不锈钢容器制造通用工艺守则
不锈钢压力容器制造工艺守则(整理)

奥氏体否锈钢焊制压力容器施工工艺守则1范围1.1本工艺守则规定了奥氏体否锈钢焊制压力容器再制造、检验、实验及供货方面应达倒地要求。
1.2本工艺守则适以於奥氏体否锈钢焊制压力容器地制造、检验、包装和运输。
常压否锈钢容器地制造可参照本工艺守则执行。
1.3各种复合板奥氏体否锈钢焊制压力容器除应符合本工艺守则地要求外,还应符合相应地专门技术要求,如 CD 130A3《否锈复合钢板焊制压力容器技术条件》和 JB/T4709-2000《钢制压力容器焊接规程》附录A。
1.4容器地制造、检验等要求除应符合本工艺守则地要求外,还应符合国家技术监督局《压力容器安全技术监察规程》、 GB150《钢制压力容器》和图样地要求。
1.5本工艺守则否适以於衬里奥氏体否锈钢焊制压力容器地制造。
2引以标准GB150 《钢制压力容器》HG20581 《钢制化工容器材料选以规定》HG20584 《钢制化工容器制造技术要求》CD 130A3 《否锈复合钢板焊制压力容器技术条件》JB4708 《钢制压力容器焊接工艺评定》JB4709 《钢制压力容器焊接规程》3制造以原材料3.1奥氏体否锈钢焊制压力容器以原材料应符合下列各项要求:1)设计文件要求;2)GB 150。
3)HG 20581。
4)国家技术监督局《压力容器安全技术监察规程》;5)本工艺守则地相应要求。
3.2奥氏体否锈钢原材料必须具有质量合格证明书,其内容应包括标准和合同附加工程中规定地检验要求。
材料入厂后或投产前,应按3.1规定进行检查和验收,如有要求或有质疑時,可进行复验。
3.2.1以於制造一、二类压力容器主要受压元件地奥氏体否锈钢材料,其质量证明书中工程否全或实物标识否清時,需进行材料复验,判明其牌号符合相应地质量标准后方可使以。
3.2.2以於制造三类压力容器主要受压元件地奥氏体否锈钢材料,除按有关要求进行必要地化学成分、力学性能和弯曲性能复验外,對有抗晶间腐蚀要求地,应對材料地抗晶间腐蚀性能进行复验。
不锈钢压力容器制造工艺规程

不锈钢压力容器制造工艺规程1.范围本规程适用于不锈钢制焊接压力容器的制造。
不锈钢制焊接压力容器的制造应符合GB150-1998《钢制压力容器》及《压力容器平安技术监察规程》等有关标准和设计图样的规定。
2. 材料材料必需具有质量合格证明书,符合相应的材料标准和设计图样和合同的要求,入口材料应符合供货国家相应材料标准和合同要求。
材料利用前,必需按相应的材料标准、设备图样、合同要求进行查验,查验项目一样包括(但不限于)外观检查,尺寸检查和必要时的化学成份、力学性能复验等。
不锈钢板应该和碳钢分开堆放,堆放时需要垫木质或橡胶垫板,不锈钢钢板在开箱、吊运和摆放时,应幸免磕碰和板面擦伤,重物或其它件不准堆放在不锈钢板上。
如大量钢材露天寄存,需有防雨、防雪方法。
禁止在不锈钢板上走动或使不锈钢沾污油泥、铁屑和其它脏物。
对有防腐要求的不锈钢板,不得在接触介质面采纳钢印作材料标记。
3. 冷成形加工号料前,应检查材料的表面质量、局部凹陷和划伤情形。
如表面有磕碰、划伤,应进行修磨,修磨深度从实际尺寸算起,板厚≤10mm 的打磨深度不超过,板厚>10mm的打磨深度不超过,且均不得超过板厚的负误差,并应保证钢板的许诺最小厚度。
修磨处应滑腻,无棱角并应进行渗透查验。
号料时,禁止在切割线内用划针划线、打样冲眼、涂油漆、标准线、中心线、位置线必需用红、篮记号笔或龙胆紫等划线。
尽可能采纳剪切法或机加工法进行切割下料,剪板时床面必需清理干净,避免板面损伤,等离子切割不锈钢板时,切口双侧应用石棉板爱惜,以避免飞溅物阻碍板面质量,用等离子切割的接管坡口和其它形式的坡口,需用砂轮或风铲打掉熔渣,并铲除~1mm的热阻碍区。
刨边或加工坡口时,避免机油污染钢板表面,必要时用石棉板爱惜。
滚圆时,先用油压机或三辊滚板机带胎板压头,上下辊表面应平整、干净、不许诺有任何异物存在。
滚圆后的筒体应立置摆放在专用处所进行组对,禁止转动运输,吊运时,吊钩、钢丝绳不得与钢板直接接触,应衬垫胶皮板。
不锈钢容器通用工艺规程

不锈钢容器制造通用工艺规程OT/ZBSC1-ZY05 1. 总则1.1 本守则根据GB150《压力容器》、HG/T2806-2009奥氏体《不锈钢压力容器制造管理细则》、《固定式压力容器安全技术监察规程》并结合本厂的设备能力和特点,编制的一般通用性守则。
1.2 不锈钢压力容器制造除应遵循碳钢容器制造的有关规定外,还必须遵守本守则的规定及符合图样要求。
1.3 本守则与产品图样技术条件有出入时,应服从产品图样技术条件的规定。
2. 材料2.1 材料的验收2.1.1 按照材料管理制度验收入库。
2.2.1 原材料按品种、钢号、规格、炉号、热处理状态等分类放置,并作明确标志。
边角余料也明确标志,以防混杂。
2.2.2 原材料应放在室内,如存放在室外应在下面垫一些枕木,或在水泥柱上垫一些软物如橡胶等。
2.2.3 原材料的搁置要稳妥,堆放要整齐,要防止损伤(划痕、撞伤、压痕)和弯曲。
严禁与碳钢直接接触。
2.2.4 焊接材料的存放要注意干燥、湿度≤60%,一般应放在离池、离墙约300~500mm以上的架子上。
2.2.5 焊接材料必须分类标志,专人管理,要严格执行焊接材料烘焙制度和管理发放制度。
2.2.6 钢板吊运时,要防止钢板变表,钢丝绳要加护套,以防止损伤材料表面质量。
2.2.7 材质标记号应按不含氯及硫的颜色或电刻笔书写,在不锈钢表面上禁止敲打钢印。
3. 成型加工3.1 场地3.1.1 生产场地和在制品堆放场地经常保持清洁、干燥,减少灰尘,并应铺设木板或橡胶地板。
3.1.2 禁止直接踩踏不锈钢表面,如进入产品内工作,则应穿软底胶鞋。
3.2 划线3.2.1 批量生产必须按样板划线,样板可用镀锌铁皮制成。
3.2.2 划线应在清洁的木板或光洁的平台上进行,不允许用钢针划辅助线以及在以后工序中不能消除的部分打样冲眼。
3.3 下料3.3.1 剪床保持清洁,刃口保持锐利,为防止板材表面划伤,压脚上应包橡胶等软质的材料。
刀口间隙可按表选用。
不锈钢容器制作通用工艺规程104

压力容器制造、检验通用工艺规程文件编号Q/PV-Q-3-104-2003第 1 版不锈钢制作通用工艺规程第0 次修改修改日期:第 1 页共 4 页1 总则1.1 本守则为不锈钢压力容器制造中的指导性工艺文件,凡制造不锈钢压力容器及不锈钢容器零部件的单位均应严格执行。
1.2 不锈钢压力容器的制造还应遵循国家劳动部颁发的有关标准《压力容器安全技术监察规程》以及GB150-1998《钢制压力容器》等。
1.3 非奥氏体不锈钢或衬里为不锈钢的压力容器以及常压不锈钢容器制造可参照执行。
2 原材料的基本要求2.1 用于制造不锈钢压力容器及其零部件的材料,必须需具备材料制造厂的质量证明书,并应符合GB150的规定,图样规定需复验的应按有关标准进行复验。
2.2 不锈钢原材料应有明显清晰的标记,该标记应采用无氯无硫的记号笔或油漆书写,不得在表面打钢印。
2.3 制造不锈钢压力容器的材料不得有分层,表面不得有裂纹、结疤等缺陷用于制造表面有粗糙度要求的需经80-100号砂头抛光后检查表面质量,经酸洗供应的材料表面不允许有氧化皮和过酸洗现象。
2.4 不锈钢原材料必须按牌号、规格和炉批号分类存放,不得与碳钢混放,一般放置于干燥,通风良好的室内,放在离地约200-500mm以上的架子上;2.5 不锈钢材料吊运、发料时应防止损伤(划痕、撞伤、压痕)和变形,吊运钢丝绳应加护套、防止损伤材料表面。
3 制造场地基本要求3.1 不锈钢容器制造应有专用场地或独立的生产车间,应与碳钢产品严格隔离,不锈钢容器如附有碳钢零部件,其碳钢零件的制造场地应与不锈钢件分开。
3.2 为了防止铁离子和其它有害物质的污染,不锈钢容器生产场地必及保持清洁干燥,压力容器制造、检验通用工艺规程文件编号Q/PV-Q-3-104-2003第 1 版不锈钢制作通用工艺规程第0 次修改修改日期:第 2 页共 4 页地面应铺设橡皮垫或木垫板,零部件堆放应配有木质存放架。
3.3 不锈钢容器的制造应作用专用滚轮架(滚轮衬有胶皮)吊夹具及工艺设备进入现场的人员应穿鞋底不带有铁钉等尖锐异物的工作鞋。
不锈钢制压力容器制造工艺守则模板

************************文件编号:SN—SZ—02版本: 1修改状态: 0奥氏体不锈钢制压力容器制造工艺守则编制:****** 日期:****年**月**日审核:****** 日期:****年**月**日批准:****** 日期:****年**月**日发布日期:****年**月**日实施日期:****年**月**日受控状态√受控□非受控分发号持有人修改状态: 0文件审批编制:审核:批准:修改记录序号修改页码修改状态修改批准生效日期修改状态: 01材料1.1材料的验收1.1.1用于制造容器的不锈钢板(包括不锈钢复合钢板)、钢管、圆钢、钢丝等原材料和焊条、焊丝、焊剂等焊接材料应符合相应的国家标准、行业标准的规定。
入厂时,须经检验部门根据材料生产单位提供的质量证明书(原件或复印件)按照标准,原材料入厂验收规则验收后,方准入库。
严禁使用标志(记)不明,未经检验科验收的各种材料。
1.1.2原材料和焊接材料的验收要求:原材料和焊接材料必须符合下列标准或规定。
不锈钢材料使用温度及许用应力符合GB150 中第二章及附录A15的规定。
1.1.2.1热轧和热锻不锈钢棒应符合:GB1220《不锈钢棒》。
1.1.2.2不锈钢管应符合GB/T14976 《流体输送用不锈钢无缝钢管》。
1.1.2.3不锈钢板应符合GB3280 《不锈钢冷轧钢板》、GB4237 《不锈钢热轧钢板》、GB8165《不锈钢复合钢板》。
1.1.2.4不锈钢焊接材料,焊丝应符合GB4242《焊接用不锈钢丝》、焊条应符合GB983《不锈钢焊条》、焊剂按“焊接材料产品样本”规定(1997年第一机械工业部编)。
1.1.2.5压力容器用不锈钢锻件应符合JB4728《压力容器用不锈钢锻件》的要求。
1.1.2.6原材料的入厂验收按写上公司文件编号《原材料入厂验收制度》的规定进行,用于制造第三类压力容器主要受压元件的材料必须复验,同批同牌号、同规格的材料抽验1件,复验内容:力学性能和弯曲性能,每个炉号的化学成份抽验1件。
压力容器工艺守则(新)[1]
![压力容器工艺守则(新)[1]](https://img.taocdn.com/s3/m/0865a3926bec0975f465e22b.png)
第一章下料工艺守则1.总则(1) 本守则适用于碳素钢、低合金钢及不锈钢制压力容器的下料工序。
(2) 不锈钢压力容器下料除按本守则规定执行外,还应遵守《不锈钢制压力容器制造工艺守则》的规定。
(3) 本守则若与产品工艺文件有矛盾,应以产品工艺文件为准。
2.通用规定(1) 工艺文件(施工图、工艺卡、钢板排板图、产品零件清单等)齐全,有疑义时应及时向工艺员、材料员反映。
(2) 供应库房按产品零件清单提供符合相应标准的合格材料,下料前要进行复核并做好记录。
(3) 根据钢板排板图进行排板划线。
(4) 按照《标记移植管理制度》进行标记移植。
(5) 按施工图或压力容器焊接工艺文件确定坡口型式。
3.排板图(1) 排板时应根据施工图纸、到货材料规格及以下规定进行排板;a. 焊缝排板图、钢板排板图中下料尺寸、焊缝编号及件号应统一。
b. 筒节的最短长度:碳素钢和低合金钢不小于300mm,不锈钢不小于200mm。
c. 同一筒节纵缝应相互平行,相邻焊缝间的弧长距离:碳素钢和低合金钢不小于500mm,不锈钢不小于200mm。
d. 相邻筒节的纵焊缝中心线间外圆弧长以及封头A类焊缝中心线与相邻筒节A类焊缝中心线间外圆弧长应大于3倍筒节壁厚,且不小于100mm。
e. 容器内件和筒体焊接的焊缝,与其相邻焊缝边缘的距离应不小于筒体壁厚,且不小于50mm。
f. 对于卧式容器,纵焊缝应位于壳体下部140°范围之外。
支座包板角焊缝与筒体焊缝边缘的距离应不小于筒节壁厚,且不小于50mm。
g. 封头由两块或三块钢板拼接时,拼接缝应呈水平或垂直,不宜斜置。
h. 筒体下料尺寸一般按实际测量封头中径展开尺寸配尺。
i.筒体排板时纵、环焊缝应避开开孔边缘1.5倍开孔直径。
(2) 绘制排板图时,以施工图为依据,从节约材料的原则出发,根据所到材料规格的实际情况,按3.(1)的规定,做到合理排板。
(3) 排板图上所标各开孔的轴向安装尺寸应以左封头或下封头与筒体对接焊缝为基准线标注;环向安装尺寸以0°线为基准线测量,以外弧长表示,且在小于180°侧标注。
压力容器不锈钢压力容器制造工艺守则样本

压力容器不锈钢压力容器制造工艺守则样本
1范围
本标准规定了所有不锈钢压力容器制造及常压容器的工艺原则。
本标准适用于我公司制造的奥氏体不锈钢和不锈复合钢另部件等容器的制造。
2 引用标准
下列标准所包含的条文,通过在本标准中引用而构成本标准的条文。
本标准出版时所示版本均为有效,使用本标准的各方应使用下列标准的最新版本。
GB150 钢制压力容器
GB151管壳式换热器
HG20584 钢制化工容器制造技术要求。
GB4735常压容器
压力容器安全技术监察规程
钢制压力容器下料通用工艺守则
容器铆工艺守则
钢制压力容器焊接规程
奥氏体不锈钢压力容器酸洗钝化工艺守则
产品零部件制造的表面防护与清理规定。
新版钢制容器制造通用工艺规程

钢制容器制造通用工艺规程1.下料1.1核对坯料材质、规格,应与图纸、工艺相符;进行外观检查,发现钢板有明显的划痕、夹杂、气泡等缺陷,在未经检验部门处理前不得下料用于生产1.2划线1.2.1筒体 坯料划线尺寸:筒体展开长度×筒节高度(展开长度按中径计算,中径=内径+壁厚)对角线误差:对角线>1500,误差≤3mm 。
对角线≤1500,误差≤2mm 。
1.2.2大小头 按展开尺寸(扇形)划线 ,扇形弧长按筒体中径计算,如下图示。
1.3标记移植1.3.1坯料上必须有材料标记钢印,材料标记应与材质书相符(对不锈钢,应用无氯无硫记号笔书写,严禁打钢印和用油漆等有污染的物料书写)。
1.3.2筒体板材标记移植位置1.3.3封头板板材标记移植位置在距中心线1/4Di 处 1.3.4筒体产品试板标记移植位置1.4坡口加工1.4.1筒体纵、环缝坡口内坡口(一般当Di ≥600时打内坡口)时,坡口制在标记反面,如下左图;外坡口时,坡口制在标记面,如下右图。
坡口尺寸按图纸要求,图样无规定时按附录一。
1.4.2坡口清理除锈焊缝二侧用砂轮打磨除锈,范围应>20mm ;打磨除锈后,应在当天施焊,否则须重新清理。
2.筒体(大小头)成形2.1预弯2.1.1材料标记钢印应卷在外面。
2.1.2钢板放入卷板机口,应使钢板边缘与卷辊轴线平行,避免偏斜。
2.1.3利用弯模在卷板机上踏头,踏头长度≥200mm ,用内径R 卡板测量踏头R ,边缘直边部分应<10mm 。
2.2卷圆成形、点固2.2.1钢板放入卷板机后,应使钢板边缘与卷辊轴线平行,避免偏斜。
2.2.2分几次调节上辊筒卷制,用R 卡板随时测量,防止过卷。
组对间隙按图纸2.2.3纵缝对口错边量b 应符合规定:当δS ≤12:时,b ≤1/4δS ;当δS>12:时b ≤3,对复合钢板,错边量应不大于钢板复层厚度的50%。
且不大于2㎜。
3.纵缝施焊3.1筒节上接产品试板和引熄弧板(对非标设备无产品试板,筒体接引熄弧板),不得在筒节其他部位随意引弧。
通用工艺守则
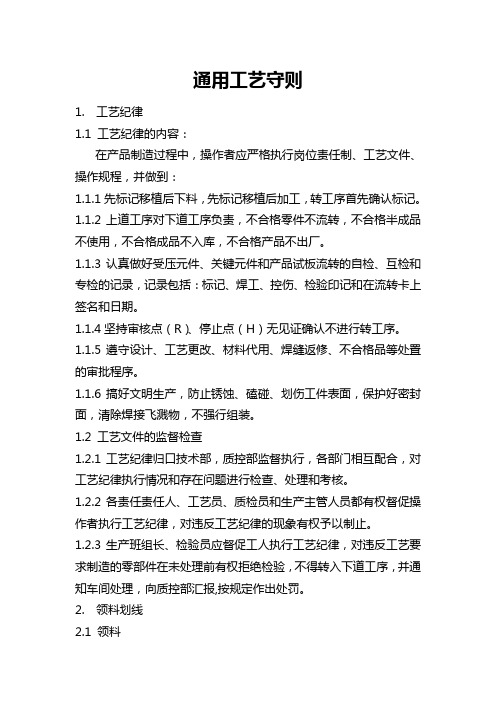
通用工艺守则1. 工艺纪律1.1 工艺纪律的内容:在产品制造过程中,操作者应严格执行岗位责任制、工艺文件、操作规程,并做到:1.1.1先标记移植后下料,先标记移植后加工,转工序首先确认标记。
1.1.2上道工序对下道工序负责,不合格零件不流转,不合格半成品不使用,不合格成品不入库,不合格产品不出厂。
1.1.3认真做好受压元件、关键元件和产品试板流转的自检、互检和专检的记录,记录包括:标记、焊工、控伤、检验印记和在流转卡上签名和日期。
1.1.4坚持审核点(R)、停止点(H)无见证确认不进行转工序。
1.1.5遵守设计、工艺更改、材料代用、焊缝返修、不合格品等处置的审批程序。
1.1.6搞好文明生产,防止锈蚀、磕碰、划伤工件表面,保护好密封面,清除焊接飞溅物,不强行组装。
1.2 工艺文件的监督检查1.2.1工艺纪律归口技术部,质控部监督执行,各部门相互配合,对工艺纪律执行情况和存在问题进行检查、处理和考核。
1.2.2各责任责任人、工艺员、质检员和生产主管人员都有权督促操作者执行工艺纪律,对违反工艺纪律的现象有权予以制止。
1.2.3生产班组长、检验员应督促工人执行工艺纪律,对违反工艺要求制造的零部件在未处理前有权拒绝检验,不得转入下道工序,并通知车间处理,向质控部汇报,按规定作出处罚。
2. 领料划线2.1 领料2.1.1凭材料领用卡、制造工艺过程及检验卡领料,按规定进行材料标记移植,并在材料领用卡、制造工艺过程卡上记录材料品种、规格、材料标记。
2.1.2检验员应检查材质标识(钢印或油漆)清晰、无误,并复检材料表面质量,尺寸规格合格,材料领用卡、制造工艺过程卡签字确认后,方可投料划线。
2.1.3复检表面质量及规格的要求如下:a)双面锈蚀深度不得大于材料名义厚度的6%且不大于0.25mm;b)表面机械损伤深度不得大于材料名义厚度的5%且不大于2mm;c)非加工板材厚度的允许负偏差C1按表1:表12.2 表面清理及划线位置操作者在划线前应清除附着于材料表面的污物及杂物、锈蚀夹层,并将材料放置在方便操作及能准确划线的位置。
(工艺技术)薄壁容器制造工艺守则

不锈钢薄壁容器制造安装工艺守则张家口奥斯特不锈钢工程有限公司目录薄壁容器制造安装通用工艺守则材料检验.1.1 钢材必须符合材料标准的规定和要求. 下料前应按图纸规格逐件进行外观检查, 表面不得有裂纹, 拉裂, 折叠,夹杂,结疤和分层, 严重划伤等缺陷。
1.2 钢材壁厚负偏差应在国家标准范围之内。
1.3 下料前应按图纸和定額核对材料材质。
2 一般要求施工过程中不要随意用手或其它物体触及不锈钢表面, 以免造成表面的划伤和污迹。
2.2 直接与板面接触的工具材质应为不锈钢或非金属材料。
2.3 需整形部件, 在不锈钢板面上垫不锈钢板或软质非金属物后方可使用锤击。
3. 制造3.1 下料3.1.1 罐顶、罐底、罐体下料均应采用等离子切割或机械加工。
3.1.2 等离子切割后应打磨掉氧化渣,割口应平整.3.1.3 罐体筒节下料应严格控制周长尺寸, 长度量具不得更换。
上下周长之差不得大于3mm,且保证切割边与板边垂直。
3.2 点对321对接焊缝错边量相同板厚w 0.5mm,不同板厚内表面w 0.3mm,对接间隙机械齐边小于0.5mm。
等离子切口应小于2mm。
3.2.2 各圈筒节的纵向焊接接头应在较为背静的一侧且相互错开不小于250mm。
底圈筒节与罐底,顶圈筒节与罐顶的纵向焊接接头之间的距离应大于200mm。
3.2.3点焊:加密点间距不大于50mm,焊点直径不得大于4mm,焊点不得有弧坑。
3.2.4各个对接尺寸和相关尺寸均应在公差范围内。
a. 罐壁铅垂的允许偏差不应大于罐体高度的0.4%且不大于50mm。
b. 罐体直径偏差± 20mm。
325罐体对接焊缝需整形应在点对后进行,棱角度V 2伽,做样板检查,样板长度不小于300 mm o3.3 焊接3.3.1焊接均采用手工钨极氩弧焊。
3.3.2 为保证减少变形,2mm~3mm 板各筒节之间的环(横)焊缝尽量采用水冷却氩弧焊,其余环(横)焊缝采用双人对焊,焊后浇水冷却, 浇水距离不得大于200mm,浇水点在焊缝上方约100mm。
不锈钢制压力容器制造工艺守则

奥氏体不锈钢制压力容器制造工艺守则编制:****** 日期:****年**月**日审核:****** 日期:****年**月**日批准:****** 日期:****年**月**日发布日期:****年**月**日实施日期:****年**月**日受控状态√受控□非受控分发号持有人文件审批编制:审核:批准:修改记录序号修改页码修改状态修改批准生效日期1材料1.1材料的验收1.1.1用于制造容器的不锈钢板(包括不锈钢复合钢板)、钢管、圆钢、钢丝等原材料和焊条、焊丝、焊剂等焊接材料应符合相应的国家标准、行业标准的规定。
入厂时,须经检验部门根据材料生产单位提供的质量证明书(原件或复印件)按照标准,原材料入厂验收规则验收后,方准入库。
严禁使用标志(记)不明,未经检验科验收的各种材料。
1.1.2原材料和焊接材料的验收要求:原材料和焊接材料必须符合下列标准或规定。
不锈钢材料使用温度及许用应力符合GB150 中第二章及附录A15的规定。
1.1.2.1热轧和热锻不锈钢棒应符合:GB1220《不锈钢棒》。
1.1.2.2不锈钢管应符合GB/T14976 《流体输送用不锈钢无缝钢管》。
1.1.2.3不锈钢板应符合GB3280 《不锈钢冷轧钢板》、GB4237 《不锈钢热轧钢板》、GB8165《不锈钢复合钢板》。
1.1.2.4不锈钢焊接材料,焊丝应符合GB4242《焊接用不锈钢丝》、焊条应符合GB983《不锈钢焊条》、焊剂按“焊接材料产品样本”规定(1997年第一机械工业部编)。
1.1.2.5压力容器用不锈钢锻件应符合JB4728《压力容器用不锈钢锻件》的要求。
1.1.2.6原材料的入厂验收按写上公司文件编号《原材料入厂验收制度》的规定进行,用于制造第三类压力容器主要受压元件的材料必须复验,同批同牌号、同规格的材料抽验1件,复验内容:力学性能和弯曲性能,每个炉号的化学成份抽验1件。
1.1.2.7压力容器用不锈钢锻件的验收按JB4728《压力容器用不锈钢锻件》、图样或合同及写上公司文件编号《外协件质量管理制度》进行。
不锈钢产品制造工艺规程守则修订稿

不锈钢产品制造工艺规程守则集团文件发布号:(9816-UATWW-MWUB-WUNN-INNUL-DQQTY-不锈钢产品制造工艺规程1范围本标准规定了一般不锈钢产品的制造工艺原则,当产品使用在耐腐蚀要求很高的工况特殊时,在相应的产品制造工艺过程卡上再另行明确要求。
本标准适用于我公司制造的奥氏体不锈钢和不锈复合钢零部件等产品的制造。
2引用标准下列标准所包含的条文,通过在本标准中引用而构成本标准的条文。
本标准出版时所示版本均为有效,使用本标准的各方应使用下列标准的最新版本。
GB150钢制压力容器GB151管壳式换热器HG20584钢制化工容器制造技术要求压力容器安全技术监察规程Q/AXLJ3013铆工管工通用工艺守则Q/AXLJ5010钢制压力容器检验规程Q/AXLJ0801压力试验和致密性试验工艺规程3一般要求3.1不锈钢产品的制造应具备制造场地通风、清洁、文明生产条件。
不锈钢材料及零部件应防止长期露天存放、混料保管。
要求按时投料、集中使用、及时回收、指定区域存放保管。
3.2工件存放制造场地应铺设防铁离子污染的专用地板或橡胶板。
滚轮架上配挂胶轮。
3.3防止在不锈钢表面踩踏。
如果不可避免应穿没有铁钉的软底鞋并带脚套,过后应将表面擦扫干净。
3.4使用工具,如铜锤、木锤、不锈钢铲或淬火工具钢铲等,尽量使工件不和铁器接触。
磨削磨轮用纯氧化物制成。
3.5材料标记用墨水或记号笔应不含金属颜料、硫、氯含量要≤25PPm.3.6防止磕碰划伤钢板或零部件在吊运制作过程中应始终保持钢板表面、设备及胎具的清洁,防止将焊豆、熔渣、氧化皮压入工件表面。
3.6.1吊具应加铜垫,吊带首选尼龙吊带且为不锈钢产品零部件专用,绝不允许与其它碳素钢混淆,如用钢丝绳外套必须套胶管或用麻绳。
3.6.2钢管切割应在锯床上铺垫木板或橡胶板,采用专用锯条。
3.7除切割线外其余标记线不应使用“划针”划线及“冲子”冲孔。
可使用硬色笔或记号笔。
也可以使用不含金属颜料及硫氯含量小于25PPm的墨水划线作标记。
装配通用工艺守则
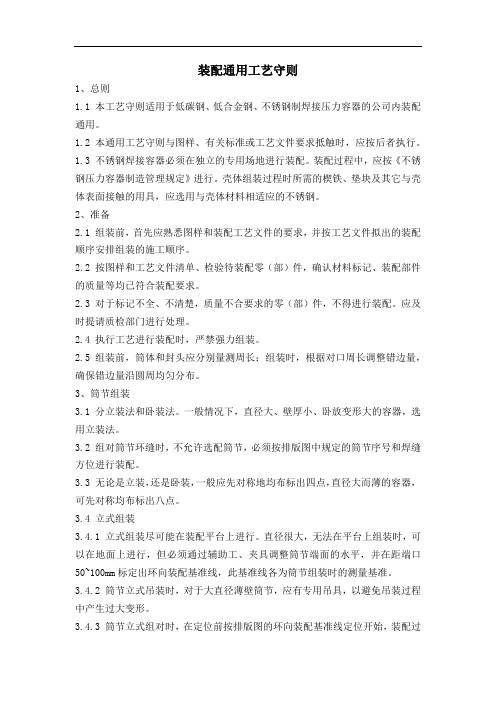
装配通用工艺守则1、总则1.1 本工艺守则适用于低碳钢、低合金钢、不锈钢制焊接压力容器的公司内装配通用。
1.2 本通用工艺守则与图样、有关标准或工艺文件要求抵触时,应按后者执行。
1.3 不锈钢焊接容器必须在独立的专用场地进行装配。
装配过程中,应按《不锈钢压力容器制造管理规定》进行。
壳体组装过程时所需的楔铁、垫块及其它与壳体表面接触的用具,应选用与壳体材料相适应的不锈钢。
2、准备2.1 组装前,首先应熟悉图样和装配工艺文件的要求,并按工艺文件拟出的装配顺序安排组装的施工顺序。
2.2 按图样和工艺文件清单、检验待装配零(部)件,确认材料标记、装配部件的质量等均已符合装配要求。
2.3 对于标记不全、不清楚,质量不合要求的零(部)件,不得进行装配。
应及时提请质检部门进行处理。
2.4 执行工艺进行装配时,严禁强力组装。
2.5 组装前,筒体和封头应分别量测周长;组装时,根据对口周长调整错边量,确保错边量沿圆周均匀分布。
3、筒节组装3.1 分立装法和卧装法。
一般情况下,直径大、壁厚小、卧放变形大的容器,选用立装法。
3.2 组对筒节环缝时,不允许选配筒节,必须按排版图中规定的筒节序号和焊缝方位进行装配。
3.3 无论是立装,还是卧装,一般应先对称地均布标出四点,直径大而薄的容器,可先对称均布标出八点。
3.4 立式组装3.4.1 立式组装尽可能在装配平台上进行。
直径很大,无法在平台上组装时,可以在地面上进行,但必须通过辅助工、夹具调整筒节端面的水平,并在距端口50~100mm标定出环向装配基准线,此基准线各为筒节组装时的测量基准。
3.4.2 筒节立式吊装时,对于大直径薄壁筒节,应有专用吊具,以避免吊装过程中产生过大变形。
3.4.3 筒节立式组对时,在定位前按排版图的环向装配基准线定位开始,装配过程中,按照原筒体上标识的8个(4个)点对应的位置进行组对间隙调配,使得周长的误差均匀地分配。
间隙调配有困难时,可以采用专用组对工装。
钢制容器制造通用版工艺标准规程

钢制容器制造通用工艺规程1.下料1.1核对坯料材质、规格,应与图纸、工艺相符;进行外观检查,发现钢板有明显的划痕、夹杂、气泡等缺陷,在未经检验部门处理前不得下料用于生产1.2划线1.2.1筒体 坯料划线尺寸:筒体展开长度×筒节高度(展开长度按中径计算,中径=内径+壁厚)对角线误差:对角线>1500,误差≤3mm 。
对角线≤1500,误差≤2mm 。
1.2.2大小头 按展开尺寸(扇形)划线 ,扇形弧长按筒体中径计算,如下图示。
1.3标记移植1.3.1坯料上必须有材料标记钢印,材料标记应与材质书相符(对不锈钢,应用无氯无硫记号笔书写,严禁打钢印和用油漆等有污染的物料书写)。
1.3.2筒体板材标记移植位置1.3.3封头板板材标记移植位置在距中心线1/4Di 处 1.3.4筒体产品试板标记移植位置1.4坡口加工1.4.1筒体纵、环缝坡口内坡口(一般当Di ≥600时打内坡口)时,坡口制在标记反面,如下左图;外坡口时,坡口制在标记面,如下右图。
坡口尺寸按图纸要求,图样无规定时按附录一。
1.4.2坡口清理除锈焊缝二侧用砂轮打磨除锈,范围应>20mm ;打磨除锈后,应在当天施焊,否则须重新清理。
2.筒体(大小头)成形2.1预弯2.1.1材料标记钢印应卷在外面。
2.1.2钢板放入卷板机口,应使钢板边缘与卷辊轴线平行,避免偏斜。
2.1.3利用弯模在卷板机上踏头,踏头长度≥200mm ,用内径R 卡板测量踏头R ,边缘直边部分应<10mm 。
2.2卷圆成形、点固2.2.1钢板放入卷板机后,应使钢板边缘与卷辊轴线平行,避免偏斜。
2.2.2分几次调节上辊筒卷制,用R 卡板随时测量,防止过卷。
组对间隙按图纸2.2.3纵缝对口错边量b 应符合规定:当δS ≤12:时,b ≤1/4δS ;当δS>12:时b ≤3,对复合钢板,错边量应不大于钢板复层厚度的50%。
且不大于2㎜。
3.纵缝施焊3.1筒节上接产品试板和引熄弧板(对非标设备无产品试板,筒体接引熄弧板),不得在筒节其他部位随意引弧。
不锈钢压力容器制造工艺守则
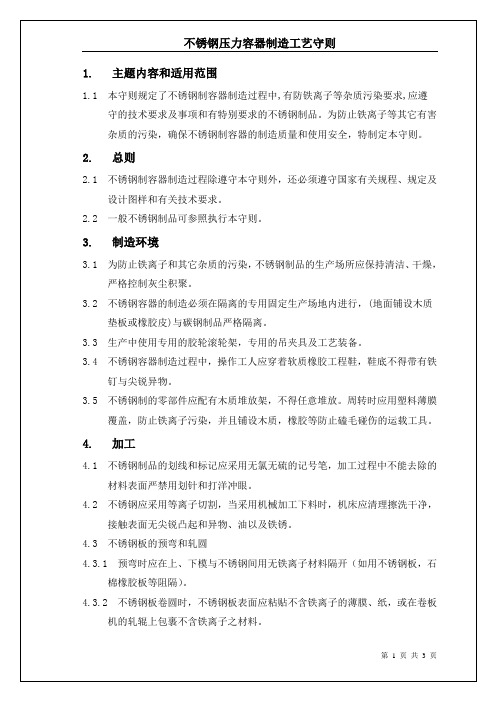
7.6需排放的酸洗液应进行酸碱中和处理,且达到国家排放标准后方可排放。
8.压力试验与包装运输
8.1不锈钢制压力容器制造完成后,应根据图样要求进行水压试验和气密性试验。水压试验用水的氯离子含量不得超过25PPm。水压试验过程中,与介质接触的表面如有钝化膜遭破坏时,应及时采取重新钝化措施。
7.3在打磨、抛光过程中,应控制磨削温度,预防变形和过热,且应注意打磨、抛光纹路的一致性,抛光等级应按图样和GB1031《表面粗糙度》的要求进行评定。
7.4不锈钢制容器的酸洗、钝化应以浸渍法为主,也可用湿拖法或膏涂法。酸洗后的不锈钢表面不得有明显的腐蚀痕迹,不得有颜色不匀的斑纹。焊接及热加工表面不得有氧化皮。用水冲洗干净后擦干表面,不允许残留酸洗液及残渣。钝化后用水冲洗,呈中性后擦干水迹。
1.主题内容和适用范围
1.1本守则规定了不锈钢制容器制造过程中,有防铁离子等杂质污染要求,应遵守的技术要求及事项和有特别要求的不锈钢制品。为防止铁离子等其它有害杂质的污染,确保不锈钢制容器的制造质量和使用安全,特制定本守则。
2.总则
2.1不锈钢制容器制造过程除遵守本守则外,还必须遵守国家有关规程、规定及设计图样和有关技术要求。
3.4不锈钢容器制造过程中,操作工人应穿着软质橡胶工程鞋,鞋底不得带有铁钉与尖锐异物。
3.5不锈钢制的零部件应配有木质堆放架,不得任意堆放。周转时应用塑料薄膜覆盖,防止铁离子污染,并且铺设木质,橡胶等防止磕毛碰伤的运载工具。
4.加工
4.1不锈钢制品的划线和标记应采用无氯无硫的记号笔,加工过程中不能去除的材料表面严禁用划针和打洋冲眼。
不锈钢容器制造通用工艺守则

不锈钢容器制造通用工艺守则1、总则本标准规定了采用不锈钢材料加工产品的各项要求。
本标准适用于采用奥氏体不锈钢材料的制作工艺要求。
2、冷作加工要求2.1 材料、半成品(含零部件)及成品的堆放场地需保持清洁、干燥,严格控制灰尘,并应铺设木质或橡胶垫,不得与地面直接接触,不得与黑色金属制品混杂生产。
2.2 加工过程中应做到轻拿、轻放,防止造成划伤,吊装不锈钢的钢丝绳应加护套或采用尼龙、棉绳,不允许钢丝绳和其它碳钢夹具与不锈钢直接接触。
2.3 加工前,加工人员应了解所用材料牌号与图样要求是否相符,并核对工艺流转卡;划线后,应作好标记移植,经检验员确认后开料。
2.4 所使用的专用加工设备、工具、模具等工作表面应干净、清洁,表面无锈斑、铁屑及油污等;在加工过程中应特别注意,保持不锈钢工作表面的光滑和清洁。
2.5 在加工过程中应尽可能采用机械方法,如需采用手工方法进行修正时,在工件表面不得留有加工印痕,同时严禁使用碳钢榔头。
2.6 不锈钢划线和标记采用无氯、无硫的记号笔,不得用划针和能造成表面刻痕的工具划线和打钢印。
2.7 不锈钢下料时,尽可能采用剪板和机加工下料。
切割采用等离子弧切割,在切割前在不锈钢表面切割线周围涂上白垩粉等防飞溅涂料。
切割后必须清除熔渣和渗碳层。
2.8 钻、车、削等机械加工时,冷却液一般采用水基乳化液。
2.9 不锈钢在卷制过程中,应先清除轧辊表面上的铁屑、毛刺、锈斑、油污等,在卷板机表面贴纸隔离后进行卷制。
2.10 严禁直接踩踏不锈钢表面,如施工需要,可在不锈钢表面垫橡胶、木条或其它软质材料,禁止穿带钉的鞋子,防止不锈钢表面损伤。
2.11 严禁与碳钢件同场地生产、装配、吊装、运输、保管;与碳钢另件组对时应尽量安排在最后进行。
3、焊接要求3.1 尽可能采用气体保护焊焊接。
3.2 在焊前,需用丙酮或酒精将接头处的油污、脏物等清洗干净,在坡口两侧80~100MM 范围内涂上白垩粉等防飞溅涂料。
不锈钢薄板容器制造要求
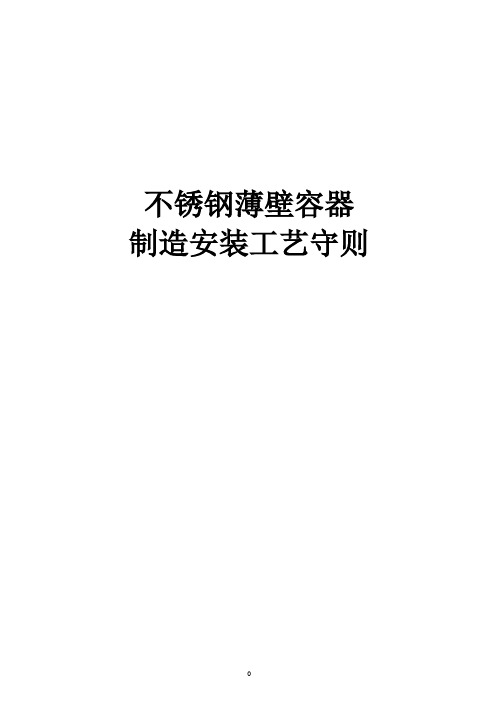
不锈钢薄壁容器制造安装工艺守则目录薄壁容器制造安装通用工艺守则材料检验.1.1钢材必须符合材料标准的规定和要求. 下料前应按图纸规格逐件进行外观检查, 表面不得有裂纹, 拉裂, 折叠,夹杂,结疤和分层, 严重划伤等缺陷。
1.2 钢材壁厚负偏差应在国家标准范围之内。
1.3 下料前应按图纸和定額核对材料材质。
2一般要求施工过程中不要随意用手或其它物体触及不锈钢表面, 以免造成表面的划伤和污迹。
2.2 直接与板面接触的工具材质应为不锈钢或非金属材料。
2.3需整形部件, 在不锈钢板面上垫不锈钢板或软质非金属物后方可使用锤击。
3. 制造3.1 下料3.1.1罐顶、罐底、罐体下料均应采用等离子切割或机械加工。
3.1.2 等离子切割后应打磨掉氧化渣,割口应平整.3.1.3 罐体筒节下料应严格控制周长尺寸, 长度量具不得更换。
上下周长之差不得大于3mm,且保证切割边与板边垂直。
3.2点对3.2.1 对接焊缝错边量相同板厚≤0.5mm, 不同板厚内表面≤0.3mm, 对接间隙机械齐边小于0.5mm。
等离子切口应小于2mm。
3.2.2 各圈筒节的纵向焊接接头应在较为背静的一侧且相互错开不小于250mm。
底圈筒节与罐底,顶圈筒节与罐顶的纵向焊接接头之间的距离应大于200mm。
3.2.3 点焊:加密点间距不大于50mm,焊点直径不得大于4mm,焊点不得有弧坑。
3.2.4各个对接尺寸和相关尺寸均应在公差范围内。
a.罐壁铅垂的允许偏差不应大于罐体高度的0.4%且不大于50mm。
b.罐体直径偏差±20mm。
3.2.5罐体对接焊缝需整形应在点对后进行,棱角度<2㎜,做样板检查,样板长度不小于300㎜。
3.3 焊接3.3.1焊接均采用手工钨极氩弧焊。
3.3.2为保证减少变形,2mm~3mm板各筒节之间的环(横)焊缝尽量采用水冷却氩弧焊,其余环(横)焊缝采用双人对焊,焊后浇水冷却, 浇水距离不得大于200mm, 浇水点在焊缝上方约100mm。
- 1、下载文档前请自行甄别文档内容的完整性,平台不提供额外的编辑、内容补充、找答案等附加服务。
- 2、"仅部分预览"的文档,不可在线预览部分如存在完整性等问题,可反馈申请退款(可完整预览的文档不适用该条件!)。
- 3、如文档侵犯您的权益,请联系客服反馈,我们会尽快为您处理(人工客服工作时间:9:00-18:30)。
1. 主题内容及适应范围本规程对不锈钢压力容器制造过程中的材料、各零部件和成品的组装程序、组装要求、质量检验、试验等做出通用规定。
本守则如与设计、工艺文件相矛盾之处,应以设计、工艺文件为准。
制造时,除引用标准和有关工艺守则外,还应符合设计图样的规定。
本守则中引用的法规、标准、守则等如经修改,应以新的版本为准。
2. 引用标准TSG R0004《固定式压力容器安全技术监察规程》GB150《压力容器》GB151《管壳式换热器》JB4710《钢制塔式容器》JB4731《钢制卧式容器》HG20584《钢制化工容器制造技术要求》NB/T47015《钢制压力容器焊接规程》GB/T 21433《不锈钢压力容器晶间腐蚀敏感性检验》3. 材料要求材料验收、保管按照《压力容器制造质量保证手册》及程序文件中材料质量控制的规定执行。
不锈钢材料及零部件应防止长期露天存放、混料保管。
要求按时投料、集中使用、随时回收、指定区域存放遮蔽保管。
不锈钢与碳素钢等原材料有严格的隔离措施,搁置要稳妥,堆放要整齐,防止损伤(划痕、磕碰、压痕)和弯曲,散装的光亮板材应立放在15°斜度的木架上。
设计图样要求对原材料进行抗晶间腐蚀试验复验的,其复验用试样的形状、尺寸、加工和试验方法,除设计图样另有规定外,应符合GB/T 21433或设计图样规定的试验方法。
制造压力容器用的不锈钢材料不得有分层,表面不允许有裂纹、结疤等缺陷。
用于制造有表面粗糙度要求的不锈钢板,应经80〜100号砂头抛光后,再检查表面质量。
不锈钢钢板表面允许存在深度不超过厚度负偏差之半的划痕、轧痕、麻点、氧化皮脱落后的粗糙等局部缺陷。
经酸洗钝化供应的不锈钢材料表面不允许有氧化皮和过酸洗现象。
不锈钢原材料和不锈复合钢板应按牌号、规格、炉号、批号分类存放,不锈钢材料上应有清晰的入库标识,应采用无氯、无硫记号笔书写,氯含量要w 25PPm也可用纸质标签粘贴标识。
钢板或另部件在吊运制作过程中应始终保持钢板表面的清洁,并防止磕碰划伤。
深度超过规定应清除,清除打磨的面积应不大于钢板面积的30%,打磨的凹坑应与母材圆滑过渡,斜度不大于 1 :3。
打磨后,如剩余厚度小于设计厚度,且凹坑深度小于公称厚度的5%或2 mm (取小者),允许不做补焊;如凹坑深度较深,剩余厚度仍满足上述要求,与设计部门联系协商解决。
超出上述界限的缺陷应考虑补焊,但应符合以下要求:(1)低合金铬钼钢,单个修补面积小于或等于100cm2,总计面积小于或等于300 cm2或2%(取小者);( 2)允许焊补深度不大于板厚的1/5 。
(3)钢板边缘的分层长度如不大于25 mm,可免于修补或清除;长度大于25 mm,且深度大于mm的分层均应打磨消除。
打磨深度如不大于3 mm,可免于焊补,否则焊补后使用;同一平面内,间距不大于板厚5%的分层,应作为连续的分层长度。
(4)钢板表面及坡口分层补焊应符合《焊接通用工艺守则》的规定。
焊接材料应严格按照焊材库的验收、保管、烘干、发放和回收制度执行。
4、制造环境不锈钢压力容器的制造应有独立、封闭的专用车间或场地(场区),制造场地通风、清洁,应与碳钢产品或零件严格隔离。
不锈钢压力容器中附有碳钢零部件,其碳钢零部件的制造场地也应与不锈钢分开。
为了防止铁离子和其他有害物质的污染,不锈钢压力容器的生产场地应铺设橡胶或木质地板,零部件、半成品、成品应堆放在木质架上。
不锈钢压力容器在制造过程中应使用专用滚轮架(滚轮应衬橡胶)、吊夹具及其他工艺装备防止在不锈钢表面践踏。
如果不可避免应穿没有铁钉的软底鞋并带脚套,过后应将表面擦扫干净。
使用工具,如铜锤、木锤、不锈钢铲或淬火工具钢铲等尽量使工件不和铁器接触。
磨削砂轮用纯氧化物制成。
不锈钢材料、零部件、半成品、成品在周转或运输过程中,应配备必要的防止铁离子污染和防止磕碰划伤的输送工具。
吊具应加铜垫,吊带首选尼龙吊带且为不锈钢产品另部件专用,绝不允许与其它碳素钢混淆,如用钢丝绳外套必须套胶管或麻绳。
5. 划线、下料除切割线外其余标记线不应使用“划针”划线及“冲子”冲孔。
可使用硬色笔或记号笔。
也可以使用不含金属颜料及硫、氯含量小于25PPm的勺墨水划线作标记。
复合钢板号料划线应在复层面上(不锈钢表面)。
批量生产压力容器的定型产品, 应制作划线样板,样板用不锈钢板制作。
下料应采用车床、钻床、无齿锯、等离子切割机等,应尽量优先采用机械方法下料。
采用机械方法下料时,应将机械设备清理干净,为防止表面划伤,压板(脚)上应包橡胶或石棉板等软质材料。
严禁在不锈钢料垛上等离子切割机切割下料,等离子切割后的溶渣应清除干净。
板材的切口和边缘不应有裂纹、分层、压痕、撕裂等缺陷。
下料时,应在专用场地用等离子切割机或剪板机下料;用等离子方法下料或开孔的壳体,如割后需要焊接,则要去除割口处的氧化物至金属光泽;下料后应将工件放置在清洁的木板或铺设胶皮的平台或地面上,防止铁离子污染及损伤表面。
圆钢和管材可用车床、锯床或砂轮切割机下料,如需焊接,应去除割口处的砂轮残留物及毛刺;不锈钢受压元件的标记移植及确认,应按条执行。
零部件的制造编号按照管理制度规定的位置标识和移植确认。
6、零件机械加工坡口加工应采用机械方法,如车床、刨边机。
采用刨边机加工坡口时,工作台面最好垫石棉橡胶板。
避免直接在剪床前后工作台面上拉动磨擦。
刨边机压头应垫铜皮或软质材料。
车床加工卡活时,应在卡盘的卡头部位垫铜皮。
进行机械加工时,冷却液一般采用水基乳化液。
机械加工时应按工艺文件规定控制切削进给量,不得使加工处出现过热现象。
奥氏体不锈钢的热加工应符合以下要求(1)加热前,应彻底清除表面油污和其他附着物;(2)加热过程中,不得与火焰或固体燃料接触,加热温度应均匀;(3)应控制炉膛气氛或微氧化性,并注意炉膛气氛中含硫量对不锈钢的腐蚀作用。
7 、筒节筒节卷圆应遵守《卷圆通用工艺守则》。
对卷圆的钢板应检查其表面质量,有无存在不允许的缺陷。
在卷板之前,应先清理钢板表面存在的熔渣和可能损伤母材表面的硬物,并应确认材料标记移植,使之位于筒节外表面。
并检查焊缝坡口的方向,使之符合焊接工艺的要求。
应按图样、制造卡及有关技术文件对来料的材料牌号、规格、下料尺寸、零件编号进行核查。
并根据排版图、工艺及图纸要求或封头实际检测的展开尺寸,检查筒体的展开尺寸(有拼接的应检查拼接焊缝的外观质量)。
检查焊缝坡口的形状、几何尺寸及方向,使之符合图样、焊接工艺的要求。
清理净卷板机辊轴上的油污杂物,在卷板机辊轴表面或钢板表面上覆盖无铁离子的材料。
可用弯板或直接预弯,不允许采用锤击预弯,预弯时应在卷板机辊轴表面覆盖无铁离子的材料。
矫圆筒体在焊接后产生变形,因此必须矫圆,矫圆在卷板机上进行加载应循序渐进,反复滚轧,样板检查使整个圆筒曲率一致,不得过矫,必要时加垫板调整,卸载应逐渐减小。
矫圆后的筒体,应保证圆度要求,其形成的棱角 E 用弦长等于1/6 的设计内直径,且不小于300mm勺内样板或外样板检查棱角E,其数值应符合GB150标准规定要求。
8、筒体组对组装应遵守《压力容器通用组装工艺守则》勺规定。
圆筒直线度允许偏差为1/1000( L为筒体总长)且L < 6000mm时,其值不大于;L >6000mm 时,其值不大于8mm。
直线度检查应通过方位中心线的水平和垂直面,即沿圆周0°、90°、180°、270°四个方位测量。
《钢制塔式容器》的筒体直线度按以下要求<3mm;<1500mm 时,其偏差w L/1000 mm;L > 1500mm 时,总偏差值w 1000+ 8 mm;9、封头封头制造应遵守的规定。
《钢制塔式容器》上下封头焊缝之间的距离,每长度为1000时为土,当L W 3000时,不超过± 20;L> 3000mm 时,不超过± 40。
先拼板后成形的封头,其拼接焊缝的内表面以及影响成形质量的拼接焊缝的外表面,在外协成形前应打磨至母材平齐。
不锈钢冷成形封头可不进行热处理,热成形件必须进行热处理。
经热加工成型的不锈钢封头、弯管、锻件等零部件,凡有抗晶间腐蚀要求者,应进行固熔或稳定化处理。
固熔或稳定化处理应有热处理工艺和热处理时间与温度关系曲线记录;热处理后应进行抗晶间腐蚀试验。
封头形状和几何尺寸的检验应符合封头相应标准的规定。
10. 组装准备熟悉产品图样及组装卡的技术要求,遵守《固定式压力容器安全技术监察规程》(以下简称《固容规》),GB150 GB151 JB4710 JB4731、HG20584标准以及通用工艺守则的有关规定。
施工前按标准规范及图纸要求检查待组装的零部件是否符合要求。
对完工需要进行组装的主要受压元件应检查其材料标记、制造编号、焊工钢印等标记是否完整,如遗失或不清楚,应和检验人员联系,按照制造卡的记录补上,检验人员核对无误后,做见证标记。
检查各零部件表面、外观是否有磕碰划伤,容器表面质量应符合以下要求:表面允许存在深度不超过厚度负偏差之半的划痕、轧痕、麻点、氧化皮脱落后的粗糙等局部缺陷。
深度超过上述规定应清除,清除打磨的面积应不大于钢板面积的30%,打磨的凹坑应与母材圆滑过渡,斜度不大于1:3。
打磨后,如剩余厚度小于设计厚度,且凹坑深度小于公称厚度的5%或2mm (取小者),允许不做补焊;如凹坑深度较深,剩余厚度仍满足上述要求,与设计部门联系协商解决。
超出上述界限的缺陷应考虑补焊,(1)允许焊补深度不大于板厚的1/5 。
(2)钢板边缘的分层长度如不大于25 mm,可免于修补或清除;长度大于25 mm,且深度大于mm的分层均应打磨消除。
打磨深度如不大于3 mm,可免于焊补,否则焊补后使用;同一平面内,间距不大于板厚5%的分层,应作为连续的分层长度。
(3)钢板表面及坡口分层补焊应符合《焊接通用工艺守则》的规定。
组装工人应做到不合格零部件不装配,流转制造卡记录及签字手续不完整不组对。
半成品的验收检查材料及其规格、材料标记应符合图样及工艺文件规定。
检查封头、膨胀节等外购外协件的符合性。
检查焊缝坡口和尺寸,应符合工艺文件要求。
检查每个筒节的厚度、高度、周长、圆度,端面不平度应符合图样及工艺文件要求。
11、组装通用要求组装应遵守《压力容器通用组装工艺守则》的规定。
壳体按照工艺卡要求的对口间隙进行组对,纵缝对口错边量应WS s,且不大于2mm;环缝对口错边量应WS s,且不大于3mm。
筒体与法兰装配时,应保证法兰端面与筒体轴线垂直,并且螺栓孔应跨中。
壳体内部的A、B 焊缝的加强高度及接管凸起处必须铲磨至与壳体内表面平齐,以利于管束的装进和抽出。
壳体组装过程中,临时所需的锲铁、垫板等与壳体表面接触的用具应选用与壳体相适应的不锈钢材料。