患判定标准(试行)依据有关法律法规、部门规章和国家标准,以下情形应当判定为重大事故隐患:一、危险化学品生产、经营单位主要负责人和安全生产管理人员未依法经考核合格。
二、特种作业人员未持证上岗。
三、涉及“两重点一重大”的生产装置、储存设施外部安全防护距离不符合国家标准要求。
四、涉及重点监管危险化工工艺的装置未实现自动化控制,系统未实现紧急停车功能,装备的自动化控制系统、紧急停车系统未投入使用。
五、构成一级、二级重大危险源的危险化学品罐区未实现紧急切断功能;涉及毒性气体、液化气体、剧毒液体的一级、二级重大危险源的危险化学品罐区未配备独立的安全仪表系统。
六、全压力式液化烃储罐未按国家标准设置注水措施。
七、液化烃、液氨、液氯等易燃易爆、有毒有害液化气体的充装未使用万向管道充装系统。
八、光气、氯气等剧毒气体及硫化氢气体管道穿越除厂区(包括化工园区、工业园区)外的公共区域。
九、地区架空电力线路穿越生产区且不符合国家标准要求。
十、在役化工装置未经正规设计且未进行安全设计诊断。
十一、使用淘汰落后安全技术工艺、设备目录列出的工艺、设备。
十二、涉及可燃和有毒有害气体泄漏的场所未按国家标准设置检测报警装置,爆炸危险场所未按国家标准安装使用防爆电气设备。
十三、控制室或机柜间面向具有火灾、爆炸危险性装置一侧不满足国家标准关于防火防爆的要求。
十四、化工生产装置未按国家标准要求设置双重电源供电,自动化控制系统未设置不间断电源。
十五、安全阀、爆破片等安全附件未正常投用。
十六、未建立与岗位相匹配的全员安全生产责任制或者未制定实施生产安全事故隐患排查治理制度。
十七、未制定操作规程和工艺控制指标。
十八、未按照国家标准制定动火、进入受限空间等特殊作业管理制度,或者制度未有效执行。
十九、新开发的危险化学品生产工艺未经小试、中试、工业化试验直接进行工业化生产;国内首次使用的化工工艺未经过省级人民政府有关部门组织的安全可靠性论证;新建装置未制定试生产方案投料开车;精细化工企业未按规范性文件要求开展反应安全风险评估。
3.4 化工和危险化学品生产经营单位重大生产安全事故隐患判定标准

化工和危险化学品生产经营单位重大生产安全事故隐患判定标准(试行)安监总管三【2017】121号依据有关法律法规、部门规章和国家标准,以下情形应当判定为重大事故隐患:一、危险化学品生产、经营单位主要负责人和安全生产管理人员未依法经考核合格。
二、特种作业人员未持证上岗。
三、涉及“两重点一重大”的生产装置、储存设施外部安全防护距离不符合国家标准要求。
四、涉及重点监管危险化工工艺的装置未实现自动化控制,系统未实现紧急停车功能,装备的自动化控制系统、紧急停车系统未投入使用。
五、构成一级、二级重大危险源的危险化学品罐区未实现紧急切断功能;涉及毒性气体、液化气体、剧毒液体的一级、二级重大危险源的危险化学品罐区未配备独立的安全仪表系统。
六、全压力式液化烃储罐未按国家标准设置注水措施。
七、液化烃、液氨、液氯等易燃易爆、有毒有害液化气体的充装未使用万向管道充装系统。
八、光气、氯气等剧毒气体及硫化氢气体管道穿越除厂区(包括化工园区、工业园区)外的公共区域。
九、地区架空电力线路穿越生产区且不符合国家标准要求。
十、在役化工装置未经正规设计且未进行安全设计诊断。
十一、使用淘汰落后安全技术工艺、设备目录列出的工艺、设备。
十二、涉及可燃和有毒有害气体泄漏的场所未按国家标准设置检测报警装置,爆炸危险场所未按国家标准安装使用防爆电气设备。
十三、控制室或机柜间面向具有火灾、爆炸危险性装置一侧不满足国家标准关于防火防爆的要求。
十四、化工生产装置未按国家标准要求设置双重电源供电,自动化控制系统未设置不间断电源。
十五、安全阀、爆破片等安全附件未正常投用。
十六、未建立与岗位相匹配的全员安全生产责任制或者未制定实施生产安全事故隐患排查治理制度。
十七、未制定操作规程和工艺控制指标。
十八、未按照国家标准制定动火、进入受限空间等特殊作业管理制度,或者制度未有效执行。
十九、新开发的危险化学品生产工艺未经小试、中试、工业化试验直接进行工业化生产;国内首次使用的化工工艺未经过省级人民政府有关部门组织的安全可靠性论证;新建装置未制定试生产方案投料开车;精细化工企业未按规范性文件要求开展反应安全风险评估。
化工和危险化学品生产经营单位重大生产安全事故隐患判定标准
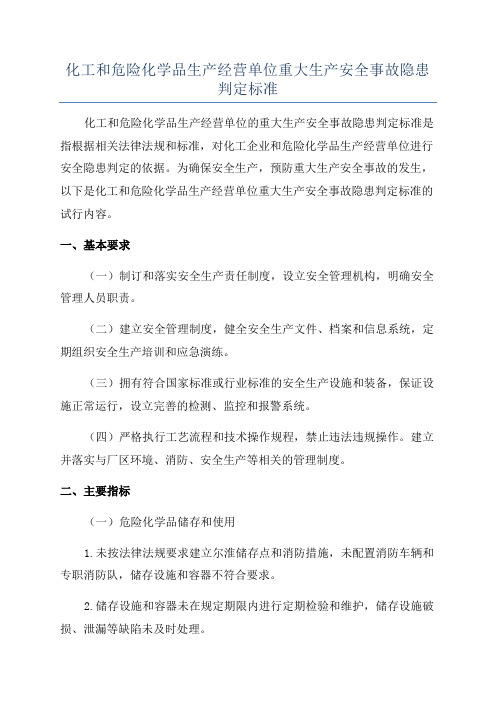
化工和危险化学品生产经营单位重大生产安全事故隐患判定标准化工和危险化学品生产经营单位的重大生产安全事故隐患判定标准是指根据相关法律法规和标准,对化工企业和危险化学品生产经营单位进行安全隐患判定的依据。
为确保安全生产,预防重大生产安全事故的发生,以下是化工和危险化学品生产经营单位重大生产安全事故隐患判定标准的试行内容。
一、基本要求(一)制订和落实安全生产责任制度,设立安全管理机构,明确安全管理人员职责。
(二)建立安全管理制度,健全安全生产文件、档案和信息系统,定期组织安全生产培训和应急演练。
(三)拥有符合国家标准或行业标准的安全生产设施和装备,保证设施正常运行,设立完善的检测、监控和报警系统。
(四)严格执行工艺流程和技术操作规程,禁止违法违规操作。
建立并落实与厂区环境、消防、安全生产等相关的管理制度。
二、主要指标(一)危险化学品储存和使用1.未按法律法规要求建立尔淮储存点和消防措施,未配置消防车辆和专职消防队,储存设施和容器不符合要求。
2.储存设施和容器未在规定期限内进行定期检验和维护,储存设施破损、泄漏等缺陷未及时处理。
3.危险化学品储存点周边环境存在易燃易爆物品、高压电线、开火源等隐患,未采取安全防护措施。
4.未建立健全危险化学品储存和使用管理制度,未进行安全培训和检查。
(二)化工生产过程1.生产设备、工艺和防护设施未符合国家或行业标准,存在严重安全隐患。
2.未建立完备的安全检查和维护制度,设备未在规定期限内进行定期检验和保养。
3.未采取相应的防爆措施,涉爆场所和涉爆设备存在严重安全隐患。
4.未配备必要的防护设施和个人防护用品,未对生产操作人员进行必要的安全培训。
5.未建立紧急预案和应急机制,未进行漏泄、泄漏和污染的应急演练。
6.未建立消防设施和人员配备,未进行有效的消防演练和检查。
(三)生产场所和环境管理1.火灾隐患:未建立火灾防控措施,生产场所存在可燃物质堆积和火源;灭火器材配备不足,消防通道被堵塞。
化工和危险化学品重大生产安全事故隐患判定标准

化工和危险化学品生产经营单位重大生产安全事故隐患判定标准(试行)依据有关法律法规、部门规章和国家标准,以下情形应当判定为重大事故隐患:一、危险化学品生产、经营单位主要负责人和安全生产管理人员未依法经考核合格。
二、特种作业人员未持证上岗。
三、涉及“两重点一重大”的生产装置、储存设施外部安全防护距离不符合国家标准要求。
四、涉及重点监管危险化工工艺的装置未实现自动化控制,系统未实现紧急停车功能,装备的自动化控制系统、紧急停车系统未投入使用。
五、构成一级、二级重大危险源的危险化学品罐区未实现紧急切断功能;涉及毒性气体、液化气体、剧毒液体的一级、二级重大危险源的危险化学品罐区未配备独立的安全仪表系统。
六、全压力式液化烃储罐未按国家标准设置注水措施。
七、液化烃、液氨、液氯等易燃易爆、有毒有害液化气体的充装未使用万向管道充装系统。
八、光气、氯气等剧毒气体及硫化氢气体管道穿越除厂区(包括化工园区、工业园区)外的公共区域。
九、地区架空电力线路穿越生产区且不符合国家标准要求。
十、在役化工装置未经正规设计且未进行安全设计诊断。
十一、使用淘汰落后安全技术工艺、设备目录列出的工艺、设备。
十二、涉及可燃和有毒有害气体泄漏的场所未按国家标准设置检测报警装置,爆炸危险场所未按国家标准安装使用防爆电气设备。
十三、控制室或机柜间面向具有火灾、爆炸危险性装置一侧不满足国家标准关于防火防爆的要求。
十四、化工生产装置未按国家标准要求设置双重电源供电,自动化控制系统未设置不间断电源。
十五、安全阀、爆破片等安全附件未正常投用。
十六、未建立与岗位相匹配的全员安全生产责任制或者未制定实施生产安全事故隐患排查治理制度。
十七、未制定操作规程和工艺控制指标。
十八、未按照国家标准制定动火、进入受限空间等特殊作业管理制度,或者制度未有效执行。
十九、新开发的危险化学品生产工艺未经小试、中试、工业化试验直接进行工业化生产;国内首次使用的化工工艺未经过省级人民政府有关部门组织的安全可靠性论证;新建装置未制定试生产方案投料开车;精细化工企业未按规范性文件要求开展反应安全风险评估。
化工和危险化学品生产经营单位重大生产安全事故隐患判定标

化工和危险化学品生产经营单位重大生产安全事故隐患判定标准解读2018-02-02 09:41 来源:安全监管总局监督管理三司为准确判定、及时整改化工和危险化学品生产经营单位重大生产安全事故隐患(以下简称重大隐患),有效防范遏制重特大事故,根据《安全生产法》和《中共中央国务院关于推进安全生产领域改革发展的意见》,国家安全监管总局制定印发了《化工和危险化学品生产经营单位重大生产安全事故隐患判定标准(试行)》(以下简称《判定标准》)。
《判定标准》依据有关法律法规、部门规章和国家标准,吸取了近年来化工和危险化学品重大及典型事故教训,从人员要求、设备设施和安全管理三个方面列举了二十种应当判定为重大事故隐患的情形。
为进一步明确《判定标准》每一种情形的内涵及依据,便于有关企业和安全监管部门应用,规范推动《判定标准》有效执行,现逐条进行简要解释说明如下:一、危险化学品生产、经营单位主要负责人和安全生产管理人员未依法经考核合格。
近年来,在化工(危险化学品)事故调查过程中发现,事故企业不同程度地存在主要负责人和安全管理人员法律意识与安全风险意识淡薄、安全生产管理知识欠缺、安全生产管理能力不能满足安全生产需要等共性问题,人的因素是制约化工(危险化学品)安全生产的最重要因素。
危险化学品安全生产是一项科学性、专业性很强的工作,企业的主要负责人和安全生产管理人员只有牢固树立安全红线意识、风险意识,掌握危险化学品安全生产的基础知识、具备安全生产管理的基本技能,才能真正落实企业的安全生产主体责任。
《安全生产法》、《危险化学品安全管理条例》、《生产经营单位安全培训规定》(国家安全监管总局令第3号)均对危险化学品生产、经营单位从业人员培训和考核作出了明确要求,其中《安全生产法》第二十四条要求“生产经营单位的主要负责人和安全生产管理人员必须具备与本单位所从事的生产经营活动相应的安全生产知识和管理能力。
危险物品的生产、经营、储存单位以及矿山、金属冶炼、建筑施工、道路运输单位的主要负责人和安全生产管理人员,应当由主管的负有安全生产监督管理职责的部门对其安全生产知识和管理能力考核合格。
化工和危化品重大生产安全事故隐患判定标准

新开发的危险化学品生产工艺未经小试、中试、工业化试验直接进行工业化 生产;国内首次使用的化工工艺未经过省级人民政府有关部门组织的安全可 19 靠性论证;新建装置未制定试生产方案投料开车;精细化工企业未按规范性 文件要求开展反应安全风险评估 20 未按国家标准分区分类储存危险化学品,超量、超品种储存危险化学品,相 互禁配物质混放混存
化工和危化品重大生产安全事故隐患判定标准
1 危险化学品生产、经营单位主要负责人和安全生产管理人员未依法经考核合 2 格 特种作业人员未持证上岗 涉及“两重点一重大”的生产装置、储存设施外部安全防护距离不符合国家 标准要求 涉及重点监管危险化工工艺的装置未实现自动化控制,系统未实现紧急停车 4 功能,装备的自动化控制系统、紧急停车系统未投入使用 3 构成一级、二级重大危险源的危险化学品罐区未实现紧急切断功能;涉及毒 5 性气体、液化气体、剧毒液体的一级、二级重大危险源的危险化学品罐区未 配备独立的安全仪表系统 6 全压力式液化烃储罐未按国家标准设置注水措施 液化烃、液氨、液氯等易燃易爆、有毒有害液化气体的充装未使用万向管道 充装系统 光气、氯气等剧毒气体及硫化氢气体管道穿越除厂区(包括化工园区、工业 8 园区)外的公共区域 7 9 地区架空电力线路穿越生产区且不符合国家标准要求 10 在役化工装置未经正规设计且未进行安全设计诊断 11 使用淘汰落后安全技术工艺、设备目录列出的工艺、设备 涉及可燃和有毒有害气体泄漏的场所未按国家标准设置检测报警装置,爆炸 危险场所未按国家标准安装使用防爆电气设备 控制室或机柜间面向具有火灾、爆炸危险性装置一侧不满足国家标准关于防 13 火防爆的要求 化工生产装置未按国家标准要求设置双重电源供电,自动化控制系统未设置 14 不间断电源 12 15 安全阀、爆破片等安全附件未正常投用 16 未建立与岗位相匹配的全员安全生产责任制或者未制定实施生产安全事故隐 患排查治理制度 未按照国家标准制定动火、进入受限空间等特殊作业管理制度,或者制度未 有效执行
- 1、下载文档前请自行甄别文档内容的完整性,平台不提供额外的编辑、内容补充、找答案等附加服务。
- 2、"仅部分预览"的文档,不可在线预览部分如存在完整性等问题,可反馈申请退款(可完整预览的文档不适用该条件!)。
- 3、如文档侵犯您的权益,请联系客服反馈,我们会尽快为您处理(人工客服工作时间:9:00-18:30)。
化工和危险化学品企业重大安全生产隐患第一、《化工和危险化学品生产经营单位重大生产安全事故隐患判定标准(试行)》
⒈危险化学品生产、经营单位主要负责人和安全生产管理人员未依法经考核合格。
⒉特种作业人员未持证上岗。
⒊涉及“两重点一重大”的生产装置、储存设施外部安全防护距离不符合国家标准要求。
⒋涉及重点监管危险化工工艺的装置未实现自动化控制,系统未实现紧急停车功能,装备的自动化控制系统、紧急停车系统未投入使用。
⒌构成一级、二级重大危险源的危险化学品罐区未实现紧急切断功能;涉及毒性气体、液化气体、剧毒液体的一级、二级重大危险源的危险化学品罐区未配备独立的安全仪表系统。
⒍全压力式液化烃储罐未按国家标准设置注水措施。
⒎液化烃、液氨、液氯等易燃易爆、有毒有害液化气体的充装未使用万向管道充装系统。
⒏光气、氯气等剧毒气体及硫化氢气体管道穿越除厂区(包括化工园区、工业园区)外的公共区域。
⒐地区架空电力线路穿越生产区且不符合国家标准要求。
⒑在役化工装置未经正规设计且未进行安全设计诊断。
⒒使用淘汰落后安全技术工艺、设备目录列出的工艺、设备。
⒓涉及可燃和有毒有害气体泄漏的场所未按国家标准设置检测报警装置,爆炸危险场所未按国家标准安装使用防爆电气设备。
⒔控制室或机柜间面向具有火灾、爆炸危险性装置一侧不满足国家标准关于防火防爆的要求。
⒕化工生产装置未按国家标准要求设置双重电源供电,自动化控制系统未设置不间断电源。
⒖安全阀、爆破片等安全附件未正常投用。
⒗未建立与岗位相匹配的全员安全生产责任制或者未制定实施生产安全事故隐患排查治理制度。
⒘未制定操作规程和工艺控制指标。
⒙未按照国家标准制定动火、进入受限空间等特殊作业管理制度,或者制度未有效执行。
⒚新开发的危险化学品生产工艺未经小试、中试、工业化试验直接进行工业化生产;国内首次使用的化工工艺未经过省级人民政府有关部门组织的安全可靠性论证;新建装置未制定试生产方案投料开车;精细化工企业未按规范性文件要求开展反应安全风险评估。
⒛未按国家标准分区分类储存危险化学品,超量、超品种储存危险化学品,相互禁配物质混放混存。
第二、《甘肃省生产安全事故隐患排查治理办法》
⒈未按规定建立事故隐患排查治理工作制度或者未开展重大事故隐患排查治理工作的;
⒉未按规定如实向负有安全生产监督管理职责的有关部门报告重大事故隐患排查治理情况的;
⒊交通运输工具、农业机械存在超速、超载、超限运输或者违法载人、无牌行驶、无证驾驶行为的;
⒋特种作业人员以及特种设备作业人员、现场管理人员违章作业、违章指挥、冒险蛮干或者强令作业人员冒险作业的;
⒌生产经营单位未制定、落实教育培训计划或者主要负责人、安全生产管理人员安全知识和能力考核不合格,或者特种作业人员无证上岗的;
⒍停工停产停业整顿和技改期间擅自组织生产经营或者建设施工的;
⒎使用国家明令淘汰、禁止使用的危及生产安全和劳动者身体健康的工艺、设备、原材料或者生产经营国家明令淘汰、禁止生产的产品的;
⒏新建、改建、扩建的生产经营性建设项目的安全设施和职业病防护设施未按规定经设计审查,擅自建设或者未经验收合格投入生产和使用的;
⒐危险物品的生产经营场所以及储存数量构成重大危险源的储存设施、油气管道、高压输电线路和尾矿库与居民区(楼)、学校、幼儿园、集贸市场以及其他公众聚集的建筑物未保持国家规定的安全距离的;
⒑重大危险源未按规定安装泄漏报警、监控预警、安全联锁等装置或者系统,不能实现实时有效监测监控的;
⒒采用不正当手段致使监测、监控、联锁、报警、保险等装置或者系统不能发挥正常作用的;
⒓作业场所有毒有害物质种类、浓度和强度超过规定范围而没有及时按规定报告,也未采取相应处置措施的;
⒔涉及重点监管的危险化工工艺、生产装置、储存设施未按规定安装自动化控制系统或者大型和高度危险的化工装置未按照规定安装安全仪表系统和安全联锁报警、紧急停车等系统的;
⒕生产经营单位将生产经营项目、场所、设备发包或者出租给不具备安全生产条件或者相应资质的单位、个人的;
⒖生产经营单位主要负责人和领导班子成员未轮流现场带班;
⒗对上级有关安全生产工作部署执行不力,致使存在事故隐患或者安全生产问题不能及时解决或者拒不执行相关执法部门下达的安全监察指令的;
⒘事故发生单位对较大以上事故的防范和整改措施逾期未落实的;
⒙生产经营单位未按照有关规定和安全生产保障需要落实安全生产经费投入、挤占或者挪用安全生产经费的;
⒚有关安全生产法律、法规、规章规定的其他构成重大事故隐患的情形。
第三、淘汰落后安全技术装备目录(2015年第一批)。