中英文生产作业指导书
生产作业指导书英文
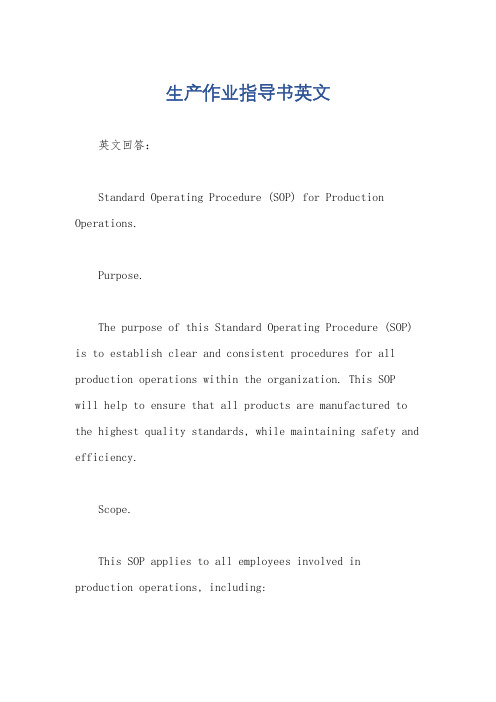
生产作业指导书英文英文回答:Standard Operating Procedure (SOP) for Production Operations.Purpose.The purpose of this Standard Operating Procedure (SOP) is to establish clear and consistent procedures for all production operations within the organization. This SOPwill help to ensure that all products are manufactured to the highest quality standards, while maintaining safety and efficiency.Scope.This SOP applies to all employees involved in production operations, including:Production operators.Supervisors.Quality control inspectors.Maintenance personnel.Definitions.Batch: A specific quantity of product that is produced at one time.Lot: A group of batches that are produced under the same conditions.Operating Procedure: A set of instructions that describes how a specific task should be performed.Quality Control: The process of ensuring that products meet the required specifications.Standard Operating Procedure (SOP): A document that describes the standard procedures for a specific operation.Procedures.1. Pre-Production Planning.Review production schedule and ensure that all necessary materials and equipment are available.Calibrate and verify all equipment to ensure accuracy and functionality.Train operators on the specific production procedures for the scheduled products.2. Production.Follow the established operating procedures for each production task.Monitor production processes closely and makenecessary adjustments to maintain quality standards.Record all production data, including batch numbers, lot numbers, and any deviations from standard procedures.3. Quality Control.Inspect products at regular intervals to ensure they meet the required specifications.Conduct final inspections on completed products before they are released for distribution.Document all quality control inspections and any corrective actions taken.4. Maintenance.Perform regular maintenance on all equipment to prevent breakdowns and ensure optimal performance.Keep a maintenance log to record all maintenanceactivities and repairs.Calibrate and verify equipment regularly to ensure accuracy and functionality.5. Continuous Improvement.Monitor production processes and identify areas for improvement.Implement process improvements to enhance efficiency, reduce costs, and improve product quality.Train employees on new or updated operating procedures.6. Safety.Adhere to all safety regulations and wear appropriate personal protective equipment (PPE).Identify and mitigate potential hazards in the production area.Report all accidents and near-misses to the safety department.7. Documentation.Maintain a production log to record all production activities, including batch numbers, lot numbers, and any deviations from standard procedures.Keep quality control records, including inspection reports and corrective action plans.Retain maintenance logs for all equipment.8. Training.Provide comprehensive training to all employees involved in production operations.Train employees on specific operating procedures, quality control methods, and safety regulations.Conduct refresher training on a regular basis.9. Management Responsibility.Supervisors are responsible for ensuring that production operations are conducted in accordance with this SOP.Supervisors are responsible for providing training, monitoring production processes, and implementingcorrective actions.Management is responsible for reviewing and approving this SOP, as well as any updates or revisions.10. Performance Monitoring.Regularly review production metrics, including efficiency, quality, and safety.Identify trends and areas for improvement.Implement corrective actions to address any performance issues.Review and Revision History.This SOP will be reviewed and revised as needed to ensure that it remains current and effective. All revisions will be documented and approved by management.中文回答:生产作业指导书。
workinstructiontemplate作业指导书模板英文版

TITLE of ELEMENTRevision: A Page 1 of 2WORK INSTRUCTION01-01-011.0 PURPOSE1.1(What is the reason for writing this work instruction) Start with the following statement:purpose of this document is to provide instructions for - - - - - - - - .” 1.2Be as specific as you need to be to define the purpose of the document.2.0 SCOPE2.1(Define the area or process that this instruction applies to)3.0 RECORDS3.1(Indicate specific type of records to be maintained and where they will be maintained)4.0 ASSOCIATED DOCUMENTS4.1(Reference upward to the procedures that the work instruction is controlled by andreference forms by control number used to create records. Also, reference other documents, standards or information that are relevant.)5.0 DEFINITIONS5.1(Define any terms and phrases that might be unique to this instruction or to this particularindustry)6.0 RESPONSIBILITY6.1(List department(s) or functions responsible for maintaining these instructions)7.0 TOOLS, GAGES, FIXTURES7.1(List all unique tools required to perform tasks as indicated in this work instruction)8.0 SAFETY REQUIREMENTS8.1(List all necessary safety precautions that employees must comply with and all safetyequipment that must be used while following the operations specified in this work instruction)9.0 INSTRUCTIONS9.1(List all steps to be taken to complete the scope of this work instruction, in the exactsequence necessary. Work instructions may be in the form of flow charts, bulletinstructions, text, photos, digitized images, numbered instructions or any combination of all, as long as the instructions are clear, crisp and do the job as intended)。
生产作业指导书-ENG-PMP
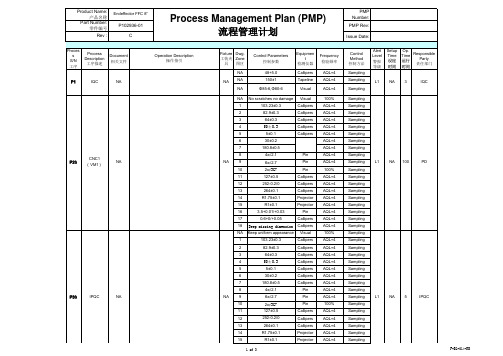
PMP Number: PMP Rev: Issue Date:
Alert Level 警报 等级 Setup Time 设定 时间 Op. Responsible Time Party 运行 责任部门 时间
Process Description 工序描述
Document 相关文件
Equipment 检测仪器 Callipers Tapeline Visual Visual Callipers Callipers Callipers Callipers Callipers
P60
DB
NA
2 3 4 1
L1
NA
5
IPQC
P70
WC
NA
NA
2 3 4
L1
NA
3
IQC
P80
SC
NA
NA
NA NA
L1
SB
120
SQE
P90
IQC
NA
NA
1 2 3
L1
NA
3
IQC
P100 P110
PA OQC
NA NA
NA NA
NA NA
L1 L1
NA NA
2 2
PD OQC
Remark: 工序必须做首件确认,未明确注明的尺寸单位为INCH Type of Instrument used : BG=Block Gauge(块规); RG=Ring Gauge(环规); CMM=Coordinate Measuring Machine(三坐标); DM=Depth Micrometer(深度千分尺); DG=Dial Gauge(千分表); TG=Thread Gauge(牙规);'EMM=External Micrometer(外径千分尺); HG=Height Gauge(高度仪); HT=Hardness Te Alert Level: L1:Inform Supervisor(通知现场主管) L2:Inform QE/PD MGR(通知生产经理及质量工程师) L3:Inform QA MGR/MR(通知质量经理及管理者代表) L4:Inform GM(通知总经理) Sampling Size: Specify or As per AQL, ISO2859, Single sampling, Level 2 (如无特别要求,则按照标准ISO2859,单次抽样,2级水平检验).
文件变更通知(DCN)生成作业指导书-中英文对照
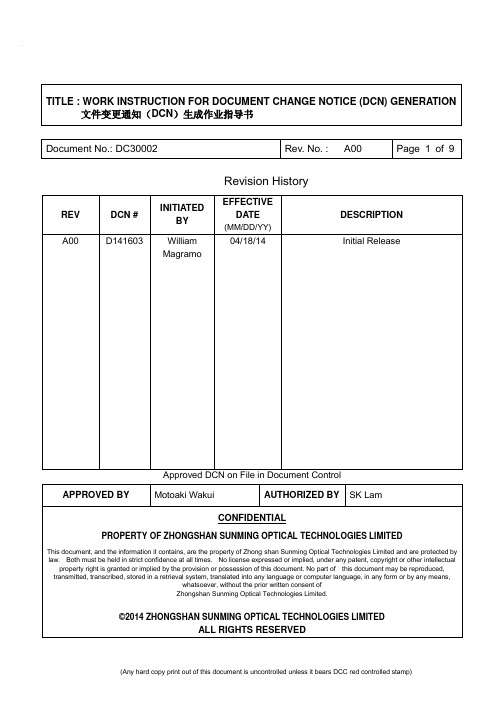
TITLE : WORK INSTRUCTION FOR DOCUMENT CHANGE NOTICE (DCN) GENERATION 文件变更通知(DCN)生成作业指导书Document No.: DC30002 Rev. No. : A00 Page 1 of 9Revision HistoryREV DCN # INITIATEDBYEFFECTIVEDATE(MM/DD/YY)DESCRIPTIONA00 D141603 WilliamMagramo04/18/14 Initial ReleaseAPPROVED BY Motoaki Wakui AUTHORIZED BY SK LamCONFIDENTIALPROPERTY OF ZHONGSHAN SUNMING OPTICAL TECHNOLOGIES LIMITEDThis document, and the information it contains, are the property of Zhong shan Sunming Optical Technologies Limited and are protected by law. Both must be held in strict confidence at all times. No license expressed or implied, under any patent, copyright or other intellectual property right is granted or implied by the provision or possession of this document. No part of this document may be reproduced, transmitted, transcribed, stored in a retrieval system, translated into any language or computer language, in any form or by any means,whatsoever, without the prior written consent ofZhongshan Sunming Optical Technologies Limited.©2014 ZHONGSHAN SUNMING OPTICAL TECHNOLOGIES LIMITEDALL RIGHTS RESERVED1.0 SCOPE范围1.1 This work instruction is used in generating Document Change Notice (DCN) applicable toquality management system (QMS) documentation such as system quality manual,corporate procedures and working instructions..本作业指导书适用于质量管理体系(QMS)的系统文件,如系统手册,程序文件和作业指导书的文件变更通知(DCN)的生成。
【最新文档】指导书英语-范文word版 (10页)

本文部分内容来自网络整理,本司不为其真实性负责,如有异议或侵权请及时联系,本司将立即删除!== 本文为word格式,下载后可方便编辑和修改! ==指导书英语篇一:英文版作业指导书(1)WI-0210-001Report Name: Receiver and distributor working instruction to Main warehouseEffective Date: 201X.2.1Code No: WI-0210-001Approve by:1. Purpose: Guarantee the data accurate about the whole course that fabric in-out warehouse2. Scope: All fabrics, which enter into warehouse.3. Concept: Receiver and distribute is the whole course that counts out the fabric and arranges till to fabric distribution.4. Specific process4.1 Flow diagramFabric entranceCount and accept, arrangingFabric receipt information Fabric swatch making and distribution Input the receipt dataCreate the computer barReceive the manufacture indicationMaking the fabric and material swatchDistribute the fabric cutting roomSubcontract produceSettle accounts Return of goodsInput the receipt sheetStock managingMake an inventory4.2 Procedure.4.2.1 Goods receipt dataIncluding Key invoice, invoice and packing list. When the Key invoice reach, the concerned clerk will know the actual arrival time offabric and prepare for it.4.2.2 The fabric delivery. check and receipt4.2.2.1 While the fabric delivery into warehouse, should put the packing mark face tooutside.4.2.2.2 According to the packing list, check each roll in each container. If find anydifference with the packing breakdown, must mark it down carefully.4.2.2.3 Fabric arrangement and stock4.2.3.1 Know well about all the fabric in warehouse; put the un-inspect fabric into theto-inspect area, and put the inspected fabric into the regulative area strictly. Thepile height should be within the limitation, No higher than 1.7m for silk fabric andman-make fabric, and no higher than 1.5m for wool.4.2.3.2 Keep the fabric stock in dry, clean and net environment and stock should be keptwith the indoor temperature. To silk fabric, should be covered up to keep thesunlight out.4.2.4 Input and distribute the report form, create the computer bar.4.2.4.1 Make sure the amount is correctly and this group fabric will be use in which style.If find any difference , should mark down on the sheet.4.2.4.2 Distribute the sheet , which be confirmed by in-charge and PPIC/F, to account,scheduler, PPIC/F, and ask for receipt signure.4.2.5 Making the fabric swatch, confirming and distributing4.2.5.1 Fill the fabric swatch (including supplier, fabric No., fabric width, construction,custom, style, arrival date.)4.2.5.2 To elastic and inclined fabric, should make a decision by PPIC/F, whether makethe red fabric sample and remark the specialty.4.2.5.3 Making fabric swatch, the fabric should be face up according to the custominstruction and fabric factory remark. If unclear, should ask for confirm by PPIC/F.4.2.5.4 To the paint, plaid, check fabric, should pay attention to whether has the recyclespecialty. To the warp fabric, should point out the fabric way.4.2.5.5 Pass the fabric swatch to confirm by the in-charge of receiver and distributor team,PPIC and PPIC/F. The PPIC should remark the important point, just like whether。
生产制程稽核行为标准_双语中英文对照版_
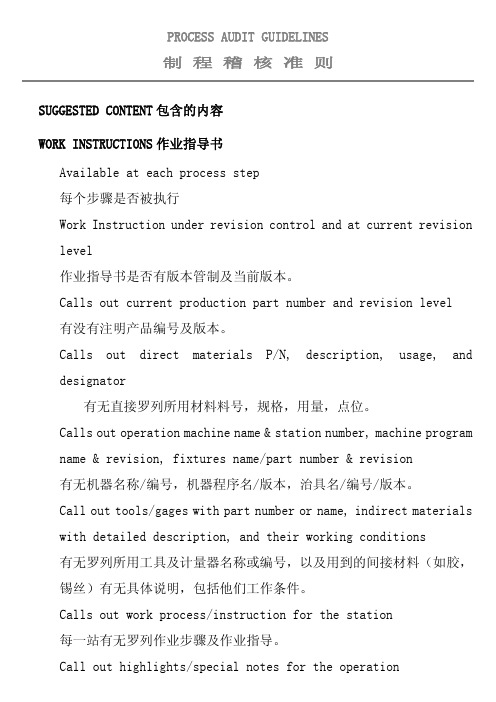
PROCESS AUDIT GUIDELINES制 程 稽 核 准 则SUGGESTED CONTENT包含的内容WORK INSTRUCTIONS作业指导书Available at each process step每个步骤是否被执行Work Instruction under revision control and at current revision level作业指导书是否有版本管制及当前版本。
Calls out current production part number and revision level有没有注明产品编号及版本。
Calls out direct materials P/N, description, usage, and designator有无直接罗列所用材料料号,规格,用量,点位。
Calls out operation machine name & station number, machine program name & revision, fixtures name/part number & revision有无机器名称/编号,机器程序名/版本,治具名/编号/版本。
Call out tools/gages with part number or name, indirect materials with detailed description, and their working conditions有无罗列所用工具及计量器名称或编号,以及用到的间接材料(如胶,锡丝)有无具体说明,包括他们工作条件。
Calls out work process/instruction for the station每一站有无罗列作业步骤及作业指导。
Call out highlights/special notes for the operation在作业指导书中有没有对相关注意事项做重点标识。
3PE防腐钢管生产线作业指导书_中英文版本

1. 上管前在存管平台上检查并去除钢管内外表面的毛刺、灰尘等杂质。如有缺 陷返回材料不合格区或修复区。
1. Check and remove the burr, dust and other impurities on the inner and outer surface of the steel pipe on the storage platform before pipe installation. In case of defects, return to the unqualified area or repair area.
2.调整好胶粘剂和PE 挤出机的前后位置。
2. Adjust the position of the adhesive and PE extruder.
3.调整硅胶轮的位置和角度。
3. Adjust the position and angle of the silicone rubber wheel.
三.抛 丸 除 锈
III. Ball Blasting Rust Removal
1. 除锈前必须检查并清除钢管内外表面的油污、毛刺、附着物等杂质。 1. Before derusting, it is necessary to check and remove the oil, burr, attachment and other impurities on the inner and outer surface of the steel pipe.
签名&日期 Sign&date
起草
Draft
审核
Review 批准
【最新文档】作业指导书英文-范文word版 (8页)
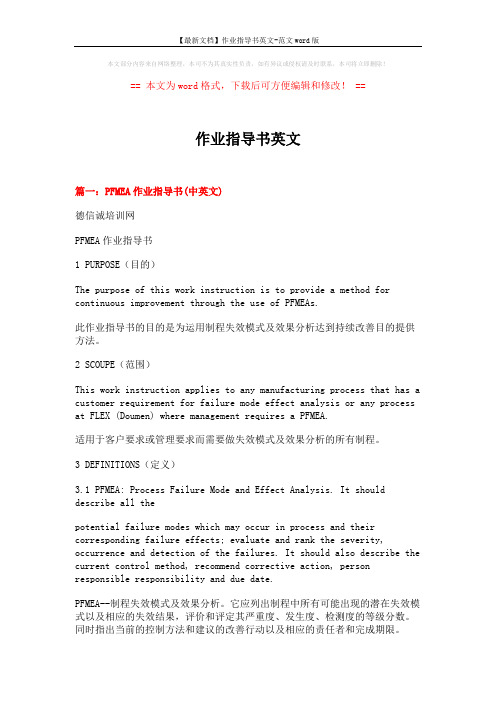
本文部分内容来自网络整理,本司不为其真实性负责,如有异议或侵权请及时联系,本司将立即删除!== 本文为word格式,下载后可方便编辑和修改! ==作业指导书英文篇一:PFMEA作业指导书(中英文)德信诚培训网PFMEA作业指导书1 PURPOSE(目的)The purpose of this work instruction is to provide a method for continuous improvement through the use of PFMEAs.此作业指导书的目的是为运用制程失效模式及效果分析达到持续改善目的提供方法。
2 SCOUPE(范围)This work instruction applies to any manufacturing process that has a customer requirement for failure mode effect analysis or any process at FLEX (Doumen) where management requires a PFMEA.适用于客户要求或管理要求而需要做失效模式及效果分析的所有制程。
3 DEFINITIONS(定义)3.1 PFMEA: Process Failure Mode and Effect Analysis. It should describe all thepotential failure modes which may occur in process and their corresponding failure effects; evaluate and rank the severity, occurrence and detection of the failures. It should also describe the current control method, recommend corrective action, person responsible responsibility and due date.PFMEA--制程失效模式及效果分析。
滚轮机作业指导-2中译英
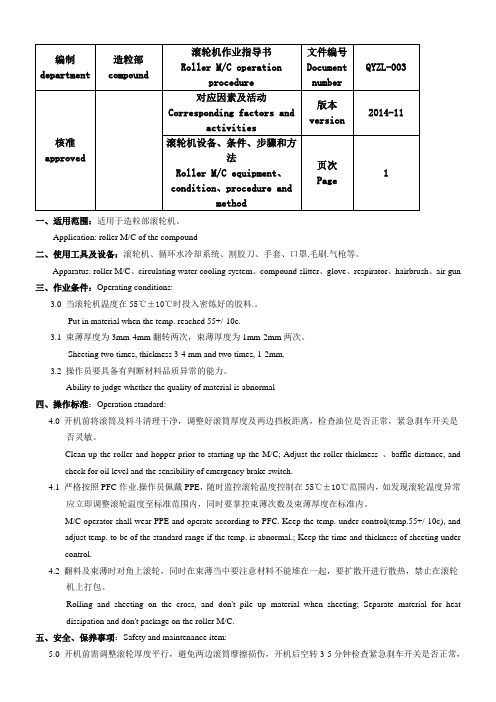
一、适用范围:适用于造粒部滚轮机。
Application: roller M/C of the compound二、使用工具及设备:滚轮机、循环水冷却系统、割胶刀、手套、口罩.毛刷.气枪等。
Apparatus: roller M/C、circulating water cooling system、compound slitter、glove、respirator、hairbrush、air gun三、作业条件:Operating conditions:3.0 当滚轮机温度在55℃±10℃时投入密炼好的胶料.。
Put in material when the temp. reached 55+/-10c.3.1 束薄厚度为3mm-4mm翻转两次,束薄厚度为1mm-2mm两次。
Sheeting two times, thickness 3-4 mm and two times, 1-2mm.3.2 操作员要具备有判断材料品质异常的能力。
Ability to judge whether the quality of material is abnormal四、操作标准:Operation standard:4.0 开机前将滚筒及料斗清理干净,调整好滚筒厚度及两边挡板距离,检查油位是否正常,紧急刹车开关是否灵敏。
Clean up the roller and hopper prior to starting up the M/C; Adjust the roller thickness 、baffle distance, and check for oil level and the sensibility of emergency brake switch.4.1 严格按照PFC作业.操作员佩戴PPE,随时监控滚轮温度控制在55℃±10℃范围内,如发现滚轮温度异常应立即调整滚轮温度至标准范围内,同时要掌控束薄次数及束薄厚度在标准内。
作业指导书标准范文英语(3篇精选)

作业指导书标准范文英语(3篇精选)作业指导书标准范文英语(篇1)1. IntroductionThis Standard Operating Procedure (SOP) outlines the detailed steps for completing a specific task within our organization. It ensures consistency, safety, and compliance with industry standards. This document is to be followed by all personnel involved in the task.2. Job OverviewProvide a brief overview of the task, including its purpose, importance, and the expected outcome. Identify the key objectives and the overall workflow.3. Tools and MaterialsList all the necessary tools, equipment, and materials required to complete the task. Specify the type, model, and any specific requirements for each item. Ensure that all necessary safety certifications and approvals are met.4. Job StepsProvide a detailed, step-by-step guide to completing the task. Each step should be clearly written and easy to understand. Include any specific techniques, procedures, or measurements required. Reference any diagrams, sketches, or images that may aid in understanding.5. Safety PrecautionsOutline all the necessary safety measures to be taken during the task. This should include personal protective equipment, environmental controls, and any specific safety procedures or protocols. Emphasize the importance of adhering to these measures to prevent accidents or injuries.6. Quality StandardsDefine the expected quality outcomes for the task. Include any specific metrics, tolerances, or performance criteria. Identify any quality control measures or testing procedures that will be used to ensure compliance.7. Common Issues and TroubleshootingIdentify common problems or issues that may arise during the task. For each issue, provide a troubleshooting guide with steps to resolve the problem. Include any specific tools or techniques that may be required.8. AppendicesInclude any additional information or references that may be useful for completing the task. This could include technical specifications, drawings, diagrams, safety data sheets, or any other relevant documents.Remember to review and update this SOP periodically to ensure it remains accurate and compliant with industry standards.作业指导书标准范文英语(篇2)1. Purpose and ScopeThis Standard Operating Procedure (SOP) outlines the specific steps and guidelines for performing a particular task within our organization. It aims to ensure consistency, safety, and quality in the execution of the task. The scope of this SOP covers all necessary steps, tools, materials, and safety measures required for the successful completion of the task.2. Safety PrecautionsBefore commencing the task, it is crucial to ensure the safety of all personnel involved. Appropriate safety gear, such as gloves, eye protection, and safety shoes, must be worn at all times. Ensure the workspace is clean, organized, and free of any hazards. Familiarize yourself with the safety measures outlined in the relevant safety data sheets and follow them strictly.3. Tools and MaterialsGather all the necessary tools and materials required for the task. Verify their condition and ensure they are suitable for the job. Keep them organized and easily accessible throughout the task. Refer to the tool and material list provided in the appendix for a detailed inventory.4. Step-by-Step GuideFollow the step-by-step guide provided below to ensure the task is completed accurately and efficiently. Read each step carefully and perform the task in the order provided. Do not skip any steps or deviate from the guidelines without explicit authorization.Step 1: [Description of step 1]Step 2: [Description of step 2]Step 3: [Description of step 3]...Final Step: [Description of the final step]5. TroubleshootingIn case of any issues or problems encountered during the task, refer to the troubleshooting section below. It provides solutions and workarounds for common problems that may arise. If the issue persists, contact the designated support team or supervisor for assistance.Issue 1: [Description of issue 1]Solution: [Description of solution for issue 1]Issue 2: [Description of issue2]Solution: [Description of solution for issue 2]...6. Quality ControlQuality is paramount in our organization. Therefore, itis essential to perform quality checks throughout the task to ensure the desired outcomes are achieved. Follow the quality control measures outlined below and record the results for future reference.Quality Check 1: [Description of quality check 1]Quality Check 2: [Description of quality check 2]...7. Post-Task ActionsUpon completion of the task, it is crucial to perform certain post-task actions to ensure the workspace is left in a safe and organized condition. This includes cleaning up any debris, storing tools and materials properly, and verifying that all safety measures are in place.8. ReferencesFor further information or additional guidance, refer to the following references:[Reference 1: Title or Description][Reference 2: Title or Description]...Appendices:Tool and Material ListSafety Data SheetsRelevant Technical DocumentsRemember to adhere strictly to this SOP to ensure the safety, quality, and efficiency of the task. Regular updates and reviews are recommended to reflect any changes or improvements.作业指导书标准范文英语(篇3)1. Assignment ObjectivesThe primary objective of this assignment is to achieve [specific goal or objectives of the assignment]. This SOPoutlines the necessary steps, tools, and precautions to ensure a smooth and safe completion of the task.2. Tool PreparationBefore starting the assignment, ensure that you have all the necessary tools and materials prepared. This includes but is not limited to:[List of tools and materials required for the assignment]It is essential to have these tools ready and functioning properly to avoid any delays or issues during the assignment.3. Step-by-Step GuideFollow the step-by-step guide below to complete the assignment effectively:Step 1: [Description of Step 1]Step 2: [Description of Step 2]...Step N: [Description of the final step]Refer to the diagrams, screenshots, or additional resources provided for further clarification if needed.4. Safety PrecautionsWhile performing the assignment, it is crucial to prioritize safety. Therefore, adhere to the following safety guidelines:Wear protective gear as recommended.Handle tools and materials with caution to avoid accidents.Follow the correct procedures and do not take shortcuts that may compromise safety.Immediately stop the assignment and seek assistance if any unsafe conditions are observed.5. Assignment Check Upon completion of the assignment, conduct a thorough check to ensure the desired results are achieved. Verify that all steps have been followed correctly, and there are no errors or omissions. It is recommended to refer to the assignment rubric or criteria for guidance.6. Problem HandlingIf any issues or challenges arise during the assignment, take the following steps to address them:Refer to the troubleshooting section or relevant resources for solutions.Seek assistance from classmates, mentors, or teachers if needed.Be proactive in seeking help and communicating any issues to ensure timely resolution.7. Assignment SubmissionOnce you have completed the assignment, follow the submission guidelines provided:Ensure all work is saved and backed up.Submit the assignment through the designated platform or system.Adhere to the submission deadline and any additional instructions provided.By following this SOP, you will be able to completethe assignment effectively, safely, and in a timely manner. Remember to refer to the resources and additional guidance provided throughout the assignment process.。
PFMEA作业指导书(中英文)

PFMEA作业指导书1 PURPOSE(目的)The purpose of this work instruction is to provide a method for continuous improvement through the use of PFMEAs.此作业指导书的目的是为运用制程失效模式及效果分析达到持续改善目的提供方法。
2 SCOUPE(范围)This work instruction applies to any manufacturing process that has a customer requirement for failure mode effect analysis or any process at FLEX (Doumen) where management requires a PFMEA.适用于客户要求或管理要求而需要做失效模式及效果分析的所有制程。
3 DEFINITIONS(定义)3.1 PFMEA: Process Failure Mode and Effect Analysis. It should describe all thepotential failure modes which may occur in process and their corresponding failure effects; evaluate and rank the severity, occurrence and detection of the failures. It should also describe the current control method, recommend corrective action, person responsible responsibility and due date.PFMEA--制程失效模式及效果分析。
英文版作业指导书(1)

WI-0210-001Report Name: Receiver and distributor working instruction to Main warehouseEffective Date: 2000.2.1 Code No: WI-0210-001 Approve by:1.P urpose: Guarantee the data accurate about the whole course that fabric in-out warehouse2.S cope: All fabrics, which enter into warehouse.3.C oncept: Receiver and distribute is the whole course that counts out the fabric and arranges till to fabric distribution.4.S pecific process4.1Flow diagramFabric entranceCount and accept, arrangingFabric receipt informationFabric swatch making and distributionInput the receipt dataCreate the computer barReceive the manufacture indicationMaking the fabric and material swatchDistribute the fabric cutting roomSubcontract produceSettle accounts Return of goodsInput the receipt sheetStock managingMake an inventory4.2Procedure.4.2.1Goods receipt dataIncluding Key invoice, invoice and packing list. When the Key invoice reach, the concerned clerk will know the actual arrival time of fabric and prepare for it.4.2.2The fabric delivery. check and receipt4.2.2.1While the fabric delivery into warehouse, should put the packing mark face tooutside.4.2.2.2According to the packing list, check each roll in each container. If find anydifference with the packing breakdown, must mark it down carefully.4.2.2.3Fabric arrangement and stock4.2.3.1Know well about all the fabric in warehouse; put the un-inspect fabric into theto-inspect area, and put the inspected fabric into the regulative area strictly. Thepile height should be within the limitation, No higher than 1.7m for silk fabric andman-make fabric, and no higher than 1.5m for wool.4.2.3.2Keep the fabric stock in dry, clean and net environment and stock should be keptwith the indoor temperature. To silk fabric, should be covered up to keep thesunlight out.4.2.4Input and distribute the report form, create the computer bar.4.2.4.1Make sure the amount is correctly and this group fabric will be use in which style.If find any difference , should mark down on the sheet.4.2.4.2Distribute the sheet , which be confirmed by in-charge and PPIC/F, to account,scheduler, PPIC/F, and ask for receipt signure.4.2.5Making the fabric swatch, confirming and distributing4.2.5.1Fill the fabric swatch (including supplier, fabric No., fabric width, construction,custom, style, arrival date.)4.2.5.2To elastic and inclined fabric, should make a decision by PPIC/F, whether makethe red fabric sample and remark the specialty.4.2.5.3Making fabric swatch, the fabric should be face up according to the custominstruction and fabric factory remark. If unclear, should ask for confirm by PPIC/F.4.2.5.4To the paint, plaid, check fabric, should pay attention to whether has the recyclespecialty. To the warp fabric, should point out the fabric way.4.2.5.5Pass the fabric swatch to confirm by the in-charge of receiver and distributor team,PPIC and PPIC/F. The PPIC should remark the important point, just like whetherneed to cross cut, nap-up cut, and the requirement to match check or plaid.4.2.5.6Distribute the confirmed fabric swatch to PPIC/F,PPIC, cutting room, samplemaking group, scheduler, accessory warehouse4.2.6Fabric distribution4.2.6.1Making the fabric and accessory swatch: While receive the manufactureindication, at first , should record the receive date, then decide how many swatchshould be make according to the order amount:7 copies for less than 1000pcs9 copies for more than 1000pcs12 copies for more than 4000pcsThe receiver and distributor make the fabric swatch, should pay attention to thecorrect fabric way, flower way and vertical and horizontal, Meanwhile, attach theconcerned the lining and interlining. If find any problem at the instruction ofmanufacture indication, should inform PPIC/F and PPIC, till to be clarify byconfirm; then pass to be confirmed by the in-charge of receiver and distributorteam. Following, make the “accessory receipt seal”to the first sample swatch,mark down the distribute date, pass to accessory warehouse, ask for receipt bysign.4.2.6.2 Distribute the PP sample fabric Before send out the fabric, must checkwhich roll fabric’s shrinkage is serious.。
【最新文档】ts16949作业指导书-word范文 (4页)

本文部分内容来自网络整理,本司不为其真实性负责,如有异议或侵权请及时联系,本司将立即删除!== 本文为word格式,下载后可方便编辑和修改! ==ts16949作业指导书篇一:TS16949来料检验作业指导书(中英文)TS16949来料检验作业指导书 Incoming_Inspection_Work_Instruction文件更改历史记录Amendment HistoryTS16949来料检验作业指导书 Incoming_Inspection_Work_Instruction1.0 Purpose目的The objective of this procedure is to define a standard inspection method in performing inspection and testing of components or materials. 本程序目的在于定义对元件或材料进行检验/测试的标准操作方法。
Scope适用范围This procedure is applicable to all components and materials that require the relevant inspection and testing, as specified in the individual Part or Material Specification.本程序适用于所有按照元件和材料规格进行检验和测试的元件和材料。
2.0 Sampling / Equipment Used 取样 / 使用设备2.1 Per sampling plan stated in the Incoming Inspection Procedure: AQL:MA=0.4、MI=1.0按照来料检验程序所规定的抽样计划;AQL:MA=0.4、MI=1.0级别进行抽样. 2.2 Inspection Aids检验工具4.2.1 LCR Meter / LCR 测量仪4.2.2 Fluke Multimeter / Fluke 万用表4.2.3 Caliper / Plug Gauge /Pin Gauge / 游标卡尺/ 塞规/针规 4.2.4 Magnifier / Microscope / 放大镜/ 显微镜3.0 Reference Documents参考文件3.1 Customer’s AVL / 客户接受的供应商清单3.2 Manufacturer Part Specification / 供应商的元件规格(来自: :ts16949作业指导书 )篇二:TS16949控制计划的作业指导书控制计划的作业指导书1、目的:通过控制计划的制定、实施、管理,确保制造过程处于受控状态,生产出符合顾客要求的产品。
质量管理体系中英文缩写与其解释

质量管理体系中英文缩写与其解释Engineering 工程/ Process 工序(制程)4M&1E Man, Machine, Method, Material,Environment 人,机器,方法,物料,环境- 可能导致或造成问题的根本原因AI Automatic Insertion 自动插机ASSY Assembly 制品装配ATE Automatic Test Equipment 自动测试设备BL Baseline 参照点BM Benchmark 参照点BOM Bill of Material 生产产品所用的物料清单C&ED/CAEDCause and Effect Diagram 原因和效果图CA Corrective Action 解决问题所采取的措施CAD Computer-aided Design 电脑辅助设计.用于制图和设计3维物体的软件CCB Change Control Board 对文件的要求进行评审,批准,和更改的小组CI Continuous Improvement 依照短期和长期改善的重要性来做持续改善COB Chip on Board 邦定-线焊芯片到PCB板的装配方法. CT Cycle Time 完成任务所须的时间DFM Design for Manufacturability 产品的设计对装配的适合性DFMEA Design Failure Mode and EffectAnalysis 设计失效模式与后果分析--在设计阶段预测问题的发生的可能性并且对之采取措施DFSS Design for Six Sigma 六西格玛(6-Sigma)设计-- 设计阶段预测问题的发生的可能性并且对之采取措施并提高设计对装配的适合性DFT Design for Test 产品的设计对测试的适合性DOE Design of Experiment 实验设计-- 用于证明某种情况是真实的DPPM Defective Part Per Million 根据一百万件所生产的产品来计算不良品的标准DV Design Verification / DesignValidation设计确认ECN Engineering Change Notice 客户要求的工程更改或内部所发出的工程更改文件ECO Engineering Change Order 客户要求的工程更改ESD Electrostatic Discharge 静电发放-由两种不导电的物品一起摩擦而产生的静电可以破坏ICs和电子设备FI Final Inspection 在生产线上或操作中由生产操作员对产品作最后检查F/T Functional Test 测试产品的功能是否与所设计的一样FA First Article / Failure Analysis 首件产品或首件样板/ 产品不良分析FCT Functional Test 功能测试-检查产品的功能是否与所设计的一样FFF Fit Form Function 符合产品的装配,形状和外观及功能要求FFT Final Functional Test 包装之前,在生产线上最后的功能测试FMEA Failure Mode and Effect Analysis 失效模式与后果分析-- 预测问题的发生可能性并且对之采取措施FPY First Pass Yield 首次检查合格率FTY First Test Yield 首次测试合格率FW Firmware 韧体(软件硬化)-控制产品功能的软件HL Handload 在波峰焊接之前,将PTH元件用手贴装到PCB上,和手插机相同I/O Input / Output 输入/ 输出iBOM Indented Bill of Material 内部发出的BOM(依照客户的BOM)ICT In-circuit Test 线路测试-- 用电气和电子测试来检查PCBA短路,开路,少件,多件和错件等等不良IFF Information Feedback Form 情报联络书-反馈信息所使用的一种表格IR Infra-red 红外线KPIV Key Process Input Variable 主要制程输入可变因素-在加工过程中,所有输入的参数/元素,将影响制成品的质量的可变因素KPOV Key Process Output Variable 主要制程输出可变因素-在加工过程中,所有输出的结果,所呈现的产品品质特征。
汽车常用术语中英文对照表
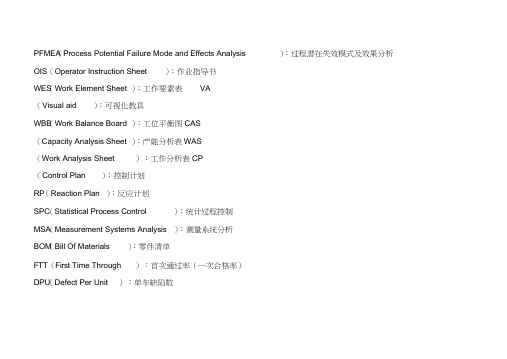
PFME(A Process Potential Failure Mode and Effects Analysis ):过程潜在失效模式及效果分析OIS(Operator Instruction Sheet ):作业指导书WES(Work Element Sheet ):工作要素表 VA(V isual aid ):可视化教具WBB(Work Balance Board ):工位平衡图CAS(Capacity Analysis Sheet ):产能分析表WAS(Work Analysis Sheet ):工作分析表CP(C ontrol Plan ):控制计划RP(R eaction Plan ):反应计划SPC(Statistical Process Control ):统计过程控制MSA(Measurement Systems Analysis ):测量系统分析BOM(Bill Of Materials ):零件清单FTT(First Time Through ):首次通过率(一次合格率)DPU(Defect Per Unit ):单车缺陷数JPH(Jobs Per Hour ):每小时工作量PPM(Parts Permillion): 零部件百万分之不合格品率CPU(Cost Per Unit ):单位成本VRT(Variability Reduction Teams): 变差减少小组PD(P roduct Development ):产品开发PVT(PlantVehicle Teams ):工厂车辆小组STA (Supplier Technical Assistance ):供应商技术支持IQ(I ncoming Quality ):进货质量检查 VE(V ehicle Engineering ):整车质量评价ME(M anufacturing Engineering ):制造工程AE(A dvanced Engineering ):先期项目 PE(Plant Engineering ): 设备工程MBO(Manufacturing Business Office ):制造办公室CPS(Changan Production System ):长安生产体系MSD(S Material Safety Data Sheet ):材料安全数据单。
非常实用的英文版作业指导书

公司名称:` 1. CHECK AMOUNT OF NEJILOCK ON SKEW SCREW.IT SHOULD BE MINIMUM OF HALF FULL(180 DEGREES) OF SKEW SCREW1. Get Drive from the conveyor and place it to the Deck Platform.2. CHECK FOR THE FOLLOWING MAIN PCB ITEM. A. MAIN PCB OPTION PIN SETTING (FOR PATA) B. LABEL BARCODE ON MAIN PCB. IT SHOULD BE SAME WITH RUNNING MODEL 2. Get.Main PCB from Danpla.Start from lower horizontal to upperC. DETACHED/ MISSING CONDENSER.. slot of Danpla.Visual Inspect for possible defets.D. MAIN PCB CONNECTOR FOR POSSIBLE DAMAGE.3. CHECK FOR PICK UP FFC PIN CONDITION. IT SHOULD BE NO BENT,DENT ,OFFSET PIN AND MUST BEFULLY INSERTED IN CONNECTOR..3. Insert Pick-Up FFC to MPCB Connector. Make sure that FFCis fully inserted.Avoid leaning of hand on the step motor during FFC insertionthat could damage the leadscrew run out4. CHECK FOR PICK UP FFC. IT SHOULD BE FULLY INSERTED AND LOCKED IN THE CONNECTOR..5. CHECK PICK UP FFC. IT SHOULD NOT TOUCHING ANY PICK UP PART.4. Lock the connector of MPCB. Make sure connector reachedits locking point.Then Pass to the next process.6OS-15C-340(08.03.04)REV:11SSSAll H/H Lines WORKING PROCEDURE CHECK POINTSINPUT PARTSTOOLS AND EQUIPMENTS REVISION HISTORY PROCESSNOPROCESS NAME MAIN PCB LOADING & FFC INSERTION 09MODELALL MODELS LINE 20-Sep Change Picture,Add process check poiints XXX 221-Dec Improvement of FFC insertion method EARTH RING / WRISTSTRAP 3026-Jan ESTABLISH NEW WORK I FOR H-H SHORTLINE AAA 2MAIN PCB 1 PC 2REV NO.DATE REASON PIC 1DECK ASSEMBLY 1 SET 1HAND GLOVES NO.DESCRIPTION QTY CODE CONTROL / SPECS DRAFTER REVISION 2DATE21-Dec CHECK APPROVE APPROVE CONTROL DOCUMENT STANDARD NO.EBRY-1426E STEP 01STEP 02 STEP 03 STEP 04GOODGOODNO GOOD GOOD FULLY-LOCKED HALF LOCKEDGOOD NO GOOD GOOD NO GOODDAMAGE PIN。
英文版作业指导书(2)

WI-0210-001When making test samples, send the fabric of the largest shrinkage or the one used to test shinkage out.4.2.6.3Use the bill of material (BOM) drafted out by the cutting room to take the fabrics fromthe warehouse. The clerk in the warehouse will check the BOM to see if it matches thecutting percentage of the Material Consumption List and dispense the fabric if there isno discrepancy. Before dispensing the fabric, check the inspection documents carefully,if there are bad rolls or some rolls which need narrow marks, deal with them accordingly: for bad rolls, stick special bad-roll labels ( red stickers) on them and separate them fromother rolls; for the rolls which need narrow marks, set them on top of any other styles sothe cutting room can avoid excessive losses. Dispense the fabrics of the same style,quantity, colour and shading as stated in the BOD to the cutting room.4.2.6.4Check if the cutting room need defective swatches or not. Generally, to get the defectiveswatches, the cutting room should obtain permission from PPIC/F.4.2.7Subcontract:Give the materials out according to the procedures at once when receiving the subcontract advice from PPIC/F.4.2.8Entry of BODEnter the the BOD No. and the actual dispensed materials into the computer.4.2.9When finishing the dispensation of each lot, settle the fabric account with PPIC/F, for thesurplus rolls, make virements or D/B; for the converting order, keep the surplus fabricsseperately for the customer’s reclamation.4.2.10When receiving the return notice from PPIC/F, pack the fabrics to return in cartons,make out the return list, count out the weight and volume of the rolls to return. Thereturn list should be presented to the supervisor and PPIC/F for confirmation and to thein-chief or manager and factory director for signature. Then, the return list will bedistributed to PPIC/F, Accounting Dept. and Import & Export Dept. and will be returnedwhen receiving notice from the Import & Export Dept.4.2.11Check the warehouse periodically each month and keep the results in record.4.2.12Stock-taking: this is for all the assets of the company, usually conducted in the middleand the end of the year. The staff in the warehouse should check the actual amount of thefabrics of their customers and fill in the stock-taking list for the confirmation of theAccounting Dept. and the Group Corporation.5.documents required: the list of orders; fabric consumption assessment sheet; the cuttingsheet; invoice; packing list; purchase orders, etc.6.Documents created: the list of reception and distribution; account cards; swatches; mainmaterial samples; accessory samples; return lists; stock-taking lists, etc.QI-0210-001Instruction Sheet of Fabric Inspection in Main Warehouse1.Purpose:1.1 Fabric inspection is a very important process to improve the quality of finishedgarments and ensure the successful export of factory products.1.2 Through fabric inspection, we can have an idea of the fabric quality and advise thecustomer the percentage of fabric utilisation.2.Objects to Inspect:a. All shell fabricsb. Some lining fabricsFor Japanese Line, inspect a roll at random per colour; all polyester lining should be examined.For American Line, 10% of lining from Hongkong should be examined at random;20% of lining from South Korea and Taiwan should be examined at random.3.Definition: when conducting fabric inspection, we should mark the defects and check thelength, width, quantity of the fabrics.4.Inspection Process4.1 Process Diagram:Preparation↓inspect and stick AA stickers↓pack and trim the fabrics↓distribute the defective swatches and documents4.2 Process Steps:4.2.1 Preparation4.2.1.1 clean the inspection machine and workbench and check if the machineworks normally.4.2.1.2 the inspector must know the customer name of the fabric and also thecharacteristics of the fabric.4.2.2 before inspection, the foreman of the inspection team should accompany his/herstaff to inspect a roll (two rolls at least for a lot) per colour so that the staff canhave a general idea of how to inspect.4.2.3 the inspection of ordinary fabric:4.2.3.1 quality inspection4.2.3.1.1 place the fabric on the inspection machine with the face upside.4.2.3.1.2 set the measurement device at “0” position and operate the machine.4.2.3.1.3 when inspect the fabric, fill in the inspection report correctly. The fabricNo., factory No., cutomer’s No., colour, shading, serial No., excess,customer grade label, inspection date and AA stickers should be filled incorrectly in the report.4.2.3.1.4 when inspecting, the inspectors should have a sense of quality. Theunacceptable defects like holes and cavities should be cycled by colourspowder or pointed by a fault sticker; the acceptable defects need notbe marked by fault stickers; for an uncertain defects, stitch a three-inch thread loop about 1” away from the defect. The number ofunacceptable defects and uncertain defects should be filled in in thereport.4.2.3.1.5 distinguish the name and the degree of the defects and if the defects areof different degrees, they should be kept in record seperately.4.2.3.1.6 for the defects which are difficult to find, when necessary, the inspectorsshould open the base light of the machine to check if there are skewedwefts and other defects in the roll.4.2.3.1.7 for uncertain defects, the foreman of the inspection team should firstjudge which ones need to cut defective swatches; for those the supervisorcannot decide, give them to the warehouse supervisor; if there are stillsome uncertain ones, present them to PPIC/F. PPIC/F will then decidewhither to cut defective swatches or not. Usually, for the rolls which havefive points of defects, we should make defective swatches and set them asstandards after confirmation. If the lot contains 4 rolls or is about 200yards long and the inspection loss is above 10% of the total lot, theinspector must advise the PPIC/F to view the fabric and decide whetherto cut defective swatches or not.4.2.3.2 Quantity Inspection:4.2.3.2.1 Fabric width inspection:Generally, for the American Line, the width and cutting width of the rollshould be measured. For the Japanese Line, the inspector shouldmeasure the distance between the selvage holes. The inspector shouldmeasure three places to get the cutting width of the roll: 1) 3 yardsaway from the head; 2) the middle; 3) 3 yards away from the end.There will be three widths and the inspector should keep the shortest onein record.4.2.3.2.2 Fabric length inspection:when finishing the inspection, check the number displayed on themeasurement device of the machine to get the “excess and lack” amountand fill it in the inspection report, if no discrepancy, mark “0” in the“excess and lack” column of the inspection report.4.2.4 The inspection of special fabric:The inspection of special fabrics is the same as that of common fabrics, but theinspector should pay attention to the following aspects:4.2.4.1 for fabrics with loose yarn or elastic warp and weft, the inspector shouldadjust the soft-roll and the hard-roll functions of the machine so the fabric willnot distort when being pulled. If necessary, the inspector can loosen or hang thefabric to inspect and measure several rolls in hand in the cutting room.4.2.4.2 For the fabrics with tight selvages, the inspector can use the iron frame ofthe machine to straighten the fabric so the fabric will not form skewed wefts or plaits which will not be ironed out.4.2.4.3 For the fabrics with obvious wefts, the inspector should not distort thewefts and roll the fabric carefully. For checks, the inspector must measure thedistances of adjacent checks in the head and end of the roll, and keep record.4.2.4.4 For printing fabrics, the inspector should emphasis on if the distancesbetween flowers vary and if the flowers are oblique. The general practice of this inspection is to rip the head of the roll to tidy the wefts and see if the flowersand the wefts are on the same horizonal line. If not, write down the obliquedegree.4.2.4.5 For plaid fabrics, the inspector, apart from inspecting the length of theroll, should also check if the number of plaids is the same as displayed in thereceipt, and keep records. Moreover, the inspector should make clear whetherthe areas of plaids are the same and if the plaids are made of small patterns,measure the distances between these small patterns, and inspect if the distance between the selvage and the most outside flower is enough for cutting. Theinspector should use the biggest size of the garment to check it.4.2.4.6 For fabrics with directions, the inspector should measure the differentlengths of the roll when placed in obverse or reverse directions. The inspectorshould also measure the length of the roll in hand in the cutting room for more accurate data.4.2.4.7 when inspecting fabrics of light colour, the workbench and machineshould keep clean and the machine should be covered with white paper. Theinspector should wear white sleeves.4.2.4.8 when inspecting the colour fastness of fabrics of light colour, use a whiteswatch to rub the fabric to see if it fades, or expose the fabric to fluorescentlamp for 72 hours and compare the colour of exposed areas with that ofunexposed areas to see if there is fading.4.2.5 Manual Inspection:4.2.5.1 when finishing the machine inspection, inspect in hand a roll at random inthe cutting room ( no less than 2 rolls for each lot) keep records, and comparethe results with those of the results of machine inspection.4.2.5.2 4-point system:According to the 4-point system, the defects will be marked in differentpoints by the lengths of the defects. The general exchange rates betweenthe defect lengths and the points are as below:0—3” = 1 point; 3”—6” = 2 points;6”—9” = 3 points; 9” or more = 4 points;for holes, 1 hole = 4 points.4.2.5.3 Packaging the fabrics:when the inspection processes are finished, seal up the fabrics in plasticbags and stick the customer’s fabric labels and the factory’s serial cardsto the heads or ends of the fabrics. Write down the actual yardages, thecutting width, excess or lack of yardage on the customer’s fabric labels.All the fabrics should be placed in the same direction on top of tables, andin order to prevent the fabrics from being scratched by pointed things,paperboards must be placed between the tables and the fabrics.4.2.8.the presentation of defective swatches and documents:4.2.8.1 usually, when bulk fabrics arrive, the inspectors should inspect20-30% of the total rolls at random and write the inspection report; whensmall lots arrive, then they must be 100% inspected within three days,and when finishing one colour, keep the records and make clear if theswatches are smoothly trimmed and meet the standards ( name stickers andfault stickers must be attached on the face sides of the swatches). If there isno probelem, present the swatches and documents to the secretary forconfirmation and signature, and register the presentation date, number ofrolls and swatches.4.2.9 the end of inspecting work & cleaning4.2.9.1 do cleaning again, shut down the inspection machine and gooff work.5.The principles of defect point-calculating and point-deducting5.1 width of the fabricWide rolls: width above 54.5”Medium rolls: width between 40” to 4.5”Narrow rolls: width below 40”5.2There are three defect point-deducting methods:5.2.1 punctate defects:when encountering such problems, the Cutting Room will replace thepanel. For wide rolls, 0.25 points will be deducted for one such defect; formedium rolls, 0.33 points; for narrow rolls, 0.5 points. Such defectsinclude black dots, smears, thread knots, etc.5.2.2 vertical defects:For defects longer than 5 yards, Mark Room will make special marks5.2.2.1 A defect less than 0.5 yards long is deducted by one point; 0.5—1 yard,2 points; 1—2 yards,3 points; 4—5 yards, 6 points.5.2.2.2 for wide rolls, 0.25 yards will be deducted for each point; for mediumrolls, 0.33 points; and for narrow rolls, 0.5 yards. Such defects includevertical dark strips, vertically pulling yarn, etc.5.2.3 horizonal defects:5.2.3.1 small horizonal defects:the length of one such defect is less 1/4 of a wide roll ( deduct 0.25yards for each defect), 1/3 of a medium roll ( deduct 0.33 yards), 1/2 ofa narrow roll (deduct 0.5 yards)5.2.3.2medium horizonal defects:the length of one such defect is between 1/4 to 1/2 of a wide roll, 1/3to 1/2 of a medium roll, less than 1/2 of a narrow roll. For all suchdefects, 0.5 yards will be deducted for each defect.5.3Narrow Mark5.3.1If the defect lies in area next to the sides (less than 5”), cut the defectivearea.5.3.2I f the defect is more than 5” and less than 14.5” away from the sides, thepoint-deducting principles will be as follows:For wide rolls, 1/4 of the length of the defect;For medium rolls, 1/3 of the length of the defect;For narrow rolls, 1/2 of the length of the defect;5.3.3If the defect is more than 14.5” and less than 29” away from the sides,then:For wide rolls, 1/2 of the length of the defect;For medium and narrow rolls, it is considered as bad rolls.5.4Bad Rolls5.4.1If there are discontinuous unacceptable defects along the whole length of thefabric, then it is considered as a bad roll5.4.2If there are discontinuous unacceptable horizonal defects among a certainlength of the fabric, then deduct the actual yardage.5.4.3For medium rolls and narrow rolls, if there are unacceptable vertical defects inarea more than 14.5” away from the sides, then the rolls will be considered asbad rolls. For wide rolls, if there are unacceptable vertical defects in area morethan 29” away fro m sides, then the rolls are considered as bad rolls.6.The Inspection Process Rate of Fabrics ( roll / hour ):。
制袋作业指导书中英文

制袋作业指导书中英文制袋作业指导书Instructions一、目的:规范制袋生产管理过程,确保成品满足客户和相关标准要求;A.Objective:make the process of production management in a Standard, and ensure the products to meet customer's requirements and standards;二、范围:适用于本公司制袋生产作业的管理和控制;B.Confines: applicable to the management and control of production homework ;三、职责:C.Responsibilities:3.1制袋班长负责制袋生产作业过程中实施全面监督,安排人员和生产计划;一.Monitor takes charge the whole production process of bag making, arrange personnel and make up production plan;3.2机长、机长助理、操作工、收袋工负责生产过程中的制袋作业;二.The captain,captain assistant,operator and work are responsible for the production process of the bag making;四作业内容D.Job content一)生产确认一.Production Validation1. 机长认真审阅《施工单》,包括:成品名称、规格、数量、热封位置、热封边宽、切刀位置、冲孔位置、冲孔尺寸、使用材料及特别要求等;a.The captain must check and approve the construction form carefully, including: product name, specification, quantity, hotsealing position, heat sealing side wide, the position of cutting knife, punching position, punching size, using material and special requirements, etc.;2. 机长将生产安排及注意事项向各工位人员讲解,各工位人员应认真了解生产要求和制程注意事项。
- 1、下载文档前请自行甄别文档内容的完整性,平台不提供额外的编辑、内容补充、找答案等附加服务。
- 2、"仅部分预览"的文档,不可在线预览部分如存在完整性等问题,可反馈申请退款(可完整预览的文档不适用该条件!)。
- 3、如文档侵犯您的权益,请联系客服反馈,我们会尽快为您处理(人工客服工作时间:9:00-18:30)。
适用机种/Mode All the models 工站名称 Process 物料
Material 名 称/Name
料号/(P/N)规格/Specification 数量Quantity . 1CHASSIS MAIN
HNSR0303200N/A N/A
2
BRKT DECK HAET1401400步驟/Step 攻 牙tapping
Specification material number is correct, look no more
than 10 centimeters obvious scratch, no deformation
Check the incoming material 4送料进行试产。
生产至少5PCS,确认生产无异常。
做好工件定位,丝攻和供油到位,通知好品质人员进行首检
生产顺畅;工件首检合格。
Production flow; Artifacts first inspection qualified.
工件传递和放置确定好,进行连续作业进行生产。
操作人员随机抽检,每30个至少检查一次,发现不良及时停机确认。
Feeding testing. Production at least 5 PCS,confirm production without exception Completes the workpiece positioning, screw tap and oil in place, first inspection notice good quality staff
3将来料放入专用夹具中,定位放好,装好所需丝攻。
做好工件堆放和机台旁的辅助台清理的工作.
2检查来料
规格料号正确,外观无10厘米以上明显刮伤,无变形。
Material to be included in the special
fixture, positioning and installed the
screw tap
Make workpiece stacking and beside the machine
auxiliary machine cleaning work 操 作 內容Fuck for content
注 意 事 項/Notices 1点检攻牙机 攻牙机开关正常,气压和供油正常。
tally tapping machine Tapping machine, switch to normal air pressure and oil
supply is normal
攻牙机
Tapping
machine 牙规Tooth gauge
En kang metal products co., LTD 攻牙作业指导书Tapping wi
版次Rev: 1备注/Remark Customer name HJ 使用工具Use Tools o l
Remark Remark 附件8o l
6WANGYONG Production date 2014年4月2
*出现的品质问题:漏攻牙,孔攻错导致尺寸不良要重点项目管控。
* the quality problem: leak tapping, size our lead to adverse to control key projects 7检查无误后传到下一工站。
动作要轻,以免碰伤工件。
Check and send to the next station.The movement wants light, in order to avoid artifacts
bruised
核准
APPR 審核CHECK 做好自主检查。
Independent inspection 无漏攻牙,攻牙歪斜,攻牙深度不够等不良现象.
No leakage tapping, tapping askew, tapping depth etc.
Bad phenomenon
Random operator, check at least once every 30, adverse downtime to confirm in time.制作PRO 5Artifacts and determine well placed,
continuous operation for production
備注Remark 備注Remark Remark
Remark。