蒸馏流程图
酒精工艺流程、设备图

002.蒸煮、糖化工段常用工艺、设备流程004.蒸馏工段常用设备工艺流程图
005.酒精生产中常用的搅拌、预热设备
006.酒精蒸馏工艺流程图
1.回流装置 3.液相进塔的两塔流程 5.三塔蒸馏流程图 7.五塔蒸馏流程 9.上海酒精厂蒸馏流程 11.半直接式脱甲醇三塔蒸馏流程 13.五塔系醪液精馏机组 15.制取无水酒精的设备流程
粉碎工段工艺设备流程图蒸煮糖化工段常用工艺设备流程图酒母发酵工段常用工艺设备流程图蒸馏工段常用设备图酒精生产中常用的搅拌预热设备酒精蒸馏工艺流程图01
粉碎工段工艺、设备流程图 蒸煮、糖化工段常用工艺、设备流程图 酒母、发酵工段常用工艺、设备流程图 蒸馏工段常用设备图 酒精生产中常用的搅拌、预热设备 酒精蒸馏工艺流程图
2.精馏塔冷凝器装置 4.两塔气相过塔蒸馏流程图 6.半直接式三塔蒸馏流程图 8.哈尔滨五塔蒸馏流程 10.半直接式三塔蒸馏流程 12.四塔系酒精蒸馏机组工艺流程 14.五塔系醪液精馏设备 16.超阿罗斯帕斯式蒸馏机组工艺流程
精馏工艺流程图
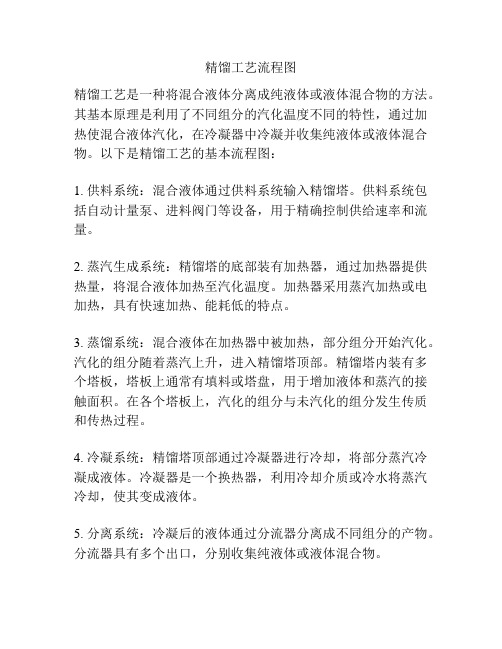
精馏工艺流程图
精馏工艺是一种将混合液体分离成纯液体或液体混合物的方法。
其基本原理是利用了不同组分的汽化温度不同的特性,通过加热使混合液体汽化,在冷凝器中冷凝并收集纯液体或液体混合物。
以下是精馏工艺的基本流程图:
1. 供料系统:混合液体通过供料系统输入精馏塔。
供料系统包括自动计量泵、进料阀门等设备,用于精确控制供给速率和流量。
2. 蒸汽生成系统:精馏塔的底部装有加热器,通过加热器提供热量,将混合液体加热至汽化温度。
加热器采用蒸汽加热或电加热,具有快速加热、能耗低的特点。
3. 蒸馏系统:混合液体在加热器中被加热,部分组分开始汽化。
汽化的组分随着蒸汽上升,进入精馏塔顶部。
精馏塔内装有多个塔板,塔板上通常有填料或塔盘,用于增加液体和蒸汽的接触面积。
在各个塔板上,汽化的组分与未汽化的组分发生传质和传热过程。
4. 冷凝系统:精馏塔顶部通过冷凝器进行冷却,将部分蒸汽冷凝成液体。
冷凝器是一个换热器,利用冷却介质或冷水将蒸汽冷却,使其变成液体。
5. 分离系统:冷凝后的液体通过分流器分离成不同组分的产物。
分流器具有多个出口,分别收集纯液体或液体混合物。
6. 冷却系统:分离后的产物通过冷却器进行冷却,使其达到所需的温度。
冷却器通常采用冷却介质或冷水进行冷却。
7. 收集系统:经过冷却后的产物被收集到不同容器中,用于进一步的处理或包装。
以上就是精馏工艺的基本流程图。
根据实际需要,可以根据不同的物料和要求进行调整和改进。
此外,精馏工艺还可以与其他工艺结合使用,如萃取、蒸汽压缩等,以获得更高的分离效果和节能效果。
第三节 原油蒸馏工艺流程原

第三节原油蒸馏工艺流程一、原油蒸馏工艺流程的类型原油蒸馏工艺流程,就是用于原油蒸馏生产的炉、塔、泵、换热设备、工艺管线及控制仪表等按原料生产的流向和加工技术要求的内在联系而形成的有机组合。
将此种内在的联系用简单的示意图表达出来,即成为原油蒸馏的流程图。
现以目前燃料一润滑油型炼油厂应用最为广泛的初馏一常压一减压三段汽化式为例,对原油蒸馏的工艺流程加以说明,装置的工艺原则流程如图2.3.1所示。
图2.3.1 三段汽化的常减压蒸馏原理工艺流程图经过严格脱盐脱水的原油换热到230-240℃,进入初馏塔,从初馏塔塔顶分出轻汽油或催化重整原料油,其中一部分返回塔顶作顶回流。
初馏塔侧线不出产品,但可抽出组成与重汽油馏分相似的馏分,经换热后,一部分打入常压塔中段回流入口处(常压塔侧一线、侧二线之间),这样,可以减轻常压炉和常压塔的负荷;另一部分则送回初馏塔作循环回流。
初馏塔底油称作拔头原油(初底油)经一系列换热后,再经常压炉加热到360-370℃进入常压塔,它是原油的主分馏塔,在塔顶冷回流和中段循环回流作用下,从汽化段至塔顶温度逐渐降低,组分越来越轻,塔顶蒸出汽油。
常压塔通常开3-5根侧线,煤油(喷汽燃料与灯煤)、轻柴油、重柴油和变压器原料油等组分则呈液相按轻重依次馏出,这些侧线馏分经汽提塔汽提出轻组分后,经泵抽出,与原油换热,回收一部分热量后经冷却到一定温度才送出装置。
常压塔底重油又称常压渣油,用泵抽出送至减压炉,加热至400℃左右进入减压塔。
塔顶分出不凝气和水蒸气,进入冷凝器。
经冷凝冷却后,用二至三级蒸气抽空器抽出不凝气,维持塔内残压 0.027-0.1MPa,以利于馏分油充分蒸出。
减压塔一般设有 4-5根侧线和对应的汽提塔。
经汽提后与原油换热并冷却到适当温度送出装置。
减压塔底油又称减压渣油,经泵升压后送出与原油换热回收热量,再经适当冷却后送出装置。
润滑油型减压塔在塔底吹入过热蒸汽汽提,对侧线馏出油也设置汽提塔,因为塔内有水蒸气而称为湿式操作。
蒸馏实验

蒸馏实验---基本操作实验报告
在多年的有机化学实验教学中,看到刚刚学做有机实验的学生,无论是药学、制药工程专业的,还是如临床医学、检验医学、生物科学等相关专业的学生,对于刚刚接触蒸馏、重结晶、水蒸气蒸馏等基本操作实验,多不明白如何动手正确、规范地进行实验操作(如收集产品)与应该观察记录那些实验现象,也不清楚如何完成实验报告,严重地影响了实验教学质量,所以结合本学院有机实验报告的格式,写此蒸馏报告,希望能够对大家有所帮助。
仅供广大学生的学习之用参考。
三、主要试剂、产物、副产物的物理常数:
四、药品与试剂的用量及产物的理论产量:
五、主要仪器、器材名称及型号:
250ml蒸馏烧瓶100℃温度计直形冷凝管接液管100ml三角烧瓶50ml量筒玻璃漏斗调温电热套升降台铁架台万用夹双口夹乳胶管
六、仪器装置图
七、流程图:
(基本操作实验略,待做合成实验时用)
八、实验记录:。
第三节原油蒸馏工艺流程原
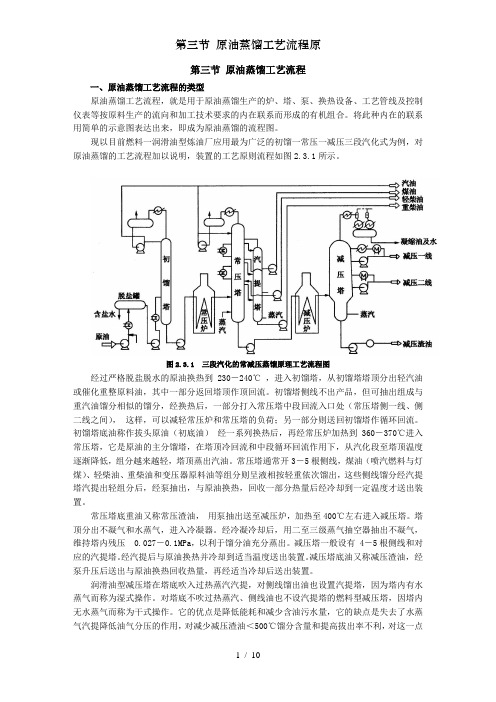
第三节原油蒸馏工艺流程一、原油蒸馏工艺流程的类型原油蒸馏工艺流程,就是用于原油蒸馏生产的炉、塔、泵、换热设备、工艺管线及控制仪表等按原料生产的流向和加工技术要求的内在联系而形成的有机组合。
将此种内在的联系用简单的示意图表达出来,即成为原油蒸馏的流程图。
现以目前燃料一润滑油型炼油厂应用最为广泛的初馏一常压一减压三段汽化式为例,对原油蒸馏的工艺流程加以说明,装置的工艺原则流程如图2.3.1所示。
图2.3.1 三段汽化的常减压蒸馏原理工艺流程图经过严格脱盐脱水的原油换热到230-240℃,进入初馏塔,从初馏塔塔顶分出轻汽油或催化重整原料油,其中一部分返回塔顶作顶回流。
初馏塔侧线不出产品,但可抽出组成与重汽油馏分相似的馏分,经换热后,一部分打入常压塔中段回流入口处(常压塔侧一线、侧二线之间),这样,可以减轻常压炉和常压塔的负荷;另一部分则送回初馏塔作循环回流。
初馏塔底油称作拔头原油(初底油)经一系列换热后,再经常压炉加热到360-370℃进入常压塔,它是原油的主分馏塔,在塔顶冷回流和中段循环回流作用下,从汽化段至塔顶温度逐渐降低,组分越来越轻,塔顶蒸出汽油。
常压塔通常开3-5根侧线,煤油(喷汽燃料与灯煤)、轻柴油、重柴油和变压器原料油等组分则呈液相按轻重依次馏出,这些侧线馏分经汽提塔汽提出轻组分后,经泵抽出,与原油换热,回收一部分热量后经冷却到一定温度才送出装置。
常压塔底重油又称常压渣油,用泵抽出送至减压炉,加热至400℃左右进入减压塔。
塔顶分出不凝气和水蒸气,进入冷凝器。
经冷凝冷却后,用二至三级蒸气抽空器抽出不凝气,维持塔内残压 0.027-0.1MPa,以利于馏分油充分蒸出。
减压塔一般设有 4-5根侧线和对应的汽提塔。
经汽提后与原油换热并冷却到适当温度送出装置。
减压塔底油又称减压渣油,经泵升压后送出与原油换热回收热量,再经适当冷却后送出装置。
润滑油型减压塔在塔底吹入过热蒸汽汽提,对侧线馏出油也设置汽提塔,因为塔内有水蒸气而称为湿式操作。
常减压蒸馏装置工艺流程图

可再生能源
利用太阳能、风能等可再生能源,减少 化石燃料的使用,降低碳排放,促进能源 可持续利用。
能源监测
建立能源管理信息系统,实时监测能源 使用情况,及时发现异常情况并采取措 施,提高能源利用效率。
产品质量控制
严格检测
对所有生产的产品进行全面、 细致的理化检测,确保产品指 标符合质量标准。
抽样分析
离方法,提高分离效率和纯 度。
3 提高能源利用率
采用节能技术,如废热回收 利用,降低整体能耗。
4 降低生产成本
优化原料、催化剂、工艺参 数等,减少原材料消耗和废 弃物产生。
设备检修
定期检查
定期检查装置内各设备的运行状态,及 时发现并修复故障,确保设备安全可靠 运行。
及时维修
发现问题后立即采取维修措施,防止故 障扩散,最大限度减少对生产的影响。
产品包装
合适的包装材料
1
选用安全环保的包装材料,如玻璃瓶、塑料容器或金属罐
,以确保产品的密封性和防渗漏性。
2
适当的包装尺寸
根据产品特性和客户需求,设计不同容量的包装规格,满
醒目的标签设计
3
足不同消费场景。
在包装上印刷产品名称、成分、生产日期等关键信息,同
时兼顾美观大方的视觉效果。
废气处理
尾气洁净
1
确保废气排放达到环保标准
液态回收 2
从废气中回收可用液体成分
热量回收 3
利用废气热量进行能源回收
常减压蒸馏装置会产生各种废气,包括含有有机物的尾气、酸性气体和含热量较高的气体。通过设置多级废气处理系统,可以实现 尾气洁净、液态成分回收以及热量回收,最大限度地提高资源利用率,降低环境影响。
冷却水系统
常减压蒸馏装置工艺流程图

减压渣油出装置 减压渣油出装置
3
中国石油华东设计院
4.1常减压蒸馏装置—工艺流程
4
中国石油华东设计院
4.1常减压蒸馏装置—工艺流程
5
中国石油华东设计院
注水 注氨 注缓蚀剂
常压塔
常一中油泵
常二中油泵 初底油自常压炉来
汽提蒸汽
常压塔顶回流罐
常压塔顶产品罐
常压汽提塔
含硫污水 ห้องสมุดไป่ตู้压塔顶回流泵
含硫污水
常顶产品油泵
常一线油泵 气提蒸汽
常二线油泵 汽提蒸汽
常三线油泵 常四线油泵
常底油泵
2
常顶不凝气
常顶油至轻烃回收部分 常顶一级油出装置 常一线油出装置 常二线油出装置
常三线油出装置 常四线油去减压塔 常底油至减压炉
中国石油华东设计院
4.1常减压蒸馏装置—工艺流程
蒸汽 减顶气 减顶油出装置
常压渣油自常压部分来
减顶真空泵
减顶油泵 含油污水
减顶油罐 减顶水泵
汽提蒸汽
减一线及一中泵 减二线及二中泵
减三线及三中泵 洗涤油泵
燃料油 燃料气 减压炉
减压塔
减压渣油泵
减一线油出装置
4.1常减压蒸馏装置—工艺流程图
脱盐排水
电脱盐罐
电脱盐罐
净化水
注水 注氨 注缓蚀剂
含硫污水 初顶油泵
初侧油泵
原油自罐区来
原油泵
初馏塔
初底油泵
1
常压炉
初顶不凝气 初顶油至轻烃回收部分 初侧油至常压塔
初底油至常压塔 燃料油 燃料气
中国石油华东设计院
化工原理 第六章 蒸馏(传质过程)
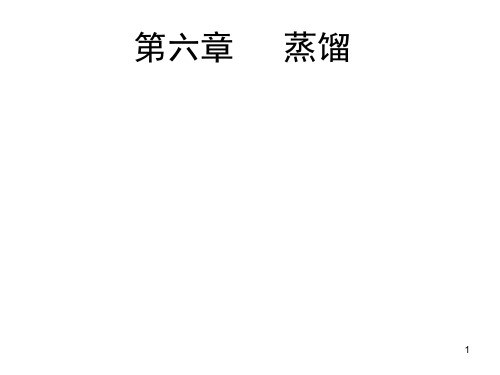
t
121.9℃
X=0.383
负偏差
x y
x y
y
y
x
x
19
挥发度与相对挥发度
挥发度:表示某种溶液易挥发的程度。 若为纯组分液体时,通常用其当时温度下饱和蒸 气压PA°来表示。 若为混合溶液时,各组分的挥发度,则用它在一 定温度下蒸气中的分压和与之平衡的液相中该组 分的 摩尔分数之比来表示, vA = pA / xA vB = pB / xB
演示
37
xn
xn 1 yn 1 yn
第四节 双组分连续精馏计算
38
物料衡算
F—原料(液)摩尔流量,kmol/h; D—馏出液摩尔流量,kmol/h; W—釜残液摩尔流量,kmol/h; 总物料衡算 易挥发组分的物料衡算
D xD F xF
F D W
D F ( xF xW ) xD xW
xn 1
n 1
yn xn yn 1
n
n 1
T-x(y) 图
t 假设蒸汽和液体充分接触,并在离 n 1 开第 n 层板时达到相平衡,则 yn 与 xn t n t n 1 平衡,且yn>yn+1,xn<xn-1。
这说明塔板主要起到了传质作用, 使蒸汽中易挥发组分的浓度增加, 同时也使液体中易挥发组分的浓度 减少。
t5 t4 t3 t2 t1
E D
C
B A
x(y)
温度-组成图( t-x-y 图)
12
上述的两条曲线将tx-y图分成三个区域。
液相线以下的区域 代表未沸腾的液体, 称为液相区 气相线上方的区域 代表过热蒸气,称为 过热蒸气区; 二曲线包围的区域 表示气液同时存在, 称为气液共存区。
蒸馏流程图

连续精馏装置系统主要有以下几部分组成:
1、精馏塔:分为精馏段和提馏段,精馏段的作用是精制汽相中易挥发组分;提
馏段的作用是提浓液相中难挥发组分。
2、全凝器:其作用是将塔顶蒸汽全部冷凝为液体。
3、贮槽:贮存从全凝器流出的液体。
4、冷却器;用冷却水冷却塔顶产品。
5、回流液泵:将贮槽的一部分液体打回塔顶,作为回流液,提供塔内各板上所
必需的液流,建立各塔板上的正常浓度分布、维持全塔正常操作。
6、再沸器(蒸馏釜):其作用是加热塔底液体,产生上升蒸汽,保证塔内各板处
于沸腾状态,与下降的液体逆流接触进行物质传递。
7、原料预热器:其作用是加热原料,冷却塔底产品。
常减压蒸馏装置—工艺流程图.ppt

常压塔
注水 注氨 注缓蚀剂
常压塔顶回流罐
常压塔顶产品罐
常顶不凝气
常顶循油泵 含硫污水 初侧油自初馏塔来 常压汽提塔 含硫污水 常顶油至轻烃回收部分 常压塔顶回流泵 常顶产品油泵
常顶一级油出装置
常一线油出装置 常一中油泵
常一线油泵
常二中油泵
气提蒸汽
常二线油出装置
初底油自常压炉来 常二线油泵
汽提蒸汽
汽提蒸汽 常三线油出装置
常三线油泵 常四线油去减压塔 常四线油泵 常底油至减压炉
常底油泵
1
中国石油华东设计院
4.1常减压蒸馏装置—工艺流程
2
中国石油华东设计院
4.1常减压蒸馏装置—工艺流程
初顶不凝气
初顶油至轻烃回收部分
初侧油至常压塔
3
中国石油华东设计院
4.1常减压蒸馏装置—工艺流程
4
中国石油华东设计院
4.1常减压蒸馏装置—工艺流程
初顶不凝气 注水 注氨 注缓蚀剂
含硫污水
初顶油至轻烃回收部分
初顶油泵
脱盐排水
电脱盐罐
电脱盐罐 初侧油至常压塔
初侧油泵
净化水
初底油至常压塔
燃料油 燃料气
原油自罐区来
原油泵
初馏塔
初底油泵
常压炉
5
中国石油华东设计院
活动方案 常压蒸馏系统流程图

常压蒸馏系统流程图常压工艺流程简述常压蒸馏系统流程图2.1.工艺原理常压蒸馏是原油加工的第一道工序,本装置是根据原油中各组分的沸点(挥发度)的不同,用加热和蒸馏的方法从原油中分离出各种石油馏分。
原油经过换热进初馏塔,从塔顶馏出,初馏点~80℃的馏分,进入常压塔中部。
拔头原油经常压炉升温为汽液两相,在常压塔内与冷液相充分接触,进行传质传热。
从塔顶分离汽油组份,塔自上而下得到侧线产品:轻柴油、重柴油、蜡油等,塔底分离出沸点较高的重油。
这部分重油分子量较大,在高温下易发生裂解反应,而降低馏分油质量或引起结焦,根据在减压下油品沸点低易蒸馏道理,将减压塔用往复式真空泵抽成负压塔进行蒸馏,从减压塔顶分出的馏分,作为柴油混入常二线;减一线油和常三线油作为重柴油;减二线油做蜡油;减三线油做催化裂化原料.另外,减二、三线油还可以做润滑基础油,减压塔底渣油除做燃料以外,还可做氧化沥青装置原料。
常压蒸馏系统流程图2.2.流程说明2.2.1换热部分常压蒸馏系统流程图大约45℃的原油从原稳灌区的C101、C102罐进装置,经原油泵(B101/1.2)升压后进入原油换热系统。
原油经E-101与常顶循换热到67℃;经E-102与减一线换热至85℃;经E-103与常一中换热;经E-104与减三线(Ⅲ)换热至100℃左右。
原油经E-104后分成两路进行换热。
一路去F201(减压炉)的对流室,做为减压炉冷进料,换热至200℃左右。
另一路经E-105与减二线(Ⅲ)换热至165℃,经E-107与减三线(Ⅱ)换热,经E-108与常二线(Ⅱ)换热,经E-109与减二线(Ⅱ)换热,经E-110与减渣(Ⅱ)换热,最后换热至200℃左右,两路原油合并成一路,进入初馏塔T101,进塔温度约为200℃左右。
2.2.2常压分馏部分两路原油合为一路进入初馏塔(T101),初馏塔顶油气进入常压塔(T102)的第30层塔盘,作为常压塔的汽相进料。
初馏塔底拔头油,温度为190℃左右,经初底油泵(泵102/1.2)抽出进行换热。
常减压蒸馏

7.常减压蒸馏塔模拟软件
模拟软件按功能可分为设计型和核算型两类。
7.1设计型软件
可以分别采用快捷法和严格法两种数学模型编制,前者适 于做方案设计,快速确定全塔物料平衡、热量平衡、初定 理论板数等设计值;后者可提供诸如塔板上汽液相组成和 性质等详细资料,对于做蒸馏塔的详细设计,以及实施自 动化控制方案是必要的。(如:) 7.2核算型软件 主要用于装置标定,应该以快捷数学模型编制,既满足标 定要求,又方便用户使用。(如:上海申迪软件工程有限 公司开发的常减压指导系统CDDS )
5.1.3高温烟气的腐蚀 在常减压装置加热炉设备中,燃烧过程中生成含 SO2和SO3的烟气在加热炉的低温部位与空气中的 水分冷凝,产生硫酸露点腐蚀,造成设备的损坏。
5.2相应对策 5.2.1设计防腐 在易腐蚀部位合理选用耐腐蚀材料或复合材料 5.2.2施工防腐 加强易腐蚀部位焊缝的全过程监测和监督(主要是对成 千上万条焊缝从焊工管理、焊接工艺管理、焊条管理、 焊条质量管理等环节进行全过程控制) 5.2.3工艺防腐 a.优化原油电脱盐; b.塔顶“三注”:在初顶、常顶和减顶馏出线上注氨水、 缓蚀剂和冷凝水) 5.2.4管理防腐 全员参与腐蚀管理
现代石油馏分气液平衡和石油精馏的数值计算 都是采用虚拟组分的处理方法,即将石油馏分 切割成有限数目的窄馏分,每一个窄馏分都视 为一个纯组分,称为“虚拟组分”; 选择适合各石油馏分的系列关联式计算虚拟组 分的物理性质(平均沸点、特性因数,相对密度 等),从而将复杂的石油体系转化为由多个虚拟 组分构成的混合物体系,用多元系的方法进行 处理计算。
应用实例—大型减压蒸馏塔
企业/时间 茂名石化公司四蒸馏润 滑油减压塔,1998.8 上海高桥石化公司润滑 油减压塔,2002.9 乌鲁木齐石化公司润滑 油减压塔,2000.8 齐鲁石化公司炼油厂, 2003.3 燕山石化公司润滑油减 压塔,2000.9 规模 万吨/年 500 800 350 600 350 直径 米 8.4 10.2 6.4 7.4 6.4 采用技术 新型填料、导液盘式液体分布 器,气体分布器 新型填料、导液盘式液体分布 器,气体分布器,桁架梁 新型填料、导液盘式液体分布 器,气体分布器 新型填料、导液盘式液体分布 器,气体分布器 新型槽式液体分布器
蒸馏过程与设备
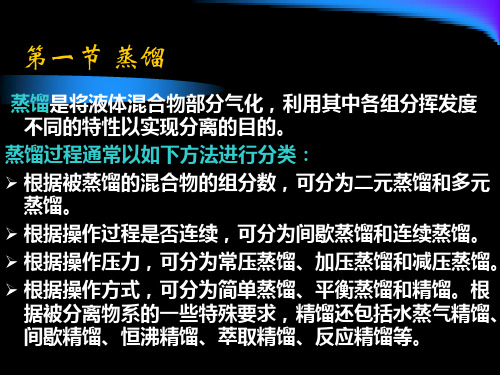
➢ 半直接式:粗酒精由粗馏塔进入排醛塔是气相过塔, 而脱醛酒进入酒精塔是液相进。
7
8
9
1
56
来
工业
成 熟
醛酯酒
自
酒精
醪
醪
3
成品
池
蒸汽
蒸汽 2
酒精
4 杂酯油
蒸汽
废水
图12-14 半直接式三塔流程 1-预热器 2-精馏塔 3-脱醛塔 5、7、8-分凝器 6-冷凝器
3.间接式。粗酒精进入排醛塔以及脱醛酒进入精馏塔
都是液相进塔。可以较半直接式多一次驱除头级杂质的
机会。因此可以产出高纯度的酒精。
2 10
蒸汽 1
3 3 11
蒸汽 酒精
5 4 不合格
69
酒精
头
级
12
杂
质
15 15 脱醛酒
8
杂醇酒 7
蒸汽
蒸 馏 酒 精 13
14
15
杂醇油
废水
图12-15 间接式三塔流程
2. 减压蒸馏装置
减压蒸馏装置主要由蒸馏、抽气(减压)、安全保 护和测压四部分组成。
2. 1 蒸馏部分
➢ 由蒸馏瓶、克氏蒸馏头、毛细管、温度计及冷凝管、接 受器等组成。
➢ 克氏蒸馏头:减少由于液体暴沸而溅入冷凝管的可能性 ➢ 毛细管:提供气化中心,使蒸馏平稳,避免液体过热而
产生暴沸冲出现象。毛细管口距瓶底约1~2mm,为了 控制毛细管的进气量,可在毛细玻璃管上口套一段软橡 皮管,橡皮管中插入一段细铁丝,并用螺旋夹夹住。 ➢ 蒸出液接受部分:通常用多尾接液管连接两个或三个梨 形或圆形烧瓶,在接受不同馏分时,只需转动接液管, 在减压蒸馏系统中切勿使用有裂缝或薄鄙的玻璃仪器。 尤其不能用不耐压的平底瓶(如锥形瓶等),以防止内 向爆炸。
分子蒸馏PPT课件

9. 黄油
2019/2/11 34
1.盐基油
石 油 化 工
2. 亮库存油
3. 润滑油
4. 石蜡油
5. 沥青残留物
6. 焦油
2019/2/11
35
1.羊毛酯酸
日
化
2. 羊毛酯醇
3. 烷基多酣 4. 海藻、金雀花、褐苔、鲜花、 根菜作物、辣椒的提取物
2019/2/11
36
1.广藿香油 2. 玫瑰油
应用领域和产品
1. 酸性氯化物 2. 氨基酸酯 3. 葡萄糖衍生物 4. 吲哚 5. 萜酯 6. 天然和合成维生素 7. 互叶白千层油 8. 辣椒碱 9. 大蒜素的精制 10. 川芎 11. 当归 12. 姜油 13. 中草药有效成分的提纯
制 药
2019/2/11
31
1.醇类 2. —酯 3. 乙二醇醚
2019/2/11 17
刮 膜 式 蒸 发 器
机械 “刮膜”,温度梯度和死点被大大减 小 极限装 置
2019/2/11
内部冷凝器,流阻小,极限真空高
19
分子蒸馏器的模式
离心薄膜式
转子刮膜式
主要区别在于物料形成薄膜的方法不同 现在国内、外的工业化装置以转子刮膜式为主
在远远低于沸点下进行操作的。 常规的真空蒸馏通常在沸腾状态下操作,由于 塔板或填料的阻力较大,使操作温度比分子蒸 馏要高得多,如某一混合物的分离,采用真空
蒸馏时其操作温度为260℃,换用分子蒸馏的
操作温度可能降到160℃左右。
2019/2/11 5
2.蒸馏压强低
由于分子蒸馏装置独特的结构形式, 其内部压 强极小, 可以获得很高的真空度。同时, 由分子 运动自由程公式可知, 要想获得足够大的平均 自由程, 可以通过降低蒸馏压强来获得, 一般为 1×10-4Pa数量级。
- 1、下载文档前请自行甄别文档内容的完整性,平台不提供额外的编辑、内容补充、找答案等附加服务。
- 2、"仅部分预览"的文档,不可在线预览部分如存在完整性等问题,可反馈申请退款(可完整预览的文档不适用该条件!)。
- 3、如文档侵犯您的权益,请联系客服反馈,我们会尽快为您处理(人工客服工作时间:9:00-18:30)。
必需的液流,建立各塔板上的正常浓度分布、维持全塔正常操作。
6、再沸器(蒸馏釜):其作用是加热塔底液体,产生上升蒸汽,保证塔内各板处
于沸腾状态,与下降的液体逆流接触进行物质传递。
7、原料预热器:其作用是加热原料,冷却塔底产品。
Байду номын сангаас
连续精馏装置系统主要有以下几部分组成:
1、精馏塔:分为精馏段和提馏段,精馏段的作用是精制汽相中易挥发组分;提
馏段的作用是提浓液相中难挥发组分。
2、全凝器:其作用是将塔顶蒸汽全部冷凝为液体。
3、贮槽:贮存从全凝器流出的液体。
4、冷却器;用冷却水冷却塔顶产品。