自动焊接的不良原因及对策
焊接中出现的问题和解决方案
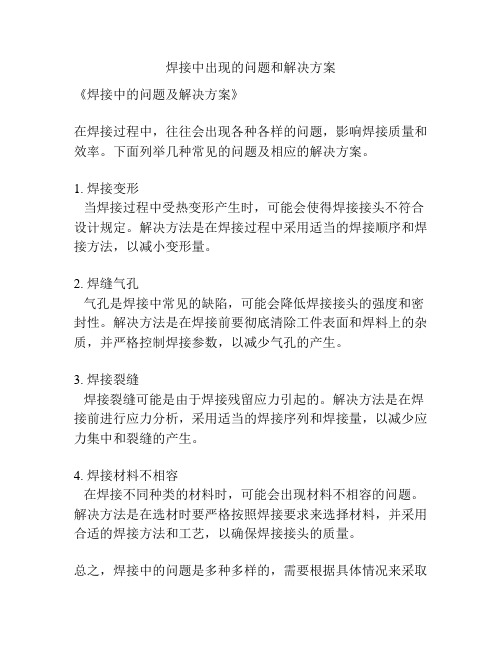
焊接中出现的问题和解决方案
《焊接中的问题及解决方案》
在焊接过程中,往往会出现各种各样的问题,影响焊接质量和效率。
下面列举几种常见的问题及相应的解决方案。
1. 焊接变形
当焊接过程中受热变形产生时,可能会使得焊接接头不符合设计规定。
解决方法是在焊接过程中采用适当的焊接顺序和焊接方法,以减小变形量。
2. 焊缝气孔
气孔是焊接中常见的缺陷,可能会降低焊接接头的强度和密封性。
解决方法是在焊接前要彻底清除工件表面和焊料上的杂质,并严格控制焊接参数,以减少气孔的产生。
3. 焊接裂缝
焊接裂缝可能是由于焊接残留应力引起的。
解决方法是在焊接前进行应力分析,采用适当的焊接序列和焊接量,以减少应力集中和裂缝的产生。
4. 焊接材料不相容
在焊接不同种类的材料时,可能会出现材料不相容的问题。
解决方法是在选材时要严格按照焊接要求来选择材料,并采用合适的焊接方法和工艺,以确保焊接接头的质量。
总之,焊接中的问题是多种多样的,需要根据具体情况来采取
相应的解决方法。
只有不断积累经验、改进技术,才能够提高焊接质量和效率。
焊接接头不良的原因

焊接接头不良的原因
焊接是一种常见的金属连接方式,但是在焊接过程中可能会出
现接头不良的情况。
接头不良会导致焊接件的质量下降,甚至可能
引发安全隐患。
接下来,我们将探讨一些导致焊接接头不良的原因。
首先,焊接过程中的不良操作可能是导致接头不良的主要原因
之一。
例如,焊接工艺参数设置不当、焊接速度过快或过慢、焊接
电流电压不稳定等都会影响焊接接头的质量。
此外,焊接操作人员
的技术水平和经验也会对焊接接头的质量产生重要影响。
其次,焊接材料的选择和准备也是影响接头质量的重要因素。
如果焊接材料的质量不达标,或者在焊接前没有进行适当的清洁和
处理,都可能导致接头不良。
此外,焊接材料的配比和焊接件的设
计也会对接头质量产生影响。
另外,环境因素也可能导致焊接接头不良。
例如,焊接过程中
的气氛控制不当、环境温度过高或过低、湿度过大等都会对焊接接
头的质量产生影响。
此外,焊接过程中可能产生的气泡、氧化物等
也会导致接头不良。
综上所述,焊接接头不良可能是由多种因素共同作用导致的。
为了确保焊接接头的质量,我们需要在焊接过程中严格控制焊接工艺参数,选用合格的焊接材料,保证焊接环境的良好,并加强对焊接操作人员的培训和管理。
只有这样,才能有效地避免焊接接头不良的发生,确保焊接件的质量和安全。
管道焊接缺陷及对策
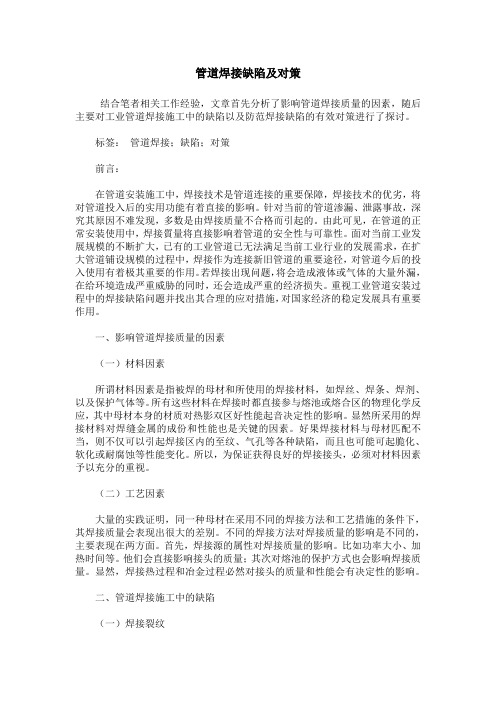
管道焊接缺陷及对策结合笔者相关工作经验,文章首先分析了影响管道焊接质量的因素,随后主要对工业管道焊接施工中的缺陷以及防范焊接缺陷的有效对策进行了探讨。
标签:管道焊接;缺陷;对策前言:在管道安装施工中,焊接技术是管道连接的重要保障,焊接技术的优劣,将对管道投入后的实用功能有着直接的影响。
针对当前的管道渗漏、泄露事故,深究其原因不难发现,多数是由焊接质量不合格而引起的。
由此可见,在管道的正常安装使用中,焊接質量将直接影响着管道的安全性与可靠性。
面对当前工业发展规模的不断扩大,已有的工业管道已无法满足当前工业行业的发展需求,在扩大管道铺设规模的过程中,焊接作为连接新旧管道的重要途径,对管道今后的投入使用有着极其重要的作用。
若焊接出现问题,将会造成液体或气体的大量外漏,在给环境造成严重威胁的同时,还会造成严重的经济损失。
重视工业管道安装过程中的焊接缺陷问题并找出其合理的应对措施,对国家经济的稳定发展具有重要作用。
一、影响管道焊接质量的因素(一)材料因素所谓材料因素是指被焊的母材和所使用的焊接材料,如焊丝、焊条、焊剂、以及保护气体等。
所有这些材料在焊接时都直接参与熔池或熔合区的物理化学反应,其中母材本身的材质对热影双区好性能起音决定性的影响。
显然所采用的焊接材料对焊缝金属的成份和性能也是关键的因素。
好果焊接材料与母材匹配不当,则不仅可以引起焊接区内的至纹、气孔等各种缺陷,而且也可能可起脆化、软化或耐腐蚀等性能变化。
所以,为保证获得良好的焊接接头,必须对材料因素予以充分的重视。
(二)工艺因素大量的实践证明,同一种母材在采用不同的焊接方法和工艺措施的条件下,其焊接质量会表现出很大的差别。
不同的焊接方法对焊接质量的影响是不同的,主要表现在两方面。
首先,焊接源的属性对焊接质量的影响。
比如功率大小、加热时间等。
他们会直接影响接头的质量;其次对熔池的保护方式也会影响焊接质量。
显然,焊接热过程和冶金过程必然对接头的质量和性能会有决定性的影响。
大河工业:超实用,自动焊锡机器人在焊接过程中出现的不良原因及解决对策

超实用,自动焊锡机器人在焊接过程中出现的不良原因及解决对策自动焊锡机器人在使用过程中,有时候会遇到一些焊接不良的问题,这些问题主要表现有吃锡不良、冷焊或点不光滑、焊点裂痕等,针对这些焊接不良问题。
除了调试本身外还有一些外在的因素,那么这些问题该如何解决呢?下面让深圳自动焊锡机器人厂家小编带我们来详细了解一下一,吃锡不良其现象为线路的表面有部份未沾到锡,原因为:1.表面附有油脂、杂质等,可以溶剂洗净。
2.基板制造过程时打磨粒子遗留在线路表面,此为印刷电路板制造厂家的问题。
3.硅油,一般脱模剂及润滑油中含有此种油类,很不容易被完全清洗干净。
所以在电子零件的制造过程中,应尽量避免化学品含有硅油者。
焊锡炉中所用的氧化防止油也须留意不是此类的油。
4.由于贮存时间、环境或制程不当,基板或零件的锡面氧化及铜面晦暗情形严重。
换用助焊剂通常无法解决此问题,重焊一次将有助于吃锡效果。
5.助焊剂使用条件调整不当,如发泡所需的空气压力及高度等。
比重亦是很重要的因素之一,因为线路表面助焊剂分布数量的多寡受比重所影响。
检查比重亦可排除因卷标贴错,贮存条件不良等原因而致误用不当助焊剂的可能性。
6.自动焊锡机器人焊锡时间或温度不够。
一般焊锡的操作温度较其溶点温度高55~80℃7.不适合之零件端子材料。
检查零件,使得端子清洁,浸沾良好。
8.预热温度不够。
可调整预热温度,使基板零件侧表面温度达到要求之温度约90℃~110℃。
9.焊锡中杂质成份太多,不符合要求。
可按时测量焊锡中之杂质,若不合规定超过标准,则更换合于标准之焊锡。
退锡多发生于镀锡铅基板,与吃锡不良的情形相似;但在欲焊接的锡路表面与锡波脱离时,大部份已沾在其上的焊锡又被拉回到锡炉中,所以情况较吃锡不良严重,重焊一次不一定能改善。
原因是基板制造工厂在渡锡铅前未将表面清洗干净。
此时可将不良之基板送回工厂重新处理。
二,冷焊或点不光滑此情况可被列为焊点不均匀的一种,发生于基板脱离锡波正在凝固时,零件受外力影响移动而形成的焊点。
cmt焊接缺陷及对策

网球的开题报告网球的开题报告一、引言网球作为一项受欢迎的体育运动,吸引了无数人的关注和参与。
它不仅是一项健身运动,还是一种竞技运动,具有独特的魅力和特点。
本开题报告将从网球的历史、规则、技术和影响等方面进行探讨,以期更好地了解和认识这项运动。
二、历史背景网球的起源可以追溯到古代的手球运动。
在14世纪的法国,人们开始使用球拍和网来进行类似于现代网球的游戏。
18世纪末,网球开始在英国流行起来,并逐渐发展成为一项正式的比赛项目。
1877年,第一届温布尔登网球公开赛举行,标志着网球正式成为一项国际比赛项目。
三、规则与比赛形式网球比赛通常分为单打和双打两种形式。
比赛场地为长方形的球场,中间有一道隔网将场地分成两半。
比赛中,选手通过发球、接发球、回击球等动作来争夺比赛的胜利。
比赛规则包括发球规则、计分规则、判罚规则等,确保比赛的公平性和规范性。
四、技术要点网球的技术包括正手击球、反手击球、发球、截击等。
正手击球是选手用球拍的正面击打球,反手击球则是用球拍的反面击打球。
发球是选手用手将球抛起并击打过网,以开始比赛。
截击是选手在对方回击球时,通过站位和预判来抢在对方击球之前将球拦截下来。
掌握这些技术要点,对于提高选手的竞技水平和比赛成绩至关重要。
五、网球的影响网球作为一项全民健身运动,对个人的身体健康和心理素质有积极的影响。
通过打网球,人们可以锻炼身体的协调性、灵活性和耐力,提高心肺功能。
同时,网球也是一项需要高度集中和反应能力的运动,可以培养人们的意志力和应变能力。
此外,网球还具有社交和团队合作的特点。
在双打比赛中,选手需要与搭档配合默契,共同制定战术和应对对手的攻势。
通过参与网球比赛,人们可以结识新朋友,拓展社交圈子,并培养团队合作意识。
六、结语通过本开题报告的探讨,我们对网球这项运动有了更深入的了解。
网球不仅是一项受欢迎的体育运动,更是一种具有独特魅力的竞技项目。
通过继续研究和实践,我们可以进一步提高自己在网球比赛中的技术水平和竞技能力,享受到网球带来的乐趣和收获。
违规电气焊动火作业存在的问题及建议
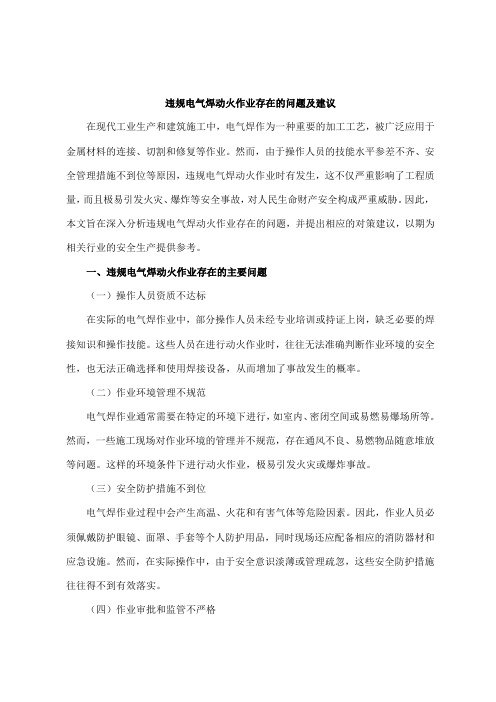
违规电气焊动火作业存在的问题及建议在现代工业生产和建筑施工中,电气焊作为一种重要的加工工艺,被广泛应用于金属材料的连接、切割和修复等作业。
然而,由于操作人员的技能水平参差不齐、安全管理措施不到位等原因,违规电气焊动火作业时有发生,这不仅严重影响了工程质量,而且极易引发火灾、爆炸等安全事故,对人民生命财产安全构成严重威胁。
因此,本文旨在深入分析违规电气焊动火作业存在的问题,并提出相应的对策建议,以期为相关行业的安全生产提供参考。
一、违规电气焊动火作业存在的主要问题(一)操作人员资质不达标在实际的电气焊作业中,部分操作人员未经专业培训或持证上岗,缺乏必要的焊接知识和操作技能。
这些人员在进行动火作业时,往往无法准确判断作业环境的安全性,也无法正确选择和使用焊接设备,从而增加了事故发生的概率。
(二)作业环境管理不规范电气焊作业通常需要在特定的环境下进行,如室内、密闭空间或易燃易爆场所等。
然而,一些施工现场对作业环境的管理并不规范,存在通风不良、易燃物品随意堆放等问题。
这样的环境条件下进行动火作业,极易引发火灾或爆炸事故。
(三)安全防护措施不到位电气焊作业过程中会产生高温、火花和有害气体等危险因素。
因此,作业人员必须佩戴防护眼镜、面罩、手套等个人防护用品,同时现场还应配备相应的消防器材和应急设施。
然而,在实际操作中,由于安全意识淡薄或管理疏忽,这些安全防护措施往往得不到有效落实。
(四)作业审批和监管不严格按照相关规定,电气焊动火作业前应进行严格的审批程序,并指定专人负责现场监管。
但在实际工作中,这一制度往往执行不力,审批流程形同虚设,监管人员也未能尽职尽责。
这导致了一些本应避免的事故得以发生。
二、违规电气焊动火作业的危害违规电气焊动火作业的危害是显而易见的。
首先,它直接威胁到作业人员的生命安全,一旦发生事故,往往会造成严重的人身伤害甚至死亡。
其次,事故还可能对周边的设备和设施造成破坏,给企业带来巨大的经济损失。
常见的焊接缺陷及处理办法
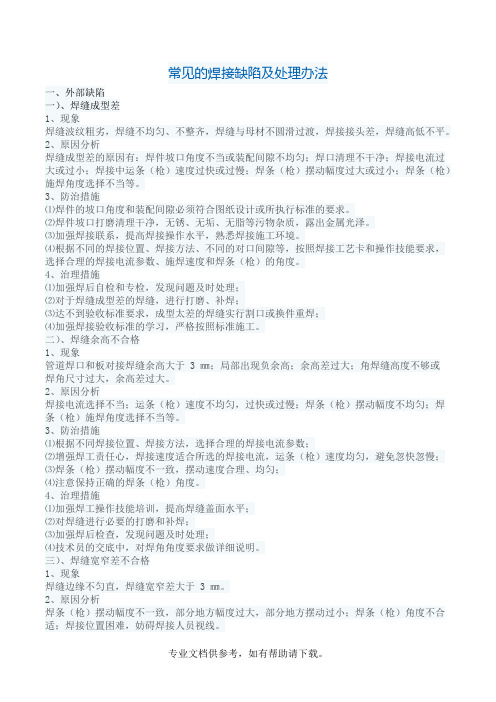
常见的焊接缺陷及处理办法一、外部缺陷一)、焊缝成型差1、现象焊缝波纹粗劣,焊缝不均匀、不整齐,焊缝与母材不圆滑过渡,焊接接头差,焊缝高低不平。
2、原因分析焊缝成型差的原因有:焊件坡口角度不当或装配间隙不均匀;焊口清理不干净;焊接电流过大或过小;焊接中运条(枪)速度过快或过慢;焊条(枪)摆动幅度过大或过小;焊条(枪)施焊角度选择不当等。
3、防治措施⑴焊件的坡口角度和装配间隙必须符合图纸设计或所执行标准的要求。
⑵焊件坡口打磨清理干净,无锈、无垢、无脂等污物杂质,露出金属光泽。
⑶加强焊接联系,提高焊接操作水平,熟悉焊接施工环境。
⑷根据不同的焊接位置、焊接方法、不同的对口间隙等,按照焊接工艺卡和操作技能要求,选择合理的焊接电流参数、施焊速度和焊条(枪)的角度。
4、治理措施⑴加强焊后自检和专检,发现问题及时处理;⑵对于焊缝成型差的焊缝,进行打磨、补焊;⑶达不到验收标准要求,成型太差的焊缝实行割口或换件重焊;⑷加强焊接验收标准的学习,严格按照标准施工。
二)、焊缝余高不合格1、现象管道焊口和板对接焊缝余高大于 3 ㎜;局部出现负余高;余高差过大;角焊缝高度不够或焊角尺寸过大,余高差过大。
2、原因分析焊接电流选择不当;运条(枪)速度不均匀,过快或过慢;焊条(枪)摆动幅度不均匀;焊条(枪)施焊角度选择不当等。
3、防治措施⑴根据不同焊接位置、焊接方法,选择合理的焊接电流参数;⑵增强焊工责任心,焊接速度适合所选的焊接电流,运条(枪)速度均匀,避免忽快忽慢;⑶焊条(枪)摆动幅度不一致,摆动速度合理、均匀;⑷注意保持正确的焊条(枪)角度。
4、治理措施⑴加强焊工操作技能培训,提高焊缝盖面水平;⑵对焊缝进行必要的打磨和补焊;⑶加强焊后检查,发现问题及时处理;⑷技术员的交底中,对焊角角度要求做详细说明。
三)、焊缝宽窄差不合格1、现象焊缝边缘不匀直,焊缝宽窄差大于 3 ㎜。
2、原因分析焊条(枪)摆动幅度不一致,部分地方幅度过大,部分地方摆动过小;焊条(枪)角度不合适;焊接位置困难,妨碍焊接人员视线。
电气焊管理制度和电气焊事故原因分析及对相关管控对策

电气焊作业管理制度为规范电气焊作业,确保安全生产,特制定本制度。
1、一般规定:1.1电焊工必须经焊接或气割培训,考试合格取得合格证后,方可进行电气焊作业。
1.2电焊工按规定穿戴劳动保护用品,并严格执行操作规程。
1.3现场必须配备齐消防器材。
严禁在瓦斯含量超过0.5%或煤尘浓度大于10mg/m³的场所进行焊接作业。
1.4作业现场必须通风良好,无易燃、易爆物品。
各类气瓶与明火的距离必须在10m以上。
氧气瓶与乙炔瓶必须在5m以上。
禁止作业现场吸烟。
1.5 严禁在带压容器及管路上进行焊接和气割,确需补焊时必须释放压力,打开与大气相通的排气口或观察孔盖,方可烧焊。
在带压容器和储放易燃易爆物品容器上焊割时,要制定专门的的安全技术措施,经审批后,方可按措施烧焊。
1.6对存放过易燃易爆、有毒物品和情况不明的容器进行焊接时,应当采取彻底清洗或置换惰性气体等防爆措施,并经检查合格后才能操作。
1.7严禁在带电设备以及正在运转的机械上进行焊接、气割。
1.8对于彩钢板封闭的皮带走廊,烧焊时,烧焊负责人要详细的检查彩钢板的结合部位是否有缝隙,如有要用不燃物堵上,烧焊过程中,安全负责人要做好安全监控,防止火星掉入彩钢板的接缝中引起火灾。
1.9因工作需要进入设备内部或容器内部工作时,焊工要穿干燥工作服和绝缘鞋,并设专人监护。
禁止行灯变压器带入设备内和容器内,禁止照明电压超过12V,禁止将漏气的焊炬、割炬携带到设备内和容器内,以防混合气体遇明火爆炸。
1.10电焊设备及工具,必须绝缘良好。
焊机外壳必须接地,必须双线作业。
1.11遇4级以上大风和雨雪天气,禁止从事户外露天作业。
在潮湿的地方作业,应当穿绝缘鞋并站在绝缘垫上。
1.12工作完毕或暂停时,施焊作业人员必须切断电源、气源、详细检查现场,确认无起火危险后,方可离开作业现场。
2、现场电焊机及固定把线的使用:2.1 电焊机应安装在通风良好、干燥、煤尘较小的地点。
2.2 电焊机现场电源要有专用开关,长时间停用时,电源开关必须断电。
点焊机虚焊、掉焊原因[修改版]
![点焊机虚焊、掉焊原因[修改版]](https://img.taocdn.com/s3/m/134a44d7482fb4daa48d4b00.png)
第一篇:点焊机虚焊、掉焊原因产生虚焊掉焊的原因及解决办法由于长期以来点焊出现虚焊、掉焊的问题,此类问题严重影响产品的安全性,属致命缺陷。
产生虚焊掉焊的问题分析:点焊机主要电源、机器设备、操作员工三个方面因素影响。
一、电源自2010年11月份已从原线上分线接换从主电线拉线接电源。
保证了电源电压的稳定。
二、1、机器设备点焊数调节。
一般按点焊工作的上下材料厚度按规定正常点焊参数:2、现车间工装夹具因年久磨损还有制作人不一,规格参差不齐,铜棒与主杆连接孔大小不一,配合不良或本身生锈未擦试干净,导电性能不好。
3、点焊机使用时间过长,维修过程中,一些配件可能与原机器组件不匹配。
造成放电不稳定。
4、现车间点焊机调的预压时间多为0.4-0.6秒,预压时间为上电极下行压紧工件时间;预压时间根据行程高度来设定,一般设定为0.6—1秒,如果预压时间不够容易产生火花,工件表面有毛刺不光滑影响工件质量,操作工在生产过程中不能随便调整参数。
三、1、操作员工自检频率不够。
2、操作员工图快随意调整点焊机参数。
3、由于点焊方式为电阻焊,刚开机点焊时,因点焊机处于常温状态,电阻稳定。
点了一会后点焊机各接触部位发热,导致电阻加大,此时应增大电流。
解决方案1.将组织装配车间技工调试好了再让员工上机点焊,并告知点焊机电阻因导体受热影响点焊质量的原理。
2.焊机的预压时间应调至6-10以上,严禁调至6以下,班组长每小时要求检查一次。
发现一次对操作员工50元一次的罚款。
3.作员工应以点焊20件为单位自检一次,车间班组长应每小时对点焊效果检查一次,看点焊工作有无掉焊现象,如有应立即停机调整。
4.员工学点焊时,老员工应教会其点焊相关技巧注意事项。
保证点焊质量。
5.将装配车间工装夹具清理并维修,尽可能标准化。
此项将列入本人今后工作重点,在四月份前完成工装夹具的检修,五月份完成不良模具的更新。
6.车间调模技工应该测试工装夹具是否配合良好,并将有锈的铜棒处理干净后再组装模具,保证导电性能。
焊接不良改进报告

焊接不良改进报告
焊接不良改善报告
⼀、鱼⾻图分析
⼀、综上鱼⾻图分析,产线焊接不良主要原因如下:
1.作业随意性⼤,⽆责任⼼和质量意识;作业不作⾃检。
2.对焊锡⼯艺⽆接受标准:
3.焊锡作业员未经培训就直接上岗,是否可以胜任本岗位⼯作也监督与考核;
4.焊接⼯序没有对所使⽤的电铬铁、焊接温度进⾏明确(⽬前所⽤的均为普通电铬铁;温度没法控制)
5.作业员没有及时清理铬铁上锡渣;焊接造成连锡。
⼆、改善对策:
1.⽣产管理⼈员对作业进⾏教育培训;提⾼员⼯责任⼼和质量意识;加强对员⼯的培训与监控,⽽不是有问题只是对员⼯说⼀声:“做好⼀点”,要让员⼯养成⾃检互检的习惯。
2.由研发部拟订焊接⼯艺接受标准;与图⽚的形成明⽰可接受、不可接受,并对作业员进⾏培训,让作业掌握标准;
3.研发部对⽣产线作业员进⾏焊锡作业培训;让员⼯熟练掌握焊锡技能;以后新招进的焊锡作业员上岗必须经过培训⽅可上岗;由品质部IPQC负责监控;
4.①⽬前所⽤的均为普通电铬铁;建议公司对⽣产所⽤的电铬铁统⼀更换成恒温铬铁;
②研发部制定作业指导书时需明确该⼯位所使⽤的电铬铁规格及温度控制要求;
③品质部申购铬铁温度测试仪,对焊锡⼯位铬铁温度进⾏管控;
5.①⽣产管理⼈员需对焊接作业进⾏培训和指导;让员⼯养成电铬铁有残留锡渣时须及时清理;并成焊接进⾏⾃检;
②IPQC加强对焊锡⼯位巡检⼒度;每个焊接⼯作需抽检5-10PCS检查焊接效果;
拟定:审核:。
SMT再流焊接中常见的焊接缺陷分析与预防对策

SMT再流焊接中常见的焊接缺陷分析与预防对策
一、焊接不良
1.焊接开关不全:焊接不良的主要原因是焊锡不足或焊盘上的元件安装不准确。
预防对策是加强操作者的培训,确保他们按照工艺要求进行焊接,定期维护和校准设备。
2.元件未焊接到位:元件未正确焊接到位会导致焊接不良,可能是由于焊盘上的焊膏不均匀或元件安装错误引起的。
预防对策是优化焊膏的设计和应用,确保焊膏均匀涂布并满足焊盘的要求。
二、控制问题
1.温度过高或过低:焊接过程中温度控制不当会导致焊接不良,可能是由于温度曲线不准确或设备故障引起的。
预防对策是在焊接过程中严格控制温度,确保温度曲线的准确性,并进行定期的设备维护和检修。
2.焊锡过量或不足:焊锡过量会导致元件无法正确安装,而焊锡不足则会导致焊盘无法完全湿润,影响焊接效果。
预防对策是优化焊锡的设计和应用,确保焊锡量的准确控制,以及监测焊锡的质量。
三、材料问题
1.焊膏问题:焊膏的质量问题可能导致焊接不良,比如焊膏中的活性助焊剂含量太高或太低,都会影响焊接的质量。
预防对策是选择合适的焊膏供应商,并进行严格的质量控制。
2.元件质量问题:元件的质量问题也可能导致焊接不良,比如焊盘上的元件与焊膏、焊盘不匹配,都会影响焊接的质量。
预防对策是选择合适的元件供应商,并进行严格的质量管控。
波峰焊常见焊接缺陷原因分析及预防对策
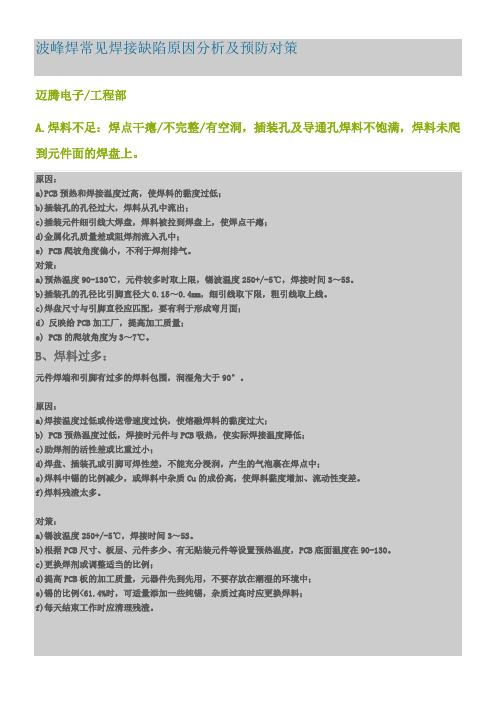
波峰焊常见焊接缺陷原因分析及预防对策迈腾电子/工程部A.焊料不足:焊点干瘪/不完整/有空洞,插装孔及导通孔焊料不饱满,焊料未爬到元件面的焊盘上。
原因:a)PCB预热和焊接温度过高,使焊料的黏度过低;b)插装孔的孔径过大,焊料从孔中流出;c)插装元件细引线大焊盘,焊料被拉到焊盘上,使焊点干瘪;d)金属化孔质量差或阻焊剂流入孔中;e) PCB爬坡角度偏小,不利于焊剂排气。
对策:a)预热温度90-130℃,元件较多时取上限,锡波温度250+/-5℃,焊接时间3~5S。
b)插装孔的孔径比引脚直径大0.15~0.4mm,细引线取下限,粗引线取上线。
c)焊盘尺寸与引脚直径应匹配,要有利于形成弯月面;d)反映给PCB加工厂,提高加工质量;e) PCB的爬坡角度为3~7℃。
B、焊料过多:元件焊端和引脚有过多的焊料包围,润湿角大于90°。
原因:a)焊接温度过低或传送带速度过快,使熔融焊料的黏度过大;b) PCB预热温度过低,焊接时元件与PCB吸热,使实际焊接温度降低;c)助焊剂的活性差或比重过小;d)焊盘、插装孔或引脚可焊性差,不能充分浸润,产生的气泡裹在焊点中;e)焊料中锡的比例减少,或焊料中杂质Cu的成份高,使焊料黏度增加、流动性变差。
f)焊料残渣太多。
对策:a)锡波温度250+/-5℃,焊接时间3~5S。
b)根据PCB尺寸、板层、元件多少、有无贴装元件等设置预热温度,PCB底面温度在90-130。
c)更换焊剂或调整适当的比例;d)提高PCB板的加工质量,元器件先到先用,不要存放在潮湿的环境中;e)锡的比例<61.4%时,可适量添加一些纯锡,杂质过高时应更换焊料;f)每天结束工作时应清理残渣。
C、焊点桥接或短路原因:a) PCB设计不合理,焊盘间距过窄;b)插装元件引脚不规则或插装歪斜,焊接前引脚之间已经接近或已经碰上;c) PCB预热温度过低,焊接时元件与PCB吸热,使实际焊接温度降低;d)焊接温度过低或传送带速度过快,使熔融焊料的黏度降低;e)阻焊剂活性差。
电路板焊接过程中出现的问题及解决方法
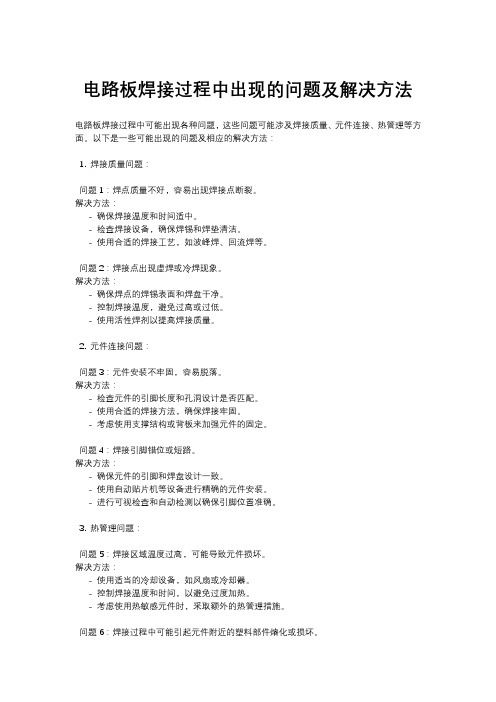
电路板焊接过程中出现的问题及解决方法电路板焊接过程中可能出现各种问题,这些问题可能涉及焊接质量、元件连接、热管理等方面。
以下是一些可能出现的问题及相应的解决方法:1. 焊接质量问题:问题1:焊点质量不好,容易出现焊接点断裂。
解决方法:- 确保焊接温度和时间适中。
- 检查焊接设备,确保焊锡和焊垫清洁。
- 使用合适的焊接工艺,如波峰焊、回流焊等。
问题2:焊接点出现虚焊或冷焊现象。
解决方法:- 确保焊点的焊锡表面和焊盘干净。
- 控制焊接温度,避免过高或过低。
- 使用活性焊剂以提高焊接质量。
2. 元件连接问题:问题3:元件安装不牢固,容易脱落。
解决方法:- 检查元件的引脚长度和孔洞设计是否匹配。
- 使用合适的焊接方法,确保焊接牢固。
- 考虑使用支撑结构或背板来加强元件的固定。
问题4:焊接引脚错位或短路。
解决方法:- 确保元件的引脚和焊盘设计一致。
- 使用自动贴片机等设备进行精确的元件安装。
- 进行可视检查和自动检测以确保引脚位置准确。
3. 热管理问题:问题5:焊接区域温度过高,可能导致元件损坏。
解决方法:- 使用适当的冷却设备,如风扇或冷却器。
- 控制焊接温度和时间,以避免过度加热。
- 考虑使用热敏感元件时,采取额外的热管理措施。
问题6:焊接过程中可能引起元件附近的塑料部件熔化或损坏。
解决方法:- 在焊接过程中采取屏蔽措施,防止焊接热量直接照射到塑料部件。
- 考虑使用高温耐受的塑料部件。
- 调整焊接设备的温度和焊接时间,以降低对周围塑料部件的影响。
以上解决方法只是一些常见问题的应对策略,具体问题的解决还需要根据具体情况进行综合分析。
在电路板焊接过程中,定期进行设备维护、工艺参数调整以及质量检测是确保焊接质量的重要手段。
电焊作业的危险性及预防措施
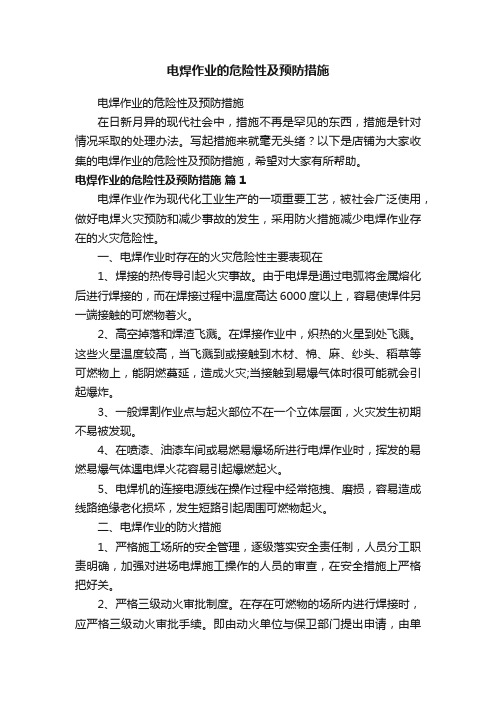
电焊作业的危险性及预防措施电焊作业的危险性及预防措施在日新月异的现代社会中,措施不再是罕见的东西,措施是针对情况采取的处理办法。
写起措施来就毫无头绪?以下是店铺为大家收集的电焊作业的危险性及预防措施,希望对大家有所帮助。
电焊作业的危险性及预防措施篇1电焊作业作为现代化工业生产的一项重要工艺,被社会广泛使用,做好电焊火灾预防和减少事故的发生,采用防火措施减少电焊作业存在的火灾危险性。
一、电焊作业时存在的火灾危险性主要表现在1、焊接的热传导引起火灾事故。
由于电焊是通过电弧将金属熔化后进行焊接的,而在焊接过程中温度高达6000度以上,容易使焊件另一端接触的可燃物着火。
2、高空掉落和焊渣飞溅。
在焊接作业中,炽热的火星到处飞溅。
这些火星温度较高,当飞溅到或接触到木材、棉、麻、纱头、稻草等可燃物上,能阴燃蔓延,造成火灾;当接触到易爆气体时很可能就会引起爆炸。
3、一般焊割作业点与起火部位不在一个立体层面,火灾发生初期不易被发现。
4、在喷漆、油漆车间或易燃易爆场所进行电焊作业时,挥发的易燃易爆气体遇电焊火花容易引起爆燃起火。
5、电焊机的连接电源线在操作过程中经常拖拽、磨损,容易造成线路绝缘老化损坏,发生短路引起周围可燃物起火。
二、电焊作业的防火措施1、严格施工场所的安全管理,逐级落实安全责任制,人员分工职责明确,加强对进场电焊施工操作的人员的审查,在安全措施上严格把好关。
2、严格三级动火审批制度。
在存在可燃物的场所内进行焊接时,应严格三级动火审批手续。
即由动火单位与保卫部门提出申请,由单位主管批准,经审批,做好充分准备后,才能在规定的时间、规定的地点内进行焊接。
3、电焊前做好各项准备工作,在有火灾、爆炸危险的场所内,一般不得进行焊接作业,需要检修的设备应拆卸移到安全地点修理。
在这些场所焊接时,应严格执行动火制度。
要求进行电焊作业的地点要与易燃易爆车间、仓库、油库、气柜、堆垛等保持足够的安全距离,并尽量远离正在生产易燃易爆的装置、设备和管道。
焊接工艺存在的问题及对策分析
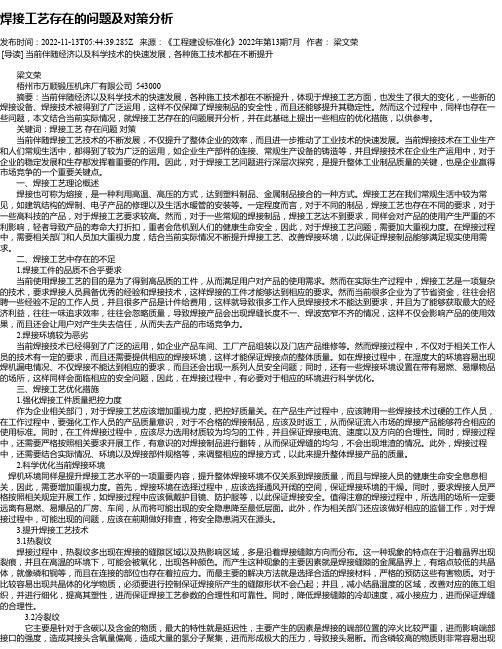
焊接工艺存在的问题及对策分析发布时间:2022-11-13T05:44:39.285Z 来源:《工程建设标准化》2022年第13期7月作者:梁文荣[导读] 当前伴随经济以及科学技术的快速发展,各种施工技术都在不断提升梁文荣梧州市万顺锻压机床厂有限公司 543000摘要:当前伴随经济以及科学技术的快速发展,各种施工技术都在不断提升,体现于焊接工艺方面,也发生了很大的变化,一些新的焊接设备、焊接技术被得到了广泛运用,这样不仅保障了焊接制品的安全性,而且还能够提升其稳定性。
然而这个过程中,同样也存在一些问题,本文结合当前实际情况,就焊接工艺存在的问题展开分析,并在此基础上提出一些相应的优化措施,以供参考。
关键词:焊接工艺存在问题对策当前伴随焊接工艺技术的不断发展,不仅提升了整体企业的效率,而且进一步推动了工业技术的快速发展。
当前焊接技术在工业生产和人们常规生活中,都得到了较为广泛的运用,如企业生产部件的连接、常规生产设备的铸造等,并且焊接技术在企业生产运用中,对于企业的稳定发展和生存都发挥着重要的作用。
因此,对于焊接工艺问题进行深层次探究,是提升整体工业制品质量的关键,也是企业赢得市场竞争的一个重要关键点。
一、焊接工艺理论概述焊接也可称为熔接,是一种利用高温、高压的方式,达到塑料制品、金属制品接合的一种方式。
焊接工艺在我们常规生活中较为常见,如建筑结构的焊制、电子产品的修理以及生活水暖管的安装等。
一定程度而言,对于不同的制品,焊接工艺也存在不同的要求,对于一些高科技的产品,对于焊接工艺要求较高。
然而,对于一些常规的焊接制品,焊接工艺达不到要求,同样会对产品的使用产生严重的不利影响,轻者导致产品的寿命大打折扣,重者会危机到人们的健康生命安全,因此,对于焊接工艺问题,需要加大重视力度。
在焊接过程中,需要相关部门和人员加大重视力度,结合当前实际情况不断提升焊接工艺、改善焊接环境,以此保证焊接制品能够满足现实使用需求。
焊接不良现象分析

焊接不良现象分析一、标准焊点的要求:1、可靠的电气连接2、足够的机械强度3、光洁整齐的外观电子元件标准焊点(1)不良术语短路:不在同一条线路的两个或以上的点相连并处于导通状态。
起皮:线路铜箔因过分受热或外力作用而脱离线路底板。
少锡:焊盘不完全,或焊点不呈波峰状饱满。
假焊:焊锡表面看是波峰状饱满,显光泽,但实质上并未与线路铜箔相熔化或未完全熔化在线路铜箔上。
脱焊:元件脚脱离焊点。
虚焊:焊锡在引线部与元件脱离。
角焊:因过分加热使助焊剂丢失多引起焊锡拉尖现象。
拉尖:因助焊剂丢失而使焊点不圆滑,显得无光泽。
元件脚长:元件脚露出板底的长度超过1.5-2.0mm。
盲点:元件脚未插出板面。
(2)不良现象形成原因,显现和改善措施1、加热时间问题(1)加热时间不足:会使焊料不能充分浸润焊件而形成松香夹渣而虚焊。
(2)加热时间过长(过量加热),除有可能造成元器件损坏以外,还有如下危害和外部特征。
A、焊点外观变差。
如果焊锡已经浸润焊件以后还继续进行过量的加热,将使助焊剂全部挥发完,造成熔态焊锡过热。
当烙铁离开时容易拉出锡尖,同时焊点表面发白,出现粗糙颗粒,失去光泽。
B、高温造成所加松香助焊剂的分解碳化。
松香一般在210度开始分解,不仅失去助焊剂的作用,而且造成焊点夹渣而形成缺陷。
如果在焊接中发现松香发黑,肯定是加热时间过长所致。
C、过量的受热会破坏印制板上铜箔的粘合层,导致铜箔焊盘的剥落。
因此,在适当的加热时间里,准确掌握加热火候是优质焊接的关键。
(3)不良焊点成因及隐患1、松香残留:形成助焊剂的薄膜。
隐患:造成电气上的接触不良。
原因分析:烙铁功率不足焊接时间短引线或端子不干净。
2、虚焊:表面粗糙,没有光泽。
隐患:减少了焊点的机械强度,降低产品寿命。
原因分析:焊锡固化前,用其他东西接触过焊点加热过度重复焊接次数过多3、裂焊::焊点松动,焊点有缝隙,牵引线时焊点随之活动。
隐患:造成电气上的接触不良。
原因分析:焊锡固化前,用其他东西接触过焊点加热过量或不足引线或端子不干净。
汽车焊接技术运用中的缺陷与预防探究
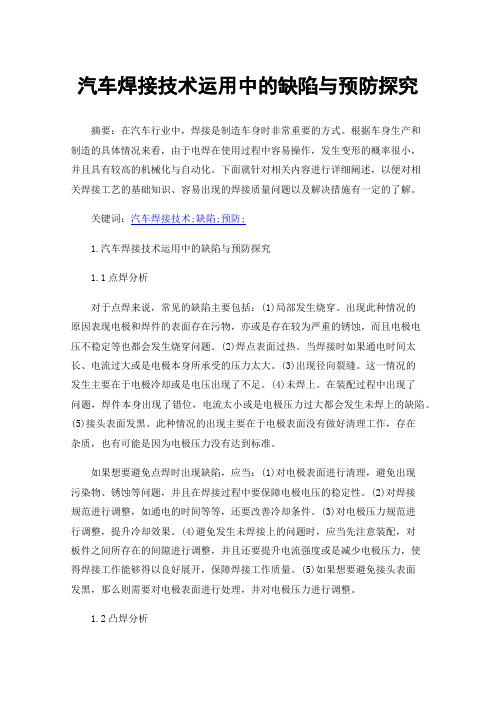
汽车焊接技术运用中的缺陷与预防探究摘要:在汽车行业中,焊接是制造车身时非常重要的方式。
根据车身生产和制造的具体情况来看,由于电焊在使用过程中容易操作,发生变形的概率很小,并且具有较高的机械化与自动化。
下面就针对相关内容进行详细阐述,以便对相关焊接工艺的基础知识、容易出现的焊接质量问题以及解决措施有一定的了解。
关键词:汽车焊接技术;缺陷;预防;1.汽车焊接技术运用中的缺陷与预防探究1.1点焊分析对于点焊来说,常见的缺陷主要包括:(1)局部发生烧穿。
出现此种情况的原因表现电极和焊件的表面存在污物,亦或是存在较为严重的锈蚀,而且电极电压不稳定等也都会发生烧穿问题。
(2)焊点表面过热。
当焊接时如果通电时间太长、电流过大或是电极本身所承受的压力太大。
(3)出现径向裂缝。
这一情况的发生主要在于电极冷却或是电压出现了不足。
(4)未焊上。
在装配过程中出现了问题,焊件本身出现了错位,电流太小或是电极压力过大都会发生未焊上的缺陷。
(5)接头表面发黑。
此种情况的出现主要在于电极表面没有做好清理工作,存在杂质,也有可能是因为电极压力没有达到标准。
如果想要避免点焊时出现缺陷,应当:(1)对电极表面进行清理,避免出现污染物、锈蚀等问题,并且在焊接过程中要保障电极电压的稳定性。
(2)对焊接规范进行调整,如通电的时间等等,还要改善冷却条件。
(3)对电极压力规范进行调整,提升冷却效果。
(4)避免发生未焊接上的问题时,应当先注意装配,对板件之间所存在的间隙进行调整,并且还要提升电流强度或是减少电极压力,使得焊接工作能够得以良好展开,保障焊接工作质量。
(5)如果想要避免接头表面发黑,那么则需要对电极表面进行处理,并对电极压力进行调整。
1.2凸焊分析(1)焊接电流当焊接电流变得过大时,其所产生的热量与焊接标准件熔化时需要的热量要远多,这在一定程度上将造成浪费,并且还会导致凸点部位因为受热而发生变形,焊点强度也会不断下降,其本身性能变得越来越差,从而对装配质量与焊接质量造成了严重影响。
- 1、下载文档前请自行甄别文档内容的完整性,平台不提供额外的编辑、内容补充、找答案等附加服务。
- 2、"仅部分预览"的文档,不可在线预览部分如存在完整性等问题,可反馈申请退款(可完整预览的文档不适用该条件!)。
- 3、如文档侵犯您的权益,请联系客服反馈,我们会尽快为您处理(人工客服工作时间:9:00-18:30)。
自動焊接的不良原因及對策第一節吃錫不良(POOR WETTING)其現象為線路的表面有部份未沾到錫,原因為:1.表面附有油脂、雜質等,可以溶劑洗淨2.基板制造過程時的打磨粒子遺留在線路表面,此為印刷電路板制造廠家的問題。
3.SILCON OIL,一般脫模劑及潤滑油中含有此種油類,很不容易被完全清洗干淨,所以在電子零件的制造過程中,應盡量避免化學品含SILICON OIL者。
焊錫爐中所用的氧化防止油也須留意不是此類的油。
4.由於貯存時間、環境或制造不當,基板或零件的錫面氧化及銅面晦暗情形嚴重。
換用助焊劑通常無法解決此問題,重焊一次將有助於吃錫效果。
5.助焊劑使用條件調整不當,如發泡所需的空氣壓力及高度等。
比重亦是很重要的因素之一,因為線路表面助焊劑分佈數量的多寡受比重所影響。
檢查比重亦可排除因標簽貼錯,貯存條件不良等原因而致誤用不當助焊劑的可能性。
6.焊錫時間或溫度不夠。
一般焊錫的操作溫度應較其溶點溫度高55~80℃。
7.不適合之零件端子材料,檢查零件,使得端子清潔,浸沾良好。
8.預熱溫度不夠,可調整預熱溫度,使基板零件側表面溫度達到要求之溫度約90℃~110℃。
9.焊錫中雜質成份太多,不符合要求,可按時測量焊旬錫中之雜質,若不合規定超過標准,則更換合標准之焊錫。
第二節NG退錫(DE-WETTI)多發生於鍍錫鉛基板,與吃錫不良的情形相似;但在於線路表面與錫波脫離時,大部份已沾附在其上的焊錫又拉回到錫爐中,所以情況較吃錫不良嚴重,重焊一次不一定能改善。
原因是基板制造工廠在鍍錫鉛前未將表面清洗干淨,此時可將不良之基板送回工廠重新處理。
第三節冷焊或焊點不光滑(CCLD SOLDER OR DISTURBED SOLDERING)此情況可被列為焊點不均勻的一種,發生於基板脫離錫波正在凝固時,零件受外力影響移動而形成的焊點。
保持基板在焊錫過後的傳送動作平穩,例如加強零件的固定,注意零件線腳方向等;總之,待焊錫的基板午到足夠的冷卻后再移動,可避免此一問題的發生,解決的辦法為再過一次錫波。
至於冷焊,錫溫太高或太低都有可能造成此情形。
第四節焊點裂痕(CRACK SOLDERING)造成的原因為基板,貫穿孔及焊點中零件腳等熱膨脹收縮系數方面配合不當,可以說實際上不算是焊錫的問題,而是牽涉到線路及零件設計時,材料及尺寸在熱方面的配合。
另基板裝配品的碰撞、重疊也是主因之一。
因此,基板裝配品皆不可碰撞、重疊、堆積;又,用切斷機剪切線腳更是主要殺手,對策是采用自動插件機或事先剪腳或購買不必再剪腳的的尺寸的零件。
第五節錫量過多(EXCESS SOLDER)過大的焊點對電流的流通並無幫助,但對焊點的強度則有不良影響,形成的原因為:1.基板與焊錫的接觸角度不當,改變角度(1∘~7∘),可使溶錫脫離線路滴下時有較大的拉力,而得到較薄的焊點。
2.焊錫溫度過低或焊錫時間太短,使溶錫在線路表面上未及完全滴下便已冷凝。
3.預熱溫度不夠,使助焊劑未完全發揮清潔線路表面的作用。
4.調高助焊劑的比重,亦將有助避免大焊點的產生;然而,亦須留意比重太高,焊錫過后基板上助焊劑殘余物過多,第六節錫尖(ICICLING)在線路上或零件腳端形成,是另一種形狀的焊錫過多。
再次焊接可將此尖消除,有時此情形亦與吃錫不良及不吃錫同時發生,原因如下:1.基板的可焊性差,此項推斷可以從線路接點邊緣吃錫不良及不吃錫來確認,在此情形下,再次過焊錫爐並不能解決問題,因為如前所述,線路表面的情況不佳,如此處理方法將無效。
2.基板上未插零件的大孔。
焊錫進入孔中,冷凝時孔中的焊錫因數量太多,被重力拉下而形成冰柱。
3.在手焊錫方面,烙鐵頭溫度不夠是主要原因,或是雖然溫度夠,但烙鐵頭上的焊錫太多,亦會有影響。
第七節焊錫沾附於基板基材上(SOLDER WEBBING)1.若有和助焊劑配方不相容的化學品質殘留在基板上,將會造成如此情況。
在焊錫時,這些材料因高溫變軟發黏,而沾住一些焊錫。
用強的溶劑如酮等清洗基板上的此類化學品,將有助於改善情況。
如果仍然發生焊錫附於基板上,則可能是基板在烘烤過程時處理不當。
2.基板制工廠在積層板烘烤干過程不當,在基板裝配前先放入烤箱中以80℃~100℃烘烤2~3小時,或可改善此問題。
3.焊錫中的雜質及氧化物與基板接觸亦將造成此現象,此為一設備維護之問題。
第八節白色殘留物(WHITE RESIDUE)焊錫或清洗過后,有時會發現基板上有白色殘留物,雖然並不影響表面電阻值,但因外觀的因素而仍不能接受,造成的原因為:1.基板本身已有殘留物,吸收了助焊劑,再經焊錫及清洗,就形成白色殘留物。
在焊前保持基板無殘留物是很重要的。
2.積層板的烘干不當,偶樂會發現某一基板,總是有白色殘留物問題,而使用下批基板時,問題又自動消失,因為此種原因而造成的白色殘留物一般可以溶劑清洗干淨。
3.銅面氧化防止劑之配方不相容,在銅面板上一定有銅面氧化防止劑,此為基板制造廠所涂抹。
以往銅面氧化防止都是松香為主要原料,但在焊錫過程卻有使用水溶性助焊劑者。
因此在裝配線上清洗后的基板就呈現白色的松香殘留物。
若在清洗過程加一鹹化劑便可解決此問題。
目前亦已有水溶性銅面氧化防止劑。
4.基板制造時積壓項制程控制不當,使基板變質。
5.使用過舊的助焊劑,吸收了空氣中水份,而在焊錫過程後形成白色殘留的水漬。
6.基板在使用松香焊劑時,焊錫過後時間停留太久才清洗,以致不易洗淨,盡量縮短焊錫與清洗之間的延遲時間,將可改善此現象。
7.清洗基板的溶劑中水份含量過多,吸收了溶劑中的IPA的成份局部積存,降低清洗能力,解決方法為適當的去除溶劑中水份,如使用水分離器吸收水份的材料於分離器中等。
第九節深色殘留物及浸蝕痕跡(DARK RESIDUE AND ETCH MARKS)在基板的線路及焊點表面,雙層板的上下兩面都有可能發現此情形,通常是因為助焊劑的使用及清除不當:1.使用松香助焊劑時,焊錫後未在短時間內清洗。
時間拖延過長才清洗,造成基板上殘留此類痕跡。
2.酸性助焊劑的遺留亦將造成焊點發暗及腐蝕痕跡。
解決方法為在焊錫後立即清洗,或在清洗過程加入中和劑。
3.因焊錫溫度過高而致焦黑的助焊殘留物,解決方法為查出助焊劑制造廠所建議的焊錫溫度。
使用可容許較高溫度的助焊劑可免除此情況的發生。
4.焊錫雜質含量不符合要求,需加純錫可更換焊錫。
第十節針孔及氣孔(PINHOLES AND BLOWHOLES)外表上,針孔及氣孔的不同在針孔的直徑較小,現於表面,可看到底部。
針孔及氣孔都代表著焊點中有氣泡,只是尚未擴大至表層,大部份都發生在基板底部,當底部的氣光完全擴散爆開前已冷凝時,即形成了針孔或氣孔。
形成原因如下:1.在基板或零件的線腳上沾有有機污染物。
此類污染材料來自自動插件機,零件成型機及貯存不良等因素。
用普通的溶劑即可輕易的去除此類污染物,但遇SILICON OIL及類似含有SILICON的產品則較困難。
如發現問題的造成是因為SILICON OIL,則必須考慮改變潤沒油或脫模劑的來源。
2.基板含有電鍍溶液和類似材料所產生之水氣,如果基板使用較廉價的材料,則有可能吸入此類水氣,焊錫時產生足夠的熱,將溶液氧化因而造成氣孔。
裝配前將基板在烤箱中烘烤,可以改善此問題。
3.基板儲存太多或包裝不當,吸收附近環境的水氣,故裝配前需先烘烤。
4.助焊劑槽中含有水份,需定期更換助焊劑。
5.發泡及空氣刀用壓縮空氣中含有過多的水份,需加裝濾水器,並定期排氣。
6.預熱溫度過低,無法蒸發水氣或溶劑,基板一旦進入錫爐,瞬間與高溫接觸,而產生爆裂,故需調高預熱溫度。
7.錫溫過高,遇有水份或溶劑,立刻爆裂,故需調低錫爐溫度。
第十一節短路(SHORT)1.焊墊設計不當,可由圓形焊墊改為橢圓形,加大點與點之間的距離。
2.零件方向設計不當,如SOIC的腳如與錫波平行,便易短路,修改零件方向,使其與錫波垂直。
3.自動插件彎腳所致,由於IPC規定線腳的長度在2mm以上。
4.基板孔太大,錫由孔中穿透至基板的上側而造成短路,故需縮小徑至不影響零件裝插的程度5.自動插件時,余留的零件腳太長,需限制在2mm以下。
6.錫爐溫度太低,錫無法迅速滴回錫槽,需調高錫爐溫度。
7.輸送帶速度太慢,錫無法快速滴回,需調快輸送帶速度。
8.板面的可焊性不佳,將板面清潔之。
9.基板中玻璃材料溢出,在焊接前檢查板面是否有玻璃物突出。
10.阻焊膜失效,檢查適當的阻焊膜型式和使用方式。
11.板面污染,將板面清潔之。
第十二節暗色及粒狀的接點(DULL GRAINY JOINT)1.多筆因於焊錫被污染及溶錫中混入的氧化物過多,形成焊點結構太脆。
須注意勿與使用含錫成份低的焊錫造成的暗色混淆。
2.焊錫本身成份產生變化,雜質含量過多,需加純錫或更換焊錫。
第十三節斑痕(MEASLING)玻璃織維積層起物理變化,如層與層之間發生分離現象。
但這種情形並非焊點不良。
降低預熱及焊錫溫度或者基板行進速度。
第十四節焊點呈金黃色(YELLOW SOLDER FILLETS)焊錫溫度過高所致,需調低錫爐溫度。