重力浇铸
重力浇铸和压铸的区别专业知识讲座

Page: 5
文档来源于网络,文档所提供的信息仅供参考之用,不能作为科学依据,请勿模仿。文档如有
低压铸造
不当之处,请联系本人或网站删除。
低压铸造的工艺过程为:在密封的坩埚(或密封罐)中,通入干燥的压缩空气,金属液在气体压 力的作用下,沿升液管进入直浇道上升,通过内浇道平稳地进入型腔,并保持坩埚内液面上的气 体压力。直到铸件完全凝固为止。然后解除液面上的气体压力,使升液管中未凝固的金属液流回 坩埚。 再开型并取出铸件。
Page: 3
文档来源于网络,文档所提供的信息仅供参考之用,不能作为科学依据,请勿模仿。文档如有
高压铸造
不当之处,请联系本人或网站删除。
压力铸造分为高压铸造和低压铸造两种。
高压铸造是一种将熔融合金液倒入压室内,以高速充填钢制模具的型腔,并使合金液在压力下凝 固而形成铸件的铸造方法。
高压压铸区别于其它铸造方法的主要特点是高压和高速。 ①金属液是在压力下填充型腔的,并在更高的压力下结晶凝固,常见的压力为 15—100MPa。 ②金属液以高速充填型腔,通常在 10—50米/秒,有的还可超过80米/秒,(通过内浇口导入型
优缺点对比艺 复杂
模具 模具 气孔 费用 寿命 率
高短 差
热处 加工 表面 适宜产品 生产效率 理 余量 光洁
不可 小 高 薄壁件 高
低压铸造 简单 低 长 好 重力浇铸 简单 低 长 好
可以 大 高 中
中
可以 大 低 厚壁件 低
在强度方面,由于所事宜的铝合金原材料不同,其强度差异也较大: 压铸产品由于在高压下成型,产品致密性高,其强度较高。比如 A380的压铸产品,其强度可达到 360MPa,而其延伸率只能达到 3.7%左右。 重力浇铸产品一般情况强度要较压铸低。其材料较好的 ZL101A,热处理后也只能达到有310MPa, 但其延伸率较高,能达到5-6%。也有强度能达到380MPa以上的材料,如ZL201A、ZL204A 。
浇铸是铸造吗
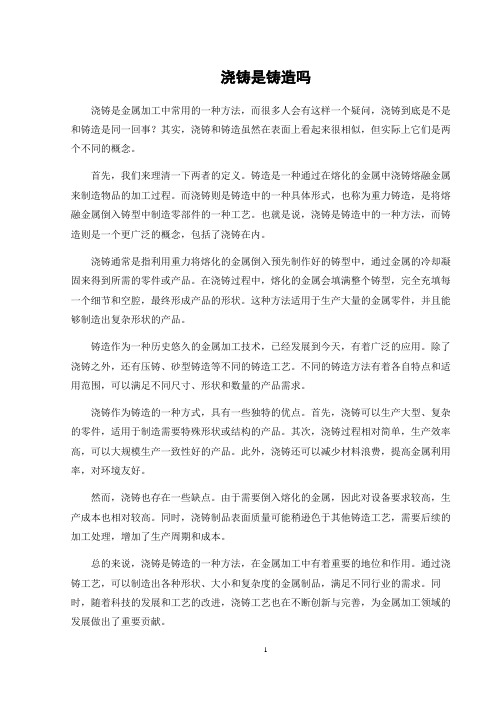
浇铸是铸造吗浇铸是金属加工中常用的一种方法,而很多人会有这样一个疑问,浇铸到底是不是和铸造是同一回事?其实,浇铸和铸造虽然在表面上看起来很相似,但实际上它们是两个不同的概念。
首先,我们来理清一下两者的定义。
铸造是一种通过在熔化的金属中浇铸熔融金属来制造物品的加工过程。
而浇铸则是铸造中的一种具体形式,也称为重力铸造,是将熔融金属倒入铸型中制造零部件的一种工艺。
也就是说,浇铸是铸造中的一种方法,而铸造则是一个更广泛的概念,包括了浇铸在内。
浇铸通常是指利用重力将熔化的金属倒入预先制作好的铸型中,通过金属的冷却凝固来得到所需的零件或产品。
在浇铸过程中,熔化的金属会填满整个铸型,完全充填每一个细节和空腔,最终形成产品的形状。
这种方法适用于生产大量的金属零件,并且能够制造出复杂形状的产品。
铸造作为一种历史悠久的金属加工技术,已经发展到今天,有着广泛的应用。
除了浇铸之外,还有压铸、砂型铸造等不同的铸造工艺。
不同的铸造方法有着各自特点和适用范围,可以满足不同尺寸、形状和数量的产品需求。
浇铸作为铸造的一种方式,具有一些独特的优点。
首先,浇铸可以生产大型、复杂的零件,适用于制造需要特殊形状或结构的产品。
其次,浇铸过程相对简单,生产效率高,可以大规模生产一致性好的产品。
此外,浇铸还可以减少材料浪费,提高金属利用率,对环境友好。
然而,浇铸也存在一些缺点。
由于需要倒入熔化的金属,因此对设备要求较高,生产成本也相对较高。
同时,浇铸制品表面质量可能稍逊色于其他铸造工艺,需要后续的加工处理,增加了生产周期和成本。
总的来说,浇铸是铸造的一种方法,在金属加工中有着重要的地位和作用。
通过浇铸工艺,可以制造出各种形状、大小和复杂度的金属制品,满足不同行业的需求。
同时,随着科技的发展和工艺的改进,浇铸工艺也在不断创新与完善,为金属加工领域的发展做出了重要贡献。
1。
重力铸造的原理

重力铸造的原理一、什么是重力铸造重力铸造(Gravity Casting)是一种常用的铸造工艺,利用重力作用将熔融金属注入铸型中,实现铸件的制造。
相比于其他铸造方法,重力铸造具有工艺简单、产品质量高等优点,广泛应用于汽车、航空航天、机械制造等行业。
二、重力铸造的原理重力铸造的原理是利用重力作用使熔融金属顺利流动,并填充整个铸型中的空腔。
具体的原理如下:1. 重力作用重力是物体沿斜面或垂直方向运动的推力,其大小与物体质量成正比。
在重力铸造中,首先需要将熔融金属加热至液态,并保持一定的流动性。
然后,通过恰当设计的铸型和铸造工艺,使熔融金属在重力作用下顺利流动,填充整个铸型中的空腔。
2. 流动性熔融金属的流动性是实现重力铸造的关键因素之一。
流动性受到熔融金属的黏度、表面张力等多种因素的影响。
为了提高流动性,可以适当调整熔融金属的温度、合金成分和添加剂等。
3. 铸型设计铸型的设计对于重力铸造的成功至关重要。
合理的铸型设计可以保证熔融金属在重力作用下均匀流动,避免铸件内部出现气孔、夹渣等缺陷。
铸型的形状、尺寸和壁厚等要素需要根据具体铸件的要求进行调整,以保证铸件的质量。
4. 浇注系统浇注系统是指将熔融金属引导至铸型中的一系列通道和构件。
浇注系统要求合理布局,以减小熔融金属在流动过程中的阻力和波动,确保熔融金属能够顺利地流动到各个空腔中。
三、重力铸造的工艺步骤重力铸造的工艺步骤通常包括准备工作、铸型制作、熔炼、铸造和后处理等阶段。
具体步骤如下:1. 准备工作包括准备熔炼炉、熔炼材料和铸型原料等。
熔炼炉要求能够提供足够高的温度和合适的保温能力,以确保熔融金属的质量。
熔炼材料一般为金属锭或废旧铸件等。
铸型原料包括砂型、金属模具等。
2. 铸型制作根据铸件的形状和尺寸,制作相应的铸型。
常用的铸型制作方法有砂型铸造、金属模具铸造等。
制作完成后,还需要进行铸型的烘干和预热,以提高铸件的表面质量。
3. 熔炼将熔炼材料放入熔炼炉中,加热至熔点以上,使其融化成熔融金属。
铸件的浇注方法

铸件的浇注方法铸件的浇注方法多种多样,今天我们来说一说。
铸件的浇注方法按照金属液流动的动力来源来分可分为重力浇注和反重力浇注。
一般情况下,采取的都是重力浇注。
所谓重力浇注,指的就是金属液流动的动能来自金属液的重力势能。
也就是说,将金属液提高到一定位置,然后让金属液流进模壳或者模型里,金属液的重力势能转换为金属液流动的动能。
一个简单的判定方法就是,金属液位置比模型或者模壳高。
金属液从一个较低的位置流向较高位置,而反重力浇注则是动能变动能再变势能,判定方法就是金属液低,而模型高。
按照浇注方式的具体情况可分为:挑壳浇注,转包浇注,反转浇注,真空浇注,负压吸铸,离心浇注,低压铸造等,下面一一介绍。
挑壳浇注,主要是应用于小件钢件。
模壳从焙烧炉中取出,快速将模壳的浇口杯与中频炉流口对接,然后倾动炉体,使金属液快速进入模壳中。
由于金属液直接进入模壳,所以,金属液氧化较少,而且热损失少,可避免冷隔、浇不足、夹杂等缺陷。
但是,对炉台人员操作要求高,挑壳工必须与炉台默契配合。
属于重力浇注。
转包浇注,主要是应用于稍微大的产品或者炉台水平一般的情况。
这也是常用的一种浇注方法。
炉台将金属液倒至浇包中,然后浇注工将金属液浇注进模壳中。
由于金属液与大气接触时间较长,金属液氧化严重,热量损失大,但是,相对挑壳浇注比较容易,对炉台人员要求低。
不足之处还有易产生夹杂,冷隔,浇不足等缺陷。
属于重力浇注。
翻转浇注,主要是将模壳固定在炉体上,然后慢慢翻转炉体,金属液在重力作用下平稳流入模壳中。
由于金属液流动平稳,不产生紊流,因此,铸件基本没有气孔,没有夹杂等缺陷,但是,必须使用专用设备。
也是重力浇注的一种。
真空浇注,就是金属液在真空状态下熔化,浇注。
所谓真空,也是相对而言。
在真空情况下,由于合金的蒸汽压变小,所以,金属的熔点相对降低,而且,金属液流动阻力变小,流动性提高。
金属液与大气接触少,氧化较少,很少产生夹杂,气孔,浇不足,冷隔等缺陷。
重力铸造
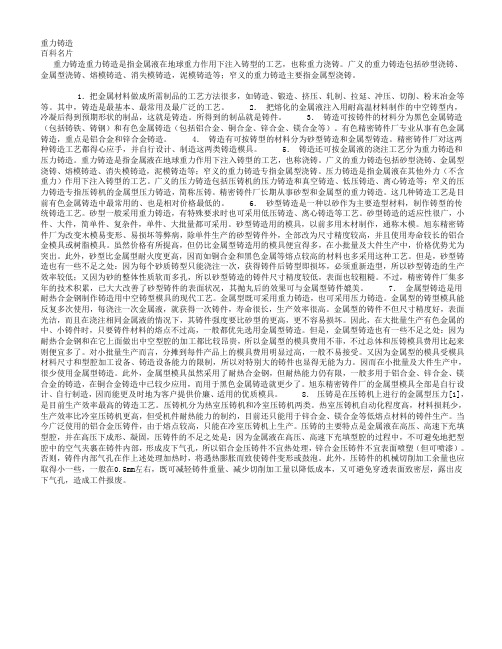
重力铸造百科名片重力铸造重力铸造是指金属液在地球重力作用下注入铸型的工艺,也称重力浇铸。
广义的重力铸造包括砂型浇铸、金属型浇铸、熔模铸造、消失模铸造,泥模铸造等;窄义的重力铸造主要指金属型浇铸。
1.把金属材料做成所需制品的工艺方法很多,如铸造、锻造、挤压、轧制、拉延、冲压、切削、粉末冶金等等。
其中,铸造是最基本、最常用及最广泛的工艺。
2.把熔化的金属液注入用耐高温材料制作的中空铸型内,冷凝后得到预期形状的制品,这就是铸造。
所得到的制品就是铸件。
3.铸造可按铸件的材料分为黑色金属铸造(包括铸铁、铸钢)和有色金属铸造(包括铝合金、铜合金、锌合金、镁合金等)。
有色精密铸件厂专业从事有色金属铸造,重点是铝合金和锌合金铸造。
4.铸造有可按铸型的材料分为砂型铸造和金属型铸造。
精密铸件厂对这两种铸造工艺都得心应手,并自行设计、制造这两类铸造模具。
5.铸造还可按金属液的浇注工艺分为重力铸造和压力铸造。
重力铸造是指金属液在地球重力作用下注入铸型的工艺,也称浇铸。
广义的重力铸造包括砂型浇铸、金属型浇铸、熔模铸造、消失模铸造,泥模铸造等;窄义的重力铸造专指金属型浇铸。
压力铸造是指金属液在其他外力(不含重力)作用下注入铸型的工艺。
广义的压力铸造包括压铸机的压力铸造和真空铸造、低压铸造、离心铸造等;窄义的压力铸造专指压铸机的金属型压力铸造,简称压铸。
精密铸件厂长期从事砂型和金属型的重力铸造。
这几种铸造工艺是目前有色金属铸造中最常用的、也是相对价格最低的。
6.砂型铸造是一种以砂作为主要造型材料,制作铸型的传统铸造工艺。
砂型一般采用重力铸造,有特殊要求时也可采用低压铸造、离心铸造等工艺。
砂型铸造的适应性很广,小件、大件,简单件、复杂件,单件、大批量都可采用。
砂型铸造用的模具,以前多用木材制作,通称木模。
旭东精密铸件厂为改变木模易变形、易损坏等弊病,除单件生产的砂型铸件外,全部改为尺寸精度较高,并且使用寿命较长的铝合金模具或树脂模具。
重力浇铸冒口设计原则
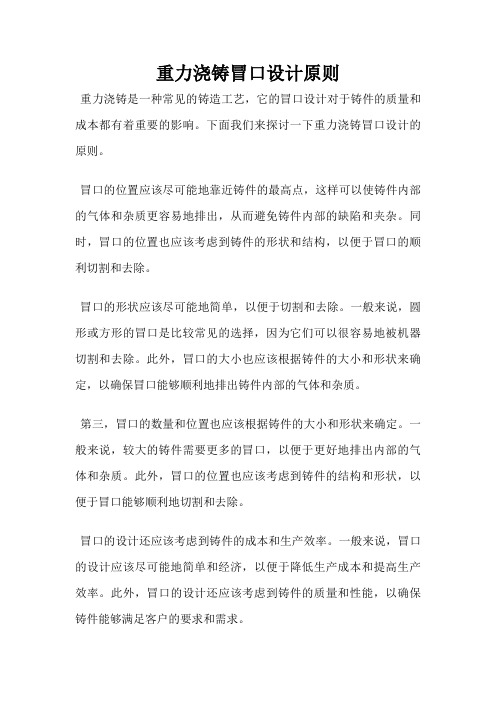
重力浇铸冒口设计原则
重力浇铸是一种常见的铸造工艺,它的冒口设计对于铸件的质量和成本都有着重要的影响。
下面我们来探讨一下重力浇铸冒口设计的原则。
冒口的位置应该尽可能地靠近铸件的最高点,这样可以使铸件内部的气体和杂质更容易地排出,从而避免铸件内部的缺陷和夹杂。
同时,冒口的位置也应该考虑到铸件的形状和结构,以便于冒口的顺利切割和去除。
冒口的形状应该尽可能地简单,以便于切割和去除。
一般来说,圆形或方形的冒口是比较常见的选择,因为它们可以很容易地被机器切割和去除。
此外,冒口的大小也应该根据铸件的大小和形状来确定,以确保冒口能够顺利地排出铸件内部的气体和杂质。
第三,冒口的数量和位置也应该根据铸件的大小和形状来确定。
一般来说,较大的铸件需要更多的冒口,以便于更好地排出内部的气体和杂质。
此外,冒口的位置也应该考虑到铸件的结构和形状,以便于冒口能够顺利地切割和去除。
冒口的设计还应该考虑到铸件的成本和生产效率。
一般来说,冒口的设计应该尽可能地简单和经济,以便于降低生产成本和提高生产效率。
此外,冒口的设计还应该考虑到铸件的质量和性能,以确保铸件能够满足客户的要求和需求。
重力浇铸冒口设计是铸造工艺中非常重要的一环,它的设计原则应该考虑到铸件的形状、结构、大小、成本和生产效率等多个方面。
只有合理地设计冒口,才能够保证铸件的质量和性能,从而满足客户的要求和需求。
重力浇铸机工作原理

重力浇铸机工作原理一、引言重力浇铸机是一种常见的铸造设备,用于制造各种金属零件。
它的工作原理是利用重力作用将熔化金属倒入模具中,通过自由流动充填模腔,然后冷却凝固形成所需的铸件。
本文将详细介绍重力浇铸机的工作原理及其关键步骤。
二、重力浇铸机的工作原理重力浇铸机的工作原理基于重力作用。
首先,将金属材料(一般为铝合金或铜合金)加热至熔化状态,并保持在一定的温度范围内。
然后,将熔化金属倒入浇注系统中的储熔炉中。
在浇注过程中,重力起着至关重要的作用。
借助于重力的作用,熔融金属会自由流动并充填整个模腔。
而不同于其他浇铸方法,如压力浇铸或真空浇铸,重力浇铸不需要额外施加压力或抽气,只需依靠金属液体自身的重力作用即可实现充填。
三、重力浇铸机的关键步骤1. 模具准备在进行重力浇铸之前,需要准备好合适的模具。
模具通常由两个或多个部分组成,包括上模和下模。
上模和下模之间形成的空腔即为模腔,用于充填熔化金属。
2. 模具预热为了确保熔化金属能够均匀地流动并填充整个模腔,模具需要进行预热。
预热温度通常根据具体金属材料的熔点和浇注温度来确定。
3. 熔炼金属将所需的金属材料加入到浇注系统中的储熔炉中,并通过加热使其熔化。
熔化温度取决于具体的金属材料。
4. 浇注过程当熔化金属达到适当的温度后,打开储熔炉的出口,使金属液体开始流动。
由于重力的作用,金属液体会自由流动并充填模腔。
5. 冷却凝固一旦金属液体充填完成,需要等待一定的时间,让金属材料冷却并凝固。
冷却时间取决于具体的金属材料以及所需的铸件尺寸和形状。
6. 取出铸件当金属材料完全冷却凝固后,可以将模具打开,并取出已成型的铸件。
铸件经过后续的处理(如去除余温、抛光等)后,即可得到最终的产品。
四、总结重力浇铸机是一种利用重力作用进行铸造的设备。
它通过将熔化金属倒入模具中,依靠重力使金属液体自由流动并充填整个模腔,然后冷却凝固形成铸件。
重力浇铸机的工作原理简单且可靠,适用于制造各种金属零件。
铝合金重力浇铸与高压铸造
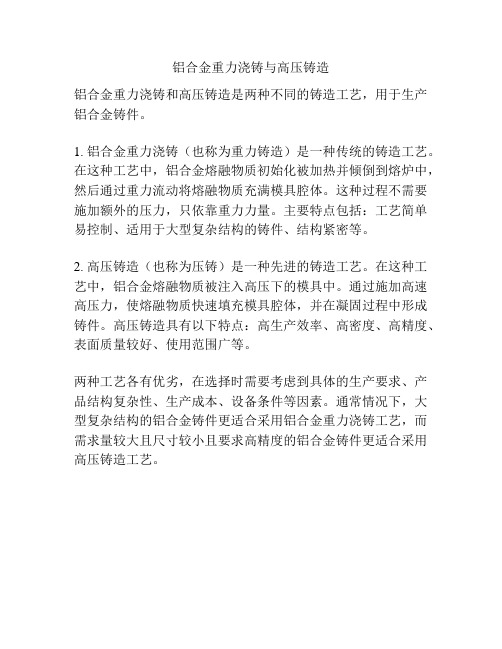
铝合金重力浇铸与高压铸造
铝合金重力浇铸和高压铸造是两种不同的铸造工艺,用于生产铝合金铸件。
1. 铝合金重力浇铸(也称为重力铸造)是一种传统的铸造工艺。
在这种工艺中,铝合金熔融物质初始化被加热并倾倒到熔炉中,然后通过重力流动将熔融物质充满模具腔体。
这种过程不需要施加额外的压力,只依靠重力力量。
主要特点包括:工艺简单易控制、适用于大型复杂结构的铸件、结构紧密等。
2. 高压铸造(也称为压铸)是一种先进的铸造工艺。
在这种工艺中,铝合金熔融物质被注入高压下的模具中。
通过施加高速高压力,使熔融物质快速填充模具腔体,并在凝固过程中形成铸件。
高压铸造具有以下特点:高生产效率、高密度、高精度、表面质量较好、使用范围广等。
两种工艺各有优劣,在选择时需要考虑到具体的生产要求、产品结构复杂性、生产成本、设备条件等因素。
通常情况下,大型复杂结构的铝合金铸件更适合采用铝合金重力浇铸工艺,而需求量较大且尺寸较小且要求高精度的铝合金铸件更适合采用高压铸造工艺。
铝合金重力铸造浇注工艺
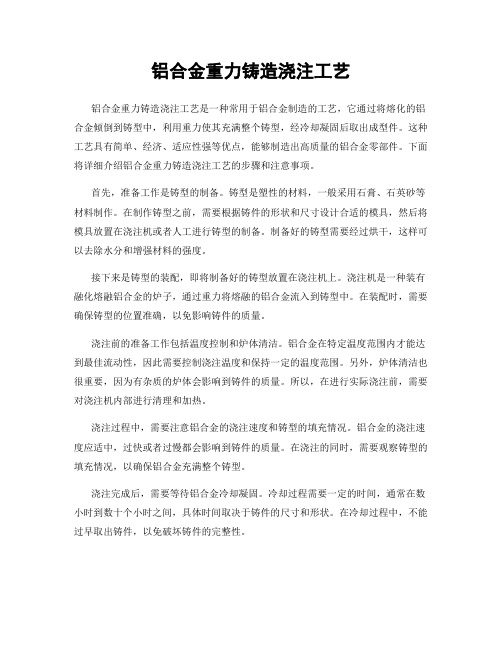
铝合金重力铸造浇注工艺铝合金重力铸造浇注工艺是一种常用于铝合金制造的工艺,它通过将熔化的铝合金倾倒到铸型中,利用重力使其充满整个铸型,经冷却凝固后取出成型件。
这种工艺具有简单、经济、适应性强等优点,能够制造出高质量的铝合金零部件。
下面将详细介绍铝合金重力铸造浇注工艺的步骤和注意事项。
首先,准备工作是铸型的制备。
铸型是塑性的材料,一般采用石膏、石英砂等材料制作。
在制作铸型之前,需要根据铸件的形状和尺寸设计合适的模具,然后将模具放置在浇注机或者人工进行铸型的制备。
制备好的铸型需要经过烘干,这样可以去除水分和增强材料的强度。
接下来是铸型的装配,即将制备好的铸型放置在浇注机上。
浇注机是一种装有融化熔融铝合金的炉子,通过重力将熔融的铝合金流入到铸型中。
在装配时,需要确保铸型的位置准确,以免影响铸件的质量。
浇注前的准备工作包括温度控制和炉体清洁。
铝合金在特定温度范围内才能达到最佳流动性,因此需要控制浇注温度和保持一定的温度范围。
另外,炉体清洁也很重要,因为有杂质的炉体会影响到铸件的质量。
所以,在进行实际浇注前,需要对浇注机内部进行清理和加热。
浇注过程中,需要注意铝合金的浇注速度和铸型的填充情况。
铝合金的浇注速度应适中,过快或者过慢都会影响到铸件的质量。
在浇注的同时,需要观察铸型的填充情况,以确保铝合金充满整个铸型。
浇注完成后,需要等待铝合金冷却凝固。
冷却过程需要一定的时间,通常在数小时到数十个小时之间,具体时间取决于铸件的尺寸和形状。
在冷却过程中,不能过早取出铸件,以免破坏铸件的完整性。
最后是取出成型件。
冷却凝固完成后,铝合金变得坚固,可以取出成型件。
在取出时,需要小心操作,避免损坏铸件。
有时候会通过切割、抛光等后续加工步骤来进一步提高铸件的精度和表面质量。
铝合金重力铸造浇注工艺具有许多优点。
首先,它是一种简单、成本低廉的工艺,不需要复杂的设备和技术。
其次,铝合金重力铸造浇注工艺适用于各种形状和尺寸的铝合金零部件制造,具有很大的适应性。
铝合金重力铸造对策
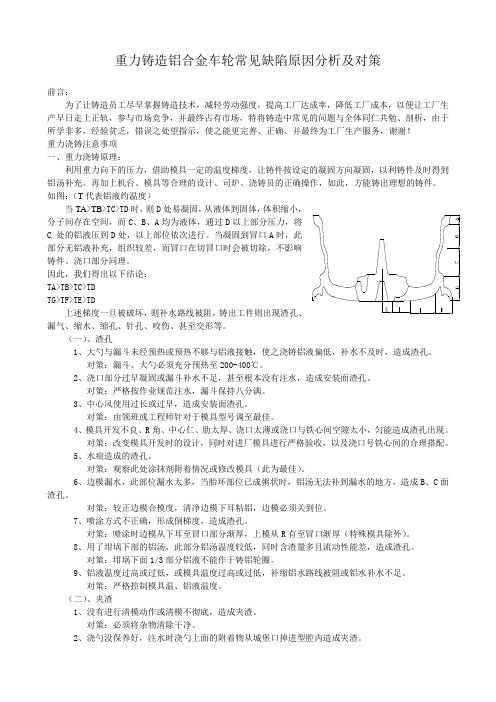
重力铸造铝合金车轮常见缺陷原因分析及对策前言:为了让铸造员工尽早掌握铸造技术,减轻劳动强度,提高工厂达成率,降低工厂成本,以便让工厂生产早日走上正轨,参与市场竞争,并最终占有市场,特将铸造中常见的问题与全体同仁共勉、剖析,由于所学非多,经验贫乏,错误之处望指示,使之能更完善、正确、并最终为工厂生产服务,谢谢!重力浇铸注意事项一、重力浇铸原理:利用重力向下的压力,借助模具一定的温度梯度,让铸件按设定的凝固方向凝固,以利铸件及时得到铝汤补充。
再加上机台、模具等合理的设计、司炉、浇铸员的正确操作,如此,方能铸出理想的铸件。
如图:(T代表铝液约温度)当TA>TB>TC>TD时,则D处易凝固,从液体到固体,体积缩小,分子间存在空间,而C、B、A均为液体,通过D以上部分压力,将C 处的铝液压到D处,以上部位依次进行。
当凝固到冒口A时,此部分无铝液补充,组织较差,而冒口在切冒口时会被切除,不影响铸件。
浇口部分同理。
因此,我们得出以下结论:TA>TB>TC>TDTG>TF>TE>TD上述梯度一旦被破坏,则补水路线被阻,铸出工件则出现渣孔、漏气、缩水、缩孔、针孔、咬伤、甚至交形等。
(一)、渣孔1、大勺与漏斗未经预热或预热不够与铝液接触,使之浇铸铝液偏低,补水不及时,造成渣孔。
对策:漏斗、大勺必须充分预热至200-400℃。
2、浇口部分过早凝固或漏斗补水不足,甚至根本没有注水,造成安装面渣孔。
对策:严格按作业规范注水,漏斗保持八分满。
3、中心风使用过长或过早,造成安装面渣孔。
对策:由领班或工程师针对于模具型号调至最佳。
4、模具开发不良、R角、中心仁、肋太厚、浇口太薄或浇口与铁心间空隙太小,匀能造成渣孔出现。
对策:改变模具开发时的设计,同时对进厂模具进行严格验收,以及浇口号铁心间的合理搭配。
5、水痕造成的渣孔。
对策:观察此处涂抹剂附着情况或修改模具(此为最佳)。
6、边模漏水,此部位漏水太多,当胎环部位已成粥状时,铝汤无法补到漏水的地方,造成B、C面渣孔。
铝合金重力铸造工艺

铝合金重力铸造工艺铝合金是一种轻质、高强度、耐腐蚀的金属材料,广泛应用于航空、汽车、电子、建筑等领域。
而铝合金重力铸造浇注工艺是一种常用的铝合金制造工艺,本文将对其进行详细介绍。
一、铝合金重力铸造浇注工艺的原理铝合金重力铸造浇注工艺是利用重力作用将熔融的铝合金液体倒入铸型中,通过冷却凝固形成所需的铝合金零件。
该工艺的原理是利用铝合金液体的密度差异,使其在铸型中自然流动,从而实现铝合金零件的制造。
二、铝合金重力铸造浇注工艺的优点1. 生产效率高:铝合金重力铸造浇注工艺可以实现大批量生产,生产效率高。
2. 零件质量好:铝合金重力铸造浇注工艺可以制造出高精度、高质量的铝合金零件,具有良好的机械性能和耐腐蚀性能。
3. 工艺简单:铝合金重力铸造浇注工艺相对于其他铝合金制造工艺来说,工艺简单,操作容易,不需要复杂的设备和技术。
4. 节约成本:铝合金重力铸造浇注工艺可以节约成本,因为其生产效率高,可以实现大规模生产,从而降低生产成本。
三、铝合金重力铸造浇注工艺的缺点1. 铸件尺寸受限:铝合金重力铸造浇注工艺的铸件尺寸受限,无法制造过大或过小的铝合金零件。
2. 铸件表面粗糙:铝合金重力铸造浇注工艺的铸件表面粗糙,需要进行后续的加工处理。
3. 铸件内部缺陷:铝合金重力铸造浇注工艺的铸件内部可能存在气孔、夹杂等缺陷,需要进行后续的检测和修补。
四、铝合金重力铸造浇注工艺的应用铝合金重力铸造浇注工艺广泛应用于航空、汽车、电子、建筑等领域。
例如,航空领域中的飞机发动机零件、汽车领域中的发动机缸体、电子领域中的散热器等都可以采用铝合金重力铸造浇注工艺进行制造。
五、铝合金重力铸造浇注工艺的发展趋势随着科技的不断进步,铝合金重力铸造浇注工艺也在不断发展。
未来,铝合金重力铸造浇注工艺将更加注重环保、节能、高效的特点,同时也将更加注重铸件的质量和精度,以满足不断提高的市场需求。
铝合金重力铸造浇注工艺是一种常用的铝合金制造工艺,具有生产效率高、零件质量好、工艺简单、节约成本等优点。
浇铸成型方法有哪几种
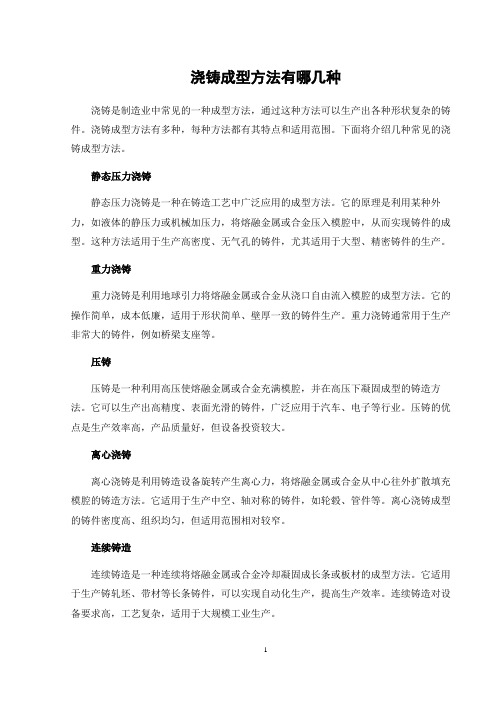
浇铸成型方法有哪几种浇铸是制造业中常见的一种成型方法,通过这种方法可以生产出各种形状复杂的铸件。
浇铸成型方法有多种,每种方法都有其特点和适用范围。
下面将介绍几种常见的浇铸成型方法。
静态压力浇铸静态压力浇铸是一种在铸造工艺中广泛应用的成型方法。
它的原理是利用某种外力,如液体的静压力或机械加压力,将熔融金属或合金压入模腔中,从而实现铸件的成型。
这种方法适用于生产高密度、无气孔的铸件,尤其适用于大型、精密铸件的生产。
重力浇铸重力浇铸是利用地球引力将熔融金属或合金从浇口自由流入模腔的成型方法。
它的操作简单,成本低廉,适用于形状简单、壁厚一致的铸件生产。
重力浇铸通常用于生产非常大的铸件,例如桥梁支座等。
压铸压铸是一种利用高压使熔融金属或合金充满模腔,并在高压下凝固成型的铸造方法。
它可以生产出高精度、表面光滑的铸件,广泛应用于汽车、电子等行业。
压铸的优点是生产效率高,产品质量好,但设备投资较大。
离心浇铸离心浇铸是利用铸造设备旋转产生离心力,将熔融金属或合金从中心往外扩散填充模腔的铸造方法。
它适用于生产中空、轴对称的铸件,如轮毂、管件等。
离心浇铸成型的铸件密度高、组织均匀,但适用范围相对较窄。
连续铸造连续铸造是一种连续将熔融金属或合金冷却凝固成长条或板材的成型方法。
它适用于生产铸轧坯、带材等长条铸件,可以实现自动化生产,提高生产效率。
连续铸造对设备要求高,工艺复杂,适用于大规模工业生产。
以上是几种常见的浇铸成型方法,每种方法都有其独特的优势和适用范围。
在实际生产中,根据具体的铸件要求和生产条件选择合适的浇铸成型方法至关重要,可以有效提高生产效率和产品质量。
铝合金重力铸造浇注工艺

铝合金重力铸造浇注工艺铝合金重力铸造是一种常见的铝合金铸造工艺,其优点包括制造成本低、加工性能好、耐腐蚀性能优异等。
在铝合金重力铸造浇注工艺中,铸型内热液金属通过重力作用,从浇注口进入模腔,填充整个铸型,最终形成所需的铸件。
以下是相关参考内容,分为四个部分进行说明。
1. 铝合金重力铸造工艺的基本原理:- 浇注温度:铝合金浇注温度是铝液和模腔之间的接触温度,决定了铝液充填铸型的时间和温度。
- 流动速度:铝液在铸型中的流动速度会直接影响铸件的成形质量,太快会导致气体夹杂和缺陷,太慢则会使铸件有孔隙。
- 液体表面张力:液体与气体和固体界面处产生的接触角,直接影响液体在铸型中的流动性能。
- 浇注过程:铝合金的重力铸造浇注可以分为铸型充填、冷凝固化和铸型脱模三个阶段。
2. 铝合金重力铸造工艺的主要工艺参数:- 浇注温度:一般情况下,浇注温度稍高于铝合金固化温度,可根据铸造钢型的形态和凝固性能进行调整。
- 浇注速度:决定了铝液在铸型中的流动速度,一般较低速度有利于减少气体夹杂和提高铸件质量。
- 浇注压力:通过设置铝液头部的高度差,调整铝液在铸型中的流动压力,控制铸件中的缺陷和气孔。
- 浇注时间:一般通过控制浇注的时间来调整铸件中的冷缩和应力分布,以防止铸件出现表皮裂纹等缺陷。
3. 铝合金重力铸造工艺的工装设计:- 浇注系统设计:包括浇注杯、导流装置和浇注通道等,用于引导铝液从浇注杯顺利流入铸型。
- 温度控制:通过在浇注系统中加设温度探针、温度传感器等设备,实时监控铝液的温度,确保浇注温度的稳定性。
- 模具设计:根据铸件的形状、尺寸和结构要求,设计模具的冷却系统,保证铸件能够均匀冷却并快速凝固。
4. 铝合金重力铸造工艺的缺陷控制方法:- 气孔控制:通过优化浇注系统设计、减小铝液的冷凝压力,降低气泡在铸件中的聚集程度,减少气孔的产生。
- 热裂缝控制:合理设计模具的冷却系统,控制铸件的冷缩差异,减少内部应力累积,从而减少热裂缝的产生。
重力浇铸与压铸的区别
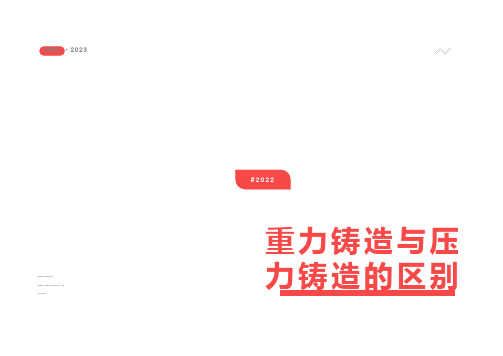
高压铸造
压力铸造分为高压铸造和低压铸造两种。 高压铸造是一种将熔融合金液倒入压室内,以高速充填钢制 模具的型腔,并使合金液在压力下凝固而形成铸件的铸造方 法。 高压压铸区别于其它铸造方法的主要特点是高压和高速。
1. 金属液是在压力下填充型腔的,并在更高的压力下结晶凝 固,常见的压力为15—100MPa。
Page: 8
工艺 模具费用 模具寿命 气孔率 热处理 加工余量 表面光洁 适宜产品 生产效率
高压铸造 复杂
高
低压铸造 简单
低
重力浇铸 简单
低
短
差
不可
小
长
好
可以
大
长
好
可以
大
高
薄壁件
高
高
中
中
低
厚壁件
低
在强度方面,由于所事宜的铝合金原材料不同,其强度差异也较大: 压铸产品由于在高压下成型,产品致密性高,其强度较高。比如A380的压铸产品,其强度 可达到360MPa,而其延伸率只能达到3.7%左右。 重力浇铸产品一般情况强度要较压铸低。其材料较好的ZL101A,热处理后也只能达到有 310MPa,但其延伸率较高,能达到5-6%。也有强度能达到380MPa以上的材料,如 ZL201A、ZL204A。 由上可知,我们在选择产品采用何种工艺生产的时候,主要根据产品的壁厚选择: 由于高压铸造生产效率极高,在生产工艺和产品性能下能满足要求的前提下,应首选高压铸 造。 而产品壁厚大于8mm时,高压铸造的产品可能会由于内部气孔太多而使产品强度不能达到 预期要求,可考虑选择重力浇铸或低压铸造。
导致产品强度降低。 八.模具成本高,模具寿命小。
Page: 6
低压铸造
重力铸造工艺

1,砂芯无强度,易断芯 2,易掉砂,易砂眼 1,密封处缺料漏水 2,影响出水量(缺陷在水道处), 3妨 碍加工(缺陷在阀芯,水嘴等需加 工出) 4,增加成本(消耗铜) 1,断芯 2,偏心,铸件壁厚不匀
清理不良(毛刺未刮干 净,表面凹坑)
铸造篇——浇不满原因
原因分析:
1、铜水温度过低 2、浇铸工艺不当 4、铜材成份不良,导致流动性差 5、模具温度偏低、铸件壁厚太薄,铜液过早凝固
铸造篇——浇不满改善
解决办法:
1、提高浇铸温度(控制在1000℃—1010℃之间);
2、增加进浇口横截面; 3、平稳流注,严禁中途中断 4、改善铜材晶体结构组织(高温熔炼,作精炼细化处理) 5、适当调整铜材成份结构(注意控制Cu 58.5%-61.0%、 Zn 37%-39%、Al 0.6%-0.7%等含量) 6、提高或控制模具温度 6、清理模具,避免因氧化物堵塞浇道 7、改善浇铸工艺,如增大流量,缩小预浇时间等
按主加元素(如Sn、Al,Be等)命名为锡青铜、铝青铜、铍青铜,并以Q+主添元 素化学符号及百分含量表示,如QSn6.5-0.1为6.5%Sn、0.1%P、余为铜的锡磷青铜。 QA15为5%A1、余为铜的铝青铜。QBe2为2%Be、余下为铜的铍青铜。
浇铸篇——初识hpb-591
H59密度:/cm-3 线膨胀系数:21*10-6K-1 热导率:125.60W.m-1K-1 电导率:0.062*10-6Ω.m 电阻温度系数:-1 黄铜
注 意 事 项
1,原砂应充分干燥,因为砂中的水分加热后 会 破坏树脂膜,影响粘结强度 2,砂温不宜过低(15-30度),过低降低树脂粘 度,不宜混匀 3,砂温不宜过高,加速反应,存放性差
重力铸造基础理论
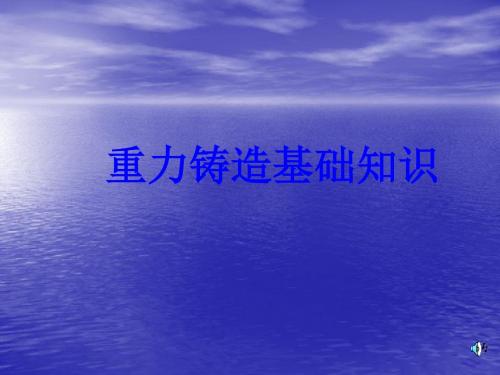
什么是重力铸造?
用铁、钢或其它金属型材料作铸型,在重力 作用下,将熔融的金属注入铸型而获得铸件的工 艺方法称之为重力铸造。
原因分析: 1、浇铸温度过低 2、操作技能不熟练 3、铜材晶体组织结构粗大,流动性差 4、铜材成份控制不达标,某些元素偏高或偏低
5、模具温度偏低、铸件壁厚太薄,铜液过早凝固
三、砂眼、掉砂(铸造过程中大面积或 孤立掉至重力模型腔的型砂或杂物) 哪些因素会影响砂眼、掉砂? 1、砂芯强度不够,投芯合模过程中受震动自表面开始 剥落的型砂 2、砂芯强度不够,投芯合模后在金属液(铜水)高温冲 击作用下自表面开始剥落的型砂 3、投芯过程中未彻底清除型砂残留在型腔内 4、砂芯与重力模间隙配合不当,在合模过程中因碰撞、 摩擦而引起的掉砂(砂芯定位尺寸大于重力模定位尺寸) 5、在高温作用挥发下,因浸涂液不纯含有杂质(砂粒、 氧化渣在模具型腔而聚结的附着物
十三、其它
其它难以明确区分或生产过程出现的一 些不良缺陷要结合生产实际、因地制宜作出 理论上的分析、实践的总结、过程的控制及 工艺上的改善
重力铸造对模具的两点基本要求
1、倾斜注入 2、一定要刷(浸)涂
2
2
挥洒智慧的汗水
铸造闪亮的人生
到此结束!
再见!
抽芯及产品结构过渡处R角,消除应力集中,利于铸件 自由收缩 合理设计铸件的壁厚,改善铸件的凝固条件,提高铸 件的力学性能及机械性能 改善砂芯制作的工艺(参数),降低砂芯的膨胀系数 改善金属材料晶体组织结构,对金属液进行细化处理 (高温重熔或精炼细化) 设置专门的补缩系统,对缩料位置进行补缩 放大收缩余量,迫使缩料位置移位,然后对其进行加 工去除
369
铸件的冷隔与接痕
现场产品的缺陷
重力浇铸铝合金

重力浇铸铝合金1. 引言重力浇铸是一种常用的铸造方法,广泛应用于铝合金的生产中。
本文将介绍重力浇铸铝合金的原理、工艺流程、设备和优缺点。
2. 原理重力浇铸是利用重力作用将熔融金属倒入铸型中进行凝固成形的一种铸造方法。
在重力浇铸过程中,通过控制熔融金属的流动速度和方向,可实现较好的凝固结构和性能。
3. 工艺流程重力浇铸铝合金的工艺流程主要包括:准备工作、熔炼和调温、浇注、冷却和清理。
3.1 准备工作准备工作包括设计和制造模具、选取合适的合金材料、清洁模具等。
模具设计应考虑到产品形状、尺寸和结构要求,以确保最终产品质量。
3.2 熔炼和调温在进行重力浇铸前,需要将所需的铝合金材料进行熔炼和调温。
这一步骤的目的是确保熔融金属的温度和成分符合要求,以获得理想的凝固结构和性能。
3.3 浇注浇注是将熔融金属倒入模具中的过程。
在浇注过程中,需要控制浇注速度、倾斜角度和浇注位置,以避免气体夹杂和其他缺陷的产生。
3.4 冷却在浇注完成后,需要等待铝合金凝固冷却。
冷却时间一般根据铝合金的厚度来确定,以确保产品内部结构稳定,并避免热应力引起的裂纹。
3.5 清理清理是将凝固后的铝合金产品从模具中取出,并进行修整、打磨等处理。
清理过程中需要注意保护产品表面,避免划伤或损坏。
4. 设备重力浇铸铝合金需要一些特定的设备来实现。
常见的设备包括:•熔炼炉:用于将铝合金材料加热至熔化温度。
•浇注设备:用于将熔融金属倒入模具中,控制浇注速度和方向。
•模具:用于定型铝合金,可根据产品要求进行设计和制造。
•冷却设备:用于加速铝合金的凝固冷却过程。
5. 优缺点重力浇铸铝合金具有以下优点:•成本低:相比其他铸造方法,重力浇铸的设备和工艺要求相对简单,成本较低。
•产品质量好:重力浇铸能够获得较好的凝固结构和性能,产品质量稳定可靠。
•生产效率高:重力浇铸可以批量生产,提高生产效率。
然而,重力浇铸也存在一些缺点:•限制形状复杂度:由于熔融金属是通过重力流动进行浇注的,因此对于形状复杂的产品来说,可能无法完全填充模具空腔。
重力铸造的优缺点

重力铸造的优缺点重力铸造是一种常见的铸造技术,它利用重力的作用将熔融金属或合金浇注至模具中进行成型。
与其他铸造技术相比,重力铸造具有独特的优缺点。
本文将分析重力铸造的优缺点。
优点1. 产品质量高重力铸造可以消除熔融金属或合金在浇注过程中受到的紊流和气泡的影响。
因此,重力铸造的成品通常比其他铸造工艺生产的产品质量更高,具有优异的力学性能和表面质量。
另外,重力铸造得到的产品可以在加工前无需进行改善处理,这可以节省时间和成本。
2. 生产效率高重力铸造不需要高昂的模具和设备成本。
简单的模具可以重复使用,并且可以在较短的时间内完成生产。
由于不需要进行额外的加工处理,重力铸造可以显著提高生产效率。
3. 可适应于不同的材料重力铸造适用于近乎所有的金属或合金材料。
可以铸造铁、铝、钢、黄铜等材料,还可以铸造合金材料,如钛合金、镍基合金、铝合金等。
这种灵活性使得重力铸造成为制造各种零部件和元件的理想工艺。
4. 可以减少废品率在其他铸造工艺中,气泡和缺陷可能会导致废品率高。
然而,在重力铸造过程中,皮砂材料的表面张力可以消除气泡和缺陷,从而显著减少废品率。
缺点1. 设备成本高相对于其他铸造工艺,重力铸造所需的设备和设施成本较高。
重力铸造机器的制造和运行成本可能超过数百万美元,因此,运营商需要对这种工艺的长期可行性进行仔细评估。
2. 不适合生产大尺寸的产品由于重力铸造使用重力的作用,因此在生产大尺寸的产品时需要更大的模具。
这要求更昂贵的设备和设施,并增加了铸造成本。
因此,在生产非常大的铸件时,重力铸造可能不是最好的选择。
3. 可能存在气孔缺陷虽然使用皮砂材料可以消除气泡,但在模具填充过程中,仍有可能存在孔洞。
这可能导致成品的质量下降,需要使用更昂贵的修理工艺进行处理。
结论总体而言,重力铸造的优缺点在很大程度上取决于铸造的问题和需求以及运营商的要求。
对于小尺寸的中低精度零部件,重力铸造通常是一种经济、快捷、质量高的选择。
但对于大尺寸精密零件,成本和生产效率可能成为制约铸造工艺的关键因素。
重力铸造技术
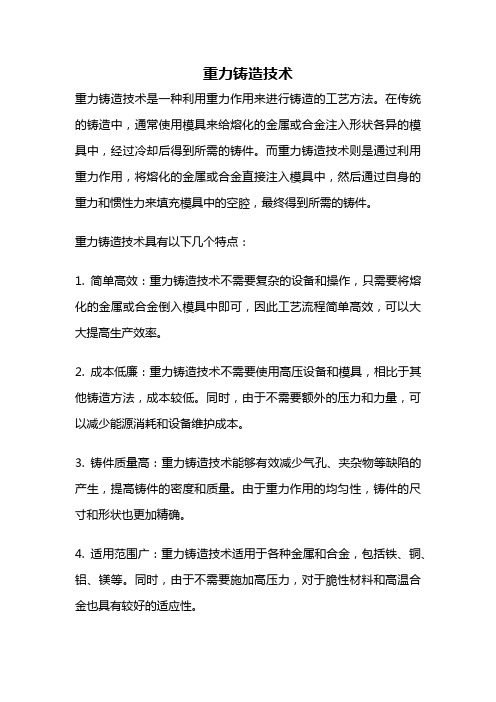
重力铸造技术重力铸造技术是一种利用重力作用来进行铸造的工艺方法。
在传统的铸造中,通常使用模具来给熔化的金属或合金注入形状各异的模具中,经过冷却后得到所需的铸件。
而重力铸造技术则是通过利用重力作用,将熔化的金属或合金直接注入模具中,然后通过自身的重力和惯性力来填充模具中的空腔,最终得到所需的铸件。
重力铸造技术具有以下几个特点:1. 简单高效:重力铸造技术不需要复杂的设备和操作,只需要将熔化的金属或合金倒入模具中即可,因此工艺流程简单高效,可以大大提高生产效率。
2. 成本低廉:重力铸造技术不需要使用高压设备和模具,相比于其他铸造方法,成本较低。
同时,由于不需要额外的压力和力量,可以减少能源消耗和设备维护成本。
3. 铸件质量高:重力铸造技术能够有效减少气孔、夹杂物等缺陷的产生,提高铸件的密度和质量。
由于重力作用的均匀性,铸件的尺寸和形状也更加精确。
4. 适用范围广:重力铸造技术适用于各种金属和合金,包括铁、铜、铝、镁等。
同时,由于不需要施加高压力,对于脆性材料和高温合金也具有较好的适应性。
重力铸造技术在工业生产中有着广泛的应用。
例如,在汽车制造业中,重力铸造技术可以用来生产发动机缸体、曲轴箱等关键零部件。
在航空航天领域,重力铸造技术能够制造轻量化的航空零部件,提高飞行器的性能和燃油效率。
在能源行业中,重力铸造技术可以制造燃气轮机叶片、核电设备等重要组件。
然而,重力铸造技术也存在一些局限性。
首先,重力铸造技术对于复杂形状和细小结构的铸件制造相对困难,需要根据具体情况进行工艺优化和模具设计。
其次,重力铸造技术在填充过程中容易产生气孔和夹杂物,需要通过改善金属液流动性和温度控制等手段进行缺陷控制。
此外,重力铸造技术的生产效率相对较低,不适用于大批量生产。
为了克服重力铸造技术的局限性,还可以与其他工艺方法结合使用。
例如,在重力铸造的基础上引入压力或振动,可以进一步提高铸件的致密度和表面质量。
另外,结合先进的数值模拟和仿真技术,可以优化重力铸造的工艺参数和模具设计,提高生产效率和产品质量。