数控切削速度计算公式
铣刀转速和进给公式

铣刀转速和进给公式铣刀转速和进给是数控铣床加工中的重要参数,对于加工质量和效率起着至关重要的作用。
本文将对铣刀转速和进给进行详细介绍,并给出相应的计算公式。
一、铣刀转速铣刀转速是指铣刀在加工过程中每分钟旋转的圈数,通常用单位时间内的转数来表示,单位为转/分钟(rpm)。
铣刀转速的选择直接影响到加工表面的质量、切削刃的寿命以及加工效率。
铣刀转速的选择应根据材料的硬度、刀具材料和刀具直径来确定。
一般来说,硬度较高的材料需要较低的转速,而硬度较低的材料需要较高的转速。
刀具材料的选择也会影响到转速的确定,不同材料的刀具具有不同的切削性能,因此需要根据刀具材料来选择合适的转速。
此外,刀具直径也会对转速的选择产生影响,直径较大的刀具需要较低的转速,而直径较小的刀具则需要较高的转速。
铣刀转速的计算公式如下:n = (1000 × v) / (π × d)其中,n为转速(转/分钟),v为切削速度(m/min),d为刀具直径(mm)。
二、进给进给是指铣刀在单位时间内移动的距离,通常用毫米/转(mm/rev)来表示。
进给的选择直接影响到加工的精度和效率。
进给的选择应根据材料的硬度、切削性能和加工要求来确定。
一般来说,硬度较高的材料需要较小的进给,而硬度较低的材料则可以选择较大的进给。
切削性能也会对进给的选择产生影响,切削性能好的材料可以选择较大的进给,而切削性能差的材料则需要选择较小的进给。
此外,加工的要求也会对进给的选择产生影响,如果对加工精度要求高,则需要选择较小的进给。
进给的计算公式如下:f = n × z其中,f为进给(mm/rev),n为转速(转/分钟),z为每分钟切削齿数(个/分钟)。
三、铣刀转速和进给的关系铣刀转速和进给是密切相关的,它们之间的关系可以通过切削速度来体现。
切削速度是指切削刀具上每分钟切削齿数所移动的距离,通常用米/分钟(m/min)来表示。
切削速度的计算公式如下:v = π × d × n / 1000其中,v为切削速度(m/min),d为刀具直径(mm),n为转速(转/分钟)。
加工中心切削转速和进给速度计算方法及公式
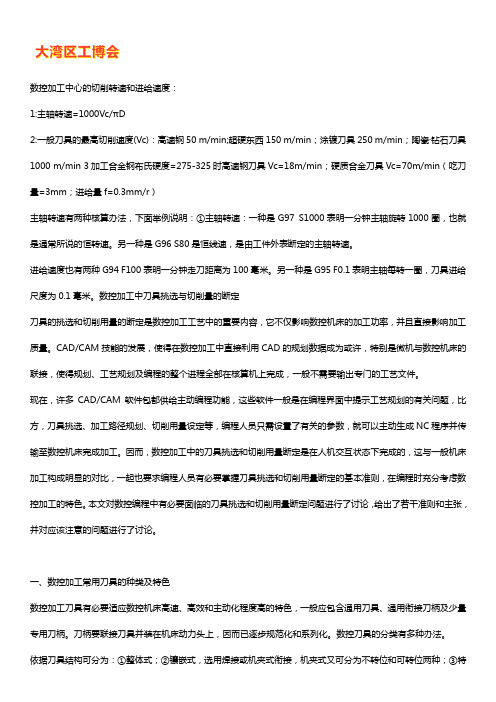
数控加工中心的切削转速和进给速度:1:主轴转速=1000Vc/πD2:一般刀具的最高切削速度(Vc):高速钢50 m/min;超硬东西150 m/min;涂镀刀具250 m/min;陶瓷·钻石刀具1000 m/min 3加工合金钢布氏硬度=275-325时高速钢刀具Vc=18m/min;硬质合金刀具Vc=70m/min(吃刀量=3mm;进给量f=0.3mm/r)主轴转速有两种核算办法,下面举例说明:①主轴转速:一种是G97 S1000表明一分钟主轴旋转1000圈,也就是通常所说的恒转速。
另一种是G96 S80是恒线速,是由工件外表断定的主轴转速。
进给速度也有两种G94 F100表明一分钟走刀距离为100毫米。
另一种是G95 F0.1表明主轴每转一圈,刀具进给尺度为0.1毫米。
数控加工中刀具挑选与切削量的断定刀具的挑选和切削用量的断定是数控加工工艺中的重要内容,它不仅影响数控机床的加工功率,并且直接影响加工质量。
CAD/CAM技能的发展,使得在数控加工中直接利用CAD的规划数据成为或许,特别是微机与数控机床的联接,使得规划、工艺规划及编程的整个进程全部在核算机上完成,一般不需要输出专门的工艺文件。
现在,许多CAD/CAM软件包都供给主动编程功能,这些软件一般是在编程界面中提示工艺规划的有关问题,比方,刀具挑选、加工路径规划、切削用量设定等,编程人员只需设置了有关的参数,就可以主动生成NC程序并传输至数控机床完成加工。
因而,数控加工中的刀具挑选和切削用量断定是在人机交互状态下完成的,这与一般机床加工构成明显的对比,一起也要求编程人员有必要掌握刀具挑选和切削用量断定的基本准则,在编程时充分考虑数控加工的特色。
本文对数控编程中有必要面临的刀具挑选和切削用量断定问题进行了讨论,给出了若干准则和主张,并对应该注意的问题进行了讨论。
一、数控加工常用刀具的种类及特色数控加工刀具有必要适应数控机床高速、高效和主动化程度高的特色,一般应包含通用刀具、通用衔接刀柄及少量专用刀柄。
数控机床线速度计算公式

数控机床线速度计算公式摘要:一、引言二、数控机床线速度的概念三、数控机床线速度的计算公式四、计算公式中的参数说明五、注意事项六、总结正文:一、引言数控机床是一种高精度的机械加工设备,它能够实现自动化生产和加工,提高生产效率和产品质量。
在数控机床的加工过程中,线速度是一个重要的参数,它直接影响到加工效果和刀具的寿命。
因此,了解数控机床线速度的计算公式是非常必要的。
二、数控机床线速度的概念数控机床线速度是指刀具在单位时间内沿着刀具路径移动的线段长度,通常用米/分钟表示。
线速度是刀具切削速度的一个重要组成部分,它决定了刀具在切削过程中的切削效果和切削力。
三、数控机床线速度的计算公式数控机床线速度的计算公式为:线速度= 圆周率× 刀具直径× 主轴转速÷ 1000其中,圆周率(π)取3.14,刀具直径(d)是指刀具的实际直径,主轴转速(n)是指数控机床主轴的转速。
四、计算公式中的参数说明1.圆周率(π):圆周率是一个无理数,约等于3.14,它在数学中有广泛的应用。
2.刀具直径(d):刀具直径是指刀具的实际直径,通常根据加工工艺和刀具材料来选择。
3.主轴转速(n):主轴转速是指数控机床主轴的转速,它是数控机床加工过程中的一个重要参数。
五、注意事项1.在计算线速度时,要注意刀具直径和主轴转速的选择,它们会影响到线速度的计算结果。
2.在实际加工过程中,要注意线速度的选择,不同的加工工艺和刀具材料需要选择不同的线速度。
3.在计算线速度时,要考虑到刀具的耐用度和加工效率,选择合适的线速度可以提高刀具的寿命和加工效率。
六、总结数控机床线速度的计算公式为线速度= 圆周率× 刀具直径× 主轴转速÷ 1000,它是数控机床加工过程中的一个重要参数。
切削速度,吃刀量,吃刀量的选择原则与计算

数控编程时,编程人员必须确定每道工序的切削用量,并以指令的形式写入程序中。
切削用量包括切削速度、背吃刀量及进给速度等。
对于不同的加工方法,需要选用不同的切削用量。
1、刀具切削用量的选择原则粗加工时,一般以提高生产率为主,但也应考虑经济性和加工成本;半精加工和精加工时,应在保证加工质量的前提下,兼顾切削效率、经济性和加工成本。
具体数值应根据机床说明书、切削用量手册,并结合经验而定。
从刀具的耐用度出发,切削用量的选择顺序是:先确定背吃刀量,其次确定进给量,最后确定切削速度。
2、吃刀量的确定背吃刀量由机床、工件和刀具的刚度来决定,在刚度允许的条件下,应尽可能使背吃刀量等于工件的加工余量,这样可以减少走刀次数,提高生产效率。
确定背吃刀量的原则:(1)在工件表面粗糙度值要求为Ra12.5μm~25μm时,如果数控加工的加工余量小于5mm~6mm,粗加工一次进给就可以达到要求。
但在余量较大,工艺系统刚性较差或机床动力不足时,可分多次进给完成。
(2)在工件表面粗糙度值要求为Ra3.2μm~12.5μm时,可分粗加工和半精加工两步进行。
粗加工时的背吃刀量选取同前。
粗加工后留0.5mm~1.0mm余量,在半精加工时切除。
(3)在工件表面粗糙度值要求为Ra0.8μm~3.2μm时,可分粗加工、半精加工、精加工三步进行。
半精加工时的背吃刀量取1.5mm~2mm。
精加工时背吃刀量取0.3mm~0.5mm。
3、刀具进给量的确定进给量主要根据零件的加工精度和表面粗糙度要求以及刀具、工件的材料选取。
最大进给速度受机床刚度和进给系统的性能限制。
确定进给速度的原则:1)当工件的质量要求能够得到保证时,为提高生产效率,可选择较高的进给速度。
一般在100~200m/min范围内选取。
2)在切断、加工深孔或用高速钢刀具加工时,宜选择较低的进给速度,一般在20~50m/min范围内选取。
3)当加工精度,表面粗糙度要求高时,进给速度应选小些,一般在20~50m/min 范围内选取。
数控机床线速度计算公式(一)

数控机床线速度计算公式(一)
数控机床线速度计算公式
什么是数控机床线速度?
数控机床线速度,简称为线速度,是指工件或切削工具在数控机床上的运动速度。
它是数控机床加工过程中一个重要的参数,常用于计算切削速度、进给速度和主轴转速等关键数据。
线速度计算公式
根据数控机床的运动原理,线速度一般可以使用以下公式计算:线速度(v)= π * 直径(d) * 主轴转速(n)
其中,v表示线速度,d表示直径,n表示主轴转速。
根据实际情况,可以使用该公式进行计算。
举例说明
假设数控机床主轴转速为500转/分钟,直径为50毫米,我们可以通过上述公式计算出线速度。
线速度(v)= π * 50 * 500 = 毫米/分钟。
这意味着在该情况下,工件或切削工具在数控机床上的线速度为毫米/分钟。
需要注意的是,该公式仅适用于计算数控机床上的线速度,对于其他情况可能不适用。
总结
数控机床线速度是数控加工过程中的重要参数,通过计算公式可以得到准确的线速度数值。
在实际应用中,需要根据具体的机床参数进行计算,并对线速度进行合理调整,以确保加工效率和产品质量。
参考文献: - [数控机床基本知识]( - [数控机床操作手册](。
数控加工切削参数计算公式
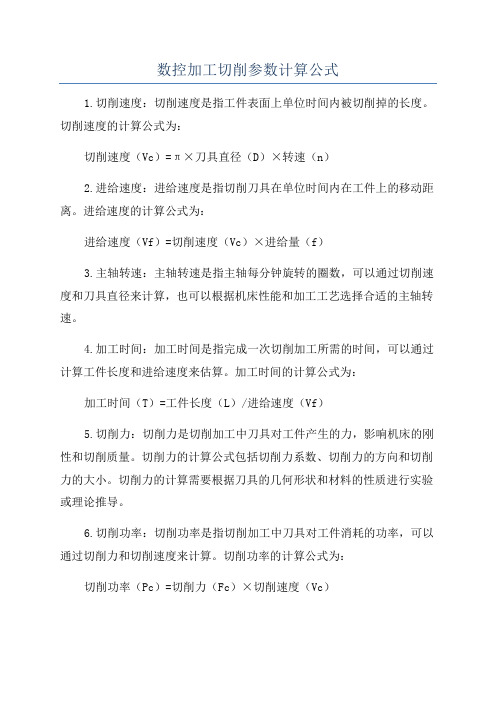
数控加工切削参数计算公式
1.切削速度:切削速度是指工件表面上单位时间内被切削掉的长度。
切削速度的计算公式为:
切削速度(Vc)=π×刀具直径(D)×转速(n)
2.进给速度:进给速度是指切削刀具在单位时间内在工件上的移动距离。
进给速度的计算公式为:
进给速度(Vf)=切削速度(Vc)×进给量(f)
3.主轴转速:主轴转速是指主轴每分钟旋转的圈数,可以通过切削速度和刀具直径来计算,也可以根据机床性能和加工工艺选择合适的主轴转速。
4.加工时间:加工时间是指完成一次切削加工所需的时间,可以通过计算工件长度和进给速度来估算。
加工时间的计算公式为:
加工时间(T)=工件长度(L)/进给速度(Vf)
5.切削力:切削力是切削加工中刀具对工件产生的力,影响机床的刚性和切削质量。
切削力的计算公式包括切削力系数、切削力的方向和切削力的大小。
切削力的计算需要根据刀具的几何形状和材料的性质进行实验或理论推导。
6.切削功率:切削功率是指切削加工中刀具对工件消耗的功率,可以通过切削力和切削速度来计算。
切削功率的计算公式为:
切削功率(Pc)=切削力(Fc)×切削速度(Vc)。
车床工时计算法
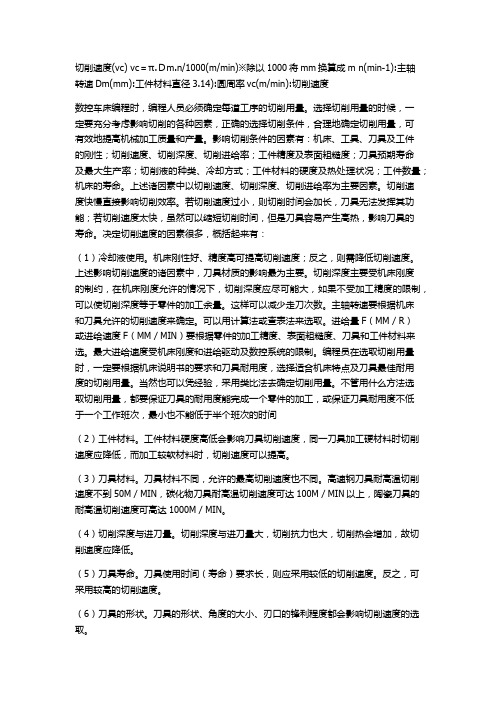
切削速度(vc) vc=π.Dm.n/1000(m/min)※除以1000将mm换算成m n(min-1):主轴转速Dm(mm):工件材料直径3.14):圆周率vc(m/min):切削速度数控车床编程时,编程人员必须确定每道工序的切削用量。
选择切削用量的时候,一定要充分考虑影响切削的各种因素,正确的选择切削条件,合理地确定切削用量,可有效地提高机械加工质量和产量。
影响切削条件的因素有:机床、工具、刀具及工件的刚性;切削速度、切削深度、切削进给率;工件精度及表面粗糙度;刀具预期寿命及最大生产率;切削液的种类、冷却方式;工件材料的硬度及热处理状况;工件数量;机床的寿命。
上述诸因素中以切削速度、切削深度、切削进给率为主要因素。
切削速度快慢直接影响切削效率。
若切削速度过小,则切削时间会加长,刀具无法发挥其功能;若切削速度太快,虽然可以缩短切削时间,但是刀具容易产生高热,影响刀具的寿命。
决定切削速度的因素很多,概括起来有:(1)冷却液使用。
机床刚性好、精度高可提高切削速度;反之,则需降低切削速度。
上述影响切削速度的诸因素中,刀具材质的影响最为主要。
切削深度主要受机床刚度的制约,在机床刚度允许的情况下,切削深度应尽可能大,如果不受加工精度的限制,可以使切削深度等于零件的加工余量。
这样可以减少走刀次数。
主轴转速要根据机床和刀具允许的切削速度来确定。
可以用计算法或查表法来选取。
进给量F(MM/R)或进给速度F(MM/MIN)要根据零件的加工精度、表面粗糙度、刀具和工件材料来选。
最大进给速度受机床刚度和进给驱动及数控系统的限制。
编程员在选取切削用量时,一定要根据机床说明书的要求和刀具耐用度,选择适合机床特点及刀具最佳耐用度的切削用量。
当然也可以凭经验,采用类比法去确定切削用量。
不管用什么方法选取切削用量,都要保证刀具的耐用度能完成一个零件的加工,或保证刀具耐用度不低于一个工作班次,最小也不能低于半个班次的时间(2)工件材料。
车削时切削用量的选择原则

三要素获得最佳组合,此时的高生产率才是合理的。
◆ 2. 刀具寿命 切削用量三要素对刀具寿命影响的大小,按顺 序为v、f、ap。因此,从保证合理的刀具寿命出发,在确定切
削用量时,首先应采用尽可能大的背吃刀量;然后再选用大的
接近要求的形状和尺寸。
◆ 粗车以提高生产率为主,在生产中加大切削深度,对提
高生产率最有利,其次适当加大进给量,而采用中等或中
等偏低的切削速度。
5
◆
粗车铸、锻件毛坯时,因工件表面有硬皮,为保护
刀尖,应先车端面或倒角,第一次切深应大于硬皮厚
度。若工件夹持的长度较短或表面凸凹不平,切削用 量则不宜过大。 粗车应留有精车余量。粗车后的精度
6
二、 刀具寿命的选择原则
◆切削用量与刀具寿命有密切关系。在制定 切削用量时,应首先选择合理的刀具寿命, 而合理的刀具寿命则应根据优化的目标而 定。一般分最高生产率刀具寿命和最低成 本刀具寿命两种,前者根据单件工时最少 的目标确定,后者根据工序成本最低的目 标确定。
7
◆1. 根据刀具复杂程度、制造和磨刀成本来 选择。复杂和精度高的刀具寿命应选得比 单刃刀具高些。 ◆2. 对于机夹可转位刀具,由于换刀时间短, 为了充分发挥其切削性能,提高生产效率, 刀具寿命可选得低些。
(1)几何因素 (2)物理因素 (3)工艺因素
从切削过程的物理实质考虑,刀具的刃口圆角及后面 的挤压与摩擦使金属材料发生塑性变形,严重恶化了表 从几何的角度考虑,刀具的形状和几何角度,特 面粗糙度。在加工塑性材料而形成带状切屑时,在前刀 从工艺的角度考虑其对工件表面粗糙度的影响,主要 别是刀尖圆弧半径、主偏角、副偏角和切削用量中的 面上容易形成硬度很高的积屑瘤。它可以代替前刀面和 有与切削刀具有关的因素、与工件材质有关的因素和与加 进给量等对表面粗糙度有较大的影响。 切削刃进行切削,使刀具的几何角度、背吃刀量发生变 工条件有关因素等。 化。积屑瘤的轮廓很不规则,因而使工件表面上出现深 浅和宽窄都不断变化的刀痕。有些积屑瘤嵌入工件表面, 更增加了表面粗糙度。切削加工时的振动,使工件表面 粗糙度参数值增大。
怎么计算各中加工中心刀具的切削速度

质量+效率+成本控制=效益怎么计算各中加工中心刀具的切削速度?浏览次数:202次悬赏分:10 | 解决时间:2011-3-3 10:15 | 提问者:zhaoqizhi521问题补充:例如:(16,20,25,32,50,63,80,125)平面铣刀,(1~20)涂层合金立铣刀,(1~30)钨钢钻,(6~80)镗刀((求切削速度切削用量))不是公式,公式我知道,就是刀具的切削用量,切削速度!!最佳答案 S=Vc*1000/3.1415*DF=S*fz*z刀具线速度(刀具商提供)乘以1000再除去3.1415再除掉刀具直径就等于主轴转数;主轴转数乘以每齿进刀量(刀具不同进刀量不同)再乘以刀具总齿数就等于进给速度;高速钢铣刀的线速度为50M/MIN硬质合金铣刀的线速度为150M/MIN切削用量的话是每齿切削0.08-0.2之间。
切削速度为转速*齿数*每齿进给。
不锈钢的话*80%铝合金本身材料很软,主轴转速应当高点(刀具能承受的情况下),进给速度要竟量小点,如果进给大的话排屑就会很困难,只要你加工过铝,不难发现刀具上总会有粘上去的铝,那说明用的切削液不对,做铝合金进给可以打快一点每一刀也可以下多一点转数不能打的太快10MM F150020MM F120050MM F1000加工中心-三菱系统的操作步骤与刀具应用 (2009-04-23 09:02:03)转载标签:数控刀具转速进给杂谈三菱系统操作:1,打开机床开关—电源接通按钮2,归零:将旋钮打到ZRN—按循环启动键,三轴同时归零。
(也可以xyz分开来归零:将旋钮打到ZRN—按Z+,X+,Y+,一般要先将Z轴归零)注意:每次打开机床后,就要归零。
3,安装工件(压板或虎口钳)4,打表(平面和侧面)侧面打到2丝之内,表面在5丝之内,最好再打一下垂直度。
5,中心棒分中,转速500.6,打开程序,看刀具,装刀具,注意刀具的刃长和需要的刀长,绝不能装短了。
7,模拟程序—传输程序。
数控机床常用计算项目与计算方法

目录一、AC主轴伺服电机及变频(biàn pín)调速电机●几个(jǐ ɡè)基本概念(一)主轴电机转速(zhuàn sù)的计算(二)主轴电机额定输出(shūchū)扭矩及最大输出扭矩的计算。
(三)主轴电机恒扭矩转速范围内实际(shíjì)输出功率的计算。
(四)机床主轴额定输出扭矩及最大输出扭矩的计算。
车、铣、钻方式下,主轴及电机所需功率的计算一、AC主轴伺服电机及变频调速电机●基本概念1、电机的功率负载特性:做为一般驱动负载工作的回转电机有以下三种常用的功率负载特性:(1)连续工作制(S1):是指该电机在额定工作条件和负载条件下允许长时间、不间断的工作。
(2)短时工作制(S2):是指该电机在规定的短时间内允许超出额定功率进行运转工作,其超载时间优先采用10、30或60分钟等。
(3)断续工作制(S3):是指该电机应按一定的通、断周期进行工作,以保证电机在大电流、超载情况下不致因电机温度过高,击穿绝源而烧坏。
在S3工作制下工作的电机允许的每一通、断工作周期为10分钟,例FANUC AC主轴电机规定在50%ED率下(S3工作制),其循环时间周期为10分钟(即ON:5min,OFF:5min)。
目前的AC主轴电机有一个重要特性就是允许在S2或S3工作制下运转,其实际就是一种短的工作制电机。
如FANUC的α11型主轴电机的额定连续输出功率为11kw。
S2工作制下的30分钟时间内允许的超载功率为15kw。
因数控机床在实际超载切削时每一次走刀时间很难超出30分钟,故许多机床制造厂在标定其生产的某型机床动力参数时,常用主轴电机的30分钟超载功率做为其样本上标示的主轴电机的主参数。
同样,进行数控机床设计时,设计者亦充分利用好主轴电机的这种特性。
特别需要指出的是,目前多采用的标准型普通变频电机,其仅能在S1工作制下工作,不允许超载使用,因此设计者选用时必须注意。
怎么计算各中加工中心刀具的切削速度?

质量+效率+成本控制=效益怎么计算各中加工中心刀具的切削速度?浏览次数:202次悬赏分:10 | 解决时间:2011-3-3 10:15 | 提问者:zhaoqizhi521问题补充:例如:(16,20,25,32,50,63,80,125)平面铣刀,(1~20)涂层合金立铣刀,(1~30)钨钢钻,(6~80)镗刀((求切削速度切削用量))不是公式,公式我知道,就是刀具的切削用量,切削速度!!最佳答案 S=Vc*1000/3.1415*DF=S*fz*z刀具线速度(刀具商提供)乘以1000再除去3.1415再除掉刀具直径就等于主轴转数;主轴转数乘以每齿进刀量(刀具不同进刀量不同)再乘以刀具总齿数就等于进给速度;高速钢铣刀的线速度为50M/MIN硬质合金铣刀的线速度为150M/MIN切削用量的话是每齿切削0.08-0.2之间。
切削速度为转速*齿数*每齿进给。
不锈钢的话*80%铝合金本身材料很软,主轴转速应当高点(刀具能承受的情况下),进给速度要竟量小点,如果进给大的话排屑就会很困难,只要你加工过铝,不难发现刀具上总会有粘上去的铝,那说明用的切削液不对,加工铝要用柴油着为切削液,刀具一定在相当锋利,最好用两刃或是三刃的立铣刀.直径太大的铣刀我认为会震动,用直径20的就好了.本人QQ117701584有问题再问做铝合金进给可以打快一点每一刀也可以下多一点转数不能打的太快10MM F150020MM F120050MM F1000加工中心-三菱系统的操作步骤与刀具应用 (2009-04-23 09:02:03)转载标签:数控刀具转速进给杂谈三菱系统操作:1,打开机床开关—电源接通按钮2,归零:将旋钮打到ZRN—按循环启动键,三轴同时归零。
(也可以xyz分开来归零:将旋钮打到ZRN—按Z+,X+,Y+,一般要先将Z轴归零)注意:每次打开机床后,就要归零。
3,安装工件(压板或虎口钳)4,打表(平面和侧面)侧面打到2丝之内,表面在5丝之内,最好再打一下垂直度。
车床工时计算法

切削速度(vc) vc=π.D1000(m/min)※除以1000将mm换算成m n(min-1):主轴转速Dm(mm):工件材料直径:圆周率vc(m/min):切削速度数控车床编程时,编程人员必须确定每道工序的切削用量。
选择切削用量的时候,一定要充分考虑影响切削的各种因素,正确的选择切削条件,合理地确定切削用量,可有效地提高机械加工质量和产量。
影响切削条件的因素有:机床、工具、刀具及工件的刚性;切削速度、切削深度、切削进给率;工件精度及表面粗糙度;刀具预期寿命及最大生产率;切削液的种类、冷却方式;工件材料的硬度及热处理状况;工件数量;机床的寿命。
上述诸因素中以切削速度、切削深度、切削进给率为主要因素。
切削速度快慢直接影响切削效率。
若切削速度过小,则切削时间会加长,刀具无法发挥其功能;若切削速度太快,虽然可以缩短切削时间,但是刀具容易产生高热,影响刀具的寿命。
决定切削速度的因素很多,概括起来有:(1)冷却液使用。
机床刚性好、精度高可提高切削速度;反之,则需降低切削速度。
上述影响切削速度的诸因素中,刀具材质的影响最为主要。
切削深度主要受机床刚度的制约,在机床刚度允许的情况下,切削深度应尽可能大,如果不受加工精度的限制,可以使切削深度等于零件的加工余量。
这样可以减少走刀次数。
主轴转速要根据机床和刀具允许的切削速度来确定。
可以用计算法或查表法来选取。
进给量F(MM/R)或进给速度F(MM/MIN)要根据零件的加工精度、表面粗糙度、刀具和工件材料来选。
最大进给速度受机床刚度和进给驱动及数控系统的限制。
编程员在选取切削用量时,一定要根据机床说明书的要求和刀具耐用度,选择适合机床特点及刀具最佳耐用度的切削用量。
当然也可以凭经验,采用类比法去确定切削用量。
不管用什么方法选取切削用量,都要保证刀具的耐用度能完成一个零件的加工,或保证刀具耐用度不低于一个工作班次,最小也不能低于半个班次的时间(2)工件材料。
工件材料硬度高低会影响刀具切削速度,同一刀具加工硬材料时切削速度应降低,而加工较软材料时,切削速度可以提高。
数控车切削三要素
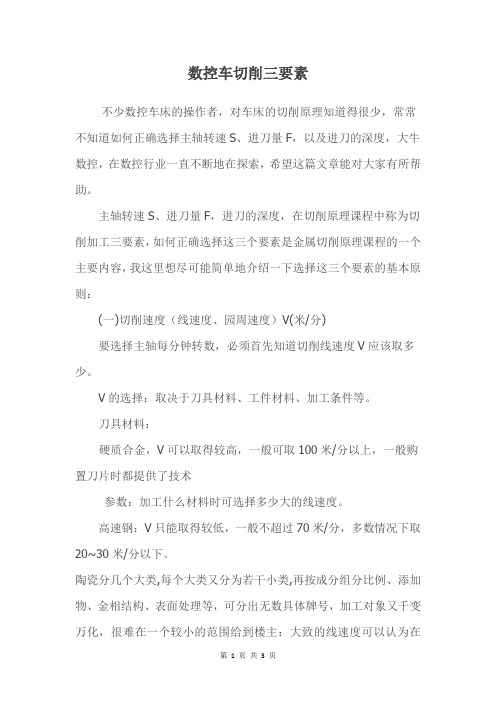
数控车切削三要素不少数控车床的操作者,对车床的切削原理知道得很少,常常不知道如何正确选择主轴转速S、进刀量F,以及进刀的深度,大牛数控,在数控行业一直不断地在探索,希望这篇文章能对大家有所帮助。
主轴转速S、进刀量F,进刀的深度,在切削原理课程中称为切削加工三要素,如何正确选择这三个要素是金属切削原理课程的一个主要内容,我这里想尽可能简单地介绍一下选择这三个要素的基本原则:(一)切削速度(线速度、园周速度)V(米/分)要选择主轴每分钟转数,必须首先知道切削线速度V应该取多少。
V的选择:取决于刀具材料、工件材料、加工条件等。
刀具材料:硬质合金,V可以取得较高,一般可取100米/分以上,一般购置刀片时都提供了技术参数:加工什么材料时可选择多少大的线速度。
高速钢:V只能取得较低,一般不超过70米/分,多数情况下取20~30米/分以下。
陶瓷分几个大类,每个大类又分为若干小类,再按成分组分比例、添加物、金相结构、表面处理等,可分出无数具体牌号,加工对象又千变万化,很难在一个较小的范围给到楼主:大致的线速度可以认为在200~1200m/min的范围之内。
工件材料:硬度高,V取低;铸铁,V取低,刀具材料为硬质合金时可取70~80米/分;低碳钢,V可取100米/分以上,有色金属,V可取更高些(100~200米/分).淬火钢、不锈钢,V应取低一些。
加工条件:粗加工,V取低一些;精加工,V取高些。
机床、工件、刀具的刚性系统差,V取低。
如果数控程序使用的S是每分钟主轴转数,那么应根据工件直径,及切削线速度V计算出S:S(主轴每分钟转数)=V(切削线速度)*1000/(3.1416*工件直径)如果数控程序使用了恒线速,那么S可直接使用切削线速度V(米/分)(二)进刀量(走刀量)F主要取决于工件加工表面粗糙度要求。
精加工时,表面要求高,走刀量取小:0.06~0.12mm/主轴每转。
粗加工时,可取大一些。
主要决定于刀具强度,一般可取0.3以上,刀具主后角较大时刀具强度差,进刀量不能太大。
数控车床速度计算公式

数控车床速度计算公式
数控车床是一种自动化加工设备,广泛应用于各种零部件的加工中。
在进行数
控车床加工时,准确计算速度是非常重要的,因为速度的控制直接影响到加工质量和效率。
在数控车床中,常用的速度计算公式包括切削速度、主轴转速和进给速度的计
算公式。
1. 切削速度(Vc)的计算公式:
切削速度是指旋转刀具在工件表面的线速度,通常用米/分钟(m/min)表示。
它的计算公式如下:
Vc = π × D × n
其中,Vc代表切削速度,π代表3.14(近似值),D代表刀具直径,n代表
主轴转速。
2. 主轴转速(n)的计算公式:
主轴转速是指车床主轴每分钟旋转的圈数,通常用转/分钟(rpm)表示。
它
的计算公式如下:
n = Vc / (π × D)
其中,n代表主轴转速,Vc代表切削速度,π代表3.14(近似值),D代表
刀具直径。
3. 进给速度(Vf)的计算公式:
进给速度是指工件在车床上移动的速度,通常用毫米/分钟(mm/min)表示。
它的计算公式如下:
Vf = f × z × n
其中,Vf代表进给速度,f代表每转进给量,z代表主轴齿数,n代表主轴转速。
通过以上三种速度的计算公式,我们可以准确地计算出数控车床的切削速度、主轴转速和进给速度,从而高效地进行加工过程。
这些计算公式的正确应用可以提高加工质量和生产效率,确保数控车床的稳定运行。
数控车床转速和进给计算公式

数控车床转速和进给计算公式
数控车床转速和进给计算公式如下:
1. 转速计算公式:
转速= (刀具主偏角平均值×3.82)÷(切削直径×π)
其中,“刀具主偏角平均值”是指刀具在切削时,取90°处、肩部与主轴线间的角度,再用多次测量的平均值。
切削直径是指在切削过程中,刀具切削时直径的平均值。
2. 进给计算公式:
进给量(mm/min)= 主轴转速(转/分)×每牙进给量(mm/牙)×齿数
其中,“每牙进给量”是指每一齿的切削深度;“齿数”是指每分钟齿轮传动的齿数。
例如,当刀具每转一圈切削12mm长度的轴杆,主轴转速为50转/分,每牙进给量为0.2mm/牙,齿数为4,则进给速度就是:50 ×0.2 ×4 = 40mm/min。
需要注意的是,数控车床的转速和进给的具体数值需要根据加工材料、
刀具种类、切削状态等因素进行调整,否则可能会对材料造成损伤或影响加工效率。
数控加工参数表

数控加工参数表 The manuscript was revised on the evening of 2021一、主轴转速n(r/min)主轴转速一般根据切削速度V来选定,计算公式为:n=1000V/(π×d)式中,d为刀具直径(mm),V为刀具切削速度(m/min)。
对于球头铣刀,工作直径要小于刀具直径,故其实际转速应大于计算转速n。
表1铣刀的切削速度V(单位:m/min)二、进给速度V f (mm/min)Vf = fz×z×n式中n为主轴转速,z为铣刀齿数,f z为每齿进给量(mm/齿).每齿进给量fz的选取主要取决于工件材料的力学性能、刀具材料、工件表面粗糙度等因素。
工件材料的强度和硬度越高,f z越小;反之则越大。
硬质合金铣刀的每齿进给量高于同类高速钢铣刀。
工件表面粗糙度要求越高,f z就越小。
1.铣削加工表2 铣刀每齿进给量f z (单位:mm/齿)2.镗削加工表3 镗孔切削用量3、攻螺纹攻螺纹前底孔直径的确定:攻米制螺纹螺距P<1mm:d0=d-PP>1mm:d0=d-(~)P式中P —螺距(mm)d0 —钻头直径(mm)d—螺纹公称直径(mm)攻不通孔螺纹钻孔深度=所需螺孔深度- d表4 攻普通螺纹前的底孔直径表5 攻英制螺纹前的底孔直径表6 攻螺纹切削速度(单位:m/min)4、钻孔加工表7 用高速钢钻头钻孔切削用量(f单位:mm/r)5、铰孔加工铰孔属于精加工工序,加工过程中应合理选择铰刀的类型及材质,高速钢铰刀属于通用铰刀,硬质合金铰刀一般用于加工钢、铸钢、灰铸铁和冷硬铸铁。
为了达到较高的孔径精度和表面质量,应采用较低的切削速度和进给量并合理选择切削液。
铰孔前应留有铰削余量,一般为~底孔直径=铰刀直径-(~)mm铰削加工时切削速度V取3~15m/min进给量f取~r注意:在正式加工之前应试铰,并检验孔径及粗糙度是否符合要求。
三、切削液的选择注:以上各表是加工中心和数控铣床常用的加工参数,供参考。
数控加工公式

基础知识---数控加工常用计算公式车削部分:一、三角函数计算1.tanθ=b/a θ=tan-1b/a2.Sinθ=b/c Cos=a/c二、切削速度的计算Vc=(π×D×n)/1000n=(1000×Vc)/π×DVc:线速度(m/min)π:圆周率(3.14159)D:刀具直径(mm)n:转速(rpm)三、进给量(f值)的计算f=ι/nf:进给量(mm/rev)ι:每分钟进给速度(mm/min)四、切削助力的计算F=ks×a p×fF:切削阻力(N)ks:比切削阻力(单位面积切削阻力)(a p:切削深度(mm)五、精加工面粗糙度(理论值)的计算方式h=(1000×f²)/8Rh:精加工表面理论粗糙度(μm)f:进给量(mm/rev)R:刀尖圆弧半径(mm)铣削部分:一、切削速度的计算:切削速度与车削一样,只是直径一个是指刀具,一个指工件。
Vc=(π*D*S)/1000Vc:线速度(m/min)π:圆周率(3.14159)D:刀具直径(mm)S:转速(rpm)V c二、进给量(F值)的计算F=S*Z*fF:进给量(mm/min)S:转速(rpm)Z:刃数f:(实际每刃进给)三、加工时间Tc=L/FTc:加工时间(min)L:工作台总进给长度(工件材料长度+铣刀刀刃直径D)F:进给速度(mm/min)四、每刃进给量的计算Fz=hm * √(D/ap )Fz:实施每刃进给量hm:理论每刃进给量ap:Z pitch(mm)D:刀片直径(mm)五、钻头钻孔时间公式T(min)=L(min)/N(rpm)*f(mm/rev)=πDL/1000vfL:钻孔全长N:回转数f:进刀量系数D:钻头直径v:切削速度孔深l,钻头孔全长L,则L=l+D/3,T=L/Nf=πDL/1000vf六、精加工理论表面粗糙度顺铣Ro= f²/(4D+f×Z/π)逆铣Ro= f²/(4D-f×Z/π)Ro:精加工理论表面粗糙度f:每刃进给量Z:刃数D:工具直径。
数控切削速度计算公式

数控切削速度计算公式
当切削材料是钢时,切削速度可以通过以下公式计算:
v=π*d*n
其中,v表示切削速度,d表示刀具直径,n表示切削转速。
当切削材料是铝合金时,切削速度可以通过以下公式计算:
v=K*d*n
其中,v表示切削速度,d表示刀具直径,n表示切削转速,K是铝合金切削速度系数,其数值一般为0.8-1.2
当切削材料是不锈钢时,切削速度可以通过以下公式计算:
v=P/(π*d*f)
其中,v表示切削速度,d表示刀具直径,P表示主轴功率,f表示进给率。
在实际计算中,需要事先确定不锈钢的切削系数。
当切削材料是铸铁时,切削速度可以通过以下公式计算:
v=K*d*n
其中,v表示切削速度,d表示刀具直径,n表示切削转速,K是铸铁切削速度系数,其数值一般为0.8-1.2
需要注意的是,不同的刀具材料、切削条件和工件材料等因素会影响切削速度的计算结果。
在实际应用中,可以通过试验和经验总结,结合切削力、切削效果和加工精度等要求,选择合适的切削速度。
同时,还需注意机床的最大切削转速和工件的材料性质等限制因素。
总结起来,数控切削速度计算公式是根据刀具材料、切割条件和工件材料等因素所确定的。
通过切削力、刀具直径和切削转速等参数,可以计算得到切削速度。
但是需要根据实际情况选择合适的切削速度,并考虑机床和工件的限制因素,以获得满足加工要求的切削效果。
主轴转速和切削速度的关系

主轴转速和切削速度的关系
主轴转速和切削速度是数控机床中两个非常重要的参数。
主轴转速是指主轴每分钟转动的圈数,切削速度是指在加工过程中工具相对于工件的移动速度。
这两个参数之间的关系是非常密切的。
切削速度是数控机床上非常关键的参数之一。
它对加工精度和加工效率有直接的影响。
切削速度过快会导致刀具过早磨损,而切削速度过慢则会导致加工时间过长,减慢加工效率。
主轴转速与切削速度的关系是,当主轴转速提高时,切削速度也会相应提高。
这是因为切削速度是由主轴转速和刀具半径共同决定的。
具体而言,切削速度等于主轴转速乘上刀具半径再乘上3.14。
需要注意的是,在选择主轴转速时,要结合所使用的切削工具和切削材料的特性,确保主轴转速与切削速度能够达到最佳的加工效果。
因为不同的切削工具和切削材料对主轴转速和切削速度的要求也是不同的。
总之,主轴转速和切削速度是数控机床上非常重要的加工参数,它们之间的关系也非常密切。
在进行数控加工时,要结合切削工具和切削
材料的特性,选择适当的主轴转速和切削速度,以确保加工效果的最佳化。
数控切削加工时间计算公式
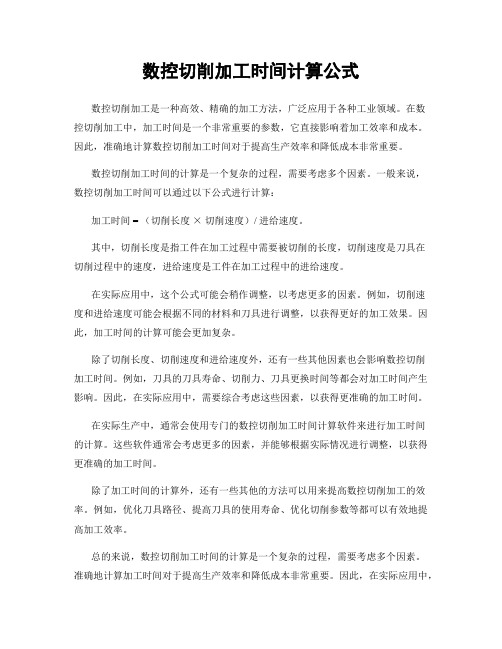
数控切削加工时间计算公式数控切削加工是一种高效、精确的加工方法,广泛应用于各种工业领域。
在数控切削加工中,加工时间是一个非常重要的参数,它直接影响着加工效率和成本。
因此,准确地计算数控切削加工时间对于提高生产效率和降低成本非常重要。
数控切削加工时间的计算是一个复杂的过程,需要考虑多个因素。
一般来说,数控切削加工时间可以通过以下公式进行计算:加工时间 = (切削长度×切削速度)/ 进给速度。
其中,切削长度是指工件在加工过程中需要被切削的长度,切削速度是刀具在切削过程中的速度,进给速度是工件在加工过程中的进给速度。
在实际应用中,这个公式可能会稍作调整,以考虑更多的因素。
例如,切削速度和进给速度可能会根据不同的材料和刀具进行调整,以获得更好的加工效果。
因此,加工时间的计算可能会更加复杂。
除了切削长度、切削速度和进给速度外,还有一些其他因素也会影响数控切削加工时间。
例如,刀具的刀具寿命、切削力、刀具更换时间等都会对加工时间产生影响。
因此,在实际应用中,需要综合考虑这些因素,以获得更准确的加工时间。
在实际生产中,通常会使用专门的数控切削加工时间计算软件来进行加工时间的计算。
这些软件通常会考虑更多的因素,并能够根据实际情况进行调整,以获得更准确的加工时间。
除了加工时间的计算外,还有一些其他的方法可以用来提高数控切削加工的效率。
例如,优化刀具路径、提高刀具的使用寿命、优化切削参数等都可以有效地提高加工效率。
总的来说,数控切削加工时间的计算是一个复杂的过程,需要考虑多个因素。
准确地计算加工时间对于提高生产效率和降低成本非常重要。
因此,在实际应用中,需要综合考虑各种因素,并使用专门的软件来进行加工时间的计算。
同时,还可以通过优化刀具路径、提高刀具的使用寿命、优化切削参数等方法来提高加工效率。
希望通过不断的努力,能够进一步提高数控切削加工的效率,为工业生产提供更好的服务。