闪蒸釜输料堵塞的原因分析及预防措施
PP装置闪蒸罐出料阀堵塞紧急预案的优化

摘
要 : 对 聚 丙 烯 装置 扩 能 改 造 后 , 置 各 设 备 间 的 匹配 及操 作 弹 性 下 降 , 装 致使 原 闪蒸 罐 底 部 t 料 阀堵 塞 的 t l
紧 急 预案 不 再 适 用 原 有预 案 存 在 反 直系 统 安 全平 稳 性 下 降 、 急排 放 罐 能 力不 足 、 紧 丙烯 浪 费等 问 题 经 过优 化 , 在
工 业技 术
合成树脂及塑料,0 ,5 )CS 28 2(:4 0 PL6 4 CHI NA SYNT HET C I RES N I AND AS TI
P P装置 闪蒸罐 出料 阀堵塞 紧 急预 案 的优 化
苏 俊
( 同石 油 化 _股 份 有 限 公 司荆 门分 公 司t TJ 湖 北 荆 门 , 4 0 9 巾 } i . : 一, 483)
正 常 生 产时 ,反应 物 料经 高压 闪蒸 线 、 3 1 HV 0
闪 蒸 温 度 过 低 ( 于 5 ,而 引 起 的 闪 蒸 罐 底 小 5c c)
T 艺方 向进 入 闪 蒸 罐 , 步 分 离 聚 合 物 和 丙 烯 单 初 体 。L 3 1 4 m 的 V 型 球 阀 。聚 合 物 粉 料 在 V 0 为 0m 闪 蒸 罐 底 部 停 留时 间过 长 或 高 压 闪 蒸 线 中形 成 的
切入紧急排放罐 , 达到隔离闪蒸罐 的 目的。 具体方
案为 : ( ) 故判 断 一旦 闪 蒸 罐 料 位 迅 速 上 升 ,立 1事 即将 H 3 l 至 排 放 方 向 , 0 10 大 幅 活 动 V 1切 在 —0 % L 3 1 以料 位 下 降 及 闪蒸 罐 顶 部 气 体 流 量 明 显 V 0, 降 低 来 判 断 出料 是 否畅 通 。此 时 应 注 意 排 除 因 为
酸站闪蒸系统常见故障探讨

酸站闪蒸系统常见故障探讨酸站闪蒸系统是一种常用于化工生产中的蒸发器系统,它能够对酸性溶液进行蒸发浓缩,很好地满足了酸性溶液处理的需求。
在长时间的运行中,酸站闪蒸系统也会出现一些常见的故障问题。
本文将探讨一些可能出现的故障,并提供相应的解决方案。
一个常见的问题是酸站闪蒸系统中泵的故障。
酸站闪蒸系统中通常会使用泵进行酸液的输送,在长时间的运行中,泵可能会出现堵塞、漏水、泄露等问题。
在出现这些故障时,我们可以首先检查泵的进出口是否有堵塞物,可以清洗或更换相关的部件;对于泵的漏水问题,可以进行密封件的更换或调整;如果是泄露问题,可以对相关管道进行检查,修复损坏的部分。
酸站闪蒸系统中加热器的故障也比较常见。
加热器是酸站闪蒸系统中非常重要的设备,它通过提供热量来促使酸液的蒸发。
在长时间运行中,加热器可能会出现加热不充分、加热不均匀、漏电等问题。
对于这些故障,我们可以首先检查加热器的加热元件是否完好,可以进行更换;对于加热不均匀的问题,可以调整加热器的温度、流量等参数;对于漏电问题,可以检查加热器的绝缘状况,进行维修。
酸站闪蒸系统中常见的故障还包括控制系统的故障和传感器的故障。
控制系统是酸站闪蒸系统中用于控制温度、压力等参数的重要部分,而传感器则是用于监测这些参数的设备。
在长时间运行中,控制系统可能会出现无法正常启动、失灵等问题,而传感器可能会出现误差、无法检测等问题。
在出现这些故障时,我们可以检查控制系统的电源、线路连接是否正常;对于传感器的故障,可以进行校准或更换。
除了以上提到的常见故障,酸站闪蒸系统在运行中还可能出现其他一些故障问题,如阀门的故障、管道的堵塞等。
对于这些问题,我们需要根据具体情况进行分析和解决。
酸站闪蒸系统在长时间运行中,可能会出现泵的故障、加热器的故障、控制系统的故障和传感器的故障等问题。
对于这些故障,我们需要进行及时的排查和解决,以保证酸站闪蒸系统能够正常运行,达到预期的蒸发浓缩效果。
酸站闪蒸系统常见故障探讨

酸站闪蒸系统常见故障探讨酸站闪蒸系统是一种常用的化工设备,其作用是将进入系统的混合气体进行分离和除湿。
正常情况下,酸站闪蒸系统可以稳定运行并达到预期效果。
然而,在使用过程中,用户经常会遇到运行故障并需要进行排解。
以下是酸站闪蒸系统常见故障的讨论。
1. 凝结水管堵塞凝结水管是连接冷凝器和脱除器的重要管道,其作用是将凝结水从冷凝器中放出,并将其送至脱除器。
如果凝结水管堵塞,就会导致凝结水无法流入脱除器,同时也会限制气体的流动。
在这种情况下,可以检查凝结水管是否有杂物,如异物和沉淀物。
如果有,应该清理管道并确保凝结水顺畅。
2. 溢流阀不工作溢流阀是酸站闪蒸系统中的一个重要组件,其作用是控制气体流量,并保持系统的稳定性。
如果溢流阀不工作,就会导致气体压力增加,从而影响整个系统的性能。
在这种情况下,可以检查溢流阀是否正确安装,并检查是否存在阀门内部的问题,如磨损和松动。
3. 冷凝器故障冷凝器是酸站闪蒸系统中的一个重要组件,其作用是冷却混合气体并将其转化为液体。
如果冷凝器故障,就会导致气体无法被冷却和分离,并且在系统内部产生过高的压力。
在这种情况下,可以检查冷凝器是否损坏或管道是否堵塞,并采取必要的措施进行修理和清洗。
4. 气缸内部故障5. 粘液管道堵塞总之,酸站闪蒸系统常见故障的排解需要多方面因素的综合考虑。
如果遇到故障,用户应该及时进行检查和维修,以确保系统能够顺利运行并达到预期效果。
同时,用户还应该根据系统的特点和运行情况,制定相应的维护计划和安全措施,以保障设备的长期稳定运行。
液氮洗装置中液化天然气储罐闪蒸气通道堵塞原因分析及对策

&'( 罐顶 )*(
)*( 压缩机出口气
/0%!1 /*!!#2.- 露点 /*!!#2.- 露点
,"-0 年 -" 月 第 7- 卷第 D 期
#$%&' ()$*' +,-%.&'/.01 2'%-,*,3'% 4/501-%6
+CE1,"-0 F$&17- 5$1D
液氮洗装置中液化天然气储罐闪蒸气通道堵塞
原因分析及对策
樊志强!谢晋琴!李录彦
'山西中煤平朔能源化工有限公司!山西朔州 "!3""3$
5% )*( 压缩机为往复式机组!原动机带动曲
判断是否因其指标不合格导致通道堵塞(
轴旋转!而曲轴通过连杆与活塞杆相连!连杆将曲
!% )*( 压缩机置换不彻底( 试车之初!)*( 轴的旋转运动转换为活塞的往复运动! 活塞在气
压缩机开停较为频繁!在其停车期间!)*( 压缩机 缸内对 )*( 进行压缩(在出界区之前有一油水分
冷箱的大部分合成气温度很低! 一部分被送到低 温甲醇洗装置用于冷却原料气! 另一部分气体通 过主换热器升温至环境温度&
氮洗塔的塔釜液组成主要为 5,(6+( 部分溶 解的 4, 和 647&这股液体膨胀后进入氮气 " 甲烷闪 蒸塔塔顶闪蒸!以 提 高 647 的 回 收 率 &氮 气 " 甲 烷 闪蒸塔是用来从 6+ 和 4, 中分离甲烷液体! 上升 气体由氮气 "甲烷闪蒸塔塔底再沸器分离出的气 体和来自液化天然气储罐顶部的闪蒸气体'以下 称为 #+( 或 85( 罐顶 #+($组成!中间回流液由 气体提纯分离罐提供! 塔顶回流液来自于氮洗塔 塔底釜液&该塔在低压下操作!从塔顶出来的气体 在 主 换 热 器 中 升 温 后 ! 到 尾 气 压 缩 机 加 压 到 !1, 9:)! 送 至 变 换 装 置 & 塔 底 的 液 态 甲 烷 产 品 用 甲 烷
酸站闪蒸系统常见故障探讨

酸站闪蒸系统常见故障探讨【摘要】酸站闪蒸系统是化工工程中常见的设备之一,其正常运行对生产过程至关重要。
由于长期运行和不良操作等因素,闪蒸系统存在着多种常见故障。
本文通过介绍酸站闪蒸系统的概述,以及常见的四种故障类型:闪蒸器渗漏、传热管结垢、水位控制失灵和泵故障,分析了故障的可能原因和解决方法。
在对故障进行了总结,展望了未来可能的发展趋势,并提出了相关建议,希望可以为相关工程技术人员和操作人员提供一些参考,保障酸站闪蒸系统的正常运行,确保生产的顺利进行。
通过对酸站闪蒸系统常见故障的探讨,可以提高相关人员的故障排除能力,提升设备的稳定性和可靠性,达到预期的生产效果。
【关键词】酸站闪蒸系统、常见故障、闪蒸器渗漏、传热管结垢、水位控制失灵、泵故障、问题分析、解决方案、预防措施、维护保养、优化运行、安全性。
1. 引言1.1 介绍酸站闪蒸系统是一种常用于化工生产中的设备,可以实现原料的蒸发和浓缩。
其主要由闪蒸器、传热管、水位控制装置和泵等部件组成。
在使用过程中,酸站闪蒸系统常常会出现各种故障,影响生产效率和安全性。
为了更好地了解酸站闪蒸系统常见故障及排除方法,本文将对闪蒸器渗漏、传热管结垢、水位控制失灵和泵故障等常见问题进行探讨。
通过对这些故障的分析和解决,可以帮助工程师更好地维护和管理酸站闪蒸系统,提高生产效率和质量。
在接下来的我们将逐一介绍这些常见故障的具体表现、可能的原因和解决方法。
希望通过本文的分享,能为读者提供更多关于酸站闪蒸系统的知识,帮助他们在实际工作中更好地应对各种挑战。
1.2 目的本文的目的是探讨酸站闪蒸系统常见故障,并分析造成这些故障的原因以及解决方法。
通过对酸站闪蒸系统的常见故障进行深入研究,我们可以更好地了解系统运行过程中可能出现的问题,并及时采取相应的维修措施以保障系统的正常运行。
通过对这些故障的探讨,我们还可以总结出一些预防措施和维护方法,帮助管理人员提高系统的运行效率和可靠性,减少因故障带来的生产损失和安全隐患。
酸站闪蒸系统常见故障探讨
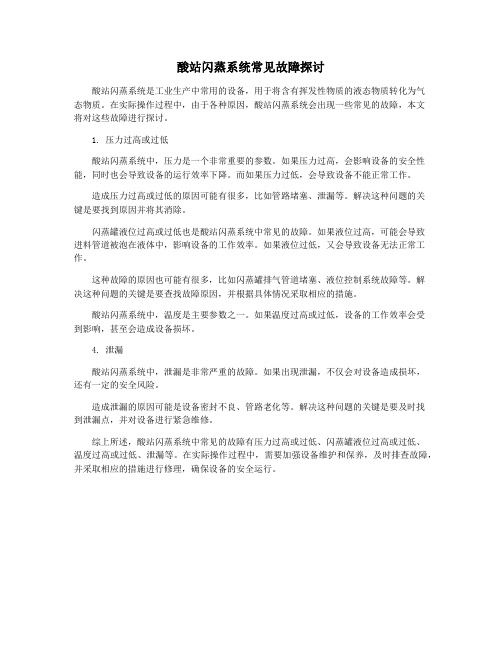
酸站闪蒸系统常见故障探讨酸站闪蒸系统是工业生产中常用的设备,用于将含有挥发性物质的液态物质转化为气态物质。
在实际操作过程中,由于各种原因,酸站闪蒸系统会出现一些常见的故障,本文将对这些故障进行探讨。
1. 压力过高或过低酸站闪蒸系统中,压力是一个非常重要的参数。
如果压力过高,会影响设备的安全性能,同时也会导致设备的运行效率下降。
而如果压力过低,会导致设备不能正常工作。
造成压力过高或过低的原因可能有很多,比如管路堵塞、泄漏等。
解决这种问题的关键是要找到原因并将其消除。
闪蒸罐液位过高或过低也是酸站闪蒸系统中常见的故障。
如果液位过高,可能会导致进料管道被泡在液体中,影响设备的工作效率。
如果液位过低,又会导致设备无法正常工作。
这种故障的原因也可能有很多,比如闪蒸罐排气管道堵塞、液位控制系统故障等。
解决这种问题的关键是要查找故障原因,并根据具体情况采取相应的措施。
酸站闪蒸系统中,温度是主要参数之一。
如果温度过高或过低,设备的工作效率会受到影响,甚至会造成设备损坏。
4. 泄漏酸站闪蒸系统中,泄漏是非常严重的故障。
如果出现泄漏,不仅会对设备造成损坏,还有一定的安全风险。
造成泄漏的原因可能是设备密封不良、管路老化等。
解决这种问题的关键是要及时找到泄漏点,并对设备进行紧急维修。
综上所述,酸站闪蒸系统中常见的故障有压力过高或过低、闪蒸罐液位过高或过低、温度过高或过低、泄漏等。
在实际操作过程中,需要加强设备维护和保养,及时排查故障,并采取相应的措施进行修理,确保设备的安全运行。
闪蒸干燥机的常见故障现象、原因分析及排除方法
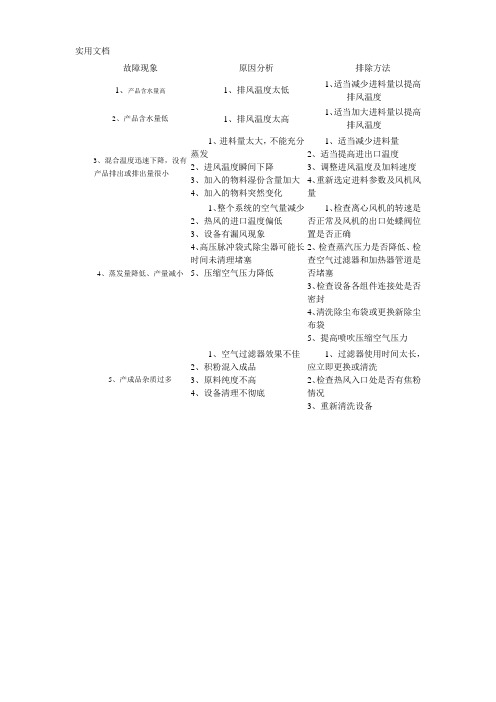
3、调整进风温度及加料速度
4、重新选定进料参数及风机风量
4、蒸发量降低、产量减小
1、整个系统的空气量减少
2、热风的进口温度偏低
3、设备有漏风现象
4、高压脉冲袋式除尘器可能长时间未清理堵塞
5、压缩空气压力降低
1、检查离心风机的转速是否正常及风机的出口处蝶阀位置是否正确
2、检查蒸汽压力是否降低、检查空气过滤器和加热器管道是否堵塞
3、检查设备各组件连接处是否密封
4、清洗除尘布袋或更换新除尘布袋
5、提高喷吹压缩空气压力
5、产成品杂质过多
1、空气过滤器效果不佳
2、积粉混入成品
3、原料纯度不高
4、设备清理不彻底
1、过滤器使用时间太长,应立即更换或清洗
2、检查热风入口处是否有焦粉情况
3、重新清洗设备
故障现象
原因分析
排除方法
量以提高排风温度
2、产品含水量低
1、排风温度太高
1、适当加大进料量以提高排风温度
3、混合温度迅速下降,没有产品排出或排出量很小
1、进料量太大,不能充分蒸发
2、进风温度瞬间下降
3、加入的物料湿份含量加大
4、加入的物料突然变化
1、适当减少进料量
蒸压釜的常见故障及其处理方法详解

蒸压釜的常见故障及其处理方法详解(总7页)“本页仅作为文档封面,使用时请直接删除即可一"内页可以根据需求调整合适字体及大小一蒸压釜的常见故障及其处理1・蒸压釜的釜内腐蚀釜体的腐蚀就是材料和它所处的周围环境发生作用而使材料产生损坏或使其性质发生恶化的现象。
蒸压釜的釜内腐蚀已成为影响其安全运行的一个主要因素。
蒸压釜的腐蚀大致可分为:表面腐蚀、应力裂纹腐蚀、疲劳裂纹腐蚀。
表面腐蚀:这种腐蚀存在于釜的底部冷凝水区域内,它是通过在冷凝水中的腐蚀性电解液和高温下溶解数量增加了的氧而产生的,在浓缩的腐蚀性电解液里.这种损坏显着提高。
这种腐蚀的主要原因是从蒸养小车上掉下来的加气混凝土坯料或砖料粘着在釜体,逐步形成单独分布的腐蚀孔洞,表面腐蚀也可能有裂纹生存。
应力裂纹腐蚀:这种腐蚀主要出现在釜体的底部,也出现在轨道支座焊接点的周围,这种腐蚀通过在釜底内表面上焊缝的拉力和内应力与冷凝水中的碳金属氢氧化物溶液的共同作用而形成。
这种腐蚀是最危险的一种,因为从不同部位产生的许多小裂纹会很快地发展并连接在一起,形成导致蒸压釜爆炸的大裂纹。
这种腐蚀的主要原因是由于釜内的冷凝水不能及时排除,釜顶和釜底内表面的温差所引起。
疲劳裂纹腐蚀:这种腐蚀的出现范围同应力裂纹腐蚀相同,不同的仅是以穿过金属晶粒的形成发展的,它通过机械交变应力和腐蚀性介质的共同作用而形成腐蚀。
这种腐蚀的主要原因是由于蒸压釜一直处在周期性运行过程中,釜壁温度若是波动或有差异,以及冷凝水的位置有波动,很容易发生晶间的应力裂纹腐蚀和穿晶疲劳裂纹腐蚀。
上述的几种腐蚀在实际运行的蒸压釜中并不单独发生,有时是同时存在的,而且几种腐蚀形式一再叠加,使蒸压釜的腐蚀速率加快。
这种情况可使釜在投入运行几个月就会发生严重的腐蚀现象。
为避免蒸压釜发生严重的腐蚀情况,在使用中应该注意以下几个问题:A、减少进入釜内的氧含量并尽量排除釜内的空气,提高蒸汽的质量,即减少蒸汽中的含氧量;进出料车时,尽量缩短进出时间;在通入蒸汽前应进行抽真空并适当提高真空度。
闪蒸釜输料堵塞的原因分析及预防措施

闪蒸釜输料堵塞的原因分析及预防措施闪蒸釜输料堵塞的原因分析及预防措施许雄杰宗林曹雄聚丙烯车间炼化总⼚聚丙烯装置1990年破⼟动⼯,1992年建成投产,采⽤间歇式液相本体法⽣产⼯艺,经过多次技术改造和科技投⼊,特别是在2005年装置扩容改造后,现有8台聚合釜,7台闪蒸釜,⽣产能⼒为4万吨/年。
闪蒸釜是聚丙烯⽣产的主要设备,在整个⼯艺流程中的作⽤极其重要,其能否正常运作直接决定了⽣产的持续性和后续系统操作的稳定性。
因此,保证闪蒸釜输料通畅,才能避免聚合釜中丙烯的回收处理,保障聚合持续进⾏,减少丙烯损耗。
1 闪蒸釜输料现状分析间歇式聚丙烯⽣产,车间选⽤12m3聚合釜,10m3闪蒸釜配套操作(F311除外)。
闪蒸釜下部为倒锥形,可加快粉料出料速度,预防釜内粉料⼤量残留,通过卸料阀接连φ100mm 输料管道⾄储料仓。
输料期间,循环氮⽓通过⽓动⾓阀往输料管道内通⼊压缩氮⽓,将粉料切割成拴状(即⼀段粉料柱,⼀段⽓柱)。
多年的⽣产实践发现,聚丙烯粉料夹带块料是输料堵塞的主要原因。
正常平稳操作,⼀般不会发⽣闪蒸釜输料堵塞现象,然⽽随着DJD-Z等⾼效催化剂的相继投⽤,装置多次扩容改建,以及聚合釜传热能⼒弱化,聚丙烯粉料时有块料产⽣,给⽇常⽣产运⾏增添不少操作难题。
聚丙烯粉料夹带块料,可使闪蒸釜输料不畅,甚⾄管道堵塞,若未及时妥当处理,容易阻滞聚合投料持续进⾏,造成丙烯⼤量回收,不利于丙烯单耗的降低。
2块料产⽣原因分析聚丙烯粉料夹带块料,影响了装置的安、稳、长、满、优运⾏,事实上,国内外同类装置也经常遇上同样的难题,现在从⼯艺选择、设备状况及⽣产操作等⽅⾯探讨分析块料产⽣的原因。
2.1 催化剂和活化剂过量,聚合反应剧烈实践表明,原料丙烯中的杂质含量偏⾼,可使⾼效催化剂的活性受到抑制,尤其是⽔等有害杂质。
聚合反应中,活化剂的作⽤,⼀是与催化剂配位形成活性中⼼,⼆是消除原料丙烯的少量杂质。
因此,活化剂加⼊量除了与催化剂量有关,还与原料丙烯质量有很⼤关系。
酸站闪蒸系统常见故障探讨

酸站闪蒸系统常见故障探讨
酸站闪蒸系统是一种常见的化工设备,常用于氯化氢、盐酸等化学品的生产过程中。
由于操作不当、设备老化等原因,闪蒸系统在实际运行中可能会出现各种故障。
本文将探讨酸站闪蒸系统常见故障及其解决方法。
1. 管道堵塞:由于生产过程中酸类物质极易结晶,在系统中会产生结垢,导致管道堵塞。
解决方法可以采用清洗管道、加热管道或更换部分管道等方式。
2. 泵失效:闪蒸系统中的泵是重要的设备之一,如果泵失效,将无法正常进行液体的输送。
解决方法包括检查泵的电机运行情况、调整泵的进出口阀门以及更换泵等。
3. 传热效果差:闪蒸系统中的传热器是用来将热量传递给酸类物质的关键设备,如果传热效果差,将导致系统温度无法达到要求。
解决方法可以通过清洗或更换传热器来改善传热效果。
4. 温度控制不准确:闪蒸系统中的温度控制对于化学反应的进行至关重要,如果温度控制不准确,将影响产品的质量和产量。
解决方法可以采用更换温度传感器、调整温度控制阀门或更换控制系统等方式。
5. 压力异常:闪蒸系统中的压力异常可能导致设备破裂,对操作人员和设备造成安全风险。
解决方法可以通过增加安全阀的负载压力、调整闪蒸系统的工作压力或更换安全阀等方式。
6. 气体泄漏:闪蒸系统中的气体泄漏会造成环境污染和工作人员安全隐患。
解决方法可以采用检查阀门和管道的密封性、更换泄漏阀门或加强管道的维护等方式。
酸站闪蒸系统常见故障的解决方法主要包括清洗管道、更换设备、调整阀门控制等。
在实际操作中,操作人员应加强设备的维护保养,定期检查设备的工作状态,及时发现并处理潜在故障,确保系统的正常运行。
酸站闪蒸系统常见故障探讨

酸站闪蒸系统常见故障探讨
酸站闪蒸系统在石油化工生产过程中起着至关重要的作用,但是在长时间的使用中,会出现一些常见的故障问题。
本文将结合实际生产经验,探讨这些故障问题可能的原因和解决办法。
一、闪蒸器运行不平稳
闪蒸器运行不平稳的原因有多种,例如闪蒸器进料浓度不稳定,闪蒸器进料温度变化大,闪蒸器级数不合理,闪蒸器内部结构不当等。
因此,需要注意以下几点:
1.调整进料流量使其稳定。
2.保持进料温度的稳定性,可采用前置加热器、改变蒸汽压力等方法。
3.优化闪蒸器的级数,适当调整进出料口的位置,以便使进出料流更加均匀。
4.优化闪蒸器内部结构,改善物料在闪蒸器内的流动性和均匀性。
二、闪蒸器壳体温度异常升高
一般来说,闪蒸器壳体温度升高的原因可能是负荷过大、进出料温差过大等导致的。
如果发现闪蒸器壳体温度异常升高,需要注意以下几点:
1.适当减少进料流量,降低闪蒸器负荷。
2.调整进出料口的位置和尺寸,使得进出料流均匀,避免进出料温差过大。
3.使用合适的绝热材料,增加闪蒸器的绝热性能。
四、闪蒸器水泵故障
闪蒸器水泵故障主要是由于泵内物质积累、泵轴承老化、流量计磨损等导致的。
为了解决水泵故障问题,我们需要注意以下几点:
1.定期清理水泵内部物质,避免积累导致故障。
2.适时更换泵轴承,避免老化导致故障。
3.使用高品质的流量计,从源头上避免磨损导致故障问题。
总之,在酸站闪蒸系统的运行过程中,无法避免地会出现一些故障问题,但是通过以上的探讨,我们可以找到一些解决办法,提高闪蒸系统的稳定性和可靠性,保证石油化工生产的连续稳定运行。
酸站闪蒸系统常见故障探讨

酸站闪蒸系统常见故障探讨
酸站闪蒸系统主要用于酸站脱水过程中,将水蒸发出来,使得酸站中的酸浓缩。
然而,在使用过程中,酸站闪蒸系统也会出现一些常见故障,下面就对几种常见故障进行探讨。
一、酸液倒回闪蒸系统
酸站闪蒸系统中的料槽与酸液盘管之间需要设置闪蒸器,在酸液盘管内蒸发出水汽后,通过闪蒸器排出系统。
但当酸站中的酸浓缩程度不足或闪蒸器出现堵塞时,会导致酸液大
量倒回到闪蒸系统中。
这时需要迅速关闭闪蒸器并将系统中的酸液放空,以免影响随后的
酸站操作。
二、闪蒸器堵塞
酸站闪蒸系统中的闪蒸器是将酸液盘管中的水蒸发掉的关键部件。
但闪蒸器在操作过
程中容易出现堵塞,导致水汽无法排出,影响到后续的操作。
处理方法可通过拆装闪蒸器
进行清洗,如未能清除堵塞物体,可以更换闪蒸器。
三、温度异常
闪蒸器所在的酸液盘管需要控制温度,如果温度过高或过低,都会影响到酸站的操作。
比如温度过高会导致液态酸与气态水汽发生化学反应,产生酸雾,而温度过低则会导致闪
蒸器无法正常蒸发水汽。
因此,在实际操作中要时刻监控系统温度,并及时调整。
四、气流不足
闪蒸器正常工作需要充足的气流,但在使用过程中会出现气流不足的情况,导致闪蒸
效果差。
如发现气流不足,可通过增加气流量或增大闪蒸器的表面积来解决问题。
总之,酸站闪蒸系统的运作需要实时检测和维护,及时解决故障可有效保证酸站的正
常运行,提高生产效率。
HDPE采样闪蒸系统堵塞原因及对策
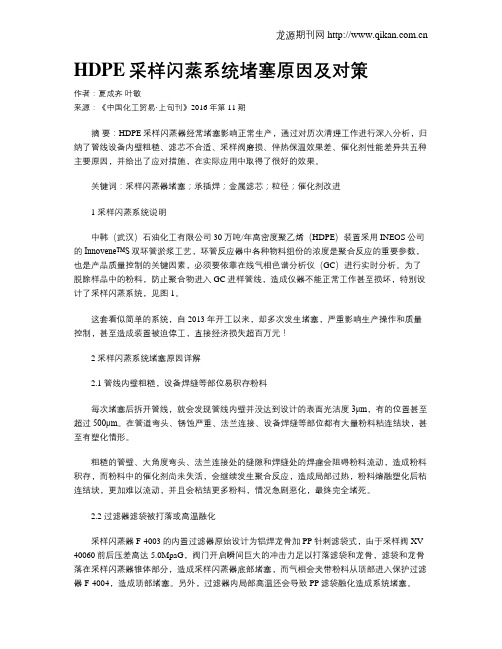
HDPE采样闪蒸系统堵塞原因及对策作者:夏成齐叶敏来源:《中国化工贸易·上旬刊》2016年第11期摘要:HDPE采样闪蒸器经常堵塞影响正常生产,通过对历次清理工作进行深入分析,归纳了管线设备内壁粗糙、滤芯不合适、采样阀磨损、伴热保温效果差、催化剂性能差异共五种主要原因,并给出了应对措施,在实际应用中取得了很好的效果。
关键词:采样闪蒸器堵塞;承插焊;金属滤芯;粒径;催化剂改进1 采样闪蒸系统说明中韩(武汉)石油化工有限公司30万吨/年高密度聚乙烯(HDPE)装置采用INEOS公司的Innovene™S双环管淤浆工艺,环管反应器中各种物料组份的浓度是聚合反应的重要参数,也是产品质量控制的关键因素,必须要依靠在线气相色谱分析仪(GC)进行实时分析。
为了脱除样品中的粉料,防止聚合物进入GC进样管线,造成仪器不能正常工作甚至损坏,特别设计了采样闪蒸系统,见图1。
这套看似简单的系统,自2013年开工以来,却多次发生堵塞,严重影响生产操作和质量控制,甚至造成装置被迫停工,直接经济损失超百万元!2 采样闪蒸系统堵塞原因详解2.1 管线内壁粗糙,设备焊缝等部位易积存粉料每次堵塞后拆开管线,就会发现管线内壁并没达到设计的表面光洁度3μm,有的位置甚至超过500μm。
在管道弯头、锈蚀严重、法兰连接、设备焊缝等部位都有大量粉料粘连结块,甚至有塑化情形。
粗糙的管壁、大角度弯头、法兰连接处的缝隙和焊缝处的焊瘤会阻碍粉料流动,造成粉料积存,而粉料中的催化剂尚未失活,会继续发生聚合反应,造成局部过热,粉料熔融塑化后粘连结块,更加难以流动,并且会粘结更多粉料,情况急剧恶化,最终完全堵死。
2.2 过滤器滤袋被打落或高温融化采样闪蒸器F-4003的内置过滤器原始设计为铝焊龙骨加PP针刺滤袋式,由于采样阀XV-40060前后压差高达5.0MpaG,阀门开启瞬间巨大的冲击力足以打落滤袋和龙骨,滤袋和龙骨落在采样闪蒸器锥体部分,造成采样闪蒸器底部堵塞,而气相会夹带粉料从顶部进入保护过滤器F-4004,造成顶部堵塞。
聚丙烯装置闪蒸罐出料阀堵塞的原因分析0

了处 理 的方 法 。
活性最高可达 8 / 。在实 际生产中 , 化剂在 0 g 催
反 应 器 内 的停 留时 间约 为 15h . 。据 资 料 报道 , I5h只能使 N型催化 剂释放 约 13的活性 。 . / 同时 根 据工 艺 要求 ,浆 料从 反应 器 的 出料 阀到离 开
聚效果不好 , 反应不均匀 。() 聚合 2环管 反应器 的
温度 、 压力有波 动。( ) 浓度的变化 。 3
23 闪蒸管线 内壁不光滑 . 从反应器 出来 的聚丙烯浆料在 闪蒸管线 内壁 的一些毛刺 、凹槽处 停留 、堆积 ,逐渐 形成塑化 块 。当塑化块 变大 , 被浆料带人 闪蒸罐 后 , 最终堵
2 V 0 堵塞 的原 因 L 3 1 2 1 聚丙烯浆料在 闪蒸罐 内停 留时 间过长 .
原 因主要有 :1催化剂混合罐 的温度波动较 大。 () 催化剂混合罐 温度主要通过其 夹套冷冻水量来 控 制 ,而冷冻水是 由装 置内 的冰机 提供 的 当装 置
收 稿 E期 : 2o —0 —2 t o0 2 7
在 闪蒸罐底 部堆积 , 最终形成较 大 的块料 , 而堵 从 塞 L 31 V0。 进一步 分析可知 ,造成反应 器 内反应 波动的
由此 可见 ,L 3 1 V 0 在整个工 艺流程 中的作用
极 其重要 ,其 能否正常工作直接决 定了生产 的连 续性 、 后续工 段操作 的稳定性 和产 品的质量 。
※新书 介绍 ※
《 英华塑料技 术词 汇》 出版发行
为适应塑料 工业的飞速发展 ,吸 收 国外先进
本词汇 由钱 德基等编著 , 中国石化 出版社 出
酸站闪蒸系统常见故障探讨

酸站闪蒸系统常见故障探讨酸站闪蒸系统是炼化厂中常用的一种处理酸性废水的技术,其基本原理是利用高温和高压的条件将废水中的酸性物质蒸发出来,以达到回收酸性物质和净化废水的目的。
然而,酸站闪蒸系统也存在一些常见的故障问题,下面就对其进行讨论。
一、设备堵塞设备堵塞是酸站闪蒸系统中的一种常见故障。
由于废水中含有一定的杂质和颗粒物,这些杂质和颗粒物会在闪蒸系统的管道、阀门、泵等部件上积累,形成阻塞,导致设备运行不畅或停止运行。
解决方法:1.定期清洗设备,除去管道内的积垢和颗粒物。
2.增加过滤设备,限制进入酸站闪蒸系统的杂质和颗粒物。
二、泄漏泄漏是酸站闪蒸系统中的另一种常见故障。
泄漏可能会发生在管道、阀门、泵、安全阀等设备上。
如果泄漏严重,可能导致系统的停机和故障。
1.定期检查设备,发现泄漏立即修复。
2.增加安全阀等安全设备,并确保其正常运行。
三、沉淀酸站闪蒸系统中的沉淀问题主要由于废水中含有大量金属、硫化物等杂质,这些杂质在高温高压下易于沉淀下来,附着于设备内部,导致设备的运行不畅或停机。
1.增加设备的清洗频率,定期清理设备内的沉淀物。
2.控制进入闪蒸系统的废水中金属、硫化物等杂质的含量。
四、设备损坏酸站闪蒸系统中的设备损坏是一种比较严重的故障问题,可能会导致设备的停机和维修。
设备损坏可能是由于设计不合理、制造质量不佳或者使用不当等原因引起的。
1.加强对设备的设计和制造质量的把控。
2.加强对设备的使用和维护管理,定期进行维修和保养。
综上所述,酸站闪蒸系统虽然在炼化厂中具有重要的作用,但是其常见故障问题也应引起我们的重视,正确处理故障,保证设备的正常运行,提高生产效率和净化效果。
PP装置闪蒸罐下料阀出料不畅的解决和预防

PP装置闪蒸罐下料阀出料不畅的解决和预防
陈颖;刘军勇
【期刊名称】《现代塑料加工应用》
【年(卷),期】2007(19)6
【摘要】N型催化剂的后活性强,工艺条件不恰当和操作经验不足是闪蒸罐下料阀LV301易堵的主要原因,通过选用恰当工艺条件和改善操作来解决此问题.
【总页数】4页(P52-55)
【作者】陈颖;刘军勇
【作者单位】荆门职业技术学院,湖北,荆门,448002;中石化荆门分公司,湖北,荆门,448002
【正文语种】中文
【中图分类】TQ32
【相关文献】
1.PP装置闪蒸罐出料阀堵塞紧急预案的优化 [J], 苏俊
2.聚丙烯装置闪蒸罐出料阀堵塞的原因分析 [J], 杨爱新
3.蒸汽凝液闪蒸罐安全阀管道设计要点分析 [J], 孙羽佳;
4.溶出闪蒸器内部出料管磨穿分析及处理 [J], 陆善友
5.江阴工业区中景石化一期PP装置正式出料 [J],
因版权原因,仅展示原文概要,查看原文内容请购买。
酸站闪蒸系统常见故障探讨

酸站闪蒸系统常见故障探讨1. 引言1.1 背景介绍酸站闪蒸系统是化工装置中常见的一种设备,用于对液态混合物进行蒸馏分离。
由于其操作复杂性和工作环境的特殊性,系统常常出现各种故障问题。
为了提高系统的稳定性和效率,对闪蒸系统的故障进行深入分析是非常必要的。
本文将对酸站闪蒸系统的常见故障进行探讨,包括可能导致故障的原因、故障排除的方法以及系统优化的建议。
通过对实际案例的分析,我们将总结反思系统运行中存在的问题,并展望未来对系统性能的提升。
背景介绍的目的在于引入读者对酸站闪蒸系统的基本概念,并明确本文的研究范围和目的。
通过本文的研究,我们希望能够帮助工程师和操作人员更好地理解闪蒸系统的运行机理,提高系统的稳定性和效率,从而实现生产的安全和高效运行。
1.2 研究目的本文旨在探讨酸站闪蒸系统常见故障及解决方法,旨在帮助读者更好地理解和应对酸站闪蒸系统在运行中可能遇到的问题。
通过系统的概述、故障原因分析、故障排除方法、系统优化建议和案例分析,本文旨在为工程师和相关人员提供清晰的解决方案,以确保酸站闪蒸系统的稳定、高效运行。
通过总结反思和未来展望,我们希望可以为行业发展提供借鉴和参考,提高酸站闪蒸系统的运行效率和可靠性,推动行业向更加绿色、环保方向发展。
2. 正文2.1 酸站闪蒸系统概述酸站闪蒸系统是一种用于减少酸废气排放的环保设备,主要用于处理含有酸性气体的工业废气。
该系统通过将废气冷却至露点以下并与水接触,使酸性气体在水中溶解或转化为液态酸,从而实现酸废气的治理和处理。
酸站闪蒸系统通常由冷却器、吸收塔、冷却水循环系统、泵等组成。
废气进入吸收塔后,通过喷淋装置与冷却水接触,使酸性气体被吸收和溶解。
随后,吸收塔中的酸性水会通过闪蒸器升温并释放出酸性气体,从而实现气液分离和酸性气体的收集和处理。
酸站闪蒸系统具有结构简单、操作方便、处理效率高等优点,广泛应用于化工、冶金、电力等行业。
在实际运行中,由于设备老化、操作不当、设备设计不合理等原因,常常容易出现故障,影响系统的正常运行。
酸站闪蒸系统常见故障探讨

酸站闪蒸系统常见故障探讨
酸站闪蒸系统是一种常见的工业设备,主要用于酸性物质的蒸发和回收。
在长时间的
使用中,酸站闪蒸系统可能会出现一些常见的故障,下面将对这些故障进行探讨。
常见的故障之一是闪蒸罐压力异常。
闪蒸罐是酸站闪蒸系统中的一个关键组成部分,
用于蒸发酸性液体并将酸气冷却回收。
如果闪蒸罐的压力异常,可能是由于操作不当、阀
门堵塞或供热系统故障等原因造成的。
解决这个问题的方法可以是检查和清理阀门,修复
或更换不良的传感器,并进行供热系统的维护和保养。
酸站闪蒸系统中还存在着泄漏问题。
泄漏可能发生在管道连接处、阀门密封不良或系
统内部漏气等位置。
这样会导致系统不能正常工作以及安全隐患。
解决这个问题的方法可
以是检查管道连接处的紧固情况,检查和更换不良的密封件,并进行系统漏气排查和修
复。
酸站闪蒸系统常见的故障包括闪蒸罐压力异常、冷却系统失效、泄漏问题、温度异常、流量异常和浓度异常等。
针对这些故障,需要进行全面的检查和维护,及时修复和更换不
良的零部件,以确保酸站闪蒸系统的正常运行和安全使用。
- 1、下载文档前请自行甄别文档内容的完整性,平台不提供额外的编辑、内容补充、找答案等附加服务。
- 2、"仅部分预览"的文档,不可在线预览部分如存在完整性等问题,可反馈申请退款(可完整预览的文档不适用该条件!)。
- 3、如文档侵犯您的权益,请联系客服反馈,我们会尽快为您处理(人工客服工作时间:9:00-18:30)。
闪蒸釜输料堵塞的原因分析及预防措施许雄杰宗林曹雄聚丙烯车间炼化总厂聚丙烯装置1990年破土动工,1992年建成投产,采用间歇式液相本体法生产工艺,经过多次技术改造和科技投入,特别是在2005年装置扩容改造后,现有8台聚合釜,7台闪蒸釜,生产能力为4万吨/年。
闪蒸釜是聚丙烯生产的主要设备,在整个工艺流程中的作用极其重要,其能否正常运作直接决定了生产的持续性和后续系统操作的稳定性。
因此,保证闪蒸釜输料通畅,才能避免聚合釜中丙烯的回收处理,保障聚合持续进行,减少丙烯损耗。
1 闪蒸釜输料现状分析间歇式聚丙烯生产,车间选用12m3聚合釜,10m3闪蒸釜配套操作(F311除外)。
闪蒸釜下部为倒锥形,可加快粉料出料速度,预防釜内粉料大量残留,通过卸料阀接连φ100mm 输料管道至储料仓。
输料期间,循环氮气通过气动角阀往输料管道内通入压缩氮气,将粉料切割成拴状(即一段粉料柱,一段气柱)。
多年的生产实践发现,聚丙烯粉料夹带块料是输料堵塞的主要原因。
正常平稳操作,一般不会发生闪蒸釜输料堵塞现象,然而随着DJD-Z等高效催化剂的相继投用,装置多次扩容改建,以及聚合釜传热能力弱化,聚丙烯粉料时有块料产生,给日常生产运行增添不少操作难题。
聚丙烯粉料夹带块料,可使闪蒸釜输料不畅,甚至管道堵塞,若未及时妥当处理,容易阻滞聚合投料持续进行,造成丙烯大量回收,不利于丙烯单耗的降低。
2块料产生原因分析聚丙烯粉料夹带块料,影响了装置的安、稳、长、满、优运行,事实上,国内外同类装置也经常遇上同样的难题,现在从工艺选择、设备状况及生产操作等方面探讨分析块料产生的原因。
2.1 催化剂和活化剂过量,聚合反应剧烈实践表明,原料丙烯中的杂质含量偏高,可使高效催化剂的活性受到抑制,尤其是水等有害杂质。
聚合反应中,活化剂的作用,一是与催化剂配位形成活性中心,二是消除原料丙烯的少量杂质。
因此,活化剂加入量除了与催化剂量有关,还与原料丙烯质量有很大关系。
聚丙烯装置在精制系统装有水含量在线分析仪,要求精制后的原料丙烯水含量低于10μg/g,确定单釜催化剂60~75g,活化剂300~550ml。
但精制系统进料量偏高时,粗丙烯杂质脱除不彻底,精制后的原料丙烯水含量高于10μg/g。
为了消除杂质影响,激活聚合反应,通常多加催化剂和活化剂,以致反应后期压力和温度难以控制,聚合釜温度、压力过高,引起聚丙烯粉料局部塑化结块。
2.2 控制不佳,产生过度干锅正常情况下,反应结束时聚合釜内有一定量的液态丙烯,回收时丙烯相变化吸收部分热量,使聚合釜温度降到55 ℃以下,聚丙烯粉料一般不会塑化结块。
然而装置的长周期运转,以致设备老化,聚合釜夹套结垢,聚合釜换热能力逐步减弱;再者装置DCS系统仍以传统的单回路控制为主,现场动态生产信息反馈滞后,导致聚合反应在过度、恒压阶段自控困难,改变循环水量撤热不及时,前期控制不住而回收部分丙烯,造成反应结束回收时,基本无液相丙烯可蒸发。
而此时聚合釜内大量的聚丙烯因传热效果差,热量很难散发,在反应热和搅拌热的作用下,聚合釜温度逐渐升高,导致回收后聚合釜温度往往超过60 ℃甚至70 ℃,发生过度干锅,引起聚丙烯粉料局部塑化结块。
2.3 尾气回收系统负荷大,聚丙烯粉料在聚合釜停留时间过长实验表明,DJD-Z型催化剂的活性寿命超过6h,而实际生产中,聚合单釜操作时间3.5~6.0h,催化剂活性仍未释放完全。
2005年装置扩容改造为4万吨/年,并引进膜分离工艺,而气柜犹未扩容优化,与装置产能组合不配套。
由于产量上升,在生产高峰期,尾气处理量加大,而膜分离处理量有限,导致压缩机循环量不断加大,气柜中的气相丙烯未能及时压缩,气柜居高不下,从而阻滞喷料的正常进行,延长聚丙烯粉料在聚合釜停留时间,催化剂的后活性很容易在此继续发挥作用,残余丙烯继续发生聚合反应,并放出大量的热,使聚合釜中聚丙烯粉料局部塑化结块。
3 闪蒸釜输料堵塞判断及处置措施生产操作中,可借助DCS的闪蒸釜输料釜压趋势变化及储料仓载荷判断堵塞状况,提供处置依据。
(1)釜压长时间无变化,储料仓未满却无输料动静,则堵塞一般发生在输料管道或储料仓进料阀阀芯中。
此时先减缓对应聚合釜反应程度或暂缓投料,再停止输料,利用其他闪蒸空釜充压冲击输料管线,将块料推进储料仓;若无效,通知闪蒸外巡至储料仓顶部察看,如果进料阀被块料卡住则活动进料阀辗碎块料,再用空釜充压扫净碎块;若进料阀难关动,则进料阀阀芯卡死,需停止输料排净输料系统压力,最后拆开进料阀疏通阀芯。
(2)釜压下降快,输料管道内只有气流声,则堵塞一般发生在闪蒸釜出口或卸料阀阀芯中。
此时先减缓对应聚合釜反应程度或暂缓投料,再停止输料,放净釜压,通知闪蒸外巡至储料仓顶部关进料阀,再用其他闪蒸空釜充压反吹,块料摩擦碰撞变小,使输料通畅;若无效,则卸料阀阀芯卡死,需停止输料排净输料系统压力,最后拆开卸料阀疏通阀芯。
(3)上述情况若判断正确处理及时,输料恢复在1h以内,一般不影响聚合持续生产,若情况严重,块料较大较多,完全卡死在闪蒸釜出口或输料管道内,此时充压吹扫无效,且处理过程复杂,且时间长,必须立即中止相应聚合釜持续生产,开人孔清釜或疏通更换相应管道。
4输料堵塞预防措施4.1 优化精制系统,严格控制杂质含量2012年以前,闪蒸置换后的尾气经压缩冷凝,最后回收的液态丙烯与上游粗丙烯混合,进入丙烯精制系统,精制后的丙烯也仅有直接进入精丙烯罐的流程。
从分析可知,确保丙烯质量,不合格的丙烯不投料,是预防块料产生的有效措施,因此有必要对精制系统进行优化改造,进一步提高精制后的丙烯纯度。
自炼厂的“两降一提”技术攻关开展后,车间针对精制系统先后进行两次技术改造和科技投入:(1)实施回收丙烯直输气分装置精馏回炼工艺,尾气回收的丙烯返回气分装置精馏回炼回炼。
车间采用的是湿式尾气回收工艺,回收后的丙烯中水含量较高,不能直接用于聚合投料生产,只有通过精制系统清除杂质后才能达到生产要求,对精制系统操作的稳定性影响大。
而将尾气回收的丙烯回炼,使得进入精制系统的粗丙烯杂质更少,精制系统负荷降低,进而提高精制后的丙烯纯度。
(2)实施丙烯精制大循环工艺,针对开停厂期间,精制丙烯水含量高于10μg/g,将不合格丙烯在精制系统内循环精制,直至达到聚合投料要求。
上述精制系统技造项目投入低,见效快,相继投产后,经标定观察,精制系统杂质祛除更彻底,精制后丙烯纯度更高,催化剂、活化剂用量更稳定,产品质量更优良,进一步降低了闪蒸釜输料堵塞的次数。
4.2开展技术攻关,精确控制两剂加料量由于间歇式聚丙烯生产工艺的特殊性,DCS控制程序比较复杂,催化剂、活化剂加料量精确控制比较困难,为此,车间专门组织开展相关技术攻关工作。
(1)加强精细化管理,完善分装考核制度,提高分装精度,防止催化剂在分装过程中与空气长时间接触,保证催化剂活性,进一步稳定单釜催化剂加料量。
(2)通过标定计算,发现活化剂单釜实际加料量明显低于DCS显示的物料值;排查DCS控制源程序也发现,活化剂计量式未考虑计量罐变径对计量的影响,存在较大偏差,导致活化剂多次超量,引起聚合异常出现块料。
针对活化剂计量系统中存在的问题,车间进行了一系列工作:a测量活化剂计量罐尺寸,计算各部位体积;b解读DCS控制源程序,协同仪表车间修改活化剂计量算法,并对其它对应的数据进行调整;c更换故障阀门,调节闸阀开度,延长计量罐的补料时间,提升精确控制质量。
(3)组织人员采集单釜催化剂、活化剂消耗数据,并建立数学模型,绘制铝钛比趋势图,探讨铝钛比的最优值,重新确定单釜两剂加料量。
技术攻关完成后,催化剂、活化剂单釜加料量明显降低,且更加稳定。
4.3定期化学清洗,改善聚合釜传热能力循环水在聚合釜夹套和U型管中长期流动,容易形成一层水垢,使聚合釜总传热系数降低。
针对聚合釜传热能力偏弱的问题,可对聚合釜定期进行化学清洗。
依据理论公式K =1/(1/α0+1/αi+δ/λ+Re0+ Re i),对化学清洗后的聚合釜进行传热核算,式中:δ—聚合釜壁厚,30mmαi—聚合釜内壁对流传热系数,有机物取500 W/(cm2•℃)α0—聚合釜外壁对流传热系数,循环冷水取1500 W/(cm2•℃)λ—聚合釜釜壁材料的导热系数,16MnR取45 W/(cm2•℃)Re i—聚合釜内壁聚丙烯薄层热阻,取2.0×10-3 m2•℃/WRe0—聚合釜外壁污垢热阻,经验值取3.4394×10-4 m2•℃/W根据多年的生产实践经验,化学清洗可以清除釜外壁80%的垢层,釜内壁100%的垢层,在计算总传热系数过程中采用部分理想化状态,则:清洗前K =1/(1/1500+1/500+0.03/45+3.4394×10-4+ 2.0×10-3)=176.1 4w/(cm2•℃)清洗后K’=1/(1/1500+1/500+0.03/45+3.4394×10-4×0.2)=293.93 W/(cm2•℃)因此K’/K=293.93/176.14=1.67,即传热系数增大了67%。
根据上述核算,经化学清洗后,聚合釜传热能力可提高67%,基本能解决撤热困难的问题。
4.4优化联锁控制PID,提升控制质量装置自动控制采用浙江中控的JX-300X系统,在控制方案上以传统的单回路控制为主,但由于生产经验丰富的技术人员缺乏自动控制方面的知识,而开发、优化控制程序的人员又缺乏生产经验,以致循环水量与聚合釜温度的联锁控制PID数值设置不合理,造成聚合反应在过渡和恒压阶段平稳控制困难,自动化程度偏低,改变循环水量撤热不及时,引起聚丙烯粉料局部塑化结块。
显然,优化联锁控制PID,提升控制质量势在必行。
(1)组织生产技术与自控技术人员,采集运行数据,排查DCS控制源程序,调整PID 参数,切实让DCS自控系统服务于生产。
(2)组织现场操作人员,联合仪表车间,排查循环水系统各阀运作状况,更换故障阀门,努力实现信息反馈迅速,DCS控制撤热及时,确保过程在“自动”模式下平稳运作,提升过度、恒压阶段控制质量。
4.5减轻尾气回收系统负荷,确保聚合釜喷料及时聚合反应完成后,先高压回收至1.3MPa,然后喷料,喷料过程的气相丙烯全部进入尾气回收系统,尾气回收系统的处理量完全由首次喷料时聚合釜内存在的气相丙烯量决定。
为确保聚合釜喷料及时,降低聚丙烯粉料局部塑化结块风险,减轻尾气回收系统负荷是关键。
2013年检修期间,车间利用旧有的设备、管线,新增中压回收工艺(见图1)。
聚合釜高压回收完成后,由精氮罐继续回收,聚合釜压力可降至0.8MPa,减轻了尾气回收系统负荷,达到避免高负荷生产时不能及时喷料而造成聚丙烯粉料局部塑化结块的目的,而且将进一步减少丙烯浪费。