液压元件清洁度控制通用工艺规程
液压元件清洁度控制通用工艺规程
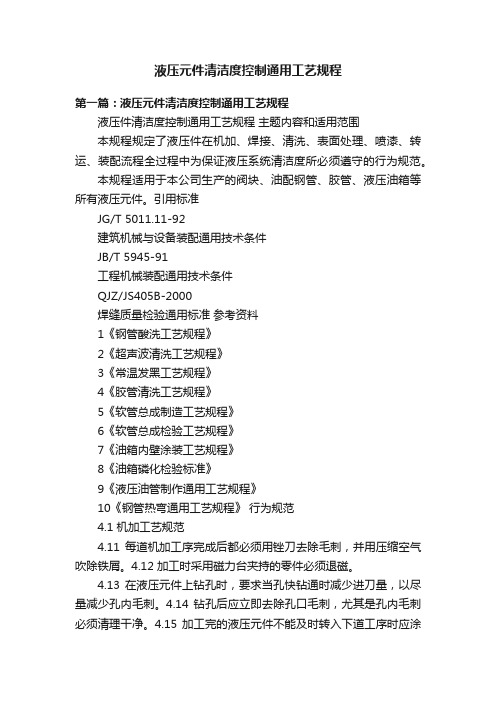
液压元件清洁度控制通用工艺规程第一篇:液压元件清洁度控制通用工艺规程液压件清洁度控制通用工艺规程主题内容和适用范围本规程规定了液压件在机加、焊接、清洗、表面处理、喷漆、转运、装配流程全过程中为保证液压系统清洁度所必须遵守的行为规范。
本规程适用于本公司生产的阀块、油配钢管、胶管、液压油箱等所有液压元件。
引用标准JG/T 5011.11-92建筑机械与设备装配通用技术条件JB/T 5945-91工程机械装配通用技术条件QJZ/JS405B-2000焊缝质量检验通用标准参考资料1《钢管酸洗工艺规程》2《超声波清洗工艺规程》3《常温发黑工艺规程》4《胶管清洗工艺规程》5《软管总成制造工艺规程》6《软管总成检验工艺规程》7《油箱内壁涂装工艺规程》8《油箱磷化检验标准》9《液压油管制作通用工艺规程》10《钢管热弯通用工艺规程》行为规范4.1 机加工艺规范4.11 每道机加工序完成后都必须用锉刀去除毛刺,并用压缩空气吹除铁屑。
4.12 加工时采用磁力台夹持的零件必须退磁。
4.13 在液压元件上钻孔时,要求当孔快钻通时减少进刀量,以尽量减少孔内毛刺。
4.14 钻孔后应立即去除孔口毛刺,尤其是孔内毛刺必须清理干净。
4.15 加工完的液压元件不能及时转入下道工序时应涂油防锈。
4.2 弯管工艺规范4.2.1 采用灌砂热弯方法弯管时,工件热弯完成后,应彻底清除管内砂粒。
4.3 焊接及配焊工艺规范4.3.1 焊后需清除焊渣、飞溅并打磨焊缝。
4.3.2 对于管接头内侧需施焊的钢管,管内的飞溅焊渣必须清除干净。
4.3.3 焊接前检查接口处应无毛刺,如有,应清除后再焊接。
4.3.4 在钢管中间焊接管接头时,应使用小电流或氩弧焊机施焊,以免烧穿钢管壁而导致熔渣堵塞钢管。
4.3.5在钢管中间钻孔时,要求当孔快钻通时减少进刀量,以尽量减少孔内毛刺。
4.3.6在钢管中间钻孔后应立即去除孔口毛刺,尤其是管内毛刺必须清理干净。
4.3.7 喷漆后的油箱不允许再施焊。
液压件清洗通用工艺规程

• 3.2.6煤油清洗机精洗零件内外表面,冲洗时
间2-4分钟。
• 3.2.7压缩空气吹干(压缩空气须干燥处理,
压力0.6-0.8MPa)。
• 3.2.8各接口防尘保护。
• 3.3阀块的清理
• 3.3.1清除阀块零件内外表面异物,吹干。
• 3.3.2用锉刀、钢丝刷等工具将零件各孔道、
沟槽、倒角及其它各处毛刺、锈斑去除干净。
• 3.6.2拆装后的零件直接进入精洗槽清洗。 • 3.6.3清洗后的零件应及时组装,以免二次污
染。
• 3.6.4拆装、清洗和装配过程中应小心谨慎,
以免碰伤、划伤零件。
• 3.6.5清洗,组装后的液压元件如不能马上进
入下道工序,则应进行适当的防尘保护。
• 3.6.6手动阀用专用接头接高压煤油进行清洗。 • 3.7密封件的清理 • 各种密封件都必须在精洗槽进行清洗,并用
• 1目的 • 保证液压零件及管件装配过程中的清洁度。 • 2范围
• 本规程规定了所有液压零件清洗过程的基本
工艺方法。
• 3几种常用液压零件清洗 • 3.1油箱内表面的处理按混凝土泵系列产品
的相关工艺文件执行。
• 3.2液压硬管表面处理及清洗:
• 3.2.1外圆表面用锉刀、钢丝刷等工具将零
件的毛刺、锈斑去除干净。
• 3.3.7防尘保护。
• 3.4接头等自制零件的清理: • 3.4.1用锉刀、钢丝刷等工具将零件各孔道、
沟槽、倒角及其它各处毛刺、锈斑去除干净。
• 3.4.2煤油清洗机初洗零件内外各表面,去除
灰尘、颗粒、油污、铁屑等。
3.4.3煤油清洗机精洗零件内外各表面,各 孔道均要清洗到位。
• 3.4.4压缩空气吹干零件(压缩空气压力
浅论液压系统清洁度工艺控制
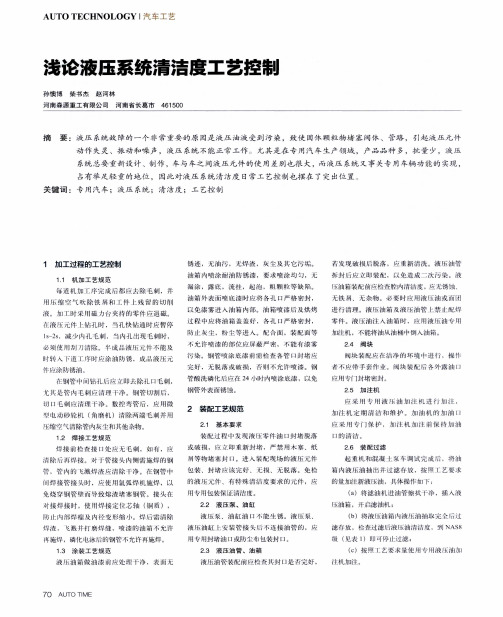
的 垃加 注新液压汕 ,具体操作如下 : ( a )将 滤油帆进 汕 擦拭 十净 ,插 人液 压油箱 ,开启滤油机 ;
( b )将液压汕 辅I ~液 压 油 抽 取 完 全 J , j 过 滤 仔 放 ,检 杏 过 滤 后液 『 J 油 清 洁 度 .Y 0 NAS 8 缴 ( 见表 1 )即 u J . 停I I : 过滤 ; ( c )按 照 I : 艺 要 求 疑使 用 专 液 压 汕 加
缩- C 清除管 灰尘和 他杂物 。
1 _ 2 焊 接 工 艺 规 范 接 前 检 查 接 口 处 应 厄 己 刺 , 如 有 , 应 消 除 再焊 按 。 对 1 管 接
:
,
装 配 过 程 巾 发现 液 压 件 油 【 _ I _ 封 堵 脱 落 或 破 损 ,应 立 即 重 新 封 堵 , 严 禁 用 木 塞 、 纸 等 物堵 塞封 l 】 。 进 入 装 配 现 场 的 液 压 元 什 包装 、 封 堵 应 i 袤完 好 、 损 、 无 脱 落 。 免 检
关键 词 : 专 用 汽 车 ;液 压 系统 ;清 洁 度 ;工 艺控 制
1 加 工过 程的工艺锈 迹,无 油污 ,无焊 淹,灰 尘及 其它 污垢 。
并发现破 损后 脱i ; = ; = ,应 最新 清洗。液 压汕 管 拆封 后应 克 口 J J 装配 ,以 r 见造 成 次 污 染。液 门 i 油箱装配前应榆奄 内清浩度 ,应无锈蚀 、 无铁 屑 、无 杂物 。必 嘤l I I f 应用 液 f t t t 或 面 进 行清理 。液 压油 箱 眨液 压油 管上 禁 【 毗 零 件。液压 油注 人油输 时 ,应 用液 压油 『 = I 1 J J I j E 机 ,不能将油从汕} 甬 中倒入油箱 。
浅论自动变速器液压系统清洁度工艺控制
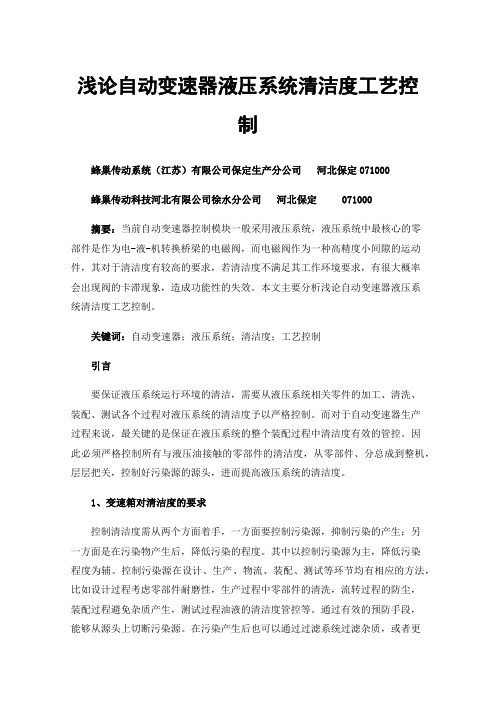
浅论自动变速器液压系统清洁度工艺控制蜂巢传动系统(江苏)有限公司保定生产分公司河北保定071000蜂巢传动科技河北有限公司徐水分公司河北保定071000摘要:当前自动变速器控制模块一般采用液压系统,液压系统中最核心的零部件是作为电-液-机转换桥梁的电磁阀,而电磁阀作为一种高精度小间隙的运动件,其对于清洁度有较高的要求,若清洁度不满足其工作环境要求,有很大概率会出现阀的卡滞现象,造成功能性的失效。
本文主要分析浅论自动变速器液压系统清洁度工艺控制。
关键词:自动变速器;液压系统;清洁度;工艺控制引言要保证液压系统运行环境的清洁,需要从液压系统相关零件的加工、清洗、装配、测试各个过程对液压系统的清洁度予以严格控制。
而对于自动变速器生产过程来说,最关键的是保证在液压系统的整个装配过程中清洁度有效的管控。
因此必须严格控制所有与液压油接触的零部件的清洁度,从零部件、分总成到整机,层层把关,控制好污染源的源头,进而提高液压系统的清洁度。
1、变速箱对清洁度的要求控制清洁度需从两个方面着手,一方面要控制污染源,抑制污染的产生;另一方面是在污染物产生后,降低污染的程度。
其中以控制污染源为主,降低污染程度为辅。
控制污染源在设计、生产、物流、装配、测试等环节均有相应的方法,比如设计过程考虑零部件耐磨性,生产过程中零部件的清洗,流转过程的防尘,装配过程避免杂质产生,测试过程油液的清洁度管控等。
通过有效的预防手段,能够从源头上切断污染源。
在污染产生后也可以通过过滤系统过滤杂质,或者更换清洁油液的方式来控制清洁度。
通过标准化的思维,明确各个环节对清洁度的控制要求及方法。
2、工作原理在对液压传动进行出厂试验之前,使用定量补充装置将传动注入适量的变速器油,并以常规方式加载变速器,如一系列出厂试验。
在工厂测试过程中,还启动了换油功能。
更换机油时,装置自动启动前后油泵,清洁变速器油通过液压变速器入口连续从第一止回阀注入液压变速器。
同时打开管道阀门,通过出口将液压传动中受污染的变速器油从前面的油泵抽入变速器油箱。
液压污染控制技术第4讲液压元件的清洁度控制和系统冲洗
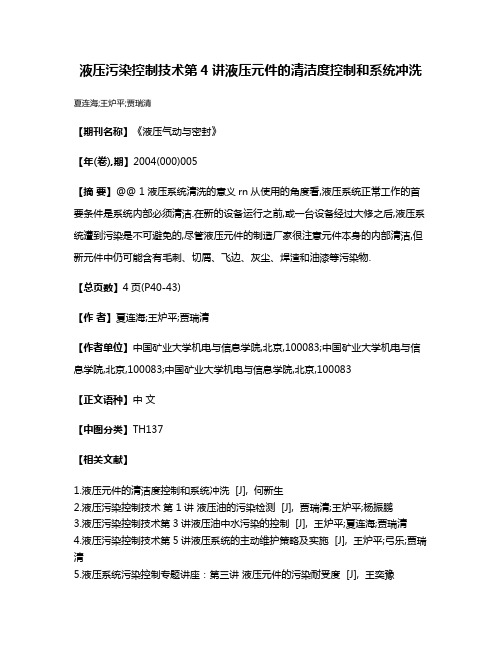
液压污染控制技术第4讲液压元件的清洁度控制和系统冲洗夏连海;王炉平;贾瑞清
【期刊名称】《液压气动与密封》
【年(卷),期】2004(000)005
【摘要】@@ 1液压系统清洗的意义rn从使用的角度看,液压系统正常工作的首要条件是系统内部必须清洁.在新的设备运行之前,或一台设备经过大修之后,液压系统遭到污染是不可避免的,尽管液压元件的制造厂家很注意元件本身的内部清洁,但新元件中仍可能含有毛刺、切屑、飞边、灰尘、焊渣和油漆等污染物.
【总页数】4页(P40-43)
【作者】夏连海;王炉平;贾瑞清
【作者单位】中国矿业大学机电与信息学院,北京,100083;中国矿业大学机电与信息学院,北京,100083;中国矿业大学机电与信息学院,北京,100083
【正文语种】中文
【中图分类】TH137
【相关文献】
1.液压元件的清洁度控制和系统冲洗 [J], 何新生
2.液压污染控制技术第1讲液压油的污染检测 [J], 贾瑞清;王炉平;杨振鹏
3.液压污染控制技术第3讲液压油中水污染的控制 [J], 王炉平;夏连海;贾瑞清
4.液压污染控制技术第5讲液压系统的主动维护策略及实施 [J], 王炉平;弓乐;贾瑞清
5.液压系统污染控制专题讲座:第三讲液压元件的污染耐受度 [J], 王奕豫
因版权原因,仅展示原文概要,查看原文内容请购买。
浅论液压系统清洁度工艺控制
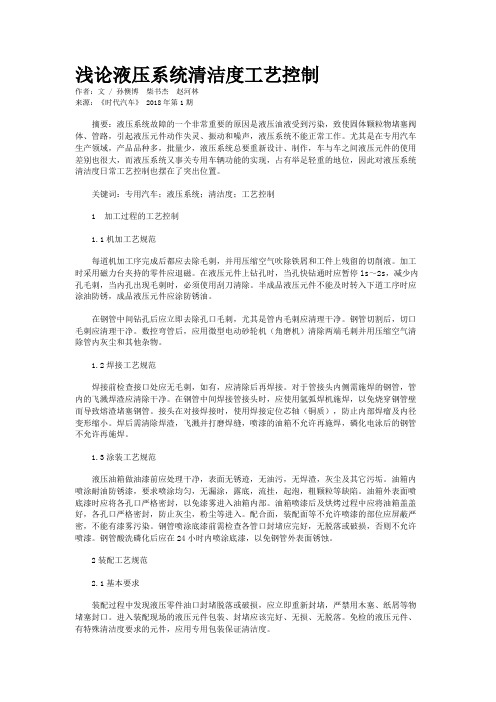
浅论液压系统清洁度工艺控制作者:文 / 孙懊博柴书杰赵河林来源:《时代汽车》 2018年第1期摘要:液压系统故障的一个非常重要的原因是液压油液受到污染,致使固体颗粒物堵塞阀体、管路,引起液压元件动作失灵、振动和噪声,液压系统不能正常工作。
尤其是在专用汽车生产领域,产品品种多,批量少,液压系统总要重新设计、制作,车与车之间液压元件的使用差别也很大,而液压系统又事关专用车辆功能的实现,占有举足轻重的地位,因此对液压系统清洁度日常工艺控制也摆在了突出位置。
关键词:专用汽车;液压系统;清洁度;工艺控制1 加工过程的工艺控制1.1机加工艺规范每道机加工序完成后都应去除毛刺,并用压缩空气吹除铁屑和工件上残留的切削液。
加工时采用磁力台夹持的零件应退磁。
在液压元件上钻孔时,当孔快钻通时应暂停ls~2s,减少内孔毛刺,当内孔出现毛刺时,必须使用刮刀清除。
半成品液压元件不能及时转入下道工序时应涂油防锈,成品液压元件应涂防锈油。
在钢管中间钻孔后应立即去除孔口毛刺,尤其是管内毛刺应清理干净。
钢管切割后,切口毛刺应清理干净。
数控弯管后,应用微型电动砂轮机(角磨机)清除两端毛刺并用压缩空气清除管内灰尘和其他杂物。
1.2焊接工艺规范焊接前检查接口处应无毛刺,如有,应清除后再焊接。
对于管接头内侧需施焊的钢管,管内的飞溅焊渣应清除干净。
在钢管中间焊接管接头时,应使用氩弧焊机施焊,以免烧穿钢管壁而导致熔渣堵塞钢管。
接头在对接焊接时,使用焊接定位芯轴(铜质),防止内部焊瘤及内径变形缩小。
焊后需清除焊渣,飞溅并打磨焊缝,喷漆的油箱不允许再施焊,磷化电泳后的钢管不允许再施焊。
1.3涂装工艺规范液压油箱做油漆前应处理干净,表面无锈迹,无油污,无焊渣,灰尘及其它污垢。
油箱内喷涂耐油防锈漆,要求喷涂均匀,无漏涂,露底,流挂,起泡,粗颗粒等缺陷。
油箱外表面喷底漆时应将各孔口严格密封,以免漆雾进入油箱内部。
油箱喷漆后及烘烤过程中应将油箱盖盖好,各孔口严格密封,防止灰尘,粉尘等进入。
08液压元件清洁度测定法(称重法)
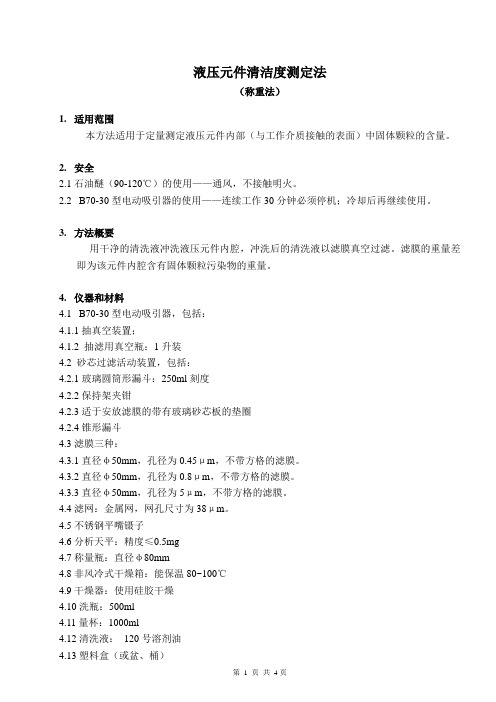
液压元件清洁度测定法(称重法)1.适用范围本方法适用于定量测定液压元件内部(与工作介质接触的表面)中固体颗粒的含量。
2.安全2.1石油醚(90-120℃)的使用——通风,不接触明火。
2.2B70-30型电动吸引器的使用——连续工作30分钟必须停机;冷却后再继续使用。
3.方法概要用干净的清洗液冲洗液压元件内腔,冲洗后的清洗液以滤膜真空过滤。
滤膜的重量差即为该元件内腔含有固体颗粒污染物的重量。
4.仪器和材料4.1B70-30型电动吸引器,包括:4.1.1抽真空装置;4.1.2 抽滤用真空瓶:1升装4.2 砂芯过滤活动装置,包括:4.2.1玻璃圆筒形漏斗:250ml刻度4.2.2保持架夹钳4.2.3适于安放滤膜的带有玻璃砂芯板的垫圈4.2.4锥形漏斗4.3滤膜三种:4.3.1直径φ50mm,孔径为0.45μm,不带方格的滤膜。
4.3.2直径φ50mm,孔径为0.8μm,不带方格的滤膜。
4.3.3直径φ50mm,孔径为5μm,不带方格的滤膜。
4.4滤网:金属网,网孔尺寸为38μm。
4.5不锈钢平嘴镊子4.6分析天平:精度≤0.5mg4.7称量瓶:直径φ80mm4.8非风冷式干燥箱:能保温80~100℃4.9干燥器:使用硅胶干燥4.10洗瓶:500ml4.11量杯:1000ml4.12清洗液:120号溶剂油4.13塑料盒(或盆、桶)第 1 页共4页5. 准备工作5.1用0.45μm滤膜过滤120号溶剂油。
5.2用过滤好的120号溶剂油清洗称量瓶、塑料盆及其它容器。
6. 试验步骤6.1称重:取一张0.8μm滤膜置称量瓶中,半开盖放入干燥箱,经80℃恒温30分钟,合盖取出置干燥器中冷却30分钟,称出其原始重量G1。
6.2清洗:根据被测元件的内腔湿容积(即与油液接触的内腔容积)确定清洗液的用量。
一般为被测元件内腔湿容积的2~5倍。
用过滤后的清洗液油喷洗与工作介质接触的零件表面;重复清洗至少两次。
6.3将已称重的滤膜固定在过滤装置上,充分搅拌待测样品后,倒入过滤漏斗中抽滤;盛过样品的容器都须用溶剂油清洗,洗液一并倒入过滤漏斗中;待抽滤到约5ml余液时,用洗瓶以溶剂油冲洗漏斗壁,继续抽滤直至抽干滤膜。
液压清洁度过程控制的流程

液压清洁度过程控制的流程下载温馨提示:该文档是我店铺精心编制而成,希望大家下载以后,能够帮助大家解决实际的问题。
文档下载后可定制随意修改,请根据实际需要进行相应的调整和使用,谢谢!并且,本店铺为大家提供各种各样类型的实用资料,如教育随笔、日记赏析、句子摘抄、古诗大全、经典美文、话题作文、工作总结、词语解析、文案摘录、其他资料等等,如想了解不同资料格式和写法,敬请关注!Download tips: This document is carefully compiled by theeditor. I hope that after you download them,they can help yousolve practical problems. The document can be customized andmodified after downloading,please adjust and use it according toactual needs, thank you!In addition, our shop provides you with various types ofpractical materials,such as educational essays, diaryappreciation,sentence excerpts,ancient poems,classic articles,topic composition,work summary,word parsing,copy excerpts,other materials and so on,want to know different data formats andwriting methods,please pay attention!液压清洁度过程控制流程。
1. 制定清洁度目标,确定液压系统的目标清洁度等级,根据ISO 4406 标准或其他相关标准。
现场液压系统清洗工艺规程

现场液压系统清洗工艺规程一、清洗的基本要求:1)环境:有条件尽可能在室内进行清洗,如果必须在现场或室外也应避免周围环境有尘土较多的情况下进行清洗。
2)清洗剂:可采用干净的汽油、煤油、柴油等轻质油。
3)容器:清洗应具有清洗的容器,可用脸盆、饭盒等作为容器。
4)擦试布:应采绸布之类不掉纤维的拭布进行擦试。
5)过滤纸:精洗时应把清洗剂进行过滤后再清洗元件或零件,或用多层绸布进行过滤。
6)毛刷:用不易掉毛的毛刷刷洗元件、零件。
二、清洗的方法:1}粗洗:对擦洗的元件、零件、管件应对外面的明显可见脏物进行清洗。
2)半精洗:对元件的内部进行清洗,对元件的阀芯应尽可能的活动清洗。
清洗后应放到干净处,并遮盖好防止再污染。
(注意:放置的元件开口不应朝下,应侧放或向上放置)3)精洗:对清洗剂进行过滤后再对元件、零件进行清洗,清洗后应马上安装。
不易放置。
三、清洗规程1)油箱的清洗油箱是主要囤积脏物的地方,先放出油箱里的油到清洗干净的容器里存放好,然后用清洗油箱。
清洗干净后,用揉好的面(粉)对油箱内部进行粘贴(注意:揉好的面应以表光不粘手为易),粘贴的面不能掉渣,粘贴干净后,应立即封油箱盖。
2)元件、零件等清洗元件、零件应在清洗前取下安装用的密封圈,并将密封圈放置好,以免损伤,然后用清洗剂对元件和零件进行粗洗和半精洗,对特别脏的元件应进行分解清洗(对分解的元件应仔细拆卸,并注意拆卸的顺序,但禁止拆卸复杂元件和比例伺服阀)。
清洗后应检查密封件外表是否有损伤,并对损伤件进行更换,然后安装到元件的原密封位置处。
清洗后的元件和零件能够立刻安装的应立刻安装,不能安装的,应将油口封装好,放置在干净处,待安装。
3)管件清洗拆下的管件清洗时应尽可能采用冲洗的方法,冲洗时的清洗液应进行过滤,清洗后,能安装的尽量先安装,不能安装的也应将管子两端用干净的塑料布封装好,以防止污染物进入管内。
4)油路块的清洗对油路块的油孔,最好采用注射器注射清洗,如无条件,一事实上采用先在油液中涮洗,然后用干净的清洁剂对管中反复涮洗。
工业车辆液压系统清洁度的控制
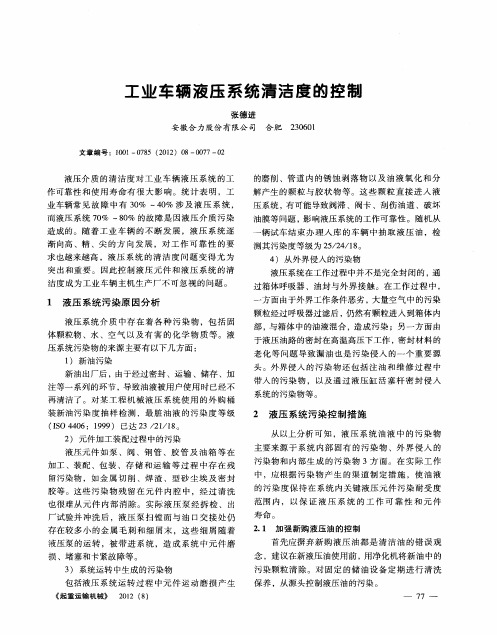
渐 向高 、精 、尖 的 方 向发 展 ,对 工 作 可 靠 性 的要
求也 越来 越高 ,液 压 系 统 的清 洁 度 问 题 变 得 尤 为 突 出和重 要 。因此 控 制 液 压 元 件 和 液 压 系 统 的清 洁 度 成 为工 业 车辆 主 机 生产 厂 不可 忽 视 的 问题 。
清洗 过程 中应 使 泵 作 间歇 运转 ,清 洗 时 间根 据 液
压 系统 的容 量 大小 、所 需 过 滤 精 度 和 液 压 系统 污 染程 度 确定 。查 看 滤 清 器 杂 质 积 聚 情 况 ,清洗 干
般 主机 厂 液 压 系 统 主要 的外 购外 协 元 件 有
泵 、阀 、钢 管 、胶 管 等 ,是 液 压 系 统 的重 要 组 成 部 分 ,其 清 洁 度 对 系 统组 装 后 运转 的可 靠 性 有 直
寿命 。
2 1 加 强新 购液 压油 的控 制 .
首 先应 摒 弃 新 购 液 压 油 都 是 清 洁 油 的 错 误 观
损 、堵塞 和卡 紧故 障等 。
3 系统运 转 中生成 的污染 物 ) 包括 液压 系 统 运 转 过 程 中元 件 运 动 磨 损 产 生
《 起重运输机械》 2 1 ( ) 02 8
而液 压 系统 7 % ~8 % 的故 障是 因液 压介 质 污 染 0 0 造成 的 。随 着 工 业 车 辆 的不 断 发 展 ,液 压 系 统 逐
辆试 车 结 束 办 理 入 库 的车 辆 中抽 取 液 压 油 ,检 4 从外 界侵 入 的污染 物 ) 液 压 系统在 工作过 程 中并不 是完 全封 闭 的 , 通
2 )元 件加工 装配 过程 中 的污染
液压元 件 如 泵 、 阀 、钢 管 、胶 管 及 油 箱 等 在
液压件清洗清洁度检测方法及评定

• 5.2 液压胶管总成必须在规定的曲率半径范
围内工作,应避免急转弯,弯曲半径不得超 过最小允许值,最小允许弯曲半径根据不同 胶管规格确定,推荐弯曲半径R≥(9-10)D (D为软管外径)。并且胶管弯曲时应在大于 其直径1.5倍长度的位置开始弯曲,见图2、图 3所示,同时应装有折弯保护。
• 5.3 采用正确合适的附件及连接件避免液
•
• 3.2 清洁度检测 • 按JJ/38-86标准,用颗粒分析仪(PAMAS-S 按JG/T-5035标准确定清洁度等级。 • 4评定方法 • 4.1规定被清洗件清洁度等级为19/16。 • 4.2按《液压件清洗工艺规程》清洗后的液压
零件清洁度质量指标(清洁度等级)应符合产 品质量《抽样检验规程》之规定。
液压件清洗清洁度检测 方法及评定
• 1范围 • 本标准规定了液压零部件清洗过程中及清洗后,
检测与控制清洁度的方法和程序。
• 本标准在装配厂液压零部件清洗车间试用。 • 2一般要求 • 2.1环境 • 清洗液压零部件应在环境污染受到有效控制的工
作场地进行。
• 2.2 工艺装备 • 用于清洗的工艺装备、工具(清洗机、清洗槽等)应
压胶管总成的附加应力,如直接使用45°或 90°过渡接头或管接头来布置液压胶管。见 图4、图5所示。
• 5评定
• 5.1用3.2清洁度检测方法,若被检验件的清
洁度都达到要求的清洁度等级(19/16),则 经过清洗的液压零件的净化为合格。
• 5.2按3.2方法检验时,如果有一个被检验件
超过了要求的清洁度等级,则应按《抽样检 验规程》选另一批被检验件进行连续检验, 这种改变只进行一次,若仍不合格,此时必 须对清洗液(煤油)清洁度进行检测,若其 清洁度等级超过了要求的清洁度等级 (16/13),则按《清洗机使用管理规定》清 洗或更换滤芯、滤网或换煤油。
液压元件清洁度评定方法及液压元件清洁度指标

液压元件清洁度评定方法及液压元件清洁度指标JB/T7858-19951 主题内容与适用范围本标准规定了以液压元件内部残留污染物重量评定液压元件清洁度的方法以及按液压元件内部污染物许可残留量确定的清洁度指标。
本标准适用于以矿物油为工作介质的各类液压元辅件。
2 定义2.1内腔湿容积:与油液接触的内腔容积。
2.2内腔湿面积:与油液接触的内腔面积。
3 设备和器材3.1滤膜过滤器一套。
3.2混合纤维素酯微孔滤膜若干,直径φ60 mm,孔径0.45 μm、0.8 μm。
3.3真空泵一台。
3.4精度为0.5mg的天平一台。
3. 5 温度保持80℃的非风冷式干燥箱一台。
3. 6 其他用品(抽滤瓶、平嘴镊子、量杯、培养皿、小盒、手动油枪、注射器、白绸布、取样瓶等)。
4 环境和条件4. 1 检测工作室清洁度应达到100000 级(GBS 73《洁净厂房设计规范》),操作者应穿着专用工作服。
4.2被测元件应是完成全部加工、试验工序的元件。
4.3清洁容器应为经过预清洗的取样瓶及其他需用容器,其清洁度不得超出被检测元件清洁度的5%。
4.4清洁清洗液应为经过预过滤的石油醚(沸程60~90℃)或120号工业汽油等溶剂,其清洁度不得超出被检测元件清洁度的10%。
注:推荐用孔径0.45um的微孔滤膜过滤。
5检测程序5.1测量并记录磁性,需要时退磁到12Gs以下。
5.2清洗被测元件的外表面。
5.3确定被测元件的内腔湿容积。
5.4将被测元件解体(工艺螺堵及过盈配合的部件不拆卸)。
5.5取下各结合面的密封件(液压缸活塞密封件除外),用白绸布擦净密封面。
5.6将所有解体后内腔零件放入清洁容器内。
5.7用清洁清洗液喷洗与工作介质接触的零件。
与工作介质部分接触的零件,只清洗零件的接触部分。
不与工作介质接触的零件(如泵的法兰盘、阀的手柄、缸的耳环等)不清洗。
清洁清洗液用量为被测元件内腔湿容积的2~5倍。
5.8将5.7条的冲洗液收集至符合清洁度要求的容器中,并标注容器编号(如1号样)。
液压系统清洁度控制

液压系统清洁度控制方案1、目的规范风机整装过程中油品、液压和润滑系统及整机生产过程中清洁度的控制检验2、适用适用于风机液压油、管类元件、阀类元件、整机液压系统清洁度的检验。
3、职责3.1仓库负责油品及零部件的存储整理、管理与配送。
3.1质保部门负责生产过程中的监督检验。
4、分类目前所有检验中涉及到清洁度检验的主要有:液压油、管类元件、润滑泵、液压站、制动器等液压件。
5、原油的清洁度5.1检测方法:目测法、颗粒法、重量法5.2目测:取油品约200ML倒入透明玻璃瓶中与标准样品(液压油经过颗粒法检测其清洁度为NAS7级)进行比较,根据澄清度初步判定该油品的清洁度是否达标。
5.3颗粒法6、管类元件的清洁度6.1检测方法:观察法6.2观察法:6.2.1液压管及接头的防尘堵头(或防尘螺钉)是否完好。
6.2.2液压管、接头的堵头出现掉落要重新确认其是否清洁。
6.2.3在装配过程中,管、接头的堵头要在装配时才拧下。
6.2.4装配环境是否保持干净。
6.2.5工人要戴干净的手套进行装配。
6.2.6拆卸时,要重新用防尘堵头或防尘螺钉堵好,确保其清洁。
6.2.7润滑接头元件不能裸露,要用自封袋封装。
6.2.8润滑管使用后,用螺栓封堵。
6.2.9物料放在物料架上,并保持清洁卫生7、泵类部件的清洁度控制方案7.1检测方法:观察法7.2观察法:7.2.1润滑泵的进油口、出油口在现场要确保用防尘堵头堵好。
7.2.2润滑泵的油脂严禁做其他润滑用。
8、加注系统清洁度控制方案8.1检验方法:观察法、严格操作8.2措施8.2.1保持滤油车、注脂机表面无浮尘、油污。
8.2.2滤油车裸露在外的油管头要注意防护。
8.2.3滤油车排污口要定期排污:LYC-50滤油车用新油时,每装配25台整机要排污一次;用循环油时,每装配2台整机排污一次。
LYC-4每装配60台整机排污一次。
液压元件的清洁度控制和系统冲洗
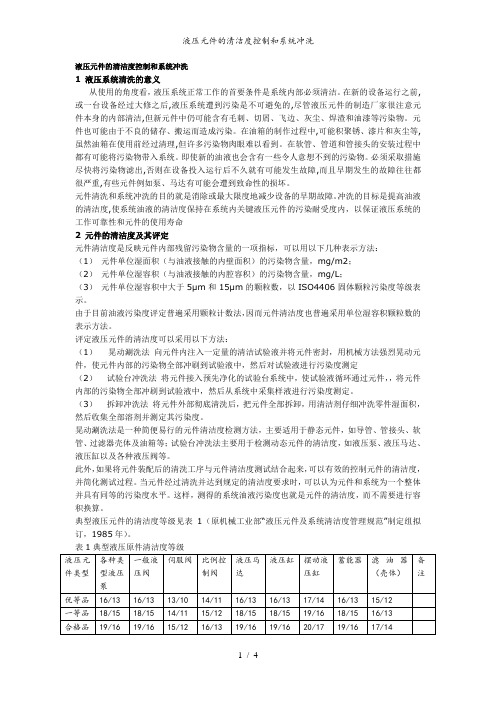
液压元件的清洁度控制和系统冲洗1 液压系统清洗的意义从使用的角度看,液压系统正常工作的首要条件是系统内部必须清洁。
在新的设备运行之前,或一台设备经过大修之后,液压系统遭到污染是不可避免的,尽管液压元件的制造厂家很注意元件本身的内部清洁,但新元件中仍可能含有毛刺、切屑、飞边、灰尘、焊渣和油漆等污染物。
元件也可能由于不良的储存、搬运而造成污染。
在油箱的制作过程中,可能积聚锈、漆片和灰尘等,虽然油箱在使用前经过清理,但许多污染物肉眼难以看到。
在软管、管道和管接头的安装过程中都有可能将污染物带入系统。
即使新的油液也会含有一些令人意想不到的污染物。
必须采取措施尽快将污染物滤出,否则在设备投入运行后不久就有可能发生故障,而且早期发生的故障往往都很严重,有些元件例如泵、马达有可能会遭到致命性的损坏。
元件清洗和系统冲洗的目的就是消除或最大限度地减少设备的早期故障。
冲洗的目标是提高油液的清洁度,使系统油液的清洁度保持在系统内关键液压元件的污染耐受度内,以保证液压系统的工作可靠性和元件的使用寿命2 元件的清洁度及其评定元件清洁度是反映元件内部残留污染物含量的一项指标,可以用以下几种表示方法:(1)元件单位湿面积(与油液接触的内壁面积)的污染物含量,mg/m2;(2)元件单位湿容积(与油液接触的内腔容积)的污染物含量,mg/L;(3)元件单位湿容积中大于5μm和15μm的颗粒数,以ISO4406固体颗粒污染度等级表示。
由于目前油液污染度评定普遍采用颗粒计数法,因而元件清洁度也普遍采用单位湿容积颗粒数的表示方法。
评定液压元件的清洁度可以采用以下方法:(1)晃动涮洗法向元件内注入一定量的清洁试验液并将元件密封,用机械方法强烈晃动元件,使元件内部的污染物全部冲刷到试验液中,然后对试验液进行污染度测定(2)试验台冲洗法将元件接入预先净化的试验台系统中,使试验液循环通过元件,,将元件内部的污染物全部冲刷到试验液中,然后从系统中采集样液进行污染度测定。
液压件清洁度控制规范

液压系统零部件供货、储运、装配过程清洁度控制规范编制:校对:审核:批准:会签:发布日期:实施日期:目录1范围 (1)2规范性引用文件 (1)3零部件的清洁度 (1)3.1软管 (1)3.2钢管 (1)3.3管接头 (2)3.4密封垫圈的清洁度控制 (2)3.5液压油箱的清洁度控制 (3)3.6主要液压件清洁度控制 (3)3.7零部件装配前的检查 (3)4液压件装配过程中的要求 (4)5液压油加注 (4)6整机下线后的液压系统清洁度的控制 (4)液压清洁度常用标准 (5)主要液压元器件清洁度指标 (6)1范围本标准规范了液压零部件供货、储运、装配过程清洁度控制规范。
本规范适用于农业装备产品中液压油、液压油箱、软管、钢管、接头等液压零部件及整机生产过程中液压系统的清洁度的控制。
2规范性引用文件GB/T 14039 液压传动油液固体颗粒污染等级代号(ISO 4006-1999)JB/T 7858 液压元件清洁度评定方法及液压元件清洁度指标3零部件的清洁度液压系统清洁度的控制是一个系统工程,它与液压系统的初期设计水平、零部件加工、储运、装配过程等环节清洁度控制息息相关。
要控制产品液压系统的清洁度,首先必须严格控制与液压系统相关的零部件的清洁度,如软管、钢管、管接头等零部件的清洁度。
否则,零件制造过程中产生的及空气中的灰尘杂物等随着零部件进入液压系统,从而影响液压系统的清洁度,尤其是那些颗粒较大的(大于10μm)的异物,一旦进入,对于液压系统就是毁灭性的。
对该类零部件的控制措施为:所有进入装配现场的油液、油箱、滤油器、软管、钢管、管接头等零部件外露应全部封堵,否则判断为零部件不合格。
3.1 软管所有胶管类零部件外露油口必须有堵盖密封,为防止塑料堵盖在搬运过程中意外掉落,另外要求在胶管接头两端用小塑料袋捆扎牢靠以避免堵盖掉落导致污染物进入胶管内部。
(如:图1)3.2 钢管所有钢管类零部件外露油口必须有堵盖密封,为防止塑料堵盖在搬运过程中意外掉落,另外要求在钢管接头两端用小塑料袋捆扎牢靠以避免堵盖掉落导致污染物进入钢管内部。
液压系统清洁度国家标准
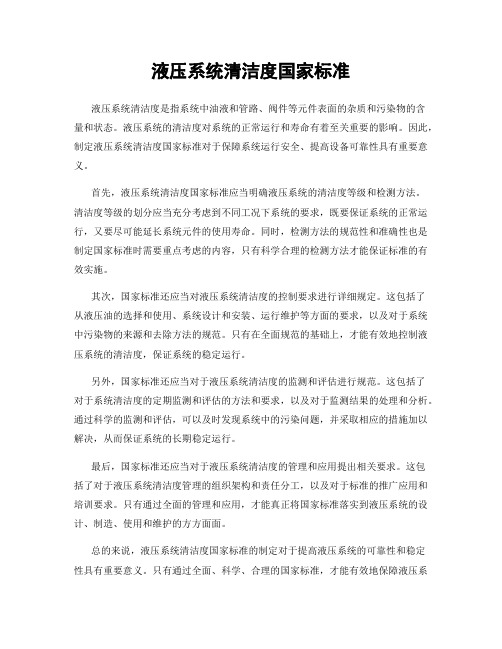
液压系统清洁度国家标准液压系统清洁度是指系统中油液和管路、阀件等元件表面的杂质和污染物的含量和状态。
液压系统的清洁度对系统的正常运行和寿命有着至关重要的影响。
因此,制定液压系统清洁度国家标准对于保障系统运行安全、提高设备可靠性具有重要意义。
首先,液压系统清洁度国家标准应当明确液压系统的清洁度等级和检测方法。
清洁度等级的划分应当充分考虑到不同工况下系统的要求,既要保证系统的正常运行,又要尽可能延长系统元件的使用寿命。
同时,检测方法的规范性和准确性也是制定国家标准时需要重点考虑的内容,只有科学合理的检测方法才能保证标准的有效实施。
其次,国家标准还应当对液压系统清洁度的控制要求进行详细规定。
这包括了从液压油的选择和使用、系统设计和安装、运行维护等方面的要求,以及对于系统中污染物的来源和去除方法的规范。
只有在全面规范的基础上,才能有效地控制液压系统的清洁度,保证系统的稳定运行。
另外,国家标准还应当对于液压系统清洁度的监测和评估进行规范。
这包括了对于系统清洁度的定期监测和评估的方法和要求,以及对于监测结果的处理和分析。
通过科学的监测和评估,可以及时发现系统中的污染问题,并采取相应的措施加以解决,从而保证系统的长期稳定运行。
最后,国家标准还应当对于液压系统清洁度的管理和应用提出相关要求。
这包括了对于液压系统清洁度管理的组织架构和责任分工,以及对于标准的推广应用和培训要求。
只有通过全面的管理和应用,才能真正将国家标准落实到液压系统的设计、制造、使用和维护的方方面面。
总的来说,液压系统清洁度国家标准的制定对于提高液压系统的可靠性和稳定性具有重要意义。
只有通过全面、科学、合理的国家标准,才能有效地保障液压系统的正常运行,提高设备的可靠性,为各行业的发展提供更加可靠的技术支撑。
希望通过不断完善和推广液压系统清洁度国家标准,能够为我国的工程技术发展贡献更大的力量。
液压元件的清洁度控制和系统冲洗
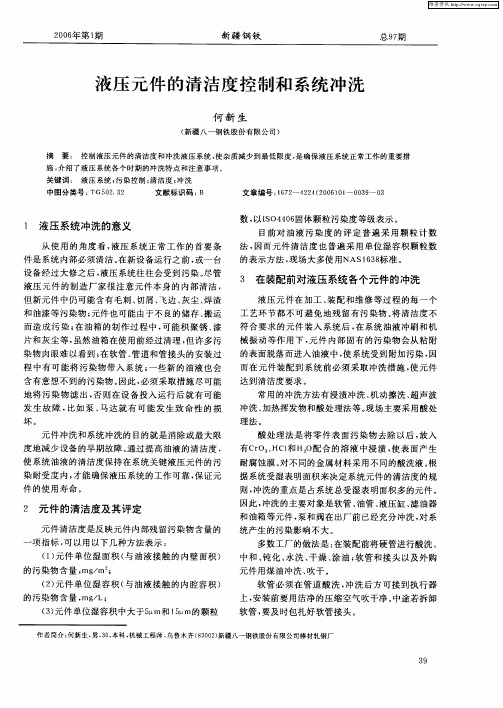
2 元件 的清洁度及其评定
元 件清 洁度 是反映 元件 内部 残 留污 染 物含 量的
一
项 指 标 , 以用 以下几 种 方法表 示 : 可 () 1 元件 单 位 湿面 积 ( 油 液接 触 的 内壁 面积 ) 与
中和 、 化 、 钝 水洗 、 干燥 、 油 ; 涂 软管 和接 头 以及 外 购
坏。
元 件 冲洗 和系统 冲洗 的 目的就是 消除 或最 大 限
酸 处理 法 是 将零 件 表 面 污染 物 去 除 以后 , 放入 有C O 、 I 合 的溶 液 中浸渍 , r 。HC 和H O配 使表 面 产 生 耐腐 蚀膜 。 不 同的金属 材料 采 用不 同的酸洗液 。 对 根
维普资讯
2 0 年第 1 06 期
新 疆 钢 铁
总9 期 7
液 压 元件 的 清Байду номын сангаас 度 控 制 和 系统 冲 洗
何 新 生
( 疆 八 一 钢 铁 股份 有 限公 司 ) 新 摘 要 : 控 制 液 压 元件 的清 洁 度 和 冲 洗 液 压 系 统 , 杂 质 减 少到 最 低 限 度 , 确 保 液 压 系 统 正 常工 作 的重 要 措 使 是
液 压 元件 在 加 工 、 配 和维 修 等过 程 的每 一 个 装 工艺 环 节都 不 可避 免 地 残 留 有污 染物 。 清洁 度 不 将 符合 要 求 的元件 装 入 系 统后 , 系统 油液 冲刷 和 机 在
械 振 动 等作 用 下 , 件 内部 固有 的污染 物 会从 粘 附 元
理法。
染 物 肉眼难 以看 到 ; 软 管 、 在 管道 和管 接头 的 安装过
程 中有 可 能将 污 染 物带 入 系统 ; 一些 新 的 油液 也会 含有意 想 不到 的污染 物 。 因此 , 必须采 取措 施尽 可能 地 将 污 染 物滤 出 , 则 在设 备 投入 运 行后 就 有 可能 否 发 生故 障 , 比如泵 、 达 就 有 可 能发 生 致 命 性 的损 马
液压油箱清洗通用工艺规程

油箱状态检查
检查油箱内部状况
在开始清洗前,应检查液压油箱 内部的状况,了解油泥和杂质的 分布情况,以便制定合理的清洗 计划。
记录油箱状况
在开始清洗前,应对液压油箱内 部的状况进行拍照或录像,以便 后续评估清洗效果和记录。
03 清洗步骤
排空油箱
关闭液压油箱的进油 口和出油口,确保油 箱内的液压油全部排 出。
进一步优化工艺
在现有基础上,进一步研究并优化清洗工艺,提 高清洗效果和效率。
引入智能化技术
探索引入智能化清洗设备和技术,实现自动化、 智能化的液压油箱清洗。
加强清洗后检测
完善清洗后的质量检测标准和方法,确保清洗效 果达到预期目标。
THANKS FOR WATCHING
感谢您的观看
气压测试
01
向油箱内部充入一定压力的气体,观察油箱是否有漏气现象,
以确保油箱的密封性能。
水压测试
02
向油箱内部加入一定压力的水,观察油箱是否有渗漏现象,以
确保油箱的密封性能。
涂抹密封剂
03
在油箱密封处涂抹适量的密封剂,以增强密封效果,防止渗漏。
油箱的维护和保养
01
02
03
定期清洗
根据使用情况定期对油箱 进行清洗,以去除杂质和 沉淀物,保持油箱内部的 清洁。
清洁度标准
根据液压系统的要求和油箱的使用环境,制定清洁度标准,如残留物数量、颗 粒度大小等,以确保油箱在使用过程中不会对液压系统造成不良影响。
油箱性能测试
密封性能
检查油箱密封圈、密封垫等密封元件 的完好性和性能,确保油箱在使用过 程中不会出现渗漏现象。
过滤性能
对油箱内的过滤器进行检查和测试, 确保过滤器能够有效地去除油液中的 杂质和颗粒物,保证油液的清洁度。
液压系统的冲洗技术及冲洗规程

3 收稿日期 981026 3 3 燕山大学机械工程学院液压研究所, 066004 河北省秦 皇岛市
笔者曾同英国同一家公司的技术人员合作, 先后 参加了秦皇岛港务局煤三期、煤四期码头和湖北鄂州
42
液压与气动 1999 年第 3 期
液压系统的冲洗技术及冲洗规程3
吴晓明3 3
摘 要 新设备或经过大修后的设备在投入使用前都需要对其液压系统进行冲洗, 以保证系统正常运 行。根据实际工作经验, 介绍了液压系统的冲洗技术及规程。实践证明有效地冲洗可消除液压系统的早期故 障隐患, 防止液压元件遭到致命性的损坏。
紊流程度的大小由雷诺数决定:
R e=
vd
Τ
(1)
式中 Τ ——运动黏度, m 2 s
d ——管道直径, m
v ——流速, m s
为了确保紊流, R e 应大于 13800。在 2320< R e<
13800 时, 层流、紊流的可能性都存在, 但紊流的情况
居多。雷诺数和冲洗效率之间的关系表明, 普通采用小
关键词 液压系统 冲洗 污染 清洁度
1 引言 在新的设备运行之前, 或一台设备经过大修之后,
液压系统遭到污染是不可避免的, 尽管液压元件的制 造厂家很注意元件本身的内部清洁, 但新元件中仍可 能含有毛刺、切屑、飞边、灰尘、焊渣和油漆等污染物。 元件也可能由于不良的储存、搬运而造成污染。在油箱 的制作过程中, 可能积聚锈、漆片和灰尘等, 虽然油箱 在使用前经过清理, 但许多污染物肉眼难以看到。在软 管、管道和管接头的安装过程中都有可能将污染物带 入系统。 即使新的油液也会含有一些令人意想不到的下几点不足:
液压管路清洁度控制方法

液压管路清洁度控制方法1.引言1.1 概述液压系统作为一种常见的动力传输和控制系统,在工业领域中具有广泛的应用。
液压管路作为该系统的重要组成部分,其清洁度对系统的性能和稳定性起着至关重要的作用。
因此,控制液压管路的清洁度成为了液压系统维护和管理的重要内容之一。
本文将重点探讨液压管路清洁度的控制方法,旨在为液压系统的安全运行和长期稳定性提供有力支持。
1.2 文章结构文章结构部分的内容可以包括对整篇文章的框架和各个章节的内容进行简要介绍。
例如:文章结构部分主要介绍了本篇文章的整体架构和各个章节的内容安排。
本文包括引言、正文和结论三个部分。
引言部分概述了文章的背景和目的,正文部分分为液压管路清洁度的重要性、影响因素和控制方法三个小节,分别探讨了液压管路清洁度的重要性、影响因素以及针对液压管路清洁度的控制方法。
结论部分总结了文章的主要内容,并对其实践意义和未来展望进行了展望。
整体来说,本文将从不同角度深入探讨液压管路清洁度控制方法,为读者提供全面的信息和建议。
1.3 目的目的部分的内容:本文旨在探讨液压管路清洁度控制的方法,以解决液压系统在运行过程中可能发生的污染问题。
通过深入分析清洁度对液压系统性能和寿命的重要影响,旨在为工程师和操作人员提供有效的管路清洁度控制方案,从而确保液压系统的稳定运行和可靠性,提高设备的使用寿命和效率。
同时,希望通过本文的研究,引起行业对液压管路清洁度重视,推动管路清洁度控制技术的进步。
2.正文2.1 液压管路清洁度的重要性液压管路清洁度对于液压系统的正常运行起着至关重要的作用。
首先,液压管路的清洁度直接影响着液压系统的工作效率和性能。
如果管路内存在杂质和污染物,将会导致管路阻塞和摩擦增大,从而使得液压系统的传动效率降低,甚至引起系统泄漏或失效。
其次,液压管路清洁度的不良会使得液压元件的使用寿命大大缩短。
细小的颗粒污染物会造成液压元件的磨损和损坏,例如活塞环、阀芯等部件长时间受到污染物的侵蚀,会导致密封不良、漏油等问题的发生,最终导致液压系统失效。
- 1、下载文档前请自行甄别文档内容的完整性,平台不提供额外的编辑、内容补充、找答案等附加服务。
- 2、"仅部分预览"的文档,不可在线预览部分如存在完整性等问题,可反馈申请退款(可完整预览的文档不适用该条件!)。
- 3、如文档侵犯您的权益,请联系客服反馈,我们会尽快为您处理(人工客服工作时间:9:00-18:30)。
液压件清洁度控制通用工艺规程
1 主题内容和适用范围
本规程规定了液压件在机加、焊接、清洗、表面处理、喷漆、转运、装配流程全过程中为保证液压系统清洁度所必须遵守的行为规范。
本规程适用于本公司生产的阀块、油配钢管、胶管、液压油箱等所有液压元件。
2 引用标准
JG/T 5011.11-92 建筑机械与设备装配通用技术条件
JB/T 5945-91 工程机械装配通用技术条件
焊缝质量检验通用标准QJZ/JS405B-2000
3 参考资料
1《钢管酸洗工艺规程》
2《超声波清洗工艺规程》
3《常温发黑工艺规程》
4《胶管清洗工艺规程》
5《软管总成制造工艺规程》
6《软管总成检验工艺规程》
7《油箱内壁涂装工艺规程》
8《油箱磷化检验标准》
9《液压油管制作通用工艺规程》
10《钢管热弯通用工艺规程》
4 行为规范
4.1 机加工艺规范
4.11 每道机加工序完成后都必须用锉刀去除毛刺,并用压缩空气吹除铁屑。
4.12 加工时采用磁力台夹持的零件必须退磁。
4.13 在液压元件上钻孔时,要求当孔快钻通时减少进刀量,以尽量减少孔内毛刺。
4.14 钻孔后应立即去除孔口毛刺,尤其是孔内毛刺必须清理干净。
4.15 加工完的液压元件不能及时转入下道工序时应涂油防锈。
页4 共页1 第
4.2 弯管工艺规范
4.2.1 采用灌砂热弯方法弯管时,工件热弯完成后,应彻底清除管内砂粒。
4.3 焊接及配焊工艺规范
4.3.1 焊后需清除焊渣、飞溅并打磨焊缝。
4.3.2 对于管接头内侧需施焊的钢管,管内的飞溅焊渣必须清除干净。
4.3.3 焊接前检查接口处应无毛刺,如有,应清除后再焊接。
4.3.4 在钢管中间焊接管接头时,应使用小电流或氩弧焊机施焊,以免烧穿钢管壁而导致熔渣堵塞钢管。
4.3.5在钢管中间钻孔时,要求当孔快钻通时减少进刀量,以尽量减少孔内毛刺。
4.3.6在钢管中间钻孔后应立即去除孔口毛刺,尤其是管内毛刺必须清理干净。
4.3.7 喷漆后的油箱不允许再施焊。
4.3.8 酸洗磷化后的钢管不允许再施焊。
4.4 胶管制作工艺规范
4.4.1 胶管下料应使用专门的胶管切割机,禁止使用一般的砂轮切割机。
4.4.2 胶管下料并剥胶后应彻底除去切口向内50mm范围内的灰垢,铁屑等杂物,用干净白布擦拭应无明显脏物。
4.5 表面处理工艺规范
4.5.1 主阀块等镀镍前必须将阀孔、螺纹孔内铁屑等异物清除干净;镀镍后镀层表面必须清洁,无残渣、灰尘、颗粒及其他污垢。
4.5.2 液压元件常温发黑前除油除锈必须彻底,工件上应无铁屑等异物,无水珠及油垢。
4.5.3 发黑处理后的零件表面及内腔必须清洁,膜层致密完整,无锈迹,内腔无处理液残留物。
4.5.4 液压油箱转酸洗磷化前应将焊渣、飞溅物及严重的锈蚀清除干净。
4.5.5 油箱磷化后磷化膜应致密完整,表面无锈蚀,无油,无溶液残渣。
4.6 油漆工艺规范
4.6.1 液压油箱做油漆前必须处理干净,表面无锈迹、无油污、无焊渣、灰尘及其他污垢。
页4 共页2 第
4.6.2 油箱内腔喷涂耐油防锈漆,要求喷涂均匀,无漏涂、露底、流挂、漆瘤、起泡、粗颗粒等缺陷。
4.6.3 油箱外表面喷底漆时应将各孔口严格密封,以免漆雾进入油箱内部。
4.6.4 油箱喷漆后及烘烤过程中应将油箱盖盖好,各孔口严格密封,防止灰尘、粉尘等进入。
4.6.5 配合面、装配面等不允许喷漆的部位应屏蔽严密,不能有漆雾污染。
4.6.6 钢管喷涂底漆前需检查各管口封堵应完好,无脱落或破损,否则不允许喷漆。
4.7 酸洗工艺规范
4.7.1 每周测试酸液浓度,并按工艺要求补充酸液至上限值。
4.7.2 钢管放入酸洗槽应从一端到另一端逐渐缓慢放入,使钢管尽量全部浸入酸中且一端管口最后入酸。
避免钢管中间弯曲部分最后入酸,以免钢管内残留空气。
4.7.3 水洗槽应使用流动水洗,以便及时排出污物。
零件在水洗槽中放置时间不超过30分钟,以免钢管返锈。
4.7.4 酸洗槽每月倒槽清洗一次;防锈水每月更换一次。
4.7.5 酸洗槽中沉淀物过多时应打开循环泵进行过滤。
4.7.6 检查钢管内壁应无飞溅焊渣,若有,应先除去焊渣后再进行酸洗。
4.7.7 酸洗磷化完成的钢管内外表面应基本干燥,无粘附水珠,用干净白布擦拭钢管内壁,应无明显脏物。
4.7.8 经检验合格的钢管应及时封口,避免灰尘进入。
酸洗完成的钢管未喷涂底漆前不能粘水,以免钢管返锈。
4.7.9
4.8 清洗工艺规范
4.8.1 胶管应用煤油或专门的清洗剂冲洗,且冲洗时间应不少于30秒。
4.8.2 胶管冲洗后内表面应基本吹干,用干净白布擦拭胶管内壁,应无明显脏物。
4.8.3 清洗后的胶管应立即用专用封堵或塑料纸密封管口。
4.8.4 液压阀块清洗前应彻底除去各内孔的毛刺及可能存在的飞溅焊渣。
4.8.5 液压阀块各内孔均应用高压水和压缩空气充分冲洗。
4.8.6 液压阀块清洗后内外表面应基本干燥,且无锈迹、无油污、无粉尘、无铁屑等缺陷,用用磁铁搭上铁丝伸到各内孔中环绕一周后取出,铁丝末端应无铁屑。
4.8.7 阀块装配应在无尘的环境中进行,操作者不允许戴手套作业。
页4 共页3 第
4.8.8 阀块装配后各外露油口应用专用封堵密封,或用塑料纸包裹密封。
4.9 装配工艺规范
4.9.1 在液压泵或液压油缸上安装管接头后,如不立即连接油管,应用专用封堵封口,或用塑料纸包扎封口;严禁用塑料纸、纸屑等物堵塞封口。
4.9.2 液压油管装配前应检查其封口是否完好,若发现破损或脱落,应重新清洗。
4.9.3 若在装配过程中发现液压零件油口封堵脱落或破损,应立即重新封堵,严禁用塑料纸、纸屑等物堵塞封口。
4.9.4 液压油管拆封后应立即装配,以免造成二次污染。
4.9.5 液压油箱装配前应检查腔内清洁度,应无锈蚀、无铁屑、无杂物。
必要时应用煤油或面团进行清理。
4.9.6 液压油箱及油配钢管上禁止配焊零件。
4.9.7 液压油注入油箱时,必须经过过滤,严禁将油从油桶直接倒入油箱。
4.9.8 整机调试后,检验液压油污染等级应不大于8级,并更换相应的过滤芯。
4.10 转运工艺规范
4.10.1 液压件应使用专用转运车及专用存放架,并保持其清洁度。
4.10.2 油配钢管酸洗磷化后应在24小时内喷涂底漆,以免钢管外表面锈蚀。
4.10.3 液压元件转运过程中应注意轻拿轻放,摆放整齐,避免损坏零件及其封口。
4.10.4 磷化后的油箱转运过程中应避免淋雨,以免油箱返锈。
4.10.5 转运及存放时零件不允许着地。
4.10.6在转运过程中发现液压零件油口封堵脱落或破损,应立即重新封堵或重新清洗;严禁用塑料纸、纸屑等物堵塞封口。
页4 共页4 第。