禁止双面焊2011.10.9
气割、电焊“十不焊”规定范本

气割、电焊“十不焊”规定范本
一、禁止在人体上焊割,如绝对需要,必须经过严格的安全防护措施并由专业人员操作。
二、禁止在易燃易爆场所进行气割、电焊作业,必须将易燃易爆物品移除作业现场,并采取相应的防火措施。
三、禁止在没有通风设施的封闭空间进行气割、电焊作业,必须确保空气流通,并配备相应的防排毒设备。
四、禁止在无人监护的情况下进行气割、电焊作业,必须有专人负责现场监督,及时发现并解决安全隐患。
五、禁止使用失修、失效的气割、电焊设备进行作业,必须定期检修、保养设备,并确保设备的功能正常。
六、禁止在未经批准的作业场所进行气割、电焊作业,必须严格遵守有关规定,仅在规定的场所进行作业。
七、禁止在不熟悉操作规程的情况下进行气割、电焊作业,必须接受专业培训并持有相应的操作证书。
八、禁止疲劳和酒后进行气割、电焊作业,必须确保身体状态良好,不会因疲劳或酒精影响而导致操作不慎。
九、禁止在没有适当的个人防护装备的情况下进行气割、电焊作业,必须佩戴防护面具、手套、耳塞等安全装备。
十、禁止随意抛弃气割、电焊废料和使用过的焊花,必须妥善处理废料和焊渣,避免引发火灾或其他意外事故。
以上为气割、电焊“十不焊”规定范本,希望广大从事气割、电焊作业的人员能够认真遵守,确保作业安全。
第 1 页共 1 页。
“十不焊割”规定模版(三篇)

“十不焊割”规定模版《十不焊割》是针对焊接作业的安全生产管理规定,旨在规范焊接作业的安全操作,防止事故的发生,保护焊工安全和身体健康。
下面是《十不焊割》规定的模板,供参考。
一、不戴帽子、口罩、护目镜以及其他必要的防护装备进行焊接作业。
二、不擅自更改、维修焊接设备,不使用不符合技术要求或者破损的设备进行作业。
三、不在不符合安全要求的场所进行焊接作业,禁止在易燃易爆、有毒有害、粉尘密集等环境中进行有火焊接。
四、不与其他易燃易爆物品摆放在一起,严禁在有燃气、液化气、油桶等物体附近进行焊接作业。
五、不将焊接电源线、引弧线等线缆穿越人行通道和消防通道,不随意践踏、扭曲线缆。
六、不在密闭空间内进行焊接作业,必要时需采取通风措施并配备专门的呼吸器材。
七、不在没有安全保护措施的情况下进行高空焊接、脚手架上的焊接以及其他危险作业。
八、不在无防护措施的情况下进行对人员有伤害的焊接作业,必要时需采取遮盖或者隔离措施。
九、不在没有清理涂层、油污等可燃物的情况下进行焊接作业,注意周围环境的清洁与整理。
十、不擅自操作焊接设备的电气系统,严禁使用未经专业检验合格的设备进行焊接作业。
以上是《十不焊割》规定的模板,企业在制定具体的安全生产管理规定时,可以参考这些内容,并根据实际情况进行调整和完善。
同时,还需结合国家相关法规和标准进行制定,以确保焊接作业的安全和有效进行。
“十不焊割”规定模版(二)导言:“十不焊割”是我国现代化建设中的一大重要环节,通过对焊割作业的规范和管理,减少安全事故的发生,保障人民群众的生命财产安全,提升工作效率和质量。
本文将从“十不焊割”规定的内容和意义、实施方案和具体操作措施等方面进行阐述,以期提高焊割作业的安全性和标准化水平。
一、“十不焊割”规定的内容和意义:1. 不随便焊割:指焊割作业必须有明确的任务目标和需要焊割的零部件,不得随意开展焊割作业,以免造成无谓损失。
2. 不盲目焊割:指焊割作业必须有明确的方案和步骤,对焊割区域进行充分的调查和评估,避免盲目操作导致事故发生。
电焊气割“十不焊、割”规定(3篇)

电焊气割“十不焊、割”规定1.焊工必须持证上岗,无特种作业人员安全操作证的人员,不准进行焊、割作业;2.凡属一、二、三级动火范围的焊、割,未经办理动火审批手续,不准进行焊、割;3.焊工不了解焊、割现场周围情况,不得进行焊、割;4.焊工不了解焊件内部是否安全时,不得进行焊、割;5.各种装过可燃气体,易燃液体和有毒物质的容器,未经彻底清洗,排除危险性之前,不准进行焊、割;6.用可燃材料作保温层、冷却层、隔热设备的部位,或火星能飞溅的地方,在未采取切实可靠的安全措施之前,不准焊、割;7.有压力或密闭的管道、容器,不准焊、割;8.焊、割部位附近易燃易爆物品,在未作清理或未采取有效的安全措施之前,不准焊、割;9.附近有与明火作业相抵触的工种作业时,不准焊、割;10.与外单位相连的部位,在没有弄清有无险情,或明知存在危险而未采取有效的措施之前,不准焊、割。
电焊气割“十不焊、割”规定(2)是指在特定环境下,电焊和气割作业的禁止行为。
这些规定的目的是确保作业安全,防止火灾、爆炸和其他意外事故的发生。
以下是一般的“十不焊、割”规定:1. 不在易燃、易爆和有毒危险物质环境下进行电焊和气割作业。
2. 不在油箱、管道和其他可能含有易燃液体或气体的设备上进行电焊和气割作业。
3. 不在高温、高压、高含氧环境下进行电焊和气割作业,以免引发火灾或爆炸。
4. 不在有粉尘或可燃物质的场所,在容易引起火灾的地方进行电焊和气割作业。
5. 不在人员密集的地方进行电焊和气割作业,以防止对他人的人身安全造成危害。
6. 不在有可能出现电感应现象的地方进行电焊和气割作业,以避免损坏设备和电气系统。
7. 不在有风化、开裂或损坏的设备上进行电焊和气割作业,以免设备破裂或引发意外事故。
8. 不在有树脂、塑料或可燃材料的地方进行电焊和气割作业,以防止引发火灾。
9. 不在不适合安装临时防护措施的地方进行电焊和气割作业,以确保工人的安全。
10. 不在不具备安全防护措施的环境中进行电焊和气割作业,以减少事故发生的风险。
气割、电焊“十不焊”规定模版
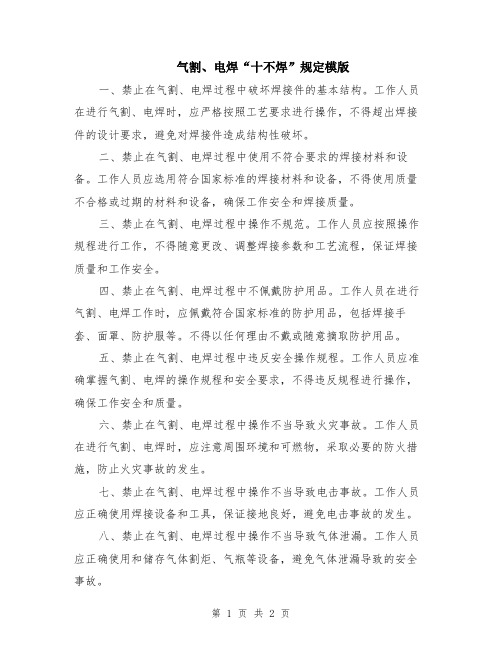
气割、电焊“十不焊”规定模版一、禁止在气割、电焊过程中破坏焊接件的基本结构。
工作人员在进行气割、电焊时,应严格按照工艺要求进行操作,不得超出焊接件的设计要求,避免对焊接件造成结构性破坏。
二、禁止在气割、电焊过程中使用不符合要求的焊接材料和设备。
工作人员应选用符合国家标准的焊接材料和设备,不得使用质量不合格或过期的材料和设备,确保工作安全和焊接质量。
三、禁止在气割、电焊过程中操作不规范。
工作人员应按照操作规程进行工作,不得随意更改、调整焊接参数和工艺流程,保证焊接质量和工作安全。
四、禁止在气割、电焊过程中不佩戴防护用品。
工作人员在进行气割、电焊工作时,应佩戴符合国家标准的防护用品,包括焊接手套、面罩、防护服等。
不得以任何理由不戴或随意摘取防护用品。
五、禁止在气割、电焊过程中违反安全操作规程。
工作人员应准确掌握气割、电焊的操作规程和安全要求,不得违反规程进行操作,确保工作安全和质量。
六、禁止在气割、电焊过程中操作不当导致火灾事故。
工作人员在进行气割、电焊时,应注意周围环境和可燃物,采取必要的防火措施,防止火灾事故的发生。
七、禁止在气割、电焊过程中操作不当导致电击事故。
工作人员应正确使用焊接设备和工具,保证接地良好,避免电击事故的发生。
八、禁止在气割、电焊过程中操作不当导致气体泄漏。
工作人员应正确使用和储存气体割炬、气瓶等设备,避免气体泄漏导致的安全事故。
九、禁止在气割、电焊过程中忽视环保要求。
工作人员应根据环保要求,妥善处理焊接产生的废气、废水和固体废弃物,防止环境污染。
十、禁止在气割、电焊过程中操作不当导致伤人事故。
工作人员应注意作业区域的安全防护,避免操作不当导致的人身伤害事故的发生。
以上是气割、电焊“十不焊”规定的模版,提醒工作人员在气割、电焊过程中严格遵守规定,确保工作安全和质量。
同时,还应注意不要使用分段语句。
焊工的十不焊割
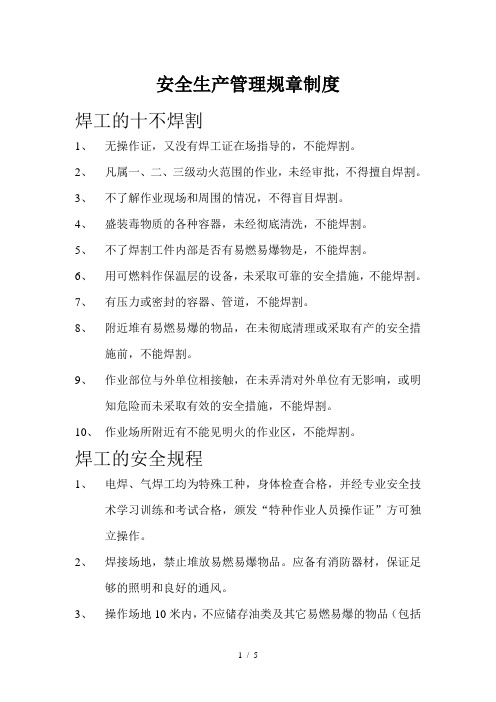
安全生产管理规章制度焊工的十不焊割1、无操作证,又没有焊工证在场指导的,不能焊割。
2、凡属一、二、三级动火范围的作业,未经审批,不得擅自焊割。
3、不了解作业现场和周围的情况,不得盲目焊割。
4、盛装毒物质的各种容器,未经彻底清洗,不能焊割。
5、不了焊割工件内部是否有易燃易爆物是,不能焊割。
6、用可燃料作保温层的设备,未采取可靠的安全措施,不能焊割。
7、有压力或密封的容器、管道,不能焊割。
8、附近堆有易燃易爆的物品,在未彻底清理或采取有产的安全措施前,不能焊割。
9、作业部位与外单位相接触,在未弄清对外单位有无影响,或明知危险而未采取有效的安全措施,不能焊割。
10、作业场所附近有不能见明火的作业区,不能焊割。
焊工的安全规程1、电焊、气焊工均为特殊工种,身体检查合格,并经专业安全技术学习训练和考试合格,颁发“特种作业人员操作证”方可独立操作。
2、焊接场地,禁止堆放易燃易爆物品。
应备有消防器材,保证足够的照明和良好的通风。
3、操作场地10米内,不应储存油类及其它易燃易爆的物品(包括易燃气体产生的器皿、管道)。
临时工地若有此类物品,面又必须在此操作时,应通知消防部门和安全技术部门到现场检查,采取临时性措施后,方可进行操作。
4、工作前必须穿戴好防护用品,操作时(包括打焊潭)所有工作人员必须戴好防护镜或面罩,仰面焊接要扣紧衣领,扎紧袖口,戴好防火帽。
5、对受压容器,密闭容器,各种油桶、管道,沾有可气体和溶液的工件进行操作时,必须事先进行检查,并经过清洗除掉有毒、易燃易爆物质,解除容器及管道压力,消除容器的密闭状态(敞开口、旋开盖),再进行工作。
6、在焊接、切割密闭空心工件,必须留有出气也。
在容光焕发器里焊接外面必须设人监护,并有良好的通风设施,照明电压应采用12伏。
禁止在已经油漆或喷涂过的塑料容器内焊接。
7、电焊机接地零线及电焊工作回线都不准搭在易燃易爆的物品上,也不准接在管道和机床设备上,不作回线应绝缘良好,机壳接地必须符合安全规定。
气割、电焊“十不焊”规定(4篇)
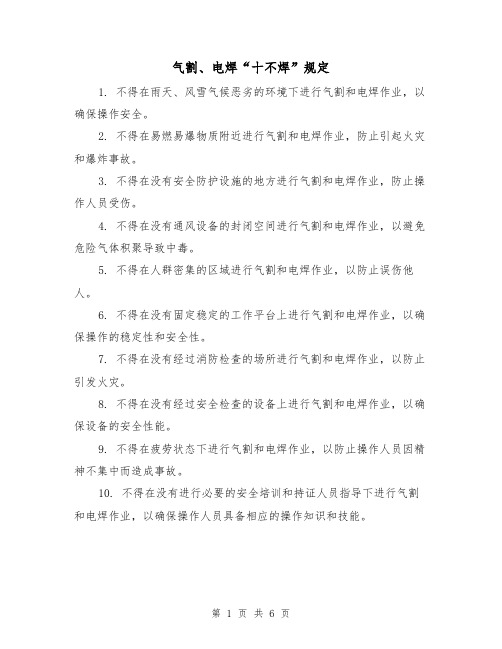
气割、电焊“十不焊”规定1. 不得在雨天、风雪气候恶劣的环境下进行气割和电焊作业,以确保操作安全。
2. 不得在易燃易爆物质附近进行气割和电焊作业,防止引起火灾和爆炸事故。
3. 不得在没有安全防护设施的地方进行气割和电焊作业,防止操作人员受伤。
4. 不得在没有通风设备的封闭空间进行气割和电焊作业,以避免危险气体积聚导致中毒。
5. 不得在人群密集的区域进行气割和电焊作业,以防止误伤他人。
6. 不得在没有固定稳定的工作平台上进行气割和电焊作业,以确保操作的稳定性和安全性。
7. 不得在没有经过消防检查的场所进行气割和电焊作业,以防止引发火灾。
8. 不得在没有经过安全检查的设备上进行气割和电焊作业,以确保设备的安全性能。
9. 不得在疲劳状态下进行气割和电焊作业,以防止操作人员因精神不集中而造成事故。
10. 不得在没有进行必要的安全培训和持证人员指导下进行气割和电焊作业,以确保操作人员具备相应的操作知识和技能。
以上是气割和电焊作业中的“十不焊”规定,旨在保障操作人员的安全和避免事故的发生。
在进行气割和电焊作业时,务必严格遵守相关规定,做好安全防护工作。
气割、电焊“十不焊”规定(2)气割、电焊是一种重要的金属加工技术,广泛应用于建筑、船舶、汽车制造等行业。
为了保证工作安全和质量,各国纷纷制定了气割、电焊的操作规范和安全标准。
在中国,工业和信息化部于2013年发布了《焊接操作规程》(GB/T 15495-2013),其中包括了气割、电焊的“十不焊”规定,以规范操作行为,减少事故发生。
“十不焊”是指在特定情况下禁止进行气割、电焊作业的十种情况,下面将详细介绍每一种情况:1. 不得在易燃、易爆物体附近焊接易燃、易爆物体指的是易燃气体、液体或固体,如煤气、汽油、乙醇、硝酸等。
因为气割、电焊会产生高温和火花,容易引发火灾或爆炸,因此在易燃、易爆物体附近禁止焊接。
2. 不得在有毒有害气体环境下焊接有毒有害气体指的是对人体有害的气体,如一氧化碳、氮氧化物、臭氧、硫化氢等。
焊接管理制度安全禁令
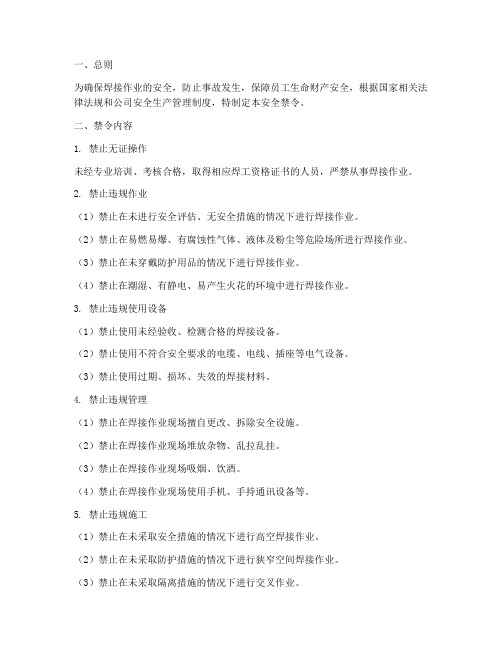
一、总则为确保焊接作业的安全,防止事故发生,保障员工生命财产安全,根据国家相关法律法规和公司安全生产管理制度,特制定本安全禁令。
二、禁令内容1. 禁止无证操作未经专业培训、考核合格,取得相应焊工资格证书的人员,严禁从事焊接作业。
2. 禁止违规作业(1)禁止在未进行安全评估、无安全措施的情况下进行焊接作业。
(2)禁止在易燃易爆、有腐蚀性气体、液体及粉尘等危险场所进行焊接作业。
(3)禁止在未穿戴防护用品的情况下进行焊接作业。
(4)禁止在潮湿、有静电、易产生火花的环境中进行焊接作业。
3. 禁止违规使用设备(1)禁止使用未经验收、检测合格的焊接设备。
(2)禁止使用不符合安全要求的电缆、电线、插座等电气设备。
(3)禁止使用过期、损坏、失效的焊接材料。
4. 禁止违规管理(1)禁止在焊接作业现场擅自更改、拆除安全设施。
(2)禁止在焊接作业现场堆放杂物、乱拉乱挂。
(3)禁止在焊接作业现场吸烟、饮酒。
(4)禁止在焊接作业现场使用手机、手持通讯设备等。
5. 禁止违规施工(1)禁止在未采取安全措施的情况下进行高空焊接作业。
(2)禁止在未采取防护措施的情况下进行狭窄空间焊接作业。
(3)禁止在未采取隔离措施的情况下进行交叉作业。
(4)禁止在未采取防护措施的情况下进行焊接作业。
三、违反禁令的处罚1. 对违反本禁令的员工,视情节轻重,给予警告、记过、降职、撤职、解除劳动合同等处分。
2. 对违反本禁令,造成事故的,依法承担相应法律责任。
3. 对违反本禁令,导致重大事故的,追究相关责任人的刑事责任。
四、附则1. 本禁令自发布之日起施行。
2. 本禁令由公司安全生产管理部门负责解释。
3. 各部门、各单位要严格执行本禁令,加强焊接作业安全管理,确保焊接作业安全。
安全生产九不准、五拒绝、十不焊

安全生产一、安全生产九禁止(一)没有安全技术举措和安全交底禁止作业 .(二)安全举措未做到齐备有效禁止作业.(三)危险作业面未做到防备周祥禁止作业.(四)发现事故隐患,未实时清除禁止作业 .(五)不按规定使用安全劳动保护用品(安全帽,安全带等),禁止上岗作业.(六)非特种作业人员禁止从事特种作业.(七)机械,电器设施安全防备装置不齐备禁止作业.(八)对机械,设施,工具的性能不熟习禁止操作使用.(九)新工人不经培训,或培训考试不合格禁止上岗作业.二、施工安全五拒绝(一)安排施工生产任务时,如不安排安全生产举措,员工有权拒绝上岗作业.(二)现场条件有了变化,安全举措跟不上时,员工有权拒绝施工.(三)干部违章指挥,员工有权拒绝听从.(四)设施安全保护装置不安全,员工有权拒绝操作.(五)在作业地址条件发生恶化,简单造成事故的状况下,不采纳相应举措,员工有权拒绝进入作业地址.三、焊工十不焊1.没有操作证又没有正式焊工在场指导,不得进行焊割作业.2.凡属一,二,三级功火范围的焊,割,未办理动火审批手续,不得私自进行焊割.3.焊工不认识焊,割现场的状况,不可以盲目焊,割.4.不认识焊割件内部能否安全时,未经完全冲洗,不可以焊割.5.盛过可燃气体,有毒物质的各样容器 ,未经冲洗,不得焊割.6.可燃资料作保温,冷却,隔音,隔热的部位,火星能飞溅到的地方,在未经采纳确实靠谱的安全举措以前,不可以焊割.7.有电流,压力的导管,设施,用具等,在未断电,泄压前,不可以焊割.8.焊割部位邻近堆放易爆物件,在未完全清理或未采纳有效举措前 ,不可以焊割.9.与外单位相接触的部位,在没有弄清外单位能否影响或理智存在危险但又未采纳确实有效的安全举措前,不可以焊割.10.焊割场所与邻近其余工种相互反抗时 ,不可以焊割.油漆、油料和化学品使用、防火管理规定1、储存油料、油漆及化学品的库房一定设置在干燥、阴凉、通风的地方。
2、库房内一定采纳必需的举措,使库房内保持适合的温度和湿度。
十不焊割的内容
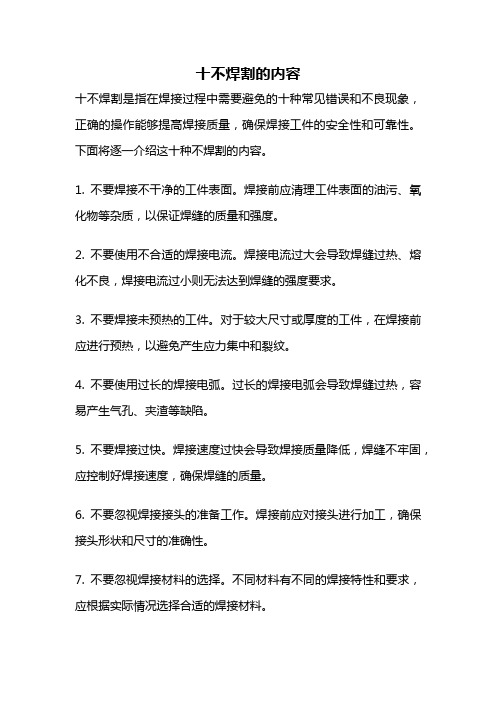
十不焊割的内容十不焊割是指在焊接过程中需要避免的十种常见错误和不良现象,正确的操作能够提高焊接质量,确保焊接工件的安全性和可靠性。
下面将逐一介绍这十种不焊割的内容。
1. 不要焊接不干净的工件表面。
焊接前应清理工件表面的油污、氧化物等杂质,以保证焊缝的质量和强度。
2. 不要使用不合适的焊接电流。
焊接电流过大会导致焊缝过热、熔化不良,焊接电流过小则无法达到焊缝的强度要求。
3. 不要焊接未预热的工件。
对于较大尺寸或厚度的工件,在焊接前应进行预热,以避免产生应力集中和裂纹。
4. 不要使用过长的焊接电弧。
过长的焊接电弧会导致焊缝过热,容易产生气孔、夹渣等缺陷。
5. 不要焊接过快。
焊接速度过快会导致焊接质量降低,焊缝不牢固,应控制好焊接速度,确保焊缝的质量。
6. 不要忽视焊接接头的准备工作。
焊接前应对接头进行加工,确保接头形状和尺寸的准确性。
7. 不要忽视焊接材料的选择。
不同材料有不同的焊接特性和要求,应根据实际情况选择合适的焊接材料。
8. 不要焊接过厚的工件。
对于过厚的工件,应采用多道焊接或采用其他连接方式,以保证焊接质量。
9. 不要焊接过薄的工件。
过薄的工件容易产生变形和裂纹,应采取适当的措施,如采用夹具等,以减少焊接变形。
10. 不要忽视焊接后的处理工作。
焊接后应对焊缝进行除渣、打磨等处理,以提高焊缝的外观和机械性能。
通过以上对十不焊割内容的介绍,我们可以看到在焊接过程中需要避免的错误和不良现象。
只有正确的操作和注意这些细节,才能保证焊接质量和焊接工件的安全性和可靠性。
因此,在进行焊接工作时,我们应牢记这十个不焊割的内容,以提高焊接质量,确保焊接工作的顺利进行。
“十不焊割”规定
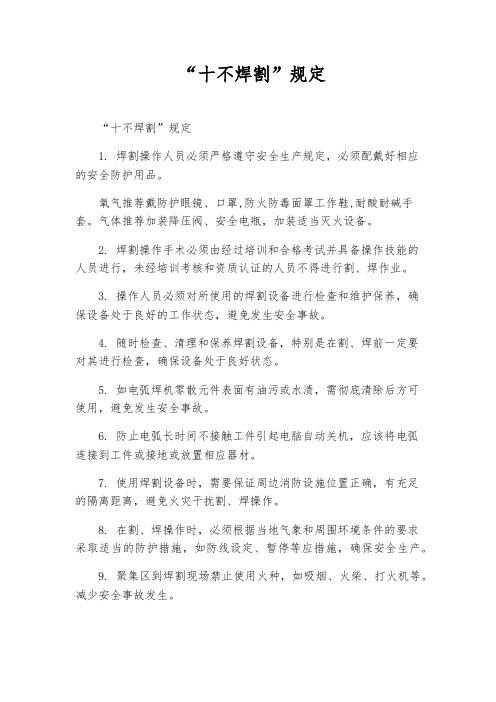
“十不焊割”规定
“十不焊割”规定
1. 焊割操作人员必须严格遵守安全生产规定,必须配戴好相应
的安全防护用品。
氧气推荐戴防护眼镜、口罩,防火防毒面罩工作鞋,耐酸耐碱手套。
气体推荐加装降压阀、安全电瓶,加装适当灭火设备。
2. 焊割操作手术必须由经过培训和合格考试并具备操作技能的
人员进行,未经培训考核和资质认证的人员不得进行割、焊作业。
3. 操作人员必须对所使用的焊割设备进行检查和维护保养,确
保设备处于良好的工作状态,避免发生安全事故。
4. 随时检查、清理和保养焊割设备,特别是在割、焊前一定要
对其进行检查,确保设备处于良好状态。
5. 如电弧焊机零散元件表面有油污或水渍,需彻底清除后方可
使用,避免发生安全事故。
6. 防止电弧长时间不接触工件引起电脑自动关机,应该将电弧
连接到工件或接地或放置相应器材。
7. 使用焊割设备时,需要保证周边消防设施位置正确,有充足
的隔离距离,避免火灾干扰割、焊操作。
8. 在割、焊操作时,必须根据当地气象和周围环境条件的要求
采取适当的防护措施,如防线设定、暂停等应措施,确保安全生产。
9. 聚集区到焊割现场禁止使用火种,如吸烟、火柴、打火机等。
减少安全事故发生。
10. 焊割设备所操作的工件应符合作业规定,切勿以任何方式将设备用于未经验过的工件上,避免安全事故的发生。
总之,在进行焊割作业时,一定要遵守安全生产规定,切实做到“十不焊割”,让工作更加健康、稳定、顺利。
安全生产“十禁令”

安全生产“十禁令”一、电焊气割“十不准”1.无特种作业操作证,不焊、不割。
2.雨天、露天作业无可靠安全措施,不焊、不割。
3.装过易燃、易爆及有害物品的容器,未进行彻底清洗、未进行可燃浓度检测,不焊、不割。
4.在容器内工作无12伏低压照明和通风不良,不焊、不割。
5.设备内无断电,设备未卸压,不焊、不割。
6.作业区周围有易燃易爆物品未消除干净,不焊、不割。
7.焊体性质不清、火星飞向不明,不焊、不割。
8.设备安全附件不全或失效,不焊、不割。
9.锅炉、容器等设备内无专人监护、无防护措施,不焊、不割。
10.禁火区内未采取安全措施、未办理动火手续,不焊、不割。
二、起重作业“十不吊”1.超过额定负荷不吊。
2.指挥信号不明,重量不明,光线暗淡不吊。
3.吊绳和附件捆缚不牢,不符合安全要求不吊。
4.行车吊挂重物直接进行加工的不吊。
5.歪拉斜挂不吊。
6.工件上站人或物体上浮有活动物的不吊。
7.氧气瓶等具有爆炸性物体不吊。
8.带棱角缺口未整好不吊。
9.埋在地下的物体不吊。
10.违章指挥不吊。
三、电气安全“十不准”1.无证电工不准安装电气设备。
2.任何人不准玩弄电气设备和开关。
3.不准使用绝缘损坏的电气设备。
4.不准利用电热设备和灯泡取暖。
5.任何人不准启动挂有警告牌和拔掉熔断器的电气设备。
6.不准用水冲洗和揩擦电气设备。
7熔丝熔断时不准调换容量不符的熔丝。
8.不准在埋有电缆的地方未办任何手续打桩动土。
9.有人触电时应立即切断电源,在未脱离电源前不准接触触电者。
10.雷电时不准接触避雷器和避雷针。
四、高处作业“十不准”1.患有高血压、心脏病、贫血、癫痫、深度近视眼等疾病不准登高。
2.无人监护不准登高。
3.没有戴安全帽、系安全带、不扎紧裤管时不准登高作业。
4.作业现场有六级以上大风及暴雨、大雪、大雾不准登高。
5.脚手架、跳板不牢不准登高。
6.梯子无防滑措施、未穿防滑鞋不准登高。
7.不准攀爬井架、龙门架、脚手架,不能乘坐非载人的垂直运输设备登高。
电焊气割“十不焊、割”规定模版
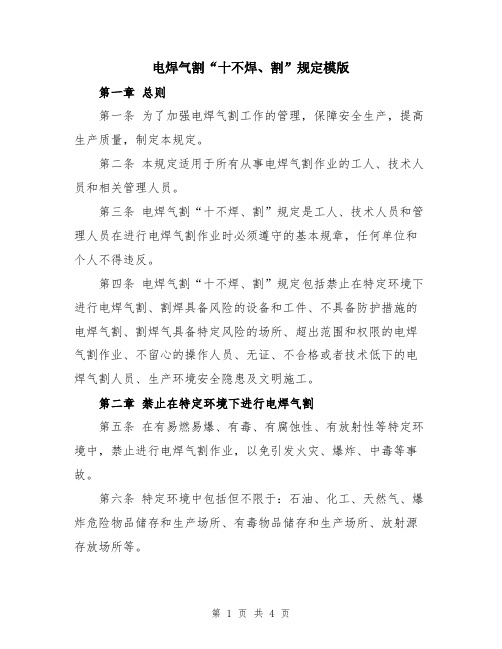
电焊气割“十不焊、割”规定模版第一章总则第一条为了加强电焊气割工作的管理,保障安全生产,提高生产质量,制定本规定。
第二条本规定适用于所有从事电焊气割作业的工人、技术人员和相关管理人员。
第三条电焊气割“十不焊、割”规定是工人、技术人员和管理人员在进行电焊气割作业时必须遵守的基本规章,任何单位和个人不得违反。
第四条电焊气割“十不焊、割”规定包括禁止在特定环境下进行电焊气割、割焊具备风险的设备和工件、不具备防护措施的电焊气割、割焊气具备特定风险的场所、超出范围和权限的电焊气割作业、不留心的操作人员、无证、不合格或者技术低下的电焊气割人员、生产环境安全隐患及文明施工。
第二章禁止在特定环境下进行电焊气割第五条在有易燃易爆、有毒、有腐蚀性、有放射性等特定环境中,禁止进行电焊气割作业,以免引发火灾、爆炸、中毒等事故。
第六条特定环境中包括但不限于:石油、化工、天然气、爆炸危险物品储存和生产场所、有毒物品储存和生产场所、放射源存放场所等。
第七条进行电焊气割作业前,必须对作业环境进行认真检查,确保没有特定环境的存在。
如发现存在特定环境,必须及时采取措施清除或进行必要的防护。
第三章禁止割焊具备风险的设备和工件第八条对于具备风险的设备和工件,禁止进行割焊作业。
具备风险的设备和工件包括但不限于:封闭容器、高压容器、易燃易爆物品、有毒物品、贮存有压力的容器等。
第九条在进行电焊气割作业前,必须对设备和工件进行彻底检查,发现具备风险的设备和工件,必须采取措施移除或进行必要的防护。
第四章不具备防护措施的电焊气割第十条在进行电焊气割作业时,必须配备适当的防护措施,包括但不限于:防护眼镜、防护罩、防护手套、防护服等。
任何对电焊气割作业的操作人员不得离开工作岗位,不得擅自解除或减弱防护措施。
第十一条电焊气割操作人员必须经过专门的培训,了解电焊气割作业的基本知识和安全操作规范。
未经培训或没有相关证书的人员不得从事电焊气割作业。
第五章割焊气具备特定风险的场所第十二条在割焊气具备特定风险的场所,禁止进行电焊气割作业。
焊工“十不焊割”规定

焊工“十不焊割”规定
1. 不得在无焊接设备或不具备焊接条件的情况下进行焊接操作。
2. 不得在有爆炸、易燃、易爆、毒害或腐蚀性物质存在的场所进行焊接操作。
3. 不得使用劣质或未经检验的焊接材料和设备进行焊接操作。
4. 不得在没有采取必要的防护措施的情况下进行焊接操作,如佩戴护目镜、防护面罩、防护手套等。
5. 不得在没有进行必要的安全检查的情况下进行焊接操作,如检查电源线是否有缺陷、设备是否正常等。
6. 不得在没有进行必要的焊接培训和持证上岗的情况下进行焊接操作。
7. 不得在没有经过合格的焊接工程师指导的情况下进行焊接操作。
8. 不得在没有经过焊接操作计划或焊接评估的情况下进行焊接操作。
9. 不得在没有取得相关部门批准的情况下进行特殊焊接作业,如高空焊接、密封容器焊接等。
10. 不得在没有熟悉或掌握焊接材料和设备操作规程的情况下进行焊接操作。
以上是一些常见的焊工“十不焊割”规定,旨在确保焊接操作的安全和质量。
在进行任何焊接操作之前,焊工都应遵守以上规定,并使用正确的焊接设备和材料。
2023年焊工“十不焊割”规定

2023年焊工“十不焊割”规定为了进一步加强焊工行业的管理,提高焊接工作的安全性和质量,2023年,相关部门发布了焊工“十不焊割”规定。
这些规定旨在明确焊工在工作中不得采取的不安全或不合规范的做法,以确保焊工和周围环境的安全。
一、“十不焊割”规定的内容1. 不进行未经许可的焊接工作。
焊工需获得相关证书和执业资格,同时需要遵守焊接作业许可制度,不得擅自进行未经许可的焊接工作。
2. 不在不安全的工作环境下进行焊接工作。
焊工需在安全、通风良好的工作环境下进行焊接作业,不得在易燃、易爆等危险环境下焊接。
3. 不投机取巧,缺乏必要的焊接防护措施。
焊工需正确佩戴个人防护装备,如焊帽、焊眼镜、防护手套等,并确保防护设备完好且能正常使用。
4. 不采用不合规范的焊接操作。
焊工应严格按照焊接工艺规程进行操作,并禁止使用过期、损坏的焊接设备,确保焊接质量和安全。
5. 不进行超负荷的焊接作业。
焊工需根据设备负荷能力和焊接作业规范合理安排焊接工作,不得超过设备负荷能力范围。
6. 不对尚未冷却的焊接部件进行处理。
焊工应等待焊接部件完全冷却后再进行处理,避免烫伤和变形等问题。
7. 不对未知气体进行焊接操作。
焊工需了解工作环境中的气体情况,不得在含有未知气体的环境下进行焊接作业。
8. 不进行超远距离无人监管的焊接作业。
焊工应保持良好的工作纪律,不得单独进行超远距离无人监管的焊接作业。
9. 不对未检修的设备进行焊接作业。
焊工需确保待焊设备或焊接部件经过检修和维护,不得在未经检修的设备上进行焊接。
10. 不以市场竞争为借口违规操作。
焊工应严守职业道德,不得以市场竞争为借口采用不安全、不合规范的焊接操作。
二、严格执行“十不焊割”规定的意义焊工“十不焊割”规定的出台,对于提高焊工工作的安全性和质量具有重要意义。
首先,规定明确了焊工在工作中不得采取的不安全或不合规范的行为,减少了潜在的安全隐患,保障了焊工的人身安全。
其次,规定规范了焊工的工作环境和焊接操作,提升了焊接作业的质量和效率。
焊接作业安全操作规定

焊接作业安全操作规定第一章总则为保障焊接作业人员的人身安全和财产安全,遵循法律法规、安全操作规范,制定本安全操作规定。
第二章基本原则1. 安全第一,预防为主。
尽可能采取措施预防事故的发生,降低事故风险。
2. 严格遵守规章制度。
依法依规进行焊接作业,严禁违反操作规定进行任何形式的焊接工作。
3. 培训合格焊工。
所有从事焊接作业的人员都必须经过正规的培训,取得相应的资格证书。
4. 使用合格设备和工具。
所有使用的焊接设备和工具必须符合国家标准,具备相应的安全保护措施。
第三章应用范围适用于所有从事焊接作业的人员,包括焊工、辅助人员等。
第四章工地安全管理1. 严格遵守工地安全规定。
遵守工地的安全管理制度,穿戴符合规定的安全装备。
2. 保持工作区域整洁有序。
工作区域周边要保持整洁,防止杂物堆积造成火灾隐患。
3. 确保作业区域通风良好。
焊接作业时,需确保通风良好,以防止有毒气体和有害物质的积聚。
4. 禁止在明火附近操作。
在焊接现场,严禁携带火种和其他易燃易爆物品。
第五章个人安全防护1. 穿戴合适的个人防护装备。
在焊接作业过程中,必须穿戴适合的焊接安全帽、防护面罩、防护手套等。
2. 防止电击。
使用绝缘手套、绝缘鞋、绝缘工具等,避免与裸露的电极和电流导线直接接触。
3. 注意人身安全。
焊接作业时,要注意站稳,避免摔倒和跌落,避免与热源、尖锐物体接触。
第六章焊接设备安全操作1. 检查焊接设备。
在使用焊接设备之前,必须仔细检查设备是否正常运转,并确保连接良好。
2. 操作前检查电源和线缆。
焊接设备的电源和线缆必须符合安全规定,无破损或暴露的情况。
3. 尽量避免在湿润的地面上操作。
湿润的地面容易导电,增加触电的风险。
4. 正确使用焊接电流。
根据具体焊接任务,选择合适的电流,避免超负荷操作,以免设备损坏或引发事故。
第七章焊接作业前的准备1. 检查焊接材料。
焊接材料必须符合标准要求,材质应正确、无损伤、无裂纹和缺陷。
2. 清理焊接表面。
焊工“十不焊割”规定模板

焊工“十不焊割”规定模板一、引言为了规范焊工的行为表现,确保焊接工作的安全性和质量,提升企业的整体形象以及员工的工作效率,依据公司相关规定和实际工作需要,订立本规定。
二、适用范围本规定适用于公司全部从事焊接工作的职工。
三、管理标准1.焊工必需遵守焊接工艺规程和相关安全操作规程,确保焊接质量和人身安全。
2.焊工必需熟识使用和保养焊接设备,确保设备安全、正常工作。
3.焊工必需做好焊接料子的检验和保管工作,确保料子质量和使用寿命。
4.焊工必需依照作业计划和要求,定时完成焊接任务。
5.焊工必需保持工作场合的乾净、有序,严禁在工作区域内堆放杂物。
6.焊工必需遵守公司的纪律和规定,听从领导的工作布置。
7.焊工必需自发参加公司相关的培训和学习,提高本身的专业技能水平。
8.焊工必需乐观参加公司的安全生产活动,发现和报告存在的安全隐患。
9.焊工必需妥当处理与同事、领导及其他部门的关系,保持团队合作精神。
10.焊工必需保护公司的机密信息,严禁偷窃公司财物和泄露商业机密。
四、考核标准1.焊接质量标准:焊工的焊接工艺和质量应符合相关标准要求,经质检部门验收合格率应实现90%以上。
2.设备管理标准:焊工对焊接设备的使用和保养工作应得到相关部门的认可,设备故障率应掌控在5%以内。
3.料子管理标准:焊工对焊接料子的检验和保管工作应按要求进行,料子报废率应低于3%。
4.任务完成标准:焊工定时完成焊接任务、工作计划和工作量要求,任务完成率应实现95%以上。
5.工作场合标准:焊工保持工作场合的乾净、有序,工作区域内无杂物,工作区域评估合格率应实现100%。
6.纪律遵守标准:焊工遵守公司的纪律和规定,没有违反工作纪律的行为。
7.学习参加标准:焊工乐观参加公司的培训和学习,参加率应实现90%以上。
8.安全生产标准:焊工参加公司的安全生产活动,发现和报告存在的安全隐患,无重点安全事故发生。
9.团队合作标准:焊工与同事、领导及其他部门的关系处理良好,合作氛围乐观向上。
焊工应遵守的“十不焊割”

焊工应遵守“十、禁止焊接和切割”
“十、禁止焊接和切割”的规定是:
(1)焊工未通过安全技术培训和考试,领取操作证者,不能焊割。
(2)在重点要害部门和重要场所,未采取措施,未经单位有关领导、车间、安全、安全保卫部审批办理动火作业许可证手续,不能焊割。
(3)在容器内工作没有12V低压照明、通风不良,无人看管,不
允许焊接、切割。
(4)未经领导问意,车间、部门擅自拿来的物件,不知道它的用
法和结构,不能焊割。
(5)盛装过易燃、易爆气体(固体)的容器管道,未彻底清洁并
用碱水处理以消除火灾和爆炸风险,不能焊割。
(6)用可燃材料充作保温层、隔热、隔音设备的部位,未采取切
实可靠的安全措施,不能焊割。
(7)压力管道或封闭容器,如空气压缩机、高压气瓶、高压管道、带气锅炉等,不能焊割。
(8)焊接场所附近有易燃物品,未采取间隙或安全措施,不能焊割。
(9)在禁火区内(防爆车间、危险品仓库附近)未采取严格隔离
等安全措施,不能焊割。
(10)在一定距离内,存在与焊接和切割明火操作冲突的工作类
型(如汽油擦洗、喷漆、灌装汽油等能排出大量易燃气体),不能焊割。
安全生产“十不”规定选编.doc

安全生产“十不”规定选编一、电焊气割“十不焊、割”1.焊工一定持证上岗,无特种作业人员安全操作证的人员,禁止进行焊、割作业;2.凡属一、二、三级动火范围的焊、割,未经办理动火审批手续,禁止进行焊、割;3.焊工不认识焊、割现场四周状况,不得进行焊、割;4.焊工不认识焊件内部能否安全时,不得进行焊、割;5.各样装过可燃气体,易燃液体和有毒物质的容器,未经完全冲洗,清除危险性以前,禁止进行焊、割;6.用可燃资料作保温层、冷却层、隔热设备的部位,或火星能飞溅的地方,在未采纳确实靠谱的安全举措以前,禁止焊、割;7.有压力或密闭的管道、容器,禁止焊、割;8.焊、割部位邻近易燃易爆物品,在未作清理或未采纳有效的安全举措以前,禁止焊、割;9.邻近有与明火作业相反抗的工种作业时,禁止焊、割;10.与外单位相连的部位,在没有弄清有无险情,或明知存在危险而未采纳有效的举措以前,禁止焊、割。
1、无特种作业操作证,不焊、割。
2、雨天、露天作业无靠谱安全举措,不焊、割。
3、装过易燃、易爆及有害物品的容器,未进行完全冲洗、未进行可燃浓度检测,不焊、割。
4、在容器内工作无12 伏低压照明和通风不良,不焊、割。
5、设备内无断电,设备未卸压,不焊、割。
6、作业区四周有易燃易爆物品未除去洁净,不焊、割。
7、焊体性质不清、火星飞向不明,不焊、割。
8、设备安全附件不全或无效,不焊、割。
9、锅炉、容器等设备内无专人监护、无防备举措,不焊、割。
10、禁火区内未采纳安全举措、未办理动火手续,不焊、割。
二、起重作业“十不吊”1、起重臂和吊起的重物下边有人逗留或行走禁止吊。
2、起重指挥应由培训合格的专职人员担当,无指挥或信号不清禁止吊。
3、钢筋、型钢、管材等修长和多根物品一定捆扎牢靠,多点起吊。
单头“千斤”或捆扎不牢靠禁止吊。
4、多孔板、积灰斗、手颠覆斗车不用四点吊或大模板外挂板不用卸甲禁止吊。
预制钢筋混凝土楼板禁止双拼吊。
5、吊砌块一定使用安全靠谱的砌块夹具,吊砖一定使用砖笼,并堆放齐整。
- 1、下载文档前请自行甄别文档内容的完整性,平台不提供额外的编辑、内容补充、找答案等附加服务。
- 2、"仅部分预览"的文档,不可在线预览部分如存在完整性等问题,可反馈申请退款(可完整预览的文档不适用该条件!)。
- 3、如文档侵犯您的权益,请联系客服反馈,我们会尽快为您处理(人工客服工作时间:9:00-18:30)。
再论实施军用PCBA“禁止双面焊”的必要性与可行性陈正浩一.引言2009年4月,笔者应北京中际赛威文化有限公司的邀请作了关于“电子装联禁(限用工艺与装联缺陷分析”专题讲座以来,关注者甚多,也引发了一些争议。
二.什么是禁限用工艺?对于严重影响产品质量和可靠性的设计和工艺、影响环境保护和职业健康安全的设计和工艺,包括:易造成产品质量常见病、多发病的工艺,导致产品合格率低的工艺,导致产品质量不稳定又难以控制、难以检测的工艺等;特别是严重影响产品可制造性的设计,我们用禁(限)用工艺来表示。
1.什么是禁用工艺?禁用工艺规定为:“违反国家法律法规、严重污染环境、危害安全生产需要明令禁止的或明确淘汰的工艺,以及严重影响产品质量,易造成引起质量常见病、多发病的工艺;致使产品工艺质量不稳定又难以控制的工艺;技术要求不明确又难以检测的工艺;目前仍在使用但必须明令禁止的工艺;已有先进、成熟的工艺可以取代落后的老工艺”。
2.什么是限用工艺?限用工艺“特指对于从保证产品质量、环境和技术安全的角度出发应予以禁止的,但近期实际使用情况而言,尚无成熟替代工艺,在一定期限内采取规定控制手段的前提下还可使用,但长远必须逐步淘汰的工艺”。
3.禁限用工艺并非航天专利“禁、限用工艺”各行各业都有。
建筑行业有建筑行业的“禁、限用工艺”,食品行业有食品行业的“禁、限用工艺”,机械行业有机械行业的“禁、限用工艺”,林林总总。
“禁、限用工艺”这个名词起因于国家有关部门对加快产品技术进步,淘汰落后的生产能力,促进生产工艺装备和产品的升级换代而发布的《淘汰落后生产能力、工艺和产品的目录》。
“禁、限用工艺”这个名词不是航天的专利,也不是由航天部门首先提出来的。
在电子装联领域,对于实施“禁、限用工艺”的必要性和可行性,长期以来得不到应有的重视。
虽然很多标准内都以“不”、“不能”、“不应”、“不允许”、“应按”等词表述,但或许认识不足,或者由于内容分散,或许由于宣贯不力,并未引起工艺师尤其是电路设计师的高度重视,航天部门给予强调,提出“禁、限用工艺”来规范设计和工艺,对于规范电子产品的设计和工艺,提高产品质量无疑是有益的。
三.“禁止双面焊”的提出及必要性1.“禁止双面焊”的提出QJ3012和QJ3117中规定:“印制电路板金属化孔焊接应采用单面焊,焊料从印制板的一侧连续流到另一侧,禁止双面焊”。
QJ3012和QJ3117相继于1998年和1999年制定,而在这两个标准出台之前,1995年航空部已经制定了《航空产品电装工艺电子元器件的焊接》工艺规范。
《航空产品电装工艺电子元器件的焊接》工艺规范规定:1)金属化孔双面印制板的焊接应符合图1的要求;采用单面焊接,使焊料在孔内充分润湿,并流向另一侧。
2)多层印制板的焊接应符合图2的要求。
严禁两面焊接以防金属化孔内出现焊接不良。
图1图22.“禁止双面焊”的必要性双面印制板,尤其是多层印制板要求单面焊接,禁止两面焊接的原因是显而易见的,就是为了防止金属化孔内出现焊接不良。
图3多层板插装金属化孔、中继孔孔壁隐患的金相分析照片焊料在多层PCB金属化孔中渗透不良的焊点缺陷,将有可能存在内层连接盘与元器件引线接触不良的隐患。
以75%的渗透深度计算,焊点可能存在下面不可靠的结果:厚度为2mm的四至八层印制电路板:金属化孔中将可能有2层中的内层连接盘与元器件引线不能直接通过焊料连接。
见图4a。
厚度为2.2mm的十层以上印制电路板:金属化孔中将可能有3层中的内层连接盘与元器件引线不能直接通过焊料连接。
见图4b。
图4图5插装元器件的金属化孔透锡率差案例3.有人提出这样的问题:“难道就因几个孔不达透锡率要求而报废”?“或重做PCB或废弃元器件”?!并认为处于“消防队员”角色的工艺,一般来讲只能采取“不得已”的做法,只能在航天产品的焊接操作中,往往不得已还是要对不到75%的(甚至还低)透锡率焊接孔进行补焊或另一面焊接(特别是PCB上的连接器插座)”。
那么我们有必要反问,那几块印制板值几个钱?难道为了区区几个钱就可以拿我们战士的生命开玩笑吗?如果多层印制板孔内出现焊接不良,焊接出现隐性故障,还要不要我们宇宙飞船的宇航员和歼击机的飞行员回到祖国的怀抱?四.“禁止双面焊”可以做到有人认为:“这个规定是对的,但在实际操作中这个“禁止”条项是永远完全做不到的”!其实实施“禁止双面焊”并不困难,印制电路板金属化孔透锡率达到100%是可以做到的。
要实施包括“禁止双面焊”需要采取二个步骤:1.构建PCBA的DFM应用平台1)结合产品进行DFM宣贯,《电路可制造性设计》形成企业标准;2)对电路设计人员进行《电路可制造性设计》培训;3)引进PCBA的DFM/DFA分析软件;4)完成DFM/DFA分析软件的二次开发,结合产品应用,用PCBA的DFM/DFA分析软件取代人工审核;5)成立由电路设计师和电装工艺师组成的PCB专业设计组,确保可制造性设计的实施。
2.建立的对电装操作人员长效培训机制,实施“高级电子装联技术”的系统培训。
3.实践的验证实施“禁止双面焊”确实并不困难。
中电科技集团华东电子工程研究所做得比较好;2008年秋,笔者在中国电子科技集团公司举办的培训中,华东电子工程研究所的电装工艺人员明确表态“禁止双面焊”可以做到。
西南电子技术研究所也做得较好,西南电子技术研究所电装车间的电装师傅认为“禁止双面焊”可以做到。
2010年9月我作为中国电子科技集团公司航天产品专项质量检查专家组的一名成员,陪同集团公司张冬辰副总经理和质量安全部仲里主任对西南电子设备研究所进行“航天产品专项质量检查”,其中江南电子通信研究所质量部主任孙勇任设计专家组组长,中电科航空电子有限公司质量部杜培光部长任管理专家组组长,笔者任工艺专家组组长;西南电子设备研究所所毛嘉艺所长等12位西南电子设备研究所领导接待了我们。
西南电子设备研究所工艺室主任及电装工艺师都明确答复:该所的PCBA一般都是单面焊。
同时我们也了解到中国空间技术研究院及航天八院也都做到了禁止双面焊。
华东电子工程研究所,西南电子技术研究所、西南电子设备研究所及中国空间技术研究院及航天八院的经验表明:“禁止双面焊”在实际操作中是可以做到的!五.影响通孔插装元件金属化孔透锡率的主要因素剖析“禁止双面焊”问题的实质实际上就是如何提高通孔插装元器件金属化孔透锡率?印制电路板金属化孔透锡率是衡量电子产品印制电路板焊接质量的一项硬指标,国内外对于不同使用场合电子产品印制电路板的金属化孔透锡率的标准是不一致的。
美国MIL军标和我国航天标准对印制电路板金属化孔透锡率的标准是100%;通孔插装元件金属化孔透锡率不是一个简单的安装焊接问题,它牵涉到以下三个要素:a)元器件引线直径与金属化孔孔径的匹配;b)材料及元器件引线的可焊性;c)焊接工艺参数的正确设置。
1.元器件引线直径与金属化孔孔径不匹配:例如,元器件引线直径过大,堵住了焊料的正常流动,这种情况在IC插座的插针、钽电容器引线与金属化的配合中经常出现。
2.材料及元器件引线的可焊性差:例如,镀金插座的引脚是镀金的,按工艺要求插座引脚首先应作镀锡处理,但实际操作中整机部往往把镀金插座直接送电装工段电装,镀金引脚的焊锡的引流性差,金属化孔透锡率很难达到要求。
又如,我们常用的晶振,其引线材料的可焊性差,不但金属化孔透锡率很难达到要求,而且容易造成虚焊。
再如,对IC的引脚是不进行预处理的,IC的引脚在空气中暴露时间过长,表面氧化严重,金属化孔透锡率也很难达到要求。
3.元器件引线根部的漆层未去除干净或元器件安装贴板安装,元器件引线根部的漆层堵住了焊料的流动,使金属化孔透锡率差;这种情况在独石电容的焊接中经常出现。
4.印制板焊盘的可焊性差:印制板生产检验合格后必须用聚乙烯塑料薄膜包装,严禁用手触摸,并且包装开封后一周内必须装配完成。
但实际情况是检验合格的印制板大部分是未经包装由设计师用手触摸交到电装工段的,从印制板生产检验合格到电装完成很难在一周内装配完成,生产过程中在没有经过任何保护的情况下,在空气中暴露保存;如此势必造成印制板焊盘及印制板金属化孔严重氧化,降低了印制板金属化孔的可焊性。
5.印制板金属化孔的镀覆质量差,印制板金属化孔的镀覆质量并不能达到相关标准:1)金属化孔镀铜层平均厚度为25um~30um,最薄处不小于20um。
2)金属化孔铜镀层不应有超过以下规定的任何空洞:(1)一个金属化孔的镀层空洞应不多于1个;(2)空洞的长度不应超过金属化孔孔壁总高的5%。
(3)空洞的长度不应超过金属化孔孔壁总高的5%。
3)孔壁缺陷:金属化孔壁不应有超过以下规定的任何缺陷:(1)结瘤、镀层空洞以及玻璃钎维伸出而使孔径或孔壁铜层厚度减少时,其值不得小于规定的最小值;(2)镀层及涂层应无裂纹。
4)金属化孔可焊性:按航天标准“印制电路板试验方法”的规定试验后,焊料应润湿到孔顶周围的焊盘(连接盘)上,必须完全润湿孔壁,不允许有不润湿或露基底金属的现象。
不完全填满孔是可接受的,但焊料相对于孔壁的接触角应小于90º。
板厚与孔径比大于5的印制板,金属化孔的可焊性由供需双方商定。
但实际情况是,印制板金属化孔的镀覆质量缺乏有效的检测手段;用视频检测仪对部分印制板金属化孔的镀覆质量进行检测,金属化孔内镀层空洞及空洞的长度均没有达标,金属化孔内镀层结瘤多,镀层及涂层出现裂纹等。
6.焊接温度偏低:手工焊接温度偏低或焊接时间的太短,波峰焊预热温度偏低及预热时间不足,波峰焊焊接温度偏低及传动速度过快,会造成金属化孔未焊透。
对于手工焊接温度偏低或焊接时间的太短,大部分发生在经验不足的操作人员以及落后的装配工具上。
上述这些问题,有些是技术问题,有些是设备问题,有些则是管理上的问题,其中主要是元器件引线直径与金属化孔孔径的匹配问题,只要做到上述三个方面,克服目前在印制板设计、加工、装配中存在的问题,金属化孔透锡率合乎要求并不难做到。
六.如何提高印制电路板金属化孔透锡率?要做到印制电路板金属化孔透锡率为100%,实现“禁止双面焊”需要从以下五个方面着手:a)元器件引线直径与金属化孔孔径匹配;b)基体金属-印制电路板焊盘、金属化孔的可焊性;c)基体金属-元器件引线、焊脚的可焊性;d)焊接温度与焊接时间;e)助焊剂的润湿作用。
1.PCB电路设计元器件引线直径必须与金属化孔孔径匹配,采用手工焊接工艺时金属化孔孔径应比元器件引线直径大0.2mm~0.4mm,采用波峰焊接工艺时金属化孔孔径应比元器件引线直径大0.2mm~0.3mm;这是提高印制电路板金属化孔透锡率的关键因素。
为实现上述要求,设计人员对元器件引线直径的了解和掌握应如同对片式元器件引脚/焊端尺寸了解和掌握一样,像设计片式元器件焊盘一样来设计通孔插装元器件的金属化孔。