失效模式及后果分析FMEA(PPT 66页)
什么叫失效模式及后果分析(fmea)
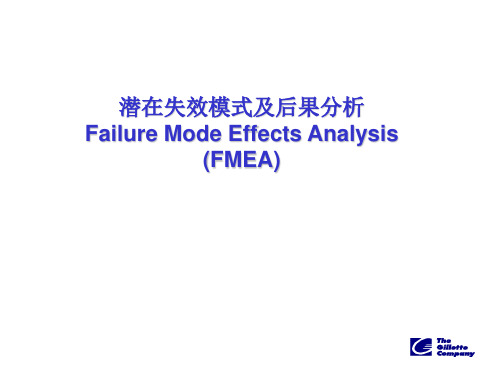
类型
DFMEA PFMEA
6
PFMEA 表格
潜在的失效模式及后果分析
项目名称: 产品类型: 核心小组:
过程 功能
潜在失 效模式
要求
过程责任部门: 关键日期:
FMEA编号:
页码:第 页 共 页 编制者: FMEA日期(编制):
潜在失效
严 重
分
潜在失效
频
现行预防
潜在失效模式及后果分析 Failure Mode Effects Analysis
(FMEA)
失效
什么是失效模式
失效模式是指系统、子系统或零件有可能未达致到设计/加工意图 的形式。 失效分类:一般的、严重的、灾难性的
失效产生的原因
原因分类:普通原因和特殊原因 普通原因:生产工艺、材料、设备等固有的不足 特殊原因:操作错误、设备损坏、材料用错等非正常因素
(修订)
措施结果
采取的措施
严频探S R
重度测* P
度
度O N
从失效模式开始,失 效模式的后果是什么 ?在这些后果中,最 坏的情况是什么?
列举失效模式而不是失效 后果的所有发生原因。 每
一个原因发生的几率有多 大?
列举针对每一原因的所有工 序控制点。 我们防止这些 原因发生或找出它的后果/ 失效模式的信心是什么?
确定关键特性. 对设计和生产中的不足进行评定及排序. 确定用于消除或减少潜在失效的措施以防止发生或到达客
户手中. 工序文件化.
5
FMEA 的发展及类型
发展
50’ 60’ 70’ 80’ 90’
用于战斗机的设计 Apollo (阿波罗)计划 汽车及医疗设备 微电子
潜在失效模式和后果分析FMEA
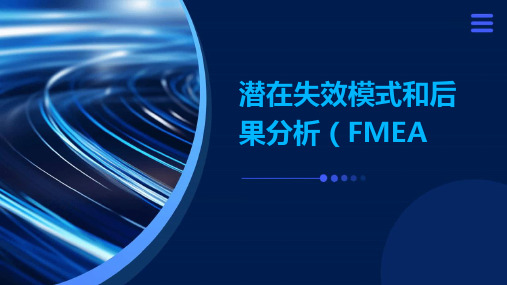
制定优先改进措施
01
根据RPN值评估结果,确定需要优先改进的潜在失效模式。
02
制定针对性的改进措施,包括设计优化、工艺改进、检验加强
等。
制定改进措施的实施计划和时间表,确保改进措施的有效执行
03 。
跟踪改进措施的实施情况
要点二
详细描述
在汽车行业中,FMEA被广泛应用于产品设计、生产和质 量控制过程中。例如,在发动机设计阶段,FMEA分析可 能识别出发动机气缸密封圈的潜在失效模式,如密封圈材 料疲劳或安装不当。这种失效可能导致发动机性能下降或 漏油,影响车辆的安全性和可靠性。通过FMEA分析,设 计团队可以采取措施优化密封圈材料和安装工艺,降低失 效风险。
服务流程改进
在服务流程中应用FMEA,有助于发 现和改进可能导致服务失败的潜在问
题。
生产过程控制
在生产过程中应用FMEA,有助于识 别和解决可能导致生产不合格品的潜 在问题。
维修和维护
在产品维修和维护过程中应用FMEA ,有助于预防和解决可能导致产品失 效的潜在问题。
02
CATALOGUE
FMEA分析过程
详细描述
潜在失效模式是指产品或过程中可能发生的故障或性能下降。通过分析历史数据、类似产品的失效模式以及专家 意见等途径,可以识别出潜在的失效模式。
确定失效影响
总结词
评估潜在失效模式对系统、产品或过程 的影响,有助于了解失效的严重程度。
VS
详细描述
失效影响是指潜在失效模式发生时,对系 统、产品或过程性能的影响程度。通过评 估失效影响,可以了解失效的严重程度, 为后续的风险评估提供依据。
FMEA潜在的失效模式及后果分析
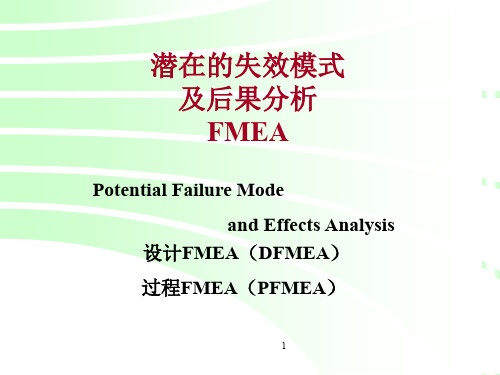
措施结果
项目 功能
潜在失 效模式
潜在失 效后果
严 重 度 S
级 别
潜在失 频 效起因/ 度
机理 O
现行设 计控制
预防
现行设 计控制
探测
探 测 度 D
R P N
建议措 施
责任及目 标完成日
期
采取的措 施
S
O
R DP
N
19
正表 DFMEA(设计)
项目/功能:
1、零部件、编号,修改状态 2、要满足设计意图的功能 3、工作环境
计、分析、试验、可 靠性、材料、质量、 服务、供方、以及高 一层和低一层总成、 系统、零部件设计人
• FMEA应成为促进不 同部门之间充分交换 意见的催化剂,从而 提高整个集体的工作 水平
• 可以邀请一位有 FMEA和团队工作推 进经验的推进员来协 助小组工作。
11
DFMEA是一份动态文件
• DFMEA要在一个设计概念最终 形成之时或之前开始
理效
的师是 一、负 种小责 分组设 析主计 技要的 术采工
用程
)Leabharlann 、9降低失效风险的方式
• 能客观评价设计,包括 功能要求及设计方案
• 为满足生产、装配、服 务和回收要求而评价初 步的设计
• 潜在失效对系统和车辆 运行产生影响在设计和 开发过程中得到考虑
• 为设计、开发、确认项 目的策划提供更多信息
4、其他方法
8
二、DFMEA简介
•
•
•
•
•
和维计体 文过过现 件程程了 化,中工
并正程 规常师 范的在 化思设
(
避 免 可 能 的 出 错
零 部 件 的 设 计 思 想
FMEA失效模式及后果分析 (ppt 88页)
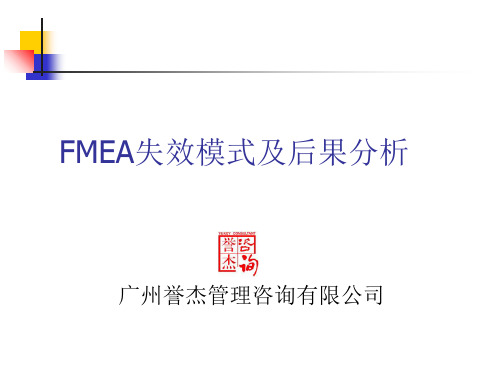
设计更改可以减轻失效模式如防错设计
2.1FMEA的质量目标
设计改进:以此为主要目标 高风险失效模式:重视并有可实施的措施计划 分析/开发/确认或DVP&R/CP:对FM进行考虑 接口:综合及衔接框图中各种FM 吸取的教训:作为FM的输入如保修费及如回 KPC及KCC:适用时在相关过程中选择 小组:选择合适的人选(有培训)和组织者 文件:文件化要完全填写 时间性(目标:The sooner The Better)
FMEA开发小组团队(1/2)
和期
FMEA开发小组团队(2/2)
FMEA范围的确定
功能模式QFD,方框图,界面图,PFC,特性矩 阵图,示意图,PFC工艺流程图,BOM
FMEA分析方式:硬件分析法(由下至上)
例:发动机的节流阀
FMEA分析方式:功能分析法(由上至下)
例:压缩空气系统功能结构(由上而下)
2.2 DFMEA的输入(设计框图)
框图是D-FMEA分析的开始,了 解系统,子系统及零部件
框图例2
2.3 DFMEA开发必备条件
DFMEA必须聚集于最终交付顾客的设计产品,其过程反 映顾客或组织的R&D过程
DFMEA应在了解所需分析的系统、子系统、零部件的开 发信息,功能要求和特性的情况下开始,至少包括:
可靠性方块图
定义FMEA的客户(4个层次)
编写FMEA的步骤
第一步(1)确定“功能”, 要求和规范, (2)识别失效模式, (3)识别失效模式后果, (4)评估失效后果的严重度S(从1到10), (5)提出消除失效模式的建议措施
第二步 (1)识别失效模式的所有潜在原因, (2)评估失效原因发生的频度(从1到10), (3)提出消除失效原因的建议措施
过程FMEA失效模式及后果分析PPT培训课件

评估失效模式的 后果
确定失效模式的 严重程度…
制定预防和探测 措施
食品加工过程,包括原料 采购、加工、包装和储存 等环节。
例如,原料可能存在农药 残留、微生物污染等问题 ;加工过程中可能出现烘 烤不均匀、切割尺寸不对 等;包装过程中可能出现 标签错误、密封不严等。
例如,农药残留可能导致 消费者健康问题;烘烤不 均匀可能导致食品口感和 质量下降;标签错误可能 导致消费者对产品的误解 。
THANKS FOR WATCHING
感谢您的观看
跟踪实施效果
对改进措施的实施情况进行跟 踪和效果评估,持续改进。
02 过程FMEA的实施过程
确定分析范围和边界
确定分析对象
明确过程FMEA的分析对象,如产品、服务或系统 等,并定义其边界和范围。
确定分析阶段
确定失效模式可能发生的阶段,如设计、制造、 运输、安装等。
确定分析重点
根据分析对象和阶段,确定失效模式分析的重点 和关注点。
如何制定有效的改进措施和行动计划?
制定改进措施和行动计划是FMEA分析的最终目的。
根据风险优先级,选择具有最大潜在改进的失效模式进行改进。这可能包括设计更改、工艺改进、过 程控制强化等。制定行动计划时,应明确责任人、完成时间和检查点,以确保改进措施的有效实施。
如何持续改进FMEA分析?
持续改进FMEA分析可以提高其有效性和可靠性。
明确分析的对象,包括产品、系统、过程等,并对其进行 定义和描述。
列出所有可能的失效模式
全面考虑可能出现的失效模式,并对其进行分类和归纳。
评估失效模式的后果
分析失效模式可能导致的影响和后果,包括对产品、系统 、过程的影响以及对顾客的影响。
确定失效模式的严重程度、发生频率…
FMEA培训ppt课件
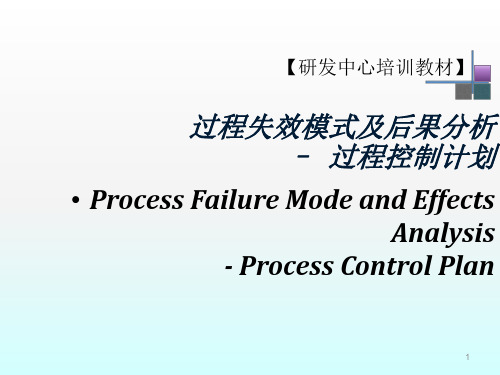
宏观的描述:装护板
将护板取出
微
对护板进行检查
观
的
护板放置到底座上
活
动
操作工拿出5颗螺钉
将螺钉放置到护板上
操作工将螺钉打紧
①
③
⑤
④
②
32
PFMEA -- 过程定义
详细叙述各个流程的作用(用动词+名词的方式)
------进行这样的分析是为后面用头脑风暴的方法来分析失效模式做准备
工步 列出要研究的各个工步 将护板取出 对护板进行检查 护板放置到底座上 操作工拿出5颗螺钉 将螺钉放置到护板上 操作工将螺钉打紧
关键日期—(5) FMEA计划完成日期,APQP进度计 划安排日期。 FMEA编号/版本—(6) 用于追溯FMEA的内部编号与版本 编制人—(7) FMEA编制人的姓名、电话及所属 公司 日期—(8) 原始稿编制日期、修订号和日期
22
製程名稱: 核心小組:
工程放行日期: 製 表 人 員:
措施執行的結果
已采取的 措施
严频探 R
重度测 度数度 (S)(O)(D)ss FMEA 开发思路
团队组建
•多功能小组 •成员来自各个级别的人员,如客户、产品设计、过程设计 、生产 线等 •确定小组组长 • 获得领导支持
过程定义
过程流程图 识别过程中每一工步的目的(采用“动词+名词”形式)
采取降低风险的行动
• 更改产品/过程设计,降低严重度(伤害性风险与设计风险); • 更改产品/过程设计,降低频度数; • 采用防错技术,提高可探测性,降低不可探测度数; • 提高在线检测技术和不合格品控制,提高可探测性,降低不可探测风险; • 变更过程控制计划; • 改进加工工艺、工装刀具。
第六单元FMEA失效模式及后果分析手册

现行控制方法几乎确定 X X 可以侦测
当场侦错(有自动停止功能的自动化量具)。缺陷 2 零件不能通过
几乎肯定
现行控制方法肯定可以 X 侦测
PPT文档演模•检板 查类型:A、防错 B、量测 C、人工检查
该项目由过程/产品设计了防错法,不会生产出缺陷 1 零件
第六单元FMEA失效模式及后果分析 手册
•FMEA分析表填写说明
涂以最 小厚度 的蠟,
外 观 不7 满
以延缓
意
腐蚀
* 车
间
内
附
件7
功
能
损
害
PPT文档演模板
人工插
8度 太高 --温度 太低 --压力 太低
因撞击
2
使喷头
变形
每小时进行目 5 测检查一次喷 膜厚度(深度计) 和范围
在开始和 停机后试 验喷雾形 状,按照 预防维护 程序清洗 喷头
•2.预估产品可能发生的制程缺点及衡量该项缺点可能造成的影 • 响,并分析其制程或装配上的可能原因及推测防止或检测该 • 项缺点应改善的制程管制(Process Control)
PPT文档演模板
•3.研究各项缺点的发生机率(Occurrence),发生后的严重程
度
• (Severity),及缺点检测难易度(Detection)计算出“风险优先
建议措 施 (19)
责任和目标 完成日期 (20)
措施执行结果(22)
采取措施(21)
严 发 探 R. 重 生 测 P. 度 率 度 N.
车门内 部人工 涂蠟
在 指 定
车 间 寿 命
7
的 表 面
降 低 导 致:
兔*
蠟 不 足
使 用 一 段
FMEA失效模式及后果分析手册精选全文

可编辑修改精选全文完整版FM E A 失效模式及后果分析手册FMEA (Failue Mode &Effect Analgsis ) Failue :失效、失败、不良 Mode :模式Effect :后果、效应、影响 Analgsis :分析一、FMEA 思维逻辑方法:D ’FMEA —→分析着重点BOM 表的零件及组装件P ’FMEA —→分析着重点OPC/AC 的零件加工及组装的工艺流程PRN 高风险优先系数 重点管理原则控制重点少数,不重要大多数列为次要管理 轻重缓急,事半功倍类比量产品(模块化) 工艺流程 过程参数/工艺条件 质量特性类比量产品 质量不良履历失败经验产品病历卡预设未来新产品投产后可能/潜在的会出现类似的不良事前 分析原因 整改措施(鱼刺图)先期产品质量策划结果控制计划(欧美) QC 工程表(台/日)新产品投产施工的要求监视和测量(首中末件检查)开发新产品例:有20项不良,前3项不良占70%,对策能解决50%的不良,70%*50%=35%后17项不良占30%,对策能解决100%的不良,30%*100%=30%①质量管理AC 柏拉图分析②物料管理MC 物料ABC法避免待料停工目的降低库存量的成本二、在何种情况下应进行FMEA分析:新产品开发阶段1、RP N≥1002、严重度/发生度/难检度(任一项)≥7;3、严重度≥7,发生度≥3;4、发生度≥5,难检度≥4量产阶段秉持持续改善的精神三、FMEA建立与更新时机1、新产品开发时;2、设计变更时(材质变更,BOM变更);3、工程变更;4、检验方法变更(检验设备/项目/频度)5、定期审查更新(建议每季度修订,至少也要每半年)四、FMEA分析表作成说明35%>30%重效果大,轻效果小活性化文件随时更新有效版本的识别(以修订日期)1、增加零件编号与名称:与BOM 表一致(D ’FMEA 分析,着眼在构成零件及组装件);2、增加工序编号与名称:与OPC/AC 表一致(P ’FMEA 分析,着眼在加工与组装工艺流程,D ’FMEA 可省略)3、功能与要求:已含外观、颜色、尺寸及ES TEST 功能质量要求;4、潜在失效模式:类比量产品质量不良履历(历史档)→产量履历→失效分析累积5、潜在失效效应(后果):万一不良时会造成的后果,如影响安全性/功能性/一般性,必须站在广义的客户中思考,包含: ● 下工程● 直接客户:下购销合同者/客户:如代理商 ● 最终客户:user/消费者6、严重度:参照对照表予以评估,复合型≥7;功能性4~6;一般性<4;7、分类(等级)class :与CC/SC 管制特性计划清单一致,包含符号识别,如FORD ▽,通用,依客户指定或本司对等的符合标注。
FMEA分析PPT演示文稿

PFMEA的原理
(1) “过程功能/要求”:是指被分 析的过程或工艺。该过程或工艺可以是技 术过程,如焊接、产品设计、软件代码编 写等,也可以是管理过程,如计划编制、 设计评审等。尽可能简单地说明该工艺过 程或工序的目的,如果工艺过程包括许多 具有不同失效模式的工序,那么可以把这 些工序或要求作为独立过程列出。
PFMEA 分析
PFMEA以其最严密的形式总结了人们在生 产制造过程中防范于未然、追求卓越的思 想。
它通过对工艺和制造过程要求和功能的系 统分析,凭借已往的经验,在最大范围, 充分考虑到那些潜在的失效模式及其相关 的起因与后果。
PFMEA的原理
几个关键步骤: ● 确定工艺或制造过程潜在失效模式与起因; ● 评价失效对产品质量和顾客的潜在影响; ● 找出减少失效发生条件的过程控制变量,并制 定预防措施; ● 编制潜在失效模式严重程度分级表,确保严重 的失效模式得到优先控制; ● 跟踪控制措施的实施情况,更新失效模式分级 表。
PFMEA的原理
(9) “措施结果”:是对上述“建议采取 的措施”计划方案之实施状况的跟踪和确 认。在明确了纠正措施后,重新估计并记 录采取纠正措施后的严重性、可能性和不 易探测性数值,计算并记录纠正后的新的 风险级值,该数值应当比措施结果之前的 风险级值低得多,从而表明采取措施后能 够充分降低失效带来的风险。
这项技术出现于上世纪60年代中期,最早 应用在美国航空航天领域,如阿波罗登月 计划。
1974年被美国海军采用。 再后来被通用汽车、福特和克莱斯勒三大
汽车公司用来减少产品制造及工艺过程中 出现的失效模式,从而达到控制和提升质 量的目的。
PFMEA 分析
2003年2月1日,美国东部时间上午9时(北 京时间1日22时),返航的哥伦比亚号航天 飞机在大约63 km高空处与地面控制中心失 去联系,在得克萨斯州地区上空爆炸解体, 机上7名航天员全部遇难。
培训课件潜在的失效模式及后果分析fmea

协作性:
虽然 FMEA 的编制责任通 常都指派到某个人,但是 FMEA 的输入应该是小组的努力。
小组成员应由知识丰富的 人员组成(如设计、分析/试验 、制造、装配、服务、质量及 可靠性等方面的有丰富经验的 工程师)
7
潜在失效模式及后果分析 FMEA
主观性
FMEA 的特点(3)
31
(22)
过程 FMEA 的開發
5 )車型年/車輛類型
填入將使用和/或正被分析的設計所影響的預期車型年
及車輛類型。 (如果已知的話)
过 程 FMEA
系统
X 子系统 ______部件 01.03/车身密封 (2) 车型年/车辆类型 199X/狮牌 4门/旅行车 (5) 核心小组: T.芬德-轿车产品开发部、切利得斯-制造部、J.福特-总
建議 措施
責任及目標 完成日期
措施結果
采取 的措施
R S ODP
N
功能、特性或 要求是什么?
綴彆岆 妦繫ˋ
衄嗣 媎詹ˋ
岆妦繫ˋ
楷汜腔 ˋ
能做些什么? - ??更改 - ?程更改
特殊控制 - ?准、程序或
指南的更改
?有什么??? - ?功能 - 部分功能/功能
?? /功能降? - 功能?歇 - 非?期功能
2
潜在失效模式及后果分析 FMEA
3
潜在失效模式及后果分析
FMEA
4
潜在失效模式及后果分析 FMEA 什么是 FMEA
FMEA 一組系統化的活動
(a)發現、評價產品/過程中潛在的失效及其後果 (b)找出能夠避免或減少這些潛在失效發生的措施 (c)全部過程形成文件
5
潜在失效模式及后果分析 FMEA
潜在失效模式及后果分析(FMEA)
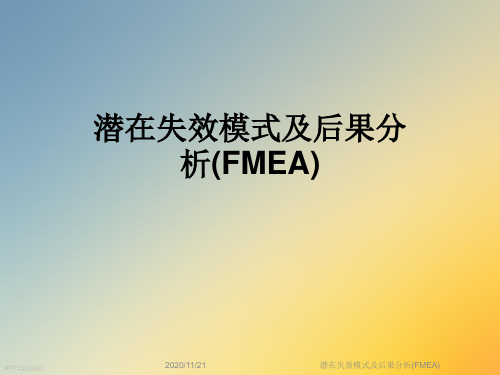
PPT文档演模板
2020/11/21
潜在失效模式及后果分析(FMEA)
•FMEA 在质量体系中
•顾客满意度的改进过程
•获得顾客需求输入
•DFMEA
•PFMEA
•更新PFMEA •控制计划 •反应计划
•过程怎样改变
•控制计划
•过程变量
•产品特性
•数据收集
PPT文档演模板
•进行适当的比较
2020/11/21
潜在失效模式及后果分析(FMEA)
•失效链
•水箱支架断裂
•1 失效原因
•水箱后倾
•1 失效模式
•2 失效原因
•水箱与风扇碰撞
•1 失效后果
•2 失效模式
•水箱冷却水管被风扇刮伤
•2 失效后果
•3 失效原因
•水箱冷却液泄漏
•冷却系统过热
•3 失效后果
PPT文档演模板
•时间
•发动机气缸损坏
2020/11/21
PPT文档演模板
2020/11/21
潜在失效模式及后果分析(FMEA)
•FMEA和FMA、FTA
• FMEA是一种事前行为:
• FMA(Failure Mode Analysis)是一种事后行 为。
• FMA是对产品/过程已经发生的失效模式分析 其产生的原因,评估其后果及采取纠正措施的一 种活动。
潜在失效模式及后果分析(FMEA)
•什么是 FMEA?
•2.术语定义
(影响的)严重度( Severity )- 影响对顾客要求 的重要程度 - 如果失败发生,也可以和安全及其他 风险相关(1=不严重,10=非常严重)
(要因的)发生率( Occurrence )- 给定要因发
失效模式及后果分析FMEAppt
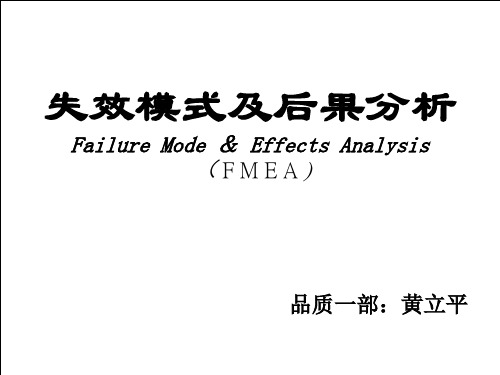
FMEA简介--2
源头管理概念 失效的早期识別越来越重要,
从源头防止,包括设计和制造 利用FMEA进行分析是其中之一技术 越来越多的客戶将实施FMEA作为对供应
商管理的內容
FMEA简介--3
FMEA的思路 假定产品或过程会产生的失效 寻找产生失效的原因 制定防止发生的管制措施
分析/测试、制造、装配、回收、质量及可靠 度等方面的工程技术人员) 5、工程师确保FMEA实施:
评审设计、过程、图样 确认ECN编入设计、组装、制造文件 评审DFNEA、PFMEA、其他FMEA/CP
图示法
直因主 方果次 图图图 法法法
失效分析方法
常用的失效分析方法
失效模式与效果分析法
綜合分析法
FTA使 用 示 议 图
房间灯黑了 或
线路上沒 有电
或
两个灯泡都 坏了
或
电源 故障
保险 断了
灯炮1 灯泡2坏了 坏了
FMEA简介--1
起源于六十年代中期,应用于军方及军用 品的采购。
首先在航天工业界应用 美国汽车业界作为管理的必备工具
(QS9000的参考手冊之一) 广泛应用于ISO9004、 CE-MARK
及失 致效 命模 性式 分影 析响
故 障 树 分 析
事 件 树 分 析
FMEA FTA ETA
FMEA FTA
與
與
FTA ETA
綜
綜
合
合
故障树状分析法FTA(fault tree analysis)
FTA法是一种系统图法,它从某个故障出现开 始,以树状形式按因果关系对一切可能导致故障 的原因一层一层地展开分析,直到找出存在于某 个零部件上的故障根源,并且能够直接采取纠正 措施为止,实施要点为: •将故障看作事件,FTA是从最高层事件向下一层 分析; •直到能夠直接采取措施加以预防和纠正为止 。
- 1、下载文档前请自行甄别文档内容的完整性,平台不提供额外的编辑、内容补充、找答案等附加服务。
- 2、"仅部分预览"的文档,不可在线预览部分如存在完整性等问题,可反馈申请退款(可完整预览的文档不适用该条件!)。
- 3、如文档侵犯您的权益,请联系客服反馈,我们会尽快为您处理(人工客服工作时间:9:00-18:30)。
包括但不限于:专案经理,设计工程师, 测试工程师,可靠性工程师,装配,制 造,材料,质量,服务,安全,分供方,顾 客.(技术专家)
• DFMEA顾客定义
–产品的使用者和最 终使用者
8
FMEA三种基本案例:
1、新的设计、技术、过程 2、修改现有的设计、过程 3、新地点用现有FMEA
9
常用方法及小组跟踪
1、图示法:直方图、因果图、主次图。 2、FMEA:FMECA(失效模式影响及致命性分析)、
FTA(故障树分析)、ETA(事件树分析) 3、综合法:FMEA+FTA、FTA+ETA 4、 FMEA的输入依靠经验丰富的人员(如:设计、
16
设计失效模式概论--1
一般习惯将FMEA分为两部分
DFMEA:
考虑产品设计的 缺陷而可能导致 的失效及后果
PFMEA:
考虑制造过程的 缺陷而可能导致 的失效及后果
17
设计FMEA作业流程
18
设计失效模式概论--2
DFMEA定义 设计结果未达到设计意图造成的失效. 可是一般环境下,也可是极限条件下.
失效模式及后果分析
Failure Mode & Effects Analysis (FMEA)
品质一部:黄立平
內容:
1 目的及概念 2 失效的分类及展开 3 常用方法及FMEA小组跟踪 4 FMEA简介 5 设计FMEA概论 6 DFMEA的分析方法 7 过程FMEA概论 8 PFMEA的分析方法 9 后果及原因分析 10 失效风险分析(RPN) 11 FMEA工作表
3、产品在工作范围内导致零组件破裂、 断裂、卡死等损坏现象
4
FMEA的特点
▪ 因分析对象不同分成〝D FMEA〞及 〝P FMEA〞二种。 ▪ 是一项以失效为讨论重点的支援性与辅助性的分析技术。 ▪ 用表格方式进行工程分析,使产品在设计与制程规划时,
早期发现缺陷及影响程度以便及早提出预防及解决措施。 〝事前行为〞避免事后修改的风险。 ▪ 是一种系统化工程设计辅助工具。(与设计过程正常
7
失效的分类及展开
根据原因、危害程度、失效程度、发生频率分: 1、致命失效:危及安全,总机报废,损失重大 2、严重失效:影响安全,设备主总成损坏或功能显著下 降,30分内无法用简易工具修复 3、一般失效:不影响安全,功能下降,不会导致设备主 总成损坏,30分内用简易工具修复 4、轻微失效:不会导致功能下降,不需更换零件,用简 易工具5分内轻易排除
及失 致效 命模 性式 分影 析响
故 障 树 分 析
事 件 树 分 析
FMEA FTA ETA
FMEA FTA
與
與
FTA ETA
綜
綜
合
合
11
故障树状分析法FTA(fault tree analysis)
FTA法是一种系统图法,它从某个故障出现开 始,以树状形式按因果关系对一切可能导致故障 的原因一层一层地展开分析,直到找出存在于某 个零部件上的故障根源,并且能够直接采取纠正 措施为止,实施要点为: •将故障看作事件,FTA是从最高层事件向下一层 分析; •直到能夠直接采取措施加以预防和纠正为止 。
(对策) 管制
水太浅
探测水深
跳跃距离太短 站位不当
掌握力量与方向 调整站位
跳的姿式不正确 头朝下
鼻子沒有夹具
鼻子夹住
水太涼 体质差 下水时机不正确
探测水溫 平时锻炼 避免剧烈运动后立即下水
风险优先数(RPN) 严= 重性(Severi发ty生)*频率(Occurren难ce易)*程度(Detection)
19
பைடு நூலகம்
设计失效模式概论--3
DFMEA细分类
功能导向方式
由系统工程师 分析,在设计早 期进行
硬件导向方式
由设计工程师 分析,在设计图 则(BOM)明确后
20
设计失效模式概论--4
典型的设计失效模式包括:
可靠性寿命不足 功能丧失 功能达不到要求 泄漏 短路等
21
设计失效模式概论--5
d)确实把握失效原因,适时采取预防与改善。
2.制造阶段:
a)透过制程分析过程,了解可能失效类別。
b)利用分析手法,改善制造上的缺点。 c)根据缺失检讨,制订合理的制程作业标准。
6
一.例题 (潜在危险) 工序 失效
(后果) 效应
头撞地
跳水
呛水
抽筋
致伤 危及生命 肺部受损 危及生命 溺水 危及生命
原因
2
目的及概念(1)
目的:1、发掘产品过程中的失效及后果 2、找出控制失效发生的措施 3、将上述过程标准化(文件化)
FMEA的重点:无论是用在设计产品还是过程制造 中,都是事前预防重于事后纠正。
3
目的及概念(2)
失效:1、在规定条件下(环境、操作、时间) 不能完成既定功能
2、在规定条件下产品参数不能维持在规 定的上下限参数之间
12
FTA使 用 示 议 图
房间灯黑了 或
线路上沒 有电
或
两个灯泡都 坏了
或
电源 故障
保险 断了
灯炮1 灯泡2坏了 坏了
13
FMEA简介--1
起源于六十年代中期,应用于军方及军用 品的采购。
首先在航天工业界应用 美国汽车业界作为管理的必备工具
(QS9000的参考手冊之一) 广泛应用于ISO9004、 CE-MARK
ISO14000/OHSAS18000等多领域
14
FMEA简介--2
源头管理概念 失效的早期识別越来越重要,
从源头防止,包括设计和制造 利用FMEA进行分析是其中之一技术 越来越多的客戶将实施FMEA作为对供应
商管理的內容
15
FMEA简介--3
FMEA的思路 假定产品或过程会产生的失效 寻找产生失效的原因 制定防止发生的管制措施
分析/测试、制造、装配、回收、质量及可靠 度等方面的工程技术人员) 5、工程师确保FMEA实施:
评审设计、过程、图样 确认ECN编入设计、组装、制造文件 评审DFNEA、PFMEA、其他FMEA/CP
10
图示法
直因主 方果次 图图图 法法法
失效分析方法
常用的失效分析方法
失效模式与效果分析法
綜合分析法
思维过程一致并使之系统化、规范化、文件化。 ▪ FMEA为归纳法的应用,根据零组件的失效资料(以往的
经验教训),由下而上推断系统的失效模式,是一种向 前推演的方法。
5
1.设计阶段
FMEA之功用
a)分析与发掘可能的失效模式。
b)执行早期研发阶段的风险性评估。 c)依分析与评估结果,进行必要的设计变更。