夹杂物与析出物的区别
浅析钢材的内部缺陷及其对热处理工艺和性能的影响
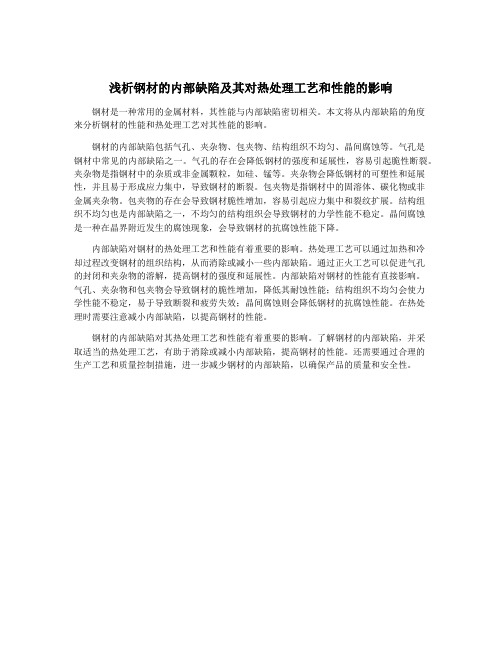
浅析钢材的内部缺陷及其对热处理工艺和性能的影响钢材是一种常用的金属材料,其性能与内部缺陷密切相关。
本文将从内部缺陷的角度来分析钢材的性能和热处理工艺对其性能的影响。
钢材的内部缺陷包括气孔、夹杂物、包夹物、结构组织不均匀、晶间腐蚀等。
气孔是钢材中常见的内部缺陷之一。
气孔的存在会降低钢材的强度和延展性,容易引起脆性断裂。
夹杂物是指钢材中的杂质或非金属颗粒,如硅、锰等。
夹杂物会降低钢材的可塑性和延展性,并且易于形成应力集中,导致钢材的断裂。
包夹物是指钢材中的固溶体、碳化物或非金属夹杂物。
包夹物的存在会导致钢材脆性增加,容易引起应力集中和裂纹扩展。
结构组织不均匀也是内部缺陷之一,不均匀的结构组织会导致钢材的力学性能不稳定。
晶间腐蚀是一种在晶界附近发生的腐蚀现象,会导致钢材的抗腐蚀性能下降。
内部缺陷对钢材的热处理工艺和性能有着重要的影响。
热处理工艺可以通过加热和冷却过程改变钢材的组织结构,从而消除或减小一些内部缺陷。
通过正火工艺可以促进气孔的封闭和夹杂物的溶解,提高钢材的强度和延展性。
内部缺陷对钢材的性能有直接影响。
气孔、夹杂物和包夹物会导致钢材的脆性增加,降低其耐蚀性能;结构组织不均匀会使力学性能不稳定,易于导致断裂和疲劳失效;晶间腐蚀则会降低钢材的抗腐蚀性能。
在热处理时需要注意减小内部缺陷,以提高钢材的性能。
钢材的内部缺陷对其热处理工艺和性能有着重要的影响。
了解钢材的内部缺陷,并采取适当的热处理工艺,有助于消除或减小内部缺陷,提高钢材的性能。
还需要通过合理的生产工艺和质量控制措施,进一步减少钢材的内部缺陷,以确保产品的质量和安全性。
非调质塑料模具钢中夹杂物和析出相的作用及行为

非调质塑料模具钢中夹杂物和析出相的作用及行为摘要:非调质塑料模具钢中夹杂物和析出相对钢的性能和加工性能具有重要影响。
本文对非调质塑料模具钢中夹杂物和析出相的种类、形态、数量和分布进行了详细分析,探讨了夹杂物和析出相对钢的力学性能、热处理性能和加工性能的影响机理,并提出了相应的改善措施。
关键词:非调质塑料模具钢;夹杂物;析出相;力学性能;热处理性能;加工性能一、引言非调质塑料模具钢是目前广泛应用于塑料模具制造领域的一种重要材料。
该种钢材具有高硬度、高强度、高耐磨性和高耐蚀性等优良性能,能够满足模具制造过程中的高强度、高硬度和高耐磨性的要求。
然而,在非调质塑料模具钢的生产和加工过程中,夹杂物和析出相的存在会对钢的性能和加工性能产生严重影响,降低钢的使用寿命和加工效率,甚至导致模具失效。
因此,深入了解非调质塑料模具钢中夹杂物和析出相的种类、形态、数量和分布,探究它们对钢的性能和加工性能的影响机理,具有重要的理论和实际意义。
二、非调质塑料模具钢中夹杂物的种类、形态、数量和分布夹杂物是指钢中的杂质,包括氧化物、硫化物、氮化物、碳化物等。
夹杂物对钢的性能和加工性能的影响主要体现在以下几个方面: 1、夹杂物会降低钢的强度和韧性,使钢变得脆性,易于产生裂纹和断裂。
2、夹杂物会影响钢的热处理性能,使钢的硬化能力降低,导致钢的硬度和强度降低。
3、夹杂物会影响钢的加工性能,使钢的切削性能和耐磨性降低,加工难度增大。
非调质塑料模具钢中的夹杂物种类较多,主要包括氧化物、硫化物、氮化物和碳化物等。
其中,氧化物的含量最高,占夹杂物总量的60%以上。
硫化物和氮化物的含量较少,占夹杂物总量的10%左右。
碳化物含量较少,通常在0.1%以下。
夹杂物的形态和数量也对钢的性能和加工性能产生影响。
夹杂物的形态可以分为球形、板状、纤维状和链状等。
球形和板状夹杂物对钢的性能和加工性能的影响比较小,而纤维状和链状夹杂物对钢的性能和加工性能的影响比较大。
焊缝中的夹杂物名词解释

焊缝中的夹杂物名词解释焊接作为一种常见的连接技术,广泛应用于工业生产和制造领域中。
在焊接过程中,焊接接头中往往会存在一些不理想的因素,其中之一就是夹杂物。
夹杂物是焊缝中的一种非金属或金属异物,它们可能对焊接接头的强度和性能产生不良影响。
因此,了解夹杂物的类型和特点,对于优化焊接接头的质量和性能具有重要意义。
一、夹杂物的定义夹杂物是指在焊缝中存在的各种杂质,包括金属夹杂物和非金属夹杂物。
金属夹杂物主要指金属颗粒、气泡和夹杂等形状的物质,而非金属夹杂物主要指矿渣、油污、灰尘等。
夹杂物可能是由于焊接材料、焊接工艺、操作不当或环境污染等因素引起的。
二、夹杂物的分类1. 金属夹杂物金属夹杂物包括金属颗粒、气泡和夹杂等。
金属颗粒是金属夹杂物中最常见的形式,它们可能来自焊材、母材或其他焊接材料。
气泡是由于焊接过程中存在气体溶解度和气泡脱出问题而形成的。
夹杂是指不溶于金属基体的残余物质。
2. 非金属夹杂物非金属夹杂物主要包括矿渣、油污、灰尘等。
矿渣是在焊接过程中产生的,由于焊芯和焊渣等材料的残留而形成。
油污则是指焊件表面或环境中存在的油脂或润滑剂等污染物。
灰尘是由于焊接作业环境不洁净所致。
三、夹杂物的形成原因夹杂物的形成原因多种多样,主要包括以下几个方面:1. 焊材质量问题:焊材中含有金属碎屑、气泡,或含有过多的夹杂物。
2. 焊接工艺问题:焊接工艺参数设置不当,如焊接温度、焊接速度等。
3. 操作不当:焊接操作过程中存在疏忽或操作不规范等问题。
4. 环境污染:焊接作业环境中存在油脂、灰尘等污染物。
四、夹杂物对焊接接头的影响夹杂物的存在对于焊接接头的质量和性能可能产生以下不良影响:1. 强度降低:夹杂物会破坏焊接接头的结晶结构,导致焊缝强度降低。
2. 腐蚀敏感性增加:夹杂物会使焊接接头的耐腐蚀性下降,易受到腐蚀介质的侵蚀。
3. 疲劳性能下降:夹杂物可能成为应力集中点,导致焊接接头在循环载荷下易于发生疲劳破坏。
4. 导电性能下降:夹杂物会影响焊接接头的导电性能,降低其电流传导能力。
夹杂物

钢中非金属夹杂物 (non-metallic inclusions in steel)钢中夹带的各种非金属物质颗粒的统称。
钢中含有氧、氮、硫等元素,它们在钢中的溶解度在高温下高,而在室温下溶解度很低,在钢冷却和凝固时析出并同铁和其它金属等结合成为各种化合物,称为非金属的夹杂物。
除此以外,炉渣、耐火材料、泥沙等外来物质也可能混入钢中形成非金属夹杂物。
早期文献曾把钢中非金属夹杂物称为“夹渣”,这个名称容易使人误解,以为非金属夹杂物就是混入钢中的炉渣。
现在通常把各种混入钢中的物质称为外来夹杂物,它们的形状不规则(图1、图2),而将由于内部物理和化学反应产生的夹杂物称为内生夹杂物,其典型特征是尺寸较小,数目多,分布均匀。
钢中生成夹杂物的过程大致如下:脱氧剂加入钢液中以后,脱氧元素和氧发生化学反应生成不溶于钢的氧化物;有的脱氧元素也能和硫、氮化合生成硫化物、氮化物。
这类化合物称为初生夹杂物。
除极少数颗粒细小的夹杂物外,大多数初生夹杂都能从钢液中浮升出来进入渣中。
而当钢液冷却和凝固时,由于溶解度下降和氧、硫等的偏析,在凝固过程中又产生氧化物和硫化物等,称为次生夹杂物。
次生夹杂难以从钢中排除而残留在树枝晶间或最后析出于晶粒界上。
图3为FeO夹杂,图4为FeS夹杂。
钢液脱氧后,继续接触到空气或其他氧化物如耐火材料等,使钢液重新吸收氧,即发生二次氧化。
二次氧化是成品钢中非金属夹杂物的重要来源。
钢中有非金属夹杂物存在,破坏了金属基体的连续性,使钢的品质变坏。
在特殊情况下,有的夹杂物有利于钢的某种性能(如切削性),但这只是在特殊的条件下。
一般说非金属夹杂物对钢的力学性能、物理性能和化学性能都有相当大的危害。
用通俗的话来说,含夹杂物多的钢是“脏”的,纯净的钢所含有的夹杂物很少。
然而纯净钢是一个相对的概念,钢的洁净与否和它的用途有关,也和夹杂物的形状、颗粒大小和可塑性等有关。
数量虽少但颗粒较大的夹杂物往往比数量较多但尺寸细小的夹杂物危害更大;形状不规则的比球形的夹杂物危害大。
非调质塑料模具钢中夹杂物和析出相的作用及行为
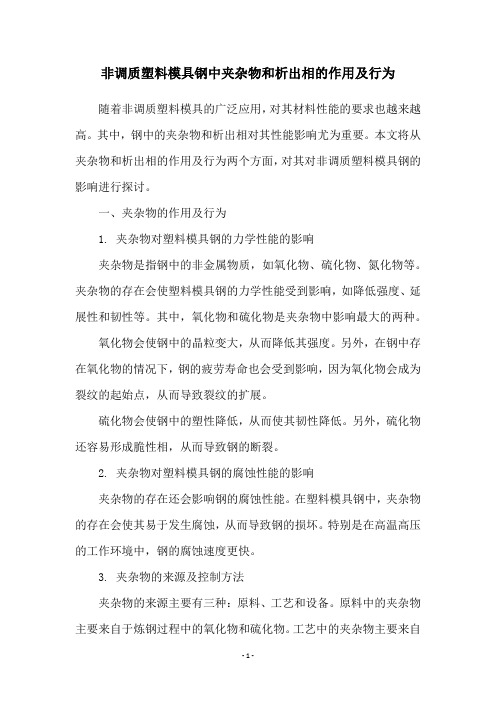
非调质塑料模具钢中夹杂物和析出相的作用及行为随着非调质塑料模具的广泛应用,对其材料性能的要求也越来越高。
其中,钢中的夹杂物和析出相对其性能影响尤为重要。
本文将从夹杂物和析出相的作用及行为两个方面,对其对非调质塑料模具钢的影响进行探讨。
一、夹杂物的作用及行为1. 夹杂物对塑料模具钢的力学性能的影响夹杂物是指钢中的非金属物质,如氧化物、硫化物、氮化物等。
夹杂物的存在会使塑料模具钢的力学性能受到影响,如降低强度、延展性和韧性等。
其中,氧化物和硫化物是夹杂物中影响最大的两种。
氧化物会使钢中的晶粒变大,从而降低其强度。
另外,在钢中存在氧化物的情况下,钢的疲劳寿命也会受到影响,因为氧化物会成为裂纹的起始点,从而导致裂纹的扩展。
硫化物会使钢中的塑性降低,从而使其韧性降低。
另外,硫化物还容易形成脆性相,从而导致钢的断裂。
2. 夹杂物对塑料模具钢的腐蚀性能的影响夹杂物的存在还会影响钢的腐蚀性能。
在塑料模具钢中,夹杂物的存在会使其易于发生腐蚀,从而导致钢的损坏。
特别是在高温高压的工作环境中,钢的腐蚀速度更快。
3. 夹杂物的来源及控制方法夹杂物的来源主要有三种:原料、工艺和设备。
原料中的夹杂物主要来自于炼钢过程中的氧化物和硫化物。
工艺中的夹杂物主要来自于热处理过程中的氧化物和硫化物。
设备中的夹杂物主要来自于设备的磨损和腐蚀。
控制夹杂物的方法主要有两种:一是通过改变原料和工艺条件,减少夹杂物的生成。
二是通过热处理过程中的热处理工艺,使夹杂物分散在钢中,从而减少其对钢的影响。
二、析出相的作用及行为1. 析出相对塑料模具钢的力学性能的影响析出相是指钢中的一些金属化合物,如碳化物、氮化物、硫化物等。
析出相的存在会使钢的强度和硬度增加,但会降低其延展性和韧性。
特别是在高温高压的工作环境中,析出相会导致钢的断裂。
2. 析出相对塑料模具钢的磨损性能的影响析出相的存在也会影响钢的磨损性能。
在高温高压的工作环境中,析出相会导致钢的磨损速度加快,从而降低其使用寿命。
钢中夹杂物的产生与去除途径
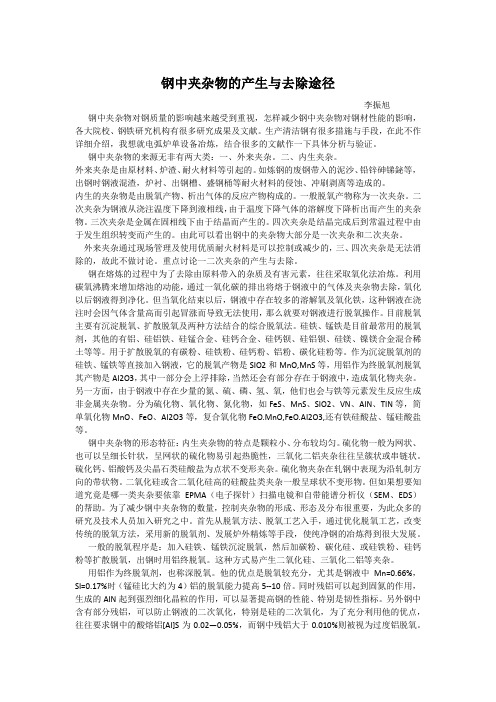
钢中夹杂物的产生与去除途径李振旭钢中夹杂物对钢质量的影响越来越受到重视,怎样减少钢中夹杂物对钢材性能的影响,各大院校、钢铁研究机构有很多研究成果及文献。
生产清洁钢有很多措施与手段,在此不作详细介绍,我想就电弧炉单设备冶炼,结合很多的文献作一下具体分析与验证。
钢中夹杂物的来源无非有两大类:一、外来夹杂。
二、内生夹杂。
外来夹杂是由原材料、炉渣、耐火材料等引起的。
如炼钢的废钢带入的泥沙、铅锌砷锑鉍等,出钢时钢液混渣,炉衬、出钢槽、盛钢桶等耐火材料的侵蚀、冲刷剥离等造成的。
内生的夹杂物是由脱氧产物、析出气体的反应产物构成的。
一般脱氧产物称为一次夹杂。
二次夹杂为钢液从浇注温度下降到液相线,由于温度下降气体的溶解度下降析出而产生的夹杂物。
三次夹杂是金属在固相线下由于结晶而产生的。
四次夹杂是结晶完成后到常温过程中由于发生组织转变而产生的。
由此可以看出钢中的夹杂物大部分是一次夹杂和二次夹杂。
外来夹杂通过现场管理及使用优质耐火材料是可以控制或减少的,三、四次夹杂是无法消除的,故此不做讨论。
重点讨论一二次夹杂的产生与去除。
钢在熔炼的过程中为了去除由原料带入的杂质及有害元素,往往采取氧化法冶炼。
利用碳氧沸腾来增加熔池的动能,通过一氧化碳的排出将熔于钢液中的气体及夹杂物去除,氧化以后钢液得到净化。
但当氧化结束以后,钢液中存在较多的溶解氧及氧化铁,这种钢液在浇注时会因气体含量高而引起冒涨而导致无法使用,那么就要对钢液进行脱氧操作。
目前脱氧主要有沉淀脱氧、扩散脱氧及两种方法结合的综合脱氧法。
硅铁、锰铁是目前最常用的脱氧剂,其他的有铝、硅铝铁、硅锰合金、硅钙合金、硅钙钡、硅铝钡、硅镁、镍镁合金混合稀土等等。
用于扩散脱氧的有碳粉、硅铁粉、硅钙粉、铝粉、碳化硅粉等。
作为沉淀脱氧剂的硅铁、锰铁等直接加入钢液,它的脱氧产物是SIO2和MnO,MnS等,用铝作为终脱氧剂脱氧其产物是AI2O3,其中一部分会上浮排除,当然还会有部分存在于钢液中,造成氧化物夹杂。
帘线钢中钛夹杂物形貌和析出尺寸的计算
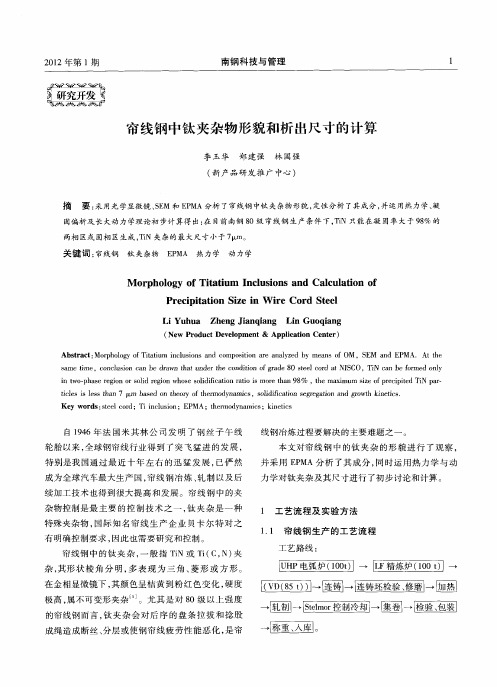
到平衡时 的析 出温度为 19 . 因此 , 3 34K, 正常 TN夹 i
杂 不 会 在 液 相 区 和 两 相 区生 成 , 能 在 固 相 区且 只 只
有在温度低 于 19 . 以下才 会 生成 。以上分 析 33 4 K
结果是在假定钢液成分及 温度均匀 的理 想条 件下得 出的 。实际钢液凝 固时 , 溶质原 子在 固 、 液两相 问因 溶解度不 同将 发生 再分 配 , 果导 致铸 坯产 生宏 观 结 偏析 。帘线钢液 结 晶前沿 r 和 N发 生 富集 , T ) r i ( i ・ N) W( 达到 比较大的数值时就可能生成 TN i。 考虑偏析 , 当微 区域 的凝 固率 ( 固相质量 与微 即 区域原始质 量 之 比) g时 , i 微 区 中 的偏 析 用 为 T在
成为全球汽车最大生产国 , 帘线钢 冶炼 、 制 以及 后 轧 续加工 技术 也得到很大提高和发 展。帘线 钢 中的夹 杂物控制是 最 主要 的控制 技术 之一 , 夹杂是 一 种 钛
特 殊 夹 杂 物 , 际 知 名 帘 线 生 产 企 业 贝 卡 尔 特 对 之 国
1 工 艺 流 程 及 实 验 方 法
K e wor y ds:t lc r see o d;Tii cuso n l i n; EPM A ;t e mo y mis;kie is h r d na c n tc
自 14 9 6年 法 国米其林 公 司 发 明了钢 丝 子午 线 轮胎以来 , 全球钢帘线行业得到 了突 飞猛 进 的发展 ,
,
,
平 衡 分配 系数 k和扩 散 系数 D
见表 2: .
表 2 C N元 素 在 固 相 与 钢 液 之 间 的 、
平 衡 分 配 系数 k及 扩 散 系数 D
非金属夹杂物分类及特征

非金属夹杂物分类及特征
非金属夹杂物可以分为以下几类:
1. 氧化物夹杂物:包括氧化物粉尘、氧化物颗粒、氧化物鳞片等。
这些夹杂物通常具有较高的硬度和熔点,对金属制品的机械性能和耐热性能有较大影响。
2. 硫化物夹杂物:包括硫化物颗粒、硫化物晶体等。
硫化物夹杂物对金属制品的韧性和耐蚀性有较大影响,同时还会引起金属制品的应力腐蚀裂纹。
3. 硅夹杂物:包括硅颗粒、硅鳞片等。
硅夹杂物会降低金属制品的延展性和强度,同时还会引起金属脆性断裂。
4. 硝酸盐夹杂物:包括硝酸盐颗粒、硝酸盐结晶等。
硝酸盐夹杂物会降低金属制品的耐腐蚀性能。
5. 气孔:由于金属在凝固过程中会产生气体,如果没有完全排除,就会形成气孔。
气孔对金属制品的强度和密封性能有较大影响。
这些非金属夹杂物通常会降低金属制品的力学性能、耐蚀性能和耐热性能。
因此,在金属制品的生产过程中,需要严格控制这些夹杂物的含量和分布,以确保最终产品的质量。
微合金化钢中析出物和夹杂物的控制和利用的开题报告

微合金化钢中析出物和夹杂物的控制和利用的开题报告一、研究背景微合金化钢在现代冶金制造业中具有广泛的应用和普及,其制造工艺和性能转型已经成为钢铁工业的主要议题之一。
针对微合金化钢的控制和利用,如何控制微合金化钢中的析出物和夹杂物的数量和尺寸,不仅涉及到钢铁制造的技术成熟度,而且也与钢铁材料的性能和质量密切相关。
因此,研究微合金化钢中析出物和夹杂物的控制和利用是非常有必要的。
二、研究内容1. 分析微合金化钢中析出物的形成机理和成分组成2. 探究夹杂物在微合金化钢中的生成原因和形成机理3. 研究微合金化钢中析出物和夹杂物的性质和对材料性能的影响4. 分析和探索微合金化钢中控制和利用析出物和夹杂物的方法和技术5. 对微合金化钢中析出物和夹杂物控制和利用的研究成果进行分析和总结三、研究意义1. 掌握微合金化钢中析出物和夹杂物的形成机理和成分组成,对于钢铁材料的制造和性能的提升有着积极的作用。
2. 研究析出物和夹杂物对微合金化钢的材料性能的影响,有助于优化微合金化钢的制造工艺,提高劣化微合金化钢的抗变形和耐腐蚀性能等。
3. 探究控制和利用微合金化钢中析出物和夹杂物的方法和技术,对于微合金化钢的高效制造和节约资源也有着重要的意义。
四、研究方法1. 应用断口分析、金相显微镜、扫描电镜等现代金属材料分析技术,对微合金化钢中的夹杂物和析出物进行观察和鉴定。
2. 通过实验室控制微合金化钢的制造工艺,调整合金元素、原料组成等各种条件来试验微合金化钢中析出物和夹杂物的控制方法。
3. 利用热力学计算软件,模拟微合金化钢中析出物和夹杂物的生成和分布规律,优化工艺条件和合金元素的组成等。
五、预期成果通过对微合金化钢中析出物和夹杂物的控制和利用的研究,预计能达到以下目标:1. 分析和总结微合金化钢中析出物和夹杂物的形成机理和成分组成,为微合金化钢的生产提供更加科学的基础理论。
2. 研究微合金化钢中析出物和夹杂物的性质和对材料性能的影响,增加微合金化钢的使用价值。
浅析钢材的内部缺陷及其对热处理工艺和性能的影响
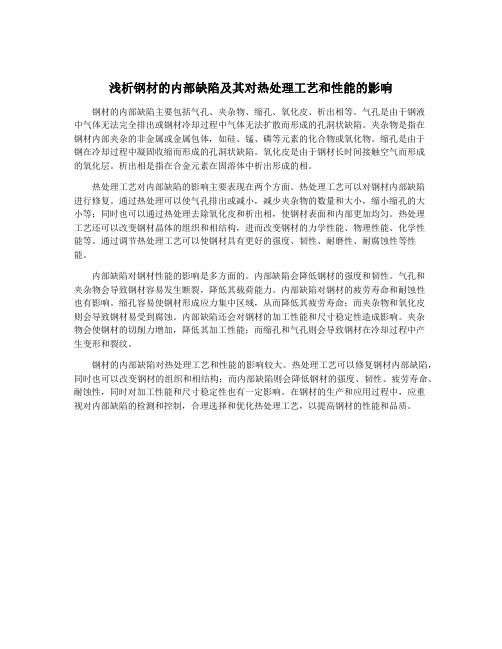
浅析钢材的内部缺陷及其对热处理工艺和性能的影响钢材的内部缺陷主要包括气孔、夹杂物、缩孔、氧化皮、析出相等。
气孔是由于钢液中气体无法完全排出或钢材冷却过程中气体无法扩散而形成的孔洞状缺陷。
夹杂物是指在钢材内部夹杂的非金属或金属包体,如硅、锰、磷等元素的化合物或氧化物。
缩孔是由于钢在冷却过程中凝固收缩而形成的孔洞状缺陷。
氧化皮是由于钢材长时间接触空气而形成的氧化层。
析出相是指在合金元素在固溶体中析出形成的相。
热处理工艺对内部缺陷的影响主要表现在两个方面。
热处理工艺可以对钢材内部缺陷进行修复。
通过热处理可以使气孔排出或减小,减少夹杂物的数量和大小,缩小缩孔的大小等;同时也可以通过热处理去除氧化皮和析出相,使钢材表面和内部更加均匀。
热处理工艺还可以改变钢材晶体的组织和相结构,进而改变钢材的力学性能、物理性能、化学性能等。
通过调节热处理工艺可以使钢材具有更好的强度、韧性、耐磨性、耐腐蚀性等性能。
内部缺陷对钢材性能的影响是多方面的。
内部缺陷会降低钢材的强度和韧性。
气孔和夹杂物会导致钢材容易发生断裂,降低其载荷能力。
内部缺陷对钢材的疲劳寿命和耐蚀性也有影响。
缩孔容易使钢材形成应力集中区域,从而降低其疲劳寿命;而夹杂物和氧化皮则会导致钢材易受到腐蚀。
内部缺陷还会对钢材的加工性能和尺寸稳定性造成影响。
夹杂物会使钢材的切削力增加,降低其加工性能;而缩孔和气孔则会导致钢材在冷却过程中产生变形和裂纹。
钢材的内部缺陷对热处理工艺和性能的影响较大。
热处理工艺可以修复钢材内部缺陷,同时也可以改变钢材的组织和相结构;而内部缺陷则会降低钢材的强度、韧性、疲劳寿命、耐蚀性,同时对加工性能和尺寸稳定性也有一定影响。
在钢材的生产和应用过程中,应重视对内部缺陷的检测和控制,合理选择和优化热处理工艺,以提高钢材的性能和品质。
从微观形貌探索钢中白点与夹杂物和偏析的关系
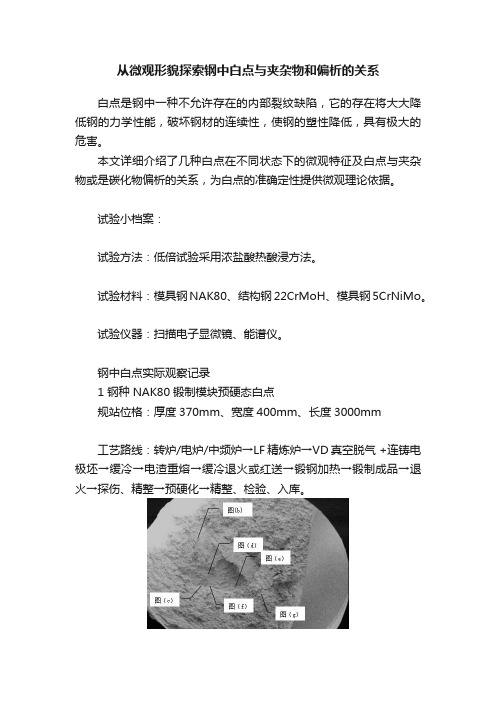
从微观形貌探索钢中白点与夹杂物和偏析的关系白点是钢中一种不允许存在的内部裂纹缺陷,它的存在将大大降低钢的力学性能,破坏钢材的连续性,使钢的塑性降低,具有极大的危害。
本文详细介绍了几种白点在不同状态下的微观特征及白点与夹杂物或是碳化物偏析的关系,为白点的准确定性提供微观理论依据。
试验小档案:试验方法:低倍试验采用浓盐酸热酸浸方法。
试验材料:模具钢NAK80、结构钢22CrMoH、模具钢5CrNiMo。
试验仪器:扫描电子显微镜、能谱仪。
钢中白点实际观察记录1 钢种NAK80锻制模块预硬态白点规站位格:厚度370mm、宽度400mm、长度3000mm工艺路线:转炉/电炉/中频炉→LF精炼炉→VD真空脱气 +连铸电极坯→缓冷→电渣重熔→缓冷退火或红送→锻钢加热→锻制成品→退火→探伤、精整→预硬化→精整、检验、入库。
图1(a)断口形貌图1(b)断口上的圆形斑点形貌图1(c)冰糖状断口形貌图1(d)碎条状断口形貌图1(e)混合断口形貌图1(f)自由表面及气蚀小孔形貌图1(g)基体解理断口形貌图1NAK80预硬态白点断口形貌2 钢种22CrMoH热轧态白点规站位格:直径φ160mm工艺路线:转炉/电炉+LF精炼炉+RH/VD真空脱气→连铸→加热、开坯、轧制成材→缓冷→精整→检查→包装入库。
图2(a)断口形貌图2(b)断口上的长条斑点形貌图2(c)准解理颗粒状形貌图2(d)斑点处夹杂物形貌图2(e)解理花样形貌图2 22CrMoH热轧态白点断口形貌3 钢种5CrNiMo调质态白点规站位格:厚度355mm、宽度505mm、长度2500mm工艺路线:转炉→LF 精炼炉→VD真空脱气→模铸→红转→加热→锻造→退火→光面探伤→粗加工→调质→探伤→检验→精整→包装→入库。
图3(a)圆形斑点形貌图3(b)浮云状断口形貌图3(c)蛀道花样形图3(d)夹杂物形貌图3(e)过渡区小韧窝形貌图3(f)解理花样形貌图3 5CrNiMo调质态白点断口形貌4 钢种5CrNiMo退火态白点规站位格:厚度455mm、宽度805mm、长度2850mm工艺路线:转炉→LF 精炼炉→VD真空脱气→模铸→红转→加热→锻造→退火→光面探伤→粗加工→调质→探伤→检验→精整→包装→入库。
低压铸造常见缺陷及预防

低压铸造常见缺陷及预防一、气孔:1、特征〔1〕气孔:铸件内部由气体形成的孔洞类缺陷。
其外表一般比较光滑,主要呈梨形、圆形或椭圆形。
一般不在铸件外表露出,大孔常孤立存在,小孔那么成群出现。
〔2〕皮下气孔:位于铸件表皮下的分散性气孔。
为金属液与砂型〔铸型、湿芯、涂料、外表不干净的冷铁〕之间发生化学反响产生的反响性气孔。
形状有针状、蝌蚪状、球状、梨状等。
大小不一,深度不等。
通常在机械加工或热处理后才能发现。
〔3〕气窝〔气坑式外表气孔〕:铸件外表凹进去一块较平滑的气孔。
〔4〕气缩孔:分散性气孔与缩孔和缩松合并而成的孔洞类铸造缺陷。
〔5〕针孔:一般为针头大小分布在铸件截面上的析出性气孔。
铝合金铸件中常出现这类气孔,对铸件性能危害很大。
①点状针孔:此类针孔在低倍显微组织中呈圆点状,轮廓明晰且互不相连,能清点出每平方厘米面积上的针孔数目并测得针孔的直径。
这类针孔容易和缩孔、缩松相区别。
点状针孔由铸件凝固时析出的气泡所形成,多发生于结晶温度范围小,补缩才能良好的铸件中,如ZL102合金铸件中。
当凝固速度较快时,离共晶成分较远的ZL105合金铸件中也会出现点状针孔。
②网状针孔:此类针孔在低倍显微组织中呈密集相联成网状,伴有少量较大的孔洞,不易清点针孔数目,难以测量针孔的直径,往往带有末梢,俗称“苍蝇脚〞。
结晶温度宽的合金,铸件缓慢凝固时析出的气体分布在晶界上及兴隆的枝晶间隙中,此时结晶股价已形成,补缩通道被堵塞,便在晶界上及枝晶间隙中形成网状针孔。
③混合型针孔:此类针孔点状针孔和网状针孔混杂一起,常见于构造复杂、壁厚不均匀的铸件中。
针孔可按国家标准分等级,等级越差,那么铸件的力学性能越低,其抗蚀性能和外表质量越差。
当达不到铸件技术条件所允许的针孔等级时,铸件将被报废,其中网状针孔割裂合金基体,危害性比点状针孔大。
〔6〕外表针孔:成群分布在铸件表层的分散性气孔。
其特征和形成原因与皮下气孔一样,通常暴露在铸件外表,机械加工1~2mm后即可去掉。
铸造-气孔及夹杂、偏析

第三章铸件中的气孔3.1 铸件中气体的存在形态:原子、化合物、分子。
以氮为例子:原子的氮:固溶体,氮与金属反应,氮化物,氮以气体方式存在:氮气,形成气孔。
前两种方式:不是咱们本节讨论的问题,因此不予讨论。
本节主要讨论以分子方式存在所产生的问题。
3.2铸件中的气孔的种类概念:气孔:铸件在凝固过程中气体残留在铸件中形成的孔洞---气孔(1)析出性气孔:在金属溶液中,--------温度高,------气体的溶解度高,-------温度降低,---- -金属溶解度降低--——气体析出——析出的气体来不及排出——残留在铸件内部——形成气孔。
这种气孔主要是由溶液中析出的,因此称为析出性气孔。
形成部位:气体在溶液中各个部位均有溶解,因此,析出性气孔在铸件整个断面上均有,可以呈现大面积分布。
在冒口、铸件厚壁部位:溶液凝固较晚,气体容易向此处转移,因此,在此部位容易出现析出性气孔的聚集,在此部位分布比较密集。
形状:球团形、多角裂纹形,断续裂纹形或混合型。
(2)反应性气孔:金属液与铸型或金属液内部各种成分之间产生化学反应,产生一定的气体,这些气体在金属液凝固过程中来不及排出铸件之外,在铸件中形成气孔。
C+O2 CONH3 N2+H2气体是由化学反应造成的,因此成为反应性气孔。
产生部位:主要原因:与铸型之间的反应:因此一般在铸件表面或铸件表面1~3毫米以下。
出现在铸件表面以下:一般称为皮下气孔。
(主要原因:金属液与助兴之间的反应产生)金属液内部各成分之间产生的反应,在整个断面上出现,因此,气孔也出现在整个断面上。
形状:一般应该为圆形,产生后有向铸件外逸出的趋势,因此在向外逸出的过程中(3)侵入性气孔金属液外部的气体进入到金属液内部,在金属液凝固过程中来不及逸出到金属液外部而残留在铸件内部,所形成的气孔,称为侵入性气孔。
最主要原因:水分:受热后液态变为气态,体积大大膨胀,产生非常高的压力,在压力作用下进入金属液内部。
9气孔及夹杂、偏析
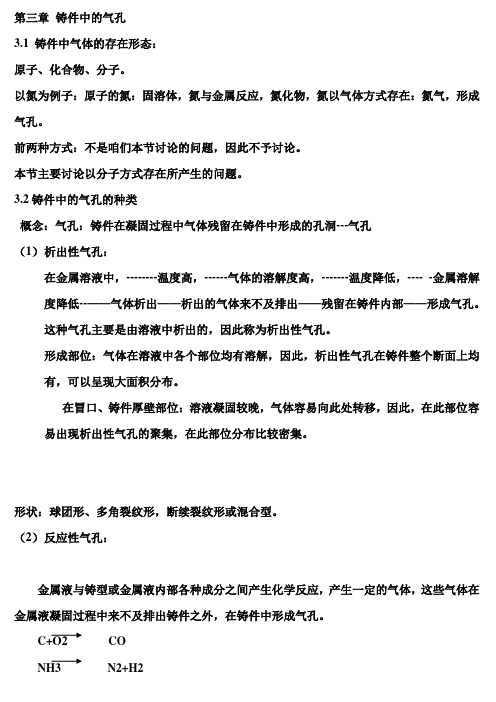
第三章铸件中的气孔3.1 铸件中气体的存在形态:原子、化合物、分子。
以氮为例子:原子的氮:固溶体,氮与金属反应,氮化物,氮以气体方式存在:氮气,形成气孔。
前两种方式:不是咱们本节讨论的问题,因此不予讨论。
本节主要讨论以分子方式存在所产生的问题。
3.2铸件中的气孔的种类概念:气孔:铸件在凝固过程中气体残留在铸件中形成的孔洞---气孔(1)析出性气孔:在金属溶液中,--------温度高,------气体的溶解度高,-------温度降低,---- -金属溶解度降低--——气体析出——析出的气体来不及排出——残留在铸件内部——形成气孔。
这种气孔主要是由溶液中析出的,因此称为析出性气孔。
形成部位:气体在溶液中各个部位均有溶解,因此,析出性气孔在铸件整个断面上均有,可以呈现大面积分布。
在冒口、铸件厚壁部位:溶液凝固较晚,气体容易向此处转移,因此,在此部位容易出现析出性气孔的聚集,在此部位分布比较密集。
形状:球团形、多角裂纹形,断续裂纹形或混合型。
(2)反应性气孔:金属液与铸型或金属液内部各种成分之间产生化学反应,产生一定的气体,这些气体在金属液凝固过程中来不及排出铸件之外,在铸件中形成气孔。
C+O2 CONH3 N2+H2气体是由化学反应造成的,因此成为反应性气孔。
产生部位:主要原因:与铸型之间的反应:因此一般在铸件表面或铸件表面1~3毫米以下。
出现在铸件表面以下:一般称为皮下气孔。
(主要原因:金属液与助兴之间的反应产生)金属液内部各成分之间产生的反应,在整个断面上出现,因此,气孔也出现在整个断面上。
形状:一般应该为圆形,产生后有向铸件外逸出的趋势,因此在向外逸出的过程中(3)侵入性气孔金属液外部的气体进入到金属液内部,在金属液凝固过程中来不及逸出到金属液外部而残留在铸件内部,所形成的气孔,称为侵入性气孔。
最主要原因:水分:受热后液态变为气态,体积大大膨胀,产生非常高的压力,在压力作用下进入金属液内部。
钢中硫化铁夹杂物析出原理_概述说明以及解释

钢中硫化铁夹杂物析出原理概述说明以及解释1. 引言1.1 概述在现代钢铁冶炼过程中,硫化铁夹杂物的析出对于钢材的质量和性能具有重要影响。
硫化铁夹杂物是由于钢中含有过多的硫元素而形成的一种微观结构,在钢材中分布不均匀,并且会导致钢材在使用过程中出现脆化、断裂等问题。
因此,深入研究硫化铁夹杂物析出原理及其相应的控制技术具有重要的理论和实际意义。
1.2 文章结构本文将围绕硫化铁夹杂物析出原理展开全面系统的阐述。
首先,我们将介绍硫化铁夹杂物的含义和特点,探讨其在钢铁材料中的重要作用。
然后,我们将概述硫化铁夹杂物析出原理,并解释其形成与演变机制。
进一步地,我们将介绍并分析影响硫化铁夹杂物析出过程的关键因素,从实验方法与表征手段上进行详细说明。
最后,我们将总结当前已取得的研究成果,并提出未来研究的方向与展望。
1.3 目的本文旨在深入探讨钢中硫化铁夹杂物析出原理,全面了解其形成机理和影响因素。
通过研究不同的控制技术和措施,实现对硫化铁夹杂物的有效控制,以提高钢材的质量和性能。
为此,我们将介绍当前已有的相关研究工作,并总结实践中所取得的成果。
同时,本文还将对未来的研究方向进行展望,为进一步深入研究该领域提供参考。
以上是“1. 引言”部分内容,请根据此内容撰写文章。
2. 钢中硫化铁夹杂物析出原理2.1 硫化铁夹杂物的含义和特点在钢中,硫化铁是一种常见的夹杂物。
硫化铁夹杂物指的是由铁与硫元素结合形成的硫化铁晶体,通常呈现出片状、条状或球状的形态。
这些夹杂物在钢中存在的主要原因是来自于原材料中的硫元素和工艺过程中的硫污染。
2.2 析出原理的概述硫化铁夹杂物析出是指在钢水冷却过程中,由于温度下降和相应成分变化,导致溶解在钢中的硫与其他元素结合生成硫化物并析出。
当钢水冷却至一定温度时,其中所含的溶解性硫会与流动态产生相互作用,并进而促使以二聚、多聚体形态析出出来。
这些形成的固相颗粒就是我们所说的硫化铁夹杂物。
2.3 解释硫化铁夹杂物析出影响因素造成钢中硫化铁夹杂物析出量和分布情况的因素有很多。
Ti、Nb微合金化Q345B钢板夹杂物和析出物分析
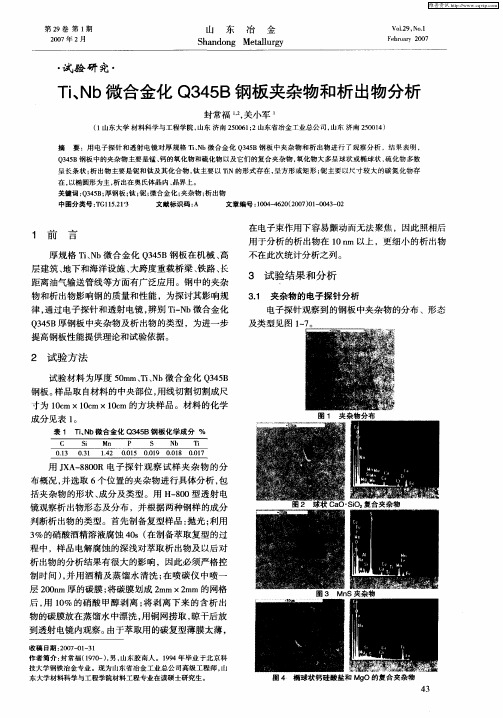
形成 铌和钛 的复合 碳氮化 物 。
图 9 示析 出物 分布不 均匀 ,方 形 的是 TN析 所 i
出物 , 其余形状不规则的是钛的碳硫化物。T i N多为
方形 和矩 形 ;i TS一般 为椭 圆形 、圆形 和不规 则形 状
等 ;i TC多为 圆形 和椭 圆形等 。根据 它们 的析 出尺寸
维普资讯
维普资讯
20 年 2 07 月
山 东
冶
金
第 2 卷 9
图 7 硫 化物 和 氧化 物的 复合 夹杂 物
椭 圆为主 , 有 圆片 形及有 棱多边 形 。 出的部 位主 也 析 要 在奥 氏体 晶内 、 晶界上 。 寸较小 的不规则 析 出物 尺
20 0 7年 2月
山 东 冶 金
S a d n M ea lr y h n og tlu g
ห้องสมุดไป่ตู้
Vo .9. . 1 2 No 1
Fe r ay 2 0 b u r 0 7
・
试验 研 究 ・
高氯酸氧化 三价锰滴定 法测定硅锰 铝合金 中的锰
刘 兴沂 , , 梁彦 平 z苏 文星 z ,
为铌 和 钛 的复 合 析 出物 , 大小 为 3 0~6 n 有 较好 0 m, 的析 出强 化作用 。由于 N b或 T 的碳化 物 、 物及 i 氮化 碳 氮化物 的 晶格 类 型 、 晶格 常数 相差 不大 , 都是 面心
立方 , 晶格 常数 在 4~ 5 m之 间 , 容易 相互 溶 解 , 4n 很
可知 , 二相粒 子 的析出顺 序应为 TN TS TC 第 i — i— i 。
杂物是钙硅酸盐和 A , I 的复合夹杂物且含有少量 O 硫 化物 。在钢 的夹 杂物 中 ,最 常见 的 晶体是 钙长石
夹杂物与析出物的区别
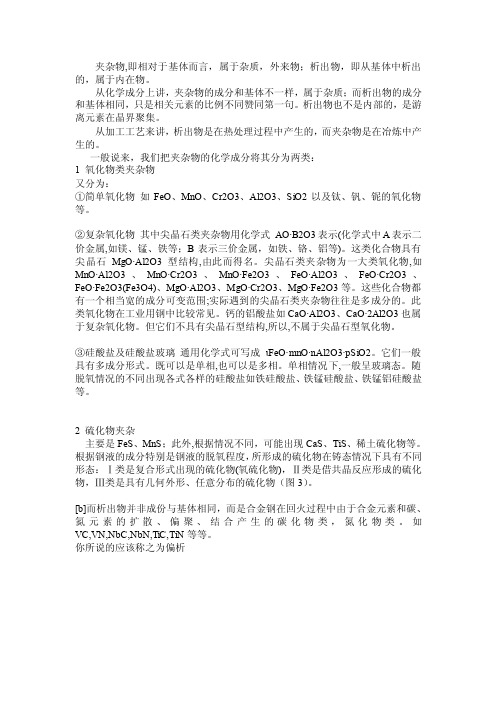
夹杂物,即相对于基体而言,属于杂质,外来物;析出物,即从基体中析出的,属于内在物。
从化学成分上讲,夹杂物的成分和基体不一样,属于杂质;而析出物的成分和基体相同,只是相关元素的比例不同赞同第一句。
析出物也不是内部的,是游离元素在晶界聚集。
从加工工艺来讲,析出物是在热处理过程中产生的,而夹杂物是在冶炼中产生的。
一般说来,我们把夹杂物的化学成分将其分为两类:1 氧化物类夹杂物又分为:①简单氧化物如FeO、MnO、Cr2O3、Al2O3、SiO2以及钛、钒、铌的氧化物等。
②复杂氧化物其中尖晶石类夹杂物用化学式AO·B2O3表示(化学式中A表示二价金属,如镁、锰、铁等;B表示三价金属,如铁、铬、铝等)。
这类化合物具有尖晶石MgO·Al2O3型结构,由此而得名。
尖晶石类夹杂物为一大类氧化物,如MnO·Al2O3、MnO·Cr2O3、MnO·Fe2O3、FeO·Al2O3、FeO·Cr2O3、FeO·Fe2O3(Fe3O4)、MgO·Al2O3、MgO·Cr2O3、MgO·Fe2O3等。
这些化合物都有一个相当宽的成分可变范围;实际遇到的尖晶石类夹杂物往往是多成分的。
此类氧化物在工业用钢中比较常见。
钙的铝酸盐如CaO·Al2O3、CaO·2Al2O3也属于复杂氧化物。
但它们不具有尖晶石型结构,所以,不属于尖晶石型氧化物。
③硅酸盐及硅酸盐玻璃通用化学式可写成ιFeO·mnO·nAl2O3·pSiO2。
它们一般具有多成分形式。
既可以是单相,也可以是多相。
单相情况下,一般呈玻璃态。
随脱氧情况的不同出现各式各样的硅酸盐如铁硅酸盐、铁锰硅酸盐、铁锰铝硅酸盐等。
2 硫化物夹杂主要是FeS、MnS;此外,根据情况不同,可能出现CaS、TiS、稀土硫化物等。
根据钢液的成分特别是钢液的脱氧程度,所形成的硫化物在铸态情况下具有不同形态:Ⅰ类是复合形式出现的硫化物(氧硫化物),Ⅱ类是借共晶反应形成的硫化物,Ⅲ类是具有几何外形、任意分布的硫化物(图3)。
第三节 夹杂物和化学成分偏析的检验

似,沿加工方向呈颗粒状,也呈暗灰色。一般硅酸盐类夹杂
物端部呈锐角。
D类(球状不变形夹杂物):例如铬轴承钢中的点状夹杂 物主要是由镁尖晶石和含钙的铝酸盐或含铝、钙、锰的 硅酸盐所组成。这种不变形夹杂物经加工后不变形,以 点状形式存在,形态比较小,呈黑色或蓝色无规则分布 如图示:
分析夹杂物的类型数量大小和分布是材料质量和实效分析的重要依据钢中夹杂物的存在破坏了金属基体的连续性它们在钢中的形态数量大小和分布都不同程度的影响钢的各种性能导致应力集中疲劳断裂显著降低钢的塑韧性焊接性以及耐腐蚀性因此钢中夹杂物的数量和分布通常被认为是评定钢质量的一个重要指标一钢中夹杂物的类型和特征钢中的夹杂物根据其来源可分为两大类1外来夹杂物主要是由耐火材料炉渣等在冶炼浇注过程中进入钢液中来不及上浮而留在钢中称为外生夹杂物
评定夹杂物级别时,一般不计较其组成、 性能以及可能来源,只注意其数量、形状、 大小和分布情况。
对钢中的非金属夹杂物进行显微评定时, 目前主要采用GB/T10561-2005标准,通常 采用与标准图谱进行比较来对钢中的非金 属夹杂物进行显微评定。
夹杂物的粗系和细系 A类:2μm~4μm称为细系 4~12 μm称为粗系 B类: 2μm~9μm称为细系 9~15 μm称为粗系 B类: 2μm~5μm称为细系 5~12 μm称为粗系 B类: 3μm~8μm称为细系 8~13 μm称为粗系
但常规的金相检验不能确定夹杂物成分 和晶体结构。目前电子显微技术已广泛应 用于夹杂物的鉴定,经深腐蚀的金相试样 在扫描电子显微镜下可直接观察夹杂物的 形态。
同时电子探针可直接确定微区的化学成 分及组成相。
三、夹杂物的评级
夹杂物试样不经过腐蚀,一般在明场下 放大100倍,直径80mm的视场下进行检验。 从试样中心到边缘全面观察,选取夹杂物 污染最严重的视场,与钢种的相应标准评 级图加以对比来评定。
化学物质的析出物
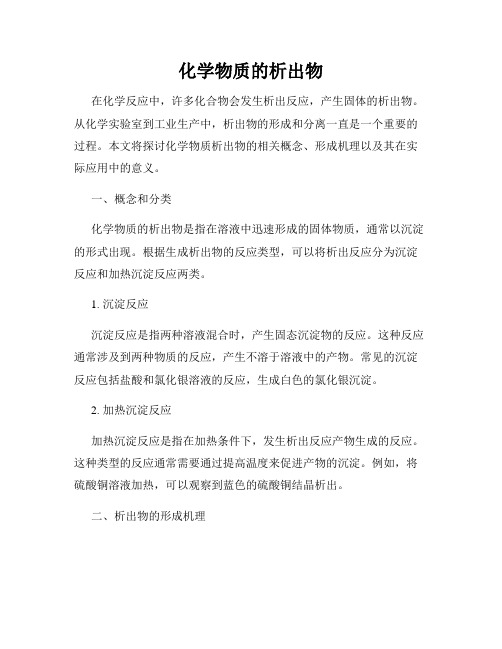
化学物质的析出物在化学反应中,许多化合物会发生析出反应,产生固体的析出物。
从化学实验室到工业生产中,析出物的形成和分离一直是一个重要的过程。
本文将探讨化学物质析出物的相关概念、形成机理以及其在实际应用中的意义。
一、概念和分类化学物质的析出物是指在溶液中迅速形成的固体物质,通常以沉淀的形式出现。
根据生成析出物的反应类型,可以将析出反应分为沉淀反应和加热沉淀反应两类。
1. 沉淀反应沉淀反应是指两种溶液混合时,产生固态沉淀物的反应。
这种反应通常涉及到两种物质的反应,产生不溶于溶液中的产物。
常见的沉淀反应包括盐酸和氯化银溶液的反应,生成白色的氯化银沉淀。
2. 加热沉淀反应加热沉淀反应是指在加热条件下,发生析出反应产物生成的反应。
这种类型的反应通常需要通过提高温度来促进产物的沉淀。
例如,将硫酸铜溶液加热,可以观察到蓝色的硫酸铜结晶析出。
二、析出物的形成机理化学物质的析出物形成机理主要涉及到反应物的溶解度和反应条件的控制。
在溶液中,化合物的溶解度决定了将其析出为固体沉淀物的能力。
当反应物的溶解度超过其饱和溶解度时,将会发生沉淀反应。
反应条件的控制也对析出物的形成起着关键作用。
例如,在沉淀反应中,通常需要静置溶液或加入沉淀试剂来促进沉淀物的形成。
加热沉淀反应则需要提高温度,以增加反应物的分子运动能力,从溶液中析出。
三、实际应用析出物在实际应用中具有广泛的用途。
1. 分离纯化析出物的形成使得化合物可以从混合物或溶液中进行有效的分离纯化。
通过对溶液进行过滤或离心操作,可以将固体析出物与溶液分离,得到纯净的产物。
这在实验室中的化学合成、制药工业以及废水处理等方面都有重要的应用。
2. 检测方法许多分析方法都依赖于析出物的形成反应来进行化学物质的定性和定量分析。
例如,在金属离子的检测中,可以通过添加沉淀试剂,观察是否形成特定的沉淀物来确定金属离子的存在。
3. 材料制备某些固体材料的合成也依赖于析出物的形成反应。
例如,通过控制金属离子沉淀的条件,可以制备出具有特定形貌和结构的纳米颗粒。
- 1、下载文档前请自行甄别文档内容的完整性,平台不提供额外的编辑、内容补充、找答案等附加服务。
- 2、"仅部分预览"的文档,不可在线预览部分如存在完整性等问题,可反馈申请退款(可完整预览的文档不适用该条件!)。
- 3、如文档侵犯您的权益,请联系客服反馈,我们会尽快为您处理(人工客服工作时间:9:00-18:30)。
夹杂物,即相对于基体而言,属于杂质,外来物;析出物,即从基体中析出的,属于内在物。
从化学成分上讲,夹杂物的成分和基体不一样,属于杂质;而析出物的成分和基体相同,只是相关元素的比例不同赞同第一句。
析出物也不是内部的,是游离元素在晶界聚集。
一般说来,我们把夹杂物的化学成分将其分为两类:
1 氧化物类夹杂物
又分为:
①简单氧化物如FeO、MnO、Cr2O3、Al2O3、SiO2以及钛、钒、铌的氧化物等。
②复杂氧化物其中尖晶石类夹杂物用化学式AO·B2O3表示(化学式中A表示二价金属,如镁、锰、铁等;B表示三价金属,如铁、铬、铝等)。
这类化合物具有尖晶石MgO·Al2O3型结构,由此而得名。
尖晶石类夹杂物为一大类氧化物,如MnO·Al2O3、MnO·Cr2O3、MnO·Fe2O3、FeO·Al2O3、FeO·Cr2O3、FeO·Fe2O3(Fe3O4)、MgO·Al2O3、MgO·Cr2O3、MgO·Fe2O3等。
这些化合物都有一个相当宽的成分可变范围;实际遇到的尖晶石类夹杂物往往是多成分的。
此类氧化物在工业用钢中比较常见。
钙的铝酸盐如CaO·Al2O3、CaO·2Al2O3也属于复杂氧化物。
但它们不具有尖晶石型结构,所以,不属于尖晶石型氧化物。
③硅酸盐及硅酸盐玻璃通用化学式可写成ιFeO·mnO·nAl2O3·pSiO2。
它们一般具有多成分形式。
既可以是单相,也可以是多相。
单相情况下,一般呈玻璃态。
随脱氧情况的不同出现各式各样的硅酸盐如铁硅酸盐、铁锰硅酸盐、铁锰铝硅酸盐等。
2 硫化物夹杂
主要是FeS、MnS;此外,根据情况不同,可能出现CaS、TiS、稀土硫化物等。
根据钢液的成分特别是钢液的脱氧程度,所形成的硫化物在铸态情况下具有不同形态:Ⅰ类是复合形式出现的硫化物(氧硫化物),Ⅱ类是借共晶反应形成的硫化物,Ⅲ类是具有几何外形、任意分布的硫化物(图3)。
[b]而析出物并非成份与基体相同,而是合金钢在回火过程中由于合金元素和碳、氮元素的扩散、偏聚、结合产生的碳化物类,氮化物类。
如VC,VN,NbC,NbN,TiC,TiN等等。
你所说的应该称之为偏析。