节能减排低碳炼铁实现中国高炉生产的科学发展
炼铁高炉热风炉现状及发展方向

千里之行,始于足下。
炼铁高炉热风炉现状及进展方向炼铁高炉热风炉是炼铁工艺中的重要设备,其主要功能是为高炉供应高温高压的燃料气体,实现高炉的高效运行。
随着工业化的快速进展,炼铁高炉热风炉也在不断改进和进展,以适应新的技术需求和环保要求。
目前,炼铁高炉热风炉存在以下一些主要问题:1. 能源消耗问题:传统的热风炉接受煤炭作为燃料,燃烧效率较低,能源利用率不高,造成能源铺张。
2. 环境污染问题:煤炭燃烧产生的烟尘、SO2等污染物对环境造成严峻影响,对空气质量和生态环境都有肯定的危害。
3. 高炉生产问题:热风炉是高炉的重要设备之一,其性能和运行稳定性直接影响高炉的生产效率和产品质量。
为了解决这些问题,炼铁高炉热风炉的进展方向主要包括以下几个方面:1. 燃料多元化:接受多种燃料替代传统的煤炭,如自然气、生物质能源等。
这样可以提高热风炉的燃烧效率,降低能源消耗,削减环境污染。
2. 热风炉技术改进:通过改进热风炉的结构和工艺参数,提高炉内燃烧效率和传热效果,削减能源铺张。
同时,优化气体流淌分布和热风炉燃烧工艺,降低烟气排放浓度,削减环境污染。
3. 热风炉智能化:利用现代化的把握系统和自动化技术,实现对热风炉的智能监控和操作,提高热风炉的运行稳定性和平安性。
第1页/共2页锲而不舍,金石可镂。
4. 绿色化生产:在炼铁高炉热风炉的建设和运行过程中,留意削减煤炭燃烧对环境的污染,推广清洁能源的利用,接受先进的环保技术,削减废气废水的排放,实现高炉的绿色化生产。
总之,炼铁高炉热风炉的进展方向是以节能减排和提高生产效率为主要目标,通过技术改进和创新,实现炼铁工艺的可持续进展和绿色化生产。
同时,结合智能化和自动化技术,提高热风炉的运行稳定性和平安性,为高炉的正常生产供应牢靠的支持。
提高高炉炉料中球团矿配比,促进节能减排

提高高炉炉料中球团矿配比、促进节能减排(资料来源:冶金管理,王维兴)一、优化炼铁炉料结构的原则高炉炼铁炉料是由烧结矿、球团矿和块矿组成,各高炉要根据不同的生产条件,决定各种炉料的配比,实现优化炼铁生产和低成本。
世界各国、各钢铁企业没有一个标准的炼铁炉料结构,都要根据各企业的具体情况制定适宜的炉料结构,同时还要根据外界情况的变化,进行及时调整。
2017 年中钢协会员单位高炉的炉料中平均有13%左右的球团矿,78%烧结矿,9%块矿。
在高炉生产时,各企业要根据其具体生产条件下,实现科学高炉炼铁操作(满足炼铁学基本原理),完成环境友好、低成本生产的目的。
实现低成本炼铁的方法包括:优化配矿、优化高炉操作、设备维护完好、生产效率高。
而实现高产低耗就要高炉入炉矿含铁品位高,有优质的炉料,包括高质量烧结矿要实现高碱度(1.8-2.2倍)。
但炼铁炉渣碱度要求在1.0-1.1 倍,炉料就需要配低碱度的球团矿(或块矿)。
高炉生产实现低燃料比,要求原燃料质量要好(入炉铁品位要高、冶金性能好、低MgO 和Al2O3、低渣量、焦炭质量好、含有害杂质少等),成分稳定,粒度均匀等。
要实现资源的合理利用,就要合理回收利用企业内含铁尘泥等等资源。
建议将含有害杂质高的烧结机头灰、高炉布袋灰,加石灰混合,造球,干燥,给转炉生产用,切断炼铁系统有害杂质的循环富集。
此外,球团工艺相比烧结工艺具有一定的优越性:1)产品冶金性能一般来说,烧结矿综合冶金性能优于球团矿,因此,高炉炼铁炉料中以高碱度烧结矿(在1.8-2.2 倍)为主。
但是,炼铁炉渣碱度要求在1.0 左右,必须搭配一部分酸性球团矿,这样结构炉料的冶金性能才最优,使高炉生产正常进行。
球团矿的缺点是膨胀率高,易粉化。
目前,北美和欧洲一些高炉使用100%自熔性球团矿,冶金性能完全能满足高炉炼铁的要求,也取得了较好的高炉生产指标。
2)生产运行费用球团工序能耗是烧结的2/3,环保治理费用低,球团矿铁品位比烧结矿高5-9 个百分点(原料品位、碱度相同条件下),炼铁生产效益高10 元/t。
炼铁工业的绿色生产与可持续发展
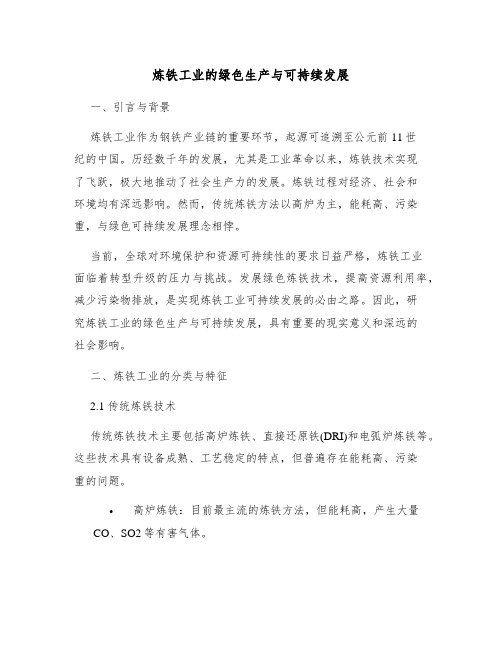
炼铁工业的绿色生产与可持续发展一、引言与背景炼铁工业作为钢铁产业链的重要环节,起源可追溯至公元前11世纪的中国。
历经数千年的发展,尤其是工业革命以来,炼铁技术实现了飞跃,极大地推动了社会生产力的发展。
炼铁过程对经济、社会和环境均有深远影响。
然而,传统炼铁方法以高炉为主,能耗高、污染重,与绿色可持续发展理念相悖。
当前,全球对环境保护和资源可持续性的要求日益严格,炼铁工业面临着转型升级的压力与挑战。
发展绿色炼铁技术,提高资源利用率,减少污染物排放,是实现炼铁工业可持续发展的必由之路。
因此,研究炼铁工业的绿色生产与可持续发展,具有重要的现实意义和深远的社会影响。
二、炼铁工业的分类与特征2.1 传统炼铁技术传统炼铁技术主要包括高炉炼铁、直接还原铁(DRI)和电弧炉炼铁等。
这些技术具有设备成熟、工艺稳定的特点,但普遍存在能耗高、污染重的问题。
•高炉炼铁:目前最主流的炼铁方法,但能耗高,产生大量CO、SO2等有害气体。
•直接还原铁(DRI):能耗较高炉低,但设备要求高,对原料有特殊要求。
•电弧炉炼铁:主要用于废钢铁的回收利用,但对电力资源要求较高。
2.2 绿色炼铁技术绿色炼铁技术旨在降低能耗、减少污染,提高铁矿产物的回收率。
•熔融还原炼铁:采用熔融盐或熔融金属作为反应介质,减少CO排放。
•氢还原炼铁:利用氢气作为还原剂,实现零碳排放。
•生物炼铁:利用微生物将铁氧化物还原为铁,具有环境友好、成本低的特点。
2.3 应用领域及市场潜力传统炼铁技术在短期内仍为主流,但绿色炼铁技术正逐步应用于钢铁生产,特别是在高档钢材、汽车用钢等领域展现出巨大市场潜力。
2.4 炼铁工业与其他领域的交叉融合炼铁工业与材料科学、环境科学、能源科学等领域紧密相关,绿色炼铁技术的发展需多学科交叉融合,共同推进。
三、关键技术及性能原理3.1 绿色炼铁技术的关键技术•熔融还原炼铁技术:科学基础是熔融盐的物理化学性质,工作原理是利用熔融盐中的离子移动传递电子给铁氧化物,实现还原。
钢铁行业生产流程与节能减排

钢铁行业生产流程与节能减排钢铁行业作为基础工业之一,扮演着重要的角色。
然而,钢铁行业的生产过程中却存在着大量的能源消耗和环境污染问题,因此,实施节能减排措施对于促进钢铁行业的可持续发展至关重要。
一、炼铁生产流程钢铁生产的第一步是炼铁过程。
传统的高炉炼铁工艺具有能源消耗高、排放多的缺点,因此,现如今越来越多的钢铁企业采用了先进的炼铁技术,如直接还原法、COREX煤气化炉等。
这些技术能够有效降低炼铁过程中的能源消耗和二氧化碳排放,实现节能减排的目标。
二、炼钢生产流程炼铁完成后,接下来是炼钢过程。
炼钢是将生铁中的杂质去除,得到高质量的钢材的过程。
常用的炼钢方法有转炉法、电炉法和氧气顶吹法等。
这些方法相比传统的开炉冶炼方式,不仅能够提高产能和产品质量,还能够减少能源消耗和环境污染。
三、钢铁生产过程中的节能减排措施1. 能源回收利用:钢铁生产过程中产生大量的热能和煤气等废气,通过设备和技术手段进行回收利用,可以减少能源消耗。
2. 节能技术应用:引入高效节能设备和技术,如电磁加热技术、高效燃烧技术等,可以提高能源利用效率,减少能源浪费。
3. 环保减排措施:使用先进的废气处理设备,如排烟脱硫、脱氮、脱氯等,可以减少大气污染物排放,改善环境质量。
4. 资源循环利用:钢铁生产过程中产生的废渣、废渣可以进行资源化利用,如炉渣可以用于生产水泥、砖块等,废气可以用于热电联供等。
四、钢铁行业节能减排的挑战与前景尽管钢铁行业在节能减排方面取得了一定的成绩,但仍面临着许多挑战。
首先,技术升级改造需要大量的资金投入,对企业而言是一项巨大的经济压力。
其次,有些地区对环保政策的执行不到位,导致一些企业依然存在违规排污行为。
此外,钢铁行业产能过剩也给节能减排带来了一定的困难。
然而,钢铁行业的节能减排前景仍然较为乐观。
随着科技的进步和政策的支持,钢铁企业将更加重视节能减排工作。
同时,新技术的应用和推广,将进一步提高钢铁行业的能源利用效率,减少环境污染。
绿色低碳炼铁关键技术介绍

绿色低碳炼铁关键技术介绍
绿色低碳炼铁是指利用环保、节能、低碳的技术和方法进行炼铁生产,以减少对环境的影响并降低碳排放。
以下是绿色低碳炼铁的一些关键技术介绍:
1. 高炉燃料替代技术,传统高炉使用焦炭作为还原剂和燃料,而绿色低碳炼铁技术中,可以采用生物质炭、再生资源炭等替代传统焦炭,以减少对森林资源的开采和减少二氧化碳排放。
2. 高炉煤气利用技术,高炉煤气是高炉生产过程中的副产品,通过先进的煤气净化技术和利用技术,可以将高炉煤气中的有用成分提取出来,用于发电、加热或化工原料,从而提高资源利用率和能源利用效率。
3. 高炉炉渣综合利用技术,绿色低碳炼铁技术中,炉渣不再被视为废弃物,而是被视为资源。
通过先进的炉渣处理技术,可以将炉渣中的有用金属成分回收利用,同时生产出对环境影响较小的新型建材产品,如水泥、砖块等。
4. 高炉烟气脱硫脱硝技术,绿色低碳炼铁技术要求高炉烟气中
的二氧化硫和氮氧化物排放达标。
因此,采用先进的脱硫脱硝技术,如湿法脱硫、SCR脱硝等,可以有效降低高炉烟气对环境的污染。
5. 高炉余热回收技术,高炉生产过程中会产生大量余热,通过
余热回收技术,可以将这些余热用于发电或供暖,提高能源利用效率,减少对外部能源的依赖,从而降低碳排放。
总的来说,绿色低碳炼铁技术是一个综合性、系统性的工程,
需要在高炉冶炼的每个环节都进行技术创新和改进,以实现对环境
友好、资源高效利用和碳排放降低的目标。
这些关键技术的应用将
为炼铁行业的可持续发展做出重要贡献。
高炉冶炼智能化的发展与探讨
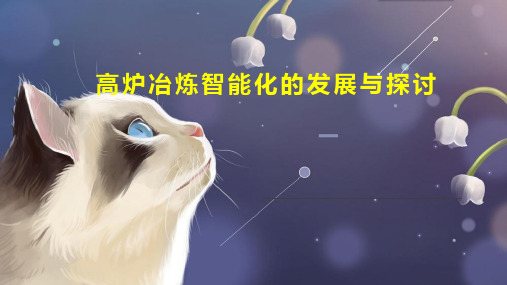
(3)提高产业协同:加强产业链上下游企业的合作与协同,实现资源共享和 优势互补,共同推动高炉冶炼智能化的发展。
(4)注重人才培养:加强高炉冶炼智能化领域人才的培养和引进,提高企业 和技术人员的专业素质和技术水平,为产业的可持续发展提供人才保障。
参考内容
随着全球气候变化和资源紧张问题的日益严峻,高炉炼铁行业面临着巨大的挑 战。为了降低碳排放、提高能源利用效率和推动可持续发展,高炉炼铁的低碳 化和智能化技术发展成为了行业的重要趋势。本次演示将详细介绍高炉炼铁低 碳化和智能化技术发展现状,以期为相关领域的研究和应用提供参考。
2、高炉冶炼智能化中安全问 题
高炉冶炼智能化中的安全问题主要包括设备安全和生产安全两个方面。设备安 全主要是指设备的稳定性和可靠性,以及针对设备故障的预警和处理能力。生 产安全主要是指生产过程中的安全隐患和事故预防,以及应对突发事件的应急 处理能力。保障高炉冶炼智能化的安全运行需要从设备选型、控制系统设计、 预警机制建立、应急预案制定等多个方面进行综合考虑和优化。
谢谢观看
高炉冶炼智能化的发展与探讨
目录
01 一、高炉冶炼智能化 的发展
03 参考内容
02
二、高炉冶炼智能化 的探讨
随着科技的快速发展,高炉冶炼智能化已成为现代钢铁工业的重要发展方向。 高炉冶炼智能化有助于提高钢铁企业的生产效率和产品质量,同时还能降低能 源消耗和环境污染。本次演示将从高炉冶炼智能化的发展历程和现状、关键技 术、安全与环保问题以及未来发展趋势等方面进行探讨。
3、高炉冶炼智能化的发展方向 与前景
未来,高炉冶炼智能化将朝着以下几个方向发展:
(1)全面智能化:通过不断引进新技术和设备,实现高炉冶炼全流程的智能 化,包括原料准备、高炉操作、煤气回收等环节。
炼铁技术感悟心得体会(3篇)

第1篇自从进入炼铁行业以来,我有幸见证并参与了我国炼铁技术的飞速发展。
从最初的土法炼铁到现代化的高炉炼铁,每一次技术革新都让我对炼铁技术有了更深的理解和感悟。
以下是我对炼铁技术的一些心得体会。
一、炼铁技术的演变与发展1. 土法炼铁在我国古代,炼铁技术经历了漫长的发展过程。
最初,人们采用土法炼铁,即用炉灶将铁矿石加热,使其还原成铁。
这种炼铁方法工艺简单,但效率低下,产量有限。
2. 烧结炼铁随着科技的进步,人们开始采用烧结炼铁技术。
烧结炼铁是将铁矿石与焦炭混合,通过高温烧结,使铁矿石还原成铁。
这种方法提高了炼铁效率,但烧结过程能耗较高,对环境造成一定影响。
3. 高炉炼铁20世纪以来,我国炼铁技术取得了重大突破。
高炉炼铁技术逐渐成为主流。
高炉炼铁是将烧结矿、焦炭和石灰石等原料送入高炉内,通过高温还原反应,将铁矿石还原成铁水。
这种方法具有生产效率高、能耗低、环境污染小等优点。
4. 现代炼铁技术近年来,我国炼铁技术不断向高效、低碳、环保方向发展。
如采用新型高炉、节能技术、富氧喷煤技术等,进一步提高炼铁效率,降低能耗和污染物排放。
二、炼铁技术的感悟与体会1. 技术创新是推动炼铁技术发展的关键炼铁技术的发展离不开技术创新。
从土法炼铁到现代炼铁,每一次技术革新都为炼铁行业带来了巨大的进步。
作为一名炼铁工作者,我们要紧跟时代步伐,不断学习新技术、新工艺,为炼铁行业的发展贡献自己的力量。
2. 节能减排是炼铁技术发展的必然趋势随着全球环境问题的日益严峻,节能减排成为炼铁技术发展的必然趋势。
我们要在提高炼铁效率的同时,注重降低能耗和污染物排放,为我国炼铁行业的可持续发展做出贡献。
3. 人才培养是炼铁技术发展的基石炼铁技术发展离不开人才的支撑。
我们要重视人才培养,提高炼铁工作者的综合素质,为炼铁行业输送更多优秀人才。
4. 团队协作是炼铁技术发展的保障炼铁技术涉及多个环节,需要各个部门、各个岗位的紧密协作。
我们要加强团队建设,提高团队凝聚力,确保炼铁技术顺利实施。
炼铁行业的技术创新与转型升级

美国阿勒格尼技术公司:利用AI技术优化生产流程,提高生产效率
韩国浦项制铁:采用环保技术,减少污染物排放
技术创新与转型升级的效益分析
提高生产效率:通过技术创新,提高生产效率,降低生产成本
减少环境污染:通过技术创新和转型升级,减少环境污染,实现绿色生产
提高企业效益:通过技术创新和转型升级,提高企业效益,增强企业竞争力
应用:智能控制系统、机器人技术、大数据分析、人工智能等
概念:利用先进的信息技术和自动化技术,实现炼铁过程的智能化、高效化和绿色化
特点:提高生产效率、降低能耗、减少污染、提高产品质量
前景:推动炼铁行业转型升级,提高竞争力,实现可持续发展
新型炉衬材料的应用
添加标题
添加标题
添加标题
添加标题
新型炉衬材料的特点:耐高温、耐腐蚀、耐磨损
炼铁行业技术创新与转型升级的实践与案例
6
国内典型企业实践
宝钢集团:引进先进技术,提高生产效率
首钢集团:推进绿色制造,降低环境污染
鞍钢集团:加强技术创新,开发新产品
沙钢集团:优化生产流程,提高产品质量
国际先进企业案例
德国蒂森克虏伯:采用高效节能技术,降低生产成本
日本新日铁:开发高强度钢,提高产品质量
加强与上下游企业的合作,实现产业链的智能化升级
炼铁行业的技术创新与转型升级的挑战与机遇
5
面临的挑战
环保压力:炼铁行业是高能耗、高污染的行业,需要应对越来越严格的环保法规和标准。
资源紧张:铁矿石等原材料价格波动较大,供应不稳定,需要应对资源紧张的挑战。
技术更新:炼铁行业的技术更新速度较快,需要不断更新技术和设备,以保持竞争力。
市场竞争:炼铁行业竞争激烈,需要应对竞争对手的压力,提高产品质量和降低成本。
炼铁行业碳排放分析与减排措施

制定低碳排放标准:根据炼铁行业的特点和需求,制定相应的低碳排放标准。
5
炼铁行业减排技术发展
低碳燃烧技术
原理:通过优化燃烧过程,降低碳排放
应用:广泛应用于钢铁、电力等行业
优点:减少碳排放,降低环境污染
挑战:需要不断改进技术,提高燃烧效率
碳捕获和储存技术
碳捕获技术:通过吸收、吸附、分离等方法,将二氧化碳从工业排放中分离出来
生产规模对碳排放的影响
生产规模越大,碳排放量越高
Байду номын сангаас
生产规模与碳排放量成正比关系
生产规模增加会导致能源消耗增加,从而增加碳排放
生产规模扩大会导致生产过程中的碳排放增加
4
炼铁行业减排措施
优化生产工艺,提高能效
采用先进的生产工艺和技术,如高炉富氧喷煤、烧结余热回收等,提高能源利用效率。
加强生产管理,提高设备运行效率,减少能源浪费。
炼铁行业是全球碳排放的主要来源之一
中国是全球最大的炼铁生产国,碳排放量占全球总排放量的60%以上
欧盟、美国、日本等发达国家的炼铁行业碳排放量相对较低,但近年来也在逐步增加
中国炼铁行业碳排放现状
炼铁行业碳排放主要来源
燃料燃烧:煤炭、焦炭等燃料在炼铁过程中的燃烧
能源消耗:电力、热力等能源在炼铁过程中的消耗和排放
2060年,中国炼铁行业碳排放量预计将减少80%
中国政府已经制定了一系列减排政策和措施,包括推广清洁能源、提高能源效率、发展循环经济等
炼铁行业减排技术创新与突破
碳捕集与封存技术:研究和应用碳捕集与封存技术,减少碳排放
绿色炼铁:推广使用可再生能源和清洁能源,减少对化石燃料的依赖
突破:实现炼铁过程零排放或接近零排放的目标
论高炉炼铁节能降耗及资源合理利用技术高永

论高炉炼铁节能降耗及资源合理利用技术高永发布时间:2021-10-24T08:28:54.827Z 来源:《基层建设》2021年第20期作者:高永[导读] 摘要:随着社会的日益发展对于各行各业都提出了更高的要求,也带来了更多的挑战。
承德建龙特殊钢有限公司河北承德 067200摘要:随着社会的日益发展对于各行各业都提出了更高的要求,也带来了更多的挑战。
钢铁企业面临不断缩小的利润空间,其发展形势较为严峻。
要想在激烈的竞争之中站稳脚跟,相应企业应当在进行高炉炼铁时采取合理的节能降耗措施,并对原有的高炉炼铁技术进行优化,这样才能够有效拓宽自身的发展空间。
本文就高炉炼铁节能降耗及资源合理利用相关技术的实际操作和优化策略展开了讨论,以期为钢铁行业的发展提供一些帮助。
关键词:高炉炼铁;节能降耗;资源合理利用一、铁焦技术铁焦技术最早出现于日本,发展至今其在实际应用中发挥了一定的作用,但与此同时此项技术发展在目前并未十分成熟。
此项技术主要是使用微黏结霉或非黏结煤等价格更低的结煤作为原料,再生产煤矿资源,并且这些结煤还可以与铁矿粉按照一定的比例混合,在其成为块状后进行干馏处理,从而能够得到三七成比例的铁焦。
最后还需要对其进行二次处理,然后才能得到较好的炼铁效果。
据相关研究和实践表明,此项技术能够使主焦煤和焦的使用量大幅减少,同时也说明了铁焦对于高炉炼铁过程中的反应速率的提高有着十分重要的作用,另外,这也说明了在高炉炼铁中铁焦含量即使达到百分之三十也不会对高炉炼铁质量产生较大的影响[1]。
二、高炉喷吹炼铁技术的具体操作方式(一)高炉喷吹生物质和木炭技术生物质可以算得上是高炉炼铁领域内的一种新型能源,属于有机物的一种。
而对于这种有机物,主要应用于热解行为。
其中,可在碳化温度下,不断减少二氧化碳的排放量。
相关学者在研究中发现,生物质与废塑料多应用于高炉炼铁多个工艺环节中,在这些环节中,企业并不需要使用过多的是人力、物力和财力。
高炉炼铁低碳化和智能化技术发展现状

高炉炼铁低碳化和智能化技术发展现状随着全球工业化的不断加速以及环境保护的日益重视,绿色低碳的生产方式已经成为了全球炼铁行业的发展趋势。
为了适应这一趋势,高炉炼铁低碳化和智能化技术正在不断发展,其中包括了炼铁工艺、设备、自动化控制等各个方面。
在本文中,我们将对高炉炼铁低碳化和智能化技术的发展现状进行分析和总结,为读者提供一份关于这一领域的全面了解。
炼铁是制造钢铁的重要工艺,而高炉是常见的炼铁设备。
高炉炼铁低碳化技术主要包括原料的优化利用、能源的节约利用以及尾气的处理等方面。
在原料的利用方面,一些新型的铁矿石还原工艺在不断研究和应用中,例如煤质还原法、气体还原法等,这些工艺大大减少了炼铁过程中的二氧化碳排放量。
一些新型的冶炼石灰石等辅料的研究也在不断进行。
在能源的利用方面,高炉炼铁过程中大量的余热被浪费,因此一些余热的回收利用工艺也在不断研究和应用中。
在尾气处理方面,一些新型的高炉炼铁尾气处理技术也在不断发展,例如炼铁风炉尾气的除尘脱硫。
这些技术的应用,大大减少了高炉炼铁过程中的碳排放和其他污染物排放,使得炼铁行业的环保水平得到了显著提高。
高炉炼铁智能化技术是近年来兴起的一个新兴领域,通过引入先进的自动化控制技术和信息化技术,实现了炼铁工艺的自动化、智能化和数字化。
在高炉炼铁过程中,很多操作都需要依赖于人工判断和控制,而这些操作的精准度和效率都无法与自动化系统相比。
引入智能化技术,可以大大提高炼铁的生产效率和产品质量。
目前,在高炉炼铁中,一些先进的自动化设备已经得到了应用,例如高炉喷吹控制技术、高炉温度控制系统等。
这些设备的应用,提升了炼铁生产线的自动化水平,减少了人为操作的失误和工艺参数的波动,最终提高了产品的质量和产量。
有一些企业也在不断研究和开发高炉炼铁的智能化管理系统,从生产计划、原料控制、设备监测等多个方面实现了炼铁过程的全面数字化管理。
面对全球气候变化的挑战,绿色低碳的生产方式已经成为了各行业的发展趋势,而炼铁行业作为能源消耗和碳排放较大的行业,更是需要加快推进低碳化技术的研发和应用。
高炉炼铁低碳化和智能化技术发展现状

高炉炼铁低碳化和智能化技术发展现状随着经济的发展和工业的需求,钢铁行业一直处于发展的高峰。
炼铁是钢铁制造的第一道工序,是钢铁行业的重要组成部分。
因此,炼铁技术的进步对钢铁行业的发展起着决定性作用。
高炉炼铁是目前最常用的炼铁方法,但高炉在炼铁过程中产生的 CO2 是温室气体的主要来源之一,对环境造成了巨大的影响。
因此,炼铁行业急需低碳化和智能化技术的进步,以达到国家的环保和可持续发展的要求。
低碳化技术是目前炼铁技术的重要发展方向。
当前低碳化技术的研究主要集中在两个方面:一是提高炼铁砂的质量,二是优化高炉操作以减少 CO2 的排放。
在提高炼铁砂质量方面,学者们通过深入研究矿石结构、晶体形貌、成分分析等方面,开发了一系列新型矿石。
同时,通过化学药剂的加入,改善了炼铁砂的质量,减少了高炉的碳消耗率。
在高炉操作方面,优化高炉内气体的流动,提高燃烧效率,减少CO2排放。
此外,运用先进技术和设备对高炉进行监控和控制,使炼铁过程更加准确和精确。
煤气发电和余热利用等技术也是减少CO2排放的有效手段。
煤气发电可以利用高炉内的余热,发电产生收益的同时减少了CO2的排放。
余热利用则可以在高炉炼铁过程中收集多余的热量,用于加热周边的设备或供暖,避免浪费。
智能化技术是炼铁行业发展的新趋势。
借助现代高科技手段,对传统炼铁技术进行升级,从而实现智能化生产。
目前,智能化技术在炼铁行业的应用主要包括以下几个方面:一、自动化控制系统的应用。
自动化控制系统通过传感器和计算机系统对高炉进行监测和控制,适时地预防和解决高炉内外的问题。
二、智能化测量系统的应用。
智能化测量系统利用高精度计算机技术,精确测量炼铁过程中的各种参数数据,实现数据采集、处理、存储和传输。
三、机器人装备的应用。
机器人装备可以取代人力进行复杂或危险的工作,提高工作效率和安全性。
四、大数据和人工智能的应用。
大数据和人工智能技术结合炼铁制造的复杂特性,可以实现数据分析和预测、决策优化等功能。
高炉炼铁工艺节能减排技术探究

高炉炼铁工艺节能减排技术探究摘要:据统计数据表明:2020年,我国的粗钢产量达到10.65亿t,其中生铁产量为88752.4万t,钢铁产量与消费量均位列世界首位。
而在这利好形势的背后,不得不看到,钢铁行业作为能源消耗密集型行业,节约能源与减少碳排放已经成为当下亟需面对与解决的问题。
降低能源消耗、减少碳排放、保护自然生态环境是钢铁企业健康可持续发展的坚实保障,因此,在进入21世纪后,我国的钢铁生产企业在完成经济效益指标的同时,也将社会效益与生态效益纳入到企业的长远发展规划当中,不断对高炉炼铁工艺的节能减排技术进行创新与优化,并取得了良好的实际应用效果。
关键词:高炉;炼铁工艺;节能减排技术引言近年来,随着社会经济和工业部门的迅速发展,全球环境污染问题日益严重,减少二氧化碳排放一直是全球环境治理的优先事项。
目前,我们每年的粗铁产量是世界上最高的,但它在生产过程中产生更多的二氧化碳,造成更严重的污染和环境损害。
在节能、减排和环境保护概念的推动下,钢铁工业还开始致力于优化高速铁的创新工艺,积极应用减排和节能技术,以有效降低发展现状,由于钢铁企业分布相对分散,运营设备落后,节能、环保和技术概念应用不完善,高铁精炼过程尚未达到国家对污染物排放的要求。
因此,深入研究和积极探索高铁炼制过程中节能减排技术的应用措施,对于改善区域环境、提高高铁炼制的经济效益和促进高铁的可持续发展具有重要作用。
1高炉炼铁工艺流程高炉炼铁工艺技法简单、生产效率高、生产量大、能源消耗量低,在钢铁生产领域被普遍推广使用。
其生产工艺流程为:首先将焦炭、矿石、烧结矿、球团矿等生产原料经过粉碎处理后,由皮带运输机直接运送至高炉料仓当中,并经过筛分与计量后输送至加热炉内;然后由高炉的下风口鼓入热风,使高炉内各种原料中的碳元素与热风发生燃烧反应,继而产生大量的一氧化碳与氢气等还原性气体;当高炉内的温度上升到一定区间范围后,高炉内的矿石将与还原性气体发生还原反应,这时矿石中的铁被还原出来;再经过熔化与渗碳工序,便形成铁水。
钢铁行业如何推动绿色低碳发展和节能减排

钢铁行业如何推动绿色低碳发展和节能减排在全球气候变化的大背景下,绿色低碳发展和节能减排已成为各行各业的重要任务,钢铁行业也不例外。
钢铁行业作为能源消耗和碳排放的大户,其绿色转型对于实现全球可持续发展目标具有关键意义。
那么,钢铁行业该如何推动绿色低碳发展和节能减排呢?首先,技术创新是关键。
钢铁生产过程中,能源消耗和污染物排放主要集中在炼铁、炼钢等环节。
通过研发和应用先进的技术,可以有效降低能耗和排放。
例如,采用新型的炼铁技术,如富氧喷煤、高炉煤气余压透平发电等,可以提高能源利用效率,减少煤炭消耗。
在炼钢环节,推广转炉负能炼钢、电炉炼钢等技术,能够降低电能消耗和废气排放。
同时,余热余能回收利用技术的应用也至关重要。
钢铁生产过程中会产生大量的余热余能,如高温炉渣、高温废气等。
通过余热锅炉、余热发电等技术,将这些余热余能回收利用,不仅可以减少能源浪费,还能为企业创造经济效益。
此外,新型的节能设备和节能工艺的研发与应用,如高效电机、变频调速技术等,也能为钢铁行业的节能减排提供有力支持。
优化能源结构也是推动钢铁行业绿色发展的重要途径。
目前,钢铁行业的能源消耗仍以煤炭为主,而煤炭的燃烧是碳排放的主要来源之一。
因此,逐步提高清洁能源在钢铁生产中的比例,如加大天然气、太阳能、风能等清洁能源的使用,能够有效降低碳排放。
同时,积极探索氢能在钢铁生产中的应用,如氢能炼铁等,也是未来钢铁行业能源结构转型的一个重要方向。
加强能源管理同样不可或缺。
钢铁企业应建立完善的能源管理体系,对能源的购入、存储、使用等环节进行全面监测和管理。
通过能源审计、能效对标等手段,发现能源利用中的问题和潜力,制定针对性的节能措施,并严格落实执行。
此外,加强员工的节能意识培训,提高全员参与节能的积极性和主动性,也是推动能源管理工作的重要保障。
在生产流程方面,钢铁企业可以通过优化生产组织和工艺路线,实现节能减排。
例如,合理安排生产计划,减少设备的频繁启停和空转,提高生产效率;采用连续化、紧凑化的生产工艺,减少中间环节的能源消耗和物料损失。
钢铁行业的节能减排实现低碳和环保的可行方案

钢铁行业的节能减排实现低碳和环保的可行方案钢铁行业是工业领域中能源消耗和碳排放最高的行业之一。
在当前全球环境问题日益严峻的背景下,实施节能减排并推动低碳和环保发展已成为钢铁行业的当务之急。
本文将针对钢铁行业的特点和挑战,提出一些可行的节能减排方案。
一、技术创新与升级技术创新是实现钢铁行业节能减排的关键。
通过引入先进的生产技术和设备,钢铁企业可以减少能源消耗和排放物的产生。
例如,采用高效炼钢技术和新型冶炼炉,可以大幅提高冶炼效率,减少碳排放。
此外,利用废气和废热发电,实现能源的再利用和回收,也能有效降低能源消耗。
二、能源结构优化钢铁行业在生产过程中主要依赖高耗能的煤炭和焦炭。
因此,优化能源结构对于实现节能减排至关重要。
钢铁企业可以考虑使用清洁能源替代传统燃料,如采用天然气、生物质能源以及太阳能和风能等可再生能源。
此外,鼓励能源综合利用和能源互联网建设,促进不同领域之间的能源共享和优化利用,也是一种有效的节能减排方案。
三、资源循环利用与废弃物处理在传统冶炼过程中,存在大量废水、废气和固体废弃物的排放。
要实现低碳和环保发展,钢铁企业需要加强废弃物处理和资源循环利用。
通过建设废弃物处理设施,并采用先进的废弃物处理技术,可以将废弃物转化为资源,减少对自然资源的依赖。
同时,钢铁企业还应该优化生产工艺,减少原材料的消耗,提高资源利用效率。
四、绿色供应链建设钢铁行业的供应链管理对于实现节能减排和环保发展至关重要。
通过建立绿色供应链,钢铁企业可以减少能源和物资浪费。
在供应商选择过程中,优先选择环保产品和服务提供商,建立合作伙伴关系,并共同推动绿色生产和消费。
此外,加强供应链信息化建设,实现信息共享和及时响应,也能提高整体效率和减排效果。
五、政策支持和行业合作政府的政策支持和行业间的合作对于钢铁行业实现低碳和环保发展至关重要。
政府可以出台相关法规和政策,鼓励企业节能减排和技术创新。
同时,行业协会和企业之间需要加强合作,共同开展技术研发、经验分享和示范项目,形成可持续发展的良好氛围。
高炉炼铁工艺节能减排技术探究
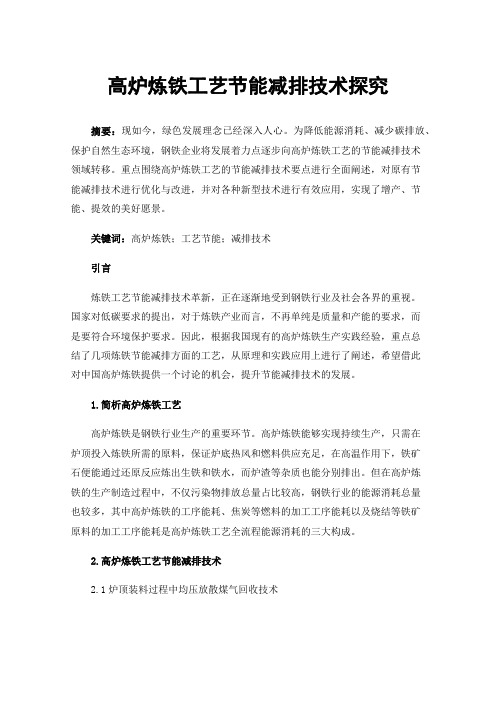
高炉炼铁工艺节能减排技术探究摘要:现如今,绿色发展理念已经深入人心。
为降低能源消耗、减少碳排放、保护自然生态环境,钢铁企业将发展着力点逐步向高炉炼铁工艺的节能减排技术领域转移。
重点围绕高炉炼铁工艺的节能减排技术要点进行全面阐述,对原有节能减排技术进行优化与改进,并对各种新型技术进行有效应用,实现了增产、节能、提效的美好愿景。
关键词:高炉炼铁;工艺节能;减排技术引言炼铁工艺节能减排技术革新,正在逐渐地受到钢铁行业及社会各界的重视。
国家对低碳要求的提出,对于炼铁产业而言,不再单纯是质量和产能的要求,而是要符合环境保护要求。
因此,根据我国现有的高炉炼铁生产实践经验,重点总结了几项炼铁节能减排方面的工艺,从原理和实践应用上进行了阐述,希望借此对中国高炉炼铁提供一个讨论的机会,提升节能减排技术的发展。
1.简析高炉炼铁工艺高炉炼铁是钢铁行业生产的重要环节。
高炉炼铁能够实现持续生产,只需在炉顶投入炼铁所需的原料,保证炉底热风和燃料供应充足,在高温作用下,铁矿石便能通过还原反应炼出生铁和铁水,而炉渣等杂质也能分别排出。
但在高炉炼铁的生产制造过程中,不仅污染物排放总量占比较高,钢铁行业的能源消耗总量也较多,其中高炉炼铁的工序能耗、焦炭等燃料的加工工序能耗以及烧结等铁矿原料的加工工序能耗是高炉炼铁工艺全流程能源消耗的三大构成。
2.高炉炼铁工艺节能减排技术2.1炉顶装料过程中均压放散煤气回收技术高炉是高温高压的冶炼容器,整个炼铁的过程中,都要不断地从炉顶进行原矿和焦炭的加入。
一般来说,加入过程是在常温常压下进行,由传统传料胶带机或者运料车提升到炉顶直接进行原料的加入。
加入炉内的过程,需要装料罐有一个泄压的过程,装料进入后再进行冲压,将原料装入炉内。
泄压过程中,会存在高炉中煤气放散至空气中的情况。
这部分煤气富含毒性和灰尘,直接排放会造成较大的污染,并且排放煤气中具有一定热量热值的二次能源,也造成了一定的能源浪费。
为了进行能源的回收利用以及保证污染排放的杜绝,因此开发出一个处理回收工艺和设备:炉顶装料过程中均压放散煤气回收技术[1]。
高炉炼铁低碳化和智能化技术发展现状

高炉炼铁低碳化和智能化技术发展现状高炉炼铁是目前主要的铁制品生产方法,其低碳化和智能化技术发展正成为行业发展的关键。
随着全球环境保护意识的提升和清洁能源的推广,炼铁行业正不断加大对低碳化和智能化技术的研究和应用,以实现可持续发展。
本文将结合当前的技术发展现状,探讨高炉炼铁低碳化和智能化技术的发展趋势和前景。
1. 绿色能源应用高炉炼铁工艺中最常用的还是焦炭作为还原剂和燃料,然而焦炭的生产和使用过程会产生大量的二氧化碳和其他有害气体。
为了减少炼铁工艺对环境的影响,绿色能源的应用成为当前的主要趋势。
生物质能、天然气等替代燃料的应用得到了广泛研究和推广,能够有效减少炼铁工艺的碳排放。
2. 炼铁炉改进针对传统高炉炼铁过程中的碳排放问题,一些国家和企业正在投入大量资金进行炼铁炉改进研究。
其中包括了高炉炼铁技术改进,通过提高高炉的技术水平和效率,减少炼铁过程中的排放。
一些新型的低碳炼铁炉技术也在不断涌现,这些炉型不仅能够降低炼铁成本,还可以减少排放。
3. 脱碳技术研究为了改善炼铁过程中的碳排放问题,一些企业正在研究开发新的脱碳技术。
通过在高炉炉料中添加适当量的钢渣或其他脱碳剂,可以有效降低碳排放。
利用先进的碳捕集技术,也能够帮助企业在炼铁过程中更好地控制碳排放。
1. 自动化生产设备随着科技的发展,高炉炼铁行业也开始逐渐向智能化和自动化方向发展。
目前,一些世界知名的炼铁企业已经引入了自动控制系统、智能化生产设备,实现了生产的自动化和智能化。
通过这些设备,可以实现对炼铁生产过程的全面监控和实时调节,提高生产效率和产品质量。
2. 大数据应用智能化技术在高炉炼铁行业中的应用不仅体现在生产设备上,还包括了对大数据的应用。
通过对生产过程中产生的大量数据进行收集和分析,企业可以更好地理解炼铁生产的规律和特点,进而优化生产过程和提高生产效率。
3. 智能化管理系统除了生产过程的智能化,高炉炼铁行业还在不断推进智能化管理系统的建设。
低碳炼铁 节能减排 实现清洁生产

表 1 合金烘烤前后 出钢温 降统计情况
钢铁行业的节能减排技术了解如何应用节能减排技术提升钢铁生产效率

钢铁行业的节能减排技术了解如何应用节能减排技术提升钢铁生产效率为了应对全球气候变化和环境保护的需求,各行各业都在积极推动节能减排技术的应用,而钢铁行业作为高能耗、高排放的重工业也不例外。
本文将讨论钢铁行业中的节能减排技术,并阐述如何通过应用这些技术来提升钢铁生产效率。
一、炼铁工艺中的节能减排技术1. 高炉煤气回收利用技术在传统炼铁过程中,炉排出的煤气往往直接排放,造成了能源的浪费和环境污染。
而采用高炉煤气回收利用技术,可以将煤气中的有价值组分回收利用,用于发电或热能回收,降低能源消耗,同时减少二氧化碳等污染物的排放。
2. 废热回收利用技术钢铁生产中会产生大量的废热,如果不进行有效的利用,不仅会浪费能源,还会对环境造成负面影响。
采用废热回收利用技术,可以将废热转换成电能或者用于提供热水、供暖等方面,从而实现能源的再利用和节约。
二、钢铁生产过程中的节能减排技术1. 高效燃烧技术在钢铁生产过程中,燃烧是不可避免的环节,但传统的燃烧方式存在能量利用率低、污染物排放高等问题。
使用高效燃烧技术,如喷煤、高温燃烧等,可以提高燃烧效率,减少能源消耗,同时也减少了污染物的产生。
2. 脱硫脱硝技术钢铁生产中常常伴随着废气中的硫化物和氮氧化物排放,对环境造成了严重影响。
脱硫脱硝技术的应用,可以有效地降低废气中的硫化物和氮氧化物含量,减少对大气造成的污染,保护环境。
三、节能减排技术对钢铁生产效率的提升1. 能源利用效率的提高通过采用上述节能减排技术,钢铁企业可以提高能源利用效率,充分利用废气、废热等资源,实现能源的循环利用。
这不仅减少了能源的消耗和成本,还提高了钢铁生产的经济效益。
2. 生产质量的提升节能减排技术的应用使得钢铁行业能够更加环保,降低了废气和废水的排放,减少了对环境的污染。
这不仅有利于企业树立良好的形象,增强市场竞争力,还有助于提升产品的质量和附加值。
3. 资源的可持续利用传统的钢铁生产方式往往会浪费大量的资源,而节能减排技术的应用可以使得资源得到更加合理的利用。
钢铁生产中的节能减排方案

钢铁生产中的节能减排方案
钢铁生产是一个能耗较高、排放量较大的行业,因此在开展生产过程中采取节
能减排方案显得尤为重要。
以下是一些针对钢铁生产中节能减排的方案:
1. 提高焦炉煤气利用率:焦炉煤气是钢铁生产中的副产品,通过采用余热锅炉
等设备,可以将焦炉煤气中的热能回收利用,提高能源利用率,降低能耗。
2. 使用先进的高炉炉料预处理技术:通过对高炉炉料的预处理,可以提高炉石、焦炭和铁矿石的利用率,降低能耗和排放量。
3. 采用先进的炼钢技术:利用先进的炼钢技术,如转炉炼钢、电炉炼钢等,可
以降低原料、能耗和排放量,提高钢铁生产的效率和品质。
4. 推广能源替代技术:在钢铁生产中推广使用煤气发电、焦炉余热发电等能源
替代技术,减少对传统煤炭等能源的依赖,降低碳排放。
5. 完善废气处理系统:加强对钢铁生产过程中废气的处理,采用先进的除尘、
脱硫、脱硝等设备,降低废气的排放浓度,保护环境。
6. 提倡循环经济理念:建立钢铁生产的循环经济体系,促进废渣、废水等资源
的再利用,减少资源浪费和环境污染。
在实施上述节能减排方案的同时,企业应加强管理,建立科学的能源管理体系、环境管理体系,制定详细的节能减排计划,鼓励员工参与节能减排工作,形成全员参与的节能减排氛围。
同时,政府应出台相应政策,加大对节能减排技术研究和推广的支持力度,引导钢铁生产企业朝着绿色、低碳、可持续发展的方向前进。
总的来说,钢铁生产中的节能减排方案有着重要的意义,是企业应尽的社会责任,也是实现可持续发展的必由之路。
通过不断改进技术、管理和政策的手段,钢铁生产行业可以实现更环保、更高效的生产模式,为建设美丽中国作出贡献。
- 1、下载文档前请自行甄别文档内容的完整性,平台不提供额外的编辑、内容补充、找答案等附加服务。
- 2、"仅部分预览"的文档,不可在线预览部分如存在完整性等问题,可反馈申请退款(可完整预览的文档不适用该条件!)。
- 3、如文档侵犯您的权益,请联系客服反馈,我们会尽快为您处理(人工客服工作时间:9:00-18:30)。
Abstract: In this paper, an o ver view of blast furnace iro nmaking in China and t echnolo g ical prog ress in f ields o f en er gy sav ing, high blast temper ature, larg e scale equipment etc. ar e int roduced. Subsequent ly , scient ific dev elo p ment concept of iro nmaking technolog ies is deeply ex po sited. T he contents include: strengt hen adjustment of iron making industrial structure, chang e development mo del and change concepts. O n the base of hig h g rade burden, ai ming at lo w car bo n ironmaking, seek pro per smelting intensity, rat ional o xy gen enr ichment and P CI , increase blast temper atur e and decr ease coke r ate. Impro ve gas distributio n and energ y ut ilization, lo wer ing all ty pes of ener gy co nsumpt ion invo lv ing blast and po wer et c. Decr ease emissio n and str eng then innocuo us tr eat ment. T hus some new br eakthr ough in the aspects of low co nsumption, high efficiency, high quality , long campaig n life and environment pr otectio n ar e achiev ed. M eanw hile, r eso lute measures sho uld be taken to r ectify the disor der in ir onmaking pr oduc tion and prohibit backwar d pr oductio n capacity retur n o r co nt inue pr oducing. T o sum up, energ y saving , em ission reductio n and low carbon ironmaking are t he centr al steps of realizing scientif ic dev elo pment o f blast fur nace iron making in China. Key words: energ y sav ing and emissio n reducing; lo w car bo n ironmaking; scientific dev elo pment
1. 910 57. 35 1 127 83. 39 6. 84 13. 11
2. 106 57. 32 1 133 83. 12 6. 84 13. 03 0. 74 1. 661 57. 62 1 158 84. 02 6. 83 12. 50 0. 71
炼铁工序 能耗/
( kg t - 1) 426. 84 426. 58
2 高炉炼铁技术的主要进展
2. 1 节能降耗 由 表1看出, 2009 年的燃料比较2007年下降
作者简介: 杨天钧( 1943 ) , 男, 博士, 教授; E mail: yangt j@ ust b edu cn; 收稿日期: 2010 05 28
2
中国冶金
第 20 卷
表 1 2007- 2009 年重点统计钢铁企业高炉炼铁技术经济指标
145
5ቤተ መጻሕፍቲ ባይዱ9
注: 燃料比中尚未包括小块焦比
2. 677 2. 563
2. 616
2. 599
2. 607 2. 615
1. 524 57. 71 1 125 83. 16 6. 75 12. 52 0. 68 1. 838 57. 50 1 085 83. 54 6. 80 12. 73
1. 616 57. 30 1 127 83. 45 6. 84 12. 80
Energy Saving, Emission Reducing and Low Carbon Ironmaking, Realizing Scientific Development of BF Production in China
YAN G T ian jun, ZH ANG Jian liang, ZUO H ai bin
辽宁 4 782. 98 4 742. 38 内蒙古 1 261. 94 1 381. 29
山西 2 648. 49 3 127. 45
广东 1 126. 57 755. 86
河南 2 328. 99 1 944. 63
浙江 1 045. 64 535. 96
天津 2 124. 20 1 763. 40
近年来新建的 50 余座大于 1 000 m3 高炉, 风温均有 达到 1200 ! 以上的能力。尤其是 2009 年投产的首 钢曹 妃 甸 5500 m3 高 炉 的 风 温 达 到 了 1 280 ~ 1 300 ! 的水平, 这是中国高风 温技术的巨大进步。 当然更应看到大部分高炉的风温水平, 特别是中小 高炉大多低于平均水平, 其热风炉设备简陋, 耐火砖 和施工质量较差, 尚不具备高风温的能力, 有的甚至 在 1 000 ! 以下风温徘徊, 而且热风炉寿命也只有 5 ~ 8 年。这需要企业转变观念, 淘汰落后, 改进热风 炉系统及其结构, 选用优质耐火材料, 采用先进换热 技术, 使热风炉寿命达到 15~ 30 年, 烧单一高炉煤 气、稳定达到风温 1 200 ! 甚至更高的水平。 2. 3 装备大型化与技术进步
430. 52
429. 49
427. 72 410. 65
表 2 2009 年中国粗钢/ 生铁产量 1 000 万 t 以上的省市
Table 2 Province and city of steel/ iron production over 10 million tons in China in 2009
Table 1 The Main technical indexes of BF for Chinese focusing steelworks f rom 2007 to 2009
年度
产量/ 焦比/
煤比/ 燃料比/ 利用系数/ 休风率/ 品位/
万 t ( kg t - 1 ) ( kg t - 1 ) ( kg t - 1) ( t m- 3 d- 1 ) %
云南 1 049. 05 1 280. 85
上海 2 032. 24 1 787. 48
广西 1 000. 91 967. 72
万t 湖北 1 985. 30 1 956. 70
10 kg / t , 较 2008 年下降 13kg/ t, 达到 519 kg/ t 。这 主要由于焦炭质量略有改善, 入炉品位略有上升, 风 温水平有所提高等造成焦比有所降低, 许多企业正 朝着这个方向继续努力。据统计, 中国重点钢铁企 业燃料比低于 500 kg / t 的有: 新冶钢( 467kg/ t ) , 首 钢( 468 kg/ t ) , 宝钢( 472kg/ t ) , 马钢 ( 484 kg / t ) , 太 钢( 490 kg/ t ) , 武钢( 498kg/ t ) , 沙钢 ( 498 kg / t ) , 邯 钢( 499 kg / t ) , 鞍钢、本钢、湘钢( 500 kg/ t ) 等 11 家, 已经步入世界先进行列。此外, 有 24 家企业燃料比 下降幅度较大, 达到了 20 kg/ t 以上, 有的甚至超过 60 kg / t , 取得可喜的进步。
%
风温/ !
焦炭性能/ % M 40 M 10 灰分 硫
2007 47 141 392
137
529
2008 11 780 401
131
532
一季度
2008 24 642 398
134
532
上半年
2008 36 673 398
135
532
前 3 季度
2008 47 067 396
136
532
2009 57 375 374
由于高炉工序能耗占钢铁生产总能耗的 50% 以上, 2009 年高炉炼铁燃料比的降低, 使吨 铁工序 能耗降到 410 65 kg/ t, 为中国吨钢综合能耗降低做 出了贡献。 2. 2 风温提高
2009 年 全国 重 点 企 业 风温 达 到 1 158 ! , 较 2008 年提高了 25 ! , 统计资料表明有 51 个单位的 热风温度得到了提高, 占企业总数的 70 83% , 风温 高于平均水平的有太钢( 1 216 ! ) 、宝钢( 1 206 ! ) 、 首钢( 1 196 ! ) 、攀钢( 1195 ! ) 、鞍钢( 1 186 ! ) 、福 建 三 明 ( 1184 ! ) 、长 治 ( 1 173 ! ) 、新 兴 铸 管 ( 1 165 ! ) 、唐钢( 1 164 ! ) 、建龙( 1159 ! ) 等 10 家。