轴承钢连铸技术
轴承钢连铸工艺流程
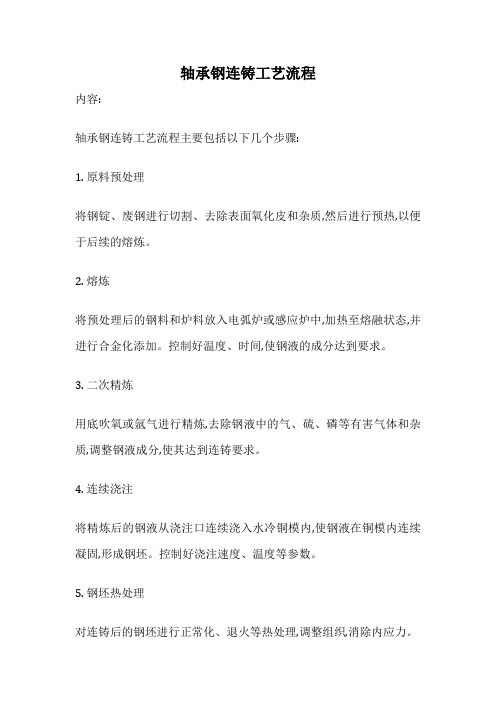
轴承钢连铸工艺流程
内容:
轴承钢连铸工艺流程主要包括以下几个步骤:
1. 原料预处理
将钢锭、废钢进行切割、去除表面氧化皮和杂质,然后进行预热,以便于后续的熔炼。
2. 熔炼
将预处理后的钢料和炉料放入电弧炉或感应炉中,加热至熔融状态,并进行合金化添加。
控制好温度、时间,使钢液的成分达到要求。
3. 二次精炼
用底吹氧或氩气进行精炼,去除钢液中的气、硫、磷等有害气体和杂质,调整钢液成分,使其达到连铸要求。
4. 连续浇注
将精炼后的钢液从浇注口连续浇入水冷铜模内,使钢液在铜模内连续凝固,形成钢坯。
控制好浇注速度、温度等参数。
5. 钢坯热处理
对连铸后的钢坯进行正常化、退火等热处理,调整组织,消除内应力。
6. 切断、标记
将连铸的钢坯切割成定长,进行标记,作为后续加工的原材料。
通过上述工艺流程,可以获得性能优良的轴承钢坯,为后续加工提供优质的原材料,以生产高品质的轴承钢产品。
260mm×300mm轴承钢连铸坯生产Ф70~Ф75mm棒材的工艺实践
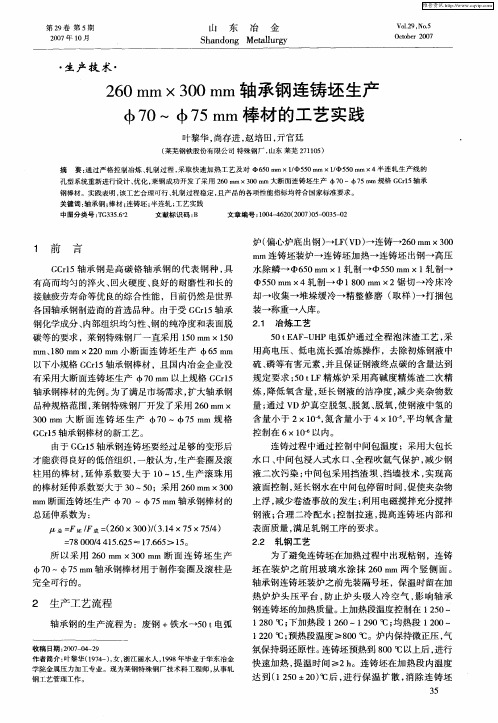
孔型系统重新 进行设 计 、 优化 , 莱钢成 功开发了采用 2 0riX30m 6 n 0 m大断面连铸坯 生产 7 7 l a 0~ 5In规格 G r5轴承 i l C1
钢棒材 。实践表 明 , 该工艺合理可行 、 轧制过程稳定 , 品的各项性 能指标 均符合国家标准要求 。 且产
为 了避免 连铸坯 在加 热过 程 中出现粘 钢 ,连铸
坯 在 装 炉之 前 用 玻 璃水 涂 抹 20m 6 m两 个 竖 侧 面 。 轴 承钢连 铸坯 装炉 之前先 装 隔号坯 ,保温 时 留在 加 热 炉 炉 头 压平 台 , 防止 炉 头 吸 人 冷 空气 , 响轴 承 影
量; 过 V 通 D炉 真空 脱氢 、 氮 、 氧 , 脱 脱 使钢 液 中氢 的
轴承钢棒 材 的先 例 。 了满 足市场 需求 , 为 扩大轴 承钢
品种规 格范 围 , 莱钢 特殊 钢厂 开发 了采 用 2 0m 6 mX 3 0r 大 断 面 连 铸 坯 生 产 7 7 m 规 格 0 m n 0~ 5m G r5轴承钢 棒材 的新 工艺 。 Cl 由于 G r5 承钢连铸 坯要 经过足 够 的变形后 Cl 轴
7 7 0~ 5mm棒材 的工艺实践
叶黎华 , 尚存进 , 培 I, 赵 t 亓官廷 l
( 莱芜钢铁股份有 限公 司 特殊 钢厂 , 山东 莱芜 2 10 ) 7 15
摘 要: 通过严格控制冶炼 、 轧制过程 , 采取快速加 热工艺及对  ̄60rnX1O5 0ri X1O5 0ri 5a i / 5 a n / 5 a n×4半连 轧生产线的
却一 收集一堆垛缓冷一精整修磨 ( 取样 ) 一打捆包
装一 称重一 人库 。 21 冶炼工艺 . 5 E F U P电弧 炉通 过全 程 泡 沫渣 工艺 , 0 A — H t 采 用高 电压 、低 电流长 弧冶炼 操作 ,去 除初炼钢 液 中
轴承钢的生产与发展

引入人工智能、大数据等先进技术,实现轴承钢生产过程的自动化 、智能化,提高生产效率和产品质量。
高性能轴承钢研发
针对高端装备领域的需求,研发具有更高强度、耐磨性、耐腐蚀性 等综合性能的新型轴承钢。
04
轴承钢的市场现状与前景
全球轴承钢市场规模与分布
规模庞大
全球轴承钢市场规模已经达到数十亿 美元,显示出这一领域的重要性和活 跃度。
通过改进热处理工艺,如控制淬火 和回火的温度和时间,轴承钢的力 学性能和尺寸稳定性得到了提升。
轴承钢的现代化生产阶段
01
先进的生产技术
现代化生产阶段采用了如电炉炼钢、连铸连轧等先进生产技术,显著提
高了轴承钢的生产效率和产品质量。
02
多元化的产品系列
随着轴承应用领域的不断拓展,轴承钢的产品系列也日益多元化,包括
高效连铸技术
通过优化连铸机的设计和 工艺参数,提高连铸坯的 拉速和质量,降低生产成 本。
控轧控冷技术
在热轧过程中,采用控轧 控冷技术可以精确控制钢 材的组织和性能,提高轴 承钢的使用寿命。
轴承钢生产的未来技术趋势
绿色环保生产技术
随着环保要求的提高,轴承钢生产将更加注重节能减排和废弃物 回收利用,实现绿色生产。
智能制造与数字化转型
在工业互联网、大数据等技术的推动下,轴承钢企业将加 快智能制造和数字化转型步伐,提高生产效率和产品质量 ,增强企业竞争力。
跨界合作与创新
面对新技术、新市场的挑战,轴承钢企业将积极寻求与其 他产业、科研机构的跨界合作与创新,共同推动轴承钢产 业的技术进步和市场拓展。
THANKS
感谢观看
环保要求提高
随着全球环保意识的提高,轴承钢的环保要求也将越来越高,推动轴 承钢产业向环保和可持续发展的方向转型。
连铸生产GCr15轴承钢工艺的改进

3 - 1
GC r15 钢是 一种 合金 含量较 少、 具有 良好性 能、 应用 最 广泛的高碳铬轴承钢。由于其使用环境 的特殊性 , 用户 对其 质量提出较为严格的要 求。 GCr15 钢 的特点 是两相 区宽 , 柱 状晶发达 , 易产生 中心疏 松和 偏析 , 生产 过程 中对 于连铸 工 艺的精 确控制 要求非 常严格。虽 然 GC r15 低过 热度浇注 有 利 , 可减轻中心疏松和偏析的缺陷 , 但过 热度低 , 可导致 钢水 在水口冻结 , 造 成生 产事故 , 不 利于 连续生 产。本钢 特钢 厂 生产 GC r15 钢时 , 中间包过 热度控 制在 10 ~ 20 , 出现因 中 包过热度低而发生 冻钢 事故造 成断 浇。铸坯 拉速 和负滑 动 时间等因素 , 影响 结晶器 保护 渣的润 滑作 用 , 使铸 坯表面 振 痕较深。经过对连铸工艺过程的改进 , 连铸生 产的 G Cr15 低 倍合格率明显提高 , 带状组 织合格率达 100% 。
弧形半径 /mm 台数 机数 流数
流间距 /mm 断面 /mm mm 中间包工作容量 / t 中间包控流方式 设计年产量 / t
自 2006 年本钢特 钢厂 连铸 生产轴 承钢 以来 , 采 用的 连 铸工艺参数见 表 2。由 于对 连铸 生产 轴承 钢的 生产 经验 不 足 , 工艺参数选取不尽合理 , 出现一些质量问题和生产事故 ,
经过对连铸工艺过程的改进连铸生产的gcr15倍合格率明显提高带状组织合格率达100有必要对连铸工艺参数进行优化调整原有的连铸工艺参数液相线1447102017026430改进后连铸生产gcr15的工艺条件根据生产实际情况和产品检验结果结合查阅相关文献gcr15钢的连铸工艺参数进行优化调整具体参数见表连铸工艺的优化参数原有连铸生产gcr15的工艺条件本钢特钢厂连铸机主要参数见表连铸机的主要参数14472524470弧形半径mm台数间距mm断面mmmm中间包工作容量优化后的过热度和拉速150001515202030303535404065180023526519中间包控流方式设计年产量塞棒自动控流4800002006年本钢特钢厂连铸生产轴承钢以来采用铸工艺参数见表2
连续铸钢技术项目设计方案

连续铸钢技术项目设计方案1.1 连铸技术的发展概况连续铸钢是钢铁冶金领域内发展最快、最受重视和最为成功的技术之一,其原因在于连铸技术具有显著的技术经济优越性,是钢铁生产流程中结构优化的重要环节。
转炉的发明者亨利·贝塞麦(Herry Bessemer)于1846年首先提出了连续浇注的概念并于1857 年获得专利权。
从那时以来,近一个世纪的时间里,世界上的一些冶金工作者在连续浇铸技术方面进行了有益的探索,上世纪三十代,德国人容汉斯开创性的提出结晶器振动法,浇注铜铝合金获得成功,使有色合金的连续铸造应用于生产,金属(铜、铝)的连续铸造获得了工业应用。
但钢液的连续浇铸却始终没有获得工业化[1]。
钢的连铸取得突破性进展是由1945 年,容汉斯(S.Junghans)及其合作者罗西(I.Rossi)采用了振动式结晶器代替以前的固定式结晶器,解决了固定式结晶器拉坯漏钢的难题,钢水的连铸才首次获得成功。
1950 年容汉斯和曼内斯曼(Mannesmann)公司合作,建成了世界上第一台能浇铸 5 t 钢水的连铸机[2]。
钢水连铸获得巨大成功的另一重要的技术关键是英国人哈里德(Halliday)提出的“负滑脱(Negative Slip)”的概念。
“负滑脱”能够有效地防止了凝固壳与结晶器的粘结和更好地改善润滑。
20 世纪40 年代,德国建成了第一台浇注钢水的实验性连铸机。
连铸技术在20 世纪50 年代初开始步入工业应用阶段,70 年代以后钢的连铸技术迅速发展,80 年代连铸技术日臻完善,一个国家的连铸技术水平的高低己成为衡量其钢铁工业现代化程度的重要标志。
20 世纪90 年代,随着钢的连铸技术的日益成熟,连铸技术又有新的重大发展。
从那时以来,薄板坯连铸(连轧)技术在世界上获得了重大发展;薄带连铸技术也受到广泛重视,进行了深入研究;高效连铸技术随之出现,并获得了迅速发展。
今天,钢的连铸技术无论从深度和广度上,都远远超过了20 世纪80年代的水平。
轴承钢冶炼和连铸技术
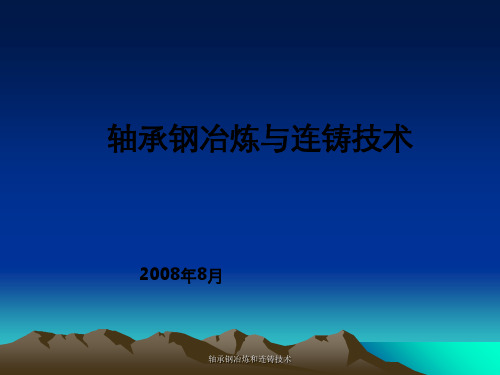
钢生产鼠基本占西方工业化国家轴承钢产最的70 %以上,由于轴承钢 生产的高度集中,国外轴承钢生产工艺及实物质量达到了一个很高的水 平。
滚动轴承的内外圈和滚动体应具有较高的硬度和接触 疲劳强度、良好的耐磨性和冲击韧性,一般用
性变形;
(4) 要有一定的韧性,防止轴承在受冲击载荷作用时发生破坏; (5) 要有一定的抗腐蚀性能; (6) 要有良好的工艺性能,如冷热成型、切削、磨削等性能,以
适应大批量、高效率、高质量生产的需要;
(7) 具有良好的尺寸稳定性,防止轴承在长期存放或使用中因尺
寸变化而降低精度。
轴承钢冶炼和连铸技术
对轴承钢的质量要求
轴承钢冶炼与连铸技术
2008年8月
轴承钢冶炼和连铸技术
内容:
1 :轴承钢发展概况 2 :轴承钢性能要求 3 :钢液精炼渣的设计
轴承钢冶炼和连铸技术
轴承钢发展概况
轴承钢冶炼和连铸技术
轴承钢是重要的冶金产品,它被广泛应用于机械制造、 铁路运输、汽车制造、国防工业等领域。
滚动轴承一般由内圈、外圈、滚动体和保持架组成。
轴承钢冶炼和连铸技术
轴承钢冶炼和连铸技术
钢水纯洁度 氧含量是轴承钢纯洁度的最重要标志之一。轴承钢当氧含
量由30ppm下降到20ppm时,其接触疲劳寿命提高1.5 倍;降到15ppm时提高2倍;降到8ppm时提高3倍。因此,各
大厂家都非常重视对氧含量的控制。目前,国际上先进水平,
如日本山阳制钢的轴承钢,氧含量可以达到5~8ppm。
• 我国轴承钢与国外相比最主要的差距是在技术装备。国外 在轴承钢熔炼上,初炼炉和精炼炉朝高功率、大容量发展。
轴承钢生产工艺技术简介
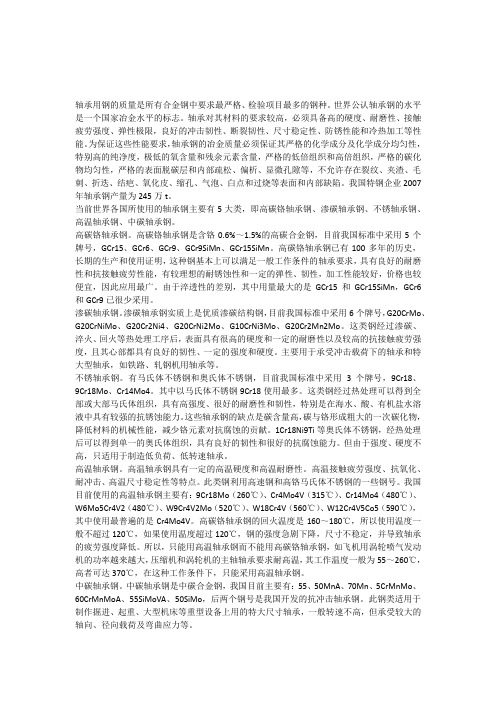
轴承用钢的质量是所有合金钢中要求最严格、检验项目最多的钢种。
世界公认轴承钢的水平是一个国家冶金水平的标志。
轴承对其材料的要求较高,必须具备高的硬度、耐磨性、接触疲劳强度、弹性极限,良好的冲击韧性、断裂韧性、尺寸稳定性、防锈性能和冷热加工等性能。
为保证这些性能要求,轴承钢的冶金质量必须保证其严格的化学成分及化学成分均匀性,特别高的纯净度,极低的氧含量和残余元素含量,严格的低倍组织和高倍组织,严格的碳化物均匀性,严格的表面脱碳层和内部疏松、偏析、显微孔隙等,不允许存在裂纹、夹渣、毛刺、折迭、结疤、氧化皮、缩孔、气泡、白点和过烧等表面和内部缺陷。
我国特钢企业2007年轴承钢产量为245万t。
当前世界各国所使用的轴承钢主要有5大类,即高碳铬轴承钢、渗碳轴承钢、不锈轴承钢、高温轴承钢、中碳轴承钢。
高碳铬轴承钢。
高碳铬轴承钢是含铬0.6%~1.5%的高碳合金钢,目前我国标准中采用5个牌号,GCr15、GCr6、GCr9、GCr9SiMn、GCr15SiMn。
高碳铬轴承钢已有100多年的历史,长期的生产和使用证明,这种钢基本上可以满足一般工作条件的轴承要求,具有良好的耐磨性和抗接触疲劳性能,有较理想的耐锈蚀性和一定的弹性、韧性,加工性能较好,价格也较便宜,因此应用最广。
由于淬透性的差别,其中用量最大的是GCr15和GCr15SiMn,GCr6和GCr9已很少采用。
渗碳轴承钢。
渗碳轴承钢实质上是优质渗碳结构钢,目前我国标准中采用6个牌号,G20CrMo、G20CrNiMo、G20Cr2Ni4、G20CrNi2Mo、G10CrNi3Mo、G20Cr2Mn2Mo。
这类钢经过渗碳、淬火、回火等热处理工序后,表面具有很高的硬度和一定的耐磨性以及较高的抗接触疲劳强度,且其心部都具有良好的韧性、一定的强度和硬度。
主要用于承受冲击载荷下的轴承和特大型轴承,如铁路、轧钢机用轴承等。
不锈轴承钢。
有马氏体不锈钢和奥氏体不锈钢,目前我国标准中采用3个牌号,9Cr18、9Cr18Mo、Cr14Mo4。
轴承钢绿色高效连铸及均质化关键技术

轴承钢绿色高效连铸及均质化关键技术在咱们日常生活中,轴承钢可能大家不是特别关注,但它在咱们的工业中可起着举足轻重的作用。
想象一下,汽车、机器、工厂的设备这些“大家伙”都离不开轴承钢,它就像个默默无闻的幕后英雄,虽然不显眼,可是每时每刻都在提供动力支持。
而要让这些钢材的质量更好、性能更稳定,关键的一个环节就是连铸和均质化技术。
这就像做饭一样,要想炖出一锅好汤,火候、食材都得讲究,而这两项技术就是保证轴承钢“好味道”的秘诀。
说到轴承钢的绿色高效连铸,很多人可能一脸懵。
其实啊,连铸就是把液态的钢水通过一种特殊的工艺直接铸造成钢坯。
以前,我们的钢铁生产老是用那种“粗暴”的方法,要经过好多步,浪费能量,污染环境。
现在好了,绿色高效连铸的技术就像给钢铁生产换上了“环保模式”。
这个过程不仅减少了资源浪费,还能大大提高生产效率。
你想啊,原本得几天的工序,搞不好几小时就能搞定了,这对生产效率和环境保护来说,简直是“省时省力又省钱”的好事。
但是,连铸只是第一步,接下来最让人头疼的就是均质化了。
均质化听起来好像是个高深的技术名词,但其实就是让钢材内部的组织更加均匀、稳定。
就像你炒菜,调料得均匀分布,菜才会好吃。
如果调料撒得不均匀,一口咸一口淡,谁吃了都不好受。
轴承钢也一样,均匀的结构能让它在使用过程中更加坚固耐用,不容易出现裂纹、变形。
均质化其实是通过高温处理来“让钢材慢慢舒展”,让它内部的成分分布更加均匀。
这个过程中,温度、时间和工艺的掌控就得像大师级厨师一样精准,稍微偏差一点,就可能影响到最终的质量。
说白了,这就是把一块块钢材从“粗糙”打磨到“细腻”,让它在以后承受更大的压力时,不会容易坏掉。
就像你每天吃的苹果,表面看着挺好,但切开一看,内部有点斑点或者不均匀,那吃着可就不舒服了。
同理,钢材的均质化,能有效减少内部缺陷,增强钢材的强度和抗疲劳能力,这对于做轴承的钢材尤为重要。
不得不说,绿色高效连铸和均质化技术的结合真是让轴承钢的质量提升了不止一个档次。
轴承钢连铸技术
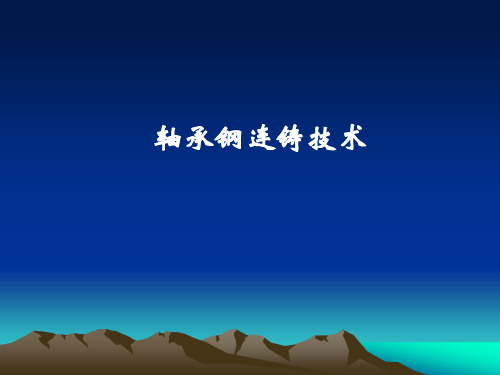
速,将二冷配水量控制在0.25-0.31 L/kg。
3.5 保护浇铸
• 是防止二次氧化所必备的条件。四个环节:钢包至中间包 的钢流、中间包的内钢液面、中间包至结晶器钢流、结晶 器内钢液面;
钢包至中间包采用长水口,氩气保护
内空部 熔钢流耐磨 性 身体部 耐热冲击性
熔渣,侵入部 长时间耐侵 蚀性
中间包耐火材料多采用碱性涂层(或碱性绝 热板);中间包的钢液面使用特殊碱性覆盖 剂;
致偏析与缩孔主要因素。影响连铸坯低倍质量的连铸工艺 参数中,过热度占主要地位;
• 轴承钢要求尽可能低的过热度、较慢的拉速下浇铸才能得
到偏析小、组织均匀而致密的钢坯。
精炼终点温度计算
• T精炼终点=T液+ΔT钢包-中间包+ΔT+k(t1+t2)
k值与钢包容量、耐火材料的导热性和加热周转情况密
切相关,使钢包于热平衡状态取得的值。
轴承钢连铸技术
内容:
1 :轴承钢概述
2 :影响轴承钢质量的关键成分和夹杂物及其 控制 3:轴承钢的连铸
一、概述
轴承是“工业的心脏”。 轴承钢是重要的冶金产品,它被广泛应用于机械制造、铁路运 输、汽车制造、国防工业等领域。轴承钢是特钢产品中生产难 度较大的钢类之一。 2009年和2010年我国轴承钢产量分别为 350万吨和358万吨,占当年特钢产量的7.8%和7.6%。 轴承钢总产量连续6年列为世界第一,高等级轴承钢仅占1/5; 高质量轴承钢仅占34%;多数为高碳含铬轴承钢、中碳轴承 钢和渗碳表面硬化轴承钢,而不锈耐蚀、高温难溶及防磁类型 的轴承钢比例在3.8%以下(约13~15万吨)。
• 高的接触疲劳强度,保证轴承的正常使用寿命;
• 高的弹性极限和一定的冲击韧性,承受高的负荷而不变 形,承受一定的冲击负荷;
- 1、下载文档前请自行甄别文档内容的完整性,平台不提供额外的编辑、内容补充、找答案等附加服务。
- 2、"仅部分预览"的文档,不可在线预览部分如存在完整性等问题,可反馈申请退款(可完整预览的文档不适用该条件!)。
- 3、如文档侵犯您的权益,请联系客服反馈,我们会尽快为您处理(人工客服工作时间:9:00-18:30)。
低2.5×10-4%;
• 瑞典SKF公司Ovako厂于1991年投入的新车间沿用模铸生 产轴承钢,美国Timken公司没有采用连铸。1991年和
1997年在ASTM举办的轴承钢国际会议,轴承钢连铸仍然
是一个有争议的课题;
• 到目前为止,没有一片文章报道,彻底解决了轴承钢连铸 坯的中心碳偏析问题; • 轴承钢的连铸工艺一般应包括:钢包和中间包烘烤、下渣
在几种力的综合作用下,在套圈或滚动体的表面上抗疲
劳强度低的部位首先产生疲劳裂纹,最后形成疲劳剥落, 使轴承破损失效。轴承钢正常破损的形式是接触疲劳损坏,
其次是摩擦磨损使精度丧失。
非金属夹杂物或粗大碳化物,则可促进裂纹的产生。
轴承钢要求高疲劳寿命
轴承钢性能的要求
• 对化学成分的要求; • 对非金属夹杂物的要求; • 高且均匀的硬度,高的耐磨性;
轴承钢连铸技术
内容:
1 :轴承钢概述
2 :影响轴承钢质量的关键成分和夹杂物及其 控制 3:轴承钢的连铸
一、概述
轴承是“工业的心脏”。 轴承钢是重要的冶金产品,它被广泛应用于机械制造、铁路运 输、汽车制造、国防工业等领域。轴承钢是特钢产品中生产难 度较大的钢类之一。 2009年和2010年我国轴承钢产量分别为 350万吨和358万吨,占当年特钢产量的7.8%和7.6%。 轴承钢总产量连续6年列为世界第一,高等级轴承钢仅占1/5; 高质量轴承钢仅占34%;多数为高碳含铬轴承钢、中碳轴承 钢和渗碳表面硬化轴承钢,而不锈耐蚀、高温难溶及防磁类型 的轴承钢比例在3.8%以下(约13~15万吨)。
• 较少或消除铸坯内裂和偏析裂,Mn/S≥30,钢液残铝量 0.01%-0.015%——堵水口,减少Al2O3
3.2 温度控制
• 冷却强度比模铸大,凝固界面的温度梯度高,柱状晶发达, 树枝晶相遇,产生“搭桥”现象。因此,连铸坯心部产生 周期性断续的缩孔与偏析;
• 铸坯凝固时柱状晶发达因素中,过热度、二冷强度等是导
中间包至结晶器使用浸入式水口
•结晶器内钢液面采用适应低过热度和低拉速浇铸的保护渣。
3.6 连铸电磁搅拌
• 电磁搅拌对改善轴承钢的连铸坯质量有重要作用——高温 区和低温区充分混合,加快过热度的导出,并折断树枝晶, 增加结晶核心及等轴晶数量,有效地控制树枝晶“搭桥”
想象,改善铸坯中心碳偏析、中心疏松、缩孔等缺陷。
浇注过程中夹杂物的控制
• 模铸——重点放在避免钢包和锭模之间钢水流的二次氧化; 最大限度地避免钢水和耐材的作用;最大限度地避免钢包 渣、保温剂或浇注保温渣的卷入;
• 连铸——检测钢包中的下渣量;吹氩保护,防二次氧化;
选用优质的耐材。
2.3 轴承钢中残余铝的控制
• 金属铝及AlN溶于酸,用[Al]S表示。终脱氧用Al是获得低 氧含量的钢液和保证钢中有合适[Al]S。[Al]S高——保护条 件不好易二次氧化增加Al 2 O3 夹杂;[Al] S 低——Si的二次
比真空前少1/3;
• SKF研究发现:出钢后15min夹杂主要由Al2O3和 Al2O3· 2· SiO MnO组成,来自电弧炉出钢的预脱氧产物;真空
前——Al2O3· CaO夹杂,是Al2O3和铁合金Ca-Si中的钙的反应
产物;真空后——夹杂中的Al2O3· CaO往往包着一层MgS, Mg来自真空下的耐材,并与Al2O3生成Al2O3· MgO。
高碳轴承钢的特点
• 高碳 • 加铬 • 加入Mo、Mn、Si、V等合金
• 严格控制杂质元素,特别是P、S、Ni、Cu
危害最大的是氧化物夹杂,其次是硅酸盐。氧化物夹 杂的最大粒径和粒子个数是轴承钢疲劳寿命的根本原因— —轴承钢冶炼和浇铸的关键在于控制钢中氧含量到极限值、
提高纯净度和组织的均匀性,即降低钢中氧及非金属夹杂
• 大冶经验:小方坯生产特殊钢,尤其是轴承钢,为质量问
题根源。压缩比小,钢材致密度不够,宏观组织满足不了 要求;压缩比小,碳化物偏析得不到改善。
• 高碳铬轴承钢连铸坯:180mm×180mm、200mm×200mm、 210mm×240mm,轧制成直径≤55mm圆钢,可满足我国现 行轴承钢的要求,压缩比为14-21,压缩比不得小于14。
速,将二冷配水量控制在0.25-0.31 L/kg。
3.5 保护浇铸
• 是防止二次氧化所必备的条件。四个环节:钢包至中间包 的钢流、中间包的内钢液面、中间包至结晶器钢流、结晶 器内钢液面;
钢包至中间包采用长水口,氩气保护
内空部 熔钢流耐磨 性 身体部 耐热冲击性
熔渣,侵入部 长时间耐侵 蚀性
中间包耐火材料多采用碱性涂层(或碱性绝 热板);中间包的钢液面使用特殊碱性覆盖 剂;
滚动轴承一般由内圈、外圈、滚动体和保持架组成。
内圈:与轴颈相配(一般转动) 外圈:与轴承座相配(一般静止) 滚动体:将滑动摩擦转化为滚动摩擦 保持架:防止滚动体直接接触
2 2
4
1
4
1
3
3
除保持架外,其余都是由轴承钢制成。
常见的滚动体有六种形状,一种是球形,五种是滚子。
当轴承工作时,轴承内外套圈、滚动体间承受高频率、 变应力作用。在轴承旋转时,还承受离心力的作用,并随 转速的增加而增大;滚动体与套圈间不仅存在滚动,而且 还有滑动,所以在滚动体与套圈之间还存在摩擦。
监测、留钢及中间包钢水加热,全程无氧化保护浇注,结
晶器页面自动控制,结晶器小振幅高频率振动,结晶器二 冷末端电磁搅拌,轻压下技术。
• • • • • • •
钢液准备 温度控制 连铸机的选择 拉速和二冷的控制 保护浇铸 连铸电磁搅拌 连铸轴承钢的碳化物特性及其均匀化技 术 • 铸坯断面、压缩比及轻压下 • 连铸坯的质量
物含量,控制好夹杂物形态和分布。核心——高纯净度钢 的生产。
二、影响轴承钢质量的关键成分和 夹杂物及其控制
• 氧对轴承钢质量的影响及其控制 • 轴承钢中的夹杂物及其控制 • 轴承钢中残余铝的控制 • 轴承钢中残余钛的控制 • 硫含量 • 钢中碳化物缺陷
2.1 氧对轴承钢质量的影响及其控制
钢中wT.O=10×10-4%轴承钢的疲劳寿命比wT.O=40×104%提高10倍。w =5×10-4%的疲劳寿命比wT.O=40×10-4% T.O
利于多炉连浇。
• 二冷水量过大——铸坯表面温度低,横断面上温度梯度大, 利于柱状晶生长,柱状晶区就宽;
• 二冷水量过小——可使柱状晶区宽度减少,等轴晶区扩 大,但刚的凝固系数下降,液相穴增长,对于改善轴心 碳偏析不利;
• 使用0.15-0.20 Mpa的压缩空气,实现气-雾冷却工艺,二
冷水量很小,配合低拉速保证铸坯温度大于900℃。拉速 一般控制在0.3-0.8m/min,并根据铸坯的断面尺寸调整拉
3.7 连铸轴承钢的碳化物特性及其均匀 化技术
• 为改善碳化物,一般在连铸浇铸和铸坯的加热过程中,采 用净化钢水、中间包钢水低过热度浇铸、低拉速和合适的 二冷强度、合理的结晶器和二冷末端的电磁搅拌组合使用、
轻压下技术和合理的连铸坯加热技术。
3.8 铸坯断面、压缩比及轻压下
• 压缩比与某些质量指标发生关系,如低倍组织、碳化物不 均匀性; • 连铸坯钢材的压缩比小于钢锭成材——连铸轴承钢碳化物
提高30倍。轴承钢生产的关键在于脱氧。
全氧含量与轴承疲劳寿命的关系
冶炼过程中应注意的问题
• 初炼钢液实现低氧化和低温化; • 强化初炼钢水的预脱氧; • 采用SiC和Al粉进行扩散脱氧;
• 精炼中期,钢中氧含量降低,Al也随之降低,采用喂
Al线的方法添加Al;
• 选择合适的精炼渣系; • 防止二次氧化; • 合理的吹氩制度;
钢中硫化物夹杂对轴承钢质量的影响
• 有益 • 有害 • 对钢的疲劳寿命影响不大
工艺参数对钢中夹杂物含量的影响
• 电炉出钢温度 • 搅拌时间 • 铝脱氧工艺
Ascometal公司认为,对于轴承钢的精炼,应把重点
放在:选择碱性耐材钢包内衬;最大限度地去除炉渣; 尽早形成非常低氧势的脱氧精炼渣;控制气体搅拌,使 夹杂物上浮。
氧化及钢液随温度降低溶解氧析出,产生含SiO2很高的粗
大玻璃质硅酸盐夹杂。如果要使钢材晶粒细化,获得高强 韧性,残余铝可高些。对渗碳轴承钢来说,残余铝需要控
制得高些;对于高碳轴承钢对此控制要求不太高。
特殊钢中典型 的球状不变形 钙铝镁酸盐夹 杂物形貌
2.4 轴承钢中残余钛的控制
• 钛对于高碳铬轴承钢有害,在钢中以Ti(C,N)、TiC、TiN 存在呈坚硬的菱角。在相同尺寸下,危害大于Al2O3; • 实践证明,wTi超过50×10-4%,轴承疲劳寿命明显下降。
致偏析与缩孔主要因素。影响连铸坯低倍质量的连铸工艺 参数中,过热度占主要地位;
• 轴承钢要求尽可能低的过热度、较慢的拉速下浇铸才能得
到偏析小、组织均匀而致密的钢坯。
精炼终点温度计算
• T精炼终点=T液+ΔT钢包-中间包+ΔT+k(t1+t2)
k值与钢包容量、耐火材料的导热性和加热周转情况密
切相关,使钢包处于热平衡状态取得的值。
• 控制适当的残铝量;
• 确保足够的真空度和真空时间。
2.2 轴承钢中的夹杂物及其控制
• 钢中非金属夹杂物数量和组分的变化 • 钢中硫化物夹杂对轴承钢质量的影响 • 工艺参数对钢中夹杂物含量的影响 • 浇注过程中夹杂物的控制
夹杂物造成的滚动面疲劳破坏
钢中非金属夹杂物数量和组分的变化
• 钢中大于5μm的夹杂物在真空后大部分被去除。夹杂物数量
2.6 钢中碳化物缺陷
• 碳化物缺陷包括液析碳化物、带状碳化物和网状碳化物, 其危害相当于夹杂物; • 碳化物缺陷主要起源于钢在凝固过程中的偏析,控制和减
少凝固偏析是控制和减少碳化物缺陷的关键环节;