重点讲解锂电池极片挤压涂布常见缺陷
锂电池辊压工艺中存在的问题及解决措施
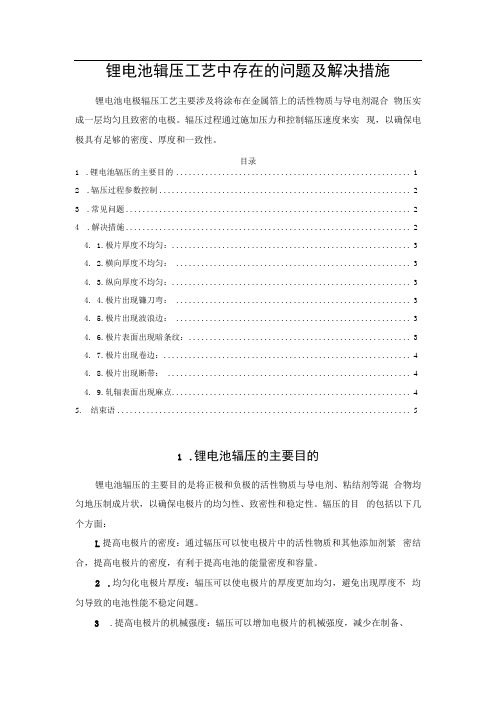
锂电池辑压工艺中存在的问题及解决措施锂电池电极辐压工艺主要涉及将涂布在金属箔上的活性物质与导电剂混合物压实成一层均匀且致密的电极。
辐压过程通过施加压力和控制辐压速度来实现,以确保电极具有足够的密度、厚度和一致性。
目录1.锂电池辐压的主要目的 (1)2.辐压过程参数控制 (2)3.常见问题 (2)4.解决措施 (2)4. 1.极片厚度不均匀: (3)4. 2.横向厚度不均匀: (3)4. 3.纵向厚度不均匀: (3)4. 4.极片出现镰刀弯: (3)4. 5.极片出现波浪边: (3)4. 6.极片表面出现暗条纹: (3)4. 7.极片出现卷边: (4)4. 8.极片出现断带: (4)4. 9.轧辐表面出现麻点 (4)5. 结束语 (5)1.锂电池辐压的主要目的锂电池辐压的主要目的是将正极和负极的活性物质与导电剂、粘结剂等混合物均匀地压制成片状,以确保电极片的均匀性、致密性和稳定性。
辐压的目的包括以下几个方面:L提高电极片的密度:通过辐压可以使电极片中的活性物质和其他添加剂紧密结合,提高电极片的密度,有利于提高电池的能量密度和容量。
2.均匀化电极片厚度:辐压可以使电极片的厚度更加均匀,避免出现厚度不均匀导致的电池性能不稳定问题。
3.提高电极片的机械强度:辐压可以增加电极片的机械强度,减少在制备、组装和使用过程中的断裂和变形。
4.改善电极片的电导率:通过辐压可以使电极片中的导电剂均匀分布,提高电极片的电导率,有利于提高电池的充放电性能。
2.辐压过程参数控制在锂电池制作中,辐压是电池正极和负极片时应控制好以下几个方面:1、辐压温度:控制辐压温度能够影响电池片与电解质层、隔膜的结合程度, 一般需要在一定的温度范围内进行辐压。
2、辐压压力:合适的辐压压力能够确保电池片与电解质层、隔膜的紧密结合,但过大的压力可能会导致电池片变形或损坏。
3、辐压速度:辐压速度的控制也是辐压过程中需要考虑的因素,适当的辐压速度可以确保复合过程的均匀性。
锂电浆料涂布瑕疵及改善方法
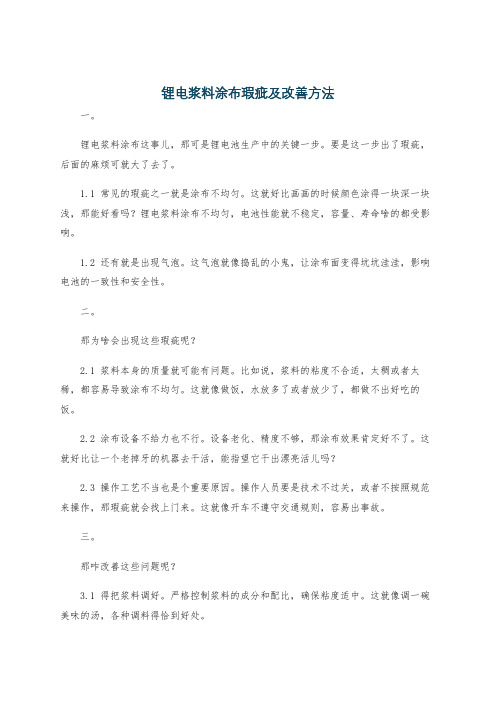
锂电浆料涂布瑕疵及改善方法
一。
锂电浆料涂布这事儿,那可是锂电池生产中的关键一步。
要是这一步出了瑕疵,后面的麻烦可就大了去了。
1.1 常见的瑕疵之一就是涂布不均匀。
这就好比画画的时候颜色涂得一块深一块浅,那能好看吗?锂电浆料涂布不均匀,电池性能就不稳定,容量、寿命啥的都受影响。
1.2 还有就是出现气泡。
这气泡就像捣乱的小鬼,让涂布面变得坑坑洼洼,影响电池的一致性和安全性。
二。
那为啥会出现这些瑕疵呢?
2.1 浆料本身的质量就可能有问题。
比如说,浆料的粘度不合适,太稠或者太稀,都容易导致涂布不均匀。
这就像做饭,水放多了或者放少了,都做不出好吃的饭。
2.2 涂布设备不给力也不行。
设备老化、精度不够,那涂布效果肯定好不了。
这就好比让一个老掉牙的机器去干活,能指望它干出漂亮活儿吗?
2.3 操作工艺不当也是个重要原因。
操作人员要是技术不过关,或者不按照规范来操作,那瑕疵就会找上门来。
这就像开车不遵守交通规则,容易出事故。
三。
那咋改善这些问题呢?
3.1 得把浆料调好。
严格控制浆料的成分和配比,确保粘度适中。
这就像调一碗美味的汤,各种调料得恰到好处。
3.2 设备要更新维护。
定期检查设备,有问题及时修,该换新的就换新的。
别心疼那点钱,不然因小失大。
锂电浆料涂布这事儿可不能马虎,得用心去做,才能做出高质量的锂电池,让咱们的新能源产业越来越好!。
锂电池辊压工艺中存在的问题及解决措施

锂电池辊压工艺中存在的问题及解决措施锂电池辊压工艺中存在的问题主要包括:1.极片厚度不均匀:这可能是由于涂布厚度不均匀、轧辊同轴度误差、轧辊圆柱度误差、轧辊接触母线不平行、轧辊轴向挠曲变形、辊压设备的刚性稳定性差等因素导致的。
2.极片出现镰刀弯:这主要是由两轧辊接触母线不平行或极片涂布横向厚度不均造成的。
3.极片出现波浪边:这主要是由极片辊压延展较大、轧辊自身直径小、极片辊压前张力小、极片厚度压缩量大、极片涂布两边凸起等原因造成的。
4.极片表面出现暗条纹:这主要是由于轧辊表面存在振纹、轧辊圆柱度误差较大、前张力小且不均匀等因素导致的。
5.检测难度大:目前,锂电池辊压机设备并没有专门针对辊压均匀性的检测仪器,对于辊压均匀性的检测主要依靠目测或手感,因此,检测难度较大。
6.辊压均匀性不足:在锂电池辊压过程中,由于生产设备的精度和工艺的限制,辊压均匀性有时会存在问题,导致电池性能不稳定或寿命缩短。
解决措施包括:1.调整设备参数:针对涂布厚度不均匀、轧辊同轴度误差、轧辊圆柱度误差等问题,可以通过调整设备参数来解决。
例如,调整涂布机的涂布厚度、调整轧辊的同轴度和圆柱度等。
2.加强质量检测:在生产过程中,应该加强质量检测,及时发现并处理问题。
例如,可以采用X光机、超声波测厚仪等设备进行质量检测。
3.优化工艺流程:针对极片出现镰刀弯、波浪边和暗条纹等问题,可以通过优化工艺流程来解决。
例如,优化涂布工艺、调整辊压设备的参数等。
4.引入先进设备:为了提高生产效率和产品质量,可以引入先进的设备,例如激光测距仪、智能控制系统等。
这些设备可以自动检测和调整生产过程中的各种参数,提高生产效率和产品质量。
5.加强员工培训:员工是生产过程中的重要因素,因此,加强员工培训也是解决锂电池辊压工艺问题的有效途径。
培训内容可以包括设备操作、工艺流程、质量检测等方面,以提高员工的技能水平和质量意识。
6.建立质量管理体系:建立完善的质量管理体系是保证产品质量和稳定性的重要措施。
锂电池极片设计及表面缺陷分析检测知识汇总
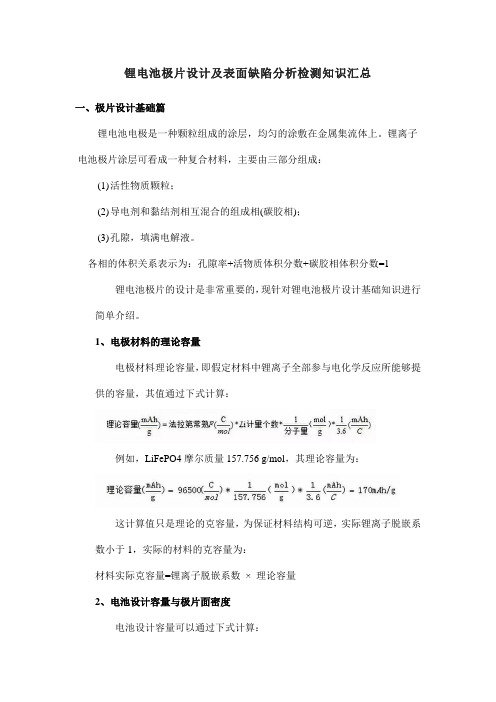
锂电池极片设计及表面缺陷分析检测知识汇总一、极片设计基础篇锂电池电极是一种颗粒组成的涂层,均匀的涂敷在金属集流体上。
锂离子电池极片涂层可看成一种复合材料,主要由三部分组成:(1)活性物质颗粒;(2)导电剂和黏结剂相互混合的组成相(碳胶相);(3)孔隙,填满电解液。
各相的体积关系表示为:孔隙率+活物质体积分数+碳胶相体积分数=1 锂电池极片的设计是非常重要的,现针对锂电池极片设计基础知识进行简单介绍。
1、电极材料的理论容量电极材料理论容量,即假定材料中锂离子全部参与电化学反应所能够提供的容量,其值通过下式计算:例如,LiFePO4摩尔质量157.756 g/mol,其理论容量为:这计算值只是理论的克容量,为保证材料结构可逆,实际锂离子脱嵌系数小于1,实际的材料的克容量为:材料实际克容量=锂离子脱嵌系数×理论容量2、电池设计容量与极片面密度电池设计容量可以通过下式计算:电池设计容量=涂层面密度×活物质比例×活物质克容量×极片涂层面积其中,涂层的面密度是一个关键的设计参数,压实密度不变时,涂层面密度增加意味着极片厚度增加,电子传输距离增大,电子电阻增加,但是增加程度有限。
厚极片中,锂离子在电解液中的迁移阻抗增加是影响倍率特性的主要原因,考虑到孔隙率和孔隙的曲折连同,离子在孔隙内的迁移距离比极片厚度多出很多倍。
3、负极-正极容量比N/P负极容量与正极容量的比值定义为:N/P要大于1.0,一般1.04~1.20,这主要是处于安全设计,防止负极侧锂离子无接受源而析出,设计时要考虑工序能力,如涂布偏差。
但是,N/P 过大时,电池不可逆容量损失,导致电池容量偏低,电池能量密度也会降低。
而对于钛酸锂负极,采用正极过量设计,电池容量由钛酸锂负极的容量确定。
正极过量设计有利于提升电池的高温性能:高温气体主要来源于负极,在正极过量设计时,负极电位较低,更易于在钛酸锂表面形成SEI膜。
锂电池涂布工序常见故障和解决方法汇总

锂电池涂布工序是锂电池生产中非常关键的一环,涂布工序的质量直接影响着锂电池的性能和安全性。
然而,在实际生产过程中,涂布工序常常会出现各种故障,影响整个生产线的正常运转。
本文将就锂电池涂布工序常见的故障进行梳理和总结,并提供相应的解决方法,以期为从事锂电池生产的工程师和技术人员提供一定的参考和帮助。
1. 涂布机出现涂布不均匀情况1.1 可能原因:涂布刀片磨损不均匀,导致涂布厚度不均匀;涂布辊与输送辊之间的间隙不一致;涂布材料的粘度不一致。
1.2 解决方法:定期更换涂布刀片,保持其锋利度;调整涂布辊与输送辊的间隙,确保一致;加强涂布材料的粘度控制,确保一致。
2. 涂布机出现漏涂现象2.1 可能原因:涂布刀片损坏或安装不良;输送辊转速过快,导致涂布材料无法被充分涂覆;涂布材料的粘度过高,无法完全附着在电极上。
2.2 解决方法:检查涂布刀片的完好度并及时更换;适当调整输送辊的转速,确保涂布材料可以被充分涂覆;控制涂布材料的粘度,避免过高。
3. 涂布机出现起泡现象3.1 可能原因:涂布材料的挥发性成分过快,导致涂布过程中产生气泡;涂布刀片与电极间的间隙不一致,导致气体无法顺利逸出。
3.2 解决方法:调整涂布材料的挥发性成分,避免过快;确保涂布刀片与电极间的间隙一致,避免气泡产生。
4. 涂布机出现堵塞现象4.1 可能原因:涂布材料中有杂质,导致管道堵塞;输送辊转速过慢,无法及时排出涂布材料。
4.2 解决方法:加强涂布材料的过滤工作,确保无杂质;适当调整输送辊的转速,确保涂布材料能够顺利流动。
5. 涂布机出现电极破损现象5.1 可能原因:输送辊表面粗糙,易划伤电极;涂布刀片安装不稳,易引起电极损伤。
5.2 解决方法:定期对输送辊进行维护和更换,确保表面光滑;定期检查涂布刀片的安装情况,确保稳定可靠。
总结:通过对锂电池涂布工序常见故障和解决方法的梳理和总结,我们可以看到,涂布工序的质量受到多种因素的影响,需要全面而细致的管理和维护。
锂电涂布丨涂布车间常见问题及解决方案
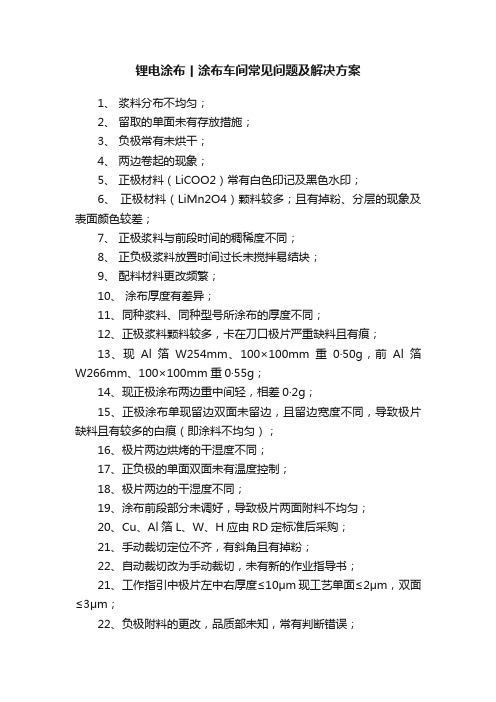
锂电涂布丨涂布车间常见问题及解决方案1、浆料分布不均匀;2、留取的单面未有存放措施;3、负极常有未烘干;4、两边卷起的现象;5、正极材料(LiCOO2)常有白色印记及黑色水印;6、正极材料(LiMn2O4)颗料较多;且有掉粉、分层的现象及表面颜色较差;7、正极浆料与前段时间的稠稀度不同;8、正负极浆料放置时间过长未搅拌易结块;9、配料材料更改频繁;10、涂布厚度有差异;11、同种浆料、同种型号所涂布的厚度不同;12、正极浆料颗料较多,卡在刀口极片严重缺料且有痕;13、现Al箔W254mm、100×100mm重0·50g,前Al箔W266mm、100×100mm重0·55g;14、现正极涂布两边重中间轻,相差0·2g;15、正极涂布单现留边双面未留边,且留边宽度不同,导致极片缺料且有较多的白痕(即涂料不均匀);16、极片两边烘烤的干湿度不同;17、正负极的单面双面未有温度控制;18、极片两边的干湿度不同;19、涂布前段部分未调好,导致极片两面附料不均匀;20、Cu、Al箔L、W、H应由RD定标准后采购;21、手动裁切定位不齐,有斜角且有掉粉;22、自动裁切改为手动裁切,未有新的作业指导书;21、工作指引中极片左中右厚度≤10μm现工艺单面≤2μm,双面≤3μm;22、负极附料的更改,品质部未知,常有判断错误;23、负极涂布双面温度无法升起(设125℃最多升至118℃);24、开窗后外面的温湿度对极片有影响吗;25、正、负单面涂布都是右边卷起,且正极收卷不齐易打皱;26、涂布机的温度与走速是成正比的,如何控制?未有标准;27、单面调机人员未带手套,留在Cu、Al上的手印(即汗渍),导致双面涂布后有明显的黑印迹;28、Al较窄不能留边,导致附在单面两干料,双面极易拉断且拉断次数较多,产生报废;29、涂布未有自检记录及习惯;30、刚停机,极片存放在烘箱中易掉粉;31、涂布完的极片未有明确规定如何存放;32、涂布后放Cu、Al箔位,未经其他部门认可已更换,且Cu、Al箔多次撞伤及两边松紧度不同;33、涂布机内辊轮未经常擦洗,易有干料附在极片上;34、加料未经常搅拌浆料稀稠不同,极片附料不均匀;35、同一大片分切后6小片,极片左中右厚度不稳定且重量在上中下限都有;36、加料最后的浆料(有干料、较稠、结块)对所涂极片都有影响;37、停机卡在刀口处的印记应切除,辊压后易断裂(正极);38、涂布工艺上所给的公差较大,能否缩小;39、涂布工艺两边附料不同,如063048 –ve单:1·7±0·05g双:3·41±0·05g ;083048 +ve单:3·74±0·08g双:7·48±0·15g ;40、未涂完的单面,用保鲜纸包后露置于空气中;41、Cu、Al箔未用后,露置于空气中且边缘未包;42、试机时所用碎布擦Cu、Al上浆料,对极片附为都有较多影响,且极片中有气泡(浆料);43、停机时,前段80mm处置于空气中,极片上浆料变色,有气泡;44、裁切大片定位不整齐,极片四角偏斜,不成直角,且切口处有毛剌及掉粉,手按片不稳定;45、RD规定涂布报废片回收,但放置空气中过久,+ve起泡-ve掉粉;46、未用电子称测量大片重量,也未规定多少时间分切小片测重;47、牵引极片受力不均,导致附料不均,试片调机应保留,经确认后方可执行;48、牵引Cu、Al箔的过程中,辅助转轴较多,箔两边受力不均;49、正极单面前加多一辊轮,负极未有;50、塞尺划痕,露基体极片较多;51、收卷越大,速度加速,应减慢,否则不能干;52、接带断带后,手拉附料不均匀(拉太快);53、负极拉完转拉正极时,极片存放烘箱过长;54、涂布机的保养未有当事人的审核;55、涂布机的排风扇未有见过清洗;56、裁切大片(手动)无设备操作、工位作业指导书,且工作台面太脏,极片易有±ve极粉到极片上;57、未调好机就涂布,造成两面附料不均匀。
锂电池极片缺陷图谱(一)
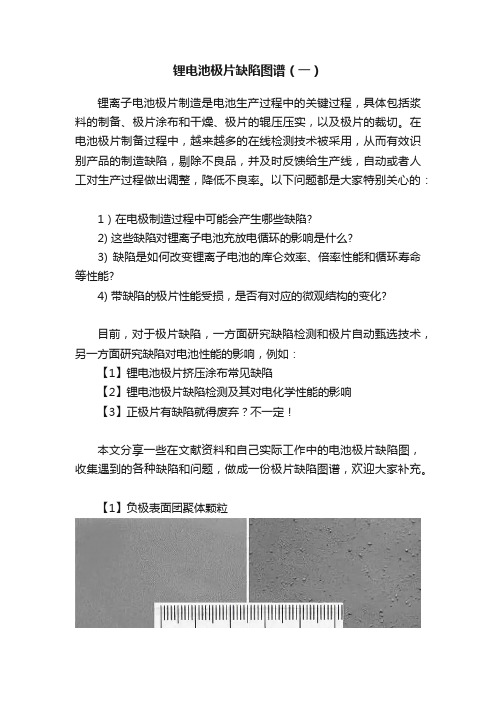
锂电池极片缺陷图谱(一)锂离子电池极片制造是电池生产过程中的关键过程,具体包括浆料的制备、极片涂布和干燥、极片的辊压压实,以及极片的裁切。
在电池极片制备过程中,越来越多的在线检测技术被采用,从而有效识别产品的制造缺陷,剔除不良品,并及时反馈给生产线,自动或者人工对生产过程做出调整,降低不良率。
以下问题都是大家特别关心的:1)在电极制造过程中可能会产生哪些缺陷?2) 这些缺陷对锂离子电池充放电循环的影响是什么?3) 缺陷是如何改变锂离子电池的库仑效率、倍率性能和循环寿命等性能?4) 带缺陷的极片性能受损,是否有对应的微观结构的变化?目前,对于极片缺陷,一方面研究缺陷检测和极片自动甄选技术,另一方面研究缺陷对电池性能的影响,例如:【1】锂电池极片挤压涂布常见缺陷【2】锂电池极片缺陷检测及其对电化学性能的影响【3】正极片有缺陷就得废弃?不一定!本文分享一些在文献资料和自己实际工作中的电池极片缺陷图,收集遇到的各种缺陷和问题,做成一份极片缺陷图谱,欢迎大家补充。
【1】负极表面团聚体颗粒配方:球形石墨+SUPER C65+CMC+蒸馏水两种不同搅拌工艺的极片宏观形貌:表面光滑(左)和表面存在大量小颗粒(右)配方:球形石墨+SUPER C65+CMC/SBR+蒸馏水极片表面小颗粒放大形貌(a和b):导电剂的团聚体,没有完全分散表面光滑极片的放大形貌:导电剂充分分散,均匀分布【Bitsch B,Willenbacher N, Wenzel V, et al. Impact of Mechanical Process Engineering onthe Fabrication Process of Electrodes for Lithium Ion Batteries[J]. ChemieIngenieur Technik. 2015, 87(4): 466-474.】【2】正极表面团聚体颗粒配方:NCA+乙炔黑+PVDF+NMP搅拌过程中,环境湿度太高,导致浆料成果冻状态,导电剂没有完全分散好,极片辊压后表面存在大量的颗粒。
锂离子电池极片狭缝式挤压涂布流场特性解析

书山有路勤为径;学海无涯苦作舟
锂离子电池极片狭缝式挤压涂布流场特性解析
锂离子电池极片涂布过程具有浆料粘度大,涂层厚,基材薄、精度要求高等特点,目前已经广泛采用狭缝挤压式涂布技术。
本文主要介绍了狭缝挤压式涂布预计量式的特点与涂布量的预估方法;流体的受力情况、流场无量纲参数的含义;以及流体力学有限元对涂布流场的分析。
锂离子电池是目前性能最优的二次电池产品,在能量密度、功率密度、
寿命、环境适应性、安全和成本方面均有较大的改进空间,锂离子动力电池是混合动力车、纯电动汽车、储能系统等应用技术和工程技术的基础。
极片制作工艺是制造锂离子动力电池的基础工艺,所以对于此环节所用设备的精度、智能化水平、生产性能的可靠性等要求非常高。
目前,锂离子动力电池行业已经普遍采用狭缝挤压式涂布技术制造电池极片。
挤压涂布技术能获得较高精度的涂层,同时也可以用于较高粘度流体涂布,被广泛应用于柔性电子、功能薄膜、平板显示器、微纳米制造、印刷等众多领域。
实际工艺过程中,涂布液的均匀性、稳定性、边缘和表面效应受到涂布
液的流变特性影响,从而直接决定涂层的质量。
采用理论分析、涂布实验技术、流体力学有限元技术等研究手段可以进行涂布窗口的研究,涂布窗口就是可以进行稳定涂布,得到均匀涂层的工艺操作范围,其受到三类因素的影响:
(1)流体特性,如粘度μ、表面张力σ、密度ρ;
(2)挤压模头几何参数,如涂布间距H,模头狭缝尺寸w;
(3)涂布工艺参数,如涂布速度v,浆料送料流量Q等。
对于挤压式涂布,在固定的流量下,存在一个涂布速度上限和一个涂布
专注下一代成长,为了孩子。
重点讲解锂电池极片挤压涂布厚边现象及解决措施
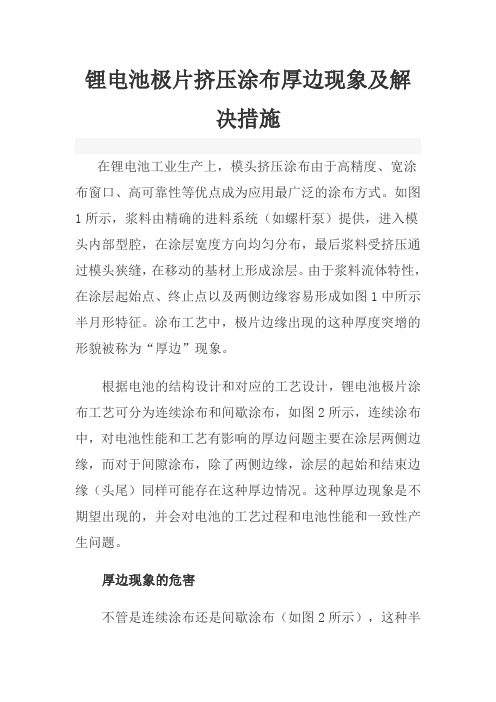
锂电池极片挤压涂布厚边现象及解决措施在锂电池工业生产上,模头挤压涂布由于高精度、宽涂布窗口、高可靠性等优点成为应用最广泛的涂布方式。
如图1所示,浆料由精确的进料系统(如螺杆泵)提供,进入模头内部型腔,在涂层宽度方向均匀分布,最后浆料受挤压通过模头狭缝,在移动的基材上形成涂层。
由于浆料流体特性,在涂层起始点、终止点以及两侧边缘容易形成如图1中所示半月形特征。
涂布工艺中,极片边缘出现的这种厚度突增的形貌被称为“厚边”现象。
根据电池的结构设计和对应的工艺设计,锂电池极片涂布工艺可分为连续涂布和间歇涂布,如图2所示,连续涂布中,对电池性能和工艺有影响的厚边问题主要在涂层两侧边缘,而对于间隙涂布,除了两侧边缘,涂层的起始和结束边缘(头尾)同样可能存在这种厚边情况。
这种厚边现象是不期望出现的,并会对电池的工艺过程和电池性能和一致性产生问题。
厚边现象的危害不管是连续涂布还是间歇涂布(如图2所示),这种半月形形貌特征都会严重影响涂层的均匀性。
一般地,涂层边缘厚度比正常区域厚几微米至十几微米,在涂布干燥后收卷时,成百上千层极片收成一卷,涂层侧面边缘厚度凸起线累积成几毫米,导致极卷产生鼓边现象,严重时会造成极片断裂,这严重影响涂布收卷整齐度及其后续工序。
这种厚边情况也会影响极片的辊压工艺,由于边缘厚度较中间部位大几微米或十几微米,辊压轧辊压力作用在极片上时,边缘厚度大的区域承受更大的轧制力,从而导致极片辊压压实横向密度不一致,一方面这会造成辊压之后的极片翘曲度更大形成蛇形极片,在后续的分条或模切、卷绕等工艺过程中,极片张力分布不均衡,极片收放卷对齐度无法保证,这也会影响极片加工尺寸,容易出现不良品。
厚边现象造成的极片厚度、压实密度不均匀同样对电池性能有影响,在充放电过程中,可能出现电流分布不均匀,更容易形成极化。
因此,电池极片在充放电膨胀、收缩过程中受力也不一致,厚边缘更容易失效。
一般地,3C电池工艺设计时,切除极片边缘来消除这种厚边的不利影响。
锂离子电池原理常见不良项目及成因涂布方法汇总

锂离子电池原理常见不良项目及成因涂布方法汇总一、锂离子电池原理1.正极:通常采用锂化合物(如LiCoO2、LiFePO4)作为正极材料。
正极材料能嵌入或释放锂离子。
2.负极:通常采用石墨作为负极材料。
负极材料能嵌入或释放锂离子。
3.电解液:电解液是锂离子传输的介质,通常由有机溶剂和一种锂盐组成。
4.隔膜:隔膜起到隔离正负极的作用,防止短路。
在充电过程中,锂离子从正极材料中嵌出,经过电解液迁移到负极材料中嵌入。
在放电过程中,则反之。
正负极嵌入或嵌出锂离子的过程伴随着电子的流动,从而产生电能。
二、常见不良项目及成因1.容量衰减:锂离子电池的容量随着使用次数和充放电次数的增加而逐渐衰减。
这是由于正负极材料的脱钠和脱锂导致的。
2.电池发热:电池发热可能是由于不均匀的电池放电、充电导致的。
3.电池容量不匹配:电池组中的不同电池单体之间容量差异较大,导致一些单体的电压和容量迅速下降。
4.短路:短路可能是由于电池在使用过程中遭受外来损坏,引起正负极的直接连接。
以上这些不良项目的成因多是因为电池的设计不合理、材料不理想或使用环境不恰当等因素导致的。
三、涂布方法1.滚涂法:滚涂法是一种常用的涂布方法,通过将浆料涂刷在转动的滚筒上,然后将电极片从滚筒上剥离,完成正负极材料的涂布。
2.刮涂法:刮涂法是将浆料用刮刀均匀地涂抹在电极片上,然后通过烘干等工艺固化材料。
3.喷涂法:喷涂法是利用高速风切割浆料,将其喷射到电极片上,在快速干燥后,形成均匀的材料膜。
以上这些涂布方法各有优缺点,选用何种方法取决于电池设计的要求以及制造工艺的实际条件。
总结:锂离子电池是一种重要的电池类型,广泛应用于各个领域。
通过正负极的嵌入和嵌出实现充放电过程。
在使用过程中可能出现不良项目,如容量衰减、发热等,其成因多与设计、材料、使用环境等因素有关。
涂布方法有滚涂法、刮涂法和喷涂法等,选用何种方法需根据实际情况决定。
这些信息可以帮助我们更好地了解锂离子电池的原理和制造工艺。
锂离子电池原理、常见不良项目及成因、涂布方法汇总
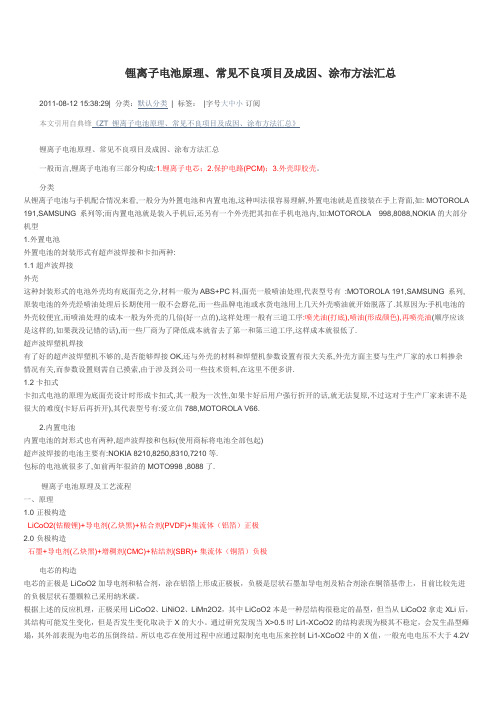
锂离子电池原理、常见不良项目及成因、涂布方法汇总2011-08-12 15:38:29| 分类:默认分类| 标签:|字号大中小订阅本文引用自典锋《ZT 锂离子电池原理、常见不良项目及成因、涂布方法汇总》锂离子电池原理、常见不良项目及成因、涂布方法汇总一般而言,锂离子电池有三部分构成:1.锂离子电芯;2.保护电路(PCM);3.外壳即胶壳。
分类从锂离子电池与手机配合情况来看,一般分为外置电池和内置电池,这种叫法很容易理解,外置电池就是直接装在手上背面,如: MOTOROLA 191,SAMSUNG 系列等;而内置电池就是装入手机后,还另有一个外壳把其扣在手机电池内,如:MOTOROLA998,8088,NOKIA的大部分机型1.外置电池外置电池的封装形式有超声波焊接和卡扣两种:1.1超声波焊接外壳这种封装形式的电池外壳均有底面壳之分,材料一般为ABS+PC料,面壳一般喷油处理,代表型号有:MOTOROLA 191,SAMSUNG 系列,原装电池的外壳经喷油处理后长期使用一般不会磨花,而一些品牌电池或水货电池用上几天外壳喷油就开始脱落了.其原因为:手机电池的外壳较便宜,而喷油处理的成本一般为外壳的几倍(好一点的),这样处理一般有三道工序:喷光油(打底),喷油(形成颜色),再喷亮油(顺序应该是这样的,如果我没记错的话),而一些厂商为了降低成本就省去了第一和第三道工序,这样成本就很低了.超声波焊塑机焊接有了好的超声波焊塑机不够的,是否能够焊接OK,还与外壳的材料和焊塑机参数设置有很大关系,外壳方面主要与生产厂家的水口料掺杂情况有关,而参数设置则需自己摸索,由于涉及到公司一些技术资料,在这里不便多讲.1.2卡扣式卡扣式电池的原理为底面壳设计时形成卡扣式,其一般为一次性,如果卡好后用户强行折开的话,就无法复原,不过这对于生产厂家来讲不是很大的难度(卡好后再折开),其代表型号有:爱立信788,MOTOROLA V66.2.内置电池内置电池的封形式也有两种,超声波焊接和包标(使用商标将电池全部包起)超声波焊接的电池主要有:NOKIA 8210,8250,8310,7210等.包标的电池就很多了,如前两年很浒的MOTO998 ,8088了.锂离子电池原理及工艺流程一、原理1.0 正极构造LiCoO2(钴酸锂)+导电剂(乙炔黑)+粘合剂(PVDF)+集流体(铝箔)正极2.0 负极构造石墨+导电剂(乙炔黑)+增稠剂(CMC)+粘结剂(SBR)+ 集流体(铜箔)负极电芯的构造电芯的正极是LiCoO2加导电剂和粘合剂,涂在铝箔上形成正极板,负极是层状石墨加导电剂及粘合剂涂在铜箔基带上,目前比较先进的负极层状石墨颗粒已采用纳米碳。
干货锂电池极片挤压涂布常见缺陷
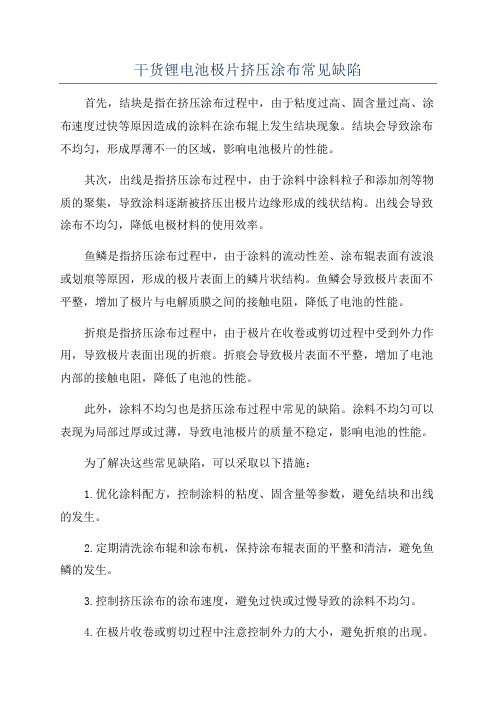
干货锂电池极片挤压涂布常见缺陷
首先,结块是指在挤压涂布过程中,由于粘度过高、固含量过高、涂布速度过快等原因造成的涂料在涂布辊上发生结块现象。
结块会导致涂布不均匀,形成厚薄不一的区域,影响电池极片的性能。
其次,出线是指挤压涂布过程中,由于涂料中涂料粒子和添加剂等物质的聚集,导致涂料逐渐被挤压出极片边缘形成的线状结构。
出线会导致涂布不均匀,降低电极材料的使用效率。
鱼鳞是指挤压涂布过程中,由于涂料的流动性差、涂布辊表面有波浪或划痕等原因,形成的极片表面上的鳞片状结构。
鱼鳞会导致极片表面不平整,增加了极片与电解质膜之间的接触电阻,降低了电池的性能。
折痕是指挤压涂布过程中,由于极片在收卷或剪切过程中受到外力作用,导致极片表面出现的折痕。
折痕会导致极片表面不平整,增加了电池内部的接触电阻,降低了电池的性能。
此外,涂料不均匀也是挤压涂布过程中常见的缺陷。
涂料不均匀可以表现为局部过厚或过薄,导致电池极片的质量不稳定,影响电池的性能。
为了解决这些常见缺陷,可以采取以下措施:
1.优化涂料配方,控制涂料的粘度、固含量等参数,避免结块和出线的发生。
2.定期清洗涂布辊和涂布机,保持涂布辊表面的平整和清洁,避免鱼鳞的发生。
3.控制挤压涂布的涂布速度,避免过快或过慢导致的涂料不均匀。
4.在极片收卷或剪切过程中注意控制外力的大小,避免折痕的出现。
综上所述,干货锂电池极片挤压涂布常见缺陷主要包括结块、出线、鱼鳞、折痕和涂料不均匀等。
了解这些缺陷的原因,并采取相应的措施进行预防和修复,可以提高锂电池极片的质量和性能。
干货锂电池极片挤压涂布常见缺陷

干货|锂电池极片挤压涂布常见缺陷目前,电动车、储能电池等新能源产业在全球范围内发展迅速。
作为公认的理想储能元件,动力锂电池也得到高度关注。
涂布机是动力锂电池极片的生产关键工艺设备。
目前,锂电池极片涂布工艺主要有刮刀式、辊涂转移式和狭缝挤压式等。
我在工作过程中,这三种涂布方式都接触过。
一般实验室设备采用刮刀式,3C电池采用辊涂转移式,而动力电池多采用狭缝挤压式。
刮刀涂布工作原理如图1所示,箔基材经过涂布辊并直接与浆料料槽接触,过量的浆料涂在箔基材上,在基材通过涂辊与刮刀之间时,刮刀与基材之间的间隙决定了涂层厚度,同时将多余的浆料刮掉回流,并由此在基材表面形成一层均匀的涂层。
刮刀类型主要逗号刮刀。
逗号刮刀是涂布头中的关键部件之一,一般在圆辊表面沿母线加工成形似逗号的刃口,这种刮刀具有高的强度和硬度,易于控制涂布量和涂布精度,适用于高固含量和高黏度的浆料。
图1 逗号刮刀涂布示意图辊涂转移式涂辊转动带动浆料,通过逗号刮刀间隙来调节浆料转移量,并利用背辊和涂辊的转动将浆料转移到基材上,工艺过程如图2所示。
辊涂转移涂布包含两个基本过程:(1)涂布辊转动带动浆料通过计量辊间隙,形成一定厚度的浆料层;(2)一定厚度的浆料层通过方向相对的涂辊与背辊转动转移浆料到箔材上形成涂层。
图2 辊涂刮刀转移涂布工艺示意图狭缝挤压涂布作为一种精密的湿式涂布技术,如图3所示,工作原理为涂布液在一定压力一定流量下沿着涂布模具的缝隙挤压喷出而转移到基材上。
相比其它涂布方式,具有很多优点,如涂布速度快、精度高、湿厚均匀;涂布系统封闭,在涂布过程中能防止污染物进入,浆料利用率高、能够保持浆料性质稳定,可同时进行多层涂布。
并能适应不同浆料粘度和固含量范围,与转移式涂布工艺相比具有更强的适应性。
图3 狭缝挤出式涂布示意图要形成稳定均匀的涂层,涂布过程中就需要同时满足这几个条件:(1)浆料性质稳定,不发生沉降,粘度、固含量等不变化。
(2)浆料上料供应稳定,在模头内部形成均匀稳定的流动状态。
锂离子电池车间生产过程中常见涂布异常及处理方式
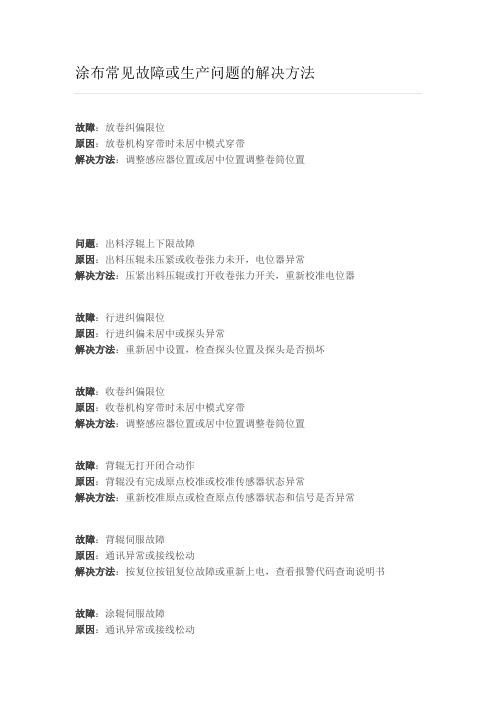
故障:放卷纠偏限位原因:放卷机构穿带时未居中模式穿带解决方法:调整感应器位置或居中位置调整卷筒位置问题:出料浮辊上下限故障原因:出料压辊未压紧或收卷张力未开,电位器异常解决方法:压紧出料压辊或打开收卷张力开关,重新校准电位器故障:行进纠偏限位原因:行进纠偏未居中或探头异常解决方法:重新居中设置,检查探头位置及探头是否损坏故障:收卷纠偏限位原因:收卷机构穿带时未居中模式穿带解决方法:调整感应器位置或居中位置调整卷筒位置故障:背辊无打开闭合动作原因:背辊没有完成原点校准或校准传感器状态异常解决方法:重新校准原点或检查原点传感器状态和信号是否异常故障:背辊伺服故障原因:通讯异常或接线松动解决方法:按复位按钮复位故障或重新上电,查看报警代码查询说明书故障:涂辊伺服故障原因:通讯异常或接线松动解决方法:按复位按钮复位故障或重新上电,查看报警代码查询说明书故障:第二面不间歇涂布原因:光纤故障解决方法:检查涂布参数或光纤信号是否异常故障:刮刀伺服故障原因:调刀伺服驱动器报警或传感器状态异常、设备急停解决方法:检查急停按钮或按复位按钮消除报警、重新校准刮刀辊原点并检查传感器状态是否异常故障:划痕原因:浆料颗粒引起或刮刀有缺口解决方法:塞尺清颗粒、检查刮刀故障:掉粉原因:a.过烘引起掉粉;b.车间湿度大、极片吸水;c.浆料粘接性差;d.浆料长时间未进行搅拌浆料解决方法:联系现场品质技术故障:面密度不够原因:a.液面高度落差大; b.走速 c.刀口解决办法:检查速度、刀口参数,保持一定的液位高度故障:颗粒较多原因:a.浆料本身所带或沉淀;b.单面涂布时辊轴造成;c.浆料长时间未搅拌(静止状态)解决办法:涂布前擦干净过辊、长时间浆料未用需要咨询品质技术是否搅拌故障:拖尾原因:浆料拖尾、背辊或涂辊间隙不平行、背辊弹开速度解决办法:调节间涂间隙参数、加大背辊弹开速度故障:正面错位原因:对齐有误差时未修正对齐参数解决方法:检查箔材有无打滑、清洗背辊,压住基准辊压辊、修正对齐参数故障:反面间涂呈平行状拖尾原因:涂背辊间距过小、过小或背辊弹开距离过小解决方法:调整涂背辊间距增加背辊弹开距离故障:头厚尾薄原因:头尾削薄参数未调好解决方法:调节头尾速度比及头尾起点距离故障:涂长、间歇过程变化原因:背辊表面有浆料、未压牵引胶辊,背辊与涂辊间隙太小过紧解决方法:清洁背辊表面、调整间涂参数,压上牵引、胶辊故障:极片上有明显裂痕原因:干燥速度过快、烘箱温度过高、烘烤时间过长解决方法:检查相关涂布参数是否符合工艺要求故障:运行时极片打皱原因:1、过辊之间平行度;2、背辊、过辊表面有严重浆料或水;3、箔带接头不良致两边张力不平衡;4、纠偏系统异常或未开启纠偏;5、张力过大或过小;6、背辊拉开行程间隙不一致;7、背辊的橡胶表面在使用时间较长后发生周期弹性形变解决方法:1、调整过辊平行度;2、及时处理背辊及过辊间异物;3、先调节机头的张力调节辊,待箔材平稳后再调整到原来状态;5、检查张力设定值、各传动辊、收放辊的转动是否灵活,及时处理不灵活辊;6、把间隙适当扩大,再慢慢缩小到合适位置;7、出现弹性形变严重时,更换新胶辊故障:边缘鼓边原因:档料板泡棉阻挡导致解决方法:安装挡料板时呈外八字即可或移动挡料板时由外向内移动即可故障:漏料原因:挡料板泡棉或刮料板安装不紧解决方法:刮料板间隙稍比图层厚度大10-20微米,压紧挡料板泡棉故障:收卷不齐原因:收卷轴未安装好、未充气、纠偏未开启或未开启收卷张力解决方法:安装固定好收卷轴、气胀轴充气、开启纠偏功能、收卷张力等故障:两边留白不均原因:挡料板安装位置、放卷纠偏未开启解决方法:移动挡料板、检查收卷纠偏故障:反面间涂无法追踪原因:光纤无感应输入或正面无间涂解决方法:检查光纤头的检测距离、光纤参数、正面涂布效果故障:纠偏不动作原因:光纤参数不对、纠偏开关未开解决方法:检查光纤参数是否合理(纠偏指示灯有无左右闪烁),纠偏开关是否开启故障:涂布时有大气泡方案:1、搅拌不均匀,试下浆料回锅重搅拌2、涂布管道或挤压头腔体内有气体残留。
干货丨解决涂布中出现的缺陷,你需要懂得这些技术手段!

⼲货⼁解决涂布中出现的缺陷,你需要懂得这些技术⼿段!导读相信锂电池电极⼯程师经常遇到这样的问题:涂布过程中出现露箔、划痕、波浪、⾊差、暗斑、⾯密度波动……,诸多问题,那么我们必须去分析异常出现的原因,解决异常、总结经验,并且杜绝异常的再次出现。
涂布异常问题之多,多达数⼗项,但导致涂布缺陷出现的原因可以分为⼏⼤类:来料问题、涂布⼯艺不匹配、涂布设备异常、浆料表⾯张⼒问题、⼲燥异常等。
今天,我们不讲这些繁杂的缺陷及其原因,⼯欲善其事必先利其器,我们需要先了解分析涂布缺陷异常的技术⼿段有哪些。
根据平⽇所接触的缺陷,⼩编介绍常⽤的设备和分析⽅法供⼤家参考使⽤:⾸先我们需要知道确定缺陷的基本特征的⽅法,通俗⼀点就是说,判断缺陷处的特征,其⽬的是为了得到缺陷与正常处有何不同,有什么规律、⼤概是哪⽅⾯原因。
理论上,涂布出现问题时有很多科技⼿段来分析,但是⽣产过程中节拍快,能耗⼤,没有⾜够的时间去充分表征,需要依靠经验、分析能⼒、简便的测试仪器判断解决。
经验、分析能⼒因⼈⽽异,在基本数据收集⽅⾯我们可以各尽⼈⼒,平时使⽤的异常分析仪器和⽅法有:(1)影像仪、光学显微镜等影像仪和光学显微镜可以较⼤倍率放⼤涂布缺陷的外观,光学显微镜放⼤倍数可以达到⼏百倍,基本可以确定缺陷的外观,由此我们可以确定极⽚的表⾯缺陷是暗斑、硌伤、划痕抑或是其它缺陷。
(2)扫描电镜SEM和EDX扫描电镜的放⼤倍数可以达到数万倍,⽐光学显微镜放⼤倍数更⼤,此外它还有其它功能,其中⼀项重要功能是定性分析物质的元素组成,另外⼀项重要功能是扫描整体元素,获得正常位置和缺陷位置的元素差异。
举例1.若发现极⽚表⾯有⾊泽不⼀致的圈或者点,我们在⾁眼或光学显微镜下⽆法确定异常时,可以⽤SEM来进⼀步确定是什么缺陷;举例2.当发现有暗斑时,利⽤定性分析我们可以知道暗斑造成的原因时⽓泡还是异物?异物的组成时什么?这样我们可以获取更多的信息,按图索骥来解决问题的根源。
锂电池挤压涂布机原理及异常处理
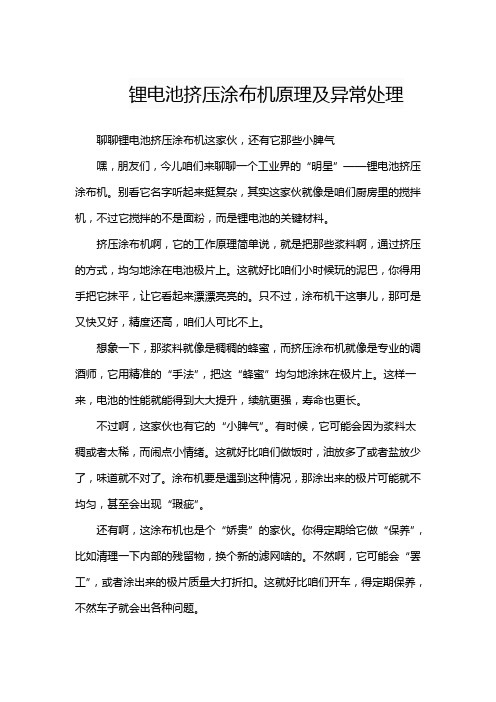
锂电池挤压涂布机原理及异常处理聊聊锂电池挤压涂布机这家伙,还有它那些小脾气嘿,朋友们,今儿咱们来聊聊一个工业界的“明星”——锂电池挤压涂布机。
别看它名字听起来挺复杂,其实这家伙就像是咱们厨房里的搅拌机,不过它搅拌的不是面粉,而是锂电池的关键材料。
挤压涂布机啊,它的工作原理简单说,就是把那些浆料啊,通过挤压的方式,均匀地涂在电池极片上。
这就好比咱们小时候玩的泥巴,你得用手把它抹平,让它看起来漂漂亮亮的。
只不过,涂布机干这事儿,那可是又快又好,精度还高,咱们人可比不上。
想象一下,那浆料就像是稠稠的蜂蜜,而挤压涂布机就像是专业的调酒师,它用精准的“手法”,把这“蜂蜜”均匀地涂抹在极片上。
这样一来,电池的性能就能得到大大提升,续航更强,寿命也更长。
不过啊,这家伙也有它的“小脾气”。
有时候,它可能会因为浆料太稠或者太稀,而闹点小情绪。
这就好比咱们做饭时,油放多了或者盐放少了,味道就不对了。
涂布机要是遇到这种情况,那涂出来的极片可能就不均匀,甚至会出现“瑕疵”。
还有啊,这涂布机也是个“娇贵”的家伙。
你得定期给它做“保养”,比如清理一下内部的残留物,换个新的滤网啥的。
不然啊,它可能会“罢工”,或者涂出来的极片质量大打折扣。
这就好比咱们开车,得定期保养,不然车子就会出各种问题。
记得有一次,车间里的涂布机突然“罢工”了。
大家伙儿都急得像热锅上的蚂蚁,生怕耽误了生产进度。
后来,经过一番检查,才发现是浆料的粘度出了问题。
咱们赶紧调整了粘度,重新开机,这才让涂布机恢复了正常工作。
所以啊,跟涂布机打交道,就像跟老朋友相处一样。
你得了解它的脾气秉性,知道它喜欢啥,不喜欢啥。
只有这样,你才能跟它“合作愉快”,共同生产出高质量的锂电池。
而且啊,这涂布机还是个“学霸”。
它的精度和效率,那可都是经过无数次的试验和优化才得来的。
咱们人类啊,有时候还真得向这些机器学习学习,看看它们是怎么做到精准无误的。
当然啦,涂布机也不是万能的。
有时候,它也会遇到一些解决不了的问题。
锂离子电池搅拌和涂布工艺及异常处理

锂离子电池(含动力电池)搅拌和涂布工艺知识及异常处理新能源的锂离子电池发展很快,作为锂离子电池制造,每个工厂都在不断创新新的工艺,而这个工艺的发展速度很快,而真正核心的技术是新材料配方的应用和制作极片(涂布)过程中遇到问题的解决成为一个难点,而这个难点需要系统的知识才能解决,总结十几年的心得体会供大家学习。
主要内容有:一、术语二、正极材料三、负极材料四、陶瓷隔离膜材料五、正极搅拌六、负极搅拌七、陶瓷隔离膜搅拌八、正极涂布九、负极涂布十、陶瓷隔离膜tubu十一、正极底涂印刷一术语1.1 粘度:粘度是指液体受外力作用移动时,分子间产生的内磨擦力的量度;单位是mpa.s,我们测量粘度用旋转粘度计:包括一块平板和一块锥板样品粘度越大,扭矩越大。
扭矩检测器内设有一个可变电容器,其动片随着锥板转动,从而改变本身的电容数值。
这一电容变化反映出的扭簧扭矩即为被测样品的粘度,由仪表显示出来。
1.2 颗粒度:粒的大小。
通常球体颗粒的粒度用直径表示,立方体颗粒的粒度用边长表示。
一般所说的粒度是指造粒后的二次粒子的粒度。
表示粒度特性的几个关键指标:D50/D90/D991.3 比表面积:单位重量的颗粒的表面积之和。
比表面积的单位为m2/kg或cm2/g。
比表面积与粒度有一定的关系,粒度越细,比表面积越大,但这种关系并不一定是正比关系。
1.4 固含量:浆料中固体物质质量占总质量的百分比1.5 透气度:严格来讲应该称为透气度或者透气量。
空气透过织物(PE及PTFE等等)的性能。
以在规定的试样面积、压降和时间条件下,气流垂直通过试样的速率表示。
对于我们所做的陶瓷隔离膜,透气度越大,说明孔隙率小。
1.6 公转:对我们搅拌来讲就是一个浆绕着另一个浆转动叫做公转1.7 自转:是指物件自行旋转的运动,物件会沿著一条穿越身件本身的轴进行旋转,这条轴被称为自转轴。
1.8 搅拌速度:每分钟搅拌的速度,单位是RPM1.9 涂布重量:一般厂家是按照面密度来做,有的移50*100=500m2为单位,有的是以标准的圆1540.25MM2的重量来做为标准单位设计和监控1.10 压实密度:=面密度/(极片碾压后的厚度—集流体厚度) ,单位:g/cm3压实密度,冷压后的不含基材的厚度1.11 振实密度:在规定条件下容器中的粉末经振实后所测得的单位容积的质量,振实密度与压实密度不成正比例关系1.12 克容量:实际指的并不是“电池”的克容量,而是电池内部材料如:磷酸铁锂、钴酸锂、锰酸锂、镍酸锂等等的克容量,每种材料的克容量是不相同的。
- 1、下载文档前请自行甄别文档内容的完整性,平台不提供额外的编辑、内容补充、找答案等附加服务。
- 2、"仅部分预览"的文档,不可在线预览部分如存在完整性等问题,可反馈申请退款(可完整预览的文档不适用该条件!)。
- 3、如文档侵犯您的权益,请联系客服反馈,我们会尽快为您处理(人工客服工作时间:9:00-18:30)。
锂电池极片挤压涂布常见缺陷
目前,电动车、储能电池等新能源产业在全球范围内发展迅速。
作为公认的理想储能元件,动力锂电池也得到高度关注。
涂布机是动力锂电池极片的生产关键工艺设备。
目前,锂电池极片涂布工艺主要有刮刀式、辊涂转移式和狭缝挤压式等。
我在工作过程中,这三种涂布方式都接触过。
一般实验室设备采用刮刀式,3C电池采用辊涂转移式,而动力电池多采用狭缝挤压式。
刮刀涂布
工作原理如图1所示,箔基材经过涂布辊并直接与浆料料槽接触,过量的浆料涂在箔基材上,在基材通过涂辊与刮刀之间时,刮刀与基材之间的间隙决定了涂层厚度,同时将多余的浆料刮掉回流,并由此在基材表面形成一层均匀的涂层。
刮刀类型主要逗号刮刀。
逗号刮刀是涂布头中的关键部件之一,一般在圆辊表面沿母线加工成形似逗号的刃口,这种刮刀具有高的强度和硬度,易于控制涂布量和涂布精度,适用于高固含量和高黏度的浆料。
图1 逗号刮刀涂布示意图
辊涂转移式
涂辊转动带动浆料,通过逗号刮刀间隙来调节浆料转移量,并利用背辊和涂辊的转动将浆料转移到基材上,工艺过程如图2所示。
辊涂转移涂布包含两个基本过程:(1)涂布辊转动带动浆料通过计量辊间隙,形成一定厚度的浆料层;(2)一定厚度的浆料层通过方向相对的涂辊与背辊转动转移浆料到箔材上形成涂层。
图2 辊涂刮刀转移涂布工艺示意图
狭缝挤压涂布
作为一种精密的湿式涂布技术,如图3所示,工作原理为涂布液在一定压力一定流量下沿着涂布模具的缝隙挤压喷出而转移到基材上。
相比其它涂布方式,具有很多优点,如涂布速度快、精度高、湿厚均匀;涂布系统封闭,在涂布过程中能防止污染物进入,浆料利用率高、能够保持浆料性质稳定,可同时进行多层涂布。
并能适应不同浆料粘度和固含量范围,与转移式涂布工艺相比具有更强的适应性。
图3狭缝挤出式涂布示意图
要形成稳定均匀的涂层,涂布过程中就需要同时满足这几个条件:
(1)浆料性质稳定,不发生沉降,粘度、固含量等不变化。
(2)浆料上料供应稳定,在模头内部形成均匀稳定的流动状态。
(3)涂布工艺在涂布窗口范围内,在模头与涂辊之间形成稳定的流场。
(4)走箔稳定,不发生走带滑动,严重抖动和褶皱。
涂布操作窗口是狭缝涂布一个重要的工艺参数,在实际
生产中,当工艺参数超出操作窗口的范围时,涂布缺陷便会产生。
而涂布膜出现的缺陷种类众多,原因各异,本文主要针对锂离子电池狭缝挤压涂布,就几种常见缺陷进行分析,并给出相应解决方案。
常见缺陷有点缺陷、边缘效应、锯齿缺陷等。
1点状缺陷
1.1气孔:一是气泡产生(搅拌过程、输运过程、涂布过程); 气泡产生的针孔缺陷比较容易理解,湿膜中的气泡从内层向膜表面迁移,在膜表面破裂形成针孔缺陷。
气泡主要来自搅拌、涂液输运以及涂布过程。
1.2异物缩孔:各种颗粒(灰尘、油污、金属颗粒等) 产生。
外来颗粒的存在导致颗粒表面处的湿膜存在低表面张力区域,液膜向颗粒周围发射状迁移,形成缩孔点状缺陷,如图4所示。
预防措施主要有:涂液过滤除铁、环境粉尘控制、基材表面清洁。
图4 异物颗粒处表面张力低,涂液向四周迁移
1.3 团聚体颗粒凸起:如果浆料搅拌不均匀,导电剂没有分散开,形成团聚体时就会产生此类缺陷,如图5所示,极片表面出现大面积的凸起,放大这些地方观察,发现这是导电剂的团聚体。
这种缺陷主要还是改善浆料搅拌工艺来消
除。
图5团聚体颗粒凸起SEM形貌
2线状缺陷
2.1划痕:与涂布方向平行的线状薄区或漏箔线条,如图6所示。
图6 涂布极片划痕缺陷
•可能原因
–异物或大颗粒卡在狭缝间隙内或涂布间隙上
–基材质量不佳,造成有异物挡在涂辊与背辊的涂布间隙上
–模具模唇损伤
•对策
–清除唇口或涂布间隙的颗粒、检查模头唇口
2.2竖条道:与涂布方向平行的波纹,如图7所示。
图7 涂布极片竖条道缺陷
•可能原因
–通常发生于接近涂布窗口的速度上限,薄涂层更明显。
•对策
–调整浆料粘度
–降低涂布速度
–降低涂辊与背辊之间的涂布间隙
2.3横向纹:垂直于涂布方向,固定间隔所产生的波纹或线条。
•可能原因
–机械震动
–走带速度波动
–浆料供料的流动发生周期性波动
•对策
–确认机械扰动频率与横纹发生频率是否相同
3边缘效应
3.1厚边:涂布过程,经常出现边缘厚,中间薄的现象,即厚边。
产生厚边的原因是表面张力驱动下的物质迁移。
如图8所示,开始时,湿膜的边缘处较薄,溶剂挥发速度较中间快,导致边缘固含量迅速升高,边缘的表面张力远大于中间湿膜的表面张力,边缘处较大的表面张力以及较快的溶剂挥发驱动内侧液体向边缘移动,烘干后形成厚边。
图8 干燥过程中厚边现象产生过程
涂布厚边现象是一种不利的缺陷,阻止和缓解厚边现象的措施有:
(1)浆料流量一定时,减小狭缝尺寸能够增加浆料在模头的出口速度,从而降低浆料的拖曳力比值,进而减小厚边涂层的厚度,但是狭缝尺寸变小模头内部的压力更大,更容易造成模头出口形状的膨胀,从而出现涂层横向厚度不均匀性,这需要更高精度的涂布设备配合。
(2)涂布间隙减小能够有限减小厚边涂层的厚度和宽度。
(3)降低浆料的表面张力,如添加界面活性剂等,抑制干燥过程中浆料向边缘的流延。
(4)优化狭缝垫片出口形状,改变浆料流动速度方向和大小,降低边缘浆料的应力状态,减弱浆料边缘膨胀效应。