国内外自动钻铆技术的发展现状及应用
2024年自动钻孔机市场前景分析
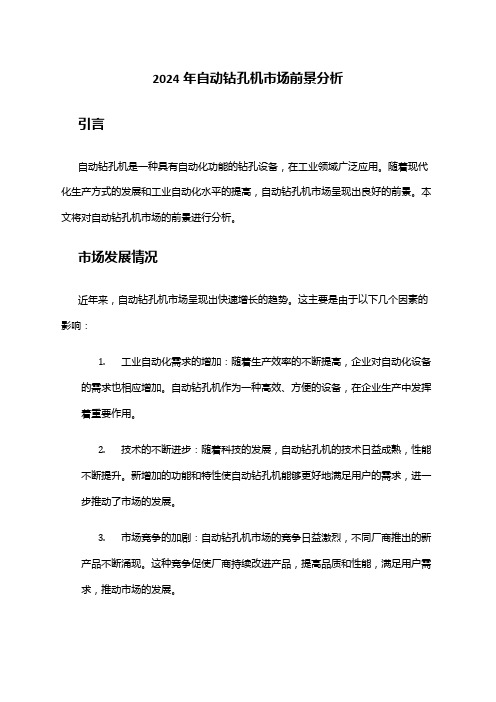
2024年自动钻孔机市场前景分析引言自动钻孔机是一种具有自动化功能的钻孔设备,在工业领域广泛应用。
随着现代化生产方式的发展和工业自动化水平的提高,自动钻孔机市场呈现出良好的前景。
本文将对自动钻孔机市场的前景进行分析。
市场发展情况近年来,自动钻孔机市场呈现出快速增长的趋势。
这主要是由于以下几个因素的影响:1.工业自动化需求的增加:随着生产效率的不断提高,企业对自动化设备的需求也相应增加。
自动钻孔机作为一种高效、方便的设备,在企业生产中发挥着重要作用。
2.技术的不断进步:随着科技的发展,自动钻孔机的技术日益成熟,性能不断提升。
新增加的功能和特性使自动钻孔机能够更好地满足用户的需求,进一步推动了市场的发展。
3.市场竞争的加剧:自动钻孔机市场的竞争日益激烈,不同厂商推出的新产品不断涌现。
这种竞争促使厂商持续改进产品,提高品质和性能,满足用户需求,推动市场的发展。
市场规模与增长预测目前,自动钻孔机市场的规模较大,市场整体增长势头强劲。
根据市场调研数据显示,自动钻孔机市场在未来几年将继续保持较高的增长速度。
预计到2025年,自动钻孔机市场规模将达到X亿元,年复合增长率为XX%。
这主要受益于工业自动化需求的增加和技术的不断成熟。
市场竞争格局目前,自动钻孔机市场存在着一定的竞争格局。
国内外知名厂商在该市场中占据主导地位,同时还有一些小型企业在市场中崭露头角。
知名厂商通过不断创新和技术升级来保持市场优势。
他们在品质、性能和服务上的优势使其能够稳定地占据市场份额。
小型企业由于灵活性和创新能力的优势,在特定领域中也逐渐崭露头角。
他们通过专注某一细分市场,提供差异化的产品和服务,获得一定市场份额。
市场驱动因素自动钻孔机市场发展的驱动因素主要包括:1.工业自动化需求的增加:随着工业生产的自动化程度不断提高,对自动钻孔机的需求也相应增加。
2.技术创新的推动:技术的不断创新为自动钻孔机的发展提供了新的机遇。
新功能和特性的引入不断提高自动钻孔机的性能和效率。
铆工领域的新技术和趋势分析
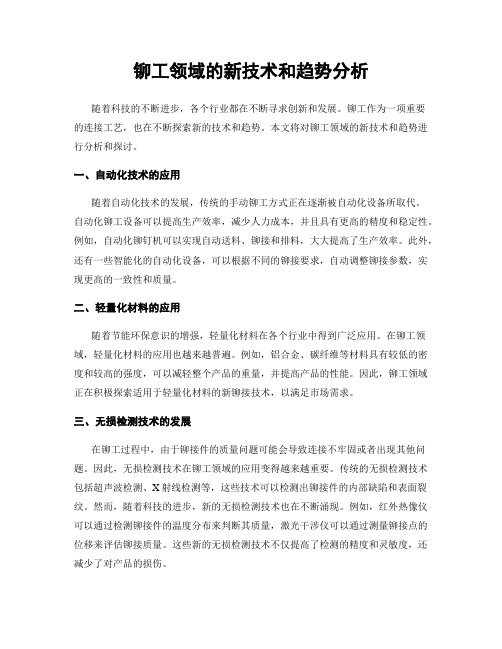
铆工领域的新技术和趋势分析随着科技的不断进步,各个行业都在不断寻求创新和发展。
铆工作为一项重要的连接工艺,也在不断探索新的技术和趋势。
本文将对铆工领域的新技术和趋势进行分析和探讨。
一、自动化技术的应用随着自动化技术的发展,传统的手动铆工方式正在逐渐被自动化设备所取代。
自动化铆工设备可以提高生产效率,减少人力成本,并且具有更高的精度和稳定性。
例如,自动化铆钉机可以实现自动送料、铆接和排料,大大提高了生产效率。
此外,还有一些智能化的自动化设备,可以根据不同的铆接要求,自动调整铆接参数,实现更高的一致性和质量。
二、轻量化材料的应用随着节能环保意识的增强,轻量化材料在各个行业中得到广泛应用。
在铆工领域,轻量化材料的应用也越来越普遍。
例如,铝合金、碳纤维等材料具有较低的密度和较高的强度,可以减轻整个产品的重量,并提高产品的性能。
因此,铆工领域正在积极探索适用于轻量化材料的新铆接技术,以满足市场需求。
三、无损检测技术的发展在铆工过程中,由于铆接件的质量问题可能会导致连接不牢固或者出现其他问题。
因此,无损检测技术在铆工领域的应用变得越来越重要。
传统的无损检测技术包括超声波检测、X射线检测等,这些技术可以检测出铆接件的内部缺陷和表面裂纹。
然而,随着科技的进步,新的无损检测技术也在不断涌现。
例如,红外热像仪可以通过检测铆接件的温度分布来判断其质量,激光干涉仪可以通过测量铆接点的位移来评估铆接质量。
这些新的无损检测技术不仅提高了检测的精度和灵敏度,还减少了对产品的损伤。
四、数字化技术的应用随着数字化技术的飞速发展,铆工领域也开始应用数字化技术来提高生产效率和质量。
例如,数字化设计软件可以帮助工程师更加准确地设计铆接结构,减少设计错误和重复工作。
数字化仿真软件可以模拟铆接过程,评估不同参数对铆接质量的影响,从而优化铆接方案。
此外,数字化技术还可以实现铆接过程的实时监控和数据采集,为质量控制和过程改进提供依据。
综上所述,铆工领域的新技术和趋势主要包括自动化技术的应用、轻量化材料的应用、无损检测技术的发展和数字化技术的应用。
飞机装配自动钻铆技术研究与分析
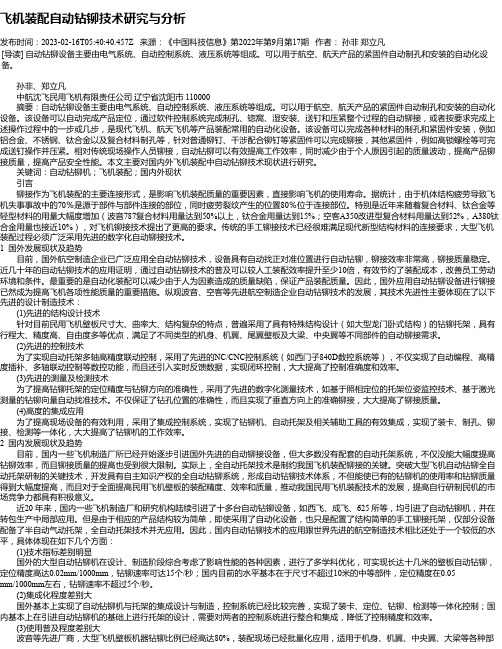
飞机装配自动钻铆技术研究与分析发布时间:2023-02-16T05:40:40.457Z 来源:《中国科技信息》第2022年第9月第17期作者:孙非郑立凡[导读] 自动钻铆设备主要由电气系统、自动控制系统、液压系统等组成。
可以用于航空、航天产品的紧固件自动制孔和安装的自动化设备。
孙非、郑立凡中航沈飞民用飞机有限责任公司辽宁省沈阳市 110000摘要:自动钻铆设备主要由电气系统、自动控制系统、液压系统等组成。
可以用于航空、航天产品的紧固件自动制孔和安装的自动化设备。
该设备可以自动完成产品定位,通过软件控制系统完成制孔、锪窩、湿安装、送钉和压紧整个过程的自动铆接,或者按要求完成上述操作过程中的一步或几步,是现代飞机、航天飞机等产品装配常用的自动化设备。
该设备可以完成各种材料的制孔和紧固件安装,例如铝合金、不锈钢、钛合金以及复合材料制孔等,针对普通铆钉、干涉配合铆钉等紧固件可以完成铆接,其他紧固件,例如高锁螺栓等可完成送钉操作并压紧。
相对传统现场操作人员铆接,自动钻铆可以有效提高工作效率,同时减少由于个人原因引起的质量波动,提高产品铆接质量,提高产品安全性能。
本文主要对国内外飞机装配中自动钻铆技术现状进行研究。
关键词:自动钻铆机;飞机装配;国内外现状引言铆接作为飞机装配的主要连接形式,是影响飞机装配质量的重要因素,直接影响飞机的使用寿命。
据统计,由于机体结构疲劳导致飞机失事事故中的70%是源于部件与部件连接的部位,同时疲劳裂纹产生的位置80%位于连接部位。
特别是近年来随着复合材料、钛合金等轻型材料的用量大幅度增加(波音787复合材料用量达到50%以上,钛合金用量达到15%;空客A350改进型复合材料用量达到52%,A380钛合金用量也接近10%),对飞机铆接技术提出了更高的要求。
传统的手工铆接技术已经很难满足现代新型结构材料的连接要求,大型飞机装配过程必须广泛采用先进的数字化自动铆接技术。
1 国外发展现状及趋势目前,国外航空制造企业已广泛应用全自动钻铆技术,设备具有自动找正对准位置进行自动钻铆,铆接效率非常高,铆接质量稳定。
看了国外的飞机自动钻铆技术,才知道什么是差距!

看了国外的飞机自动钻铆技术,才知道什么是差距!飞机壁板的连接质量对飞机的气动外形及其疲劳寿命有至关重要的影响,铆接作为一种传统的机械连接技术,由于其连接可靠、质量轻、成本低等特点被广泛用于航空航天领域,因此铆接质量对飞机的安全性能有重要的影响。
采用自动钻铆技术实现飞机壁板的制孔和铆接是提高飞机装配质量与效率的有效途径。
资料显示,手工钻铆效率平均为15s/ 钉,自动钻铆效率最快能达到3s/ 钉,效率提高5 倍;手工铆接镦头高度公差为±0.5mm,自动钻铆所形成镦头高度公差能达到±0.05mm,精度提高10倍。
自动钻铆设备按结构形式可分为龙门式自动钻铆系统、C 型架式自动钻铆系统以及机器人自动钻铆系统。
前两种设备刚性好,精度高,提供的铆接力大,可用于开敞性好的大型结构件的自动钻铆;机器人自动钻铆系统成本低,运动灵活,空间利用率高,可达性高,适用于开敞性差的壁板的自动钻铆装配。
自动钻铆设备按铆接驱动方式又可分为气动锤铆、伺服压铆和电磁铆接。
气动锤铆结构简单,体积小,铆接力小,易于集成,与工业机器人构成机器人自动钻铆系统已成为发展趋势。
伺服压铆采用伺服电机驱动,行星滚珠丝杠传动,可实现高精度、大负载的伺服压铆,较传统的气动铆接具备更高的控制精度与柔性化的速度调节能力,能够按照设定的位移曲线或力曲线进行加载,目前已成功取代液压铆接广泛运用在飞机装配中。
电磁铆接是在电磁成形工艺的基础上发展起来的一种新型铆接工艺,能够实现钛合金和复合材料的连接,以及大直径和难成形材料铆钉成形。
国外自动钻铆技术研究应用现状自动钻铆技术起源于20 世纪50 年代,经过几十年的发展,已成为能够自动完成定位、制孔、送钉、铆接及检测功能的先进制造技术。
国外自动钻铆设备主要供应商以美国捷姆科(GEMCOR)、EI (Electroimpact)、德国宝捷(BROETJE)、意大利B&C (BISUACH & CARRU)为代表,各公司的典型产品型号及其应用情况如表1 所示。
国内外钻机自动送钻技术发展现状
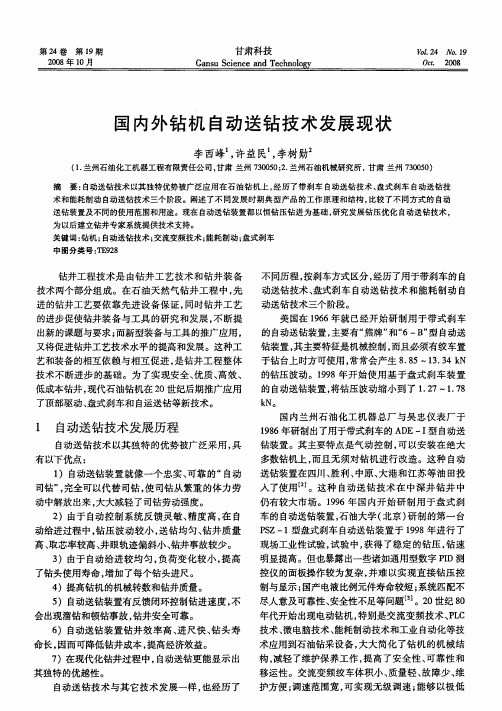
控仪的面板操作较 为复杂 , 并难 以实现直接钻压控 制与显示 ; 国产 电液比例元件寿命较短 ; 系统匹配不 尽人意及可靠性、 安全性不足等问题 。2 】 O世纪 8 O 年代开始 出现 电动钻机 , 特别是交流变频技术 、L PC 技术、 电脑技术、 微 能耗制动技术和工业 自 动化等技
现场工业性试验 , 试验 中, 获得了稳定 的钻压 , 钻速 明显提高 。但也暴露出一些诸如通用型数字 PD测 I
3 )由于 自动给进较均匀 , 负荷变化较小 , 提高 了钻头使用寿命 , 增加了每个钻头进尺。 4 )提高钻机的机械转数 和钻井质量。 5 )自动送钻装置有反馈闭环控制钻进速度 , 不 会出现溜钻和顿钻事故 , 钻井安全可靠 。 6 )自动送钻装置钻井效率 高、 进尺快、 钻头 寿 命长 , 因而可降低钻井成本 , 提高经济效益。 7 )在现代化钻井过程 中, 自动送钻更能显示 出
1 )自动送钻装置就像一个忠实、 可靠的“ 自动 司钻” 完全可 以代 替司钻 , 司钻从繁重 的体力 劳 , 使
动中解放出来 , 大大减轻了司钻劳动强度。 2 )由于 自动控制系统反馈灵敏、 精度 高 , 自 在 动给进过程 中, 钻压波动较小 , 送钻均匀、 钻井质量 高、 取芯率较高 、 井眼轨迹偏斜小、 钻井事故较少 。
液压讯号并传送给转换器。转换器 由司钻根据钻头
自 动送钻技术主要有主电机 自 动送钻和小 电机 自动 送钻, 将钻压波动缩小到了 0 0 0 5k , .4— . N 4 这两 L J 种都是基于变频技术和能耗制动技术 。对提高钻井 时效, 优化钻井工艺、 处理井下事故等十分有利。新
第2 卷 4
自动钻铆
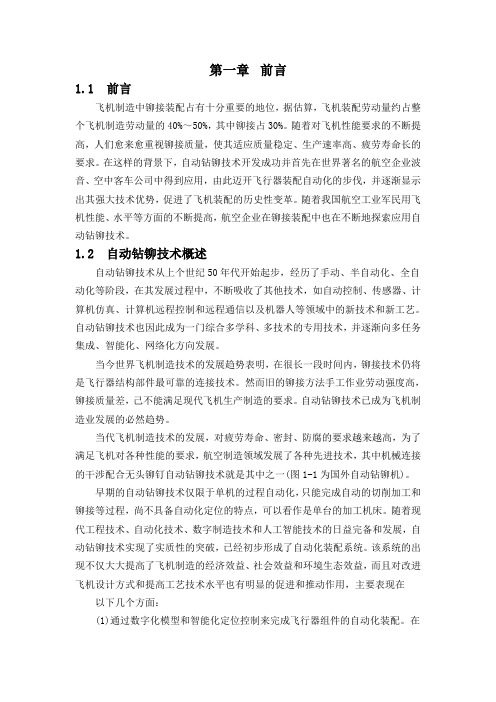
第一章前言1.1 前言飞机制造中铆接装配占有十分重要的地位,据估算,飞机装配劳动量约占整个飞机制造劳动量的40%~50%,其中铆接占30%。
随着对飞机性能要求的不断提高,人们愈来愈重视铆接质量,使其适应质量稳定、生产速率高、疲劳寿命长的要求。
在这样的背景下,自动钻铆技术开发成功并首先在世界著名的航空企业波音、空中客车公司中得到应用,由此迈开飞行器装配自动化的步伐,并逐渐显示出其强大技术优势,促进了飞机装配的历史性变革。
随着我国航空工业军民用飞机性能、水平等方面的不断提高,航空企业在铆接装配中也在不断地探索应用自动钻铆技术。
1.2 自动钻铆技术概述自动钻铆技术从上个世纪50年代开始起步,经历了手动、半自动化、全自动化等阶段,在其发展过程中,不断吸收了其他技术,如自动控制、传感器、计算机仿真、计算机远程控制和远程通信以及机器人等领域中的新技术和新工艺。
自动钻铆技术也因此成为一门综合多学科、多技术的专用技术,并逐渐向多任务集成、智能化、网络化方向发展。
当今世界飞机制造技术的发展趋势表明,在很长一段时间内,铆接技术仍将是飞行器结构部件最可靠的连接技术。
然而旧的铆接方法手工作业劳动强度高,铆接质量差,己不能满足现代飞机生产制造的要求。
自动钻铆技术已成为飞机制造业发展的必然趋势。
当代飞机制造技术的发展,对疲劳寿命、密封、防腐的要求越来越高,为了满足飞机对各种性能的要求,航空制造领域发展了各种先进技术,其中机械连接的干涉配合无头铆钉自动钻铆技术就是其中之一(图1-1为国外自动钻铆机)。
早期的自动钻铆技术仅限于单机的过程自动化,只能完成自动的切削加工和铆接等过程,尚不具备自动化定位的特点,可以看作是单台的加工机床。
随着现代工程技术、自动化技术、数字制造技术和人工智能技术的日益完备和发展,自动钻铆技术实现了实质性的突破,已经初步形成了自动化装配系统。
该系统的出现不仅大大提高了飞机制造的经济效益、社会效益和环境生态效益,而且对改进飞机设计方式和提高工艺技术水平也有明显的促进和推动作用,主要表现在以下几个方面:(1)通过数字化模型和智能化定位控制来完成飞行器组件的自动化装配。
飞机自动钻铆技术研究现状及其关键技术

飞机自动钻铆技术研究现状及其关键技术发布时间:2022-11-07T05:47:54.026Z 来源:《中国科技信息》2022年第13期7月作者:周华[导读] 随着计算机、信息和自动化技术的发展,数字飞机的组装技术迅速发展。
数字装配技术被周华中航飞机股份有限公司陕西西安 710089摘要:随着计算机、信息和自动化技术的发展,数字飞机的组装技术迅速发展。
数字装配技术被空客、波音等大型飞机制造商平等使用。
我国大型飞机研究项目的实施将加快数字飞机的装配。
自动钻铆技术是数字装配技术不可或缺的组成部分,可以大大提高飞机装配效率,有效保证装配质量,提高疲劳强度。
关键词:航空壁板;自动钻铆;高精度定位随着现代飞机制造技术的发展,对飞机性能、密封性和耐腐蚀性的要求越来越高。
为了满足飞机的性能要求,航天工业开发了一系列先进技术,如机械连接与自动钻铆的应用。
几十年来国外铆接装配技术的应用表明,自动自动钻铆机的效率至少是手工铆接的十倍,节省了安装成本,改善了工作条件。
最重要的是保证安装质量,大大减少人为缺陷。
自动钻铆机的使用是目前提高飞行效率的主要技术措施之一。
一、自动钻铆技术的发展现状1.设备开发。
针对不同类型的飞机设计,开发了各种数控自动钻铆系统,不仅壁板铆接,而且肋、框、梁、翼面、前缘铆接。
因此,自动钻铆系统的作用范围明显扩大,铆接整体性能得到显着提高。
2.自动安装紧固件。
添加附件后,可自动安装两件型紧固件(槽、高锁、锥形螺栓),从而使无头铆钉铆接干涉配合。
因此,铆接结构的疲劳可以增加5至6倍,改进油箱的密封铆接至关重要。
3.自动钻铆。
整个过程是通过数字程序编程的,自动钻铆程序是一个连续的过程,用于夹紧、钻孔、锪窝、注胶、铣平。
机床配有高速旋转轴,可同时钻至0.005mm钻孔精度高,埋头窝深度精确控制在±0.0lmm范围内。
此外,机床还通过数字控制系统和自动化化工装夹具。
无论人为影响因素如何,铆钉镦头的高度都是恒定的。
2023年铆接设备行业市场发展现状
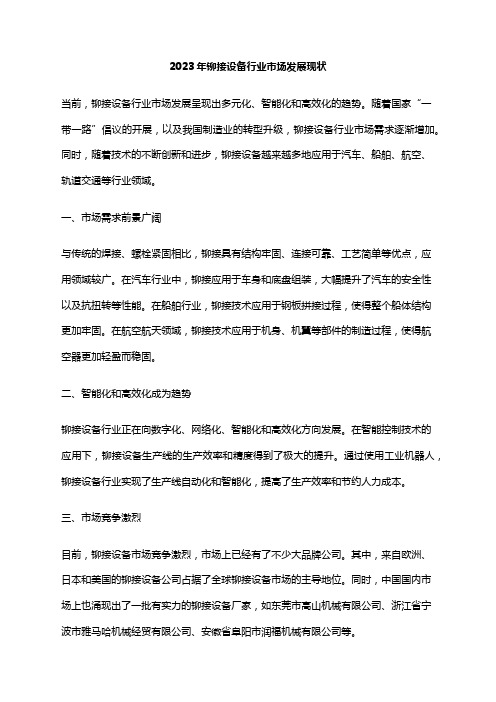
2023年铆接设备行业市场发展现状
当前,铆接设备行业市场发展呈现出多元化、智能化和高效化的趋势。
随着国家“一带一路”倡议的开展,以及我国制造业的转型升级,铆接设备行业市场需求逐渐增加。
同时,随着技术的不断创新和进步,铆接设备越来越多地应用于汽车、船舶、航空、轨道交通等行业领域。
一、市场需求前景广阔
与传统的焊接、螺栓紧固相比,铆接具有结构牢固、连接可靠、工艺简单等优点,应用领域较广。
在汽车行业中,铆接应用于车身和底盘组装,大幅提升了汽车的安全性以及抗扭转等性能。
在船舶行业,铆接技术应用于钢板拼接过程,使得整个船体结构更加牢固。
在航空航天领域,铆接技术应用于机身、机翼等部件的制造过程,使得航空器更加轻盈而稳固。
二、智能化和高效化成为趋势
铆接设备行业正在向数字化、网络化、智能化和高效化方向发展。
在智能控制技术的应用下,铆接设备生产线的生产效率和精度得到了极大的提升。
通过使用工业机器人,铆接设备行业实现了生产线自动化和智能化,提高了生产效率和节约人力成本。
三、市场竞争激烈
目前,铆接设备市场竞争激烈,市场上已经有了不少大品牌公司。
其中,来自欧洲、日本和美国的铆接设备公司占据了全球铆接设备市场的主导地位。
同时,中国国内市场上也涌现出了一批有实力的铆接设备厂家,如东莞市高山机械有限公司、浙江省宁波市雅马哈机械经贸有限公司、安徽省阜阳市润福机械有限公司等。
总之,铆接设备行业市场随着全球工业化进程和中国制造2025战略的推进,市场前景将会更广阔。
行业企业不断加强自身技术创新,提高产品质量和性能,增强企业核心竞争力,才能在竞争激烈的市场环境中获得更好的发展。
国内外钻机技术的发展趋势与对策
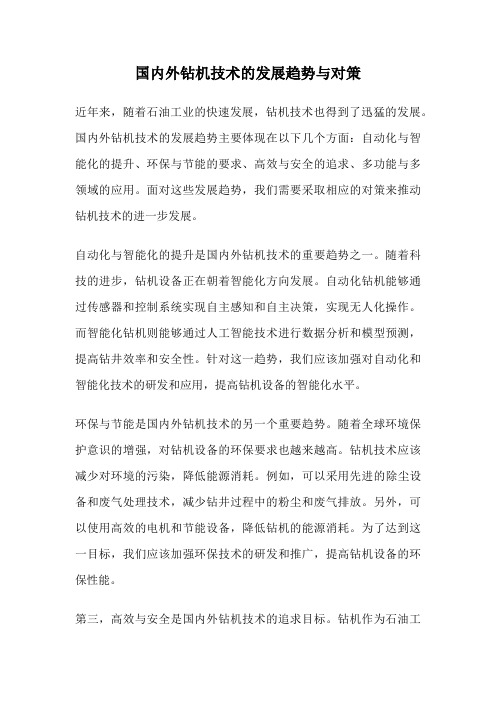
国内外钻机技术的发展趋势与对策近年来,随着石油工业的快速发展,钻机技术也得到了迅猛的发展。
国内外钻机技术的发展趋势主要体现在以下几个方面:自动化与智能化的提升、环保与节能的要求、高效与安全的追求、多功能与多领域的应用。
面对这些发展趋势,我们需要采取相应的对策来推动钻机技术的进一步发展。
自动化与智能化的提升是国内外钻机技术的重要趋势之一。
随着科技的进步,钻机设备正在朝着智能化方向发展。
自动化钻机能够通过传感器和控制系统实现自主感知和自主决策,实现无人化操作。
而智能化钻机则能够通过人工智能技术进行数据分析和模型预测,提高钻井效率和安全性。
针对这一趋势,我们应该加强对自动化和智能化技术的研发和应用,提高钻机设备的智能化水平。
环保与节能是国内外钻机技术的另一个重要趋势。
随着全球环境保护意识的增强,对钻机设备的环保要求也越来越高。
钻机技术应该减少对环境的污染,降低能源消耗。
例如,可以采用先进的除尘设备和废气处理技术,减少钻井过程中的粉尘和废气排放。
另外,可以使用高效的电机和节能设备,降低钻机的能源消耗。
为了达到这一目标,我们应该加强环保技术的研发和推广,提高钻机设备的环保性能。
第三,高效与安全是国内外钻机技术的追求目标。
钻机作为石油工业的重要设备,其高效和安全性直接影响到整个生产过程的效益和安全。
因此,钻机技术应该不断提高钻井效率和安全性。
例如,可以采用高效的钻头和钻井液,提高钻井速度和质量。
另外,可以加强对钻机设备的监测和维护,减少设备故障和事故发生的概率。
为了实现高效和安全,我们应该加强对钻机设备的研发和改进,提高设备的可靠性和稳定性。
多功能与多领域的应用是国内外钻机技术的发展趋势之一。
随着石油工业的多样化需求,钻机技术也需要具备更多的功能和适应更多的领域。
例如,钻机可以用于石油勘探、水井钻探、地热能开发等多个领域。
为了实现多功能和多领域的应用,我们应该加强对钻机技术的研发和推广,提高钻机设备的适应性和灵活性。
铆工技术的发展趋势与前景展望
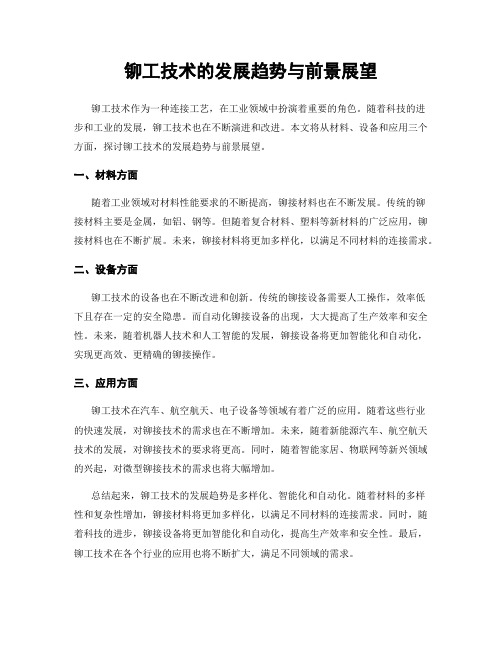
铆工技术的发展趋势与前景展望铆工技术作为一种连接工艺,在工业领域中扮演着重要的角色。
随着科技的进步和工业的发展,铆工技术也在不断演进和改进。
本文将从材料、设备和应用三个方面,探讨铆工技术的发展趋势与前景展望。
一、材料方面随着工业领域对材料性能要求的不断提高,铆接材料也在不断发展。
传统的铆接材料主要是金属,如铝、钢等。
但随着复合材料、塑料等新材料的广泛应用,铆接材料也在不断扩展。
未来,铆接材料将更加多样化,以满足不同材料的连接需求。
二、设备方面铆工技术的设备也在不断改进和创新。
传统的铆接设备需要人工操作,效率低下且存在一定的安全隐患。
而自动化铆接设备的出现,大大提高了生产效率和安全性。
未来,随着机器人技术和人工智能的发展,铆接设备将更加智能化和自动化,实现更高效、更精确的铆接操作。
三、应用方面铆工技术在汽车、航空航天、电子设备等领域有着广泛的应用。
随着这些行业的快速发展,对铆接技术的需求也在不断增加。
未来,随着新能源汽车、航空航天技术的发展,对铆接技术的要求将更高。
同时,随着智能家居、物联网等新兴领域的兴起,对微型铆接技术的需求也将大幅增加。
总结起来,铆工技术的发展趋势是多样化、智能化和自动化。
随着材料的多样性和复杂性增加,铆接材料将更加多样化,以满足不同材料的连接需求。
同时,随着科技的进步,铆接设备将更加智能化和自动化,提高生产效率和安全性。
最后,铆工技术在各个行业的应用也将不断扩大,满足不同领域的需求。
展望未来,铆工技术将继续发展壮大,成为工业领域中不可或缺的连接技术。
随着科技的进步和工业的发展,铆工技术将不断创新和改进,为各个行业提供更高效、更可靠的连接解决方案。
同时,铆工技术的发展也将推动相关产业链的发展,带动经济增长和就业机会的增加。
总之,铆工技术的发展前景广阔,将在材料、设备和应用方面不断创新和进步。
我们有理由相信,铆工技术将在未来的工业领域中发挥更加重要的作用,为工业发展和社会进步做出贡献。
铆工技术的发展趋势与未来展望分析
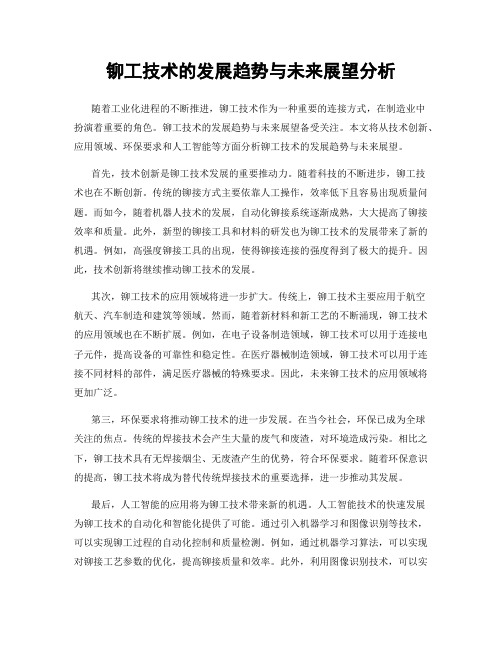
铆工技术的发展趋势与未来展望分析随着工业化进程的不断推进,铆工技术作为一种重要的连接方式,在制造业中扮演着重要的角色。
铆工技术的发展趋势与未来展望备受关注。
本文将从技术创新、应用领域、环保要求和人工智能等方面分析铆工技术的发展趋势与未来展望。
首先,技术创新是铆工技术发展的重要推动力。
随着科技的不断进步,铆工技术也在不断创新。
传统的铆接方式主要依靠人工操作,效率低下且容易出现质量问题。
而如今,随着机器人技术的发展,自动化铆接系统逐渐成熟,大大提高了铆接效率和质量。
此外,新型的铆接工具和材料的研发也为铆工技术的发展带来了新的机遇。
例如,高强度铆接工具的出现,使得铆接连接的强度得到了极大的提升。
因此,技术创新将继续推动铆工技术的发展。
其次,铆工技术的应用领域将进一步扩大。
传统上,铆工技术主要应用于航空航天、汽车制造和建筑等领域。
然而,随着新材料和新工艺的不断涌现,铆工技术的应用领域也在不断扩展。
例如,在电子设备制造领域,铆工技术可以用于连接电子元件,提高设备的可靠性和稳定性。
在医疗器械制造领域,铆工技术可以用于连接不同材料的部件,满足医疗器械的特殊要求。
因此,未来铆工技术的应用领域将更加广泛。
第三,环保要求将推动铆工技术的进一步发展。
在当今社会,环保已成为全球关注的焦点。
传统的焊接技术会产生大量的废气和废渣,对环境造成污染。
相比之下,铆工技术具有无焊接烟尘、无废渣产生的优势,符合环保要求。
随着环保意识的提高,铆工技术将成为替代传统焊接技术的重要选择,进一步推动其发展。
最后,人工智能的应用将为铆工技术带来新的机遇。
人工智能技术的快速发展为铆工技术的自动化和智能化提供了可能。
通过引入机器学习和图像识别等技术,可以实现铆工过程的自动化控制和质量检测。
例如,通过机器学习算法,可以实现对铆接工艺参数的优化,提高铆接质量和效率。
此外,利用图像识别技术,可以实时监测铆接过程中的缺陷和问题,提前预警并进行处理。
因此,人工智能的应用将为铆工技术的发展带来新的突破。
自动钻柳技术发展现状与应用分析
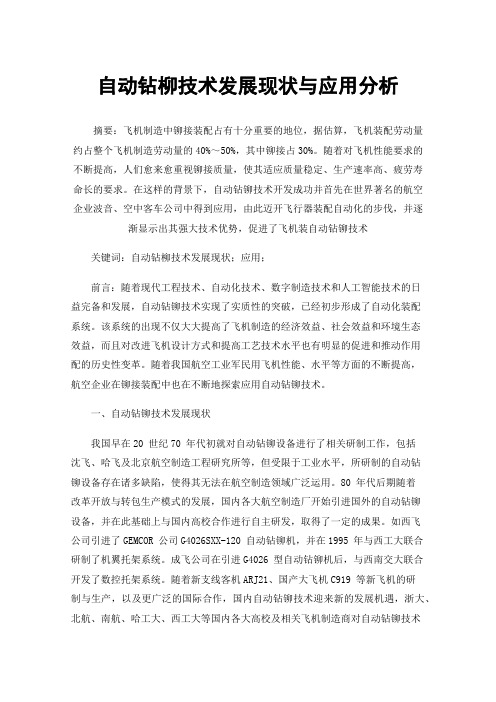
自动钻柳技术发展现状与应用分析摘要:飞机制造中铆接装配占有十分重要的地位,据估算,飞机装配劳动量约占整个飞机制造劳动量的40%~50%,其中铆接占30%。
随着对飞机性能要求的不断提高,人们愈来愈重视铆接质量,使其适应质量稳定、生产速率高、疲劳寿命长的要求。
在这样的背景下,自动钻铆技术开发成功并首先在世界著名的航空企业波音、空中客车公司中得到应用,由此迈开飞行器装配自动化的步伐,并逐渐显示出其强大技术优势,促进了飞机装自动钻铆技术关键词:自动钻柳技术发展现状;应用;前言:随着现代工程技术、自动化技术、数字制造技术和人工智能技术的日益完备和发展,自动钻铆技术实现了实质性的突破,已经初步形成了自动化装配系统。
该系统的出现不仅大大提高了飞机制造的经济效益、社会效益和环境生态效益,而且对改进飞机设计方式和提高工艺技术水平也有明显的促进和推动作用配的历史性变革。
随着我国航空工业军民用飞机性能、水平等方面的不断提高,航空企业在铆接装配中也在不断地探索应用自动钻铆技术。
一、自动钻铆技术发展现状我国早在20 世纪70 年代初就对自动钻铆设备进行了相关研制工作,包括沈飞、哈飞及北京航空制造工程研究所等,但受限于工业水平,所研制的自动钻铆设备存在诸多缺陷,使得其无法在航空制造领域广泛运用。
80 年代后期随着改革开放与转包生产模式的发展,国内各大航空制造厂开始引进国外的自动钻铆设备,并在此基础上与国内高校合作进行自主研发,取得了一定的成果。
如西飞公司引进了GEMCOR 公司G4026SXX-120 自动钻铆机,并在1995 年与西工大联合研制了机翼托架系统。
成飞公司在引进G4026 型自动钻铆机后,与西南交大联合开发了数控托架系统。
随着新支线客机ARJ21、国产大飞机C919 等新飞机的研制与生产,以及更广泛的国际合作,国内自动钻铆技术迎来新的发展机遇,浙大、北航、南航、哈工大、西工大等国内各大高校及相关飞机制造商对自动钻铆技术进行了深入研究,并取得了一定的成就。
国内外钻机技术的发展趋势与对策
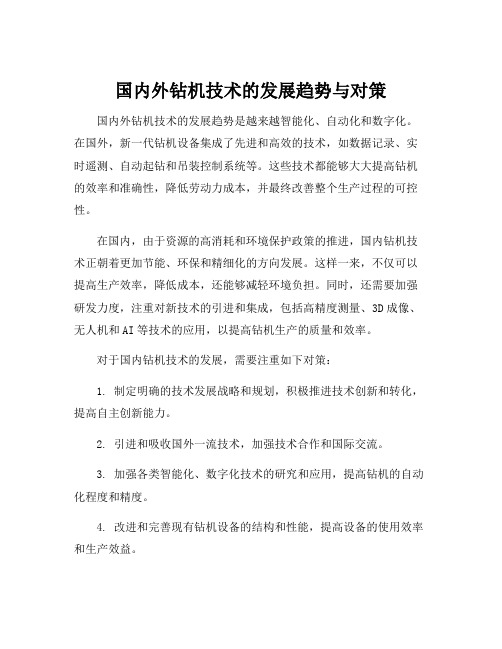
国内外钻机技术的发展趋势与对策国内外钻机技术的发展趋势是越来越智能化、自动化和数字化。
在国外,新一代钻机设备集成了先进和高效的技术,如数据记录、实时遥测、自动起钻和吊装控制系统等。
这些技术都能够大大提高钻机的效率和准确性,降低劳动力成本,并最终改善整个生产过程的可控性。
在国内,由于资源的高消耗和环境保护政策的推进,国内钻机技术正朝着更加节能、环保和精细化的方向发展。
这样一来,不仅可以提高生产效率,降低成本,还能够减轻环境负担。
同时,还需要加强研发力度,注重对新技术的引进和集成,包括高精度测量、3D成像、无人机和AI等技术的应用,以提高钻机生产的质量和效率。
对于国内钻机技术的发展,需要注重如下对策:
1. 制定明确的技术发展战略和规划,积极推进技术创新和转化,提高自主创新能力。
2. 引进和吸收国外一流技术,加强技术合作和国际交流。
3. 加强各类智能化、数字化技术的研究和应用,提高钻机的自动化程度和精度。
4. 改进和完善现有钻机设备的结构和性能,提高设备的使用效率和生产效益。
5. 加强钻机设备的维护和管理,延长设备使用寿命,降低维修费用。
综上,国内外钻机技术的发展趋势是日益智能化和环保,需要加强创新和转化,提升自主研发能力,注重引进和应用一流技术,加强设备管理和维护,以提高钻机生产效率和效益。
飞机自动钻铆技术发展趋势

飞机自动钻铆技术开展趋势飞机自动钻铆技术开展趋势摘要:自动钻铆技术是新一代飞机研制的关键技术,对于提高我国的飞机制造水平,增强国防能力具有深远的意义。
本文将重点探讨飞机自动钻铆技术的开展趋势。
飞机制造中铆接装配占有十分重要的地位,据估算,飞机装配劳动量约占整个飞机制造劳动量的40%~50%,其中铆接占30%。
随着对飞机性能要求的不断提高,人们愈来愈重视铆接质量,使其适应质量稳定、生产速率高、疲劳寿命长的要求。
在这样的背景下,自动钻铆技术开发成功并首先在世界著名的航空企业波音、空中客车公司中得到应用,由此迈开飞行器装配自动化的步伐,并逐渐显示出其强大技术优势,促进了飞机装配历史性变革。
1.自动钻铆技术的应用国外自动钻铆技术应用简况。
国外使用的自动钻铆机,估计在一千台以上。
这些钻铆机主要由美国GEMCOR公司生产,此外还有德国的BROTlE AUTOMATION、法国的RECOUIESETFIIS。
俄国生产的自动钻铆机有CKAK、Y9K等类型此外,美国的AEROSPACE PRECISION SYSTEM s,INC也制造一些钻铆机。
在国外所有飞机制造公司都有自动钻铆机,如渡音、法宇航、“空中客车〞集团等。
为这些公司进行转包生产的日本、韩国,也大量引进自动钻铆机。
自动钻铆机的加工范围:无头铆钉、有头铆钉、双体紧固件――环槽铆钉与高锁螺栓、抽铆钉等。
国内自动钻铆技术应用情况。
在国外航空零、部件转包生产之前,国内自动钻铆技术的应用仅处于起步阶段。
70年代初,原航空工业部曾组织有关单位研制过各种型号的自动钻铆机,由于没有型号需求的牵头,使研制工作半途而废,加上当时研制的设备中所采用的元件、控制系统等均存在各种质量问题,绝大局部设备都存在一些故障,无法正常使用,有的被撤除,有的搁置至今。
从1985年起,我国先后从国外引进了七台自动钻铆机,其中西飞三台、上飞一台、成飞一台、625所一台、沈飞一台这七台中除西飞有两台已用于生产外,其余五台困各种原因,在安装、调试完毕后均没投人使用另外,由于自动钻铆机价格昂贵及国产飞机尚无强制性的自动钻铆要求,目前自动钻铆技术仅在航空零部件转包生产线上使用。
国内外自动钻铆技术的发展现状及应用

国内外自动钻铆技术的发展现状及应用西飞国际设备维修中心 楼阿莉当代飞机制造技术的发展,对疲劳寿命、密封、防腐的要求越来越高,为了满足飞机对各种性能的要求,航空制造领域发展了各种先进技术,其中机械连接技术的干涉配合无头铆钉自动钻铆技术就是其中之一。
国外铆接装配技术几十年的应用证明,采用自动钻铆机后装配效率至少比手工铆接装配提高10倍,并能节约安装成本,改善劳动条件,更主要的是能够确保安装质量,大大减少人为因素造成的缺陷。
现在采用自动钻铆机已成为改善飞机性能的主要工艺措施之一。
美国是最早发展自动钻铆技术的国家,早在 50 年代初就已在飞机铆接装配生产线上应用了自动钻铆机,经过 50 多年的发展,现在世界各航空工业发达国家都已广泛采用这项技术。
自动钻铆技术主要包含以下内容:(1) 设备的研制、开发。
以不同飞机的结构为对象,发展多种型号的数控自动钻铆系统,不仅能铆接壁板,而且还可铆接各种组件,如肋、框、梁、翼面、前缘等,从而使自动钻铆系统的工作覆盖面大幅度增加,使整个飞机的铆接工作有较大的改观。
(2) 对各种干涉配合新型紧固件进行自动安装。
通过增加附件,可以对两件型紧固件进行自动安装,如环槽钉、高锁螺栓、锥形螺栓等,也可对无头铆钉进行干涉配合铆接,从而提高铆接结构疲劳寿命5~6倍,对提高飞机整体油箱的密封铆接质量有重大意义。
(3) 自动钻铆工艺。
结构铆接的整个过程通过预先编程全部由CNC程序控制,自动钻铆工艺是在一台设备上一次性地连续完成夹紧、钻孔、锪窝、注胶、放铆、铣平等工序。
由于机床带有高速、高精度的转削主轴头,一次进给即能钻出0.005mm以内高精度的孔,同时埋头窝的深度也可精确控制在±0.01mm以内,再加上机床由数控系统控制各轴运动,并采用精密自动化工装夹具,使得铆钉镦头高度保持一致,不受人为因素的影响。
所有这些因素均使钉杆在孔中充填质量大为改善,从而有利于提高细节疲劳强度许用值。
此外,由于钻孔时铆接件处在高的夹紧力下,层间不会产生毛刺和进入切削,可以减小疲劳载荷下发生磨蚀损伤的程度,这些均有利于提高接头的疲劳强度。
飞机自动钻铆技术研究现状及其关键技术
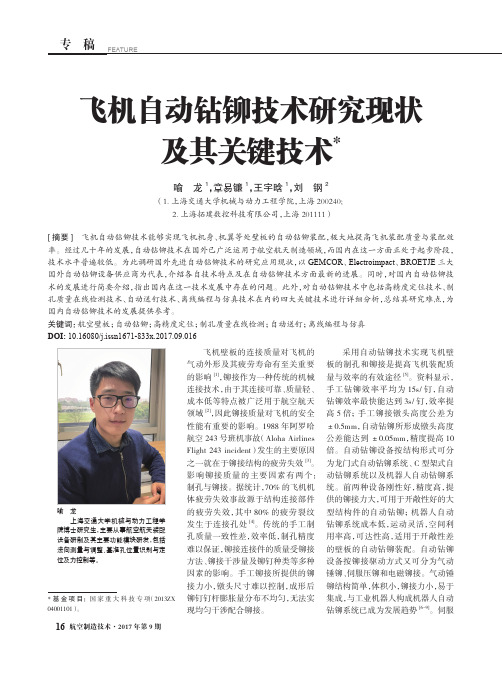
连接技术,由于其连接可靠、质量轻、 手工钻铆效率平均为 15s/ 钉,自动
成本低等特点被广泛用于航空航天 钻铆效率最快能达到 3s/ 钉,效率提 领域 [2],因此铆接质量对飞机的安全 高 5 倍;手工铆接镦头高度公差为
性能有重要的影响。1988 年阿罗哈 ±0.5mm,自动钻铆所形成镦头高度
航空 243 号班机事故(Aloha Airlines 公差能达到 ±0.05mm,精度提高 10
专稿 FEATURE
飞机自动钻铆技术研究现状 及其关键技术*
喻 龙 1,章易镰 1,王宇晗 1,刘 钢 2
(1. 上海交通大学机械与动力工程学院,上海 200240; 2. 上海拓璞数控科技有限公司,上海 201111)
[ 摘要 ] 飞机自动钻铆技术能够实现飞机机身、机翼等处壁板的自动钻铆装配,极大地提高飞机装配质量与装配效 率。经过几十年的发展,自动钻铆技术在国外已广泛运用于航空航天制造领域,而国内在这一方面正处于起步阶段, 技术水平普遍较低。为此调研国外先进自动钻铆技术的研究应用现状,以 GEMCOR、Electroimpact、BROETJE 三大 国外自动钻铆设备供应商为代表,介绍各自技术特点及在自动钻铆技术方面最新的进展。同时,对国内自动钻铆技 术的发展进行简要介绍,指出国内在这一技术发展中存在的问题。此外,对自动钻铆技术中包括高精度定位技术、制 孔质量在线检测技术、自动送钉技术、离线编程与仿真技术在内的四大关键技术进行详细分析,总结其研究难点,为 国内自动钻铆技术的发展提供参考。 关键词:航空壁板;自动钻铆;高精度定位;制孔质量在线检测;自动送钉;离线编程与仿真 DOI: 10.16080/j.issn1671-833x.2017.09.016
16 航空制造技术·2017 年第 9 期
2024年自动钻孔机市场发展现状

2024年自动钻孔机市场发展现状摘要本文分析了自动钻孔机市场的发展现状。
首先介绍了自动钻孔机的定义和功能,接着分析了市场规模、市场竞争状况以及市场发展趋势。
随着科技的不断进步和市场需求的增加,自动钻孔机市场有着巨大的发展潜力。
然后,针对市场中存在的挑战,本文提出了一些解决方案,并对未来市场发展进行了展望。
1. 引言自动钻孔机是一种用于在地面上或土壤中钻孔的机器设备。
它具有自动化功能,可以根据预设的参数和路径进行操作,提高工作效率,减少人力成本。
自动钻孔机广泛应用于建筑、地质勘探、矿山开采等领域,具有广阔的市场前景。
2. 市场规模自动钻孔机市场规模正在逐年扩大。
根据最新的市场调查数据显示,自动钻孔机市场的年复合增长率达到了10%以上。
随着建筑和矿山行业的发展,对自动钻孔机的需求也在不断增加。
目前,自动钻孔机市场的总体规模已经达到数十亿美元。
3. 市场竞争状况自动钻孔机市场的竞争非常激烈。
主要的竞争者包括国内外的机械制造企业和工程机械公司。
这些企业通过不断创新和技术研发来提高产品质量和性能,以增加市场份额。
4. 市场发展趋势自动钻孔机市场的发展存在以下几个趋势:4.1 技术创新随着科技的不断进步,自动钻孔机的技术也在不断创新。
自动化程度越来越高,智能化水平不断提升。
例如,一些自动钻孔机配备了先进的传感器和控制系统,可以实现自动控制和监测,提高工作效率和安全性。
4.2 市场需求增加随着城市化的进程和基础设施建设的不断推进,对自动钻孔机的需求也在不断增加。
建筑工地、矿山和地质勘探等领域对自动钻孔机的需求有望持续增长。
4.3 环保意识提升随着环境保护意识的提高,传统的钻孔方式受到了限制。
自动钻孔机因其高效、精确和对环境影响小的特点,成为替代方案,将受到更多关注和应用。
5. 挑战和解决方案自动钻孔机市场面临着一些挑战,包括技术难题、成本控制和市场竞争等方面。
为了应对这些挑战,可以采取以下措施:•加强技术研发,提升产品性能和质量;•降低自动钻孔机的成本,以提高市场竞争力;•加大市场营销力度,提高产品知名度和市场份额。
铆工技术的前沿发展与未来趋势
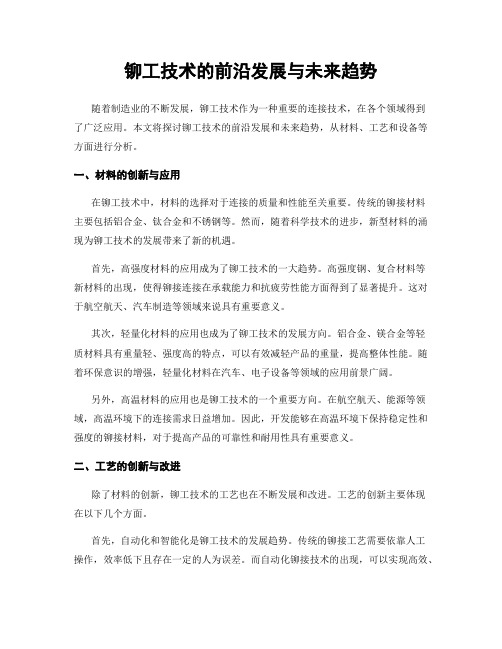
铆工技术的前沿发展与未来趋势随着制造业的不断发展,铆工技术作为一种重要的连接技术,在各个领域得到了广泛应用。
本文将探讨铆工技术的前沿发展和未来趋势,从材料、工艺和设备等方面进行分析。
一、材料的创新与应用在铆工技术中,材料的选择对于连接的质量和性能至关重要。
传统的铆接材料主要包括铝合金、钛合金和不锈钢等。
然而,随着科学技术的进步,新型材料的涌现为铆工技术的发展带来了新的机遇。
首先,高强度材料的应用成为了铆工技术的一大趋势。
高强度钢、复合材料等新材料的出现,使得铆接连接在承载能力和抗疲劳性能方面得到了显著提升。
这对于航空航天、汽车制造等领域来说具有重要意义。
其次,轻量化材料的应用也成为了铆工技术的发展方向。
铝合金、镁合金等轻质材料具有重量轻、强度高的特点,可以有效减轻产品的重量,提高整体性能。
随着环保意识的增强,轻量化材料在汽车、电子设备等领域的应用前景广阔。
另外,高温材料的应用也是铆工技术的一个重要方向。
在航空航天、能源等领域,高温环境下的连接需求日益增加。
因此,开发能够在高温环境下保持稳定性和强度的铆接材料,对于提高产品的可靠性和耐用性具有重要意义。
二、工艺的创新与改进除了材料的创新,铆工技术的工艺也在不断发展和改进。
工艺的创新主要体现在以下几个方面。
首先,自动化和智能化是铆工技术的发展趋势。
传统的铆接工艺需要依靠人工操作,效率低下且存在一定的人为误差。
而自动化铆接技术的出现,可以实现高效、精确的铆接操作,提高生产效率和质量稳定性。
智能化铆接设备的应用,可以通过传感器和控制系统实现实时监测和调整,提高生产过程的可控性和稳定性。
其次,激光铆接技术是铆工技术的一个重要发展方向。
激光铆接技术具有无接触、高精度、快速等优点,可以应用于各种材料的连接,尤其适用于薄板材料和复杂形状的连接。
随着激光技术的不断发展和成熟,激光铆接技术在航空航天、电子设备等领域的应用前景广阔。
另外,电磁铆接技术也是铆工技术的一个研究热点。
国内外锚杆钻机的现状及发展趋势

国内外锚杆钻机的现状及发展趋势锚杆支护是近年来发展较快的一种井巷支护方法,通过锚入围岩内的锚杆,改善围岩本身的力学状态,使支护体与围岩本身形成一个统一的能够承受载荷的结构体,从而提高岩体自身的强度,阻止或延缓围岩的变形发展,有效地保持围岩的完整性和巷道断面形状。
锚杆钻机是锚杆支护施工中的关键施工设备。
锚杆支护的施工速度和支护质量的好坏很大程度上取决于锚杆钻机。
锚杆支护钻机技术已是影响锚杆支护施工速度、质量、效率的关键技术之一。
因此,研究性能好、可靠性高、符合我国煤矿实际情况的锚杆钻机是发展我国锚杆支护技术关键技术之一。
1 国外锚杆钻机的现状及发展趋势早在20世纪40年代,国外已将锚杆支护技术应用于巷道支护工程。
随着锚杆支护技术发展,锚杆钻机作为锚杆支护的主要施工机具,就成为该项技术发展的重点。
经过几十年的研究与攻关,锚杆钻机已从当初的功能单一、技术含量低、可靠性差、安全性差、笨重发展到今天的功能齐全、可靠性好、安全性好、自动化水平高的新型钻机。
在锚杆支护技术应用初期,国外在锚杆支护施工中采用普通凿岩机械钻凿锚杆孔,人工安装锚杆,用扳手拧紧螺母。
到20世纪50年代初,美国、瑞典等西方国家已广泛应用伸缩式气动凿岩机钻凿顶板锚杆孔,同时,美国已研制成功钻车式锚杆钻机并在支护工程中推广使用。
国外仅用了10 a左右时间就实现了锚杆支护的机械化。
20世纪50年代末,随着锚杆支护理论及设计方法的不断完善,英国等国家率先将锚杆支护技术应用于煤矿巷道支护。
为适应煤矿巷道断面积较小的特点,英国、波兰等国研发了单体电动和液压回转式锚杆钻机。
20世纪70年代,为适应大断面巷道锚杆支护快速施工,美国英格索兰、法国赛克马、瑞典阿特拉斯等凿岩设备公司陆续推出了功能多、机械化程度高的台车式锚杆钻装机。
该类钻机既能钻锚杆孔,又能安装锚杆,基本实现了锚杆孔施工、锚杆安装的机械化。
20世纪80年代至20世纪90年代,澳大利亚成功研制了轻型支腿式气动锚杆钻机,并在澳大利亚、英国、中国、波兰和印度等国的煤矿得到广泛应用。
- 1、下载文档前请自行甄别文档内容的完整性,平台不提供额外的编辑、内容补充、找答案等附加服务。
- 2、"仅部分预览"的文档,不可在线预览部分如存在完整性等问题,可反馈申请退款(可完整预览的文档不适用该条件!)。
- 3、如文档侵犯您的权益,请联系客服反馈,我们会尽快为您处理(人工客服工作时间:9:00-18:30)。
国内外自动钻铆技术的发展现状及应用西飞国际设备维修中心 楼阿莉当代飞机制造技术的发展,对疲劳寿命、密封、防腐的要求越来越高,为了满足飞机对各种性能的要求,航空制造领域发展了各种先进技术,其中机械连接技术的干涉配合无头铆钉自动钻铆技术就是其中之一。
国外铆接装配技术几十年的应用证明,采用自动钻铆机后装配效率至少比手工铆接装配提高10倍,并能节约安装成本,改善劳动条件,更主要的是能够确保安装质量,大大减少人为因素造成的缺陷。
现在采用自动钻铆机已成为改善飞机性能的主要工艺措施之一。
美国是最早发展自动钻铆技术的国家,早在 50 年代初就已在飞机铆接装配生产线上应用了自动钻铆机,经过 50 多年的发展,现在世界各航空工业发达国家都已广泛采用这项技术。
自动钻铆技术主要包含以下内容:(1) 设备的研制、开发。
以不同飞机的结构为对象,发展多种型号的数控自动钻铆系统,不仅能铆接壁板,而且还可铆接各种组件,如肋、框、梁、翼面、前缘等,从而使自动钻铆系统的工作覆盖面大幅度增加,使整个飞机的铆接工作有较大的改观。
(2) 对各种干涉配合新型紧固件进行自动安装。
通过增加附件,可以对两件型紧固件进行自动安装,如环槽钉、高锁螺栓、锥形螺栓等,也可对无头铆钉进行干涉配合铆接,从而提高铆接结构疲劳寿命5~6倍,对提高飞机整体油箱的密封铆接质量有重大意义。
(3) 自动钻铆工艺。
结构铆接的整个过程通过预先编程全部由CNC程序控制,自动钻铆工艺是在一台设备上一次性地连续完成夹紧、钻孔、锪窝、注胶、放铆、铣平等工序。
由于机床带有高速、高精度的转削主轴头,一次进给即能钻出0.005mm以内高精度的孔,同时埋头窝的深度也可精确控制在±0.01mm以内,再加上机床由数控系统控制各轴运动,并采用精密自动化工装夹具,使得铆钉镦头高度保持一致,不受人为因素的影响。
所有这些因素均使钉杆在孔中充填质量大为改善,从而有利于提高细节疲劳强度许用值。
此外,由于钻孔时铆接件处在高的夹紧力下,层间不会产生毛刺和进入切削,可以减小疲劳载荷下发生磨蚀损伤的程度,这些均有利于提高接头的疲劳强度。
(4) 数字化铆接的实现。
现代飞自动钻铆技术不只是工艺机械化、自动化的要求,更主要的还是飞机本身性能的要求。
目前世界各航空工业发达国家都已广泛采用自动钻铆技术。
随着我国航空工业研制的新机种的性能、水平不断提高,在铆接装配中发展自动钻铆技术已经势在必行50航空制造技术2005年第6期FORUM机设计已实现数字化,开发应用脱机编程系统使得飞机各组件的数模通过脱机编程系统生成数控铆接程序,实现各种组件的铆接数字化,对实现飞机制造数字化具有重大意义。
目前,波音、空客的有关飞机结构设计手册中明确规定: 为确保连接质量,设计时应使自动化铆接获得最大限度的使用。
由此可以看出,自动钻铆技术不只是工艺机械化、自动化的要求,更主要的还是飞机本身性能的要求。
由于设计上的这一要求,就使得自动钻铆技术的发展具有生命力。
所以近20年来,自动钻铆技术得到迅速发展。
美国自动钻铆机的最早制造厂商是GEMCOR(通用电气机械公司),它是向世界各国飞机制造行业提供自动钻铆机的主要厂商之一。
该公司生产的系列化产品质量可靠,并配套有各种型号的数控托架。
到现在为止,销售的自动钻铆机数量已达 2000台以上,其中190台具有定位系统。
公司生产的自动钻铆机主要型号有G200、G300、G400、G900、G666、G39A、G4013、G4026、G5013。
其中 G200、G400 型是较早的型号,G300为比较通用的型号,而G900型的功能比较齐全。
具有无头铆钉钻铆功能的型号有G900、G666、 G39A 、G4013、 G4026、G5013。
近几年无头铆钉的工作原理有所发展,机床采用GEMCOR专利的SQUEEZE/SQUEEZE双挤铆方式,先预挤铆,再进行挤铆,不仅能保证上下铆头同步成形上下镦头,而且铆接质量大大提高。
各种型号机床可通过改变下铆砧形状和尺寸来适应各种结构的要求。
GEMCOR 公司生产的数控托架(也称自动定位系统)主要型号有 G63、G79、G86、747WRS、G2000等。
(1) G63自动定位系统。
G63的工作原理是:钻铆机固定不动,托架的框架固定在两端的架车上,架车在地面导轨上纵向移动,所有X、Y、Z轴方向的运动由伺服控制的液压马达通过滚珠丝杠来带动,而绕X向的旋转则依靠伺服操作液压作动筒。
该系统应用于空客公司A300机翼壁板的装配中,与G666Sp-145无头铆钉钻铆机配套组成自动钻铆系统。
在美国VOUGHT公司的波音747机身壁板的装配中,它与G400B/39A-120 钻铆机配套组成自动钻铆系统。
(2) G79自动定位系统。
它与G400BH/39A-120自动钻铆机配套用于MITSUBISHI公司转包生产波音767机身段的装配。
G79为CNC控制、六坐标、中型自动定位系统。
它是 GEMCOR 产品中最通用、最多功能的定位系统。
铆接机作X向运动,而托架作Y、Z和a、b、c向的运动(a、b、c为绕X、Y、Z轴的转动)。
所有的动作均由自动和手动控制的电伺服马达驱动。
(3) G86自动定位系统。
它可以与 G200、G300、G400、G900、G4013、G4026、G5013等配套组成自动钻铆系统。
G86的CNC定位系统有独特的低重心设计,这样可以保证即使在高速运行的状态下也具有稳定性和可重复性。
托架可以通过宽度调节容纳不同大小的夹具。
目前,该机型已发展成全电动自动铆接系统,铆接方式也从液压镦铆发展为SQUEEZE/SQUEEZE的双挤铆方式;10/32"以下的铆钉铆接驱动采用全电动方式,用滚柱丝杠传动,并配有自动换刀装置。
近两年开发了脱机编程系统,可与CATIA V5进行数据交换,实现数字化铆接。
(4) ROUSIER机翼钻铆系统。
该钻铆机作X、Y、Z、a、b向运动,而工件的支持结构固定不动。
X、Y轴的定位由数控系统控制,而Z、a、b的运动则通过法向传感器/伺服系统来控制。
该系统用于钻铆波音747/767机翼壁板。
世界各航空工业发达国家的自动钻铆技术基本上都是从美国引进的,然后再进行国产化,以适应本国航空工业发展的需要。
如原苏联在 70年代从美国引进GEMCOR的 G300型和G666型自动钻铆机,并在此基础上研制出自己的系列自动钻铆机及数控托架,并已广泛装备于各飞机工厂,主要产品有AK-5.5-2.4、AK-2.2-0.5等,用于飞机机身、机翼的装配,机铆系数可达70‰。
但其自动钻铆机的控制系统较落后,故其产品未打入国际市场。
此外,法国在从美国引进各种型号自动钻铆机的基础上,从 80 年代起也开始进行国产化,其产品曾打入国际市场与美国产品竞争,法国自动钻铆机在国外推销较多的产品为 recoules et fils公司的PRECA300和PRECA600,其性能与美国G300相当,上动力头也为3个主轴。
该公司现已倒闭。
德国在发展自动钻铆技术方面走的是另一条道路,在此项技术的应用与发展中,凭借其雄厚的资金、技术国外自动钻铆技术发展简况西飞引进的GEMCOR G400自动钻铆机51航空制造技术2005年第6期自动钻铆技术Automatic Drilling and Riveting Technology力量,一方面大量引进先进的自动钻铆系统和柔性装配系统,另一方面自己也积极研制开发高自动化的铆接装配系统。
故德国的自动钻铆技术虽然起步较晚,但已比较先进,脱机编程系统已应用成熟,可与CATIA V5进行数据交换,实现数字化铆接。
目前BR歍JE公司的机身铆接柔性工装和柔性装配生产线在世界处于领先地位。
美国ELECTROIMPACT(EI)公司是一家1986年成立的、迅速发展的研制开发高自动化卧式铆接装配系统的有潜力的公司。
公司生产的E4000型系列自动钻铆系统用于空客公司的A320、A340、A380机翼的铆接。
EI公司采用电磁铆接,特点是电磁力大,速度快,更适合大铆钉、大型机翼壁板的铆接。
由于采用卧式主轴结构,铆接时几乎没有后坐力,同时工件不动,故铆接质量高。
EI公司直接在CATIA V5平台上开发的脱机编程系统可实现数字化铆接。
2003年,EI公司为空客建立了两条165m长的生产线,共8台E4380设备,分别加工A380上下壁板。
随着我国航空工业研制的新机种的性能、水平不断提高,在铆接装配中发展自动钻铆技术已经势在必行。
我国自动钻铆机的研制起步较早,70年代初,原航空部曾组织有关单位研制过各种型号的自动钻柳机,但因种种原因没能坚持下去。
分析其原因主要还是当时研制或生产的飞机机种对使用自动钻铆机没有迫切要求,由于没有型号需求的牵引,使得继续开展这项工作缺乏动力,加之当时研制的设备中所采用的元件、控制系统等均存在各种质量问题,致使工作被迫中断。
到了80 年代中期,各厂外协加工项目增加,开始承担一些民机小部件(如垂尾、平尾)的铆接装配,因国外要求进行这些部件的铆接装配时必须使用自动钻铆机,以保证达到所要求的质量,于是自动钻铆机又再度得到应用。
此外,我国的干线飞机研制也正在逐步开展,为了确保干线飞机的疲劳寿命和安装质量要求,也迫切要求尽快发展我国的自动钻铆技术。
此后,我国一些航空工厂先后引进了自动钻铆机。
1985年,西飞公司引进一台从波音公司退役的二手设备G400,1992 年引进G900。
这两台机床均配以手动托架,分别加工美国波音和前麦道公司的垂尾平尾及法航、意航、加航的零件。
随着国际间技术交流的不断深化,我国又同美国麦道公司合作生产干线机 MD-90-30。
西飞公司的两台自动钻铆机已满足不了生产的需求。
1993年又引进了GEMCOR公司的G4026SXX-120型自动钻铆机,用于麦道公司MD-90-30等飞机的机翼壁板的铆接装配生产。
该机床引进时,未引进托架装置,1995年西飞公司同西工大联合研究、设计、制造了该机翼托架,采用了 Z坐标两立柱支撑的结构形式。
由于受当时工艺制造水平的限制,围框刚性不足,存在一定问题,而麦道干线机生产的下马使该项科研最终未进行下去。
1998年西飞又引进APS公司的RMS335钻铆机,取代G400机床。
与此同时,成飞公司先后引进了G4026、RMS335钻铆机,沈飞公司也引进法国的PRECA 300和BR歍JE的BA96,2000年陕飞公司引进GEMCOR GRS6R30-120,配有自动送钉装置和法线传感器,但均未配置全自动定位系统。
飞机机械连接自动钻铆技术在国外发展极为迅速,而我国与国际先进水平差距越来越大。
我们应从整个航空工业全局的生存和发展出发,从技术经济综合效益考虑,努力逐步缩小与国外先进水平的差距。