挤压铝型材表面颗粒状毛刺的形成原因与对策
铝合金挤压制品缺陷分析及预防措施
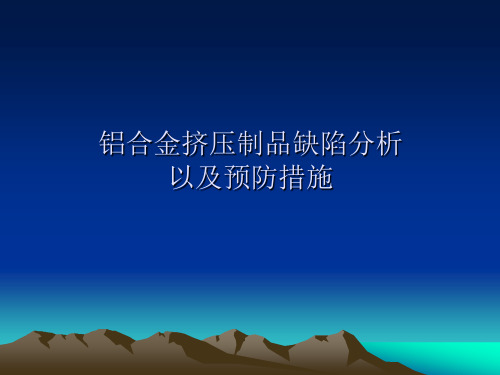
1 挤压裂纹 • 形成机理:由于摩擦力的原因,金属变形不均匀,使表层金属受 附加拉应力的作用,当拉应力积累到超过金属破断强度时就产生裂纹。 挤压裂纹多发生铝制品棱角、尖角锐边或厚度较大的台阶附近产生的 锯齿状开裂。因铝合金不纯,杂质超标,热塑性差;坯料加热温度偏 高,晶粒粗化,从而使金属破断抗力降低;控温仪表失灵,挤压温度 偏高,挤压速度失控,突然加快,增大了挤压热塑性变形应力,接近 模壁外层的金属因承受过大拉应力被撕裂为锯齿状或皮下裂纹;挤压 热塑性变形不均,表层金属承受较大的摩擦力和附加拉应力:当瞬时 应力超过金属抗拉强度时产生挤压裂纹,在外力作用下裂纹由表面向 内扩展至断裂。
10 擦伤 铝制品轻微擦伤不仅表面不美观且急剧降低机械力学性能和耐用度, 严重擦伤铝制品不能使用,成为废品,造成经济损失。 • 因挤压模型面粗糙度大,有较深冷加工刀痕、磨痕和碰伤沟痕,擦 伤铝制品表面,产生凹凸印迹;模具红硬性、耐磨性不足,模面与约 450℃-500℃铝金属坯料接触,且焖模时间长,过度回火导致型面硬 度降低而软化。由于铝制品挤压时激烈的金属塑性流动与模腔发生强 烈摩擦,将加深模面沟槽,使铝制品表面更加粗糙,失去商品表面; 挤压工模具装配不合理且间隙过大,导致热塑铝金属从模孔流出过程 中表面与工模具及设备接触不良,从而造成严重擦伤;压型导管和导 路装配不当,或挤压筒内有铝金属氧化物硬壳、夹渣、尘砂等异物进 入模孔,擦伤模具工作带,造成铝制品擦伤。 •
7 组织线、模线及毛刺
•
该缺陷与铸造工艺、挤压工艺和模具有关,严重影响铝制品商品美 观和质量。因铝铸锭宏观或微观组织不均匀和铝铸锭均匀化处理不充 分以及铝铸锭合金成分与结晶方式不同。易形成不同结晶粒度与不同 结晶方向,导致出现与挤压方向一致的带状组织线;铝铸锭若有折迭 和夹渣时,往往会因不适当地从边缘 间隙进料,使铝金属强烈热塑性 流动;挤压力偏心造 成坯料氧化皮及其它异物挤进工作带和模孔;铝 坯料与挤压筒之间间隙过大,或坯料夹渣、过热及工作带 长度突然变 化等均会导致组织线、模线产生。毛刺是在制品表面出现的不规则的 蝌蚪状、点状的划伤缺陷,由挤压筒和金属温度过高挤压速度太快或 不均匀,模具工作带硬度不够软硬不均、工作带太长、工作带粘铝等 原因造成。
6063铝合金挤压型材觉缺陷及其解决方法

6063铝合金挤压型材觉缺陷及其解决方法
1.毛刺:毛刺是挤压型材表面的突出物,会影响外观和触感。
毛刺的
主要原因是金属挤压时的不均匀变形和模具壁口的磨损。
解决方法包括增
加材料的充填比例,优化挤压工艺参数,增加模具壁口的滑移润滑剂等。
2.断裂:断裂是挤压型材在生产和使用过程中出现的一个严重问题。
断裂的原因可以是材料本身的强度不足、挤压工艺参数设置不当、模具设
计不合理等。
解决方法包括选择合适的6063铝合金型材,优化挤压工艺
参数,加强模具的冷却和加热控制等。
3.冷裂纹:冷裂纹是在挤压型材的表面或内部出现的长而细的裂纹。
冷裂纹的出现与材料的热处理过程和冷却速度不当有关。
解决方法包括优
化挤压工艺参数,控制冷却速度,合理设计材料的热处理过程等。
4.物理性能不稳定:6063铝合金挤压型材的物理性能,如硬度、抗
拉强度、延展性等,可能存在不稳定的情况。
这可能是由于挤压工艺中的
应力集中和不均匀变形导致的。
解决方法包括优化挤压工艺参数,增加冷
却控制,合理设计模具结构等。
5.起皮:起皮是指挤压型材表面出现的局部脱层现象,降低了型材的
使用寿命。
起皮的原因主要是模具的磨损和使用不当。
解决方法包括定期
检查和维护模具,增加模具的使用寿命,减少起皮现象的发生。
总之,6063铝合金挤压型材的觉缺陷可能会影响其质量和使用寿命。
通过合理选择材料、优化挤压工艺参数、改进模具设计和加强质量控制等
措施,可以有效地解决这些问题,提高挤压型材的质量和性能。
“毛刺”及“震痕”产生的原因及解决思路

( 肇庆亚洲铝厂有 限公 司 , 广东 肇庆 5 2 6 2 3 8 ) 摘 要: 论述 了模具 、 铸棒 、 挤压工艺 3个 因 素影 响“ 毛刺 ” 和“ 震 痕” 的产 生及 解决 方法. 在生 产高端 产 品的过程
中, 需要各 工序 、 各操作人员 的紧密配合 , 总接经验 , 不断提高操作水平 , 才能达到提高成品质量 、 降低成本 的 目的.
是: 在氧化电泳 、 喷涂型材的生产过程 中, 很难去除
掉, 影 响型 材 的表 面美 观 , 造成 废 品. 一 般 厂 家 对 表 面处 理为 喷粉 ( 漆) 型材 全部 经 喷 砂 处理 后 , 再 进 行
喷粉 ( 漆) , 效果较好 ; 但 氧化光 面电泳 料处理起来
就 很棘 手 , 给挤 压 工 序造 成 极 大 的 困 扰. 因此 , 要 在
1 “ 毛刺 ” 和“ 震痕" 的区别
其实 , “ 毛刺” 和“ 震痕” 专业的术语叫“ 吸 附颗
在型材上 , 表面粗糙 , 甚至刺手. 只有极少可以去 除 掉, 形成凹点 , 无法除掉的则形成凸点. 由于“ 毛刺” 密集 , 且几 乎在 同 一截 面 上 . 如 表 面 处 理 为氧 化 , 通
实践生产中不断地观察分析 、 总结 , 采取相应措施 , 以减少或杜绝这种缺陷的出现.
预处理工序, 由于槽液浓度规定范围的限制 , 有的可 以去除掉 , 有的去除不掉 , 形成 凸点. 此 问题在表 面
处理 车 间生产 中经 常 出现. “ 震痕 ” 在型 材表 面 预处 理 工序 , 因粘 铝 颗粒 镶
关键词 : 铸棒 缺陷 ; 挤压工艺 ;“ 毛刺” 及“ 震痕 ”
中圈分类号 : T G 3 7 6 文献标识码 :B
铝合金挤压、氧化型材缺陷、原因及其对策
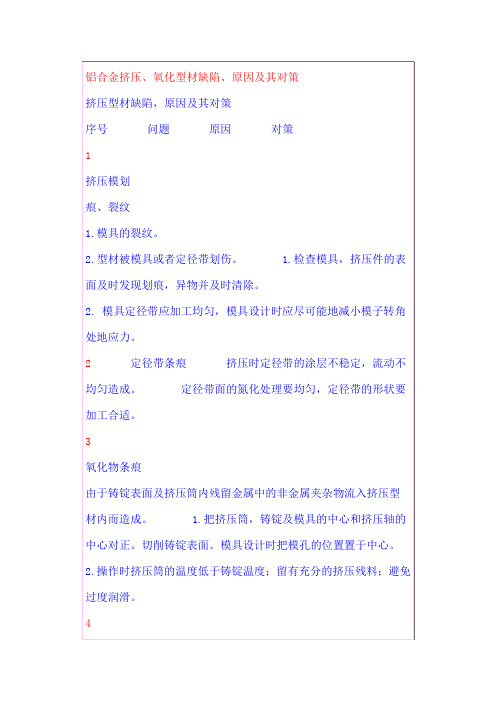
3.腐蚀液中的锌浓度减少到3ppm或腐蚀液中加硫化物离子。
3.2氧化型材缺陷,原因及其对策
序号问题原因对策
1
阳极氧化槽液温度过高,降不下来。1.冷冻机制冷量不够。
2.冷冻机冷媒不足。
3.热交换量不足或热交换面结垢。
4.电能在槽液中消耗大,发热量大。1.增加冷冻机功率(台数)。
2.模具进行改进。
3.修整模具导流腔或定径带。
5
桔皮锭坯的成份有偏差或固溶处理不充分,以及不适当的挤压条件等使晶粒变粗大所造成。1.适当调节挤压温度和挤压速度。
2.在矫直工艺中减少拉伸量。
6
粗晶组织
和锭坯的成份及组织有关,或者由于在挤压时变形热效应造成温度升高所致。1.改变化学成份或选择适当的均匀化处理条件。重新设计合理的模具结构。
2.电接点少。
3.导电杆退膜不彻底,使得导电杆与型材接触不良。
4.电解液温度过高。
5.阴极面积不足。
2.使用没有裂纹和氧化物夹杂的锭坯;防止锭坯过热;铸锭前对溶液进行充分除气处理。
3.操作中减慢挤压速度;控制热处理的气氛,防止水蒸气的进入;增大余压;减少对挤压垫和模具的润滑。
8
夹渣
锭坯的表面层或挤压筒内壁上的异物被卷入而出现在挤压型材的表面;由于模具设计时模孔位置过于接近外圆所造成。1.在模具设计上尽可能使模孔位于模具中心;对于中空的型材时,应把分流孔的外接圆缩小。
2.补充冷媒。
3.增大热交换面或清洗热交换部分。
4.采用脉冲阳极氧化。
2槽端实际电压远低于表上显示数值。1.导电横梁与电极接触不良。
2.电极连接处螺丝松动或锈蚀,使得此处电阻大。
3.电压表故障。
1.用砂纸将接触部位磨平磨光亮。
铝合金挤压工序中的主要缺陷分析及质量控制方法
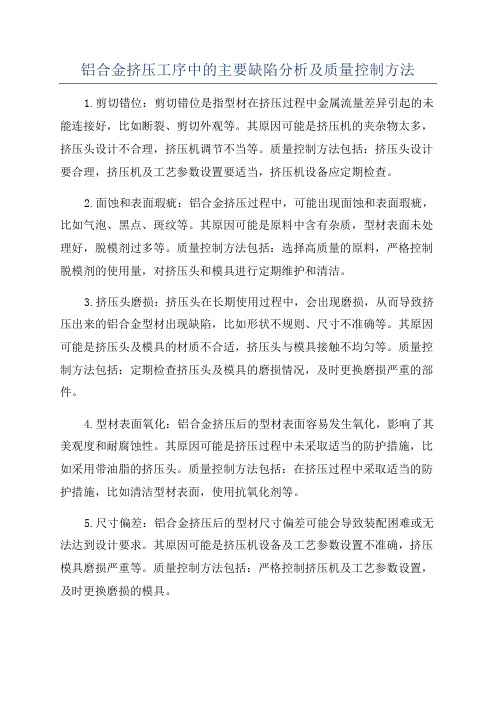
铝合金挤压工序中的主要缺陷分析及质量控制方法1.剪切错位:剪切错位是指型材在挤压过程中金属流量差异引起的未能连接好,比如断裂、剪切外观等。
其原因可能是挤压机的夹杂物太多,挤压头设计不合理,挤压机调节不当等。
质量控制方法包括:挤压头设计要合理,挤压机及工艺参数设置要适当,挤压机设备应定期检查。
2.面蚀和表面瑕疵:铝合金挤压过程中,可能出现面蚀和表面瑕疵,比如气泡、黑点、斑纹等。
其原因可能是原料中含有杂质,型材表面未处理好,脱模剂过多等。
质量控制方法包括:选择高质量的原料,严格控制脱模剂的使用量,对挤压头和模具进行定期维护和清洁。
3.挤压头磨损:挤压头在长期使用过程中,会出现磨损,从而导致挤压出来的铝合金型材出现缺陷,比如形状不规则、尺寸不准确等。
其原因可能是挤压头及模具的材质不合适,挤压头与模具接触不均匀等。
质量控制方法包括:定期检查挤压头及模具的磨损情况,及时更换磨损严重的部件。
4.型材表面氧化:铝合金挤压后的型材表面容易发生氧化,影响了其美观度和耐腐蚀性。
其原因可能是挤压过程中未采取适当的防护措施,比如采用带油脂的挤压头。
质量控制方法包括:在挤压过程中采取适当的防护措施,比如清洁型材表面,使用抗氧化剂等。
5.尺寸偏差:铝合金挤压后的型材尺寸偏差可能会导致装配困难或无法达到设计要求。
其原因可能是挤压机设备及工艺参数设置不准确,挤压模具磨损严重等。
质量控制方法包括:严格控制挤压机及工艺参数设置,及时更换磨损的模具。
总之,铝合金挤压工序中的缺陷主要包括剪切错位、面蚀和表面瑕疵、挤压头磨损、型材表面氧化和尺寸偏差等。
通过选择合适的原料,合理设计挤压机及模具,严格控制工艺参数,及时维护和更换设备和模具等方式,可以有效地控制和消除这些缺陷,提高铝合金挤压工序的质量。
铝合金挤压型材几种常见缺陷解析
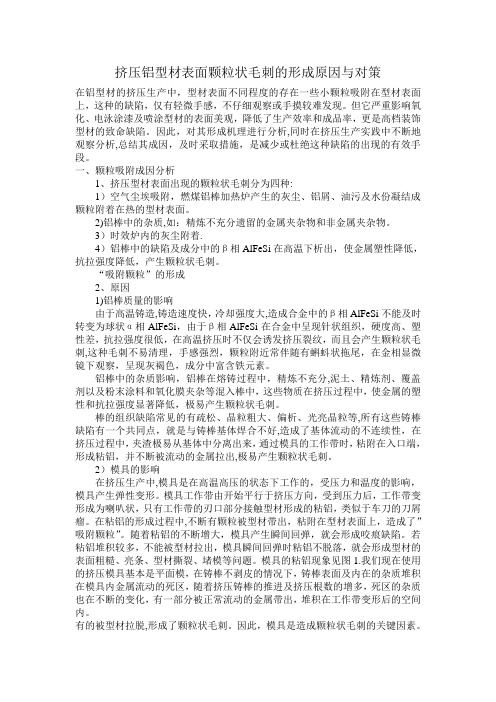
挤压铝型材表面颗粒状毛刺的形成原因与对策在铝型材的挤压生产中,型材表面不同程度的存在一些小颗粒吸附在型材表面上,这种的缺陷,仅有轻微手感,不仔细观察或手摸较难发现。
但它严重影响氧化、电泳涂漆及喷涂型材的表面美观,降低了生产效率和成品率,更是高档装饰型材的致命缺陷。
因此,对其形成机理进行分析,同时在挤压生产实践中不断地观察分析,总结其成因,及时采取措施,是减少或杜绝这种缺陷的出现的有效手段。
一、颗粒吸附成因分析1、挤压型材表面出现的颗粒状毛刺分为四种:1)空气尘埃吸附,燃煤铝棒加热炉产生的灰尘、铝屑、油污及水份凝结成颗粒附着在热的型材表面。
2)铝棒中的杂质,如:精炼不充分遗留的金属夹杂物和非金属夹杂物。
3)时效炉内的灰尘附着.4)铝棒中的缺陷及成分中的β相AlFeSi在高温下析出,使金属塑性降低,抗拉强度降低,产生颗粒状毛刺。
“吸附颗粒”的形成2、原因1)铝棒质量的影响由于高温铸造,铸造速度快,冷却强度大,造成合金中的β相AlFeSi不能及时转变为球状α相AlFeSi,由于β相AlFeSi在合金中呈现针状组织,硬度高、塑性差,抗拉强度很低,在高温挤压时不仅会诱发挤压裂纹,而且会产生颗粒状毛刺,这种毛刺不易清理,手感强烈,颗粒附近常伴随有蝌蚪状拖尾,在金相显微镜下观察,呈现灰褐色,成分中富含铁元素。
铝棒中的杂质影响,铝棒在熔铸过程中,精炼不充分,泥土、精炼剂、覆盖剂以及粉末涂料和氧化膜夹杂等混入棒中,这些物质在挤压过程中,使金属的塑性和抗拉强度显著降低,极易产生颗粒状毛刺。
棒的组织缺陷常见的有疏松、晶粒粗大、偏析、光亮晶粒等,所有这些铸棒缺陷有一个共同点,就是与铸棒基体焊合不好,造成了基体流动的不连续性,在挤压过程中,夹渣极易从基体中分离出来,通过模具的工作带时,粘附在入口端,形成粘铝,并不断被流动的金属拉出,极易产生颗粒状毛刺。
2)模具的影响在挤压生产中,模具是在高温高压的状态下工作的,受压力和温度的影响,模具产生弹性变形。
铝型材挤压工艺造成毛刺震痕解决方法

毛刺和震痕是在铝型材挤压加工中经常会出现的两种缺陷。
造成毛刺和震痕的原因有很多种,今天,我们就来一起研究挤压工艺对毛刺和震痕产生有什么样的影响,以及怎样解决这个问题。
挤压工艺对产生毛刺和震痕的影响:在挤压铝型材时,粘铝是造成毛刺和震痕的主要原因。
如果金属液流的温度过高、流动的速度过快,就会导致模具变形的程度增加,这样容易形成粘铝现象。
而且,这样还会使铝型材的变形抗力相对增加,从而在模具内腔的金属死区内更容易形成粘铝。
另外,如果铸棒的温度、模具的温度、盛锭筒的温度三者之间相差过大,也容易产生粘铝问题。
在模具投入生产前,一定要使用指定的模垫或专用垫进行保护。
同时还要特别注意,模垫、专用垫和模具之间的配合是否存在间隙,是否有撞击位、裂纹以及由于退火而产生的凹痕等。
如果某一个工件的端面不平,在挤压生产过程中,就会给模具的弹性变形留下空间。
挤压工艺造成毛刺和震痕的解决方法:首先,要想解决问题,就必须及时发现问题。
这就要求在挤压机出口处按装白色灯光,以便“明察秋毫”,及时观察到“毛刺”的产生情况。
然后,就是要根据“毛刺”问题的实时情况,以及根据铝型材的挤压系数、型材断面情况、模具情况、设备情况等,选择最合适的挤压温度、铸棒加热温度、模具温度以及挤压速度,并在生产过程中,不断对这些参数进行调整。
随着一次上机生产棒数量的增加,工作带的温度会上升,这样会导致铝水与工作带的摩擦加剧,使工作带硬度下降,表面变得粗糙,积铝越来越多,从而形成毛刺和震痕。
因此,对一次上机生产的铸棒数量进行限制时非常有必要的。
挤压铝型材的操作人员应在加工开始前,对模垫、专用垫、模具之间是否存在间隙进行检查。
如果存在间隙,可以采取磨平的方法加以解决。
如果磨掉的量过大,模垫和专用垫不能立即投入生产,必须要进行加温后,再重新投入生产。
模具的挤压中心位核挤压杆的位置一定要正。
假如模具中心位不正,棒皮就容易进入模具内;假如挤压杆的位置不正,盛锭筒的筒壁会把本应倒流的杂质送入模具。
铝压铸件去毛刺方法【大全】

铝压铸件毛刺是常见的问题,它不仅会影响产品的尺寸、装配精度,还会严重影响产品的外观和质量。
毛刺的多寡是衡量压铸件品质好坏的重要指标之一,毛刺越多,质量标准也就越低。
在实际工业生产中,对于铝压铸件去除毛刺的问题,各个企业都没有根本的办法来彻底解决。
从某种意义来讲,毛刺的产生还是带有行业的客观存在性和必然性的,反复洗模、修模还会影响生产效率以及模具的使用寿命。
铝压铸件毛刺产生原因:在生产过程中,毛刺产生的因素是多方面的,主要有压铸机性能的稳定性、压铸工艺参数的选用、合金成分及熔炼工艺、脱模剂的使用、模具结构的合理和制造质量。
传统去铝压铸件毛刺的方法:铝压铸件传统的去毛刺方法由人工采用锉刀、刀具等手工工具对毛刺去除,该方法耗工时长,生产效率低,对其精度要求高,因此人工去毛刺不能满足使用的要求。
另外,在用冲压模去除冒口的时候也能将铸件外周毛刺去除,但该方法对内部结构处及细节处的毛刺不能去除。
去除铝压铸件毛刺新方法:“热能去毛刺”将所需去毛刺的零件,放在密闭容器内,然后充入一定量的氢气(或甲烷)和氧气,经火花塞点燃以后,混合气体在瞬间内反应,放出大量的热,使毛刺(飞边)在高温(约3 000 ℃),高压(充气压力的20倍),高速(8倍音速)作用下,加热自燃,而达到去除毛刺(飞边)的目的。
热能去毛刺的效率很高,工艺性能稳定。
因此我们分析出铝压铸件去除毛刺问题的两种方案,一是通过控制压铸工艺参数及调整模具结构来避免毛刺的产生。
二是采用新技术“热能去毛刺”的方法去除毛刺。
扩展资料:特性:由于金属铜、锌、铝及铝合金具有很好的流动性和可塑性,而且铸造加工是在有压力的压铸机中铸造,因此铝压铸件可以做出各种较复杂的形状,也可作出较高的精度和光洁度,从而很大程度的减少了铸件的机械加工量和金属铜、锌、铝或铝合金的铸造余量,不仅节约了电力、金属材料、还大大节约了劳动成本;而铜、锌、铝及铝合金具有优良的导热性,较小的比重和高可加工性;从而压铸件被广泛应用于汽车制造、内燃机生产、摩托车制造、电动机制造、油泵制造、传动机械制造、精密仪器、园林美化、电力建设、建筑装饰等各个行业。
铝合金型材表面金属豆、毛刺、三角口产生的原因及解决办法
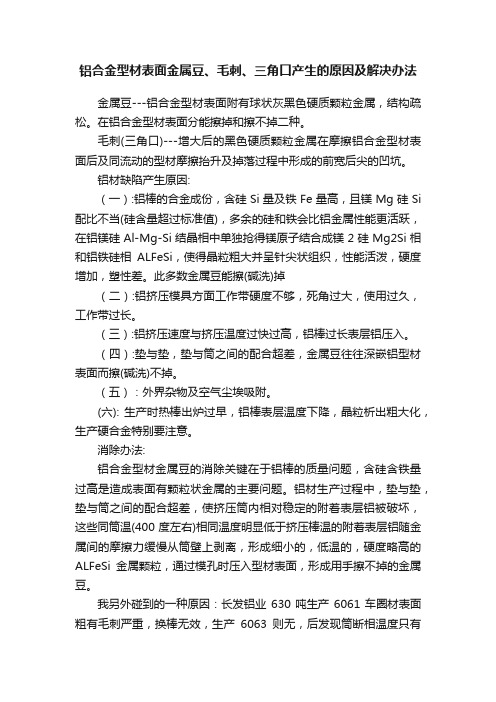
铝合金型材表面金属豆、毛刺、三角口产生的原因及解决办法金属豆---铝合金型材表面附有球状灰黑色硬质颗粒金属,结构疏松。
在铝合金型材表面分能擦掉和擦不掉二种。
毛刺(三角口)---增大后的黑色硬质颗粒金属在摩擦铝合金型材表面后及同流动的型材摩擦抬升及掉落过程中形成的前宽后尖的凹坑。
铝材缺陷产生原因:(一):铝棒的合金成份,含硅Si量及铁Fe量高,且镁Mg硅Si 配比不当(硅含量超过标准值),多余的硅和铁会比铝金属性能更活跃,在铝镁硅Al-Mg-Si结晶相中单独抢得镁原子结合成镁2硅Mg2Si相和铝铁硅相ALFeSi,使得晶粒粗大并呈针尖状组织,性能活泼,硬度增加,塑性差。
此多数金属豆能擦(碱洗)掉(二):铝挤压模具方面工作带硬度不够,死角过大,使用过久,工作带过长。
(三):铝挤压速度与挤压温度过快过高,铝棒过长表层铝压入。
(四):垫与垫,垫与筒之间的配合超差,金属豆往往深嵌铝型材表面而擦(碱洗)不掉。
(五):外界杂物及空气尘埃吸附。
(六): 生产时热棒出炉过早,铝棒表层温度下降,晶粒析出粗大化,生产硬合金特别要注意。
消除办法:铝合金型材金属豆的消除关键在于铝棒的质量问题,含硅含铁量过高是造成表面有颗粒状金属的主要问题。
铝材生产过程中,垫与垫,垫与筒之间的配合超差,使挤压筒内相对稳定的附着表层铝被破坏,这些同筒温(400度左右)相同温度明显低于挤压棒温的附着表层铝随金属间的摩擦力缓慢从筒壁上剥离,形成细小的,低温的,硬度略高的ALFeSi金属颗粒,通过模孔时压入型材表面,形成用手擦不掉的金属豆。
我另外碰到的一种原因:长发铝业630吨生产6061车圈材表面粗有毛刺严重,换棒无效,生产6063则无,后发现筒断相温度只有365度,修好后390度挤压型材毛刺消失。
原因是6061车圈材挤速慢,棒(520度)外层与筒壁传热冷却过程中镁2硅Mg2Si相和铝铁硅相ALFeSi析出集中在铝棒表层,经死区在型材表面反映出来。
挤压铝型材表面粗糙缺陷形成原因
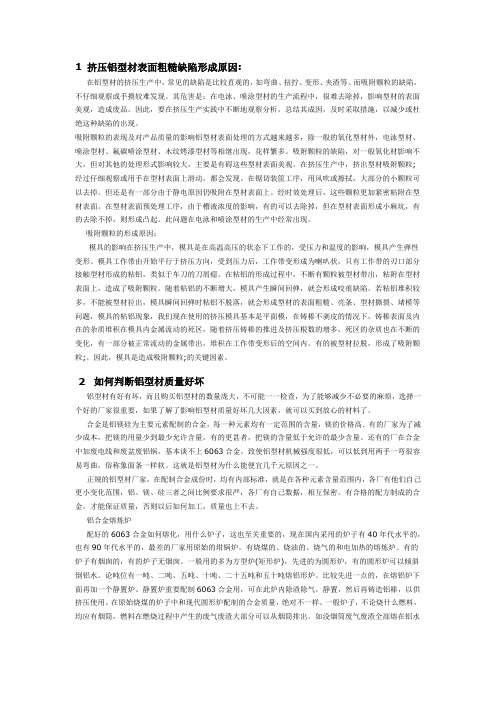
1 挤压铝型材表面粗糙缺陷形成原因:在铝型材的挤压生产中,常见的缺陷是比较直观的,如弯曲、扭拧、变形、夹渣等。
而吸附颗粒的缺陷,不仔细观察或手摸较难发现。
其危害是:在电泳、喷涂型材的生产流程中,很难去除掉,影响型材的表面美观,造成废品。
因此,要在挤压生产实践中不断地观察分析,总结其成因,及时采取措施,以减少或杜绝这种缺陷的出现。
吸附颗粒的表现及对产品质量的影响铝型材表面处理的方式越来越多,除一般的氧化型材外,电泳型材、喷涂型材、氟碳喷涂型材、木纹烤漆型材等相继出现,花样繁多。
吸附颗粒的缺陷,对一般氧化材影响不大,但对其他的处理形式影响较大,主要是有碍这些型材表面美观。
在挤压生产中,挤出型材吸附颗粒;经过仔细观察或用手在型材表面上滑动,都会发现。
在锯切装筐工序,用风吹或擦拭,大部分的小颗粒可以去掉。
但还是有一部分由于静电原因仍吸附在型材表面上。
经时效处理后,这些颗粒更加紧密粘附在型材表面。
在型材表面预处理工序,由于槽液浓度的影响,有的可以去除掉,但在型材表面形成小麻坑,有的去除不掉,则形成凸起。
此问题在电泳和喷涂型材的生产中经常出现。
吸附颗粒的形成原因:模具的影响在挤压生产中,模具是在高温高压的状态下工作的,受压力和温度的影响,模具产生弹性变形。
模具工作带由开始平行于挤压方向,受到压力后,工作带变形成为喇叭状,只有工作带的刃口部分接触型材形成的粘铝,类似于车刀的刀屑瘤。
在粘铝的形成过程中,不断有颗粒被型材带出,粘附在型材表面上,造成了吸附颗粒。
随着粘铝的不断增大,模具产生瞬间回弹,就会形成咬痕缺陷。
若粘铝堆积较多,不能被型材拉出,模具瞬间回弹时粘铝不脱落,就会形成型材的表面粗糙、亮条、型材撕裂、堵模等问题,模具的粘铝现象,我们现在使用的挤压模具基本是平面模,在铸棒不剥皮的情况下,铸棒表面及内在的杂质堆积在模具内金属流动的死区,随着挤压铸棒的推进及挤压根数的增多,死区的杂质也在不断的变化,有一部分被正常流动的金属带出,堆积在工作带变形后的空间内。
铝合金挤压型材几种常见缺点解析

挤压铝型材表面颗粒状毛刺的形成原因与对策在铝型材的挤压生产中,型材表面不同程度的存在一些小颗粒吸附在型材表面上,这种的缺陷,仅有轻微手感,不仔细观察或手摸较难发现。
但它严重影响氧化、电泳涂漆及喷涂型材的表面美观,降低了生产效率和成品率,更是高档装饰型材的致命缺陷。
因此,对其形成机理进行分析,同时在挤压生产实践中不断地观察分析,总结其成因,及时采取措施,是减少或杜绝这种缺陷的出现的有效手段。
一、颗粒吸附成因分析1、挤压型材表面出现的颗粒状毛刺分为四种:1)空气尘埃吸附,燃煤铝棒加热炉产生的灰尘、铝屑、油污及水份凝结成颗粒附着在热的型材表面。
2)铝棒中的杂质,如:精炼不充分遗留的金属夹杂物和非金属夹杂物。
3)时效炉内的灰尘附着。
4)铝棒中的缺陷及成分中的β相AlFeSi在高温下析出,使金属塑性降低,抗拉强度降低,产生颗粒状毛刺。
“吸附颗粒”的形成2、原因1)铝棒质量的影响由于高温铸造,铸造速度快,冷却强度大,造成合金中的β相AlFeSi不能及时转变为球状α相AlFeSi,由于β相AlFeSi在合金中呈现针状组织,硬度高、塑性差,抗拉强度很低,在高温挤压时不仅会诱发挤压裂纹,而且会产生颗粒状毛刺,这种毛刺不易清理,手感强烈,颗粒附近常伴随有蝌蚪状拖尾,在金相显微镜下观察,呈现灰褐色,成分中富含铁元素。
铝棒中的杂质影响,铝棒在熔铸过程中,精炼不充分,泥土、精炼剂、覆盖剂以及粉末涂料和氧化膜夹杂等混入棒中,这些物质在挤压过程中,使金属的塑性和抗拉强度显著降低,极易产生颗粒状毛刺。
棒的组织缺陷常见的有疏松、晶粒粗大、偏析、光亮晶粒等,所有这些铸棒缺陷有一个共同点,就是与铸棒基体焊合不好,造成了基体流动的不连续性,在挤压过程中,夹渣极易从基体中分离出来,通过模具的工作带时,粘附在入口端,形成粘铝,并不断被流动的金属拉出,极易产生颗粒状毛刺。
2)模具的影响在挤压生产中,模具是在高温高压的状态下工作的,受压力和温度的影响,模具产生弹性变形。
铝材挤压加工毛刺的产生原因及解决方法
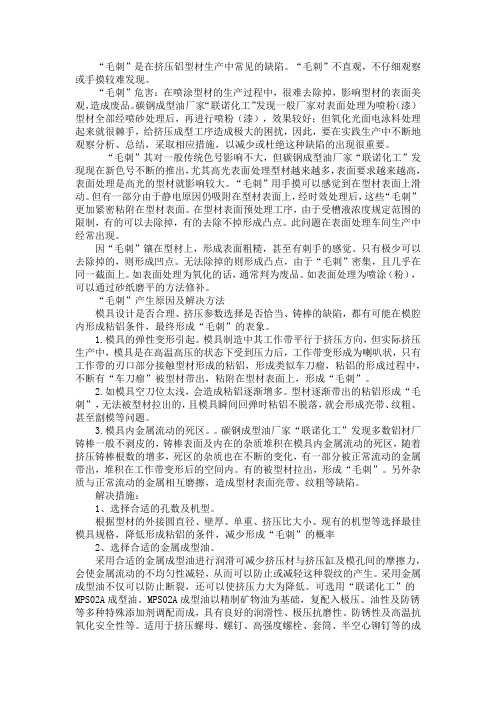
“毛刺”是在挤压铝型材生产中常见的缺陷。
“毛刺”不直观,不仔细观察或手摸较难发现。
“毛刺”危害:在喷涂型材的生产过程中,很难去除掉,影响型材的表面美观,造成废品。
碳钢成型油厂家“联诺化工”发现一般厂家对表面处理为喷粉(漆)型材全部经喷砂处理后,再进行喷粉(漆),效果较好;但氧化光面电泳料处理起来就很棘手,给挤压成型工序造成极大的困扰,因此,要在实践生产中不断地观察分析、总结,采取相应措施,以减少或杜绝这种缺陷的出现很重要。
“毛刺”其对一般传统色号影响不大,但碳钢成型油厂家“联诺化工”发现现在新色号不断的推出,尤其高光表面处理型材越来越多,表面要求越来越高,表面处理是高光的型材就影响较大。
“毛刺”用手摸可以感觉到在型材表面上滑动。
但有一部分由于静电原因仍吸附在型材表面上,经时效处理后,这些“毛刺”更加紧密粘附在型材表面。
在型材表面预处理工序,由于受槽液浓度规定范围的限制,有的可以去除掉,有的去除不掉形成凸点。
此问题在表面处理车间生产中经常出现。
因“毛刺”镶在型材上,形成表面粗糙,甚至有刺手的感觉。
只有极少可以去除掉的,则形成凹点。
无法除掉的则形成凸点,由于“毛刺”密集,且几乎在同一截面上。
如表面处理为氧化的话,通常判为废品。
如表面处理为喷涂(粉),可以通过砂纸磨平的方法修补。
“毛刺”产生原因及解决方法模具设计是否合理、挤压参数选择是否恰当、铸棒的缺陷,都有可能在模腔内形成粘铝条件,最终形成“毛刺”的表象。
1.模具的弹性变形引起。
模具制造中其工作带平行于挤压方向,但实际挤压生产中,模具是在高温高压的状态下受到压力后,工作带变形成为喇叭状,只有工作带的刃口部分接触型材形成的粘铝,形成类似车刀瘤,粘铝的形成过程中,不断有“车刀瘤”被型材带出,粘附在型材表面上,形成“毛刺”。
2.如模具空刀位太浅,会造成粘铝逐渐增多。
型材逐渐带出的粘铝形成“毛刺”,无法被型材拉出的,且模具瞬间回弹时粘铝不脱落,就会形成亮带、纹粗、甚至劏模等问题。
铝合金挤压型材拉毛及颗粒缺陷的研究

压铝材表面产生麻面缺陷的主要原因。这是因为铝 材的挤压过程是在 450 ℃左右的高温下进行的,如 果加上变形热、摩擦热的作用,金属在流出模孔时 的温度会更高[6]。当制品流出模孔时,由于处于高 温状态,金属与模具工作带存在粘铝现象[7]。这种 粘结的形式往往是:粘结—撕开—再粘结—再撕开 的反复过程,而制品又是向前流动着的,从而在制 品表面出现了许多小麻点,造成了挤压制品表面的 拉毛、颗粒缺陷 。 [8] 这种粘结现象又与铸锭质量、 模具工作带的表面状况、挤压温度、挤压速度、变 形程度以及金属的变形抗力等因素有关。
Copyright©博看网 . All Rights Reserved.
马 旭, 等:铝合金挤压型材麻面缺陷的研究
氧化处理后呈暗黑色,最终会影响型材美观, 如图 1 中小圈所示。
(2) 颗粒缺陷又称金属豆或吸附颗粒。铝合金 型材表面附有球状灰黑色硬质颗粒金属,结构疏 松,在铝合金型材表面分能擦掉和擦不掉二种。尺 寸一般小于 0.5 mm,手触有粗糙感,前端不带有划 道,经氧化后与基体差别不大,如图 1 中大圈所 示。
1 试验材料与方法
通过前期调研了解到冶金纯净度、模具状态、 挤压工艺、成分 (难溶杂质相)、生产状况等因素 可能会影响到表面拉毛、颗粒缺陷。试验选用 6005A 和 6060 两种合金棒材挤压相同断面,通过直 读光谱仪、SEM 等检测手段对拉毛、颗粒位置进行 形貌与成分分析,并与周围正常基体进行对比。
上呈现明显堆叠痕迹。
1 基体 4~6 小点
技术工程
2~3 拉毛
(a) 放大 100 倍
(a) 表面处理前
(b) 表面处理后 图 1 挤压型材表面缺陷
挤压型材常见缺陷

铝合金常见缺陷铝合金型材以其良好的塑性、适中的热处理强度、良好的焊接性能以及阳极氧化处理后表面华丽的色泽等诸多优点而被广泛应用。
但在生产过程中经常会出现一些缺陷而致使产品质量低下,成品率降低,生产成本增加,效益下降,最终导致企业的市场竞争能力下降。
因此,从根源上着手解决铝合金挤压型材的缺陷问题是企业提高自身竞争力的一个重要方面。
笔者根据多年的铝型材生产实践,在此对铝合金挤压型材常见缺陷及其解决办法作一总结,和众多同行交流,以期相互促进。
1 划、擦、碰伤划伤、擦伤、碰伤是当型材从模孔流出以及在随后工序中与工具、设备等相接触时导致的表面损伤。
1.1 主要原因①铸锭表面附着有杂物或铸锭成分偏析。
铸锭表面存在大量偏析浮出物而铸锭又未进行均匀化处理或均匀化处理效果不好时,铸锭内存在一定数量的坚硬的金属颗粒,在挤压过程中金属流经工作带时,这些偏析浮出物或坚硬的金属颗粒附着在工作带表面或对工作带造成损伤,最终对型材表面造成划伤;②模具型腔或工作带上有杂物,模具工作带硬度较低,使工作带表面在挤压时受伤而划伤型材;③出料轨道或摆床上有裸露的金属或石墨条内有较硬的夹杂物,当其与型材接触时对型材表面造成划伤;④在叉料杆将型材从出料轨道上送到摆床上时,由于速度过快造成型材碰伤;⑤在摆床上人为拖动型材造成擦伤;⑥在运输过程中型材之间相互摩擦或挤压造成损伤。
1.2 解决办法①加强对铸锭质量的控制;②提高修模质量,模具定期氮化并严格执行氮化工艺;③用软质毛毡将型材与辅具隔离,尽量减少型材与辅具的接触损伤;④生产中要轻拿轻放,尽量避免随意拖动或翻动型材;⑤在料框中合理摆放型材,尽量避免相互摩擦。
2机械性能不合格2.1 主要原因①挤压时温度过低,挤压速度太慢,型材在挤压机的出口温度达不到固溶温度,起不到固溶强化作用;②型材出口处风机少,风量不够,导致冷却速度慢,不能使型材在最短的时间内降到200℃以下,使粗大的Mg2Si过早析出,从而使固溶相减少,影响了型材热处理后的机械性能;③铸锭成分不合格,铸锭中的Mg、Si含量达不到标准要求;④铸锭未均匀化处理,使铸锭组织中析出的Mg2Si相无法在挤压的较短时间内重新固溶,造成固溶不充分而影响了产品性能;⑤时效工艺不当、热风循环不畅或热电偶安装位置不正确,导致时效不充分或过时效。
铝合金切削加工过程中毛刺形成机理与控制

上海交通大学硕士学位论文铝合金切削加工过程中毛刺形成机理与控制姓名:董洪艳申请学位级别:硕士专业:机械工程指导教师:邵华;张其然20080601BURR FORMATION MECHANISM AND CONTROLIN MILLING OF 2A12 ALUMINUM ALLOYABSTRACTBurr formed during metal cutting process,is harmful to both function and quality of mechanical components. In this thesis, based on FEM analysis and cutting experiment in milling of 2A12(LY12) aluminum-alloy,burr formation mechanism and the impact of cutting parameters on burr dimensions were explored. FEM analysisⅠdemonstrated that when cutting 2A12(LY12) aluminum-alloy ,the type burr was formed in cutting out direction due to chip bending at theⅡend of the work piece and the burr is big ;The type burr is formedⅠdue to the breakage of type burr with further plastic bending at the endof the work piece and the burr is relatively small. FEM analysis and cutting experiment showed that the bigger the depth of cut is,the larger the formed burr is; the increase the cutting velocity decreases the burr dimensions,and the impact of feed rate on burr dimension depends on the machining system. The orthogonal experiments of the two machining system indicated that the optimized cutting conditions of the first machining system are : depth of cut 0.1mm,feed per tooth 0.05mm/z,spindle speed 250m/min and corresponding burr height was about 0.02mm;the optimization cutting conditions of the second machiningsystem are :depth of cut 0.2mm,feed per tooth 0.2mm/z,spindle speed 4000r/min, and corresponding burr height was around 0.01mm. In this thesis machinability of 2A12(LY12) aluminum alloy was further explored. The work is of some practical value to the machining of the material.KEY WORDS:2A12(LY12) aluminum alloy,milling,burr,metal cutting,machinability, FEA上海交通大学学位论文原创性声明本人郑重声明:所呈交的学位论文,是本人在导师的指导下,独立进行研究工作所取得的成果。
铝合金挤压缺陷分析及质量控制方法

铝合金挤压缺陷分析及质量控制方法一、缩尾在某些挤压制品的尾端,经低倍检查,在截面的中间部位有不合层形似喇叭状现象,称为缩尾。
经常可以见到一类缩尾或二类缩尾两种情况.一类缩尾位于制品的中心部位,呈皱褶状裂缝或漏斗状孔洞。
二类缩尾位于制品半径1/2区域,呈环状或月牙状裂缝。
有时在离制品表面层0。
5-2mm处出现连续的或不连续的不合层裂纹或裂纹痕迹,有人把它称为第三类缩尾。
一般正向挤压制品的缩尾比反向挤压的长,软合金比硬合金的长.正向挤压制品的缩尾多表现为环形不合层,反向挤压制品的缩尾多表现为中心漏斗状。
金属挤压到后端,堆积在挤压筒死角或垫片上的铸锭表皮和外来夹杂物流入制品中形成二次缩尾;当残料留得过短,制品中心补缩不足时,则形成一类缩尾。
从尾端向前,缩尾逐渐变轻以至完全消失.缩尾的主要产生原因:1、残料留得过短或制品切尾长度不符合规定;2、挤压垫不清洁,有油污;3、挤压后期,挤压速度过快或突然增大;4、使用已变形的挤压垫(中间凸起的垫);5、挤压筒温度过高;6、挤压筒和挤压轴不对中;7、铸锭表面不清洁,有油污,未车去偏析瘤和折叠等缺陷;8、挤压筒内套不光洁或变形,未及时用清理垫清理内衬。
防止方法:1、按规定留残料和切尾;2、保持工模具清洁干净;3、提高铸锭的表面质量;4、合理控制挤压温度和速度,在平稳挤压;5、除特殊情况外,严禁在工、模具表面抹油;6、垫片适当冷却。
二、粗晶环织区,称为粗晶环。
由于制品外形和加工方式不同,可形成环状、弧状及其他形式的粗晶环.粗晶环的深度同尾端向前端逐渐减小以至完全消失。
形成机理是由热挤压后在制品表层形成的亚晶粒区,加热固溶处理后形成粗大的再结晶晶粒区。
粗晶环主要的产生原因:1、挤压变形不均匀;2、热处理温度过高,保温时间过长,使晶粒长大;3、便金化学成分不合理;4、一般的可热处理强化合金经热处理后都有粗晶环产生,尤其是6A02、2A50等合金的型、棒材最为严重,不能消除,只能控制在一定范围内;5、挤压变形小或变形不充分,或处于临界变形范围,易产生粗晶环。
关于铝型材毛刺问题的解决

关于铝型材毛刺问题的解决郑光为(广东兴发集团有限公司,广东佛山528219)毛刺的产生是由于型材出口处的强度小于型材表面与模具定径带的摩擦力而造成局部的撕裂。
要解决此问题主要从提高出口处型材的强度降低型材与模具之间的摩擦力着手。
1 提高出口处型材的强度在同一合金情况下,合金的温度越高,强度越低。
所以降低出口温度可以提高型材出口的强度,可通过以下方式:1.1 降低棒温尽量用较低的棒温挤压.1.2 提高铝棒的塑性,即挤压性能铝棒的塑性越好,挤压的变形力越少,挤压过程的温升越少。
铝棒的塑性主要受合金成份,含渣,含气量,均匀化状态影响,同一条件下,成份越低越好挤,工艺一 定的情况下,含渣含气量主要受原材料的影响,废料越多越差,尤其是氧化皮越多的废料,杂质含量也会使铝棒的塑性降低,有些特别难挤压的模具用全部铝锭做的 棒较好。
1.3 降低挤压速度降低挤压速度是减少毛刺最有效的方法,但会影响产量,最好根据每个型号模具制定合理的速度范围,有些模具要加速以提高产量,有些模具要减速以保证表面质量。
1.4 提高模具的加工精度,合理设计减少铝棒通过模孔的阻力,减少温升,另外同样的型材,采用小一级的棒径的模挤压,降低挤压比(比如:1800T转880T挤压),对减少毛刺相当有效。
2 减少型材与定径带之间的摩擦力(1)提高定径带的表面光洁度。
(2)采用先进的氮化工艺及设备,提高氮化层的硬度和耐磨性。
(3)建立完善的保养制度,每个模挤压到—定数量要重新氮化。
(4)有条件可采用模具通氮冷却。
纵上所述,解决毛刺是一个系统问题,只有熔铸、挤压、模具水平的不断提高,才能逐步减少毛刺的发生。
影响挤压型材表面颗粒形成的因素研究

影响挤压型材表面颗粒形成的因素研究发布时间:2021-01-27T09:41:19.860Z 来源:《基层建设》2020年第26期作者:傅小华[导读] 摘要:采用单因素试验法分别探究了模具钢种类和6063均质棒对挤压型材表面颗粒形成的影响,结果表明,本厂的模具材质对表面颗粒形成的影响不明显,并且使用6063均质棒的方法也未能改善挤压型材的表面颗粒状况;模具挤压比的影响作用值得进一步研究。
佛山市三水凤铝铝业有限公司广东佛山市 528100摘要:采用单因素试验法分别探究了模具钢种类和6063均质棒对挤压型材表面颗粒形成的影响,结果表明,本厂的模具材质对表面颗粒形成的影响不明显,并且使用6063均质棒的方法也未能改善挤压型材的表面颗粒状况;模具挤压比的影响作用值得进一步研究。
关键词:建筑铝型材;表面颗粒;均质棒前言随着金属材料表面处理技术的发展,挤压铝型材可以加工的品种越来越多,同时对型材表面质量的要求也日益苛刻,其中毛刺颗粒是一种很常见的铝型材表面质量问题。
针对此问题,凤铝厂已创造了一个发明专利,名称为“一种铝型材挤压模具的液氮冷却方法及装置”,专利号CN201310069616,其改善产品质量效果很明显,但成本较高,只用于高端产品的制造工艺。
目前挤压车间推广使用氮气代替液氮并通入出料筒内,该工艺尚未成熟应用,只能降低一定量的颗粒,因此探究型材表面颗粒形成的原因具有很大的价值意义。
因此本论文结合本厂的实际情况,采用单因素试验法分别研究了模具钢和6063铸棒对挤压型材表面颗粒形成的影响。
1试验由于影响铝型材表面颗粒形成的因素较多,因此本试验尽可能地结合挤压车间实际生产情况进行单因素试验,根据现场经验选取合适的订单作为试验对象,以做到试验结果对生产有指导意义。
1.1模具材质试验选取两种不同牌号的模具钢作为模具的原材料,产品型号定为A00652,并以相同的制造工艺制作两套模具,编号是A00652-002和A00652-003,采用金相法和光谱法对模具钢的化学成分、非金属夹杂物以及调质后的显微组织进行分析。
论挤压毛刺的形成原因

表面毛刺的形成:挤压速度极限图中的新极限A.J. den Bakker, Nedal Aluminum, Utrecht, The Netherlands(荷兰)X. Ma, M2i Materials Innovation Institute, Delft, The Netherlands(荷兰)R.W. Werkhoven, TNO Science & Industry, The Netherlands(荷兰)M.B. de Rooij, University of Twente, Enschede, The Netherlands(荷兰)摘要:铝挤压材的表面质量常由不希望出现的产品缺陷特性所制约,如毛刺。
毛刺形成的关键区域在模具的工作带,在此处可分出粘性区和滑移区。
滑移区的长度可根据工作带的压力分布及摩擦行为进行计算。
在滑移区内,挤压制品上的铝会转移至模具表面。
基于毛刺的形成机理,创建了一种描述铝挤压产品表面质量的模型。
该模型计算了工作带表面铝瘤的形成,生长以及脱落。
其中重要的参数是工作带的微观几何形貌,铝合金特定行为,工作带上的压力分布,以及挤压参数,如挤出速度和挤压材的表面温度。
从AA6063实验室规模试验测量的结果表明:实际情况同模型符合性很好。
以表面质量图表的形式介绍了计算结果,而且还介绍了毛刺数的归一化计算曲线。
结合传统的挤压极限图,这些表面质量图表开启了一扇改进实际操作工艺的观察窗口。
简介:挤压极限图(见图解1)是表示无缺陷挤压安全操作边界的规定。
该工艺窗口一边由压力和达到适当的机械性能的限制线包围,另一边由表面缺陷开始产生的限制线包围,如模线多、撕裂等由热问题引起的缺陷。
在极限区内,可以避免这些缺陷。
从产品质量和生产效率考虑,最佳的操作条件的区域位于直线图中的“最高点”。
图1. 挤压极限图的图解说明表面毛刺的产生是同挤压制品质量要求相关的主要问题之一,但不是由现有的挤压极限图确定的一个缺陷特征。
- 1、下载文档前请自行甄别文档内容的完整性,平台不提供额外的编辑、内容补充、找答案等附加服务。
- 2、"仅部分预览"的文档,不可在线预览部分如存在完整性等问题,可反馈申请退款(可完整预览的文档不适用该条件!)。
- 3、如文档侵犯您的权益,请联系客服反馈,我们会尽快为您处理(人工客服工作时间:9:00-18:30)。
挤压铝型材表面颗粒状毛刺的形成原因与对策
一、颗粒吸附成因分析
1、挤压型材表面出现的颗粒状毛刺分为四种
1)、空气尘埃吸附,燃煤铝棒加热炉产生的灰尘、铝屑、油污及水份凝结成颗粒附着
在热的型材表面。
2)、铝棒中的杂质,如:精炼不充分遗留的金属夹杂物和非金属夹杂物。
3)、时效炉内的灰尘附着。
4)、铝棒中的缺陷及成分中的β相AlFeSi在高温下析出,使金属塑性降低,抗拉强
度降低,产生颗粒状毛刺。
2、原因
1)、铝棒质量的影响
由于高温铸造,铸造速度快,冷却强度大,造成合金中的β相AlFeSi不能及时转变为球状α相AlFeSi,由于β相AlFeSi在合金中呈现针状组织,硬度高、塑性差,抗拉强度很低,在高温挤压时不仅会诱发挤压裂纹,而且会产生颗粒状毛刺,这种毛刺不易清理,手感强烈,颗粒附近常伴随有蝌蚪状拖尾,在金相显微镜下观察,呈现灰褐色,成分中富含铁元素。
铝棒中的杂质影响,铝棒在熔铸过程中,精炼不充分,泥土、精炼剂、覆盖剂以及粉末涂料和氧化膜夹杂等混入棒中,这些物质在挤压过程中,使金属的塑性和抗拉强度显著降低,极易产生颗粒状毛刺。
棒的组织缺陷常见的有疏松、晶粒粗大、偏析、光亮晶粒等,所有这些铸棒缺陷有一个共同点,就是与铸棒基体焊合不好,造成了基体流动的不连续性,在挤压过程中,夹渣极易从基体中分离出来,通过模具的工作带时,粘附在入口端,形成粘铝,并不断被流动的金属拉出,极易产生颗粒状毛刺。
2)、模具的影响
在挤压生产中,模具是在高温高压的状态下工作的,受压力和温度的影响,模具产生弹性变形。
模具工作带由开始平行于挤压方向,受到压力后,工作带变形成为喇叭状,只有工作带的刃口部分接触型材形成的粘铝,类似于车刀的刀屑瘤。
在粘铝的形成过程中,不断有颗粒被型材带出,粘附在型材表面上,造成了"吸附颗粒"。
随着粘铝的不断增大,模具产
生瞬间回弹,就会形成咬痕缺陷。
若粘铝堆积较多,不能被型材拉出,模具瞬间回弹时粘铝不脱落,就会形成型材的表面粗糙、亮条、型材撕裂、堵模等问题。
模具的粘铝现象见图1。
我们现在使用的挤压模具基本是平面模,在铸棒不剥皮的情况下,铸棒表面及内在的杂
质堆积在模具内金属流动的死区,随着挤压铸棒的推进及挤压根数的增多,死区的杂质也在不断的变化,有一部分被正常流动的金属带出,堆积在工作带变形后的空间内。
有的被型材拉脱,形成了颗粒状毛刺。
因此,模具是造成颗粒状毛刺的关键因素。
另外工模具表面的粗糙度越高、工作带表面的硬度越低,也是造成粘铝,形成颗粒状毛刺原因之一。
3)、挤压工艺的影响
挤压中发现,挤压工艺参数的选择正确与否也是影响颗粒状毛刺的重要因素。
经过现场观察,挤压温度、挤压速度过快颗粒毛刺就越多,原因温度高、速度快,型材流动速度增加模具变形的程度增加,金属的流动加快,金属的变形抗力相对减弱,更易形成粘铝现象;对大的挤压系数来说,金属的变形抗力相对增加了,死区相对增大,提高了形成粘铝的条件,形成"吸附颗粒"的概率增加;铸棒加热温度与模具温度之差过大,也易造成颗粒状毛刺问题。
4)、空气中的尘埃、水、油污等强烈附着于铝型材表面,原因是热的铝型材遇到灰尘
后粘附,发生化学反应并产生胶状物质,在时效过程中又与炉中的灰尘结合,生成较大的颗粒状毛刺,在随后的氧化、电泳、喷涂过程中不易清除。
二、减少颗粒状毛刺的措施
1、提高铝棒质量,从源头抓起,对于表面质量要求高的型材,铸棒过程中要清洗炉膛,优选原料和辅料,如喷涂型材再制品禁止进入,选用优质铝锭等,加强铸造工艺过程控制,防止铸造缺陷等,提高金属高温塑性,减少发生颗粒状毛刺的几率。
2、狠抓模具质量,优化模具结构设计,较少死区金属流入,提高模具强度和刚度,减少模具挤压形变,采取合理的氮化工艺,提高工作带硬度和提高抛光质量,减少金属粘附。
3、优化工艺参数,不同的铝合金成分和型材断面,根据铝合金挤压原理,采用合理的挤压工艺温度,对挤压速度进行分段控制,减少棒温和模温的温度差,增大挤压筒与棒温差,可以进一步减少死区金属流入和铸棒表面金属氧化物和夹杂流入,从而减少夹渣和毛刺的出现。
4、对所有工作现场采取“5S”现场管理,提高环境质量,对铸棒表面清理,较少灰渣灰尘附着,杜绝"跑冒滴漏",及时清理型材表面的灰尘,尽可能减少灰尘附着。