金属的表面处理硬度
金属表面处理方法6种
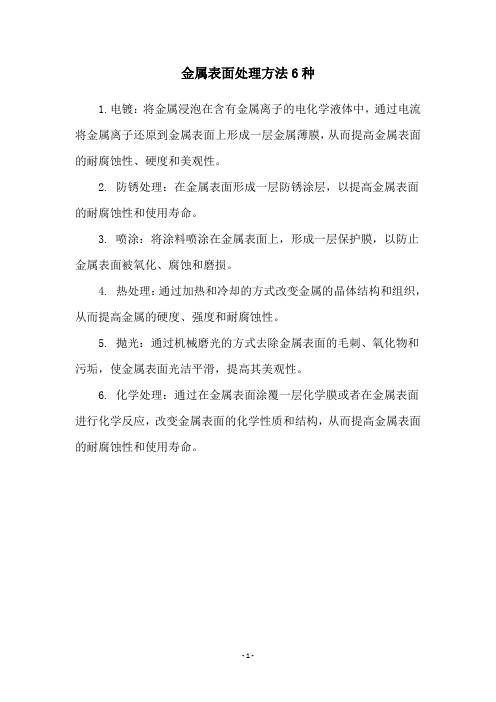
金属表面处理方法6种
1.电镀:将金属浸泡在含有金属离子的电化学液体中,通过电流将金属离子还原到金属表面上形成一层金属薄膜,从而提高金属表面的耐腐蚀性、硬度和美观性。
2. 防锈处理:在金属表面形成一层防锈涂层,以提高金属表面的耐腐蚀性和使用寿命。
3. 喷涂:将涂料喷涂在金属表面上,形成一层保护膜,以防止金属表面被氧化、腐蚀和磨损。
4. 热处理:通过加热和冷却的方式改变金属的晶体结构和组织,从而提高金属的硬度、强度和耐腐蚀性。
5. 抛光:通过机械磨光的方式去除金属表面的毛刺、氧化物和污垢,使金属表面光洁平滑,提高其美观性。
6. 化学处理:通过在金属表面涂覆一层化学膜或者在金属表面进行化学反应,改变金属表面的化学性质和结构,从而提高金属表面的耐腐蚀性和使用寿命。
- 1 -。
常用金属表面处理工艺及技术

金属表面处理工艺一、表面热处理1、表面淬火 n 表面淬火是指在不改变钢的化学成分及心部组织情况下,利用快速加热将表层奥氏体化后进行淬火以 强化零件表面的热处理方法。
感火焰加热 应加 热n 表面淬火目的: n ① 使表面具有高的硬度、耐磨性和疲劳极限; n ② 心部在保持一定的强度、硬度的条件下,具有足够的塑性和韧性。
即表硬里韧。
n 适用于承受弯曲、扭转、摩擦和冲击的零件。
轴 的 感 应 加加 热 表 面 淬淬 火n ①表面淬火用材料 n ⑴ 0.4-0.5%C的中碳钢。
n 含碳量过低,则表面硬度、耐磨性下降。
n 含碳量过高,心部韧性下降; n ⑵ 铸铁 提高其表面耐磨性。
机床导轨表面淬火齿轮n ②预备热处理 n ⑴工艺: n 对于结构钢为调质或正火。
n 前者性能高,用于要求高的重要件,后者用于要求不高的普 通件。
n ⑵目的: n 为表面淬火作组织准备; n 获得最终心部组织。
回火索氏体 索氏体n ③表面淬火后的回火 n 采用低温回火,温度不高于200℃。
n 回火目的为降低内应力,保留淬火高硬度、耐磨性。
n ④表面淬火+低温回火后的组织 n 表层组织为M回;心部组织为S回(调质)或F+S(正火)。
感应加热表面淬火 感应淬火机床n ⑤表面淬火常用加热方法 n ⑴ 感应加热: 利用交变电流在工件表面感应巨大涡流, 使工件表面迅速加热的方法。
感应加热 表面淬火示意图n 感应加热分为: n 高频感应加热频率为250-300KHz,淬 硬层深度0.5-2mm火传 感动 应轴 器连续 淬感应加热表面淬火齿轮的截面图n 中频感应加热 频 率 为 25008000Hz , 淬 硬 层 深度2-10mm。
中频感应加热表面淬火的机车凸轮轴各种感应器n 工频感应加热 n 频率为50Hz,淬硬层深度10-15 mm感应穿透加热各种感应器n ⑵ 火焰加热: 利用乙炔火焰直接加 热工件表面的方法。
成本低,但质 量不易控制。
金属表面处理国家标准
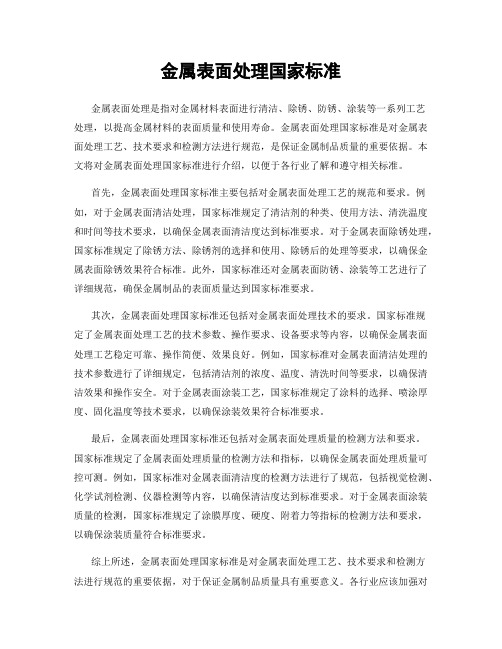
金属表面处理国家标准金属表面处理是指对金属材料表面进行清洁、除锈、防锈、涂装等一系列工艺处理,以提高金属材料的表面质量和使用寿命。
金属表面处理国家标准是对金属表面处理工艺、技术要求和检测方法进行规范,是保证金属制品质量的重要依据。
本文将对金属表面处理国家标准进行介绍,以便于各行业了解和遵守相关标准。
首先,金属表面处理国家标准主要包括对金属表面处理工艺的规范和要求。
例如,对于金属表面清洁处理,国家标准规定了清洁剂的种类、使用方法、清洗温度和时间等技术要求,以确保金属表面清洁度达到标准要求。
对于金属表面除锈处理,国家标准规定了除锈方法、除锈剂的选择和使用、除锈后的处理等要求,以确保金属表面除锈效果符合标准。
此外,国家标准还对金属表面防锈、涂装等工艺进行了详细规范,确保金属制品的表面质量达到国家标准要求。
其次,金属表面处理国家标准还包括对金属表面处理技术的要求。
国家标准规定了金属表面处理工艺的技术参数、操作要求、设备要求等内容,以确保金属表面处理工艺稳定可靠、操作简便、效果良好。
例如,国家标准对金属表面清洁处理的技术参数进行了详细规定,包括清洁剂的浓度、温度、清洗时间等要求,以确保清洁效果和操作安全。
对于金属表面涂装工艺,国家标准规定了涂料的选择、喷涂厚度、固化温度等技术要求,以确保涂装效果符合标准要求。
最后,金属表面处理国家标准还包括对金属表面处理质量的检测方法和要求。
国家标准规定了金属表面处理质量的检测方法和指标,以确保金属表面处理质量可控可测。
例如,国家标准对金属表面清洁度的检测方法进行了规范,包括视觉检测、化学试剂检测、仪器检测等内容,以确保清洁度达到标准要求。
对于金属表面涂装质量的检测,国家标准规定了涂膜厚度、硬度、附着力等指标的检测方法和要求,以确保涂装质量符合标准要求。
综上所述,金属表面处理国家标准是对金属表面处理工艺、技术要求和检测方法进行规范的重要依据,对于保证金属制品质量具有重要意义。
金属表面处理方法
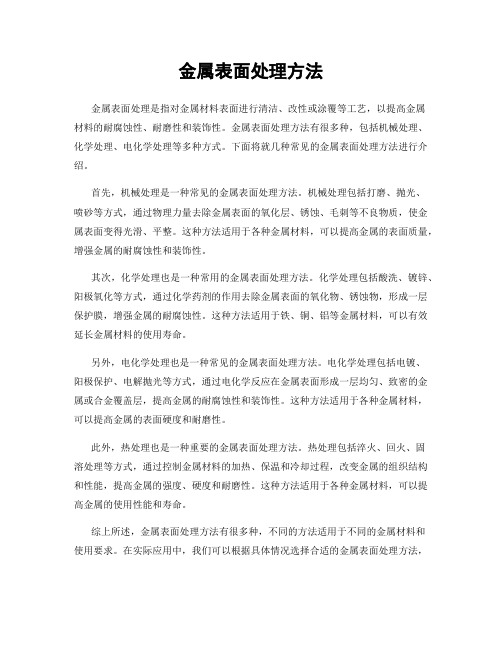
金属表面处理方法金属表面处理是指对金属材料表面进行清洁、改性或涂覆等工艺,以提高金属材料的耐腐蚀性、耐磨性和装饰性。
金属表面处理方法有很多种,包括机械处理、化学处理、电化学处理等多种方式。
下面将就几种常见的金属表面处理方法进行介绍。
首先,机械处理是一种常见的金属表面处理方法。
机械处理包括打磨、抛光、喷砂等方式,通过物理力量去除金属表面的氧化层、锈蚀、毛刺等不良物质,使金属表面变得光滑、平整。
这种方法适用于各种金属材料,可以提高金属的表面质量,增强金属的耐腐蚀性和装饰性。
其次,化学处理也是一种常用的金属表面处理方法。
化学处理包括酸洗、镀锌、阳极氧化等方式,通过化学药剂的作用去除金属表面的氧化物、锈蚀物,形成一层保护膜,增强金属的耐腐蚀性。
这种方法适用于铁、铜、铝等金属材料,可以有效延长金属材料的使用寿命。
另外,电化学处理也是一种常见的金属表面处理方法。
电化学处理包括电镀、阳极保护、电解抛光等方式,通过电化学反应在金属表面形成一层均匀、致密的金属或合金覆盖层,提高金属的耐腐蚀性和装饰性。
这种方法适用于各种金属材料,可以提高金属的表面硬度和耐磨性。
此外,热处理也是一种重要的金属表面处理方法。
热处理包括淬火、回火、固溶处理等方式,通过控制金属材料的加热、保温和冷却过程,改变金属的组织结构和性能,提高金属的强度、硬度和耐磨性。
这种方法适用于各种金属材料,可以提高金属的使用性能和寿命。
综上所述,金属表面处理方法有很多种,不同的方法适用于不同的金属材料和使用要求。
在实际应用中,我们可以根据具体情况选择合适的金属表面处理方法,以确保金属材料具有良好的表面质量和使用性能。
希望本文介绍的金属表面处理方法对大家有所帮助。
金属材料的表面处理与涂层技术

金属材料的表面处理与涂层技术金属材料是现代工业生产和生活中极其重要的基础材料之一,在机械、建筑、汽车等领域都有着广泛的应用。
然而,在使用过程中,金属材料的表面容易受到腐蚀、磨损等影响,降低了材料的质量和寿命。
因此,对金属材料进行表面处理和涂层技术的研究和应用具有重要意义。
一、表面处理技术表面处理技术是指对金属材料表面进行机械或化学加工以改变其性质的一系列工艺。
常见的表面处理技术包括抛光、酸洗、酸碱清洗、电化学抛光和喷砂等。
这些处理方法能够去除金属表面的氧化膜和污垢,并在金属表面形成一层适当的薄膜,增强材料的耐腐蚀性和耐磨性。
例如,在汽车制造中,对金属材料进行抛光、酸洗和酸碱清洗处理后,在零件装配前进行防腐涂层处理,能够大大增加汽车的使用寿命。
二、涂层技术涂层技术是指将一层薄膜涂覆到金属表面上以改变其性质的工艺。
涂层技术主要包括物理镀膜和化学镀膜两种类型。
1.物理镀膜物理镀膜是将金属薄膜通过真空蒸发或离子镀放在金属表面上的一种涂层技术。
经过物理镀膜处理后的金属材料表面能够形成一层均匀、密实、质量稳定、外观优美的保护层,能够提高金属表面的硬度和耐磨性,从而减少金属表面的磨损和腐蚀程度,延长其使用寿命。
物理镀膜广泛应用于电子、光学、医疗、航天等领域。
2.化学镀膜化学镀膜是将一层化合物电镀到金属表面上的一种涂层技术。
当金属表面与镀液中的化学物质发生反应时,会在金属表面上形成一层稳定、均匀、具有机械强度和化学稳定性的保护层。
化学镀膜涂层具有较好的耐腐蚀性和耐磨性,可以延长金属材料的使用寿命。
化学镀膜广泛应用于制造业、航空、汽车等领域。
三、表面处理与涂层技术的应用表面处理与涂层技术的应用十分广泛,在实际生产中有着举足轻重的地位。
例如,在航空航天领域,表面处理技术可以大大增强飞机材料的耐腐蚀性和耐磨性,从而增加飞机的安全性和寿命。
在汽车工业中,抗腐蚀和防火涂料有助于提高汽车的安全性和使用寿命。
此外,表面处理与涂层技术在建筑、医疗、电子和制造等行业中也得到了广泛应用。
金属表面处理标准说明及各种标准比较

金属表面处理标准说明及各种标准比较编写:审核:1.金属的表面处理标准GB8923-88 中国国家标准ISO8501-1:1988 国际标准化组织标准SIS055900-1967 瑞典标准SSPC-SP2,3,5,6,7和10 美国钢结构涂装协会表面处理标准 BS4232 英国标准DIN55928 德国标准JSRA SPSS 日本造船研究协会标准2.各种金属表面处理标准说明2.1 金属表面处理中影响最大的标准是瑞典标准SIS 05 5900 1967,该标准最早由瑞典腐蚀研究所、美国测试和材料协会(ASTM)和钢结构涂装协会(SSPC)联合制定。
其它国家的标准,比如德国DIN 55928、丹麦DS 2019 等都是在此基础上建立起来的。
瑞典标准现在已经与国际标准ISO 8501-1:1988合并且由后者取代。
2.2 ISO8501则是现在普遍采用的国际标准。
美国由于科技力量的强大,SSPC/NACE是他们使用的主要标准而不使用ISO国际标准,并且随着NACE 在全球推广涂装检查培训认证,以及很多钢结构设计机构也使用这一标准,因此在中国也经常会遇到并使用SSPC/NACE标准。
2.3 中国的国家标准GB8923等效采用于ISO8501-1:1988。
3.国标GB8923-88 的除锈等级3.1 喷射或抛射除锈以字母“Sa”表示。
本标准订有四个除锈等级:3.1.1 Sa1 轻度的喷射或抛射除锈钢材表面应无可见的油脂和污垢,并且没有附着不牢的氧化皮,铁锈和油漆涂层等附着物。
Sa2 彻底的喷射或抛射除锈钢材表面应无可见的油脂和污垢,并且氧化皮,铁锈和油漆涂层等附着物已基本清除,其残留物应该是附着牢固的。
3.1.2 Sa2.5 非常彻底的喷射或抛射除锈钢材表面应无可见的油脂,污垢,氧化皮,铁锈和油漆涂层等附着物,任何残留的痕迹应仅是点状或条纹状的轻微色斑。
3.1.3 Sa3 钢材表面外观洁净的喷射或抛射除锈钢材表面应无可见的油脂,污垢,氧化皮,铁锈和油漆涂层等附着物,该表面应显示均匀的金属色泽。
金属表面处理—喷丸、抛丸、喷砂

一、喷丸喷丸使用高压风机或压缩空气作动力,将~2.5mm直径的弹丸喷射出去,冲击金属表面。
广泛应用于金属表面的消光、去氧化皮;提高零件机械强度、抗疲劳性、耐磨性和耐腐蚀性;消除铸、锻、焊件的残余应力等。
1、表面清理功能用喷丸进行表面处理,打击力大,清理效果明显,动力消耗大。
一般喷丸用来消除厚度不小于2~6mm的或不要求保持准确尺寸及轮廓的中型、大型金属制品以及铸、锻件上的氧化皮、铁锈、型砂及旧漆膜,是表面涂(镀)覆前段一种清理方法。
原理:当钢丸打击到工件表面(无论是喷丸或抛丸)使金属基材发生变形,由于Fe3O4和Fe2O3没有塑性,破碎后剥离,而油膜与基材一同变形,所以对有油污的工件,喷丸无法彻底清除油污。
2、喷丸强化功能原理:当钢丸撞击金属零件表面上,宛如一个微型棒锤敲打表面,捶出小压痕或凹陷。
为了形成凹陷,金属表层必定会产生拉伸。
表层下,压缩的晶粒试图将表面恢复到原来形状,从而产生一个高度压缩力作用下的半球。
无数凹陷重叠形成均匀的残余应力层。
最终,零件在压应力层保护下,极大程度地改善了抗疲劳强度。
如:将高速弹丸喷射到弹簧表面,使弹簧表层发生塑性变形,形成一定而形成一定厚度的强化层,强化层内形成较高的残余应力,由于弹簧表面压应力的存在,当弹簧承受载荷时可以抵消一部分抗应力,从而提高弹簧的疲劳强度。
喷丸强化分为一般喷丸和应力喷丸。
一般处理时,钢板在自由状态下,用高速钢丸打击钢板的表面,使其表面产生预压应力,以减少工作中钢板表面的拉应力。
应力喷丸是将钢板在一定的作用力下预先弯曲,然后进行喷丸处理。
3、喷丸使用的丸的种类:铸钢丸、铸铁丸、玻璃丸铸钢丸,硬度一般为40~50HRC,加工硬金属时,可把硬度提高到57~62HRC。
铸钢丸的韧性较好,使用广泛,其使用寿命为铸铁丸的几倍。
喷丸粒度一般在~1.2mm为宜,喷丸强度要求越高,粒度相对加大。
4、表面清洁质量⑴、Sa1—手工刷除清理级(或清扫级)Sa1级处理的技术标准:工件表面应不可见油污、油脂、残留氧化皮、锈斑和残留油漆等污物;处理后表面上出现大量分别均匀的金属斑点。
金属表面处理工艺技术指标
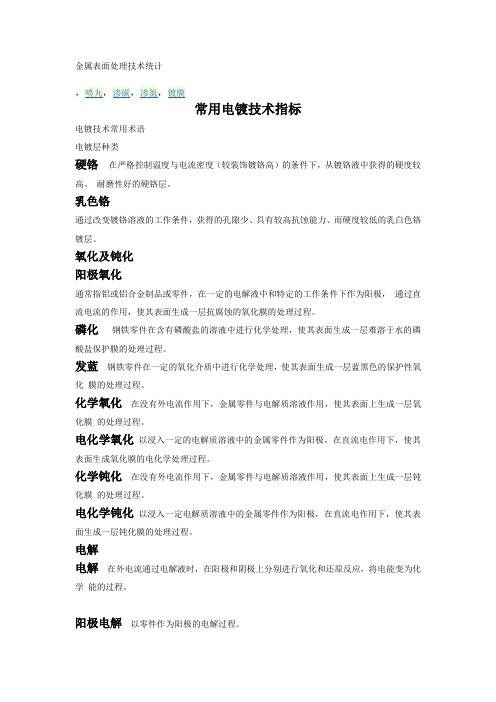
金属表面处理技术统计,喷丸,渗碳,渗氮,镀膜常用电镀技术指标电镀技术常用术语电镀层种类硬铬在严格控制温度与电流密度(较装饰镀铬高)的条件下,从镀铬液中获得的硬度较高、耐磨性好的硬铬层。
乳色铬通过改变镀铬溶液的工作条件,获得的孔隙少、具有较高抗蚀能力、而硬度较低的乳白色铬镀层。
氧化及钝化阳极氧化通常指铝或铝合金制品或零件,在一定的电解液中和特定的工作条件下作为阳极,通过直流电流的作用,使其表面生成一层抗腐蚀的氧化膜的处理过程。
磷化钢铁零件在含有磷酸盐的溶液中进行化学处理,使其表面生成一层难溶于水的磷酸盐保护膜的处理过程。
发蓝钢铁零件在一定的氧化介质中进行化学处理,使其表面生成一层蓝黑色的保护性氧化膜的处理过程。
化学氧化在没有外电流作用下,金属零件与电解质溶液作用,使其表面上生成一层氧化膜的处理过程。
电化学氧化以浸入一定的电解质溶液中的金属零件作为阳极,在直流电作用下,使其表面生成氧化膜的电化学处理过程。
化学钝化在没有外电流作用下,金属零件与电解质溶液作用,使其表面上生成一层钝化膜的处理过程。
电化学钝化以浸入一定电解质溶液中的金属零件作为阳极,在直流电作用下,使其表面生成一层钝化膜的处理过程。
电解电解在外电流通过电解液时,在阳极和阴极上分别进行氧化和还原反应,将电能变为化学能的过程。
阳极电解以零件作为阳极的电解过程。
阴极电解以零件作为阴极的电解过程。
镀前处理化学除油在含碱的溶液中,借助皂化和乳化作用,除去零件或制品表面油垢的过程。
有机溶剂除油利用有机溶剂对油垢的溶解作用,除去零件或制品表面油垢的过程。
电化学除油(即电解除油)在含有碱的溶液中,以零件作为阳极或阴极,在电流作用下,除去零件或制品表面油垢的过程。
化学酸洗在含酸的溶液中,除去金属零件表面的锈蚀物和氧化物的过程。
化学抛光金属零件在一定组成的溶液中和特定条件下,进行短时间的浸蚀,从而将零件表面整平,获得比较光亮的表面的过程。
磨光利用磨轮来磨削零件表面上的粗糙不平处,从而提高零件表面的平整程度的过程。
金属表面加硬的方法有哪些

金属表面在各种热处理、机械加工、运输的过程中,不可避免地会产生腐蚀、随着油污和杂质等,产生氧化现象,这就需要进行表面处理。
常用的表面加硬方法有:
一、QPQ工艺处理
它是一种先进的表面处理工艺。
具有良好的耐磨性、良好的耐腐蚀性、良好的耐疲劳性、极小的变形、低碳环保、可替代多道工序,降低时间成本。
二、渗碳处理
在渗碳炉中将低碳钢表面碳含量增至规定范围然后进行淬火,使表面硬度达到HRc56~62,然后低温回火以消除应力和稳定组织。
三、氮化处理
氮化是在氮化炉中进行,因此变形小。
氮化后一般可不加工。
氮化硬度要根据材质而定。
需要注意的是设计时应尽可能采用整体氮化处理,因为氮化层本身对使用来说只有益处,没必要加工处理掉。
四、表面淬火
工艺简单而灵活,适合局部处理,特别适合于提高耐磨性的场合。
由于只加热表面层,心部强度保持着表淬前的状态。
表面淬火一般工艺是高频感应加热、中频感应加热或火焰加热,喷水冷却,然后进行低温回火。
表面淬火后零件表面将产生很大的残余压应力,因而使材料的疲劳强度大大提高。
焦作汇鑫恒机械制造有限公司是一家主要做金属模具表面加硬处理的专业性技术公司,主要采用QPQ处理工艺。
怎样提高金属的硬度
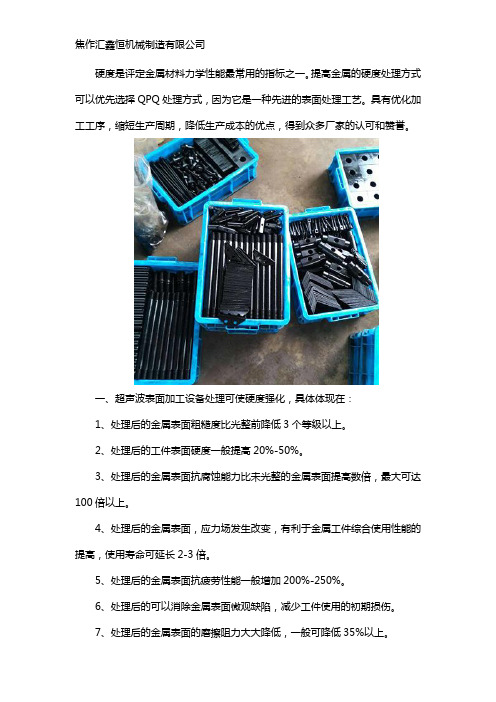
硬度是评定金属材料力学性能最常用的指标之一。
提高金属的硬度处理方式可以优先选择QPQ处理方式,因为它是一种先进的表面处理工艺。
具有优化加工工序,缩短生产周期,降低生产成本的优点,得到众多厂家的认可和赞誉。
一、超声波表面加工设备处理可使硬度强化,具体体现在:1、处理后的金属表面粗糙度比光整前降低3个等级以上。
2、处理后的工件表面硬度一般提高20%-50%。
3、处理后的金属表面抗腐蚀能力比未光整的金属表面提高数倍,最大可达100倍以上。
4、处理后的金属表面,应力场发生改变,有利于金属工件综合使用性能的提高,使用寿命可延长2-3倍。
5、处理后的金属表面抗疲劳性能一般增加200%-250%。
6、处理后的可以消除金属表面微观缺陷,减少工件使用的初期损伤。
7、处理后的金属表面的磨擦阻力大大降低,一般可降低35%以上。
二、采用(溶胶-凝胶法)纳米技术制造,新型薄涂层处理液。
高硬度具有良好的抗酸渍性,可用于不锈钢,铝、镁、铜、锌等金属,作为保护涂层使用。
目前,QPQ表面改性技术在国内也得到大量推广应用,尤其在汽车、摩托车、纺机、机床、电器开关、工模具上使用效果非常突出。
其具体的特点如下:1 良好的耐磨性、耐疲劳性能该工艺能极大地提高各种黑色金属零件表面的硬度和耐磨性,降低摩擦系数。
产品经过QPQ处理后,耐磨性比常规淬火、高频淬火高16倍以上,比20#钢渗碳淬火高9倍以上,比镀硬铬和离子氮化高2倍以上。
疲劳试验表明:该工艺可使中碳钢的疲劳强度提高40%以上,比离子氮化,气体氮化效果均好。
该工艺特别适合于形状复杂的零件,解决技术关键,让变形难题迎刃而解。
2 良好的抗腐蚀性能对几种不同材料、不同工艺处理的样品按同样的试验条件,按ASTMBll7标准进行了连续喷雾试验,盐雾试验温度35±2℃,相对湿度>95%,5%NaCL 水溶液喷雾。
试验结果表明,经QPQ处理后的零件抗蚀性是1Crl8Ni9Ti不锈钢的5倍,是镀硬铬的70倍,是发黑的280倍。
硬度和粗糙度的关系
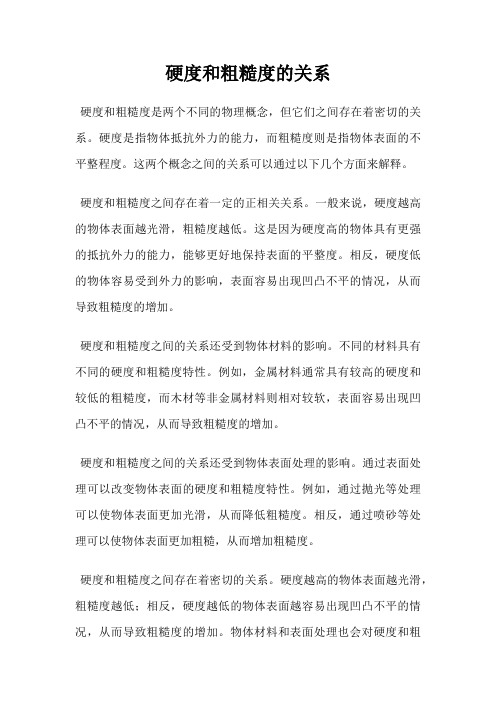
硬度和粗糙度的关系
硬度和粗糙度是两个不同的物理概念,但它们之间存在着密切的关系。
硬度是指物体抵抗外力的能力,而粗糙度则是指物体表面的不平整程度。
这两个概念之间的关系可以通过以下几个方面来解释。
硬度和粗糙度之间存在着一定的正相关关系。
一般来说,硬度越高的物体表面越光滑,粗糙度越低。
这是因为硬度高的物体具有更强的抵抗外力的能力,能够更好地保持表面的平整度。
相反,硬度低的物体容易受到外力的影响,表面容易出现凹凸不平的情况,从而导致粗糙度的增加。
硬度和粗糙度之间的关系还受到物体材料的影响。
不同的材料具有不同的硬度和粗糙度特性。
例如,金属材料通常具有较高的硬度和较低的粗糙度,而木材等非金属材料则相对较软,表面容易出现凹凸不平的情况,从而导致粗糙度的增加。
硬度和粗糙度之间的关系还受到物体表面处理的影响。
通过表面处理可以改变物体表面的硬度和粗糙度特性。
例如,通过抛光等处理可以使物体表面更加光滑,从而降低粗糙度。
相反,通过喷砂等处理可以使物体表面更加粗糙,从而增加粗糙度。
硬度和粗糙度之间存在着密切的关系。
硬度越高的物体表面越光滑,粗糙度越低;相反,硬度越低的物体表面越容易出现凹凸不平的情况,从而导致粗糙度的增加。
物体材料和表面处理也会对硬度和粗
糙度的关系产生影响。
因此,在实际应用中,需要根据具体情况选择合适的材料和表面处理方式,以达到最佳的硬度和粗糙度特性。
金属材料表面处理简介
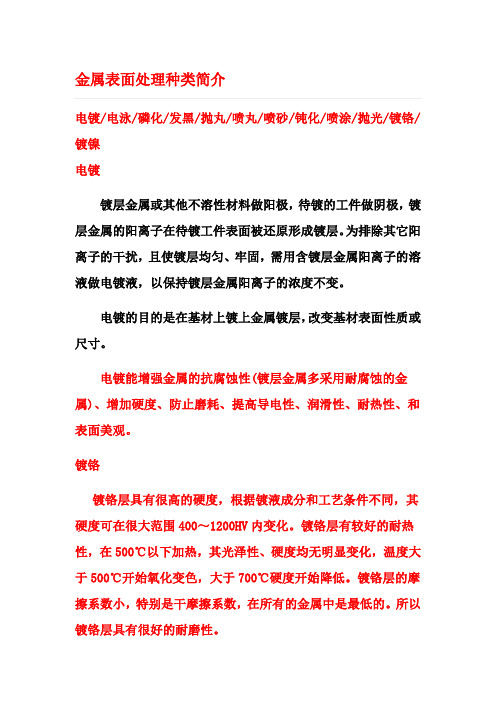
金属表面处理种类简介电镀/电泳/磷化/发黑/抛丸/喷丸/喷砂/钝化/喷涂/抛光/镀铬/镀镍电镀镀层金属或其他不溶性材料做阳极,待镀的工件做阴极,镀层金属的阳离子在待镀工件表面被还原形成镀层。
为排除其它阳离子的干扰,且使镀层均匀、牢固,需用含镀层金属阳离子的溶液做电镀液,以保持镀层金属阳离子的浓度不变。
电镀的目的是在基材上镀上金属镀层,改变基材表面性质或尺寸。
电镀能增强金属的抗腐蚀性(镀层金属多采用耐腐蚀的金属)、增加硬度、防止磨耗、提高导电性、润滑性、耐热性、和表面美观。
镀铬镀铬层具有很高的硬度,根据镀液成分和工艺条件不同,其硬度可在很大范围400~1200HV内变化。
镀铬层有较好的耐热性,在500℃以下加热,其光泽性、硬度均无明显变化,温度大于500℃开始氧化变色,大于700℃硬度开始降低。
镀铬层的摩擦系数小,特别是干摩擦系数,在所有的金属中是最低的。
所以镀铬层具有很好的耐磨性。
镀铬层具有良好的化学稳定性,在碱、硫化物、硝酸和大多数有机酸中均不发生作用,但能溶于氢氯酸(如盐酸)和热的硫酸中。
在可见光范围内,铬的反射能力约为65%,介于银(88%)和镍(55%)之间,且因铬不变色,使用时能长久保持其反射能力而优于银和镍。
镀镍通过电解或化学方法在金属或某些非金属上镀上一层镍的方法,称为镀镍。
镀镍分电镀镍和化学镀镍。
电镀镍是在由镍盐(称主盐)、导电盐、pH缓冲剂、润湿剂组成的电解液中,阳极用金属镍,阴极为镀件,通以直流电,在阴极(镀件)上沉积上一层均匀、致密的镍镀层。
从加有光亮剂的镀液中获得的是亮镍,而在没有加入光亮剂的电解液中获得的是暗镍。
1、厚度均匀性厚度均匀和均镀能力好是化学镀镍的一大特点,也是应用广泛的原因之一,化学镀镍避免了电镀层由于电流分布不均匀而带来的厚度不均匀。
化学镀时,只要零件表面和镀液接触,镀液中消耗的成份能及时得到补充,镀件部位的镀层厚度都基本相同,即使凹槽、缝隙、盲孔也是如此。
常用金属表面处理方式

表面处理方式:金属:1.喷砂喷砂是利用压缩空气把石英砂高速吹出去对零件表面进行清理的一种方法。
工厂里也叫吹砂,不仅去锈,还可以顺带除油,对涂装来说非常有用。
常用于零件表面除锈;对零件表面修饰(市场卖的小型的湿式喷砂机就是这个用途,砂粒通常是刚玉,介质是水);在钢结构中,应用高强螺栓进行联接是一种比较先进的方法,由于高强联接是利用结合面之间的摩擦来传力的,所以对结合表面的质量要求很高,这时必须用喷砂对结合表面进行处理。
喷砂用于形状复杂,易于用手工除锈,效率不高,现场环境不好,除锈不均匀。
一般的喷砂机都有各种规格的喷砂枪,只要不是特别小的箱体,都可以把枪放进去打干净。
压力容器的配套产品—封头采用喷砂方式清除工件表面的氧化皮,石英砂的直径为1.5mm~3.5mm.有一种加工就是利用水作载体,带动金刚砂来加工零件的,就是一种喷砂。
2.喷塑喷塑是为了提高防腐蚀能力,与喷砂结合更好,主要是因为结合力提高了导致质量提高。
可以增加防锈和美观效果3.氮化和软氮化氮化包括气体氮化、辉光离子氮化和软氮化,软氮化是一种通俗的叫法,严格的讲,软氮化是一种以渗氮为主的低温氮碳共渗,主要特点是渗速快(2-4h),但渗层薄(一般在0.4以下),渗层梯度陡,硬度并不低,如果是液体氮化,硬度甚至略高于气体氮化。
气体氮化可以做到深渗层,它的硬度梯度缓,比软氮化承受的载荷高,外观漂亮,缺点是周期长,表面有脆性相,一般要有一道精加工(加工余量很小,一般1丝到2丝)。
辉光离子氮化有气体氮化的优点,在0.4㎜渗层以下,渗速比气体氮化快的多,而且表面不会有脆性相,可以局部氮化,缺点是成本略高,对形状复杂或带长孔的工件效果不好。
变形方面应该是辉光离子氮化变形最小,实际中相差很小,很多时候几乎一样。
为了缩短氮化周期,并使氮化工艺不受钢种的限制,在近年间在原氮化工艺基础上发展了软氮化和离子氮化两种新氮化工艺。
软氮化实质上是以渗氮为主的低温氮碳共渗,钢的氮原子渗入的同时,还有少量的碳原子渗入,其处理结果与一般气体氮化相比,渗层硬度较氮化低,脆性较小,故称为软氮化。
常用金属表面处理方式

For personal use only in study andresearch; not for commercial use表面处理方式:金属:1.喷砂喷砂是利用压缩空气把石英砂高速吹出去对零件表面进行清理的一种方法。
工厂里也叫吹砂,不仅去锈,还可以顺带除油,对涂装来说非常有用。
常用于零件表面除锈;对零件表面修饰(市场卖的小型的湿式喷砂机就是这个用途,砂粒通常是刚玉,介质是水);在钢结构中,应用高强螺栓进行联接是一种比较先进的方法,由于高强联接是利用结合面之间的摩擦来传力的,所以对结合表面的质量要求很高,这时必须用喷砂对结合表面进行处理。
喷砂用于形状复杂,易于用手工除锈,效率不高,现场环境不好,除锈不均匀。
一般的喷砂机都有各种规格的喷砂枪,只要不是特别小的箱体,都可以把枪放进去打干净。
压力容器的配套产品—封头采用喷砂方式清除工件表面的氧化皮,石英砂的直径为1.5m m~3.5mm.有一种加工就是利用水作载体,带动金刚砂来加工零件的,就是一种喷砂。
2.喷塑喷塑是为了提高防腐蚀能力,与喷砂结合更好,主要是因为结合力提高了导致质量提高。
可以增加防锈和美观效果3.氮化和软氮化氮化包括气体氮化、辉光离子氮化和软氮化,软氮化是一种通俗的叫法,严格的讲,软氮化是一种以渗氮为主的低温氮碳共渗,主要特点是渗速快(2-4h),但渗层薄(一般在0.4以下),渗层梯度陡,硬度并不低,如果是液体氮化,硬度甚至略高于气体氮化。
气体氮化可以做到深渗层,它的硬度梯度缓,比软氮化承受的载荷高,外观漂亮,缺点是周期长,表面有脆性相,一般要有一道精加工(加工余量很小,一般1丝到2丝)。
辉光离子氮化有气体氮化的优点,在0.4㎜渗层以下,渗速比气体氮化快的多,而且表面不会有脆性相,可以局部氮化,缺点是成本略高,对形状复杂或带长孔的工件效果不好。
变形方面应该是辉光离子氮化变形最小,实际中相差很小,很多时候几乎一样。
为了缩短氮化周期,并使氮化工艺不受钢种的限制,在近年间在原氮化工艺基础上发展了软氮化和离子氮化两种新氮化工艺。
钝化的标准

钝化的标准
钝化是一种金属加工表面处理技术,常用于金属表面处理,以提高金属表面耐腐蚀和
耐磨性能。
随着社会发展和技术进步,钝化要求也在不断提升。
1. 目的:钝化处理的主要目的是提高金属材料的耐腐蚀性、耐磨性和抗粘附性,保
护表面金属不被外来材料侵蚀或损坏。
2. 表面品质:钝化表面应达到光洁度,耐蚀性和硬度要求,必须根据设备的实际情
况进行选择。
3.钝化的深度:钝化深度一般为30-100μm,最常用的是50μm,经过钝化处理的表
面硬度为250-320HV。
4.处理方法:常用的钝化方法有化学钝化、电化学钝化、非易失性钝化等。
5.使用时限:钝化表面有效使用时间必须依照实际应用情况,对各种环境和化学腐蚀
媒质的影响进行考虑。
6.其他要求:钝化表面一般不影响金属的质量和物理性能,但应考虑金属抛光性和色泽。
表面钝化后要进行除锈处理,不可以含有剩料和气泡,更不可以有氧化或腐蚀的痕迹。
金属表面处理剂概要
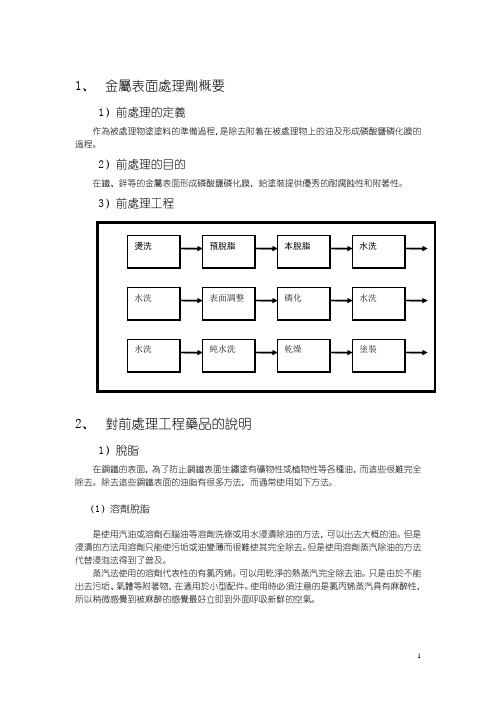
1、金屬表面處理劑概要1)前處理的定義作為被處理物塗塗料的準備過程,是除去附着在被處理物上的油及形成磷酸鹽磷化膜的過程。
2)前處理的目的在鐵、鋅等的金屬表面形成磷酸鹽磷化膜,給塗裝提供優秀的耐腐蝕性和附著性。
3)前處理工程2、對前處理工程藥品的說明1)脫脂在鋼鐵的表面,為了防止鋼鐵表面生鏽塗有礦物性或植物性等各種油,而這些很難完全除去。
除去這些鋼鐵表面的油脂有很多方法,而通常使用如下方法。
(1)溶劑脫脂是使用汽油或溶劑石腦油等溶劑洗條或用水浸漬除油的方法,可以出去大概的油。
但是浸漬的方法用溶劑只能使污垢或油變薄而很難使其完全除去。
但是使用溶劑蒸汽除油的方法代替浸泡法得到了普及。
蒸汽法使用的溶劑代表性的有氯丙烯。
可以用乾淨的熱蒸汽完全除去油。
只是由於不能出去污垢、氣體等附著物,在適用於小型配件。
使用時必須注意的是氯丙烯蒸汽具有麻醉性,所以稍微感覺到被麻醉的感覺最好立即到外面呼吸新鮮的空氣。
(2)ENULSION脫脂往煤油、石腦油等溶劑加入乳化活性劑或溶解在水里形成乳化液並加熱使用。
脫脂能力一般,所以油垢多時脫脂比較困難。
特別是附著油脂的地方,使用溶劑輕輕擦拭之後進行脫脂。
為了提高脫脂能力,有時也加入少許鹼。
脫脂以後必須用溫水洗條,以除去附著的乳化劑及污垢。
(3)電解洗條法陰極及陽極產生的氫氣及氧氣破壞附著在金屬表面的油脂膜,並通過攪拌溶液以機械方式除去油脂。
(4)鹼性洗條法附著在金屬表面的油可分為植物油和礦物油。
甲)植物油的脫脂植物油的成分為脂肪酸丙酯(甘油酯),和NaOH一起加熱時被皂化分解為肥皂和甘油。
由於都是水溶性(溶於水)物質,所以可以充分的水洗方法予以除去。
O‖CH2ONaCH2-O-C-R1 R2COONaO 3NaOH CH2ONa + R2COONa‖CH2-O-C-R2 CH2ONa R2COONaO‖CH2-O-C-R2[皂化(肥皂的反應式)]已)礦物油的脫脂1階段:用界面活性乳化劑及分散油(乳化)2階段:與鹼性中的SiO2結合並沉澱。
金属热处理及表面处理

400MPa (100HB)
0
ak
0.4
0.8
C%
y
d 1.2
20% 8J/cm2
4、常用热处理工艺
常用热处理工艺可分为普通热处理和表面热处理 两大类:
a.普通热处理包括退火、正火、淬火和回火。 b.表面热处理包括表面淬火、渗碳、渗氮和碳氮
共渗等。渗碳、渗氮和碳氮共渗又叫化学热处 理。
1)退火
退火是将钢件加热,保温后以极缓慢的 速度冷却的一种热处理工艺。
3.2 金属的表面处理
3.2.1表面防护
为防止金属腐蚀而采用各种方法叫金属表 面防护。常用的金属表面防护方法有表面 涂层和表面转化膜工艺。
3.2.2 金属的表面改性 金属的表面改性也称表面优化,就是借助 于离子束、激光、等离子体等新技术手段, 改变材料表面及近表面的组分、结构与性 质,
(1)电镀Electroplate
1. 物理气相沉积(PVD)
(1)蒸发镀膜 (2)溅射 (3)离子镀
2. 化学气相沉积(CVD)
(1)蒸发镀膜
蒸发镀膜通常是在真空 中进行,例如图3-21所 示的真空蒸镀。将零件 和涂层材料同时放在钟 罩形的真空室内,涂层 材料受热蒸发,蒸发出 的分子或原子在自由行 程内与受镀零件表面相 遇,不断凝结成膜。
(1)钢的氧化处理Black oxide
钢在加热的硝酸钠、氢氧化钠水溶液中氧化处理。 钢氧化处理后零件表面上能生成保护性磁性氧化
铁(Fe3O4)和氧化亚铁 膜。膜的颜色一般呈黑 色和蓝黑色。又称发兰或发黑。膜层的厚度约为 0.6~1.5 微米,因此氧化处理不影响零件的精 度。发兰后的零件再进行浸油和其他填充处理, 能进一步提高膜层的耐蚀性和润滑能力。
金属热处理硬度检验标准

名称通用检验标准版本日期A 2009.10.20一、制定目的明确并统一本公司自制及委外生产产品热处理硬度检验与测试的方法和依据,使产品质量得到有效控制,从而确保本公司向客户提供满意的产品。
二、适用范围上海纬泰自制或委外生产的各类产品及金属热处理零件硬度的检验与测试三、抽样标准抽样方法及判定标准,按照国标GB/T2828.1-2003规定的抽样程序及计数抽样表中之规定执行。
规定如下:检验项目检验水平Inspection levels合格质量水平Acceptable quality levels硬度测试S-1 2.5(不作抽样转换)四、检验项目及方法1.热处理件进厂时要查验供应商附送的相应的热处理检验记录,并确认记录内容是否符合相关技术要求。
2.硬度测试仪器的选用原则:1)铸铁类产品(灰铁、球墨铸铁等),应选用布氏硬度计或维氏、里氏硬度计测试,但不可用洛氏或表面洛氏硬度计测试。
2)各类钢件可依产品特性选用适当的测试仪器:布氏、洛氏、维氏或里氏硬度计等。
3)薄壁件(厚度在2mm以下),及有色金属类应选用维氏、里氏或表面洛氏硬度计等,但不可用布氏硬度计测试。
3.表面打磨为得到较为准确的测试结果,零件的测试部位均应进行表面打磨、抛光,表面光洁度应达到Ra1.6以上。
(成品件或不允许表面打磨的零件测试时,先不进行表面打磨直接在零件不影响外观表面检测。
若测试结果不合格时,则须进行破坏性打磨检测,若打磨后检测合格,则判定合格)4.每一零件原则上应至少检测四点,取其平均值作为评价结果。
(零件较小或无法取多点除外)5.当热处理零件表面产生脱碳现象时,须将零件表面磨深0.5~2mm后再进行检测。
名称通用检验标准版本日期A 2009.10.206.表面热处理硬度检测:1)化学热处理化学热处理是使工件表面渗入一种或几种化学元素的原子,从而改变工件表面的化学成分、组织和性能。
化学热处理工件的主要技术参数是硬化层深度和表面硬度。
金属表面处理工艺
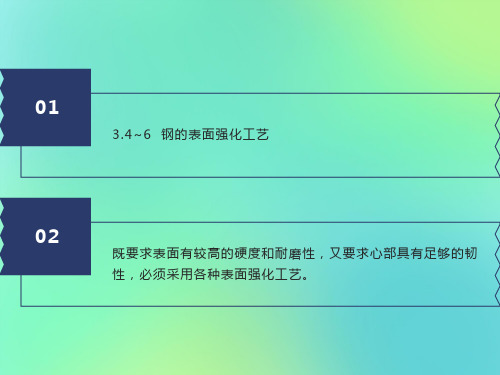
表面形变强化
01
表面形变强化指使钢件在常温下发生塑性变形,以提高其表面硬度并产生有利的残余压应力分布的表面强化工艺。 工艺简单,成本低廉,是提高钢件抗疲劳能力,延长其使用寿命的重要工艺措施。
02
03
02
01
喷丸强化是将大量高速运动的弹丸喷射到零件表面上,犹如无数个小锤锤击金属表面,使零件表层和次表层发生一定的塑性变形而实现强化的一种技术。
表面相互作用而在基体表面形成金属或化合物薄膜的方法。 例如,气态的TiCl4与N2和H2在受热钢的表面反应生成TiN,并沉积在钢的表面形成耐磨抗蚀的沉积层。
CVD设备
②化学气相沉积(CVD) 化学气相沉积是指在一定温度下,混合气体与基体
由于化学气相沉积膜层具有良好的耐磨性、耐蚀性、耐热性及电学、光学等特殊性能,已被广泛用于机械制造、航空航天、交通运输、煤化工等工业领域。 经CVD处理的模具 经CVD处理的活塞环
滲氮层硬度和耐磨性高于滲碳层,硬度可达69~72HRC,且在600~650℃高温下仍能保持较高硬度;
01
滲氮层具有很高的抗疲劳性和耐蚀性;
ห้องสมุดไป่ตู้02
滲氮后不需再进行热处理,可避免热处理带来的变形和其他缺陷;
03
滲氮温度较低。
04
只适用于中碳合金钢,需要较长的工艺时间才能达到要求的滲氮层。
05
滲氮与滲碳相比:
⑴渗碳目的 提高工件表面硬度、耐磨性及疲劳强度,同时保持心部良好的韧性。 ⑵渗碳用钢 为含0.1-0.25%C的低碳钢。碳高则心部韧性降低。
经渗碳的机车从动齿轮
②钢的渗碳 是指向钢的表面渗入碳原子的过程。
③渗碳方法 ⑴ 气体渗碳法 将工件放入密封炉内,在高温渗碳气氛中渗碳。 渗剂为气体 (煤气、液化气等)或有机液体(煤油、甲醇等)。 优点: 质量好, 效率高; 缺点: 渗层成分与深度不易控制
- 1、下载文档前请自行甄别文档内容的完整性,平台不提供额外的编辑、内容补充、找答案等附加服务。
- 2、"仅部分预览"的文档,不可在线预览部分如存在完整性等问题,可反馈申请退款(可完整预览的文档不适用该条件!)。
- 3、如文档侵犯您的权益,请联系客服反馈,我们会尽快为您处理(人工客服工作时间:9:00-18:30)。
HV也就是维氏硬度,HRC是洛氏硬度都是硬度的表示。
手册上有对应表,比如:HV=289对应HRC=30。
它们的区别主要在硬度实验时,压痕形状不一样。
金属材料抵抗硬的物体压陷表面的能力,称为硬度。
根据试验方法和适用范围不同,硬度又可分为布氏硬度、洛氏硬度、维氏硬度、肖氏硬度、显微硬度和高温硬度等。
对于管材一般常用的有布氏、洛氏、维氏硬度三种。
A、布氏硬度(HB)
用一定直径的钢球或硬质合金球,以规定的试验力(F)压入式样表面,经规定保持时间后卸除试验力,测量试样表面的压痕直径(L)。
布氏硬度值是以试验力除以压痕球形表面积所得的商。
以HBS(钢球)表示,单位为N/mm2(MPa)。
其计算公式为:
式中:F--压入金属试样表面的试验力,N;
D--试验用钢球直径,mm;
d--压痕平均直径,mm。
测定布氏硬度较准确可靠,但一般HBS只适用于450N/mm2(MPa)以下的金属材料,对于较硬的钢或较薄的板材不适用。
在钢管标准中,布氏硬度用途最广,往往以压痕直径d 来表示该材料的硬度,既直观,又方便。
举例:120HBS10/1000130:表示用直径10mm钢球在1000Kgf(9.807KN)试验力作用下,保持30s(秒)测得的布氏硬度值为120N/ mm2(MPa)。
B、洛氏硬度(HK)
洛氏硬度试验同布氏硬度试验一样,都是压痕试验方法。
不同的是,它是测量压痕的深度。
即,在初邕试验力(Fo)及总试验力(F)的先后作用下,将压头(金钢厂圆锥体或钢球)压入试样表面,经规定保持时间后,卸除主试验力,用测量的残余压痕深度增量(e)计算硬度值。
其值是个无名数,以符号HR表示,所用标尺有A、B、C、D、E、F、G、H、K 等9个标尺。
其中常用于钢材硬度试验的标尺一般为A、B、C,即HRA、HRB、HRC。
硬度值用下式计算:
当用A和C标尺试验时,HR=100-e
当用B标尺试验时,HR=130-e
式中e--残余压痕深度增量,其什系以规定单位0.002mm表示,即当压头轴向位移一个单位(0.002mm)时,即相当于洛氏硬度变化一个数。
e值愈大,金属的硬度愈低,反之则硬度愈高。
上述三个标尺适用范围如下:
HRA(金刚石圆锥压头)20-88
HRC(金刚石圆锥压头)20-70
HRB(直径1.588mm钢球压头)20-100
洛氏硬度试验是目前应用很广的方法,其中HRC在钢管标准中使用仅次于布氏硬度HB。
洛氏硬度可适用于测定由极软到极硬的金属材料,它弥补了布氏法的不是,较布氏法简便,可直接从硬度机的表盘读出硬度值。
但是,由于其压痕小,故硬度值不如布氏法准确。
C、维氏硬度(HV)
维氏硬度试验也是一种压痕试验方法,是将一个相对面夹角为1360的正四棱锥体金刚石压头以选定的试验力(F)压入试验表面,经规定保持时间后卸除试验力,测量压痕两对角线长度。
维氏硬度值是试验力除以压痕表面积所得之商,其计算公式为:
式中:HV--维氏硬度符号,N/mm2(MPa);
F--试验力,N;
d--压痕两对角线的算术平均值,mm。
维氏硬度采用的试验力F为5(49.03)、10(98.07)、20(196.1)、30(294.2)、50(490.3)、100(980.7)Kgf(N)等六级,可测硬度值范围为5~1000HV。
表示方法举例:640HV30/20表示用30Hgf(294.2N)试验力保持20S(秒)测定的维氏硬度值为640N/mm2(MPa)。
维氏硬度法可用于测定很薄的金属材料和表面层硬度。
它具有布氏、洛氏法的主要优点,而克服了它们的基本缺点,但不如洛氏法简便。
维氏法在钢管标准中很少用。
HB是用一定的力将一定直径(2.5、5、10)的钢球压向被测材料的表面,然后测量被测材料表面钢球压痕的直径以判断材料的硬度。
材料的原始状态和钢材的退火、正火或调质常用HB。
HR有A、B 、C3三种。
A和C 用120度的金刚石正圆锥体作测头,B用直径1.588的钢球作测头。
测量方法都是先用一个预压力将测头压在被测材料的表面,再施以主压力,然后撤除主压力,测量压入深度判断材料的硬度。
HV是对HR的一种改良。
因120度的正圆锥体不符合金刚石的晶体结构,不易磨好,所以HV将测头改为棱圆椎体,顶端可以制作得非常精良。
测量方法同HR。
HRA和HV用来测量材料经表面热处理,如氮化、渗碳以后的表面硬度,HRC常用于测量淬火后硬度。