夹具的对刀教学教材
夹具在机床上的对刀

第二章 夹具在机床上的定位、对刀和分度
§2-2 夹具在机床上的对刀
一、铣床夹具的对刀
常 见 的 对 刀 装 置
第24次课
教学课型:理论课
机床夹具设计
第二章 夹具在机床上的定位、对刀和分度
§2-2 夹具在机床上的对刀
一、铣床夹具的对刀
制造夹具时,
b 、 h1 已保证,
故只需调整 δ即 可。
第24次课
第24次课
教学课型:理论课
机床夹具设计
第二章 夹具在机床上的定位、对刀和分度
§2-2 夹具在机床上的对刀
二、钻床夹具中刀具的对准和导引
钻套的形式
钻套导引孔尺寸及公差的确定原则
钻套高度和钻套与工件的距离
钻床夹具钻套位置尺寸的标注
影响对刀精度的因素
第24次课
教学课型:理论课
机床夹具设计
第二章 夹具在机床上的定位、对刀和分度
§2-2 夹具在机床上的对刀
二、钻床夹具中刀具的对准和导引 3.钻套高度和钻套与工件的距离
定位元件定位面相对于对刀装置的位置误差:要正 确确定对刀块对刀表面的位置尺寸及公差,并以定 位元件定位面为基准标注,避免基准转换。
第24次课
教学课型:理论课
机床夹具设计
第二章 夹具在机床上的定位、对刀和分度
§2-2 夹具在机床上的对刀
一、铣床夹具的对刀
第24次课
教学课型:理论课
机床夹具设计
第二章 夹具在机床上的定位、对刀和分度
§2-2 夹具在机床上的对刀
二、钻床夹具中刀具的对准和导引 1.钻套的形式
固定钻套 可换钻套 ↗ 钻 套 ↘ 快换钻套
特殊钻套
第24次课
教学课型:理论课
数控工艺第五章第二节数控车削加工件的装夹及对刀

( 2 ) 尺寸标注方法分析 零件图上尺寸标注方法应适应数控车床加工的特点,应以同 一基准标注尺寸或直接给出坐标尺寸。这种标注方法既便于编程,
又有利于设计基准、工艺基准、测量基准和编程原点的统一。
( 3 ) 精度及技术要求分析 对被加工零件的精度及技术要求进行分析是零件工艺性分析
的重要内容,只有在分析零件尺寸精度和表面粗糙度的基础上,
一般来说,编程原点的确定原则为: ( l ) 将编程原点选在设计基准上并以设计基准为定位基准,这样可避免 基准不重合而产生的误差及不必要的尺寸换算。如图5-33 所示零件,批量 生产,编程原点选在左端面上。 ( 2 ) 容易找正对刀,对刀误差小。如图5-33 ,若单件生产,G92 建立工 件坐标系,选零件的右端面为编程原点,可通过试切直接确定编程原点在z 向的位置,不用测量,找正对刀比较容易,对刀误差小。
的坐标值就是指刀位点的坐标值;自动编程时程序输出的
坐标值就是刀位点在每一有序位置的坐标数据,刀具轨迹 就是由一系列有序的刀位点的位置点和连接这些位置点的 直线(直线插补)或圆弧(圆弧插补)组成的。
( 2 ) 起刀点它是刀具相对零件运动的起点,即零件
加工程度开始时刀位点的起始位置,而且往往还是程序 运行的终点。有时也指一段循环程序的起点。
编程原点安装后的位置采用其他方法对刀确定。
5.3 数控车削加工工艺制定
工艺分析是数控车削加工的前期工艺准备工作。 工艺制定得合理与否,对程序编制、机床的加工效率 和零件的加工精度都有重要影响。因此,应遵循一般 的工艺原则并结合数控车床的特点,认真而详细的制
定好零件的数控车削加工工艺。其主要内容有:分析
零件图纸、确定工件在车床上的装夹方式、各表面的 加工顺序和刀具的进线路线以及刀具、夹具和切削用 时的选择等。
夹具第4章对刀分度(2006)
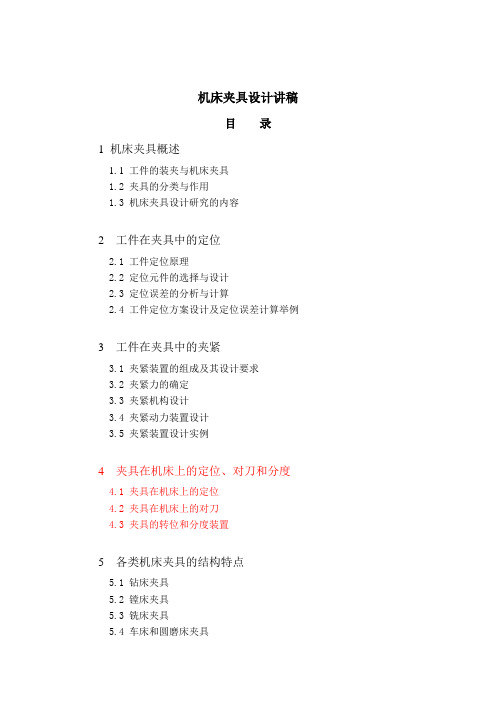
机床夹具设计讲稿目录1 机床夹具概述1.1 工件的装夹与机床夹具1.2 夹具的分类与作用1.3 机床夹具设计研究的内容2 工件在夹具中的定位2.1 工件定位原理2.2 定位元件的选择与设计2.3 定位误差的分析与计算2.4 工件定位方案设计及定位误差计算举例3 工件在夹具中的夹紧3.1 夹紧装置的组成及其设计要求3.2 夹紧力的确定3.3 夹紧机构设计3.4 夹紧动力装置设计3.5 夹紧装置设计实例4 夹具在机床上的定位、对刀和分度4.1 夹具在机床上的定位4.2 夹具在机床上的对刀4.3 夹具的转位和分度装置5 各类机床夹具的结构特点5.1 钻床夹具5.2 镗床夹具5.3 铣床夹具5.4 车床和圆磨床夹具5.5 齿轮加工机床夹具6 可调夹具及组合夹具设计6.1 概述6.2 通用可调夹具和成组夹具6.3 组合夹具7 机床夹具的设计方法及步骤7.1 机床夹具设计的一般步骤7.2 机床夹具设计举例7.3 机床夹具计算机辅助设计简介7.4 夹具体的设计7.5 夹具结构的工艺性4 夹具在机床上的定位、对刀和分度4.1 夹具在机床上的定位4.1.1 夹具在机床上定位的目的能否保证工件的加工要求,取决于工件与刀具间的相互位置,而引起此位置产生误差的因素有四方面:第一是工件在夹具中因位置不一致而引起的误差,称为定位误差,用ΔD 表示。
第二是定位元件和机床上安装夹具的装夹面之间的位置不准确所引起的误差,以ΔA 表示。
第三是定位元件与对刀或导向元件之间的位置不准确引起的误差,以Δr 表示,这两项误差与夹具在机床上的安装和对刀调整有关,统称调安误差,以Δr-A 表示。
第四是由于机床运动精度以及工艺系统的变形等因素引起的误差,称为加工方法误差,以ΔG 表示。
为了保证工件的加工要求,上述四方面误差合成后应不超出工件的加工公差 T K 的范围,即在初步确定工件的定位方案时,可以先假设上述三项误差各占工件公差的 1/3 ,最后可根据实际情况进行调整。
机械加工的对刀方法课件

(5)检验 检验对刀是否正确,这一步是 非常关键的。
2.塞尺、标准芯棒、块规对刀法 此法与试切对刀法相似,只是 对刀时主轴不转动,在刀具和工件 之间加入塞尺(或标准芯棒、块规), 以塞尺恰好不能自由抽动为准,注 意计算坐标时这样应将塞尺的厚度 减去。因为主轴不需要转动切削, 这种方法不会在工件表面留下痕迹, 但对刀精度也不够高。
坐标系中的Z值,如-140.400等, 则工件坐标系原点W在机床坐标系中 的Z坐标值为-140.400。 (3)数据存储 将测得的X、Y、Z值输入到机床 工件坐标系存储地址G5*中(一般使用 G54~G59代码存储对刀参数)。 (4)起动生效 进入面板输入模式(MDI),输入 “G5*”,按起动键(在“自动”模式下), 运行G5*使其生效。
◎在手轮模式下,利用手摇移动 工作台至适合位置,向下移动主轴, 用刀的底端压对刀器的顶部,表盘指 针转动,最好在一圈以内,记下此时 Z轴设定器的示数A并将相对坐标 Z轴清零。 ◎抬高主轴,取下第一把刀。 (2)对第二把刀 ◎装上第二把刀。
◎在手轮模式下,向下移动主 轴,用刀的底端压对刀器的顶部,表 盘指针转动,指针指向与第一把刀相 同的示数A位置。 ◎记录此时Z轴相对坐标对应的数值 Z0(带正负号)。 ◎抬高主轴,移走对刀器。 ◎将原来第一把刀的G5*里的Z1坐标 数据加上Z0(带正负号),得到一个新 的Z坐标
件左侧,使刀具恰好接触到工件左侧 表面(观察,听切削声音、看切痕、看 切屑,只要出现其中一种情况即表示 刀具接触到工件),再回退0.01mm 。记下此时机床坐标系中显示的X坐 标值,如-240.500等。 ◎沿Z正方向退刀,至工件表面以上, 用同样方法接近工件右侧,记下此时 机床坐标系中显示的X坐标值,如 -340.500等。
夹具第4章对刀分度(2006)资料

机床夹具设计讲稿目录1 机床夹具概述1.1 工件的装夹与机床夹具1.2 夹具的分类与作用1.3 机床夹具设计研究的内容2 工件在夹具中的定位2.1 工件定位原理2.2 定位元件的选择与设计2.3 定位误差的分析与计算2.4 工件定位方案设计及定位误差计算举例3 工件在夹具中的夹紧3.1 夹紧装置的组成及其设计要求3.2 夹紧力的确定3.3 夹紧机构设计3.4 夹紧动力装置设计3.5 夹紧装置设计实例4 夹具在机床上的定位、对刀和分度4.1 夹具在机床上的定位4.2 夹具在机床上的对刀4.3 夹具的转位和分度装置5 各类机床夹具的结构特点5.1 钻床夹具5.2 镗床夹具5.3 铣床夹具5.4 车床和圆磨床夹具5.5 齿轮加工机床夹具6 可调夹具及组合夹具设计6.1 概述6.2 通用可调夹具和成组夹具6.3 组合夹具7 机床夹具的设计方法及步骤7.1 机床夹具设计的一般步骤7.2 机床夹具设计举例7.3 机床夹具计算机辅助设计简介7.4 夹具体的设计7.5 夹具结构的工艺性4 夹具在机床上的定位、对刀和分度4.1 夹具在机床上的定位4.1.1 夹具在机床上定位的目的能否保证工件的加工要求,取决于工件与刀具间的相互位置,而引起此位置产生误差的因素有四方面:第一是工件在夹具中因位置不一致而引起的误差,称为定位误差,用ΔD 表示。
第二是定位元件和机床上安装夹具的装夹面之间的位置不准确所引起的误差,以ΔA 表示。
第三是定位元件与对刀或导向元件之间的位置不准确引起的误差,以Δr 表示,这两项误差与夹具在机床上的安装和对刀调整有关,统称调安误差,以Δr-A 表示。
第四是由于机床运动精度以及工艺系统的变形等因素引起的误差,称为加工方法误差,以ΔG 表示。
为了保证工件的加工要求,上述四方面误差合成后应不超出工件的加工公差 T K 的范围,即在初步确定工件的定位方案时,可以先假设上述三项误差各占工件公差的 1/3 ,最后可根据实际情况进行调整。
第四章 夹具在机床上的定位

一、夹具在在机床上定位的目的
二、夹具在机床上的定位方式
(一)夹具在工作台面上的连接定位
定向、定位键
U形槽结构
(二)夹具在机床主轴上的连接
(a)主轴锥孔连接 (b)端面B和圆柱孔D (c)短锥面K和端面B (d)过渡盘以锥孔 定位
三、夹具在机床上的定位误差
(一)车床夹具的定位误差
1.心轴: 同轴度误差 2.专用夹具:
(二)铣床夹具的定位误差
(三)钻床夹具的定位误差
四、提高夹具在机床上定位的措施
(一)对夹具进行找整安装 (二)对定位元件定位面进行就地加工
对于铰孔、镗孔、绗孔、拉孔刀具进行浮动连接
§4-2夹
(五)影响对刀精度的因素
§4-3夹具的转位和分度装置
一、分度装置的基本形式
1.轴向分度装置
2.径向分度装置
二、分度装置的对定机构
分度误差
三、分度装置的拔销及锁紧装置
四、精密分度装置
一夹具在在机床上定位的目的第四章夹具在机床上的定位对刀和分度41夹具在机床上的定位二夹具在机床上的定位方式一夹具在工作台面上的连接定位定向定位键u形槽结构二夹具在机床主轴上的连接a主轴锥孔连接b端面b和圆柱孔dc短锥面k和端面b定位三夹具在机床上的定位误差一车床夹具的定位误差1
第四章 夹具在机床上的定位、对刀和分度
1.测量误差 2.定位元件定位面相对对刀装置的位置误差
二、钻床夹具中刀具的对准和导向 (一)钻套的四种形式 1.固定钻套 2.可换钻套 3.快换钻套
4.特殊钻套
(二)钻套引导尺寸和公差的确定
(三)钻套高度和钻套与工件距离
1.钻套高度 钻一般非配合孔,H=(1.5~2)d,钻套内径采用基轴制F8 的公差。 加工IT6、IT7级精度,孔在Ф 12mm以上或加工孔距精度要求在 ±0.10~ ±0.15mm时,H=(2.5~3.5)d。 加工IT7、IT8级精度的孔,孔距精度要求在±0.0.06~ ±0.10mm时 H=(1.25~1.5)(h+B)。 2.钻套与工件的距离
夹具在机床上的对刀

1.钻套的形式
机床夹具设计
⑵可换钻套
可换钻套:凸缘铣有台肩用螺钉固定,以防钻套转动。 为避免钻模板的磨损,中间加衬套。
特 点:磨损后可更换,但精度不如固 定钻套。
应 用:比较广泛。
配 合:钻套与衬套为H7/g6、H6/g5, 衬套与钻模板为H7/n6、H7/r6。
机床夹具设计
1.钻套的形式
⑶快换钻套
机床夹具设计
二、钻床夹具中刀具的对准和导引
钻床夹具一 般用钻套对刀。 加工中,只要 钻头对准钻套, 所钻孔的位置 即能达到工序 要求。并且钻 套还能增强刀 具的刚度。
机床夹具设计
❖钻套的形式 ❖钻套导引孔尺寸及公差的确定原则 ❖钻套高度和钻套与工件的距离 ❖钻床夹具钻套位置尺寸的标注 ❖影响对刀精度的因素
当孔精度要求不高、孔距精度为±0.25或自由公差 时,取H=(1.5~2)d; 当 孔 精 度 为 IT6 、 IT7 、 孔 径 >φ12 或 孔 距 精 度 为 ±0.10~±0.15时,取H=(2.5~3.5)d; 当孔精度为IT7、IT8、孔距精度为±0.06~±0.10时, 取H=(1.25~1.5)(h+B)。
二、钻床夹具中刀具的对准和导引 5.影响对刀精度的因素
TL夹:钻模板底孔轴线到定位零件表面距离L夹的公
差;
影响因素 Δ1、Δ2:钻头与钻套、钻套与衬套的最大配合间隙;
e1、e2:钻套、衬套内外圆的同轴度;
E:钻头末端偏斜量。E=Δ1·(B+h+H/2)/H。
5.影响对刀精度的因素
机床夹具设计
利用样件或对 切一些工件,而每次安装使用夹具时,
刀装置对刀: 不需再试切,故最为方便。
一、铣床夹具的对刀
夹具第4章对刀分度
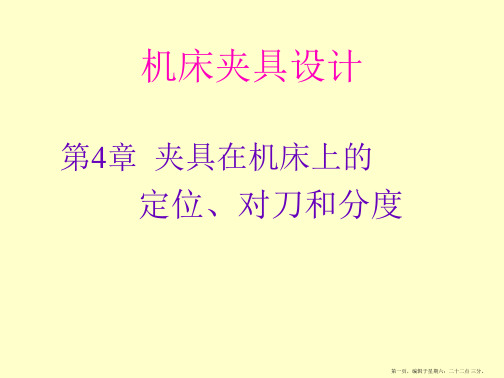
上图为铣键槽在机床上的定位简图;
要求保证键槽在垂直平面及水平平面与工件轴线平行;
1)保证V形块中心线与刀具的运动平行; 2)在垂直平面内的平行度是靠与机床工作台的良好接触完成的; 3)在水平平面内的平行度是靠两个定向键、T形槽来完成的;
第三页,编辑于星期六:二十二点 三分。
所以,夹具在机床上的定位,其本质是夹具
定位元件对刀具切削成形运动的定位。为此,就
要解决好夹具与机床的连接与配合问题以及正确 规定定位元件定位面对即将安装面的要求。
保证夹具的定位表面相对于机床工作台 和导轨或主轴轴线具有正确的位置关系。
第四页,编辑于星期六:二十二点 三分。
4.1.2 夹具在机床上的定位方式
别对铣床夹具和钻床夹具在机床上的对 刀进行分析。
第四十五页,编辑于星期六:二十二点 三分。
• 4.2.1 铣床夹具的对刀 对刀的方法通常由三种:
一种方法为单件试切;
第二种方法是每加工一批工件,即安 装调整一次具,通过试切数个工件来对 刀;
第三种方法是用样件或对刀装置对刀, 这时只是在制造样件或调整对刀装置时, 才需要试切一些工件,而在每次安装使用 夹具时,不需再试切工件,这是最方便的 方法。
△jw对=0.1+0.021=0.121
第三十二页,编辑于星期六:二十二点 三分。
• 铣床夹具的安装误差: • 表现为夹具本体底面和定向键侧面与机床工
作台平面及T形槽间的位置变动量。 • 铣床夹具上采用对刀装置对刀: • ΔT=δs+δh. • δs:塞尺的制造公差。 • δh:对刀块工作面至定位元件的尺寸公差。
钻夹具的定位误差分析
刀具与钻套最大配合间隙Xmax会引起刀具的偏斜, 导致孔的偏移X2:
铣床夹具的对刀
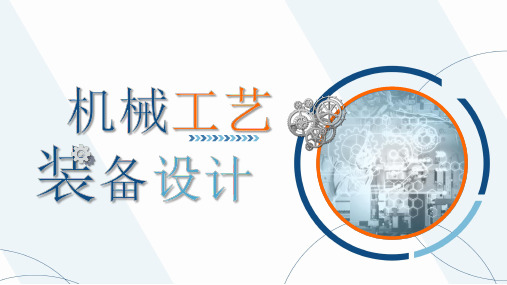
的对刀对刀装置由对刀块和塞尺组成,用来确定夹具和刀具的相对位置。
对刀装置的形式根据加工表面的情况而定,下图为几种常见的对刀块。
这些标准对刀块的结构参数均可从有关手册中查取。
对刀调整工作通过塞尺(平面型或圆柱型)进行,这样可以避免损坏刀具和对刀块的工作表面。
塞尺的厚度或直径一般为3~5mm,按国家标准h6的公差制造,在夹具总图上应注明塞尺的尺寸。
采用标准对刀块和塞尺进行对刀调整时,加工精度不超过 IT8 级公差。
当对刀调整要求较高或不便于设置对刀块时,可以采用试切法;标准件对刀法;或用百分表来校正定位元件相对于刀具的位置,而不设置对刀装置。
(1)材料:20钢,按GB/T699-1999的规定。
(2)热处理:渗碳深度 0.8~1.2mm,58~64HRC。
(3)其他技术要求条件按GB/T2259的规定。
标记示例D=25mm的圆形:对刀块25 GB/T2240。
D H h d d116106 5.510257 6.612(1)材料:20钢按GB/T699-1999的规定。
(2)热处理:渗碳深度 0.8~1.2mm,58~64HRC。
(3)其他技术要求条件按GB/T2259的规定。
标记示例方形对刀块:对刀块25 GB/T2241。
直角对刀块 (摘自GB/T2242-1991)(1)材料:20钢按GB/T699-1999的规定。
(2)热处理:渗碳深度0.8~1.2mm,58~64HRC。
(3)其他技术要求条件按GB/T2259的规定。
标记示例直角对刀块:对刀块20GB/T2242。
侧装对刀块(摘自GB/T2243-1991)(1)材料:20钢按GB/T699--1999的规定。
(2)热处理:渗碳深度0.8~1.2mm,58~64HRC。
(3)其他技术要求条件按GB/T2259的规定。
标记示例侧装对刀块:对刀块25 GB/T2243夹具在机床上安装完毕,在进行加工之前,尚需进行夹具的对刀,使刀具相对夹具定位元件处于正确位置。
第四章 夹具在机床上的定位、对刀、分度

第 四 章 夹 具 在 机 床 上 的 定 位 、 对 刀 、 分 度
b)图中夹具以端面B和圆柱孔D在主轴上定位。靠螺纹M连 接紧固,靠两只压板2防松。制造简单,定位精度低。 d)图中夹具为过渡盘,适用于尺寸较大的夹具。1是过渡 盘,2是键,3是缩紧螺母。工件以端面和圆柱面实现定位。
第 四 章 夹 具 在 机 床 上 的 定 位 、 对 刀 、 分 度
第 四 章 夹 具 在 机 床 上 的 定 位 、 对 刀 、 分 度
2)孔的位置精度要求高时,可取h=0,以保证钻套有较好 的导引作用,而让切屑从钻头的螺旋槽中排出,这样,排屑 条件反比只留很小h值的要好,但此时钻套磨损严重。 3)钻深孔(B/d>5)时,要求排屑畅快,可取h=1.5d。 此外,各种钻套内孔和外圆的同轴度不应大于O.005mm。
第 四 章 夹 具 在 机 床 上 的 定 位 、 对 刀 、 分 度
(二) 钻套导引孔尺寸和公差的确定: 在选用标准结构的钻套时,钻套导引孔的尺寸与公差需 由设计者按下述原则确定: 1 钻套导引孔直径的基本尺寸,应等于所导引刀具的最大 极限尺寸,以防止卡住和咬死。 2 钻套导引孔与刀具的配合,应按基轴制选择,这是因为 刀具的结构和尺寸均已标准化。 3 钻套导引孔与刀具之间应保证有一定的配合间隙,以防 卡死。导引孔的工差带根据所导引刀具的种类和加工精度要 求选定,钻孔和扩孔选F7、F8;粗铰时选G7;精铰时选G6。 4 当采用标准铰刀铰H7或H9孔时,导引孔的基本尺寸与加 工孔的基本尺寸相同,公差选用F7或E7。
第 四 章 夹 具 在 机 床 上 的 定 位 、 对 刀 、 分 度
圆柱定向键 耐磨损
图示圆柱定向键的结构,上半圆柱体与夹具体的圆孔相 配合,下半圆柱体加工出与T型槽宽度相等的两平面,这样可 以改善上图中圆柱定向键易磨损的缺点。 图b)、c)为圆柱定向键的固定方式。
7.5-夹具的连接元件、对刀装置和引导元件PPT课件
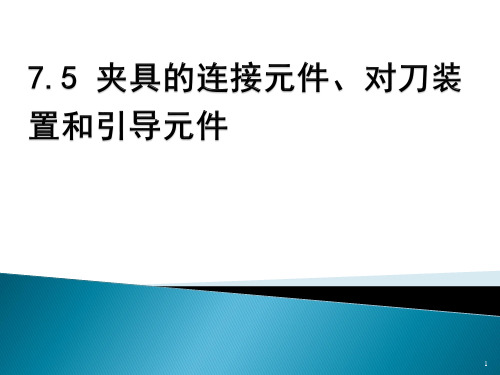
通常取 H=1~2.5d (d为被加工孔径); 当加工精度较高或加工的孔径较小时,可以 H=2.5~3.5d。
18
1.钻床夹具的刀具引导元件—钻套
设计钻套时,应注意以下几个方面的问题: 4) 钻套与工件间的排屑空间 h
① 加工铸铁时、黄铜时: h=(0.3~0.7)d; ② 加工钢件时:h=(0.7~1.5)d。
1
1. 夹具在机床工作台面上的连接定位
(1)铣床夹具
铣床夹具是如何实现它在机床上的定位的呢?
2
1. 夹具在机床工作台面上的连接定位
(1)铣床夹具
定向键
3
1. 夹具在机床工作台面上的连接定位
(1)铣床夹具
H7/h6、H8/h8
定向键的结构
4
1. 夹具在机床工作台面上的连接定位
(1)铣床夹具
U型槽耳座结构形式
设计钻套时,应注意以下几个方面的问题: 2)标准的定尺寸刀具(麻花钻、扩孔钻、铰刀)设 计时:
①钻套导向孔与刀具的配合应按基轴制选取; ②钻套导向孔与刀具之间,应保证一定的配合 间隙。 如:钻孔和扩孔时,钻套导向孔公差可选F7或F8;
铰孔时,粗铰可选G7,精铰可选G6;
17
1.钻床夹具的刀具引导元件—钻套
特殊情况: 斜面钻孔,h=0.3d; 位置精度较高,h=0; 钻深孔,h=1.5d。
19
2.镗床夹具的刀具引导元件—镗套
(1)回转式镗套
适用于镗杆速度高
于20m/min时的镗孔。
a-内滚式镗套 b-外滚式镗套
1、6-导向支架 2、5-镗套 3-导向滑套 4-镗杆
20
2.镗床夹具的刀具引导元件—镗套
对刀教案
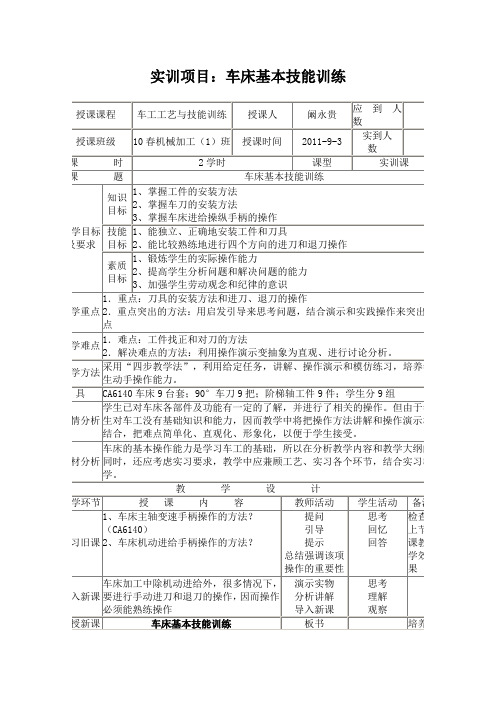
车床的基本操作能力是学习车工的基础,所以在分析教学内容和教学大纲的同时,还应考虑实习要求,教学中应兼顾工艺、实习各个环节,结合实习教学。
教 学 设 计
教学环节
授 课 内 容
教师活动
学生活动
备注
复习旧课
1、车床主轴变速手柄操作的方法?(CA6140)
2、车床机动进给手柄操作的方法?
提问
引导
提示
实训项目:车床基本技能训练
授课课程
车工工艺与技能训练
授课人
阚永贵
应到人数
授课班级
10春机械加工(1)班
授课时间
2011-9-3
实到人数
课 时
2学时
课型
实训课
课 题
车床基本技能训练
教学目标及要求
知识目标
1、掌握工件的安装方法
2、掌握车刀的安装方法
3、掌握车床进给操纵手柄的操作
技能目标
1、能独立、正确地安装工件和刀具
总结强调该项操作的重要性
思考
回忆
回答
检查上节课教学效果
导入新课
车床加工中除机动进给外,很多情况下,要进行手动进刀和退刀的操作,因而操作必须能熟练操作
演示实物
分析讲解
导入新课
思考
理解
观察
讲授新课
车床基本技能训练
一、工件安装
1、夹具介绍
2、找正
3、操作示范
预紧?找正?夹紧
二、刀具安装
1、刀具选择
2、预装
1、夹具介绍
2、找正
3、操作示范
二、刀具安装
1、刀具选择
2、预装
3、对刀
4、操作示范
三、手动进刀和退刀
03课题3 工件和刀具的装夹及对刀步骤(一)

操作演示
3)其他刀具刀补值得输入
(1)主轴启动
(2)选刀
(3)Z轴刀补输入:对刀、输入刀补
(4)X轴刀补输入:对刀、数额刀补
练习三:
3-1、车床仿真软件中的工件、刀具的装夹
1)机床参数设定:
机床参数:前置刀架、非单步加工关闭车门、换刀速度控制快、夹具装夹速度控制快。
速度控制:加工步长设置为最小。
(7)车削外圆
(8)+ Y向退出刀具
(9)测量直径
(10)输入刀补
1、2#刀刀补:
1)调2#刀至加工位
2)Z轴刀补输入:
用以上方法接近工件端面,接近工件时,改为手摇,逐步接近工件,并放大画面,最后用X1接近工件,直到见到铁屑,Z轴不动移动,刀具+X移出工件。
输入刀补:功能键OFFET SET—软键补正—软键形状—移动光标G002 Z—Z0—测量(显示值即为2#刀Z刀补值。)
第3次课
摘要
授课题目(章、节):课题3工件和刀具的装夹及对刀步骤(一)
授课主要内容及重点难点
1、主要内容:
1)车床仿真软件中机床参数的设定及工件、刀具的装夹
2)数控车床的对刀和刀补值的输入
2、重点:刀补输入
3、难点:对刀过程
内容
复习:
机床的基本操作及练习:
(一).数控车床的系统启动、系统停止和紧急停止
3)X轴刀补输入:
用以上方法接近工件外圆,接近工件时,改为手摇,逐步接近工件,并放大画面,最后用X1接近工件,直到见到铁屑,X轴不动移动,刀具+Z移出工件。
输入刀补:功能键OFFET SET—软键补正—软键形状—移动光标G002 X—X82.898—测量(G002显示值即为2#刀X刀补值。)
- 1、下载文档前请自行甄别文档内容的完整性,平台不提供额外的编辑、内容补充、找答案等附加服务。
- 2、"仅部分预览"的文档,不可在线预览部分如存在完整性等问题,可反馈申请退款(可完整预览的文档不适用该条件!)。
- 3、如文档侵犯您的权益,请联系客服反馈,我们会尽快为您处理(人工客服工作时间:9:00-18:30)。
⑶对刀装置位置尺寸标注示例
例1:如图4.13(a)在工件上铣平面,保证 H-δH ,对 刀装置如图(b),试标注对刀装置位置尺寸。
2020/7/20
解:①对刀基准:为V型块中心线(工件 平均尺寸定位后的中心线)。
②对刀装置的位置尺寸:V型块中心 线到对刀块工作面间的位置尺寸。
③对刀装置位置尺寸 H J ± δH /2确 定:
图4.13(c)
2020/7/20
例2:如图4.14(a)钻孔保证L+δL, 导引装 置如图(b),试标注导引装置位置尺寸。
解:左右方向对刀基准为左支承工作面,对刀尺 寸为左支承工作面到钻套中心线位置尺寸,工序尺 寸 L+δL为直接保证的尺寸,对刀尺寸LJ±δLJ/2确定 方法同上。 2020/7/20
3、对刀误差△jd的计算
⑴对铣床夹具:产生对刀误差的因素 有:δH、 δS 、塞尺测量松紧误差。 若增加首件检验调整,
△jd≈δHJ+δS。
2020/7/20
(2)对钻床夹具:产生对刀误差的因素较 多,见图4.15,主要有:
2020/7/20
δ1——钻模板底孔中心线到定位元件的位置尺寸
e1——快换钻套内、外圆同轴度公差
4.2 夹具的对刀
2020/7/20
对刀的方法通常有三种:试切法;调 整法;用样件或对刀装置对刀。本节主 要讲解用对刀装置对刀。
2020/7/20
1、对刀装置 ⑴对刀装置的组成
①铣床夹具的对刀装置4.9
2020/7/20
2020/7/20
4.10
铣床对刀装置位置一般安排在刀具开始进给一方。
e2——衬套内、外圆同轴度公差
X1——快换钻套与衬套间最大配合间隙
X2——刀具与钻套间最大配合间隙
X3——刀具钻出工件偏斜量,
tgα= X2 /H =
X3
Bh0.5H
→→所以
X3
Байду номын сангаас
=
X H
2
(B+h+0.5H)
其中B、h、H代表的意义见图4.15所示。
2020/7/20
因各项误差不可能同时出现最大,故 对这些随机变量按概率法合成为:
2020/7/20
2020/7/20
4.11
平面塞尺厚度S常用1、3、5mm,(b) 圆柱塞尺d常用3、5mm。塞尺尺寸公差 均为h6
2020/7/20
② 钻床夹具的对刀装置
• 由钻套、衬套 、钻套螺钉组 成,也均已标 准化。称为导 引装置。
2020/7/20
2020/7/20
2020/7/20
⑵特点:对刀方便、迅速,但对准精 度一般比试切法低
2020/7/20
2、对刀装置的尺寸标注
⑴对刀基准:对专用夹具来讲,就是确 定刀具与夹具相对位置的基准,X(Y)向 的对刀基准,一般选X(Y)向与定位基准 重合的定位元件上的要素,即为确定对 刀、导引装置位置的尺寸基准。
2020/7/20
⑵对刀装置的位置尺寸:为X(Y)向对刀 基准到对刀块工作表面或钻套中心线(理 解为钻模板底孔中心线)的位置尺寸,简 称对刀尺寸。对应加工零件上的尺寸为 直接保证的尺寸。
2020/7/20
2.铣槽对刀尺寸标注(s=3mm) ,并 标出元件定位面对夹具定位面 的位置要求。
2020/7/20
3.铣槽(塞尺厚度选3mm)
2020/7/20
4.钻孔钻套位置尺寸标注,并标出 元件定位面对夹具定位面的位置 要求。
2020/7/20
目录 下一节
2020/7/20
1)工序尺寸H-δH为对刀直接保证的尺寸: a)把工序尺寸换算成平均尺寸、对称偏差:
-
H± δH/2
-
b) HJ= H-S (塞尺厚度); δH J=(1/5~1/2)δH,并对称分布:± δHJ/2
2020/7/20
2)若工序尺寸为H1,为加工间接保证: 先解工-序尺寸H1为封闭环的尺寸链:计 算出 H ±δH/2,再按上述步骤计算。
△jd= 12e1 2e2 2x1 2(2x3)2
2020/7/20
4、结论
⑴对刀就是确定刀具与夹具定位元件之间的相对 位置,目的就是把刀具对到工件相应尺寸公差带 的中间位置。
⑵夹具精度 误差不等式: 4.16
精度分析误差不等式:
dw 2jw 2jd2 ≤
2020/7/20
2T 3
对刀尺寸标注: 1.铣槽(塞尺厚度选3mm)