金属凝固计算机模拟b
金属凝固原理

2 研究对象:
研究液态金属或合金转变为固态金属或合金这一凝固过程 的理论和技术,定性地特别是定量地揭示其内在联系和规 律,发现新现象,探求未知参数,开拓新的凝固技术和工 艺。 凝固学是材料成形技术的基础,也是近代新型材料开拓和 制备的基础。
第一节 单向凝固工艺 第二节 单晶生长 第三节 柱状晶的生长 第四节 自生复合材料
第八章 快速凝固
第一节 快速凝固技术及其传热特点 第二节 快速凝固的热力学 第三节 快速凝固的动力学及界面形貌稳定性 第四节 快速凝固晶态合金的显微结构特征与 应用 第五节 快速凝固的非晶态合金
绪论
研究对象
1 凝固:
两个原子的相互作用势能 W(R) 的曲线如图 1-1b 所示。可 用下式计算相互作用力,当 R 增加 dR 时,力 F 就靠势能 W(R)减小作外功FdR。因此得到: 或 当R=R0 时,F(R0)=0,即 对应于能量的极小值,状态稳定。原子之间倾向于保持一 定的间距,这就是在一定条件下,金属中的原子具有一定 排列的原因。当R=R1时,吸引力最大,即
第二章 凝固热力学
第一节 液态金属结构 第二节 二元合金的稳定相平衡 第三节 溶质平衡分配系数 第四节 液-固相界面成分及界面溶质
分配系数
第三章 凝固动力学
第一节 自发形核 第二节 非自发形核 第三节 固-液相界面结构 第四节 晶体生长方式
第四章 单相合金的凝固
第一节 凝固过程的溶质再分配 第二节 金属凝固过程中的“成分过冷” 第三节 界面稳定性与晶体形态 第四节 胞晶组织与树枝晶 第五节 微观偏析 第六节 固-液界面非线性动力学理论
表1-1 一些金属的熔化潜热和汽化潜热的比较
连铸过程原理及数值模拟

连铸过程原理及数值模拟连铸是一种重要的金属成形工艺,广泛应用于钢铁、铝合金等金属材料的生产和加工中。
连铸过程原理及数值模拟是研究连铸工艺的关键内容,通过对连铸过程的原理分析和数值模拟,可以优化连铸工艺参数,提高产品质量和生产效率。
连铸过程是将熔融金属直接注入到连续运动的铸坯中,通过冷却和凝固过程,将熔融金属转化为固态铸坯。
连铸的基本原理是利用连续运动的铸坯带走热量,使熔融金属迅速凝固,形成连续的固态铸坯。
在连铸过程中,主要包括液相区、液固两相区和固相区三个区域。
在液相区,熔融金属通过连续浇注,填充到铸坯的空腔中。
熔融金属的温度高于固相线,处于液态状态。
随着熔融金属的注入,液相区的长度逐渐增加。
在液固两相区,熔融金属和正在凝固的铸坯同时存在。
由于熔融金属的温度高于固相线,所以熔融金属仍然保持液态。
而铸坯由于受到液相的热量传递,开始逐渐凝固。
在这个区域中,液相区的长度逐渐减小,凝固铸坯的长度逐渐增加。
在固相区,整个铸坯都已经完全凝固。
熔融金属已经完全转化为固态,形成连续的固态铸坯。
在这个区域中,液相区的长度为零,凝固铸坯的长度为整个连铸过程的长度。
为了研究连铸过程的细节和优化连铸工艺参数,数值模拟成为一种重要的方法。
数值模拟是通过数学模型和计算机仿真技术,对连铸过程进行模拟和分析。
数值模拟可以准确地计算连铸过程中的温度场、流场和凝固结构等关键参数,为工艺优化提供科学依据。
在连铸过程的数值模拟中,需要考虑多个物理过程的相互作用。
首先是流体力学过程,包括熔融金属的流动和铸坯带走热量的过程。
其次是热传导过程,包括熔融金属的冷却和凝固过程。
最后是凝固结构演化过程,包括铸坯的晶粒生长和偏析等现象。
为了建立连铸过程的数值模型,需要考虑材料的物理性质、流体力学和热传导方程等方面的参数。
同时,还需要考虑边界条件和初始条件等参数。
通过数值模拟,可以预测连铸过程中的温度分布、流速分布和凝固结构等重要参数,为工艺优化提供指导。
fluent凝固相变模型

fluent凝固相变模型Fluent凝固相变模型引言:Fluent凝固相变模型是一种用于模拟物质从液态到固态的相变过程的计算模型。
该模型基于流体动力学(CFD)方法,并考虑了物质的输运、热传导和相变等过程。
在工程领域中,该模型广泛应用于研究和优化凝固过程,例如金属凝固、半导体生长和冷冻食品制造等。
一、Fluent凝固相变模型的原理Fluent凝固相变模型是基于质量守恒、动量守恒和能量守恒等基本方程进行建模的。
在模型中,通过引入凝固速率、凝固热和凝固界面等参数,可以准确地描述物质的凝固过程。
模型中的凝固速率方程通常采用Stefan方程或类似的数学形式,用于描述凝固界面的移动速度。
二、Fluent凝固相变模型的关键特点1. 考虑相变潜热:Fluent凝固相变模型考虑了物质在凝固过程中释放或吸收的相变潜热。
这对于准确预测凝固过程的温度分布和相变界面的位置非常重要。
2. 考虑界面传热:Fluent凝固相变模型考虑了凝固界面处的热传导效应。
在模型中,通过引入界面传热系数和界面温度跳跃等参数,可以考虑凝固界面处的热传导现象。
3. 考虑物质输运:Fluent凝固相变模型不仅考虑了物质的凝固过程,还考虑了物质的输运过程。
在模型中,通过引入扩散系数和输运速率等参数,可以准确地描述物质的输运过程。
4. 考虑晶体生长:Fluent凝固相变模型考虑了晶体生长的过程。
在模型中,通过引入晶体生长速率和晶体取向等参数,可以准确地描述晶体生长的动力学行为。
三、Fluent凝固相变模型的应用案例1. 金属凝固过程模拟:利用Fluent凝固相变模型,可以模拟金属凝固过程中的温度分布、相变界面的位置和晶体生长等行为。
这对于优化金属凝固工艺、提高产品质量具有重要意义。
2. 半导体生长过程模拟:Fluent凝固相变模型可以应用于半导体生长过程的模拟和优化。
通过模拟生长过程中的温度分布和晶体生长行为,可以预测生长过程中可能出现的缺陷,并采取相应的措施进行修正。
金属冶炼中的数值模拟与模型预测

模型预测在金属冶炼中的优势与局限性
模型简化与误差
为了简化计算和提高计算效率,模型通常会做出一些假设和简化 ,可能导致预测结果存在误差。
数据需求
建立精确的模型需要大量的实验数据和参数支持,数据获取可能存 在困难。
计算资源要求
环保监测
通过数值模拟与模型预测技术对金属冶炼过 程中的环境影响进行监测和评估,为环保决 策提供科学依据。
提高数值模拟与模型预测技术应用效果的措施与建议
01
加强人才培养
培养具备数值模拟与模型预测技 术的专业人才,提高技术应用水 平。
02
强化技术研发
03
建立标准体系
持续投入资源进行数值模拟与模 型预测技术的研发和创新,保持 技术领先优势。
模型预测通常需要高性能计算机和专业的数值计算软件,对计算资 源要求较高。
04
金属冶炼中的数值模拟与 模型预测的未来发展
数值模拟与模型预测技术的发展趋势
智能化
随着人工智能和机器学习技术的 快速发展,数值模拟与模型预测 将更加智能化,能够自动识别和 解决复杂问题。
精细化
随着计算能力的提升和数值方法 的改进,数值模拟与模型预测将 更加精细化,能够处理更复杂、 更高精度的模型。
基于物理定律和数学方程,通过计算机程序建立数学模型, 将实际生产过程中的复杂物理和化学变化转化为可计算的数 学问题。通过求解这些数学问题,可以得到各种工艺参数和 性能指标。
数值模拟在金属冶炼中的应用领域
熔炼过程模拟
连铸过程模拟
模拟金属熔炼过程中的传热、传质、化学 反应等过程,预测金属的熔化温度、熔体 成分、温度分布等参数。
铸件凝固过程温度场的数值模拟
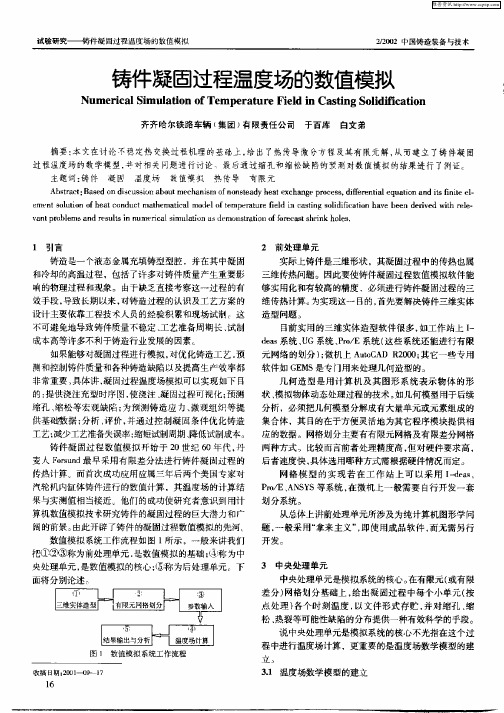
3 中央处 理 单元
从总体上讲前处理单拿来 主义” 即使用成品软件 , , 而无需另行
开 发。
中央处理单元是模拟系统 的核心。 在有限元 ( 或有限 差分) 网格划分基础上 , 给出凝 固过程 中每个小单元 ( 按
点处理 ) 各个时刻温度 , 以文件形式存贮 , 并对缩孔 、 缩
实际上铸件是三维形状 ,其凝固过程中的传热也属
三维传热问题 。因此要使铸件凝固过程数值模拟软件能
够实用化和有较高的精度 ,必须进行铸件凝固过程 的三 维传热计算 。 为实现这一 目的, 首先要解决铸件三维实体
造 型问题 。
目 前实用的三维实体造型软件很多 , 如工作站上 I — da 系统 、G系统、r E系统 ( es U Po / 这些系统还能进行有限
状、 模拟物体动态处理过程 的技术。 如几何模型用于后续
缩孔 、 缩松等宏观缺陷 ; 为预测铸造应力 、 微观组织等提 分析,必须把几何模型分解成有大量单元或元素组成的 供基础数据 ; 分析 、 评价 , 并通过控制凝固条件优化铸造 集合体 ,其 目的在于方便灵活地为其它程序模块提供相 工艺; 减少工艺准备失误率; 缩短试制周期 、 降低试制成本。 应的数据 。网格划分主要有有 限元网格及有限差分网格 铸件凝 固过程数值模拟 开始于 2 0世纪 6 年代 , o 丹 两种方式 比较而言前者处理精度高 , 但对硬件要求高, 麦人 Fr n 最早采用有 限差分法进行铸件凝 固过程 的 os d u 后者速度快 , 具体选用哪种方式需根据硬件情况而定 。 传热计算。而首次成功应用应属 三年后两个美国专家对 网格 模型 的实现 若在 工作 站上可 以采用 Ida 、 - es 汽轮机内缸体铸件进行的数值计算 ,其温度场的计算结 PoE A S S等系统 , r 、N Y / 在微机上一般需要 白行开发一套 果与实测值相当接近。他们 的成功使研究者意识到用计 划 分系统 。 算机数值模拟技术研究铸件的凝固过程的巨大潜力和广 阔的前景。 由此开辟了铸件的凝固过程数值模拟的先河。 数值模拟系统工作流程如图 1 所示 ,一般来讲我们 把①②⑧称为前处理单元 , 是数值模 拟的基础 ; ④称 为中 央处理单元 , 是数值模拟的核心 ; ⑤称为后处理单元 下 面将 分别论 述 ÷
金属凝固原理习题与答案
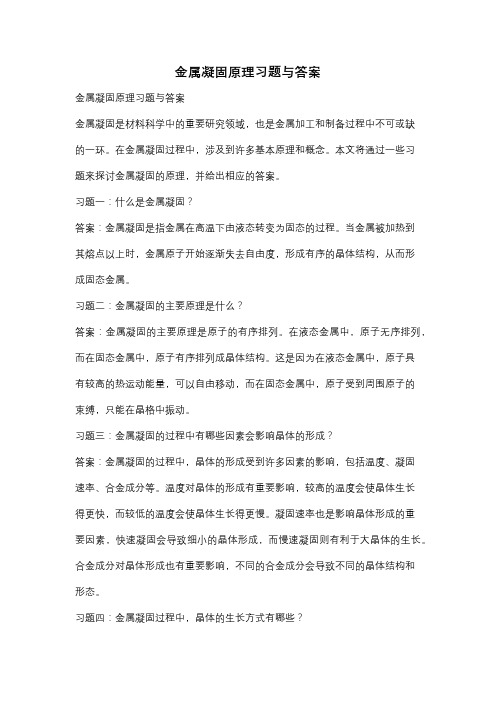
金属凝固原理习题与答案金属凝固原理习题与答案金属凝固是材料科学中的重要研究领域,也是金属加工和制备过程中不可或缺的一环。
在金属凝固过程中,涉及到许多基本原理和概念。
本文将通过一些习题来探讨金属凝固的原理,并给出相应的答案。
习题一:什么是金属凝固?答案:金属凝固是指金属在高温下由液态转变为固态的过程。
当金属被加热到其熔点以上时,金属原子开始逐渐失去自由度,形成有序的晶体结构,从而形成固态金属。
习题二:金属凝固的主要原理是什么?答案:金属凝固的主要原理是原子的有序排列。
在液态金属中,原子无序排列,而在固态金属中,原子有序排列成晶体结构。
这是因为在液态金属中,原子具有较高的热运动能量,可以自由移动,而在固态金属中,原子受到周围原子的束缚,只能在晶格中振动。
习题三:金属凝固的过程中有哪些因素会影响晶体的形成?答案:金属凝固的过程中,晶体的形成受到许多因素的影响,包括温度、凝固速率、合金成分等。
温度对晶体的形成有重要影响,较高的温度会使晶体生长得更快,而较低的温度会使晶体生长得更慢。
凝固速率也是影响晶体形成的重要因素,快速凝固会导致细小的晶体形成,而慢速凝固则有利于大晶体的生长。
合金成分对晶体形成也有重要影响,不同的合金成分会导致不同的晶体结构和形态。
习题四:金属凝固过程中,晶体的生长方式有哪些?答案:金属凝固过程中,晶体的生长方式主要有三种:平面生长、柱状生长和体内生长。
平面生长是指晶体在平面上逐渐生长,形成平坦的晶界;柱状生长是指晶体在某个方向上生长,形成柱状晶界;体内生长是指晶体在整个体积内均匀生长,没有明显的晶界。
不同的金属和凝固条件下,晶体的生长方式可能不同。
习题五:金属凝固过程中,晶体的缺陷有哪些?答案:金属凝固过程中,晶体的缺陷主要有晶格缺陷和晶界缺陷。
晶格缺陷是指晶体内部原子的位置偏离理想位置,包括点缺陷(如空位、间隙原子等)和线缺陷(如位错等)。
晶界缺陷是指晶体之间的界面上存在的缺陷,包括晶界错配、晶界位错等。
基于ANSYS的铝合金铸件凝固过程温度场的数值模拟

中图分 类 号 : G 4 2 1 文献标 识码 : 文章 编号 : 0 6 9 5 ( 0 8) 4 4 T 1 6. : A; 1 0— 6 820 0—
固 过程 的温 度场 分 布进行 了数值模 拟 。 1 计 算 温度 场 的数 理模 型 实 验 所 用 材 料 为 A 一 %C l4 u合 金 ,由高 纯 度 A l ( 99 % ) 电 解 C ( 99 % ) 电 阻 炉 中 的石 墨 坩 9 .9 和 u 9. 9 在 埚里 熔炼 。采用 砂 型铸 造 。合 金 熔 体 的浇 注 温度 为 9 0C, 温 为 2 ℃。 为使 铸件 在 长 度方 向上 快 速凝 0 ̄ 室 5 固 , 铸 件 的末 端 放置 一冷 铁 。 在
铸造 凝 固过 程数 值 模拟 技术 是 学科 发 展 的前 沿 领域 , 括宏 观模 拟 ( co Mo e ig 和 微 观 模 拟 包 Mar— d ln ) l ( co Mo el g 。其 中 以研 究铸 件凝 固过 程 中温 Mi — d ln ) r i 度场 变化 规律 为基础 内容 的数值 模 拟 ,被许 多学 者 称 之 为铸 件凝 固过程 的宏 观 模拟 。它是 指从 传 热 学 角度 模拟 金属 从 液态 转 变为 固态 的过程 ,在存 在 相
维普资讯
基于 A Y NS S的铝合 金 铸 件 凝 固过 程温 度 场 的数 值 模 拟
Nu e i a i u a i n o m p r t r il eS l i c to o e s m rc l m l to f S Te e a u eF e d i t o i f a i nPr c s n h di o l y Ca t s d OnANS f Al s e Al o Ba YS
快速凝固技术

快速凝固技术快速凝固技术是目前材料科学与工程领域最活跃的课题之一。
它是通过对合金熔体进行快速冷却(冷却速率大于104~106K/s)或遏制冷却过程中的非均匀形核,使合金在大的过冷度下发生高生长速率(耳~100cm/s)的凝固。
冷却速率是决定合金凝固组织的关键因素,它不仅决定着凝固组织形态,而且对组织中各相的析出次序、种类及数量都有重要的影响。
所以较好地理解冷却速率对合金凝固组织和性能的影响,在解释同一成分合金铸造出不同形状铸件时微观组织的差异是相当有益的。
传统的铸造工艺,由于凝固速度较低,合金在冷却过程中的过冷度和凝固速度较小,因此常规铸造合金有着晶粒粗大、偏析严重等严重缺陷。
快速过冷技术无论对合金的成分设计还是还是对合金围观组织以及宏观特性都有很大的影响。
一、快速凝固技术快速凝固即由液相到固相的相变过程进行的非常快,从而得到普通铸件和铸锭无法获得的成分、相结构和显微组织结构的过程。
目前快速凝固技术已经在许多方面显示出其优越性,与常规铸锭材料相比,快速凝固材料的偏析程度大幅度降低,而且快速凝固材料的化学成分多比较均匀。
应用快速凝固技术可以制备具有超高强度、高耐蚀性和磁性的材料,非晶、准晶、微晶和纳米晶合金等。
目前,快速凝固技术已成为一种挖掘金属材料潜在性能与发展前景的开发新材料的重要手段。
快速凝固技术已开始应用于研究合金在凝固时的各种组织形态的变化以及如何控制才能得到符合实际生活、生产要求的合金。
二、快速凝固的基本原理和分类从技术原理上讲,快速冷却主要有两种原理:急冷凝固技术和大过冷凝固技术。
1、急冷凝固技术急冷凝固技术又称熔体淬火技术,即提高熔体凝固时的传热速度从而提高凝固时的冷却速度,使熔体的形核时间短、效率高,来不及在平衡熔点附近凝固,只能在远离平衡熔点的较低温度下凝固。
急冷凝固技术的核心是要提高凝固过程中熔体的冷却速度。
一个相对于环境放热的系统的冷却速度取决于该系统在单位时间内产生的热量和传出系统的热量。
金属凝固过程枝晶生长相场法模拟研究进展

枝晶生长相场法模拟
相场法是一种基于物理原理的数值模拟方法,通过相场的变化来描述的。 具体而言,相场是一个标量场,用于表示材料中不同相的分布情况。通过计算 相场的变化,可以模拟出枝晶在不同条件下的生长行为。
相场法的模拟过程包括以下几个步骤:(1)建立数学模型;(2)初始化模型; (3)对模型进行求解;(4)对求解结果进行后处理。在建立数学模型时,需要 考虑材料的物理性质、溶质扩散、热量传输等因素。常用的数学模型包括 Cahn-Hilliard方程和Langer-Shtrikman方程等。在初始化模型时,需要根 据实际实验条件设定初始相分布和边界条件等参数。
研究现状:
随着计算能力和模拟技术的不断提高,微观模拟在金属凝固领域的应用日益广 泛。国内外研究者利用分子动力学、元胞自动机、蒙特卡罗等方法,对金属凝 固过程中的晶体生长、溶质扩散、微观组织演化等问题进行了深入研究。
然而,由于金属凝固过程的高度复杂性和多尺度性,目前微观模拟研究仍面临 着不少挑战,如如何提高模拟精度、减小计算成本,如何实现从微观到宏观的 尺度过渡等。
观察金属合金枝晶生长同步辐射射线实时成像观察的方法主要有以下步骤:首 先,需要选择适合的金属合金样品;其次,将样品置于高真空或惰性气体环境 中,以避免样品氧化或被污染;然后,利用同步辐射光源对样品进行照射,通 过采集透射或反射的射线信号,得到金属合金枝晶生长的实时图像;最后,对 图像进行处理和分析,得出枝晶生长的特点和机制。
通过对金属合金枝晶生长同步辐射射线实时成像观察的实验结果进行分析,可 以得出以下结论:首先,金属合金枝晶生长具有各向异性,即不同方向上的枝 晶生长速率和形态存在差异;其次,金属合金枝晶生长受到溶质浓度、温度等 多种因素的影响;最后,金属合金枝晶生长过程中存在竞争和择优取向等现象。 这些结论对于优化金属合金的性能和制备具有重要指导意义。
铸件充型凝固过程数值模拟实验报告

哈尔滨工业大学《材料加工过程数值模拟基础》实验课程铸件充型凝固过程数值模拟实验报告姓名:学号:班级:材料科学与工程学院铸件充型凝固过程数值模拟实验报告实验一:铸件凝固过程数值模拟一、实验目的1.学习有限差分法温度场模拟的数学模型和基本思路;2.掌握用AnyCasting 铸造模拟软件进行温度场模拟的方法。
二、实验原理1.有限差分法温度场模拟的基本思路:设计铸造工艺方案→根据定解条件求解能量方程→揭示凝固行为细节→预测凝固缺陷→改进工艺方案,返回第二步循环。
2.有限差分法温度场模拟的数学模型:222222T T T T L C t x y z t三、铸件凝固模拟过程及参数设置1.凝固模拟过程铸件、浇冒口等三维实体造型(输出STL 文件)→网格剖分、纯凝固过程参数设置等前处理→凝固温度场和收缩缺陷计算模拟数据→后处理得到动态的液相凝固、铸件色温图和缩孔缺陷等文件。
2.参数设置铸件材质:AC1B铸型材质:SM20C初始条件:上下模500℃,侧模400℃,升液管700℃。
边界条件:所有界面与空气间的界面传热系数都为10W/(m 2∙K),熔融金属液与模具之间的界面传热系数为4000 W/(m 2∙K),各部分模具间和模具与升液管间界面传热系数都为5000 W/(m 2∙K)。
四、模拟结果图1 冷却时间由于模拟中设置了水冷和空冷条件,所以铸件冷却速度较快。
由图1可知凝固首先发生在铸件表面,铸件的轮辋区厚度较薄,冷却速度比轮辐处冷却快。
内浇口先于轮辐凝固,在内浇口凝固后升液管内铝合金熔液无法对轮毂进行补缩,则在轮毂中最后凝固处容易产生缩松缩孔。
图2 冷却率由冷却率分布情况可知凝固过程中各部分冷却速率不同,可以判断出凝固时内应力较大的区域,在应力较大区域铸件容易产生裂纹缺陷。
由模拟结果中铸件的温度场情况,合理设置工艺参数减少缩松缩孔及裂纹的产生,合理布置冷却水管的分布位置。
实验二:铸件充型过程数值模拟一、实验目的1.学习有限差分法流动场模拟的数学模型和基本思路;2.掌握用AnyCasting 铸造模拟软件进行流动场模拟的方法。
金属液在充型和凝固过程中夹杂物运动的数值模拟的开题报告

金属液在充型和凝固过程中夹杂物运动的数值模拟的开题报告1.研究背景和意义金属液在充型和凝固过程中夹杂物的运动对于最终铸件的质量有着重要影响。
一些重要的金属夹杂物,比如氧化物和硫化物等,往往会影响金属的机械性能、耐腐蚀性和导电性等,这在一些高品质铸件的制造过程中具有重要意义。
而数值模拟技术可以为铸造工艺提供更为准确的预测和优化。
2.主要研究内容本项目将重点研究金属液在充型和凝固过程中夹杂物的运动问题,主要包括以下内容:(1)建立金属液的流体模型:利用流体力学模型和计算机辅助设计软件建立金属液在铸模内的流动模型,对金属液流动进行模拟,并对模型进行验证和优化。
(2)建立夹杂物的运动模型:利用计算流体力学模拟技术建立夹杂物在金属液中的运动模型,研究夹杂物在金属液中的运动规律并优化模型。
(3)模拟分析:模拟分析金属液在充型和凝固过程中夹杂物的运动轨迹、分布以及浓度等数据,为优化铸造工艺提供科学依据。
3.研究方法和技术路线(1)建立金属液的流体模型:通过建立Navier-Stokes方程和质量守恒方程,利用ANSYS等计算机辅助设计软件对金属液在铸模内的流动进行模拟,对流动模型进行优化和验证。
(2)建立夹杂物的运动模型:结合Goldsmid-Allnatt模型,采用计算流体力学模拟技术建立夹杂物在金属液中的运动模型,进行数值模拟并优化模型。
(3)模拟分析:根据铸造工艺的特点,利用数值模拟技术进行模拟分析,包括金属液的流动、夹杂物的分布和浓度等数据的统计和分析,并提出优化铸造工艺的方案。
4.预期成果(1)建立金属液的流体模型,建立夹杂物在金属液中的运动模型。
(2)获得铸造过程中夹杂物浓度分布、运动轨迹等信息,并分析优化铸造过程工艺。
(3)撰写论文并发表论文,提升科研水平。
金属凝固原理--第八章快速凝固
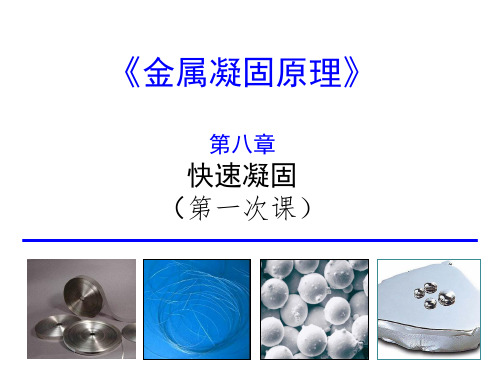
13
§6.1 引言 快速凝固:在极快的冷却速率下完成由液相到固相的相变过 程,从而获得常规凝固方法所无法得到的合金成分、相组成 和显微结构。
获得独特的微观组织、结构特征
所制备材料具有优异的使用性能 (如:力学、物理、化学性能等)
14
§6.1 引言 三. 本章学习内容
(1)
(2)
(3)
(4)
快
速
快速凝固 快速凝固 快速凝固
快速凝固
凝
原理、技术 热力学与 显微结构 晶态(微/纳米晶)
固
及 传热特点
动力学
特征
准晶/非晶 材料及应用
15
§6.2 快速凝固原理、技术及其传热特点—快速凝固原理
快速凝固的内涵
定义1:从液态到固态的冷却速度大于某一临界冷却速率的 凝固过程(103 K/s)。
定义2:由液相到固相的相变过程进行得非常快,从而获得 普通铸件和铸锭无法获得的成分、相结构和显微结构的凝固 过程。
27
§6.2 快速凝固原理、技术及其传热特点—快速凝固技术
02
急冷凝固技术—雾化技术—雾化法
基本原理:以水、气作为冷却介质(水雾化 /气雾化),冲击金属流,冷却速率可达104~ 107 K/s 。
特点:(1)可以大批量生产预合金粉末; (2)粉体可以通过各种不同的固结方法(粉 末冶金方法)加工成块体坯料或成形零件。
§6.6 非晶态合金
3
§6.1 引言
普通凝固过程存在的问题:
冷却速度慢 凝固速度小
常规工艺下金属的冷却速度一般不会超过102 ℃/S
大型砂型铸件及铸锭凝固时的冷却速度约为:10-6 ~10-3 ℃/S;中等铸件及铸锭约为10-3~100 ℃/S; 薄壁铸件、压铸件、普通雾化约为100~102 ℃/S
铸件充型凝固过程数值模拟
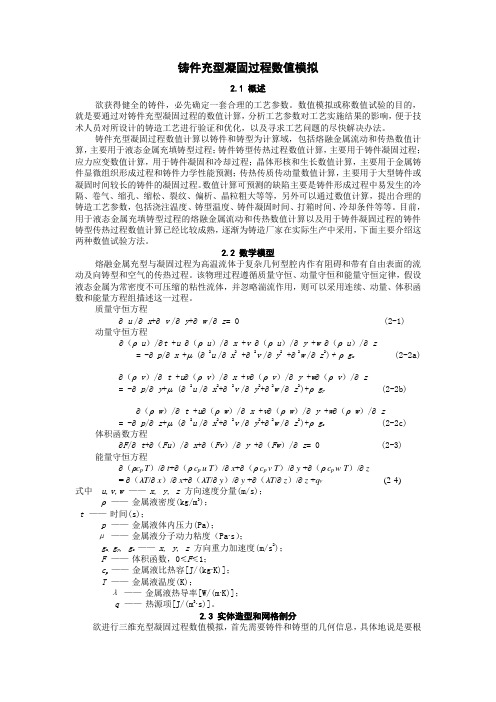
铸件充型凝固过程数值模拟2.1 概述欲获得健全的铸件,必先确定一套合理的工艺参数。
数值模拟或称数值试验的目的,就是要通过对铸件充型凝固过程的数值计算,分析工艺参数对工艺实施结果的影响,便于技术人员对所设计的铸造工艺进行验证和优化,以及寻求工艺问题的尽快解决办法。
铸件充型凝固过程数值计算以铸件和铸型为计算域,包括熔融金属流动和传热数值计算,主要用于液态金属充填铸型过程;铸件铸型传热过程数值计算,主要用于铸件凝固过程;应力应变数值计算,用于铸件凝固和冷却过程;晶体形核和生长数值计算,主要用于金属铸件显微组织形成过程和铸件力学性能预测;传热传质传动量数值计算,主要用于大型铸件或凝固时间较长的铸件的凝固过程。
数值计算可预测的缺陷主要是铸件形成过程中易发生的冷隔、卷气、缩孔、缩松、裂纹、偏析、晶粒粗大等等,另外可以通过数值计算,提出合理的铸造工艺参数,包括浇注温度、铸型温度、铸件凝固时间、打箱时间、冷却条件等等。
目前,用于液态金属充填铸型过程的熔融金属流动和传热数值计算以及用于铸件凝固过程的铸件铸型传热过程数值计算已经比较成熟,逐渐为铸造厂家在实际生产中采用,下面主要介绍这两种数值试验方法。
2.2 数学模型熔融金属充型与凝固过程为高温流体于复杂几何型腔内作有阻碍和带有自由表面的流动及向铸型和空气的传热过程。
该物理过程遵循质量守恒、动量守恒和能量守恒定律,假设液态金属为常密度不可压缩的粘性流体,并忽略湍流作用,则可以采用连续、动量、体积函数和能量方程组描述这一过程。
质量守恒方程∂ u/∂ x+∂ v/∂ y+∂ w/∂ z= 0 (2-1) 动量守恒方程∂(ρ u)/∂t +u ∂(ρ u)/∂ x +v ∂(ρ u)/∂ y +w ∂(ρ u)/∂z= -∂ p/∂ x +μ(∂2u/∂ x2 +∂2v/∂y2 +∂ 2w/∂ z2)+ ρ g x (2-2a) ∂(ρ v)/∂ t +u∂(ρ v)/∂ x +v∂(ρ v)/∂ y +w∂(ρ v)/∂z= -∂ p/∂y+μ (∂2u/∂x2+∂2v/∂y2+∂ 2w/∂ z2)+ρ g y (2-2b) ∂(ρ w)/∂ t +u∂(ρ w)/∂x +v∂(ρ w)/∂ y +w∂(ρ w)/∂ z = -∂ p/∂z+μ (∂2u/∂ x2+∂2v/∂ y2+∂ 2w/∂z2)+ρ g z (2-2c)体积函数方程∂F/∂ t+∂(Fu)/∂ x+∂(Fv)/∂y +∂(Fw)/∂z= 0 (2-3)能量守恒方程∂(ρc p T)/∂t+∂(ρ c p u T)/∂x+∂(ρ c p v T)/∂ y +∂(ρ c p w T)/∂ z= ∂(λT/∂x)/∂x+∂(λT/∂ y)/∂ y +∂(λT/∂ z)/∂ z +q v(2-4)式中u,v,w —— x, y, z 方向速度分量(m/s);ρ——金属液密度(kg/m3);t ——时间(s);p ——金属液体内压力(Pa);μ——金属液分子动力粘度(Pa.s);g x, g y, g z —— x, y, z 方向重力加速度(m/s2);F ——体积函数,0≤F≤1;c p ——金属液比热容[J/(kg.K)];T ——金属液温度(K);λ——金属液热导率[W/(m.K)];q——热源项[J/(m3.s)]。
procast凝固模拟简介
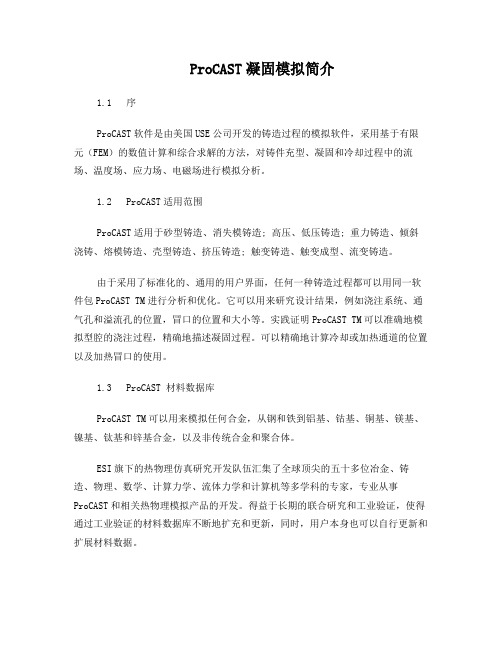
ProCAST凝固模拟简介1.1 序ProCAST软件是由美国USE公司开发的铸造过程的模拟软件,采用基于有限元(FEM)的数值计算和综合求解的方法,对铸件充型、凝固和冷却过程中的流场、温度场、应力场、电磁场进行模拟分析。
1.2 ProCAST适用范围ProCAST适用于砂型铸造、消失模铸造; 高压、低压铸造; 重力铸造、倾斜浇铸、熔模铸造、壳型铸造、挤压铸造; 触变铸造、触变成型、流变铸造。
由于采用了标准化的、通用的用户界面,任何一种铸造过程都可以用同一软件包ProCAST TM进行分析和优化。
它可以用来研究设计结果,例如浇注系统、通气孔和溢流孔的位置,冒口的位置和大小等。
实践证明ProCAST TM可以准确地模拟型腔的浇注过程,精确地描述凝固过程。
可以精确地计算冷却或加热通道的位置以及加热冒口的使用。
1.3 ProCAST 材料数据库ProCAST TM可以用来模拟任何合金,从钢和铁到铝基、钴基、铜基、镁基、镍基、钛基和锌基合金,以及非传统合金和聚合体。
ESI旗下的热物理仿真研究开发队伍汇集了全球顶尖的五十多位冶金、铸造、物理、数学、计算力学、流体力学和计算机等多学科的专家,专业从事ProCAST和相关热物理模拟产品的开发。
得益于长期的联合研究和工业验证,使得通过工业验证的材料数据库不断地扩充和更新,同时,用户本身也可以自行更新和扩展材料数据。
除了基本的材料数据库外,ProCAST还拥有基本合金系统的热力学数据库。
这个独特的数据库使得用户可以直接输入化学成分,从而自动产生诸如液相线温度、固相线温度、潜热、比热和固相率的变化等热力学参数。
1.4 ProCAST 模拟分析能力可以分析缩孔、裂纹、裹气、冲砂、冷隔、浇不足、应力、变形、模具寿命、工艺开发及可重复性。
ProCAST几乎可以模拟分析任何铸造生产过程中可能出现的问题,为铸造工程师提供新的途径来研究铸造过程,使他们有机会看到型腔内所发生的一切,从而产生新的设计方案。
金属凝固原理课件
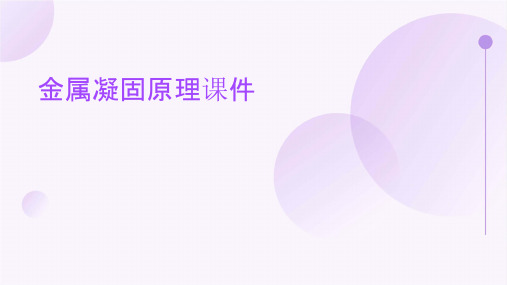
描述形核过程的快慢,与温度、过 冷度等因素有关。
晶体的长大与生长形态
晶体长大
晶核形成后,周围的原子或分子 继续附着到晶核上,使晶体逐渐
长大的过程。
生长形态
晶体生长过程中形成的外观形态, 如树枝状、柱状、球状等。
生长速率
晶体长大的速度,通常与温度梯 度、溶质浓度等因素有关。
04
金属凝固过程中的组织与性能
02
金属凝固过程中的传热与传质
传热与传质的基本概念
传热
指热量从高温处传递到低温处的 现象,是热量传递的一种方式。
传质
指物质从一处传递到另一处的现 象,是物质传递的一种方式。
金属凝固过程中的传热与传质现象
传热现 象
在金属凝固过程中,热量从液态传递 到固态,使液态金属逐渐冷却并转变 为固态。
传质现 象
03
金属凝固过程中的形核与长大
形核的基本概念
形核
指在液态金属中形成固相 晶核的过程。
形核过程
在液态金属冷却过程中, 原子或分子的排列逐渐变 得有序,最终形成固体晶 格结构。
形核率
单位时间内形成的晶核数量。
形核机制与形核速率
均质形核
在液态金属中自发形成晶核的过 程,需要克服能量障碍。
异质形核
在金属中的杂质或界面上形成晶核 的过程,通常较容易发生。
02
金属凝固是金属材料制备和加工 过程中最重要的物理过程之一, 对金属材料的性能和应用具有重 要影响。
金属凝固的物理过程
01
02
03
冷却过程
金属液体在冷却过程中, 原子逐渐失去液态的无序 性,开始形成固态晶格结 构的过程。
形核过程
在金属液体冷却到熔点以 下时,原子开始聚集形成 晶核的过程,是金属凝固 的起始点。
fluent融化凝固数学模型

fluent融化凝固数学模型Fluent融化凝固数学模型随着科技的不断发展,计算机模拟在工程领域中扮演着越来越重要的角色。
在工程设计和优化过程中,数学模型的建立是关键一步。
而Fluent融化凝固数学模型则是一种被广泛应用于熔融金属凝固过程模拟的数学模型。
熔融金属凝固是指将高温熔化的金属冷却至固态的过程。
这个过程在许多工业应用中都扮演着重要的角色,比如铸造、焊接和凝固成型等。
Fluent融化凝固数学模型能够帮助工程师们更好地理解和优化这个过程,从而提高产品质量和生产效率。
Fluent融化凝固数学模型基于质量守恒、动量守恒、能量守恒和物质守恒等基本原理。
它通过求解一组偏微分方程来描述熔融金属的流动、热传导和相变等过程。
这些方程包括质量守恒方程、动量守恒方程、能量守恒方程和物质守恒方程。
通过将这些方程与适当的边界条件和初始条件相结合,可以得到熔融金属在时间和空间上的温度、速度和浓度分布等信息。
在Fluent融化凝固数学模型中,金属的凝固过程主要通过相变模型来描述。
相变模型可以根据金属的凝固行为来确定固相和液相之间的界面位置和凝固速率。
这些参数的准确预测对于优化金属制造过程至关重要。
Fluent融化凝固数学模型提供了多种不同的相变模型,可以根据具体情况选择合适的模型。
除了相变模型,Fluent融化凝固数学模型还考虑了熔融金属的流动和热传导等因素。
流动模型可以描述金属在熔融过程中的流动行为,从而帮助工程师们优化金属的填充和冷却过程。
热传导模型则可以计算金属的温度分布,从而帮助工程师们避免热应力和裂纹等问题。
Fluent融化凝固数学模型的应用范围非常广泛。
它可以用于优化铸造过程,从而提高铸件的质量和性能。
它还可以用于改进焊接过程,减少焊接缺陷和变形等问题。
此外,Fluent融化凝固数学模型还可以应用于凝固成型和材料合成等领域。
Fluent融化凝固数学模型是一种强大的工程工具,可以帮助工程师们更好地理解和优化熔融金属凝固过程。
凝固原理与应用

c
式中,t为温度;τ为时间;x, y ,z为空间坐标;α为热扩散率; λ为导热系数;c为比热容;ρ为密度。
对于一维导热问题,导热微分方程式 具有如下形式: 2 t t 2 x
以置换变量法求解,其解为:
(2)铸型结构复杂,流动阻力大,金属液也难于充 满型腔。
第三章
铸件的凝固
第一节 铸件的温度场 第二节 铸件的凝固方式
第三节 金属的凝固方式
与铸件质量之间的关系 第四节 铸件的凝固时间
第一节 铸件的温度场
一、数学解析法
半无限大铸件中冷却
在铸件和铸型的不稳定导热过程中,温 度与时间和空间的关系可由傅里叶导热微分 方程来描述。
F1 kL c1 (t浇 t K ) l P t L t型
式中: l—充型能力(流动长度); v—在静压头作用下,液态金属的 平均流速;F—流动液体断面积;ρ1—液态金属的密度;P—流动液体 断面F的周长;α—液态金属换热系数;k—停止流动时液流前端的固相 量;L—结晶潜热;c1—液态金属的比热容;tk—停止流动时的温度; tL—合金液相线温度
二、数值模拟法
有限差分法:
沿热流方向把均质物体分割为若干单元,各单位的 端面为一单位面积,单元长度为Δx。
一维均质物体的分割
t 2t 2 对于一维传热问题,其导热微分方程为: x
用差分代替上述方程中的微分,可得到相应的有限差 分算式: t t ( , x ) t ( , x ) 2 t t ( , x x ) 2t ( , x ) t ( , x x ) 2 x 2
一、金属性质方面的因素
(1)合金成分
2010秋《金属凝固》思考题最终版

《金属凝固过程及组织控制》复习思考题1.为什么说液态金属的结构更接近固态而非气态?液体介于气体和固体之间,大量的实验数据证明它更接近于固体,特别是在接近熔点附近更是如此。
首先,从熔化潜热和汽化潜热的对比上来看,汽化潜热L g与熔化潜热L l之间的比值(L g /L l)是很大的。
以面心立方结构为例,其汽化潜热比熔化潜热约大28倍,这就意味着将固体原子完全变成气态所需的能量要比将同样的原子从固态转变成液态所需的能量多28倍。
(汽化潜热远大于溶化潜热)在金属原子由固态转变为液态时,其熵值的增加相对于熔点前的熵值并不算大,特别对于金属活性较强的元素更是如此。
熵的增值愈大,意味着金属由固态转变为液态时原子的排列结构紊乱性愈大;反之,其紊乱性就愈小。
所以,从金属由固态转变为液态过程中熵的增值来看,可以再次说明,在熔点附近金属的液态结构与固态结构相差不会太大。
(ΔS m极小)2.液态金属的微观结构的特点有那些?这些特点在宏观性能上是如何表现?液体状态的结构有以下特点:(1) 原子间仍保持较强的结合能,因此原子排列在较小距离内仍具有一定规律性,且其平均原子间距增加不大。
金属固体是由许多晶粒组成的,液体则是由许多原子集团所组成,在原子集团内保持固体的排列特征,而在原子集团之间的结合处则受到很大破坏。
这种仅在原子集团内的有序排列称为近程有序排列(short range order)。
(2) 由于液体中原子热运动的能量较大,每个原子在三维方向都有相邻的原子,经常相互碰撞,交换能量。
在碰撞时,有的原子将一部分能量传给别的原子,而本身的能量降低了。
结果是每时每刻都有一些原子的能量超过原子的平均能量,有些原子的能量则远小于平均能量。
这种能量的不均匀性称为能量起伏(fluctuation of energy)。
(3) 液体中存在的能量起伏造成每个原子集团内具有较大动能的原子能克服邻近原子的束缚(原子间结合所造成的势垒),除了在集团内产生很强的热运动(产生空位及扩散等)外,还能成簇地脱离原有集团而加入到别的原子集团中,或组成新的原子集团。
MPI并行计算在金属凝固温度场模拟中的实现

个 完整 的并 行 环境具体 应包括 硬件和软 件环境 ,
即并 行 体 系结 构及 运 行于 其 上 的并 行 编 程语 言 实 现 。 高 性能 计算 领域 经过 多年 的发 展 ,已经 出现 了多 种并 行 体系 结构 和并 行编 程语 言实 现 。因此 用户 需要根 据 自己的实际情况来 构建有效 且实用 的并行 环境 。
微观 组 织模 拟 等都 需 要依 据 宏 观 温度 场 模拟 的结果 。
但在模 拟 大型 复杂铸 件 的凝 固过程 温度 场变 化时需 要
很 大 的计 算量 ,基 于冯 . 伊曼 串行机 模型 上 的现有 的 诺
数值模 拟 串行算 法 已很难 进一 步提 高计算 速 度 ,难 以 满足用 户对模 拟 计算 精度 及 速度 的高 要求 。而且C U P 的频率 尽管越 来 越快 ,但从 硬 件 的发展趋 势来 看 ,现 有 的计 算机 C U生产 工 艺所 开发 的C U的运算 速 度 已 P P 经 开始 接近极 限 。能进 一 步提高 模拟 计算 速度 的一 种
关键 词 :模拟 ;MP并行 计算 ;数据 域分解 ;Wi o 机群 I n ws d 中 图分类 号 :T 3 1 文 献标 识码 :A 文 章编 号 :10 — 9 7 (0 7 7 0 0 — 4 P9. 9 0 1 4 7 2 0 )0 — 7 8 0
Re l a ino ar l m p t g wi PI o em p r t r a i t fP a l Co z o el ui t M r n h f T e au e
摘 要 :利用基-W no s  ̄ i w 异构机群平台的MP并行编程方式对金属凝固过程温度场模拟串 d I 行算法进行数据域分块的方