陶瓷磨削液
磨削液

对于缓进给磨削推荐选用下述配方制备磨削液:亚硝酸钠1%,苯甲酸钠0.5%,甘油0.5%,三乙醇胺0.4%,水(其余)。
普通磨削:可采用防锈乳化液或苏打水及合成切削液,简单配方如下。
A:2%防锈乳化液,0.5%亚硝酸纳,0.2%碳酸纳,97.3%水;B:0.8%亚硝酸纳,0.3%碳酸纳,0.5%甘油,98.6%水;C:直接用3%~4%的防锈乳化液或化学合成液D: 硼酸0.2-0.7%,三乙醇胺0.2-0.5%,水余量。
磨削钢、铸铁、铜等有色金属材料时,一般采用苏打水:第一种配方:苏打(碳酸钠):1%;亚硝酸钠:0.25~0.5%;水:其余。
第二种配方:苏打(碳酸钠):0.5%;亚硝酸钠:1~1.2%;甘油:0.5~1%;水:其余。
碳酸钠0.3-0.5 亚钠0.5-0.8 乳化油0.8-1.5碳酸钠1%,亚硝酸钠0.5~0.8%,余量是水.将以上物质加3~4重量的温水搅拌3~5分钟后,再加入剩余重量的水.,在搅拌几分钟即可. 需要注意的是碳酸钠哦不应多于1%,否则对人体皮肤有害.在以后使用过程中水分不断蒸发浓度逐渐变浓,可逐渐加入较低浓度的碳酸钠或清水.磨削液:水+碱+亚硝酸钠100:1:1水溶液:(1)用0.25~0.5%亚硝酸钠+0.25~0.3%无水碳酸钠+水余量。
(2)3%油酸钠皂+0.5%亚硝酸钠+水余量。
(3)10%癸二酸+17.5%三乙醇胺+8%亚硝酸钠+水余量。
切削液的维护切削液要满足冷却、润滑、清洗、防锈四个目的,因此从这四方面着手1.冷却高水基切削液在常规使用状态时的含水量95%以上,磨削时含水量在97%以上;2.润滑水溶性润滑剂(聚乙烯醇、甘油)3.清洗在切削液中采用非离子性表面活性剂(如平平加、太古油)和阴离子表面活性剂(烷基苯磺酸钠、十二烷基硫酸钠)进行复配,能起到显著降低切削液表面张力的作用,达到清洗的目的。
4.防锈水溶性防锈剂品种较多,通常分为有机防锈剂与无机防锈剂两类。
磨削液对陶瓷结合剂CBN砂轮磨削性能影响
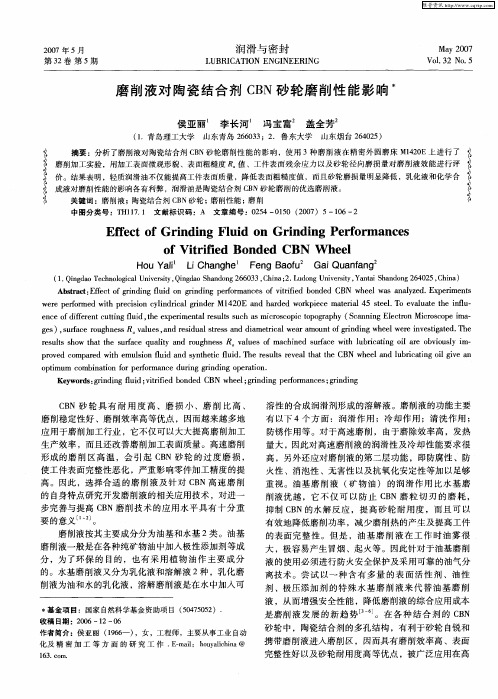
20 07年 5月
润滑 与密封
LUBRI ATI C ON ENGI NEERI NG
Ma 0 7 y2 0
第3 2卷 第 5期
Vo_ 2 No 5 l3 .
磨 削 液对 陶瓷 结合 剂 C N砂 轮 磨 削性 能影 响 B
e c f iee t ut gf i ,h x e me tleut sc s cocpctp ga h S a nn lcrnMirso ei — n eo f rn tn ud teep r na sl u ha rso i orp y( c n igEe t coc p df c i l i r s mi o o ma
p o e o ae t mu so ud a d s nh tcfu d T e r s l e e h tte CBN e la d l b c t g olgv n rv d c mp rd wi e lin f i n y tei i . h e u t rv a t a h h l l s l wh e n u r ai i ie a i n
o t i e n d CBN he l fVirf d Bo de i W e
H uY l L Ch n h F n a f Ga Qu na g o ai i age e g B ou i a fn
( . iga eh o gcl n e i , iga hn og2 63 , hn ;. u ogU i rt, a t hn og24 2 ,hn ) 1Qnd oTc nl ia U i r t Qnd oSa dn 6 0 3 C ia2 L dn nv sy Y na Sa dn 6 0 5 C i o v sy ei i a
磨削机床改善方案

磨削机床改善方案磨削机床是一种用于精密加工的重要设备,可以对各种材料进行高精度的磨削加工。
然而,由于磨削机床长期使用,容易产生磨损,导致加工品质降低,损耗加剧,影响工作效率。
因此,为了提高磨削机床的效率和品质,需要采取一些改善措施。
调整磨削机床的刀具首先,需要对磨削机床的刀具进行调整。
刀具的调整可以优化磨削过程,并确保磨削效果的稳定性。
调整刀具可以通过调节切削深度、切削速度等方式实现。
此外,还可以使用更先进的刀具材料,如钨钢、陶瓷等,以提高磨削效果和寿命。
进行磨削液的优化其次,需要对磨削液进行优化。
磨削液是保证磨削效果稳定的关键因素之一,可以防止磨削过程中产生的高温和磨损。
因此,需要定期更换磨削液,并保证其质量符合标准。
此外,还需根据具体需要选择不同种类的磨削液,以适应不同的磨削材料和精度要求。
定期维护磨削机床另外,还需要定期对磨削机床进行维护。
维护可以保证磨削机床的运行效率和寿命。
具体而言,维护可以包括清洗、润滑、更换磨损部件等方面。
此外,还应该对整个磨削过程进行监测和控制,以实现磨削效果的最大化。
引入先进的自动化技术最后,可考虑引入先进的自动化技术来帮助改善磨削机床的性能和效率。
例如,可以将数字控制技术或机器人技术应用到磨削机床中,以优化加工过程,提高磨削机床的自动化程度和精度。
总之,实现对磨削机床的改善需要多方面的措施。
通过优化刀具、磨削液、定期维护和引入先进自动化技术等方式,可以帮助提高磨削机床的效率和品质,提高磨削的精度和寿命。
陶瓷材料磨削加工的技术研究与发展现状
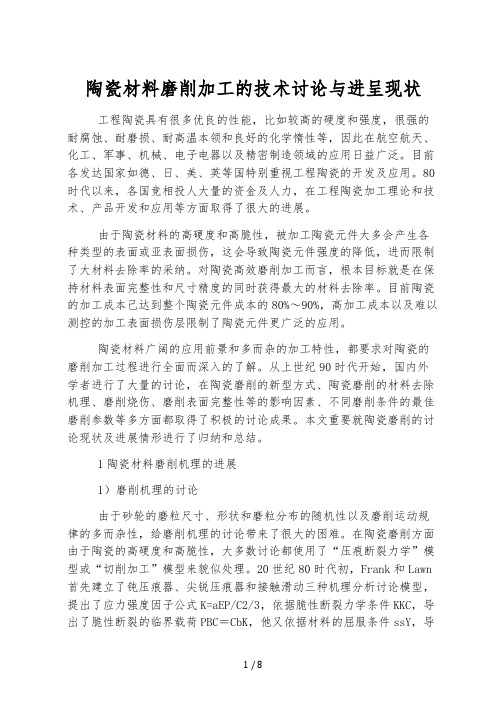
陶瓷材料磨削加工的技术讨论与进呈现状工程陶瓷具有很多优良的性能,比如较高的硬度和强度,很强的耐腐蚀、耐磨损、耐高温本领和良好的化学惰性等,因此在航空航天、化工、军事、机械、电子电器以及精密制造领域的应用日益广泛。
目前各发达国家如德、日、美、英等国特别重视工程陶瓷的开发及应用。
80时代以来,各国竞相投人大量的资金及人力,在工程陶瓷加工理论和技术、产品开发和应用等方面取得了很大的进展。
由于陶瓷材料的高硬度和高脆性,被加工陶瓷元件大多会产生各种类型的表面或亚表面损伤,这会导致陶瓷元件强度的降低,进而限制了大材料去除率的采纳。
对陶瓷高效磨削加工而言,根本目标就是在保持材料表面完整性和尺寸精度的同时获得最大的材料去除率。
目前陶瓷的加工成本己达到整个陶瓷元件成本的80%~90%,高加工成本以及难以测控的加工表面损伤层限制了陶瓷元件更广泛的应用。
陶瓷材料广阔的应用前景和多而杂的加工特性,都要求对陶瓷的磨削加工过程进行全面而深入的了解。
从上世纪90时代开始,国内外学者进行了大量的讨论,在陶瓷磨削的新型方式、陶瓷磨削的材料去除机理、磨削烧伤、磨削表面完整性等的影响因素、不同磨削条件的最佳磨削参数等多方面都取得了积极的讨论成果。
本文重要就陶瓷磨削的讨论现状及进展情形进行了归纳和总结。
1陶瓷材料磨削机理的进展1)磨削机理的讨论由于砂轮的磨粒尺寸、形状和磨粒分布的随机性以及磨削运动规律的多而杂性,给磨削机理的讨论带来了很大的困难。
在陶瓷磨削方面由于陶瓷的高硬度和高脆性,大多数讨论都使用了“压痕断裂力学”模型或“切削加工”模型来貌似处理。
20世纪80时代初,Frank和Lawn 首先建立了钝压痕器、尖锐压痕器和接触滑动三种机理分析讨论模型,提出了应力强度因子公式K=aEP/C2/3,依据脆性断裂力学条件KKC,导出了脆性断裂的临界载荷PBC=CbK,他又依据材料的屈服条件ssY,导出了塑性变形模式下临界载荷PYYC=s3/g3(或PYYC=H3Y/g3)。
常用加工方法及切削液的选用

常用加工方法及切削液的选用1)车削、镗削(1)粗车:粗车时加工余量较大,因而切削深度和进给量都较大,切削阻力大,产生大量切削热,刀具磨损也较严重,主要应选择用以冷却作用为主并具有一定清洗、润滑和防锈作用的水基切削液,将切削热及时带走,降低切削温度,从而提高刀具耐用度,一般选用极压乳化液效果更好。
极压乳化液除冷却性能好之外,还具备良好的极压润滑性,可明显延长刀具使用寿命,提高切削效率,使用水基切削液要注意机床导轨面的保养,下班前要将工作台上的切削液擦干,涂上润滑油。
(2)精车:精车时,切削余量较小,切削深度只有0.05~0.8mm,进给量小,要求保证工件的精度和粗糙度。
精车时由于切削力小,温度不高,所以宜采用高浓度(10%以上)的乳化液和含油性添加剂的切削液为宜。
对于精度要求很高的车削,如精车螺纹,要采用菜籽油、豆油划其他产品作润滑液才能达到精度要求。
正如上面所提到的,由于植物油稳定发差,易氧化,有的工厂采用了精密切削润滑剂全损耗系统用油作为精密切削油,效果很好。
(3)镗削:镗削机理与车削一样,不过它是内孔加工,切削是和切削速度均不大,但散热条件差,可采用乳化液作切削液,使用时应适当增加切削液的流量和压力。
2)铣削:铣削是断续切削,每个刀齿的切削深度时刻变化,容易产生振动和一定和冲击力,所以铣削条件比车削条件差。
用高速刀具高速平铣或高速端铣时,均需要冷却性好,并有一定润滑性能的切却液,如极压乳化液。
在低速铣削时,要求用润滑性好的切削油,如精密切削油和非活性极压油。
对不锈钢和耐热合金钢,可用含硫、氯极压添加剂的切削油。
3)螺纹加工:切削螺纹时,刀具与切削材料成楔形接触,刀刃三面被切削材料所包围,切削力矩大排屑较困难,热量不能及时由切屑带走,刀具容易磨损,切屑碎片挤塞并且容易产生振动。
尤其车螺纹和攻螺纹时切削条件更苛刻,有时会出现崩刃和断丝锥,要求切削液同时具备较低的摩擦系数和较高的极压性,以减少刀具的摩擦阻力和延长刀具使用寿命,一般应选用同时含有油性剂和极压剂的复合切削液。
磨具磨料酚醛树脂-概述说明以及解释

磨具磨料酚醛树脂-概述说明以及解释1.引言1.1 概述磨具磨料酚醛树脂是一种重要的工业材料,广泛应用于各类磨削、研磨、抛光等加工过程中。
它是一种由酚醛树脂为基体,通过添加一定比例的磨料制成的新型复合材料。
酚醛树脂作为一种高性能合成树脂,具有很好的耐磨性、耐高温性、耐化学品侵蚀性和机械强度等优异特性。
而添加的磨料则可以增加材料的磨削能力和磨损耐久性。
在工业制造中,磨具磨料酚醛树脂扮演着重要的角色。
它可以用于金属、石材、陶瓷等材料的磨削和抛光过程,能够提高加工效率、改善表面质量和尺寸精度。
同时,磨具磨料酚醛树脂还广泛应用于制造业的各个领域,如汽车零部件的加工、机械零件的制造、电子元件的加工等。
它的应用范围非常广泛,对于提高产品的加工质量和降低生产成本具有重要意义。
本文将主要介绍磨具磨料酚醛树脂的概念、分类以及特性和应用。
首先,我们将对磨具和磨料酚醛树脂进行概念的解释,并介绍它们的分类和特点。
然后,我们将重点讨论磨料酚醛树脂的特性,包括其耐磨性、耐高温性、耐化学品侵蚀性等。
同时,我们还将探讨磨具磨料酚醛树脂的应用领域,如何在实际生产中发挥优势和应用场景。
最后,我们将总结磨具磨料酚醛树脂的重要性,并展望其未来的发展前景。
通过对磨具磨料酚醛树脂的全面了解和深入研究,我们可以更好地应用这一材料于工业生产中,提高生产效率和产品质量,促进制造业的快速发展。
本文将为读者提供有关磨具磨料酚醛树脂的全面介绍和详细信息,希望能够对相关行业和学术界的研究人员提供有价值的参考和借鉴。
文章结构本文分为引言、正文和结论三个部分。
1. 引言部分1.1 概述在引言部分,将简单介绍磨具磨料酚醛树脂的概念和应用,并指出其在实际生产和加工中的重要性。
1.2 文章结构本文将按照以下结构进行展开:第2部分为正文部分,主要包括磨具的概念和分类以及磨料酚醛树脂的特性和应用。
第3部分为结论部分,总结磨具磨料酚醛树脂的重要性,并展望其未来的发展前景。
陶瓷内孔磨加工方法

陶瓷内孔磨加工方法摘要:一、陶瓷内孔磨加工方法简介二、陶瓷内孔磨加工工艺流程1.预加工2.粗磨3.精磨4.抛光三、陶瓷内孔磨加工注意事项1.选择合适的磨料和磨具2.控制加工过程中的温度和湿度3.保持设备良好状态四、陶瓷内孔磨加工的应用领域1.电子行业2.光学行业3.医疗器械行业正文:陶瓷内孔磨加工方法是一种在陶瓷材料内部进行精密磨削的技术,广泛应用于电子、光学和医疗器械等领域。
陶瓷材料具有高硬度、高熔点、低热导率等特点,因此陶瓷内孔磨加工具有一定的难度。
为了获得高质量的陶瓷内孔,我们需要掌握合适的加工方法和工艺流程。
陶瓷内孔磨加工的工艺流程主要包括预加工、粗磨、精磨和抛光四个步骤。
1.预加工:在进行内孔磨削前,首先要对陶瓷工件进行预加工,去除工件表面的毛刺和污垢,为后续磨削做好准备。
预加工方法包括磨削、铣削、钻孔等。
2.粗磨:粗磨是将陶瓷工件的内孔尺寸加工到接近最终尺寸的阶段。
在这一阶段,需要选用合适的磨料和磨具,根据工件的材质和加工要求进行磨削。
粗磨过程中,要注意控制磨削速度、进给量和磨削液的流量,以保证磨削效果和磨具的寿命。
3.精磨:精磨是将陶瓷工件的内孔尺寸精确到设计要求的阶段。
精磨时,要选用更高精度的磨具和更细的磨料,同时调整加工参数,以提高内孔的加工精度。
4.抛光:抛光是将陶瓷工件内孔表面抛光至光滑、平整的阶段。
抛光过程中,要选用合适的抛光剂和抛光液,并根据工件的表面状况调整抛光参数。
在进行陶瓷内孔磨加工时,还需注意以下事项:1.选择合适的磨料和磨具:根据工件的材质、加工要求和内孔尺寸,选用合适的磨料和磨具,以提高加工效果和效率。
2.控制加工过程中的温度和湿度:陶瓷材料对温度和湿度的敏感性较高,加工过程中要严格控制温度和湿度,以防止工件变形和裂纹。
3.保持设备良好状态:定期检查和维护加工设备,确保设备在良好的工作状态下进行加工。
陶瓷内孔磨加工在电子、光学和医疗器械等行业具有广泛的应用前景。
陶瓷结合剂CBN砂轮的特性
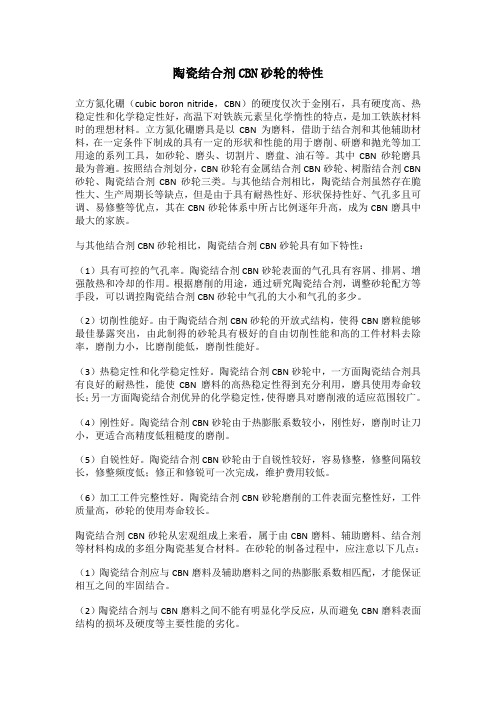
陶瓷结合剂CBN砂轮的特性立方氮化硼(cubic boron nitride,CBN)的硬度仅次于金刚石,具有硬度高、热稳定性和化学稳定性好,高温下对铁族元素呈化学惰性的特点,是加工铁族材料时的理想材料。
立方氮化硼磨具是以CBN为磨料,借助于结合剂和其他辅助材料,在一定条件下制成的具有一定的形状和性能的用于磨削、研磨和抛光等加工用途的系列工具,如砂轮、磨头、切割片、磨盘、油石等。
其中CBN砂轮磨具最为普遍。
按照结合剂划分,CBN砂轮有金属结合剂CBN砂轮、树脂结合剂CBN 砂轮、陶瓷结合剂CBN砂轮三类。
与其他结合剂相比,陶瓷结合剂虽然存在脆性大、生产周期长等缺点,但是由于具有耐热性好、形状保持性好、气孔多且可调、易修整等优点,其在CBN砂轮体系中所占比例逐年升高,成为CBN磨具中最大的家族。
与其他结合剂CBN砂轮相比,陶瓷结合剂CBN砂轮具有如下特性:(1)具有可控的气孔率。
陶瓷结合剂CBN砂轮表面的气孔具有容屑、排屑、增强散热和冷却的作用。
根据磨削的用途,通过研究陶瓷结合剂,调整砂轮配方等手段,可以调控陶瓷结合剂CBN砂轮中气孔的大小和气孔的多少。
(2)切削性能好。
由于陶瓷结合剂CBN砂轮的开放式结构,使得CBN磨粒能够最佳暴露突出,由此制得的砂轮具有极好的自由切削性能和高的工件材料去除率,磨削力小,比磨削能低,磨削性能好。
(3)热稳定性和化学稳定性好。
陶瓷结合剂CBN砂轮中,一方面陶瓷结合剂具有良好的耐热性,能使CBN磨料的高热稳定性得到充分利用,磨具使用寿命较长;另一方面陶瓷结合剂优异的化学稳定性,使得磨具对磨削液的适应范围较广。
(4)刚性好。
陶瓷结合剂CBN砂轮由于热膨胀系数较小,刚性好,磨削时让刀小,更适合高精度低粗糙度的磨削。
(5)自锐性好。
陶瓷结合剂CBN砂轮由于自锐性较好,容易修整,修整间隔较长,修整频度低;修正和修锐可一次完成,维护费用较低。
(6)加工工件完整性好。
陶瓷结合剂CBN砂轮磨削的工件表面完整性好,工件质量高,砂轮的使用寿命较长。
四种常见的磨削方法

四种常见的磨削方法在制造业中,磨削是一种常见且重要的加工方式,它通过磨削材料表面,使其达到所需的形状、尺寸和表面质量。
磨削方法可以分为四种:砂轮磨削、研磨、酸洗和磨削钢。
砂轮磨削是最常见的磨削方法之一,它利用砂轮的旋转磨削能力,对工件表面进行磨削。
砂轮磨削具有设备简单、成本低廉等优点,同时,还可以根据需要对工件进行不同厚度的磨削。
砂轮磨削广泛应用于金属、非金属和陶瓷等材料的磨削加工。
研磨是一种利用研磨剂对工件表面进行研磨的方法。
研磨剂可以是砂浆、液体石蜡等,它可以改变材料的表面性质,提高表面的光洁度。
研磨常用于精密加工、玻璃钢制造等领域。
在研磨过程中,研磨剂的粘度、粒径和分布对研磨效果有着重要的影响。
酸洗是一种通过酸与金属表面的污垢反应,将其清除的方法。
酸洗通常在磨削之前进行,可以有效地提高磨削表面的光洁度。
常见的酸洗方法有盐酸酸洗、硫酸酸洗等。
酸洗广泛应用于机械、电子、航空航天等领域。
磨削钢是一种通过磨削的方式,对钢材料进行加工的方法。
磨削钢通常在研磨或砂轮磨削之后进行,可以有效地提高钢材料的耐腐蚀性、耐磨性和强度。
磨削钢广泛应用于建筑、船舶、汽车等领域。
四种磨削方法在加工过程中具有不同的优缺点。
砂轮磨削具有设备简单、成本低廉等优点,广泛应用于金属、非金属和陶瓷等材料的磨削加工。
研磨可以提高材料的表面光洁度,常用于精密加工、玻璃钢制造等领域。
酸洗可以在磨削之前进行,广泛应用于机械、电子、航空航天等领域。
磨削钢则具有提高钢材料性能的优点,广泛应用于建筑、船舶、汽车等领域。
综上所述,四种磨削方法——砂轮磨削、研磨、酸洗和磨削钢,在磨削加工中发挥着重要作用。
浅谈普通车床加工陶瓷

OCCUPATION1392011 6浅谈普通车床加工陶瓷文/黄建平一、陶瓷在车床上机械加工的必要性陶瓷零件由于成形、烧结工艺的限制,毛坯产品的加工余量较大。
磨床常用于小余量的轻加工,很少用于大余量的切削加工,因为磨床的刚度不适合进行大余量加工。
当砂轮周边的磨粒切入工件表面时,就像许多锤子敲击工件表面一样,使工件表面产生裂纹或凹坑,使主轴产生挠曲变形,且可能引起磨削颤振及反复冲击现象,严重削弱了砂轮的寿命,并可能使其破裂或使工件破裂。
为了减少这种现象,生产中最常用的方法是减少磨削深度和进给量,这又大大降低了生产效率,增加了生产成本。
虽然陶瓷材料的特种加工技术获得了很大的进展,胜任传统常规加工无法完成的加工任务,具有非接触式、不污染工件、没有切削力、热影响小、加工速度快、能加工特殊型面等优点。
但不能加工大面积零件,只能加工小孔或细小部位,而且要求技术高,价格昂贵,成本难以控制。
在普通车床上机械加工陶瓷,工艺简单,加工效率高,操作方便,容易掌握,对工人的技术要求不高,价格实惠,容易推广,同时可达较高的加工精度和低平面粗糙度。
综上所述,普通车床上机械加工能解决许多磨床和新技术的不足等问题,车床车削陶瓷还是很有必要的。
二、陶瓷机械加工机理在陶瓷材料加工的研究中,最复杂的是材料的去除机理。
在陶瓷磨削加工过程中,材料去除主要采用以下几种方法:晶粒去除、剥落、脆性断裂、破碎、晶界微破碎等脆性去除,粉末化去除和塑性去除方式等。
三、陶瓷在车床上进行研磨、磨削技术要实现在车床上对陶瓷进行研磨、磨削加工,需要将刀架部分换成带有切割锯片或砂轮机构。
电机带动皮带轮传动,并借助支架使砂轮机构运动,底下小托盘可以使砂轮横向、纵向进给,从而保证加工的尺寸要求及加工平面的平行度、表面粗糙度。
陶瓷材料的车削加工通常采用湿法切削,即不断向砂轮喷射切削液,目的是带走切削屑,减少刀具与材料的摩擦,降低砂轮和加工材料的温度,延长砂轮使用寿命,减少材料表面损伤等。
磨削液离心分离机介绍
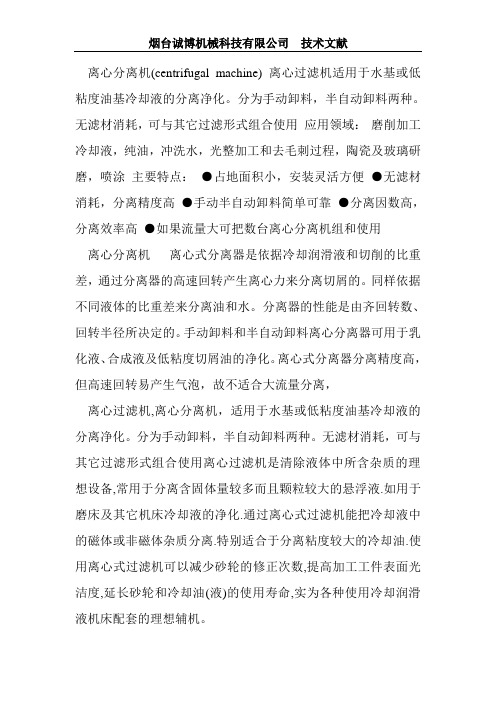
离心分离机(centrifugal machine) 离心过滤机适用于水基或低粘度油基冷却液的分离净化。
分为手动卸料,半自动卸料两种。
无滤材消耗,可与其它过滤形式组合使用应用领域:磨削加工冷却液,纯油,冲洗水,光整加工和去毛刺过程,陶瓷及玻璃研磨,喷涂主要特点:●占地面积小,安装灵活方便●无滤材消耗,分离精度高●手动半自动卸料简单可靠●分离因数高,分离效率高●如果流量大可把数台离心分离机组和使用离心分离机离心式分离器是依据冷却润滑液和切削的比重差,通过分离器的高速回转产生离心力来分离切屑的。
同样依据不同液体的比重差来分离油和水。
分离器的性能是由齐回转数、回转半径所决定的。
手动卸料和半自动卸料离心分离器可用于乳化液、合成液及低粘度切屑油的净化。
离心式分离器分离精度高,但高速回转易产生气泡,故不适合大流量分离,离心过滤机,离心分离机,适用于水基或低粘度油基冷却液的分离净化。
分为手动卸料,半自动卸料两种。
无滤材消耗,可与其它过滤形式组合使用离心过滤机是清除液体中所含杂质的理想设备,常用于分离含固体量较多而且颗粒较大的悬浮液.如用于磨床及其它机床冷却液的净化.通过离心式过滤机能把冷却液中的磁体或非磁体杂质分离.特别适合于分离粘度较大的冷却油.使用离心式过滤机可以减少砂轮的修正次数,提高加工工件表面光洁度,延长砂轮和冷却油(液)的使用寿命,实为各种使用冷却润滑液机床配套的理想辅机。
离心过滤机具有一个转动体和一个进液口,脏液通过进口进入到离心过滤机,然后流入到高速旋转的顶部开口的回转器内,在离心力的作用下,由于杂质与液体的比重不同,杂质在离心力的作用下附着在橡胶内衬的内壁上.过滤完的冷却液经叶片组合件流出转子. 应用领域:磨削加工冷却液,纯油,冲洗水,光整加工和去毛刺过程,陶瓷及玻璃研磨,喷涂主要特点:●占地面积小,安装灵活方便●无滤材消耗,分离精度高●手动半自动卸料简单可靠●分离因数高,分离效率高●如果流量大可把数台离心分离机组和使用配备安全自锁装置,在工作状态如发生开盖等误操作,电机会自动停止工作。
磨削液工艺流程

磨削液工艺流程
《磨削液工艺流程》
磨削液是在工业生产中用于金属表面处理和磨削的一种液体。
其主要作用是冷却、润滑和清洁金属表面,提高磨削的效果和效率。
磨削液的工艺流程十分重要,正确的工艺流程可以保证磨削液的性能和稳定性。
首先,选择合适的原料是工艺流程中的第一步。
磨削液的原料包括水、添加剂和润滑剂等。
水是磨削液的主要成分,其质量和纯度直接影响着磨削液的效果。
添加剂一般包括防锈剂、抗菌剂和PH调节剂等,这些添加剂可以提高磨削液的防锈和抗
菌性能,以及稳定其PH值。
润滑剂则可以减少磨损,并提高
磨削的效率。
选择合适的原料要根据不同的磨削需求和工件材质来确定。
其次,根据工艺流程,将原料按一定的比例混合均匀。
混合中需要注意控制好水和添加剂的比例,以及控制润滑剂的使用量,这样才能保证磨削液的性能。
接着,混合好的磨削液需要进行过滤处理,以去除其中的颗粒和杂质。
过滤的目的是使磨削液更加纯净,避免在磨削过程中对工件造成损坏。
最后,经过严格的检验和测试,确保磨削液符合相应的标准和要求后,方可用于磨削工艺中。
在使用过程中要不断监测磨削液的性能,并对其进行维护和管理,以确保磨削的效果和稳定
性。
总的来说,磨削液工艺流程是一个复杂而重要的过程,正确的工艺流程能够提高磨削液的效果和稳定性,保证磨削过程的顺利进行。
各种磨料用途
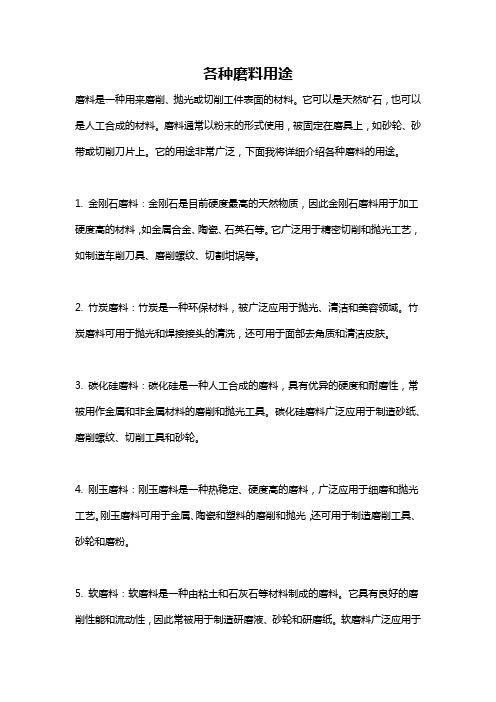
各种磨料用途磨料是一种用来磨削、抛光或切削工件表面的材料。
它可以是天然矿石,也可以是人工合成的材料。
磨料通常以粉末的形式使用,被固定在磨具上,如砂轮、砂带或切削刀片上。
它的用途非常广泛,下面我将详细介绍各种磨料的用途。
1. 金刚石磨料:金刚石是目前硬度最高的天然物质,因此金刚石磨料用于加工硬度高的材料,如金属合金、陶瓷、石英石等。
它广泛用于精密切削和抛光工艺,如制造车削刀具、磨削螺纹、切割坩埚等。
2. 竹炭磨料:竹炭是一种环保材料,被广泛应用于抛光、清洁和美容领域。
竹炭磨料可用于抛光和焊接接头的清洗,还可用于面部去角质和清洁皮肤。
3. 碳化硅磨料:碳化硅是一种人工合成的磨料,具有优异的硬度和耐磨性,常被用作金属和非金属材料的磨削和抛光工具。
碳化硅磨料广泛应用于制造砂纸、磨削螺纹、切削工具和砂轮。
4. 刚玉磨料:刚玉磨料是一种热稳定、硬度高的磨料,广泛应用于细磨和抛光工艺。
刚玉磨料可用于金属、陶瓷和塑料的磨削和抛光,还可用于制造磨削工具、砂轮和磨粉。
5. 软磨料:软磨料是一种由粘土和石灰石等材料制成的磨料。
它具有良好的磨削性能和流动性,因此常被用于制造研磨液、砂轮和研磨纸。
软磨料广泛应用于金属、木材和陶瓷的加工,以及玻璃和塑料的抛光。
6. 微晶磨料:微晶磨料是一种人工合成的磨料,具有高硬度和细腻的颗粒。
它广泛应用于半导体材料的切削和抛光、光学玻璃的加工和化妆品的制造等领域。
7. 钢砂磨料:钢砂磨料是一种金属磨料,主要由铁和碳等元素组成。
它通常用于铸造和焊接工艺中的磨削和清理过程,如去除铸件表面的氧化皮或焊接接头的瑕疵。
8. 刚玉砂磨料:刚玉石料是一种硬度高、密度大的天然矿石,常用于金属和陶瓷的抛光、表面处理和清理工艺。
刚玉砂磨料广泛应用于除锈、去污和打磨等领域。
总结起来,各种磨料都有着自己独特的用途。
金刚石磨料适用于加工硬度高的材料,竹炭磨料适用于抛光和清洁,碳化硅磨料适用于磨削和抛光工具的制造,刚玉磨料适用于细磨和抛光工艺,软磨料适用于金属和塑料的加工,微晶磨料适用于半导体材料和光学玻璃的加工,钢砂磨料适用于铸造和焊接工艺,刚玉砂磨料适用于除锈、去污和打磨等领域。
陶瓷材料及其成型工艺

陶瓷材料及其成型工艺一、陶瓷原料陶瓷原料主要包含粘土、石英、长石等,是制作陶瓷的基础。
不同的原料配方可以影响陶瓷的物理性质,如硬度、耐磨性、耐腐蚀性等。
二、成型工艺成型工艺是陶瓷制造的关键环节,主要分为以下几种:1.手糊成型:手糊成型是一种直接在模具上涂抹陶瓷浆料的方法,适用于制造大型或形状复杂的陶瓷制品。
2.注射成型:注射成型是一种将陶瓷浆料注入模具的方法,适用于制造小型、复杂的陶瓷制品。
3.压力注浆成型:压力注浆成型是一种在一定压力下将陶瓷浆料注入模具的方法,适用于制造薄壁、大型的陶瓷制品。
4.等静压成型:等静压成型是一种利用液体介质对陶瓷坯体进行均匀压力作用的方法,适用于制造高精度、高密度的陶瓷制品。
三、烧成工艺烧成工艺是陶瓷制造的另一个关键环节,主要分为以下几种:1.低温烧成:低温烧成是一种在较低温度下进行烧制的方法,适用于制造不耐高温的陶瓷制品。
2.高温烧成:高温烧成是一种在较高温度下进行烧制的方法,适用于制造需要高温烧制的陶瓷制品。
3.烧结法:烧结法是一种将陶瓷粉末经过高温烧结成为致密材料的方法,适用于制造高强度、高硬度的陶瓷制品。
四、表面处理表面处理是陶瓷制造的另一个重要环节,主要分为以下几种:1.涂装:涂装是在陶瓷表面涂上一层涂料,以增加美观度和保护层。
2.抛光:抛光是在陶瓷表面进行机械加工,以增加表面的光滑度和光泽度。
3.蚀刻:蚀刻是在陶瓷表面进行化学腐蚀加工,以制造出各种图案和纹理。
五、加工工艺加工工艺是陶瓷制造的最后一个环节,主要分为以下几种:1.切割:切割是将陶瓷材料进行切割成所需尺寸和形状的方法。
2.磨削:磨削是使用磨削液及磨具对工件进行磨削加工的方法。
陶瓷高速深磨磨削能的形成和分配机制研究

2 1 第 3期 0 2年
陶瓷高速深磨磨 削能的形成和 分配机制研 究
徐 慧 易 勇
长 沙 4 0 0) 12 0 ( 南信 息职 业技术 学 院机 电工程 系 湖
摘 要
在磨 削试验 的基础 上 ,对 工程 陶瓷氧化 锆和氧 化铝 高速深磨 磨 削能 的形成和 分配机 制进 行 了深入地
工程 陶 瓷 的高速 深磨 …是一种 全 新 的技术 ,它 具有 高砂 轮线速 度 、大 切深 、大 工作 台进给 速度 等 特 点 。陶瓷在 磨削 过程 中存在 较 大 的接 触 弧长和 最
性 能对材 料磨 削加 工去 除机 制 的影 响 。P Z试 件 的 S 尺 寸大 小为 5 0mm ̄1 5mmX1 ll A1 试 件 的 0ff 2 rr; O3
表 面形 成 能和 摩擦 能组 成 。在采 用 大磨 削用 量 的粗
研究 。介绍 了比磨削能 的变化情况,针对工程陶瓷在高速深磨时磨除率与 比磨削能的不同表现 ,详细分析了各磨
削 参 数 对 比磨 削 能 等 的 影 响 规 律 , 探 讨 了 工 程 陶 瓷材 料 在 高速 深 磨 时 的磨 削 机 制 。 关键词 工程陶瓷 高 速 深 磨 比磨 削 能 磨 削 力
P Z 和 氧化 铝 Al )在 金 刚石砂 轮高 速深 磨条 件 S 2 O3
下 ,分 别 进 行 磨 削 力 的研 究 。通 过 改 变 砂 轮 线 速 度 、切深 、工 作 台速 度 以及在 相 同 的比磨 除率条 件 下 的切深和 工 作 台速 度 ,来观 察 磨削力 ( 随磨削 条
磨
料
/ln r f ' /mn r
磨料粒度
/ %
结合
Al2O3陶瓷电火花磨削工作液实验研究

O5 p lVI l ch l 0ol ae lo a rmoeMR moe hn1% . i ei i dwaea .% oy iy o o 衄 iw t e s nC po t R r a 0 Us gd- n e t l a l r mu i火花磨削; 非导电工程陶瓷 中图分类号 :G 6 T61 文献标识码 : A
E p rme t n W o kn li o e tia s h r ea d ̄rn ig o u n r mis x e i n so r i g F Id f rElcrc lDic a g n l idn fAlmia Ce a c
子电器以及精密制造等领域中, 但是 由于其高强度 、 高 硬度、 易碎性以及不导 电等性质使其难 以加工。现有 的热压 、 烧结、 真空热挤压等工艺仅能成形出几何形状
较为简单和精度较低 的陶瓷构件 , 传统 的机械磨削加 工方法需要 昂贵的金刚石砂轮和高刚度 的磨床 , 其加 工成本高 、 效率低 , 且磨削时砂轮和工件之间存在强烈 的机械去除作用力 , 易使工件表面产生微裂纹 , 降低 了
Ab ta t sr c :W o kn ud h s s ien fe tOlte n w rc s ig meh d o y c r n u ev o be r ig f i a i f a te c i h e p o e s to f s n h o o s sr o d u l l i n
wo k gf i, h ets raeq ai al eo tie . r i ud te b s ufc u ly er b b an d n l t ,
Ke od : rigf i;l tcl ih g  ̄n ignncnut e肌咖 er gcrmi yw rs wok ud e cra s a n l e i d cr e rd ;o -odci i n v en a c i e s
磨削加工中的陶瓷磨削技术
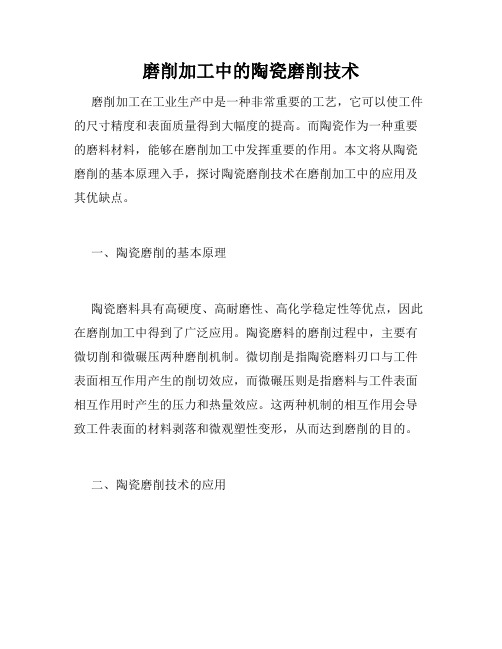
磨削加工中的陶瓷磨削技术磨削加工在工业生产中是一种非常重要的工艺,它可以使工件的尺寸精度和表面质量得到大幅度的提高。
而陶瓷作为一种重要的磨料材料,能够在磨削加工中发挥重要的作用。
本文将从陶瓷磨削的基本原理入手,探讨陶瓷磨削技术在磨削加工中的应用及其优缺点。
一、陶瓷磨削的基本原理陶瓷磨料具有高硬度、高耐磨性、高化学稳定性等优点,因此在磨削加工中得到了广泛应用。
陶瓷磨料的磨削过程中,主要有微切削和微碾压两种磨削机制。
微切削是指陶瓷磨料刃口与工件表面相互作用产生的削切效应,而微碾压则是指磨料与工件表面相互作用时产生的压力和热量效应。
这两种机制的相互作用会导致工件表面的材料剥落和微观塑性变形,从而达到磨削的目的。
二、陶瓷磨削技术的应用由于陶瓷磨料具有高硬度和高耐磨性的优点,因此它在磨削加工中的应用非常广泛。
下面将从精密磨削、超精密磨削和砂带磨削三个方面来介绍陶瓷磨削技术的应用。
1. 精密磨削精密磨削是一种高度精密的磨削工艺,其目的在于对工件表面进行高精度的加工。
在精密磨削中,陶瓷磨料通常被用作磨盘和砂轮的磨料。
陶瓷磨盘和砂轮能够产生高精度的磨削效果,并能够对工件表面进行光洁度的改善,从而提高工件的使用寿命和使用效果。
2. 超精密磨削超精密磨削是一种高度精密的磨削工艺,其目的在于对工件表面进行超高精度的加工。
在超精密磨削中,陶瓷磨料常常被用作超精密磨削工具的磨料。
陶瓷磨料在超精密磨削中能够产生高精度的磨削效果,并且能够对工件表面进行光洁度的改善,从而提高工件的使用寿命和使用效果。
3. 砂带磨削砂带磨削是一种高效的磨削工艺,其目的在于对工件表面进行快速加工。
在砂带磨削中,陶瓷磨料常被用作砂带的磨料。
陶瓷磨料在砂带磨削中能够产生高效的磨削效果,并且能够对工件表面进行光洁度的改善,从而提高工件的使用寿命和使用效果。
三、陶瓷磨削技术的优缺点陶瓷磨削技术作为一种高效的磨削技术,其优点在于:1. 磨削效率高:陶瓷磨料具有高硬度和高耐磨性的特性,因此能够在磨削中产生高效的磨削效果。
磨削液性能评价试验方法研究
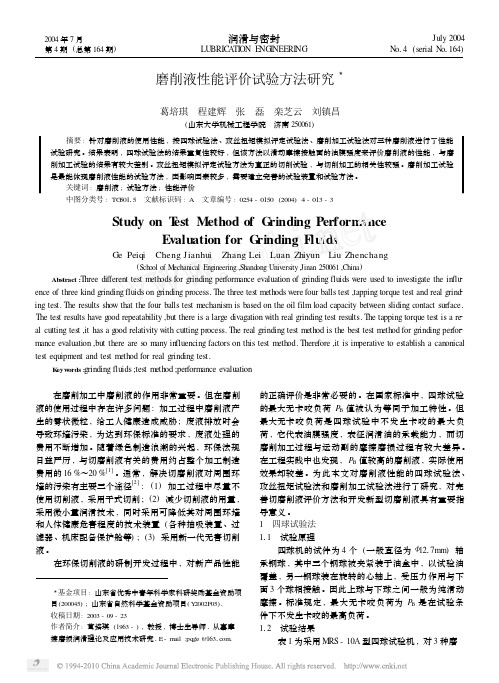
盘 ,扭矩盘与扭矩传感器联接 ,测定攻丝扭矩 。 212 试验结果
本文采用 MRG - 005 型金属加工液攻丝扭矩模拟 评定试验机 ,对上述三种不同磨削液按标准试验方法 进行了试验研究 ,试验结果如表 2 所示 。本试验是按 攻丝切削加工 ,主轴转速为 243r/ min ,数据采集系统的 启动扭矩为 015N·m ,螺母试件材料为 20Cr ,丝锥为关 中产 4 # 。
关键词 : 磨削液 ; 试验方法 ; 性能评价 中图分类号 : TG50115 文献标识码 : A 文章编号 : 0254 - 0150 (2004) 4 - 013 - 3
Study on Test Method of Grinding Performance
Evaluation for Grinding Fluids
15
但与磨削加工试验的结果却有较大差别 。在磨削加工 试验中 , HB - 1 磨削液在磨削力 、表面粗糙度方面表 现的都较好 。
攻丝扭矩 模 拟 评 定 试 验 方 法 比 四 球 试 验 方 法 要 复杂一些 。为了消除不同丝锥的影响 , 需首先使用标 准液校验丝锥 , 选出一批性能非常相近的丝锥 , 并视 其为同一丝锥 , 然后对不同磨削液进行攻丝试验 。因 这种试验方法为真正的切削试验 , 若磨削液性能较 差 , 丝锥的切削刃上很快即产生积屑瘤 , 这对试验结 果的影响较大 , 因此需严格控制试验条件 , 否则试验 结果的重复性就不可能很好 。而且该试验方法是以攻 丝加工为对象 , 没有考虑具体的加工工艺要求 , 在评 价磨削液性能时存在一定偏差 。在试验结果上 , 虽与 四球试验的 PB 值在趋势上一致 , 但在数值量差上二 者还是有区别的 。
触面的油膜承载强度来评价磨削液的性能 , 而滑动摩
碳化硅精抛液成分

碳化硅精抛液成分全文共四篇示例,供读者参考第一篇示例:碳化硅精抛液是一种用于精密磨削和抛光加工的液体磨料,具有较高的硬度和耐磨性,广泛应用于机械加工、光学制造、半导体制造等领域。
碳化硅精抛液的成分是关键的因素,直接影响着加工效果和产品质量。
本文将从碳化硅精抛液的成分、特性、应用范围以及未来发展方向等方面进行详细介绍。
一、碳化硅精抛液的成分碳化硅精抛液主要由硅碳化物、磨料颗粒、添加剂和溶剂等几种主要成分组成。
硅碳化物是碳化硅精抛液的主要成分之一,具有高硬度、耐磨性好等特点,能够有效提高磨削和抛光加工效率。
磨料颗粒是碳化硅精抛液中起到磨削作用的颗粒材料,一般为均匀分散在溶剂中的微小颗粒体。
添加剂在碳化硅精抛液中也扮演着重要的角色,常用的添加剂包括润滑剂、抗蚀剂、防锈剂等,能够有效改善碳化硅精抛液的性能和稳定性。
溶剂则是碳化硅精抛液的载体,通常为水或有机溶剂,能够帮助磨料颗粒均匀分散,并在加工过程中起到冷却和润滑的作用。
1. 高硬度:碳化硅精抛液中的硅碳化物具有极高的硬度,能够有效提高磨削和抛光加工的效率,延长工具和工件的使用寿命。
2. 耐磨性好:碳化硅精抛液中的硅碳化物颗粒具有较好的耐磨性,能够保持磨料颗粒在加工过程中的稳定性,减少工件表面的磨损。
3. 耐高温性:碳化硅精抛液在高温下依然能够保持稳定性,不易发生化学变化,适用于高温加工环境。
4. 净化性好:碳化硅精抛液具有较好的净化性能,能够有效清除工件表面的杂质、氧化层等,提高加工精度和表面质量。
5. 环保性:碳化硅精抛液在加工过程中不会产生有毒有害的废水、废气等,对环境友好,符合绿色制造的理念。
碳化硅精抛液广泛应用于机械加工、光学制造、半导体制造等领域,主要用于金属、陶瓷、玻璃等材料的精密磨削和抛光加工。
在机械加工领域,碳化硅精抛液可用于精密零部件的加工,如轴承、齿轮、气缸套等;在光学制造领域,碳化硅精抛液可用于光学元件的加工,如透镜、棱镜、反射镜等;在半导体制造领域,碳化硅精抛液可用于芯片、光刻模板等的加工。
- 1、下载文档前请自行甄别文档内容的完整性,平台不提供额外的编辑、内容补充、找答案等附加服务。
- 2、"仅部分预览"的文档,不可在线预览部分如存在完整性等问题,可反馈申请退款(可完整预览的文档不适用该条件!)。
- 3、如文档侵犯您的权益,请联系客服反馈,我们会尽快为您处理(人工客服工作时间:9:00-18:30)。
陶瓷磨削液
陶瓷磨削液,借鉴国外先进产品,中性环保配方,不伤皮肤,对环境无污染;不起泡、渗透性强,废屑沉淀快,不悬浮,研磨效率高;主要用于各种宝石、陶瓷、玻璃的磨削、研磨、切削加工使用。
【美科切削液全国招商火热进行中,诚邀您的加盟!】
一、陶瓷磨削液参数:
二、陶瓷磨削液相关推荐:
三、陶瓷磨削液知识分享:
切削液为什么会变臭
切削液具有优良防锈性,良好润滑性和优越抗挤压效果,具有很好的低泡性,适用各种
不同硬度、不同金属材质的使用。
但是如果切削液中含有大量细菌,切削液就会变臭。
1、细菌如何进入到切削液中呢?
a.配制过程中有细菌侵入;
b.空气中的细菌进入切削液;
c.工件工序间的转运造成切削液的感染;
d.操作者的不良习惯;
e.机床及车间的清洁度差。
2、如何控制细菌呢?
a.使用高质量、稳定性好的切削液;
b.用纯水配制浓缩液;
c.使用时,要控制切削液中浓缩液的比率不能过低,否则易使细菌生长;
d.由于机床所用油中含有细菌,所以要尽可能减少机床漏出的油混入切削液;
e.切削液的pH值在8.3~9.2时,细菌难以生存,所以应及时加入新的切削液,提高pH值;
f.保持切削液的清洁,不要使切削液与污油、食物、烟草等污物接触;。