核燃料元件生产中化工转化工艺的评述
铀钚燃料循环的工艺

铀钚燃料循环的工艺铀钚燃料循环是一种核燃料循环方式,通过对铀和钚的利用,可以提高核能资源的利用率,降低核废料的产生以及减少电力生产过程中的环境污染。
下面是铀钚燃料循环的主要工艺流程:1. 铀矿石加工和浓缩:铀矿石是从地下采矿或露天矿开采中得到的矿石,其中铀的含量一般很低,需要进行加工和浓缩。
通常的浓缩方式是将矿石进行破碎、磨细,并采用化学方法将铀浓缩到可用的水平。
2. 铀燃料制备:铀燃料制备是将浓缩后的铀转化为可用于核反应堆的燃料形态。
一种常见的制备方法是将浓缩的铀氧化成U3O8,然后与氟化铵反应得到铀氟化物(UF6)。
接下来,UF6经过多次升降温和化学转化反应,最终得到UO2和U3O8。
3. 铀燃料在反应堆中使用:铀燃料制备完成后,将其装填到核反应堆中进行核裂变反应。
在反应堆中,铀核发生裂变,并释放出大量的热能,用于产生蒸汽驱动涡轮机发电。
4. 钚提取与分离:在反应堆中,铀核的裂变会释放出一小部分钚。
为了回收利用钚资源,可以采用多种方法将钚从废核燃料中提取出来。
一种常见的方法是将废核燃料溶解在硝酸溶液中,然后通过化学反应将其中的钚与其它元素分离。
5. 钚燃料制备:将从废核燃料中提取出来的钚与铀混合,制备成钚铀混合氧化物燃料(MOX)。
MOX燃料可以在反应堆中代替部分铀燃料使用,实现对钚资源的有效利用。
6. 钚燃料在反应堆中使用:钚燃料制备完成后,将其装填到核反应堆中进行核裂变反应。
与铀燃料类似,钚燃料在反应堆中也可以发生裂变,并释放出大量的热能,用于发电。
7. 利用后核废料的处理:核燃料在反应堆中使用后,产生的核废料具有高放射性和长寿命的特点。
通常采用深地层封存等方法,将核废料安全地处理和储存,以防止对人体和环境的伤害。
总之,铀钚燃料循环是一种通过对铀和钚的利用,提高核能资源利用率、减少核废料产生的核燃料循环方式。
通过铀矿石加工和浓缩、铀燃料制备、铀燃料在反应堆中使用、钚提取与分离、钚燃料制备、钚燃料在反应堆中使用等工艺步骤,可以实现对铀和钚资源的有效利用,为电力生产提供可持续、清洁的能源来源。
铀纯化转化工艺流程

铀纯化转化工艺流程引言铀是一种重要的核燃料,广泛应用于核能发电和核武器制造等领域。
铀纯化转化工艺流程是将天然铀经过一系列的物理和化学处理,提取出纯度较高的铀化合物的过程。
本文将详细介绍铀纯化转化工艺流程及其相关技术。
二级标题1:铀矿石的处理铀矿石是铀纯化转化工艺的起始原料,其主要包括天然铀矿石和次生铀资源。
铀矿石的处理主要包括矿石选矿、破碎、磨矿等步骤。
三级标题1:矿石选矿矿石选矿是将铀矿石中的有用矿物与非有用矿物进行分离的过程。
常用的选矿方法包括浮选、重选、磁选等。
通过选矿,可以提高铀矿石的品位,减少杂质的含量。
三级标题2:破碎和磨矿破碎和磨矿是将铀矿石进行粉碎的过程,以便于后续的提取工艺。
破碎通常采用颚式破碎机、圆锥破碎机等设备,磨矿则采用球磨机、砂轮磨机等设备。
破碎和磨矿的目的是将铀矿石细化到一定的粒度,提高提取效率。
二级标题2:铀的浸取铀的浸取是将破碎和磨矿后的铀矿石中的铀溶解到溶液中的过程。
常用的浸取方法有酸浸法、碱浸法和氧化浸法等。
三级标题1:酸浸法酸浸法是将破碎和磨矿后的铀矿石与酸性溶液进行接触,使铀溶解到溶液中。
常用的酸浸剂有硫酸、盐酸等。
酸浸法的优点是操作简单、反应速度快,但同时也存在酸性废液处理难等问题。
三级标题2:碱浸法碱浸法是将破碎和磨矿后的铀矿石与碱性溶液进行接触,使铀溶解到溶液中。
常用的碱浸剂有氢氧化钠、氢氧化铵等。
碱浸法的优点是溶液中铀的浓度较高,但同时也存在碱性废液处理难等问题。
三级标题3:氧化浸法氧化浸法是将破碎和磨矿后的铀矿石与氧化剂反应,使铀氧化成可溶性的铀酸盐,再将其溶解到溶液中。
常用的氧化剂有过氧化氢、高锰酸钾等。
氧化浸法的优点是无需使用酸碱,但同时也存在氧化剂的成本较高等问题。
二级标题3:铀的纯化和转化经过浸取后的含铀溶液中仍然含有杂质,需要进行纯化处理。
纯化过程主要包括铀的沉淀、溶液的过滤和浓缩等步骤。
三级标题1:铀的沉淀铀的沉淀是将含铀溶液中的铀与沉淀剂发生反应,形成沉淀物的过程。
核反应堆中的燃料循环
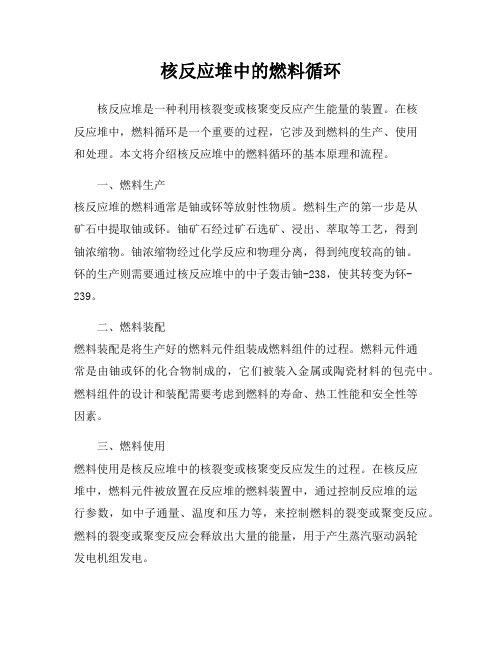
核反应堆中的燃料循环核反应堆是一种利用核裂变或核聚变反应产生能量的装置。
在核反应堆中,燃料循环是一个重要的过程,它涉及到燃料的生产、使用和处理。
本文将介绍核反应堆中的燃料循环的基本原理和流程。
一、燃料生产核反应堆的燃料通常是铀或钚等放射性物质。
燃料生产的第一步是从矿石中提取铀或钚。
铀矿石经过矿石选矿、浸出、萃取等工艺,得到铀浓缩物。
铀浓缩物经过化学反应和物理分离,得到纯度较高的铀。
钚的生产则需要通过核反应堆中的中子轰击铀-238,使其转变为钚-239。
二、燃料装配燃料装配是将生产好的燃料元件组装成燃料组件的过程。
燃料元件通常是由铀或钚的化合物制成的,它们被装入金属或陶瓷材料的包壳中。
燃料组件的设计和装配需要考虑到燃料的寿命、热工性能和安全性等因素。
三、燃料使用燃料使用是核反应堆中的核裂变或核聚变反应发生的过程。
在核反应堆中,燃料元件被放置在反应堆的燃料装置中,通过控制反应堆的运行参数,如中子通量、温度和压力等,来控制燃料的裂变或聚变反应。
燃料的裂变或聚变反应会释放出大量的能量,用于产生蒸汽驱动涡轮发电机组发电。
四、燃料处理燃料处理是核反应堆中燃料使用后的处理过程。
燃料使用一段时间后,燃料中的铀或钚会逐渐耗尽,同时产生大量的放射性废物。
燃料处理的目的是将燃料中的未耗尽的铀或钚回收利用,并处理掉放射性废物。
燃料处理的方法包括化学萃取、溶解、浸出等工艺,通过这些工艺可以将燃料中的铀或钚分离出来,用于再次生产燃料。
五、废物处理废物处理是核反应堆中产生的放射性废物的处理过程。
放射性废物包括燃料使用后的废燃料、燃料处理过程中产生的废液和废气等。
废物处理的方法包括固化、封存、贮存和处置等。
固化是将放射性废物转化为固体形式,通常是将其与玻璃或陶瓷等材料混合,形成固体块状物。
封存是将固化的放射性废物封装在耐久的容器中,以防止辐射泄漏。
贮存是将封存的放射性废物安全地存放在地下设施中,以待最终处置。
六、燃料循环的优势和挑战燃料循环的优势在于可以充分利用铀和钚等资源,延长燃料的使用寿命,减少对自然资源的依赖。
化学工程与化学工艺在能源领域中的应用

化学工程与化学工艺在能源领域中的应用化学工程与化学工艺在能源领域中扮演着重要的角色。
从能源生产到能源转化和利用,化学工程和工艺技术提供了许多关键的解决方案。
本文将介绍几个在能源领域中广泛应用的化学工程与化学工艺技术。
一、化学工程与化学工艺在石油工业中的应用1. 炼油过程石油炼制过程是将原油转化为各种有用产品的过程,其中包括汽油、柴油和航空燃料等。
化学工程与化学工艺在炼油过程中发挥了重要作用,例如催化裂化、重整和催化加氢等技术,可以提高石油产品的产量和质量,并减少废物和污染物的产生。
2. 裂解过程裂解是将石油或天然气等碳氢化合物分解为较小分子的过程,以产生乙烯等重要化学品。
通过炼油过程中的热裂解和催化裂解技术,可以大幅增加乙烯的产量。
从而,化学工程与化学工艺在石油工业中促进了乙烯等石化产品的生产。
二、化学工程与化学工艺在可再生能源领域中的应用1. 生物质能源转化生物质能源转化包括生物质燃烧、生物质气化和生物质液化等过程,旨在通过化学工程与化学工艺技术将生物质资源转化为可再生能源。
例如,糖类、纤维素和木质素等生物质组分可以通过气化和液化过程转化为生物质能源,用于发电和热能供应。
2. 太阳能电池太阳能电池是将光能转化为电能的装置,其中涉及到光催化剂、光电极和电解质等关键技术。
化学工程与化学工艺在太阳能电池的材料研发、器件设计和制造过程中发挥了重要作用,提高了太阳能电池的效率和稳定性。
三、化学工程与化学工艺在电池技术中的应用1. 锂离子电池锂离子电池是目前电动汽车和移动设备中广泛使用的能源储存装置。
化学工程与化学工艺在锂离子电池的正负极材料、电解质和电池制造等关键环节中发挥了重要作用。
通过优化电池材料和电极结构等技术,可以提高锂离子电池的能量密度和循环寿命。
2. 燃料电池燃料电池是一种将化学能转化为电能的装置,其中最常见的是氢燃料电池。
化学工程与化学工艺在燃料电池的催化剂、电解质膜和电池系统设计等方面发挥了重要作用。
中核建中:50春秋铸就我国“核电粮仓”美名扬

中核建中:50春秋铸就我国“核电粮仓”美名扬■ 本刊记者 曹福成 通讯员 杨显强 葛莉莎 林辉 高旭鹏50年前,为响应国家号召,一大批有志青年从祖国四面八方,来到大西南的金沙江畔、鸡爪山下。
他们艰苦奋斗,拼搏进取,创建中核建中核燃料元件有限公司(简称中核建中),拉开了军工报国的序幕。
如今,历经50载的风风雨雨,中核建中已成为以核电燃料元件为主导产业,兼营核级锆合金管材制造、精细化工生产、金属锂生产、锂电池制造等,集生产、科研和国内外贸易为一体的国有大型骨干企业,成为我国最大的压水堆核电燃料元件生产基地,为保障我国核电站安全稳定经济运行以及我国核电“走出去”战略落地做出了重要贡献,被誉为“核电粮仓”,成为支撑我国核能打天下的重要企业之一。
那么,中核建中是靠什么实现成功转型并取得如此辉煌业绩的?初夏时节,记者来到中核建中这个在“军转民”先期饱尝艰辛,依然忠诚于国家战略,矢志不渝建设国际一流核燃料元件制造基地,为支撑中国核电大发展屡立功勋,经营中创造了诸多奇迹的企业,探究个中奥秘。
核燃料是核电站运行的必备“口粮”,同时,核燃料元件是核电站运行的首道安全屏障。
核电的发展,离不开核燃料元件产业的支撑和助推。
建中人为推进国家核电发展战略的顺利实施拼搏奉献,只争朝夕地打造“核电粮仓”,创造了“建中速度”2015年5月6日,随着中核建中总经理丁建波宣布:“公司生产、制造的第10000组压水堆核电燃料组件下线”,在生产现场人员雷鸣般的掌声中,岗位操作人员启动翻转平台电动电钮,身披着大红花的“福清3.7%AFA3GZr-4燃料组件”——中核建中第10000组核电燃料组件徐徐升起,调入组件库。
“中核建中核电燃料组件生产迈入万组大关,是中核建中核燃料元件制造发展史上的又一重要里程碑,为中核建中建成国际一流核燃料元件制造基地打下了坚实的基础。
”丁建波对此倍感欣慰。
丁建波告诉记者,将天然铀打造成可供核电站使用的核燃料元件,要经历纯化和转化、同位素分离、燃料元件生产3个环节,任何1个环节生产能力不足,都将导致核电站“断粮”。
让中国核事业的“脊梁骨”挺起来拓展核燃料元件发展空间大有作为
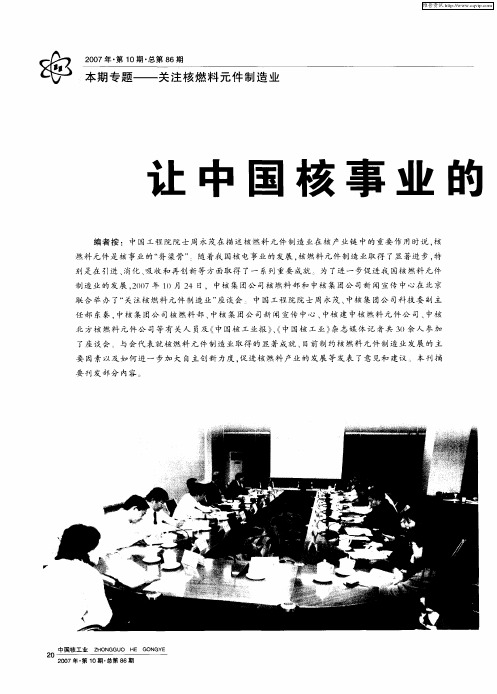
燃料 元件是核 事业 的“ 梁骨” 脊 :随着我 国核 电事业的发展 , 核燃料元件制造业取得 了显著进 步, 特
别是 在 引进 、 消化 、 收 和 再 创 新 等 方 面取 得 了一 系列 重要 成 就 :为 了进 一 步 促 进 我 国核 燃 料 元 件 吸 制 造 业 的发 展 ,0 7年 1 20 0月 2 4日 , 中核 集 团公 司核 燃 料 部 和 中核 集 团公 司新 闻 宣传 中心 在 北 京 联 合 举 办 了“ 注核 燃 料 元 件 制 造 业 ” 关 座谈 会 、中 国 工程 院 院 士 周 永 茂 、 中核 集 团公 司科 技 委 副 主
了座 谈 会 . 会 代 表 就 核 燃 料 元 件 制 造 业 取 得 的 显 著 成 就 、 .与 目前 制 约核 燃 料 元 件 制 造 业 发 展 的 主
要 因 素 以及 如 何 进 一 步加 大 自主 创 新 力度 , 进 核 燃 料 产 业 的发 展 等 发 表 了意 见 和 建议 .本 刊 摘 促
脊 梁 骨 " 起 来 挺
拓展核燃料元件发展空 间 大有作 为
中核 集 团公 司 燃 料 部 主 任 李 广 长
和 多数核大 国相似 , 国的核 燃料产业源于 国防建 我
设和军 工需要 。其创 业与成长发展是 中国核工业 5 0多 年来 的发展 历程 的缩影。 两弹一艇” “ 的研制成功离不开
2 0多年来 ,经过 引进技 术 、生产线 改造和科学 研
了市场 空间 ,发展 前景 看好 ,也 得 到 了社会 越 来越 多
的 关注 ,是 核 燃 料 元 件 制 造 业形 成 自我 发 展 的好 机
遇。
究、 再创新 , 国核 燃料元 件制造技 术 、 我 装备 、 管理水 平
燃料生产工艺有哪些

燃料生产工艺有哪些燃料生产工艺是指将原料转化为可燃燃料的一系列生产过程。
燃料是现代社会不可或缺的能源,它广泛应用于交通运输、工业生产、农业生产等领域。
以下是几种常见的燃料生产工艺。
1. 煤炭转化工艺:煤炭是最主要的化石燃料之一,通过煤炭转化工艺,可以将煤炭转化为液体燃料,如煤油和煤气。
常见的煤炭转化工艺包括煤直接液化(CTL)、煤气化及煤制合成气(CWS)技术等。
这些工艺可以利用煤炭资源,提高燃料能源的利用效率。
2. 石油提炼工艺:石油是目前主要的燃料资源之一,石油提炼工艺将原油中的各种组分进行分离和精制,生产出各种石油产品,如汽油、柴油、煤油和润滑油等。
常见的石油提炼工艺包括蒸馏、裂化、重整、脱硫、脱氮等。
3. 天然气液化工艺:天然气是一种重要的清洁能源,但在长距离和大规模运输方面存在困难。
天然气液化工艺将天然气通过降温和压缩的方式,将其转化为液态天然气(LNG),方便储存和运输。
液化天然气广泛用于液化石油气(LPG)、城市燃气、工业用气等领域。
4. 生物质转化工艺:生物质燃料是一种可再生能源,通过生物质转化工艺,将农作物秸秆、木屑、城市生活垃圾等生物质资源转化为生物燃料。
常见的生物质转化工艺包括焚烧、气化、发酵和液化等。
生物质转化工艺具有环保、可持续的特点,能够有效减少对化石燃料的依赖。
5. 核能发电工艺:核能是一种高效、清洁的能源,核能发电工艺利用核反应产生的热能,驱动蒸汽轮机发电。
常见的核能发电工艺包括核反应堆的建设和运行、核燃料的制备和重新加工等。
核能发电工艺具有高能量密度、低碳排放的特点,是一种可持续发展的能源。
以上是几种常见的燃料生产工艺,每种工艺都有其特定的原料、操作步骤和设备要求。
在工艺的选择和优化过程中,需要考虑资源利用效率、环境影响、经济可行性等因素,以实现燃料生产的可持续发展。
核工程中的燃料循环与核废料再利用研究

核工程中的燃料循环与核废料再利用研究核工程中的燃料循环与核废料再利用研究摘要:核工程是现代能源领域不可或缺的一部分。
然而,核能发电过程中产生的大量核废料一直是人们关注的焦点。
为了解决核废料问题并更好地利用核能资源,燃料循环和核废料再利用成为了研究的重点。
本论文将介绍核工程中燃料循环的基本原理和技术路线,并探讨核废料再利用的潜力和挑战。
通过对国内外相关研究成果的梳理和分析,本论文旨在为未来核能工程的发展提供借鉴和参考。
关键词:核工程、燃料循环、核废料再利用、放射性废料、可持续能源一、引言核能作为一种清洁、高效、可持续的能源形式,在世界各国广泛应用于电力生产、医疗、工业等领域。
然而,核能发电过程中产生的核废料一直是人们关注的焦点。
核废料的长寿命和放射性污染性质使其必须得到妥善处理,否则可能对人类和环境造成严重的影响。
为了解决核废料问题并更好地利用核能资源,燃料循环和核废料再利用成为了研究的重点。
二、燃料循环的基本原理和技术路线燃料循环是核工程中的关键环节,它涉及到核燃料的提取、制备、使用和废料处理等方面。
燃料循环的基本原理是通过对核燃料的回收和再利用,最大限度地提高核燃料的利用效率和核能资源的可持续性。
核燃料的提取是燃料循环的第一步。
目前主要采用的是钚-铀循环和铀-铀循环两种技术。
钚-铀循环通过对使用过的核燃料进行化学处理,提取出可以再利用的钚和铀。
铀-铀循环则是通过对自然铀进行提纯和浓缩,得到适合再利用的铀燃料。
核燃料的制备是燃料循环的第二步。
在核工程中,核燃料是以核燃料元件的形式使用的。
核燃料元件一般由铀或钚化合物制成,并通过化学、物理或冶金方法进行成型和加工。
制备好的核燃料元件可以直接用于核反应堆的运行。
核燃料的使用是燃料循环的第三步。
核燃料一旦放入核反应堆中发生核裂变反应,产生大量的能量和核废料。
在核废料问题得到妥善解决之前,核废料需要进行安全的贮存和处理。
同时,核燃料在使用过程中的变化和衰变也需要进行研究和监测。
5.1_核燃料后处理解析
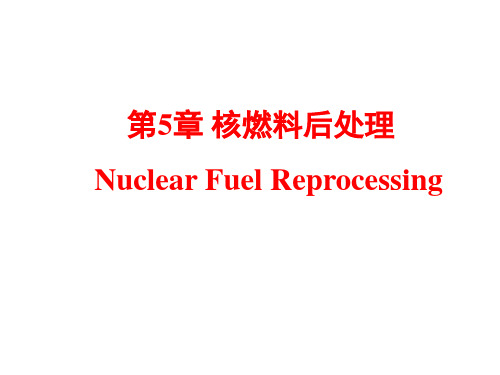
核燃料后处理是核燃料循环中的一个重要组成部分,同
时它又是军民两用技术。核工业中的地位和作用如下: 1. 后处理对于充分利用核能资源意义重大 ☞ 核电是我国能源的重要组成部分。对动力堆乏燃料进行后 处理,实现核燃料闭路循环,对充分利用铀资源、实现核 能可持续发展,起着举足轻重的作用。我国已探明的铀资 源量有限,且铀矿品位低、规模小,如果不搞后处理,铀 资源将会限制我国核能的发展。 ☞ 核燃料通过反应堆使用一次,只能利用燃料总量的极少 部分。生产堆仅用了千分之几,较先进的动力堆,燃料的 利用率也只有百分之几。
3. 化学分离过程
任务是除去裂变产物,高收率地回收核燃料物质。化学分
离流程分为水法和干法两大类:
☞ 水法流程指采用诸如沉淀、溶剂萃取、离子交换等在水 溶液中进行的化学分离纯化过程;
☞ 干法流程则指采用诸如氟化挥发流程、高温冶金处理、
高温化学处理、液态金属过程、熔盐电解流程等在无水状 态下进行的化学分离方法。 目前,工业上应用的后处理流程都是水法流程。历史上曾 采用沉淀法流程从辐照天然铀中提取核武器用钚。但不久
离较差,综合提取同位素较困难等,目前尚未被实际应用.
4. 尾端处理过程
经溶剂萃取分离和净化得到的硝酸钚或硝酸铀
酰溶液,无论在纯度或存放形式上有时还不能完
全满足要求,因而在铀、钚主体萃取循环之后, 还需要采取一些尾端处理步骤。其目的在于将纯
化后的中间产品进行补充净化、浓缩以及将其转
化为所需最终形态。
(3)高的技术要求和指标
核燃料后处理的主要目的是回收核燃料物质。 根据这些物质进一步加工的方式、方法的不同, 对净化有不同的要求。 一般都要求对经后处理回收的核燃料物质在进 行再加工时要能做到不需要昂贵的防护和远距离 操作设备。这就要求后处理过程具有高的净化系 数,如 107 ;高的铀钚分离系数,如 108 。从而得 到优质的铀、钚产品。这些都是远高于一般化工 分离过程的要求。此外,还要求对核燃料物质有 尽可能高的回收率。
核电站中的燃料循环过程详解
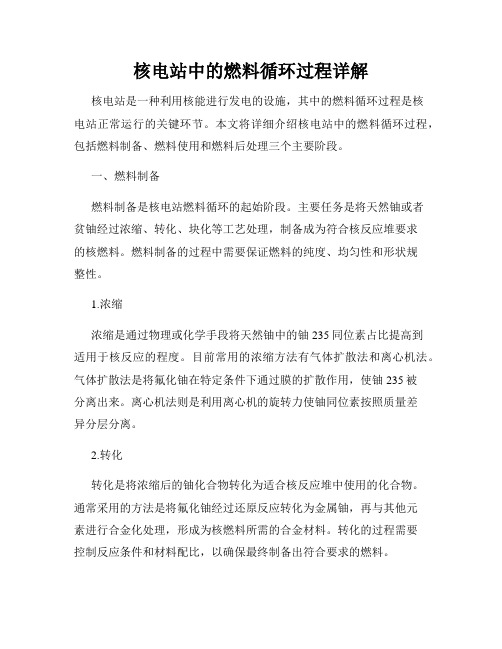
核电站中的燃料循环过程详解核电站是一种利用核能进行发电的设施,其中的燃料循环过程是核电站正常运行的关键环节。
本文将详细介绍核电站中的燃料循环过程,包括燃料制备、燃料使用和燃料后处理三个主要阶段。
一、燃料制备燃料制备是核电站燃料循环的起始阶段。
主要任务是将天然铀或者贫铀经过浓缩、转化、块化等工艺处理,制备成为符合核反应堆要求的核燃料。
燃料制备的过程中需要保证燃料的纯度、均匀性和形状规整性。
1.浓缩浓缩是通过物理或化学手段将天然铀中的铀235同位素占比提高到适用于核反应的程度。
目前常用的浓缩方法有气体扩散法和离心机法。
气体扩散法是将氟化铀在特定条件下通过膜的扩散作用,使铀235被分离出来。
离心机法则是利用离心机的旋转力使铀同位素按照质量差异分层分离。
2.转化转化是将浓缩后的铀化合物转化为适合核反应堆中使用的化合物。
通常采用的方法是将氟化铀经过还原反应转化为金属铀,再与其他元素进行合金化处理,形成为核燃料所需的合金材料。
转化的过程需要控制反应条件和材料配比,以确保最终制备出符合要求的燃料。
3.块化块化是将转化后的核燃料材料加工成为固定形状和尺寸的燃料块。
常用的方法有热压法和挤压法。
热压法是将燃料粉末加热至高温状态后,通过机械压力将其压制成块。
挤压法则是将燃料粉末通过挤压机挤压成块,然后再进行高温烧结。
二、燃料使用燃料制备完成后,燃料将被运送至核反应堆中进行使用。
燃料使用是核电站燃料循环的核心阶段,主要是指核燃料在核反应堆中进行核反应产生能量的过程。
在核反应堆中,燃料被装入到燃料元件中,燃料元件则组成了燃料组件。
在运行过程中,核反应堆中的燃料会通过核裂变反应释放出巨大的能量,同时产生中子。
这些中子将继续引发其他铀核的裂变,形成连锁反应。
通过控制反应堆中的中子速度和密度,可以实现核反应过程的稳定控制,保持核反应堆处于可控的状态。
三、燃料后处理燃料使用完毕后,核电站还需要对使用过的燃料进行后处理,以将其中的可再利用物质分离并回收,同时将产生的放射性废物进行处理和储存。
从第一条元件生产线到高性能组件国产化

料管理 方案 , 在进行先进核 燃料 管理项 目中采 用 四分之
一
换 料 方式 ,在 我 国核 电站 中首次 采 用全 M5燃 料组
件 。建 中公司 又开 始 了全 M 5燃料 组件 制造 技术 的 引
高 起点引进 。 实现 A A一 G高性 能组件国产 化 F 3 上世 纪 9 0年 代 初 ,建 中公 司 引 进 法 马 通 公 司
U O 粉末生产 线和含 钆燃料棒生产线 , 生产各类型 号压 水堆燃料组件 累计达到 3 0 4 0多组 ,产 品质 量达到 国际
同类产 品的先进水平 。
和含钆燃料棒 生产线的建设 , 并引进 了法马通 A A一 G F 3
高性 能燃料组件 设计与 制造技术 ,建成 了 A A 3 F 一 G燃 料组件 生产线 。通过对转让 的产品技术条件 、 技术 图纸
进。 为 A A 3 作 F 一 G的技术升级 , M5 A A 3 燃料组 全 F 一G 件 无疑是 当今世 界最为先进 的核 电燃料 元件之一 , 它完 全 能满足第三代核 电站对燃料组件的更高要求。 经过 一
中国核 工业 Z O G U H G N Y H NG O E O G E 20 年・ 1期・ 0 7 第 O 总第 8 6期 3 3
AA 2 F 一 G燃料组件设计 与制造技术 ,并制造 出高质量产
维普资讯
20 0 7年 ・ 1 第 0期 ・ 第 8 总 6期
本 期 专 题— — 关 注 核 燃 料 元 件 制 造 业
年 多的努力 。 M5 A A 3 的燃料组 件通过 了产 品合 全 F一G 格 性鉴定 , 现入堆运行半年多 , 各项 数据 良好。
的消化 , 建立 了适合企业 自身 的工艺体 系。
核工业工程中高级技术资格评审条件试行总则为客观

附件:核工业工程中、高级技术资格评审条件〔试行〕总则一、为客观公正地评价从事核工业工程技术人员的专业技术水平,鼓励科技人员钻研业务、多出成果、快出成果,促进我国核工业科学技术水平的提高和生产发展,结合核工业工程的特点,特制定本评审条件。
二、核工业工程中、高级技术资格的名称分别为工程师、高级工程师。
三、凡按本条件评审合格并获得相应技术 XX 书者,表明已具备担任相应专业技术职务的水平和能力,其职务与工资待遇由企事业单位根据国家有关规定自行确定。
四、核工业工程分为:核反应堆工程、核燃料循环、核技术应用、辐射防护与核安全等四个专业。
五、各专业的合用 X 围〔一〕核反应堆工程专业本专业评审条件,合用于从事下列工作的科研、设计、建造、生产、技术开发和成果推广等工程技术人员:1.各种核反应堆的物理、热工、水力、控制、化学化工、结构力学、材料与结构等;2.各种核反应堆与其内外实验装置的运行、生产管理;3.各种核反应堆与热能动力装置系统、专用设备和辅助设备;4.各种核反应堆工程建造与安装。
〔二〕核燃料循环专业本专业评审条件,合用于从事下列工作的科研、设计、生产、技术开辟和成果推广等工程技术人员:1.铀水冶技术、铀、钚、锂冶金与核部件成型工艺等核冶金技术;2.铀化合物的制备与转换、锂化合物制备成型工艺等放射化工、铀化工;3.同位素分离与其设备与工艺;4.反应堆核燃料元件与组件、裂变核部件、聚变核部位、特种结构部件等材料加工技术与核部件连接与装配工艺技术;5.核燃料生产过程的控制与检测、分析以与放射化工材料的专用设备;6.乏燃料后处理与核废物处理与处置;7.核燃料生产设施。
〔三〕核技术应用专业本专业评审条件,合用于从事下列工作的科研、设计、生产、技术开辟和成果推广、运行等工程技术人员:1.各种加速器与等离子体设备的工程技术;2.各种同位素与其制品的生产与应用技术;3.辐照在工、农、医、生物等行业中的开辟应用;4.各种专用核设备、核仪器与核探测器的研制生产。
浅谈核燃料后处理_林灿生
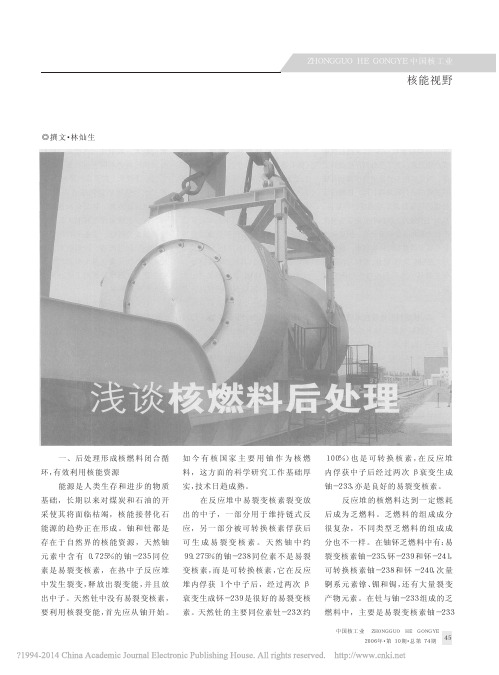
素含量大, 放射性比活度高, 燃料 元件的结构也不同于生产堆, 因此 在后处理技术上有更高的要求。如: 更严密的辐射防护和核临界安全, 工艺过程远距离、自动化和连续操 作, 减少机械操作过程和实现最少 维修量或免维修, 设备和材料耐腐 蚀和抗辐射性能强, 次量锕系元素 和裂变产物元素含量大引起的相关 效应及其去污难度等对工艺分离流 程也有新的要求。
中国核工业 ZHONGGUO HE GONGYE
2006 年·第 10 期·总第 7Байду номын сангаас 期 45
2006 年·第 10 期·总第 74 期
核能视野
和可转换核素钍- 232 以及相应的裂 年 宣 布 停 止 核 燃 料 后 处 理 。 而 俄
变产物元素。为了充分利用核燃料资 ( 苏) 、英、法、日、印仍然坚持后处理,
纪来显示出很强的通用性和生命 国家对钍铀燃料循环给予足够的重
核能的可持续发展, 需要充足
力, 当然该流程也存 在缺 点 和 局 限 视, 对钍燃料 在 CANDU 堆 、轻 水 增 的核燃料。为了更 有效地 利 用 铀 钍
性。随着反应堆技术的进步, 燃料元 殖 堆 、快 中 子 增 殖 堆 、高 温 气 冷 堆 、 资源, 必须形成核燃料闭合循环。为
比 动 力 堆 乏 燃 料 后 处 理 也 相 对 低 乏燃料后处理厂。
些。我国于上世纪 60 年代研究和开
发的生产堆核燃料后处理工艺流
三、我国后处理科研中应关注
程, 在当时是比较先进的, 满足了我 的问题
国武器级钚生产的要求, 也为后处
1. 突出重点, 满足建造大型后
理工厂的设计和建造积累了经验。 处理厂的急需
产物元素和次量锕系元素, 提取和纯 成UP2- 800, 主要用于处 理 轻 水 堆
核燃料加工流程
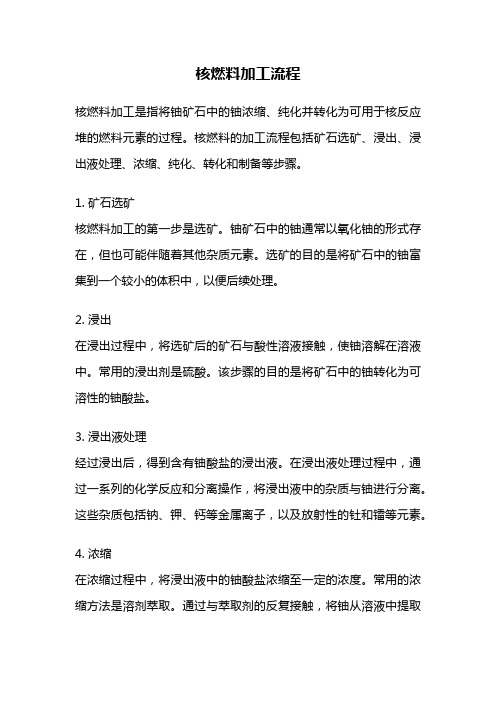
核燃料加工流程核燃料加工是指将铀矿石中的铀浓缩、纯化并转化为可用于核反应堆的燃料元素的过程。
核燃料的加工流程包括矿石选矿、浸出、浸出液处理、浓缩、纯化、转化和制备等步骤。
1. 矿石选矿核燃料加工的第一步是选矿。
铀矿石中的铀通常以氧化铀的形式存在,但也可能伴随着其他杂质元素。
选矿的目的是将矿石中的铀富集到一个较小的体积中,以便后续处理。
2. 浸出在浸出过程中,将选矿后的矿石与酸性溶液接触,使铀溶解在溶液中。
常用的浸出剂是硫酸。
该步骤的目的是将矿石中的铀转化为可溶性的铀酸盐。
3. 浸出液处理经过浸出后,得到含有铀酸盐的浸出液。
在浸出液处理过程中,通过一系列的化学反应和分离操作,将浸出液中的杂质与铀进行分离。
这些杂质包括钠、钾、钙等金属离子,以及放射性的钍和镭等元素。
4. 浓缩在浓缩过程中,将浸出液中的铀酸盐浓缩至一定的浓度。
常用的浓缩方法是溶剂萃取。
通过与萃取剂的反复接触,将铀从溶液中提取出来,并使溶液中的铀浓度得到提高。
5. 纯化在纯化过程中,对浓缩后的铀酸盐进行纯化处理,以去除残余的杂质。
常用的纯化方法包括溶剂萃取、离子交换和溶剂萃取等。
这些方法可以有效地去除溶液中的杂质,使铀的纯度达到要求。
6. 转化在转化过程中,将纯化后的铀酸盐转化为可用于核反应堆的燃料元素。
常用的转化方法是将铀酸盐与氯化镁反应,生成铀四氯化物。
然后,通过还原反应将铀四氯化物转化为金属铀或铀氧化物。
7. 制备在制备过程中,将转化后的铀氧化物或金属铀进行成型,以便于使用。
常见的制备方法包括压制和烧结。
通过将铀粉末或颗粒进行压制,使其成型为燃料棒或燃料片。
然后,通过烧结过程将颗粒状的铀烧结成致密的块体。
通过以上步骤,核燃料加工流程将铀矿石中的铀转化为可用于核反应堆的燃料元素。
这些燃料元素经过进一步处理和装配后,将用于核电站或核武器等应用中。
核燃料加工过程需要严格的工艺控制和质量保证,以确保燃料的安全可靠性。
铀化工干法转换技术简析

1 . 试 验 原 理 分 析
采用 I D R ( 1 n t e g r a t e d D r y R o u t e ) I艺, 在一 台转换 装置 中将 u F 6 转 化为 U O : 粉末 , 总的化学反应方程式如下 :
U F 6 ( g ) + 2 t { 2 0( + H d g ) - -  ̄ U O d s ) + 6 HF ( g ) u F 6 气体 、 水蒸汽在反应室内进行气相水解 , 得到 U O Y: 微粒 , 与H 、
2 0 1 5 年l 5 期
科技 一向导
◇ 科技之窗◇
铀化工干法转换技术简析
张 超 何广 昌 ( 中国核电工程 有限公 司郑州分公司核工程研究设计所
【 摘
河南
郑州
4 5 0 0 0 0 )
要】 介绍 了铀化工干法转换技术 ( I D R ) 的试验原理 、 工 艺流程 . 以及 1 0 0 吨铀/ 年规模干法转化工 艺( G F X一 1 0 0型) 的关键设备和运行
效果 , 突显 了干 法 转 换技 术相 对 湿 法转 换 技 术的 优 越 性 。
【 关键词 】 铀化工干法转换技术 ( I D R ) ; G F X — 1 0 0 型; 优越性
0 . 前 言
“ 十二五 ” 以来 , 根据 国家最新 发布 的《 核 电中长期发展 规划》 , 在 “ 安全 、 高效” 思路 的指导下 , 到2 0 2 0年我 国的核 电总装机容量可望增 加至 5 8 0 0 万 千瓦… 。 这无 疑对我国核燃料元件产量的提升和工艺技术 升级提出了迫切要求 因此 , 为了保证 “ 十二五 ” 以后我 国核 电站对核燃料元件用 U O , 粉 末的需求 ,就需 要在干法生产 线关键的化 工转 换工艺装置 上实现突 破。 中国核电工程有限公 司郑州分公 司( 原核工业第五研究设计院 . 以 下简称郑 州分公司 ) 与 中核建 中核燃料元件 有限公 司f 以下 简称 8 1 2 厂) 在“ 十一五” 初期提 出了联合开展干法 生产线 的关 键系统一铀化工 干法转换装置和相应 工艺的研究
核燃料循环重点

另外还有:分离锶铯的有 CCD-PEG 流程;用冠醚分离锶的 SREX 流程;用杯冠化合物 直接萃取铯的 CSEX 流程。
第四类后处理技术有: 主要采用的是干法后处理技术。主要用于在水溶液中难以溶解的辐照燃料及靶件、金属
元件快堆乏燃料中锕系元素的回收分离。 主要有以下二种方法: 1) 氟化物挥发法: 铀钚的六氟化物易挥发,且有合适差异的沸点。在对铀附加净化 后对裂片元素的去污系数和铀钚分离系数接近水法。可以处理金属或氧化物燃料元 件,尤其适合于熔盐堆的在线后处理。 2) 熔盐电解法:美国的金属锂还原熔盐电解精炼流程;俄罗斯的金属氧化物电沉积流 程。
废物处理与处置的基本原则:(希望大家帮忙找答案)
对反射性废水处理原则是:稀释排放、浓缩贮存和回收利用。
对放射性废气处理原则是:
对反射性固体废物处理原则是:
9-2:放射性废水处理技术有哪些?(书 P204)
答:反射性废水处理技术有:
1) 凝聚沉淀:是一种化学处理方法,其过程是往废水中加入某些称为凝聚剂的化学物质, 使废水中的胶体状物质聚集成细小的可沉淀颗粒,颗粒与颗粒或与废水中的悬浮状物质 组合成绒粒,绒粒具有很大的比表面积和吸附能力,吸附更多的溶质形成絮状物。经过 澄清和机械过滤,将沉淀从水中分离。
件也有关以及悬浮物的组成合燃料及形态。
另外一种答案: 1) 乏燃料溶解液的预处理,除去溶解液中的固体颗粒; 2) 调整酸度以满足高酸流程或低酸流程的要求 3) 调整铀浓度 4) 调整钚的价态,以使铀钚分别处于易于被 TBP 萃取的 U(VI)和 Pu(IV)。
第五章 铀钚共去污—分离循环
5-2:铀钚共去污—分离工艺过程。(书 P101) 答:铀钚共去污—分离循环包括铀钚共萃取共去污、铀钚分离、铀的反萃三个单元操作。其 中萃取净化过程包括萃取、洗涤、反萃三个单元操作。 PS:所对应的框图是在课本 P102,大家自己画。 5-6:铀和钚分离原理是什么?(书 P111) 答:实现铀钚分离原理是:选择合适的还原反萃剂,将钚由 Pu(IV)还原到不被 TBP 萃取 的 Pu(III),使钚从有机相转入水相,而铀仍以铀(VI)保留在有机相中,从而实现铀与钚 的分离。 5-7:第三代、第四代后处理技术有哪些?(PPT) 答:第三代后处理有:
加氢裂化工艺特点
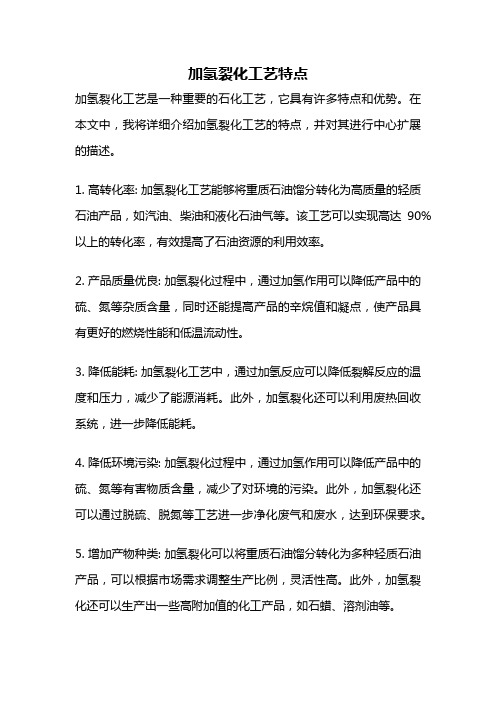
加氢裂化工艺特点加氢裂化工艺是一种重要的石化工艺,它具有许多特点和优势。
在本文中,我将详细介绍加氢裂化工艺的特点,并对其进行中心扩展的描述。
1. 高转化率: 加氢裂化工艺能够将重质石油馏分转化为高质量的轻质石油产品,如汽油、柴油和液化石油气等。
该工艺可以实现高达90%以上的转化率,有效提高了石油资源的利用效率。
2. 产品质量优良: 加氢裂化过程中,通过加氢作用可以降低产品中的硫、氮等杂质含量,同时还能提高产品的辛烷值和凝点,使产品具有更好的燃烧性能和低温流动性。
3. 降低能耗: 加氢裂化工艺中,通过加氢反应可以降低裂解反应的温度和压力,减少了能源消耗。
此外,加氢裂化还可以利用废热回收系统,进一步降低能耗。
4. 降低环境污染: 加氢裂化过程中,通过加氢作用可以降低产品中的硫、氮等有害物质含量,减少了对环境的污染。
此外,加氢裂化还可以通过脱硫、脱氮等工艺进一步净化废气和废水,达到环保要求。
5. 增加产物种类: 加氢裂化可以将重质石油馏分转化为多种轻质石油产品,可以根据市场需求调整生产比例,灵活性高。
此外,加氢裂化还可以生产出一些高附加值的化工产品,如石蜡、溶剂油等。
6. 提高石油加工利润: 加氢裂化可以将低价值的重质石油馏分转化为高价值的轻质石油产品,提高了石油加工的经济效益。
此外,加氢裂化还可以降低产品中的硫、氮等有害物质含量,符合环保要求,有助于企业提升形象和竞争力。
7. 技术成熟: 加氢裂化是一种成熟的石化工艺,在工业应用中已经有数十年的历史。
相关的设备和工艺技术已经非常成熟可靠,具有较高的操作稳定性和安全性。
加氢裂化工艺具有高转化率、产品质量优良、降低能耗、降低环境污染、增加产物种类、提高石油加工利润和技术成熟等特点。
这些特点使得加氢裂化工艺成为石油加工行业中不可或缺的工艺之一,对于提高石油资源利用率、改善环境质量和促进经济可持续发展具有重要意义。
化工变换工艺总结

化工变换工艺总结引言化工变换工艺是指将某种物质通过化学反应或其他过程转变为另一种物质的工艺过程。
化工变换工艺在化工行业中广泛应用,包括有机合成、无机合成、催化反应、蒸馏、萃取等等。
本文将对化工变换工艺进行总结,包括其定义、分类、基本原理、应用领域等。
定义化工变换工艺是指通过物质的化学反应或其他过程,将原始物质转变为所需物质的工艺过程。
化工变换工艺广泛应用于化工行业,是化工生产的核心环节之一。
化工变换工艺的目的是通过改变物质的结构或组成,实现物质的转化和加工。
分类根据不同的工艺和反应方式,化工变换工艺可以分为多种类型。
有机合成有机合成是指利用有机化学方法将低价的原始材料,如石油、天然气等,通过有机合成反应转化为高价值的化学品的工艺过程。
有机合成在药物、精细化学品、涂料等行业有着广泛的应用。
无机合成无机合成是指将无机物质通过化学反应转化为其他无机物质的工艺过程。
无机合成在玻璃制造、陶瓷制造、金属加工等行业中起着重要的作用。
无机合成工艺包括熔融法、溶液法、气相法等多种方法。
催化反应催化反应是指通过催化剂的作用,加速化学反应速率的工艺过程。
催化反应广泛应用于石油化工、化学肥料、化工塑料等行业。
常见的催化反应包括氧化反应、加氢反应、裂解反应等。
分离工艺分离工艺是指通过物理或化学方法,将混合物中的组分分离出来的工艺过程。
分离工艺在化工生产中起着重要的作用,包括蒸馏、萃取、结晶、吸附等方法。
基本原理化工变换工艺的基本原理是通过控制反应条件、选择适当的催化剂和采用合适的工艺参数,实现物质的转化和加工。
化工变换工艺中的关键步骤包括物料的混合、反应的进行和产物的分离等。
化工反应的基本原理包括反应动力学、热力学、传质和传热等。
反应动力学研究反应速率和反应机制,热力学研究反应的热效应和平衡常数,传质和传热研究物料在反应过程中的质量传递和热量传递。
应用领域化工变换工艺在各个领域都有广泛的应用,包括能源、石油化工、化学制药、冶金、环保等行业。
化工流程中的能量转化与原料利用率

化工流程中的能量转化与原料利用率在化工流程中,能量转化与原料利用率是至关重要的因素。
优化这些过程可以提高生产效率,降低成本,并减少资源浪费。
本文将探讨化工流程中能量转化与原料利用率的关系,以及如何通过技术和策略来提高它们。
化工流程中的能量转化主要涉及能源的消耗和产生。
化工生产通常需要大量的能量,包括热能、电能和化学能。
优化能源利用可以降低生产成本,并减少对环境的负面影响。
一种常见的做法是采用高效能源转换技术,如余热利用系统和节能设备。
此外,优化生产过程的布局和操作也可以减少能量损失。
原料利用率是衡量生产过程效率的重要指标。
高原料利用率意味着更少的废物产生,减少了对原料资源的需求,并降低了生产成本。
在化工流程中,提高原料利用率的方法包括优化生产工艺,提高反应物的转化率,以及改进废物处理和回收技术。
例如,通过催化剂的使用可以促进反应物的选择性转化,减少副产物的生成,从而提高原料利用率。
另一个影响能量转化和原料利用率的因素是生产设备的性能和状态。
定期维护和优化设备可以保持其高效运行,并减少能量损耗和生产中断。
同时,采用先进的监控和控制系统可以实时监测生产过程,并及时调整操作参数以优化能量转化和原料利用率。
除了技术方面的改进,管理策略也对能量转化和原料利用率的提高起到关键作用。
制定有效的生产计划和供应链管理策略可以确保原料的及时供应和合理利用,从而降低废料和库存的浪费。
此外,培训员工并建立良好的生产实践和文化也是提高能量转化和原料利用率的重要举措。
综上所述,化工流程中的能量转化与原料利用率密切相关,对于提高生产效率和降低成本具有重要意义。
通过技术创新、设备优化和管理策略的综合应用,可以实现更高水平的能量转化和原料利用率,为可持续发展做出贡献。
核反应堆燃料的回收与再利用技术

核反应堆燃料的回收与再利用技术咱今天就来唠唠核反应堆燃料的回收与再利用技术。
你说这核反应堆燃料的回收和再利用,听起来是不是感觉特别高大上,好像离咱们日常生活特别遥远?其实啊,这事儿跟咱的生活还真有着千丝万缕的联系。
我记得有一次,我去一个核电站参观。
那可是个严格管理的地方,进去之前各种安检、培训,搞得我紧张兮兮的。
等终于进去了,看到那巨大的核反应堆设施,心里那叫一个震撼。
当时有个工作人员给我们讲解,他说这核反应堆燃料用过之后,如果直接扔掉,那可太浪费,而且还可能对环境造成污染。
所以就得想办法把里面还有用的东西给回收再利用起来。
那这回收和再利用到底是咋回事呢?简单来说,就好比咱们家里的东西,能用的咱就接着用,不能用的咱想办法改造改造再用。
核反应堆燃料也是这个道理。
先来说说回收。
用过的核燃料里面,其实还有不少有价值的东西,比如铀和钚。
这就需要通过一系列复杂的化学和物理过程把它们给提取出来。
这过程可不容易,得在特殊的工厂里,由专业的人员操作那些精密的设备。
然后是再利用。
把回收来的铀和钚经过处理,又能重新放回核反应堆里发挥作用。
这就好比给核反应堆来了个“二次生命”。
这技术的好处可多了去了。
首先,能节省资源啊。
核燃料可不是随随便便就能得到的,回收再利用能让有限的资源发挥更大的作用。
其次,减少了核废料的产生,对环境保护那是相当重要。
不过,这事儿也不是一帆风顺的。
回收和再利用的过程中,技术要求特别高,稍有不慎就可能出问题。
而且成本也不低,需要大量的资金和人力投入。
但是,人类的智慧是无穷的。
为了能更好地利用核能,科学家们一直在努力研究和改进这些技术。
说不定在未来的某一天,核反应堆燃料的回收与再利用技术会变得更加高效、更加安全、更加普及。
就像我那次参观完核电站,虽然对很多专业的东西还是一知半解,但我深深地感受到,科技的发展就是在不断地解决问题、突破难关,让我们的生活变得更美好。
而核反应堆燃料的回收与再利用技术,就是这科技发展道路上的一个重要探索。
- 1、下载文档前请自行甄别文档内容的完整性,平台不提供额外的编辑、内容补充、找答案等附加服务。
- 2、"仅部分预览"的文档,不可在线预览部分如存在完整性等问题,可反馈申请退款(可完整预览的文档不适用该条件!)。
- 3、如文档侵犯您的权益,请联系客服反馈,我们会尽快为您处理(人工客服工作时间:9:00-18:30)。
核燃料元件生产中化工转化工艺的评述
吴忠俭
核工业第五研究设计院 450052
摘要:本文对核燃料元件生产中三大化工转化工艺作了评述,系统介绍了IDR工艺的优点,提出了我国今后建厂所采取的工艺路线及现有ADU生产线的利用,并对IDR工艺中所存在的问题提出了建议。
关键词 核燃料 化工转化 IDR工艺 建议
1 前言
在核燃料生产中,铀化合物转化加工占有很大的比重。
一般来讲,铀矿石水法冶金和纯化精制是获取核纯物料的手段。
但从上述过程中制得的铀化合物的物理、化学性质和核性能尚不能适于核裂变的应用,必须经过化学转化加工,为生产金属铀和铀同位素分离提供适宜的铀化合物。
目前绝大多数核动力反应堆都是采用不同加浓度的铀,所以二氧化铀是生产合乎要求的二氧化铀燃料的重要原料,并且世界各国均随着我国核电事业及其它核动力的发展,对核燃料二氧化铀的需求量越来越大。
大家知道,在压水堆核燃料元件生产中,首先必须把含有一定富集度的UF6转化为符合要求的陶瓷级UO2粉末。
UO2粉末的性能决定了化工转化工艺。
当今世界上,压水堆核燃料化工转化工艺,用于生产实践的,主要有三种,即ADU工艺,AUC工艺及IDR工艺。
ADU工艺是世界上发展最早的湿法工艺,随后西德研究并使用了AUC湿法工艺。
IDR工艺是由英国的核燃料公司(BNFL)研究成功并首先使用的一种干法工艺,英国于1971年在斯普林菲尔德厂建造了世界上第一条IDR工艺生产线投入运行,并取代了该厂原来采用的ADU工艺生产线。
1975年法国-比利时核燃料公司(FBFC)引进了该项专利,在法国的罗芒建立了IDR工艺生产线,也取代了该厂原来采用的ADU工艺生产线。
法国在吸收、
消化英国IDR工艺的基础上,发展了自己的IDR工艺,在法国的皮尔拉特建造了CFC工厂,并于1984年投产运行。
后来,美国的西屋电气公司也从英国购买了该项技术。
南非也在借鉴法国干法技术的基础上,建立了自己的干法生产线。
目前,多个核技术国家采用了IDR工艺。
2 核燃料元件生产中化工转换的三大流程
2.1 重铀酸铵(ADU)工艺流程
从六氟化铀生产二氧化铀的重铀酸铵工艺是发展得最早的、比较成熟的典型工艺。
ADU湿法工艺是由原料六氟化铀(UF6)经气化、水解生成氟化铀酰(UO2F2),后经氨水沉淀生成重铀酸铵(ADU),最后经干燥、分解、还原制得陶瓷级UO2粉末。
能处理生产过程中产生的各种不合格返料是该工艺的一大优点。
2.2 三碳酸铀酰铵(AUC)工艺流程
三碳酸铀酰铵工艺是另一个比较典型的湿法流程。
该工艺是把气态的六氟化铀(UF6)与氨气、二氧化碳气同时通入水中,经反应而生成三碳酸铀酰铵(即AUC)晶体,再经过滤、分解还原而制得陶瓷级二氧化铀粉末。
与ADU工艺相比,该流程具有流程短、生产量较大、所得AUC具有晶体结构,组分单一,芯块压制前不需制粒,再现性好,最终产品成品率高等优点,但其废液回收处理系统较复杂。
2.3 综合干法(IDR)工艺流程
综合干法流程即转炉干法流程,该工艺是把气态的六氟化铀与水蒸汽、氢气加入到一个回转式的反应炉中,在该设备内进行水解、还原而制得陶瓷级的UO2粉末。
IDR流程与ADU、AUC等湿法流程相比,具有流程短、生产量大、设备结构简单、不产生废液、尾气中的氟化氢气体可以回收利用、环境污染少等优点。
但IDR工艺只局限于用六氟化铀作为原料的转化,不能处理生产过程中产生的
各种不合格返料。
3 IDR流程的优点
ADU、AUC和IDR三大流程各有优缺点,但总的来说,IDR流程在许多方面具有明显的优越性。
3.1 IDR流程生产线短,成本低。
湿法中的ADU流程,其主工艺生产线需经过气化、水解、沉淀、过滤、干燥、还原及稳定化等工序才能生产出合格的二氧化铀粉末,而IDR流程只需一步便可制得二氧化铀粉末,这使得生产线得以大大缩短。
采用干法IDR流程,使得工程总投资与湿法相比有明显的降低,生产运行成本得以下降,这就使得IDR流程在激烈的市场竞争中具有强大的生命力。
3.2 IDR流程污染小
IDR流程由于主工艺是干法生产,没有液相过程,故不会产生废液。
在工艺尾气处理回收系统会产生一定量的氢氟酸液体。
只要操作正常,氢氟酸液体中的放射性剂量水平就不会偏高,这样的氢氟酸液体就可以做为副产品出售,得以综合利用。
3.3IDR流程生产能力大。
IDR流程主要由关键设备转炉等设备构成, 当转炉的直为10英寸时,生产能力为75吨铀/年,当转炉的直为16英寸时,生产能力可达200吨铀/年。
3.4产品性能好、成品率高。
由于在IDR转炉中产生的HF是气态,比湿法工艺产生的液态的HF对设备腐蚀小,使得产品中杂质金属含量低。
产品由于比表面小(2-3m2/g),性能稳定,抗氧化性能好,存放时不被氧化,同时吸湿性低(0.2%),粉末对大气湿度没有要求。
UO2粉末的压块成型性能好,烧结性能好,芯块质量好。
其优良的产品性能,为制造高性能的燃料元件创造了有利条件。
3.5过程容易控制,临界安全性好。
整个过程在一个转炉内完成,连续进料及出料,操作简单,容易控制易于实现及提高自动化水平。
生产过程中无液相,临界安全性好,可以减少或免除湿法生产中由于确保临界安全而采取的种种措施而带来的复杂性及付出的昂贵代价。
4 我国核燃料元件生产中化工转化生产工艺的现状
按照中国政府有关部门对核电发展规划的初步设想,在未来的16年里,中国核电装机容量占全国电力总装机容量的比重将由目前的1.6%增至4%,也就是,到2020年,中国核电装机容量将达到3600万千瓦。
这个规划意味着,从2004年起,中国每年将至少批准建设两个百万级核电机组,即意味着中国今后16年每年都要建一座“大亚湾”。
核电站的快速发展,是必要扩大核燃料元件的生产能力。
而我国目前的组件制造生产线已无法满足核电发展需要,因而必须对其进行改造和扩大规模。
虽然我国已掌握了一套湿法ADU流程生产工艺,国内核燃料元件厂目前化工转化工艺均为ADU流程生产工艺,但由于ADU流程自身的缺点和不足,不宜再上新的ADU生产线。
根据化工转换技术的发展以及我们所了解的有关技术资料,目前多个核技术国家采用了IDR工艺。
我国也关心此项技术,自1983年后,多次派出考察团到英、法等国有关厂进行考察 ,并多次邀请英、法等国专家来华介绍、座谈以及洽谈引进该项技术问题,通过考察及技术洽谈,我国对IDR工艺有了较多的了解,并获得了一些技术资料。
5 结论和建议
5.1 随着我国核电建设的快速发展,相应的核燃料元件生产也将逐渐扩大生产规模。
IDR流程工艺简单、生产能力大,产品质量稳定;过程连续,操作简单,工艺参数容易控制;流程对环境污染小,剂量防护问题易解决。
IDR工艺的采用
及完善,对我国核燃料技术的提高及生产成本的降低将起着重大的推动作用,具有十分重要的意义。
该工艺路线是我国核燃料元件生产中化工转化的发展方向,在新建核燃料元件生产厂中应大力推广采用。
在我们已经掌握ADU流程的基础上,并结合我们的实际情况,把原有的湿法ADU生产线经局部调整、配套完善后,作为我国干法生产厂的化工回收设施。
5.2 针对引进IDR工艺及设备所存在的问题,结合我国的实际情况,必须补充完善残留的六氟化铀收集系统;改进UF6和水蒸气喷嘴的结构形式,防止堵塞;转炉内翻料机构的结构形式及转速;转炉反应室内重要部件的结构及配置;转炉动态密封形式及密封材料的研究;UO2 粉末中水分的在线分析的研究;UF6流量测量的研究以及氟化氢尾气回收利用的研究。
5.3 在IDR流程中,每消耗1吨六氟化铀就会产生约600kg 40%的氢氟酸。
但在我国氢氟酸的消耗量不大,而含铀的氢氟酸市场则更小。
如果国内没有销售市场,仍采用国外技术时就必须设置贮槽以贮存大量的氢氟酸,按照年产量为75吨铀的生产能力,每年约产生氢氟酸60吨左右。
大量贮存氢氟酸既无用处又会给生产带来不必要的麻烦及安全隐患。
因此,氢氟酸的市场问题将直接影响IDR生产线的发展,这个问题要引起足够的重视。
在IDR流程中,产生的氢氟酸其浓度约40%,这种浓度的氢氟酸无法用于核工业系统内部,而必须售往冶金等行业。
由于核工业以外的行业对核相关知识了解较少,有“谈核色变”现象,一般不愿意接收我们的副产品。
由于氢氟酸的特点,长期、大量存放氢氟酸是极其不安全的。
为此我们建议:
5.4 目前已存有大量的贫化UF6,并且每天还在产生新的贫化UF6。
如何贮存和处置这些贫料已成为大家极为关注的问题。
U3O8是铀的氧化物中最为稳定、便于存放及计量的一种形式。
利用IDR工艺将贫化UF6转化为U3O8来存放,既可以消除存放UF6带来的腐蚀问题又可以减少
存放空间。
当将来需要利用贫料时,再将U3O8转化为某一化合物。
5.5 引进IDR流程的基础上,建议国家投入部分科研经费,厂院共同组织人力,参与生产运行,摸清工艺参数和设备运行情况,找出存在的技术关键问题并积极收集有关资料,及时了解国外同类设备的生产和运行信息,结合我国的实际情况,在10英寸转炉的基础上,研究制造出具有自主知识产权的16英寸转炉,以适应我国核电发展的需要。