MX1508RX2产品手册V1.0
双电子 XGPS150 蓝牙 GPS 接收器用户手册说明书
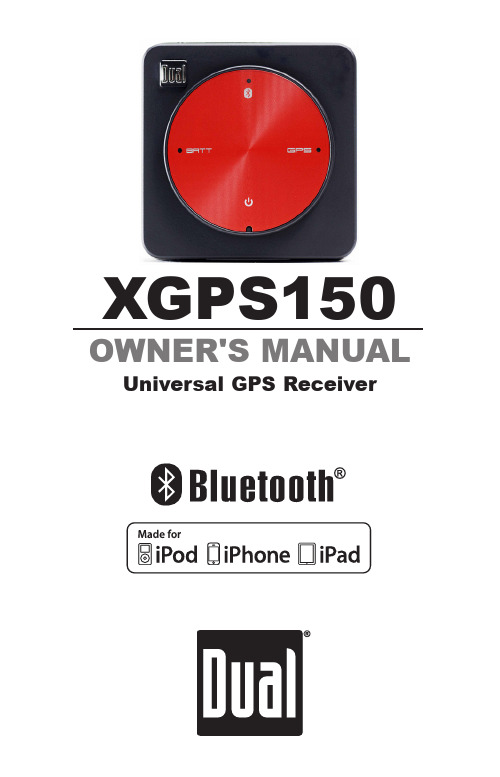
OWNER'S MANUALUniversal GPS ReceiverXGPS150XGPS1502IntroductionThank you for purchasing the XGPS150 Universal Bluetooth ® GPS Receiver from Dual Electronics.The XGPS150 works with signals from GPS satel-lites to determine your location anywhere in the world. It then can transmit your location informa-tion to many kinds of devices which have Blue-tooth connectivity and support the Bluetooth Serial Port Profile (SPP). This includes:• the iPhone ® (generations 2 through 4)• the iPod touch ® (generations 2 through 4)• the first generation of the iPad ®You can also connect the XGPS150 to many An-droid ®, Windows ® or Blackberry ® smart phones and tablets, as well as to notebook computers run-ning Windows or OS X.NOTE: Not all manufacturers include SPP in their devices, even if the device has Bluetooth. Please consult the owner’s manual for your specific de -vice to determine whether it supports SPP . Some devices, like Android-based devices, may need a helper app to connect to the XGPS150. See Pair-ing with your device for more information.Low battery indicator. This light will flash red when the battery level is low and the device re-quires recharging. (See Charging the XGPS150.) During charging, the light will glow red and change to green when charging is complete. This light is normally off while the XGPS150 is running. Bluetooth status indicator. This light will indicate whether the XGPS150 is searching for a device to connect to, negotiating a connection with a device, or has successfully paired to a device. A slow flash(about once per second) indicates the XGPS1503XGPS1504Features (cont’d)is available to connect to another device. A quick flash (approx. 5 times per second) briefly hap -pens when the XGPS150 is pairing with another device. A solid glow indicates that the XGPS150 has successfully paired and is communicating with another device.GPS status indicator. The GPS indicator will flash while the XGPS150 is searching for satellite signals. The light will change to a steady green when your location is successfully determined. NOTE: when paired with an iPad, iPod or iPhone the GPS status light will not illuminate until an app is actively requesting GPS information.XGPS1505charging the XGPS150.Mode switch . The mode switch must be set for the device you want to use the XGPS150 with:XGPS1506SetupThe XGPS150 is very simple to use. There is a one-time setup process to connect it to your iPad, iPod, smart phone, tablet or laptop computer. Once this setup process is completed, simply turn on the XGPS150 to begin using it.To setup the XGPS150 with your device, you will need to do two things:• Set the mode switch on the XGPS150 for the type of device you will be using.• Pair the XGPS150 with the device you will be using.Setting the mode switchWith the tip of a fine ballpoint pen, move the mode switch to the proper position:• If you are using the XGPS150 with an iPad, iPod touch or iPhone slide the switch right, away from the USB connector.• To use the XGPS150 with an Android, Win -dows or Blackberry smart phone, laptop com-puter or tablet, move the mode switch to the left, towards the USB connector.XGPS1507Pairing with your devicePairing is the process connecting two devices over Bluetooth and allowing them to communicate. You will need to go through the pairing process each time you use the XGPS150 with a new device, and the XGPS150 will automatically try to reconnect to the last device it was paired with.NOTE: If your device requires a code to connect during the pairing process, use “0000” or “1234”.Pairing the XGPS150 with the iPod touch, iPad or iPhone(NOTE: these instructions were written using iOS version 4.1 and may be different if you are using a different version of the iPhone OS.)• Make sure the mode switch on the XGPS150 is set correctly for your device (see Setup ).• On the touch/iPad/iPhone device, go to:Settings->General->Bluetoothand turn on Bluetooth. The device will automati-cally begin looking for the XGPS150.• Turn on the XGPS150. The blue Bluetooth status light on the XGPS150 will begin to blink slowly (about once per second).• After a few seconds, the XGPS150 will appear as XGPS150-xxxxxx in the list of devices on the touch/iPad/iPhone screen. (The last 6 digitsXGPS1508are part of the XGPS150 serial number andwill be different for each unit.) The word Misc may also appear for a few moments before XGPS150-xxxxxx appears.• Tap XGPS150-xxxxxx in the list of devices to connect to it. The words “Not Paired” will disap-pear and be replaced by the spinning cursor.• After approximately 10 seconds, theXGPS150-xxxxxx name in the device list will change to blue text and the word Connected will appear. The blue LED on the XGPS150 will blink rapidly for a few seconds and then stay illuminated, confirming the two devices have successfully paired and are communicating.Pairing the XGPS150 with an Android device (NOTE: these instructions were written using An-droid OS version 2.1 and may be different if you are using a different version of the Android OS.)• Make sure the mode switch on the XGPS150 is set correctly for your device (see Setup).• Turn on the XGPS150. The blue Bluetooth status light on the XGPS150 will begin to blink slowly (about once per second).• On the Android device go to:Settings->Applications->Development and enable the option for Allow mock loca-tions. This will let the Android device use GPSXGPS1509information from an external device like the XGPS150.• On the Android device go to:Settings->Wireless & networksand turn on Bluetooth.• On the Android device go toSettings->Wireless & networks->Bluetooth settingsand select Scan for devices .• After a few seconds, the word XGPS150-xxxxxx will appear in the list of devices. (Note: the last 6 digits are part of the XGPS150 serial number and will vary from device to device.) At this point, the Android device may say Paired but not connected and the blue Bluetooth indicator XGPS150 will continue to blink slowly.• In order for GPS-enabled apps to use informa -tion from an external GPS, you will likely need to install a helper app on your Android device. This helper app runs in the background and will let apps communicate with the XGPS150. Sev-eral helper apps are available, and we recom-mend using a free app on the Android Market called Bluetooth GPS .Using the Bluetooth GPS helper app with the XGPS150• Please make sure you have completed theXGPS15010steps above in Pairing the XGPS150 with an Android device .• Download and install the Bluetooth GPS app from the Android Marketplace.• Open the Bluetooth GPS app and select the XGPS150 from the pull-down menu on the Main tab.• Check the box next to Enable Mock GPS Provider .• Tap the Connect button. Your Android device will connect to the XGPS150 and begin stream-ing location data to apps on your device. The blue Bluetooth indicator on the XGPS150 will illuminate without blinking.Pairing the XGPS150 with a Blackberry device (NOTE: these instructions were written using a Blackberry Storm 9550 and may be different if you are using a different model of Blackberry smart phone.)• Make sure the mode switch on the XGPS150 is set correctly for your device (see Setup ).• Turn on the XGPS150. The blue Bluetooth light on the XGPS150 will begin to blink slowly (about once per second).• From the Blackberry main menu go to:Manage ConnectionsXGPS15011and turn on Bluetooth.• From the Blackberry main menu go to:Options->Bluetooth->Add Deviceand select Search .• After a few seconds, the name XGPS150-xxxxxx will appear in the list of paired devices. (Note: the last 6 digits are part of the XGPS150 serial number and will vary from device to device.)• From the Blackberry main menu go toOptions->Advanced Options->GPSand select the XGPS150-xxxxxx from the GPS Data Source list of devices. Also, on the same menu, make sure that GPS Services is set for Location On and Location Data is Enabled .If you need additional help connecting the XGPS150 to your device, please contact customer service(***************************).How -ever, due to the enormous number and variety of available devices, you may need to contact the manufacturer of your device for additional instruc-tions.XGPS15012Using the XGPS150Once the XGPS150 is paired with your device, you can begin using apps that utilize GPS information.The XGPS150 includes a non-slip pad for use in a car or on a boat. Slide the XGPS150 into the pad to secure it, making sure that the lip of the pad seals over the top edges of the XGPS150. The XGPS150 is not waterproof, but it will withstand light splashing when it is seated properly in the non-slip pad.A two-piece armband is also included for using the XGPS150 during hiking, geocaching, jogging, cy-cling or other outdoor activities. Use the armband without the extension to secure the XGPS150 around the strap of a backpack. With the exten -sion, the XGPS150 can be secured around your arm.Charging the XGPS150The XGPS150 is charged via the USB connector on the side of the device. To charge, simply con-nect the XGPS150 to the USB port on any com-puter using the included USB cable. A 12V ciga-rette lighter adapter is also included for charging the XGPS150 in a car. It takes approximately 2.5 hours to fully charge the XGPS150.XGPS15013Tips for best performance• Put the XGPS150 in a location with a clear view of the sky: the dashboard of your car, a boat bulkhead, the shoulder strap of a backpack, etc.• The range of the Bluetooth connection will drop as the battery level drops. If you find that the wireless connection is failing, try recharging the XGPS150.XGPS15014SpecificationsDimensions (WxHxD in mm)• XGPS150: 55.0 x 55.0 x 18.5• Non-slip pad: 94.0 x 144.0 x 22.0XGPS150 Voltage• Input voltage: 5 VDCCigarette Lighter Power Adapter Voltage • Input voltage: 12-24 VDC• Output: 5 VDCGPS• 65 Channel SkyTraq engine• Cold start: < 29 sec. typ. (open sky)• Warm start: < 25 sec. typ. (open sky)Bluetooth• CSR engine• Version: 2.1+EDR• Range: ~10m (~33 ft.) (open space)Internal Battery• Capacity: 680 mAh• Operating time: ~8.5 hours• Charging time: ~2.5 hoursEnvironment Requirements• Operating temp: 14˚F - 140˚F (-10˚C - 60˚C)• Storage temp: -4˚F - 176˚F (-20˚C - 80˚C)• Relative humidity: 5% - 95% non condensingXGPS15015ComplianceICC ComplianceThis Class [B] digital apparatus complies with Ca -nadian ICES-003.FCC Compliance This device complies with Part 15 of the FCC Rules. Operation is subject to the following two conditions:(1) this device may not cause harmful interfer -ence, and(2) this device must accept any interference re -ceived, including interference that may cause un-desired operation.Warning: Changes or modifications to this unit not expressly approved by the party responsible for compliance could void the user’s authority to oper-ate the equipment.Note: This equipment has been tested and found to comply with the limits for a Class B digital de -vice, pursuant to Part 15 of the FCC Rules. These limits are designed to provide reasonable protec-tion against harmful interference in a residential installation. This equipment generates, uses and can radiate radio frequency energy and, if not in-stalled and used in accordance with the instruc-tions, may cause harmful interference to radioXGPS15016Compliance (cont’d)communications. However, there is no guarantee that interference will not occur in a particular in-stallation. If this equipment does cause harmful interference to radio or television reception, which can be determined by turning the equipment off and on, the user is encouraged to try to correct the interference by one or more of the following measures:• Reorient or relocate the receiving antenna.• Increase the separation between the equipment and receiver.• Connect the equipment into an outlet on a circuit different from that to which the receiver is con-nected.• Consult the dealer or an experienced radio/TV technician for help.XGPS15017Limited One-Year Warranty This warranty gives you specific legal rights. You may also have other rights which vary from state to state. Dual Electronics Corp. warrants this prod -uct to the original purchaser to be free from de-fects in material and workmanship for a period of one year from the date of the original purchase.Dual Electronics Corp. agrees, at our option, dur -ing the warranty period, to repair any defect in ma-terial or workmanship or to furnish an equal new, renewed or comparable product (whichever is deemed necessary) in exchange without charges, subject to verification of the defect or malfunction and proof of the date of purchase. Subsequent re-placement products are warranted for the balance of the original warranty period.Who is covered? This warranty is extended to the original retail purchaser for products purchased from an authorized Dual dealer and used in the U.S.A.What is covered? This warranty covers all defects in material and workmanship in this product. The following are not covered: software, installation/re -moval costs, damage resulting from accident, mis-use, abuse, neglect, product modification, improp -er installation, incorrect line voltage, unauthorized repair or failure to follow instructions supplied withXGPS15018Warranty (cont’d)the product, or damage occurring during return shipment of the product. Specific license condi -tions and copyright notices for the software can be found via .What to do?1. Before you call for service, check the trou-bleshooting guide in your owner’s manual. A slight adjustment of any custom controls may save you a service call.2. If you require service during the warranty pe-riod, you must carefully pack the product (prefer -ably in the original package) and ship it by prepaid transportation with a copy of the original receipt from the retailer to an authorized service center.3. Please describe your problem in writing and include your name, a return UPS shipping address (P .O. Box not acceptable), and a daytime phone number with your shipment.4. For more information and for the location of the nearest authorized service center please con-tact us by one of the following methods:• Call us toll-free at 1-866-382-5476•***********************Exclusion of Certain Damages: This warranty is exclusive and in lieu of any and all other warran -XGPS15019Warranty (cont’d)ties, expressed or implied, including without limita -tion the implied warranties of merchantability and fitness for a particular purpose and any obligation, liability, right, claim or remedy in contract or tort, whether or not arising from the company’s negli-gence, actual or imputed. No person or represen-tative is authorized to assume for the company any other liability in connection with the sale of this product. In no event shall the company be liable for indirect, incidental or consequential damages.Dual Electronics Corp.Toll Free: 1-866-382-5476©2011 Dual Electronics Corp. All rights reserved.Windows is a registered trademark of Microsoft Corporation in the United States and or other coun-tries. iPod, iPad and iPhone are trademarks ofApple Inc., registered in the US and other countries. “Made for iPod,” “Made for iPhone,” and “Made for iPad” mean that an electronic accessory has been designed to connect specifically to iPod, iPhone, or iPad, respectively, and has been certified by the devel-oper to meet Apple performance standards. Appleis not responsible for the operation of this device orits compliance with safety and regulatory standards. The Bluetooth® word mark and logos are owned by the Bluetooth SIG, Inc. and any use of such marks by Namsung is under license. Other trademarks and trade names are those of their respective owners.NSA1210-V01。
MX1508 SOP
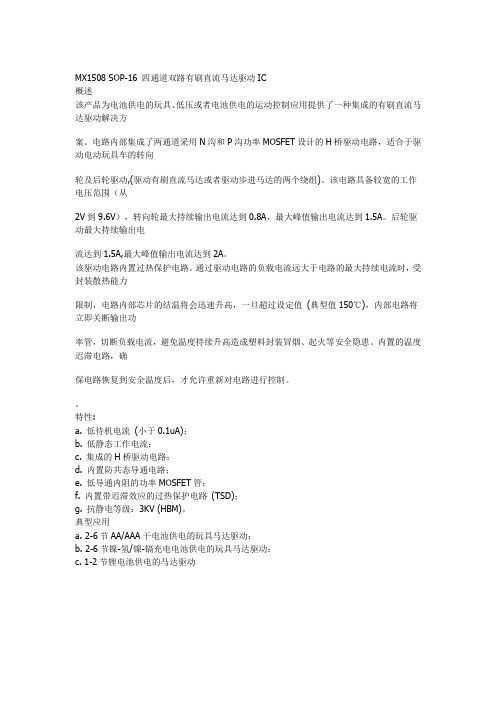
MX1508 SOP-16 四通道双路有刷直流马达驱动IC
概述
该产品为电池供电的玩具、低压或者电池供电的运动控制应用提供了一种集成的有刷直流马达驱动解决方
案。
电路内部集成了两通道采用N沟和P沟功率MOSFET设计的H桥驱动电路,适合于驱动电动玩具车的转向
轮及后轮驱动,(驱动有刷直流马达或者驱动步进马达的两个绕组)。
该电路具备较宽的工作电压范围(从
2V到9.6V),转向轮最大持续输出电流达到0.8A,最大峰值输出电流达到1.5A。
后轮驱动最大持续输出电
流达到1.5A,最大峰值输出电流达到2A。
该驱动电路内置过热保护电路。
通过驱动电路的负载电流远大于电路的最大持续电流时,受封装散热能力
限制,电路内部芯片的结温将会迅速升高,一旦超过设定值(典型值150℃),内部电路将立即关断输出功
率管,切断负载电流,避免温度持续升高造成塑料封装冒烟、起火等安全隐患。
内置的温度迟滞电路,确
保电路恢复到安全温度后,才允许重新对电路进行控制。
特性:
a. 低待机电流(小于0.1uA);
b. 低静态工作电流;
c. 集成的H桥驱动电路;
d. 内置防共态导通电路;
e. 低导通内阻的功率MOSFET管;
f. 内置带迟滞效应的过热保护电路(TSD);
g. 抗静电等级:3KV (HBM)。
典型应用
a. 2-6节AA/AAA干电池供电的玩具马达驱动;
b. 2-6节镍-氢/镍-镉充电电池供电的玩具马达驱动;
c. 1-2节锂电池供电的马达驱动。
ZXDU58_W121(V1.0)30A系列组合电源用户手册
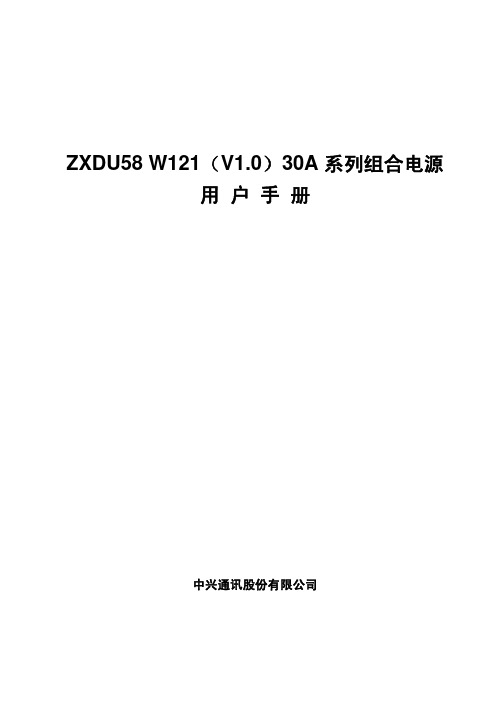
3. 《ZXD1500(V4.0)30A 开关整流器用户手册》
该手册介绍 ZXD1500(V4.0)整流器的功能特点、性能参数、工作原理、 外形结构、安装调试、使用操作、日常维护和运输存储。本手册适用于安 装人员和操作维护人员。
请在安装、操作和维护前仔细阅读以上手册,并注意设备上的各种警示牌及警示 语句。所有的随机资料阅读完毕后请妥善保存,以便日后查阅。
亚特洛纳高速HDMI发送器与接收器说明书
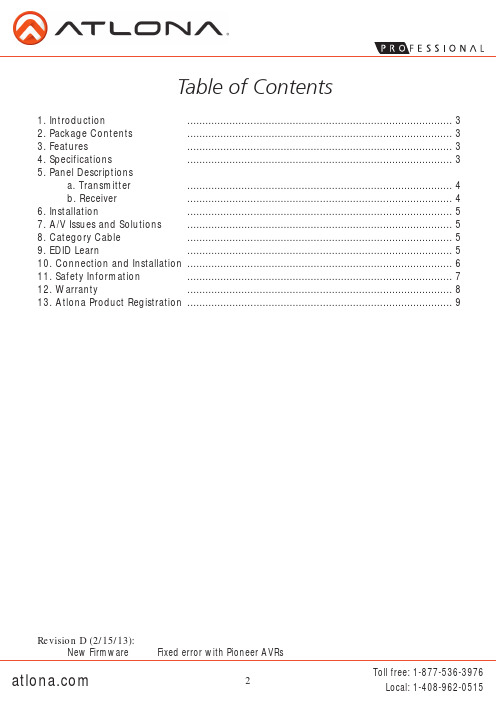
1
2
3
4
1. +5V DC: Connect to 5V DC power supply. 2. CAT IN: Connect category cable from the transmitter’s CAT out 3. EQ: The 8-level equalization dial varies from MAX (long distance) to MIN (short distance).
Sender: Input Port 1 x HDMI Output Port 1 x CAT5e/6/7 Receiver: Input Port 1 x CAT5e/6/7 Outputfree: 1-877-536-3976
Installation
1. Connect the source to the HDMI IN on the transmitter 2. Connect the display to the HDMI OUT on the receiver 3. Use a category cable terminated 568B to connect the transmitter and receiver 4. Connect the power sources to the transmitter and receiver The extenders are now connected. Depending on cable type and distance, some minor adjustments may be needed to ensure the best quality.
Table of Contents
1. Introduction ........................................................................................ 3 2. Package Contents ........................................................................................ 3 3. Features ........................................................................................ 3 4. Specifications ........................................................................................ 3 5. Panel Descriptions
3G150M 用户手册 v1.01
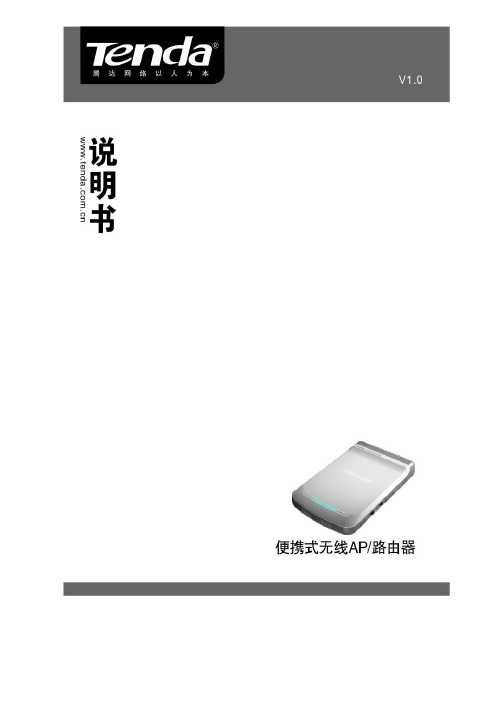
版权声明目录第1章产品简介 (1)1.1产品简介 (1)1.2产品规格 (2)1.3包装清单 (3)1.4面板指示灯及接口说明 (4)第2章产品硬件安装 (6)2.1硬件安装 (6)2.2网络连接拓扑 (7)第3章如何登录到设备 (11)3.1使用有线网卡连接 (11)3.2使用无线网卡连接 (15)3.3登陆WEB设置界面 (16)第4章工作模式设置向导 (17)4.13G路由器模式设置向导 (17)4.2无线接入点模式设置向导 (22)4.3无线信号放大模式设置向导 (22)4.4无线路由器模式设置向导 (24)第5章高级设置 (27)5.1LAN设置 (27)5.2W AN口设置 (29)5.3MAC地址克隆 (33)5.4域名服务器 (34)第6章无线设置 (35)6.1无线基本设置 (35)6.2无线安全设置 (38)6.3高级设置 (41)6.4WPS设置 (43)6.5无线访问控制 (45)6.6连接状态 (45)第7章DHCP服务器 (46)7.1DHCP服务设置 (46)7.2DHCP列表与绑定 (47)第8章虚拟服务器 (48)8.1端口段映射 (48)8.2DMZ主机 (50)8.3UPNP设置 (51)第9章带宽控制 (51)第10章3G流量统计 (53)10.13G流量统计 (53)10.2上网时间统计 (54)第11章安全设置 (55)11.1客户端过滤 (55)11.2URL过滤 (56)11.3MAC地址过滤 (58)11.4防网络攻击 (59)11.5远程WEB管理 (60)11.6W AN口PING (61)第12章路由设置 (62)第13章系统工具 (63)13.1时间设置 (63)13.2动态DNS (64)13.3备份/恢复设置 (65)13.4恢复出厂设置 (67)13.5软件升级 (68)13.6重启设备 (68)13.7修改登录密码 (69)13.8系统日志 (70)13.9退出登录 (70)附录一设置电脑自动获取IP地址 (71)附录二设备加密后如何设置网卡 (74)附录三名词解释 (76)附录四常见问题解答 (77)附录五3G上网卡兼容清单V 0.5 (81)联系方式 (83)第1章产品简介1.1产品简介感谢您购买3G150M便携式3G路由器/无线接入点/无线路由器(以下简称设备)。
MT-1508 Pocket Auto Range Multimeter用户手册说明书
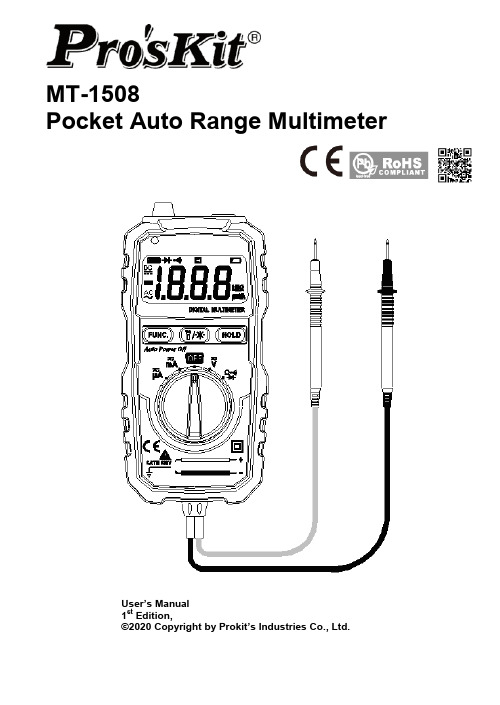
MT-1508Pocket Auto Range MultimeterUser’s Manual1st Edition,©2020 Copyright by Prokit’s Industries Co., Ltd.THE STATEMENTIn accordance with the international copyright law, without permission and written consent, please do not copy the contents of this manual in any form (including storage and retrieval or translation into languages of other countries or regions). The manual is subject to change in future edition without prior notice.Caution“Caution” mark refers to the condition and operation which may cause damage to the instrument or equipment.It requires that you must be careful during the execution of the operation. If you incorrectly perform the operation or do not follow the procedure, it may damage the instrument or equipment. In the circumstances that such conditions are not met or not fully understood, please do not continue to perform any operation indicated by the caution mark.Warning“Warning” mark indicates the condition and operation which may cause danger to u sers.It requires that you must pay attention during the execution of this operation. If incorrectly perform the operation or do not follow the procedure, it may result in personal injury or casualties. In the circumstances that such conditions are not met or not fully understood, please do not continue to perform any operation indicated by the warning mark.Before using the instrument, please read this manual carefully and pay attention to the relevant safety warning information.OVERVIEWThe instrument is a portable digital multimeter. It features stable performance, high accuracy, low power consumption and novel structure, more safe and reliable. I t’s an ideal measuring instrument for users.The instrument can measure DC voltage, AC voltage, DC current, AC current, resistance, diode and connectivity, and non-contact voltage detection function.This manual includes the relevant safety information, warning notices and so on, please read the related contents carefully before using the instrument, and strictly follow all warnings and precautions.SAFETY INSTRUCTIONSThe instrument is designed and manufactured strictly in accordance with the safety standard IEC61010 and in conformity with double insulation, over-voltage standard 600V CAT III and pollution level 2 safety standards.Please follow the manual to use the instrument, otherwise the protection function provided by the instrument may be reduced or invalid.SAFETY OPERATIONWarningIn order to avoid possible electric shock or personal injury, please abide by the following specification:●Before using the instrument, please read the “Safety Instructions” in advance. Use theinstrument in strict accordance with the provisions”, otherwise the protection ability provided by the instrument may be reduced or invalid.●Check the external shell first before using the instrument. Check whether there are anycracks or defects on the plastic parts. Please carefully check the insulator near the input terminal.●If the instrument is not working properly or is damaged, please do not use.●Do not touch the electrified body with more than 30V true effective value AC, 42V AC peak or60V DC.●The instrument shall be used according to the specified measurement category, voltage orcurrent rating.●When it shows low battery indication, please replace the battery in time to avoid anymeasurement error.●Please comply with local and national safety code. Wear personal protection equipment(such as approved rubber gloves, masks and flame retardant clothes, etc.) to prevent being damaged by electric shock and electric arc due to exposed hazardous live conductor.●The voltage applied between input terminals or between each terminal and earth point cannotexceed the specified ratings of the instrument.●Measure a known voltage to determine whether the instrument works properly.●When measuring, correct input terminal, function shift and range shift must be used.●Do not use the instrument around explosive gas, steam or in wet environment.●Do not use damaged probe. Check whether the insulation layer of the probe is damaged,whether there’s any exposed metal or sign of wear. Check the continuity of the probe.●When measuring, please connect the zero line or the ground line first, then connect the livewire; but when disconnecting, please cut off the live wire first, then disconnect the zero line and ground line.●When measuring, please keep your fingers behind the finger protector of the probe.●Before opening the back cover of the instrument, please disconnect the probe from themeasured object.●Do not use the instrument in the environment of exceeding the measurement category (CAT)rating of a single element with the lowest rating among the instrument, probe or accessories.CAT II⏹ INTRODUCTION 1. Flashlight2. Non-contact voltage detecting probe3. Non-contact voltage indicator4. Displaypress and hold it for 2 seconds, the backlight will be turn off. The auto power off function will automatically turn off after approx. 15 seconds of no operation.: Data hold button 7. Red probe of test lead 8. Black probe of test lead General Specifications●Environment condition of use:IEC/EN 61010-1 600V CAT III, pollution level 2 Altitude < 2000 mWorking environment temperature and humidity: 0~40(do not consider when it’s <80% RH, <10)Storage environment temperature and humidity: -10~60(<70% RH, remove the battery) ●Temperature coefficient: 0.1⨯ accuracy /●Maximum voltage allowed between the measuring terminal and the ground: 600V DC or AC RMS●Fuse protection: fuse FF250mA/600V ●Sampling rate: about 3 times/second. ●Display: 3 1/2 bit LCD●Over range indication: LCD display will show “OL”.●e displayed on the LCD display. ●-” ●Power requirement: 2x1.5V AAA batteries ●Dimension: 125*60*26mm Accuracy SpecificationsThe accuracy applies up to one year after the calibration.●Reference condition: environment temperature 18℃ to 28℃, relative humidity is no more than 80%.Frequency range: 40Hz~400Hz;Input protection: Maximum 250V DC or AC RMS.METHOD OF MEASUREMENTAC and DC Voltage Measurement1. Scroll the rotary switch to , press “FUNC.” button, select DC voltage or AC voltagemeasurement.2. Connect the probe in parallel to the circuit or power supply to be measured.3. Read the measuring value from the display. When measuring DC voltage, the display alsoshows the voltage polarity of the red probe test point.Warning●Do not input voltage higher than 600V, it’s possible to display higher voltage, but there maybe risk of damaging the instrument.●When measuring high voltage, be careful to avoid electric shock.●After completing all the measuring operation, make sure to disconnect the probe from themeasured circuit.1. Turn the rotary , press “FUNC.” button, select DC cur rent or AC currentmeasurement.2. Shut off the power supply of the circuit under test. Discharge all the high voltage capacitorson the circuit under test.3. Disconnect the circuit to be measured. Connect the instrument to the circuit to be measuredin series.4. Connect to the power of the circuit, and then read the measuring result from the display. If itdisplays “OL”, it means the input exceeds the measur ing range of the instrument. When measuring the DC and AC, it will show the voltage polarity of red probe test point on the display as well.5. Shut off the power of the circuit under test. Remove the probe of the instrument and restorethe circuit.Warning●To prevent possible electric shock, fire or personal injury, when measuring the current, pleasedisconnect the power of the circuit under test in advance, and fully discharge all the high voltage capacitors, then connect the instrument to the circuit in series.●Do not input above 200mA maximum measurement current value of the instrument,otherwise it may burn the fuse in the instrument.●After completed all the measuring operation, please disconnect the probe from the circuitunder test.1. Turn the rotary switch to ,(if not resistance measurement function, please press2. Connect the probe to the circuit under test in parallel to measure the resistance.3. Read the measuring results from the display.Warning●To prevent possible electric shock, fire or personal injury, before measuring the resistance,please disconnect the power supply of the circuit under test in advance, and fully discharge all the high voltage capacitors.●After completed all the measurement operation, make sure to disconnect the probe from thecircuit under test.Diode Test1. Turn the rotary switch tocathode of the diode to be measured, the reads on the display is the approximate value of diode forward voltage drop. If connected backwards, it will display “OL”.Warning●To prevent possible electric shock, fire or personal injury, before measuring the diode orconnectivity, please disconnect the power supply of the circuit to be measured in advance, and fully discharge all the high voltage capacitors.●If the measured diode is open circuit or in reverse polarity, the instrument will display “OL”. ●After completing all the measurement operations, make sure to disconnect the probe from thecircuit under test.Connectivity Test1. Turnmeasured circuit is less than 50Ω, the buzzer will sound.Warning●To prevent possible electric shock, fire or personal injury, before measuring the diode orconnectivity, please disconnect the power supply of the circuit to be measured in advance, and fully discharge all the high voltage capacitors.●After completing all the measurement operations, make sure to disconnect the probe from thecircuit under test.Non-contact Voltage Detection1. Turn the rotary switch of the instrument to any position except OFF.2. Put the non-contact voltage detecting probe of the instrument close to the live wire of the ACvoltage (less than 5mm).3. The indicator of the non-contact voltage will light up, it shows that there’s AC voltage on thelive wire.INSTRUMENT MAINTENANCEThis section provides the basic maintenance information, including description of replacing fuse and batteries.WarningDo not try to repair the instrument unless you are experienced repair person and have associated calibration, performance test and maintenance information.To prevent possible electric shock, fire or personal injury:●When the cabinet is opened, do not use the instrument to do any measurement.●Remove the input signal before cleaning the instrument.●Specified replacement parts shall be used. Please ask the qualified technicians to repair theinstrument.General MaintenanceUse a damp cloth and a small amount of detergent to clean the housing of the instrument. Please do not use abrasive or chemical solvents.Replace Fuse and BatteryWarning●electric shock or personal injury caused by error reading, when it displays” on the screen, the batteries should be replaced.●period, please remove the batteries to avoid any damage caused by battery leakage.●Use the fuse with specified amperage, fuse ratings, voltage ring and fuse speed.●To avoid electric shock or personal injury, before opening the back cover to replace batteries,the instrument should be shut down and checked to ensure that the probe has already been disconnected from the measuring circuit.Please follow the steps as below to replace the battery:1. Power off the instrument.2. Disconnect the probe from the circuit under test.3. Unscrew and open the cover of battery compartment on the back of this instrument.4. Remove the exhausted batteries, replace with new batteries.5. Close and screw the cover.Please follow the steps as below to replace the fuse:1. Turn off the power of the instrument.2. Disconnect the probe from the circuit under test.3. Unscrew and open the cover on the back of this instrument.4. Remove the damaged fuse, replace with new fuse.5. Close and screw the cover.MT-1508 袖珍型電表使用說明書聲明根據國際版權法,未經允許和書面同意,不得以任何形式(包括存儲和檢索或翻譯為其他國家或地區語言)複製本說明書的任何內容。
Cognex MX-1502 快速参考指南说明书

MX-1502Quick Reference Guide2020June05Revision:1.0.0.10PrecautionsTo reduce the risk of injury or equipment damage,observe the following precautions when you install the Cognex product:l Route cables and wires away from high-current wiring or high-voltage power sources to reduce the risk of damage or malfunction from thefollowing causes:over-voltage,line noise,electrostatic discharge(ESD),power surges,or other irregularities in the power supply.l Changes or modifications not expressly approved by the party responsible for regulatory compliance could void the user’s authority to operate theequipment.l Ensure that the cable bend radius begins at least six inches from the connector.Cable shielding can be degraded or cables can be damaged orwear out faster if a service loop or bend radius is tighter than10X the cablediameter.l This device should be used in accordance with the instructions in this manual.l All specifications are for reference purposes only and can change without notice.LayoutStandard front coverIndicator LEDsSide trigger buttonsPower buttonTouch screenHome buttonSpeaker ventsRecessed area for mobile cameraSlider to lock battery coverBattery coverLanyard hookEnd cap of pistol grip*Trigger button on the pistol grip* *Pistol grip is optional1Using or storing the device outside of the recommended temperature ranges may damage or reduce the lifespan of the battery.Leaving the MX Series Mobile Terminal with a mobile device in direct sunlight for an extended amount of time can raise the temperature above the recommended limit.MX-1502standard front cover model:MX-1502-LR Readers with6.2mm Lens1.Place the rubber insert on the base unit.2.Plug the USB cable into the base unit.3.Put the mobile device on the rubberinsert and connect it to the base unit withthe USB cable.4.Attach the top cover.5.Tighten the screws to fix the top cover.6.Open the back cover to take out thereader battery.7.Plug the pistol grip cable into the gripconnector.8.Insert the reader battery.9.Assemble the reader with the pistol gripand tighten the screws.Installation procedures and specifications are presented in detail in the MX-1502 Reference Manual,which is installed with the DataMan Setup Tool.From the Windows Start menu,select the following to access the manual:All Programs> Cognex>DataMan Software v6.1.0>Documentation.:All cable connectors are keyed to fit the connectors on the reader.not force the connections or damage may occur.Install Software and Documentation and Connect the ReaderTo configure an MX-1502reader,the DataMan Setup Tool software must be installed on a networked PC.The DataMan Setup Tool is available from the DataMan support site:/support/dataman.1.After installing the software,connect the MX-1502to your PC.unch the DataMan Setup Tool and click Refresh.3.Select your MX-1502reader from the list and click Connect.Imager SpecificationsLED WavelengthsThe MX-1502has Regulatory Model R00045(inductive)and Regulatory ModelR00079(non-inductive),and meets or exceeds the requirements of all applicable standards organizations for safe operation.However,as with any electrical equipment,the best way to ensure safe operation is to operate them according to the agency guidelines that follow.Please read these guidelines carefully before using your device.The following specifications apply to the MX-1502readers:CanadianKoreaJapanese StatementFor European Union UsersCognex complies with Directive2012/19/EU OF THE EUROPEAN PARLIAMENT AND OF THE COUNCIL of4July2012on waste electrical and electronic equipment (WEEE).This product has required the extraction and use of natural resources for its production.It may contain hazardous substances that could impact health and the environment,if not properly disposed.diminish the pressure on the natural resources,we encourage you to use the appropriate take-back systems for product disposal.Those systems will reuse or recycle most of the materials of the product you are disposing in a sound way.The crossed out wheeled bin symbol informs you that the product should not be disposed of along with municipal waste and invites you to use the appropriate separate take-back systems for product disposal.If you need more information on the collection,reuse,and recycling systems,please contact your local or regional waste administration.You may also contact your supplier for more information on the environmental performance of this product.Compliance Statements:Wireless Charging StationThe Wireless Charging Station has Regulatory Model1ABA(inductive)and Regulatory Model R00080(non-inductive),and meets or exceeds the requirements of all applicable standards organizations for safe operation.However,as with any electrical equipment,the best way to ensure safe operation is to operate them according to the agency guidelines that follow.Please read these guidelines carefully before using your device.Laser safety statement:Illumination and Lens assembly:This device has been tested inwith IEC60825-13rd ed.,2014.,and has been certified to be the limits of a Class2Laser device.Cognex complies with Directive2012/19/EU OF THE EUROPEAN PARLIAMENT AND OF THE COUNCIL of4July2012on waste electrical and electronic equipment (WEEE).This product has required the extraction and use of natural resources for its production.It may contain hazardous substances that could impact health and the environment,if not properly disposed.In order to avoid the dissemination of those substances in our environment and to diminish the pressure on the natural resources,we encourage you to use the appropriate take-back systems for product disposal.Those systems will reuse or recycle most of the materials of the product you are disposing in a sound way.The crossed out wheeled bin symbol informs you that the product should not be disposed of along with municipal waste and invites you to use the appropriate separate take-back systems for product disposal.If you need more information on the collection,reuse,and recycling systems,please contact your local or regional waste administration.You may also contact your supplier for more information on the environmental performance of this product.CanadianKorean Statement Japanese StatementCompliance)根据中国大陆《电子信息产品污染控制管理办法》( 也称为中国大陆RoHS),以下部份列出了本产品中可能包含的有毒有害物质或元素的名称和含量。
A1508系列温控表

A1508系列温控表A1508系列温控表使用操作说明书特点:⊙热电偶/热电阻/模拟信号通用,软件选择输入 ⊙具有显示、报警、调节功能 ⊙采用先进双自由度PID 算法⊙具备不同系统(快速升降温和慢速加热系统)的自整定功能⊙多种控制输出选择,模块化设计 ⊙抗干扰能力强⊙开关电源100-240V AC⊙适用于系统温度控制场合为了您的安全,在使用前请仔细阅读以下内容!※请遵守下面的要点警告如果不按照说明操作会发生意外。
注意 如果不按照说明操作会导致产品毁坏。
1. 在以下情况下使用这个设备,如(核能控制、医疗设备、汽车、火车、飞机、航空、娱乐或安全装置等),需要安装安全保护装置,或联系我们索取这方面的资料,否则会引起严重的损失,火灾或人身伤害。
2. 必须要安装面板,否则可能会发生触电。
3. 在供电状态中不要接触接线端子,否则可能会发生触电。
4. 不要随意拆卸和改动这个产品,如确实需要请联系我们,否则会引起触电和火灾。
5.请在连接电源线或信号输入时检查端子号,否则会引起火灾。
1.这个装置不能使用在户外。
否则会缩短此产品的使用寿命或发生触电事故。
2.当电源输入端或信号输入端接线时,NO.20AMG(0.50m ㎡)螺丝拧到端子上的力矩为0.74·m-0.9n ·m 否则可能会发生损坏或连接端子起火。
3.请遵守额定的规格。
否则会缩短这个产品的寿命后发生火灾。
4.清洁这个产品时,不要使用水或油性清洁剂。
否则会发生触电或火灾,也将损坏本产品。
5.在易燃易爆,潮湿,太阳光直射,热辐射,振动等场所应避免使用这个单元。
否则可能会引起爆炸。
6.在这个单元中不能有流尘或沉淀物。
否则可能会引起火灾或机械故障。
7.不要用汽油,化学溶剂清洁仪表外壳。
使用这些溶剂会损害仪表外壳。
请用柔软的湿布(水或酒精)清洁塑料外壳。
一、仪表型号二、型号说明三、主要技术参数1、整机参数2、输入(4-20MA. 1-5V输入可订做)3、输出四、面板名称五、面板按键操作1、SET键:在正常显示状态下,点动SET键可进入SV设置菜单,长按SET键可以进入设置菜单。
USB Rover 2850 2-port USB 1.1 40米Cat 5扩展器用户手册说明书

USB Rover® 2850 2-port USB 1.1 40m Cat 5 ExtenderUser GuideThank you for purchasing the USB Rover® 2850,2-port USB 1.1 40 m (131 ft) Cat 5 ExtenderPlease read this guide thoroughly.FCC Radio Frequency Interference Statement WarningThis device complies with FCC Part 15 Subpart B.CE StatementThe product meets European Standard EMC EN 55022 Class B and EN 55024.IC StatementThis Class B digital apparatus complies with Canadian ICES-003.Environmental StatementThis product is RoHS compliant and conforms to the requirements of Directive 2002/95/EC. Saftey StatementsThis product conforms to the standards set out by the CPSIA.This product has a flammability rating of V-1.ContentsIntroduction (4)Product Contents (4)Requirements (4)About the USB Rover® 2850 (4)Local Extender (LEX) and Remote Extender (REX) Descriptions (5)Installation Guide (6)Installing the LEX (6)Installing the REX (6)Connecting the LEX to the REX (7)Connecting a USB device (7)Troubleshooting (8)Specifications (9)Contacting Technical Support (10)Warranty Information (10)Obtaining Warranty Service (11)Technical Glossary (12)IntroductionThe instructions in this guide assume a general knowledge of computer installation procedures, familiarity with cabling requirements, and some understanding of USB devices.NOTE symbol emphasizes additional information that could be useful.CAUTION symbol indicates important information about an operational requirement.Product ContentsPackaged with:• LEX (Local Extender)• REX (Remote Extender)• 2m (6 ft) USB A-B Cable• Quick Start Guide and Warranty InformationRequirementsTo complete the installation you will require the following items that are not included:• USB compatible computer (host computer) with a USB compliant operating system• USB device(s)• Cat 5 Unshielded Twisted Pair (UTP) cable with two RJ45 connectors (if using surface cabling), or Cat 5 cabling with two information outlets and two Cat 5 patch cords with RJ45 connectors(if using premise cabling)A ll references to Cat 5 cable in this document refer to Cat 5e and represent the minimum cablerequirement.About the USB Rover® 2850The USB Rover® 2850 enables users to extend USB devices up to 40m (131 ft). Extension distances of up to 85 meters may be acheivable with some Low-Speed HID devices, such as keyboards and mice. notenotenoteRemote Extender (REX) DescriptionThe REX provides two downstream USB Type A ports for standard USB devices. Additional devices may be connected by connecting USB hubs.ITEMTYPE DESCRIPTION 1Link Port (RJ45)Accepts RJ45 connector for Cat 5 cabling.2 2 Device Ports (USB Type A)Connects to USB1.1/2.0 device(s).Local Extender (LEX) Description The LEX connects to the host computer using the supplied USB A-B Cable.ITEM TYPEDESCRIPTION 1Link Port (RJ45)Accepts RJ45 connector for Cat 5 cabling.2Device Port (USB Type B)Used to connect the LEX to the host computer.2112Installation GuidePreparing your siteThe maximum extension length is reduced by 13.2m (43.3 ft) for each USB hub added between thehost computer and the end device. Extender systems cannot be daisy chained. An extender system can have only one LEX and one REX.1.Determine where the host computer is to be located and set up the computer.2.Determine where you want to locate the remote USB device(s).3.Ensure the cable run (including patch cables) between the host computer and USB device(s) is no greater than 40m.Installing the LEX1.Place the LEX near the host computer.2. P lug the supplied USB cable into the LEX and into an available USB port on the computer.Installing the REX1.Place the REX near the USB device(s) at the desired remote location.USB 1.1 up to 40m over Cat 5REXLEXConnecting the LEX to the REXSurface Cabling1. Plug one end of the Cat 5 cable into the Link port (RJ45) on the LEX.2. Plug the other end of the Cat 5 cable into the Link port (RJ45) on the REX.Premise Cabling1. Plug one end of a Cat 5 patch cord into the Link port (RJ45) on the LEX.2. Plug the other end of the patch cord into the Cat 5 information outlet near the host computer.3. P lug one end of a second Cat 5 patch cord into the Link port (RJ45) on the REX.4. Plug the other end of the second patch cord into the Cat 5 (RJ45) information outlet near the USBdevice.The information outlets at the LEX and REX must be directly connected to each other with Cat 5cabling. There cannot be a switch or router in between the information outlets.Connecting a USB Device1. On the host computer, install any software required to operate the USB device. If necessary, refer to thedocumentation for the USB device(s).2. Connect the USB device(s) to the device port(s) on the REX.PROBLEM CAUSE SOLUTIONThe USB device does not operate correctly.• The USB device ismalfunctioning.• The computer does notrecognize the USB device.• The application software forthe USB device is not operating.1. Un-install and re-install the driver for the USBdevice.2. Update the driver for the USB device.3. Directly connect the USB device to the Host toverify the USB device operates correctly.The USB deviceis detected as an “Unknown Device” in the operating system.• The host computer or USBdevice may not be capable ofsupporting extreme distances.• The USB device’s timing doesnot conform to the USB 1.1specification.1. Connect the LEX to REX using a short cable.2. Unplug the LEX from the host and wait 15seconds. Then plug the LEX back into the host.The operating system reports that a power surge occurred or that the USB device is using too much power.• The Host is not providingenough power to the Extender.1. Connect the LEX to a different USB port on thehost.2. Connect a self-powered USB hub between theREX and the USB device.TroubleshootingThe following table provides troubleshooting tips. The solutions are arranged in the order in which they should be executed in most situations. If you are unable to resolve the problem after following these instructions,pleasecontactTechnicalSupport(*********************)forfurtherassistance.SpecificationsContacting Technical SupportIf you are experiencing problems not resolved by following the steps listed in the Trouble Shooting section, contact Technical Support(*********************)and provide the following information:• Host computer make and model• Operating system installed (e.g. Windows XP, Mac OS X, Windows 7 etc.)• Part number and serial number for both the LEX and REX• Make and model of all USB device(s) attached to the extender• Description of the installation• Description of the problemWarranty InformationLimited Hardware WarrantyIcron Technologies Corporation warrants that any hardware products accompanying this documentation shall be free from significant defects in material and workmanship for a period of up to three years from the date of purchase. Icron Technologies Corporation’s hardware warranty extends to the Licensee, its customers, and end users.The Warranty does not include repair of failures caused by: misuse, neglect, accident, modification, operation outside of a normal operating environment, failure caused by servicing of the device by non-authorized servicers, or failure caused by a product for which Icron Technologies Corporation is not responsible. Hardware RemediesIcron Technologies Corporation’s entire liability and the Licensee’s exclusive remedy for any breach of warranty shall be, at Icron Technologies Corporation’s option, either (a) return of the price paid, or (b) repair or replacement of hardware, which will be warranted for the remainder of the original warranty period or30 days, whichever is longer. These remedies are void if failure of the hardware has resulted from accident, abuse, or misapplication.Limitation of LiabilityThe hardware warranty set forth in this agreement replaces all other warranties. Icron Technologies Corporation expressly disclaims all other merchantability and fitness for a particular purpose and non-infringement of third-party rights with respect to the hardware.No Icron Technologies Corporation dealer, agent, or employee is authorized to make any modification extension or addition to this warranty. Under no circumstances will Icron Technologies Corporation, its suppliers or licensors be liable for any costs of procurement of substitute products or services, lost profits, loss of information or data, or any other special, indirect, consequential, or incidental damages arising inany way out of the sale of, use of, or inability to use Icron Technologies Corporation products or services, even if Icron Technologies Corporation, its suppliers or licensors have been advised of the possibility of such damages.In no case shall Icron Technologies Corporation, its suppliers and licensors’ liability exceed the actual money paid for the products at issue.Since some jurisdictions do not allow the limitation of implied warranties of liability for incidental, consequential, special or indirect damages, the above limitation may not always apply. The above limitation will not apply in case of personal injury where and to the extent that applicable law requires such liability.Obtaining Warranty ServiceTo obtain warranty service and help us serve you better, please provide the following information with your warranty request:• Host computer make and model• Operating system installed (e.g. Windows XP, Mac OS X, Windows 7 etc.)• Part number and serial number for both the LEX and REX• Make and model of all USB device(s) attached to the extender• Description of the installation• Description of the problemContact Icron Technologies Corporation within the warranty period for a Return Material Authorization (RMA) number. Please note that Icron Technologies Corporation will not accept returns without an RMA number. Ensure the product is packaged appropriately for safe shipment and mark the RMA number on the outside of the package. The package must be sent prepaid to Icron Technologies Corporation. It is highly recommended that the package be insured and shipped via a trackable shipping method. The repaired or replaced item(s) will be returned at Icron Technologies Corporation’s expense no later than thirty days after receipt the defective product.Address the returned product to:RMA CoordinatorIcron Technologies Corporation4664 Lougheed Highway, Suite 221Burnaby, BC CanadaV5C 5T5Contacting SalesEmail:***************Tel: +1 604 638 3920Contacting Technical SupportEmail:*********************Tel: +1 604 638 3920Technical GlossaryCategory 5 (Cat 5) Network CablingCategory 5 cable is commonly also referred to as Cat 5. This cabling is available in either solid or stranded twisted pair copper wire variants and as UTP (Unshielded Twisted Pair) or STP (Shielded Twisted Pair). UTP cables are not surrounded by any shielding making them more susceptible to electromagnetic interference (EMI). STP cables include shielding over each individual pair of copper wires and provides better protection against EMI. Cat 5 has been superseded by Cat 5e cabling which includes improved data integrity to support high-speed communications.USB CablesUSB cables have two distinct connectors. The Type A connector is used to connect the cable from a USB device to the Type A port on a computer or hub. The Type B connector is used to attach the USB cable to a USB device.RJ45The Registered Jack (RJ) physical interface is what connects the network cabling (Cat 5) to the LEX and REX unit. You may use either the T568A (Table 1) or T568B scheme (Table 2) for cable termination as the extender uses all four pairs of the cable. RJ45 connectors are sometimes also referred to as 8P8C connectors.RJ45 Pin Positioning Table 1 - T568A WiringTable 2 - T568B WiringPIN PAIR WIRE CABLE COLOR PIN PAIRWIRECABLE COLOR 131WHITE/GREEN 121WHITE/ORANGE 232GREEN 222ORANGE 321WHITE/ORANGE 331WHITE/GREEN 412BLUE 412BLUE511WHITE/BLUE 511WHITE/BLUE 622ORANGE 632GREEN 741WHITE/BROWN 741WHITE/BROWN 842BROWN842BROWNUSB Type APort USB Type A ConnectorUSB Type B ConnectorUSB Type B PortNotesIcron Technologies Corporation 4664 Lougheed Highway, Suite 221 Burnaby, BC CanadaV5C 5T5Tel: +1 604 638 3920Fax: +1 604 638 3930。
摩托拉拉两路通信设备产品说明书

CDM 1550•LS CDM 1550•LS+Professional SeriesTwo-Way Radios and AccessoriesVHF UHF 200 MHz 700 MHzkeeping one step ahead of your competition. You also need communication tools that deliver immediate, reliable access to the people and information you need to get the job done. And that’s exactly what two-way radio gives you.At the touch of a button, two-way radio lets you talk with one, ten, or more people instantly – providing the individual and team communication you need to maximize productivity and meet your customers’ demands. And when you choose aMotorola radio, you know you’re getting a product designed to meet your requirements as a professional.The Intelligent Radio – So Advanced, It Practically Thinks for YouHigh-performing features combined with versatile trunking capabilities make the CDM1550•LS and CDM1550•LS +two-way radios the smart choice to keep mobile work teams performing at their best. The CDM1550•LS and CDM1550•LS +radios incorporate LTR ®trunking capabilities – offering you wide calling range, fast channel access, great privacy,and high user and talkgroup capacity. The CDM1550•LS +also offers innovative PassPort ®trunking. Ideal for users with growing communication needs, PassPort includes all the advantages of LTR trunking plus:• Wide Area Coverage, Seamless Roaming – Automatic switching between networked PassPort sites lets you maintain constant communication over long distances without touching a button• Exceptional Audio Quality – Received Signal StrengthIndicator (RSSI) communication technology utilizes one of the strongest signals available, giving you optimal sound quality• Superior System Access – Automatic site registration/deregistration can reduce busy channels and enhance system efficiency• Efficient Channel Expansion – Direct frequency assignment allows you to add channels and sites over the air without taking radios out of service• Electronic Serial Number Protection – Keeps system resources available by helping to prevent unauthorized radio cloning• Increased Flexibility – Access privileges by Mobile Identification Number* (MIN) allows radios to be directed to specific sites or talkgroups.*Optional PassPort featureCDM1550•LS with LTR ®TrunkingCDM1550•LS and CDM1550•LS +Radio Features15 PassPort and/or LTR Zones (16 talkgroups each)* 16 or 160 Conventional Channels*RSSI IndicatorDisplays signal strength levelLarge Control ButtonsEasy management of menu, navigation, and exit functions Conventional TalkaroundUnit-to-unit communications, bypassing the repeaterHome Channel RevertAutomatic, one-button return to a preferred talkgroup or channel User-Defined ListsChange scan, phone, and call lists on the fly Voice StorageRecord important messages or personal memos Telephone InterconnectPlace and receive phone calls with the radioMDC1200 Signaling (Encode/Decode) Features on Conventional and LTR Zones*• Caller ID – Identifies incoming callers• Selective Call – Lets you call a specific group or individual • Call Alert – Notifies individual users that you ’re trying to reach them • Radio Check – Tells you whether another user ’s radio is activated • Message – Allows you to send and receive pre-programmed messages PassPort Selective Call or Call Alert*Lets you initiate or receive a private call or a private page to a specific userQuick Call II TM on Conventional Zones*Send and receive information via tone or digital signals Roam Request*Optional manual initiation of roaming function Roam Lock*Optional manual lock of the radio onto a site Horn and Lights ActivationNotifies you of calls when you ’re away from your vehicle Additional CDM1550•LS and CDM1550•LS Mobile Features• 12.5/25 kHz switchable channel spacing*• Remote mountable control head • Data capable• Operates on conventional, LTR and PassPort systerms**Only available on certain models. Check with your Motorola Authorized Dealer for availability.Motorola – A Name You Know and TrustFor 75 years, Motorola has been a leader in creating state-of-the-art wireless communications for people like you. The CDM1550•LS and the CDM1550•LS +mobiles uphold that superior standard. What ’s more, each radio is backed by a limited two-year* warranty on parts and labor.So when you select the CDM1550•LS or the CDM1550•LS +mobile, you ’ll experience the same exceptional quality you ’ve come to expect from all Motorola products.*Radio accessories are covered by Motorola ’s one-year accessories warranty.CDM1550•LS +Exceptional Functionality and ConvenienceThe CDM1550•LS and the CDM1550•LS +mobiles utilize the latest in two-way technology to deliver extraordinary performance and ease-of-use, including:• Compact, Ergonomic Design to give you optimal mounting flexibility and durability• 14-Character Alphanumeric Display with User-Friendly Icons to help make the radio ’s information easy to understand • Convenient Menu Navigation so you can program scan,phone, and call lists in virtually no timethe transmissions your radio monitors• Motorola ’s Unique X-Pand ™Audio Enhancement combined with a powerful front-projecting speaker can help reducebackground noise and improve sound quality • Compatible with CES data equipment so that you can configure your radio for specific data applications and needsThe CDM1550•LS +mobile can also be programmed with both LTR and PassPort trunking systems – allowing a smooth transition when your business requires a more extensive calling area for maximum communication efficiency. The radiooperates on 16 or 160 channels as well.Motorola Original ™accessories provide an easy way to turn your CDM1550•LS or CDM1550•LS +mobile radio into a custom communication solution to fit your business requirements —maximizing on-the-job productivity and efficiency for mobile work teams and individuals. Listed below is just a portion of the accessory portfolio available for the CDM1550•LS and CDM1550•LS +. Call today for a complete accessory listing.CDM1550•LS CDM1550•LS+Radio AccessoriesTalk However You WantEnhanced Keypad Microphone —AARMN4026You can dial phone numbers on this microphone ’s full keypad, or customize its three programmable buttons with any control head features.Visor Microphone —AARMN4027Attach this microphone to your visor or hat for hands-free operation of your radio (must be used with an external PTT).Push Button Push-to-Talk —RLN4857Simply depress the button to talk with other users.Foot Switch Push-to-Talk —RLN4856A handy foot switch provides hands-free PTT functionality.Gooseneck Mount Push-to-Talk —RLN4858This PTT mounts conveniently on your steering wheel column for control that ’s right at your fingertips.Telephone Style Handset —AAREX4617 Conduct private conversations on your radio quietly and discreetly.Get Your Message Across13-Watt Speaker —RSN4001Powerful sound control allows you to increase your radio ’s volume output when working in noisy environments.Control Station —RLN5403AThe quick convenient way to convert a CDM Series mobile radio into a fully funtional base station.Take It With YouHigh-Profile Mount —GLN7317Offers a space-saving option for vehicles where every inch counts.Key Lock Mount —RLN4779Securely mounts and locks radio in your vehicle to protect against theft.Power It Up1-25 Watt Power Supply —HPN4002For use with low power radios. Provides power for using mobile radio on a desktop.25-60 Watt Power Supply —HPN4001For use with high power radios. Provides power for using mobile radio on a desktop.Enhance Your Calling Range200 MHz Wave Roof Mount Antenna — HKAD4001140-174 MHz VHF 3dB Gain Roof Mount Antenna —HAD4014494-512 MHz UHF 3.5dB Gain Roof Mount Antenna —HAE4013450-470 MHz UHF 5dB Gain Roof Mount Antenna —RAE4004ARB746-794 MHz 3dB Gain Antenna —RAF4221CDM1550•LS and CDM1550•LS +Radio SpecificationsOperating Temperature -30 to +60°C Storage Temperature -55 to +85°C Thermal Shock -40 to +85°C Humidity 95% RH @ 8 Hr.ESDIEC 801-2 KV Water Intrusion IPX4Packing TestImpact TestApplicable MIL-STD 810C810D810EMethods ProceduresMethods ProceduresMethods ProceduresLow Pressure 500.11500.22500.32High Temperature 501.11,2501.21,2501.31,2Low Temperature 502.12502.21,2502.31,2Temperature Shock 503.11503.21503.31Solar Radiation 505.11505.21505.31Rain 506.12506.22506.32Humidity 507.12507.22,3507.33Salt Fog 509.11509.21509.31Dust 510.11510.21510.31Vibration 514.28,10514.31514.41Shock 516.21,5516.31516.41VHF200 MHzUHF700 MHzFrequencies136–174 MHz,217–218 MHz, 403–470 MHz, 746–747 MHz,219–220 MHz,450–512 MHz 762–764 MHz 220–222 MHZ Channel Spacing 12.5/20/25 kHz 12.5 kHz 12.5/20/25 kHz 12.5 kHz Frequency Stability±2.5 ppm±2.5 ppm±2.5 ppm±1.5 ppm(-30°C to +60°C, +25°Ref.)Sensitivity (12 dB SINAD) EIA 0.3 µV 0.23 µV typical 0.30 µV (0.25 µV typical)0.3 µV 0.23 uV typical 0.35 µV (0.3 µV typical)Intermodulation************75dB************75dB78 dB @ 25 kHz 75 dB @ 25 kHz Adjacent Channel Selectivity ************65 dB (TIA 603)************65 dB (TIA 603)80 dB @ 25 kHz 40 dB (TIA 603-A)75 dB @ 25 kHz 40 dB (TIA 603-A)Spurious Rejection************75 dB ************75 dB 80 dB @ 25 kHz 75 dB @ 25 kHz Rated Audio3W Internal 3W Internal 3W Internal 3W Internal (External audio w/4 ohm speaker)13W External 13W External 13W External 13W External Audio Distortion @ Rated Audio 3% typical 3% typical 3% typical 3% typical Hum and Noise -40 dB 12.5 kHz -40 dB -40 dB 12.5 kHz -40 dB -45 dB 25 kHz-45 dB 25 kHzAudio ResponseTIA603 & ETS300 &+1 to -3 dB TIA603 & ETS3000 & +1 to -3 dB CEPT 84 Annex 2CEPT 84 Annex 2Conducted Spurious Emmision -57dBm < 1 GHZ -57dBm < 1 GHz -57dBm < 1 GHZ -57dBm < 1 GHz FCC Part 15-47dBm > 1 GHZ-47 dBm > 1GHz-47dBm > 1 GHZ-47 dBm > 1GHzVHF200 MHzUHF700 MHzFrequencies136–174 MHz217–218 MHz (Talkaround),403–470 MHz 776–777 MHz, 219–220 MHz,450-512 MHz792 –794 MHz,220–221 MHz (Talkaround),746–747 MHz (Talkaround),221–222 MHz 762–764 MHz (Talkaround)Power Output 1–25 W or 25–45 W 1–25 W 1–25 W or 25–40 W 1–15 W Frequency Stability±2.5 ppm ±2.5 ppm ±5 ppm @ 25 kHz ±1.5 ppm (-30°C to +60°C, +25°Ref.)±**************Modulation Limiting±***********±2.5 kHz±***********±2.5 kHz±4.0 @ 20 kHz ±4.0 @ 20 kHz ±5.0 @ 25 kHz ±5.0 @ 25 kHz Conducted and Radiated -36 dBm < 1 GHz -16 dBm -36 dBm < 1 GHz -16 dBm (except – 40 dBm Emissions-30 dBm > 1 GHz -30 dBm > 1 GHz from 1559 to 1610 MHz)Channel Spacing 12.5/20/25 kHz 12.5 kHz12.5/20/25 kHz 12.5 kHzFM Hum & Noise -40 dB 12.5 kHz - 40 dB typical -40 dB typical - 40 dB typical -45 dB 25 kHz Adjacent Channel Power *************-60 dB *************-60 dB -70 dB @ 25 kHz -70 dB @ 25 kHz Audio Response TIA 603 & ETS300 &+1 to -3 dB TIA 603 & ETS300 &+1 to -3 dB CEPT 84 Annex 2CEPT 84 Annex 2Audio Distortion3% typical3% typical 3% typical3% typical FM Modulation Designator 11K0F3E (12.5 kHz)11K0F3E 11K0F3E (12.5 kHz)11K0F3E 16K0F3E (25 kHz)16K0F3E (25 kHz)Adjacent Channel Coupled PowerN/AN/AN/AComplies with 47 CFR 27.53 (d) (1)VHF200 MHzUHF700 MHzChannel Capacity Trunking zone capacity15151515Trunking talkgroup capacity (per zone)16161616Conventional channel capacity 16 or 1601616 or 16016Typical RF Output VHF Low Power 1-25W VHF High Power 25-45W 200 MHz1-25W UHF Low Power 1-25W UHF High Power 25-40W 700 MHZ 1-15WFrequency VHF 136-174 MHz200 MHz 217-218 MHz, 219-222 MHz UHF 403-470 MHz, 450-512 MHz700 MHz746-747 MHz, 762-764 MHz, 776-777 MHz, 792-794 MHz Dimension (H x W x L)VHF/UHF Low Power and 200 MHz 2.34” x 7.05” x 7.32” (60 mm x 179 mm x 186 mm)VHF/UHF High Power and 700 MHz 2.34” x 7.05” x 7.79” (60 mm x 179 mm x 198 mm)WeightVHF/UHF Low Power and 200 MHz 3.15 lbs. (1.43 kg)VHF/UHF High Power and 700 MHz 3.5 lbs. (1.59 kg)Current Drain VHF 200UHF 700Standby.3 A .3 A .3 A .3 A Rx @ rated, external 8 ohm 1.5 A 1.5 A 1.5 A 1.5 A Transmit 7 A @ 25W 7 A @ 25W 8 A @ 25W 7 A @ 15W 13.5 A @ 45W 13.5 A @ 40W FCC DescriptionAZ492FT3796 (25W, 136-174 MHz)AZ492FT3795 (45W, 136-174 MHz)ABZ99FT3081 (25W, 217-218/219-222 MHz)AZ492FT4835 (25W, 403-470 MHz)AZ492FT4830 (40W, 403-470 MHz)AZ492FT4829 (25W, 450-512 MHz)AZ492FT4836 (40W, 450-512 MHz)ABZ99FT5001 (15W, 746-747/762-764/776-777/792-794 MHZ)MOTOROLA and the Stylized M Logo are registered in the US Patent and Trademark Office. All other product or service names are the property of their respective owners.© Motorola, Inc. 2003./cgissMD-CDM1550LS-04。
讯实O口网关MX用户手册

2.4 拨号及路由 ...................................................................................................................................................... 2-11 2.4.1 号码位图 .............................................................................................................................................. 2-11 2.4.2 路由表 .................................................................................................................................................. 2-12 2.4.3 路由表应用举例.................................................................................................................................... 2-16 2.4.4 IP 过滤 .................................................................................................................................................. 2-17
MX150双行头部器件说明书
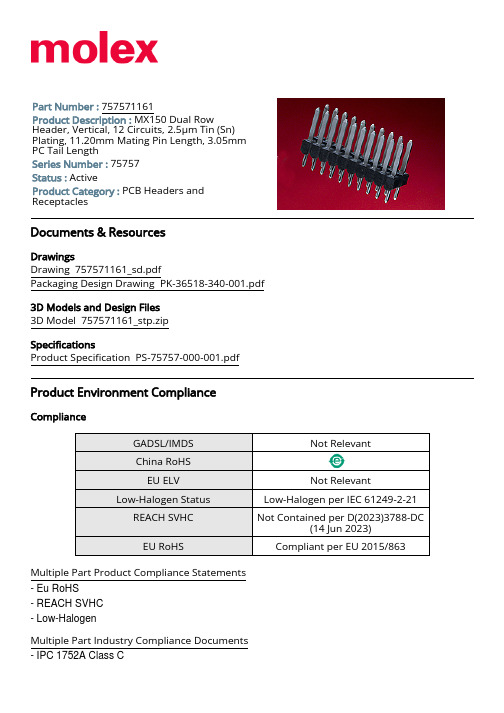
Breakaway Circuits (Loaded) Circuits (maximum)
Color - Resin Durability (mating cycles max)
First Mate / Last Break Glow-Wire Capable Guide to Mating Part
Multiple Part Industry Compliance Documents - IPC 1752A Class C
- IPC 1752A Class D - Molex Product Compliance Declaration - IEC-62474 - chemSHERPA (xml) EU RoHS Certificate of Compliance
Specifications Product Specification PS-75757-000-001.pdf
Product Environment Compliance
Complian RoHS
EU ELV Low-Halogen Status
REACH SVHC
Shrouded Temperature Range - Operating
Termination Interface Style
Solder Process Data
Max-Duration Lead-Free Process Capability
Max-Cycle Max-Temp
None Brass
3.50 x 6.00mm dual row grid PCB Header
MX150 Sealed and Unsealed Connector System MX150 822350702423
Binary 2CAT Extender 产品说明书
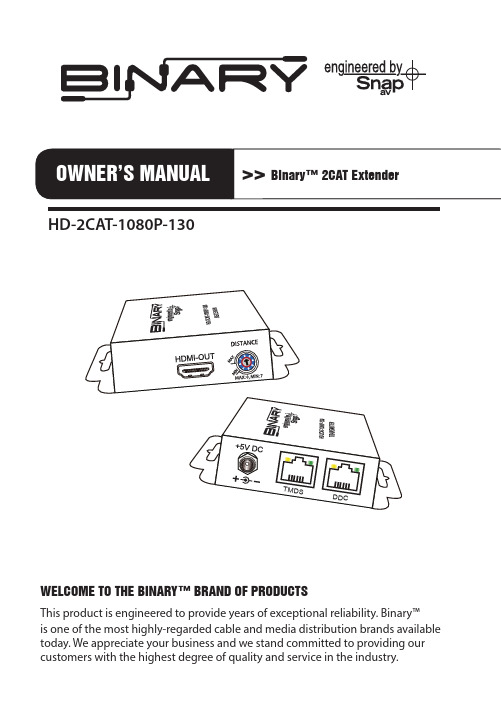
HD-2CAT-1080P-130WELCOME TO THE BINARY™ BRAND OF PRODUCTSThis product is engineered to provide years of exceptional reliability. Binary™ is one of the most highly-regarded cable and media distribution brands available today. We appreciate your business and we stand committed to providing ourcustomers with the highest degree of quality and service in the industry.IMPORTANT SAFETY INSTRUCTIONS1. Read and follow all instructions and warnings in this manual.Keep for future reference.2. Do not install near any heat sources such as radiators, heat registers, stovesor other apparatus (including amplifiers).3. Do not install the unit near water or where moisture is present.4. Clean with a dry cloth.5. Unplug this apparatus during lightning storms or when unused for longperiods of time.6. Protect the power cord from being walked on or pinched particularly at plug,convenience receptacles, and the point where it exits from the apparatus.7. Refer all servicing to qualified service personnel. Servicing is required when theapparatus has been damaged in any way, such as when the power-supply cord or plug is damaged, liquid has been spilled or objects have fallen into theapparatus, the apparatus has been exposed to rain or moisture, does notoperate normally, or has been dropped.8. To completely disconnect this equipment from the AC mains, disconnectthe power supply cord plug from the AC receptacle.CAUTION: To reduce the risk of electrical shock, inspect the premises carefully.Do not use the unit if proper equipment grounding cannot be verified. PACKAGE CONTENTS• (1) Transmitter• (1) Receiver• (4) Mounting Screws• (8) Rubber Feet• (1) 5V DC 2A Power supply• (1) User manualINTRODUCTIONThe HD-2CAT-1080P-130 extends HDMI® over two Cat5e/6 cables allowing video and audio transmission.FEATURES• H DMI 1.3c compliant• Extend the transmission up to 200 ft. from the HDMI source atHD 1080i or 720p 24-Bit on Cat6• E xtend the transmission up to 166 ft. from the HDMI source atFull HD 1080p 24-Bit on Cat6• H DCP compliant• Maximize adjustable 8-level equalization control• Uncompressed 7.1 channel digital HDMI over Cat5e/6cable transmission• DTS-HD Master and Dolby TrueHD audio support• W all-mountable housing design for easy installationNote: The transmission distance is subject to the grade of installed cable(s), source device, and display. Any keystone jack along the transmission path will reduce the transmission performance significantly.1. HDMI IN: Connect to a HDMI source with a HDMI male-to-male cable2. Latch-locking power jack: Connect to 5V DC power supply.3. TMDS: Transmission Minimized Distance Signal (Audio/Video)4. DDC: Display Data Channel (Data)TRANSMITTERNOTE: Transmission distance up to 200 feet at 1080i on Cat6, 165 feet at 1080pon Cat6, and 130 feet at 1080p on Cat5e (24-Bit).5. Latch-locking power jack: Connect to 5V DC power supply.6. TMDS: Transmission Minimized Distance Signal (Audio/Video)7. DDC: Display Data Channel (Data)8. H DMI OUT: Connect to a HDMI display with a HDMI male-to-male cable 9. Rotary control: Adjust the 8-level equalization control to the received HDMI signals. The HDMI signal level varies from 0 (strongest) to 7 (weakest) for respective transmission length from longest possible range to short distance. Adjust the signal level from 7 to 0 and stop turning the rotary switch when the audio/video is playing normally. Inappropriate signal level setting may cause an overpowering issue that would shorten the product life significantly.RECEIVERSET-UPINSTALLATION1. Test all associated equipment and cables in the system for proper operation. Turn off all power before proceeding.2. Make sure the HDMI cables being used do not exceed 1.0M (3.28 ft) andare at least 26 AWG. Any length longer than this may cause intermittence issues. To ensure maximum performance, use high-quality HDMI cables capable of transmitting 1080p signals.3. Determine the best placement of the unit based on how it will be incorporated into the system design. Leave enough room to reach the EQ adjustment after installation.4. Make sure both CAT5e or CAT6 cables are properly terminated (EIA/TIA-568B is recommended) and connected as shown in the diagram to the left. For proper connection, see pin-out diagram below. Both Cat cables must be connected.5. Connect the HDMI cables as shown in the diagram to the left.6. Turn on all associated equipment, plug in the 5V DC power, to either the transmitter or receiver, and verify that the signal LEDs are illuminated.Note: There is no need to power both units, only one power connectionis needed.7. If a flickering, blinking, or snowy image is seen, adjust the EQ dial to improve the cable signal. An EQ set to zero “0” stands for the strongest signal for longer cable lengths, while 7 is for short cable lengths. Try adjusting the EQ from 7 to 0 until picture is clear.8. Once you have a picture, turn clockwise towards 7 until you no longer have a picture; adjust counter clockwise until picture comes back. This will ensure you have reached the optimal setting.Cat5e/6EIA/TIA-568B• Pin 1 - White / Orange• Pin 2 - Orange• Pin 3 - White / Green• Pin 4 - Blue• Pin 5 - White / Blue• Pin 6 - Green• Pin 7 - White / Brown• Pin 8 - BrownGold Pins Facing UpSPECIFICATIONS*Note: Specifications are subject to change without notice. Dimensions and weight are approximate.WARRANTY2-Year Limited WarrantyThis Binary™ Product has a Two-Year Limited Warranty. This warranty includes parts and labor repairson all components found to be defective in material or workmanship under normal conditions of use. This warranty shall not apply to products which have been abused, modified or disassembled. Products to be repaired under this warranty must be returned to SnapAV or a designated service center with prior notification and an assigned return authorization number (RA).For Technical Support: 1-866-838-5052131213-1150。
Moxa Mini PCI Express Multiport Serial Boards说明书
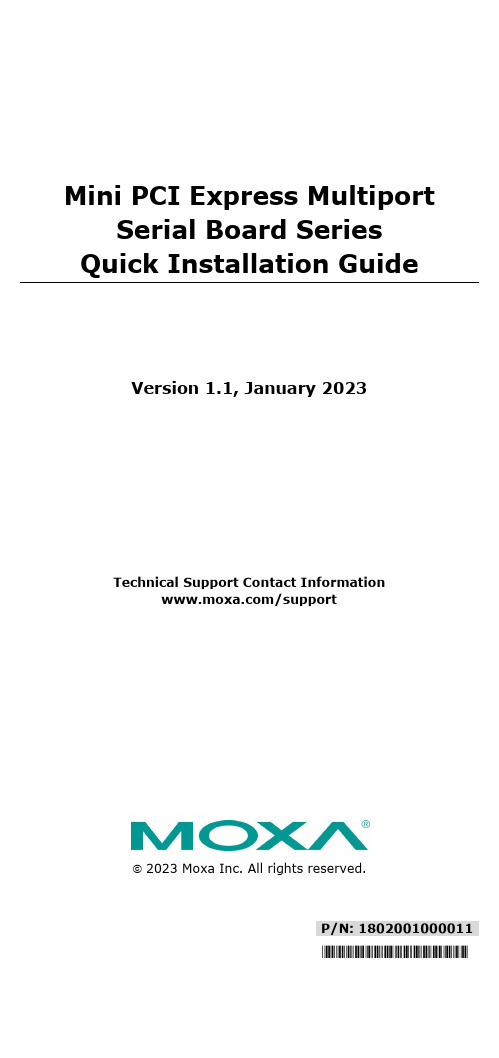
P/N: 1802001000011 *1802001000011*Mini PCI Express MultiportSerial Board Series Quick Installation GuideVersion 1.1, January 2023Technical Support Contact Information/support2023 Moxa Inc. All rights reserved.OverviewMoxa’s new Mini PCI Express Multiport Serial Boards Series fulfills a customized expansion need and provides a faster response to market. We have designed the Mini PCI Express multiport serial boards for use by industrial automation system manufacturers, system integrators, and industrial PC makers.Moxa’s Mini PCIe Express Multiport Serial Boards CP-100N Series includes the following models.Model Name DescriptionCP-102N-T 2-port RS-232 Mini PCI Express serial boardCP-102N-I-T 2-port RS-232 Mini PCI Express serial board with 2.5 kV capacitive isolationCP-132N-T 2-port RS-422/485 Mini PCI Express serial boardCP-132N-I-T 2-port RS-422/485 Mini PCI Express serial board with2.5 kV capacitive isolationCP-104N-T 4-port RS-232 Mini PCI Express serial boardCP-104N-I-T 4-port RS-232 Mini PCI Express serial board with 2.5 kV capacitive isolationCP-134N-I-T 4-port RS-422/485 Mini PCI Express serial board with2.5 kV capacitive isolationCP-114N-T 4-port RS-232/422/485 Mini PCI Express serial board Package ChecklistBefore installing the Mini PCI Express board, verify the package contains the following items:•Moxa Mini PCI Express multi-serial board (CP-104N-I-T, CP-134N-I-T, CP-114N-T models have the main board and I/O boards) •Moxa DB9 brackets•Internal connection cable 25 cm•Quick installation guide (printed)•Warranty cardNOTE The cable type, cable volume, and DB9 bracket volume might differ for different product models.Notify your sales representative if any of the above items aremissing or damagedOptional AccessoriesModel Description Suitable modelsCBL-M9HSF1x10H-15-01 10-pin female to 1 DB9male serial cable, 15 cm CP-102N-I-T CP-132N-I-TCBL-M9HSF1x10H-15-02 10-pin female to 1 DB9male serial cable, 15 cm CP-102N-T CP-132N-TCBL-M9x2HSF2x10H-15 20-pin female to 2 DB9male serial cable, 15 cmCP-104N-TCBL-HSF2x10-15 20-pin female to 20-pinfemale serial cable, 15cm CP-104N-I-T CP-134N-I-T CP-114N-TMechanical Drawing CP-102N-T/CP-132N-TCP-102N-I-T/CP-132N-I-TCP-104N-TCP-104N-I-T/CP-134N-I-T Mainboard Dimensions (Mini PCIe)(Mainboard size is the same with CP-104N-T)I/O Board DimensionsCP-114N-TMainboard Dimensions (Mini PCIe)I/O Board DimensionsBracket SizeHardware Installation ProcedureThe Mini PCI Express board must be plugged into the PC beforeinstalling the driver. The following steps show how to install the Moxa Mini PCI express cards.1. Find the Mini PCIe slot in your computer.2. Insert the Mini PCIe multiport serial board and lock the screws.3. Unscrew to remove the blank expansion plate. (We use MoxaV2406C as an example.)NOTE Moxa Mini PCIe multiport serial boards are suitable for Moxa's IPC models that have mini PCIe interfaces and expansion slots, such as the MC-7400 Series, V2403C Series, and V2406CSeries. The bracket size matches the expansion slot dimensions of the IPC models.For the models (CP-102N-T, CP-102N-I-T, CP-132N-T, CP-132N-I-T, CP-104N-T) without I/O boards.4. Unscrew the hexagonal copper pillars on the cable (DB9Connector) and use them to connect the provided cables with the bracket.5. Insert the plate through the blank expansion slot and lock thescrews.6. Connect the Mini PCIe multiport serial board with the cables.For the models (CP-104N-I-T, CP-134N-I-T, CP-114N-T) with I/O boards.4. Unscrew the hexagonal copper pillars on the I/O board and lockthe I/O board with the bracket.5. Insert the I/O board with the bracket through the blank plate holeand lock the screws.6. Connect the I/O board to the Mini PCIe multiport serial board withthe serial cables.NOTETo pull out the internalconnection cable safely from the boards, you should perpendicularly pull it out as shown in the image on the right. Also, pull out the cable gently.Software Installation Information1. Get the driver at . Based on the OS type, choosethe corresponding driver. 2. Installing the driver:• For Windows OS (Take the installation of Win7 as an example)Unzip and execute the .exe fileFollow the instructions to install the drivers •For LinuxExecute the following commands from the Linux prompt: Get the driver at and unzip the file:#cd /#mkdir moxa #cd moxa #cp /<driverdirectory>/driv_linux_smart_<version>_build_<build_dat e>.tgz. #tar -zxvfdriv_linux_smart_<version>_build_<build_date>.tgz Install the driver:#cd mxser #./mxinstallDIP Switch SettingOn OFF (Default)SW1 Enable 120-ohm termination resistorDisable termination resistor SW2 1K-ohm pull-high/low resistors150K-ohm Pull-high/low resistors SW3 Reserved for future feature SW4Reserved for future featurePin AssignmentsMale DB9Pin RS-232RS-422/RS-485-4W RS-485-2W1 DCD TxD- (A) –2 RxD TxD- (B) –3 TxD RxD+ (B) Data+ (B)4 DTR RxD- (A) Data- (A)5 GND GND GND6 DSR – –7 RTS – – 8CTS– –。
Zenith MX150 MX250 自动转换开关网络卡 50P-2035 维护与操作手册说明书
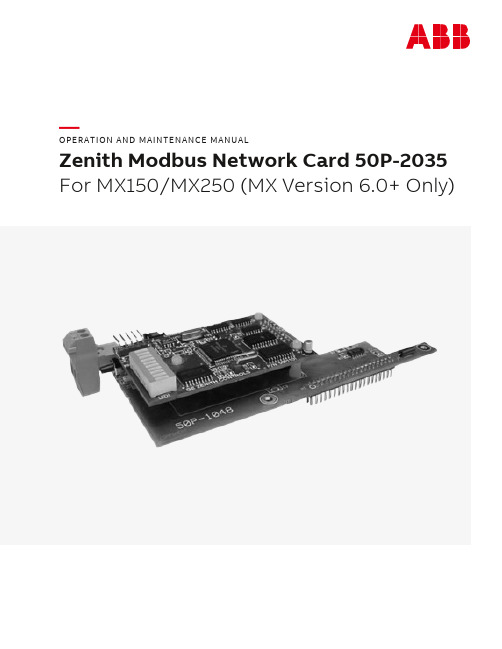
—OPERATION AND MAINTENANCE MANUALZenith Modbus Network Card 50P-2035 For MX150/MX250 (MX Version 6.0+ Only)ABB Zenith disclaims any and all liability for use of third-party application software that will be used to control the Automatic Transfer Switches.PageOverview (01)LED Indicator (01)Installation (02)Installation on the Controller (02)Termination Resistor (02)Configuring a Modbus Network Card (02)Testing a Modbus Network (03)CDP Programmable Exercisers (03)CDT Exercisers (3)Operation (04)Setting System Time (04)Operation with In-Phase Monitor (04)Operation Under Battery Backup (04)Appendix A – Read Only Register List......................................................................................................................05-12 Appendix B – Read/Write Register List................................................................................................................13-14 Appendix C – Modbus Network Card. (15)Appendix D – Connections for Configuring and Testing the Modbus Card (16)Appendix E – RS485 Multi-Drop Connection (17)Appendix F – Installation of Modbus Card on Controller (18)Appendix G – Modbus Protocol Illustration......................................................................................................19-21 Appendix H – Configuring Controller for Modbus (MX150/250). (22)Bill of Materials (23)Components for the Modbus Option (ZNET250M) (23)Components for the Modbus Card Configuration (23)Troubleshooting (24)Testing a Modbus NetworkThe Modbus network can be tested using the compo-nents in the Modbus Configuration package (ABB Zenith Part # 50P-1124). Reference Appendix D for connections.1.If testing a network consisting of more than onecard, make sure that all of the cards are daisychained as shown in Appendix E. Verify that allModbus cards are in the run mode (jumper J4 onthe Modbus card must not be installed).Termination jumper (J6) is only installed on thelast card on the network daisy chain.2.Connect the RS232/485 converter (ABB Zenith Part# 50W-1208) to the PC that contains theConfiguration software (ABB Zenith Part # 50P-1111).A cable needs to be connected to the RS485 connectorof the Modbus card and the RS485 connector of theRS232/485 connector. Check to make sure that thepolarity connections are correct. (See Appendix D)3.Run the Configuration software on the PC.4.Press the TEST button and then verify that the settingsin the Communication Settings section match the settings of the Modbus network. If necessary, make changesto the settings and click the NEXT button.5.The software will now scan the network and displaythe serial number of all controllers, which have theModbus card attached. The user can select any ofthe listed serial numbers and execute a load test ona controller associated with the selected serial num-ber, but only one controller can be tested at a time. CDP Programmable ExercisersCDP Programmable Exercisers are an option on theMX150 and MX250. They allow the controller to be pro-grammed to automatically test the generator and Automatic Transfer Switch. Up to seven exercisers can be programmed to run on a daily, 7 day, 14 day, or 28 day basis; or up to 24 exercisers can be programmed to run on a yearly basis.Configuration information regarding CDP Programmable Exercisers is available in the Exerciser Configuration Register (Holding Register 40063):Bit 0 of the Exerciser Configuration Register (Coil 81) indicates whether the controller is configured for CDTor CDP Programmable Exercisers. A one means the con-troller is configured for CDP Programmable Exercisers. Bit 2 of the Exerciser Configuration Register (Coil 82) indicates whether or not the CDP Programmable Exercisers can be configured to run under load (trans-fer the ATS to the generator). A zero indicates that exercisers can only run No-Load. A one indicates that exercisers can be programmed to run Load or No-Load. Holding Registers 40101 through 40110 are provided to control and report the status of the CDP Exercisers. These registers contain valid data only if the controller is configured for CDP Exercisers. If the controller is config-ured for CDP Exercisers, then Holding Register 40063, Bit 0 (Coil 81) will be set to 1.Reading the CDP Exerciser Holding RegistersThe controller may be programmed for multiple exer-cisers, depending on the status of the Exerciser Schedule Selection. All data relevant to every exerciser is read out through Holding Registers 40101 through 40110. These registers will contain data describing one exerciser at a time. The value of Holding Register 40101, “Exerciser Record Pointer”, determines which exerciser is presently being displayed in Holding Registers 40102 through 40109.To read the contents of a different exerciser, the Exerciser Record Pointer must be written. For example, in order to read data about CDP Exerciser #3, the Exerciser Record Pointer must be set to 3.The controller will automatically place all exercisers in chronological order.CDT ExercisersCDT Exercisers are a standard feature of the MX150 and MX250 (unless replaced by CDP Programmable Exercisers). They allow the controller to be pro-grammed to automatically test the generator and Automatic Transfer Switch. The exerciser will run at the same time of day on a daily, 7 day, 14 day, or 28 day basis. Programming of the CDT Exerciser can be done only at the HMI on the front panel of the MX150 or MX250.Configuration information regarding CDT Exercisers is available in the Exerciser Configuration Register (Holding Register 40063):Bit 0 of the Exerciser Configuration Register (Coil 81) indicates whether the controller is configured for CDT or CDP Programmable Exercisers. A zero means the controller is configured for CDT Exercisers. Conversely, bit 1 implies the controller is configured for the CDP Exerciser.Bit 1 of the Exerciser Configuration Register (Coil 82) indicates whether or not the CDT is configured for Load Exercises. A one indicates the CDT will run a Load Exercise. A zero indicates the CDT will run a No-Load Exercise.The upper byte of the Exerciser Configuration Register (bits 15 through 8) indicates the CDT Exerciser Run Duration, in minutes.Setting System TimeHolding Registers 40094 through 40099 are provided to control and report the status of the controller’s System Time. Reading Holding Register 40094 through 40099 will report the current Hour, Minute, Day, Month, Year, and Day of Week to which controller’s internal clock is currently set.Writing the System Time Holding Registers Holding Registers 40094 through 40098 must be written using a Write Multiple Holding Register Command (Function Code 16). This is to ensure that the data con-tained in these registers is a complete ordered set. Any attempt to write Holding Registers 40094, 40095, 40096, 40097, or 40098 with a Write Single Holding Register Command (Function Code 6), or a Write Multiple Holding Register Command (Function Code 16) that does not include the entire range of 40094 - 40098, will result in an Illegal Data Address exception response from the Modbus Card.Note: Holding Register 40099, “System Time-Day of Week” is Read Only. The value of this register is auto-matically computed and updated by the controller, based on the calendar date.Operation with In-Phase Monitor Special consideration is required if the controller is con-figured with the In-Phase Monitor. Most Modbus net-work data and control are unavailable while the In-Phase Monitor is waiting for phase synchronization. The Modbus Network Card will return a “Slave Device Busy”exception code (06h) to all Modbus queries, except for queries to the System Busy Status Register (Holding Register 40112) or the System Busy Control Register (Holding Register 40113).If the Modbus Network Card returns a Slave Device Busy exception code, information about the source of the busy condition may be available in the System Busy Status Register (Holding Register 40112). If Bit 0 of the System Busy Status Register (Coil 105) is set to one, the controller is busy waiting for phase synchronization.If the controller is busy waiting for phase synchroniza-tion, the In-Phase Monitor may be bypassed over the Modbus network by performing the following sequence: Warning:EXTREME CAUTION must be used when bypassing the In-Phase Monitor! Transferring between sources that are not in phase synchronization may cause unexpected operation, resulting in damage to plant equipment and personnel.1. Set Bit 0 of the System Busy Control Register (Coil 113) to one. This is a request by the Modbus user to bypass the In-Phase Monitor.2. Once an In-Phase Monitor bypass has been requested, and the controller has been waiting for phase synchro-nization for more than one minute, the controller will request confirmation of the In-Phase Monitor bypass. This request is indicated by a one in Bit 1 of the System Busy Status Register (Coil 106).3. To confirm the request to bypass, set Bit 1 of the System Busy Control Register (Coil 114) to one.The controller will bypass the In-Phase Monitor. Note:The In-Phase Monitor bypass feature is an inter-locked command-and-confirm mechanism. The Modbus Card will not allow the Confirm Bypass control bit (Coil 114) to be set before the controller has set Ready to Confirm Bypass status bit (Coil 106). If a write request is received to set Coil 114 before the controller has set Coil 106, an Illegal Data Value error code will be returned. Bypass Pending ExerciserBit 0 (Coil 121) is the Bypass Pending Exerciser bit. The MX Platform performs a logic-OR with this bit and the BPASS EXER key on the HMI. A 1 in Bit 0 bypasses the pending exerciser; a 0 does nothing.Cancel BypassBit 1 (Coil 122) is the Cancel Bypass bit. The MX Platform performs a logic-OR this bit with the CANCL BPASS key on the HMI. A 1 in Bit 1 cancels the Bypass Pending Exerciser. A 0 in this bit position does nothing. The Bypass Pending Exerciser Bit works different, between a Timer Exerciser and Clock Exerciser, depending on the state of Exerciser Type (Holding Register 40063, Bit 0, Coil 81). When Coil 81 = 0 (Timer Exerciser), if Coil 121 is set to 1, the Timer Exerciser will be bypassed until the Cancel Bypass Bit (Coil 122) is set to 1. When Coil 81 = 1 (Clock Exerciser), if Coil 121 is set to 1, only the exerciser that is pending at the time gets bypassed, and the exerciser only gets bypassed once. The Controller waits for Coil 121 to reset to a 0 before a subsequent bypass can be performed. Operation Under Battery Backup The controller can be powered from an external 12-volt battery in the event that neither S1 nor S2 are available. While the controller is on external battery backup, data will still be available over the Modbus Networkas noted below.While the controller is running on external battery backup, data regarding ATS position and limit switch inputs may be invalid if both S1 and S2 sources are lost. Therefore, if Bits 6 and 7 of Holding Register 40001,or Coils 7 and 8, are both zero, the following Modbus network data may not be reliable:•Automatic Transfer Relay –Holding Register 40001, Bit 0 or Coil 1•SN Limit Switch –Holding Register 40002, Bit 0 or Coil 9•SE Limit Switch –Holding Register 40002, Bit 1 or Coil 10•SNO Limit Switch –Holding Register 40002, Bit 2 or Coil 11•SEO Limit Switch –Holding Register 40002, Bit 3 or Coil 12•S1 Position Status –Holding Register 40004, Bit 9 or Coil 34•S2 Position Status –Holding Register 40004, Bit 10 or Coil 352 4 94104 d n o c e S 4 t n e v E 05104 r u o H 4 t n e v E 15104 e t u n i M 4 t n e v E 25104h t n o M 4 t n e v E 35104 h t n o M f o y a D 4 t n e v E 45104r a e Y 4 t n e v E 551042 5 65104 d n o c e S 5 t n e v E 75104 r u o H 5 t n e v E 85104 e t u n i M 5 t n e v E 95104h t n o M 5 t n e v E 06104 h t n o M f o y a D 5 t n e v E 16104r a e Y 5 t n e v E 261042 6 36104 d n o c e S 6 t n e v E 46104 r u o H 6 t n e v E 56104 e t u n i M 6 t n e v E 66104h t n o M 6 t n e v E 76104 h t n o M f o y a D 6 t n e v E 86104r a e Y 6 t n e v E 961042 7 07104 d n o c e S 7 t n e v E 17104 r u o H 7 t n e v E 27104 e t u n i M 7 t n e v E 37104h t n o M 7 t n e v E 47104 h t n o M f o y a D 7 t n e v E 57104r a e Y 7 t n e v E 671042 e l b a T e e S 8 t n e v E r o f n o s a e R 77104 d n o c e S 8 t n e v E 87104 r u o H 8 t n e v E 97104 e t u n i M 8 t n e v E 08104h t n o M 8 t n e v E 18104 h t n o M f o y a D 8 t n e v E 28104r a e Y 8 t n e v E 381042 9 48104 d n o c e S 9 t n e v E 58104 r u o H 9 t n e v E 68104 e t u n i M 9 t n e v E 78104h t n o M 9 t n e v E 88104 h t n o M f o y a D 9 t n e v E 98104r a e Y 9 t n e v E 091042 01 19104 d n o c e S 01 t n e v E 29104 r u o H 01 t n e v E 39104 e t u n i M 01 t n e v E 49104h t n o M 01 t n e v E 59104 h t n o M f o y a D 01 t n e v E 69104r a e Y01 t n e v E791042 11 89104 d n o c e S 11 t n e v E 99104 r u o H 11 t n e v E 00204 e t u n i M 11 t n e v E 10204h t n o M 11 t n e v E 20204 h t n o M f o y a D 11 t n e v E 30204r a e Y 11 t n e v E 402042 21 50204 d n o c e S 21 t n e v E 60204 r u o H 21 t n e v E 70204 e t u n i M 21 t n e v E 80204h t n o M 21 t n e v E 90204 h t n o M f o y a D 21 t n e v E 01204r a e Y 21 t n e v E 112042 31 21204 d n o c e S 31 t n e v E 31204 r u o H 31 t n e v E 41204 e t u n i M 31 t n e v E 51204h t n o M 31 t n e v E 61204 h t n o M f o y a D 31 t n e v E 71204r a e Y 31 t n e v E 812042 41 91204 d n o c e S 41 t n e v E 01204 r u o H 41 t n e v E 12204 e t u n i M 41 t n e v E 22204h t n o M 41 t n e v E 32204 h t n o M f o y a D 41 t n e v E 42204r a e Y 41 t n e v E 522042 51 62204 d n o c e S 51 t n e v E 72204 r u o H 51 t n e v E 82204 e t u n i M 51 t n e v E 92204h t n o M 51 t n e v E 03204 h t n o M f o y a D 51 t n e v E 13204r a e Y51 t n e v E232042.Registers 40031 and 40032 contain unscaled frequency values. In order to obtain a full-scale frequency value, use the following formula: Scales Frequency + (20,000,000 / Period Count)Notes:1.Registers 40025 - 40030 contain unscaled voltage values In order to obtain a full-scale voltage value, use the following formula:Voltage = (A/D Raw Value / 192) x Full Scale Voltage (Register 40021)RS485 Multi-Drop ConnectionFor a detailed specification of the Modbus protocol, reference the Modicon website address.The Modbus protocol provides the internal standard for parsing messages. During communications on a Modbus network, the protocol determines how each slave will know its device address, recognize a message addressed to it, determine the kind of action to be taken, and extract any data or other information contained in the message. If a reply is required, the slave will construct the reply message and send it using Modbus protocol.The following is a brief description of the Modbus com-mands supported by the Modbus Network Card. Each command consists of the following:• a sample query message that is sent out by the master device to the designated slave•the slave’s reply message to the master device The query and reply messages show how the information is packeted and sent out using the Modbus Protocol. Each query message consists of the following:•Slave Address– address of the slave you wish to establish communications with.•Function Code– code that lets the slave know what command is being requested, e.g. read coil,write single coil.•Starting Address High/Low Order– high and low byte of the address the master reads from orwrites to. Coils and Registers are addressed start-ing at 0. For instance Coil 1 is address 0 andRegister 40001 is address 0.•Error Check Field– contains either a CRC(RTU mode) or LRC(ASCII mode) error check value. The query message for specific functions requires some of the following information:•Number of Data Points High/Low Order– high and low byte of the number of addresses themaster wants to read.•Data High/Low Order– high and low byte of the data that will be written to the slave device.•Number of Coils High/Low Order– high and low byte for the number of coils to force ONor OFF.•Number of Regs High/Low Order– high and low byte for the number of registers to preset.•Byte Count– is the number of data bytes which are sent to the slave.Modbus Protocol IllustrationThese query and reply messages are for both RTU andASCII modes depending on whether the Error CheckField contains a CRC or LRC respectively. Each valuein the query message is a hexadecimal value.Figure G3 – Read Holding Register Query MessageWrite Multiple Coils (Function Code 15)Forces each coil in a sequence of coils to either ON or OFF . The requested ON /OFF states are specified by con-tents of the query data field. A logical ‘1’ in a bit position of the field requests the corresponding coil to be ON and a logical ‘0’ requests it to be OFF . Coils are addressed starting at 0. For examples coil 1 is addressed as 0.QueryThe following example is a request to force a series of six-teen coils starting at coil 41 (addressed as 40, or 28 hex)in slave device 9.The query data contents consist of two bytes: 3C 9B hex (0011 1100 1001 1011 binary). The binary bits corre-spond to the coils in the following way:The first byte sent (3C hex) addresses coils 41-48, with the least significant bit addressing coil 41. The second byte sent (9B hex) addresses coils 49-56, with the least significant bit addressing coil 49.Modbus Protocol Illustration (cont’d)Figure G5 – Write Single Coil Query MessageResponseThe slave’s normal response to the Write Single Coil query is to return the original message after the coil state has been altered.Figure G6 – Write Single Coil Response MessageFigure G7 – Write Single Holding Register Query MessageResponseThe slave’s response to the Write Single HoldingRegister query is to return the original message after the registers have been altered.Figure G8 – Write Single Holding Register Response MessageCoil:48474645444342415655545352515049Bit:0111111111Write Single Holding Register (Function Code 06)This function allows the master to modify the contents of one holding register.QueryFigure G7is an example of a request to preset register 40041 (Normal Pickup Voltage) to 92 (00 5C hex) in slave device 17.Figure G9 – Write Multiple Coils Query MessageModbus Protocol Illustration (cont’d)Figure G10 – Write Multiple Coils Response MessageFigure G11 – Write Multiple Registers Query MessageFigure G12 – Write Multiple Registers Response MessageConfiguring Controller for Modbus MX150/250ABB Zenith Controls, Inc.305 Gregson Drive Cary, NC 2751124-hour support:ABB Technical Services +1 (800) 637-1738**********************C C 303025M 0201 08/19。
MX1508RX2产品手册V1.0

功能框图
13 VDD
LDOLeabharlann 带隙基准电路振荡器
时序控制
2 SI 放大器
解码电路
逻 辑 电 路
14 VI1
15 VO1
过热保护电路
16 VI2 1 VO2
AGND 4
PGND VM1
12
栅
驱
动
FORWARD 11
电
路
PGND
VM1
栅
驱
动
BACKWARD 10
电
路
PGND 9
TURBO 3
VM2 5
栅
驱
动
4、驱动电路功耗 马达驱动电路内部功率 MOSFET 的导通内阻是影响驱动电路功耗的主要因素。驱动电路功耗的计算公式
为:PD=IL2 xRON 其中 IL 表示马达驱动电路的输出电流,RON 表示功率 MOSFET 的导通内阻。 注意:功率 MOSFET 的导通内阻随着温度的升高而升高,在计算电路的最大持续输出电流以及功耗时必
1
R8=2.2K
2
2300
3
4
VO2 SI TURBO AGND
5 VM2
6 RIGHT
7 LEFT
8 PGND
VI2 16 VO1 15 VI1 14 VDD 13 VM1 12 FORWARD 11 BACKWARD 10 PGND 9
C13=0.1uF-100uF
前进/后退马达
M
MX1508RX2
34(W1)
前进和向右
后退
40(W1)
后退
后退和向右
46(W1)
后退和向右
后退和向左
52(W1)
后退和向左
稳定性测试及诊断二合一卡说明书
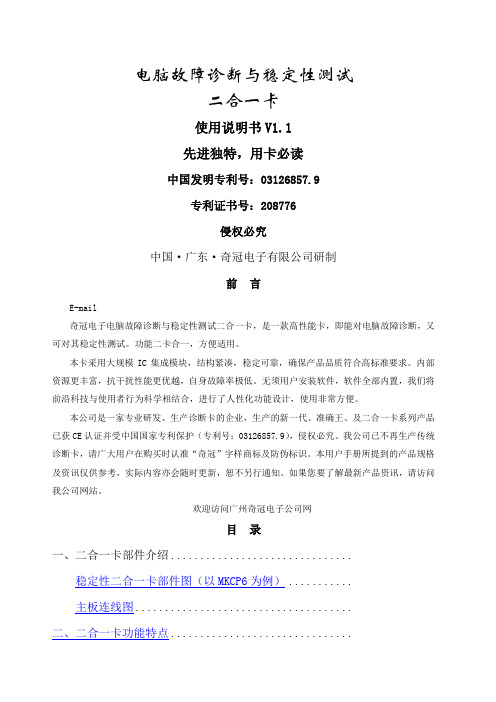
电脑故障诊断与稳定性测试二合一卡使用说明书V1.1先进独特,用卡必读中国发明专利号:03126857.9专利证书号:208776侵权必究中国·广东·奇冠电子有限公司研制前言E-mail奇冠电子电脑故障诊断与稳定性测试二合一卡,是一款高性能卡,即能对电脑故障诊断,又可对其稳定性测试。
功能二卡合一,方便适用。
本卡采用大规模IC集成模块,结构紧凑,稳定可靠,确保产品品质符合高标准要求。
内部资源更丰富,抗干扰性能更优越,自身故障率极低。
无须用户安装软件,软件全部内置,我们将前沿科技与使用者行为科学相结合,进行了人性化功能设计,使用非常方便。
本公司是一家专业研发、生产诊断卡的企业,生产的新一代、准确王、及二合一卡系列产品已获CE认证并受中国国家专利保护(专利号:03126857.9),侵权必究。
我公司已不再生产传统诊断卡,请广大用户在购买时认准“奇冠”字样商标及防伪标识。
本用户手册所提到的产品规格及资讯仅供参考,实际内容亦会随时更新,恕不另行通知。
如果您要了解最新产品资讯,请访问我公司网站。
欢迎访问广州奇冠电子公司网目录一、二合一卡部件介绍...............................稳定性二合一卡部件图(以MKCP6为例)...........主板连线图.....................................二、二合一卡功能特点...............................(一)稳定性测试功能特点.......................(二)二合一卡指示灯特性.......................(三)故障诊断功能.............................三、二合一卡稳定性测试流程.........................四、二合一卡结果显示含义介绍.......................1.代码性质与稳定性测试结果结合分析及处理方法说明表2.稳定性测试状态..............................3.指示灯状态..................................五、基本操作流程...................................附图1、检测流程总图 ...........................附图2:“不稳定”原因判断流程图.................附图3:引起“不稳定”故障部位判断及排除流程图.附图4:采用相应手段诱发出引起“不稳定”的原因流程图附图5:复位故障判断流程图......................附图6:利用二合一卡判断是否为市电引起流程图....附图7:利用二合一卡判断是否为内存条混插引起流程图附图8:利用二合一卡判断是否为电源负载能力不够引起流程图附图9:利用二合一卡判断是否为散热不良引起流程图附图10:利用二合一卡判断是否为灰尘引起流程图...附图11:利用二合一卡判断是否为强磁干扰引起流程图附图12:利用二合一卡判断是否为接触不良引起流程图六、常见问题与解决方法:...........................1. 如何利用二合一卡选配电脑工作稳定的UPS ? .....2. 如何利用二合一卡检验开发的外围设备对电脑的干扰?3. 如何利用二合一卡挑选用于重要场合的电脑? ....4. 测试时不拔除硬盘会对电脑有何不利? ..........5. 为何刚才用着很好的电脑打开机箱后就坏了? ....6. 如何选购稳定性测试卡? ...................... 7.为什么Clock 指示灯要改进,改进后有何好处? ..一、二合一卡部件介绍稳定性二合一卡部件图(以MKCP6为例)实物与图片存在差异,以实物为准,我司会不断对产品改进,恕不另行通知。
摩尔克斯 MX150 封闭和非封闭接线器系统说明说明书
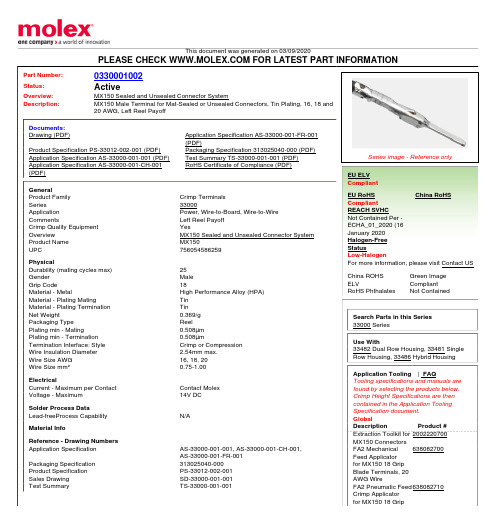
Blade Terminals, 20
AWG Wire
FA2 Pneumatic Feed 638082710
Crimp Applicator
for MX150 18 Grip
Blade Terminals, 20 AWG FA2 Mechanical 638082900 Feed Applicator for MX150 18 Grip Male Terminals, 18 AWG, 0.75mm² and 1.00mm² Wire FA2 Mechanical 638084100 Feed Applicator for MX150 Mat Seal/ Unsealed Blade Terminals, 16 AWG TXL Wire and 18 AWG GXL Wire FA2 Pneumatic Feed 638084110 Applicator for MX150 Mat Seal/Unsealed Blade Terminals, 16 AWG TXL Wire and 18 AWG GXL Wire Hand Crimp Tool, 638112400 14-16 AWG Hand Crimp Tool, 638112600 18-22 AWG Manual Extraction 638131500 Tool FineAdjust Applicator639040800 for SRC Connector using MX150 Receptacle Terminals, 0.75mm² wires
Documents: Drawing (PDF)
Product Specification PS-33012-002-001 (PDF) Application Specification AS-33000-001-001 (PDF) Application Specification AS-33000-001-CH-001 (PDF)
- 1、下载文档前请自行甄别文档内容的完整性,平台不提供额外的编辑、内容补充、找答案等附加服务。
- 2、"仅部分预览"的文档,不可在线预览部分如存在完整性等问题,可反馈申请退款(可完整预览的文档不适用该条件!)。
- 3、如文档侵犯您的权益,请联系客服反馈,我们会尽快为您处理(人工客服工作时间:9:00-18:30)。
C1 L2 R4
R3
C7
C8=0.1uF R5=2.2K
C9 470P
R7 2.2M
C11=0.1uF
图 1 MX1508RX2 典型应用线路图 MX1508RX2 的应用线路图如图 1 所示,其中 LEFT 和 RIGHT 用于驱动转向轮,BACKWARD 和 FORWARD 用 于驱动后轮马达。 特别注意事项: 图 1 中的功率电源 VMx(x=1,2)对地去耦电容(C13)容值应根据具体的应用调整,VMx(x=1,2)电压越高,输 出峰值电流越大,C13 取值越大,但是电容 C13 的取值至少需要 0.1uF。在高压、大电流的应用条件下建议 电容 C13 取值 100uF。 图 1 中左转/右转马达和前进/后退马达之间都需要添加一个 104 电容。 PCB 设计时,必须确保电路板的高频部分尤其是天线部分远离电机,否则电路易受到电机噪声的影响, 造成误码。此外,电机两端必须跨接 104 电容,否则电路极易受到电机噪声干扰,出现接收距离下降、误 码等现象。
34(W1)
前进和向右
后退
40(W1)
后退
后退和向右
46(W1)
后退和向右
后退和向左
52(W1)
后退和向左
向左
58(W1)
向左
向右
64(W1)
向右
3
MX1508RX2
绝对最大额定值(TA=25℃)
参数
符号
值
单位
最大功率电源电压 最大外加输出端电压
VM(MAX)
8
V
VOUT(MAX)
VM
最大峰值输出电流 1 通道 2 通道
(2)、不同环境温度下的最大功耗计算公式为: PD=(150℃-TA)/θJA TA 表示电路工作的环境温度,θJA 为封装的热阻。150℃表示电路的最高工作结温。
(3)、电路功耗的计算方法: P =I2xR
其中 P 为电路功耗,I 为持续输出电流,R 为电路的导通内阻。电路功耗 P 必须小于最大功耗 PD
五功能马达驱动电路
MX1508RX2
五功能马达驱动电路 MX1508RX2
概述
MX1508RX2 是为遥控汽车等玩具设计的专用单芯片解决方案,该芯片将传统方案的 RX2 接收解码芯片 以及马达驱动芯片整合为单一芯片。芯片内部集成两路 H 桥驱动电路,可同时驱动转向电机以及前进后退 电机。
单通道工作时,左转/右转通道用于驱动转向电机,最大持续输出电流达到 1.2A,最大峰值输出电流达 到 1.5A。前进/后退通道用于驱动前进后退电机,最大持续输出电流达到 1.4A,最大峰值输出电流达到 2A; 双通道同时工作时,左转/右转通道持续输出 0.8A 的情况下,前进/后退通道能持续输出 1.2A。
LDO 参数测试
负载=240Ω VM=6.5V TA=25℃
2.593
LDO 输出电压
负载=2KΩ VM=6.5V TA=25℃ VVDD VM=3V TA=25℃ 空载
2.594 V
2.584
VM=6.5V TA=25℃ 空载
2.595
解码频率
内置振荡频率
FOSC
128
kHz
允许发射频率的偏差
77
功能框图
13 VDD
LDO
带隙基准电路
振荡器
时序控制
2 SI 放大器
解码电路
逻 辑 电 路
14 VI1
15 VO1
过热保护电路
16 VI2 1 VO2
AGND 4
PGND VM1
12
栅
驱
动
FORWARD 11
电
路
PGND
VM1
栅
驱
动
BACKWARD 10
电
路
PGND 9
TURBO 3
VM2 5
栅
驱
动
465
uA
1 通道导通内阻 2 通道导通内阻
IO=±100mA VM1=6.5V TA=25℃ RON1 IO=±1000mA VM1=6.5V TA=25℃
IO=±100mA VM2=6.5V TA=25℃ RON2 IO=±1000mA VM16 0.470
反转模式的定义为:按键后退或者左转时,此时马达驱动端 BACKWARD 或 LEFT 输出高电平,马达驱动 端 FORWARD 或 RIGHT 输出低电平时,马达驱动电流从 BACKWARD 或 LEFT 流入马达,从 FORWARD 或 RIGHT 流到地端,此时马达的转动定义为反转模式。
VM
VM
3、驱动电路最大持续功耗 该系列马达驱动电路内部均设计有过热保护电路,因此当驱动电路消耗的功耗过大时,电路将进入热关
断模式,热关断状态下马达将无法正常工作。驱动电路最大持续功耗的计算公式为:
PD=(150℃-TA)/θJA 其中 150℃为热关断电路预设温度点,TA 为电路工作的环境温度(℃),θJA 为电路的结到环境的热阻(单 位℃/W)。注意:驱动电路的最大持续功耗与环境温度、封装形式以及散热设计等因素有关,与电路导通内 阻并无直接关系。
6
MX1508RX2
应用说明
1、基本工作模式 a)待机模式
在不按键的情况下,电路处于待机模式。包括驱动功率管在内的所有内部电路都处于关断状态。电路消 耗极低的电流。此时马达输出端 FORWARD、BACKWARD、RIGHT 和 LEFT 都为高阻状态。 b)正转模式
正转模式的定义为:按键前进或者右转时,此时马达驱动端 FORWARD 或 RIGHT 输出高电平,马达驱动 端 BACKWARD 或 LEFT 输出低电平时,马达驱动电流从 FORWARD 或 RIGHT 流入马达,从 BACKWARD 或 LEFT 流到地端,此时马达的转动定义为正转模式。 c)反转模式
4、驱动电路功耗 马达驱动电路内部功率 MOSFET 的导通内阻是影响驱动电路功耗的主要因素。驱动电路功耗的计算公式
为:PD=IL2 xRON 其中 IL 表示马达驱动电路的输出电流,RON 表示功率 MOSFET 的导通内阻。 注意:功率 MOSFET 的导通内阻随着温度的升高而升高,在计算电路的最大持续输出电流以及功耗时必
引脚定义
引脚编号
1 2 3 4 5 6 7 8 9 10 11 12 13 14 15 16
引脚名称
VO2 SI
TURBO AGND VM2 RIGHT LEFT PGND PGND BACKWARD FORWARD VM1 VDD
VI1 VO1 VI2
输入/输出 O I O O O O O O I O I
VM
OFF
OFF ON
OFF OFF
ON
M
M
M
OFF
OFF OFF
ON
ON
OFF
a)待机模式
b)正转模式
c)反转模式
2、过热保护电路 当驱动电路结温超过预设温度时,TSD 电路开始工作,此时控制电路强制关断所有输出功率管,驱动电
路输出进入高阻状态。TSD 电路中设计了热迟滞,只有当电路的结温下降到预设温度时,电路返回正常工作 状态。
推荐工作条件(TA=25℃)
参数
符号
最小值
典型值(VM=6.5V)
最大值 单位
功率电源电压
VM
2
--
8
V
TA=25℃
1 通道
IOUT1
1.4
独立工作持续输出电流
2 通道
IOUT2
TA=25℃
1 通道
IOUT1
1.2 A
1.2
同时工作持续输出电流
2 通道
IOUT2
0.8
注: (1)、VM 代表 VM1 和 VM2,1 通道代表 FORWARD 和 BACKWARD 通道,2 通道代表 FIGHT 和 LEFT 通
引脚功能描述
用于信号放大的反相器 2 输出端 编码信号输入端
加速功能输出端
控制部分电源地
左转右转马达 2 的输入电源 马达 2 右转输出端 马达 2 左转输出端 功率地
功率地
马达 1 后退输出端 马达 1 前进输出端 前进后退马达 1 的输入电源 LDO 输出端 用于信号放大的反相器 1 输入端 用于信号放大的反相器 1 输出端 用于信号放大的反相器 2 输入端
1
R8=2.2K
2
2300
3
4
VO2 SI TURBO AGND
5 VM2
6 RIGHT
7 LEFT
8 PGND
VI2 16 VO1 15 VI1 14 VDD 13 VM1 12 FORWARD 11 BACKWARD 10 PGND 9
C13=0.1uF-100uF
前进/后退马达
M
MX1508RX2
IOUT(PEAK)
2 1.5
A
最大功耗 结到环境热阻 工作温度范围 结温 储存温度
PD
1.1
W
θJAD
80
℃/W
Topr
-20~+85
℃
TJ
150
℃
Tstg
-55~+150
℃
焊接温度
TLED
260℃,10 秒
注:(1)、VM 代表 VM1 和 VM2,1 通道代表 FORWARD 和 BACKWARD 通道,2 通道代表 FIGHT 和 LEFT 通道。
179 kHz
注:(1)、VM 代表 VM1 和 VM2,1 通道代表 FORWARD 和 BACKWARD 通道,2 通道代表 FIGHT 和 LEFT 通道。
5
典型应用线路图
C2
L1
C6
R2
Q1 C2712 R1