滚塑产品质量问题及解决措施
滚塑制品缺陷分析及解决方案

滚塑制品缺陷分析及解决方案滚塑成型工艺义称旋转模塑或旋转成型,该成型方法是将模具沿两垂直轴不断旋转并使之加热,模具型腔内的蝮料在重力和热的作用下逐渐熔融粘附于模具型腔表面上.经冷却定型后制得塑料制品。
滚塑成型工艺常用于生产中空无缝、具有复杂形状的塑料制品,在化工、机械、电子、轻工和军工等行业有广泛应用,如摩托车、汽车等车辆燃油箱、储物箱、大中型中空容器、汽车零部件、耐腐蚀容器内且只等,近年来也逐渐用于各种民用或军用产品包装箱、运输箱等制品的生产。
目前,来自国外的大多数滚塑制品订单都直接表明采用线性低密度聚乙烯(LLDPE)滚塑专用料进行滚塑成型,制品多是对滚塑技术要求较高的不同规格的清洗机乡}壳、割草机外壳、货物运输箱、储物箱、各种机械电子包装箱、内部有发泡层的双层保温箱、汽车零部件等。
我国的滚塑成型技术和滚塑模具加工技术迅速提高,但在滚塑产品设计环节方面与欧美相比尚存在差距。
滚塑成型工艺对制品质量起非常重要的作用。
当产品设计、模具设计制造完毕后,易导致制品缺陷的模具结构通常不会轻易改变,从成型工艺上来设法解决滚塑制品缺陷就显得比较重要。
目前国内介绍有关滚塑制品设计和滚塑工艺的资料较少,产品设计者或工程制造者多数靠实际经验来设计、生产,往往会给设计、生产带来不必要的麻烦。
研究分析滚塑制品缺陷成因及解决方案,对提高滚塑制品和滚塑模具结构设计技术水平具有重要意义。
一滚塑制品缺陷分析及解决方案1 气泡或孔洞(1)成因分析滚塑时模具内的物料在受热过程中,随模具的转动逐渐熔融、流动、粘附在热的模具内表面,模具内部空气受热体积膨胀,气压升高,通过通气孔逐渐向模具外部流动,直至模具内外空气压力平衡,反之亦然。
同时,模具型腔内保持着一定压强。
在树脂熔融致密化的过程中,滞留在粉末颗粒之间的气体被挤向塑料熔体的自由表面,但由于熔体表面张力的存在,气体不足以脱离熔体表面易形成气泡,从而形成制品内表面的气泡和外表面的气扎,严重情况下形成较大的孔洞”。
滚塑制品缺陷分析及解决方案
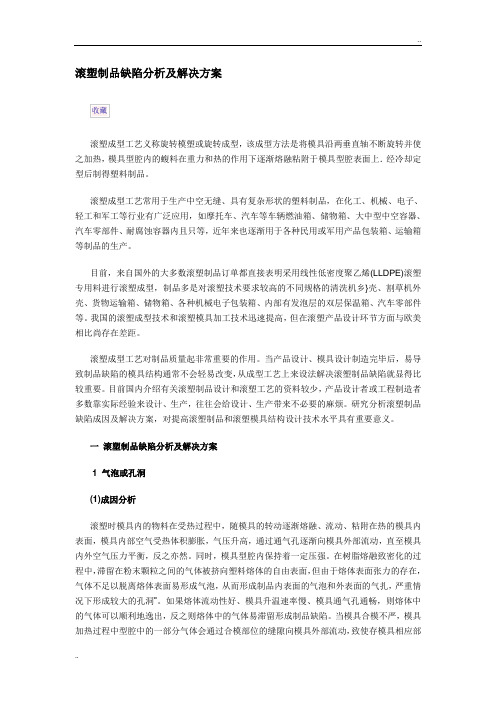
滚塑制品缺陷分析及解决方案滚塑成型工艺义称旋转模塑或旋转成型,该成型方法是将模具沿两垂直轴不断旋转并使之加热,模具型腔内的蝮料在重力和热的作用下逐渐熔融粘附于模具型腔表面上.经冷却定型后制得塑料制品。
滚塑成型工艺常用于生产中空无缝、具有复杂形状的塑料制品,在化工、机械、电子、轻工和军工等行业有广泛应用,如摩托车、汽车等车辆燃油箱、储物箱、大中型中空容器、汽车零部件、耐腐蚀容器内且只等,近年来也逐渐用于各种民用或军用产品包装箱、运输箱等制品的生产。
目前,来自国外的大多数滚塑制品订单都直接表明采用线性低密度聚乙烯(LLDPE)滚塑专用料进行滚塑成型,制品多是对滚塑技术要求较高的不同规格的清洗机乡}壳、割草机外壳、货物运输箱、储物箱、各种机械电子包装箱、内部有发泡层的双层保温箱、汽车零部件等。
我国的滚塑成型技术和滚塑模具加工技术迅速提高,但在滚塑产品设计环节方面与欧美相比尚存在差距。
滚塑成型工艺对制品质量起非常重要的作用。
当产品设计、模具设计制造完毕后,易导致制品缺陷的模具结构通常不会轻易改变,从成型工艺上来设法解决滚塑制品缺陷就显得比较重要。
目前国内介绍有关滚塑制品设计和滚塑工艺的资料较少,产品设计者或工程制造者多数靠实际经验来设计、生产,往往会给设计、生产带来不必要的麻烦。
研究分析滚塑制品缺陷成因及解决方案,对提高滚塑制品和滚塑模具结构设计技术水平具有重要意义。
一滚塑制品缺陷分析及解决方案1 气泡或孔洞(1)成因分析滚塑时模具内的物料在受热过程中,随模具的转动逐渐熔融、流动、粘附在热的模具内表面,模具内部空气受热体积膨胀,气压升高,通过通气孔逐渐向模具外部流动,直至模具内外空气压力平衡,反之亦然。
同时,模具型腔内保持着一定压强。
在树脂熔融致密化的过程中,滞留在粉末颗粒之间的气体被挤向塑料熔体的自由表面,但由于熔体表面张力的存在,气体不足以脱离熔体表面易形成气泡,从而形成制品内表面的气泡和外表面的气扎,严重情况下形成较大的孔洞”。
影响注塑产品合格率的不良因素及其相应对策
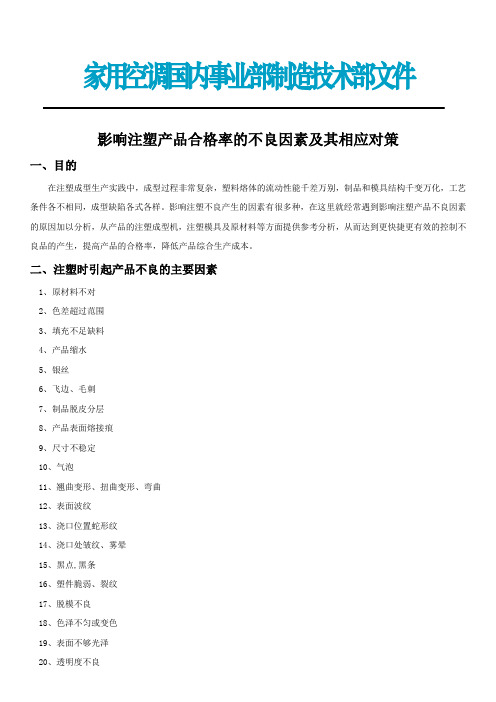
家用空调国内事业部制造技术部文件影响注塑产品合格率的不良因素及其相应对策一、目的在注塑成型生产实践中,成型过程非常复杂,塑料熔体的流动性能千差万别,制品和模具结构千变万化,工艺条件各不相同,成型缺陷各式各样。
影响注塑不良产生的因素有很多种,在这里就经常遇到影响注塑产品不良因素的原因加以分析,从产品的注塑成型机,注塑模具及原材料等方面提供参考分析,从而达到更快捷更有效的控制不良品的产生,提高产品的合格率,降低产品综合生产成本。
二、注塑时引起产品不良的主要因素1、原材料不对2、色差超过范围3、填充不足缺料4、产品缩水5、银丝6、飞边、毛刺7、制品脱皮分层8、产品表面熔接痕9、尺寸不稳定10、气泡11、翘曲变形、扭曲变形、弯曲12、表面波纹13、浇口位置蛇形纹14、浇口处皱纹、雾晕15、黑点,黑条16、塑件脆弱、裂纹17、脱模不良18、色泽不匀或变色19、表面不够光泽20、透明度不良21、污点、杂质、异物22、顶白23、局部烧焦发黑24、纤维外露25、麻点、麻面26、产品表面拉伤三、引起不良因素原因分析及解决办法原材料不对原材料使用不当一般是由于生产计划、产品的原材料更改没有及时落实到位,产品用材料时工人将材料弄混淆等原因所致。
加强产品的首检控制,做好产品的跟踪比对。
色差超过规定范围色差超过规定范围主要原因是由于注塑机在注塑生产时产品的色母和原料的比例不合适所致,根据色母和原料搅拌形式不同有下面两种:有色母机可以通过调整色母机的比例来加以控制,但色母的比例不能超过色母规定的比例用量,如果超过了规定的比例用料,色母用量提高导致产品的注塑成本提高了(色母的价格超过原料的价格)。
色母是不合格,表面上产品是合格的,其实从成本分析角度来说产品也是不合格的。
没有色母机的只能按照一定的比例放在搅拌机内搅拌后一起装在料筒内在注塑时通过注塑工艺来调整生产。
刚开始生产时颜色还可以符合要求。
但色母的密度大于塑料粒子的密度,如果没有色母机采用拌料机混合料来生产,由于两者的比重不一样导致注塑机下料的时候比重大的色母下料的速度大于原料的下料速度导致注塑时产品的色差不一致,产品的色差难控制,故建议外观件全部用色母机和注塑机匹配生产。
塑胶件常见不良状况及形成原因、改善对策
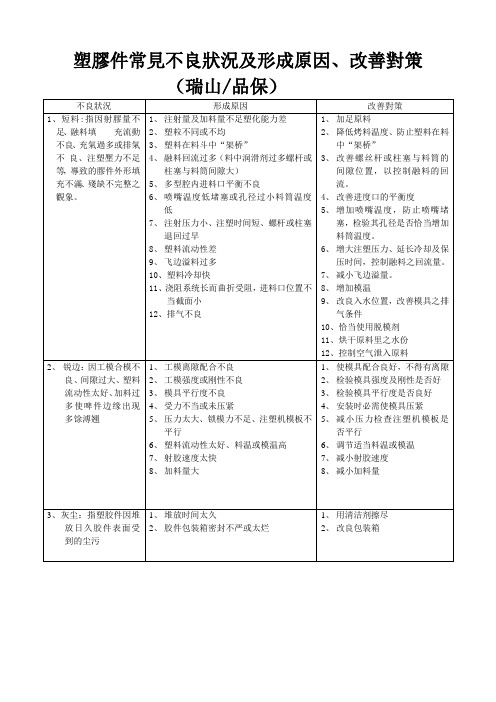
3、模温或啤塑温度低
1、烘干原料里水分
2、烤虑原料
3、增加模温及啤塑温度
10、顶白:指因部分顶针伸展太快或顶力太大,造成胶件表面呈圆形或半圆形白条称为“顶白”。
1、顶针伸展太快
2、顶力太大
3、脱模剂未使用或使用不当
1、调节顶针伸展速度
2、减小压力
3、适当使用脱模剂
11、缩水:指胶件冷却后变形一般因冷却不够或循环水温不符所致
1、压力(射胶枪)
2、增加料温及模温
3、增大压力及加快射胶速度
4、改良模具之冷却系统
5、改良水口位置及尺寸
6、供料要足
7、抛光模具改良光洁度
8、使用适当脱模剂
16、气泡:由于融料里泄入空气而导致的爆花现象多为局部起层或甩层
1、原料里含水分溶剂或挥发物
2、料温太高,加热时间太长塑料降分解
3、压力小
4、柱塞或螺丝杆退回过早
1、用布将防锈油,脱模剂擦干净
2、用抹面水擦干净胶件表面之油污
5、毛边:指因披锋后未除尽的毛刺
1、披锋太大批除不善
2、操作员操作不合理
1、调校披锋
2、指导操作员用正确的方法批除披锋
6、混色:包括黑点、白点、杂点、银纹、流纹、异色斑等
1、塑胶原料里含水分高、有低挥发物
2、料温及模温高
3、压力太大
4、模具表面有水分润滑油或脱模剂选用不相融料
5、多型腔内进料口平衡不良
6、喷嘴温度低堵塞或孔径过小料筒温度低
7、注射压力小、注塑时间短、螺杆或柱塞退回过早
8、塑料流动性差
9、飞边溢料过多
10、塑料冷却快
11、浇阻系统长而曲折受阻,进料口位置不当截面小
12、排气不良
塑胶产品不良及对策

产品成型缺陷及其对策∙一、填充不足∙二.模腔划痕和擦伤∙三、毛刺过大∙四、缩孔∙五、翘曲、弯曲和扭曲∙六、开裂、裂纹、微裂和发白∙七.熔接痕∙八、波纹∙九、银丝∙十、烧伤∙十一、黑色条纹∙十二、晕色膜(发暗)、光泽不佳∙十三、颜色不匀∙十四、气泡和空洞∙十五、透明度不好∙十六、混入异物∙十七、嵌件镶嵌不良∙十八、脱模不良∙十九、冷料凹痕(蛇行纹)∙二十、脆弱∙二十一、层状剥离一.填充不足一般情况下,填充不足是因塑料流动性不足,不能填充满整个型腔所造成的。
当然也不单纯是这个原因,造成填充不足还可能有多方面的原因。
1.注射成型机注射能力不足这是对注射机的能力估计过高而产生的,由于塑化能力不足或者注射量不足也会发生。
其中,塑化能力不足可通过延长加热时间、增加螺杆转数、提高背压来提高塑化能力。
而注射量不足,如果不换成大注射量的机床就不能解决问题。
2.多型腔有局部填充不足尽管成型机床的能力足够,这种缺陷是因浇口不平而产生的。
有时只是主浇道附近或者浇口粗而短的型腔可加工出合格制件,其余型腔的制件有缺陷。
达到浇口平衡即可消除这种缺陷,也就是加粗浇道直径,使流到浇道末端的压力降减小,同时加大离主浇道较远型腔的浇口。
如果,是由于型腔未完全闭合所致,这时就必须减少每次注射成型的数目。
3.塑料流动性不佳如果塑料流动性不佳,未等流到型腔末端或者未流到溢料槽就已冷凝,因而往往造成填充不足。
为了消除这种缺陷可提高溶料温度,并在熔料冷凝前使熔料流到型腔末端,也可加快注射速度。
也就是说提高料筒温度、提高注射压力,加快注射速度,也可提高模具温度。
在这种场合,塑料良好的流动性特别重要,所以更换流动性好的塑料也是一种解决方法。
4.流动阻力过大阻碍熔料流动的部位有喷嘴、主浇道、浇道、浇口和制件的薄壁处等。
采用如下方法可减小喷嘴流动阻力:加大喷嘴直径,提高喷嘴温度,使用流动阻力较小的喷嘴。
对于主浇道可增大其直径:对于浇道应避免采用流动阻力大的半圆形浇道,而采用圆形或梯形浇道,若增大直径则更好。
滚塑制品质量缺陷及解决方案

滚塑制品质量缺陷及解决方案背景介绍滚塑制品作为一种常见的塑料制品,广泛应用于家庭生活和工业生产中。
然而,由于制造过程中的一些问题,滚塑制品在质量方面可能存在一些缺陷。
本文将重点介绍滚塑制品常见的质量缺陷,并提供相应的解决方案。
常见质量缺陷以下是滚塑制品常见的质量缺陷:1. 毛边:在制造过程中,滚塑制品的边缘可能出现毛糙的问题,影响外观和使用舒适度。
2. 破裂:滚塑制品的强度可能不足,容易在使用过程中发生破裂。
3. 变色:长时间暴露在阳光下,滚塑制品会发生色彩变化,影响美观度。
4. 尺寸不准确:制造过程中可能出现尺寸偏差,导致滚塑制品不能完全装配或与其他部件不匹配。
5. 熔融痕迹:生产过程中的熔融痕迹可能会留在滚塑制品表面,影响外观和质量。
解决方案针对上述质量缺陷,以下是一些解决方案:1. 毛边处理:通过改进制造工艺,如优化模具设计和制备过程,可以减少滚塑制品毛边的产生。
2. 材料强度提升:选择高强度的原材料,并严格控制制造过程中的温度和压力,以提高滚塑制品的强度。
3. 防紫外线处理:在滚塑制品的表面添加抗紫外线涂层或使用具有抗紫外线特性的原材料,可以减缓滚塑制品的色彩变化。
4. 精确尺寸控制:加强对制造过程的监控,确保滚塑制品的尺寸准确性,并进行必要的仪器校准。
5. 表面处理:改进模具表面涂层以减少熔融痕迹的产生,或引入后续表面处理工艺来修复熔融痕迹。
结论滚塑制品在制造过程中可能会出现一些质量缺陷,但通过改进制造工艺和采取相应的解决方案,这些问题是可以得到解决的。
制造商应密切关注产品质量,并持续改进制造过程,以提供高质量的滚塑制品。
塑料制品缺陷及改善措施
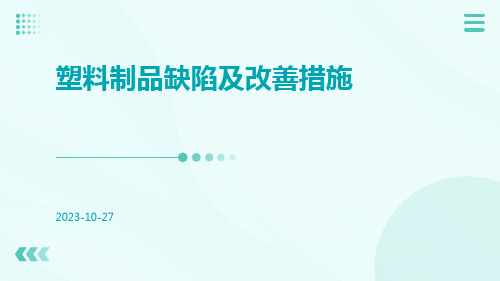
产生原因与危害
产生原因
塑料制品缺陷的产生原因很多,包括原材料质量不好、配方不合理、加工工 艺不当、设备故障、操作失误等。
危害
塑料制品缺陷会严重影响产品的质量、性能和外观,降低产品的使用价值和 寿命,甚至会对人体健康和安全造成威胁。
银纹
银纹是由于塑料在填充过程中混入的空气没有及 时排出而形成的,类似于气泡的一种缺陷。
银纹的产生可能是由于注射压力不足、注射速度 过快、模具温度不当等原因造成的。
银纹通常在塑料制品的表面或内部出现,形状为 细小的条状或网状。
改善措施:可以通过调整注射压力、注射速度和 模具温度来减少银纹的产生。在生产过程中,也 可以通过使用真空装置来帮助排出空气,从而避 免银纹的产生
VS
提高模具制造精度
采用高精度的数控机床等加工设备,提高 模具的制造精度,以减少制品缺陷。
调整生产工艺
优化注塑工艺
根据不同的塑料材料和制品要求,调整注 塑温度、压力和时间等工艺参数,以获得 理想的制品质量。
研究生产工艺优化方案
通过对生产工艺的研究和试验,找出最佳 的生产工艺参数,提高制品的质量和稳定 性。
裂纹
裂纹是由于塑料制品在冷却过程中产生的内应力 超过了塑料的抗拉强度而形成的。
裂纹的产生可能是由于注射速度过快、模具温度 过低、塑料的流动性差等原因造成的。
裂纹通常出现在塑料制品的表面或内部,形状为 线形或网状。
改善措施:可以通过降低注射速度、提高模具温 度、改善塑料的流动性来减少裂纹的产生。另外 ,可以通过调整塑料的配方,加入增韧剂等改性 剂来提高塑料的抗拉强度,从而减少裂纹的产生
滚塑制品质量疑虑与解决措施

滚塑制品质量疑虑与解决措施背景滚塑制品是一种常用的制造材料,它具有轻便、耐用、易于成型等优点,在家庭和工业领域得到广泛应用。
然而,近年来,一些关于滚塑制品质量的疑虑不断浮现,需要采取相应的解决措施,以确保其质量和安全性。
疑虑1:滚塑制品的材料质量滚塑制品通常采用聚乙烯或聚丙烯等塑料材料制成。
然而,市场上存在一些低质量的滚塑制品,这些制品的材料可能含有有害物质,如重金属和有毒化学物质。
这些有害物质可能会对人体健康造成危害。
解决措施:- 客户在购买滚塑制品时,应选择可靠的供应商,并查看相关的质量认证。
例如,CE认证和ISO质量管理体系认证等。
- 客户可以要求供应商提供滚塑制品的材料检测报告,确保其符合国内外相关质量标准。
疑虑2:滚塑制品的成型质量滚塑制品的成型质量直接影响其使用效果和寿命。
一些低质量的滚塑制品可能存在成型不完整、表面粗糙、内部疏松等问题,导致制品易损坏或功能不完善。
解决措施:- 客户在购买滚塑制品时,应仔细检查制品外观和质地,确保其成型质量良好。
- 客户可以要求供应商提供滚塑制品的成型工艺和生产流程,以了解其生产质量控制情况。
疑虑3:滚塑制品的结构强度滚塑制品在使用过程中需要承受一定的压力和负荷。
因此,滚塑制品的结构强度十分重要。
低质量的滚塑制品可能存在结构弱化、连接部位薄弱等问题,导致制品易变形或损坏。
解决措施:- 客户在购买滚塑制品时,应关注制品的结构设计和连接方式。
尽量选择结构合理、连接坚固的制品。
- 客户可以要求供应商提供滚塑制品的结构分析报告,确保其结构强度达标。
结论为了解决滚塑制品质量疑虑,客户应选择可靠的供应商,并采取相应的解决措施,确保所购买的滚塑制品质量和安全性。
同时,客户也应提高对滚塑制品质量的意识,以便及时发现并解决可能存在的问题。
塑胶产品不良原因及处理方法

架模調機操作程序
注意事項
1 檢查模具是否有異常,吊起模具.
模具組裝錯誤一定會損壞模具.
2 按下調模鍵
減漫速度,易架模
3 對準進料口中心,呈現圓孔
未呈現圓孔造成漏料
4 銷緊模具
模具會掉落,增加工作危險
5 按下細調模或粗調模,進與退並把低壓位 高壓表升至50bar,射出壓力將造成模具不能完 置向前移高壓調至90bar,逼模至壓力表 全閉合. 升至50~80bar
結晶化度 熱安全性 流動化
模腔形狀 注口形狀
耐定性
模具材質 模具溫度
成形品物性
可塑化容量 可塑化方式
成形機
銷模力
射出壓力 冷卻時間 (模具溫度)
成形條件
料管溫度 (樹脂溫度)
螺桿轉速
射出條件
一.縮水
塑膠品在表面的凹陷,空洞都稱為[縮水],除了會影響產品外觀,亦 會降低成品品質及強度,縮水的原因與成型技術,模具設計及使用塑料均有關 系.
七.毛邊
毛邊(俗稱彼峰)是一种很常到的注塑問題.當塑料在模腔內的壓力 太大,其所產的分模力大過鎖模力,因而迫開工模,使塑料走出來並在塑件表 層形成彼峰.但是引致此現象的成因卻可能有很多,种例如塑料方面的問題, 或是射出機有損,壞或是調校不適當,以至工模本身也有可能.
一般來說,與溫度,壓力及操作時序有關,因此要找出其解決方法也 不容易.由於塑料的粘度會影響其流動速度及壓力損耗,因此粘度太高或是太 低都可以引致毛邊.如果塑料的粘度太低,則其流動性高,便很容易流入工模 合模面之間的微小空隙,增大分模力,直至出現彼峰.尼龍便是一個曲型例子, 所以在模塑尼龍時便需要較大的鎖模力.在另一方,面如果塑料的粘度太高, 則其流動阻力便很大,因而產生大的背壓,使模腔內的塑料的平均壓力提高, 同樣會引致毛邊.
滚塑产品品质管控方案

滚塑产品品质管控方案
滚塑产品的品质管控方案是一个关键的过程,确保产品能够达到客户的要求和满足市场需求。
下面是一个针对滚塑产品的品质管控方案的示例。
一、品质目标
确定滚塑产品的品质目标,包括产品的外观质量、功能性能、耐久性和安全性等方面。
确保产品能够稳定地满足客户需求。
二、原材料选择和采购
1.选择高质量的原材料,确保滚塑产品的质量。
2.建立合格供应商名单,选择可靠的供应商,确保原材料的稳定供应。
3.对原材料进行严格的检验,确保其符合产品要求。
三、生产过程控制
1.建立严格的生产工艺流程,确保产品质量的稳定。
2.对生产设备进行定期维护和保养,确保其正常运行。
3.对生产过程进行严格监控,包括注塑、模具、涂装等环节,确保产品质量的一致性。
四、产品检验
1.制定产品检验标准和方法,确保产品的合格率。
2.对每批产品进行全面检验,包括外观质量、功能性能等方面。
3.建立合格率统计表,对产品品质进行监控和改进。
五、原材料和产品追溯
建立原材料和产品追溯系统,对原材料和产品进行追溯,以便及时发现和解决问题,确保产品的安全性和质量。
六、客户满意度调查
定期进行客户满意度调查,了解客户对产品质量的评价和需求,及时改进和调整产品品质管控方案。
七、培训和提升
定期对生产人员进行品质培训,提高他们的品质意识和操作技能。
定期进行品质管理评审,总结经验教训,不断提升产品质量管理水平。
通过以上的滚塑产品品质管控方案,可以有效地保证产品的质量和稳定性,满足客户的需求,提升企业的竞争力。
塑料制品的故障分析与质量改进

添加标题
压力控制不当:可能导致塑料制品 凹陷、磨损等故障
模具设计问题:可能导致塑料制品 无法脱模、表面缺陷等故障
环境因素影响
温度变化:可能导致塑料制品变形、开裂等故障 湿度变化:可能导致塑料制品吸湿、膨胀等故障 光照影响:可能导致塑料制品褪色、老化等故障 化学物质影响:可能导致塑料制品腐蚀、变质等故障
Байду номын сангаас
尺寸偏差
影响:影响产品的外观、性 能和使用寿命
原因:模具设计不合理、材 料选择不当、加工工艺问题 等
检测方法:使用卡尺、千分 尺等测量工具进行测量
改进措施:优化模具设计、 选择合适的材料、改进加工
工艺等
性能不足
强度不足:塑料制品在承受外力时 容易断裂或变形
耐候性不足:在户外环境中,塑料 制品容易老化、褪色或变脆
所在
改进措施:根 据数据分析结 果,制定针对 性的改进措施
效果评估:对 改进措施进行 效果评估,确 保改进效果达
到预期
持续改进机制
定期检查:对塑料制品进行定期的质量检查,及时发现问题 数据分析:对检查数据进行分析,找出质量问题的原因 改进措施:根据数据分析结果,制定改进措施,提高产品质量 跟踪评估:对改进措施进行跟踪评估,确保改进效果达到预期
添加标题
添加标题
添加标题
添加标题
耐热性不足:在高温环境下,塑料 制品容易软化或熔化
耐磨性不足:塑料制品在使用过程 中容易磨损,影响其使用寿命
断裂与开裂
原因:材料强度 不足,加工工艺 不当,环境因素 等
影响因素:材料 选择,模具设计, 加工条件等
预防措施:选用 合适的材料,优 化模具设计,改 善加工条件等
塑料制品的故障分析 与质量改进
塑件常见缺陷及解决方案

注塑件常见成型缺陷及解决方案在注塑成型加式过程中,可能由于原材料处理不好、塑件或模具设计不合理、操作工没有掌握合适的工艺操作条件,或者因机械方面的原因,常常使塑件产品短射、凹痕、飞边、困气、开裂、翘曲变形等成型缺陷。
塑件在成型过程中出现的各种注塑缺陷,主要有:短射,困气,发脆,烧焦,飞边,分层起皮,喷流痕,流痕,雾斑(浇口晕),银纹(水花纹),凹痕,熔接痕,成型周期过长,翘曲变形,分析了问题产生的可能原因,从原材料、塑件或模具设计、成型工艺等各方面,提出解决方案。
一.短射短射是指模具型腔不能被完全充满的一种现象。
短射形成原因:1、模温、料温或注塑压力和速度过低2、原料塑化不均3、排气不良4、原料流动性不足5、制件太薄或浇口尺寸太小6、聚合物熔体由于结构设计不合理导致过早固化短射解决方案:材料:选用流动性更好的材料模具设计:1、填充薄壁之前先填充厚壁,避免出现滞留现象2、增加浇口数量和流道尺寸,减少流程比及流动阻力3、排气口的位置和尺寸设置适当,避免出现排气不良的现象注塑机:1、检查止逆阀和料筒内壁是否磨损严重2、检查加料口是否有料或是否架桥工艺条件:1、增大注塑压力和注塑速度,增强剪切热2、增大注塑量3、增大料筒温度和模具温度二.困气困气是指空气被困在型腔内而使制件产生气泡。
困气形成原因:它是由于两股熔体前锋交汇时气体无法从分型面、顶杆或排气孔中排出造成的。
困在型腔内气体不能被及时排出,易导致出现表面起泡,制件内部夹气,注塑不满等现象。
困气解决方案:结构设计:减少厚度的不一致,尽量保证壁厚均匀模具设计:1、在最后填充的地方增设排气口2、重新设计浇口和流道系统工艺条件:1、降低最后一级注塑速度.2、增加模温塑件发脆是指制件在某些部位出现容易开裂或折断。
发脆原因:1、干燥条件不适合;使用过多回收料2、注塑温度设置不对3、浇口和流道系统设置不恰当4、熔解痕强度不高发脆解决方案:材料:1、注塑前设置适当的干燥条件2、减少使用回收料,增加原生料的比例.3、选用高强度的塑胶.模具设计:增大主流道、分流道和浇口尺寸注塑机:选择设计良好的螺杆,使塑化时温度分配更加均匀工艺条件:1、降低料筒和喷嘴的温度2、降低背压、螺杆转速和注塑速度3、通过增加料温,加大注塑压力,提高熔解痕强度四.烧焦焦痕是指型腔内气体不能及时排走,导致在流动最末断产生烧黑现象。
塑料制品缺陷及改善措施

塑料制品缺陷及改善措施
随着现代化社会的发展,塑料制品已经成为人们日常生活的必需品,因其成本低廉、易加工、轻便等优点而深受人们喜爱。
但是,由于塑料不易降解,造成了巨大的环境污染和资源浪费。
本文将以塑料制品的缺陷作为主要研究的对象,探讨塑料制品的改善措施。
一、塑料制品的缺陷
1、易碎:尽管塑料制品轻便易携带,但是它具有易碎性。
一旦掉落或者撞击,塑料制品容易出现破裂或变形的现象,影响使用寿命。
2、易老化:塑料制品通常使用寿命比较短。
当塑料制品
受到阳光、氧气、热、光的暴露,会发生老化而失去使用价值。
3、污染环境:塑料制品很难被分解,因此被誉为是环境
的“白色污染源”,严重影响了环境的美观和生态健康。
二、改善措施
1. 选择更加环保的材料
生物可降解材料是一个良好的替代品。
例如,一些聚乳酸等可生物降解塑料可以取代传统的塑料制品。
2. 降低塑料制品的污染
应当建立一个完善的废塑料回收和处理系统。
塑料制品的回收利用应该得到强化和推广,使塑料废弃物得以重生。
3.增强塑料质量
通过改变塑料的配方和工艺,生产高质量的塑料制品,提高其韧性和耐用性。
4. 推广环保理念
我们需要加强宣传,让人们认识到塑料制品的危害,引导人们减少对塑料制品的依赖,采用更加环保的替代品,从而推动环保理念广泛普及。
5.加强管理
政府和相关行业部门应加强对塑料制品的监管,推行生产、销售与使用责任制,加强塑料制品的质量监管工作。
最后,塑料制品的缺陷已经得到广泛关注,因此,我们需要加强塑料制品的改善工作,减少其对环境造成的污染,让其真正成为环保的材料。
塑料制品缺陷及改善措施

1、塑料制品缺陷及改善措施2、排除缺料的方法3、排除制品银条痕的方法4、排除制品飞边的方法5、排除制品变形的方法6、排除制品裂纹的方法7、排除制品应力龟裂的方法8、排除制品网装龟裂的方法9、排除制品白化的方法10、排除制品熔合痕的方法11、排除制品内波流的方法12、排除制品产生糊斑的方法13、排除制品产生黑条的方法14、排除制品色不平均的方法15、排除制品光洁度不良的方法16、排除制品气蚀的方法17、排除制品漩纹的方法18、排除制品脆化的方法19、排除制品使用破裂料产生白化以及脆化的方法20、排除制品内异物不良的方法21、排除制品产生剥离现象的方法22、排除制品尺寸不良的方法23、排除制品小皱纹的方法24、排除制品脱模时的破旧以及裂纹的方法25、排除注口料脱模不良的方法26、排除制品上痕迹的方法27、排除制品透亮度不良的方法28、排除制品浇口断裂的方法29、排除制品厚度偏差的方法30、排除模具错位的方法31、防止模具胀裂的方法32、防止模具导柱折断的方法33、防止模具咬合的方法34、防止模具生锈的方法35、如何使残留在模具内注口料脱出的方法36、如何使残留在模具内制品出来的方法37、补救外观不良制品的方法38、制品翘曲的矫正方法39、排除制品上热压印不明的方法40、排除制品剥落的方法41、成型缺陷的计策表42、同一材料异色的替换作业43、不同材料的替换作业44、常见塑料材料的简单判别45、常见塑料材料的注塑温度和预干燥温度46、浇口的大小同成型性能的关系47、什么是注塑成型的五要素48、一样的模具构造49、模具的注口,流边和浇口50什么是捏和性螺杆51何谓注塑机52何谓注塑机的注塑量53何谓注塑机的可塑化能力54何谓成形收缩率55何谓成形所必要的锁模力56制品脱模的方法57在固定侧使制品脱模的方法58模具冷却的方法59制品厚度的范畴60加强筋同凸起部的设计方法61设计容器类制品时地注意点62透亮塑料有那些东西63有既透亮又耐冲击性的塑料吗?64耐冲击性最好的塑料是ABS吗?65有耐热性的塑料吗?66耐摩性好的塑料材料那些67倾向于刚性用途的材料是那些68要求制品具有弹性时用什么样的材料69有那些材料是能够镀的70耐燃性的材料有那些71耐药品性的塑料有那些72有必要于干燥的塑料有那些73在料筒内容易分解的塑料有那些74要求成形模具温度高的塑料是那些75流淌性太好的塑料在成形上的注意点76成形后必须清除料筒的塑料是那些77塑料的热特性同其它材料的比较78塑料的化学特性同其它材料的比较79塑料的电气特性同其它材料的比较80塑料的老化性能同其它材料的比较81塑料的加工精度同其它材料的比较82塑料的强度同其它材料的比较83塑料使用的可塑剂有那些东西84塑料使用的安定剂有那些东西85塑料使用的润滑剂有那些东西86塑料使用的填充剂有那些东西87塑料使用的色料有那些东西88塑料使用的发泡剂有那些东西89什么叫体积电阻90什么叫表面电阻91什么叫电弧阻抗92什么叫诱电率93什么叫热变形温度94塑料的分子构造同机械性能的关系如何95塑料的分子构造同耐热性的关系如何96塑料的分子构造同耐湿性的关系如何97塑料的分子构造同耐热性的关系如何98什么是SP值99高分子的结晶化度同溶解度参数的关系如何样100转移点同分子构造的关系如何样101什么叫溶化指数102支配成形性的要点有那些参数103模具内的压力是如何样地变化104树脂温度同射出压对浇口长度有什么阻碍105成形工程中材料密度是如何样地变化106结晶性塑料在成形上的注意点107配向是如何样的现象108成形性能同分子量、分子构造的关系如何样109塑料的流淌性特性同流变学110何谓标准注嘴111何谓延长注嘴112何谓溶化型注嘴113何谓搅拌型注嘴114何谓阀控式注嘴115何谓热流道注嘴116注嘴接触应如何样117模具的一般制作方法时那些118应如何加工模具型腔内带有的花纹119何谓电铸模具120何谓铜合金铸造模具121何谓滚切模具122何谓陶瓷式成型法(肖式周密铸造法) 123何谓电火花加工124何谓L位置注塑机125何谓折缘注塑机126何谓旋转式注塑机127何谓高速注塑机128何谓排气式注塑机129何谓低压注塑机130何谓流淌型注塑机131何谓发泡专用注塑机132何谓外壳专用注塑机133何谓压缩成型机134何谓夹层发泡注塑机135何谓锤打式注塑机136注塑机注塑制品的制作程序137注塑制品的设计程序138常见注塑机的所属设备139制品的成本同日期待决定方法140模具的制作顺序141电视机外壳使用有那些特性的材料142电冰箱内装饰品使用那些特性的材料143洗衣机的小部件使用那些特性的材料144照相机的小部件使用那些特性的材料145贮存器具使用那些特性的材料146小汽车部件使用那些特性的材料147周密齿轮使用那些特性的材料148家具使用那些特性的材料149注塑成型的进展方向50、常见塑料材料的中、英名称和简写1、排除制品凹痕的方法一、产生凹痕的缘故1-1制品各部分厚度不同1-2模具内在压力不足1-3模具冷却不充分1-4由于冷却时刻不足而产生的变形二、相关联的知识2-1 在生产制品过程中,凹痕是不良现象中发生频率最高的,注入模具的塑料在冷却时发生体积收缩,早冷却部分即表面第一硬化,内部就会产动气泡,所谓凹痕,确实是冷却慢的部分在气泡收缩的方向产生了显眼的凹面。
塑料制品缺陷及改善措施
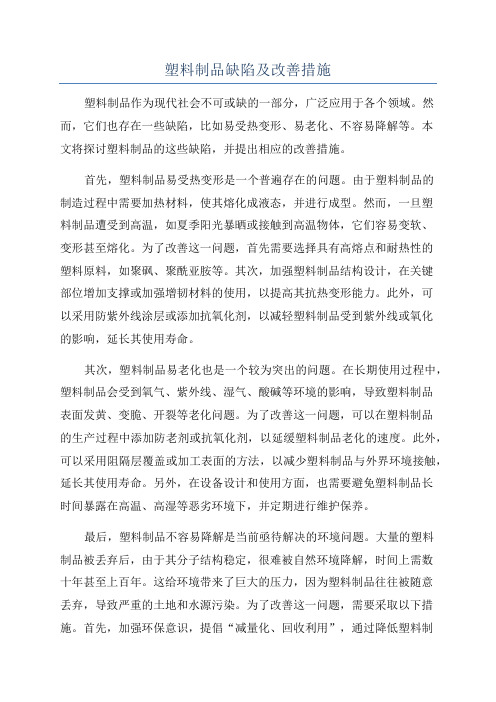
塑料制品缺陷及改善措施塑料制品作为现代社会不可或缺的一部分,广泛应用于各个领域。
然而,它们也存在一些缺陷,比如易受热变形、易老化、不容易降解等。
本文将探讨塑料制品的这些缺陷,并提出相应的改善措施。
首先,塑料制品易受热变形是一个普遍存在的问题。
由于塑料制品的制造过程中需要加热材料,使其熔化成液态,并进行成型。
然而,一旦塑料制品遭受到高温,如夏季阳光暴晒或接触到高温物体,它们容易变软、变形甚至熔化。
为了改善这一问题,首先需要选择具有高熔点和耐热性的塑料原料,如聚砜、聚酰亚胺等。
其次,加强塑料制品结构设计,在关键部位增加支撑或加强增韧材料的使用,以提高其抗热变形能力。
此外,可以采用防紫外线涂层或添加抗氧化剂,以减轻塑料制品受到紫外线或氧化的影响,延长其使用寿命。
其次,塑料制品易老化也是一个较为突出的问题。
在长期使用过程中,塑料制品会受到氧气、紫外线、湿气、酸碱等环境的影响,导致塑料制品表面发黄、变脆、开裂等老化问题。
为了改善这一问题,可以在塑料制品的生产过程中添加防老剂或抗氧化剂,以延缓塑料制品老化的速度。
此外,可以采用阻隔层覆盖或加工表面的方法,以减少塑料制品与外界环境接触,延长其使用寿命。
另外,在设备设计和使用方面,也需要避免塑料制品长时间暴露在高温、高湿等恶劣环境下,并定期进行维护保养。
最后,塑料制品不容易降解是当前亟待解决的环境问题。
大量的塑料制品被丢弃后,由于其分子结构稳定,很难被自然环境降解,时间上需数十年甚至上百年。
这给环境带来了巨大的压力,因为塑料制品往往被随意丢弃,导致严重的土地和水源污染。
为了改善这一问题,需要采取以下措施。
首先,加强环保意识,提倡“减量化、回收利用”,通过降低塑料制品的使用量,减少废弃物的产生。
其次,加强塑料制品的可降解性研究,选择可生物降解的塑料原料,并促进相关技术和产业的发展。
此外,可以推广塑料包装物回收利用,提高塑料废弃物的回收率,减少其对环境的影响。
总之,塑料制品在现代社会中具有重要的地位,但它们也存在一些缺陷。
塑件缺陷原因及改善方法
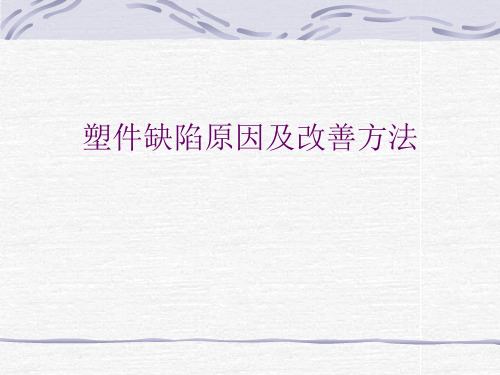
3. 厚壁塑件是最容易产生缩水的,为 减少缩水的出现,浇口形式的选择较为 关键,如翼式浇口对消除缩水的效果就 非常好。
4. 模具冷却不均衡或冷却不足,很易 产生缩水,对此,必须重视冷却系统的 设计和制造,对于易产生缩水的部位应 强化冷却措施。
5. 熔体温度太高,塑件冷却不足,容 易引起塑件凹陷,对此,应降低熔体温 度。
10.
注塑机的喷嘴孔太小或局部堵塞,
会使注射压力局部损失过大,易产生缩
水,对此,应更换大直径的喷嘴,或对
喷嘴进行清理疏通。
11.
树脂的收缩率越大,产生的缩水
可能越大,因此,应尽量先用低收缩率
的树脂为原料。
七.塑件产生气泡的原因和 改善方法?
塑件中之所以出现气泡,是因为有大 量气体混入熔体中,随熔体一起冷却成 型而得。其具体分析如下:
(1) 采用直浇口,在塑件保压结束后,型腔 中的压力比浇口前方的压力高,如此时直浇口 处的熔体尚未固化,就会发生熔体回流,使塑 件内部产生真空泡,对此,应避免选用直浇口。
(2) 浇口面积过小,或位置不正确,易于引 起真空泡,对此,要调整浇口截面积及位置。
(3) 浇口位置没有设在壁厚处,则易出现真 空泡,对此,浇口应设在塑件的厚壁处。
12. 止逆阀出现故障,会使熔体倒流, 导致熔体供料不足,对此,应检修止逆阀。
13. 射料杆与料筒间的间隙过大,熔体 便会顺其间隙回流,导致供料不足而欠注。 这种间隙过大多是过度磨损造成,对此, 要更换相关零件将其修复。
二.塑件产生夹水线的原因和 改善方法?
产生熔接痕的主要原因,系由若干胶 熔体的型腔中汇合在一起时,在其交汇处 未完全熔合在一起,彼此不能熔合为一体 而形成夹水线。其具体分析如下:
8. 保压压力过高,塑件成型时的内应力会过 高,脱模后,内应力的不均衡释放将使塑件产 生翘曲变形,对此,应适当降低保压压力。
滚塑产品质量问题及解决措施

滚塑(rotational molding)生产过程中常见的产品质量问题及应对措施(一)在滚塑生产过程中,常常会出现一些大大小小的产品质量问题,这些都可以通过一些必要的措施来避免。
本文集中描述了一些滚塑成型工艺中在滚塑生产过程中,常常会出现一些大大小小的产品质量问题,这些都可以通过一些必要的措施来避免。
本文集中描述了一些滚塑成型工艺中的常见问题及解决方案,以期与大家共同探讨。
1.插入嵌件不牢固或边缘周围有吹孔。
影响因素:1.1插入嵌件尺寸不符合要求,周围空间太小,嵌件彼此太接近或太靠近模壁,局部受到屏蔽导致受热不均匀。
1.2安装嵌件时,未注意清洁,嵌件受到污染1.3嵌件预热过度,插入后粘附粉料。
1.4嵌件固定不良,旋转模塑时松动。
1.5嵌件的材质影响。
有些导热性不强或过度导热。
可能的解决方法:嵌件做良好固定,且保证其不要松动;嵌件周围不要留有空隙,以免空气吸入造成湿气膨胀而侵入产品内部;附着在嵌件上的污染物如牛油、机油会在成型时气化,从而产生气泡而让粉料无法粘附,使用前要对嵌件作适当的清洗、干燥处理;使用大型的嵌件时要涂布兼容材料以保障其粘附效果;如果嵌件材料具良好的导热性,可对嵌件进行轻微的屏蔽,避免嵌件过热而在产品截面产生气泡;如嵌件导热性差,可提前预热至合适的温度。
2.合模线处出现吹孔。
主要原因:2.1 合模线不干净2.2通气管阻塞2.3合模线错位2.4成型时模内气压过大2.5合模线变成热沉体。
解决方案:确保合模线的干净是前提条件,合模线处残留的积塑会致合模线密封不良,模具外的空气会乘虚而入或积塑劣化而产生吹孔。
用适当的工具清理合模线处的残渣或用脱模剂涂布降低残渣的附着机会不失为一个好的方法。
在滚塑模具添加粉料时,尽量让粉料远离合模线,一旦不慎漏洒上粉料要及时清理干净。
通气管阻塞会让空气流无法进入滚塑模具,许多人认识不到这点的严重性。
在滚塑成型第三期及冷却期,模具内的聚合物仍然呈熔融状态,如果空气不能自由出入而保持模具内外的气压平衡,要么形成负压而至产品收缩,要么气体从合模线处不严密的地方穿过而留下吹孔。
塑件制品质量缺陷及改正措施

(7)制品表面有波纹
1)原料塑化不均匀,应适当提高机筒加热温度或提高螺杆工作背压。 2)注射压力选择的不合理,过高或过低的注射压力都能影响制品的 表现质量。 3)保压、降温固化时间不足,应适当延长。 4)原料中含水量过高,应对原料进行干燥处理后再使用。 5)熔料的注射速度选择的不合理,过高或过慢的注射速度都会影响 制品的表观质量。
6)模具的成型面光洁度不够,使制品表面粗糙,应研磨修光模具成
型面。
(8)制品表面有气泡和银纹
1)制品用原料含水分超标,应对原料进行干燥处理。 2)原料中的添加剂不耐高温,应调整更换。 3)原料塑化温度偏高或者是在机筒内停留时间过长,应降低机筒前 段温度或改用较小规格注塑机。 4)螺杆工作背压小,应适当提高螺杆背压。 5)保压压力偏低或降温固化时间短,应提高保压压力或延长降温定 型时间。
6)成型模具温度偏低,应提高模具温度。
7)注射压力或注射速度有些偏高,应适当降低些注射压力和注射速 度。
(9)制品表面无光泽
1)原料塑化熔融质量不均匀,应适当提高机筒加热温度或提高螺杆 工作背压。 2)原料中含水分偏高,应对原料干燥处理,使原料中含水分在允许 指标内。 3)模具内成型制品工作面粗糙或有水珠,应研磨抛光工作面,提高型 腔表面光亮度。 4)原料附加料配加不当,应调整更换。
制品的质量分析
实际生产中制品质量缺陷主要包括以下几个方面。其改正措施如下所列。 (1)注塑制品的外形结构尺寸不完整 (2)制品的外形尺寸不稳定,出现收缩现象 (3)制品脱模困难
模塑行业产品质量追溯困难应急处理预案
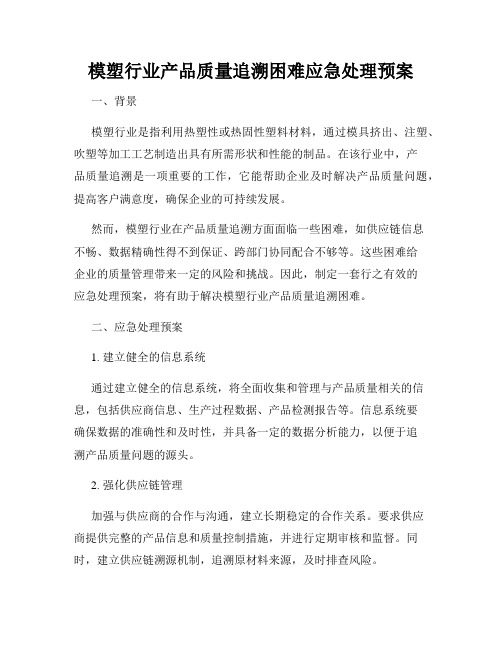
模塑行业产品质量追溯困难应急处理预案一、背景模塑行业是指利用热塑性或热固性塑料材料,通过模具挤出、注塑、吹塑等加工工艺制造出具有所需形状和性能的制品。
在该行业中,产品质量追溯是一项重要的工作,它能帮助企业及时解决产品质量问题,提高客户满意度,确保企业的可持续发展。
然而,模塑行业在产品质量追溯方面面临一些困难,如供应链信息不畅、数据精确性得不到保证、跨部门协同配合不够等。
这些困难给企业的质量管理带来一定的风险和挑战。
因此,制定一套行之有效的应急处理预案,将有助于解决模塑行业产品质量追溯困难。
二、应急处理预案1. 建立健全的信息系统通过建立健全的信息系统,将全面收集和管理与产品质量相关的信息,包括供应商信息、生产过程数据、产品检测报告等。
信息系统要确保数据的准确性和及时性,并具备一定的数据分析能力,以便于追溯产品质量问题的源头。
2. 强化供应链管理加强与供应商的合作与沟通,建立长期稳定的合作关系。
要求供应商提供完整的产品信息和质量控制措施,并进行定期审核和监督。
同时,建立供应链溯源机制,追溯原材料来源,及时排查风险。
3. 完善质量控制体系建立和完善质量控制体系,包括原材料进货检验、生产工艺控制、产品出厂检测等。
每个环节都要严格按照质量控制标准进行操作,并记录相关数据。
一旦发现质量问题,要能够快速准确地定位和排查,采取相应的纠正措施。
4. 增强数据分析能力在信息系统的基础上,建立数据分析能力,并通过数据挖掘技术对大量数据进行分析和处理。
通过对数据的深入挖掘,可以找出产品质量问题的潜在原因,采取相应的预防和改进措施。
5. 加强内外部协同配合在产品质量追溯的过程中,各部门之间需要紧密协作,共同解决问题。
要建立相应的沟通机制,及时分享信息和经验,形成合力。
同时,与相关的监管部门和行业协会保持良好的合作关系,充分发挥外部资源的作用。
6. 做好应急预案的培训和演练制定的应急处理预案需要向相关人员进行培训,并进行定期的演练。
影响滚塑(旋塑)产品质量的因素有哪些?

影响滚塑(旋塑)产品质量的因素有哪些?影响旋塑产品质量的因素有很多,其中比较重要的有模具的形状,模具的旋转速度,模具加热温度、加热时间,塑料粉末的物理特征等等。
1、旋塑产品的模具旋塑用的模具是单壁封闭模具,它给出制品的外形轮廓而对制品内部轮廓无法准确到细部。
旋塑用模具的制模材料一般选择普通碳钢板焊接。
焊接模成本比较低,尤其适用于大型旋塑制品。
旋塑工艺对其模具有如下基本要求:模具在反复加热和冷却的过程中不容易发生变形和挠曲。
模具上应附有便于松脱的夹持机构,以使模具在加热和冷却工序中能紧密闭合,而在需要卸下制品和装料时又能很容易的打开。
模具的设计和安装应有利于气流围绕模具表面作相对运动,以便使模具得到均匀的加热和冷却。
模具应设置通气管道,以防止在加热过程个模具内气体受热膨胀而把熔融的塑料沿合模缝挤出,并且防止在冷却过程中模具内产生负压而导致模具和制品变形。
模具局部结构设计时应尽量避免较深的腔和洞,以及加强筋和实心凸起之类的结构,因为粉末状的物料很难布满上述结构的表面。
模具重量和物料重量之和不能超过旋塑机的最大承受能力。
2、旋塑模具的旋转速度通常旋塑机采用两个可调速电机为模具绕主轴及次轴的旋转、摇摆运动提供动力,这样模具的绕主轴转速和绕次轴摇摆皆可调节。
操作者通过调节两个调速电机的转速,可在任何制品形状下获得相对均匀的制品壁厚。
模具旋转、摇摆的基本作用是使粉状物料均匀混合并遍布模具表面。
3、聚乙烯粉末的颗粒大小聚乙烯粉末颗粒的大小对其熔融过程有重要的影响。
颗粒越小,其表面积与体积之比越大,熔融速率就越高。
通常旋塑粉末颗粒应不低于30目,但是,粉末颗粒尺寸也不宜过小,因为太细的粉末极易吸湿、结块,很难烘干,增加工艺上的困难。
太细的粉状物料在模具中翻滚时将会结块,导致粉末的不均匀受热,最终形成不均匀的制品壁厚或者在制品中形成熔融不充分的塑料。
实验表明一次性加入旋塑模具内的的聚乙烯粉末的颗粒大小不要一致或均匀,大小有序的粉末颗粒在加热模具中,由于粗细粉末吸热熔融时间有长短、快慢,使熔融塑料逐渐堆积,逐步成型。
- 1、下载文档前请自行甄别文档内容的完整性,平台不提供额外的编辑、内容补充、找答案等附加服务。
- 2、"仅部分预览"的文档,不可在线预览部分如存在完整性等问题,可反馈申请退款(可完整预览的文档不适用该条件!)。
- 3、如文档侵犯您的权益,请联系客服反馈,我们会尽快为您处理(人工客服工作时间:9:00-18:30)。
滚塑(rotational molding)生产过程中常见的产品质量问题及应对措施(一)在滚塑生产过程中,常常会出现一些大大小小的产品质量问题,这些都可以通过一些必要的措施来避免。
本文集中描述了一些滚塑成型工艺中在滚塑生产过程中,常常会出现一些大大小小的产品质量问题,这些都可以通过一些必要的措施来避免。
本文集中描述了一些滚塑成型工艺中的常见问题及解决方案,以期与大家共同探讨。
1.插入嵌件不牢固或边缘周围有吹孔。
影响因素:插入嵌件尺寸不符合要求,周围空间太小,嵌件彼此太接近或太靠近模壁,局部受到屏蔽导致受热不均匀。
安装嵌件时,未注意清洁,嵌件受到污染嵌件预热过度,插入后粘附粉料。
嵌件固定不良,旋转模塑时松动。
嵌件的材质影响。
有些导热性不强或过度导热。
可能的解决方法:嵌件做良好固定,且保证其不要松动;嵌件周围不要留有空隙,以免空气吸入造成湿气膨胀而侵入产品内部;附着在嵌件上的污染物如牛油、机油会在成型时气化,从而产生气泡而让粉料无法粘附,使用前要对嵌件作适当的清洗、干燥处理;使用大型的嵌件时要涂布兼容材料以保障其粘附效果;如果嵌件材料具良好的导热性,可对嵌件进行轻微的屏蔽,避免嵌件过热而在产品截面产生气泡;如嵌件导热性差,可提前预热至合适的温度。
2.合模线处出现吹孔。
主要原因:合模线不干净通气管阻塞合模线错位成型时模内气压过大合模线变成热沉体。
解决方案:确保合模线的干净是前提条件,合模线处残留的积塑会致合模线密封不良,模具外的空气会乘虚而入或积塑劣化而产生吹孔。
用适当的工具清理合模线处的残渣或用脱模剂涂布降低残渣的附着机会不失为一个好的方法。
在滚塑模具添加粉料时,尽量让粉料远离合模线,一旦不慎漏洒上粉料要及时清理干净。
通气管阻塞会让空气流无法进入滚塑模具,许多人认识不到这点的严重性。
在滚塑成型第三期及冷却期,模具内的聚合物仍然呈熔融状态,如果空气不能自由出入而保持模具内外的气压平衡,要么形成负压而至产品收缩,要么气体从合模线处不严密的地方穿过而留下吹孔。
正确制定模具的通气管的长度也是必要的,且每个模塑周期都必须检查通气管内的填充物是否还具透气功能。
模具错位或配合不良必然引起合模线处的开口现象,这样的模具所生产的滚塑产品显然会有裂口。
适当地旋紧该处的螺丝或增大夹具压力是常用办法,以达到合模线的准确配合。
如果在加热成型或冷却过程中采用了模具内增压,如果压力过大会造成熔融聚合物的挤出。
你需要对模具内的压力做适当的调整。
合模线处一般比模具其它地方厚重结实,自然,在加热过程中会变成热沉体而降低此处模具的温度,如果采用的材料为成型周期较长才能消除气泡,那么整条合模线处都可能看到气泡。
你可以用预热合模线的方式来消除气泡。
3.其它地方的吹孔。
有时吹孔不一定会是在合模线处,细心的滚塑工人可能要问,这是什么原因:铸铝模与生俱来的气孔钢板模焊接不良也会留下气孔。
模具的材质问题——有不纯物夹杂其中解决方法:如果是陷在滚塑模具表面的气孔,滚塑成型时模内的热空气会迅速膨胀而致吹孔的产生。
改变这种现象首先是要提高模具铸造的技术水平。
如果是较少的气孔,且滚塑成型产品的表面痕迹可以为客户所接受,可以采用敲打或抛光冷焊接的方法来解决,当然这是事后弥补之计,无奈之举,治标不能治本,不足取。
不锈钢模具或钢板模在焊接的地方会有气孔产生,要反复加以修补直到无气孔砂眼为止。
确保模具表面的清洁也是一个重要环节。
任何的不纯物在脱落后都会形成成型产品的吹孔。
4.滚塑产品表面或截面出现气泡,其原因:滚塑成型过程中加热或循环方式不当滚塑原料——树脂聚合物的熔融指数太低脱模剂的使用不当——过多使用致脱模剂塑化原料粉体内有水分存在或混入其它加热挥发性物质粉料的颗粒粒径不符要求——过大滚塑模具内残留水分解决方法:所有的滚塑产品在成型初期都会形成泡,不过可以利用持续加热的方式来排除气泡的产生,再有一点就是变更原料的粘度来达到消除气泡的目的。
如果滚塑产品出现大量的气泡,则表示塑化不完全以及加热时间过短,适当地调整加热时间或提高加热温度可以得到改善。
树脂聚合物的熔融指数会影响气泡的生成和消失。
增加树脂原料的熔融指数会让原料颗粒更容易融合在一起。
不适合或劣质的脱模剂会在大部分材料的表面形成细微的针孔;脱模剂的过量使用也会产生针孔。
采用适当的温和方式擦掉脱模剂会收到好的效果。
树脂原料内的湿气和挥发性物质会导致滚塑产品表面的气泡。
如尼龙和聚碳酸酯材料在使用之前必须做干燥处理。
交联聚乙烯含有大量的触媒残渣,或聚碳酸酯内的残余挥发性溶剂都是气泡产生的推手。
交联类材料如加热太快会导致提前交联而致气泡残留在材料的截面。
尺寸过大的粉料或颗粒会导致产品表面气泡,需检查粉体的流动性和粉料颗粒的粒径及颗粒大小的分配比例。
(详见拙文滚塑工艺对聚乙烯粉料颗粒的要求)滚塑模具内残余的水分会在成型过程中因受热而形成水蒸气滞留在产品中而形成气泡。
闲置的滚塑模具要保持干燥,即使是模具外壁也不能挂有水珠。
所以,在滚塑生产中要注重模具的日常保护。
(滚塑钢板模具的防锈处理方法与铝合金模具和铝浇铸模具不同,滚塑钢板模具闲置时容易生锈,尤其在冬天气温较低时,先一天生产过的模具,第二天上班时就发现已经锈迹斑与铝合金模具和铝浇铸模具不同,滚塑钢板模具闲置时容易生锈,尤其在冬天气温较低时,先一天生产过的模具,第二天上班时就发现已经锈迹斑斑了。
因为热的模具在冷却的过程中,空气中的水分会逐渐凝聚在模具内表面,引起模具生锈。
解决滚塑模具锈蚀问题最好的方法是做表面防护处理,其流程为:模具清洗——磷化——清洗——烘干——喷涂特氟龙涂料——烘烤固化——密闭放置在干燥通风的地方。
有些人喜欢涂抹机油来达到防锈的目的。
虽然防锈效果不错,但这样做的结果是清洗太麻烦,笔者不大赞同。
其实,在滚塑钢板模具表面涂抹白油不失为一个好的方法。
白油也称液体石蜡,不但能起到防锈作用,还能有润滑效果。
如果模具闲置时间比较长,涂抹白油后,最好烘烤一下,以便于白油在高温下固化,形成一层保护膜。
烘烤模具时和生产滚塑产品一样操作,只是模具内不装粉料,达到粉料熔融时的加工温度就可以了。
注意模具要摆放在通风干燥的地方,密闭保存,严禁接触雨水或腐蚀性的液体、气体等。
滚塑原料内添加一种润滑剂客观上也能起到模具防锈的作用。
其原理也是润滑剂在高温下熔化,冷却后会在模具内表面形成一层保护膜,起到防锈的效果,不过,模具不适于久置不用。
滚塑模具(钢板模)的后期制作工艺流程中国滚塑门户网编辑滚塑模具的前期制作固然很重要,之中的每一个环节都关系到模具制作的成败与否,滚塑企业一般都会采取谨慎的态度。
滚塑模具的前期制作固然很重要,之中的每一个环节都关系到模具制作的成败与否,滚塑企业一般都会采取谨慎的态度来对待,相反,滚塑模具的后期制作往往因为技术程度不高而被忽视,值得一提的是,滚塑模具的后期制作更加关键,其工艺流程和滚塑产品的质量优劣有着必然的密切联系。
但是,我们看到现象却是有相当部分企业不太重视滚塑模具的后期制作,特别是一些生产小型滚塑类玩具的中小型滚塑企业似乎还没有这方面的意识,以至于整个滚塑模具的制作水平没有得到提高,滚塑模具的质量(特别是企业自行生产的钢板模)不容乐观。
滚塑模具(钢板模)的后期制作并没有想象的那么简单,具体操作过程也较为复杂。
其工艺流程图为:模具的平整度调节→ 模面打磨→焊缝补焊→合模调试→ 模面抛光→ 法兰面调试→排气孔设置→喷砂→复位调试→模具清洗→试模判定→防锈处理→脱模剂喷涂(固化)我们来阐述一下上述工艺流程中的每一步的细节可能出现的一些问题及解决这些问题采用的手段方法:1.滚塑钢板模型腔面的平整度调节。
完成钢板模的轮廓制作之后,接下来的工作可以说算是模具的后期制作了。
首先是模具主体的平整度的处理。
这期间,优秀的模具工会对模具的正反两面都进行打磨(这一点很重要,很多模具工只是对模具的正面比较重视,锻压一般都在模具的正面进行而忽略了模具反面不平滑所带来的影响),只有正反两面磨光,双向锻压,才能得到较好的效果。
锻压过程比较原始,纯粹的手工操作,即用铁锤锻打。
铁锤敲击面要预先磨光,不允许有坑点。
这种工艺的结果是模具钢板上会留下密集的疤痕和微小的凹凸,这是滚塑钢板模的一个致命弱点,也是精细滚塑制品的生产放弃使用钢板模的原因之一。
2.模面打磨。
这项工作因为简单,企业一般会选择交给普通的工人来完成。
值得注意的是,模具工应交待好打磨的方法,以及重点部位,以免造成模具钢板被过分打薄。
因为打磨工往往会过多的打磨容易操作的部位,而放弃角落等关键部位的打磨。
打磨所使用的工具为各种形状、规格的油石,金刚锉,砂纸等等。
3.焊缝修补。
打磨过程中模具工要随时注意焊缝漏焊的部位,即使进行修补。
4.合模调试。
钢板模制作采用的工艺与铝合金模具的制作不同,采用的是整体完成再分割的方法,过程中由于模具自身的重力和搬动等因素会有变形量出现,合模调试这道工序一定不能省略。
5.模面抛光。
这个就无需赘述了。
6.法兰面调试。
这直接关系到模具的密合程度,以后滚塑生产中出现溢料现象,多半因为这项工作的疏忽所造成的。
7.排气孔的设置。
这里不能简单的钻孔了事,需结合模具的特点进行制作。
(详见拙文‹‹滚塑模具设计、制作、使用中被忽视的一些重要细节››8.喷砂。
因为钢板模的厚度普遍在—之间,在砂流的冲击下容易产生变形,操作过程中要合理地选择气压参数以及砂丸喷射的角度。
还有砂丸的粒径、规格和材质选择也是值得注意的。
9.复位调试。
无论你的喷砂技艺多么高超,钢板模具通过喷砂处理后,都会出现或多或少的变形量,这就需要对模具做复位调试。
缺少这道工艺会给滚塑工人带来合模操作的难度,甚至会因此而损坏模具。
10.模具清洗。
这项工作如果企业条件容许,最好对模具进行磷化处理。
记住哦,处理过的模具一定要及时烘干,防止出现返锈现象。
11.试模。
这个环节的重要性可能每个人都很明白,我就不再多费口舌了。
12.脱模剂的喷涂。
这一点可根据滚塑产品的特点来选择相应的脱模剂来使用。
关于这个问题本网以后会邀请有关专家撰文,敬请期待。
滚塑模具之钢板模制造工艺简介中国滚塑门户网编辑文/邹克剑目前国内的滚塑模具若要分门别类,按照制作的材质区别,大致可以划分为两类:铝合金模具和钢板模中国滚塑门户网编辑文/邹克剑目前国内的滚塑模具若要分门别类,按照制作的材质区别,大致可以划分为两类:铝合金模具和钢板模。
(有的滚塑企业还有铜模和不锈钢模)网上关于铝合金滚塑模具的制造技术、加工工艺等还有零星半点的介绍和报道,至于钢板滚塑模具,几乎没有相关的内容报道。
应广大滚塑爱好者的要求,笔者将采集到的一些关于滚塑钢板模具制作工艺的信息和资料,进行了归纳和汇总,现整理成拙文一篇,聊作丰富滚塑工艺的网络知识的题材吧!滚塑用钢板模具的制作工艺与铝合金模具的制造方法有着很大的区别,基本上分为以下几个步骤进行:1.托模的制作。