铣床培训教材.
数控铣培训教材

任务二认识刀具、对刀、手动铣平面(牛刀小试)一、任务目标1、工件装夹(平口钳及装夹图片)(1课时)2、认识铣刀刀柄、键槽铣刀和立铣刀,学习如何装刀卸刀(1课时)3、讲试切法对刀及练习(寻边器介绍)(2课时)4、手动铣平面操作练习(3课时)二、相关知识(知识要点)1、工件的装夹平口钳安装于铣床工作台上,用百分表校正(钳口与X轴方向平行)。
将坯料装入平口钳中,下用垫铁,工件露出约钳口,放平且夹紧。
如图2-1所示图2—1 平口钳校正(a)工件装夹(b)2、数控立铣刀的种类和用途种类:1)两刃立铣刀2)三刃立铣刀3)多刃立铣刀用途:1)两刃立铣刀粗铣轮廓、凹槽等表面,可沿铣刀轴线方向进给加工(垂直下刀);2)三刃和多刃立铣刀精铣轮廓、凹槽等表面,一般不能沿铣刀轴线方向进给加工。
键槽铣刀、立铣刀按结构不同有整体式和可转位式。
图2—2整体式立铣刀图2—3可转位式立铣刀3、数控铣刀刀柄数控铣床使用的刀具是通过刀柄与主轴相连的,刀柄与主轴的配合锥面一般采用7:24的锥度。
目前国际和国家标准规定的BT-40和BT-50系列为常用的刀柄和拉钉,以下是几种常用的刀柄。
图2—4 弹簧夹头刀柄、卡簧及拉钉1)弹簧夹头刀柄、卡簧及拉钉如图2-4所示,用于装夹各种直柄立铣刀、键槽铣刀、直柄麻花钻等。
卡簧装入数控刀柄前端夹持数控铣刀;拉钉拧紧在数控刀柄尾部的螺纹孔中,用于拉紧主轴上。
2)莫氏锥度刀柄如图2-5所示。
莫氏锥度刀柄有莫氏2号、3号、4号等,可装夹相应的莫氏钻夹头、铣刀、攻螺纹夹头等。
图2-5 莫氏锥度刀柄4、卸刀座卸刀座是用于铣刀从铣刀柄上装卸的位置,如图2-6。
1、平口钳平口钳用于装夹工件,并用螺钉固定在工作台上,如图2-7。
图2—6卸刀座图2—7 平口钳2、“试切法”对刀及检验方法1). 刀具装夹把Ф10mm键槽铣(立铣刀)、8~10mm卡簧,装入铣刀刀柄,再把铣刀刀柄连同铣刀装入铣床主轴。
2).对刀操作一般来讲,在机床加工过程中,通常使用的有两个坐标系:一个是机床坐标系;另外一个是工件坐标系。
数控铣床加工中心操作培训教材1教程

子菜单
主菜单软体键连续按 2次,进入该项的子菜单, 用最左端的软体键进行切换。 位置——相对、绝对、总和; 程序 ——MDI/模、程序、现 / 模、现 / 次、目录; 偏置——偏置、宏变量、宏变量; 参数——参数、螺补X、螺补Y、螺补Z、求助; 诊断——MT←→PC、PC←→NC、PC、状态、 求助
(1)机能软体键
软体键用于选择各种显示画面的菜单 键,每一主菜单下又细分为一些子菜单, 软体键对应要显示的内容显示在CRT的 最下端。最左端的软体键为从子菜单返 回主菜单的初始状态,最右端的软体键 为选择同级菜单的其它菜单内容。
主菜单
第一页 —— 位置、程序、偏置、参数、 诊断; 第二页 —— 报警、图形、设置、机床、 索引。 共二页,由最右边的软体键进行切换,有5 个菜单可选择。
程序的删除
(1)选择EDIT方式; (2)按程序软体键,显示程序; (3)按地址“O”; (4)用键输入程序号; (5)按“DELET”键,则对应键入程序 号的存储器中程序被删除;
字的检索
字的检索 ①按“ CURSOR↓” 键,光标一个字一个字顺 方向移动,在被选择字的地址下面显示光标; ②按“ CURSOR↑” 键,光标一个字一个字反 方向移动,在被选择字的地址下面显示光标; ③按“PAGE↓”键,画面翻页,光标移至下页 开头的字; ④按“PAGE↑”键,画面翻到前一页,光标移 至开头的字
子菜单
报警——报警、外部; 图形——参数、图形、起动、停止、清除; 设置——设置1、设置2、设置3; 机床——第一页:方式-、方式+、单程段、回 零、空运行; 第二页:倍率-、倍率+、轴-动、轴+ 动、起/停; 第三页:主轴正、主轴反、主轴停、 主轴点、冷起停; 索引——操作表、报警表、G码表、参/诊、宏 指令
车工铣床操作培训课件

铣床和龙门数控铣床 。
•
经济
•2024/1/26
全功能
高速铣床
龙门铣床
•车工(铣床)操作培训
3• .2.2 数控铣床的结构和调整
1. 数控铣床的组成
数控铣床一般由机床本体、数控系统、进给伺 服系统、冷却润滑系统等几大部分组成。
机床本体是数控机床的主体,包括:床身、立 柱等支承部件;主轴等运动部件;工作台、刀架以 及进给运动执行部件、传动部件;此外还有冷却、 润滑、转位和夹紧等辅助装置。与传统机床相比, 数控铣床的外部造型、整体布局、传动系统与刀具 系统的部件结构以及操作机构等都发生了很大的变 化,这种变化的目的是为了满足数控技术的要求和 充分发挥数控机床的特点。
•车工(铣床)操作培训
地址 G43/ G44 G49 G50 G51 G52 G53 G54~G59 G60
• G61
G64
• G65
G68
G69
•2024/1/26
含义 刀具长度补偿—正/负 刀具长度补偿注销 缩放关 缩放开 局部坐标系设定 直接机床坐标系编程 工件坐标系选择 单方向定位 精确停止校验方式 连续方式 子程序调用
• 建立工件坐标系。工件坐标
• 系一旦建立,绝对值编程时
• 的指令值就是在此坐标系中
• 的坐标值。如右图所示。 • 程序示例:G92 X40 Y30 Z25
•2024/1/26
•车工(铣床)操作培训
坐标值X40 Y30 Z25为刀位点在工件坐标系中的
初始位置,执行G92指令时,机床不动作,即X、Y、
•2024/1/26
•车工(铣床)操作培训
(4)快速点定位指令(G00) G00指令是指刀具以点定位控制方式,从刀具 所在点以最快的速度,移动到目标点。G00指令中的 快移速度由机床参数“快移进给速度”对各轴分别设 定,不能用进给速度F规定。一般用于加工前快速定 位或加工后快速退刀。G00为模态功能可由G01、 G02、G03或G33功能注销。 注意:在执行G00指令时,由于各轴以各自速 度移动,不能保证各轴同时到达终点,因而联动直线
铣床培训教材

下压,下几个毫米,用PIN来检查是否正确,如果正确,继续铰下去
• 孔前先要调整机床的主轴垂直度,方法如下:
•
1.用一块比较长,又比较宽的顶块夹在平口钳上
•
2.用表把顶块 X ,Y方向打平
•
3.主轴在空挡,使表转动180°看两端是否在同一高度
•
4.若有高低,松动螺丝,调整主轴方向
第三周
• 第四天:机铰时应注意以下几点:
第二周
• 第五天:1. 倒角的加工方法
•
① 对于C2以下的,可以直接用倒角刀做,碰到尖点后
,多大就进多少
•
②对于C2以上的,可用45°角度块或“V”形块来垫上
,用铣刀来做(下的度深为:倒角的大小xCOS45°+双边余量之和
xCOS45°)
•
③倒角可以做大一点,但不能小
•
2.斜度的加工过程
•
①看清所加工的角度为多大,选择合适的角度块(尽量
•
先找准位置后,用Φ8.0的铣刀下4.10MM左右(外形余量
0.5MM),然后再拿把Φ8.0的刀放在平口钳上夹住磨平,经过刃磨后,
装到夹头上,把工件打平,然后用磨好的平底刀下到深度(4.0+0.25)
MM,最后用深度计来检验是否正确
•
• 第三周:应达到的要求:
•
能够做一些比较难Hale Waihona Puke 工件,对做简单的工件要达到一定的速度
• 第五天:控制尺寸的加工
•
1.深度控制
•
先去余量 ------修磨平底刀-----打平工件------做到尺寸
•
例如:加工一孔Φ8.0x4.000+0.03 +0.01 DP
•
数控铣床基础知识培训教材(DOC 77页)

2我的页脚
如有你有帮助,请购买下载,谢谢!
件在其上面能顺利装夹;选择合适的进给坐标行程保证工件的 加工尺寸在各坐标有效行程内。
CNC 铣床或加工中心的工作台面尺寸和三个直线坐标行程 都有一定比例关系,如机床的工作台为 500mm×500mm,其 X 轴行程一般为 700~800mm,Y 轴为 550~700mm,Z 轴为 500~ 600mm,因此工作台的大小基本确定了加工空间的大小。
对数控铣床和加工中心的类型进行选择 机床规格的选择 机床精度的选择
对数控铣床和加工中心的类型进行选择/机床规格的选择 /机床精度的选择
无
课外作业
教材章节后的相应习题
教学后记
课堂中讨论内容的安排,活跃了教学气氛,激发学生学 习兴趣,增强了学生的思维分析能力。学生掌握程度良好,然 须在后续教学中进一步加强巩固。
课堂教学安排
教学过程
主要教学内容及步骤
1我的页脚
如有你有帮助,请购买下载,谢谢!
引入: 数控铣床的基本特点。
新课内容:
一、适合数控铣削零件
1、空间曲面类零件: 1、复 习 及 提
问
2、平面曲线轮廓类零件
提问上一讲学 3、其它适合数控铣削加工的零件
习的主要内
容。
二、数控铣床或加工中心的选择
2、引入: 3、新课内容:
1、如何对数控铣床和加工中心的类型进行选择
2、适合数控铣削零件?
3、如何对机床精度的选择?
项目二 认识数控铣削刀具及铣削加工特点
课时 授课时数
第 2 课时 1
授课班级 授课形式
02 级数控班 讲练
授课章节 名称 使用教具 教学目的
教学重点
教学难点 补充内容 课外作业
铣床培训课
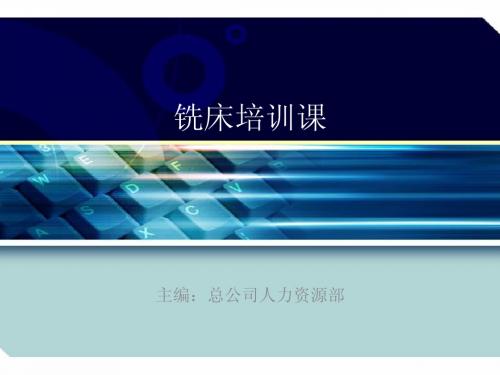
课外拓展
(2)立式铣床
课外拓展
铣刀: 圆柱铣刀、三面刃铣刀、锯片铣刀、角 度铣刀、成形铣刀、立铣刀、端铣刀、键 槽铣刀
课外拓展
铣 刀:
课外拓展
铣 刀:
课外拓展
主要附件: 平口钳 回转工作台 万能铣头 万能分度头
课外拓展
平口钳: 适合夹小型零件,如装夹轴类零件铣键槽
课外拓展
回转工作台: 可带动工件缓慢的圆周进给。一般用于 较大零件的分度工作和非整圆周的铣削工 作。
影响薄型工件加工精度的因素
• 由于薄型工件的特殊性,加之材料切削加 工性能的因素,刀具几何角度和切削用量 的选择会响应有所改变,就使得加工时的 选择和确定比较困难。若选用不当,常会 引起加工精度误差,甚至造成刀具损坏、 工件变形,甚至报废。
薄型工件装夹时应注意以下几点
• 按定位的原理,应尽量在加工部位附近设 置定位和辅助定位,并在定位元件上预留 出铣刀让刀位置。 • 在选择夹紧力的作用点位置和作用方式时, 须考虑材料的力学性能,采用较大的面积 传递夹紧力,以避免夹紧力集中在某一点 上,使工件产生变形。
• 开车前,检查机床手柄位置及刀具装夹是否牢 固可靠,刀具运动方向与工作台进给方向是否 正确。
铣工安全技术操作规程
• 将各注油孔注油,空转试车(冬季必须先开 慢车)2分钟以上,查看油窗等各部位,并听 声音是否正常。 • 清扫铁削时应用专门工具,不准用手。 • 所使用的扳手及工具,应符合规定,不准 把管子套在扳手上使用。 • 卡活件时应根据卡具情况,适当力量卡紧。 • 在工作中,不准将手锤、扳手和毛坯直接 放到机床导轨面的工作台面上。
复杂直角沟槽工件的铣削工艺特点
• 由于工件的加工精度比较高,因此所选用 的刀具、量具、辅具及夹具的精度要求都 比较高,通常在使用前,需要进行精度预 检,以保证加工过程中的使用精度。
铣床培训教材

铣床培训教材1铣床的基本知识1.1 铣床的类型:升降台式铣床(卧式铣床、立式铣床)、万能铣床、龙门铣床、特种铣床、数控铣床等。
1.2 铣床的结构部件:底座床身、主轴、主轴变速机构、纵向工作台、横向工作台、升降台等。
1.3 铣削的概念:铣削就是在铣床上以铣刀旋转作主运动,工件或铣刀作进给运动的切削加工方法。
1.4 铣削加工的特点:铣削是用多刀刃的铣刀来进行切削加工的,故生产效率较高。
1.5 铣削的加工精度:铣削加工的经济加工精度一般为IT9~IT8,表面粗糙度Ra值可达到12.5~1.60um;必要时加工精度可高达IT5,表面粗糙度Ra值可达0.20um。
1.6 铣床的加工范围:铣平面、铣直槽、铣燕尾槽、铣T型槽、铣成形面等各种形状复杂的零件。
2铣刀的基本知识2.1 铣刀的种类(按铣刀切削部分的材料分):高速钢铣刀、硬质合金铣刀2.2 铣刀切削部分材料的基本要求:2.2.1 高硬度和高耐磨性:在常温下,切削部分材料必须具备足够的硬度才能切入工件;具有高的耐磨性,刀具才不易磨损,延长使用时间。
2.2.2 好的耐热性:刀具在切削过程中会产生大量的热量,尤其在切削速度较高时,温度会很高。
因此,刀具材料应具备好的耐热性,即在高温下仍能保持较高的硬度,具有能继续进行切削的性能。
这种具有高温硬度的性质,又称热硬性或红硬性。
2.2.3 高的强度和好的韧性:在切削过程中,刀具要承受很大的冲击力,所以刀具材料要具有较高的强度,否则易断和损坏。
由于铣刀会受到冲击和振动,因此,铣刀材料还应具备好的韧性,才不易崩刃、碎裂。
2.2.4 工艺性好:这样有利于制造出各种形状和尺寸的刀具。
3基准的种类及选择原则3.1 基准的种类:3.1.1 设计基准:零件在设计图样上,用来确定其它的点、线、面位置的基准称为设计基准。
设计基准一般是零件图样上标注尺寸的起点或对称点,如齿轮的轴线或孔的中心线等。
矩形零件和箱体零件,则多数以底面为设计基准。
数控铣床基础知识培训教材

模块一数控铣床基础知识项目一认识数控铣削机床及选用课堂教学安排二、数控铣床或加工中心的选择1.数控铣床或加工中心的类型选择不同类型的数控铣床或加工中心,项目二认识数控铣削刀具及铣削加工特点课堂教学安排模块二数控铣床的差不多操作训练项目一数控铣床差不多操作课堂教学安排项目二认识数控铣床的对刀及刀具补偿课堂教学安排6.作业及辅导:布置下次提问的考虑题,及课后练习题。
对考虑题、习题难点、要求进行辅导。
(3) G40、G41、G42指令格式三、讨论:X、Y向对刀的实质?总结:1、CNC铣床坐标系与工件坐标系的差不;作业及辅导:1、CNC铣床坐标系的规定?图2-1刀具左半径补偿指令G41,右半径补偿指令G42项目二认识数控铣床的对刀及刀具补偿教学后记课堂中讨论内容的安排,活跃了教学气氛,激发学生学习兴趣,增强了学生的思维分析能力。
学生掌握程度良好,然须在后续教学中进一步加强巩固。
课堂教学安排教学过程要紧教学内容及步骤1.复习及提问提问上一讲学习的要紧内容。
2.引入:3.新课内容:逐步完成本次教学内容的讲授。
引入:数控车床对刀及补偿设置。
新课内容:(3) G40、G41、G42指令格式刀具半径补偿指令的格式如下:G00/G01 G41/G42 X~Y~D~;G00/G01 G40 X~Y~;其中:G41为左偏置刀具半径补偿指令,G42为右偏置刀具半径补偿指令。
G40 取消刀具半径补偿。
如图2-1所示,当沿着刀具前进方向看,刀具中心在零件轮廓左边时为左偏置,刀具中心在零件轮廓右边时为右偏置。
(4)半径补偿的建立、执行和撤销在轮廓加工过程中,刀具半径补偿的执行过程一般分为刀具半径补偿的建立、刀具半径补偿的执行和刀具补偿撤销三步。
如图2-2,用半径补偿功能编写轮廓加工程序。
设φ24立图2-1刀具左半径补偿指令G41,右半径补偿指令G42a、G41 建立半径补偿b、G40取消半径补偿2-2半径补偿建立和取消。
OK铣床培训教材PPT课件

(1).铣床的加工原理及如何安全操作机台;(F1部) (2).如何备料,飞六面体;(F2部) (3).如何装夹工件及工件的定位与基准;(F3部) (4).简单工件的国加工方法;(F4部) (5).以之前出现的人为疏忽为案例,分析人为原因,讲解预防措失;(J部) (6).磨钻头与铣刀的方法与技巧;(H1部)
8
加工中经常出现的人为疏失 1.看错图纸,尺寸,电子尺尺寸,卡尺尺寸. 2.对称工件做反. 3.工件铣少或铣反. 4.拿错钻头. 5.孔位偏. 6.牙未攻,角未倒. 7.外观不良及未加工完. 8.不通孔做成通孔. 避免人為不良的加工措施 1.審清圖紙 2.確認尺寸(圖紙尺寸,實際尺寸,电子尺尺寸,卡尺尺寸.) 3.集中精力 4.加工前確認圖紙,確認後再加工完後檢驗確認尺寸的准確性. 磨鑽頭的加工方法 1.先開機把砂輪修平. 2.用雙手的母指和食指捏住鑽頭中部,右手指定在砂輪機防護蓋邊定好位置. 3.利用雙手上下磨動,磨出鑽頭必須後角低於前角以便排屑順暢,中心刀口保持在 中心位置,鑽頭的兩刀基本保持對稱,並且光滑,無斷差,有刀口.
(4)折线:断裂处分界线.
4.审图时应注意(1)有无特别标注左右对称,(2)有无标注特别公差.(3)
是否要求倒角.(4)孔的位置及深度要求.
7
铣床的加工原理:把电能转化为机械能,利用多齿刀具从三个不同方
向作其中的一边作垂直运动.如何安全操作机台见标准作业指导书.F1备料, 飞六面体的加工方法: 1.先锯好粗胚料,一般粗胚料预留5.0MM的余量. 2,磨好飞刀刀片,并装夹固定好. 3.把粗胚料装夹好,对刀开机. 4.先见光一个面,再测量余量的多少来决定进刀量. 5.备好四个面后再利用虎钳的侧面打直角. F2工件定位与基准 1.装夹前必须校正虎钳的垂直度在0.005MM以内,并保证清洁. 2.定位治具必须锁紧固. 3.每次定位的标准必须保持一致. 4.每次选择作基准的垫块必须保持一致. F3孔的加工方法 1.先磨好钻头,打孔前先打孔的中心钻,以保证孔的中心位置. 2.根据工件的要求选择合适的钻头在相应的地方加工. 3.当孔的深度有要求时要选对好刀,再调动深度微调停止块,固定位置,再根 据孔的深度,把机台提升相应深度. 4.根据不同材料,打孔时选择不同转速,钢材66转/分,非金属1100转/分.
铣床工培训资料

目录章节内容页号1.0 铣刀介绍1-42.0 铣削过程的基础知识4-103.0 铣刀几何参数的合理选择10-124.0 铣削用量的选择135.0 难铣削材料的铣削13-146.0 轴上键槽的铣削14-20铣削原理铣削,就是在铣床上以铣刀旋转做主运动,工件做进给运动的切削加工方法。
刀具材料铣削性能的优劣和铣刀角度的合理选择将直接影响切削加工的生产率和加工表面的质量。
1.0铣刀简介在铣削加工中,应根据铣床的情况和加工需要合理地选择和使用铣刀。
1.1.铣刀的种类1.1.1.按用途分类按照用途的不同,可将铣刀分为铣削平面用铣刀、铣削直角沟槽用铣刀、铣削特种沟槽用铣刀和铣削特形面用铣刀等,具体见表1-1。
~1~1.1.2 铣刀的标记为了便于识别铣刀的材料、尺寸规格和制造厂家等,铣刀上都刻有标记,标记的内容主要有以下几种。
1.制造厂家商标我国制造铣刀的厂家很多,如哈尔滨量具刃具厂、上海工具厂和成都量具刃具厂等,各制造厂都将自己的注册商标标注在其产品上。
2.铣刀材料铣刀的材料一般用材料的牌号表示。
如HSS表示铣刀的材料为高速钢。
3.铣刀尺寸规格铣刀的尺寸规格标注因铣刀形状的不同而略有不同。
因铣刀上的标注尺寸均为基本尺寸,在使用和刃磨后会产生变化,所以在使用时应加以注意。
1)带孔铣刀带孔铣刀包括圆柱铣刀,三面刃铣刀和锯片铣刀等,一般以外圆直径×宽度×内孔直径来表示尺寸规格。
例如,三面刃铣刀上标有80×12×27,表示该铣刀的外圆直径为80 mm,宽度为12 mm,内孔直径为27 mm。
2)指状铣刀指状铣刀包括立铣刀和键槽铣刀等,尺寸规格一般只标注外圆直径。
如锥柄立铣刀上标有Ф18,则表示该立铣刀的外圆直径是18 mm。
3)盘形铣刀角度铣刀和半圆铣刀等盘形铣刀,一般以外圆直径×宽度×内孔直径×角度(或圆弧半径)表示。
例如,角度铣刀的外圆直径为80 mm,宽度为22 mm,内孔直径为27 mm,角度为60°,则标记为80×22×27×60°。
数控铣床项目培训课件
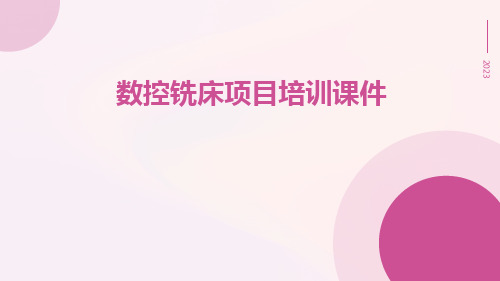
检查冷却系统的过滤 器是否需要更换。
数控铣床的二级保养
检查各轴承、丝杠、齿轮等运动 部件的磨损情况,如磨损严重及 时更换。
检查控制系统的硬件和软件是否 正常工作。
每月检查机器的精度和几何形状 精度,如发现问题及时调整。
检查液压和气压系统的元件是否 老化,如老化及时更换。
检查冷却系统的冷却效果是否良 好。
桨等。
加工沟槽和孔
数控铣床可以高效地加工各种 沟槽和孔,如键槽、直孔、斜
孔等。
加工其他零件
数控铣床还可以加工各种其他 类型的零件,如凸轮、齿轮等
。
数控铣床的加工步骤及操作
• 确定加工方案:根据零件的形状和要求,制定合理的加工方案。 • 装夹工件:将待加工的工件固定在数控铣床的工作台上。 • 选择刀具:根据加工方案,选择合适的刀具。 • 编写程序:根据加工方案和所选刀具,编写数控程序。 • 调试程序:检查编写的程序是否正确,并进行必要的调试。 • 开始加工:将程序输入数控铣床控制系统,开始加工。 • 检查质量:加工完成后,检查工件的质量是否符合要求。
在手动模式下,通过控制面板上的 按键进行程序的输入与编辑。
数控铣床的程序输入与编辑
程序导入
通过计算机与数控铣床的连接,将程序从计算机 导入到数控铣床中。
程序编辑
在控制面板上对程序进行编辑,包括插入、删除 、修改等操作。
程序保存
编辑好的程序需要保存到数控铣床中,以备后续 使用。
数控铣床的自动操作
自动模式选择
03
02
数字孪生技术
5轴联动加工技术
5轴联动加工技术能够实现复杂形 状的加工,提高加工效率和精度。 在数控铣床中引入5轴联动加工技 术,可以扩展设备的加工范围和应 用领域。
数控铣床操作基本技能(短期培训)资料
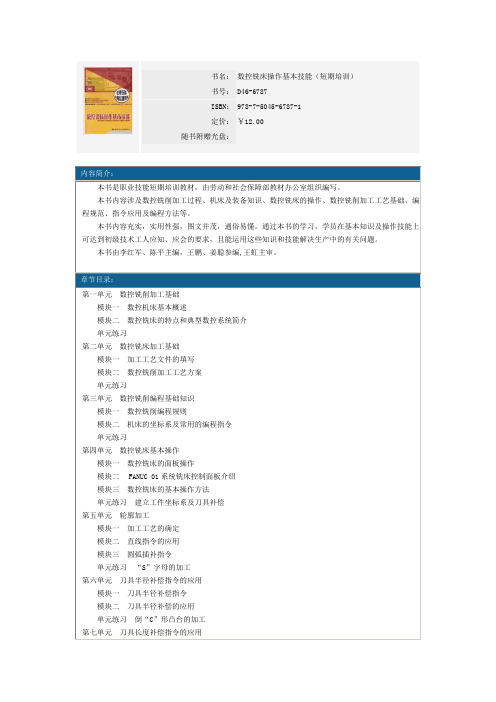
书名:数控铣床操作基本技能(短期培训)书号: D46-6787ISBN : 978-7-5045-6787-1定价:¥12.00随书附赠光盘:内容简介:本书是职业技能短期培训教材,由劳动和社会保障部教材办公室组织编写。
本书内容涉及数控铣削加工过程、机床及装备知识、数控铣床的操作、数控铣削加工工艺基础、编程规范、指令应用及编程方法等。
本书内容充实,实用性强,图文并茂,通俗易懂。
通过本书的学习,学员在基本知识及操作技能上可达到初级技术工人应知、应会的要求,且能运用这些知识和技能解决生产中的有关问题。
本书由李红军、陈平主编,王鹏、姜聪参编,王虹主审。
章节目录:第一单元数控铣削加工基础模块一数控机床基本概述模块二数控铣床的特点和典型数控系统简介单元练习第二单元数控铣床加工基础模块一加工工艺文件的填写模块二数控铣削加工工艺方案单元练习第三单元数控铣削编程基础知识模块一数控铣削编程规则模块二机床的坐标系及常用的编程指令单元练习第四单元数控铣床基本操作模块一数控铣床的面板操作模块二FANUC 0i系统铣床控制面板介绍模块三数控铣床的基本操作方法单元练习建立工件坐标系及刀具补偿第五单元轮廓加工模块一加工工艺的确定模块二直线指令的应用模块三圆弧插补指令单元练习“S”字母的加工第六单元刀具半径补偿指令的应用模块一刀具半径补偿指令模块二刀具半径补偿的应用单元练习倒“C”形凸台的加工第七单元刀具长度补偿指令的应用模块一刀具长度补偿指令模块二刀具长度补偿的应用单元练习型腔的加工第八单元钻孔加工模块一加工工艺的确定模块二钻孔指令单元练习垫块的加工第九单元镗孔加工模块一加工工艺的确定模块二镗孔指令单元练习固定套的加工第十单元螺纹加工模块一加工工艺的确定模块二螺纹加工指令单元练习四孔螺纹零件的加工第十一单元子程序应用模块一加工工艺的确定模块二子程序加工指令单元练习盖板的加工书名:数控铣床操作技能考核培训教程(初级)—职业技能培训教材书号: J62-6193ISBN: 978-7-5045-6193-0定价:¥35.00随书附赠光盘:内容简介:本书将数控铣床初级技能考核培训的范围和内容作了一个简明的叙述。
铣工培训教材

课题一铣床的分类和附件第一节铣床的种类铣床的种类很多,常用的有以下几种:1.升降台铣床:升降台铣床又称曲座式铣床,它的主要特征是沿床身垂直导轨运动的升降台,工作台可随升降台做上下垂直运动,工作台可做纵向和横向运动,故使用灵便。
适宜加工中小型零件,因此升降台铣床是用的最多最普遍的,按主轴位置可分为卧式和立式。
(如x53T,X63T)第一节铣床的种类2.万能工具铣床:万能工具铣床能够完成多种铣削工作,不仅工作台可以做两个方向的平移,立铣头可做一个方向的平移,还可以在垂直平面上左右扳转移角度。
卸掉立铣头摇出横梁还可以当卧式铣床用。
且特别适合于加工刀具,样板其他工具、量具类较复杂的小型零件(如x62w)(图1)第一节铣床的种类3.龙门铣床:属于大型铣床,铣削动力头安装在龙门导轨上,可做横向和升降运动,工作台安装在固定床身上只能做纵向运动,适宜加工大型零件。
4.除以上三类常用铣床外,使用较广泛的还有仿形铣和数控铣床等。
第二节铣床的结构铣床一般由七个部分组成。
1.床身用来安装和支承机床各部件,是铣床的身体,内部有主传动装置,变速箱、电器箱。
床身安装在底座上,底座是铣床的脚,内部还有冷却液等。
2.悬梁安装在床身上方的导轨中,悬梁可根据工作要求沿导轨作前后移动,满足加工需要。
悬梁内部的主轴变速箱是由电动机通过一系列齿轮再传递到一对锥齿轮上,最后从铣头主轴传出。
3.主轴用来带动铣刀旋转,其上有7:24的精密锥孔,可以安装刀杆或直接安装带柄铣刀。
第二节铣床的结构4.升降台沿床身的垂直导轨作上下运动,即铣削时的垂直进给运动。
5.横向工作台沿升降台水平导轨作横向进给运动。
6.纵向工作台沿转台的导轨带动固定在台面上的工件作纵向进给运动。
7.转台可随横向工作台移动,并使纵向工作台在水平内按顺或逆时针扳转某一角度,以切削螺旋槽等(视频1)第三节 X62W铣床的性能和规格X62W型万能铣床比一般铣床所特有的功能是工作台能围绕自己的中心向左右回转45度。
铣床组新进员工培训

铣床组新进员工培训计划一.思想观念教育及课内管理规定教育(课内管理数据,含制作流程教育)二.掌握第三视角法,了解课内模具图面之识图方法.三.熟悉三角函数之间的换算及运用.四.了解模具各组件的名称及作用(同模具课模具组件教育数据)五.了解常用材料特性及用途六.铣床基础知识教育6.1铣床的铣削加工原理6.2铣床各部件的名称及作用6.3铣床的保养与维护6.4铣床的操作程序及注意事项6.5铣床加工工件标准(同QC检测标准)及倒角规范七.铣床刀具的认识7.1刀具切削的基本条件及刀具的材料及种类7.2怎样选择刀具7.3社内刀具的特性7.4铣刀的安装程序及要领7.5铣削的速度及进刀量7.6铣刀的保养与维护及研磨技巧之掌握7.7根据以上要领用各种类型铣刀加工不同材质的工件,感觉铣削工件的情况7.8铣削工作之分析八.钻头的认识及研磨方法8.1钻头的材料及种类8.2钻头各部位名称及作用8.3工件的材料与钻顶角的运用8.4钻头研磨注意事项、方法、技巧及保养维护8.5 钻头的钻削速度判断8.6根据以上要领进行实际操作8.7钻削时的注意事项及不良分析九.铰刀的认识9.1铰刀的材料及种类9.2铰刀前端倒角的作用9.3铰刀的研磨方法及要领9.4钻铰预留量的运用9.5铰刀的铰削速度与进刀9.6铰刀的保养与维护9.7根据以上要领选用SKD61(淬火前)和FDAC的材料分别钻铰Φ2、Φ3、Φ4、Φ5、Φ6的顶针孔9.8铰削工作之不良分析十.螺丝攻的认识10.1螺丝攻的材料及种类10.2钻头在攻丝时钻孔直径的计算方法及标准认识10.3螺丝攻研磨方法及要领10.4根据攻丝要领,选用45#钢分别钻攻各种规格的螺牙10.5攻丝工作之不良分析十一.辅助治工具之使用及保养11.1百分表、千分表的功能使用及保养11.2油压虎钳、成型虎钳使用及保养11.3 V型座、斜度块规、正弦规使用及保养11.4倒角刀、倒角器、倒R刀、寻边器使用及保养十二.学习铣六面体12.1六面体的加工方法12.2铣六面体的注意事项十三.加工基本模具工件之要领13.1加工引张板、耐磨板、滑轨类等配件的要领(钻孔、倒角、寻边、铣六面体精度掌握及运用)十四.学习加工电极、模仁、滑座等散件14.1电极的加工[2D电极(含寻边铣)、六面体之精度掌握及运用]14.2模仁加工方法(钻、铰、攻加工之运用)14.3滑座、滑块加工方法(台阶面加工之运用)十五.了解模板相互配合关系,学习加工模板及斜面加工件15.1铜材、钢材斜度加工型式要领(治具摆放、刀刃铣削)15.2各模板加工要领顺序及方法15.3模板开框的加工方法15.4各模板加工的注意事项十六.特殊加工要领16.1细小及多位槽穴电极之加工16.2模仁台阶面及单向曲面P.L之加工要领16.33D工件的加工方法16.4热处理后材料精加工要领16.5冲子成型器夹取工件铣削方法PS: 3个月后考核1~11理论实绩80%以上,实作考核研磨各刀具掌握70%以上,加工考核12~13项:效率80%,质量95%以上;6个月后考核1~11理论实绩提升20%,实作考核研磨各刀具掌握效率提升20%.加工考核14项:效率80%,质量95%以上,含12~13考核提升效率20%;9个月考核15项:效率80%,质量95%以上,含14项效率提升20%;12个月考核16项:效率80%,质量95%以上,含15项效率提升20%.以上实作加工质量要求95%以上.承认: 确认: 作成:一.思想观念教育及厂纪厂规的教育(同课内规定)二.掌握第三视角法,了解课内模具图面之识图方法(同技术课教育数据)三.模具各组件名称及作用(同课内教育资料)四.熟悉三角函数之间的关系Sinà=A/CCosà=B/C Tgà=A/B ACtgà=B/A五.铣床基础知识5.1铣床各部件名称(同铣床图片)5.2铣床的保养与维护(同<铣床保养作业指导书>)5.3铣床的操作及注意事项(同<铣床操作说明书>)5.4了解铣床基本加工标准及倒角规范六.铣床刀具的认识6.1刀具的工作条件及刀具的材料刀具是在高温、较大压力、剧烈摩擦,有时还承受冲击和振动条件下工作.刀具是由高速钢、高碳工具钢、合金工具钢等材料组成,大多数刀具是在高温真空中以化学气体深覆一层高硬度,耐磨和难熔的金属化合物,刀具表面根据金属化合物的不同呈不同的颜色6.2 铣床的原理及刀具选择依据铣床切削加工实质是材料受到刀具刀刃挤压后,产生了弹性变形,塑性变形和剪切滑移使切削层与母体断裂分离过程一般选择刀具依据以下几点:(1)根据要加工工件的材质(2)根据加工性质(3)根据刀具的特性(4)工件是否淬过火6.3 铣刀安装程序及要领(1)安置铣刀夹头于铣床主轴上(2)选择适当之套筒(3)清拭套筒、铣刀刀柄(4)将铣刀柄推进套筒(在不防碍工作时,刀柄应尽量往里面装,但不可夹持刀刃,然后将铣床主轴变换于低速旋紧夹头螺帽)6.4 铣削速度与进刀铣削速度及进刀直接影响铣刀寿命.加工效率及加工质量,一般切削时最好以较慢之切削速度开始,然后视加工情况逐渐增至适当速度,另外还需考虑下列因素.(1)铣削的工件材料之硬度是重要的因素之一,材料的软硬其切削速度不同,硬材料应使用较低之切削速度,较金属(如镁、铝)则可选用较高之铣削速度;(2)铣刀的工件材料还影响切削速度,一般而言高速钢材质为高碳工具钢之两倍,而碳化物材质铣刀又为高速钢铣刀两倍,直径较小之铣刀以较高速度工作;(3)一般粗铣时,速度不宜过大,精铣时应提高转速,减小进刀量,可得到较好的加工面;(4)铣削速度可按下列公式计算: Cs= πDN/1000Cs为铣削速度(m/mm)D为铣刀外径(mm)N为铣刀每分钟回转数6.5 根据以上要领用各种类型的铣刀加工不同材质的工件感觉铣削效果及工作情况.6.6 铣刀的保养与维护及研磨注意事项(1)铣刀使用前应先行检查有无破损现象,若铣刀已磨损或破损应立即研磨;(2)重新再磨利时,在切刃后背处磨一狭小背刃即可,普通端铣刀之研磨均沿其端面之切刃加以轮磨;(3)装卸铣刀时,宜用软布保护以防碰击而使切刃破损或伤及手部;(4)铣削操作中,启动机器时,应将铣刀与工件分离,以防意外;(5)铣削时应选用适当的切削液;(6)使用完毕之铣刀应检察有无破损,钝化时应实时磨利;(7)铣刀之存放前应彻底擦拭清洁,存放时不可与其它刀具混合放置,以避免碰击而伤及切刃;(8)铣刀在研磨时应注意因高温而软化或变颜色,因此研磨时应随时注意冷却.6.7 铣削之工作分析(1)铣削时产生震动现象,可能是工件还未夹好,铣削深度太深或进刀量大及进刀太快,铣削速度太快等原因;(2)铣削加工面不良可能是切削速度太低,进刀量过大,铣齿钝化,工件与铣刀装置不良,铣床主轴松动等原因;(3)铣齿切刃破裂可能是铣刀及工件夹置不良而产生震动引起,或铣齿钝化后继续使用,铣齿各角度不正确,进刀量太大等原因;(4)铣削时产生黏附刀刃之切屑可能是切削速度太低,铣齿角度不良或进刀太小等原因.七.钻头的认识及研磨7.1钻头的各部分名称及材料钻头是一种旋转而头端有切削能力的工具一般以碳钢SK2或高速钢SKH2、SKH3等材料,经铣制或滚制再经淬火、回火之热处理后磨利而成.7.2工件材料与钻顶角的选用7.3研磨钻头注意事项(1)钻顶角的选用应依工件的材质选择适当之角度;(2)两切边之长度必须相等,且与轴所夹之角度必须相等;(3)钻头研磨时,应防止其因高温而软化,故研磨时,应随时注意冷却;(4)钻削铸铁工件之钻头,其切边应予倒角,钻销青铜、祡铜或其它软金属,则可将切边磨平,以减小斜角.7.4 钻头研磨方法(1)一只手握持钻头前端且微靠着砂轮挟持架上,另一手握持钻头柄端,握持力不可太大;(2)握持钻头,使其中的线与砂轮面成60°;(3)钻头压入砂轮研磨时,压力不可过大,以避免过热使切过热软化,应随时注意使用冷却剂进行冷却;(4)先研磨钻顶角及切边,应两边反复同时进行,一边磨一次切不可一边磨除太多后,再更换另一边.7.5 磨利钻头之不当影响(1)若钻头之切边与钻头轴所夹之角度相等,但切边不相等时,则表示静点偏位,钻削时将引起摆动,扩大孔径;(2)若钻轴至两切边所夹之角度不相符,钻削时仅单边切削钻头易于钝化;(3)若钻头无间隙角时,其切边不能正常切削,压力加大时,即可能扳断钻头.7.6 根据以上要领,进行实际操作7.7钻头钻削速度C.S=π2222222DN/1000C.S为钻削速度(m/min)D为工作直径N为钻床每分钟主轴的转数(rpm)(1)最适当的切速,主要受材料的硬度而定,硬度愈高,韧性愈大,切速宜低;(2)钻头愈小,主轴转速应越高,钻头越大,则转速应越低.7.8钻削工作之分析(1)钻孔前必须先打中心点;(2)钻贯通孔时,当钻头即将钻穿之瞬间,扭力最大,故此时须轻压力,慢慢进刀,以避免钻头受力过大而扭断;(3)钻深孔时,应充分使用切削剂,并注意排屑,避免钻头被切屑夹料.(4)钻削交叉孔时,应先行钻削大直径之孔,再钻小孔径;(5)钻头钻削时,破碎或突然停止的现象,可能是进刀太快,磨利或钻孔时急冷即热之缘故;(6)钻头钻削的折断,可能是钻唇间隙角太小或钻削速度太高,进刀太大,压力太大,或钻头已钝化又继续加压切削所致;(7)切削时切边破裂,可能是工件材料中有硬点、砂眼或进刀太快,钻削选择不当,钻削时无加润滑油或切削剂所致;(8)钻唇及切边破碎可能是进刀太快或钻唇间隙角太大所致;(9)钻削时仅排出一条切削,可能是切边不等长或钻顶角不相等所致;(10)钻削时所钻出孔径太大,可能是两切边不等长或两钻顶角不对中,静点偏离,主轴松动所致;(11)钻削时发生吱吱叫的声音,可能是孔不直或钻头钝化所致;(12)钻削时切屑材质产生异常变化,可能是钻头已钝化或破损所致.八.铰刀的认识及使用时注意事项8.1 铰刀的材料铰刀是以高碳钢、高速钢或碳化物所制成8.2 铰刀前端倒角的作用倒角是为了引导铰刀进入工作孔内,若铰刀无倒角,则铰削时容易产生振动现象,一般机械铰刀倒角45°,手工铰刀其前端为1°倒角.8.3 铰刀之铰削速度与进刀(1)用手工铰削时,双手的扭转速度和压力配合要适当,铰削中回转速度均匀、压力平均、无忽大忽小现象,感觉铰削极为顺畅即可;(2)机器铰削速度与进刀依工件材料之性质,加工条件等而定;(3)若铰削速度太慢,则增加铰刀磨耗,若速度太快,则会导致切削黏附刀刃而产生加工不良,一般铰削速度为钻削的1/2-2/3;(4)铰刀进刀量是钻孔之进刀量的2-3倍.8.4 铰刀的保养与维护(1)装置铰刀时最好以布接夹,以避免铰刀受损或伤手;(2)铰孔时应使用适量的攻牙油;(3)存放铰刀时,应先将铰刀擦拭干凈,并涂WD-40以防止生锈;(4)存放时铰刀尺寸要加以标示,不可重迭交叉存放,以避免刃边破碎.8.5 根据以上要领,选用SKD61和TDAC的材料分别钻铰Φ2、Φ3、Φ4、Φ5、Φ6的顶针孔.8.6 铰销工作分析(1)手工铰刀预留量为0.1mm机械铰刀预留量见下表:(2)铰孔时,孔径变小原因可能是被切材料之弹性较大,也可能是铰刀已钝化;(3)铰孔时孔径变大原因是切削齐、切削速度、进刀量、加工量等所致.机械性能和工件夹持也是主要因素,因此为得到精确之孔径必须选择适当之切削剂铰削速度、进刀量及加工预量,操作时工件夹持要稳定,铰刀夹持要正确;(4)铰孔时,铰刀不得逆转退回,以避免铰刀切边破碎.九.螺丝攻的认识及如何正确使用9.1螺丝攻材料螺丝攻是在周边上具有一个或数个所须螺纹形状切削部分之圆柱形或锥形螺纹切削刀具它一般是高碳钢、合金工具钢、高速钢等材料经制造、淬火、回火等热处理而成.9.2攻丝时钻头计算方法攻丝钻头为攻丝前钻孔所使用的钻头、理论是讲其尺寸是和螺丝底径相同,即外径减去二倍之牙深之尺寸,实际是只留牙高75%为攻丝预留量.60°牙角三角螺纹攻丝预留量75%之攻丝钻头呎寸可同下面公式求出攻丝钻头呎寸=外径(公称呎寸)-0.75*(0.6495*螺距)*2简略上式:攻丝钻头呎寸=外径-螺距P9.3根据攻丝要领选用45#钢,分别钻攻各种规格的螺牙9.4攻丝之工作分析(1)攻丝时应选用适当之螺丝扳手,攻丝时以充分之压力使螺丝攻进入孔内,然后卸下扳手,检查螺丝攻是否和工作物面垂直,若螺纹不垂直则倒转螺丝攻,然后向倾斜方向之对边方向加压旋转反复几次,直至螺丝攻垂直为止,旱行正确后,只须旋转扳手,不再施压力即可自动进行切削,此时两手所施之扭力应平均.在切削进行中,每旋转切削1/2或1圈时,即应倒转半圈,以断裂切屑;(2) 攻丝时钢或青钢等材料应使用油化学切削剂等,但黄钢及铸铁则不必加切削剂;(3) 攻丝时,螺丝攻断裂,主要原因是螺丝攻撞及孔底孔之尺寸不正确,切屑堆积在槽内攻丝偏斜、润滑不足等,有时反转时铁屑卡断螺丝攻,以上应采取措施加以避免;(4) 螺丝攻使用后应擦拭、清洁并上油,存放于组合盒内.十. 学习如何铣六面体10.1六面体的加工方法10.2铣六面体的注意事项十一. 加工基本模具工件之要领11.1耐磨板、滑轨类工伯的加工耐磨板、滑轨类工件要注意油槽的加工方向,孔的中心位置不可偏移.11.2加工引张板类工件引张板类工件应注意槽穴的长度要一致十二. 学习加工电极、模仁、滑座等散件12.1电极加工方法12.2模仁加工方法12.3滑座加工方法十三. 了解模板相互配合关系,学习加工模板13.1各模板的加工要领及方法(1) 对于有剥料板的三板式模具,剥料板和上固定板组合在一起加工,加工上固定板与剥料板用导柱串起加工螺纹孔和拉料销孔,加工时寻边分中上固定板流道衬套孔,加工拉料销孔时需铰孔,且在剥料板上钻铰一个Φ6或Φ8的孔,以便于线割寻边加工注道衬套孔;(2) 对公母模板的加工,一般先把模板框加工好,再加工斜面和斜销孔,然后加工螺线孔、顶针孔及水孔等;(3) 对于公模中板和承板的加工,如果模板上有要求和公模板同心度和精度要求较高时,要用导柱和辅助导柱等组合起来进行加工;(4) 加工上顶出板上顶针孔时,用回位销和公模板组合起来,保证公模板和上顶出板顶针孔同心,且孔位置不可偏移;(5) 加工下顶出板时要用导套套在上顶出板上;(6) 对于下固定板上有司筒针孔时,要用辅助导柱、导套组合起来保证下固定板同公模板司筒针孔同心.13.2模板开框精度要求(同QC作业标准)13.3模板开框加工方法及注意事项(同铣床组教育数据) 十四.进行技术等级考核。
- 1、下载文档前请自行甄别文档内容的完整性,平台不提供额外的编辑、内容补充、找答案等附加服务。
- 2、"仅部分预览"的文档,不可在线预览部分如存在完整性等问题,可反馈申请退款(可完整预览的文档不适用该条件!)。
- 3、如文档侵犯您的权益,请联系客服反馈,我们会尽快为您处理(人工客服工作时间:9:00-18:30)。
铣床培训教材1铣床的基本知识1.1 铣床的类型:升降台式铣床(卧式铣床、立式铣床)、万能铣床、龙门铣床、特种铣床、数控铣床等。
1.2 铣床的结构部件:底座床身、主轴、主轴变速机构、纵向工作台、横向工作台、升降台等。
1.3 铣削的概念:铣削就是在铣床上以铣刀旋转作主运动,工件或铣刀作进给运动的切削加工方法。
1.4 铣削加工的特点:铣削是用多刀刃的铣刀来进行切削加工的,故生产效率较高。
1.5 铣削的加工精度:铣削加工的经济加工精度一般为IT9~IT8,表面粗糙度Ra值可达到12.5~1.60um;必要时加工精度可高达IT5,表面粗糙度Ra值可达0.20um。
1.6 铣床的加工范围:铣平面、铣直槽、铣燕尾槽、铣T型槽、铣成形面等各种形状复杂的零件。
2铣刀的基本知识2.1 铣刀的种类(按铣刀切削部分的材料分):高速钢铣刀、硬质合金铣刀2.2 铣刀切削部分材料的基本要求:2.2.1 高硬度和高耐磨性:在常温下,切削部分材料必须具备足够的硬度才能切入工件;具有高的耐磨性,刀具才不易磨损,延长使用时间。
2.2.2 好的耐热性:刀具在切削过程中会产生大量的热量,尤其在切削速度较高时,温度会很高。
因此,刀具材料应具备好的耐热性,即在高温下仍能保持较高的硬度,具有能继续进行切削的性能。
这种具有高温硬度的性质,又称热硬性或红硬性。
2.2.3 高的强度和好的韧性:在切削过程中,刀具要承受很大的冲击力,所以刀具材料要具有较高的强度,否则易断和损坏。
由于铣刀会受到冲击和振动,因此,铣刀材料还应具备好的韧性,才不易崩刃、碎裂。
2.2.4 工艺性好:这样有利于制造出各种形状和尺寸的刀具。
3基准的种类及选择原则3.1 基准的种类:3.1.1 设计基准:零件在设计图样上,用来确定其它的点、线、面位置的基准称为设计基准。
设计基准一般是零件图样上标注尺寸的起点或对称点,如齿轮的轴线或孔的中心线等。
矩形零件和箱体零件,则多数以底面为设计基准。
3.1.2 工艺基准:工艺基准是指在机械制造过程中采用的各种基准。
其中包括:工序基准、定位基准、测量基准和装配基准。
3.1.2.1 工序基准:用来确定本工序所加工表面加工后的尺寸、位置的基准。
3.1.2.2 定位基准:工件在机床上或夹具中定位时,用以确定加工表面对刀具切削位置之间相互关系的基准。
3.1.2.3 测量基准:用以测量工件各表面的相互位置、形状尺寸的基准,测量基准通常就是设计基准。
3.1.2.4 装配基准:在装配中用以确定工件本身位置的基准。
3.2 定位基准的选择原则:3.2.1 选择定位基准是加工前的一个重要要素,定位基准选择是否正确,对加工质量和加工时的难易程度有很大的影响,这也必然会影响到产品的加工成本。
所以,选择定位基准时主要应掌握两个原则,即保证加工精度和装夹方便。
3.2.2 定位基准应能保证工件在定位时具有良好的稳定性,以及尽量使夹具的结构简单。
3.2.3 定位基准应能保证工件在受夹紧力和铣削力等外力作用时引起的变形量最小。
3.2.4 粗基准的选择原则(以毛坯上未经加工过的表面作基准):3.2.4.1 当工件的所有表面都需要加工时,应选择加工余量最小的表面作粗基准。
3.2.4.2 若工件必须首先保证其重要表面的加工余量均匀,则应选择该表面为粗基准。
3.2.4.3 工件上有不需在加工的表面时,应以不加工的面作粗基准。
3.2.4.4 尽量选择平整的表面作粗基准,以便定位准确、夹紧可靠。
3.2.4.5 粗基准一般只能使用一次,尽量避免重复使用。
因为粗基准的表面粗糙度和精度都很差,重复使用时,即使安装的条件相同,也不易使工件精确的装夹在原来的位置上,因此,必然会产生定位误差。
3.2.5 精基准的选择原则(以已加工过的表面作定位基准):3.2.5.1 基准重合原则:尽量采用设计基准、工序基准、装配基准和测量基准作定位基准。
3.2.5.2 基准统一原则:当工件上有几个相互位置精度要求高、关系比较复杂的表面、而且这些表面不能在一次安装中加工出来时,在加工过程的各次安装中应该采用同一个定位基准。
3.2.6 在实际选择定位基准时,上面的几项原则有时会相互矛盾;因此,必须根据具体情况进行综合考虑,选择最合理的定位基准。
4 常用夹具及工件的装夹4.1 夹具的作用:能保证工件的加工精度、减少辅助时间,提高生产效率、扩大通用工模部员工培训教材科瑞自动化技术(深圳)有限公司机床的使用范围、能使低等级技术工人完成复杂的加工任务、减轻操作者的劳动强度,并有利于安全生产。
4.2 夹具的种类4.2.1 通用夹具:这类夹具通用性强,由专门厂家生产,并已经标准化,其中有的作为机床附件随机床配套,如平口钳、分度头等。
4.2.2 专用夹具:专用夹具是为了适应某一特定工件的某一个工序加工要求而专门设计制造的。
4.2.3 可调夹具:为了扩大夹具的使用范围,解决专用夹具利用率低的缺点,目前大量使用可调夹具。
4.3 平口钳及工件装夹4.3.1 平口钳的用途:平口钳是铣床上用来装夹工件的附件。
铣削一般的长方体零件的平面、台阶面、斜面及轴类零件的沟槽时,都可用平口钳装夹工件。
4.3.2 平口钳的结构:常用的平口钳有回转式和非回转式两种。
回转式平口钳钳体能在底座上扳转任意角度。
非回转式平口钳结构与回转式平口钳基本相同,只是底座没有转盘,钳体不能扳转。
回转式平口钳使用方便,适应性强,但由于多了一层转盘结构,高度增加,刚度相对较差。
因此,在铣削平面、垂直面和平行面时,一般都采用非回转式平口钳。
4.3.3 平口钳的规格:平口钳规格是以钳口铁的宽度而定的,有100mm、125 mm、160 mm、200 mm、和250 mm、等规格。
4.3.4 平口钳的安装和校正4.3.4.1平口钳的安装,安装平口钳时,应擦净钳座底面和铣床工作台面。
一般情况下,平口钳在工作台面上的位置,应处于工作台长度方向的中心偏左、宽度方向的中心,以方便操作。
钳口方向应根据工件长度来确定,对于长的工件,钳口应与铣床主轴轴线垂直。
对于短的工件,钳口应与铣床主轴轴线平行。
对于一般的工件,平口钳可用定位键安装。
安装时,将平口钳底座上的定位键放入工作台中央T形槽内,双手推动钳体,使两定位键的同一侧面靠在中央T形槽的侧面上,然后固定钳座,再利用钳体上的零刻线与底座上的刻线相配合,转动钳体,使固定钳口与铣床主轴轴线垂直或平行,也可以按需要调整成所要求的角度。
4.3.4.2 固定钳口的校正:加工有较高相对位置精度要求的工件时(如铣削沟槽),钳口与主轴轴线要求有较高的垂直度或平行度,这时应对固定钳口进行校正。
用百分表校正固定钳口与铣床纵向工作台平行。
加工较长的工件,固定钳口一般采用与铣床纵向工作台平行安装,此时可用百分表校正。
将百分表座子吸在机床主轴上,百分表指针指向固定钳口,然后移动工作台,使表针跳动在±0.01mm范围内即可;紧固钳体工模部员工培训教材科瑞自动化技术(深圳)有限公司后,须再进行复检,以免紧固时发生位移。
4.4 在平口钳上装夹工件时的注意事项4.4.1 应擦净钳口铁平面、钳体导轨面及工件表面。
4.4.2 放置的位置应适当,夹紧后钳口的受力应均匀。
4.4.3 待铣去的余量层应高出钳口上平面,高出的高度以铣削时铣刀不接触钳口上平面为宜。
4.4.4 用平行垫铁辅助装夹工件时,所选垫铁的平面度、上下表面的平行度以及相邻表面的垂直度应符合要求;垫铁表面应具有一定的硬度。
5 铣削的基本知识5.1 主运动:是切除工件表面多余材料所需的最基本的运动,是直接切除工件上待切削层,使之转变为切屑的主要运动。
主运动是消耗机床功率最多的运动。
铣削运动中,铣刀的旋转运动是主运动。
5.2 进给运动:是使工件切削层材料相继投入切削,从而加工出完整表面所需的运动。
铣削运动中,工件的移动或回转、铣刀的移动等是进给运动。
5.3 铣削中顺铣和逆铣的概念及优缺点5.3.1 顺铣:铣削力的水平分力与工件的进给方向相同5.3.1.1优点:加工的表面质量好;功率消耗少;刀刃磨损较慢;对不易夹紧的工件和细长的工件更为合适。
5.3.1.2 缺点:工件台进给丝杠与固定螺母之间一般有间隙存在,因此切削力容易引起工件和工作台一起向前窜动,使进给量突然增大,引起打刀。
在铣削铸件或锻件等表面有硬度的工件时,顺铣刀齿首先接触工件硬皮,加剧了铣刀的磨损。
5.3.2 逆铣:铣削力的水平分力与工件的进给方向相反5.3.2.1 优点:可以避免顺铣时发生的窜动现象;加工表面有异物(砂粒)的毛胚时须选用逆铣。
5.3.2.2 缺点:逆铣时,切削厚度从零开始逐渐增大,因而刀刃开始经历了一段在切削硬化的已加工表面上挤压滑行的阶段,加速了刀具的磨损。
同时,铣削力将工件上抬,易引起振动,从而影响工件已加工面的表面质量;功率消耗大;刀具磨损快;容易使工件移动。
5.4 铣削用量:在铣削过程中所选用的切削量称为铣削用量。
铣削用量包括铣削宽度、铣削深度、铣削速度和进给量。
铣削用量的合理选择,对提高生产效率,改善工件表面粗糙度和加工精度都有密切的关系。
6 切削液的作用及种类6.1在铣削过程中,刀具与工件间相互摩擦所消耗的功率绝大部分转变为热能,致使刀尖处的温度升得很高。
高温会使刀刃很快磨钝和损坏,使加工出来的工件质量工模部员工培训教材科瑞自动化技术(深圳)有限公司下降。
为了降低切削时的温度,目前常采用的方法是切削时浇注切削液。
6.2切削液的作用6.2.1 冷却作用:充分浇注切削液,能带走大量热量和降低温度,有利于提高生产效率和产品质量。
6.2.2 润滑作用:切削液可以减小切削过程中的摩擦,减小切削阻力,显著提高工件表面质量和刀具耐用度。
6.2.3 防锈作用:切削液有使机床、工件、刀具不受周围介质的腐蚀的作用。
6.2.4 冲洗作用:在浇注切削液时,能把铣刀齿槽中和工件上的切屑冲去,使铣刀不因切屑阻塞而影响铣削。
6.3 切削液的种类及选用6.3.1 乳化液:乳化液是将乳化油用水稀释而成。
其流动性好,比热容大,黏度小,冷却效果良好,并具有一定的润滑性能,主要用于钢、铸铁和有色金属的切削加工。
6.3.2 切削油:切削油的主要成分是矿物油(柴油和机油等),也可以选用植物油(菜籽油和豆油等)、硫化油和其他混合油等。
这类切削液的比热容低,流动性差,是一种以润滑为主的切削液。
6.3.3 切削液的选用:应根据工件材料、刀具材料和加工工艺等因素选择切削液。
6.3.3.1粗加工时切削量大,产生的热量多,温度高,而对表面质量的要求并不高,所以应采用以冷却为主的切削液。
6.3.3.2 精加工时切削量小,产生的热量也少,对工件的表面质量要求高,并希望铣刀的耐用度高,所以选用以润滑为主的切削液。
6.3.3.3 铣削铸铁、黄铜等脆性材料时,一般不用切削液,必要时可用煤油、乳化液和压缩空气。