淬火工艺守则
热处理淬火工艺规范

热处理车间淬火工艺规范一、调质1.1 调质定义为了达到产品的工艺硬度要求,得到回火索氏体,得到良好的强韧性,提高使用性能和寿命,因此曲轴和连杆产品需进行调质处理。
调质,即淬火加高温回火,以获得回火索氏体组织,主要用于中碳碳素结构钢或低合金结构钢以获得良好的综合机械性能。
1.1.1 淬火的定义淬火是将钢加热到临界温度Ac3 (亚共析钢)或Ac1 (过共析钢)以上温度,保温一段时间,使之全部或部分奥氏体化,然后以大于临界冷却速度的冷速快冷到Ms以下(或Ms附近等温)进行马氏体(或贝氏体)转变的热处理工艺。
通常也将铝合金、铜合金、钛合金、钢化玻璃等材料的固溶处理或带有快速冷却过程的热处理工艺也称为淬火。
1.1.2淬火的目的淬火的目的是使过冷奥氏体进行马氏体或贝氏体转变,得到马氏体或贝氏体组织,然后配合以不同温度的回火,以大幅提高钢的刚性、硬度、耐磨性、疲劳强度以及韧性等,从而满足各种机械零件和工具的不同使用要求。
也可以通过淬火满足某些特种钢材的铁磁性、耐蚀性等特殊的物理、化学性能。
1.1.3回火的定义回火是工件淬硬后加热到Ac1 (加热时珠光体向奥氏体转变的开始温度)以下的某一温度,保温一定时间,然后冷却到室温的热处理工艺。
按回火温度范围,回火可分为低温回火、中温回火和高温回火。
4.1.1低温回火:工件在150~250C进行的回火。
目的是保持淬火工件高的硬度和耐磨性,降低淬火残留应力和脆性,回火后得到回火马氏体,指淬火马氏体低温回火时得到的组织。
应用范围:主要应用于各类高碳钢的工具、刃具、量具、模具、滚动轴承、渗碳及表面淬火的零件等。
4.1.2中温回火:工件在350〜500 C之间进行的回火。
目的是得到较高的弹性和屈服点,适当的韧性。
回火后得到回火屈氏体,指马氏体回火时形成的铁素体基体内分布着极其细小球状碳化物(或渗碳体)的复相组织。
应用范围:主要用于弹簧、发条、锻模、冲击工具等。
4.1.3高温回火:工件在500~650C以上进行的回火。
确定淬火工艺规范的原则3-5

3.5 确定淬火工艺规范的原则淬火工艺方法及其应用淬火工艺规范包括1)淬火加热方式、2)加热温度、3)保温时间、4)冷却介质及冷却方式等。
确定工件淬火规范的依据是工件图纸及技术要求,所用材料牌号,相变点及过冷奥氏体等温或连续冷却转变曲线,端淬曲线,加工工艺路线及淬火前的原始组织等。
只有充分掌握这些原始材料,才能正确地确定淬火工艺规范。
一、淬火加热方式及加热温度的确定原则淬火一般是最终热处理工序。
因此,应采用保护气氛加热或盐炉加热。
只有一些毛坯或棒料的调质处理(淬火、高温回火)可以在普通空气介质中加热。
因为调质处理后尚须机械切削加工,可以除去表面氧化、脱碳等加热缺陷。
但是随着少、无切削加工的发展、调质处理后仅是一些切削加工量很小的精加工,因而也要求无氧化,脱碳加热。
淬火加热一般是热炉装料。
但对工件尺寸较大,几何形状复杂的高合金钢制工件,应该根据生产批量的大小,采用预热炉(周期作业)预热,或分区(连续炉)加热等方式进行加热。
1:淬火加热温度:淬火加热温度,主要根据钢的相变点来确定。
对亚共析钢,一般选用淬火加热温度为Ac3+(30—50℃),过共析钢则为Ac1+(30—50℃)。
之所以这样确定,因为对亚共析钢来说,若加热温度低于Ac3,则加热状态为奥氏体与铁素体二相组成,淬火冷却后铁素体保存下来,使得零件淬火后硬度不均匀,强度和硬度降低。
比Ac3点高30—50℃的目的是为了使工件心部在规定加热时间内保证达到Ac3点以上的温度,铁素体能完全溶解于奥氏体中,奥氏体成分比较均匀,而奥氏体晶粒又不致于粗大。
对过共析钢来说,淬火加热温度在Ac1~Ac3之间时,加热状态为细小奥氏体晶粒和未溶解碳化物,淬火后得到隐晶马氏体和均匀分布的球状碳物。
这种组织不仅有高的强度和硬度、高的耐磨性,而且也有较好的韧性。
如果淬火加热温度过高,碳化物溶解,奥氏体晶粒长大,淬火后得到片状马氏体(孪晶马氐体),其显微裂纹增加,脆性增大,淬火开裂倾向也增大。
(完整)热处理工艺守则

一、热处理代号和材料标注方法(一)热处理代号1. 适用于结构钢和铸件代号:0—自然状态1—正火(或正火+回火)2—退火3—精锻+回火(如精锻或精辊叶片在精锻后只需高温回火)4—淬硬5—调质6—化学热处理(渗碳或氮化)7—除应力(包括活塞环定型处理)9—表面淬火或局部淬火2.适用铸造有色金属和奥氏体钢的代号:0—原始状态1—再结晶退火T—除应力退火T1-人工时效T4—淬火(固溶处理)T5—淬火和不完全时效T6-淬火和完全时效(固溶处理和完全时效到最高硬度)3.压力加工有色金属代号:0—原始状态M—退火C-淬火CZ—淬火和自然时效CS-淬火和人工时效(二)材料的标注方法:1.零件的材料或毛坯(包括铸锻件)如不作任何处理,也不作机械性能检查,则只标材料牌号(其热处理代号“0”在图纸上不标注)如:A3,20,35,ZQSn6—6-3。
2.零件的材料或毛坯在热处理后,不作硬度及机械性能检查者则只标注材料牌号和热处理代号:如:45-1,若有几种热处理,可用热处理代号按工艺路线顺序逐项填写:如:15CrMoA-1+7。
3.有些材料的技术条件,有几种检查组别,但强度等级只有一种或可按材料截面尺寸来决定强度等级,只注明材料牌号,热处理代号和检查组别:如:45—5(Ⅱ) 35CrMoA—5(Ⅱ)4.有些材料的技术条件,有几种组别,在同一热处理状态中有不同的强度等级,则注明材料牌号、热处理代号强度等级和检查组别,不需要规定检查组别时,检查组别可省略。
25Cr2MoVA-5 25Cr2MoVA-5如:735—Ⅲ 7355。
有些零件或者是比较重要或者是技术要求比较复杂,用上述标注方法不能说明全部要求者,则应注明标准号,在同一热处理状态中有不同的强度级别时,还应注明强度级别。
35CrMoA-5 35CrMoA-5如:Q/CCF M 3003-2003 590×Q/CCF M 3003—20036。
大锻件如叶轮、铸造轴、整体转子等的材料标注方法钢号锻件级别×标准编号7。
淬火工艺规程

淬火工艺规程1主题内容与适用范围本标准规定阀门零件、工具、模具等金属材料的淬火工艺。
本标准的淬火,除指在通常的冷却水、油、空气中淬火之外,还包括热浴中的分级和等温淬火。
适用于阀门零件、工具、模具等金属材料在箱式电阻炉,盐浴炉中淬火。
2技术内容2.1 淬火的定义把钢加热到临界点(Ac3或Ac1)以上,使之奥氏体化,保温一定的时间,然后以大于临界冷却速度的冷却速度快速冷却,获得马氏体组织的工艺过程,称为淬火。
2.2 淬火的目的2.2.1 对于优质结构钢工件,通过淬火与适当的回火配合来满足工件性能要求,如:强度、硬度、塑性及韧性等的不同配合。
2.2.2对于各种碳钢、合金钢及表面热处理或化学热处理的工件,通过淬火得到高硬度的马氏体组织,然后低温回火,用以提高其硬度及耐磨性。
2.3 淬火前的准备2.3.1 检查工件表面有无裂纹、尖角及锈蚀等影响淬火质量的缺陷。
2.3.2 根据图纸及工艺文件,明确工件淬火的具体要求,如硬度、局部淬火范围等。
12.3.3 检查淬火工具、冷却剂是否齐全,有不需要淬硬的孔眼、尖角或厚度变化较大时,为了防止变形和开裂危险,应采用堵塞或缠绕石棉绳,使工件各部分加热和冷却均匀。
2.3.4 如果工件表面要求不允许有氧化皮和脱碳的现象时,可在盐炉或通有保护气体的炉中加热。
2.3.5 在箱式电炉中加热时,为防止氧化、脱碳现象发生,可将工件加热到200~350℃,然后撒上硼酸粉末,放入炉中加热(加热温度不得超过950℃),也可在工件表面敷以石棉板或生铁屑,使之与空气隔绝;或将工件装入盛有木碳或已用过的铸铁屑的铁箱内,加盖密封。
2.3.6 大批工件(或两件以上),应作首件或小批量试淬。
认可后方可进行批量生产,并在生产过程中经常抽检。
2.3.7 工件淬火硬度不够而返修时,可重新淬火。
重新淬火的原则如下:形状简单的工件,水淬者可不经退火而重新淬一次;油淬者可不经退火而重新淬火两次;形状复杂的工件和精度要求高的工件需进行退火、高温回火或正火处理;高速钢需经退火、消除残余应力后,方可重新淬火。
淬火件加工工艺规范

表号:HTT-R-Q1DC004 Rev: A0文件发行(修订)/会签表文件发行类型■新版发行□版本修订□文件作废文件名称:淬火件加工工艺规范文件编号:HTT-M-M1-PC002版本生效日期修改说明编制部门编制审核批准A01 2012-04 新版发行工艺门晓波文件会签记录部门会签意见签名部门会签意见签名市场部□管理部-人力□项目部□管理部-行政□技术部□质量部□模具机械事业部□采购部□金属成型事业部□审计部□塑料材料制品事业部□财务部□淬火件加工工艺规范版本:A0文件编号:HTT-M-M1-PC002编制:门晓波日期: 2012 年 3 月 10日审核:日期: 年月日批准:日期: 年月日受控印章只有盖有“受控”副本印章的文本才可以作为工作之用途。
淬火件加工工艺规范1.目的规范淬火件加工规范,指导淬火件加工,杜绝淬火件质量事故.2.适用范围设计,工艺,NC,计划,质量,编程,线割.深孔钻3.术语/定义无淬(zhàn)火:淬火是将材料(如:钢)加热到临界温度以上,然后快速冷却的热处理工艺。
淬火的目的是大幅提高钢的强度、硬度、耐磨性、疲劳强度以及韧性等,从而满足各种机械零件和工具的不同使用要求。
4.职责4.1 设计:开料预留变形余量,布料图设计两个框,2D图画两个框,基准角标注YM;4.2工艺:在工艺中指出需淬火工件,开粗余量,工艺、工序安排;4.3工序:按工艺要求进行淬火前后的加工,加工完通知检验;4.4 NC:硬模开粗后、精加工结束分别通知质检检验;4.5 编程员:按工艺指示、本规范要求编制淬火件开粗、精加工程序;4.6 检验:淬火前检验形状是否遗漏,淬火后检验硬度,加工完标检验3D尺寸;5.工作程序/管理要求结构设计阶段:5.1 模具结构工艺评审时确定哪些工件需要淬火,确定预留变形量;5.2 预留变形量设定参考:1.工件长度≤100mm,开料尺寸单边余量△A=0.5mm;2.100mm<工件长度≤400mm,开料尺寸底面和顶面都留余量△A=1mm,侧壁单边余量△A=0.5mm;c.工件长度>400mm,开料尺寸单边余量△A=1mm;3.易变形工件:如薄板件、细长件,由工艺、结构评审定出预留变形量;5.3 需要淬火的工件工程师开料时按以上要求开毛料,零件图上的布料图设计两个框,2D图上也要画两个框,外框为毛料用虚线表示,内框为净料用实线表示,基准角标注YM,如下图所示:加工工艺规范:6.1 淬火前:(分主镶块、小镶块两种情况)6.1.1 主镶块淬火前:A.准备加工:按毛胚尺寸铣六方、磨料、加工工艺螺丝孔、吊装螺丝孔、攻丝、四周倒角;B.深孔钻:加工穿丝孔、所有避空孔、水路及胚头;C.编程:1.编程时加工坐标系设在净料基准边,Z向为净料最高点;2.按工艺要求设置开粗余量,常规情况设置如下:工件长度≤300mm时,开粗余量1mm;300mm<工件长度≤600mm时,开粗余量1.5mm;工件长度>600mm时,开粗余量2mm;3.在镶块四角各预留一个面积不小于25*25的辅助支撑平台,供磨床加工用;4.在每个平台上加工一个工艺螺丝孔,以便NC加工反面时收工艺板用,注意螺丝孔避开形状;5.避空面直接加工到数;6.开粗要求工件表面余量尽量均匀;7.有公差要求的孔加工底孔,单边预留0.5-1mm;镶块槽里的固定螺丝孔和镶块吊装孔直接加工出并攻牙;8.单独出开粗工艺卡,NC加工:按开粗工艺卡要求碰数偏移并进行加工;D.检验:因工件淬火后,不能再加工孔,以上工作完成后,由质检检查是否有漏加工部位,主要检查有没有漏加工孔,如果全部加工完成,淬火处理;6.1.2 小镶块淬火前:A.准备加工: 按毛胚尺寸铣六方、磨料、加工工艺螺丝孔、吊装螺丝孔、穿丝孔、所有避空孔、水路及胚头、攻丝、四周倒角,小镶块台阶和圆形工件外形开粗;B.检验:检验形状是否遗漏7.2.2 淬火后:A.硬度检验:淬火回厂后送质检检验硬度,编程员根据实际硬度进行编程参数设定;B.准备加工:1.校平截面积最大的一个面作为第一个磨削面,其它各面以此面为准进行磨削;2.工件底面磨削量按△A磨削到数,侧面按净料尺寸将工件分中磨削到数;3.如果工件的长度太长准备无法磨长度方向基准,准备先将其余基准磨到位后,转由线切割或NC卧铣加工长度方向基准;C.编程:a.加工坐标系跟淬火前开粗时相同;b.毛胚设置X、Y到净料,Z向比开粗后毛胚适当加大0.5mm;c.淬火件因硬度高,对刀具及切削参数有特殊要求,需选用淬火件专用刀具、专用切削参数(参考质量部实际检测硬度设置);d.淬火件程序需非常优化,刀路不严谨很容易造成刀具报废、工件过切,淬火件程序要求主管复检;e.单独出精加工工艺卡;D.NC加工:按精加工工艺卡要求碰数偏移;硬模分型面研配是打磨困难,要求NC加工必须到数,分型面加工完划线检验,如不到数重复加工,直到到数;序号记录/模版名称编号编制/使用部门保存场所12。
淬火工艺规程

淬火工艺规程一、淬火前得准备1、检查工件表面,不允许有碰伤、裂纹、锈斑、油垢及其她脏物存在,油垢可用碱煮洗,锈斑可用喷砂或冷酸清洗。
2、准备淬火所用得工具,检查设备就是否完好。
3、检查控温仪表指示就是否正确。
4、工件形状复杂得,其中有不需要淬硬得孔眼、尖角或厚度变化大得地方,为了防止变形与淬裂得危险均应采用堵塞或缠绕石棉得方法,使工件各部分加热及冷却温度均匀。
5、要求工件表面不允许有氧化脱碳现象,要用硼砂酒精溶液涂覆。
二、淬火规范1、加热温度(1)亚共析钢淬火加热温度为Ac3+30~50℃,一般在空气炉中加热比在盐浴中加热高10~30℃,采用油、硝盐淬火介质时,淬火加热温度应比水淬提高20℃左右。
(2)共析钢、过共析钢淬火加热温度为Ac1+30~50℃,一般合金钢淬火加热温度为Ac1或Ac3+30~50℃.(3)高速钢、高铬钢及不锈钢应根据要求合金碳化物溶入奥氏体得程度选择。
过热敏感性强及脱碳敏感性强得钢,不易取上限温度.(4)低碳马氏体钢淬透性较低,应提高淬火温度以增大淬硬性;中碳钢及中碳合金钢应适当提高淬火温度来减少淬火后片状马氏体得相对量,以提高钢得韧性;高碳钢采用低温淬火或快速加热可限制奥氏体固溶碳量,而增加淬火后板条马氏体得含量,减少淬火钢得脆性.另外,提高淬火温度还会增加淬火后得残余奥氏体量。
2、加热方法(1)模具:室温进炉或300—400℃进炉,并在550—600℃时等温一段时间。
(2)弹簧或原材料(调质处理),可在淬火温度时进炉.3、保温时间加热与保温时间由零件入炉到达指定工艺温度所需升温时间(ι1),透热时间(ι2)及组织转变所需时间(ι3)组成。
ι1+ι2由设备功率、加热介质及工件尺寸、装炉数量等因素决定,ι3则与钢材得成分、组织及热处理技术要求有关。
普通碳钢及低合金钢在透热后保温5~15min即可满足组织转变得要求,合金结构钢透热后应保温15~25min。
高合金工具钢、不锈钢等为了溶解原始组织中得碳化物,应在不使奥氏体晶粒过于粗化得前提下,适当提高奥氏体化温度,以缩短保温时间。
球墨铸铁淬火工艺规范(精)

球墨铸铁淬火工艺规范
热处理规范金相组织备注
回火索氏体+少量铁素体及球状石墨淬火
以前最好先经正火当铸件中存在过量
自由渗碳体时,在淬火前必须进行高温
石墨化退火,以免析出二次网状渗碳
体,这种方式叫“二阶段淬火”。
考虑
到回火脆性,应尽量避免250~300℃范围
内淬火
石墨
石墨
表面层为细针状马氏体+少量残留奥氏体及球状石墨,过渡层为小岛状马氏体+细小铁素体,内部与原始组织相同对铁素体基体的球铁,必须先进行正火,使珠光体量≥70%,有时为了消除淬火应力而在380~410℃温度范围内回火处理
提高强度、硬度和耐磨性,减少淬火变形及裂纹。
它是发挥球铁材料最大潜力的热处理方法下贝氏体+少量马氏体+少量残留奥氏体+
球状石墨
铸态组织需无游离渗碳
石墨化退火。
等温淬火
获得良好的强度和韧性下贝氏体+碎片状铁素体铸态组织需无游离渗碳石墨化退火。
等温淬火。
高频淬火工艺守则(新)

高频淬火工艺守则高频设备是主要用于表面淬火的热处理设备,但是现阶段一般中小型工厂因产品数量少,品种多,又使用万能淬火机床并且还缺乏测温装置和能量控制机构,所以仍是手工操作。
这就要求操作者有熟练的技术水平来掌握。
一、高频加热的基本原理在置于高频电流感应器中的钢铁工件内,产生频率相等、方向相反的感应电流(即所谓涡流),同时反复被磁化的钢铁的磁滞损失,使电磁能转变为热能,将工件加热到淬火温度。
在高频加热过程中将有以下两个效应特别的显示出来。
1、邻近效应:高频电流与其感生电流相互邻近的现象。
2、集肤效应(或叫趋肤效应)感生电流集中于被加热工件表面的特性。
二、特性1、设备应具备以下条件方可使用:(1) 设备必须按说明书规定调试合格后方可交付生产者使用。
(2) 水压指数正常,水压继电器及阀门开关灵敏可靠,且内部循环水管无漏水现象。
(3) 设备所有指示灯指示正常,仪表指示准确。
(4) 自动空气开关及过流继电器动作灵敏可靠。
(5) 电源电压在±10%范围内。
(6) 反馈及耦合线圈的手轮旋转灵活,指示准确。
(7) 高频室内温度在15-35℃之间使用设备室温<15或>35℃要经研究后方可使用,其它事项要按使用说明书使用。
2、设备的启用:(1)闸流管及空气二极管的灯丝分三步送电,除新设备外,正常使用的设备可分两步送电。
第一步预热加全压的2/3,为3.5-4V,待20-30分钟后,加全压5±0.25。
振荡管送电也分两步,预热电压为22-23V,工作到位33V。
预热时间与闸流管相同。
(2)把移相变阻器手轮置于最左边位置,合上整流高压开关,阳极电压应指6.75KV左右,逐渐转动移相器至右端,电压应平稳升至13.5KV左右,正常使用时应在11-13KV。
除螺纹退火,小零件加热处,低于10KV的电压,一般不采用。
(3)感应器中置入工件,接通加热电源,仔细观察阳极电流表、栅极电流表所示的数值。
以便决定反馈耦合手轮是否需进一步调节,工作时应使其在最佳工作状态,阳极电流与栅极电流应约为5:1,最大阳极电流不得超过12A,栅极电流不得超过2.5A。
淬火工艺守则

淬火工艺守则淬火是热处理的主要工序之一。
就钢铁材料而言,它是把工件加热到预期的温度。
保温一定时间,然后在选定的冷却介质中冷却,以获得马氏体等组织的一种操作。
淬火工序严格操作就为回火工序的正常进行创造条件。
如果淬火工序马虎,就会造成产品的返修或报废。
为此,在淬火过程中,必须严格按工艺进行。
一、淬火工艺总则1、淬火加热温度:正确的选择淬火加热温度是保证得到预期的淬火后的金相组织和机械性能的重要条件。
钢铁材料的成分不同,其加热温度各不相同。
就碳素钢而言,Fe-Fe3C系平衡相图就是其加热温度选择的重要依据。
G对合金钢而言,由于其合金成分不相同,所以,加热温度不相同。
设备:中温盐浴炉5CrMnMo钢热锻模淬火工艺曲线设备:箱式电阻炉淬火有时个别零件需要表面淬火而高频由于条件所限,不能处理时,用盐炉快速加热,加热温度一般为其钢牌号的正常加热温度高出100℃以上.但是形状特别复杂的零件不宜采用.2、加热时间:加热时间由工件的升温时间和保温时间两部分组成,过长的加热时间会使工件晶粒粗大,增加工件淬火后的脆性,从而降低工件的机械性能。
此外,还易使工件表面氧化及脱碳,造成能源浪费。
反之,加热时间过短又往往达不到预期的淬火目的。
所以,一般采用其实际保温时间约占加热时间的1/2-2/3。
(1)在实际生产中根据设备条件,产品材料成分、几何尺寸、装炉量各不相同,加热时间也不相同。
经验公式计算:t = 加热时间(分)H = 工件有效厚度(MM)盐炉加热时间:碳钢t = (0.25-0.5)H(分)合金结构钢t = (0.5-1)H(分)(2)中温电阻炉加热时间计算:碳钢:t = (1-1.5)H(分)合金结构钢:t = (1.5-2)H(分)箱式电阻炉装活只准单层装炉加热不准层叠装炉加热。
工件距电阻丝和后墙>100MM,距炉门口400-450MM。
井式电阻炉装活单吊装炉加热。
(3)气体渗碳炉不准做淬火加热用,如需用时经研究后是否能使用。
热处理工艺规范
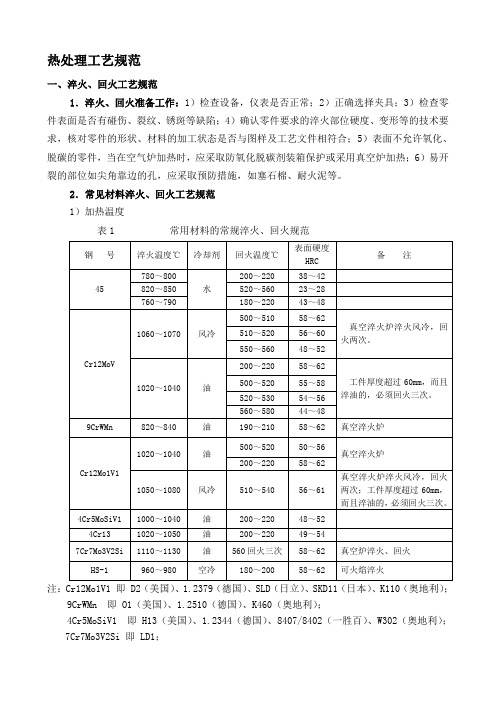
热处理工艺规范一、淬火、回火工艺规范1.淬火、回火准备工作:1)检查设备,仪表是否正常;2)正确选择夹具;3)检查零件表面是否有碰伤、裂纹、锈斑等缺陷;4)确认零件要求的淬火部位硬度、变形等的技术要求,核对零件的形状、材料的加工状态是否与图样及工艺文件相符合;5)表面不允许氧化、脱碳的零件,当在空气炉加热时,应采取防氧化脱碳剂装箱保护或采用真空炉加热;6)易开裂的部位如尖角靠边的孔,应采取预防措施,如塞石棉、耐火泥等。
2.常见材料淬火、回火工艺规范1)加热温度表1 常用材料的常规淬火、回火规范注:Cr12Mo1V1 即 D2(美国)、1.2379(德国)、SLD(日立)、SKD11(日本)、K110(奥地利);9CrWMn 即 O1(美国)、1.2510(德国)、K460(奥地利);4Cr5MoSiV1 即 H13(美国)、1.2344(德国)、8407/8402(一胜百)、W302(奥地利);7Cr7Mo3V2Si 即 LD1;HS-1是高级火焰淬火,多用模具钢;除45号钢或特别说明均采用回火两次的工艺。
2)淬火保温时间t =8~10 min+kαDk——装炉系数(1~1.5);α——保温系数(见表2);D——零件有效厚度。
表2 淬火保温系数3)回火保温时间①工件有效厚度d<=50mm,保温2小时;②工件有效厚度d>50mm,按照保温时间t=d/25(小时)计算;③每次回火后空冷至室温,再进行下次回火。
4)去应力(入炉时效)①高合金钢550~650℃,热透后,保温时间>3小时;3.淬火和回火设备1)淬火设备——真空淬火炉、中温箱式炉、高温箱式炉。
2)回火设备——真空回火炉、中温箱式炉。
3)冷却设备——水槽、油槽、风箱。
4.操作方法1)零件应均匀摆放于炉内有效加热区,在箱式炉中一般为单层排列加热,工件间适当间隙。
小件可适当堆放,但要酌情增加保温时间。
2)细长零件加热要考虑装炉方法,以减少工件变形,如垂直吊挂,侧立放平支稳等。
淬火标准工艺

淬火工艺Hardening or Quenchingcui huǒ(行业内,淬读"zàn"音,即读“zàn huǒ”)钢旳淬火是将钢加热到临界温度Ac3(亚共析钢)或Ac1(过共析钢)以上某一温度,保温一段时间,使之所有或部分奥氏体[1]化,然后以不小于临界冷却速度旳冷速快冷到Ms如下(或Ms附近等温)进行马氏体(或贝氏体)转变旳热解决工艺。
一般也将铝合金、铜合金、钛合金、钢化玻璃等材料旳固溶解决或带有迅速冷却过程旳热解决工艺称为淬火。
淬火旳目旳是使过冷奥氏体进行马氏体或贝氏体转变,得到马氏体或贝氏体组织,然后配合以不同温度旳回火,以大幅提高钢旳强度、硬度、耐磨性、疲劳强度以及韧性等,从而满足多种机械零件和工具旳不同使用规定。
也可以通过淬火满足某些特种钢材旳旳铁磁性、耐蚀性等特殊旳物理、化学性能。
淬火能使钢强化旳主线因素是相变,即奥氏体组织通过相变而成为马氏体组织(或贝氏体组织)。
钢淬火工艺最早旳应用见于河北易县燕下都遗迹出土旳战国时代旳钢制兵器。
淬火工艺最早旳史料记载见于《汉书.王褒传》中旳“清水焠其峰”。
“淬火”在专业文献上,人们写旳是“淬火”,而读起来又称“蘸火”。
“蘸火”已成为专业口头交流旳习用词,但文献中又看不到它旳存在。
也就是说,淬火是原则词,人们不读它,“蘸火”是常用词,人们却不写它,这是国内文字中不多见旳现象。
淬火是“蘸火”旳正词,淬火旳古词为蔯火,本义是灭火,引申义是“将高温旳物体急速冷却旳工艺”。
“蘸火”是冷僻词,属于现代词,是文字改革后浮现旳产物,“蘸”字本义与淬火无关。
“蘸火”本词为“湛火”,“湛”字读音同“蘸”,而其字形又与水、火有关,符合“水与火合为蔯”之意,字义与“淬火”相通。
“湛火”为本词,“蘸火”则为假借词。
淬火将金属工件加热到某一合适温度并保持一段时间,随后浸入淬冷介质中迅速冷却旳金属热解决工艺。
常用旳淬冷介质有盐水、水、矿物油、空气等。
热处理淬火工艺规范

热处理车间淬火工艺规范一、调质1.1 调质定义为了达到产品的工艺硬度要求,得到回火索氏体,得到良好的强韧性,提高使用性能和寿命,因此曲轴和连杆产品需进行调质处理。
调质,即淬火加高温回火,以获得回火索氏体组织,主要用于中碳碳素结构钢或低合金结构钢以获得良好的综合机械性能。
1.1.1 淬火的定义淬火是将钢加热到临界温度Ac3(亚共析钢)或Ac1(过共析钢)以上温度,保温一段时间,使之全部或部分奥氏体化,然后以大于临界冷却速度的冷速快冷到Ms以下(或Ms附近等温)进行马氏体(或贝氏体)转变的热处理工艺。
通常也将铝合金、铜合金、钛合金、钢化玻璃等材料的固溶处理或带有快速冷却过程的热处理工艺也称为淬火。
1.1.2 淬火的目的淬火的目的是使过冷奥氏体进行马氏体或贝氏体转变,得到马氏体或贝氏体组织,然后配合以不同温度的回火,以大幅提高钢的刚性、硬度、耐磨性、疲劳强度以及韧性等,从而满足各种机械零件和工具的不同使用要求。
也可以通过淬火满足某些特种钢材的铁磁性、耐蚀性等特殊的物理、化学性能。
1.1.3 回火的定义回火是工件淬硬后加热到Ac1(加热时珠光体向奥氏体转变的开始温度)以下的某一温度,保温一定时间,然后冷却到室温的热处理工艺。
按回火温度范围,回火可分为低温回火、中温回火和高温回火。
4.1.1低温回火:工件在150~250℃进行的回火。
目的是保持淬火工件高的硬度和耐磨性,降低淬火残留应力和脆性,回火后得到回火马氏体,指淬火马氏体低温回火时得到的组织。
应用范围:主要应用于各类高碳钢的工具、刃具、量具、模具、滚动轴承、渗碳及表面淬火的零件等。
4.1.2中温回火:工件在350~500 ℃之间进行的回火。
目的是得到较高的弹性和屈服点,适当的韧性。
回火后得到回火屈氏体,指马氏体回火时形成的铁素体基体内分布着极其细小球状碳化物(或渗碳体)的复相组织。
应用范围:主要用于弹簧、发条、锻模、冲击工具等。
4.1.3高温回火:工件在500~650℃以上进行的回火。
12锻热厂中温盐炉淬火工艺守则

中温盐炉淬火工艺守则一、对淬火零件的要求1、淬火零件的内部组织应为预先热处理(退火、正火、调质)的合格组织。
2、淬火零件表面宏观无裂纹、夹灰、磕碰、划伤、锈斑、毛刺、飞边等。
3、淬火零件材料牌号必须符合图纸、工艺要求。
4、蜗杆类零件淬火前的齿面粗糙度为:M≥12时,不大于Ra3.2;M<12时,不大于Ra6.3。
二、加热前的准备工作1、零件包扎前要仔细检查:(1)、零件表面裂纹、夹灰、磕碰、锈斑、加工余量。
(2)、确认零件要求的淬火部位、硬度、变形等技术要求,核对零件的形状、材料、加工状态是否与图纸及工艺文件相符(材料代用凭代用单)。
(3)、如有疑问预先提出联系。
2、零件包扎时要符合下列要求:(1)、所用铁丝或工具应符合下表(见表1)要求:表1注:两股合用,零件允许最大重量按单股的1.6倍计。
(2)、用钳子包扎零件时,要注意防止将铁丝扭伤。
(3)、包扎或用工具时,必须注意防止零件在加热与冷却过程中产生变形、开裂、软点等。
轴类零件用铁丝包扎时,必须对称垂直。
(4)、在下列情况下必须用铁丝石棉包扎:Ⅰ:退刀槽深大于2mm。
Ⅱ:直径不均匀的轴类:a、φ大≤50mm。
φ小≤1/3φ大者。
Ⅲ:厚薄悬殊零件:圆盘类:a) φ≤100mm、δ≤5mm。
b) φ>100mm、δ≤10mm。
轴类:a) φ<50mm、δ≤10mm者。
Ⅰ:轴类键槽。
Ⅱ:板或圆盘上的不均匀圆孔。
(3(1)、35钢、45钢、渗碳件及有效厚度(直径)≤50mm的高碳钢、合金钢、铸铁等零件,烘干即可。
(2)、有效厚度(直径)>50mm的高碳钢、合金钢、铸铁等零件应在350~400℃空气炉预热,时间不小于1小时。
(3)、盐炉快速加热零件按(2)进行预热。
三、中温盐浴加热1、加热零件或工具不得直接接触到电极、护罩,吊起加热零件时吊钩与吊具要绝缘。
2、盐浴每星期至少捞渣一次,长轴类零件加热不准触及炉渣。
3、加热时间在60分钟以上的工具钢、盐浴在加热前必须进行脱氧。
3盐炉淬火操作工艺规程

盐炉淬火操作工艺规程3.盐炉淬火操作工艺规程盐炉淬火操作工艺规程淬火的目的:一、淬火(及回火)是使零件获得最终性能的关键工序,不同要求的零件,耐磨性、强度、硬度、经淬火后进行适当温度回火,获得所需要的性能,如:塑性、韧性及其他特殊物、化学性能。
淬火零件的工艺流程:二、→清洗→喷沙→检裂→防锈;(交检) ①一般零件:淬火→清洗→回火→清洗)(交检淬火(首件硬度交检)→清洗→回火②轴类及易变形零件:→校直→回火→清洗→喷沙→检裂→防锈。
淬火前的准备:三、按委热单核对零件数量、材质等,并检查零件有无碰伤、锐边、、1 裂纹、锈蚀等影响淬火质量的缺陷。
根据图纸及工艺文件,了解零件淬火的具体要求。
2、根据零件的形状,采用正确的绑扎吊挂或选择适当的工装夹具。
3、轴类主要件必须单件绑扎。
对易产生裂纹的部位,采用适当的防护措施,如用铁皮或石棉绳4、包扎及堵孔。
表面不允许氧化、脱碳,工作者应经常观察及控制炉内气氛。
对5、、(45共析钢或过共析钢零件应保证表面不得脱碳,对于中碳钢 )零件应保证表面不得进碳与脱碳。
40Cr等涂料防护:可选用下面涂料配方:(1);95% 、酒精(防氧化脱碳溶液)5% ①硼酸。
②可选用防渗碳剂涂于零件表面(局部表面选用) - 9 -盐炉淬火操作工艺规程(2)将零件装入盛有木炭的铁罐中,加盖密封。
6、主要件及大批量零件淬火,零件加热前应仔细检查设备、仪表及冷却剂等情况,确定一切正常后,才能启动开炉;首件试淬合格后,方可进行批量处理,并在生产过程中经常抽检。
四、装炉:1、零件材质不同,但有相同加热温度的零件,允许同一炉中加热;零件入炉前表面不允许有水份或其他污物;、 2- 10 -炉的时间。
对盐浴炉是指从零件装炉起至零件出炉的整个加热时间。
)(2- 11 -盐炉淬火操作工艺规程4、保温时间的确定:加热保温时间参照表7。
7. 加热保温时间参照表表(7)在保证硬度的前提下,尽量采用缓慢的冷却介质。
热处理工艺规范

热处理工艺规范一、淬火、回火工艺规范1.淬火、回火准备工作:1)检查设备,仪表是否正常;2)正确选择夹具;3)检查零件表面是否有碰伤、裂纹、锈斑等缺陷;4)确认零件要求的淬火部位硬度、变形等的技术要求,核对零件的形状、材料的加工状态是否与图样及工艺文件相符合;5)表面不允许氧化、脱碳的零件,当在空气炉加热时,应采取防氧化脱碳剂装箱保护或采用真空炉加热;6)易开裂的部位如尖角靠边的孔,应采取预防措施,如塞石棉、耐火泥等。
2.常见材料淬火、回火工艺规范1)加热温度表1 常用材料的常规淬火、回火规范钢号淬火温度℃冷却剂回火温度℃表面硬度HRC备注45 780~800水200~220 38~42 820~850 520~560 23~28 760~790 180~220 43~48Cr12MoV 1060~1070 风冷500~510 58~62真空淬火炉淬火风冷,回火两次。
510~520 56~60550~560 48~521020~1040 油200~220 58~62工件厚度超过60mm,而且淬油的,必须回火三次。
500~520 55~58520~530 54~56560~580 44~489CrWMn 820~840 油190~210 58~62 真空淬火炉Cr12Mo1V1 1020~1040 油500~520 50~56真空淬火炉200~220 58~621050~1080 风冷510~540 56~61真空淬火炉淬火风冷,回火两次;工件厚度超过60mm,而且淬油的,必须回火三次。
4Cr5MoSiV1 1000~1040 油200~220 48~524Cr13 1020~1050 油200~220 49~547Cr7Mo3V2Si 1110~1130 油560回火三次58~62 真空炉淬火、回火HS-1 960~980 空冷180~200 58~62 可火焰淬火注:Cr12Mo1V1 即 D2(美国)、1.2379(德国)、SLD(日立)、SKD11(日本)、K110(奥地利);9CrWMn 即 O1(美国)、1.2510(德国)、K460(奥地利);4Cr5MoSiV1 即 H13(美国)、1.2344(德国)、8407/8402(一胜百)、W302(奥地利);7Cr7Mo3V2Si 即 LD1;HS-1是高级火焰淬火,多用模具钢;除45号钢或特别说明均采用回火两次的工艺。
淬火工艺及要求

淬火工艺及要求淬火工艺是金属材料加工中非常重要的一环。
淬火的目的是通过快速冷却,使金属材料在保持一定硬度的同时,提高其耐磨性和强度,从而使其在使用中更加耐久。
淬火工艺需要严格按照要求进行,以确保材料的质量和性能。
淬火工艺的要求1. 淬火前需要对金属材料进行预处理,包括去除表面氧化层、油污等杂质,以确保淬火效果和材料品质。
2. 淬火过程需要严格控制温度和时间。
温度过高或时间过长会导致材料过度硬化或变脆,影响其性能。
3. 淬火过程需要使用合适的淬火介质。
淬火介质的选择应根据材料类型和要求的硬度来决定。
4. 淬火后需要对金属材料进行回火处理,以调整硬度和降低脆性,提高其可靠性和耐久性。
5. 淬火工艺需要进行严格的质量控制。
淬火后应进行金相组织检查、硬度测试、耐磨性测试等,以确保材料达到设计要求。
淬火工艺的步骤1. 预处理:对金属材料进行清洗、去除杂质,确保材料表面洁净。
2. 加热:将材料加热至淬火温度,保持一定时间,以使材料达到均匀的温度分布。
3. 淬火:将材料迅速浸入淬火介质中,使其迅速冷却。
淬火介质的选择应根据材料类型和要求的硬度来决定。
4. 清洗:将淬火后的材料进行清洗,去除淬火介质和氧化物等杂质。
5. 回火:将材料加热至回火温度,保持一定时间,以调整硬度和降低脆性。
6. 检验:对淬火后的材料进行金相组织检查、硬度测试、耐磨性测试等,以确保材料达到设计要求。
淬火工艺的注意事项1. 淬火前应对材料进行充分的热处理,以确保材料达到一定的硬度和强度,从而提高淬火效果。
2. 淬火介质的选择应根据材料类型和要求的硬度来决定。
不同淬火介质的冷却速度不同,会对材料性能产生不同的影响。
3. 淬火过程中应控制温度和时间,以避免过度硬化或变脆。
4. 淬火后应及时进行回火处理,以调整硬度和降低脆性,提高其可靠性和耐久性。
5. 淬火工艺需要进行严格的质量控制,包括金相组织检查、硬度测试、耐磨性测试等,以确保材料达到设计要求。
淬火工艺及要求

烈火锤打造刀刃——淬火工艺及要求
淬火是一种重要的热处理工艺,通过控制材料的加热、保温和冷
却过程,使材料获得特定的组织和性能,从而提高材料的硬度、强度
和耐磨性。
淬火工艺的要求包括以下几个方面:
一、温度控制:淬火的第一步是将材料加热到适当的温度。
一般
来说,淬火温度应该略低于材料的临界温度,以避免材料发生坍塌或
过度退火。
温度的控制必须非常准确,否则会影响淬火的效果。
二、保温时间:材料在达到淬火温度后需要保温一定时间,以保
证材料内部的温度均匀。
保温时间的长短与材料的尺寸和厚度有关,
一般来说要根据实际情况选择。
三、淬火介质:淬火介质是指将材料从高温迅速冷却的介质,通
常是水、油、盐水或空气。
选择合适的淬火介质可以使材料获得更好
的淬火效果和性能。
四、冷却速率:冷却速率是影响淬火效果和性能的一项关键因素。
冷却速率有多种方式,如改变淬火介质的温度和流量、改变材料的深度、宽度和厚度等。
不同的材料需要不同的冷却速率。
五、温度回火:淬火后的材料会出现应力和脆性,需要通过温度
回火的方式来消除。
温度回火的温度和时间需要根据材料的组织和性
能来确定。
总之,淬火工艺需要结合材料的特点和实际情况来进行。
只有掌握了淬火工艺,并且在实际生产中不断进行改进和提高,才能使材料获得更好的性能和效果。
盐炉淬火操作工艺规程

盐炉淬火操作工艺规程一、淬火的目的:淬火(及回火)是使零件获得最终性能的关键工序,不同要求的零件,经淬火后进行适当温度回火,获得所需要的性能,如:强度、硬度、耐磨性、塑性、韧性及其他专门物、化学性能。
二、淬火零件的工艺流程:①一样零件:淬火→清洗→回火(交检)→清洗→喷沙→检裂→防锈;②轴类及易变形零件:淬火(首件硬度交检)→清洗→回火(交检)→清洗→校直→回火→清洗→喷沙→检裂→防锈。
三、淬火前的预备:1、按委热单核对零件数量、材质等,并检查零件有无碰伤、锐边、裂纹、锈蚀等阻碍淬火质量的缺陷。
2、依照图纸及工艺文件,了解零件淬火的具体要求。
3、依照零件的形状,采纳正确的绑扎吊挂或选择适当的工装夹具。
轴类要紧件必须单件绑扎。
4、对易产生裂纹的部位,采纳适当的防护措施,如用铁皮或石棉绳包扎及堵孔。
5、表面不承诺氧化、脱碳,工作者应经常观看及操纵炉内气氛。
对共析钢或过共析钢零件应保证表面不得脱碳,关于中碳钢(45、40Cr等)零件应保证表面不得进碳与脱碳。
(1)涂料防护:可选用下面涂料配方:①硼酸5%、酒精95% (防氧化脱碳溶液);②可选用防渗碳剂涂于零件表面(局部表面选用)。
(2)将零件装入盛有木炭的铁罐中,加盖密封。
6、要紧件及大批量零件淬火,零件加热前应认真检查设备、外表及冷却剂等情形,确定一切正常后,才能启动开炉;首件试淬合格后,方可进行批量处理,并在生产过程中经常抽检。
四、装炉:1、零件材质不同,但有相同加热温度的零件,承诺同一炉中加热;2、零件入炉前表面不承诺有水份或其他污物;3、截面尺寸大小不同的零件同装一炉时,大小零件应用钩子分别钩挂,并分别运算保温时刻,进行处理;4、零件装炉时须小心轻放,幸免碰伤零件或损坏设备;5、细长零件应在长轴炉中垂直吊挂加热,以减少变形;6、长轴类细长零件,在炉内应平均吊挂排列,零件之间间隙应大于10mm。
五、加热:1、加热方式:一样可直截了当装入淬火温度的炉中加热,也可装入比规定淬火温度高20~30℃的炉中加热。
- 1、下载文档前请自行甄别文档内容的完整性,平台不提供额外的编辑、内容补充、找答案等附加服务。
- 2、"仅部分预览"的文档,不可在线预览部分如存在完整性等问题,可反馈申请退款(可完整预览的文档不适用该条件!)。
- 3、如文档侵犯您的权益,请联系客服反馈,我们会尽快为您处理(人工客服工作时间:9:00-18:30)。
XXX公司内部老资料
淬火工艺守则
1.主题内容与适用范围
本标准规定了我厂定型产品和外协产品的淬火遵守的基本规则和要求。
本标准不适用特殊材料,如不锈钢、磁钢、耐磨钢等的淬火。
2.淬火工艺参数。
2.1加热温度。
2.1.1碳素钢的加热温度:亚共析钢为Ac3+30~50℃,共析钢和过共析钢为Ac1+30~50℃。
合金钢的加热温度:一般应选为Ac
或Ac3+50~100℃。
1
表1常用钢加热温度
质等进行调整,但不允许超过上限20℃和下限10℃。
例如采用空气电阻炉加热时,即可选择高于正常加热温度的上限20℃;采用盐(或铅)浴炉加热时,可选择加热温度的中下限或低于下限10℃。
2.1.2用盐浴炉单件加热时的快速加热温度,低碳钢、中碳钢、低合金钢和中合金钢均为960~980℃。
2.1.3碳钢和一般合金钢的预热温度为350~500℃;高合金钢(高速钢)的第一次预热温度为550~650℃,第二次预热温度为800~850℃;对快速加热的零件,应在≤200℃条件下烘干;对调质后需表面快速加热的零件,其预热温度不应高于调质的回火温度。
2.2保温时间
保温时间是指零件装炉后,炉温回升到淬火温度算起到出炉为止所需的时间,它包括零件的透热和内部组织充分转变这两个过程。
2.2.1用盐浴炉加热时的保温时间:
碳素结构钢 t=0.2~0.4D(min)
碳素工具钢、合金结构钢t=0.3~0.5D(min)
合金工具钢t=0.5~0.7D(min)
一次预热的时间为2t。
t为保温时间分,D为工件的有效厚度。
2.2.2用空气电阻炉加热的保温时间:
碳素钢t=1~1.2D(min)
合金钢t=1.2~1.5D(min)
t为保温时间分,D为工件的有效厚度。
2.2.3批量生产时,根据装炉量和零件在炉内的排列情况,实际保温时间应为kt,以k为装炉系数,一般取1~2,应根据实际生产条件,经实验定出较合适的保温时间。
2.2.4对需要快速加热的零件,其保温时间为t=aD(s),式中a为加热系数,D为工件有效厚度。
表2所列a值为单件加热系数的参数值,具体值应根据实验确定。
表2加热系数a的值s/mm
2.3加热介质
我厂有不同加热介质的热处理炉,有空气电阻炉和盐浴加热炉两大类。
其中盐浴炉的优点(升温快、加热均匀等)多于空气电阻炉。
应根据零件的技术要求、形状的复杂程度及批量大小来选择不同的加热介质。
一般批量较小形状复杂及热处理要求较高(例如硬度范围要求窄,变形小及原材料脱碳倾向大)的零件应选用盐浴炉加热,其它应选用空气电阻炉加热。
2.4冷却介质
冷却介质选择得正确与否直接影响零件的淬火质量,常用的冷却介质有水、油和其它水溶液。
碳素钢的冷却介质应选水,合金钢的冷却介质应选油。
表3各种冷却介质及用途
3
3.1零件淬火前的要求
3.1.1原始组织应是正火或退火状态,不允许存在组织上或成份上的偏析和过热,例如带状组织、魏氏组织等。
3.1.2零件表面不允许有裂纹、金属分层、碰伤或刀痕、锈斑及油污,对于弹簧零件表面不允许有划伤。
3.1.3对于零件上形状复杂、断面尺寸变化比较大或有螺孔的部位应在淬火前采用保护措施,台阶处有圆弧,端面边缘应倒角,去飞边。
3.2对设备要求
3.2.1工艺前对工艺要求校核仪表。
3.2.2使用盐浴炉加热时,工作前应进行脱氧,对于中温盐浴(30%NaCl+70%BaCl2),其氧化物应控制在0.3%~0.5%之内,对于高温盐浴(100% BaCl2),其氧化物应控制在0.8~0.9%以内,其中BaO≤0.4%。
3.2.3使用箱式电阻炉加热时,为了防止零件氧化脱碳,应向炉内喷煤油或在料盘里铺木炭加以保护。
3.2.4使用气体渗碳炉加热时,如渗碳后一次加热淬火件应控制在15~20滴/分的速度向炉内滴煤油进行保护。
3.2.5应按有关工艺文件抽查淬火后零件的硬度,应大于或等于上限,调质件d≥50mm 时其硬度≥35HRC,d为30~50mm时,其硬度≥45HRC,d≤30mm,其硬度≥50HRC。
3.3操作方法
3.3.1对形状复杂、技术要求较高的零件,淬火时应选适当的工装来保证变形量最小,有些特殊的零件应设计专用工装。
3.3.2零件浸入冷却介质时要垂直平稳、迅速,棒状零件应垂直浸入或用滚动淬火法浸入,有凹槽的零件应使凹槽向上浸入冷却介质。
3.3.3对截面厚薄悬殊、形状复杂的零件,为防止开裂和减小变形,可将危险截面处预冷到Ar1以下温度淬火,预冷可用空冷、水冷、油冷等方法。
3.3.4对盘状零件应采用与轴向方向平行方式浸入冷却介质而后在回火进程中用夹具较正其变形。
3.3.5对易变形的零件及高速钢零件应采用分级冷却。
一般在150~200℃的硝盐槽停留1min/5~10mm然后空冷;对高速钢是在580~620℃中性盐浴中停留,然后空冷。
3.3.6对在硝盐槽中冷却的零件,不得在淬火加热介质中用黄血盐脱氧,以免爆炸伤人。
3.3.7零件淬火后应尽快回火,停留时间不允许超过4小时,重要形状复杂大件、锻模、合金工具钢、碳素钢、高速钢单件应及时回火,以免发生裂纹和变形。
整理编辑:李永刚2009-11-13。