FMEA失效模式与效应分析
FMEA失效模式和效应分析

1 of 19項 目:過程責任:生產準備者:部 門:制一部零件號:關鍵日期:FMEA 日期:中心隊員:FMEA 編號: 0606242 of 19項 目:過程責任:生產準備者:部 門:制一部零件號:關鍵日期:FMEA 日期:中心隊員:FMEA 編號: 0606243 of 19項 目:過程責任:生產準備者:部 門:制一部零件號:關鍵日期:FMEA 日期:中心隊員:FMEA 編號: 0606244 of 19項 目:過程責任:生產準備者:部 門:制一部零件號:關鍵日期:FMEA 日期:中心隊員:FMEA 編號: 0606245 of 19項 目:過程責任:生產準備者:部 門:制一部零件號:關鍵日期:FMEA 日期:中心隊員:FMEA 編號: 0606246 of 19項 目:過程責任:生產準備者:部 門:制一部零件號:關鍵日期:FMEA 日期:中心隊員:FMEA 編號: 0606247 of 19項 目:過程責任:生產準備者:部 門:制一部零件號:關鍵日期:FMEA 日期:中心隊員:FMEA 編號: 0606248 of 19項 目:過程責任:生產準備者:部 門:制一部零件號:關鍵日期:FMEA 日期:中心隊員:FMEA 編號: 0606249 of 19項 目:過程責任:生產準備者:部 門:制一部零件號:關鍵日期:FMEA 日期:中心隊員:FMEA 編號: 06062410 of 19項 目:過程責任:生產準備者:部 門:制一部零件號:關鍵日期:FMEA 日期:中心隊員:FMEA 編號: 06062411 of 19項 目:過程責任:生產準備者:部 門:制一部零件號:關鍵日期:FMEA 日期:中心隊員:FMEA 編號: 06062412 of 19項 目:過程責任:生產準備者:部 門:制一部零件號:關鍵日期:FMEA 日期:中心隊員:FMEA 編號: 06062413 of 19項 目:過程責任:生產準備者:部 門:制一部零件號:關鍵日期:FMEA 日期:中心隊員:FMEA 編號: 06062414 of 19項 目:過程責任:生產準備者:部 門:制一部零件號:關鍵日期:FMEA 日期:中心隊員:FMEA 編號: 06062415 of 19項 目:過程責任:生產準備者:部 門:制一部零件號:關鍵日期:FMEA 日期:中心隊員:FMEA 編號: 06062416 of 19項 目:過程責任:生產準備者:部 門:制一部零件號:關鍵日期:FMEA 日期:中心隊員:FMEA 編號: 06062417 of 19項 目:過程責任:生產準備者:部 門:制一部零件號:關鍵日期:FMEA 日期:中心隊員:FMEA 編號: 06062418 of 19項 目:過程責任:生產準備者:部 門:制一部零件號:關鍵日期:FMEA 日期:中心隊員:FMEA 編號: 06062419 of 19項 目:過程責任:生產準備者:部 門:制一部零件號:關鍵日期:FMEA 日期:中心隊員:FMEA 編號: 060624。
FMEA前期失效模式与效应分析

4
Failure Mode & Effects Analysis
简介( 1. FMEA 简介(续)
消除 减少 减少 保存
全风险
剩余风险
损失管制程序图 1) 消除,管制及减低风险的工作不只是工程部门的责任,更是 每一个部门甚至是每一个人的工作职责. 2) 风险允许存在, 但必须降低及控制在一定范围之内. 3) FMEA就是通过风险评估与计算来确认FMEA的执行效果.
功能 项目
潜在的 失效模式
潜在的 失效原因
发 生 率
2 3
现行 管制方式
1.退料给成型重新确认 1.后制程CCD 100%测试
检 出 率
2 1
实际改善措施
端子/塑胶投入 标示不清或错误 signal pin端子 插入,折carrier 及打 kink 塑胶刮伤 缺pin
无法辨识产品 状态 客户无法使用
3 4
36 84
17
Failure Mode & Effects Analysis
7. FMEA 制作
7-2: 表格各栏位填写说明 7-2-1: FMEA编号 编号 FMEA之文件编号,以供查询,展开及追踪. 7-2-2: 系统 子系统或零部件的名称及编号 系统,子系统或零部件的名称及编号 7-2-3: Core Team(核心小组 核心小组) 核心小组 Core team 一般应由 ME/QE/RD/AUTO/FAE/PM等跨功 能团队组成,必要时可包括客户或/和分供方 7-2-4: 设计 制造单位 设计/制造单位 QS9000 FMEA手册中要求填入相应负责人的姓名&电话,此处 改为设计/制造单位名称.
5
Failure Mode & Effects Analysis
风险评估技术-失效模式和效应分析(FMEA)及失效模式、效应和危害度分析(FMECA)

失效模式和效应分析(FMEA及失效模式、效应和危害度分析(FMECA)1 概述失效模式和效应分析(Failure Mode and Effect Analysis ,简称FMEA)是用来识别组件或系统未能达到其设计意图的方法。
FMEA 用于识别:•系统各部分所有潜在的失效模式(失效模式是被观察到的是失误或操作不当);•这些故障对系统的影响;• 故障原因;• 如何避免故障及 /或减弱故障对系统的影响。
失效模式、效应和危害度分析(Failure Mode and Effect and Criticality Analysis ,简称 FMECA)拓展了 FMEA 的使用范围。
根据其重要性和危害程度,FMECA 可对每种被识别的失效模式进行排序。
这种分析通常是定性或半定量的,但是使用实际故障率也可以定量化。
2 用途FMEA 有几种应用:用于部件和产品的设计(或产品) FM EA ;用于系统的系统FMEA ;用于制造和组装过程的过程 FMEA ;服务FMEA和软件FMEA。
FMEA/ FMECA 可以在系统的设计、制造或运行过程中使用。
然而,为了提高可靠性,改进在设计阶段更容易实施。
FMEA/ FMECA 也适用于过程和程序。
例如,它被用来识别潜在医疗保健系统中的错误和维修程序中的失败。
FMEA/FMECA 可用来:•协助挑选具有高可靠性的替代性设计方案;•确保所有的失效模式及其对运行成功的影响得到分析;•列出潜在的故障并识别其影响的严重性;•为测试及维修工作的规划提供依据;• 为定量的可靠性及可用性分析提供依据。
它大多用于实体系统中的组件故障,但是也可以用来识别人为失效模式及影响。
FMEA 及 FMECA 可以为其他分析技术,例如定性及定量的故障树分析提供输入数据。
3 输入数据FMEA 及 FMECA 需要有关系统组件足够详细的信息,以便对各组件出现故障的方式进行有意义的分析。
信息可能包括:• 正在分析的系统及系统组件的图形,或者过程步骤的流程图;• 了解过程中每一步或系统组成部分的功能;• 可能影响运行的过程及环境参数的详细信息;• 对特定故障结果的了解;• 有关故障的历史信息,包括现有的故障率数据。
FMEA失效模式及后果分析手册精选全文

可编辑修改精选全文完整版FM E A 失效模式及后果分析手册FMEA (Failue Mode &Effect Analgsis ) Failue :失效、失败、不良 Mode :模式Effect :后果、效应、影响 Analgsis :分析一、FMEA 思维逻辑方法:D ’FMEA —→分析着重点BOM 表的零件及组装件P ’FMEA —→分析着重点OPC/AC 的零件加工及组装的工艺流程PRN 高风险优先系数 重点管理原则控制重点少数,不重要大多数列为次要管理 轻重缓急,事半功倍类比量产品(模块化) 工艺流程 过程参数/工艺条件 质量特性类比量产品 质量不良履历失败经验产品病历卡预设未来新产品投产后可能/潜在的会出现类似的不良事前 分析原因 整改措施(鱼刺图)先期产品质量策划结果控制计划(欧美) QC 工程表(台/日)新产品投产施工的要求监视和测量(首中末件检查)开发新产品例:有20项不良,前3项不良占70%,对策能解决50%的不良,70%*50%=35%后17项不良占30%,对策能解决100%的不良,30%*100%=30%①质量管理AC 柏拉图分析②物料管理MC 物料ABC法避免待料停工目的降低库存量的成本二、在何种情况下应进行FMEA分析:新产品开发阶段1、RP N≥1002、严重度/发生度/难检度(任一项)≥7;3、严重度≥7,发生度≥3;4、发生度≥5,难检度≥4量产阶段秉持持续改善的精神三、FMEA建立与更新时机1、新产品开发时;2、设计变更时(材质变更,BOM变更);3、工程变更;4、检验方法变更(检验设备/项目/频度)5、定期审查更新(建议每季度修订,至少也要每半年)四、FMEA分析表作成说明35%>30%重效果大,轻效果小活性化文件随时更新有效版本的识别(以修订日期)1、增加零件编号与名称:与BOM 表一致(D ’FMEA 分析,着眼在构成零件及组装件);2、增加工序编号与名称:与OPC/AC 表一致(P ’FMEA 分析,着眼在加工与组装工艺流程,D ’FMEA 可省略)3、功能与要求:已含外观、颜色、尺寸及ES TEST 功能质量要求;4、潜在失效模式:类比量产品质量不良履历(历史档)→产量履历→失效分析累积5、潜在失效效应(后果):万一不良时会造成的后果,如影响安全性/功能性/一般性,必须站在广义的客户中思考,包含: ● 下工程● 直接客户:下购销合同者/客户:如代理商 ● 最终客户:user/消费者6、严重度:参照对照表予以评估,复合型≥7;功能性4~6;一般性<4;7、分类(等级)class :与CC/SC 管制特性计划清单一致,包含符号识别,如FORD ▽,通用,依客户指定或本司对等的符合标注。
FMEA失效分析与失效模式分析全

擦伤或损坏)。 由于横向性能差而在锻件中出现分离线的失效现象。
11
在服役条件下由于质量恶化而产生失效的原因包括
过载或未预见的加载条件。 磨损(磨蚀、因过度磨损而咬住、粘住、擦伤、气蚀)。 腐蚀(包括化学接触、应力腐蚀、腐蚀疲劳、脱锌、铸铁石
找出被分析对象的“单点故障”。所谓单点故障是指这种故障单独发 生时,就会导致不可接受的或严重的影响后果。一般说来,如果单点 故障出现概率不是极低的话,则应在设计、工艺、管理等方面采取切 实有效的措施。产品发生单点故障的方式就是产品的单点故障模式。
为制定关键项目清单或关键项目可靠性控制计划提供依据。 为可靠性建模、设计、评定提供信息。 揭示安全性薄弱环节,为安全性设计(特别是载人飞船的应急措施、
16
什么是失效分析?
失效分析:考察失效的构件及失效的情景(模式), 以确定失效的原因。
失效分析的目的:在于明确失效的机理与原因。改 进设计、改进工艺过程、正确地使用维护。
失效分析的主要内容:包括明确分析对象,确定失 效模式,研究失效机理,判定失效原因,提出预防 措施(包括设计改进)。
17
失效分析的要点?
失效模式的判断分为定性和定量分析两个方面。在一般 情况下,对一级失效模式的判断采用定性分析即可。而 对二级甚至三级失效模式的判断,就要采用定性和定量、 宏观和微观相结合的方法。
19
一级失效模式的分类
20 主要失效模式的分类与分级
21
如某型涡轮叶片在第一榫齿处发生断裂,通过断口 的宏观特征可确定一级失效模式为疲劳失效。然后 通过对断口源区和扩展区特征分析和对比,并结合 有限元应力分析等,可作出该叶片的断裂模式为起 始应力较大的高周疲劳断裂的判断,即相当于作出 了三级失效模式的判断。
失效模式与效应分析 (FMEA)

失效模式與效應分析 (FMEA)何謂「FMEA、FMECA」?FMECA 是兩種分析技術的總稱:1.FMEA﹝故障型式及其影響分析﹞2.CA﹝Criticality Analysis, 嚴重度分析﹞與失誤樹分析一樣,故障型式影響及嚴重度分析﹝failure modes, effects and criticality analysis, 簡稱 FMECA﹞,首先在美國國防科技中研究發展,且在國防部各機構中普遍應用﹝DOD, 1980﹞,後來漸應用於工業界。
在核能、化工、石化、海上鑽油等高風險工業中,自不例外。
工業界的設計工程師與可靠度﹝Reliability﹞工程師常運用 FMECA 以預測複雜的產品的可靠度,預估一件產品的零件在某特定的時間及情況下,如何失去其功能,故障的次數是多少,故障之後對其他零件或對整個系統會產生怎樣的影響等。
FMECA 的功用不止於可靠度一端,其分析所得的資料,尚可作下列用途:1.協助評估所設計的裝置,如複聯系統﹝Redundancy﹞、故障偵測,以及fail-safe 特性等。
2.對測試、採購﹝Procurement﹞、檢查、改善措施等提供先後順序的參考資料。
3.提供失誤隔絕﹝Fault isolation﹞及維護性﹝Maintainability﹞分析的參考資料。
4.提供系統安全分析﹝如失誤樹分析﹞所需的硬體資料。
FMECA 可在系統週期的任一階段中,依計劃內容之需要,以不同深淺程度實施,但在設計階段的初期,一旦所需的設備確定之後,即應實施。
FMECA 的對象是系統或子系統中的零組件,尤其對於複雜的系統中的設備零件,最能發揮其故障針砭的功效,此為其他系統安全分析技術不能望其項背之處。
但因其分析對象大多限於硬體,故對於人為因素和作業環境因素較少納入分析考慮範圍。
因此,如能將 FMECA 與失誤樹分析合併使用,必更能瞭解整個作業系統的危害,進而防範事故生。
摘於【環安 Q&A】。
失效模式与效应分析(FMEA)
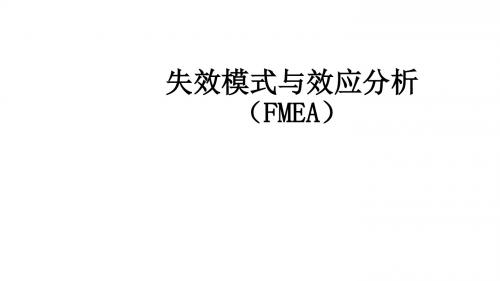
失效模式与效应分析 (FMEA)
起源
FMEA大约于1950年代由美国Grumman公 司提出,当时由于飞机系统复杂并且需要 预防失效情况发生,因此渐渐发展成安全 性与可靠度的设计模式,以期能够增加产 品质量,降低不良问题的发生。
FMEA具体项目
• 累积经验,早期发现失效原因及采取因应之道。 • 促进设计改良。 • 改善操作方法及建立维护计划的参考。 • 帮助操作人员之训练,让员工能在短期内找出 失效原因与解决之法。 • 公司人员异动时,能让员工快速上手。
FMEA表格建立
失效机率
字码体系
严重性分析
多要因评估法
单要因评估法
列表评估法
失效报告
范例
范例
范例
范例
范例
故障树分析符号
故障树分析范例
故障树简化
故障树关键性估计范例
结论
• 透过FMEA模式,可有效找出来自品失效原因,进而解决问题,是一 个可靠性的解析手法。 • 藉由实施FTA ,能让不希望发生的事情明确化,并能判别事件发 生时所带来的一些事象与对成品的影响。
潜在失效模式与效应分析

潜在失效模式与效应分析潜在失效模式与效应分析(Failure Mode and Effects Analysis,FMEA)是一种常用于产品设计与制造过程中的质量管理工具,用于识别和分析可能的失效模式和其对产品或系统性能的潜在影响,从而采取相应的改进措施以提高产品的可靠性和安全性。
FMEA包括三个关键步骤:识别潜在失效模式、分析失效效应和确定风险优先级。
首先,团队通过对产品或系统进行系统性分析,并结合以往经验,识别出所有可能的失效模式。
这些失效模式可能发生在产品的各个环节,如设计、制造、装配、运输和使用等。
然后,团队对每个失效模式进行评估,分析失效效应。
失效效应可能包括对产品功能、性能、可靠性和安全性的影响。
最后,根据失效模式和效应的严重性和概率,确定风险优先级,以便制定相应的改进措施。
FMEA的核心目标是预防失效,并通过优先处理潜在的高风险失效来提高产品质量和可靠性。
通过分析失效模式和其效应,可以识别导致失效的根本原因,并采取相应的纠正和预防措施。
FMEA可以帮助团队更好地理解产品的设计和制造过程中的潜在问题,并预测可能的质量和安全风险,从而减少后续的成本和不良后果。
FMEA也有助于团队提高对产品的理解和共识。
在FMEA过程中,团队成员就产品的设计和制造问题展开讨论,共同评估潜在的失效模式和其效应,并制定改进措施。
通过这些讨论,团队可以发现和纠正潜在的问题,并提高各部门之间的沟通和合作。
FMEA的应用领域广泛,适用于各类产品和系统的设计和制造过程。
例如,汽车制造业常用FMEA来识别和纠正潜在的设计和制造缺陷,提高汽车的质量和安全性。
医疗设备制造商也使用FMEA来评估产品的安全性和性能,减少医疗事故的风险。
此外,航空航天、电子、化工等行业也都广泛应用FMEA来提高产品的可靠性和安全性。
总之,潜在失效模式与效应分析(FMEA)是一种非常有用的质量管理工具,通过识别和分析潜在的失效模式和其效应,帮助团队预防失效、提高产品的可靠性和安全性。
FMEA失效模式及效应分析介绍

FMEA失效模式及效应分析介绍FMEA(Failure Mode and Effects Analysis)是一种用于识别、评估和减轻系统、产品或过程中可能的失效模式及其可能的效应的工具和方法。
它的目标是通过提前识别和纠正潜在的问题,从而提高系统的可靠性和安全性。
FMEA通常由一个跨职能的团队进行,包括设计工程师、工艺工程师、质量控制人员等。
这个团队将系统、产品或过程分解成多个组成部分,然后针对每个部分,逐个分析其可能的失效模式以及这些失效模式可能引起的效应。
在进行FMEA之前,团队首先需要定义一个适当的评估标准,用于对失效模式和效应进行风险评估。
评估标准通常包括失效的概率、严重性和可能性等方面。
然后,通过对每个失效模式和效应进行评估,确定其风险等级。
常用的评估方法包括风险矩阵、风险优先级数等。
FMEA的关键步骤包括:1.确定分析的范围:确定要进行FMEA的系统、产品或过程的范围,并明确所有相关的组成部分。
2.分析失效模式:对每个组成部分,团队成员进行头脑风暴,识别可能的失效模式。
失效模式是指一个组成部分不能正常工作或无法满足指定要求的一种方式。
3.分析失效效应:对于每个失效模式,分析团队评估其可能引起的效应,包括对系统性能、安全性和可靠性的影响。
这些效应需要根据评估标准进行量化或定性评估。
4.评估风险等级:通过将失效模式和效应的概率、严重性和可能性等因素综合考虑,评估每个失效模式和效应的风险等级。
这有助于团队确定哪些失效模式和效应应优先处理。
5.提出改进措施:根据风险等级,团队制定相应的改进计划。
这可以包括重新设计、改变制造流程、增加可靠性测试等措施,以降低失效模式和效应的风险。
FMEA的优点在于:1.提前识别风险:通过系统的、结构化的方法,FMEA能够识别并提前预测系统或产品中的潜在问题,从而及早采取措施来减轻或消除这些风险。
2.优化设计:通过对失效模式和效应的分析,FMEA可以帮助设计团队发现并改进设计中的潜在问题,从而提高系统的可靠性和性能。
失效模式与效应分析(FMEA)

無法傳遞扭力
配合作業或零件,填寫如下: 組配鬆動 / 扣件斷裂
填表說明 —潛在失效的影響
項目 功能 潛在失效模式 潛在失效的 影響 嚴 重 等 度 級 S 潛在失效的 原因 發 生 率 O 現行設計控制 預防 偵測 偵 測 度 D R P N 措施執行結果 建議 措施 責任/ 目標 完成日 採取 措施 嚴 發 偵 R 重 生 測 P 度 率 度 N
定義:在下一個組件、系統、次系統 或客戶發生失效之潛在影響程度的嚴 重度。 使用:評估嚴重度時以1~10分表示。 唯一降低嚴重度的方法是設計變更。
嚴重度評分之例
發生之失效極為嚴重,危及安全,並違反政府法令。 9~10 發生失效會影響產品主要功能之表現,並有可能形成不合法 規問題,但不致有安全問題。 7~8 發生失效後,會引起使用者相當的不滿,例如駕駛不靈便、 收音機故障等不影響主要功能之系統失效等。 6 發生失效後,可能引起使用者少許不滿,使用者通常是略感 不便,例如車輛收音機偶有雜音,離合器踏板不便等,使用 者偶而發現此種異常現象。 4~5 發生失效後,至少只對使用者造成輕微的不便,使用者只會 偶而發現此種異常狀況。 2~3 發生失效後通常不致對產品發生顯著影響,使用者甚難發現 此種失效存在,要消除此種失效亦甚困難。 1
中等:造成客戶不舒適或感到困擾如擋風玻璃漏水、引擎聲音 超大。 評分方法:4-6(根據客戶不舒適程度而定) 低 :客戶感到輕微的困擾 評分方法:2-3(根據客戶不舒適程度而定) 輕微:懷疑這個失效可能會真的影響操作(使用),大部份的 客戶將可能不會注意到此項失效之影響。 評分方法:1
填表說明 — 項目/功能
潛在原因/機構的失效 定義:一種設計上的缺點所導致之失效模式。 使用:列出每一可能潛在失效原因,頇盡可能的依其重要性順序準確的提出。例: 潛在失效因素 規定的材料不正確 設計壽命估計不足 壓力大材質 潤滑能力不足 潛在機構失效 不穩定 化學性氧化 彎曲變形 電位移 1
失效模式与效应分析(FMEA)

失效模式与效应分析(FMEA)一、定义失效模式与效应分析(failure mode and effects analysis,FMEA)是一种前瞻性的管理模式,是在行动之前就认清问题并预防问题发生的分析。
FMEA由失效模式(failure oode,FM)及效应分析(effects analysis,EA)两部分组成。
其中,失效模式是指能被观察到的错误或缺陷(俗称安全隐患),应用于护理质量管理中就是指任何可能发生的护理不良事件;效应分析是指通过分析该失效模式对系统的安全和功能的影响程度,提出可以或可能采取的预防改造措施,以减少缺陷,提高质量。
二、目的、目标FMEA的目的是防患未然;设计屏障,让事情不要发生;降低损害,即使有风险存在,也是可容许的最低风险;是发现、评价流程中潜在的失效及其后果,找到能够避免或减少这些潜在失效的措施,并将上述过程文件化。
FMEA的主要目标是分析现有系统(流程)或将建立之系统(流程):哪里会出错?一旦出错会有多糟糕?哪里需要修正以避免事故发生?三、执行时机1、新设计的流程2、修改现行的流程3、旧的流程用于新的情境中四、实施步骤(一)步骤一:确认问题选择那些高风险或非常薄弱的程序进行研究。
高风险流程的特性有:高复杂性(步骤多)的作业、高差异性的输入来源、未标准化的作业、紧密相依的作业、作业时间间隔太紧或太松、高度依赖人员的判断或决定。
医疗行为中的高风险流程有:用药、病人处于危险的操作流程(放射治疗,CT扫描,磁振造影)、输血与输成分血、抑制作用的药物、对高危人群进行照顾或提供服务、与复苏相关等。
(二)步骤二:组建团队组建一个多学科的综合FMEA团队,团队中至少应该有一个领导者、一个所硏究流程方面的专家、一个FMEA咨询师(即FMEA专家,可以为团队领导者提供建议,保证FMEA的顺利实施)、一个对所研究流程不太熟悉的人(可以从不同的角度和方面提出有价值的建议)。
一般建议团队成员在6〜10人之间,以便于管理,所有成员必须接受过FMEA培训。
失效模式及效应分析 FMEA

•硬體設備失效:故障狀況 ( 如:短路、漏電、 斷裂、變形、腐蝕、鬆動、磨耗、卡死、洩漏 等)
•材料失效:不良內容(如:尺寸不良、材質錯誤、 變形、漏油及油污)
•對於服務業而言可以「服務特性之失 效」,作 為失效模式思考方向。此 外, 當 FEMA 表內同時出現二個以上不正常 及故障項目時,應修改成各自不同的名 稱,然後再記入 FEMA 表內。
評價準則-失效影響嚴重度 S:
嚴重性 基
準
10
危險無預警,直接影響安全
9
危險可預警,直接影響安全
8
失去主要功能,END USER 無法工作
7
主要功能降低,END USER 仍可工作,客戶會不滿意
主機能動作,影響週邊方便性或舒適性之項目無法工 6
作,客戶感覺不方便
主機能動作,週邊方便性或舒適性之項目功能降低,客 5
失效模式及效應分析 FMEA
前言
• FMEA(Failure Mode And Effect Analysis) 自 1950 年代初期就被當做是 航空機用動力計劃的解析法,到了實施 阿波羅計劃獲得重大成就後,即被廣泛 推廣開來。此外 FMEA 亦是 QS9000 中 設計活動中要求應適當具備的技術。
產品設計開發的 FMEA 表作成
•記入 FMEA 對象的品名及名稱 。 •記入 FMEA 對象的識別編號 。 •依照製造工程順序在「名稱」欄位寫上
工程名稱、使用及設備投入的材料 。 •將工程、使用設備及投入材料這些原本
應具備的功能記入在「功能」欄內 。 •失效模式 (公司可先定義失效模式)
FMEA失效模式与效应分析

FMEA失效模式与效应分析
FMEA是一种常用的质量管理方法,全称为“失效模式和影响分析”(Flure Mode and Effects Analysis)。
它是一种定量分析工具,用于衡量所研究系统的某种失效模式和这种失效模式带来的效应。
它可以通过对失效模式进行系统的分析和归纳,找出并解决潜在的失效模式,从而提高产品、过程和系统的质量和可靠度。
下面我们来详细了解一下FMEA失效模式与效应分析。
一、FMEA的基本概念
FMEA是一种质量管理工具,可以对产品制造或过程设计进行评估,以识别可能出现的失效模式,并预先采取相应的改进措施以消除或减轻风险。
该方法可以帮助组织识别潜在问题并提供预防性控制,以最大程度地降低可能的风险。
FMEA通常包括以下步骤:
1.识别和描述潜在的失效模式;
2.评估和量化失效模式的可能性、严重性和检测能力(即失效模式对产品质量和可靠性的影响);
3.识别并建议风险缓解措施。
二、FMEA的分类
FMEA可以分为设计FMEA(DFMEA)和过程FMEA(PFMEA)两种类型。
1.设计FMEA( DFMEA)
1。
FMEA(失效模式及效应分析)教材
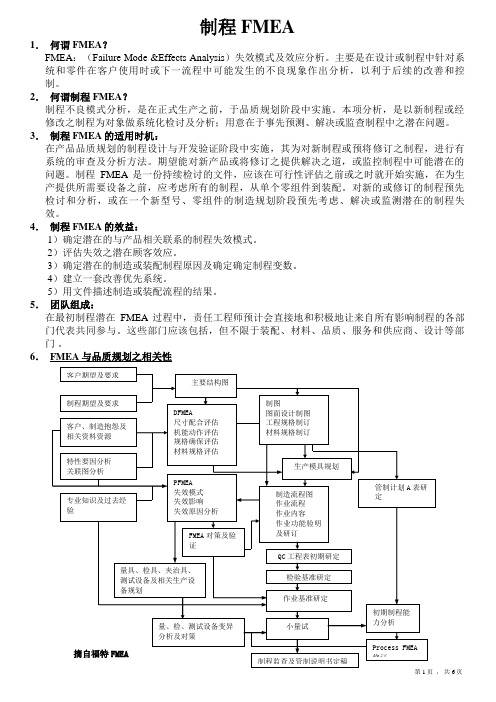
制程FMEA1.何谓FMEA?FMEA:(Failure Mode &Effects Analysis)失效模式及效应分析。
主要是在设计或制程中针对系统和零件在客户使用时或下一流程中可能发生的不良现象作出分析,以利于后续的改善和控制。
2.何谓制程FMEA?制程不良模式分析,是在正式生产之前,于品质规划阶段中实施。
本项分析,是以新制程或经修改之制程为对象做系统化检讨及分析;用意在于事先预测、解决或监查制程中之潜在问题。
3.制程FMEA的适用时机:在产品品质规划的制程设计与开发验证阶段中实施,其为对新制程或预将修订之制程,进行有系统的审查及分析方法。
期望能对新产品或将修订之提供解决之道,或监控制程中可能潜在的问题。
制程FMEA是一份持续检讨的文件,应该在可行性评估之前或之时就开始实施,在为生产提供所需要设备之前,应考虑所有的制程,从单个零组件到装配。
对新的或修订的制程预先检讨和分析,或在一个新型号、零组件的制造规划阶段预先考虑、解决或监测潜在的制程失效。
4.制程FMEA的效益:1)确定潜在的与产品相关联系的制程失效模式。
2)评估失效之潜在顾客效应。
3)确定潜在的制造或装配制程原因及确定确定制程变数。
4)建立一套改善优先系统。
5)用文件描述制造或装配流程的结果。
5.团队组成:在最初制程潜在FMEA过程中,责任工程师预计会直接地和积极地让来自所有影响制程的各部门代表共同参与。
这些部门应该包括,但不限于装配、材料、品质、服务和供应商、设计等部门。
6.FMEA与品质规划之相关性共6页7.制程FMEA 流程图第2页,共6页不良模式举例:弯曲、破裂、误装 效应范例:不规律之操作、外观瑕疵、需格外的用力,无法扣紧 原因范例: 扭力之不当、不当之工具、量具不准确、保管不当之损伤流程列出制程特性 对每一作业可能出错之处加以明定之 不良模式是对该特定之作业被判定不合格之理由的详细描述 效应可以车辆/系统功能之方式描述或以制程/作业功能之方式描述 如果该效应涉及无法符合政府法规之潜在因素或对车辆操作安全之潜在影响则必需加以指出原因必须以某种可予以改正或管制之方式加以描述 目前之管制用以防止不良模式之发生或用以侦测不良之是否发生按FMEA 手册中之表列,帮助解决各项分数。
- 1、下载文档前请自行甄别文档内容的完整性,平台不提供额外的编辑、内容补充、找答案等附加服务。
- 2、"仅部分预览"的文档,不可在线预览部分如存在完整性等问题,可反馈申请退款(可完整预览的文档不适用该条件!)。
- 3、如文档侵犯您的权益,请联系客服反馈,我们会尽快为您处理(人工客服工作时间:9:00-18:30)。
.H:rf+[ fl +:r"&]g6tFi|EA
. fls:lrf lErif ' taEFJ&^R.*.8R.FrdH.!&6th1" .t
.
+} 1+4.1'14d*.r3+El6gf nf'a.&i*1?Wt
n ,
F
a
j
"
t
rE
'
d
n
,
v
'
n
r
'
u
&
E
z
.4 ?fg+k rf tE6 ifrAtFllE(A6 Siena)
.
iF4, .tttt.*rlut
E.
+L'&-+44hhEts+ ' EE4+t-+ztttF,,-.f-rkl4
Wh.JiL*.
. 4*_1Bt-t!.sp.kY.1$( P. DM)
ffE,'"4tf 6t€+1*
4 L++hE-F"fAl*d,'i €.;* Sz.J*1. 6
1 .1 , i , t & e ^ i { ( 5 1 { 2 H ) & D e sr ei svni e u , ( 6- ]j f!l l* ) 23..&E4€i.t4+-6ir1gi f.AA1rE.+'+E#nfjfA| (i.Ci. ustorVr oice) 4. d4 &?E6 ftE&tB nE+;'trt,E 5.€6i a &i{;+ ?rtS.&isrA 6 .F . S 0 f D , : " q { q e R f r l ,rtEE, r € , , t J t r t , % . c } 6 & r a q " , i , t r
. Control plan design
. Sensorandxoonitor
APQP€*I^E-/Iffi ( AdvancedProductQualifyPlanning OFDAlH&BCEFE
ControlPlan
FMBAiTJfr&EH
.,."H&IAd.r-EtWAf*,k,{3fE\lr,i>rCtr*qrf.**i++tE[,8FJA.t"+r3""&ft."rf-€iErFrE&\*M+'lFEA(:.!AtxtzalSa #')rf,rlg.#-.Ei.itietr+"ftWl* +Yer.
t :{rAril lech.ni$'r; r t,&.J i-"i. r
?.€ n'iA3t11t+E(;t;tsop)&+m&fii 6 ++.S B..Ei:g6i;ig;i 6&Desimrevie&iA:16h(Desisn v e r if i c a t i o n ) 9.lE,4Fr{:qii (DOEor Tasuci h)lA6 f .Ettt4 &Robustness 10.€r-r:+*E61filtt.l$rE) DF$EAPFME{ 11.{tH,Ei:g6+i * e rglSr6.&.inIestone<e*,lF} 12.d ^?19AtAg 6+{t.E r"1i+*E6!BoM€./:/+ aiprtl{-q E e+{ 13.&fr &'A.!"q &++ )tl+ ji rt+(sPc ,/ Qc+r*/yAVE/MSA) 14.€n{tai A;1rt )n?€s+afi+ 6 (it4 a !i,Jt+a ?rjLL)
RiiiH;\,g+rif6r\*6(Faliure Mode&Effect
AnalysisF, MEA€)-t€e &.fhzr4a;1s1+fi
E)ti4* 4**
4' Ifrsj ht-+E\f'rEh+fEt -!"' ffitt :tEPrt
r- +z,Sit, fh&,*7.t
41t*zX_E&-te' -+tE+"/yr-,-&,E1)++* ey€A..r9'z*€iw
. ri$ a*+bii*iB.1&f &d'€*idiia&,iii*it. &tEr
{t14fi,#efiw fr.4 " . *+tf*1+6ti*ie' tA€.L4r"1|l*&iFrhff.r&6t*iri.
' t+d.*.18*1+*Ed.*1+i8er,lEfE&&il1"1itltiti4f.
E+r\,'j,t,r-6EFMAEEu,;d,, a-+E!4e.-AE h +*,
4iAA9-9' El+,WtrLffiPAeA4h"$"ft
. F MEAt4 F<ffirhi h'frt-+, &-- 4€A4+
19h\4E&' +Pfr6hl
kr4klg{/il.Lehtrl+h'if'r'4;ir-'a1Nn,E8",'#*.Mh -i,.ff^iAti
,&t*
HAfTFMEA(PFMEA-f)rE*i€ET'sil
,EEkElE?,t(t-fl+.€t.f*6oa..fri^!. rkF.E**le€ g, 1Ig,
a
I
L&E#+tr+R4+E,z"6Wt.Lt4&'.r"4.-6*.)lA4
4 ft,ry .
I A+ | *4&/M.#.x,+. .a.ftr*, EE&-
IQ@* 7tt #'lL' fi. t^*-48*- & ^ iallh6tX 4.,
iai*s(lF13r6i +J*r6 '
{ tt i4 t! ,z\}.4(Failure Modeand Effects Analysis,F"fqS FMEA)ftA.r 4 4htt6xhAE4,?e iL4i1t+*,ffirti€91 ' *a Elh :
BfiiAE
j(Eid :
E| -1' g'f6tf6r .,rl&t g+€?4) &8)7
"
'
.
r
iR+64 E ti.+a *i 4' kT#t#,64.F.+-F4P'ffi Edt t" g 7VS7q'40 ]Et, + 8 F"1&il 4,!fi:h h \! & t E f ' A + { q ^ f " F f i r i r 6 t * h ' f u f f i , + +Fffi€ ' eHElt6ifddArA^"
ft,*--'Az4*E AW16,44SE4+,4a< #14' &-
A;4ቤተ መጻሕፍቲ ባይዱt1E+E-.
€r ne.-,fir
X a4aE* ffi,iT' ft ;A',tISO$q ;+
Erl i+46ta .t4+1€+,i(QS90
0
0
)
'
*FA FMEAEi
1,84, +.:+
:,fE&AEAA
FMA)FEA)CriticalAitynalysis )CorrectiveAction
s €.i{?t 6-Qual ity Engineering ' {fi,q;r;l . DOD/TM . DFMNA
' PFMNA
€"q&.+e - Quai tly
Inproving . PSP/8D
. QIT . QCC
C""o"€nterfoil{&* Quaitl y ' sPc . rnff]* rb
**"IEt -,)Wt JLE"HFII#L
E"Hk th,6-Qual ity System
' QMS_ISO9OO ' QS9000
s €€,F 6 - Quaitl y Procedure
. QualityFunction Deployent
. APQP(advancperodduct quality planning)
, E 8"e-3.4e618 + *.rki{ d . , ""A"t4'-+A- Et--3'eH # hi krk 1s,z4.t " ' )liyt i\ ;ti.) # 4 ^^*-4*E h1et+- t+tfr,, 4',(,* ti.