磷化常见问题及解决方法
磷化常见故障分析及处理

故障处理方法常温轻质锌:铁系浸渍磷化无膜①促进剂浓度低。
补加促进剂或磷化浓缩剂。
②FA过低。
补加磷酸或磷化浓缩剂(凡工件未经除锈,FA偏高些为好)。
③杂质积累过多。
更换槽液。
成膜速度慢①FA低。
补加磷酸或磷化浓缩剂,控制FA= 2一3点。
②温度低(<50C)。
稍加温。
若无加热条件,适当提高溶液浓度。
部分泛黄生锈①促进剂浓度低。
补加磷化浓缩剂。
②温度低。
稍升温。
③时间短。
延长时间。
挂白灰①磷化前工件生锈。
尽量缩短工件空停时间,提高工序间进度。
②Fe2+积累过多。
更换槽液。
③沉渣黏附。
减少沉渣,加强清渣。
挂黑灰①FA朴。
加人适量碳酸钠降低FA 。
②温度过高。
降温。
③时间过长。
缩短时间,控制5---15min。
④Cu2+浓度过高。
用废钢铁放人槽中,消耗Cu2+。
常(低)温锌系浸渍磷化磷化膜均匀疏松,耐蚀性差或返锈(红锈或黄锈)①工件锈蚀严重,除锈后表面有残酸。
除锈要彻底,充分中和和水洗。
②工件除锈后空停时间过长。
尽量缩短空停时间。
③表调液失效。
更换表调液。
④TA低,FA高。
补加磷化浓缩剂,升高TA;用中和剂降低FA。
控制酸比(25-40):1 ⑤温度低,时间短。
提高温度,延长时间。
⑥硝酸根浓度低。
多发生在新配槽时,补加适量硝酸。
可以调整磷化浓缩剂中硝酸浓度。
⑦促进剂浓度低。
补加促进剂。
⑧Cl-污染磷化液。
除锈后充分水洗。
⑨磷化膜水洗不干净或烘干前受到酸的污染。
水洗干净,避免磷化膜受到酸污染。
膜层局部呈彩色(用指甲划无划痕)①除油不彻底。
调整或更换脱脂液,提高除油后的水洗质量。
②表调不良。
补加表调剂或更换表调液。
③TA太低和FA偏高。
补加磷化浓缩剂,升高TA;用中和剂降低FA. ④促进剂过量,且分布不均匀。
减少促进剂用量或改每日添加为隔日添加。
⑤温度低。
适当升高温度。
膜层呈均匀蓝紫色①前处理不良。
保证除油除锈干净。
②TA太低或FA偏高。
处理同前。
③促进剂浓度过量。
处理同前。
④槽液杂质太多,老化严重。
钢铁零件磷化缺陷原因分析及解决方案

Cause Analysis and Solution of Phosphating Defect of Iron and Steel Parts WU Wan - ping YAO Dian - min
( China Shipbuilding Industry Corporation N0 . 722 Research Institute , Wuhan Hubei 430079 , China ) 揖Abstract铱In this paper , the main defects existing in film forming on the surface of iron and steel parts during phosphating process are introduced , the occurrence of rust yellowing , greening and hanging white floating ash phenomenon is introduced , the causes of rust yellowing , greening and hanging white floating ash phenomenon are analyzed , and the ideas and methods to prevent and solve this problem are put forward according to the causes of the defects . 揖Key words铱Rusting ; Yellowing ; Greening ; Hanging white floating ash ; Causes of defects ; Solutions
钢铁零件磷化缺陷原因分析及解决方案
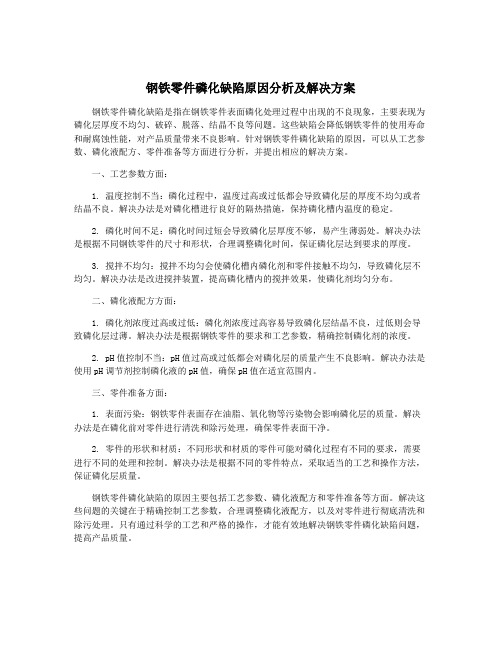
钢铁零件磷化缺陷原因分析及解决方案钢铁零件磷化缺陷是指在钢铁零件表面磷化处理过程中出现的不良现象,主要表现为磷化层厚度不均匀、破碎、脱落、结晶不良等问题。
这些缺陷会降低钢铁零件的使用寿命和耐腐蚀性能,对产品质量带来不良影响。
针对钢铁零件磷化缺陷的原因,可以从工艺参数、磷化液配方、零件准备等方面进行分析,并提出相应的解决方案。
一、工艺参数方面:1. 温度控制不当:磷化过程中,温度过高或过低都会导致磷化层的厚度不均匀或者结晶不良。
解决办法是对磷化槽进行良好的隔热措施,保持磷化槽内温度的稳定。
2. 磷化时间不足:磷化时间过短会导致磷化层厚度不够,易产生薄弱处。
解决办法是根据不同钢铁零件的尺寸和形状,合理调整磷化时间,保证磷化层达到要求的厚度。
3. 搅拌不均匀:搅拌不均匀会使磷化槽内磷化剂和零件接触不均匀,导致磷化层不均匀。
解决办法是改进搅拌装置,提高磷化槽内的搅拌效果,使磷化剂均匀分布。
二、磷化液配方方面:1. 磷化剂浓度过高或过低:磷化剂浓度过高容易导致磷化层结晶不良,过低则会导致磷化层过薄。
解决办法是根据钢铁零件的要求和工艺参数,精确控制磷化剂的浓度。
2. pH值控制不当:pH值过高或过低都会对磷化层的质量产生不良影响。
解决办法是使用pH调节剂控制磷化液的pH值,确保pH值在适宜范围内。
三、零件准备方面:1. 表面污染:钢铁零件表面存在油脂、氧化物等污染物会影响磷化层的质量。
解决办法是在磷化前对零件进行清洗和除污处理,确保零件表面干净。
2. 零件的形状和材质:不同形状和材质的零件可能对磷化过程有不同的要求,需要进行不同的处理和控制。
解决办法是根据不同的零件特点,采取适当的工艺和操作方法,保证磷化层质量。
钢铁零件磷化缺陷的原因主要包括工艺参数、磷化液配方和零件准备等方面。
解决这些问题的关键在于精确控制工艺参数,合理调整磷化液配方,以及对零件进行彻底清洗和除污处理。
只有通过科学的工艺和严格的操作,才能有效地解决钢铁零件磷化缺陷问题,提高产品质量。
钢铁零件磷化缺陷原因分析及解决方案
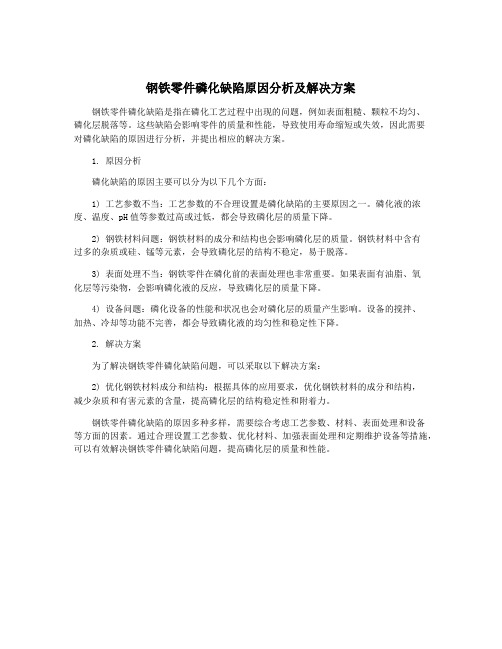
钢铁零件磷化缺陷原因分析及解决方案
钢铁零件磷化缺陷是指在磷化工艺过程中出现的问题,例如表面粗糙、颗粒不均匀、
磷化层脱落等。
这些缺陷会影响零件的质量和性能,导致使用寿命缩短或失效,因此需要
对磷化缺陷的原因进行分析,并提出相应的解决方案。
1. 原因分析
磷化缺陷的原因主要可以分为以下几个方面:
1) 工艺参数不当:工艺参数的不合理设置是磷化缺陷的主要原因之一。
磷化液的浓度、温度、pH值等参数过高或过低,都会导致磷化层的质量下降。
2) 钢铁材料问题:钢铁材料的成分和结构也会影响磷化层的质量。
钢铁材料中含有
过多的杂质或硅、锰等元素,会导致磷化层的结构不稳定,易于脱落。
3) 表面处理不当:钢铁零件在磷化前的表面处理也非常重要。
如果表面有油脂、氧
化层等污染物,会影响磷化液的反应,导致磷化层的质量下降。
4) 设备问题:磷化设备的性能和状况也会对磷化层的质量产生影响。
设备的搅拌、
加热、冷却等功能不完善,都会导致磷化液的均匀性和稳定性下降。
2. 解决方案
为了解决钢铁零件磷化缺陷问题,可以采取以下解决方案:
2) 优化钢铁材料成分和结构:根据具体的应用要求,优化钢铁材料的成分和结构,
减少杂质和有害元素的含量,提高磷化层的结构稳定性和附着力。
钢铁零件磷化缺陷的原因多种多样,需要综合考虑工艺参数、材料、表面处理和设备
等方面的因素。
通过合理设置工艺参数、优化材料、加强表面处理和定期维护设备等措施,可以有效解决钢铁零件磷化缺陷问题,提高磷化层的质量和性能。
钢铁零件磷化缺陷原因分析及解决方案
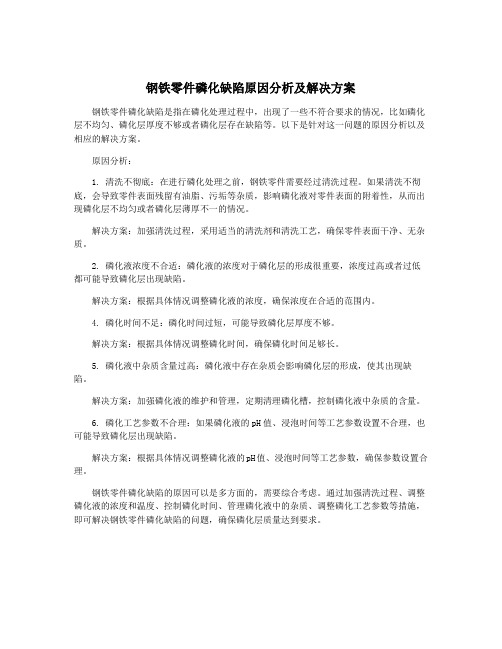
钢铁零件磷化缺陷原因分析及解决方案
钢铁零件磷化缺陷是指在磷化处理过程中,出现了一些不符合要求的情况,比如磷化层不均匀、磷化层厚度不够或者磷化层存在缺陷等。
以下是针对这一问题的原因分析以及相应的解决方案。
原因分析:
1. 清洗不彻底:在进行磷化处理之前,钢铁零件需要经过清洗过程。
如果清洗不彻底,会导致零件表面残留有油脂、污垢等杂质,影响磷化液对零件表面的附着性,从而出现磷化层不均匀或者磷化层薄厚不一的情况。
解决方案:加强清洗过程,采用适当的清洗剂和清洗工艺,确保零件表面干净、无杂质。
2. 磷化液浓度不合适:磷化液的浓度对于磷化层的形成很重要,浓度过高或者过低都可能导致磷化层出现缺陷。
解决方案:根据具体情况调整磷化液的浓度,确保浓度在合适的范围内。
4. 磷化时间不足:磷化时间过短,可能导致磷化层厚度不够。
解决方案:根据具体情况调整磷化时间,确保磷化时间足够长。
5. 磷化液中杂质含量过高:磷化液中存在杂质会影响磷化层的形成,使其出现缺陷。
解决方案:加强磷化液的维护和管理,定期清理磷化槽,控制磷化液中杂质的含量。
6. 磷化工艺参数不合理:如果磷化液的pH值、浸泡时间等工艺参数设置不合理,也可能导致磷化层出现缺陷。
解决方案:根据具体情况调整磷化液的pH值、浸泡时间等工艺参数,确保参数设置合理。
钢铁零件磷化缺陷的原因可以是多方面的,需要综合考虑。
通过加强清洗过程、调整磷化液的浓度和温度、控制磷化时间、管理磷化液中的杂质、调整磷化工艺参数等措施,即可解决钢铁零件磷化缺陷的问题,确保磷化层质量达到要求。
钢铁锌系磷化常见问题及处理方法
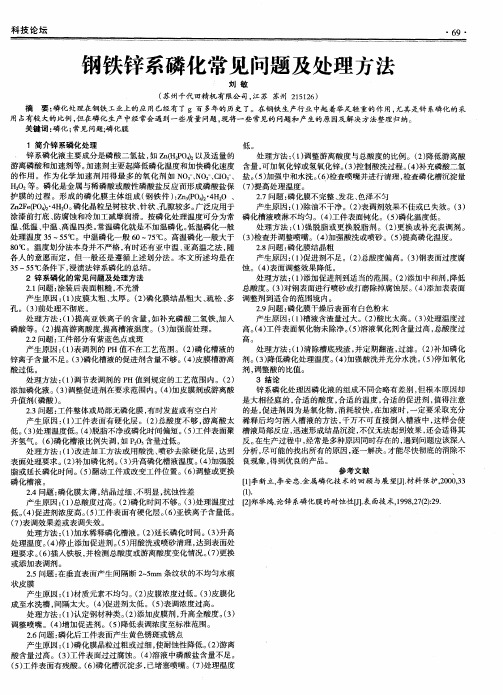
・ 6 9・
钢铁锌系磷化常见问题及处理方法
刘 敏
( 苏州千代田精机 有限公 司, 江 苏 苏州 2 1 5 1 2 6 )
摘 要: 磷 化处理在钢铁 工业上的应 用已经有 了 g百 多年 的历 史了。在钢铁 生产行业 中起 着举足轻重的作用 , 尤其是锌 系磷, I t  ̄ g j 采 用 占有较 大的比例 , 但在磷化 生产 中经 常会遇到一些质量 问题 , 现将一些常见的 问题 和产 生的原 因及解决方法整理 归纳。 关键词 : z a化 ; 常见 问题 ; 磷化膜
1简介锌系磷化 处理 低。 锌 系磷化液 主要 成分是磷 酸二氢盐 , 如 Z n ( H2 P 0 4 ) 以及适量 的 处理方法 : ( 1 ) 调整游离酸度与总酸度的 比例 。( 2 ) 降低游 离酸 游离磷酸和加速剂等 。 加 速剂 主要起 降低磷化温度和加快磷化速度 含量 , 可加氧化锌或氢氧化锌 。 ( 3 ) 控制 酸洗过程 。 ( 4 ) 补充磷酸二氢 的作 用 。作 为化学 加速剂 用得 最多 的氧化 剂如 N O  ̄ 、 N O  ̄ 、 C 1 0  ̄ 、 盐。 ( 5 ) 加强中和水洗 。 ( 6 ) 检查喷嘴并进行清理 , 检查磷化槽沉淀量 H 0 等 。磷 化是金属与稀磷 酸或酸性磷酸盐反应 而形成磷酸盐保 ( 7 ) 提高处理温度。 护膜 的过程 。形成 的磷化 膜主体 组成 ( 钢铁 件 ) : z n ( P 0 4 ) : ・ 4 H : 0 、 2 . 7问题 : 磷化膜不完整 、 发花 、 色泽不匀 Z n 2 F e ( P 0 4 ) 2 " 4 H 0。 磷化晶粒呈树枝状 、 针状 、 孔 隙较多 。 广泛应 用于 产生原 因: ( 1 ) 除油不干净。( 2 ) 表调剂效果不佳或 已失效 。( 3 ) 涂漆前打底 、 防腐蚀 和冷加工减摩润滑 。按磷化处理温度可分 为常 磷化槽液喷淋不均匀。( 4 ) 工件表面钝 化。( 5 ) 磷化 温度低 。 温、 低温、 中温 、 高温 四类 。 常温磷化就是不加温磷化。 低温磷化一般 处理 方法 : ( 1 ) 强 脱脂或更 换脱脂剂 。( 2 ) 更换 或补充表调 剂 。 处理温度 3 5 ~5 5 ℃。中温磷化一般 6 0 —7 5 %。高温磷化一般大 于 ( 3 ) 检查并 调整 喷嘴 。( 4 ) 加强 酸洗或喷砂 。( 5 ) 提高磷化温度 。 8 0  ̄ C 。温度划分法本身并不严格 , 有时还有亚 中温 、 亚高温之法 , 随 2 . 8问题 : 磷化膜结晶粗 各人 的意愿 而定 ,但 一般还是遵循上述 划分法 。本文所 述均是在 产生原 因: ( 1 ) 促进剂不 足。( 2 ) 总酸度偏 高。( 3 ) 钢表面过度腐 3 5~5 5  ̄ C 条件下 , 浸渍法锌系磷化的总结。 蚀 。( 4 ) 表 面调整效果降低。 2锌 系磷化 的常见 问题及处理方法 处理方法 : ( 1 ) 添加促进 剂到适 当的范 围。( 2 ) 添加 中和剂 , 降低 2 . 1问题 : 涂装后表面粗糙 , 不光滑 总酸度 。( 3 ) 对 钢表 面进行喷砂或打磨除掉腐蚀层 。( 4 ) 添加表表 面 产生原 因 : ( 1 ) 皮膜太粗 、 太厚 。( 2 ) 磷化膜结 晶粗大 、 疏松 、 多 调整剂到适合的范围境内。 孔 。( 3 ) 前处理不彻底 。 2 . 9问题 : 磷化膜干燥后表 面有 白色粉末 处理方 法 : ( 1 ) 提 高亚铁离 子的含量 , 如补 充磷酸二 氢铁, 加入 产生原因 : ( 1 ) 槽液含渣量过大 。( 2 ) 酸 比太高 。( 3 ) 处理温 度过 磷酸等 。( 2 ) 提 高游离酸度, 提高槽液温度 。( 3 ) 加强前处理 。 高。 ( 4 ) 工件 表面氧化物未除净 。 ( 5 ) 溶液氧化剂含量过 高, 总酸度过 2 . 2问题 : 工件部分有紫蓝 色点或斑 高。 处理方法 : ( 1 ) 清除槽底残渣 , 并定期翻渣 , 过滤。( 2 ) 补加磷化 产生原 因 : ( 1 ) 表调剂 的 P H值不 在工 艺范 围。( 2 ) 磷化槽液 的 锌离子含量不足。( 3 ) 磷化槽液 的促进剂含量不够 。( 4 ) 皮膜槽游离 剂 。 ( 3 ) 降低磷化处理 温度 。 ( 4 ) 加强酸洗并充分水洗 。 ( 5 ) 停加 氧化 酸过低 。 剂, 调整酸 的比值 。 3 结 论 处理方法 : ( 1 ) 调节表 调剂 的 P H值 到规定 的工艺范 围内。( 2 ) 锌 系磷化处理 因磷化液 的组 成不 同会 略有 差别 , 但根本原 因却 添加磷化液 。( 3 ) 调整促进剂在要求范 围内。( 4 ) 加皮膜剂 或游离酸 是大相 径庭 的 , 合 适的酸度 , 合适 的温度 , 合适 的促进剂 , 值得 注意 升值剂 ( 磷 酸) 。 的是 , 促进剂 因为是氧化物 , 消耗较快 , 在加液 时, 一定要采取充分 2 _ 3问题 : 工件整体或局部无磷化膜 , 有时发 蓝或有空 白片 产生原 因 : ( 1 ) 工件表 面有硬化层 。( 2 ) 总酸度 不够 , 游离酸太 稀 释后 均匀洒人槽液 的方法 , 千 万不可直接倒人槽液 中 , 这样会使 迅速形成结晶沉淀 , 不仅无法起到效果 , 还会适得其 低。 ( 3 ) 处理温度低。( 4 ) 脱脂不净或磷化时 间偏短。( 5 ) 工件表 面聚 槽液局部反应 , 反。 在生产过程中 , 经常是多种原因同时存在 的, 遇到 问题应该深入 齐氢气 。( 6 ) 磷 化槽 液比例失调 , 如P 2 0 含量过低 。 尽可能的找出所有 的原 因, 逐一解决 。 才能尽快彻底 的消除不 处理方 法 : ( 1 ) 改进加 工方法或用酸洗 、 喷砂去 除硬化层 , 达 到 分析 , 表面处理要求 。 ( 2 ) 补加磷化剂 。 ( 3 ) 升高磷化槽液温度 。 ( 4 ) 加强脱 良现象 , 得 到优 良的 产 品 。 参 考 文 献 脂或延长磷化时 间。( 5 ) 翻动工件或改变工件位置 。( 6 ) 调整或更换
钢铁零件磷化缺陷原因分析及解决方案
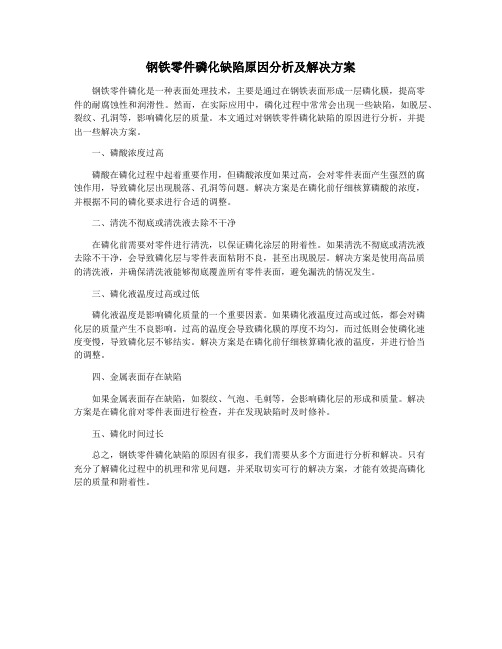
钢铁零件磷化缺陷原因分析及解决方案钢铁零件磷化是一种表面处理技术,主要是通过在钢铁表面形成一层磷化膜,提高零件的耐腐蚀性和润滑性。
然而,在实际应用中,磷化过程中常常会出现一些缺陷,如脱层、裂纹、孔洞等,影响磷化层的质量。
本文通过对钢铁零件磷化缺陷的原因进行分析,并提出一些解决方案。
一、磷酸浓度过高磷酸在磷化过程中起着重要作用,但磷酸浓度如果过高,会对零件表面产生强烈的腐蚀作用,导致磷化层出现脱落、孔洞等问题。
解决方案是在磷化前仔细核算磷酸的浓度,并根据不同的磷化要求进行合适的调整。
二、清洗不彻底或清洗液去除不干净在磷化前需要对零件进行清洗,以保证磷化涂层的附着性。
如果清洗不彻底或清洗液去除不干净,会导致磷化层与零件表面粘附不良,甚至出现脱层。
解决方案是使用高品质的清洗液,并确保清洗液能够彻底覆盖所有零件表面,避免漏洗的情况发生。
三、磷化液温度过高或过低磷化液温度是影响磷化质量的一个重要因素。
如果磷化液温度过高或过低,都会对磷化层的质量产生不良影响。
过高的温度会导致磷化膜的厚度不均匀,而过低则会使磷化速度变慢,导致磷化层不够结实。
解决方案是在磷化前仔细核算磷化液的温度,并进行恰当的调整。
四、金属表面存在缺陷如果金属表面存在缺陷,如裂纹、气泡、毛刺等,会影响磷化层的形成和质量。
解决方案是在磷化前对零件表面进行检查,并在发现缺陷时及时修补。
五、磷化时间过长总之,钢铁零件磷化缺陷的原因有很多,我们需要从多个方面进行分析和解决。
只有充分了解磷化过程中的机理和常见问题,并采取切实可行的解决方案,才能有效提高磷化层的质量和附着性。
磷化常见问题及解决方法

4.槽液沉渣浮起,黏附在工件上
5.工件表面氧化物未除净
6.溶液氧化剂含量过高,总酸度过高
1.清除槽底残渣,并定期过滤
2.补加磷化剂
3.降低磷化处理温度 4.静置磷化槽液,并翻槽
5.加强酸洗并充分水洗
6.停加氧化剂,调整酸的比值
5
磷化膜发花
磷化膜不均匀,有明显流挂痕迹
1.除油不净
2.表调剂效果不佳或失效
7.表调效果差或表调失效
1.加水稀释磷化槽液
2.延长磷化时间
3.升高处理温度
4.停加促进剂
5.用酸洗或喷砂处理,达到表面处理要求
6.插入铁板,并检测总酸度或游离酸度变化情况
7.更换或添加表调剂
3
磷化膜结晶粗大
磷化膜结晶粗大、疏松多孔、表面有水锈
1.工件未清洗干净
2.工件在磷化前生锈
3.亚铁离子含量偏低
1
无磷化膜或磷化膜不易形成
工件整体或局部无磷化膜,有时发蓝或有空白片
1.工件表面有硬化层
2.总酸度不够
3.处理温度低
4.游离酸太低
5.脱脂不净或磷化时间偏短
6.工件表面聚集氢气
7.磷化槽液比例失调,如P205含量低
8.工件重叠或工件之间发生接触
1.改进加工方法或用酸洗、喷砂去除硬化层,达到表面处理要求
磷化后工件表面附着沉渣、晶体
原因
对策
磷化工作液工作正常的条件下,表调失效
重配表调液
处理过程中加入大量中和剂,产生的沉渣(无机整体)不能充分反应,尤其在槽液《10度时加入中和剂。
加入一定量磷化液
磷化处理槽中沉渣多
倒槽排渣
酸比高于30以上,或总酸点低,游离酸点正常
磷化常见问题及解决方法
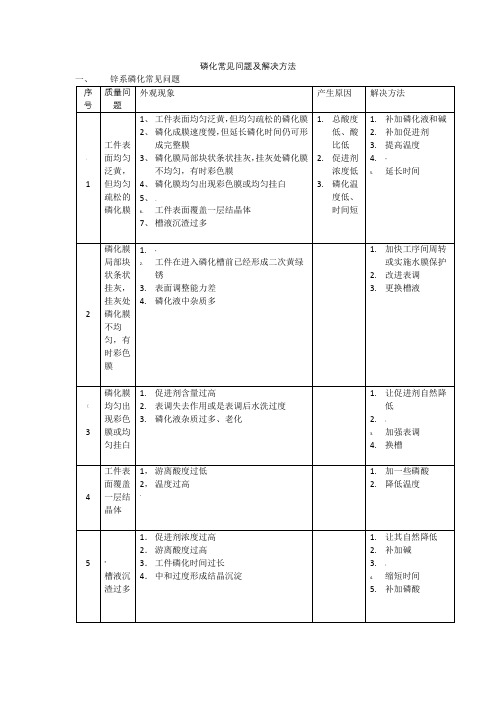
对策
磷化后不干净
:
烘干前水洗要充分
加入表调液时,未充分溶解,固体附在工件上
用温水充分溶解表调剂(固体),再加入水槽中
用后处理剂时,浓度过高
后处理剂不应超过规定值
涂装后出现异常现象与磷化膜出现的现象相吻合,则为磷化出现问题
按(5)处理
烘干时,工件中存水,未烘干
充分烘干
~
序号
质量外观
外观现象
产生原因
结疤:磷化膜形成不完全
|
原因
对策
除油未尽
表调液中混入过多杂质
磷化槽中沉渣多
游离酸点高
重新除油
/
重配表调液
倒槽排渣
用中和剂处理
磷化膜出现水锈斑
原因
对策
、
钢材经铬酸处理或附着难除尽的植物油
加强除油剂的除油能力
脱脂剂(碱性)温度低,碱性低,槽液表面浮油太多
浮油除去,升高温度
酸性除油剂除油未尽
补加药剂
点状红锈经磷化后变成白点或黄色水锈
1.促进剂浓度过高
2.游离酸度过高
3.工件磷化时间过长
4.中和过度形成结晶沉淀
1.让其自然降低
2.补加碱
3.:
4.缩短时间
5.补加磷酸
磷化膜的缺陷及解决方法:
磷化膜生锈,其中红锈产生于原料,黄锈产生于前处理 过程
现象
原因
对策
*
红锈
磷化后,磷化膜完整,但疏松。
局部泛黄,膜粗厚
原材料锈蚀过重,在工艺条件稳定的情况下,表调失去效果。
1.槽液含渣量过大
2.酸比太高
3处理温度过高
4.槽液沉渣浮起,黏附在工件上
5.工件表面氧化物未除净
磷化常见问答及解决方法

B、添加磷化液
C、倒槽或重配表调液
磷化后工件表面挂灰,磷化膜上覆盖一层白粉(粉末状)
原因
对策
酸比高
添加一定量磷化液
游离酸点高
按比例加入中和剂
促进剂浓度高或磷化液长时间不加促进剂,再突然大量加大;游离酸点高时加入促进剂。
应缓慢加入促进剂,多批次少量加入,出现问题后及时添加磷化液与中和剂。
10
磷化槽液变黑
磷化槽液变黑浑浊
1.槽液温度低于规定温度
2.溶液中亚铁离子过量
3.总酸度过低
1.停止磷化,升高槽液温度至沸点,保持1-2h,并用空气搅拌,直至灰色到原色
2.氧化剂,如高锰酸钾等
3.补充硝酸锌,提高总酸度
11
磷化膜发蓝
磷化膜部分表面产生紫兰色彩
1.表调剂的PH值不在工艺范围
2.表调与磷化间隔区的水务喷嘴堵塞
结疤:磷化膜形成不完全
原因
对策
除油未尽
表调液中混入过多杂质
磷化槽中沉渣多
游离酸点高
重新除油
重配表调液
倒槽排渣
用中和剂处理
磷化膜出现水锈斑
原因
对策
钢材经铬酸处理或附着难除尽的植物油
加强除油剂的除油能力
脱脂剂(碱性)温度低,碱性低,槽液表面浮油太多
浮油除去,升高温度
酸性除油剂除油未尽
补加药剂
点状红锈经磷化后变成白点或黄色水锈
磷化常见问题及解决方法
一、锌系磷化常见问题
序号
质量问题
外观现象
产生原因
解决方法
1
工件表面均匀泛黄,但均匀疏松的磷化膜
1、工件表面均匀泛黄,但均匀疏松的磷化膜
2、磷化成膜速度慢,但延长磷化时间仍可形成完整膜
钢铁零件磷化缺陷原因分析及解决方案
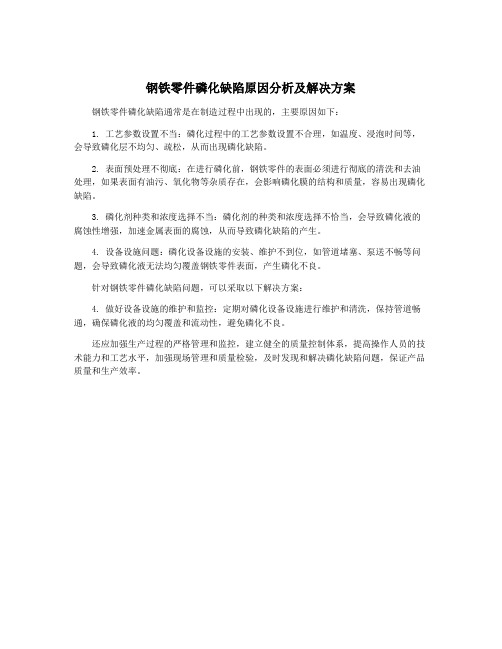
钢铁零件磷化缺陷原因分析及解决方案
钢铁零件磷化缺陷通常是在制造过程中出现的,主要原因如下:
1. 工艺参数设置不当:磷化过程中的工艺参数设置不合理,如温度、浸泡时间等,会导致磷化层不均匀、疏松,从而出现磷化缺陷。
2. 表面预处理不彻底:在进行磷化前,钢铁零件的表面必须进行彻底的清洗和去油处理,如果表面有油污、氧化物等杂质存在,会影响磷化膜的结构和质量,容易出现磷化缺陷。
3. 磷化剂种类和浓度选择不当:磷化剂的种类和浓度选择不恰当,会导致磷化液的腐蚀性增强,加速金属表面的腐蚀,从而导致磷化缺陷的产生。
4. 设备设施问题:磷化设备设施的安装、维护不到位,如管道堵塞、泵送不畅等问题,会导致磷化液无法均匀覆盖钢铁零件表面,产生磷化不良。
针对钢铁零件磷化缺陷问题,可以采取以下解决方案:
4. 做好设备设施的维护和监控:定期对磷化设备设施进行维护和清洗,保持管道畅通,确保磷化液的均匀覆盖和流动性,避免磷化不良。
还应加强生产过程的严格管理和监控,建立健全的质量控制体系,提高操作人员的技术能力和工艺水平,加强现场管理和质量检验,及时发现和解决磷化缺陷问题,保证产品质量和生产效率。
(完整版)磷化常见问题及处理方法
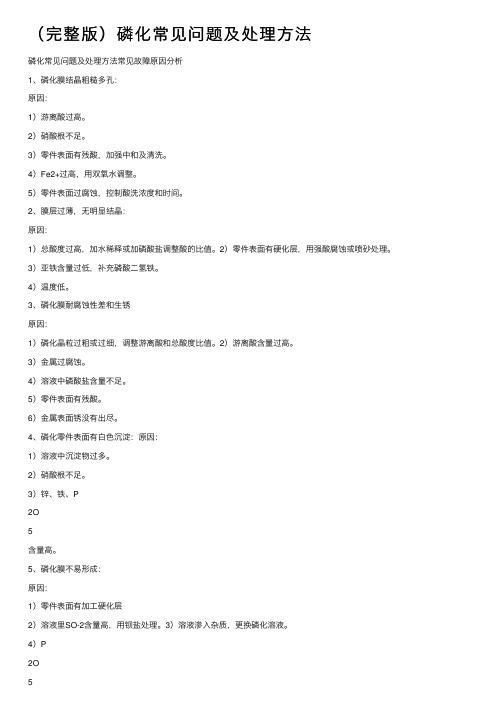
(完整版)磷化常见问题及处理⽅法磷化常见问题及处理⽅法常见故障原因分析1、磷化膜结晶粗糙多孔:原因:1)游离酸过⾼。
2)硝酸根不⾜。
3)零件表⾯有残酸,加强中和及清洗。
4)Fe2+过⾼,⽤双氧⽔调整。
5)零件表⾯过腐蚀,控制酸洗浓度和时间。
2、膜层过薄,⽆明显结晶:原因:1)总酸度过⾼,加⽔稀释或加磷酸盐调整酸的⽐值。
2)零件表⾯有硬化层,⽤强酸腐蚀或喷砂处理。
3)亚铁含量过低,补充磷酸⼆氢铁。
4)温度低。
3、磷化膜耐腐蚀性差和⽣锈原因:1)磷化晶粒过粗或过细,调整游离酸和总酸度⽐值。
2)游离酸含量过⾼。
3)⾦属过腐蚀。
4)溶液中磷酸盐含量不⾜。
5)零件表⾯有残酸。
6)⾦属表⾯锈没有出尽。
4、磷化零件表⾯有⽩⾊沉淀:原因:1)溶液中沉淀物过多。
2)硝酸根不⾜。
3)锌、铁、P2O5含量⾼。
5、磷化膜不易形成:原因:1)零件表⾯有加⼯硬化层2)溶液⾥SO-2含量⾼,⽤钡盐处理。
3)溶液渗⼊杂质,更换磷化溶液。
4)P2O5含量过低,补充磷酸盐。
6、磷化层不均、发花:原因:1)除油不净、温度太低。
2)零件表⾯有钝化状态,加强酸洗或喷砂。
3)零件因热处理加⼯⽅法不同。
7、冷挤压后磷化膜产⽣条状脱落:原因:1)肥皂溶液⾥有杂质。
2)皂化前零件表⾯有杂质和沉淀物,重新磷化。
8、磷化膜发红抗蚀能⼒下降:原因:1)酸洗液⾥铁渣附在表⾯。
2)铜离⼦渗⼊磷化液磷化常见故障及处理⽅法磷化膜结晶粗⼤的原因及处理⽅法原因:①亚铁离⼦含量过多;②零件表⾯带有残酸;③溶液⾥硝酸根不⾜;④溶液⾥硫酸根含量增⾼;⑤零件表⾯过腐蚀。
处理⽅法:①⽤压缩空⽓搅拌,或⽤双氧⽔降低亚铁离⼦含量,升⾼温度;②加强中和或⽔洗;③添加硝酸锌;④⽤碳酸钡处理硫酸根;⑤控制酸的浓度和时间。
质量问题外观现象产⽣原因解决⽅法1、⽆磷化膜或磷化膜不易形成⼯件整体或局部⽆磷化膜,有时发蓝或有空⽩⽚(1)⼯件表⾯有硬化层;(2)总酸度不够;(3)处理温度低(4)游离酸太低(5)脱脂不净或磷化时间偏短;(6)⼯件表⾯聚集氢⽓;(7)磷化槽液⽐例失调,如P2O5含量过低;(8)⼯件重叠或⼯件之间发⽣接触⽅法:(1)改进加⼯⽅法或⽤酸洗、喷砂去除硬化层、达到表⾯处理要求;(2)补加磷化剂:(3)升⾼磷化槽液温度;(4)补加磷化剂;(5)加强脱脂或延长磷化时间;(6)翻动⼯件或改变⼯件位置;(7)调整或更换磷化槽液;(8)注意增⼤⼯件间隙,避免接触2、磷化膜过薄磷化膜太薄、结晶过细或⽆明显结晶,抗蚀性能差。
磷化常见问题及解决方法

原因
对策
除油未尽
表调液中混入过多杂质
磷化槽中沉渣多
游离酸点高
重新除油
重配表调液
倒槽排渣
用中和剂处理
磷化膜出现水锈斑
原因
对策
钢材经铬酸处理或附着难除尽的植物油
加强除油剂的除油能力
脱脂剂(碱性)温度低,碱性低,槽液表面浮油太多
浮油除去,升高温度
酸性除油剂除油未尽
补加药剂
点状红锈经磷化后变成白点或黄色水锈
8
磷化膜发红
磷化膜红但不是锈
1.铜离子渗入磷化液
2.酸洗液中的铁渣附着
1.注意不用铜挂具,用铁屑置换除去或用硫化处理,调整酸度 2.加强酸洗过程的质量控制
9
膜呈彩虹花斑
用指甲划过无划痕,对光观察呈彩虹色
1.促进剂浓度过高
2.促进剂分布不均
3.除油不彻底
1.停加促进剂
2.充分搅拌,使之均匀
3.补加脱脂剂
7.表调效果差或表调失效
1.加水稀释磷化槽液
2.延长磷化时间
3.升高处理温度
4.停加促进剂
5.用酸洗或喷砂处理,达到表面处理要求
6.插入铁板,并检测总酸度或游离酸度变化情况
7.更换或添加表调剂
3
磷化膜结晶粗大
磷化膜结晶粗大、疏松多孔、表面有水锈
1.工件未清洗干净
2.工件在磷化前生锈
3.亚铁离子含量偏低
磷化后工件表面附着沉渣、晶体
原因
对策
磷化工作液工作正常的条件下,表调失效
重配表调液
处理过程中加入大量中和剂,产生的沉渣(无机整体)不能充分反应,尤其在槽液《10度时加入中和剂。
加入一定量磷化液
钢铁零件磷化缺陷原因分析及解决方案

钢铁零件磷化缺陷原因分析及解决方案钢铁零件磷化是一种常见的涂层技术,能够提高钢铁零件表面的耐蚀性和防锈性能。
磷化涂层是一种无机化学转化反应,将金属表面与含磷化学物质接触,生成具有骨架结构的涂层。
但是,在实际应用过程中,我们常常会遇到一些磷化缺陷,导致涂层的质量大打折扣。
本文将详细探讨磷化缺陷的原因分析及解决方案。
一、磷化缺陷种类磷化涂层会出现多种缺陷,主要包括以下几种:1.缺陷种类一:坑洞、孔洞2.缺陷种类二:气泡,分布不均3.缺陷种类三:浮油、白点二、磷化缺陷原因分析1.原因分析一:未彻底清洁很多磷化涂层出现缺陷的原因是在涂层前未彻底清洁零件表面,清洗不彻底会导致钢铁表面仍有一些油和垃圾残留,这些杂质会污染磷化液。
这样就会导致磷化液在钢铁零件上不易均匀分布,形成缺陷。
2.原因分析二:磷酸浓度高水中磷酸浓度过高也会导致钢铁零件表面磷化不均匀、产生坑洞和气泡,使得钢铁零件表面不光滑,影响产品的质量。
磷化液温度过高也会影响涂层质量。
磷化液温度过高会导致磷化液中含物质的溶解度降低,可能会导致镀层薄和不均匀,缺陷就难以避免。
4.原因分析四:磷化时间过长磷化涂层的质量也与磷化时间有关。
磷化时间过长会导致磷化液中含物质太多、浓度过高,造成磷化涂层非常粗糙,表面光滑度不佳,形成坑洞或气泡等缺陷。
三、磷化缺陷解决方案1.方案一:提高清洁度清洁是涂层工艺非常关键的一步。
要保证磷化涂层质量,需要增加零件的清洗量,使用高效的清洗器进行清洗,将零件表面的油和污垢完全清除。
磷酸的浓度是影响磷化涂层质量的重要因素之一。
因此,选择适当的磷酸浓度是很重要的。
通常,使用6% 左右的磷酸浓度可得到效果较好的磷化涂层。
3.方案三:控制磷化液温度控制磷化液的温度也非常关键。
在涂层工艺中,应该保持一定的磷化液温度,通常在35℃左右为合适。
过低的温度会导致磷酸结晶,而过高的温度可能会导致磷化液内的溶解度降低,从而影响涂层的质量。
在磷化涂层工艺中,磷化时间的控制是非常关键的。
钢铁零件磷化缺陷原因分析及解决方案
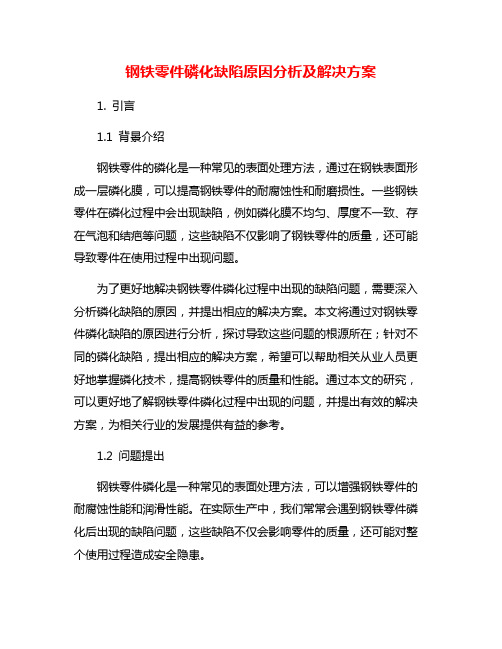
钢铁零件磷化缺陷原因分析及解决方案1. 引言1.1 背景介绍钢铁零件的磷化是一种常见的表面处理方法,通过在钢铁表面形成一层磷化膜,可以提高钢铁零件的耐腐蚀性和耐磨损性。
一些钢铁零件在磷化过程中会出现缺陷,例如磷化膜不均匀、厚度不一致、存在气泡和结疤等问题,这些缺陷不仅影响了钢铁零件的质量,还可能导致零件在使用过程中出现问题。
为了更好地解决钢铁零件磷化过程中出现的缺陷问题,需要深入分析磷化缺陷的原因,并提出相应的解决方案。
本文将通过对钢铁零件磷化缺陷的原因进行分析,探讨导致这些问题的根源所在;针对不同的磷化缺陷,提出相应的解决方案,希望可以帮助相关从业人员更好地掌握磷化技术,提高钢铁零件的质量和性能。
通过本文的研究,可以更好地了解钢铁零件磷化过程中出现的问题,并提出有效的解决方案,为相关行业的发展提供有益的参考。
1.2 问题提出钢铁零件磷化是一种常见的表面处理方法,可以增强钢铁零件的耐腐蚀性能和润滑性能。
在实际生产中,我们常常会遇到钢铁零件磷化后出现的缺陷问题,这些缺陷不仅会影响零件的质量,还可能对整个使用过程造成安全隐患。
问题提出:钢铁零件磷化缺陷是什么原因导致的?如何有效地解决这些缺陷问题?这些问题一直困扰着我们在钢铁零件磷化过程中的生产和应用,需要我们深入分析和探讨,以找到有效的解决方案。
在本文中,我们将对钢铁零件磷化缺陷的原因进行分析,探讨钢铁零件磷化缺陷的解决方案,以期为相关行业提供参考和借鉴。
2. 正文2.1 磷化缺陷的原因分析在磷化过程中,如果磷化液中的浓度或温度控制不当,会导致磷化层的形成不完整或不均匀,出现缺陷。
这可能是由于生产操作不当或设备设施问题引起的。
材料表面的油污、氧化物或其他杂质会影响磷化层的质量。
如果在磷化前没有经过充分的清洗和净化处理,这些污染物会影响磷化层与基体的结合,从而产生缺陷。
工艺参数设置不当也是导致磷化缺陷的重要原因之一。
磷化液中的PH值、温度、浸磷时间等参数如果没有严格控制,都有可能造成磷化缺陷的出现。
紧固件磷化常见问题及解决

紧固件磷化常见问题及解决(2009-12-25)紧固件磷化常用有两种,锌系磷化和锰系磷化,锌系磷化润滑性能比锰系磷化好,锰系磷化抗腐蚀性,耐磨性较锌系好。
它的使用温度可达105~205℃(华氏225F°-400F°)。
机械工业用紧固件很多用磷化涂油处理。
因为它扭矩-预紧力一致性很好,装配时能保证达到设计所预期的紧固要求,所以在机械工业中使用较多。
特别是一些重要零部件的连接。
如:钢结构连接副、发动机的连杆螺栓、螺母,缸盖、主轴承、飞轮螺栓、车轮螺栓螺母等。
高强度螺栓采用磷化,还可以避免氢脆问题,所以在机械工业领域10.9级以上的螺栓一般采用磷化表面处理。
紧固件磷化常见缺陷、产生原因及改进对策如下:常见磷化故障的解决办法类别:技术问题发布时间:2010/5/31 10:32:00浏览数:3862近年来,表面处理中转化膜技术发展较快。
在汽车摩托车的紧固件上采用较多的是磷酸盐(磷化)和氧化(发黑)。
虽然它们的防腐性能耐久性等级属于轻度保护,由于成本低廉,使用方便在表面防护领域还占有一席之地。
磷化是借磷化溶液在紧固件表面上人为地造成一层厚约10μm保护膜,这层膜是难溶的磷酸盐的混合物。
根据磷化液用的磷酸盐分类有:磷酸锌系、磷酸铁系、磷酸锰系。
此外,还有在磷酸锌中加钙的锌钙系,在磷酸锌中加铜、加镍的三元体系磷化等。
一、常见磷化故障的解决办法故障1:工件表面均匀泛黄,均匀疏松的磷化膜主要原因:⑴总酸度低、酸比低;⑵促进剂浓度低;⑶磷化温度低、时间短。
解决方法:⑴补加磷化液和碱;⑵补加促进剂;⑶提高温度,延长时间。
故障2:磷化成膜速度慢,但延长磷化时间仍可形成均匀完整膜主要原因:⑴表面调整能力不强;⑵促进剂溶度不够;⑶酸比低;⑷磷化温度低。
解决方法:⑴改进表调或换槽;⑵补加促进剂;⑶补加碱;⑷提高温度。
故障3:㈠磷化膜局部块状条状挂灰;㈡挂灰处磷化膜不均匀;㈢时有彩色膜。
主要原因:⑴工件在进入磷化槽前已经形成二次黄绿锈;⑵表面调整能力差;⑶磷化液中杂质多。
钢铁零件磷化缺陷原因分析及解决方案
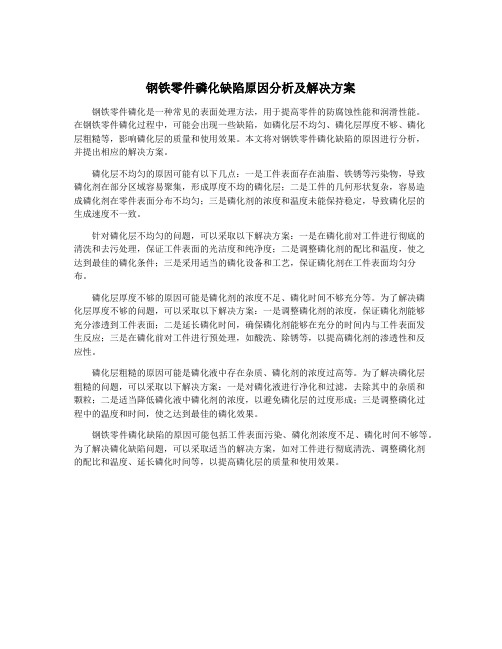
钢铁零件磷化缺陷原因分析及解决方案钢铁零件磷化是一种常见的表面处理方法,用于提高零件的防腐蚀性能和润滑性能。
在钢铁零件磷化过程中,可能会出现一些缺陷,如磷化层不均匀、磷化层厚度不够、磷化层粗糙等,影响磷化层的质量和使用效果。
本文将对钢铁零件磷化缺陷的原因进行分析,并提出相应的解决方案。
磷化层不均匀的原因可能有以下几点:一是工件表面存在油脂、铁锈等污染物,导致磷化剂在部分区域容易聚集,形成厚度不均的磷化层;二是工件的几何形状复杂,容易造成磷化剂在零件表面分布不均匀;三是磷化剂的浓度和温度未能保持稳定,导致磷化层的生成速度不一致。
针对磷化层不均匀的问题,可以采取以下解决方案:一是在磷化前对工件进行彻底的清洗和去污处理,保证工件表面的光洁度和纯净度;二是调整磷化剂的配比和温度,使之达到最佳的磷化条件;三是采用适当的磷化设备和工艺,保证磷化剂在工件表面均匀分布。
磷化层厚度不够的原因可能是磷化剂的浓度不足、磷化时间不够充分等。
为了解决磷化层厚度不够的问题,可以采取以下解决方案:一是调整磷化剂的浓度,保证磷化剂能够充分渗透到工件表面;二是延长磷化时间,确保磷化剂能够在充分的时间内与工件表面发生反应;三是在磷化前对工件进行预处理,如酸洗、除锈等,以提高磷化剂的渗透性和反应性。
磷化层粗糙的原因可能是磷化液中存在杂质、磷化剂的浓度过高等。
为了解决磷化层粗糙的问题,可以采取以下解决方案:一是对磷化液进行净化和过滤,去除其中的杂质和颗粒;二是适当降低磷化液中磷化剂的浓度,以避免磷化层的过度形成;三是调整磷化过程中的温度和时间,使之达到最佳的磷化效果。
钢铁零件磷化缺陷的原因可能包括工件表面污染、磷化剂浓度不足、磷化时间不够等。
为了解决磷化缺陷问题,可以采取适当的解决方案,如对工件进行彻底清洗、调整磷化剂的配比和温度、延长磷化时间等,以提高磷化层的质量和使用效果。
钢铁零件磷化缺陷原因分析及解决方案

钢铁零件磷化缺陷原因分析及解决方案
钢铁零件磷化缺陷是指在磷化过程中出现的不良现象或问题,主要表现为磷化膜附着
性差、脱落、不均匀等。
这些缺陷不仅影响到零件的质量和使用寿命,还可能导致零件无
法达到预期的防腐、防锈效果。
针对钢铁零件磷化缺陷问题,进行原因分析和解决方案的
研究具有重要的实际意义。
钢铁零件磷化缺陷的原因可以归纳为以下几个方面:
1. 表面处理不当:钢铁零件在磷化之前需要进行清洗和脱脂处理,如果清洗和脱脂
过程不充分,会导致表面存在油脂、污垢等难以去除的物质,影响磷化液的附着性。
解决方法:加强表面处理工艺,确保零件表面的清洁度和光洁度。
可以采用机械清洗、溶剂清洗、碱洗等方法,确保表面没有油脂等污染物。
2. 磷化液成分不合理:磷化液的成分是影响磷化质量的重要因素之一。
如果磷化液
中的磷酸盐、氯化物等成分浓度不合理,会导致磷化膜的附着力不好、脱落等问题。
解决方法:优化磷化液的配方,选择合适的磷酸盐和氯化物浓度,确保磷化液的稳定
性和均匀性。
解决方法:加强对磷化液pH值的控制,采用合适的酸碱调节剂,确保磷化液的酸碱度稳定。
4. 磷化液温度控制不恰当:磷化液的温度是磷化过程中另一个重要的操作参数。
如
果磷化液的温度过高或过低,会导致磷化膜形成不均匀,附着力差等问题。
要解决钢铁零件磷化缺陷问题,需要从表面处理、磷化液成分、pH值控制和温度控制等方面进行综合考虑和优化。
通过加强工艺管理,控制好每个操作环节,可以有效地提高
磷化膜的质量和附着性,保证钢铁零件的使用寿命和防腐、防锈效果。
- 1、下载文档前请自行甄别文档内容的完整性,平台不提供额外的编辑、内容补充、找答案等附加服务。
- 2、"仅部分预览"的文档,不可在线预览部分如存在完整性等问题,可反馈申请退款(可完整预览的文档不适用该条件!)。
- 3、如文档侵犯您的权益,请联系客服反馈,我们会尽快为您处理(人工客服工作时间:9:00-18:30)。
A、总酸点低,酸比低,没有达到工作点数。
B、促进剂少。
C、磷化温度低,相对磷化时间短。
D、游离酸点高。
A、补加磷化液
B、补加促进剂
C、多发生在配槽时,应延长磷化时间,提高温度。
D、用中和剂调整。
磷化膜呈蓝紫色
磷化后工件表面附着沉渣、晶体
原因
对策
磷化工作液工作正常的条件下,表调失效
重配表调液
处理过程中加入大量中和剂,产生的沉渣(无机整体)不能充分反应,尤其在槽液《10度时加入中和剂。
加入一定量磷化液
磷化处理槽中沉渣多
倒槽排渣
酸比高于30以上,或总酸点低,游离酸点正常
补加磷化液
水洗不充分,水洗槽受到污染
更换水
3.更换槽液
3
磷化膜均匀出现彩色膜或均匀挂白
1.促进剂含量过高
2.表调失去作用或是表调后水洗过度
3.磷化液杂质过多、老化
1.让促进剂自然降低
2.加强表调
3.换槽
4
工件表面覆盖一层结晶体
1,游离酸度过低
2,温度过高
1.加一些磷酸
2.降低温度
5
槽液沉渣过多
1.促进剂浓度过高
2.游离酸度过高
3.工件磷化时间过长
2.补加磷化剂
3.升高磷化槽液温度
4.补加磷化剂
5.加强脱脂或延长磷化时间
6.翻动工件或改变工件位置
7.调整或更换磷化槽液
8.注意增大工件间隙,避免接触
2
磷化膜过薄
磷化膜太薄,结晶过细或无明显结晶,抗蚀能力差
1.总酸度过高
2.磷化时间不够
3.处理温度过低
4.促进剂浓度高
5.工件表面有硬化层
6.亚铁离子含量低
4.中和过度形成结晶沉淀
1.让其自然降低
2.补加碱
3.缩短时间
4.补加磷酸
磷化膜的缺陷及解决方法:
磷化膜生锈,其中红锈产生于原料,黄锈产生于前处理 过程
现象
原因
对策
红锈
磷化后,磷化膜完整,但疏松。
局部泛黄,膜粗厚
原材料锈蚀过重,在工艺条件稳定的情况下,表调失去效果。
防锈完全,在没有除锈的工序中,处理前砂纸打磨,重新更换表调液。
6、槽液沉渣过多
1.总酸度低、酸比低
2.促进剂浓度低
3.磷化温度低、时间短
1.补加磷化液和碱
2.补加促进剂
3.提高温度
4.延长时间
2
磷化膜局部块状条状挂灰,挂灰处磷化膜不均匀,有时彩色膜
1.工件在进入磷化槽前已经形成二次黄绿锈
2.表面调整能力差
3.磷化液中杂质多
1.加快工序间周转或实施水膜保护
2.改进表调
1
无磷化膜或磷化膜不易形成
工件整体或局部无磷化膜,有时发蓝或有空白片
1.工件表面有硬化层
2.总酸度不够
3.处理温度低
4.游离酸太低
5.脱脂不净或磷化时间偏短
6.工件表面聚集氢气
7.磷化槽液比例失调,如P205含量低
8.工件重叠或工件之间发生接触
1.改进加工方法或用酸洗、喷砂去除硬化层,达到表面处理要求
4.游离酸度偏低
5.磷化温度低
6.工件表面产生过腐蚀现象
1.加强磷化前工件表面的预处理
2.除锈水洗后减少工件在空气中的暴露时间
3.提高亚铁离子的含量,如补充磷酸二氢铁
4.加入磷酸等,提高游离酸度
5.提高槽液温度
6.控制除锈时间或更换除锈剂
4
磷化膜挂灰
磷化膜干燥后表面有白色粉末
1.槽液含渣量过大
2.酸比太高
磷化常见问题及解决方法
一、锌系磷化常见问题
序号
质量问题
外观现象
产生原因
解决方法
1
工件表面均匀泛黄,但均匀疏松的磷化膜
1、工件表面均匀泛黄,但均匀疏松的磷化膜
2、磷化成膜速度慢,但延长磷化时间仍可形成完整膜
3、磷化膜局部块状条状挂灰,挂灰处磷化膜不均匀,有时彩色膜
4、磷化膜均匀出现彩色膜或均匀挂白
5、工件表面覆盖一层结晶体
现象
原因
对策
局部呈蓝紫色
A、工艺正常时,表调中有效成份低
B、总酸点低,游离酸点也低。
C、促进剂浓度高(5-7点)
A、补加或重配表调液。B、添加磷化液。
C、让其自然降低或加一定量的中和剂(0.3G/L)
均匀出现蓝紫色
A、工艺正常时,表调失去作用。
B、总酸点太低。
C、工艺正常,表调正常时,说明磷化处理槽中杂质太多,老化严重
3.磷化槽液喷淋不均匀
4.工件表面钝化
5.磷化温度低
7.表调效果差或表调失效
1.加水稀释磷化槽液
2.延长磷化时间
3.升高处理温度
4.停加促进剂
5.用酸洗或喷砂处理,达到表面处理要求
6.插入铁板,并检测总酸度或游离酸度变化情况
7.更换或添加表调剂
3
磷化膜结晶粗大
磷化膜结晶粗大、疏松多孔、表面有水锈
1.工件未清洗干净
2.工件在磷化前生锈
3.亚铁离子含量偏低
原因
对策
磷化后不干净
烘干前水洗要充分
加入表调液时,未充分溶解,固体附在工件上
用温水充分溶解表调剂(固体),再加入水槽中
用后处理剂时,浓度过高
后处理剂不应超过规定值
涂装后出现异常现象与磷化膜出现的现象相吻合,则为磷化出现问题
按(5)处理
烘干时,工件中存水,未烘干
充分烘干
序号
质量外观
外观现象
产生原因
解决方法
增加酸洗
磷化膜不均匀干痕
原因
对策
在工件边缘上端和空洞四周有不均匀颜色,呈金黄色和蓝紫色
充分除油
将总酸点提高到30以上
磷化后磷化膜有粗糙斜丝:工件表面产生不均匀覆膜或磷化粗糙,发白
原因
对策
表调失效
重配表调剂
磷化工作液中促进剂量低
补加促进剂
游离酸点高
用中和剂进行中和
涂装:涂装后漆膜气泡,产生异常的线状或环状涂膜
3处理温度过高
4.槽液沉渣浮起,黏附在工件上
5.工件表面氧化物未除净
6.溶液氧化剂含量过高,总酸度过高
1.清除槽底残渣,并定期过滤
2.补加磷化剂
3.降低磷化处理温度4.静置磷化槽液,并翻槽
5.加强酸洗并充分水洗
6.停加氧化剂,调整酸的比值
5
磷化膜发花
磷化膜不均匀,有明显流挂痕迹
1.除油不净
2.表调剂效果不佳或失效
结疤:磷化膜形成不完全
原因
对策
除油未尽
表调液中混入过多杂质
磷化槽中沉渣多
游离酸点高
重新除油
重配表调液
倒槽排渣
用中和剂处理
磷化膜出现水锈斑
原因
对策
钢材经铬酸处理或附着难除尽的植物油
加强除油剂的除油能力
脱脂剂(碱性)温度低,碱性低,槽表面浮油太多
浮油除去,升高温度
酸性除油剂除油未尽
补加药剂
点状红锈经磷化后变成白点或黄色水锈
A、重配表调液
B、添加磷化液
C、倒槽或重配表调液
磷化后工件表面挂灰,磷化膜上覆盖一层白粉(粉末状)
原因
对策
酸比高
添加一定量磷化液
游离酸点高
按比例加入中和剂
促进剂浓度高或磷化液长时间不加促进剂,再突然大量加大;游离酸点高时加入促进剂。
应缓慢加入促进剂,多批次少量加入,出现问题后及时添加磷化液与中和剂。