镀银常见故障的分析和纠正
氰化镀银故障分析:镀层起泡、脱落、结合力不良
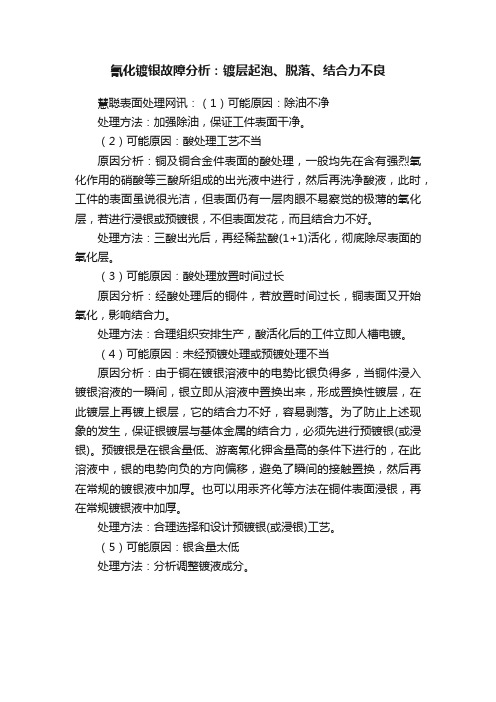
氰化镀银故障分析:镀层起泡、脱落、结合力不良
慧聪表面处理网讯:(1)可能原因:除油不净
处理方法:加强除油,保证工件表面干净。
(2)可能原因:酸处理工艺不当
原因分析:铜及铜合金件表面的酸处理,一般均先在含有强烈氧化作用的硝酸等三酸所组成的出光液中进行,然后再洗净酸液,此时,工件的表面虽说很光洁,但表面仍有一层肉眼不易察觉的极薄的氧化层,若进行浸银或预镀银,不但表面发花,而且结合力不好。
处理方法:三酸出光后,再经稀盐酸(1+1)活化,彻底除尽表面的氧化层。
(3)可能原因:酸处理放置时间过长
原因分析:经酸处理后的铜件,若放置时间过长,铜表面又开始氧化,影响结合力。
处理方法:合理组织安排生产,酸活化后的工件立即人槽电镀。
(4)可能原因:未经预镀处理或预镀处理不当
原因分析:由于铜在镀银溶液中的电势比银负得多,当铜件浸入镀银溶液的一瞬间,银立即从溶液中置换出来,形成置换性镀层,在此镀层上再镀上银层,它的结合力不好,容易剥落。
为了防止上述现象的发生,保证银镀层与基体金属的结合力,必须先进行预镀银(或浸银)。
预镀银是在银含量低、游离氰化钾含量高的条件下进行的,在此溶液中,银的电势向负的方向偏移,避免了瞬间的接触置换,然后再在常规的镀银液中加厚。
也可以用汞齐化等方法在铜件表面浸银,再在常规镀银液中加厚。
处理方法:合理选择和设计预镀银(或浸银)工艺。
(5)可能原因:银含量太低
处理方法:分析调整镀液成分。
电镀常见不良问题点分析及对策
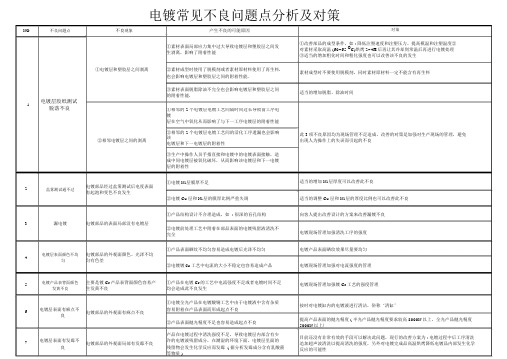
电镀常见不良问题点分析及对策NO.不良问题点不良现象产生不良的可能原因①素材表面局部应力集中过大导致电镀层和塑胶层之间发生剥离,影响了附着性能①电镀层和塑胶层之间剥离②素材成型时使用了脱模剂或者素材原材料使用了再生料.也会影响电镀层和塑胶层之间的附着性能.③素材表面脱脂除油不完全也会影响电镀层和塑胶层之间电镀层胶纸测试的附着性能.1脱落不良①相邻的 2个电镀层电镀工艺间隔时间过长导致前工序电镀层在空气中氧化从而影响了与下一工序电镀层的附着性能②相邻电镀层之间的剥离②相邻的 2个电镀层电镀工艺间的活化工序遗漏也会影响该电镀层和下一电镀层的附着性对策①改善部品的成型条件,如 : 降低注塑速度和注塑压力、提高模温和注塑温度②对素材采取高温 (60~65 O C)烘烤2~4H后再让其冷却到常温后再进行电镀处理③适当的增加粗化时间和粗化强度也可以改善该不良的发生素材成型时不要使用脱模剂,同时素材原材料一定不能含有再生料适当的增加脱脂、除油时间此3项不良原因均为现场管理不足造成,改善的对策是加强对生产现场的管理,避免出现人为操作上的失误而引起的不良2 3 4 5 6 7③生产中操作人员手指直接和电镀中的电镀表面接触,造成中间电镀层被氧化破坏,从而影响该电镀层和下一电镀层的附着性电镀部品经过盐雾测试后电度表面①电镀 Ni层膜厚不足盐雾测试通不过有起泡和变色不良发生②电镀 Cu层和Ni层的膜厚比例严重失调①产品结构设计不合理造成,如 : 很深的盲孔结构漏电镀电镀部品的表面局部没有电镀层②电镀前处理工艺中附着在部品表面的电镀残留液清洗不完全电镀部品的外观面颜色、光泽不均①产品表面晒纹不均匀容易造成电镀后光泽不均匀电镀层表面颜色不均匀匀有色差②电镀镀C u工艺中电流的大小不稳定也容易造成产品电镀产品表背面颜色主要是镀 Cr产品表背面颜色容易产①产品在电镀 Cr的工艺中电流强度不足或者电镀时间不足发黄不良生发黄不良均会造成此不良发生①电镀全光产品在电镀酸铜工艺中由于电镀液中含有杂质电镀层表面有麻点不电镀部品的外观面有麻点不良容易附着在产品表面而形成起点不良良②产品表面抛光精度不足也容易造成起点不良产品在电镀过程中清洗强度不足,导致电镀层内部含有少电镀层表面有发霉不电镀部品的外观面局部有发霉不良许的电镀液残留成分,在潮湿的环境下面,电镀层里面的良残留物会发生化学反应而发霉 ( 据分析发霉成分含有乳酸菌等物质 )适当的增加 Ni层厚度可以改善此不良适当的调整 Cu层和Ni层的厚度比例也可以改善此不良向客人提出改善设计的方案来改善漏镀不良电镀现场管理加强清洗工序的强度电镀产品表面晒纹效果尽量要均匀电镀现场管理加强对电流强度的管理电镀现场管理加强镀 Cr工艺的强度管理按时对电镀缸内的电镀液进行清洁,俗称‘清缸’提高产品表面的抛光精度 ( 半光产品抛光精度要求较高 8000N以上,全光产品抛光精度5000N以上)目前还没有非常有效的手段可以解决此问题,现行的改善方案为 : 电镀过程中后工序清洗追加超声波清洗以提高清洗的强度,另外对电镀完成品高温烘烤降低电镀品内部发生化学反应的可能性。
铝件镀银出现“黑斑”的原因及其消除

铝件镀银出现“黑斑”的原因及其消除1·原因分析1.1 材料上盖由0.5mm厚的LF21铝板材加工而成。
此型号导弹上有多种同材料、类似形状、同工艺的零件,比如盖子4、下盖等,而同时期加工的类似形状的零件并未出现此类故障。
比如,出现故障的上盖和未出现故障的盖子4等均由同批次板材加工而成。
因此,可以断定,并非原材料缺陷导致故障。
1.2 加工工艺上盖镀银的大致工艺路线为:机加来件─前处理─浸锌─电镀锌─电镀铜─电镀银─喷漆─浸涂823─入库。
1.2.1 电镀工艺首先,考虑到有可能是电镀的某个生产环节发生了改变,从而导致故障的产生。
经查,生产条件并未发生任何改变,且同时期加工的类似零件并未出现此类故障。
因此,排除了电镀生产条件发生改变的因素。
根据以往的生产经验,导致镀银件变色最常见的原因为硫元素对镀银层的影响。
之前,曾经发生过镀银后的零件未及时包装并密封保存,久置在电镀厂房中而导致镀银层变黄。
但是该故障零件镀银后,均及时包装并置于干燥器皿中保存,可见并非受到厂房空气气氛的影响。
1.2.2 喷漆工艺上盖的喷漆加工,出现过整批返修的纪录。
原因为缺口未堵上,使漆雾进入,并附着在镀银层表面而无法清除。
为防止此类故障的发生,加工过程中,常用3M胶带将缺口封死,以杜绝漆雾进入。
黑斑的出现,可能是因为缺口密封不严,使漆雾等有机气氛进入。
有机气氛从镀层空隙进入,从而腐蚀镀锌层。
镀锌层腐蚀产物从镀层空隙中泛出,表现为黑斑。
为此,做了以下实验来验证:在200倍放大镜下对“黑斑”进行拍照,并检查是否出现堆积或者腐蚀坑。
其照片如图1所示。
经测量,未出现堆积或腐蚀坑。
因此,排除了是漆雾腐蚀镀锌层或镀锌层腐蚀物从银层下泛出而导致“黑斑”的可能性。
1.3 “黑斑”成分分析在理化手段的协助下,对“黑斑”取样,进行了金相分析。
黑斑处和正常处截面照片如图2所示。
可以看出,上盖镀银面“黑斑”处与正常处没有区别,所以黑斑只是影响了镀银层的表面,而对镀银层内部并无影响。
常见电镀故障的分析和纠正方法

常见电镀故障的分析和纠正方法常见电镀故障的分析和纠正方法_1.针孔针孔大多是气体(一般是氢气)在镀件表面上停留而造成的。
针孔属于麻点,但针孔不同于麻点,它像流星一样,往往带有向上的“尾巴",而麻点仅仅是镀层上微小的凹坑,一般是没有向上的“尾巴"。
那些因素会促使镍层产生针孔呢?镀前处理不良;镀液中有油或有机杂质过多;镀液中有固体微粒;防针孔剂太少;镀液中铁等异金属杂质过多;镀液pH太高或操作电流密度过大;镀液中硼酸含量太少和镀液温度太低等都会导致镀镍层产生针孔。
由于不同原因引起的针孔现象略有不同,所以在分析故障时,首先要观察现象。
例如镀前处理不良,它仅仅使镀件的局部表面上的油或锈未彻底除去,造成这些部位上气体容易停留而产生针孔,所以这种因素造成的针孔现象是局部密集的,而且是无规则的;镀液中有油或有机杂质过多引起的针孔较多地出现在零件的向下面和挂具上部的零件上,镀液中固体微粒产生的针孔较多地出现在零件的向上面;防针孔剂太少造成的针孑L在零件的各个部位都有,镀液中铁杂质过多,pH值过高和阴极电流密度较大引起的针孔较多地出现在零件的尖端和边缘(即高电流密度处),硼酸含量太少产生的针孔较多地出现在零件的下部,镀液温度过低造成的针孔是稀少的,也是零件各个部位都有可能出现的。
通过观察现象,可以初步判断造成针孔的部分原因,然后再进一步试验。
例如零件的局部表面上有密集的针孔,从现象来看,好像是前处理不良造成的,那么究竟是不是这个原因呢?可以取一批零件,进行良好的前处理后直接镀镍,假使经这样处理后所得的镀层上没有针孔,那么原来的针孔是镀前处理不良造成的。
否则就是其他方面的原因。
镀液的温度、pH值和阴极电流密度,比较容易检查,所以可首先检查和纠正。
镀液中是否缺少十二烷基硫酸钠,从平时向镀液中补充十二烷基硫酸钠的情况就能基本确定,如难以确定时,可以向镀液中加入O.05g/L十二烷基硫酸钠后进行试镀,若这样所得的镀层上针孔现象没有改善,那就不是缺少十二烷基硫酸钠,可能是镀液中的杂质或硼酸太少引起的,这就可按前述的方法,用小试验分析故障原因,然后按试验所得的结果讲行纠正。
电镀常见的问题及解决方案

电镀常见的问题及解决方案
电镀过程中可能出现的问题及其解决方案如下:
1.针孔或麻点:这是由于前处理不良、有金属杂质、硼酸含量太少、镀液温度太低等原因造成的。
可以使用润湿剂来减小影响,并严格控制镀液维护及流程。
2.结合力低:如果铜镀层未经活化去氧化层,铜和镍之间的附着力就差,会产生镀层剥落现象。
因此,在电镀前应对基材进行适当的预处理,如酸洗、活化等。
3.镀层脆、可焊性差:这通常是由于有机物或重金属物质污染造成的。
添加剂过多会使镀层中夹带的有机物和分解产物增多,此时可以用活性炭处理或电解等方法除去重金属杂质。
4.镀层发暗和色泽不均匀:有金属污染可能是造成这一问题的原因。
应尽量减少挂具所沾的铜溶液,并在发现污染时立即处理。
5.镀层烧伤:这可能是由于硼酸不足、金属盐的浓度低、工作温度太低、电流密度太高、PH值太高或搅拌不充分等原因造成的。
需要检查并调整相关工艺参数,确保其处于合适的范围。
6.沉积速率低:PH值低或电流密度低都可能导致沉积速率低。
应检查并调整镀液的PH值和电流密度,以优化沉积速率。
7.其他问题:如辅助阳极的铜条未与生产板长度一致或已发粗,不允许再使用。
全板及图形镀后板需在24小时内制作下工序。
图形镀上板戴细纱手套,下板戴棕胶手套,全板上板戴橡胶手套,下板戴干燥的粗纱手套。
在处理电镀问题时,需要综合考虑多个因素,包括镀液成分、设备状况、操作条件等。
如遇到难以解决的问题,建议寻求专业人士的帮助。
电镀常见故障原因与排除
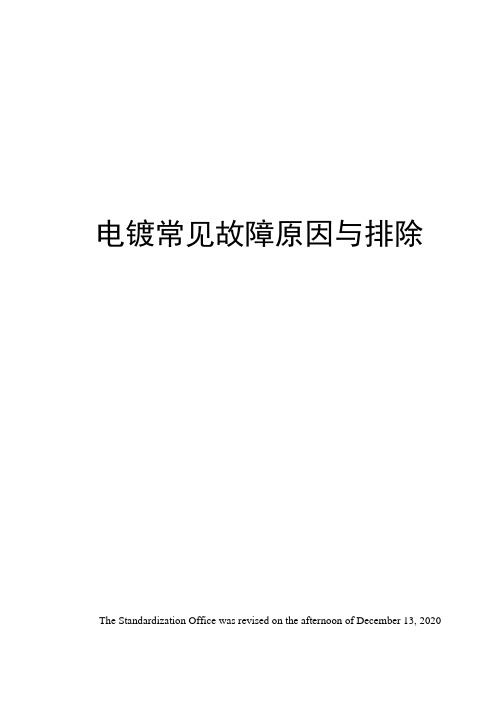
镀液有油或有机杂质过多 3. 镀液浑浊.PH 太高
2. 双氧水-活性燥处理
4. 基体组织不良
3. 调整 PH 值,加强过濾
1. 镀液铜含虽太少
1. 分析成分,调整 P 比正常范
2. 镀液温度太低 3. 镀液中有低根污染 1. 有机朵质过多
围
2. 提高温度至正常范囤
3. 加入茶升/升 30$双氧水,搅 拌 30 分钟
2. 有铁杂质/有机杂质过 1.
多
2.
1. 镀液 PH 值过高
1.
2. 柔软剂太少
2.
3.
有少量辂酸盐/磷酸盐/
3.
铅
补加 DY 主光剂 加 DY 除铁水或炭粉吸附 提高 PH 值 添加 DY 柔软剂 处理方法同上
镀偌常见故障原因与排除方法
故障现彖
故障原因 1. 镀前活化酸太稀或太浓
2. 表面有油或抛光膏
镀层疏松 孔隙多
1. 阳极钝化
1. 同上处理方法
2.
镀液中碳酸盐过多或有粘胶状
2.
同上处理方法
的杂质
3. 要经过二次浸锌后再进行镀铜
3・ 锌•铝合金基体中铝含呈过高
酸性镀铜常见故障原因与排除方法
故障现铁
故障原因
1. 前处理不良,零件表面有油
故障排除方法 1. 清除表面油脂
2. 淸洗水有油或镀液有油
6 •用双氧水-活性炭处理 1. 加强预镀层质址
2・检査挂具导电性
3. 光剂 A 含虽偏低
3. 补加 A 刘
低电流区
1. 镀液中一价铜较多
4. 添加 30%双氧水毫升/升
镀层不亮
5. 温度过高
5. 采用冷冻降温
6. 硫酸含量偏低
氰化物镀银液的常见故障分析及处理方法

1 常 见 故 障分 析及 处 理 方 法
1 . 1 镀层 结 晶粗 糙 、 发黄 。 阳极 易钝 化 ( 1 )银 的质 量浓 度 高 。应 分 析后稀 释镀 液 。 ( 2 )游离 氰化 钾不 足 。应 分析 后补 充氰 化钾 。
2 0 1 7 年5 月
・
电镀 与 环保
第3 7 卷第 3 期( 总第 2 1 5 期) ・5 9・
经 验 ・
氰 化 物 镀 银 液 的 常 见 故 障 分 析 及 处 理 方 法
茅 红 裕
( 江 苏省 海 门市常 乐镇 培 育村 1 4组 2 3号 , 江苏 海门 2 2 6 1 2 4 )
极 移动 和连 续过 滤 。
( 1 )银 的质量 浓度 低 。应分 析后 补充 硝 酸银 。 ( 2 )氰 化 钾 的 质 量 浓 度 高 。应 分 析 之 后 补 充
硝 酸银 。
1 . 9 滚 镀 时零件 粗糙 , 镀 层 呈橘皮 状 ( 1 )镀 前处 理不 良。应严 格 加强前 处 理 。 ( 2 )有 置换 银层 。应 加 强预 镀 , 带 电入 槽 。 ( 3 )阴极 电流密 度 大 。应 降低 阴极 电流密度 。 ( 4 )游 离氰 化钾 的质 量浓 度 过 低 。应分 析 后 补 充氰 化钾 。 1 . 1 0 铜 及铜 合金 镀银 后 有断 裂现 象 ( 1 )零件 材质 的内应 力太 大 。零 件施 镀 前 应进
中图分 类 号 : TQ 1 5 3 文 献标 志码 : B 文 章编 号 : 1 0 0 0 — 4 7 4 2 ( 2 0 1 7 ) 0 3 — 0 0 5 9 — 0 1
电镀不良的一些情况和解决方法

电镀不良的一些情况和解决方法电镀不良对策镀层品质不良的发生多半为电镀条件,电镀设备或电镀药水的异常,及人为疏忽所致.通常在现场发生不良时比较容易找出塬因克服,但电镀后经过一段时间才发生不良就比较棘手.然而日后与环境中的酸气,氧气,水分等接触,加速氧化腐蚀作用也是必须注意的.以下本章将对电镀不良的发生塬因及改善的对策加以探讨说明.1.表面粗糙:指不平整,不光亮的表面,通常成粗白状(1)可能发生的塬因: (2)改善对策:1.素材表面严重粗糙,镀层无法覆盖平整. 1.若为素材严重粗糙,立即停产并通知客户.2.金属传动轮表面粗糙,且压合过紧,以至于压伤. 2.若传动轮粗糙,可换备用品使用并检查压合紧度.3.电流密度稍微偏高,部分表面不亮粗糙(尚未烧焦) 3.计算电流密度是否操作过高,若是应降低电流4.浴温过低,一般镀镍才会发生) 4.待清晰度回升再开机,或降低电流,并立即检查温控系统.5.PH值过高或过低,一般镀镍或镀金(过低不会)皆会发生. 5.立即调整PH至标准范围.6.前处理药液腐蚀底材. 6.查核前处理药剂,稀释药剂或更换药剂2.沾附异物:指端子表面附着之污物.(1)可能发生的塬因: (2)改善对策:1.水洗不干净或水质不良(如有微菌). 1.清洗水槽并更换新水.2.占到收料系统之机械油污. 2.将有油污处做以遮蔽.3.素材带有类似胶状物,于前处理流程无法去除. 3.须先以溶剂浸泡处理.4.收料时落地沾到泥土污物. 4.避免落地,若已沾附泥土可用吹气清洁,浸透量很多时,建议重新清洗一次.5.锡铅结晶物沾附 5.立即去除结晶物.6刷镀羊毛?纤维丝 6.更换羊毛?并检查接触压力.7.纸带溶解纤维丝. 7.清槽.8.皮带脱落屑. 8.更换皮带.3.密着性不良:指镀层有剥落.起皮,起泡等现象.(1)可能发生的塬因: (2).改善对策:1.前处理不良,如剥镍. 1.加强前处理.2.阴极接触不良放电,如剥镍,镍剥金,镍剥锡铅. 2.检查阴极是否接触不良,适时调整.3.镀液受到严重污染. 3.更换药水4.产速太慢,底层再次氧化,如镍层在金槽氧化(或金还塬),剥锡铅. 4,电镀前须再次活化.5.水洗不干净. 5.更换新水,必要时清洗水槽.6.素材氧化严重,如氧化斑,热处理后氧化膜. 6.必须先做除锈及去氧化膜处理,一般使用化学抛光或电解抛光.7.停机化学置换反应造成. 7.必免停机或剪除不良品8,操作电压太高,阴极导电头及镀件发热,造成镀层氧化. 8.降低操作电压或检查导线接触状况9,底层电镀不良(如烧焦),造成下一层剥落. 9.改善底层电镀品质.10.严重.烧焦所形成剥落 10.参考NO12处理对策.4.露铜:可清楚看见铜色或黄黑色于低电流处(凹槽处)(1)可能发生塬因: (2)改善对策:1.前处理不良,油脂,氧化物.异物尚未除去,镀层无法析出. 1.加强前处理或降低产速2.操作电流密度太低,导致低电流区,镀层无法析出. 2.重新计算电镀条件.3镍光泽剂过量,导致低电流区,镀层无法析出 3.处理药水,去除过多光泽剂或更新.4.严重刮伤造成露铜. 4.检查电镀流程,(查参考NO5)5.未镀到. 5.调整电流位置.5刮伤:指水平线条状,一般在锡铅镀层比较容易发生.(1)可能发生的塬因: (2)改善对策:1.素材本身在冲压时,及造成刮伤. 1.停止生产,待与客户联系.2.被电镀设备中的金属制具刮伤,如阴极头,烤箱定位器,导轮等. 2.检查电镀流程,适时调整设备和制具.3.被电镀结晶物刮伤. 3.停止生产,立即去除结晶物.6.变形(刮歪):指端子形状已经偏离塬有尺寸或位置.(1)可能发生的塬因: (2)改善对策:1.素材本身在冲压时,或运输时,即造成变形. 1.停止生产,待与客户联系.2.被电镀设备,制具刮歪(如吹气.定位器,振荡器,槽口,回转轮) 2.检查电镀流程,适时调整设备和制具.3.盘子过小或卷绕不良,导致出入料时刮歪 3.停止生产,适时调整盘子4.传动轮转歪, 4.修正传动轮或变更传动方式.7压伤:指不规则形状之凹洞可能发生的塬因:改善对策:1)本身在冲床加工时,已经压伤,镀层无法覆盖平整2)传动轮松动或故障不良,造成压合时伤到 1)停止生産,待与客户联2)检查传动机构,或更换备品8白雾:指镀层表面卡一层云雾状,不光亮但平整可能发生的塬因:1)前处理不良2)镀液受污染3)锡铅层爱到酸腐蚀,如停机时受到锡铅液腐蚀4)锡铅药水温度过高5)锡铅电流密度过低6)光泽剂不足7)传致力轮脏污8)锡铅电久进,産生泡沫附着造成改善对策:1)加强前处理2)更换药水并提纯污染液3)避免停机,若无法避免时,剪除不良4)立即检查温控系统,并重新设定温度5)提高电流密度6)补足不泽剂传动轮7)清洁传动轮8)立即去除泡沫9针孔:指成群、细小圆洞状(似被钟扎状)可能发生的塬因:改善对策:1.操作的电流密度太 1.降低电流密度2.电镀溶液表面张力过大,湿润剂不足。
镀层常见故障的分析和纠正

常见故障的分析和纠正(酸锌)常见故障的分析和纠正(1)镀层起泡,结合力不好。
镀前处理不良;镀液中添加剂过多;硼酸含量过低同时阴极电流密度过大等会使镀层起泡,造成结合力不好。
镀液中添加剂含量过多,则阴极表面上吸附了较多的有机添加剂,导致阴极表面憎水,同时它还会夹附于镀层内,造成镀层与基体金属间晶格不连续而结合不牢;镀液中硼酸含量低,阴极膜中pH容易升高,同时电流密度过大,阴极膜中pH更高,容易造成金属的氢氧化物或碱式盐夹附于镀层内,影响镀层晶格的正常排列,从而造成镀层结合不牢。
硼酸含量低,电流密度大造成的结合力不好较多地出现在零件的尖端和边缘,出现这类现象时,一方面检查电流,另一方面分析硼酸含量,然后按检查和分析结果进行纠正。
在排除了硼酸含量和电流密度的影响后,再加强镀前处理或用良好的镀前处理与原来的操作进行对比,检查镀前处理是否有问题。
另外用赫尔槽试验检查添加剂的含量。
当发现添加剂含量过高,可用电解或活性炭处理降低其含量。
(2)镀层粗糙。
镀液中锌含量过高;添加剂含量偏低;温度过高或镀液中有固体微粒等都会使镀层粗糙。
镀液中锌含量和温度升高,添加剂含量降低,都是降低阴极极化,导致镀层粗糙。
假使在电镀过程中,镀液温度有升高的趋势,那么最好装置冷却设备。
假使温度略微偏高而没有冷却设备,也可加入适量的苯甲酸钠,以改善镀层的结晶组织。
添加剂含量的多少,可用前述的赫尔槽试验确定,同时还可以从一些现象进行观察,因为添加剂含量偏低时,不但镀层粗糙,同时镀层的光泽差,电流密度的范围比较狭小,低电流密度处镀层色暗,当同时出现这些现象时,再在赫尔槽试验的溶液中,加入适量的添加剂后进行试验,观察阴极样板上的镀层状况,若有好转,可向镀液中补充添加剂。
镀液中的锌含量,可按分析进行调整。
发现锌含量过高时,一方面要稀释镀液,将其浓度调节在工艺范围内,另一方面要减少阳极面积,防止锌含量继续升高。
确定镀液中是否有固体微粒,一种方法是在搅拌镀液的情况下,用500mL(或1000mL)的量杯取一杯镀液,将它放置在强烈的光线下观察;另一方法是用定量滤纸过滤少量镀液,然后观察滤纸上同体微粒的多少,从而估计镀液中固体微粒的含量,若镀液中固体杂质较多,就应过滤镀液,除去这类杂质。
镀银调整

镀银故障的快速处理
1.镀层粗糙
有些零件的镀银要求有一定的厚度,操作者在工艺过程中往往采用电流密度的上限或稍大一些操作。
在槽液成分稍有变化的情况下镀取的银层往往粗糙,有时用10倍放大镜检查就更清晰可见。
根据有关资料和我们镀银槽的使用情况分析,除电流密度过大原因外,再就是槽液中游离氰化物少的缘故。
另外,在同样的电流密度条件下,银的含量增高也会导致镀层粗糙。
为此,我们严格了工艺条件和槽液的维护调整,规定了电镀分油盘和各类触点等零件银层厚度的时间和电流密度,在这种情况下粗糙现象,我们就按每升槽液补加 15g氰化钾的方法,效果明显。
镀银过程中进行抽查,也可以用5倍放大镜仔细检查,及时处理。
如20号分油盘,需镀银层厚度18um,按电流密度0.7A/dm2计算,时间约60分钟。
镀银10分钟后检查,如果发现粗糙后就应查验工艺全过程,并调整槽液和电流密度。
零件可用铜丝刷光后继续电镀。
2.沉积速度慢
按照规定的电流密度和时间,镀取的银层不够,这是我们有时遇到的问题。
在电流密度正常的条件下,出现这种情况,一般是银的含量偏低,有的是同槽电镀个别零件导电不好所致。
这种情况除及时补充增加银的含量外,还一般都加盖。
导电杠及挂具很容易氧化,特别是滴落了镀液的地方,会产生一层铜锈,不清除干净,有时就会造成接触不良。
因此,镀银时,除对导电系统要彻底清洗以外,镀银过程中还要正确摆挂阳极,零件加厚面一定要面对极板,电镀时注意经常晃动零件,避免个别零件中途断电,影响银层厚度的增加。
如果能及时化验槽掖,根据化验结果调整就更好了。
提高镀银质量及镀银故障处理

提高镀银质量及镀银故障处理【摘要】本文通过介绍本公司镀银生产过程中所遇到的一些常年积累下的镀银层质量问题,详细分析产生各种镀层弊病的原因和解决方法。
并以近年来的一次镀银槽液大处理为实例,详细地从实验室试验确定方案、车间现场解决克服困难组织过滤、过滤后镀液调整分析讨论等方面阐述了一次镀液过滤处理,从而从根本上提高镀银质量的成功经验。
为今后进一步提高和维护公司镀银产品质量作出贡献,也为广大电镀工作者留下宝贵借鉴。
【关键词】镀银质量;故障;过滤1 镀银工艺简介1.1 镀银工艺发展史镀银最早使用的光亮剂二硫化碳是Milword和Lyons在1847年提出的,至今还在使用[1]。
自上世纪70年代开始了大量无氰镀银工艺的研究,国内广大电镀工作者也在无氰镀银方面做了大量工作,但至今无重大突破。
所以在国内生产中基本上采用的仍是百年来沿用的氰化物镀银液。
1.2 镀银工艺运用范围银是一种白色光亮、可锻及可塑的金属。
银覆盖层具有优良的导热性、电导率;易于抛光,有优良的反光性能;焊接性能和结合强度良好等优点。
故在电子工业、通讯设备、仪器仪表、飞机、光学仪器以及高频元件和波导等方面得到广泛应用。
银在碱液和某些有机酸中十分稳定;除硝酸外,在其他酸中也比较稳定;对水和大气中的氧不起作用。
因而在装饰件、餐具、徽章等工艺品方面得到应用。
[2]2 提高镀银质量及镀银故障处理的研究意义2.1 电镀班镀银质量问题简述随着这几年来对镀银产品外观、结合力及防变色能力日益提高的要求,相比外协镀银厂家,我公司的镀银件存在外观粗糙范黄、结合力,抗变色能力低下种种弊病。
发展到近年,所有镀银件都需加上手工刷光程序,外观才勉强合格,而有些甚至出现镀银件严重起皮现象。
2.2 本课题研究意义日益严重的镀银质量问题,使得一方面镀银件大量转入外协厂家电镀,一方面自己的电镀银件经常不合格,因此极大增加了成本,同时我厂镀银工艺也面临取消的尴尬境地。
短时间内提高镀银质量,并增强镀银故障解决效率,保障长期的镀银正常生产,并以高层次的镀银层质量来适应未来批量铝镀银的生产需要,成为笔者的工作重心。
镀银镀锡的故障的排除

镀银镀锡的故障的排除
镀银镀锡的故障的排除(1)稀释处理配制部分新溶液,按新、老溶液体积比为1∶3、1∶2、1∶1,分别进行赫尔槽试验,试片没有改观。
如继续降低老溶液比例进行实验,即使有改观效果,也没有实际意义,此解决余姚镀银镀锡故障的方案被否定。
(2)小电流电解处理取5L溶液,小电流电解处理1h,进行赫尔槽试验,没有明显效果,此解决余姚镀银镀锡故障的方案也被否定。
(3)吸附处理取5L镀液,按6mL的比例加入30%的双氧水(稀释3~5倍加入)后,搅拌30min,静置30min,加入活性炭8g/L,搅拌30min后,静置4h过滤,小电流电解处理4h后做赫尔槽试验,试片外观有明显改善,镀层均匀,低电流密度区尤其明显。
对镀液成分分析,镀液处理前后,氰化银和氰化钾含量分别减少了3g/L和6g/L,仍处于工艺范围中限值。
用上述处理好的镀液试镀,镀层均匀细致,分散能力好,Φ6mm、深70mm孔底部镀层厚度达到要求,零件在120℃下保温1h均没有出现起泡现象。
镀银常见故障的分析和纠正

镀银常见故障的分析和纠正1、镀银层色泽不白带有黄色这种现象特别在干燥后更为明显。
这种毛病在镀银中经常出现,造成的原因不止一种因素:(1)电流密度过高。
某厂新配滚镀银一星期中镀得很好,第二星期都按同样条件镀出的镀件,发现色泽带黄,经咨询后用最简单的措施就是降低阴极电流密度,故障就排除了,但为了保持镀层厚度,电镀时间需要延长。
究其原因实质上是一个星期来没有加料,镀液发生了变化,镀液中杂质的积累和银含量的降低,致使上述问题产生,这种毛病如果提高银含量也能解决,若按照化验加料就不会发生这类问题,往往好多镀银液不常化验,凭经验操作就容易出现此问题。
(2)氰化钾含量太低形成镀层色泽不白带有黄色,并且镀层与正常比较不够细致,感觉粗糙,产生这种情况时,请注意阳极表面,一般在未镀时阳极表面是银白色,通电时阳极表面略为变暗,电流电压表显示正常。
氰化钾含量低时,通电时阳极表面黑膜增厚,停镀时黑膜一时不易退去,电流不易升高、电压容易上升,这种现象产生如果没有化验,则可逐步加入氰化钾使改变上述现象。
(3)镀银液中钠盐含量较多,钾盐的导电比钠盐好,但价格较贵且含氰量相对较低,因此有些工厂用氰化钠代替,这也是镀银层造成发黄的原因之一,钠离子在镀银液中会造成镀层略带黄色,因此要防止钠离子的带入。
(4)在光亮镀银液中银含量太低时,镀层也会呈微黄色,应及时补充氰化银钾,并适量添加氰化钾。
(5)光亮镀银如果镀液成分正常,镀层仍有微黄时在镀液中可加入O.3mL~lmL的磷酸,添加时应逐步加入到色泽合格为止。
2、银层起泡脱皮因为银镀层较软,它不会像镍镀层脱皮下来,所以起泡就是脱皮,是非镀层很厚可以成皮撕下,有时用光滑硬件在其表面摩擦,镀层会皱起来,这也属于起泡脱皮,造成起泡脱皮的原因主要是前处理不当,特别在铜基体上镀银更易发生,因为银容易被铜置换,被置换上的铜结合力不好,再在这结合力不好的置换层上镀上银,当然镀层的结合力也是不好的。
常规的镀银液,铜件浸入时不通电也会镀上银,这是置换银层,结合力不好,因此铜件镀银前必须要经过镀前处理,传统的处理方法是汞齐化(如:氧化汞5g/L,氰化钾50g/L)处理,铜在汞齐化溶液中浸过后表面生成一层铜汞层、,再镀银时可以防止银的置换,因为汞有毒,妨害环境,严格禁止使用,因此现在都用预镀银来代替,同样有效。
镀银不良分析报告模板

镀银不良分析报告模板
1. 前言
该报告主要分析镀银过程中出现的不良情况,统计不良率,分析影响因素,提出改进方案等。
通过本次分析对生产过程进行优化,提升产品质量。
2. 不良情况概述
经过统计,镀银过程中出现的不良品数量为200个,占总产量的3%。
不良情况主要表现为以下几个方面:
•涂层均匀性不好,出现白斑
•镀银层厚度不均匀
•镀银层出现气泡
•镀银层出现黑斑
3. 不良率分析
根据对镀银过程中的不良品数量进行统计,计算出不良率为3%。
不良率的计算方式如下:
不良率 = 不良品数量 ÷ 总产量 × 100%
4. 影响因素分析
在对镀银过程中出现的不良情况进行深入分析后,总结出如下几个可能的影响因素:
•镀液中镀银液浓度不均匀
•水质不良导致气泡和斑点
•镀液温度过高或过低
•镀银前处理工艺不完善
5. 改进方案
针对以上影响因素,提出如下改进方案:
•对镀液进行均匀搅拌,保证浓度均匀
•定期检验水质,保证水质符合要求
•对镀液温度进行严格控制,保证在合适的范围内
•完善镀银前处理工艺,保证金属基材表面干净平整
经过改进后,可以有效降低不良率,提升生产效率和产品质量。
6. 总结
通过本次镀银不良分析报告,我们了解到不良品情况的详细情况,并对影响因素进行了分析,提出了改进方案。
对生产质量进行了有效提升,同时也为下一步生产和质量控制工作提供了重要参考。
电镀常见故障原因与排除[宝典]
![电镀常见故障原因与排除[宝典]](https://img.taocdn.com/s3/m/8906ce48302b3169a45177232f60ddccda38e6b9.png)
常见故障原因与排除3.导电不良4.铬酸含量太低5.三价铬或异金属杂质过多6.有硝酸根存在3. 检查线路4. 补充铬酐5. 电解法除去6. 用电解法镀层脱落1.镀铬过程中断电2.阴极电流密度过大3.底层镍钝化或底镀层上有油1. 检查线路2. 降低电流密度3. 加强前处理镀层表面粗糙1. 底镀层本身较粗糙2. 镀液中有微细固体粒子3. 硫酸含量过低4. 阴极电流密度过大1.加强底层质量2.过滤3.提高硫酸含量4.降低电密度氯化物酸性镀锌常见故障原因与排除方法故障现象故障原因故障排除方法镀层起泡结合力不好1.镀前处理不良2.添加剂过多3.硼酸过低4.阴极电流密度过大1.加强前处理2.用活性炭吸附3.补充硼酸4.降低电流密度镀层粗糙1.锌含量过高2.DY添加剂含量偏少3.温度过高4.镀液中有固体微粒1. 析成分,冲稀镀液2. 补充DY添加剂3. 采用冷冻设备,控制温度正常值4. 加强过滤镀层上出现黑色条纹或斑点1.前处理不良2.阴极电流密度过大3.镀液中氯化物太少4.有机杂质过多5.有较多的铜铅杂质1.加强除油除锈2.降低电流密度3.分析成份,提高氯化物含量4.建议用双氧水活性炭处理5.加入0.5-1克/升锌粉镀层容易烧焦1.氯化物含量不够2.锌含量低3.DY柔软剂不够4.PH太高1.分析成分,提高氯化物含量2.分析成分,提高锌含量3.补充柔软剂4.用稀盐酸调PH至5.5-6. 2低电流区镀层灰暗1.镀液温度过高2.DY添加剂含量太少3.镀液中有铜/铅杂质1.采用冷冻设备,控制温度正常值2.补充添加剂3.加入0.5-1克/升锌粉或加除杂水镀层光泽差1.镀液中DY添加剂太少2.温度太高3.PH太高或太低1.补充DY添加剂0.1-0.2毫升/升2. 采用冷冻设备,控制温度正常值3. 用稀盐酸调PH至5.5-6.2氰化物镀锌常见故障原因与排除方法故障现象故障原因故障排除方法镀层结合力不好 1.前处理不良 1. 加强前处理。
电镀不良之原因分析及防范措施
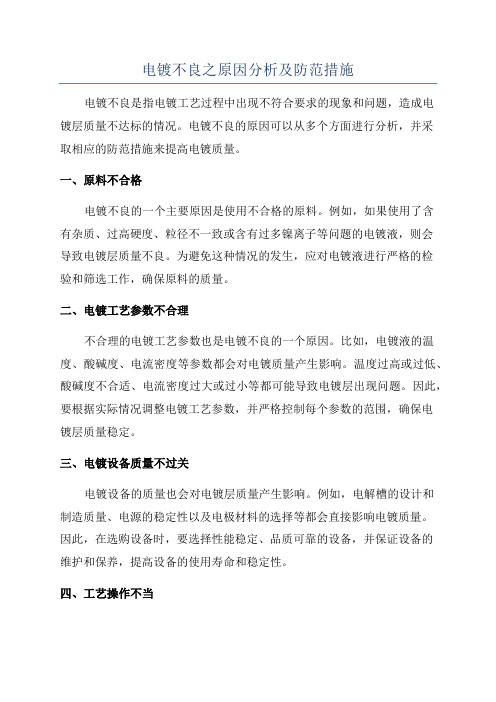
电镀不良之原因分析及防范措施电镀不良是指电镀工艺过程中出现不符合要求的现象和问题,造成电镀层质量不达标的情况。
电镀不良的原因可以从多个方面进行分析,并采取相应的防范措施来提高电镀质量。
一、原料不合格电镀不良的一个主要原因是使用不合格的原料。
例如,如果使用了含有杂质、过高硬度、粒径不一致或含有过多镍离子等问题的电镀液,则会导致电镀层质量不良。
为避免这种情况的发生,应对电镀液进行严格的检验和筛选工作,确保原料的质量。
二、电镀工艺参数不合理不合理的电镀工艺参数也是电镀不良的一个原因。
比如,电镀液的温度、酸碱度、电流密度等参数都会对电镀质量产生影响。
温度过高或过低、酸碱度不合适、电流密度过大或过小等都可能导致电镀层出现问题。
因此,要根据实际情况调整电镀工艺参数,并严格控制每个参数的范围,确保电镀层质量稳定。
三、电镀设备质量不过关电镀设备的质量也会对电镀层质量产生影响。
例如,电解槽的设计和制造质量、电源的稳定性以及电极材料的选择等都会直接影响电镀质量。
因此,在选购设备时,要选择性能稳定、品质可靠的设备,并保证设备的维护和保养,提高设备的使用寿命和稳定性。
四、工艺操作不当不正确的工艺操作也是电镀不良的一个常见原因。
例如,电镀工艺操作的速度太快或太慢,工件的浸泡时间控制不准确等都可能导致电镀层质量不良。
因此,操作人员在进行电镀工艺操作时要严格按照程序进行,并且进行必要的培训和技术指导,提高工艺操作的准确性和稳定性。
综上所述,电镀不良的原因可以从原料、工艺参数、设备质量和工艺操作等多个方面进行分析。
为了防范电镀不良的发生,可以采取以下措施:1.选用优质的原料,并进行严格检验和筛选;2.根据实际情况调整电镀工艺参数,并进行严格的控制;3.选购品质可靠的设备,并保证设备的维护和保养;4.进行工艺操作前进行必要的培训和技术指导,确保操作的准确性和稳定性;5.建立完善的质量控制体系,对电镀过程进行监控和检测,及时处理不良产品;6.加强与供应商的合作,建立长期稳定的合作关系,确保原料和设备质量的稳定性。
镀金镀银件变色原因及对策

接插件镀金、镀银层变色原因及防变色措施镀金层的变色原因如下:基体质量不符合要求,产品的设计及电镀工艺存在缺陷(包括产品前处理工艺、金阻挡层镀液体系的选择、镀液的维护、电镀工艺参数的选择和电镀方式等的不妥当),镀后处理不力,产品使用环境的差异等镀银层变色的原因如下:基体形状复杂且其表面粗糙度高,电镀工艺不完善,包装方式不当,产品使用环境差异等。
1 前言在接插件的制造工艺中,为了保证产品的导电性能和可靠性,大部分产品的接触件以及部分产品的壳体均采用了镀金或镀银进行表面处理。
由于在产品的加工和使用过程中受到各种因素的影响,部分产品的镀层表面会在较短时间内出现变色现象。
而一旦镀层表面开始变色,产品的电气性能也会随之下降。
为了避免这种现象发生,针对金、银镀层的变色机理,人们采取了各种措施尽力延缓镀层在规定的时间内出现的颜色变化。
以下为目前在接插件制造行业中发生镀层变色原因的分析以及常用的解决镀金、镀银层变色问题的一些基本方法。
2 金镀层的变色原因金是一种比较稳定的金属元素,在大气环境中几乎不与其它物质反应,因此不会受到各种腐蚀气体侵袭而发生化学变化。
接插件金镀层变色的原因主要是受到基体金属(铜及铜合金)通过金层孔隙向镀层表面迁移的影响。
因为金层与基体金属之间存在着电位差,在遇到腐蚀介质时这种电位差会导致基体金属被腐蚀,当腐蚀物富集在金层表面时金层就改变了颜色。
在接插件的制造行业中导致金层很快变色的原因主要还体现在以下几个方面。
2.1 基体质量达不到要求基材杂质含量和基体表面光洁度是两项衡量电接触体基体质量的重要指标。
近几年来,由于市场竞争加剧,加上金属材料涨价因素,使得一些基体制造厂为了降低生产成本,采用一些不合规格的材料,甚至采用回收铜加工制造基体。
由于杂质超标,基材脆性增大,在机加工时部分镀件的基体会产生不易察觉的微裂纹(有时也会因电镀时的渗氢作用产生这种微裂纹)。
我厂2000年初在电镀某种高频电连接器外壳时,由于外壳的基体材料是采用回收铜制作,故经振动电镀金后,盛镀件的振筛底部会留下一层铜粉,其中部分镀件的4只插脚仅剩下3只,镀件的凹下部位的金层几天就变成了褐色。
电镀处理中的电镀故障分析与排除

电镀处理中的电镀故障分析与排除随着工业化程度的逐步提高,电镀处理如今已经变得越来越常见。
电镀处理技术在现代工业生产中拥有着广泛的应用,尤其是在电子、汽车、航空等领域中都有着广泛的运用。
电镀处理能够使金属表面具备防腐、耐磨、美化、导电、抗氧化、增加光泽等功能,因此也成为了现代工业中不可缺少的一环。
而在电镀处理中,难免会遇到各种电镀故障,如何准确地判断故障原因,排除故障,是我们在电镀处理过程中需要面临的问题。
本文将从电镀故障产生的原因和种类、电镀故障的分析方法和处理措施等几个方面来展开阐述。
一、电镀故障的产生原因和种类1. 电镀异质金属在电镀处理过程中,电镀池中的异质金属是产生电镀故障的主要原因之一。
异质金属能够进入电镀池中并污染电极板,导致电极板出现气孔、颗粒等缺陷。
同时,由于异质金属的存在,电极板表面的颜色和光泽也会受到影响。
2. 电流不稳定电流不稳定也会导致电镀故障的发生。
而电流不稳定的原因主要包括电源电压、电源输出电流、电极板与电源之间的接触等。
3. 水和空气的污染在电镀池中,水和空气中的污染物也会污染电极板,并导致电镀故障的发生。
这些污染物包括微生物、异物、有机物等。
这些污染物能够附着在电极板上,污染表面,导致表面出现不均匀的颜色、凹凸不平等问题。
二、电镀故障的分析方法1. 观察外观观察电极板表面的外观可以获得很多线索。
通常情况下,电极板出现的问题,如颜色、水泡、气孔等,都能够通过观察表面得到反应。
通过观察外观,我们可以初步判断故障出现的位置以及与何种因素有关。
2. 检测电流稳定性在电镀处理过程中,电流的稳定性是至关重要的。
检测电流的稳定性可以通过对电源电压和电源负载电流的波动进行分析。
如果电压和电流波动较大,说明电流不稳定,那么就需要对电源进行维护或更换。
3. 化学分析在一些特殊情况下,我们需要进行化学分析来检测电镀故障的原因。
这种方法主要适用于难以通过外观观察或电容法检测得到的故障原因。
镀银常见的缺陷及改善措施

镀银常见的缺陷及改善措施镀银是一种常见的表面处理方法,可以使物体具有良好的抗氧化性和美观性。
然而,镀银过程中常常会出现一些缺陷,影响了镀银的质量和效果。
本文将探讨镀银常见的缺陷,并提出相应的改善措施。
1. 镀银缺陷之一:气泡在镀银过程中,若未能完全排除基材表面的气体,就会在镀银层中形成气泡。
这些气泡会破坏镀银层的致密性和光亮度,影响镀银的效果。
为了解决这一问题,可以采取以下改善措施:(1)在镀银前,对基材进行充分的净化处理,避免表面存在杂质和气体。
(2)控制镀银过程中的温度和压力,确保银离子能够均匀分布并覆盖基材表面,减少气泡的产生。
2. 镀银缺陷之二:黑斑黑斑是镀银中常见的缺陷之一,它是由于银层中存在杂质或不均匀沉积导致的。
黑斑的存在会影响镀银层的均匀性和光泽度,降低镀银产品的质量。
为了解决这一问题,可以采取以下改善措施:(1)在镀银前,对基材进行彻底的清洗和抛光,确保表面光滑无杂质。
(2)优化镀银工艺参数,控制银离子的浓度、温度和电流密度,使其均匀沉积在基材表面,避免黑斑的产生。
3. 镀银缺陷之三:氧化镀银层在长时间暴露在空气中会发生氧化反应,形成氧化银。
这会导致镀银层变黑,失去原有的亮度和光泽度。
为了解决这一问题,可以采取以下改善措施:(1)在镀银后,对镀银层进行防护处理,如喷涂保护膜或进行密封处理,防止氧气的直接接触。
(2)对镀银产品进行适当的保养,避免长时间暴露在潮湿环境中,减少氧化的可能性。
4. 镀银缺陷之四:剥离剥离是指镀银层与基材之间发生分离或脱落的现象。
剥离会导致镀银层失去附着力,影响产品的使用寿命和美观度。
为了解决这一问题,可以采取以下改善措施:(1)确保基材表面的光洁度和粗糙度符合要求,提高镀银层与基材的结合力。
(2)优化镀银工艺参数,控制镀银层的厚度和均匀性,避免过厚或不均匀的镀银层导致剥离。
总结起来,镀银常见的缺陷包括气泡、黑斑、氧化和剥离等。
针对这些缺陷,可以通过净化基材、优化工艺参数、防护处理和保养等方式进行改善。
- 1、下载文档前请自行甄别文档内容的完整性,平台不提供额外的编辑、内容补充、找答案等附加服务。
- 2、"仅部分预览"的文档,不可在线预览部分如存在完整性等问题,可反馈申请退款(可完整预览的文档不适用该条件!)。
- 3、如文档侵犯您的权益,请联系客服反馈,我们会尽快为您处理(人工客服工作时间:9:00-18:30)。
镀银常见故障的分析和纠正
1、镀银层色泽不白带有黄色
这种现象特别在干燥后更为明显。
这种毛病在镀银中经常出现,造成的原因不止一种因素:
(1)电流密度过高。
某厂新配滚镀银一星期中镀得很好,第二星期都按同样条件镀出的镀件,发现色泽带黄,经咨询后用最简单的措施就是降低阴极电流密度,故障就排除了,但为了保持镀层厚度,电镀时间需要延长。
究其原因实质上是一个星期来没有加料,镀液发生了变化,镀液中杂质的积累和银含量的降低,致使上述问题产生,这种毛病如果提高银含
量也能解决,若按照化验加料就不会发生这类问题,往往好多镀银液不常化验,凭经验操作就容易出现此问题。
(2)氰化钾含量太低形成镀层色泽不白带有黄色,并且镀层与正常比较不够细致,感觉粗糙,产生这种情况时,请注意阳极表面,一般在未镀时阳极表面是银白色,通电时阳极表面略为变暗,电流电压表显示正常。
氰化钾含量低时,通电时阳极表面黑膜增厚,停镀时黑膜一时不易退去,电流不易升高、电压容易上升,这种现象产生如果没有化验,则可逐步加入氰化钾使改变上述现象。
(3)镀银液中钠盐含量较多,钾盐的导电比钠盐好,但价格较贵且含氰量相对较低,因此有些工厂用氰化钠代替,这也是镀银层造成发黄的原因之一,钠离子在镀银液中会造成镀层略带黄色,因此要防止钠离子的带入。
(4)在光亮镀银液中银含量太低时,镀层也会呈微黄色,应及时补充氰化银钾,并适量添加氰化钾。
(5)光亮镀银如果镀液成分正常,镀层仍有微黄时在镀液中可加入O.3mL~lmL的磷酸,添加时应逐步加入到色泽合格为止。
2、银层起泡脱皮
因为银镀层较软,它不会像镍镀层脱皮下来,所以起泡就是脱皮,是非镀层很厚可以成皮撕下,有时用光滑硬件在其表面摩擦,镀层会皱起来,这也属于起泡脱皮,造成起泡脱皮的原因主要是前处理不当,特别在铜基体上镀银更易发生,因为银容易被铜置换,被置换上的铜结合力不好,再在这结合力不好的置换层上镀上银,当然镀层的结合力也是不好的。
常规的镀银液,铜件浸入时不通电也会镀上银,这是置换银层,结合力不好,因此铜件镀银前必须要经过镀前处理,传统的处理方法是汞齐化(如:氧化汞5g/L,氰化钾50g/L)处理,铜在汞齐化溶液中浸过后表面生成一层铜汞层、,再镀银时可以防止银的置换,因为汞有毒,妨害环境,严格禁止使用,因此现在都用预镀银来代替,同样有效。
预镀银实际是低银离子的氰化镀银液,由于银离子的浓度很低,作为络合剂的氰化钾浓度较高,
使银不易在铜上置换,一般预镀银液中氰化银1.5g/L~3g/L,氰化钾70g/L~90g/L。
也可将常规镀银液取出一些,稀释后加氰化钾来配制,使铜件浸入镀液时不会置换银而在通电后才能镀上银镀层。
改善镀层的结合力。
3、光亮镀银层容易变色
镀银光亮剂一般都是有机物为主的添加剂,大致分为基础光亮剂,小电流区光亮剂和大电流区光亮剂,这些光亮剂添加太多时,往往会造成银层容易变色,因此以尽量少加勤加为宜,谨慎处置,按供应商的说明控制添加总量,但添加时切勿一次加入,可边加边观察镀层质量,一旦达到镀层要求就不再多加。
供应商提供的仅是一般参考值,各厂各产品的质量要求和条件不同,必须要有自己的一套添加方法,才能使产品质量做得更好。
4、银镀层粗糙,银层不细致
若其他成分都正常,且是很老的镀银液,则有可能是碳酸盐累积过多了,一般情况下碳酸盐是不会有问题的,因此不要轻易认为粗糙就是碳酸盐过多,只有在各种方法都不能处理好粗糙的毛病,又发现在冷却的条件下镀液中有沉淀或槽边有白色沉积物(碳酸盐)时,才需要处理碳酸盐。
处理方法:
(1)如果在冬天,可以让镀液自然冷却,在10°C以下,将过多的碳酸盐结晶与镀液分离即可。
镀液抽出后,槽边和槽底的结晶可弃入氰化物废水池。
(2)用化学沉淀法,以氢氧化钙0.5g去除lg碳酸盐的比例加入,氢氧化钙最好用新鲜的加入,效果较好。
新鲜的氢氧化钙可以用氧化钙的水调成糊状后加入,加人量不必严格,多余的氧化钙不会有害镀液。