电渣知识
2024版电渣重熔技术新进展PPT教案

目录
• 电渣重熔技术概述 • 电渣重熔技术新进展 • 关键设备与工艺优化 • 实验研究及案例分析 • 未来发展趋势与挑战 • 总结与展望
01
电渣重熔技术概述
定义与原理
定义
电渣重熔技术是一种利用电流通过熔渣产生的热量来熔 化金属电极,并在水冷结晶器中凝固成锭的冶金工艺。
数据处理与结果分析
数据收集与整理
收集实验过程中的电压、 电流、温度等关键参数, 以及金属成分、组织等数 据。
数据处理
对收集的数据进行清洗、 整理和分析,提取有用信 息。
结果展示
通过图表、图像等形式展 示实验结果,便于分析和 比较。
案例展示及讨论
案例选择
选择具有代表性的电渣重熔实验 案例,如不同金属材料的重熔、
电渣重熔技术应用领域
介绍了电渣重熔技术在航空航天、能源、化工等领域的应用实例,突显其重要性和广泛应用 前景。
学生自我评价与反思
知识掌握程度
通过本次课程学习,我对电渣重熔技术的基本原理、新进展和应用 领域有了更深入的了解,掌握了相关知识和技能。
学习方法与效果
在学习过程中,我采用了多种学习方法,如阅读文献、听讲座、与 同学讨论等,取得了良好的学习效果。
原理
该技术基于电流的热效应,当电流通过具有高电阻的熔 渣时,产生大量热量使金属电极熔化,熔化的金属液滴 通过熔渣进入结晶器,在水冷作用下凝固成锭。
发展历程及现状
01 20世纪初
电渣重熔技术的起源,最初用于 生产特殊钢。
02 20世纪50年代
该技术得到快速发展,开始应用 于生产大型锻件和铸件。
03 21世纪初至今
03 余热回收技术
利用电渣重熔过程中产生的余热,进行回收利用, 提高能源利用效率。
焊接知识问答

焊接部分思考题解答1.熔焊、压焊和钎焊的实质有何不同?解:熔焊的实质是金属的熔化和结晶,类似于小型铸造过程。
压焊的实质是通过金属欲焊部位的塑性变形,挤碎或挤掉结合面的氧化物及其他杂质,使其纯净的金属紧密接触,界面间原子间距达到正常引力范围而牢固结合。
钎焊的实质使利用液态钎料润湿母材,填充接头间隙,并与母材相互扩散实现连接焊件。
2.焊条药皮由什么组成?各有什么作用?解:1)稳弧剂主要使用易于电离的钾、钠、钙的化合物,如碳酸钾、碳酸钠、大理石、长石和钾(或钠)水玻璃等,以改善引弧性能,提高电弧燃烧的稳定性。
2)造渣剂其组成是金红石、大理石、钛百粉、长石、菱苦土、钛铁矿、锰矿等,其主要作用是在焊接过程中形成具有一定物化性能的熔渣覆盖于熔池的表面,不让大气侵入熔池,且有冶金作用。
3)造气剂用糊精、淀粉、纤维素等有机物,或碳酸钙等无机物做造气剂。
这些物质在电弧热的作用下分解出CO和H2等气体包围在电弧与熔池周围,起到隔绝大气、保护熔滴和熔池的作用,并影响熔滴过渡。
4)脱氧剂主要应用锰铁、硅铁、钛铁、铝铁和石墨等,脱去熔池中的氧。
锰铁还兼起脱硫作用。
5)合金剂主要应用锰铁、硅铁、铬铁、钼铁、钒铁和钨铁等铁合金,向熔池中渗入合金元素,使焊缝得到必要的化学成分。
6)粘结剂常使用钾、钠水玻璃。
将上述各种药皮成分按配比制成粉末,有粘结剂调和后牢固地涂在焊芯上,从而制成焊条。
3.酸性焊条和碱性焊条在特点和应用上有何差别?解:酸性焊条碱性焊条熔渣呈酸性熔渣呈碱性保护气体是H2与CO,H2占50%左右保护气体是CO与CO2,H2<5%,因此称低氢焊条电弧稳定,可用交流或直流焊接药皮中氟化物恶化电弧稳定性,需用直流焊接,药皮中增加稳弧剂后,方可交直两用焊接电流大,焊缝成形好,但熔深较浅焊接电流较小(10%)、焊缝成形稍差、易堆高,熔深较深可长弧操作,要求不严须短弧操作,电流适当,否则产生气孔对水锈产生的敏感性不大,焊条在焊前经150~200℃烘干1小时即可,若不吸潮,可不烘干对水锈产生气孔的敏感性较大,焊条在使用前应经300~350℃烘干1~2小时,而后放保温筒中保存使用熔渣呈玻璃状,易脱渣熔渣呈结晶状,坡口第一层脱渣较困难焊接时烟尘较少焊接时烟尘稍多,产生HF有读性气体,应加强通风药皮成分氧化性强、易腐蚀有用合金,合金元素过渡性差药皮成分有还原性、合金烧蚀少,合金元素过渡效果好脱硫、脱磷能力差,抗裂性差有较多CaO,脱硫、脱磷能力强,抗裂性好焊缝中含氢量高,易生“白点”,影响塑性焊缝中含氢量低焊缝常温冲击韧度一般焊缝常温、低温冲击韧度较高用于一般钢结构,生产率高用于锅炉压力容器的受压元件与正要结构4.与手弧焊相比,埋弧自动焊有什么特点?解:埋弧自动焊与手弧焊相比,有以下特点:(1)生产率高埋弧自动焊使用的光焊丝可通过较大的电流(100A以上),能得到计较高的熔敷速度和较大的熔深;焊丝很长,卷成盘状,焊接过程中连续施焊,节省了更换焊条的时间。
建筑工程电渣压力焊安全技术交底模板

一、交底对象项目全体施工人员、焊工及管理人员。
二、交底目的为确保电渣压力焊施工过程中的安全,提高焊接质量,防止事故发生,特进行安全技术交底。
三、工程概况1. 工程名称:____________________2. 施工地点:____________________3. 施工内容:____________________4. 施工单位:____________________四、安全技术措施1. 人员资质- 焊工必须持有有效的焊工考试合格证。
- 管理人员应具备相关安全管理知识。
2. 设备检查- 焊接电源、控制箱、焊接夹具、焊剂罐等设备必须符合国家标准。
- 焊接夹具应有足够的刚度,在最大允许荷载下移动灵活,操作方便。
3. 材料要求- 焊剂应符合GB5293碳素钢埋弧焊用焊剂的规定,型号为HJ401。
- 焊剂应存放在干燥的库房内,防止受潮。
如受潮,使用前须经250~300℃烘焙2小时。
- 使用中回收的焊剂,应除去熔渣和杂物,并应与新焊剂混合均匀后使用。
- 焊剂应有出厂合格证。
4. 焊接参数控制- 焊接性能应符合GB5293碳素钢埋弧焊用焊剂的规定。
- 电压表、时间显示器应配备齐全,以便操作者掌握各项焊接参数。
- 当电源电压下降大于5%时,不宜进行焊接。
5. 现场安全- 作业场应有安全保护措施,制定和执行安全技术措施。
- 注意接头位置,同一连接区段内,纵向受力钢筋的接头面积百分率应符合要求。
6. 个人防护- 焊工应穿戴合格的防护用品,如防护眼镜、手套、工作服等。
- 焊接区域应配备消防器材,如灭火器、消防砂等。
五、应急处置1. 发生火灾时,立即切断电源,使用灭火器、消防砂等进行灭火。
2. 发生触电事故时,立即切断电源,对触电者进行急救,并立即通知医务人员。
3. 发生其他安全事故时,立即采取相应措施,并报告上级部门。
六、注意事项1. 焊接过程中,严禁无关人员进入焊接区域。
2. 焊接结束后,应清理现场,确保无安全隐患。
施工安全三级教育电渣压力焊

龙府.御澋园小区工程项目职工三级安全教育记录卡姓名:性别:年龄:班组及工种:电渣压力焊工人安全质量责任承诺卡从业人员安全风险告知书您在我项目即将从事电焊或气割工作,为了使您更好的了解该项工作中所存在的安全风险及正确的防范措施、应急处置措施等,特编制本安全风险告知书,请您认真阅知,如您有困难或疑惑,请及时向我们专职安全员提出,他们将会向您耐心讲解。
如您确定已清楚了解所从事工作的安全风险后,请在下方签上您的大名并盖上手印。
二、安全注意事项1、必须遵守焊、割设备一般安全规定及电焊机安全操作规程。
2、电焊机外壳,必须接地良好,其电源的装拆应由电工进行。
3、焊钳与把线必须绝缘良好,连接牢固,更换焊条应戴手套,在潮湿地点工作,应站在绝缘胶板或木板上。
4、严禁在带电和带压力的容器上或管道上施焊,焊接带电的设备必须先切断电源。
5、焊接贮存过易燃、易爆、有毒物品的容器或管道,必须清楚干净,并将所有孔口打开。
6、更换场地移动把线时,应切断电源并不得手持把线爬梯等高。
7、雷雨时,应停止露天焊接作业。
8、工作结束应切断焊机电源,并检查工作地点,确认无起火危险后,方可离开。
9、乙炔发生器必须设有回火防治安全装置。
氧气瓶、乙炔瓶、氧气、乙炔表及焊割工具上,严禁沾染油脂。
10、高、中压乙炔发生器应可靠接地,压力表、安全阀应定期校验。
11、乙炔发生器不得放在电线的正下方,与氧气瓶不得放一处,具易燃易爆物品和明火的距离,不得少于10米。
校验是否漏气,要用肥皂水,严禁用明火。
12、氧气瓶、乙炔瓶应有防震胶圈,旋紧安全帽,避免碰撞和剧烈震动,并防止曝晒。
13、点火时,焊枪口不准对人,正在燃烧的焊枪不得放在工件或地面上。
带有乙炔和氧气时,不准放在金属容器内,以防气体逸出,发生燃烧事故,14、刚刚施焊的金属材料应提醒周围可能接近、接触的人员防止烫伤,公共场所应设标牌警示。
四、从业人员的权利和义务1、享有的权利⑴享受工伤保险待遇和人身伤害索赔权;⑵危险因素和应急措施的知情权;⑶安全管理的批评、检举、控告权;⑷拒绝违章指挥和强令冒险作业权;⑸危险情况下的停止作业和紧急撤离权;⑹获得符合国家标准和行业标准的劳动防护用品权;⑺获得安全生产教育和培训的权利;⑻对本单位安全生产工作的建议权。
电渣压力焊安全技术交底
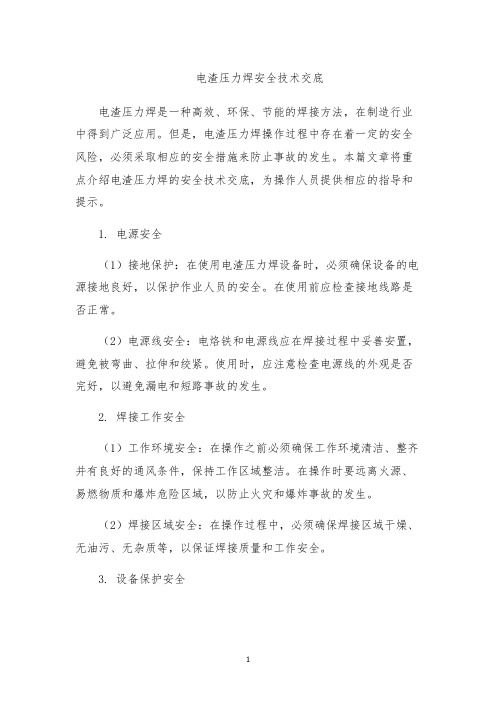
电渣压力焊安全技术交底电渣压力焊是一种高效、环保、节能的焊接方法,在制造行业中得到广泛应用。
但是,电渣压力焊操作过程中存在着一定的安全风险,必须采取相应的安全措施来防止事故的发生。
本篇文章将重点介绍电渣压力焊的安全技术交底,为操作人员提供相应的指导和提示。
1. 电源安全(1)接地保护:在使用电渣压力焊设备时,必须确保设备的电源接地良好,以保护作业人员的安全。
在使用前应检查接地线路是否正常。
(2)电源线安全:电烙铁和电源线应在焊接过程中妥善安置,避免被弯曲、拉伸和绞紧。
使用时,应注意检查电源线的外观是否完好,以避免漏电和短路事故的发生。
2. 焊接工作安全(1)工作环境安全:在操作之前必须确保工作环境清洁、整齐并有良好的通风条件,保持工作区域整洁。
在操作时要远离火源、易燃物质和爆炸危险区域,以防止火灾和爆炸事故的发生。
(2)焊接区域安全:在操作过程中,必须确保焊接区域干燥、无油污、无杂质等,以保证焊接质量和工作安全。
3. 设备保护安全(1)设备清洁:在使用电渣压力焊设备之前,必须先清洗设备的表面和内部,包括切割管道、喷嘴、钳口、销钉等,以确保设备的正常工作。
清洗时应使用特定的清洗剂,避免使用有害的物质。
(2)维护保养:在使用设备的过程中,应定期进行设备维护和保养,操作时应注意设备的运行情况。
如果发现设备出现故障或异常情况,应立即停机并进行维护。
4. 操作人员安全(1)操作技能:在使用电渣压力焊设备之前,必须接受相应的培训,掌握操作技能和安全知识。
操作人员应严格遵守操作规程,严格执行焊接规范和安全操作规定。
(2)防护用具:在操作的过程中,必须穿戴相应的防护用具,如手套、口罩、护目镜等。
使用防护用具可以降低伤害风险。
5. 废料处理安全(1)废料分类:在焊接过程中产生的废料必须分类处理,包括焊剂、涂料、残渣等。
不可将废料随意丢弃或混合分类,禁止将危险品与清洁废料混合。
(2)废料储存:废料应储存在安全区域内,禁止将废料储存在生活区或易燃物品存放区。
电渣重熔工艺和理论知识

电渣重熔工艺和理论知识ESR techniques and theoretical knowledge* 一、电渣重熔基础理论知识1、概述电渣冶金起源于美国,一九四〇年霍普金斯取得了发明专利。
一九五八年,苏联德聂泊尔特钢厂工业电渣炉建成,现代电渣冶金开始进入工业化进程。
六十年代中期,由于航空、航天、电子、原子能等工业的发展,电渣重熔在苏联、西欧、美国获得较快的发展,生产的品种包括:优质合金钢、高温合金、精密合金、耐蚀合金以及铝、铜、钛、银等有色金属合金。
我国是世界上电渣冶金起步较早的国家之一,一九六〇年,重庆特殊钢厂、大冶特殊钢厂,大连钢厂及上钢五厂的电渣炉先后建成投产。
紧随其后齐齐哈尔钢厂、抚顺钢厂等工业电渣炉相继建成投产。
五十多年来,我国电渣冶金始终保持着旺盛的发展趋势。
随着我国科学技术突飞猛进的发展,航天航海、汽车制造、石油化工、电站建设、核设施、机械制造等诸多行业,以及军工事业的发展、列车提速等许多领域越来越发挥着电渣钢的作用。
目前最大的一座是原上海重型机器厂电渣炉,重熔钢锭重达200t,现在又筹建450t大型电渣炉。
2009年,我国电渣重熔钢生产能力已超过170万t。
50多年来国内外电渣冶金取得了突飞猛进的发展,新工艺、新技术层出不穷,形成了一个跨专业、跨行业的新学科。
2、现代炼钢方法转炉,电弧炉,电渣重熔炉,真空感应炉,真空自耗炉(电弧重熔炉),电子束重熔炉(EBR)等。
电渣重熔是一种炼钢方法,而不是炉外精炼。
炉外精炼方法有LF,VD,VOD,VAD,RH 等。
3、电渣重熔炉类型3.1按工艺特点分:普通电渣重熔炉,电渣熔铸炉,加压电渣炉,保护气氛(可控气氛)电渣炉,连铸式电渣炉,电渣离心浇注炉,电渣热封顶等。
可控气氛电渣重熔技术。
电渣重熔通常在大气下进行,重熔合金中的氧含量,取决于主要脱氧元素的浓度和该脱氧元素的氧化物在渣中的活度。
此外,渣池上的氧分压或多或少也会产生一定的影响。
过去通常采用往渣池中加入脱氧剂的方法对熔渣连续脱氧,但是这会导致熔渣成分的改变。
埋弧焊电渣焊基础知识
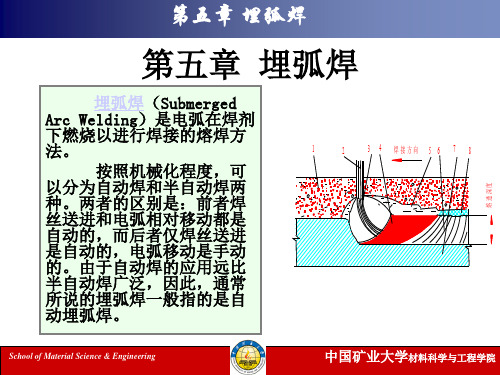
第五章 埋弧焊
埋弧焊(Submerged Arc Welding)是电弧在焊剂 下燃烧以进行焊接的熔焊方 法。 按照机械化程度,可 以分为自动焊和半自动焊两 种。两者的区别是:前者焊 丝送进和电弧相对移动都是 自动的,而后者仅焊丝送进 是自动的,电弧移动是手动 的。由于自动焊的应用远比 半自动焊广泛,因此,通常 所说的埋弧焊一般指的是自 动埋弧焊。
焊剂中MnO量增大,ΔMn(过渡的Mn量)增大。 (SiO2)+2[Mn] = [Si]+2(MnO)
锰、硅的原始浓度:焊丝中Si含量增大,ΔSi减小,ΔMn增大
焊丝中Mn含量增大,ΔMn减少,ΔSi增大 焊剂碱度:碱度增大,自由态MnO含量增大,ΔMn↑
碱度增大,自由态SiO2含量减小,ΔSi↓ 焊接参数: a)Ia:Ia↑,熔滴存在时间短,ΔSi↓ ΔMn↓
锰和硅均是低碳钢埋弧 焊焊缝中的基本成分。 其中,锰可以提高焊缝 金属的强度和韧度,并 能提高焊缝的抗热裂性 能;硅能镇静熔池,有 利于获得致密的焊缝。
中国矿业大学材料科学与工程学院
School of Material Science & Engineering
第五章 埋弧焊
(2) 影响锰、硅过渡的因素 焊剂的成分:焊剂中SiO2量增大,ΔSi(过渡的Si量)增大,ΔMn降低
中国矿业大学材料科学与工程学院
第五章 埋弧焊
School of Material Science & Engineering
中国矿业大学材料科学与工程学院
第五章 埋弧焊
School of Material Science & Engineering
中国矿业大学材料科学与工程学院
工程管理知识:钢筋电渣压力焊、接头质量检验

工程管理知识:钢筋电渣压力焊、接头质
量检验
1.取样数量
电渣压力焊接头应逐个进行外观检查。
当进行力学性能试验时,应从每批接头中随机切取3个试件做拉伸试验,且应按下列规定抽取试件。
(1)在一般构筑物中,应以300个同级别钢筋接头作为一批;
(2)在现浇钢筋混凝土多层结构中,应以每一楼层或施工区段中300个同级别钢筋接头作为一批,不足300个接头仍应作为一批。
2.外观检查
电渣压力焊接头外观检查结果应符合下列要求:
(1)四周焊包凸出钢筋表面的高度应大于或等于4mm。
(2)钢筋与电极接触处,应无烧伤缺陷;
(3)接头处的弯折角不得大于4°;
(4)接头处的轴线偏移不得大于钢筋直径0.1倍,且不得大于2mm。
外观检查不合格的接头应切除重焊,或采用补强焊接措施。
3.拉伸试验
电渣压力焊接头拉伸试验结果,3个试件的抗拉强度均不得小于该级别钢筋规定的抗拉强度。
当试验结果有1个试件的抗拉强度低于规定值,应再取6个试件进行复验。
复验结果,当仍有1个试件的抗拉强度小于规定值,应确认该批接头为不合格品。
电渣压力焊接头质量缺陷分析及预防措施

电渣压力焊接头质量缺陷分析及预防措施一、质量缺陷分析1.焊缝未熔合:焊缝未熔合是电渣压力焊接头较常见的质量缺陷之一、可能原因有:焊接电流过小,焊接速度过快,焊接时间不足,焊接压力不均匀等。
2.焊缝裂纹:焊缝裂纹是焊接头质量严重缺陷之一、裂纹常发生在焊接金属结构中,可能原因有:焊接过程中应力集中,焊缝处温度变化大,焊接变形不均匀等。
3.夹渣:夹渣是指焊缝中存在的硬质夹渣,会导致焊接头的强度下降。
夹渣可能由于焊接材料质量不过关,焊接电流过小等原因产生。
4.气孔:气孔是焊接头质量常见缺陷,对焊接性能有较大影响。
气孔的产生和气体溶解度有关,当焊接材料含气量过高,焊接过程中气体无法完全排出时,会产生气孔。
5.结合不良:结合不良是指基材和焊材之间结合力不够,会导致焊接头的强度下降。
结合不良可能与焊接材料、焊接压力不均匀等相关。
二、预防措施1.选择合适的焊接材料:焊接材料的质量对焊接头的质量有较大影响。
合格的焊接材料应具备良好的可焊性、机械性能和耐腐蚀性能。
在选择焊接材料时,应严格按照相关标准进行选材,并检验其合格证明。
2.提高操作技术:操作人员的素质和技术水平对焊接头的质量有决定性影响。
操作人员应熟悉焊接工艺要求,严格按照操作规程进行焊接操作。
在焊接过程中,应根据焊接材料的特点和实际需求,合理调节焊接参数,保证焊接质量。
3.加强设备维护:设备的性能和状态对焊接头质量有直接影响。
定期对焊接设备进行维护和检修,及时修复设备故障,确保设备正常工作。
同时,对设备的焊接压力、电流等参数进行准确调节,保证焊接质量。
4.强化质量控制:建立完善的质量控制体系,制定严格的焊接工艺规程,对焊接过程进行全程监控。
加强对焊接材料、设备、操作人员等各个环节的质量控制,确保焊接头质量。
5.加强培训和管理:加强对焊接操作人员的培训和管理,提高其技术水平和责任意识。
定期组织知识交流和培训活动,加强对质量缺陷分析及预防的学习,提高操作人员对焊接头质量缺陷的识别和解决能力。
中级电焊工理论知识
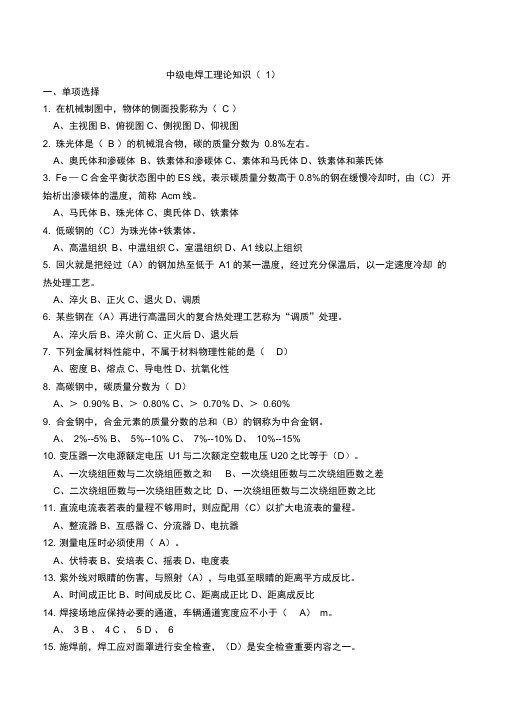
中级电焊工理论知识(1)一、单项选择1. 在机械制图中,物体的侧面投影称为(C )A、主视图B、俯视图C、侧视图D、仰视图2. 珠光体是(B )的机械混合物,碳的质量分数为0.8%左右。
A、奥氏体和渗碳体B、铁素体和渗碳体C、素体和马氏体D、铁素体和莱氏体3. Fe —C合金平衡状态图中的ES线,表示碳质量分数高于0.8%的钢在缓慢冷却时,由(C)开始析出渗碳体的温度,简称Acm线。
A、马氏体B、珠光体C、奥氏体D、铁素体4. 低碳钢的(C)为珠光体+铁素体。
A、高温组织B、中温组织C、室温组织D、A1线以上组织5. 回火就是把经过(A)的钢加热至低于A1的某一温度,经过充分保温后,以一定速度冷却的热处理工艺。
A、淬火B、正火C、退火D、调质6. 某些钢在(A)再进行高温回火的复合热处理工艺称为“调质”处理。
A、淬火后B、淬火前C、正火后D、退火后7. 下列金属材料性能中,不属于材料物理性能的是(D)A、密度B、熔点C、导电性D、抗氧化性8. 高碳钢中,碳质量分数为(D)A、>0.90%B、>0.80%C、>0.70%D、>0.60%9. 合金钢中,合金元素的质量分数的总和(B)的钢称为中合金钢。
A、2%--5%B、5%--10%C、7%--10%D、10%--15%10. 变压器一次电源额定电压U1与二次额定空载电压U20之比等于(D)。
A、一次绕组匝数与二次绕组匝数之和B、一次绕组匝数与二次绕组匝数之差C、二次绕组匝数与一次绕组匝数之比D、一次绕组匝数与二次绕组匝数之比11. 直流电流表若表的量程不够用时,则应配用(C)以扩大电流表的量程。
A、整流器B、互感器C、分流器D、电抗器12. 测量电压时必须使用(A)。
A、伏特表B、安培表C、摇表D、电度表13. 紫外线对眼睛的伤害,与照射(A),与电弧至眼睛的距离平方成反比。
A、时间成正比B、时间成反比C、距离成正比D、距离成反比14. 焊接场地应保持必要的通道,车辆通道宽度应不小于(A)m。
电渣压力焊机安全操作规程技术交底
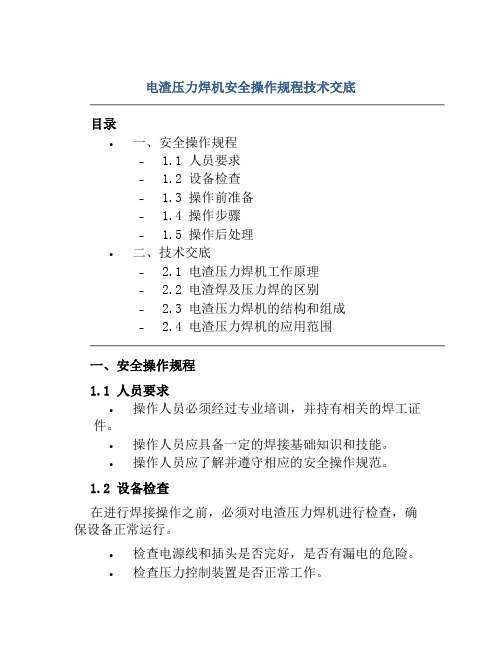
电渣压力焊机安全操作规程技术交底目录•一、安全操作规程– 1.1 人员要求– 1.2 设备检查– 1.3 操作前准备– 1.4 操作步骤– 1.5 操作后处理•二、技术交底– 2.1 电渣压力焊机工作原理– 2.2 电渣焊及压力焊的区别– 2.3 电渣压力焊机的结构和组成– 2.4 电渣压力焊机的应用范围一、安全操作规程1.1 人员要求•操作人员必须经过专业培训,并持有相关的焊工证件。
•操作人员应具备一定的焊接基础知识和技能。
•操作人员应了解并遵守相应的安全操作规范。
1.2 设备检查在进行焊接操作之前,必须对电渣压力焊机进行检查,确保设备正常运行。
•检查电源线和插头是否完好,是否有漏电的危险。
•检查压力控制装置是否正常工作。
•检查焊接机械部件是否紧固,无松动。
•检查设备上的电气元件是否损坏或老化。
1.3 操作前准备在进行焊接操作之前,需要进行一系列准备工作。
•确认焊接材料的种类、规格和焊接要求。
•准备符合要求的焊接辅助工具和设备。
•确保焊接区域的通风良好,无易燃物品。
•穿戴好焊接安全装备,如焊接手套、保护眼镜等。
1.4 操作步骤1.打开电源开关并进行设备预热,确保达到焊接所需的工作温度。
2.根据焊接要求,选择适当的焊接电流和压力。
3.将焊接材料固定于工作台上,并根据需要进行加热或预热处理。
4.将焊接头部与焊接材料接触,保持适当的压力。
5.启动设备,开始焊接操作。
6.在焊接过程中,保持适当的焊接速度和焊接质量。
7.焊接完成后,关闭设备并断开电源。
8.对焊接后的工件进行焊缝清理和表面处理。
1.5 操作后处理操作完成后,需要进行一些清理和整理工作,以确保安全和设备的正常使用。
•清理焊接区域的焊渣和废料。
•将设备归位并进行必要的维护和保养工作。
•将使用过的焊接辅助工具进行整理和存放。
二、技术交底2.1 电渣压力焊机工作原理电渣压力焊机是一种利用电弧产生的热量进行金属焊接的设备。
它通过将电流通过两个焊接材料之间产生电弧,并利用电弧的热量使材料熔化,形成焊缝。
竖向钢筋电渣压力焊操作安全要求规程
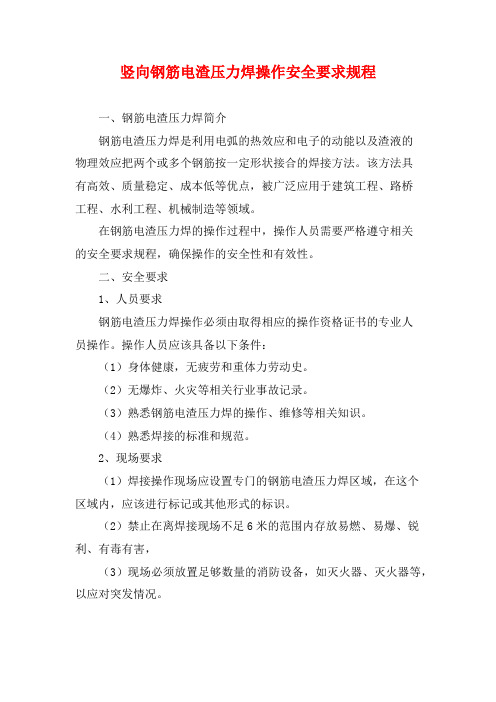
竖向钢筋电渣压力焊操作安全要求规程一、钢筋电渣压力焊简介钢筋电渣压力焊是利用电弧的热效应和电子的动能以及渣液的物理效应把两个或多个钢筋按一定形状接合的焊接方法。
该方法具有高效、质量稳定、成本低等优点,被广泛应用于建筑工程、路桥工程、水利工程、机械制造等领域。
在钢筋电渣压力焊的操作过程中,操作人员需要严格遵守相关的安全要求规程,确保操作的安全性和有效性。
二、安全要求1、人员要求钢筋电渣压力焊操作必须由取得相应的操作资格证书的专业人员操作。
操作人员应该具备以下条件:(1)身体健康,无疲劳和重体力劳动史。
(2)无爆炸、火灾等相关行业事故记录。
(3)熟悉钢筋电渣压力焊的操作、维修等相关知识。
(4)熟悉焊接的标准和规范。
2、现场要求(1)焊接操作现场应设置专门的钢筋电渣压力焊区域,在这个区域内,应该进行标记或其他形式的标识。
(2)禁止在离焊接现场不足6米的范围内存放易燃、易爆、锐利、有毒有害,(3)现场必须放置足够数量的消防设备,如灭火器、灭火器等,以应对突发情况。
(4)现场操作区内必须保持干燥和清洁,避免因为杂物和湿气引发电气事故。
(5)只有操作人员和必要的工作人员可以进入现场,其他人员必须在安全距离外观看。
(6)现场应该有充足的照明和通风设备,防止焊接过程中因照明不足或空气污染引起的事故发生。
3、操作要求(1)操作人员必须熟悉钢筋电渣压力焊的操作规程,清楚参数设置、设备维护等事项。
(2)操作人员应进行充分的安全技术交底,包括操作过程中的安全事项、突发事件的处理等。
(3)操作人员必须检查焊机设备及配件是否正常,包括电源线路、工作电缆、地线和插头等,保证电气安全。
(4)在操作过程中,操作人员必须佩戴防护器具,如焊接手套、防护眼镜等,防止爆裂飞溅伤害身体,保护人员的皮肤和眼睛。
(5)操作人员必须严格控制焊接电流及渣液量及焊接时间,严格按照参数设置操作,确保焊接质量。
(6)操作人员必须严格遵守焊接过程中的消防安全规定,如焊接不得在易燃物体附近操作,避免误将焊渣扔进草堆或容易着火的垃圾桶内等。
钢筋工程知识之竖向钢筋电渣压力焊一般规定

钢筋工程知识之竖向钢筋电渣压力焊一般规定竖向钢筋电渣压力焊一般规定?电渣压力焊是利用电流通过渣池产生的电阻热将钢筋端溶化,然后施加压力使钢筋焊合。
电渣压力焊施焊接工艺程序:安装焊接钢筋→安装引弧铁丝球→缠绕石棉绳装上焊剂盒→装放焊剂接通电源,“造渣”工作电压40~50V,“电渣”工作电压20~25V→造渣过程形成渣池→电渣过程钢筋端面溶化→切断电源顶压钢筋完成焊接→卸出焊剂拆卸焊盒→拆掉夹具。
①焊接钢筋时,用焊接夹具分别钳固上下的待焊接的钢筋,上下钢筋安装时,中心线要一致。
②安放引弧铁丝球:抬起上钢筋,将预先准备好的铁丝球安放在上、下钢筋焊接端面的中间位置,放下上钢筋,轻压铁丝球,使接触良好。
放下钢筋时,要防止铁丝球被压扁变形。
③装上焊剂盒:先在安装焊剂盒底部的位置缠上石棉绳,然后再装上焊剂盒,并往焊剂盒满装焊剂。
安装焊剂盒时,焊接口宜位于焊剂盒的中部,石棉绳缠绕应严密,防止焊剂泄漏。
④接通电源,引弧造渣:按下开头,接通电源,在接通电源的同时将上钢筋微微向上提,引燃电弧,同时开展“造渣延时读数”计算造渣通电时间。
“造渣过程”工作电压控制在40~50V之间,造渣通电时间约占整个焊接过程所需通电时间的3/4.⑤“电渣过程”:随着造渣过程完毕,即时转入“电渣过程”的同时开展“电渣延时读数”,计算电渣通电时间,并降低上钢筋,把上钢筋的端部插入渣池中,徐徐下送上钢筋,直至“电渣过程”完毕。
“电渣过程”工作电压控制在20~25V之间,电渣通电时间约占整个焊接过程所需通电时间的1/4.⑥顶压钢筋,完成焊接:“电渣过程”延时完成,电渣过程完毕,即切断电源,同时迅速顶压钢筋,形成焊接接头。
⑦卸出焊剂,拆掉焊剂盒、石棉绳及夹具。
卸出焊剂时,应将料斗卡在剂盒下方,回收的焊剂应除去溶渣及杂物,受潮的焊剂应烘、焙干燥后,可重复使用。
⑧钢筋焊接完成后,应及时开展焊接接头外观检查,外观检查不合格的接头,应切除重焊。
电渣设备基础知识复习提纲
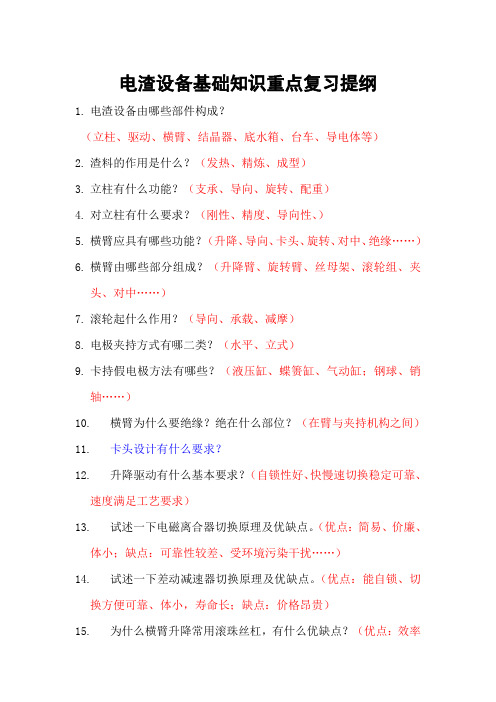
电渣设备基础知识重点复习提纲1.电渣设备由哪些部件构成?(立柱、驱动、横臂、结晶器、底水箱、台车、导电体等)2.渣料的作用是什么?(发热、精炼、成型)3.立柱有什么功能?(支承、导向、旋转、配重)4.对立柱有什么要求?(刚性、精度、导向性、)5.横臂应具有哪些功能?(升降、导向、卡头、旋转、对中、绝缘……)6.横臂由哪些部分组成?(升降臂、旋转臂、丝母架、滚轮组、夹头、对中……)7.滚轮起什么作用?(导向、承载、减摩)8.电极夹持方式有哪二类?(水平、立式)9.卡持假电极方法有哪些?(液压缸、蝶箦缸、气动缸;钢球、销轴……)10.横臂为什么要绝缘?绝在什么部位?(在臂与夹持机构之间)11.卡头设计有什么要求?12.升降驱动有什么基本要求?(自锁性好、快慢速切换稳定可靠、速度满足工艺要求)13.试述一下电磁离合器切换原理及优缺点。
(优点:简易、价廉、体小;缺点:可靠性较差、受环境污染干扰……)14.试述一下差动减速器切换原理及优缺点。
(优点:能自锁、切换方便可靠、体小,寿命长;缺点:价格昂贵)15.为什么横臂升降常用滚珠丝杠,有什么优缺点?(优点:效率高、精度好、寿命长;缺点:价格贵、维护要好)16.蝶簧油缸什么原理,有什么特点?(利用簧片自身弹力来夹紧电极,正常长时间工作不需外加动力,只是松开时用力压缩簧片即可,达到节能、保护设备效果)17.为什么要对中?(目的使电极与结晶器内壁尽量保持均衡距离,不短路、渣池温度场均匀。
)18.叙述对中方法有哪些?(动横臂、动台车、转立柱)19.用横臂对中有哪些方法?(伸缩、仰头、旋转)20.用台车怎样实现对中?(X向、Y向、Z向移动)21.实现电极交换的方法有几种?(转臂、转柱、移台车)22.台车有什么功能和作用?(支撑结晶器、底水箱、电渣锭、出锭、……)23.配重的作用和原理?(锤砣通过滑轮组来平衡臂所夹持部分重量,以减轻动力负载)24.底水箱有什么作用?(导电、存渣、冷却、引锭、凝锭)25.板坯电渣炉的结构特点有那些?(炉体高大、要抽锭;为保质保安全需加保护罩、炉口夹电极、化渣炉;运锭配翻转机等配套设备)26.电渣设备的安全操作要求?27.电渣设备生产监测哪些东西?(包括机械、电器、水、气、……各压力、流量、温度、电流、电压、速度、行程、液面监测;自动安全措施:氧含量监测、仃电补水……)。
电渣压力焊钢筋直径

电渣压力焊钢筋直径简介电渣压力焊是一种常用于钢筋连接的技术,它能够有效地提高钢筋的连接强度和稳定性。
而钢筋直径是影响焊接质量和连接强度的重要因素之一。
本文将详细介绍电渣压力焊钢筋直径的相关知识,包括其定义、影响因素、常见规范要求以及应注意的问题等。
定义钢筋直径是指钢筋截面的最大直径。
在电渣压力焊中,合适的钢筋直径对于保证焊接质量和连接强度至关重要。
通常情况下,较大直径的钢筋具有较高的承载能力,但在实际应用中需要根据具体情况进行选择。
影响因素1.结构设计要求:根据结构设计要求确定所需使用的钢筋直径范围。
2.焊接工艺:不同的焊接工艺对于钢筋直径有不同的限制,需要根据具体工艺选择合适的钢筋直径。
3.焊接设备:不同型号和规格的电渣压力焊设备对于钢筋直径也有一定的限制。
4.施工现场条件:施工现场的空间限制、操作条件等也会对钢筋直径选择产生影响。
常见规范要求根据国家相关标准和规范,电渣压力焊钢筋直径应满足以下要求: 1. 钢筋直径应在规定范围内,一般为6mm至40mm之间。
2. 相邻钢筋的直径差异不应超过规定范围,以保证焊接质量。
3. 电渣压力焊时,钢筋表面不应有明显的锈蚀、氧化和油污等。
注意事项在进行电渣压力焊钢筋直径选择和操作时,需要注意以下事项: 1. 根据结构设计要求和相关规范选择合适的钢筋直径。
2. 确保焊接设备符合要求,并按照操作说明进行正确使用。
3. 在进行电渣压力焊前,需清洁并检查钢筋表面是否有锈蚀、氧化或油污等情况,必要时进行处理。
4. 控制好焊接参数,包括电流、时间等,以确保焊接质量。
5. 过程中应注意安全,佩戴好防护设备,避免发生意外事故。
结论电渣压力焊钢筋直径的选择是确保焊接质量和连接强度的重要环节。
在进行钢筋直径选择时,需要考虑结构设计要求、焊接工艺、焊接设备和施工现场条件等因素。
同时,根据国家相关标准和规范的要求,合理选择钢筋直径,并注意操作过程中的安全和细节问题。
通过正确选择钢筋直径并采取适当的操作措施,可以确保电渣压力焊的质量和可靠性。
电渣压力焊取样规范

汇报人:汐
随机性:取样应具有随机性, 确保样本的代表性。
规范性:取样应遵循相关规范 和标准,确保样本的有效性。
准确性:取样应准确无误,避 免对样本的污染或损坏。
可靠性:取样应可靠稳定,确 保结果的重复性和可比较性。
确定取样部 位制作试样清理表面 试验与记录Part Three
按规范要求选取试样,确保代表性 选取的试样应具有典型性,能够反映整体情况 试样的尺寸和重量应符合标准要求 试样应进行标识和记录,以便后续分析
Part Four
试样尺寸应符合国家相关标准 规定
试样尺寸应满足工程实际需要
试样尺寸应满足焊接工艺要求
试样尺寸应满足试验设备要求
试样应具有代表性,能够反映 整体结构的特点和性能
试样尺寸应符合标准要求,确 保试验结果的准确性和可靠性
试样应进行标识和记录,以便 于追溯和识别
试样应妥善保管,避免损坏和 变质
切割:将试样切割成规定的尺寸,确保切口平整、无毛刺。 研磨:对试样的表面进行研磨,使其平整、光滑,无油污、锈迹等杂质。 抛光:对研磨后的试样表面进行抛光处理,以提高其光洁度。 热处理:根据需要,对试样进行热处理,以消除内应力、提高硬度等。
外观检验:观察试样的表面质量、尺寸偏差等 拉伸试验:测试试样的抗拉强度、屈服强度等力学性能 弯曲试验:测试试样的弯曲性能,检查是否存在裂纹等缺陷 冲击试验:测试试样的冲击韧性,检查材料的脆性转变温度等
遵循安全操作规 程:在取样过程 中,操作人员必 须遵循安全操作 规程,确保取样 设备、工具等符 合安全要求。
注意观察环境: 在取样过程中, 操作人员应注意 观察周围环境, 确保没有安全隐 患存在。
遵循样品处理规 定:在取样后, 操作人员应遵循 样品处理规定, 确保样品的安全、 有效。
电渣压力焊证书

电渣压力焊证书
电渣压力焊证书是焊接行业中的一种资质证书,是对焊接人员进行电渣压力焊技术能力的认可和确认。
该证书通常由焊接协会或相关焊接组织颁发,并具有一定的等级划分。
电渣压力焊证书的获得需要通过一定的培训和考试。
焊接人员通常需要参加培训课程,学习相关的理论知识和实操技能,并且需要通过理论考试和实际焊接考试,以证明其对电渣压力焊技术具备一定的掌握和应用能力。
证书的等级划分通常根据焊接人员的技术水平和工作经验来确定。
较高级别的证书要求焊接人员具备更高的技术能力和经验,能够处理更复杂的焊接工艺和焊接材料。
持有电渣压力焊证书的焊接人员通常在焊接行业中具有更高的竞争力和就业优势。
电渣压力焊证书是焊接人员技能培训和职业发展的重要参考依据,也是企业招聘和评定焊接人员的重要依据。
拥有该证书的焊接人员通常在焊接质量和安全控制方面具备更高的专业能力和责任意识。
分享电渣焊是什么焊接方法
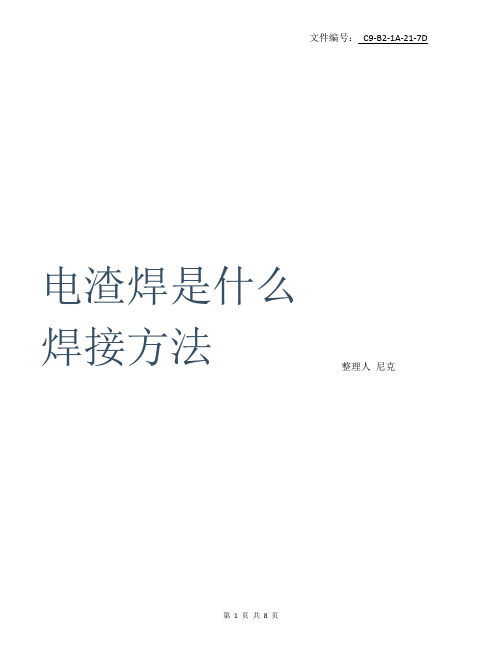
文件编号: C9-B2-1A -21-7D整理人 尼克 电渣焊是什么焊接方法中级电焊工理论知识(2)一、单项选择1.电渣焊可焊的最大焊件厚度可达( B )A.1米B.2米C. 3米D. 4米2.在下列焊接缺陷中,焊接接头脆性断裂影响最大的是( D )A,咬边 B.内部圆形夹渣 C.圆形气孔 D.弧坑冷缩3,当采用( A )电渣焊时,为适应厚板焊接,焊丝可作横向摆动。
A,丝极 B,板极 C,熔嘴 D,管状4,铣床上加附件( B )的作用是等分。
A,变速器 B,分度头 C,变位器 D,靠模5,微束等离子弧焊的优点之一是,可以焊接( B )的金属构件。
A,及薄件 B,薄板 C,中厚板 D,大厚板6,全电路欧姆定律的内容是;全电路中的( B )与电源的电动势成正比,与整个电路成正比,与整个电路的电阻成反比。
A,电阻 B,电流强度 C,电压 D,电感强度7,选择坡口形式时,应尽量( C )。
A保证焊缝金属的充天量 B,调整焊缝金属的充填物C,减少焊缝的充填物 D 增加焊缝金属的充填物8,在( B )的等离子弧,称为转移弧。
A,电极与喷嘴之间建立 B,电极与焊件之间建立C ,电极与焊丝之间建立 D,电极与离子之间建立9,利用电流通过液体熔渣所产生的电阻热来进行焊接的方法称为( D )A,电阻焊 B,电弧焊 C,埋弧焊 D,电渣焊10,编织工艺过程的步骤之一是;进行产品的工艺过程( C )A,研讨 B,试验 C,分析 D,鉴定1.氧气压力表装上后,要用扳手把丝扣拧紧,至少要拧(B )A,4扣 B,5扣 C,6扣 D,7扣12,疲劳试验是用来测定( B )在交变载荷作用下的强度。
1.熔合区 B,焊接接头 C,热影响区 D,焊缝13,有关压焊概念正确的是( C )A,对焊件施加压力但不能加热。
B,对焊件施加压力且加热C,对焊件施加压力,加热或不加热 D,以上都对14,选择耐热钢焊条主要是根据化学成分,而不根据(B )A,抗氧化性能 B ,常温机械性能 C,高温强度 D,抗裂纹性能15,焊后立即采取消氢处理的目的是( B )A,防止氢气孔 B,防止热裂纹 C,防止冻裂纹 D,再热裂纹16,焊接用的工艺装备即能是焊接工作处于( A )的位置,同时还能采用最适当的焊接工艺方法。
- 1、下载文档前请自行甄别文档内容的完整性,平台不提供额外的编辑、内容补充、找答案等附加服务。
- 2、"仅部分预览"的文档,不可在线预览部分如存在完整性等问题,可反馈申请退款(可完整预览的文档不适用该条件!)。
- 3、如文档侵犯您的权益,请联系客服反馈,我们会尽快为您处理(人工客服工作时间:9:00-18:30)。
电渣知识:电渣冶金起源于美国,一九四O年霍普金斯取得了发明专利。
一九五八年,苏联德聂泊尔特钢厂工业电渣炉建成,现代电渣冶金开始进入工业化进程。
46年来国内外电渣冶金取得了突飞猛进的发展,新工艺、新技术层出不穷,形成了一个跨专业、跨行业的新学科。
了解和掌握国内外电渣冶金发展概况,对东北特钢电渣冶金的定位及决策具有一定的参考价值。
1.国外电渣冶金发展概况一九四○年虽然霍普金斯已取得了发明专利,但是由于当时技术上的封闭和不成熟,以及理论上存在着电渣冶金是埋弧过程的错误的主导思想,致使电渣冶金的发展长期处于停滞状态。
现代电渣冶金技术是由前苏联发展起来的。
乌克兰巴顿电焊研究院在埋弧焊接过程中偶然发现,过多的渣液会使电弧熄灭,并使操作变得平稳,于是发明了电渣焊。
并在电渣焊的基础上开发出电渣冶金技术。
一九五八年,乌克兰德聂泊尔特钢厂建成了世界第一台0.5t工业电渣炉,使电渣冶金进入了工业化生产进程。
进入六十年代,出于航空航天及军备竞赛的需要,苏联对电渣冶金开展了大量的研究工作,并曾一度把发展电渣冶金作为苏联的第二党纲,极大地推动了电渣冶金的发展。
而美国和西欧的一些国家,在真空电弧重熔与电渣金熔经历了七年激烈竞争后确认,电渣重熔不仅设备简单,易于操作,成本较低,在质量方面,除去气不及真空电弧重熔外,结晶组织、钢锭表面、脱硫及去除夹杂物的能力均优于真空电弧重熔。
因此,很多航空材料转向由电渣重熔设备生产。
一些生产真空冶金设备的专业厂家如美国的Consarc公司,西德的Loybold-Hereaus公司及奥地利的BohClr公司等,也都转向生产电渣炉。
由于很多国家都致力于发展电渣冶金,六、七十年代是电渣冶金飞跃发展的年代。
多年来,国外电渣冶金已不满足于一般电渣锭的生产,在工业技术成熟的基础上向着更深更广的领域发展,形成了一个跨专业、跨行业的新学科。
已开发出的工艺技术有:电渣熔铸、电渣浇注、电渣转注、电渣热封顶、电渣离心浇注、电渣复合熔铸及快速电渣重熔等。
尤其值得重视的是电渣熔铸异形件的发展,小到几十克重的不锈钢假牙齿,大到几十吨重的发电机转子,直至重量超过百吨的水泥回转窑炉圈等,均可不经锻造在异形水冷结晶器中直接熔铸成型。
现在电渣熔铸的主要产品有大型发电机转子、水轮机叶片、船舶柴油机大型曲轴、各种高压容器、大型环件、各类轧辊、模具、透平涡轮盘、厚壁中空管、石油裂化管、齿轮毛坯、三通管、核电站压水堆主回路管道等。
种类规格之多,形状之复杂不胜枚举。
除此之外,实用性较强,具有发展前景的还有电渣热封顶、电渣离心浇注及快速电渣重熔等。
电渣热封顶(ESHT)即电渣热补缩有两种类型。
一是大型铸锭的电渣热封顶,二是大型铸件的电渣热封顶。
其功效都在于减小缩孔深度,消除疏松和偏析,提高铸锭及铸件的成材率。
大型铸锭的电渣热封顶是用一般冶炼方法冶炼的钢液浇入盛有渣料的钢锭模。
由于融渣的比重大大小于钢液,因此在锭模内钢液上面迅速形成一个渣池,将金属电极或石墨电极插入渣池,适量输入电能即可进行热封顶。
采用金属电极热封顶,可使金属液以熔滴的形式不断地填充缩孔,效果优于石墨电极。
但必须制备与铸锭化学成分相同的“本钢种”金属电极。
在采用电渣热封顶技术的国家中,奥地利采用水冷保温帽,意大利采用耐火材料做保温帽,乌克兰采用石墨衬和耐火水泥勾缝的保温帽。
水冷保温帽热损失稍高,但可避免耐火材料污染钢液,并且没有耐火材料消耗。
日本特殊电极份公司与小松制造厂推出冒口加热装置,实质上是用于铸件的电渣热封顶装置。
热封顶过程中,将带有石墨电极的活动的三角支架,固定在已浇注完毕的砂型上,然后将石墨电极降至冒口端的渣中通电保温,防止铸件在凝固过程中产生缩孔及疏松等缺陷。
实验报告表明,同样是7.6t的铸钢件,用常规方法浇注的铸件,冒口重量为3.52t,而用电渣热封顶的方法冒口重量仅为620kg。
收得率由常规方法的68%提高到92%。
过去必须开动两台电炉同时浇注才能满足铸件重量要求的产品,采用电渣热封顶,提高金属收得率后,有时仅开动一台炉子即可浇注成,使电费、耐火材料费、人工费、火切费及热处理费等均明显降低。
电渣离心浇注是把有衬电渣冶炼及离心浇注两项技术融合在一起,将有衬电渣炉冶炼的钢液连同融渣一起倒入模内,在离心铸造的旋转过程中,模具内表面形成均匀的渣壳,为各种异形铸件表面质量的提高创造了有利条件;液态金属在离心力的作用下凝固结晶,成为组织致密的铸件。
该技术在国内外应用较为广泛。
随着电渣冶金的发展及金属材料要求的不断提高,钢锭大型化已成为电渣冶金发展的必然趋势。
最初各国工业电渣炉容量仅为0.5t,大一些的一般也不超过3吨。
八十年代中期,很多国家都有了50吨以上的电渣炉,就连印度这样的发展中国家也建立了88吨电渣炉。
目前,世界上最大的电渣炉是我国上海重型机器厂的200吨电渣炉及德国萨尔钢厂的165吨电渣炉。
世界上最大的电渣钢生产厂家是乌克兰德聂泊尔特钢厂,该厂拥有22台电渣炉和年产10万吨电渣钢的生产能力。
在理论上,电渣冶金去除非金属夹杂物的机理发生了极大变化。
过去受苏联的影响电渣冶金工作者普遍认为,电渣冶金去除非金属夹杂物主要靠夹杂物从金属熔池中向上浮升,之后被融渣吸附。
当浮升速度大于金属的结晶速度时,夹杂物就能得以去除;当浮升速度小于金属的结晶速度时,夹杂物就残留在金属中。
我国李正邦等电渣冶金工作者经过实验,提出电渣冶金去除非金属夹杂物主要靠电极末端熔滴形成的过程。
这一过程使近三分之二的夹杂物得以去除。
其余三分之一是在熔滴通过渣池向金属熔池过渡及夹杂物由金属熔池向上浮升等阶段去除的。
这一理论在80年代逐渐为诸多国家的电渣冶金工作者所接受,在1988年第九届国际真空冶金会议上,美国真空冶金学会主席G?K?Bhat博士表示:“从此去夹杂物机理之争可以结束”。
在工艺方面,正常重熔期采用递减功率代替了恒功率输入,使电渣钢的冶金质量得到很大的提高。
扩大充填比(电极直径/结晶器直径)已成为电渣冶金发展的必然趋势。
很多欧美国家都采用大充填比的工艺,充填比一般控制在0.7-0.8左右,收到了明显的节电效果。
在渣系的研究和使用上,已不局限于惯用的ANF-6即CaF 2 /Al 2 O 3 =70/30的为数不多的渣系,各种二元渣、三元渣、四元渣及五元渣的出现,为提高电渣冶金工艺的适用性和再现性创造了有利条件。
在电渣冶金设备的设计与制造方面,应用了很多新技术、新材料,实现了电渣冶金先进的工艺思想与生产实际的完美结合。
尤其是保护性气氛电渣炉、高压电渣炉和真空电渣炉相继问世,为电渣冶金的发展开创了更加广阔的空间。
早期的保护性气氛电渣炉是在结晶器上方安置了可输入气体的环形保护罩,结晶器与大气是相通的。
封闭结晶器并起到保护作用的主要靠氩气、氨气及干燥空气较空气重的比重。
另外,气体输入过程中也有一定的压力。
保护性气氛电渣炉在防止电渣钢增氢,减少易氧化元素烧损方面作用比较明显。
新型保护性气氛电渣炉属于全封闭式电渣炉,结晶器上方用气密保护罩封闭、冶炼是在全封闭式惰性气体保护下进行的,因此,保护效果会更好些。
高压电渣炉主要用于生产发电机护环用无磁高氮奥氏体不锈钢。
高压电磁炉属于全封闭式电渣炉,重熔过程中熔炼室的氮气压力高达4.2MPa。
自耗电极由电弧炉生产,氮是以Si 3 N 4 的形式加入钢中的。
德国已用高压电渣炉生产出直径为一米,重达20吨的电渣锭。
重熔后钢中氮含量与自耗电极相比有很大的提高。
含氮0.85%-1.05%的元磁护环钢屈服强度达到1500N/mm 2 以上,满足了核电站建设的技术要求。
近几年来奥地利、保加利亚等国家也建造了高压电渣炉。
真空电渣炉始建于德国,它结合和保留了真空电弧炉及电渣炉的优点,克服了二者的缺点,使重熔金属不仅具有良好的结晶组织、高的纯净度、低的含硫量及气体含量,而且消除了白点及年轮状偏析,没有元素烧损,使高温合金的重熔质量得到极大的改善。
真空电炉炉和真空电渣炉同样是在真空状态下进行精炼,其主要区别在于,真空电弧炉的精炼是在没有融渣的情况下进行的,精炼过程属于电弧过程,而真空电渣炉的精炼是自耗电极自始自终插入融渣之中,精炼过程属于电渣过程。
目前世界上仅有德国、意大利、日本等国家有真空电渣炉,其普及率不高的原因,除造价因素外,工艺技术的适应性方面还存在着一定的问题。
2.我国的电渣冶金发展概况我国是世界上电渣冶金起步较早的国家之一。
一九六○年,重庆特殊钢厂、大冶特殊钢厂,大连钢厂及上钢五厂的电渣炉先后建成投产。
紧随其后齐齐哈尔钢厂、抚顺钢厂等工业电渣炉相继建成投产。
四十多年来,我国电渣冶金始终保持着旺盛的发展趋势势。
随着我国科学技术突飞猛进的发展,航天航海、汽车制造、石油化工、电站建设、核设施、机械制造等诸多行业,以及军工事业的发展、产品更新换代、列车提速等诸多环节都对钢的质量提出越来越高的要求。
电渣钢以其金属纯净度高、组织致密、成分均匀、金属各向异性小、钢锭表面光洁及成材率高等特点,进一步显现出勃勃生机。
洛阳轴承研究所于一九九七年发表在《特殊钢》杂志第四期的题目为《轴承钢冶炼工艺对滚动轴承额定功率负荷系数的影响》的文章中,对电弧炉、真空脱气和电渣工艺冶炼的204轴承进行寿命试验后,得出的结论是:“真空脱气钢的轴承额定寿命比电炉钢提高4倍,接触疲劳额定寿命提高0.8倍;用电渣钢制造的轴承平均额定寿命比电炉钢提高11倍,接触疲劳额定寿命提高2倍”。
这一事实说明,真空脱气无法代替电渣重熔。
近些年来,由于电渣钢产品质量优异,越来越多的用户订货时在合同的冶炼方法一栏明确要求“电渣重熔”。
由于电渣炉属于投资少、见效快的项目,无论是冶金行业,还是机械行业均看好电渣钢产品市场,纷纷出资建造电渣炉,很多厂家同时建造几台电渣炉。
目前国内新建电渣炉的数量之多,速度之快令人难以想象。
从趋势上看,新建电渣炉向着钢锭大型化的方向发展。
八十年代,绝大多数厂家的电渣炉都在三吨以下,而近10年来十吨以上的电渣炉已相当普遍。
就连山东民营企业也建起了40吨电渣炉。
另外,引进电渣炉的数量也呈增加的趋势,一九七九年,齐齐哈尔钢厂从西德莱保尔德——海拉斯公司引进了一台十吨单相、单支臂、双熔位、保护性气氛电渣炉。
之后近20年的时间里, 没有厂家再从国外引进电渣炉。
九十年代末期以来,邢台轧辊厂、内蒙二机及上钢五厂先后从美国引进了四台电渣炉。
随着引进电渣炉数量的增加,国外电渣炉一些先进技术也逐渐被移植。
重力传感器的使用为电子称重系统的应用以及计算机控制熔化速率提供了必要条件。
从我国电渣炉的发展情况看,控制系统已由简单的自耦,甚至手动控制,发展为可控硅或PLC控制,部分厂家采用了计算机控制。
但是由于我国在冶炼工艺与计算机的结合方面存在着薄弱环节,当前很多厂家的计算机控制实质上还是停留在一般的冶炼过程控制上。